成本会计第四章课后答案
清华大学成本会计第四章答案

CHAPTER 2AN INTRODUCTION TO COST TERMS AND PURPOSES2-1 A cost object is anything for which a separate measurement of costs is desired. Examples include a product, a service, a project, a customer, a brand category, an activity, and a department. 2-2Cost assignment is a general term that encompasses the assignment of both direct costs and indirect costs to a cost object. Direct costs are traced to a cost object while indirect costs are allocated to a cost object.∙Direct costs of a cost object are related to the particular cost object and can be traced to it in an economically feasible (cost-effective) way.∙Indirect costs of a cost object are related to the particular cost object but cannot be traced to it in an economically feasible (cost-effective) way.2-3Managers believe that costs that are traced to a particular cost object are more accurately assigned to that cost object than are allocated costs. Managers prefer to use more accurate costs in their decisions.2-4Factors affecting the classification of a cost as direct or indirect include: ∙the materiality of the cost in question,∙available information-gathering technology,∙design of operations, and∙contractual arrangements.2-5Manufacturing-sector companies purchase materials and components and convert them into different finished goods.Merchandising-sector companies purchase and then sell tangible products without changing their basic form.Service-sector companies provide serices or intangible products to their customers for example, legal advice or audits.2-6 A cost driver is a factor, such as the level of activity or volume, that causally affects costs (over a given time span).A change in the cost driver results in a change in the cost of the cost object. For example, number of vehicles assembled is a driver of the costs of steering wheels on a motor-vehicle assembly line.2-7 A variable cost changes in total in proportion to changes in the related level of total activity or volume. An example is a sales commission that is a percentage of each sales revenue dollar.A fixed cost remains unchanged in total for a given time period despite wide changes in the related level of total activity or volume. An example is the leasing cost of a machine that is unchanged for a given time period (such as a year).2-8The relevant range is the band of activity or volume in which a specific relationship between the level of activity or volume and the cost in question is valid. This concept enables the use of linear cost functions when examining cost-volume-profit (CVP) relationships as long as the volume levels are within that relevant range.2-9 A unit cost is computed by dividing some amount of total costs (the numerator) by the related number of units (the denominator). In many cases, the numerator will include a fixed cost that will not change despite changes in the denominator. It is erroneous in those cases to multiply the unit cost by activity or volume change to predict changes in total costs at different activity or volume levels.2-10Manufacturing companies typically have one or more of the following three types of inventory.1.Direct materials inventory. Direct materials in stock and awaiting use in themanufacturing process.2.Work-in-process inventory. Goods partially worked on but not yet fully completed.Also called work in progress.3.Finished goods inventory. Goods fully completed but not yet sold.2-11Inventoriable costs are all costs of a product that are regarded as an asset when they are incurred and then become cost of goods sold when the product is sold. These costs are included in work-in-process and finished goods inventory (they are "inventoried") to build up the costs of creating these assets.Period costs are all costs in the income statement other than cost of goods sold. These costs are treated as expenses of the period in which they are incurred because they are presumed not to benefit future periods (or because there is not sufficient evidence to conclude that such benefit exists). Expensing these costs immediately best matches expenses to revenues.2-12No. Service sector companies have no inventories and, hence, no inventoriable costs.2-13 Direct materials costs are the acquisition costs of all materials that eventually become part of the cost object ("work-in-process" or "finished goods"), and that can be traced to the cost object in an economically feasible way.Direct manufacturing labor costs include the compensation of all manufacturing labor that can be traced to the cost object in an economically feasible way.Indirect manufacturing costs are all manufacturing costs that are considered part of the cost object, units finished or in process, but that cannot be traced to that cost object in an economically feasible way.Prime costs are all direct manufacturing costs.Conversion costs are all manufacturing costs other than direct material costs.2-14 Overtime premium consists of the wage rate paid to all workers (for both direct labor and indirect labor) in excess of their straight-time wage rates.Idle time is a subclassification of indirect labor that typically represents wages paid for unproductive time caused by lack of orders, machine breakdowns, material shortages, poor scheduling, and the like.2-15 A product cost is the sum of the costs assigned to a product for a specific purpose.Purposes for computing a product cost include: • Pricing and product emphasis decisions. • Contracting with government agencies.• Preparing financial statements for external reporting under generally accepted accounting principles.2-16 (10 min.) Total costs and unit costs.1. Total cost, $4,000. Unit cost per person, $4,000 ÷ 500 = $8.002. Total cost, $4,000. Unit cost per person, $4,000 ÷ 2,000 = $2.003. The main lesson of this exercise is to alert the student early in the course to the desirability of thinking in terms of total costs rather than unit costs wherever feasible. Changes in the denominator (the level of total activity or volume in this case attendance) will affect total variable costs but not total fixed costs . In our example, it would be perilous to use either the $8.00 or the $2.00 unit cost to predict the total cost because the total costs are not affected by the attendance. Instead, the student association should use the $4,000 total cost. Obviously, if the musical group agreed to work for, say, $4.00 per person, such a unit variable cost could be used to predict the total cost.2-17 (15 min.) Total costs and unit costs.1. (a) $100,000 ⎪ 2,000 = $50.00 per package (b) $100,000 ⎪ 6,000 = $16.67 per package (c) $100,000 ⎪ 10,000 = $10.00 per package (d) [$100,000 + (10,000 × $8)] ⎪ 20,000 = $180,000 ⎪ 20,000 = $9.00 per packageThe unit cost to ECG decreases on a per -unit base due to the first $100,000 payment being a fixed cost. The $8 amount per package beyond 10,000 units is a variable cost. The cost function is:10,000 20,000 30,000 Total CostsPackages SoldPoint is $260,000 and 30,0002-17 (Cont’d.)2.ECG should not use any of the unit costs in requirement 1 when predicting total costs. Up to 10,000 units, the total cost is a fixed amount. Beyond 10,000 units, the total cost is a combination of a fixed amount plus a per-unit (beyond 10,000 unit) variable amount. The total costs at different volume levels cannot be predicted by using the unit cost at a specific volume level. The total cost should be predicted by combining the total fixed costs and total variable costs rather than multiplying a unit cost amount by the predicted number of packages sold.2-18 (15 min.)Computing and interpreting unit manufacturingcosts.1.Supreme Deluxe RegularDirect materials costs $ 84.00 $ 54.00 $ 62.00Direct manuf. labor costs 14.00 28.00 8.00Indirect manuf. costs 42.00 84.00 24.00Total manuf. costs $140.00 $ 166.00 $ 94.00Pounds produced 80 120 100Cost per pound $ 1.7500 $ 1.3833 $0.94002.The unit costs in requirement 1 includes $20 million of indirect manufacturing costs that are fixed irrespective of changes in the volume of output per month, while the remaining variable indirect manufacturing costs change with the production volume. Given the unit volume changes for August 2001, the use of unit costs from the past month at a different unit volume level (both in aggregate and at the individual product level) will yield incorrect estimates of total costs in August 2001.2-19(20 min.) Direct and indirect costs, effect of changing the classification ofa cost item1.Direct costs are costs that are related to the particular paper products (Supreme, Deluxe, or Regular) and can be traced to each one in an economically feasible (cost-effective) way.Indirect costs are costs that are related to the particular paper products (Supreme, Deluxe, or Regular) but cannot be traced to each one in an economically feasible (cost-effective) way.2.Energy costs of $90 million can be traced to each individual production line. This tracing will result in a more accurate assignment of costs to products than when the $150 million of indirect manufacturing costs ($20 million of which is fixed) is allocated using direct manufacturing labor costs at each line. The $90 million of energy costs do not have an identical relationship to direct manufacturing labor costs for each product line as is assumed when the direct manufacturing labor cost allocation base is used in Question 2-18:Supreme Deluxe Regular Total1. Direct energy costs $39.800 $40.700 $9.500 $90.0002. Direct manuf. labor cost 14.000 28.000 8.000 50.0003. Ratio of 1 to 2. 2.843 1.454 1.187 1.800The Supreme product line has the most energy intensive usage vis-à-vis its direct manufacturing labor cost content. The result is that the supreme product line will be undercosted when the Exercise 2-18 unit cost numbers are used.3.Supreme Deluxe RegularDirect materials costs $ 84.000 $ 54.000 $62.000Direct manuf. labor costs 14.000 28.000 8.000Direct energy costs 39.800 40.700 9.500Indirect manuf. costs 16.800 33.600 9.600Total manuf. costs $154.600 $156.300 $89.100Pounds produced 80 120 100Cost per pound $ 1.9325 $ 1.3025 $0.8910The unit cost amounts are:Supreme Deluxe Regular1. Exercise 2-19 $1.9325 $1.3025 $0.89102. Exercise 2-18 1.7500 1.3833 0.9400Ratio of 1 to 2 1.1043 0.9416 0.9479As predicted in requirement 2, the tracing of the higher than average energy costs to Supreme results in an increase in reported unit costs for the Supreme product line.2-20 (15 min). Cost drivers and the value chain.1.Business Function Representative Cost Driver Production ∙Hours the Tylenol packaging line is in operationResearch and Development ∙Number of patents filed with U.S. Patent office.Marketing ∙Minutes of TV advertising timeon "60 Minutes"Distribution ∙Number of packages shippedDesign of Products/Processes ∙Hours spent designing tamper-proof bottlesCustomer Service ∙Number of calls to toll-free customerphone line2.Business Function Representative Cost Driver Research and Development •Hours of laboratory work•Number of new drugs in development Design of Products/Processes •Number of focus groups on alternative package designs•Hours of process engineering work Production •Number of units packaged•Number of tablets manufacturedMarketing •Number of promotion packages mailed•Number of sales personnelDistribution •Weight of packages shipped•Number of supermarkets on delivery route Customer Service •Number of units of a product recalled•Number of personnel on toll-free customer phone lines2-21 (15 min.) Cost drivers and the value chain.1.Business Function Representative Cost DriverDesign of Products/Processes ∙Hours of computer-aided design (CAD) work Customer Service ∙Number of cars recalled due to defective parts Marketing ∙Number of sales personnelResearch and Development ∙Number of research scientistsProduction ∙Number of machine assembly-hoursDistribution ∙Weight of cars shipped2.Business Function Representative Cost Driver Research and Development •Square feet of R&D laboratory space•Number of new models being developed Design of Products/Processes •Number of focus groups on alternative colorcombinations•Hours of process engineering time on retoolingassembly equipmentProduction •Direct manufacturing labor-hours•Kilowatt hours of energy consumed Marketing •Number of advertisements on television•Number of total mailings to existing customersabout new modelDistribution •Number of vehicles shipped•Number of distributors in sales area Customer Service •Number of personnel on toll-free customerphone lines•Number of packages mailed about safetycomplaints with existing model2-22 (15-20 min.) Variable costs and fixed costs.1.Variable cost per ton of beach sand mined:Subcontractor $ 80 per ton Government tax 50 per ton Total $130 per ton Fixed costs per month:0 to 100 tons of capacity per day = $150,000 101 to 200 tons of capacity per day = $300,000 201 to 300 tons of capacity per day= $450,0002.T o t a l F i x e dC o s t s$450,000$300,000$150,000100200300T ons of Cap acity p er Day$975,000$650,000$325,0002,5005,0007,500Tons MinedT o t a l V a r i a b l e C o s t sThe concept of relevant range is potentially relevant for both graphs. However, the question does not place restrictions on the unit variable costs. The relevant range for the total fixed costs is from 0 to 100 tons; 101 to 200 tons; 201 to 300 tons, and so on. Within these ranges, the total fixed costs do not change in total. 3.Tons Mined per Day Tons Mined per Month Fixed Unit Cost per Ton Variable Unit Cost per Ton Total Unit Cost per Ton(1) (2) = (1) × 25 (3) = FC ÷ (2) (4) (5) = (3) + (4) (a) 180 4,500 $300,000 ÷ 4,500= $66.67$130 $196.67 (b) 220 5,500 $450,000 ÷ 5,500=$81.82$130 $211.82 The unit cost for 220 tons mined per day is $211.82, while for 180 tons it is only $196.67. This difference is caused by the fixed cost increment from 101 to 200 tons being spread over an increment of 80 tons, while the fixed cost increment from 201 to 300 tons is spread over an increment of only 20 tons.2-23 (15-20 min.) Classification of costs, service sector.Cost object: Each individual focus groupCost variability: With respect to changes in the number of focus groupsThere may be some debate over classifications of individual items. Debate is more likely as regards cost variability.aSome students will note that phone call costs are variable when each call has a separate charge. It may be a fixed cost if Consumer Focus has a flat monthly charge for a line, irrespective of the amount of usage.bGasoline costs are likely to vary with the number of focus groups. However, vehicles likely serve multiple purposes, and detailed records may be required to examine how costs vary with changes in one of the many purposes served.2-24 (15-20 min.) Classification of costs, merchandising sector.Cost object: Video section of storeCost variability: With respect to changes in the number of videos soldThere may be some debate over classifications of individual items. Debate is more likely2-25 (15-20 min.) Classification of costs, manufacturing sector.Cost object: Type of car assembled (Corolla or Geo Prism)Cost variability: With respect to changes in the number of cars assembledThere may be some debate over classifications of individual items. Debate is more likely as regards cost variability.2-26(20-30 min.)Inventoriable costs vs. period costs.1.Manufacturing-sector companies purchase materials and components and convert them into different finished goods.Merchandising-sector companies purchase and then sell tangible products without changing their basic form.Service-sector companies provide services or intangible products to their customers—for example, legal advice or audits.Only manufacturing and merchandising companies have inventories of goods for sale.2.Inventoriable costs are all costs of a product that are regarded as an asset when they are incurred and then become cost of goods sold when the product is sold. These costs for a manufacturing company are included in work-in-process and finished goods inventory (they are "inventoried") to build up the costs of creating these assets.Period costs are all costs in the income statement other than cost of goods sold. These costs are treated as expenses of the period in which they are incurred because they are presumed not to benefit future periods (or because there is not sufficient evidence to conclude that such benefit exists). Expensing these costs immediately best matches expenses to revenues.3.(a) Mineral water purchased for resale by Safeway—inventoriable cost of a merchandising company. It becomes part of cost of goods sold when the mineral water is sold.(b)Electricity used at GE assembly plant—inventoriable cost of a manufacturing company. It is part of the manufacturing overhead that is included in the manufacturing cost of a refrigerator finished good.(c)Depreciation on Excite's computer equipment—period cost of a service company. Excite has no inventory of goods for sale and, hence, no inventoriable cost.(d)Electricity for Safeway's store aisles—period cost of a merchandising company. It is a cost that benefits the current period and is not traceable to goods purchased for resale.(e)Depreciation on GE's assembly testing equipment—inventoriable cost of a manufacturing company. It is part of the manufacturing overhead that is included in the manufacturing cost of a refrigerator finished good.(f)Salaries of Safeway's marketing personnel—period cost of a merchandising company. It is a cost that is not traceable to goods purchased for resale. It is presumed not to benefit future periods (or at least not to have sufficiently reliable evidence to estimate such future benefits).(g)Water consumed by Excite's engineers—period cost of a service company. Excite has no inventory of goods for sale and ,hence, no inventoriable cost.(h)Salaries of Excite's marketing personnel—period cost of a service company. Excite has no inventory of goods for sale and, hence, no inventoriable cost.2-27 (20-25 min.) Computing cost of goods manufactured and cost ofgoods sold.Schedule of Cost of Goods Manufacturedfor the Year Ended December 31, 2001(in thousands)Direct materials used $ 87,000 Direct manufacturing labor costs 34,000 Indirect manufacturing costs:Property tax on plant building $ 3,000Plant utilities 17,000Depreciation of plant building 9,000Depreciation of plant equipment 11,000Plant repairs and maintenance 16,000Indirect manufacturing labor costs 23,000Indirect materials used 11,000Miscellaneous plant overhead 4,000 94,000 Manufacturing costs incurred during 2001 215,000 Add beginning work-in-process inventory, Jan. 1, 2001 20,000 Total manufacturing costs to account for 235,000 Deduct ending work-in-process inventory, Dec. 31, 2001 26,000 Cost of goods manufactured $209,000Schedule of Cost of Goods Soldfor the Year Ended December 31, 2001(in thousands)Beginning finished goods, Jan. 1, 2001 $ 27,000Cost of goods manufactured (above) 209,000Cost of goods available for sale 236,000Ending finished goods, Dec. 31, 2001 34,000Cost of goods sold $202,0002-28 (30-40 min.) Cost of goods manufactured.Canesco CompanySchedule of Cost of Goods Manufactured for the Year Ended December 31, 2001(in thousands)1.Direct materials costs:Beginning inventory, Jan. 1, 2001 $22,000Purchases of direct materials 75,000Cost of direct materials available for use 97,000Ending inventory, Dec. 31, 2001 26,000Direct materials used $ 71,000 Direct manufacturing labor costs 25,000 Indirect manufacturing costs:Indirect manufacturing labor costs 15,000Plant insurance 9,000Depreciation––plant building and equipment 11,000Repairs and maintenance––plant 4,000 39,000 Manufacturing costs incurred during 2001 135,000 Add beginning work-in-process inventory, Jan. 1, 2001 21,000 Total manufacturing costs to account for 156,000 Deduct ending work-in-process inventory, Dec. 31, 2001 20,000 Cost of goods manufactured $136,000 2.Canesco CompanyIncome Statement for the Year Ended December 31, 2001(in thousands)Revenues $300,000 Cost of goods sold:Beginning finished goods, Jan. 1, 2001 $ 18,000Cost of goods manufactured (requirement 1) 136,000Cost of goods available for sale 154,000Ending finished goods, Dec. 31, 2001 23,000 131,000 Gross margin 169,000 Operating costs:Marketing, distribution, and customer service 93,000General and administrative 29,000 122,000 Operating income $ 47,0002-29 (25-30 min.) Income statement and schedule of cost of goodsmanufactured.Howell CorporationIncome Statement for the Year Ended December 31, 2001(in millions)Revenues $950 Cost of goods sold:Beginning finished goods, Jan. 1, 2001 $ 70Cost of goods manufactured (below) 645Cost of goods available for sale 715Ending finished goods, Dec. 31, 2001 55 660 Gross margin 290 Marketing, distribution, and customer-service costs 240 Operating income $ 50Howell CorporationSchedule of Cost of Goods Manufacturedfor the Year Ended December 31, 2001(in millions)Direct materials costs:Beginning inventory, Jan. 1, 2001 $ 15Purchases of direct materials 325Cost of direct materials available for use 340Ending inventory, Dec. 31, 2001 20Direct materials used $320 Direct manufacturing labor costs 100 Indirect manufacturing costs:Indirect manufacturing labor 60Plant supplies used 10Plant utilities 30Depreciation––plant, building, and equipment 80Plant supervisory salaries 5Miscellaneous plant overhead 35 220 Manufacturing costs incurred during 2001 640 Add beginning work-in-process inventory, Jan. 1, 2001 10 Total manufacturing costs to account for 650 Deduct ending work-in-process, Dec. 31, 2001 5 Cost of goods manufactured $6452-30(15-20 min.) Interpretation of statements.1. The schedule in 2-29 can become a Schedule of Cost of Goods Manufactured and Sold simply by including the beginning and ending finished goods inventory figures in the supporting schedule, rather than directly in the body of the income statement. Note that the term cost of goods manufactured refers to the cost of goods brought to completion (finished) during the accounting period, whether they were started before or during the current accounting period. Some of the manufacturing costs incurred are held back as costs of the ending work-in-process; similarly, the costs of the beginning work-in-process inventory become a part of the cost of goods manufactured for 2001.2. The sales manager’s salary would b e charged as a marketing cost as incurred by both manufacturing and merchandising companies. It is basically an operating cost that appears below the gross margin line on an income statement. In contrast, an assembler’s wages would be assigned to the products worked on. Thus, the wages cost would be charged to Work-in-process and would not be expensed until the product is transferred through Finished Goods Inventory to Cost of Goods Sold as the product is sold.3. The direct-indirect distinction can be resolved only with respect to a particular cost object. For example, in defense contracting, the cost object may be defined as a contract. Then, a plant supervisor’s salary may be charged directly and wholly to that single contract.4. Direct materials used = $320,000,000 ÷ 1,000,000 units = $320 per unitDepreciation = $ 80,000,000 ÷ 1,000,000 units = $ 80 per unit5. Direct materials unit cost would be unchanged at $320. Depreciation unit cost would be $80,000,000 ÷1,200,000 = $66.67 per unit. Total direct materials costs would rise by 20% to $384,000,000, whereas total depreciation would be unaffected at $80,000,000.6. Unit costs are averages, and they must be interpreted with caution. The $320 direct materials unit cost is valid for predicting total costs because direct materials is a variable cost; total direct materials costs indeed change as output levels change. However, fixed costs like depreciation must be interpreted quite differently from variable costs. A common error in cost analysis is to regard all unit costs as one-as if all the total costs to which they are related are variable costs. Changes in output levels (the denominator) will affect total variable costs, but not total fixed costs. Graphs of the two costs may clarify this point; it is safer to think in terms of total costs rather than in terms of unit costs.2-31 (25-30 min.) Income statement and schedule of cost of goodsmanufactured.Chan CorporationIncome Statementfor the Year Ended December 31, 2001(in millions)Revenues $350 Cost of goods sold:Beginning finished goods, Jan. 1, 2001 $ 40Cost of goods manufactured (below) 204Cost of goods available for sale 244Ending finished goods, Dec. 31, 2001 12 232 Gross margin 118 Marketing, distribution, and customer-service costs 90 Operating income $ 28Chan CorporationSchedule of Cost of Goods Manufacturedfor the Year Ended December 31, 2001(in millions)Direct material costs:Beginning inventory, Jan. 1, 2001 $ 30Direct materials purchased 80Cost of direct materials available for use 110Ending inventory, Dec. 31, 2001 5Direct materials used $105 Direct manufacturing labor costs 40 Indirect manufacturing costs:Plant supplies used 6Property taxes on plant 1Plant utilities 5Indirect manufacturing labor costs 20Depreciation––plant, building, and equipment 9Miscellaneous manufacturing overhead costs 10 51 Manufacturing costs incurred during 2001 196 Add beginning work-in-process inventory, Jan. 1, 2001 10 Total manufacturing costs to account for 206 Deduct ending work-in-process inventory, Dec. 31, 2001 2 Cost of goods manufactured (to income statement) $2042-32 (15-20 min.) Interpretation of statements.1. The schedule in 2-31 can become a Schedule of Cost of Goods Manufactured and Sold simply by including the beginning and ending finished goods inventory figures in the supporting schedule, rather than directly in the body of the income statement. Note that the term cost of goods manufactured refers to the cost of goods brought to completion (finished) during the accounting period, whether they were started before or during the current accounting period. Some of the manufacturing costs incurred are held back as costs of the ending work-in-process; similarly, the costs of the beginning work-in-process inventory become a part of the cost of goods manufactured for 2001.2. The sales manager’s salary would be charged as a marketing cost as incurred by both manufacturing and merchandising companies. It is basically an operating cost that appears below the gross margin line on an income statement. In contrast, an assembler’s wages would be assigned to the products worked on. Thus, the wages cost would be charged to Work-in-process and would not be expensed until the product is transferred through Finished Goods Inventory to Cost of Goods Sold as the product is sold.3. The direct-indirect distinction can be resolved only with respect to a particular cost object. For example, in defense contracting, the cost object may be defined as a contract. Then, a plant supervisor’s salary may be charged directly and wholly to that single contract.4. Direct materials used = $105,000,000 ÷ 1,000,000 units = $105 per unitDepreciation = $ 9,000,000 ÷ 1,000,000 units = $ 9 per unit5. Direct materials unit cost would be unchanged at $105. Depreciation unit cost would be $9,000,000 ÷1,500,000 = $6 per unit. Total direct materials costs would rise by 50% to $157,500,000 ($105 1,500,000). Total depreciation cost of $9,000,000 would remain unchanged.6. Unit costs are averages, and they must be interpreted with caution. The $105 direct materials unit cost is valid for predicting total costs because direct materials is a variable cost; total direct materials costs indeed change as output levels change. However, fixed costs like depreciation must be interpreted quite differently from variable costs. A common error in cost analysis is to regard all unit costs as one-as if all the total costs to which they are related are variable costs. Changes in output levels (the denominator) will affect total variable costs, but not total fixed costs. Graphs of the two costs may clarify this point; it is safer to think in terms of total costs rather than in terms of unit costs.。
成本管理会计第四章习题参考答案

成本管理会计第四章参考答案习题一⑴制造费用分配率=4480 / (200×5+100×4 )=3.2甲产品应分配的制造费用=1000×3.2 =3200 元乙产品应分配的制造费用=400×3.2 =1280 元⑵预定分配率=62100 / (1800×5+1200×4)=4.5甲产品应分配的制造费用=200×5×4.5 =4500 元乙产品应分配的制造费用=100×4×4.5 =1800 元习题二⑴各分配表直接人工费用分配表直接人工分配率=18700/3400=5.50制造费用分配表制造费用分配率=20400/3400=6⑵产品成本计算单产品批号:#101 开工日期:09年1月产品名称:A产品产量:20台完工日期:09年3月单位:元#101A 本月完工产品成本=62 400(元)整批完工产品实际总成本=62400+40860=103 260(元)单位成本=103260/20=5 163(元)产品成本计算单产品批号:#201 开工日期:09年2月产品名称:B产品产量:30台完工日期:09年3月单位:元#201B 本月完工产品成本=45550(元)产品成本计算单产品批号:#301 开工日期:09年3月产品名称:B产品产量:45台完工日期:09年月单位:元(3)借:库存商品——A产品62400——B 产品45550贷:基本生产成本——A 产品62400——B 产品45550习题三基本生产成本二级账直接人工累计分配率=61650/13700=4.5元/小时制造费用累计分配率=76720/13700=5.6元/小时本月完工产品成本转出(直接材料)=23000+11550=34550元本月完工产品成本转出(工时)=2800+6800=9600小时本月完工产品成本转出(直接人工)=12600+30600=43200元本月完工产品成本转出(制造费用)=15680+38080=53760元产品成本计算单开工日期:09年7月21日产品批号:#701 完工日期: 09年8月15日产品名称: 甲产品产量:12件单位:元产品成本计算单开工日期: 09年7月28日产品批号:#702 完工日期: 09年8月30日产品名称: 乙产品产量:8件(本月完工3件) 单位:元本月完工产品成本转出(直接材料)=(30800/8)×3=11550元本月完工产品成本转出(直接人工)=6800×4.5=30600元本月完工产品成本转出(制造费用)=6800×5.6=38080元产品成本计算单开工日期: 09年8月15日产品批号:#703 完工日期:产品名称:丙产品产量:6件单位:元。
4《成本会计》(第四章)
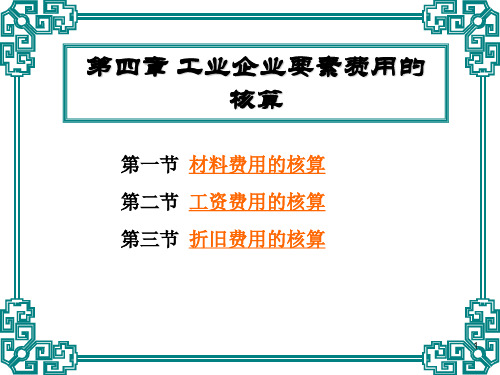
(1)发出出租出、借包装物: 借:待摊费用 18000 销售费用 1500 贷:包装物 19500 (2) 出借包装物报废,残料入库: 借:原材料 380 贷:销售费用 380 (3)结转发出包装物的成本差异 借:待摊费用 360 销售费用 30 贷:材料成本差异——包装物成本差异 390 (4)摊销本月应负担的出租包装物价值 借:其他业务成本 2940 贷:待摊费用 2940
借:低值易耗品——低值易耗品摊销 700 贷;低值易耗品——在用低值易耗品 700 (领用时也摊销了350,所以共摊销了700) (3)月末结转本月所领管理用具的成本差异时: 借:管理费用 48 贷:材料成本差异——低值易耗品成本差异 (本月领用1600,再乘以0.03)
48
30
优点:提高了费用负担的合理性,有利于进行
22
对出借包装物进行修理,发生修理费用时: 借:销售费用 贷:银行存款等 出借库存已用包装物时: 借:包装物——出借包装物 贷:包装物——库存已用包装物 出借包装物报废,摊销其一半价值时: 借:销售费用 贷:包装物——包装物摊销
23
报废包装物的残料入库时:
借:原材料等 贷:销售费用
注销报废的出借包装物及其摊销额时:
(1)领用管理用具时:
借:低值易耗品——在用低值易耗品 1 600 贷:低值易耗品——在库低值易耗品 1 600 借:管理费用 800 贷:低值易耗品——低值易耗品摊销 800
29
(2)报废管理用具时: 借:原材料 50 贷:管理费用 50 借:管理费用 350 贷:低值易耗品——低值易耗品摊销
350
返回
33
净值摊销法实例:
34
35
36
37
净值摊销法总结:
成本会计第四章练习题答案
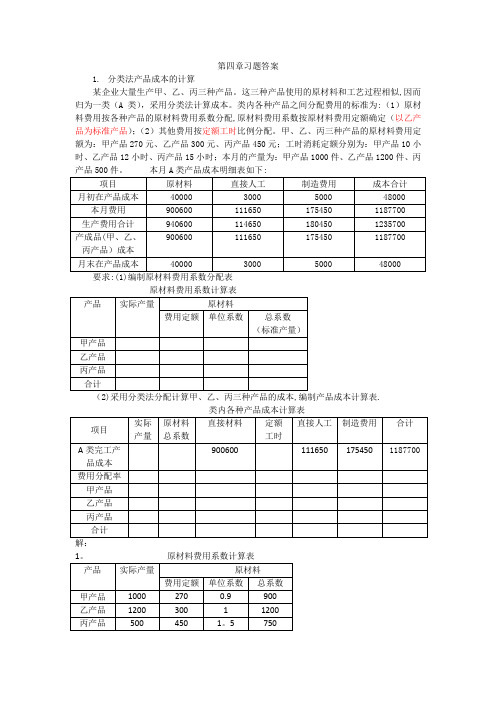
第四章习题答案1.分类法产品成本的计算某企业大量生产甲、乙、丙三种产品。
这三种产品使用的原材料和工艺过程相似,因而归为一类(A类),采用分类法计算成本。
类内各种产品之间分配费用的标准为:(1)原材料费用按各种产品的原材料费用系数分配,原材料费用系数按原材料费用定额确定(以乙产品为标准产品);(2)其他费用按定额工时比例分配。
甲、乙、丙三种产品的原材料费用定额为:甲产品270元、乙产品300元、丙产品450元;工时消耗定额分别为:甲产品10小时、乙产品12小时、丙产品15小时;本月的产量为:甲产品1000件、乙产品1200件、丙产品500件。
本月A类产品成本明细表如下:要求:(1)编制原材料费用系数分配表(2)采用分类法分配计算甲、乙、丙三种产品的成本,编制产品成本计算表.类内各种产品成本计算表原材料分配率=900600÷2850=316人工费分配率=111650÷31900=3.5制造费用分配率=175450÷31900=5。
52。
变动成本法的成本计算某厂生产甲产品,产品单价为10元/件,单位产品变动生产成本为4元,固定性制造费用总额为24000元,销售及管理费用为6000元,全部是固定性的。
存货按先进先出法计价,要求:(1)分别按变动成本法和完全成本法计算单位产品成本;(2)分别按变动成本法和完全成本法计算三年的营业利润。
第一年营业利润=6000×(10—4)—(6000+24000)=6000(元)第二年=6000×(10—4)-(6000+24000)=6000(元)第三年=6000×(10-4)-(6000+24000)=6000(元)完全成本法:营业利润=(收入—销售成本)—期间成本=毛利-期间成本第一年营业利润=6000×(10-8)-6000 =6000(元)第二年.。
.。
.。
..。
..。
=6000×(10—7)—6000=12000(元)第三年=6000×10—(2000×7+4000×10)-6000=0产销不等时,两种方法营业利润的差异=期初存货固定制造费用—期末存货固定制造费用3.解:月末在产品定额原材料费用=(2000-20)+24000-23000=2980(元)原材料脱离定额差异分配率=-(50+500)÷(23000+2980)=—0.02117完工产品负担的差异额=—0。
成本会计学 第四章习题答案(2012)

第四章习题答案一、填空题1、直接分配法顺序分配法一次交互分配法计划成本分配法代数分配法2、车间产品品种、劳务3、受益少的辅助生产车间受益多的辅助生产车间4、辅助生产车间直接发生费用第一步交互分配来的费用之和5、直接分配法二、单项选择题CACFE三、多选题1、ABCDE2、ACDE3、BC4、BC5、ABC四、判断题1、3、4对,其它错七、计算题辅助生产费用分配表(直接分配法)会计分录:借:基本生产成本10176.6制造费用——基本生产车间 21613.8管理费用8809.6贷:辅助生产成本——供电车间 12600——机修车间 28000辅助生产费用分配表(顺序分配法)分析:辅助生产车间先排序:机修车间排前,供电车间排后机修车间费用分配率=28000/2800=10供电车间费用分配率=(12600+3000)/(30000-4000)=0.6会计分录:借:辅助生产成本——供电车间3000基本生产成本12600制造费用——基本生产车间 19800管理费用82006贷:辅助生产成本——供电车间 15600——机修车间 28000辅助生产费用分配表(一次交互分配法)对外分配实际费用 供电: 12600+3000-1680=13920(元) 机修: 28000+1680-3000=26680(元)交互分配借:辅助生产成本——供电车间 3000——机修车间 1680 贷:辅助生产成本——机修车间 3000 ——供电车间 1680 对外分配借:基本生产成本 11243.4制造费用 ——基本生产车间 20815.8 管理费用 8540.8 贷:辅助生产成本——供电车间 13920 ——机修车间26680辅助生产费用分配表(计划成本分配法)供电车间实际成本=12600+2940=15540 成本差异:15540-15000=540 机修车间实际成本=28000+2000=30000 成本差异:30000-27440=2560借:辅助生产成本——机修车间2000辅助生产成本——供电车间2940基本生产成本10500制造费用——基本生产车间19140管理费用7860贷:辅助生产成本——机修车间27440——供电车间15000借:管理费用3100贷:辅助生产成本——机修车间2560——供电车间540辅助生产费用分配表(代数分配法)设每度电的成本为X元,每一机修小时的成本为Y元12600+300Y=30000X28000+4000X=2800Y解方程组,求得X=0.5275 Y=10.7536借:辅助生产成本——机修车间2110——供电车间3226.08基本生产成本11078制造费用——基本生产车间20939.48管理费用8582.52贷:辅助生产成本——机修车间30110.08——供电车间15826。
成本会计第四章习题答案.doc

成本会计第四章练习题答案习题一、练习约当产量法分配完工产品和在产品成本某企业生产A产品,木月完工产品数量为500件,期限末在产品数量为400件,原材料是随加工进度陆续投入,原材料的投入程度与加工进度完全一致。
期末在产品的完工率为50%。
有关费用资料如表所示。
要求:采用约当产量比例法将费用在完工产品和在产品之间分配,并将分配结果填入表中。
在产品约当量=400 X 50%=200直接材料费用分配率=539004- (500+200) =77直接燃料及动力费用分配率=12044- (500+200) =1.72直接人工分配率=1964- (500+20()) =0.28制造费用分配率=35004- (500+200) =5借:库存商品---A 42000贷:基本生产成本一A 42000习题二、练习定额比例法分配完工产品和在产品成本企业生产A产品,月初在产品成木原材料定额费用为12500元,工时定额为50000小时,月初在产品的实际费用为:原材料13100元,燃料及动力为4100元,工资及福利费为3890 元,制造费用为11290元。
本月原材料定额费用为:25200元,定额工时为70000小时。
本月实际费用为:原材料23469元,燃料及动力为61900元,工资及福利费为4891。
元,制造费用6671()元。
本月完工产品原材料定额费用为13000元,定额工时为800()0小时。
要求:根据上述资料采用定额比例法计算完工产品成木和在产品成木,并将计算结果填入表中。
材料费用分配率=(13100+23469) / (12500+25200) =0.97直接燃料动力费用分配率=(4100+61900) / (50000+70000) =0.55直接人工费用分配率=(3890+48910) / (50000+70000) =0.44制造费用分配率=(11290+66710) / (50000+70000) =0.65注:(1)完工产品实际成本二某项费用分配率X完工产品定额费用或工时(2)月末在产品定额成本或工时=月初在产品定额费用或工时+本月定额费用或工时一完工产品定额费用或工时(3)月末在产品实际成本=某项费用分配率X月末在产品定额费用或工时或=月初在产品实际成本+本月实际费用一完工产品实际成本借:库存商品・・・A 143810贷:基本生产成本----A 143810习题三、练习约当产量法分配完工产品和在产品成本某企业生产A产品,月初在产品数量为18件,本月投产12件,本月完工20件。
成本会计第四章(2)
【例题8· 多选题】采用定额比例法分配完工产品和 月末在产品费用,应具备的条件有( A.各月末在产品数量变化较大 B.各月末在产品数量变化不大 C.消耗定额或成本定额比较稳定 D.消耗定额或成本定额波动较大
【答案】AC 【解析】定额比例法适用于各项消耗 定额或成本定额比较准确、稳定,但各月末在产 品数量变动较大的产品。
3.费用的分配 采用约当产量法需按成本项目分别计算费用分 配率。 分配率(单位成本)= 待分配成本项目/(完工 产量+月末在产品约当产量) 完工产品成本=分配率×完工产量 月末在产品成本=分配率×月末在产品约当产量 例题P58-59,4-10,4-11,4-12
综合题. E产品经过三道工序制成,原材料分工序陆续 投入,月初在产品成本19 000,本月生产费用98000元, 完工产品2000件。
在产品完工程度计算结果如下: 第一道工序:240×50%÷600=20% 第二道工序:(240+360×50%)÷600=70% 月末在产品的约当产量=100×20%+50×70%=20+35=55(件)。
【例题】某企业A产品经过两道工序加工完成。A产品耗 用的原材料在开始生产时一次投入。生产成本在完工 产成品和在产品之间分配采用约当产量比例法。2014 年9月与A产品有关的资料如下: 本月完工产成品1 300件。月末在产品数量及完工程度为: 第一道工序500件,第二道工序200件。 A产品单位工时定额500小时,经两道工序制成。各工序 单位工时定额为:第一道工序200小时,第二道工序 300小时。为简化核算,假定各工序内在产品完工程度 平均为50%。 要求:计算直接材料、直接人工、制造费用的在产品约 当产量;直接人工和制造费用按工时比例分配。
2.材料费用分配 (1)以材料定额消耗量为标准分配材料费用 直接材料成本分配率=(月初在产品实际材料消耗量+本 月投入的实际材料消耗量)/(完工产品材料定额消耗 量+月末在产品材料定额消耗量) 完工产品应负担的直接材料成本=完工产品材料定额消耗 量×直接材料成本分配率 月末在产品应负担的直接材料成本=月末在产品材料定额 消耗量×直接材料成本分配率
成本会计第四章习题参考答案
《成本会计学》,主编:周佩,第四章习题参考答案单项选择题:1-BABAA BCCDB 11-ADCDD DDBCC 21-CBADC CBCAC 31-BACCB CBACC 41-ABDCB BA多项选择题:1-ABCD ACD BC BC AC AB ABCD AC ABCD ABD11-ABCD ABD CD ABC AC ABD ABCD ABCD BCE ABC21-ABD AB AC ABCD CD AC AC CD ABC ABC31-ABC AD ABCD AD ABCD判断题√×√√√√××××计算分析题第一题(1)材料费用分配甲乙产品分配C材料:分配率=16000/10000=(元/公斤)甲产品负担的材料费=20000+6000×=29600乙产品负担的材料费=28000+4000×=34400制造费用=2000(2)人工费用分配甲乙产品分配工资费用:分配率=24000/800=30(元/小时)甲产品负担的工资费用=300×30=9000乙产品负担的工资费用=24000-9000=15000制造费用=4600(3)计提固定资产折旧制造费用=600000×2%=12000(4)辅助生产车间(供电车间)费用的分配电费分配率=9600/1200=8(元/度)甲产品负担的电费=300×8=2400乙产品负担的电费=400×8=3200制造费用=100×8=800管理费用=400×8=3200(5)分配制造费用制造费用(借方数额)=2000+4600+12000+800=19400分配率=19400/800=甲产品负担的制造费用=300*=7275乙产品负担的制造费用=19400-7275=12125借:基本生产成本——甲产品基本生产成本——乙产品贷:制造费用(6)计算甲、乙产品成本①完成141页的表——甲产品成本计算表材料费用分配率=48400/(160+40)=242工资费用分配率=19386/(160+40×50%)=动力费用分配率=3814/(160+40×50%)=制造费用分配率=18125/(160+40×50%)=④甲、乙产品完工入库的会计分录借:库存商品——甲产品库存商品——乙产品贷:基本生产成本——甲产品基本生产成本——乙产品第二题9414批甲产品(1)原材料的分配:完工产品=3360/10*6=2016元在产品=3360/10*4=1344元工资及制造费用按约当产量进行分配4*50%=2台(2)工资的分配:完工产品=2350*6/(2+6)=元在产品=2350*2/(6+2)=元(3)制造费用的分配:完工产品=2800*6/(2+6)=2100元在产品=2800*2/(6+2)=700元甲产品本月完工产品成本=2016++2100=元甲产品本月在产品成本=1344++700=元借:库存商品--甲产品贷:生产成本--甲产品9415批乙产品完工产品按计划成本计算原材料460*2=920工资350*2=700制造费用240*2=480成本合计2100元借:库存商品--乙产品2100贷:生产成本--乙产品2100在产品成本原材料4600-920=3680工资3050-700=2350制造费用1980-480=1500成本合计7530元第三题表9-1月日摘要原材料工时直接人工费制造费用合计9 30 生产费用累计数 68880 47040 18816 28224 1159209 30 累计间接费用分配率9 30 完工产品成本 32400 23020 9208 13812 554209 30 余额 36480 24020 9608 14412 60500二级账中数字计算过程:直接人工费累计分配率=18816÷47040=完工产品原材料费用=18000+14400=32400(元)完工产品工时=9020+14000=23020(小时)完工产品直接人工费=23020×=9208(元)完工产品制造费用=23040×=13812(元)(2)产品成本明细账①甲产品成本明细账,如表9-2所示。
新编成本会计课后习题答案
100
625.89
2 516.11
合计
24 000
22 671.42 4 000
25 028.58 47 700
(四)练习辅助生产费用的核算 2.交互分配法
借:生产成本——辅助生产成本(供电车间) 1 071.42
——辅助生产成本(机修车间) 3 600
贷:生产成本——辅助生产成本(供电车间)
3 600
借:管理费用
6 500
贷:生产成本——辅助生产成本(供电车间)
——辅助生产成本(机修车间)
3 900 2 600
(四)练习辅助生产费用的核算 2.代数分配法
建立二元一次方程组: 设每度电的单位成本为X元,每小时机修费
用的单位成本为Y元,则方程组为: 28 000X=25 200+200Y 4 200Y=22 500+4 000X 解得: X=0.9447
(2)
借:生产成本——辅助生产成本 56 000
贷:原材料
51 200
应付职工薪酬
4 800
借:制造费用
16 360
贷:原材料
3 420
应付职工薪酬
2 100
累计折旧
3 340
银行存款
7 500
借:生产成本——辅助生产成本 16 360
贷:制造费用
16 360
借:生产成本——基本生产成本 52 830
合计
数量
金额
数量
金额
数量
金额
数量
金额
待分配费用
25 200
22 500
22 671.42
25 028.58
劳务供应量
28 000
4 200
24 000
成本会计第四章习题参考答案
60275
分配率
完工产品
200
34600
11632
27产品
0
0
0
0
0
0
完工单位成本
173
②完成142页的表——乙产品成本计算表
项目
产量
直接材料
直接工资
燃料及动力
制造费用
合计
月初在产品
14000
4386
614
6000
25000
本月生产投入
34400
15000
3200
库存商品乙产品
贷:基本生产成本一一甲产品
基本生产成本乙产品
第二题
9414批甲产品
(1)原材料的分配:完工产品=3360/10*6=2016元
在产品=3360/10*4=1344元
工资及制造费用按约当产量进行分配4*50%=2台
(2)工资的分配:完工产品=2350*6/(2+6)=元
在产品=2350*2/(6+2)=元
12125
64725
合计
48400
19386
3814
18125
89725
分配率
242
完工产品
160
38720
17232
月末在产品
40
9680
2154
完工单位成本
242
材料费用分配率=48400/(160+40)=242
工资费用分配率=19386/(160+40X50% =动力费用分配率=3814/(160+40X50% =
乙产品负担的材料费=28000+4000X=34400制造费用=2000
- 1、下载文档前请自行甄别文档内容的完整性,平台不提供额外的编辑、内容补充、找答案等附加服务。
- 2、"仅部分预览"的文档,不可在线预览部分如存在完整性等问题,可反馈申请退款(可完整预览的文档不适用该条件!)。
- 3、如文档侵犯您的权益,请联系客服反馈,我们会尽快为您处理(人工客服工作时间:9:00-18:30)。
第四章生产费用核算
习题一、
定额耗用量比例
辅助生产费用分配表
(1)交互分配
借:辅助生产——供水车间1200借:辅助生产——蒸汽车间240
借:辅助生产——机修车间240贷:辅助生产——发电车间1680借:辅助生产——发电车间1600借:辅助生产——蒸汽车间11200贷:辅助生产——供水车间12800借:辅助生产——发电车间18900贷:辅助生产——蒸汽车间18900
借:辅助生产——发电车间1300借:辅助生产——供水车间1300借:辅助生产——蒸汽车间2600贷:辅助生产——机修车间5200对外分配:
借:生产成本28840制造费用2060
辅助生产成本——发电车间
辅助生产成本——供水车间
管理费用 420 贷:辅助生产——发电车间 31320
借:制造费用 4650 管理费用 1550 贷:辅助生产——供水车间
6200
借:制造费用 16140
贷:辅助生产——蒸汽车间
16140
借:制造费用 8040
贷:辅助生产——机修车间
8040 2,计划成本分配法
制造费用 2600 管理费用 520
辅助生产——供水车间 5200 辅助生产——蒸汽车间 1040 辅助生产——机修车间 1040 贷:辅助生产——发电车间
46800
借:管理费用 3900
贷:辅助生产——发电车间 3900
3200
借:制造费用3000
管理费用1000
辅助生产——发电车间2000
辅助生产——蒸汽车间14000
贷:辅助生产——供水车间20000
借:生产成本2400
借:管理费用800
贷:辅助生产——供水车间3200
辅助生产——发电车间36000
贷:辅助生产——蒸汽车间40000
借:辅助生产——蒸汽车间9600
贷:管理费用9600
辅助生产——发电车间1500
辅助生产——供水车间1500
辅助生产——蒸汽车间3000
贷:辅助生产——机修车间15000
借:辅助生产——机修车间960
贷:管理费用960
借:生产成本8680
制造费用51946
管理费用1074
贷:辅助生产——发电车间11200
辅助生产——供水车间16500
辅助生产——蒸汽车间21000
辅助生产——机修车间13000习题三、
在产品约当产量计算:
生产成本明细帐
1,月末在产品的原材料按定额原材料费用计算,其他各项费用都按约当产量计算。
零件101号在产品约当产量计算:
零件102号在产品约当产量计算:
摘要直接材料直接工资制造费用合计
2,原材料费用按定额原材料费用比例分配计算,其他各项费用按定额工时比例计算。
产成品定额原材料费用:270×123=33210
在产品定额原材料费用:(150+100+200)×57+(400+250)×66=68550
直接材料分配率:91998/(33210+68550)=0.9
产成品应分配直接材料费:33210×0.9=29889
在产品应分配直接材料费:91998-29889=62109
产成品定额工时:270×10=2700
在产品定额工时:(150×2+100×4+200×5)+(400×1+250×5)=3350
直接工资分配率:34225/(2700+3350)=5.66
产成品应分配直接工资:2700×5.66=15282
在产品应分配直接工资:34225-15282=18943
制造费用分配率:66500/(2700+3350)=10.99
产成品应分配制造费用:2700×10.99=29673
在产品应分配制造费用:66500-29673=36827
生产成本明细帐
3
在产品定额原材料费用:
(150+100+200)×57+(400+250)×66=68550
在产品定额工资费用:
[(150×2+100×4+200×5)+(400×1+250×5)]×4.75=15913在产品定额制造费用:
[(150×2+100×4+200×5)+(400×1+250×5)]×13.2=44220
生产成本明细帐。