酸轧联合机组机架控制
冷连轧机动态变规格机架速度控制策略及规律

的波动量为 $T , 则对应的第 i 机架的出口速度 v fi
就应在稳定轧制速度的基础上进行调整, 来维持张
力 T 的恒定. 调整量 $v f i 为:
$v fi= -
v E
bi +
2 hi
1t1 , B b2
+
L - v bi+ 1 t1 E 1H i + 1, A b1
$T $t
.
根据带钢轧制的速度方程, 轧辊的线速度与出
机架 i 的前张力设定为变 规格前 A 材轧制的 设定值 T f i, A, 通过机架 i 的出口速度 v f i 保持其恒 定, 隔断变规格点对前规格轧制的影响. 机架 i 的 后张力设定为变规格后 B 材轧制的设定值 T bi , B, 通 过机架 i 上游机架速度 v fi - 1的控制, 隔断变规格点 对后规格轧制的影响, 即:
动态变规格是实现酸轧联合机组全连续轧制的 关键技术, 它克服了单 卷轧制穿带、抛钢作业 的弊 端, 明显提高了轧制过程的稳定性、带钢质量和轧机 的生产效率.
在冷连轧过程中, 由于机架间张力的媒介作用, 使得轧制过程的各种因素相互影响、相互作用. 这 些轧制因素包括机架入口板厚、出口板厚、机架间张 力、摩擦因数、辊缝、辊速、辊径、带钢的变形抗力等. 这些因素涉及到所有机架, 因此有几十个轧制因素 因为机架间张力的媒介相互耦合. 动态变规格过程 中, 各机架的轧制力、张力、速度、辊缝等轧制因素都 将发生变化, 使得过渡过程的求解非常复杂. 国内 外学者都对此开展了大量的工作, 主要集中在速度 协调和变规格机架的速度[ 1- 2] 和辊缝修正[ 3- 5] 、控制 算法[ 6- 7] 、张 力 变 化 规律[ 8- 9] 以 及 个 别 参 数 的 优 化[ 10- 11] 等方面. 但动态变规格时, 在很短的时间内 要完成厚度、宽度、品种等因素的变换, 反馈等控制 手段无法投入. 如果没有适当的控制策略, 几十个 因素的相互作用, 使过渡过程难于控制, 造成产品超 差, 严重时甚至断带停机. 因此研究冷连轧机变规 格机架速度控制规律具有重要意义.
1450mm酸连轧机组活套张力控制

1450mm酸连轧机组活套张力控制冷连轧活套张力控制的动静态精度对于稳定轧制过程至关重要。
在结合活套张力控制原理的基础上设计出1 450 mm 冷连轧机活套电气控制系统,详细介绍了活套张力控制系统的控制原理及实现方案,对惯性力矩、弯曲力矩和摩擦力矩进行补偿,随后分析活套的运行情况。
实践证明此活套控制系统具有较好的控制效果,满足生产工艺的要求。
标签:冷连轧机;活套;恒张力控制;S120交流传动装置1、概述在冷轧带钢控制系统中,为保证产品质量和工艺过程稳定,无论是冷连轧机还是可逆冷轧机均需要稳定的张力控制。
按照不同的工艺要求:较典型的张力控制方法有间接张力控制和直接张力控制,间接张力控制常用于开卷、卷取、活套的控制;直接张力控制则用于精度较高的张力控制系统,冷连轧生产中常用于机架间的张力控制。
文中所设计的1450mm 6辊5机架酸连轧机组已于2019年初正式投产,其活套控制系统采用间接张力控制。
在活套的控制系统中,活套不仅需在同步运行时保持张力恒定,且要求系统能准确地在加减速过程中进行动态力矩补偿,并根据活套车的位置对张力给定进行修正。
2、入口水平活套2.1设备组成入口活套为水平活套,活套系统由活套车、活套车驱动装置、活套门、底部带钢支承辊、换辊小车和钢绳缓冲装置组成。
活套车上设有带钢转向辊、滑轮组及带钢支承辊和车轮,活套车的一侧设有水平滚轮,通过偏心轮来调整滚轮的开口度。
活套车上带有滑槽用以控制活套门的关闭。
活套车车体为焊接钢结构框架。
活套车驱动装置由电机减速机驱动,并保证活套车时刻处于可控状态。
当活套车运动时,设在活套车上的滑槽引导与活套门关联的连杆机构开始转动并带动活套门开闭。
活套门用于支撑存储的带钢,安装在活套车行进方向的两边,通过连杆机构由活套车驱动来完成开闭摆动。
底部带钢支承辊用来支持底部存储带钢的运行。
2.2设备性能酸洗入口活套由3臺电机组成,电机参数如下:其交流传动采用西门子公司交流传动装置,型号为:S120系列。
首钢京唐酸轧机组厚度控制策略分析与应用

设 在 A C投 入 的初 始 状 态 时 , 式 ( G 如 3)
所示 .
P
』
由测厚仪检测点移至辊缝压上位置 , 并综合考虑 测厚仪的响应时间 以及压 上系统 的响应时间 , 实 现辊缝修正 点与测 厚仪 的监 测点 的一 致. F— F A C的最 终输 出 的辊缝 修 正量 如式 ( ) 示 . G 1所
Ke r s a d m od r l n y wo d :tn e c l ol g; g u e c n r l yt m ;f e o wa d c n r l i a g o t s o s e e d f r r o t ;masf w o t l o sl o c nr o
A F =A ・ M/ SF H ( K )=A ・ H ・ () 1
h = -S 0 t0 -
() 3
式 中 ,。 P 为初 始S N力 ; 。 L S 为初 始辊 缝 . 于 是 , 了使 出 口厚 度偏 差 为零 , 为 辊缝 .将 如 s
式 ( ) 行控 制 4进
P — P
A C( a g G G u eMee mi GC 一厚度计 一S t t S tA ) r h mi h补偿 AG C;MF MasFo ag ) 秒流 量厚 度计算 ;MF—F MasFo ed G( s lw G ue 一 F( s lw F e F rad 一秒流量前馈控制 ;MF—F ( s Fo edB c ) ow r ) B Mas l Fe ak 一秒流量反馈控制 w
程计 算 机. 轧 机具有 出色 的厚 度 调 控 能 力 , 线 设 有 5 全 组测 厚仪 , 分别 设 置在 l机架 前后 以及 5 机架 前 # #
收 稿 日期 :2 1-01 . 0 11 —8
酸轧机组过程控制系统

软件结构-酸洗轧机通讯
• L1部分通讯
– 通讯方式:DP网和硬连接。 – 通讯内容:轧件焊缝位置,停机信号等
2020/7/30
Copyபைடு நூலகம்ight© 2010 中冶南方(武汉)威仕软件公司
定值、生产计划、各种报表、HMI界面等) – 酸洗设定值计算 – 过程数据收集和处理 – 物料跟踪和焊缝跟踪(入口、处理段) – 全线速度优化 – 扰动管理和自动交接班 – 缺陷和质量数据收集
2020/7/30
软件功能
• 轧机部分
– 设定值计算 – 物料跟踪 – 过程数据收集 – 轧机设定值自学习和自适应 – 一般数据管理(PDI/PDO/工艺数据等) – 轧辊数据管理 – 轧机参数管理(压靠和弹性模量数据)
2020/7/30
软件结构-酸洗系统结构
2020/7/30
软件结构-轧机系统结构
2020/7/30
软件结构-酸洗轧机通讯
• L2部分通讯
– 通讯协议:RPC,利用通讯中间件实现进程间 通讯,数据库数据共享。
– 通讯内容:轧件主数据、带钢缺陷数据、轧机 段的实际入口速度、轧机的最高允许速度、焊 缝位置等。
酸轧联合机组计算机过程控制 系统
中冶南方工程技术有限公司 中冶南方武汉威仕软件公司
工程业绩
• 鞍钢二号酸轧机组 • 鞍钢硅钢酸轧机组 • 鞍钢三号酸轧机组 • 鞍钢四号酸轧机组 • 鞍钢莆田酸轧机组(2011年8月投产) • 本钢酸洗超薄机组 • 鞍钢1-4#硅钢连退 • 太钢5冷轧连退、重卷、常化酸洗机组 • 马钢连退和推拉式酸洗 • 通钢酸洗机组 • 通钢连退机组 • 邯郸脱脂机组 • 首钢顺义1、2号重卷机组 • 天铁中厚板 • 湘钢5米板加热炉 • 大冶步进梁式加热炉
钢铁冷轧厂酸轧机组的自动化控制方法

钢铁冷轧厂酸轧机组的自动化控制方法摘要:随着现代化的发展,工业生产已成为当今社会的核心力量,其中钢铁制造尤为突出,其制造技术不仅影响到产品的价格,还影响到其质量[1]。
随着各种高科技的发展,钢铁厂的酸轧设备正在逐步实现完全自动化,这不仅大大降低了人工操作的失误率,而且还显著提升了公司的经济效益。
为此,对钢铁厂酸轧机自动化控制方法进行了深入的探讨。
关键词:钢铁冷轧厂;酸轧机组;自动化控制;方法引言:随着科技的飞速发展,在冷轧酸轧机组中,大量的先进技术被广泛的运用,使其实现了自动化、智能化、智慧化的运行与控制,因此,酸轧机组的操作水平得到了大幅度的提升,提高了产品的精度与质量,给钢铁企业带来了更大的效益[2]。
所以,对冷轧厂酸轧机的自动控制方法的分析和研究就显得极其重要。
一、冷轧酸轧机组自动化系统的组成结构在自动化控制系统生产线上,安装了三个独立的操作室,包括轧机操作室、酸洗操作室和酸洗入口操作室,分别负责轧机段、酸洗段和酸洗入口段的主控操作。
此外,酸轧机组使用更高级的HMI人机交互系统,设置了一个计算机室和一个服务器室,计算机室配备三台一级工程师站,一台二级工程师站,一台三级工程师站,二、三级画面工程师站各一台。
服务器室配备了酸洗PDA和轧机PDA、一级画面服务器、二三级服务器和天车服务器。
一级控制系统包括8台西门子S7-400 PLC控制柜,9台西门子 TDC控制柜,2台UPS不间断电源供电柜,1台板型辊控制柜,2台测厚仪控制柜,1台边降仪控制柜。
一级系统是由现场仪表检测以及某些在现场的执行器,经过信号传输,最终到CPU大脑计算处理后再发出命令,现场设备根据指令做出相应动作。
在人机交互系统中,由一个人机交互服务器和70个人机交互客户端组成。
在S7的情况下,这些装置通过以太网络与 HMI以及服务器进行通讯,并具有较高的速度,并且每个服务器都是一用一备,在运行的服务器出现故障,能快速切换到备用服务器上,能实现无缝衔接,使系统更稳定。
41酸连轧机组操作规程

中冶恒通冷轧技术有限公司酸连轧机组操作规程ZY/MCC14-41-A发布时间:二OO七年十月一日酸连轧生产线操作规程一、开卷操作规程1、按生产计划认真核对钢卷钢种、板宽、板厚、卷重、卷号等参数,核对无误后方可上料。
2、钢卷内圈严重变形的,严重拆边或有其他不宜在酸洗机组上矫直等缺陷的料卷不得使用,待处理后方可上料。
3、天车将轧卷吊放在鞍座上(注意上卷料头方向)人工剪去捆带,上料小车从鞍座上取走钢卷,并经1#(或2#)冷金属检测器测宽后,在经卷径测量装置(1#或2#)测钢卷外径之后,送到开卷机卷筒的轧制线对中位置。
4、人工操作纵卷筒胀开.压辊压下小车下降并退回。
二、焊机操作规程1、首次焊接先检查空气压缩机的压力是否满足,冷却水的流量是否满足,冷却水的温度是否满足(大于35度不能焊接)。
2、启动液压泵,选定远程/就地开关,启动循环泵一分钟后高压泵指示按钮开始闪烁,允许高压泵启动。
3、选择手动模式移动可移动框架,入、出口夹钳、传动小车、对中单元以及修磨月牙剪等设备,仔细观察运转情况,如果发现问题应检查相应的电气和机械液压设备。
4、①选择半自动模式,选择相应的步骤程序(修磨、月牙剪、对中单元、剪切对中、中性层调整、出口电极移动等)按初始化按钮焊接程序自动中单元是否打开,入、出口活套辊是否在低位,可移动小车是否在初始位置,月牙剪、修磨单元、冲孔单元是否满足条件,移动框架夹钳中性层条件是否被初始化,如果条件具备,程序循环按钮闪烁进行下一步操作。
②定缝刀下降相应单元空气吹扫,等待焊接工艺参数的输入,按下PD1确认按钮,如果条件满足程序循环按钮闪烁等待命令。
③按下一步出口活套起套,点动主线相应按钮,带钢撞贴定缝刀,2#、3#对中单元动作,调整3#对中单元使钢带头部贴紧定缝刀。
④按下一步程序出口夹钳夹紧带钢,对中打开空气吹扫单元吹扫。
⑤按下一步入口单元动作,和出口单元类似活套辊起套,对中单元动作,夹钳夹紧带钢。
⑥按下一步可移动框架后移,定缝刀上升回到初始位置,可移动框架按照程序靠近出口带钢,调整固定单元移动使带钢对齐,执行下一步开始焊接。
酸洗冷连轧机组板形控制优化

酸洗冷连轧机组板形控制优化酸洗冷连轧机组板形控制优化随着社会的发展,人们对于钢板的工艺和质量的要求越来越高。
传统的钢板生产方式已经无法满足市场需求,需要引进先进的技术设备来提高生产效率和质量。
酸洗冷连轧机组作为一种高效的钢板生产设备,在钢铁行业广泛应用。
酸洗冷连轧机组板形控制是钢板生产中重要的技术环节,它直接影响着钢板的质量和工艺。
因此,对酸洗冷连轧机组板形控制进行优化,可以提高钢板生产的质量和效率,减少能源消耗,也可以降低生产成本,提高企业的竞争力。
1. 酸洗冷连轧机组板形控制的意义酸洗冷连轧机主要是用来生产薄板和中厚板的,它是由酸洗单机和冷连轧单机组成。
酸洗单机的主要作用是去除钢板表面的氧化皮和锈蚀物,并清除切割和热轧时产生的油和泥等杂质。
冷连轧单机则是将酸洗后的钢板进行轧制成所需的材料。
在钢板生产中,板形控制是一个十分关键的环节。
板形是钢板的表面形状和尺寸,它直接影响着油漆涂装、弯曲、对接、焊接等加工阶段的质量和效率。
而酸洗冷连轧机组的板形控制主要是通过调整机组的辊位和压力来实现。
因此,对板形控制进行优化可以减少钢板的误差,提高钢板的品质和性能,进而提高钢板的使用价值。
2. 酸洗冷连轧机组板形控制优化方法2.1 建立动态板形模型酸洗冷连轧机组板形是由辊位和辊压力共同作用下形成的。
对于所要生产的不同规格钢板,需要在机组内定义不同的辊位和辊压力。
因此,建立一个动态的板形模型可以帮助优化板形控制。
该动态模型包含机组的辊位、辊压力以及钢带的内部应力和变形信息,可以利用数学模型预测钢带轧制时的变形情况。
2.2 控制辊位角调整辊位角是影响板形控制的重要参数之一。
一般情况下,辊位角调整的优化方法为强制切换辊位位置。
但在实际操作过程中,如果调整不当,可能导致板形偏差加大。
因此,需要引进模糊控制理论,通过模糊控制算法进行辊位角的调整,使钢板产生的误差尽量小。
2.3 调整辊压力辊压力的大小直接影响着钢板的变形情况。
轧机主操操作
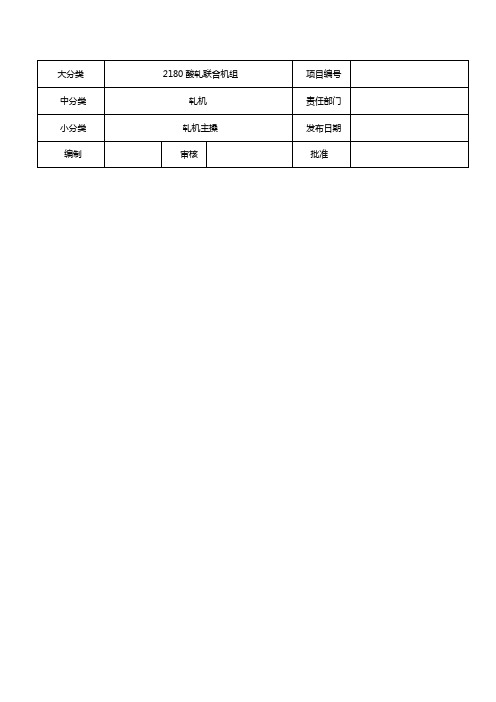
3、手动同时按下剪切信号按钮。
4、出口设备开始进行剪切准备。
5、剪切条件:
①、TRT芯轴在膨胀状态;
②、皮带助卷器在包取状态;
③、飞剪达到准备状态;
④、TRT芯轴旋转;
⑤、皮带助卷器皮带从动;
⑥、皮带运输旋转;
⑦、出口夹送辊夹紧带钢;
⑧、TRC上、下压辊压紧钢卷;
③ 根据断带的实际位置按下带钢同步位置按钮。
大分类
2180酸轧联合机组
项目编号
中分类
轧机
责任部门
小分类
轧机主操
发布日期
编制
审核
批准
2.8 根据带钢厚度和实际需求将辊缝打开8㎜以上或全部打开。
2.9 通知机架操作工将机架间的压辊抬起,并点动带钢到卷取芯轴,卸下钢卷。
2.10 真实断带及操作完成。
3. 假性断带及操作步骤:
项目编号
中分类
轧机
责任部门
小分类
轧机主操
发布日期
编制
审核
批准
(四)、套筒系统操作
1. 套筒系统的开启
1.1 根据轧制计划,钢卷需要加套筒时,主操提前通知轧机出口操作工做好上套筒准备。
1.2 在加装套筒的前一个钢卷轧制时,主操将套筒系统打开:
① 在在轧机主画面界面中点击套筒按钮。
② 在弹出的子画面中激活套筒系统。
7、轧机以60m/min的速度开始启动。
8、根据1-5机架板形状况及时适度的给予倾斜和工作辊、中间辊弯辊控制。
9、当板形趋于稳定、出口厚度达到设定值时,启动操作完成。
大分类
2180酸轧联合机门
小分类
轧机主操
发布日期
- 1、下载文档前请自行甄别文档内容的完整性,平台不提供额外的编辑、内容补充、找答案等附加服务。
- 2、"仅部分预览"的文档,不可在线预览部分如存在完整性等问题,可反馈申请退款(可完整预览的文档不适用该条件!)。
- 3、如文档侵犯您的权益,请联系客服反馈,我们会尽快为您处理(人工客服工作时间:9:00-18:30)。
位置内环
S 磁尺
伺服阀
液压辊缝控制(RGC)
主要内容
概述:检测及执行单元等; 控制模式 :辊缝控制,轧制力控制; 控制技术 :伺服阀特性补偿,泄漏检测等; 辊缝标定 ; 机架安全 ;
2020/11/21
液压辊缝控制(RGC)
概述
操作侧
驱动侧
液压辊缝控制功能(HGC)主 要实现机架的辊缝或轧制力控制,以 及倾斜控制或轧制力差控制。
2020/11/21
系统结构(外环-内环)
MFC
ITC
ITC
ITC
ITC
THFF
THFB THFF
RGC
RGC
RGC
RGC
RGC
THFB VC
VC
VC
VC
Mon
2020/11/21度外环
AGC_Corr
Ref
S
磁尺
位置内环
伺服阀
2020/11/21
张力外环 ITC_Corr
酸轧联合机组 机架控制
演讲人:**
2020/11/21
主要内容
液压辊缝控制,简称为HGC( Hydraulic Gap Control),或 者RGC(Roll Gap Control)。
机架间张力控制,简称ITC( Interstand Tension Control)。 自动厚度控制,简称AGC( Automatic Gauge Control)。
关闭辊缝
该侧切换为轧制力 控制
两侧均达到最小轧制力
该侧加载至最小轧 制力
加载轧制力至标定 轧制力
2020/11/21
转动轧辊,获取新 的零辊缝位置
记忆辊缝
打开辊缝,并换辊 加载至标定轧制力
换辊完毕
将当前辊缝标定为 记忆辊缝
获取新的零辊缝位 置
液压辊缝控制(RGC)
机架安全
辊缝锁定
急停按钮; “机架锁定”按钮; 辊缝倾斜(轧制力差)超限; 检测元件(SONY磁尺,压力传感器)故障 伺服阀(泄漏检测,阀芯反馈等)故障;
其中,Ps为系统压力,△P为伺服阀入出口压力差。 由于进出油两种情况下入出口压力差不同,所以补偿增益也需要
分两种情况考虑
2020/11/21
液压辊缝控制(RGC)
伺服阀特性补偿
3-way
Pm
k_cl
3
2
1
0
0
25
50
75
100
主腔压力 [%Ps]
Pm
K_op
3
2
1
0
0
25
50
75
100
主腔压力 [% Ps]
Actual FR
FR Setpoint 2
Diff.FR Setpoint 2
FR Setpoint DS
Ramp
Ramp Ramp Ramp
Gap Control OS
FR Control DS FR Control
Diff. FR Control
Pist Area OS Pist Pressure OS
模式1:第五机架-光辊
VC TC
自动厚度控制(AGC)
系统结构
ITC3-4
ITC2-3
ITC1-2
MFC
FF2
FB1
FF1
RGC5
RGC4
RGC3
RGC2
RGC1
ITC4-5
VC5
VC4
VC3
VC2
VC1
FB4R
2020/11/21
测厚仪 激光测速仪 带钢张力计
Mon
ITC: 中间机架张力控制 FB : 反馈控制 FF: 前馈控制 Mon: 监控控制
2020/11/21
液压辊缝控制(RGC)
Actual Position DS
Zero Position DS
Actual Gap DS
2
Actual Gap
Gap Setpoint
Gap Setpoint DS
Ramp Ramp
Gap Control DS Gap Control
2
Tilting Setpoint
平均辊缝即两侧辊缝的算术平均值,辊缝倾斜即传动侧辊缝减去 操作侧辊缝所得差值 (人为定义);
2020/11/21
液压辊缝控制(RGC)
轧制力控制:
实际轧制力由轧制力仪测量或者根据安装在液压油路中的压力传 感器检测信号进行计算。
使用压力传感器计算,单侧液压缸推上力=该侧液压缸活塞侧油 压*活塞侧横截面积 - 该侧液压缸杆侧油压*杆侧横截面积;
RGC: 辊缝控制 MFC :秒流量控制 VC: 速度控制
模式2:第五机架-毛辊(光整模式)
VC TC
自动厚度控制(AGC)-入口AGC
C1机架前馈(FF1)
ITC1-2 RGC2
TC RGC1
机架0 6#张力辊
去卷取机
TC
VC5
ITC4-5
VC4 ITC3-4
VC3 ITC2-3
VC2 ITC1-2
VC1
VC TC
2020/11/21
机架间张力控制(ITC)
速度张力模式
穿带期间采用速度张力模式;另外对于4-5机架间张力,当末机架工 作于光整模式时,采用速度张力模式;
到油箱
Ps
K_cl
Ps 2 (Ps Pm)
P = Ps-Pm
K_op Ps 2 Pm P = Pm
K_op
K_cl
2
0
Pb
0
25 50 75 100
Pb
主腔压力 [% Ps]
2
0
0
25 50 75 100
杆腔压力 [% Ps]
4-way
Pm
到油箱
K_cl
Ps
2 (Ps Pm)
Ps P = Ps-Pm
Err
Ref
参考值恒定
检查
Out Sat
2020/11/21
液压辊缝控制(RGC)
伺服输出
Ps
Pm
伺服阀流量
线性化补偿
增益选择
位置反馈 位置参考值
PID 调节器
2020/11/21
伺服阀泄露 补偿
伺服阀参考值
液压辊缝控制(RGC)
控制输出
当采用平均辊缝控制时: 传动侧输出=平均辊缝控制环输出+倾斜控制环输出; 操作侧输出=平均辊缝控制环输出-倾斜控制环输出; 当采用总轧制力控制时: 传动侧输出=总轧制力控制环输出+轧制力差控制环输出; 操作侧输出=总轧制力控制环输出-轧制力差控制环输出;
开始轧制,辊缝张力模式下,采用张力极限方式,当实际张力位于 (TL1,TH1)内时,控制器不调节,当张力波动至(TL1,TH1)以 外时,控制器投入,调节张力进入(TL2,TH2)区间时,控制器被 保持。
2020/11/21
自动厚度控制(AGC)
系统结构
ITC4-5
ITC3-4
ITC2-3
ITC1-2
每个机架安装有两个液压推上
(压下)缸,一个在操作侧,一个在
传动侧;液压缸位置通过安装在每个
液压缸内的sony磁尺进行检测。轧制
力则通过轧制力仪或者推上缸主油路 的压力传感器进行检测。
轧制线
缸固定,活塞运动。每个活塞的 运动由液压回路的油流量确定,伺服 阀控制油流量,伺服阀线圈电流设定 来自控制器的模拟输出。
液压辊缝控制(RGC)
辊缝标定
辊缝标定的目的就在于找到各侧的零辊缝位置辊缝计算,为 辊缝计算提供参考点;酸轧机组中的机架标定分为有无带钢 标定和有带钢标定两种;
无带钢标定
联锁条件满足
打开辊缝
启动顺控,进入两 侧辊缝单独控制
有带钢标定
停止轧制
启动顺控,减少轧 制力至标定值
联锁条件满足
某侧到达接触轧制力
辊缝快开
上游发生断带; 拍下辊缝快开按钮; 轧制力超限; 液压站故障;
机架卸荷
有快开请求,同时,伺服系统(检测元件,执行元件,液压站)故障;
2020/11/21
机架间张力控制(ITC)
系统结构 速度张力模式 /辊缝张力模式
ITC4-5 RGC5
ITC3-4 RGC4
ITC2-3 RGC3
上支撑辊 上中间辊 上工作辊 下工作辊 下中间辊
下支撑辊
2020/11/21
液压辊缝控制(RGC)
概述
操作侧
传动侧
有杆腔
无杆腔 压力传感器
PT
下支撑辊
Sony 磁尺
Sony 磁尺
比例伺 服阀
伺服阀
伺服阀
比例伺 服阀
压力传感器 PT
卸荷阀 锁紧阀
锁紧阀
比例减 压阀
锁紧阀
锁紧阀 卸荷阀
比例伺服阀:200L/min,快速打开; 伺服阀:90L/min,精细调节;
倾斜控制-控制倾斜,用于位置模式轧制; 轧制力差控制-控制轧制力差,用于轧制力模式轧制;
模式切换
保证切换的互斥性; 通过赋值当前值+斜坡函数实现辊缝控制和轧制力控制之间的无
冲击切换!!
2020/11/21
K SV
PS 2P
液压辊缝控制(RGC)
伺服阀特性补偿
伺服阀的流量与其入口、出口间压力差的平方根成正比,使得伺 服阀在控制系统表现为一个非线性环节,并导致整个伺服系统响 应变慢。为了补偿这一非线性环节,可以通过对伺服阀输出乘以 一个可变增益来实现:
速度张力模式又分为张力连续和张力极限两种方式。 张力连续指张力控制器连续调节使张力保持为恒值; 张力极限指张力控制器仅在张力超限时进行调节,当张力调回目标