经验公式确定钢的热处理温度
钢的热处理工艺设计经验公式大全

钢的热处理工艺设计经验公式大全热处理是钢材加工过程中非常重要的一环,通过改变钢材的晶体结构和组织状态,可以提高钢材的力学性能和耐腐蚀性能。
热处理工艺设计是确定热处理参数和过程的过程。
在热处理工艺设计中,经验公式是实践经验的总结,可以作为指导设计的依据。
以下是一些常用的钢的热处理工艺设计经验公式:1.碳钢淬火温度(Tc)经验公式:Tc=727+0.33*C其中,Tc为淬火温度(单位:摄氏度),C为碳含量(单位:百分比)。
这个公式是根据碳钢的相图和强度要求推导出来的。
2.碳钢回火温度(Th)经验公式:Th=500+5*HRC-10其中,Th为回火温度(单位:摄氏度),HRC为硬度值(单位:洛氏硬度)。
这个公式是一种经验化的关系,用于估算碳钢的回火温度。
3.碳钢退火温度(Ta)经验公式:Ta=800+20*M-10*F其中,Ta为退火温度(单位:摄氏度),M为马氏体体积分数(百分比),F为珠光体体积分数(百分比)。
这个公式是根据马氏体转变的温度范围和组织形态确定的。
4.合金钢的时效温度(Ts)经验公式:Ts=Ac3+100-60*Ln(t)其中,Ts为时效温度(单位:摄氏度),Ac3为奥氏体转变温度(单位:摄氏度),t为时效时间(单位:小时)。
这个公式是用于选择合金钢的时效温度和时间。
5.不锈钢的固溶温度(Ts)经验公式:Ts=0.6*Ac1+0.4*Ac3其中,Ts为固溶温度(单位:摄氏度),Ac1为铁素体转变温度(单位:摄氏度),Ac3为奥氏体转变温度(单位:摄氏度)。
这个公式是选择不锈钢的固溶温度的经验方法。
6.复合材料的固化温度(Tc)经验公式:Tc=0.6*Tg+0.4*Tm其中,Tc为固化温度(单位:摄氏度),Tg为玻璃化转变温度(单位:摄氏度),Tm为熔融转变温度(单位:摄氏度)。
这个公式适用于选择复合材料的固化温度。
常用钢的热处理回火计算

常用钢的热处理回火计算中国机械CAD论坛欢迎您的到来无图版在线时间:248(小时)注册时间:2007-01-28最后登录:2008-03-10常用钢的热处理回火计算钢的回火硬度(H)取决于回火温度(T)和回火时间(t),三者之间存在着一定的函数关系,即H = f(T,t)。
当t为定值时,H和T的函数关系可划分为四种类型:(1)直线型;(2)抛物线型;(3)幂函数型;(4)直线和幂函数的复合型。
因后两种类型在使用时,计算和作图极为不便,故大多数情况下,将其简化为直线和抛物线型,用经验方程可表示为:H= a1 + k1 T H = a2 + k2 T其中,a1、a2、k1、k2为特定系数。
依据实际工艺试验和有关参考文献的数据,运用数理统计方法计算和修正,得出部分常用钢种的回火方程。
实践证明,这些经验公式具有重要的适用价值。
钢号淬火温度/淬火介质回火方程45 840/水 H = 62 -(1/9000)T 220Cr 890/油 H = 50 -(2/45)T38CrMoAl 930/油 H = 64 -(1/25)T(T<550)H = 95 -(1/10)T(T>550)40Cr 850/油H = 75 -(3/40)T50CrVA 850/油 H = 73 -(1/14)T60Si2Mn 860/油 H = 68 -(1/11250)T 265Mn 820/油 H = 74 -(3/40)TT8 800/水 H = 78-(7/80)TT10 780/水 H = 82.7 -(1/11)TCrWMn 830/油 H = 69 -(1/25)TCr12 980/油H = 64 -(1/80)T(T<500)H = 107.5 -(1/10)T(T>500)Cr12MoV 1000/油 H = 65 -(1/100)T(T<500)9CrSi 865/油 H = 69 -(1/30)T5CrNiMo 855/油 H = 72.5 -(1/16)T5CrMnMo 855/油 H = 69 -(3/50)TW18Cr4V 1280/油H = 93 -(3/31250)T 2GCr15 850/油 H = 733 -(2/3)T使用说明:(1)要求原材料化学成分及力学性能符合国家技术标准(GB、YB等),最大外经(或相对厚度)接近或小于淬火临界直径。
钢的热处理工艺设计经验公式

随着科学技术的发展,为满足机械零件越来越高的性能要求,研制和引进的新钢种日益增多。
由于诸多原因,大多数生产厂家无法及时获得新钢种的有关资料数据,纷材料选择、技术设计和热处理工艺编制带来困难。
解决的办法之一是进行必要的工艺试验,为此,要消耗大量的经费和时问。
这对于从事单件、小批量生产的中小企业是难以办到的。
经过热处理工作者的多年努力,采用试验和数理统计方法导出了许多实用的经验公式。
本文收集整理出的33个公式,可在缺乏新材料的有关数据资料的情况下(只需通过理化分析得到新锕种的化学成分)估算出钢的热处理工艺参数,进行热处理工艺设计。
这是建立金属热处理柔性系统(FCM)数据库的前期工作。
1 钢的热处理相变点及再结晶温度的计算_1](1)亚共析钢加热时,所有铁素体转变为奥氏体的温度Ac (℃):Ac :908-223.7C+438 5P+30 49Si+37.92V一34.4Mn一23Ni一200(C一0 54+0.06Ni) ??(1)Ac =854—180C一14Mn+44Si一17_8Ni一1.7Cr ? ?(2)式(1),(2)适用于0.3%≤C≤0.6%,0≤si≤1.0%,O≤N 3.5%,0~<Cr<-I.5%,O<-Mc~<0.5%。
航空棚遣技术(2)钢加热时,开始形成奥氏体的温度Ac,(℃):Ac =723—14Mn+22Si一14.4Ni+23.3cr---(3)式(3)适用范围同式(1)。
Ac =723+25Si一7Mn+l5Q 一15Ni+30W +40Mo+50V ?---(4)式(4)适用于0≤c≤0.8%,0≤Mo≤0.5%,0≤v≤0.5%,oKwK1、5%,0≤CrY7.5%。
(3)钢奥氏体化后冷却时,奥氏体开始转变为马氏体的温度M (℃):M .=550—350C一40Mn一35V 一20Cr—l7Ni—Cu一10Mo一5W +15Co+30Al+0Si ? ?(5) M =561—474C一33Mn一17Cr一17Ni一21Mo?(6)式(5),(6)适用于中低碳钢。
铸钢件常见热处理工艺

铸钢件常见热处理按加热和冷却条件不同,铸钢件的主要热处理方式有:退火(工艺代号:5111)、正火(工艺代号:5121)、均匀化处理、淬火(工艺代号:5131)、回火(工艺代号:5141)、固溶处理(工艺代号:5171)、沉淀硬化、消除应力处理及除氢处理。
1.退火(工艺代号:5111) 退火是将铸钢件加热到Ac3以上20~30℃,保温一定时间,冷却的热处理工艺。
退火的目的是为消除铸造组织中的柱状晶、粗等轴晶、魏氏组织和树枝状偏析,以改善铸钢力学性能。
碳钢退火后的组织:亚共析铸钢为铁素体和珠光体,共析铸钢为珠光体,过共析铸钢为珠光体和碳化物。
适用于所有牌号的铸钢件。
图11—4为几种退火处理工艺的加热规范示意图。
表ll—1为铸钢件常用退火工艺类型及其应用。
2.正火(工艺代号:5121) 正火是将铸钢件目口热到Ac3温度以上30~50℃保温,使之完全奥氏体化,然后在静止空气中冷却的热处理工艺。
图11—5为碳钢的正火温度范围示意图。
正火的目的是细化钢的组织,使其具有所需的力学性能,也司作为以后热处理的预备处理。
正火与退火工艺的区别有两个:其一是正火加热温度要偏高些;其二是正火冷却较快些。
经正火的铸钢强度稍高于退火铸钢,其珠光体组织较细。
一般工程用碳钢及部分厚大、形状复杂的合金钢铸件多采用正火处理。
正火可消除共析铸钢和过共析铸钢件中的网状碳化物,以利于球化退火;可作为中碳钢以及合金结构钢淬火前的预备处理,以细化晶粒和均匀组织,从而减少铸件在淬火时产生的缺陷。
3.淬火(工艺代号:5131) 淬火是将铸钢件加热到奥氏体化后(Ac。
或Ac&#8226;以上),保持一定时间后以适当方式冷却,获得马氏体或贝氏体组织的热处理工艺。
常见的有水冷淬火、油冷淬火和空冷淬火等。
铸钢件淬火后应及时进行回火处理,以消除淬火应力及获得所需综合力学性能。
图11—6为淬火回火工艺示意图。
铸钢件淬火工艺的主要参数:(1)淬火温度:淬火温度取决于铸钢的化学成分和相应的临界温度点。
钢的力学性能及热处理工艺经验公式
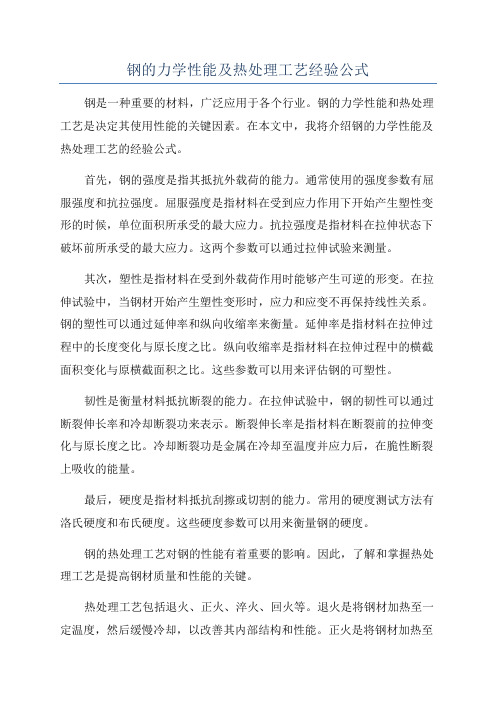
钢的力学性能及热处理工艺经验公式钢是一种重要的材料,广泛应用于各个行业。
钢的力学性能和热处理工艺是决定其使用性能的关键因素。
在本文中,我将介绍钢的力学性能及热处理工艺的经验公式。
首先,钢的强度是指其抵抗外载荷的能力。
通常使用的强度参数有屈服强度和抗拉强度。
屈服强度是指材料在受到应力作用下开始产生塑性变形的时候,单位面积所承受的最大应力。
抗拉强度是指材料在拉伸状态下破坏前所承受的最大应力。
这两个参数可以通过拉伸试验来测量。
其次,塑性是指材料在受到外载荷作用时能够产生可逆的形变。
在拉伸试验中,当钢材开始产生塑性变形时,应力和应变不再保持线性关系。
钢的塑性可以通过延伸率和纵向收缩率来衡量。
延伸率是指材料在拉伸过程中的长度变化与原长度之比。
纵向收缩率是指材料在拉伸过程中的横截面积变化与原横截面积之比。
这些参数可以用来评估钢的可塑性。
韧性是衡量材料抵抗断裂的能力。
在拉伸试验中,钢的韧性可以通过断裂伸长率和冷却断裂功来表示。
断裂伸长率是指材料在断裂前的拉伸变化与原长度之比。
冷却断裂功是金属在冷却至温度并应力后,在脆性断裂上吸收的能量。
最后,硬度是指材料抵抗刮擦或切割的能力。
常用的硬度测试方法有洛氏硬度和布氏硬度。
这些硬度参数可以用来衡量钢的硬度。
钢的热处理工艺对钢的性能有着重要的影响。
因此,了解和掌握热处理工艺是提高钢材质量和性能的关键。
热处理工艺包括退火、正火、淬火、回火等。
退火是将钢材加热至一定温度,然后缓慢冷却,以改善其内部结构和性能。
正火是将钢材加热至适宜温度,然后迅速冷却,以提高其硬度和强度。
淬火是将钢材加热至临界温度,然后迅速冷却,使其获得高硬度和高强度。
回火是将淬火后的钢材加热至适宜温度,然后缓慢冷却,以减轻淬火时产生的内应力。
在实际应用中,钢的力学性能和热处理工艺往往需要通过实验和经验进行调整和优化。
工程师们通过实验和经验总结出了一些公式,用于预测和计算钢的力学性能和热处理工艺。
一些常用的公式包括哈氏公式、拉伸公式和冷却断裂功公式等。
热处理参数确定(调质)
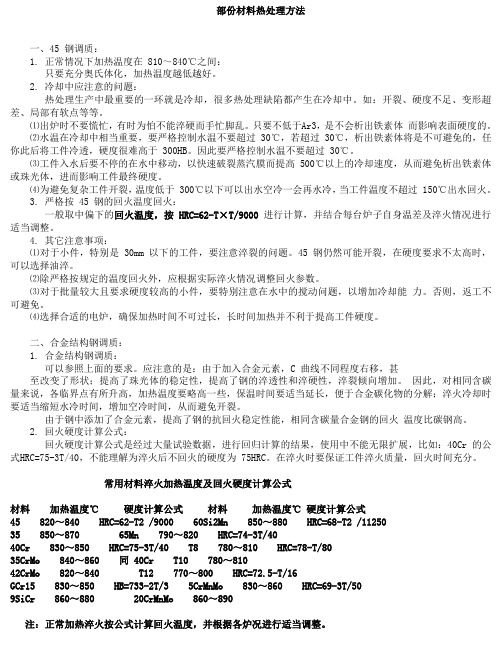
部份材料热处理方法一、45 钢调质:1. 正常情况下加热温度在 810~840℃之间:只要充分奥氏体化,加热温度越低越好。
2. 冷却中应注意的问题:热处理生产中最重要的一环就是冷却,很多热处理缺陷都产生在冷却中。
如:开裂、硬度不足、变形超差、局部有软点等等。
⑴出炉时不要慌忙,有时为怕不能淬硬而手忙脚乱。
只要不低于Ar3,是不会析出铁素体而影响表面硬度的。
⑵水温在冷却中相当重要,要严格控制水温不要超过 30℃,若超过 30℃,析出铁素体将是不可避免的,任你此后将工件冷透,硬度很难高于 300HB。
因此要严格控制水温不要超过 30℃。
⑶工件入水后要不停的在水中移动,以快速破裂蒸汽膜而提高 500℃以上的冷却速度,从而避免析出铁素体或珠光体,进而影响工件最终硬度。
⑷为避免复杂工件开裂,温度低于 300℃以下可以出水空冷一会再水冷,当工件温度不超过 150℃出水回火。
3. 严格按 45 钢的回火温度回火:一般取中偏下的回火温度,按 HRC=62-T×T/9000 进行计算,并结合每台炉子自身温差及淬火情况进行适当调整。
4. 其它注意事项:⑴对于小件,特别是 30mm 以下的工件,要注意淬裂的问题。
45 钢仍然可能开裂,在硬度要求不太高时,可以选择油淬。
⑵除严格按规定的温度回火外,应根据实际淬火情况调整回火参数。
⑶对于批量较大且要求硬度较高的小件,要特别注意在水中的搅动问题,以增加冷却能力。
否则,返工不可避免。
⑷选择合适的电炉,确保加热时间不可过长,长时间加热并不利于提高工件硬度。
二、合金结构钢调质:1. 合金结构钢调质:可以参照上面的要求。
应注意的是:由于加入合金元素,C 曲线不同程度右移,甚至改变了形状;提高了珠光体的稳定性,提高了钢的淬透性和淬硬性,淬裂倾向增加。
因此,对相同含碳量来说,各临界点有所升高,加热温度要略高一些,保温时间要适当延长,便于合金碳化物的分解;淬火冷却时要适当缩短水冷时间,增加空冷时间,从而避免开裂。
钢的热处理温度Ac1、Ac3、Ar1具体温度

钢的热处理温度Ac1、Ac3、Ar1具体温度钢的热处理温度A1、A3与Ac1、Ac3、Ar1 Acm铁碳合金,可以查阅Fe-C相图。
(铁碳相图有几条温度线---727度,1148度,1495度)如果是合金钢,只能根据具体牌号查阅有关资料。
1. A1:在平衡状态下,奥氏体、铁素体、渗碳体或碳化物共存的温度,用A1表示。
2. A3亚共析钢在平衡状态下,奥氏体和铁素体共存的最高温度。
用A3表示。
3.Ac1:钢加热时~开始形成奥氏体的温度,4.Ac3:亚共析钢加热时~所有铁素体均转变为奥氏体的温度;5.Ar1:钢高温奥氏体化后冷却时~奥氏体分解为铁素体和珠光体的温度,6.Acm:过共析钢在平衡状态下~奥氏体和渗碳体或碳化物共存的最高温度~即过共析钢的上临界点。
即一般所说的下转变温度是A1或Ac1,上转变温度是A3或Ac3或Acm。
不同化学成分,有不同的临界点这些都是一个温度范围,根据冷却速度的不同范围可能不一样,如果缓慢加热冷却的话会接近理论值。
但是理论值也根据不同的材料,C含量不同这温度都不一样。
合金含量的不同,Ac1、Ac3、Ar1......等的温度是不同,在铁碳相图你可以根据C含量找到一个大致的温度,但这个温度只能作为参考,具体的温度要经过试验才能确定下来。
可以采用膨胀法测定或者根据经验公式计算,当然经验公式可能有偏差。
不同钢材受其成分影响,临界温度不同。
根据铁碳相图查找,不同种类的钢有不同的合金元素含量,也就有不同的奥氏体转变温度,大体上说是钢在加热或冷却时奥氏体转变的温度,各种钢各自的具体温度不一样。
Q245R钢:Ac1是735、Ac3是855、Ar1是680、Ar3是855.Q345R钢:Ac1是735、Ac3是863、Ar1是685、Ar3是840.45钢为: Ac1是740、Ac3是850、Ar1是735、Ar3是785.在完整的Fe-C和Fe-Fe3C的合金相图中,有三套曲线,以平衡状态下的相图为基点,相同材料在加热和冷却两个不同的过程中,相同相变点发生的温度是不同的,有一个滞后的作用,这是由于相变的过程都需要足够的驱动力。
经验公式确定钢的热处理温度
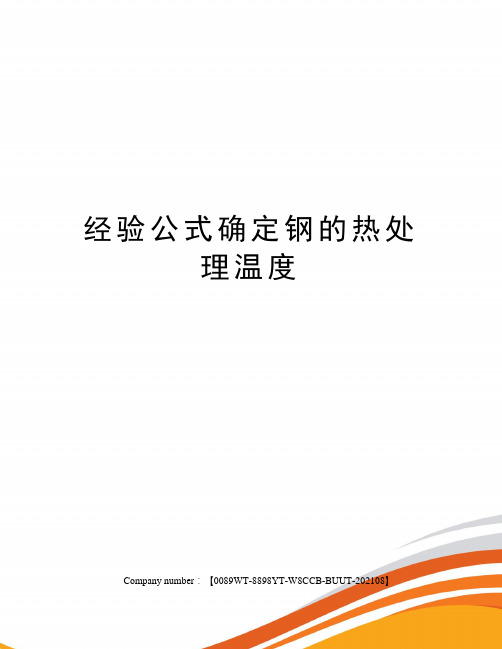
经验公式确定钢的热处理温度Company number:【0089WT-8898YT-W8CCB-BUUT-202108】钢的热处理工艺设计经验公式------------根据经验公式确定热处理的保温温度------------1钢的热处理正火加热时间加热时间t=KD (1)式中t为加热时间(s);D使工件有效厚度(mm);K是加热时间系数(s/mm)。
K值的经验数据见表1。
表1 K值的经验数据正火加热温度根据钢的相变临界点选择正火加热温度低碳钢:T=Ac3+(100~150℃)(2)中碳钢:T=Ac3+(50~100℃)(3)高碳钢:T=A Cm+(30~50℃)(4)亚共析钢:T=Ac3+(30~80℃)(5)共析钢及过共析钢:T=A Cm+(30~50℃)(6)淬火加热时间为了估算方便起见,计算淬火加热时间多采用下列经验公式:t=a· K ·D︱ (不经预热) (7)t=(a+b)· K ·D︱(经一次预热) (8)t=(a+b+c)· K ·D︱(经二次预热) (9)式中t—加热时间(min);a—到达淬火温度的加热系数(min/mm);b—到达预热温度的加热系数(min/mm);c—到达二次预热温度的加热系数(min/mm);K—装炉修正系数;D︱--工件的有效厚度(mm)。
在一般的加热条件下,采用箱式炉进行加热时,碳素钢及合金钢a多采用1~mm;b 为~2min/mm(高速钢及合金钢一次预热a=~;b=~;二次预热a=~;b=~;c=~),若在箱式炉中进行快速加热时,当炉温较淬火加热温度高出100~150℃时,系数a约为~20秒/毫米,系数b不用另加。
若用盐浴加热,则所需时间,应较箱式炉中加热时间少五分之一(经预热)至三分之一(不经预热)左右。
工件装炉修正系数K的经验值如表2:表2 工件装炉修正系数K淬火加热温度按常规工艺,亚共析钢的淬火加热温度为Ac3+(30~50℃);(10)共析和过共析钢为Ac1+(30~50℃);(11)合金钢的淬火加热温度常选用Ac1(或Ac3)+(50~100℃)(12)回火加热时间对于中温或高温回火的工件,回火时间是指均匀透烧所用的时间,可按下列经验公式计算:t=aD+b (13)式中t—回火保温时间(min);D—工件有效尺寸;(mm);a—加热系数(min/mm);b—附加时间,一般为10~20分钟。
- 1、下载文档前请自行甄别文档内容的完整性,平台不提供额外的编辑、内容补充、找答案等附加服务。
- 2、"仅部分预览"的文档,不可在线预览部分如存在完整性等问题,可反馈申请退款(可完整预览的文档不适用该条件!)。
- 3、如文档侵犯您的权益,请联系客服反馈,我们会尽快为您处理(人工客服工作时间:9:00-18:30)。
钢的热处理工艺设计经验公式------------根据经验公式确定热处理的保温温度------------1钢的热处理1.1正火加热时间加热时间t=KD (1)式中t为加热时间(s);D使工件有效厚度(mm);K是加热时间系数(s/mm)。
K值的经验数据见表1。
表1 K值的经验数据1.2 正火加热温度根据钢的相变临界点选择正火加热温度+(100~150℃)(2)低碳钢:T=Ac3中碳钢:T=Ac+(50~100℃)(3)3+(30~50℃)(4)高碳钢:T=ACm亚共析钢:T=Ac+(30~80℃)(5)3共析钢及过共析钢:T=A+(30~50℃)(6)Cm1.3淬火加热时间为了估算方便起见,计算淬火加热时间多采用下列经验公式:t=a· K ·D︱ (不经预热) (7)t=(a+b)· K ·D︱(经一次预热) (8)t=(a+b+c)· K ·D︱(经二次预热) (9)式中t—加热时间(min);a—到达淬火温度的加热系数(min/mm);b—到达预热温度的加热系数(min/mm);c—到达二次预热温度的加热系数(min/mm);K—装炉修正系数;D︱--工件的有效厚度(mm)。
在一般的加热条件下,采用箱式炉进行加热时,碳素钢及合金钢a多采用1~1.5min/mm;b为1.5~2min/mm(高速钢及合金钢一次预热a=0.5~0.3;b=2.5~3.6;二次预热a=0.5~0.3;b=1.5~2.5;c=0.8~1.1),若在箱式炉中进行快速加热时,当炉温较淬火加热温度高出100~150℃时,系数a 约为1.5~20秒/毫米,系数b 不用另加。
若用盐浴加热,则所需时间,应较箱式炉中加热时间少五分之一(经预热)至三分之一(不经预热)左右。
工件装炉修正系数K 的经验值如表2:表2 工件装炉修正系数K1.4 淬火加热温度按常规工艺,亚共析钢的淬火加热温度为Ac 3+(30~50℃); (10)共析和过共析钢为Ac 1+(30~50℃); (11) 合金钢的淬火加热温度常选用Ac 1(或Ac 3)+(50~100℃) (12) 1.5 回火加热时间对于中温或高温回火的工件,回火时间是指均匀透烧所用的时间,可按下列经验公式计算:t=aD+b (13)式中t —回火保温时间(min );D —工件有效尺寸;(mm ); a —加热系数(min/mm );b —附加时间,一般为10~20分钟。
盐浴的加热系数为0.5~0.8min/mm ;铅浴的加热系数为0.3~0.5min/mm ;井式回火电炉(RJJ 系列回火电炉)加热系数为1.0~1.5min/mm ;箱式电炉加热系数为2~2.5mim/mm 。
1.6 回火加热温度钢的回火定量关系式很早就有人研究,其经验公式为: 钢的回火温度的估算,T=200+k(60-x) (14)式中: x —回火后硬度值,HRC ;k —待定系数,对于45钢,x>30,k =11;x ≤30,k=12。
大量试验表明,当钢的回火参数P一定时,回火所达到的工艺效果——硬度值或力学性能相同。
因此,按传统经验式确定回火参数仅在标准态(回火1h)时方可使用,实际生产应用受到限制.为了解决上述问题,将有关因素均定量表达,文献中导出如下回火公式:(1)在200~40O℃范围:HV=640-(T-20)×1.05+(lgt-1.28)×366+( T-200)(lgt-1.28)×0.036 (15)(2)在400~600℃范围:HV=17.2×103/T-(1gt一1.28)×29.4-(T-400)(Igt-1.28)×0.023 (16)式中T--回火温度℃t--回火时间,min对比可以看出影响回火效果的主要因素是T和t能较好,较真实地反映出实际工艺参数的影响,定量地表达了不同温度区间回火硬度的变化特征。
2钢的热处理相变点及再结晶温度的计算2.1 A C1和A C3温度的经验公式A C1和AC3分别表示在加热过程中组织开始转变为奥氏体和全部转变为奥氏体时的温度,它们对钢的热处理工艺的制定以及新材料和新工艺的设计都具有重要意义。
因此,对AC1和AC3的预测具有较大的理论和应用价值。
Andrews搜集了英,德,法,美等国家的资料通过对大量试验数据进行回归分析,获得了根据钢的化学成分计算AC1和AC3温度的经验公式:AC3(℃)=910 - 203C1/ 2- 15.2Ni + 44.7Si + 104V + 31.5Mo +13.1W (17)AC1(℃)=723–10.7Mn –13.9Ni + 29Si + 16.9Cr + 290As + 6.38W (18) 式中的元素符号代表其含量 (质量分数,wt%,下同) ,适用钢的成分范围为:≤0.6C, ≤4.9Mn, ≤5Cr , ≤5Ni , ≤5.4Mo。
公式(1)~(2)表达了钢的AC1和AC3与化学成分之间的关系,其优点是形式简明、直观,便于应用。
2.2钢奥氏体化后冷却时,奥氏体开始转变为马氏体的温度Ms(℃)Ms=550-350C-40Mn-35V-20Cr-17Ni-Cu-10Mo-5W+15Co+30Al+0Si (19) Ms=561-474C-33Mn-17Cr-17Ni-21Mo (20) 式(19),(20)适用于中低碳钢。
Ms=539-423C-30.4Mn-17.7Ni-12.1Cr-7.5Mo (21) 式(21)适用于0.11%≤C≤0.60%,0.04%≤Mn ≤4.8%,0.11%≤Si ≤1.89% ,0≤Ni≤5.04%,0≤Cr≤4.61% ,0≤Mo≤5.4%。
注意 ,上述 Ms点的计算公式主要用于亚共析钢;对于过共析钢,由于淬火加热温度对奥氏体的成分影响较大,故根据钢的成分来计算Ms点是没有意义的。
Ms=41.7(14.6-Cr)+0.6(6.9-Ni)+33(1.33-Mn)+28(0.47-S)+1677(0.068-C-Ni)-17.8 (22) 式(22)适用于SUS类不锈钢(日本)。
2.3 奥氏体转变为马氏体(M)的终了温度Mf(℃)Mf点根据不同的马氏体转变量的计算公式:Mf=(100%M)=Ms-(215±15) (23) Mf=(90%M)=Ms-(103±12) (24) Mf=(50%M)=Ms-(47±9) (25) Mf=(10%M)=Ms-(10±3) (26) 2.4贝氏体组织开始转变的温Bs(℃)Bs=830-270C-90Mn-37Ni-70Cr-83Mo (27) 2.5 钢的再结晶温度TR(K)TR=0.4Tm (28) 式中: Tm—钢的熔点温度,K。
3钢在空气炉中加热时间(考虑节能)的计算3.1按工件形状确定加热时间t(min)t = kiw (29) 式中:ki—形状系数,k圆柱=1/6~1/9,k板=1/3~1/6,k薄壁管=(δ/D<1/4)=1/4~1/5,k厚壁管(δ/D>1/ 4) = 1/2~1/4 ;w—形状特征尺寸,直径、板厚或壁厚,mm。
3.2按实际装炉量确定加热时间t(min)t=(0.6~0.8)∑Gw (30) 式中:∑Gw—装炉工件总重量,kg。
式(30)适用于45kW箱式电炉加热。
4钢的临界冷却速度的计算4.1钢在油中淬火时心部得到马氏体的临界冷却速度νM(℃/h)logνM=9.81-4.62C+1.10Mn+0.54Ni+0.50Cr+0.60Mo+0.00183PA (31) 式中: PA—奥氏体化参数(加热时间×加热温度,此处加热时间为1h)。
4.2钢在油中淬火时心部得到贝氏体的临界冷却速度νB(℃/h)logνB=10.17-3.80C+1.07Mn+0.70Ni+0.57Cr+1.58Mo+0.0032PA (32) 4.3钢在油中淬火时心部得到珠光体-铁素体混合物的临界冷却速度νPF(℃/h)logνPF=6.36-0.43C+0.49Mn+0.78Ni+0.26Cr+0.38Mo+0.0019PA (33)4.4钢在油中淬火时心部得到50%马氏体+50%贝氏体的临界冷却速度ν50MB(℃/h)logν50MB=8.50-4.13C+0.86Mn+0.57Ni+0.41Cr+0.94Mo+0.0012PA (34) 式(31)~(34)适用条件:C≤0.50%,Mn≤1.75%,Ni≤3.0%,Cr≤2.25% ,Mo≤1.0% ,Mn+Ni+Cr+Mo≤5.0%。
5钢的淬火冷却时间的计算5.1钢预冷淬火时空气预冷时间ty(s)ty=12+(3~4)D (35) 式中:D—淬火工件危险截面厚度,mm。
5.2钢Ms 点上分级冷却时间tf(s)tf=30+5D (36)6 钢的淬火硬度的计算6.1 钢终端淬火试验时,距试样顶端4~40 mm范围内各点硬度H4~40 (HRC)=88C 1/2-0.0135E2C1/2+19Cr1/2+6.3Ni 1/2+16Mn 1/2+35Mo 1/2H4~40+5Si 1/2-0.82G-20E 1/2+2.11E-2 (37) 式中: E—到顶端距离,mm;G—奥氏体晶粒度。
6.2钢的最高淬火硬度,即淬火钢获得90%马氏体时的硬度Hh(HRC)Hh=30+50C (38) 6.3钢的临界淬火硬度,即淬火钢获得50%马氏体时的硬度Hl(HRC)Hl=24+40C (39) 6.4 钢淬火组织为马氏体时的硬度HVMHVM=127+949C+27Si+11Mn+8Ni+16Cr+21logνM (40) 6.5钢淬火组织为贝氏体时的硬度HVBHVB=-323+185C+330Si+153Mn+65Ni+144Cr+191Mo+logνB(89+54C-55Si-22Mn- 10Ni-20Cr-33Mo) (41) 6.6钢淬火组织为珠光体- 铁素体的硬度HVPFHVPF=42+223C+53Si+30Mn+13Ni+7Cr+19Mo+logνPF(10-19Si+4Ni+8Cr+130V) (42) 式(40)~(42)适用条件同式(31)~(33)。
7钢回火后硬度的计算7.1钢淬火组织为马氏体时的回火硬度HVMHVM=-74-434C-368Si+15Mn+37Ni+17Cr-335Mo-2235V+(103/PB)(260+616C+321Si-21Mn-35Ni-11Cr+352Mo-2345V) (43) 式中: PB—回火参数(回火温度×回火时间,此处加热时间为1h)。