新建炼油厂氢气综合利用和改造探讨
炼厂干气利用的现状
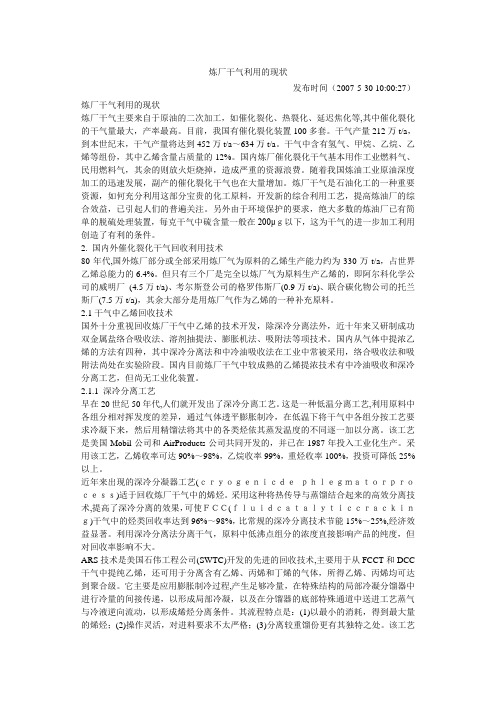
炼厂干气利用的现状发布时间(2007-5-30 10:00:27)炼厂干气利用的现状炼厂干气主要来自于原油的二次加工,如催化裂化、热裂化、延迟焦化等,其中催化裂化的干气量最大,产率最高。
目前,我国有催化裂化装置100多套。
干气产量212万t/a,到本世纪末,干气产量将达到452万t/a~634万t/a。
干气中含有氢气、甲烷、乙烷、乙烯等组份,其中乙烯含量占质量的12%。
国内炼厂催化裂化干气基本用作工业燃料气、民用燃料气,其余的则放火炬烧掉,造成严重的资源浪费。
随着我国炼油工业原油深度加工的迅速发展,副产的催化裂化干气也在大量增加。
炼厂干气是石油化工的一种重要资源,如何充分利用这部分宝贵的化工原料,开发新的综合利用工艺,提高炼油厂的综合效益,已引起人们的普遍关注。
另外由于环境保护的要求,绝大多数的炼油厂已有简单的脱硫处理装置,每克干气中硫含量一般在200μg以下,这为干气的进一步加工利用创造了有利的条件。
2. 国内外催化裂化干气回收利用技术80年代,国外炼厂部分或全部采用炼厂气为原料的乙烯生产能力约为330万t/a,占世界乙烯总能力的6.4%。
但只有三个厂是完全以炼厂气为原料生产乙烯的,即阿尔科化学公司的威明厂(4.5万t/a)、考尔斯登公司的格罗伟斯厂(0.9万t/a)、联合碳化物公司的托兰斯厂(7.5万t/a),其余大部分是用炼厂气作为乙烯的一种补充原料。
2.1干气中乙烯回收技术国外十分重视回收炼厂干气中乙烯的技术开发,除深冷分离法外,近十年来又研制成功双金属盐络合吸收法、溶剂抽提法、膨胀机法、吸附法等项技术。
国内从气体中提浓乙烯的方法有四种,其中深冷分离法和中冷油吸收法在工业中常被采用,络合吸收法和吸附法尚处在实验阶段。
国内目前炼厂干气中较成熟的乙烯提浓技术有中冷油吸收和深冷分离工艺,但尚无工业化装置。
2.1.1 深冷分离工艺早在20世纪50年代,人们就开发出了深冷分离工艺。
这是一种低温分离工艺,利用原料中各组分相对挥发度的差异,通过气体透平膨胀制冷,在低温下将干气中各组分按工艺要求冷凝下来,然后用精馏法将其中的各类烃依其蒸发温度的不同逐一加以分离。
炼厂气中氢气资源的回收和利用_魏瑞
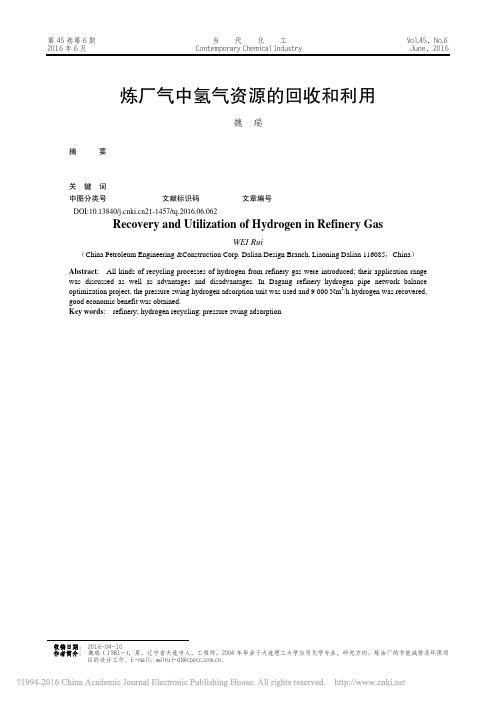
表 1 技术对比表
Table 1 The Sheet of Process Comparison
方案
变压吸附方案
膜分离方案
氢气回收率(保证值),%
〉90
〉93
主要设备投资估算/万元
1 300
1 300
占地面积/ m2
约 900
约 550
氢气纯度(保证值),%
99.9
97
消耗功率/ kW
312
500
综合效益
技术的优缺点。结合大港石化公司全厂氢气管网平衡优化项目,增加变压吸附氢气提纯设施,实际回收约
9000Nm3/h 的高纯度氢气,取得了较为明显的经济效益。
关 键 词:炼油厂;氢气回收;变压吸附
中图分类号:TE 624
文献标识码: A
文章编号: 1671-0460(2016)06-1292-04
DOI:10.13840/21-1457/tq.2016.06.062
随着石油炼制技术的发展和加工深度的提高, 在原油炼制过程中所产生的副产气体即炼厂气的数 量也显著增加。炼厂气主要来源于原油炼制的二次 加工过程,如催化裂化装置、催化重整装置、加氢 裂化装置、延迟焦化装置等。不同装置的炼厂气其 组成不尽相同,其中氢气的含量也大相径庭。如催 化重整装置炼厂气中氢气含量就很高,是炼油厂氢 气的重要来源[1]。长期以来因无适合的分离方法利 用氢气等资源,大部分作为燃料气烧掉,造成巨大 浪费。研发多种氢气提纯工艺,尽可能的回收炼厂 气中富含的氢气,可以使氢气生产工艺灵活多样化, 有效地降低氢气生产成本,具有良好的经济效益和 社会效益[2]。
氢裂化装置能力的增加而增加,一般是原油的 0.8%~1.4%。
综上所述,氢气已成为原油加工过程中不可缺 少的一种重要产品,并且随着人们对燃料清洁性要 求的日益提高,炼油厂对氢气的需求将越来越大。
炼厂的氢气与氢气供应20111009
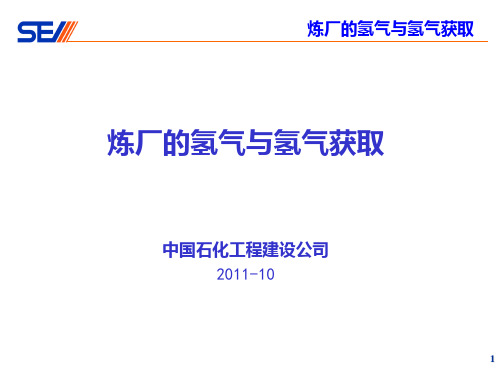
组成 H2 C1 C2 C3 C4 C5 C5+
29
炼厂的氢气与氢气获取
加氢低分气
典型的加氢裂化低分气组成
组成 H2 CH4 C2H6 C3H8 C4H10 C5H12 C5+ 空气 H2S ppm * 脱硫后 天津石化 80.72 9.01 1.68 2.25 0.24 齐鲁(II) 87.21 4.93 1.19 1.38 1.32 0.21 0.01 1.45 10600 扬子(I) 65.2 21.8 5.58 3.36 3.29 0.79 高桥* 64.01 9.78 7.7 7.32 5.90 1.8 2.71 4
22
炼厂的氢气与氢气获取 1.4 氢气在其它领域的需求
全球氢气消费分布图
23
炼厂的氢气与氢气获取 1)氢气是一种高效的清洁能源载体 氢气是公认的高能清洁燃料,用于各种航天器的发射。 氢气燃烧性能好、点火快,与空气混合时有广泛的可燃范 围,而且燃点高、燃烧速度快。 除核燃料外氢气的发热值是所有化石燃料、化工燃料和生 物燃料中最高的,为142.35kJ/kg,是汽油发热值的3倍。 2)以氢气为载体的新能源革命是未来氢气最大的潜在需求。
加氢装置
聚乙烯、聚丙烯装置
硫磺回收装置
不同装置对氢气的数量和规格要求不同
3
炼厂的氢气与氢气获取
1. 1 炼厂用氢
1) 加氢类装置
对于氢气规格的要求
CO+CO2 <= 10 ppmv (有时要求为20ppmv)
氢气纯度:通过经济对比根据加氢装置的氢分 压要求确定
主要加氢装置的耗氢量
4
炼厂的氢气与氢气获取 1) 加氢装置 主要加氢装置的耗氢量
炼厂尾气回收氢气及轻烃研究

炼厂尾气回收氢气及轻烃研究引言炼厂的尾气中含有大量的氢气和轻烃,这些资源可以通过尾气回收的方式得以利用,不仅能够提高炼厂的资源利用效率,还能够降低环境污染。
本文将对炼厂尾气回收氢气及轻烃的研究进行探讨。
一、尾气中的氢气1.原理炼厂在生产过程中会产生大量的尾气,其中含有的氢气可以通过回收的方式得到利用。
尾气回收氢气的原理主要是基于物理吸附和吸附分离的原理,将尾气中的氢气吸附到特定的吸附剂上,然后通过再生操作将吸附剂上的氢气释放出来。
2.技术尾气回收氢气的技术主要包括压力摩擦吸附(PSA)和温度摩擦吸附(TSA)两种方法。
PSA技术是通过不同的吸附剂的吸附特性来实现氢气的分离,而TSA技术则是通过调节吸附剂的温度来实现氢气的分离。
3.应用尾气回收的氢气可以应用于炼厂的各个环节,例如用于燃料供应、提供制氢工艺所需的气体、作为化学反应中的还原剂等等。
二、尾气中的轻烃1.原理尾气中的轻烃可通过类似于氢气回收的方法得以利用。
轻烃的回收主要基于物理吸附和分馏的原理,通过调节吸附剂的吸附特性和分馏塔的操作来分离得到纯净的轻烃。
2.技术尾气回收轻烃的技术主要包括吸附分离、分子筛吸附和低温凝淬等方法。
吸附分离是通过选择性吸附的原理实现轻烃的分离,而分子筛吸附则是利用吸附剂的特殊结构来实现轻烃的分离,低温凝淬则是通过降低温度使轻烃凝结为液态。
3.应用尾气回收的轻烃可以用于炼厂内部的能源供应,也可以进行压缩和储存后用于出售或外部供应。
三、尾气回收氢气及轻烃的优势和挑战1.优势尾气回收氢气及轻烃可以提高炼厂的资源利用效率,减少对外能源的依赖。
此外,尾气回收还可以减少对环境的污染,降低炼厂的碳排放。
2.挑战尾气中的氢气和轻烃含量较低,需要采用高效的分离和回收技术才能实现经济可行的回收。
此外,尾气中的杂质、温度和压力变化等因素也对回收过程产生影响。
结论炼厂尾气回收氢气及轻烃的研究具有重要的意义,可以提高资源利用效率,减少环境污染。
氢气生产技术的改进与创新

氢气生产技术的改进与创新氢气作为一种清洁、高效的能源,受到越来越多人的关注和重视。
随着社会的发展和环境问题的日益凸显,成为了当前研究的热点之一。
在过去的几十年里,人们对氢气的生产技术进行了多方面的探索和改进,不断寻求更加环保、高效的生产方式,并取得了一定的成果。
传统的氢气生产技术主要包括炭氢化学法、水蒸气重整法、电解法等。
虽然这些方法在一定程度上能够满足氢气的需求,但是却存在着一些不足之处。
比如炭氢化学法产生二氧化碳等有害气体,水蒸气重整法存在能源浪费问题,电解法则存在电能利用率低的缺陷。
因此,如何改进和创新氢气生产技术,成为了当前研究的重要课题之一。
近年来,随着科技水平的不断提升,一些新型的氢气生产技术逐渐被引入到研究和实践中。
其中,太阳能水电解技术、生物质气化制氢技术、催化重组技术等备受关注。
太阳能水电解技术利用太阳能作为能源,通过电解水来产生氢气,不仅无污染、能源丰富,而且能够有效解决能源短缺问题。
生物质气化制氢技术则是利用生物质作为原料,通过气化反应来制备氢气,既能降低碳排放,又能有效利用再生能源。
催化重组技术则是通过催化剂引发氢气生成的化学反应,提高了生产效率和氢气纯度。
在氢气生产技术的改进与创新中,催化剂的研究和开发起着至关重要的作用。
催化剂作为氢气生产的关键,直接影响生产效率和氢气纯度。
传统的催化剂存在着稳定性差、成本高等问题,限制了氢气生产技术的发展。
因此,需要不断研究和开发高效、稳定的催化剂,以提高氢气生产技术的效率和经济性。
除了催化剂的研究,反应器的设计与改进也是氢气生产技术的重要方面。
传统的反应器存在着能源浪费、生产效率低等问题,需要不断优化和改进。
通过采用新型的反应器设计,提高反应器的稳定性和效率,能够进一步提高氢气生产技术的整体性能。
此外,智能化技术在氢气生产技术中的应用也逐渐受到关注。
智能化技术可以通过传感器、自动化控制等手段,实现对氢气生产过程的智能监控和调控,提高了生产的精准度和稳定性。
氢气在石化工业中的应用
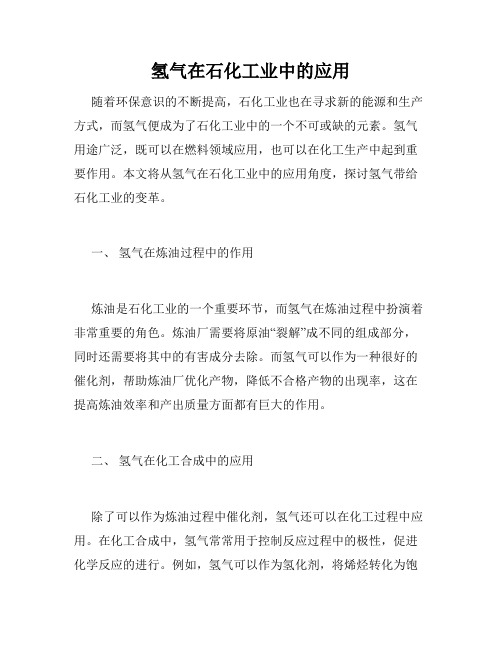
氢气在石化工业中的应用随着环保意识的不断提高,石化工业也在寻求新的能源和生产方式,而氢气便成为了石化工业中的一个不可或缺的元素。
氢气用途广泛,既可以在燃料领域应用,也可以在化工生产中起到重要作用。
本文将从氢气在石化工业中的应用角度,探讨氢气带给石化工业的变革。
一、氢气在炼油过程中的作用炼油是石化工业的一个重要环节,而氢气在炼油过程中扮演着非常重要的角色。
炼油厂需要将原油“裂解”成不同的组成部分,同时还需要将其中的有害成分去除。
而氢气可以作为一种很好的催化剂,帮助炼油厂优化产物,降低不合格产物的出现率,这在提高炼油效率和产出质量方面都有巨大的作用。
二、氢气在化工合成中的应用除了可以作为炼油过程中催化剂,氢气还可以在化工过程中应用。
在化工合成中,氢气常常用于控制反应过程中的极性,促进化学反应的进行。
例如,氢气可以作为氢化剂,将烯烃转化为饱和烃。
氢气还可以作为生成乙醇的催化剂,使食品和药品工业的生产过程更加高效。
三、氢气在能源领域中的作用氢气不仅在石化工业中发挥作用,在能源领域中也具有广泛的应用。
由于氢气的燃烧不会产生二氧化碳排放,因此被视为未来的一种可替代化石燃料的新能源。
氢燃料电池便是氢气的一个重要应用,可达到高效、低耗和环保等多重功能。
四、氢气在环保领域中的作用氢气的应用还能更进一步,将其用于环保领域。
由于氢气的燃烧不会产生任何温室气体,因此在环保方面具有得天独厚的优势。
此外,氢气还可以作为石化工业废水和气体的处理剂,使石化工业更加环保、清洁。
总之,随着环保意识的提高,氢气作为一种新的能源和化学品,已经在石化工业中发挥了越来越多的作用。
从催化剂到燃料、从化学合成到环保领域,氢气正不断地为石化工业带来变革,在推动石化工业可持续发展方面具有重要作用。
柴油加氢改质装置节能降耗技术分析与对策

柴油加氢改质装置节能降耗技术分析与对策一、柴油加氢改质装置的技术原理柴油加氢改质装置,简称加氢装置,是通过在柴油发动机的进气道中加入氢气,利用氢气与柴油混合燃烧,从而提高燃烧效率,减少尾气排放,降低燃油消耗的一种技术手段。
其技术原理主要包括以下几个方面:1. 燃烧效率提高:通过向柴油中加入氢气,可以使得燃油在燃烧过程中更加充分,提高燃烧效率,从而减少燃油的消耗。
2. 尾气排放降低:氢气在燃烧过程中可以与氧气充分混合,从而减少燃烧产生的有害气体,降低尾气排放。
3. 发动机功率提升:利用氢气的高热值特性,可以提高柴油发动机的实际功率输出,实现动力提升的效果。
2. 排放水平降低:氢气的加入可以改善柴油发动机的燃烧过程,减少有害气体的排放,对环境保护具有显著效果。
在实际应用柴油加氢改质装置时,需要克服一些技术难题,从而实现更好的节能降耗效果。
以下是针对柴油加氢改质装置的技术对策:1. 加氢装置的稳定性:加氢装置在柴油发动机中的工作稳定性是关键,需要解决在车辆长时间运行或在极端环境下出现的稳定性问题。
2. 加氢装置的安全性:在加氢改质过程中,需要保证氢气供应系统的安全和稳定,避免出现安全隐患。
3. 加氢装置的成本控制:加氢装置需要在成本可控的基础上提供良好的节能降耗效果,因此需要在技术和成本的平衡上进行合理的控制。
4. 加氢装置与柴油发动机的匹配问题:加氢装置需要与柴油发动机良好的匹配,保证在不影响发动机正常工作的情况下提供更好的节能降耗效果。
四、结语柴油加氢改质装置的节能降耗技术具有很大的应用前景,需要不断进行技术创新和实践应用,从而为我国能源资源的可持续发展作出更大的贡献。
加油加氢可行性研究报告

一、研究目的随着环保要求的不断提高和气候变化的持续加剧,替代传统石油燃料成为一种必然趋势。
加氢技术作为一种可持续发展的替代燃料技术备受关注。
本研究旨在探讨加氢作为替代传统燃料的可行性,并对加油加氢的实施进行深入分析。
二、加氢技术简介加氢技术是指利用氢气作为能源,并将其应用于交通运输。
加氢燃料电池车是一种零排放的交通工具,其底盘结构和车身设计与传统汽油车基本相同,使用氢气作为燃料来产生电能。
由于氢气燃烧后只产生水和热,对环境不会产生任何污染,且能源利用效率高,成为替代传统燃料的重要选择。
三、加氢技术的优势1. 零排放:氢气燃料电池车只会产生水蒸气,不会排放任何有害气体,对大气环境没有任何污染。
2. 高效能源利用:加氢技术能够更有效地将能量转换为动力,与传统的内燃机相比,能源利用效率更高。
3. 快速加氢:相较电动汽车充电时间很长,氢气燃料电池车快速充氢只需约3-5分钟,用户体验更好。
4. 安全性:氢气是一种轻质气体,如果发生泄漏会快速上升到大气中,相对于液态燃料的易燃易爆性更加安全。
四、加油加氢的可行性分析加油加氢的可行性是指在当前国内交通状况下,推广加氢技术并构建加氢加油站的现实可行性。
1. 行业发展趋势:我国在新能源汽车领域发展迅速,政府提出的规划和政策支持为加氢技术的推广提供了有力保障。
2. 技术成熟度:目前国内外对加氢技术的研究和应用已经相对成熟,加氢车型的推广将受到技术层面的保障。
3. 加氢设施建设:加氢技术需要建设相应的加氢设施,包括加氢站等,当前国内已经有相关的规划和建设计划。
4. 运营成本考量:相比于传统汽油车,加氢技术存在一定的成本差距。
但随着技术的进步和规模的扩大,加氢技术的成本将逐渐降低。
1. 国内政策支持:政府提出的新能源汽车补贴政策和加氢技术推广的政策将成为加氢市场发展的有力推动力。
2. 能源供给保障:加氢技术需要大量的氢气供应,目前国内外已经有大量的氢气生产基地和供给方式,为加氢技术的市场发展提供了保障。
- 1、下载文档前请自行甄别文档内容的完整性,平台不提供额外的编辑、内容补充、找答案等附加服务。
- 2、"仅部分预览"的文档,不可在线预览部分如存在完整性等问题,可反馈申请退款(可完整预览的文档不适用该条件!)。
- 3、如文档侵犯您的权益,请联系客服反馈,我们会尽快为您处理(人工客服工作时间:9:00-18:30)。
新建炼油厂氢气综合利用和改造探讨
摘要:本文介绍了炼油厂通过技术改造氢气回收项目、优化供氢网络、强化用氢管理等措施整合了氢气系统资源,有效实现了节能降耗和降低油品加工成本的目的。
关键词:氢优化氢气平衡氢气回收氢气网络
氢气是一种宝贵而洁净的资源,在炼油行业中,它既是石油炼制和石油化工的副产品,又是石油炼制和石油化工加氢工艺过程的重要原料,近年来随着氢气供需矛盾的加剧,对炼油厂的氢气资源进行优化利用具有重要意义。
本论文以中国石油某炼油厂的氢气资源优化项目为依托,对氢气资源的优化利用取得的成果进行研究。
一、氢气产出和利用分析
该炼油厂是中国石油在南方地区投资建设的第一个大型炼化基地,也是中国石油海外份额油加工基地,原油加工能力为1000万吨/年,项目包括13套主要工艺装置,及其配套的公用工程系统、储运系统、码头、铁路等设施。
氢气管网的供氢来源为制氢装置和psa1回收氢气,管网压力为 2.1mpa(g),温度为40℃,氢纯度为99.9 % ( v ),主要为蜡油加氢裂化装置、柴油加氢精制装置、汽油精制分馏装置、硫磺回收装置、聚丙烯装置供氢。
石脑油加氢装置所用氢气来自连续重整装置重整循环氢。
其中制氢装置规模为40000m3/h,加工原料为石脑油和炼厂气。
psa1规模为120000m3/h,加工原料为连续重整装置所产的重整氢和经过脱硫处理的蜡油加
氢裂化低分气和柴油加氢精制低分气。
全厂投料试车阶段,制氢装置先开工低负荷运行,为石脑油加氢装置备料试车提供氢气,同时为加氢裂化装置、柴油加氢装置、连续重整等临氢单元提供氢气进行氢气置换、气密,在正式投料试车阶段,制氢装置先开工为加氢裂化、柴油加氢装置提供催化剂硫化所需氢气。
在正常生产阶段,主要通过psa1装置为全厂提供氢气,同时制氢装置处于热备状态。
根据全厂氢气平衡和燃料气平衡的计算,催化干气直接排入燃料气管网,以弥补燃料气的不足。
当psa1故障情况下,立即提高制氢装置负荷。
根据全厂氢气平衡,此时计划安排加氢裂化装置停工。
制氢装置产氢以维持柴油加氢装置、石脑油加氢、汽油精制分馏、硫磺回收、聚丙烯等装置维持正常生产运行。
二、氢气优化利用采取的措施
按两步走的总体计划实施,在管网优化改造实施前,主要通过调整连续重整的操作来调整氢网平衡,减少放空损失。
从3月份起开始采用该思路调整氢气管网的操作,与之前用加氢裂化新氢机入口缓冲罐放空控制的方式相比,压控放空阀开度由10%左右减少为0~2%,放空量大幅减少,减少高纯氢气放空2000~3000m3/h,节约成本近2400万元/年。
6月份完成了psa1的检修消缺。
psa1装置由于设计原因,均压线管径过大,导致程控阀过度冲刷而产生泄漏,此次停工检修,分别在各吸附塔3#、4#、6#程控阀处安装限流孔板。
并对已穿透的b、e、g、f塔进行撇头。
氢气管网优化方案设计中,决定将含硫油配套装置投产以后的整个管网分为相对独立的两个部分,新上的渣油加氢、异构化和大制氢作为一个部分,柴油加氢改质和现有系统作为一个部分,用小制氢的负荷来调节管网的平衡,减少放空;同时该方案增加了pas1解析气去制氢做原料气的流程,psa1的解析气含氢量50~60%,是优质的制氢原料,但作为燃料气体积热值较低,因此用解析气做制氢原料与天然气做燃料对换是经济的选择。
三、正在研究解决的问题
1.需解决psa1长周期运行的问题
1.1psa1进一步改造。
由于技术供应商对大规模psa装置设计经验不足,多项设计缺陷导致psa1难以长周期运行,2012年6月已对均压线管径问题进行了整改,但解析气压缩机不上量等问题尚未解决,需组织专家对psa1装置进行综合研究,彻底消除缺陷和隐患,做到与其他炼油装置同步长周期运行。
1.2加氢低分气分流。
从目前的运行情况来看,加氢的低分气是影响psa1装置的长周期运行的重要因素之一。
一方面现有的上游装置流程中低分气胺洗后未设置水洗或聚结器装置,将富胺液携带至psa1,导致系统易结盐堵塞;另一方面低分气的组分相对比较复杂,大分子烃类较多,易造成吸附剂饱和。
解决方案一是在上游加氢装置增加水洗罐或聚结器,脱除低分气中的微量富胺液;方案二考虑对psa2进行改造,专用于四套加氢装置的低分气回收处理。
2.需解决汽油加氢装置废氢出路
汽油加氢装置的废氢因压力低无法进入psa回收,其中一期废氢压力0.35mpa,排放量为400~500 m3/h,原设计该股气体应并入催化裂化气压机入口,但实际操作中是排低压火炬系统,严重影响火炬气的正常回收;二期新增废氢压力 0.66mpa,设计排放
612m3/h,设计方案中采用直接排燃料气管网或火炬放空管网。
为减少对燃料气管网的冲击,计划将这股废氢在装置内部作为燃料自用,正常情况下不允许进入全厂管网。
四、总结
因系统设计缺陷和装置检修周期等因素影响,氢气系统优化课题取得阶段性成果,今后尚有很多工作要做。
作为全加氢型炼厂,氢气系统的优化直接关系到公司的精细化管理质量和经营绩效,系统的完善将使炼厂的每一股富氢组分得到合理充分利用。
对新时期新建炼油厂的平稳生产,节能降耗,资源综合利用有较好的参考意义。
参考文献
[1]梁铁伟;国外炼厂氢气的回收与优化利用[j];国外油田工程;2002年02期.
[2]凌逸群,张强;燕化公司氢气资源现状及综合利用对策[j];石化技术;1999年04期.
[3]陈苏;在炼油厂中寻找新的氢源和制氢原料[j];石油炼制与化工;2001年09期.
[4]刘伯龙,孙樵,毕文波,杨连栋,庄福成,刘贞华;焦化气制氢工艺的开发及工业应用[j];石油炼制与化工;1996年01期.。