隧道掘进施工方法浅析
隧道施工中的掘进方式和技术选择
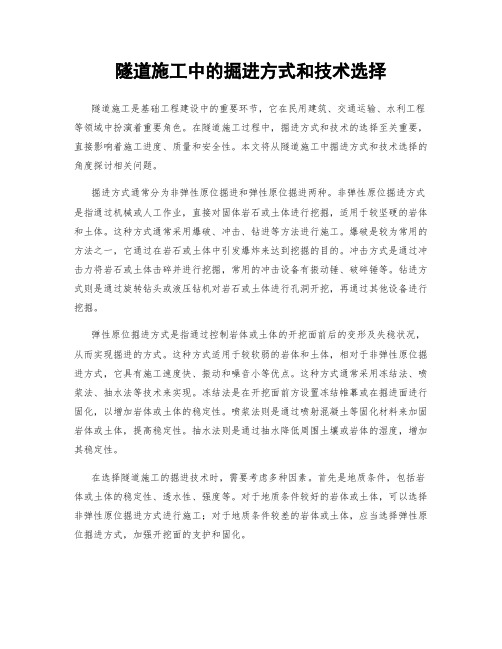
隧道施工中的掘进方式和技术选择隧道施工是基础工程建设中的重要环节,它在民用建筑、交通运输、水利工程等领域中扮演着重要角色。
在隧道施工过程中,掘进方式和技术的选择至关重要,直接影响着施工进度、质量和安全性。
本文将从隧道施工中掘进方式和技术选择的角度探讨相关问题。
掘进方式通常分为非弹性原位掘进和弹性原位掘进两种。
非弹性原位掘进方式是指通过机械或人工作业,直接对固体岩石或土体进行挖掘,适用于较坚硬的岩体和土体。
这种方式通常采用爆破、冲击、钻进等方法进行施工。
爆破是较为常用的方法之一,它通过在岩石或土体中引发爆炸来达到挖掘的目的。
冲击方式是通过冲击力将岩石或土体击碎并进行挖掘,常用的冲击设备有振动锤、破碎锤等。
钻进方式则是通过旋转钻头或液压钻机对岩石或土体进行孔洞开挖,再通过其他设备进行挖掘。
弹性原位掘进方式是指通过控制岩体或土体的开挖面前后的变形及失稳状况,从而实现掘进的方式。
这种方式适用于较软弱的岩体和土体,相对于非弹性原位掘进方式,它具有施工速度快、振动和噪音小等优点。
这种方式通常采用冻结法、喷浆法、抽水法等技术来实现。
冻结法是在开挖面前方设置冻结帷幕或在掘进面进行固化,以增加岩体或土体的稳定性。
喷浆法则是通过喷射混凝土等固化材料来加固岩体或土体,提高稳定性。
抽水法则是通过抽水降低周围土壤或岩体的湿度,增加其稳定性。
在选择隧道施工的掘进技术时,需要考虑多种因素。
首先是地质条件,包括岩体或土体的稳定性、透水性、强度等。
对于地质条件较好的岩体或土体,可以选择非弹性原位掘进方式进行施工;对于地质条件较差的岩体或土体,应当选择弹性原位掘进方式,加强开挖面的支护和固化。
其次是工程要求,包括隧道的尺寸、形状、施工时间等。
对于较长、较宽的隧道,由于施工时间较长,可以选择非弹性原位掘进方式以提高工作效率。
而对于较窄、较短的隧道,则可以选择弹性原位掘进方式,以减少施工对周围环境的干扰。
同时,还需要考虑施工成本和环境影响。
浅谈特长隧道光面爆破快速掘进施工
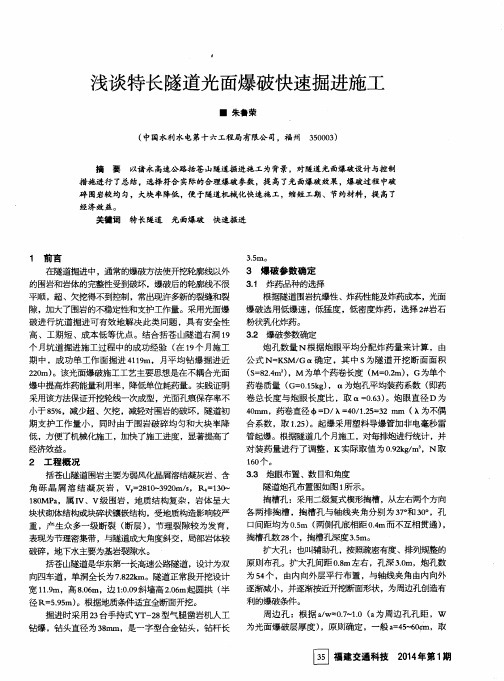
5 0 c m;w = 5 0 , , - 8 0 c m,取 6 0 c m。沿设计断面平行于轴线 布置 ,间距 0 . 5 m,孔深 3 . 0 m,炮孔数 4 8 个。
底孔 :按照间距 0 . 6 m水平布置两排 ,孔深 3 . 1 m, 炮孔数3 0 个。 3 . 4 装药量与装药结构 装药采用袋装的粉状乳化炸药 ,每循环爆破总装药
逐渐减小 ,并逐渐按近 开挖断面形状 ,为周边孔创造有 利的爆破条件。 周边孔 :根据 a / w = 0 . 7  ̄ 1 . 0( a 为周边孔孔距 ,w
向四车道 ,单洞全长为 7 . 8 2 2 k m。隧道正常段开挖设计 宽1 1 . 9 m,高 8 . 0 6 m,边 1 : 0 . 0 9 斜墙高 2 . 0 6 m起圆拱 ( 半
量 按 Q= K L S 式 来 计 算 Q= K L S = 0 . 9 2 x 3×8 2 . 4 = 2 2 7 . 4
( k ,其 中L为爆破掘进尺数 ,K为炸药单 耗量 ( k g / ), 取0 . 9 2 ,s Y j 隧道开挖断面面积。 单耗根据 类似经验确定 ,Ⅳ、V级 围岩周边 眼取 0 . 2 5 k g / m、断面 开挖取 0 . 5 ~ 1 . 9 4 k g / m3 。各孔 装药参 数 如表 1 所示,装药结构图见 图2 ,其中 d 1 、d 2 、d 3 、d 4 分别为掏槽孔 、扩大孔、周边孔 、底孔每段药卷长度 , l 1 、1 2 、1 3 为各孔孔深 ,1 4 为周边孔间隔长度 , 1 5 、l 6 分 别为周边孔、 掏槽孔、 底孔 、 扩大孔填塞炮泥长度 。 ( 1 ) 周边孔空气间隔装 药 : 将 3 2 药卷等间隔地 固 定在竹片上装入, 药卷之间用导爆管连接 , 由炮泥堵塞。 ( 2 )掏槽孔 、扩大孔和底孔不耦合连续装药 :将
浅埋隧道悬臂掘进机开挖施工工法

浅埋隧道悬臂掘进机开挖施工工法浅埋隧道悬臂掘进机开挖施工工法一、前言浅埋隧道悬臂掘进机开挖施工工法是一种适用于浅埋隧道的施工方法,通过使用悬臂式掘进机进行开挖,能够提高施工效率、保证施工质量,同时减少对周边环境和地质的影响。
二、工法特点1. 高效快速:悬臂式掘进机具有高效快速的特点,可大幅度提高开挖速度和产能。
2. 灵活适应:该工法适应于各种地质条件,能够进行曲线段和限高段的开挖。
3. 施工质量保证:悬臂式掘进机具有高度自动化的特点,能够保证施工质量的稳定和一致性。
三、适应范围浅埋隧道悬臂掘进机开挖施工工法适用于以下场景:1. 道路隧道:包括城市道路、高速公路等。
2. 铁路隧道:包括城市地铁、高速铁路等。
四、工艺原理浅埋隧道悬臂掘进机开挖施工工法的原理是通过悬臂式掘进机进行开挖。
悬臂式掘进机通过悬臂系统和推进系统相结合,实现了隧道的掘进和推进。
在实际工程中,根据地质条件和隧道设计要求,采取相应的技术措施,如控制推进速度、调整刀盘转速等,以保证施工进度和施工质量的要求。
五、施工工艺1. 初期准备:包括现场勘察、设计施工方案制定等。
2. 悬臂平台拆装:在隧道入口处安装悬臂平台,以支撑悬臂式掘进机的工作。
3. 掘进开挖:悬臂式掘进机在悬臂平台下进行开挖工作,按照隧道设计要求逐步推进。
4. 施工支护:推进过程中,根据地质情况和设计要求,进行隧道支护工作,确保施工安全和隧道稳定。
5. 施工结束:达到设计要求或者施工目标后,悬臂式掘进机进行回撤,并进行相关设备和材料的清理和归档。
六、劳动组织针对浅埋隧道悬臂掘进机开挖施工工法,需要合理组织施工人员的工作,包括施工队伍的组织和协调、施工人员的培训和指导、施工计划的制定和调整等。
七、机具设备1. 悬臂式掘进机:具有自动控制和高效快速开挖能力的专用设备。
2. 辅助设备:包括推进系统、刀盘系统、支护系统等,用于支持和辅助悬臂式掘进机的工作。
八、质量控制为了保证施工质量,需要采取一系列的质量控制措施,包括疏浚与清理、地质勘测与分析、隧道掘进和支护质量检验等,以确保施工过程中的质量符合设计要求。
隧道掘进施工方法

隧道掘进施工方法隧道掘进是指在地下挖掘运输通道的过程,它在交通、矿业和基础设施建设中发挥着重要的作用。
隧道的安全和高效施工是保证项目顺利进行的关键。
本文将介绍一些常见的隧道掘进施工方法,以及它们的优势和适用场景。
一、顶板法顶板法是隧道施工中最常用的一种方法。
它的基本原理是由上向下挖掘,首先开挖隧道的顶部,然后逐渐向下开挖底部。
这种方法适用于软土地层或岩石地层,对地质条件要求较低。
它的优势在于施工过程中比较稳定,能够有效地避免塌方和地面沉降的风险。
顶板法的施工步骤如下:1. 建立隧道入口和出口,并安装支护结构。
2. 使用爆破或机械装备来开挖顶部土层或岩石,形成一个初始开挖面。
3. 在隧道顶部、侧壁和底部安装支护结构,保证施工安全。
4. 逐渐向下进行挖掘,直到达到设计的隧道底部。
5. 完成隧道的整体支护和修整工作。
二、侧壁法侧壁法是另一种常见的隧道掘进方法。
它与顶板法相比,施工过程更加复杂,但能够适应更多的地质条件。
该方法通过从侧壁挖掘隧道,然后在侧壁上安装支护结构,最后挖掘底部完成隧道。
侧壁法的施工步骤如下:1. 建立隧道入口和出口,并安装支护结构。
2. 从侧壁开始挖掘,逐渐向底部延伸。
3. 挖掘过程中,及时安装支护结构,以保证施工安全。
4. 当达到设计的隧道底部时,完成整体支护和修整工作。
侧壁法的优势在于适用于各种复杂地质条件,例如高风压、高水压和不稳定的地层等。
然而,由于施工过程复杂,需要更高水平的技术和设备支持。
三、盾构法盾构法是一种相对先进的隧道掘进方法,适用于各种地质条件。
这种方法利用盾构机进行掘进,将隧道壁面一边挖掘一边进行支护。
盾构机由前部推进机构、刀盘和后部支承装置组成。
盾构法的施工步骤如下:1. 选取合适的盾构机,并进行预制准备工作。
2. 将盾构机放置在隧道入口,并启动机械设备。
3. 盾构机推进并同时进行地层的挖掘和支护。
4. 当到达隧道出口时,完成隧道的整体支护和修整工作。
盾构法的优势在于施工过程相对安全快速,对周围环境的干扰较小。
复杂地质下高速公路隧道施工技术浅析

关键词:复杂地质环境;高速公路;隧道;施工技术隧道工程已经成为高速公路工程建设中不可缺少的一部分,但是隧道施工过程中因为项目规模大、工期长、工序多、不可预见的因素多等特点,增加了隧道施工的安全隐患以及难度。
所以与一般工程项目相比,隧道工程施工风险很大,必须综合考虑,保证施工方案的合理性和安全性,引入先进的施工技术与工艺,提高隧道施工技术水平。
在本文中主要针对复杂地质环境下隧道施工技术进行研究,解决复杂地质环境对于隧道工程带来的影响,促进隧道工程的健康发展,切实提高我国隧道施工技术水平。
1隧道施工方法及其特点1.1隧道施工方法近年来,我国隧道施工技术伴随着高速公路工程建设的发展得到进一步提升,各种新的隧道施工技术不断涌现,对提高隧道施工技术水平起到了重要作用,而且每一种隧道施工技术都有其自身的特点,比如一些隧道施工技术的工期比较短、隧道施工技术的造价比较低,有的隧道施工技术安全性比较高等,可以根据隧道工程实际情况选择施工方法[1]。
同时,不同的隧道施工方法之间有着一定的联系,可以根据不同的隧道技术设计施工方案并从中选择经济性、安全性等比较好的方案。
1.2不同隧道施工技术的优缺点隧道工程中已经形成了比较完整的隧道施工方案体系,施工方法多种多样,常见的施工方法包括全断面法、台阶法以及分部开挖法三个大类,不同施工方法的综合比较见表1,对这三大类施工方法的优缺点进行了如下分析。
首先是全断面开挖法,是按照设计的隧道轮廓采取一次爆破形成的施工技术,在爆破后进行全方位支护然后再修建衬砌。
该施工方法需要达到I~IV级围岩,比如针对IV级围岩,围岩必须具备采取全断面开挖法时的初期到支护这一过程中能够保持稳定良好状态的条件,对施工安全很重要[2]。
同时,在隧道工程中有钻孔台车或者自制作业台架和高效率装运机械设备的条件下也可以采取该施工方法,但是需要注意的是在采用全断面施工方法时隧道的长度不宜太短,至少在1km以上,这是从经济性角度考虑的,因为大型机械设备施工需要投入大量的成本。
隧道常见的几种施工方法
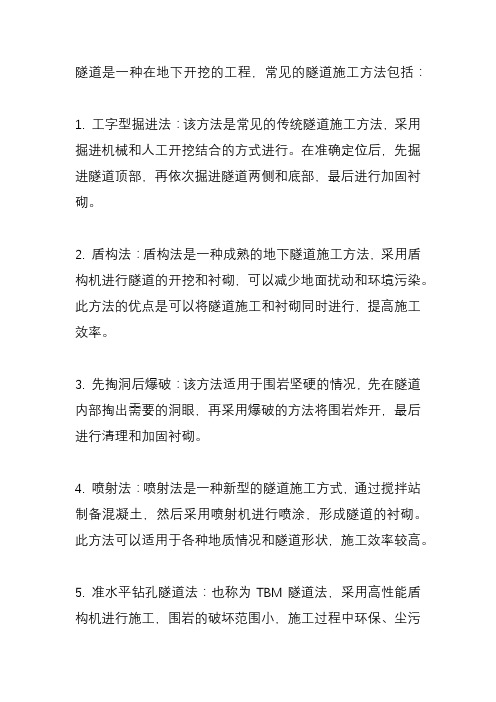
隧道是一种在地下开挖的工程,常见的隧道施工方法包括:
1. 工字型掘进法:该方法是常见的传统隧道施工方法,采用掘进机械和人工开挖结合的方式进行。
在准确定位后,先掘进隧道顶部,再依次掘进隧道两侧和底部,最后进行加固衬砌。
2. 盾构法:盾构法是一种成熟的地下隧道施工方法,采用盾构机进行隧道的开挖和衬砌,可以减少地面扰动和环境污染。
此方法的优点是可以将隧道施工和衬砌同时进行,提高施工效率。
3. 先掏洞后爆破:该方法适用于围岩坚硬的情况,先在隧道内部掏出需要的洞眼,再采用爆破的方法将围岩炸开,最后进行清理和加固衬砌。
4. 喷射法:喷射法是一种新型的隧道施工方式,通过搅拌站制备混凝土,然后采用喷射机进行喷涂,形成隧道的衬砌。
此方法可以适用于各种地质情况和隧道形状,施工效率较高。
5. 准水平钻孔隧道法:也称为TBM隧道法,采用高性能盾构机进行施工,围岩的破坏范围小,施工过程中环保、尘污
少、对周围环境影响小。
该方法适用于地质情况优良、软岩地层和地下水丰富的区域。
以上是常见的隧道施工方法,不同方法的选择会受到工程的具体条件、地质情况、资源和技术等多方面因素的影响。
隧道工程资料:掘进机施工法(TBM)的优点和缺点

隧道工程资料:掘进机施工法(TBM)的优点
和缺点
掘进机施工法(TBM)是一种利用回转刀具开挖(同时破碎和掘进)隧道的机械装置。
此法修筑隧道的方法称掘进机法。
(一)TBM施工方法的优点:施工速度快,工期得以缩短,特别是在稳定的围岩中长距离施工时,此特征尤其明显。
无爆破围岩的损伤小,减轻支护的工作量。
振动、噪声小,对周围的居民和结构物的影响小。
因机械化施工,安全,作业人员少。
安全性和作业环境有了较大的改善。
(二)TBM施工方法的缺点:费和运输、组装、解体等的费用高,初期投资高,不用于短隧道。
施工途中不易改变开挖直径和形状。
地质的适应性受到一定限制。
对软弱围岩,还存在不少问题;对硬岩,强度超过200MPa 后,刀具成本急剧增大,开挖速度也降低。
隧道工程中的掘进技术

隧道工程中的掘进技术随着城市建设的不断发展,隧道工程成为了现代化城市中不可或缺的一部分。
无论是地下通道、地铁、水利工程还是矿山开采等领域,掘进技术都扮演着重要的角色。
本文将介绍隧道工程中的掘进技术,探讨其应用和发展。
隧道工程的掘进技术主要是指通过机械、爆破或人工等方式将地下岩层进行开挖的过程。
其中最常用的方式是机械掘进。
机械掘进技术以其高效、安全、环保等优势而广泛应用于各个领域。
1. 机械掘进技术机械掘进技术主要通过推进机械(如盾构机、硬岩机)在地下钻探、爆破等方式下,将隧道内岩石土层进行连续挖掘和清理。
机械掘进技术的主要优点是高效快速,能够大幅度减少人力需求,提高施工质量和效率。
同时,机械掘进技术还能够减少对周围环境的影响,降低施工对地质环境的破坏程度。
2. 盾构机技术盾构机是机械掘进中最常用的一种机械设备,广泛应用于地下隧道的建设中。
其工作原理是通过推进盾构机,在隧道内壁上设置环形支撑结构,并同时进行挖掘和清理。
这种技术具有施工过程稳定可靠、安全风险低、效率高等优点。
盾构机采用轮式或履带行走模式,能够适应各种地质条件和施工环境,并且具有较强的承载能力。
它能够应对各种地下障碍物,如河流、铁路等的穿越,为城市交通建设和城市规划提供了有力保障。
3. 爆破技术除了机械掘进技术外,爆破技术也是隧道工程中常见的一种掘进方式。
爆破技术通过在隧道内进行定向爆破,炸碎岩石,然后进行清理和支护,从而完成隧道的开挖。
爆破技术的关键在于深入了解地下岩层的结构和特性,以及对爆破参数的合理控制。
合理的爆破能够提高施工效率,减少岩石碎屑的回填,降低支护工作量。
4. 掘进技术的挑战和发展隧道掘进技术的发展面临着一些挑战。
首先是对环境保护的要求越来越高。
隧道施工会产生大量的渣土、水泥浆等固体废弃物,如何合理处理和利用这些废弃物成为了一项难题。
其次,城市化进程使得隧道工程的施工场地空间越来越有限。
如何在有限的空间内高效进行掘进工作成为了一个需要解决的问题。
- 1、下载文档前请自行甄别文档内容的完整性,平台不提供额外的编辑、内容补充、找答案等附加服务。
- 2、"仅部分预览"的文档,不可在线预览部分如存在完整性等问题,可反馈申请退款(可完整预览的文档不适用该条件!)。
- 3、如文档侵犯您的权益,请联系客服反馈,我们会尽快为您处理(人工客服工作时间:9:00-18:30)。
1.悬臂式掘进机仅能截割巷道部分断面,要破碎全断面岩石,需多次上下左右连续移动截割头来完成工作 。可用于任何断面形状的隧道。 2.掘进速度受掘进机利用率影响很大,在最优条件下利用率可达60%左右,但若岩石需要支护或其它辅助 工作跟不上时,其利用率更低。
3.与全断面掘进机有一些相同的优点:连续开挖、无爆破震动、能更自由地决定支护岩石的适当时机;可 减少超挖;可节省岩石支护和衬砌的费用。 4.与全断面掘进机比较,悬臂式掘进机小巧,在隧道中有较大的灵活性,能用于任何支护类型。
矿岩的坚固性也是一种抵抗外力的性质,但它与矿岩的强度却是两种不同的概念。
强度是指矿岩抵抗压缩,拉伸,弯曲及剪切等单向作用的性能。而坚固性所抵抗的外力却是一种综合的外 力。(如抵抗锹,稿,机械碎破,炸药的综合作用力)。
隧道掘进成型方法
目前国内常用的隧道掘进方法有以下几种
盾构法
盾构法是暗挖法施工中的一种全机械化施工方法。它是将盾构机械在地中推进,通过盾构外壳和管片 支承四周围岩防止发生往隧道内的坍塌。同时在开挖面前方用切削装置进行土体开挖,通过出土机械运出 洞外,靠千斤顶在后部加压顶进,并拼装预制混凝土管片,形成隧道结构的一种机械化施工方法。
二氧化碳爆破法
二氧化碳气体在一定的高压下可转变为液态,通过高压泵将液态的二氧化碳压缩至圆柱体容器(爆破 筒)内,装入安全膜、破裂片、导热棒和密封圈,拧紧合金帽即完成了爆破前的准备工作。将爆破筒和起 爆器及电源线携至爆破现场,把爆破筒插入钻孔中固定好,连接起爆器电源。当微电流通过高导热棒时, 产生高温击穿安全膜,瞬间将液态二氧化碳气化,急剧膨胀产生高压冲击波致泄压阀自动打开,利用液态 二氧化碳吸热气化时体积急剧膨胀产生高压致使岩体开
在大多数的隧道施工案例中,钻爆法是比较常见的一种是施工方法。钻爆法开挖作业程序包括测量、钻孔 、装药、爆破、通风、出碴、锚杆、立架、挂网、喷锚等工序。
爆破的弊端
而在大型的隧道开采中,装药爆破环节是存在巨大的隐患.
隧道工程安全目标:杜绝因公死亡事故、杜绝严重塌方事故、杜绝爆炸事故、杜绝爆破物品丢失事故。— —《隧道工程安全管理办法》 在今开采过程中,有隧道面支护的步骤,但是架不住爆炸用量的不确定性。并且在城市隧道,或者靠山而 居的村落隧道中,爆破产生的巨大分贝,也是一种声音污染。
通常被破碎的岩石抗压强度很高,但抗拉强度低,静爆岩石分裂机以超高压油为能量源, 由液压动力站输出的超高压油又经增压器的机械放大后驱动分裂棒内的油缸产生巨大推动力, 使分裂机推动分裂棒中的液压顶向外伸出胀裂岩石,液压力瞬间超高压,达到几千吨的分裂 力,轻而易举的从岩石内部将坚硬岩石分裂,并使物体按预定方向分裂,达到胀裂破碎开挖的 目的。
5.与全断面掘进机相比,具有投资少、施工准备时间短和再利用性高等显著特点。
钻爆法
钻爆法,即是通过钻孔、装药、爆破开挖岩石的方法,简称钻爆法。这一方法从早期由人工手把钎、 锤击凿孔,用火雷管逐个引爆单个药包,发展到用凿岩台车或多臂钻车钻孔,应用毫秒爆破、预裂爆破及 光面爆破等爆破技术。施工前,要根据地质条件、断面大小、支护方式、工期要求以及施工设备、技术等 条件,选定掘进方式。 钻爆法的弊端
岩石分级
岩石级别 Ⅰ
(f=20)
Ⅱ (f=15)
Ⅲ (f=10)
坚固程度 最坚固 很坚固 坚固
代表性岩石 最坚固、致密、有韧性的石英岩、玄武岩和其他各种特别坚固的岩石
。 很坚固的花岗岩、石英斑岩、硅质片岩,较坚固的石英岩,最坚固的
砂岩和石灰岩. 致密的花岗岩,很坚固的砂岩和石灰岩,石英矿脉,坚固的砾岩,很
隧道掘进施工方法浅析
前言
公路是国民经济的重要命脉,由于其特有的灵活和优 越性,发挥着其他运输方式不可替代的作用。公路隧道是 公路工程结构的重要组成部分之一,随着我国社会主义市 场经济的发展,西部大开发战略的实施,高等级公路已从 沿海地区向西南、西北山岭区延伸,公路隧道建筑规模也 越来越大,原来的两车道隧道已远远不能满足日渐增长的 行车要求,隧道规模越大技术也相应复杂,因此,与过去 一般公路隧道在设计、施工和运营管理方面均有质的差 别,这带给我们公路隧道建设者的是机遇也是挑战,是学 习与提高的机会,同时它也挑战我们的观念、我们的技术 和管理水平。面临这些挑战,中国工程技术人员在总结自 己的经验,同时学习借鉴国外经验的基础上,也取得了很 多成绩,即在勘察设计、施工控制以及运营管理方面的水 平都有了不少成熟成果,现就山区公路大跨径隧道施工技 术方面关键环节作出几点论述。
优点
1、安全开挖和衬砌,掘进速度快; 2、盾构的推进、出土、拼装衬砌等全过程可实现自动化作业,施工劳动强度低。 3、不影响地面交通与设施,同时不影响地下管线等设施; 4、穿越河道时不影响航运,施工中不受季节、风雨等气候条件影响,施工中没有噪音和扰动; 5、在松软含水地层中修建埋深较大的长隧道往往具有技术和经济方面的优越性。
Ⅷ (f=0.6)
土状
腐殖土,泥煤,软砂质土壤,湿砂。
Ⅸ (f=0.5) 松散状
砂,山砾堆积,细砾石,松土,开采下来的煤.
Ⅹ (f=0.3)
流沙状
流沙,沼泽土壤,含水黄土及其他含水土壤.
f=xx表示矿岩的坚固性的量化指标.
人们在长期的实践中认识到,有些岩石不容易破坏,有一些则难于破碎。难于破碎的岩石一般也难于凿 岩,难于爆破,则它们的硬度也比较大,概括的说就是比较坚固。因此,人们就用岩石的坚固性这个概念 来表示岩石在破碎时的难易程度。
坚固的铁矿石.
Ⅲa (f=8) 坚 固 坚固的砂岩、石灰岩、大理岩、白云岩、黄铁矿,不坚固的花岗岩。
Ⅳ (f=6)
比较坚固
一般的砂岩、铁矿石
Ⅳa (f=5) 比较坚固
砂质页岩,页岩质砂岩。
Ⅴ (f=4)
中等坚固
坚固的泥质页岩,不坚固的砂岩和石灰岩,软砾石。
Ⅴa (f=3) 中等坚固
各种不坚固的页岩,致密的泥灰岩.
Ⅵ (f=2)
Ⅵa (f=1.5)
Ⅶ (f=1)
比较软 比较软
软
软弱页岩,很软的石灰岩,白垩,盐岩,石膏, 无烟煤,破碎的砂岩 和石质土壤.
碎石质土壤,破碎的页岩,粘结成块的砾石、碎石,坚固的煤,硬化 的粘土。
软致密粘土,较软的烟煤,坚固的冲击土层,粘土质土壤。
Ⅶa (f=0.8)
软
软砂质粘土、砾石,黄土。
施工方法对比
施工方法 盾构法
悬臂掘进法 钻爆法
二氧化碳爆破法 岩石分裂器分裂法
岩石锯切片法 岩石锯切片法Q
主机价格 高 高
中等 中等 中等
低 低
对员工依赖度 安全系数 使用成本
高
高高
高
高高
高
低低
高
中等 高
高
低高
高
中等 中等
低
低低
徐州启洋机械有限公司 2018/2/1
5、要求高:爆破筒装填工艺和现场施工均较复杂,对炮孔质量要求较高。 6、噪音及安全:爆破震动力虽不大,毕竟声响比较明显,若要在周边有居民楼及建筑物的使用,应尽量 先征求当地安监及环保是否允许。
岩石分裂机分裂法
岩石分裂机运用液压机械方式对岩石进行分裂,是针对坚硬岩石能高效裂碎的创新设备,在矿山开采 及建筑土石方工程中不能使用炸药的情况下破碎岩石具有很大的技术优势,淘汰了膨胀破碎剂。
优势
1、气体比炸药更有安全性,不属于民爆产品,运输、储存和使用不需要审批。
2、无需炸药审批的繁琐程序和公安部门的严格监管。
3、爆破过程中无破坏性震动和短波,扬尘比例降低,对周围环境影响不大。
4、复杂的作业环境均可使用,煤矿及矿山领域。
5、二氧化碳气易采购,部分装置可重复使用。
6、多个爆破筒可同时并联,爆破威力大,爆破后岩石个体大。
缺点
1、断面尺寸多变的区段适应能力差; 2、新型盾构购置费昂贵,对施工区段短的工程不太经济。 3、工人的工作环境较差。
悬臂式掘进机掘进法
悬臂式掘进机是一种能够实现截割、装载运输、自行走及喷雾除尘的联合机组。随着回采工作面综合 采煤机械化的快速发展,煤矿对巷道掘进速度要求越来越高。为了提高采准巷道的速度,悬臂式掘进机被 大力研制并逐步发展完善。
目前,掘进技术仍然会在钻爆破岩掘进、悬臂式掘进机、连续采煤机、掘锚联合机组以及全断面掘进 机五个方向持续发展。在全硬岩巷道的掘进中,钻爆破岩掘进在很长一段时间内仍会是一种主要方式,但 在一些重要领域,全断面掘进机会逐步取代钻爆破岩掘进;在硬度较低的全岩巷道和半煤岩巷道,悬臂式 掘进机会得到大力发展,逐步成为主要的掘进方式;在一些条件时宜的煤巷掘进中,掘进效率较高的连续 采煤及和掘锚联合机组将会得到推广应用。
岩石锯切片法
利用挖掘机等工程机械设备,附加液压岩石锯,对工作面进行松散切割,然后用破碎锤或 铣挖机进行剥离。这种施工方法优点是切割成本低、设备转场方便;缺点是岩石锯片普遍较 薄,母机的稳定性差时,很容易崩坏锯片。
岩石锯切片法-Q
我司最新研发的岩石切割锯控制系统,主要以挖掘机为载体可以实现单次移动母机切割范围达到宽度 3米、长度3.5米的切割范围,有效降低了锯片的事故率,降低人为干预切割、可大幅降低施工人员的劳动 强度。
盾构法特点
盾构法施工得到广泛使用,因其具有明显的优越性:①在盾构的掩护下进行开挖和衬砌作业,有足够 的施工安全性;②地下施工不影响地面交通,在河底下施工不影响河道通航;③施工操作不受气候条件的影 响;④产生的振动、噪声等环境危害较小;⑤对地面建筑物及地下管线的影响较小。
适用条件
在松软含水地层,或地下线路等设施埋深达到10m或更深时,可以采用盾构法。 1、线位上允许建造用于盾构进出洞和出碴进料的工作井 ; 2、隧道要有足够的埋深,覆土深度宜不小于6m且不小于盾构直径; 3、相对均质的地质条件 ; 4、如果是单洞则要有足够的线间距,洞与洞及洞与其它建(构)筑物之间所夹土(岩)体加固处理的最 小厚度为水平方向1.0m,竖直方向1.5m; 5、从经济角度讲,连续的施工长度不小于300m。