组件工艺流程中英文版
晶圆制造工艺流程英文版9个步骤
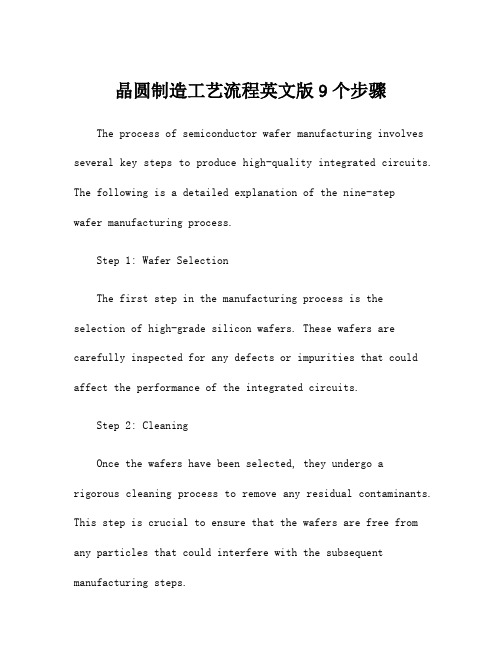
晶圆制造工艺流程英文版9个步骤The process of semiconductor wafer manufacturing involves several key steps to produce high-quality integrated circuits. The following is a detailed explanation of the nine-stepwafer manufacturing process.Step 1: Wafer SelectionThe first step in the manufacturing process is the selection of high-grade silicon wafers. These wafers are carefully inspected for any defects or impurities that could affect the performance of the integrated circuits.Step 2: CleaningOnce the wafers have been selected, they undergo arigorous cleaning process to remove any residual contaminants. This step is crucial to ensure that the wafers are free from any particles that could interfere with the subsequent manufacturing steps.Step 3: Photoresist CoatingAfter the cleaning process, a photoresist material is coated onto the wafers. This material is sensitive to light and is used to transfer the circuit patterns onto the wafers.Step 4: ExposureThe coated wafers are then exposed to ultraviolet light through a mask that contains the desired circuit patterns. This process transfers the patterns onto the photoresist material, creating a template for the circuitry.Step 5: DevelopmentThe exposed wafers are submerged in a developer solution, which removes the unexposed photoresist material. This step reveals the circuit patterns on the wafers, which will serve as a guide for the subsequent etching process.Step 6: EtchingThe wafers undergo a chemical etching process to remove the exposed silicon material, creating the actual circuit patterns on the surface of the wafers.Step 7: DopingDoping is the process of introducing impurities into the silicon to alter its electrical properties. This step is crucial for creating the necessary components, such as transistors, on the integrated circuits.Step 8: MetallizationOnce the circuit patterns have been defined, a thin layer of metal is deposited onto the surface of the wafers. This metal layer serves as the interconnects for the integrated circuits, allowing for electrical signals to pass between components.Step 9: Testing and PackagingThe final step in the manufacturing process involves testing the completed wafers for quality and functionality. Once the wafers have been tested, they are cut intoindividual chips and packaged for distribution to electronics manufacturers.In conclusion, the semiconductor wafer manufacturing process is a complex series of steps that are carefully orchestrated to produce high-quality integrated circuits. Each step plays a crucial role in defining the circuit patterns and ensuring the functionality of the final product.。
(工艺流程)TFT工艺流程、材料、设备、生产常用中英文标准名称
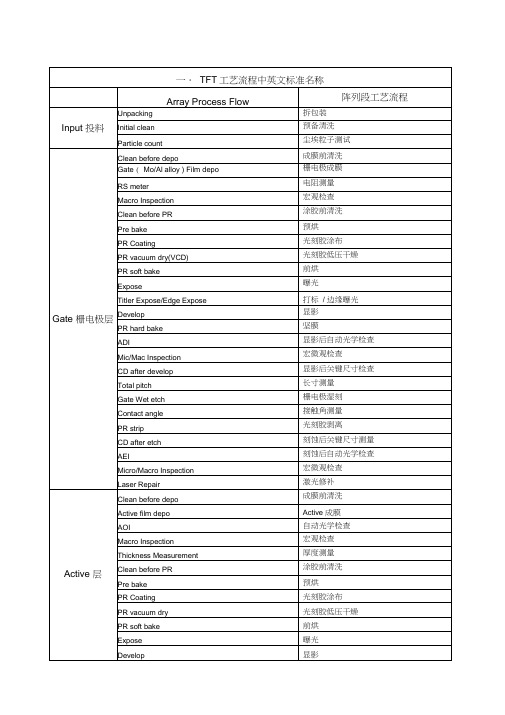
Cutting切割
1/4(1/6)Sheet Cutting,
1/4(1/6)切割
Stick Cutting,
切条
Cell Cutting
切粒
Visual Test
Visual测试
ECP
Edge Grind
磨边
Dipping clean
浸泡式清洗
Clean before Pol
贴片前清洗
Pol Attach
模块段工艺流程
COG
Pad cleaning
端子清洗
IC Bonding
IC邦定
Microscope Inspection
镜检
AOI Adhesive test
自粘动接光力学测检试查
FOG
ACF Attaching
ACF粘贴
FOG Bonding
FOG邦定
Microscope Inspection
镜检
Mic/Mac Inspection
宏微观检查
Active film Dry etch&Ashing
Active膜干刻与灰化
Thickness Measurement
厚度测量
PR strip
光刻胶剥离
AEI
刻蚀后自动光学检查
Mic/Macro Inspection
宏微观检查
S/D源/漏电极层
Clean before depo
打标/边缘曝光
Develop
显影
PR hard bake
坚膜
ADI
显影后自动光学检查
Mic/Mac Inspection
宏微观检查
CD after develop
光伏工艺流程英语
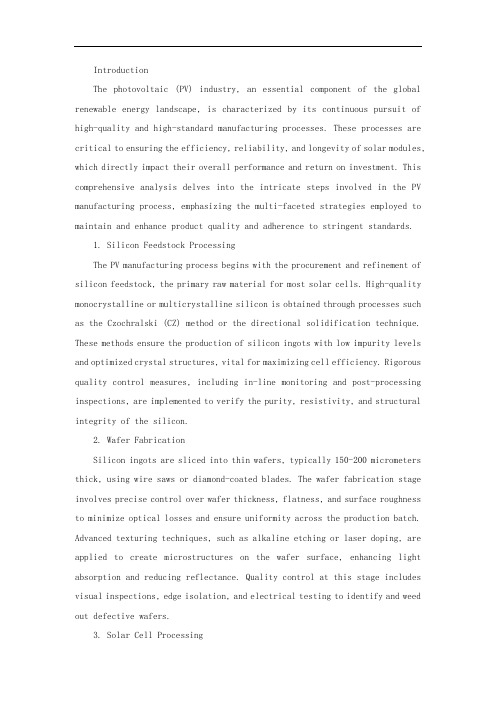
IntroductionThe photovoltaic (PV) industry, an essential component of the global renewable energy landscape, is characterized by its continuous pursuit of high-quality and high-standard manufacturing processes. These processes are critical to ensuring the efficiency, reliability, and longevity of solar modules, which directly impact their overall performance and return on investment. This comprehensive analysis delves into the intricate steps involved in the PV manufacturing process, emphasizing the multi-faceted strategies employed to maintain and enhance product quality and adherence to stringent standards.1. Silicon Feedstock ProcessingThe PV manufacturing process begins with the procurement and refinement of silicon feedstock, the primary raw material for most solar cells. High-quality monocrystalline or multicrystalline silicon is obtained through processes such as the Czochralski (CZ) method or the directional solidification technique. These methods ensure the production of silicon ingots with low impurity levels and optimized crystal structures, vital for maximizing cell efficiency. Rigorous quality control measures, including in-line monitoring and post-processing inspections, are implemented to verify the purity, resistivity, and structural integrity of the silicon.2. Wafer FabricationSilicon ingots are sliced into thin wafers, typically 150-200 micrometers thick, using wire saws or diamond-coated blades. The wafer fabrication stage involves precise control over wafer thickness, flatness, and surface roughness to minimize optical losses and ensure uniformity across the production batch. Advanced texturing techniques, such as alkaline etching or laser doping, are applied to create microstructures on the wafer surface, enhancing light absorption and reducing reflectance. Quality control at this stage includes visual inspections, edge isolation, and electrical testing to identify and weed out defective wafers.3. Solar Cell ProcessingSolar cell processing transforms the silicon wafers into functional devices capable of converting sunlight into electricity. Key steps include:a) Surface Passivation: High-quality dielectric films, such as silicon nitride or aluminum oxide, are deposited on both sides of the wafer to reduce surface recombination and improve minority carrier lifetime, thereby enhancing cell efficiency.b) Diffusion: Phosphorus or boron dopants are introduced into the wafer to form the p-n junction, the heart of the solar cell where photogenerated electrons and holes separate and generate current. Precise control over diffusion temperature, time, and gas concentration is crucial to achieve the desired junction depth and sheet resistance.c) Metallization: Fine-line screen printing or advanced plating techniques are used to deposit metal contacts (usually silver or aluminum) on the front and back surfaces of the cell. The design and layout of these contacts significantly influence cell efficiency by minimizing shading losses and optimizing current collection.d) Anti-Reflection Coating (ARC): A thin layer of silicon nitride or other materials is applied to the front surface of the cell, further reducing surface reflection and enhancing light trapping.Throughout this stage, rigorous quality control measures are in place, including real-time process monitoring, in-line metrology, and periodic sampling for detailed characterization and analysis. These measures ensure compliance with industry standards like IEC 61215 and IEC 61730, which govern the performance, safety, and durability of PV modules.4. Module AssemblyHigh-quality PV modules are assembled from individual cells, encapsulated between ethylene-vinyl acetate (EVA) sheets and protected by a durable glass cover and a weather-resistant backsheet. Stringing the cells in series, soldering interconnects, and laminating the components under vacuum and elevated temperatures ensure electrical connectivity, mechanical stability, andenvironmental protection. Quality control during module assembly encompasses visual inspections, electroluminescence imaging, and flash testing to assess cell-to-cell variations, detect micro-cracks or hotspots, and verify power output and performance parameters.5. Reliability Testing and CertificationTo meet high-standard requirements, PV modules undergo a battery of rigorous reliability tests simulating various environmental and stress conditions they may encounter during their service life. These tests, as outlined in international standards like IEC 61215, IEC 61730, and UL 1703, include thermal cycling, humidity-freeze, damp heat, mechanical load, and potential-induced degradation (PID) tests. Successful completion of these tests earns modules certifications from recognized bodies like TÜV Rheinland, UL, or Intertek, providing assurance of their long-term performance and durability.6. Supply Chain Management and TraceabilityEnsuring high-quality, high-standard PV products also necessitates robust supply chain management and traceability systems. Manufacturers collaborate closely with suppliers to verify the quality and sustainability of raw materials, components, and auxiliary services. Advanced digital platforms enable end-to-end tracking of materials and processes, facilitating quick identification and resolution of quality issues, adherence to international regulations, and fulfillment of customer-specific requirements.ConclusionThe high-quality, high-standard PV manufacturing process is a testament to the industry's commitment to delivering efficient, reliable, and long-lasting solar energy solutions. From the meticulous processing of silicon feedstock to the rigorous testing and certification of finished modules, each stage is infused with a multi-dimensional approach to quality control, technological innovation, and adherence to international standards. As the global shift towards renewable energy accelerates, the ongoing refinement and optimization of this complex process will continue to drive advancements in solar technology, fostering amore sustainable and resilient energy future.。
英文版光伏组件生产工艺

各位,你们好。
我是方文军。
下边是关于光伏组件的生产工艺,也是我的一点学习心得希望对你们有所帮助。
TEL 183******** QQ 724393030.如果有问题,可以随时联络我。
组件线又叫封装线,封装是太阳能电池生产中的关键步骤,没有良好的封装工艺,多好的电池也生产不出好的组件板。
电池的封装不仅可以使电池的寿命得到保证,而且还增强了电池的抗击强度。
产品的高质量和高寿命是赢得可客户满意的关键,所以组件板的封装质量非常重要。
工艺流程如下:1、电池检测——2、正面焊接—检验—3、背面串接—检验—4、敷设(玻璃清洗、材料切割、玻璃预处理、敷设)——5、层压——6、去毛边(去边、清洗)——7、装边框(涂胶、装角键、冲孔、装框、擦洗余胶)——8、焊接接线盒——9、高压测试——10、组件测试—外观检验—11、包装入库;1.2工艺简介:在这里只简单的介绍一下工艺的作用,给大家一个感性的认识,具体内容后面再详细介绍:1、电池测试:由于电池片制作条件的随机性,生产出来的电池性能不尽相同,所以为了有效的将性能一致或相近的电池组合在一起,所以应根据其性能参数进行分类;电池测试即通过测试电池的输出参数(电流和电压)的大小对其进行分类。
以提高电池的利用率,做出质量合格的电池组件。
2、正面焊接:是将汇流带焊接到电池正面(负极)的主栅线上,汇流带为镀锡的铜带,我们使用的焊接机可以将焊带以多点的形式点焊在主栅线上。
焊接用的热源为一个红外灯(利用红外线的热效应)。
焊带的长度约为电池边长的2倍。
多出的焊带在背面焊接时与后面的电池片的背面电极相连。
(我们公司采用的是手工焊接)3、背面串接:背面焊接是将36片电池串接在一起形成一个组件串,我们目前采用的工艺是手动的,电池的定位主要靠一个膜具板,上面有36个放置电池片的凹槽,槽的大小和电池的大小相对应,槽的位置已经设计好,不同规格的组件使用不同的模板,操作者使用电烙铁和焊锡丝将“前面电池”的正面电极(负极)焊接到“后面电池”的背面电极(正极)上,这样依次将36片串接在一起并在组件串的正负极焊接出引线。
焊接工艺流程译成英文

焊接工艺流程译成英文(中英文版)Welding Process Flow: A Comprehensive Translation焊接工艺流程:全面翻译The welding process flow encompasses a series of intricate steps that ensure the fusion of metal parts. It begins with the careful preparation of materials and equipment, followed by the execution of specific welding techniques, and concludes with rigorous inspections to guarantee the integrity of the weld.焊接工艺流程包括一系列确保金属部件融合的复杂步骤。
它从材料与设备的精心准备开始,接着执行特定的焊接技术,并以严格的检查来确保焊接的完整性。
Preparation phase involves cleaning the metal surfaces to remove dirt, oil, and rust, which could compromise the quality of the weld. This is followed by selecting the appropriate welding consumables such as electrodes, filler metals, and shielding gases.准备阶段涉及清洁金属表面,去除可能影响焊接质量的污垢、油污和锈迹。
接下来是选择合适的焊接耗材,如电极、填充金属和屏蔽气体。
In the execution phase, various welding methods such asArc Welding, MIG/MAG Welding, TIG Welding, and Flux-cored Arc Welding are employed based on the material type and thickness. Each method has its unique set of parameters that must be meticulously controlled to achieve optimal results.在执行阶段,根据材料类型和厚度,采用各种焊接方法,如电弧焊、MIG/MAG焊、TIG焊和药芯电弧焊。
线路板(PCB)制作流程中英文对照表

线路板(PCB)制作流程中英⽂对照表线路板(PCB)流程术语中英⽂对照流程简介:开料--钻孔--⼲膜制程--压合--减铜--电镀--塞孔--防焊(绿漆/绿油)--镀⾦--喷锡--成型--开短路测试--终检--雷射钻孔A. 开料( Cut Lamination)a-1 裁板( Sheets Cutting)a-2 原物料发料(Panel)(Shear material to Size)B. 钻孔(Drilling)b-1 内钻(Inner Layer Drilling )b-2 ⼀次孔(Outer Layer Drilling )b-3 ⼆次孔(2nd Drilling)b-4 雷射钻孔(Laser Drilling )(Laser Ablation )b-5 盲(埋)孔钻孔(Blind & Buried Hole Drilling)C. ⼲膜制程( Photo Process(D/F))c-1 前处理(Pretreatment)c-2 压膜(Dry Film Lamination)c-3 曝光(Exposure)c-4 显影(Developing)c-5 蚀铜(Etching)c-6 去膜(Stripping)c-7 初检( Touch-up)c-8 化学前处理,化学研磨( Chemical Milling )c-9 选择性浸⾦压膜(Selective Gold Dry Film Lamination)c-10 显影(Developing )c-11 去膜(Stripping )Developing , Etching & Stripping ( DES )D. 压合Laminationd-1 ⿊化(Black Oxide Treatment)d-2 微蚀(Microetching)d-3 铆钉组合(eyelet )d-4 叠板(Lay up)d-5 压合(Lamination)d-6 后处理(Post Treatment)d-7 ⿊氧化( Black Oxide Removal )d-8 铣靶(spot face)d-9 去溢胶(resin flush removal)E. 减铜(Copper Reduction)e-1 薄化铜(Copper Reduction)F. 电镀(Horizontal Electrolytic Plating)f-1 ⽔平电镀(Horizontal Electro-Plating) (Panel Plating)f-2 锡铅电镀( Tin-Lead Plating ) (Pattern Plating)f-3 低于1 mil ( Less than 1 mil Thickness )f-4 ⾼于1 mil ( More than 1 mil Thickness)f-5 砂带研磨(Belt Sanding)f-6 剥锡铅( Tin-Lead Stripping)f-7 微切⽚( Microsection)G. 塞孔(Plug Hole)g-1 印刷( Ink Print )g-2 预烤(Precure)g-3 表⾯刷磨(Scrub)g-4 后烘烤(Postcure)H. 防焊(绿漆/绿油): (Solder Mask)h-1 C⾯印刷(Printing Top Side)h-2 S⾯印刷(Printing Bottom Side)h-3 静电喷涂(Spray Coating)h-4 前处理(Pretreatment)h-5 预烤(Precure)h-6 曝光(Exposure)h-7 显影(Develop)h-8 后烘烤(Postcure)h-9 UV烘烤(UV Cure)h-10 ⽂字印刷( Printing of Legend )h-11 喷砂( Pumice)(Wet Blasting)h-12 印可剥离防焊(Peelable Solder Mask)I . 镀⾦Gold platingi-1 ⾦⼿指镀镍⾦( Gold Finger )i-2 电镀软⾦(Soft Ni/Au Plating)i-3 浸镍⾦( Immersion Ni/Au) (Electroless Ni/Au)J. 喷锡(Hot Air Solder Leveling)j-1 ⽔平喷锡(Horizontal Hot Air Solder Leveling)j-2 垂直喷锡( Vertical Hot Air Solder Leveling)j-3 超级焊锡(Super Solder )j-4. 印焊锡突点(Solder Bump)K. 成型(Profile)(Form)k-1 捞型(N/C Routing ) (Milling)k-2 模具冲(Punch)k-3 板⾯清洗烘烤(Cleaning & Backing)k-4 V型槽( V-Cut)(V-Scoring)k-5 ⾦⼿指斜边( Beveling of G/F)L. 开短路测试(Electrical Testing) (Continuity & Insulation Testing) l-1 AOI 光学检查( AOI Inspection)l-2 VRS ⽬检(Verified & Repaired)l-3 泛⽤型治具测试(Universal Tester)l-4 专⽤治具测试(Dedicated Tester)l-5 飞针测试(Flying Probe)M. 终检( Final Visual Inspection)m-1 压板翘( Warpage Remove)m-2 X-OUT 印刷(X-Out Marking)m-3 包装及出货(Packing & shipping)m-4 ⽬检( Visual Inspection)m-5 清洗及烘烤( Final Clean & Baking)m-6 护铜剂(ENTEK Cu-106A)(OSP)m-7 离⼦残余量测试(Ionic Contamination Test )(Cleanliness Test) m-8 冷热冲击试验(Thermal cycling Testing)m-9 焊锡性试验( Solderability Testing )N. 雷射钻孔(Laser Ablation)N-1 雷射钻Tooling孔(Laser ablation Tooling Hole)N-2 雷射曝光对位孔(Laser Ablation Registration Hole)N-3 雷射Mask制作(Laser Mask)N-4 雷射钻孔(Laser Ablation)N-5 AOI 检查及VRS ( AOI Inspection & Verified & Repaired)N-6 Blaser AOI (after Desmear and Microetching)N-7 除胶渣(Desmear)N-8 微蚀(Microetching )。
组件工艺流程及设备简介讲课文档
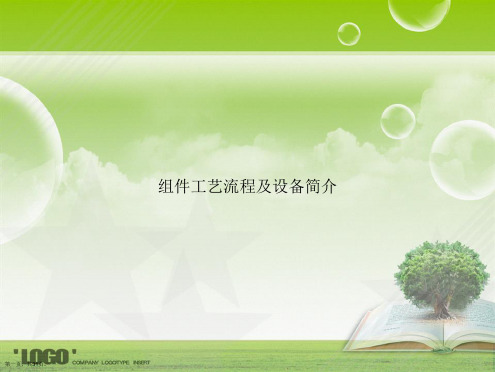
3.工具及作业用品 Tools and operating things. 作业用品应洁净、摆放有序,便于操作,实施定置管理。
Operating things should be clean, orderly place, easy to operate, implement set management.
1)作业用品应洁净、摆放有序,便于操作,实施定置管理。 Operating things should be clean, orderly place, easy to operate, implement set management.
2)戴乳胶指套:拇指、食指、中指必须佩戴(其他手指依情而定),不允许裸手直接接触电池片。
Wipe with a clean cloth to ensure clean, The table without any work-related items before cutting each rool of Backsheet. 2)将背板卷安装在指定位置。
Install the Backsheet roll at the specified location. 3.工具及作业用品 Tools and operating things.
3)手或其他身体部位,不可接触或接近背板(最小距离不得小于30mm);
Hands or other parts of the body, do not touch or close to Backsheet(minimum distance shall not be less than 30 mm) . 4)未使用完的背板需要用保鲜膜封装好退回仓库,已裁切的EVA放置不能超6小时。 Not used the Backsheet needs a good package with plastic wrap and return warehouse, Backsheet has cropped placed not exceed 6 hours.
组件生产流程中英文对照

太阳能电池组件生产流程英文解说中文:太阳能电池组件生产工艺组件线又叫封装线,封装是太阳能电池生产中的关键步骤,没有良好的封装工艺,多好的电池也生产不出好的组件板。
电池的封装不仅可以使电池的寿命得到保证,而且还增强了电池的抗击强度。
产品的高质量和高寿命是赢得可客户满意的关键,所以组件板的封装质量非常重要。
工艺流程如下:1、电池检测——2、正面焊接—检验—3、背面串接—检验—4、敷设(玻璃清洗、材料切割、玻璃预处理、敷设)——5、层压——6、去毛边(去边、清洗)——7、装边框(涂胶、装角键、冲孔、装框、擦洗余胶)——8、焊接接线盒——9、高压测试——10、组件测试—外观检验—11、包装入库;1.2工艺简介:在这里只简单的介绍一下工艺的作用,给大家一个感性的认识,具体内容后面再详细介绍:1、电池测试:由于电池片制作条件的随机性,生产出来的电池性能不尽相同,所以为了有效的将性能一致或相近的电池组合在一起,所以应根据其性能参数进行分类;电池测试即通过测试电池的输出参数(电流和电压)的大小对其进行分类。
以提高电池的利用率,做出质量合格的电池组件。
2、正面焊接:是将汇流带焊接到电池正面(负极)的主栅线上,汇流带为镀锡的铜带,我们使用的焊接机可以将焊带以多点的形式点焊在主栅线上。
焊接用的热源为一个红外灯(利用红外线的热效应)。
焊带的长度约为电池边长的2倍。
多出的焊带在背面焊接时与后面的电池片的背面电极相连。
(我们公司采用的是手工焊接)3、背面串接:背面焊接是将36片电池串接在一起形成一个组件串,我们目前采用的工艺是手动的,电池的定位主要靠一个膜具板,上面有36个放置电池片的凹槽,槽的大小和电池的大小相对应,槽的位置已经设计好,不同规格的组件使用不同的模板,操作者使用电烙铁和焊锡丝将“前面电池”的正面电极(负极)焊接到“后面电池”的背面电极(正极)上,这样依次将36片串接在一起并在组件串的正负极焊接出引线。
4、层压敷设:背面串接好且经过检验合格后,将组件串、玻璃和切割好的EVA 、玻璃纤维、背板按照一定的层次敷设好,准备层压。
- 1、下载文档前请自行甄别文档内容的完整性,平台不提供额外的编辑、内容补充、找答案等附加服务。
- 2、"仅部分预览"的文档,不可在线预览部分如存在完整性等问题,可反馈申请退款(可完整预览的文档不适用该条件!)。
- 3、如文档侵犯您的权益,请联系客服反馈,我们会尽快为您处理(人工客服工作时间:9:00-18:30)。
中文:太阳能电池组件生产工艺组件线又叫封装线,封装是太阳能电池生产中的关键步骤,没有良好的封装工艺,多好的电池也生产不出好的组件板。
电池的封装不仅可以使电池的寿命得到保证,而且还增强了电池的抗击强度。
产品的高质量和高寿命是赢得可客户满意的关键,所以组件板的封装质量非常重要。
工艺流程如下:1、电池检测——2、正面焊接—检验—3、背面串接—检验—4、敷设(玻璃清洗、材料切割、玻璃预处理、敷设)——5、层压——6、去毛边(去边、清洗)——7、装边框(涂胶、装角键、冲孔、装框、擦洗余胶)——8、焊接接线盒——9、高压测试——10、组件测试—外观检验—11、包装入库;1.2工艺简介:在这里只简单的介绍一下工艺的作用,给大家一个感性的认识,具体内容后面再详细介绍:1、电池测试:由于电池片制作条件的随机性,生产出来的电池性能不尽相同,所以为了有效的将性能一致或相近的电池组合在一起,所以应根据其性能参数进行分类;电池测试即通过测试电池的输出参数(电流和电压)的大小对其进行分类。
以提高电池的利用率,做出质量合格的电池组件。
2、正面焊接:是将汇流带焊接到电池正面(负极)的主栅线上,汇流带为镀锡的铜带,我们使用的焊接机可以将焊带以多点的形式点焊在主栅线上。
焊接用的热源为一个红外灯(利用红外线的热效应)。
焊带的长度约为电池边长的2倍。
多出的焊带在背面焊接时与后面的电池片的背面电极相连。
(我们公司采用的是手工焊接)3、背面串接:背面焊接是将36片电池串接在一起形成一个组件串,我们目前采用的工艺是手动的,电池的定位主要靠一个膜具板,上面有36个放置电池片的凹槽,槽的大小和电池的大小相对应,槽的位置已经设计好,不同规格的组件使用不同的模板,操作者使用电烙铁和焊锡丝将“前面电池”的正面电极(负极)焊接到“后面电池”的背面电极(正极)上,这样依次将36片串接在一起并在组件串的正负极焊接出引线。
4、层压敷设:背面串接好且经过检验合格后,将组件串、玻璃和切割好的EVA 、玻璃纤维、背板按照一定的层次敷设好,准备层压。
玻璃事先涂一层试剂(primer)以增加玻璃和EVA的粘接强度。
敷设时保证电池串与玻璃等材料的相对位置,调整好电池间的距离,为层压打好基础。
(敷设层次:由下向上:玻璃、EVA、电池、EVA、玻璃纤维、背板)。
5、组件层压:将敷设好的电池放入层压机内,通过抽真空将组件内的空气抽出,然后加热使EVA熔化将电池、玻璃和背板粘接在一起;最后冷却取出组件。
层压工艺是组件生产的关键一步,层压温度层压时间根据EVA的性质决定。
我们使用快速固化EVA时,层压循环时间约为25分钟。
固化温度为150℃。
6、修边:层压时EVA熔化后由于压力而向外延伸固化形成毛边,所以层压完毕应将其切除。
7、装框:类似与给玻璃装一个镜框;给玻璃组件装铝框,增加组件的强度,进一步的密封电池组件,延长电池的使用寿命。
边框和玻璃组件的缝隙用硅酮树脂填充。
各边框间用角键连接。
8、焊接接线盒:在组件背面引线处焊接一个盒子,以利于电池与其他设备或电池间的连接。
9、高压测试:高压测试是指在组件边框和电极引线间施加一定的电压,测试组件的耐压性和绝缘强度,以保证组件在恶劣的自然条件(雷击等)下不被损坏。
10、组件测试:测试的目的是对电池的输出功率进行标定,测试其输出特性,确定组件的质量等级。
英文:Solar cell module production processLine called packaging line components, packaging is the production of solar cells a key step in the packaging process without a good, multi-well battery is also not a good component of production boards. Battery package not only the battery life is guaranteed, but also to enhance the combat strength of the battery. Product quality and high service life is to win can be the key to customer satisfaction, so the quality of components of the package board is very important.Process is as follows:1, the battery test - 2, positive Welding - Inspection -3, on the back of cascading - Inspection -4, laying (glass cleaning, material cutting, glasspre-processing, laying) - 5, laminating - 6, to flash ( to the side, cleaning) - 7, fitted border (glue, loading angle keys, punching, install box, scrub I glue) - 8, the welding junction box - 9, high-pressure test - 10, component testing -- -11 appearance inspection, packaging and storage;1.2 Process Description:Here only a brief look at the role of technology, give us an emotional understanding of the specific content of a further detail later:1, the battery test: Because the randomness of the battery-chip manufacturing conditions, the production out of battery performance is different, we will be for the effective performance of identical or similar battery together, it should be classified according to their performance parameters; battery test that is by testing the battery output parameters (current and voltage) of the size of its classification. To improve the utilization of the battery to make the battery components of acceptable quality.2, positive welding: It's convergence with soldered to the battery positive (negative) of the main gate line, convergence zone for the tinned copper strip, we use a welding machine can weld with a multi-point in the form of spotwelding on the main gate Online. Welding heat source for an infrared lamp (using infrared thermal effect). Welding with the length of the side length of about 2 times the battery. More welding belt behind the back of welding with electrodes connected to the back of the battery piece. (Our company uses a manual welding)3, on the back of concatenation: back of the weld is 36 cells cascaded together to form a component of the string, we are currently used process is manual, the battery depends mainly on the positioning of a membrane with plate 36 placed above the battery film grooves, groove size and battery size correspond to the location of tank has been designed well, different specifications of the components use a different template, the operator use electric soldering iron and solder wire will "in front of the battery," the positive electrode (cathode) Welding to the "behind the battery" on the back electrode (cathode), so that in turn will be 36 series with the component string together and welded out of positive and negative leads.4, laminated lay: on the back of a good tandem and tested after passing the component string, glass and cut a good EVA, glass fiber, backplane according to a certain level, laying a good preparation for lamination. Glass pre-coated layer of reagent (primer) in order to increase the bonding strength of glass and EVA. When installed to ensure the battery strings and glass and other materials relative position, adjusting the distance between the battery, in order to laminate lay a solid foundation. (Laying of levels: from the bottom up: glass, EVA, cell, EVA, glass fiber, backplane).5, component lamination: a good battery will be laid into the laminating machine, through the vacuum component of the air out, and then heated to melt the EVA batteries, glass and back bonding together; the final cooling out components. Lamination process is a key step in component production, lamination temperature lamination time, according to the nature of EVA. We use the fast-curing EVA, the lamination cycle time is about 25 minutes. Curing temperature of 150 ℃.6, trimming: laminated EVA melt when the pressure of reaching out after curing due to the formation of flash, so it should be removed laminated finish.7, fitted box: similar to the glass mounted to a frame; to the glass component mounted aluminum frame to increase the intensity of the component, further sealing the battery components, longer battery life. Borders and glass components of the gap filled with silicone resin. The border between the connection with the angle button.8, the welding junction box: In the component lead at the back of a box welded to facilitate the battery and other equipment or connections between cells.9, high-pressure test: high-pressure test is defined as components of the border and the electrode lead a certain voltage is applied between the test component of the pressure resistance and dielectric strength to ensure that components in harsh natural conditions (lightning, etc.) will not be damaged under the .10, component testing: the test objective is to calibrate the battery output power to test its output characteristics, determine the quality grade components。