公差原则及形位公差选用
3、形位公差_3
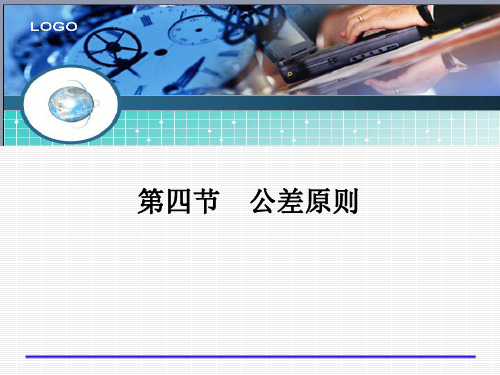
最大实体状态下 t≥0
最大实体实效边界 dfe ≤ dMV=dmax+t1 dmin ≤ da ≤ dmax
合格条件
习题:
如下图所示,若被测孔的形状正确。(1)测得其实际尺寸 为φ30.0lmm,而同轴度误差为φ0.03 mm,求该零件的最 大实体实效尺寸、体外作用尺寸。(2)若测得实际尺寸为 的φ30.02mm,同轴度误差为φ0.05 mm,问该零件是否合 格?为什么?(3)可允许的最大同轴度误差值是多少?
m
主参数L/D
一、形位公差标准
●
公差值:
一、形位公差标准
●
公差值
一、形位公差标准
●
未注形位公差值规定(GB/T1184-96)
对于形位公差要求不高,并且用一般的机械加工方
法和加工设备都能保证的加工精度,不必将形位公差在
图样上注出,未注不等于没有要求。
国标规定了三个等级:H、K、L
一、形位公差标准
第五节 形位公差的标准化与选用
一、形位公差标准
◆ 形位公差标准(GB/T1184-96)
●
圆度、圆柱度: 0,1,2,3…12 共13级 高 低 :共12级 1,2,3…12 共12级 高 低
●
一、形位公差标准
●
圆度、圆柱度公差值(部分摘录):
m
主参数d/D
一、形位公差标准
●
直线度、平面度公差值
(5)最小实体实效边界(LMVB) 尺寸的边界。
二、 独立原则(IP)
独立原则是指图样上给定的形位公差与尺寸公差相互 独立无关,分别满足要求的原则。 实际要素的尺寸由尺寸公差控制,与形位公差无关; 形位误差由形位公差控制,与尺寸公差无关。 独立原则主要用于尺寸精度和形位精度要求都较严, 且需要分别满足要求的情况。
形位公差标准(GB1184-80)
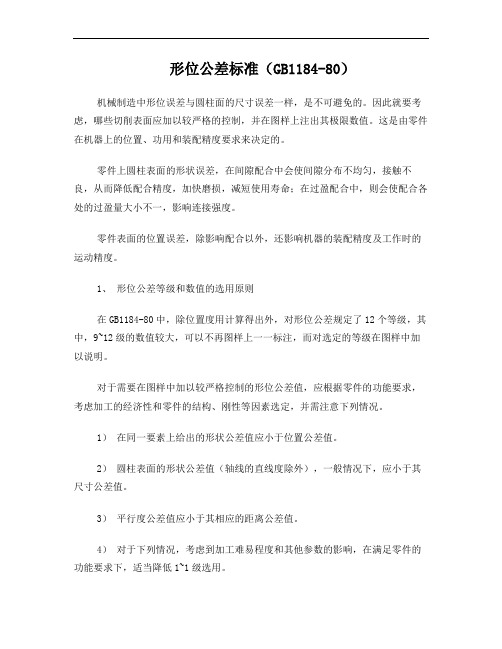
形位公差标准(GB1184-80)
机械制造中形位误差与圆柱面的尺寸误差一样,是不可避免的。
因此就要考虑,哪些切削表面应加以较严格的控制,并在图样上注出其极限数值。
这是由零件在机器上的位置、功用和装配精度要求来决定的。
零件上圆柱表面的形状误差,在间隙配合中会使间隙分布不均匀,接触不良,从而降低配合精度,加快磨损,减短使用寿命;在过盈配合中,则会使配合各处的过盈量大小不一,影响连接强度。
零件表面的位置误差,除影响配合以外,还影响机器的装配精度及工作时的运动精度。
1、形位公差等级和数值的选用原则
在GB1184-80中,除位置度用计算得出外,对形位公差规定了12个等级,其中,9~12级的数值较大,可以不再图样上一一标注,而对选定的等级在图样中加以说明。
对于需要在图样中加以较严格控制的形位公差值,应根据零件的功能要求,考虑加工的经济性和零件的结构、刚性等因素选定,并需注意下列情况。
1)在同一要素上给出的形状公差值应小于位置公差值。
2)圆柱表面的形状公差值(轴线的直线度除外),一般情况下,应小于其尺寸公差值。
3)平行度公差值应小于其相应的距离公差值。
4)对于下列情况,考虑到加工难易程度和其他参数的影响,在满足零件的功能要求下,适当降低1~1级选用。
A.细长比较大的轴和孔;
B.孔相对于轴;
C.距离较大的轴或孔;
D.宽度较大(一般大于1/2长度)的零件表面;E.线对线和线对面相对于面对面的平行度及垂直度。
2、形状公差标准
直线度、平面度
圆度、圆柱度
3、位置公差标准
平行度、垂直度、倾斜度
同轴度、对称度、圆跳动和全跳动。
形位公差的选择及未注形位公差值的规定

二、几何公差基准的选择
1、基准统一原则,即设计基准、定位基 准和装配基准为同一要素。
轴颈的圆柱度 和轴肩端面圆 跳动影响轴承 装配精度
设计、加工、 测量基准
几何公差基准的选择
2、选用三基面体系 时,应选对被测要 素影响最大或定位 最稳定的平面为第 一基准,依次选择 第二、第三基准。
三、公差原则的选择
公差原则
1
应用场合
示
例
独 立 原 则
尺寸 齿轮箱体孔的尺寸精度与 精度与几 两孔轴线的平行度;连杆活 何精度需 塞销孔的尺寸精度与圆柱度; 分别满足 滚动轴承内、外圈滚道的尺 要求
寸精度与形状的精度
公差原则的选择.1
公差原则
应用场合
示
例
独 立 原 则
滚筒类零件尺寸精度要求很 尺寸精 低,形状精度要求较高; 平板的形状精度要求很高, 度与几何 尺寸精度要求不高; 精度要求 冲模架的下模座尺寸精度要 相差较大 求不高,平行度要求较高; 通油孔的尺寸精度有一定要 求,形状精度无要求。
公差原则的选择.2
公差原则
应用场合
示
例
独 立 原 则
滚子链条套筒或滚子内、外 圆柱面的轴线同轴度与尺寸精度
尺寸精度 齿轮箱体孔的尺寸精度与孔 与几何精 轴线间的位置精度; 度无联系 发动机连杆上的尺寸精度与 孔轴线间的位置精度。
公差原则的选择.3
公差原则
应用场合
示
例
独 立 原 则
保证 导轨的形状精度要求严格,尺 运动精度 寸精度要求次高 保证 汽缸套的形状精度要求严格, 密封性 尺寸精度要求次高 凡未注尺寸公差与未注几何公 未注公差 差都采用独立原则,例如退刀槽 倒角、圆角等非功能要素
尺寸公差和形位公差关系的公差原则
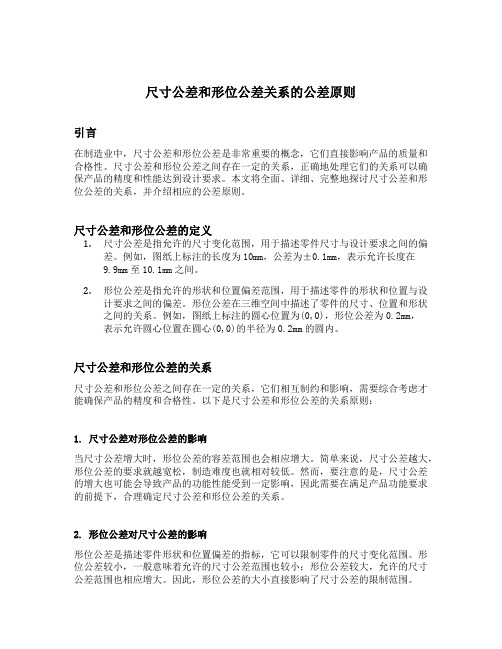
尺寸公差和形位公差关系的公差原则引言在制造业中,尺寸公差和形位公差是非常重要的概念,它们直接影响产品的质量和合格性。
尺寸公差和形位公差之间存在一定的关系,正确地处理它们的关系可以确保产品的精度和性能达到设计要求。
本文将全面、详细、完整地探讨尺寸公差和形位公差的关系,并介绍相应的公差原则。
尺寸公差和形位公差的定义1.尺寸公差是指允许的尺寸变化范围,用于描述零件尺寸与设计要求之间的偏差。
例如,图纸上标注的长度为10mm,公差为±0.1mm,表示允许长度在9.9mm至10.1mm之间。
2.形位公差是指允许的形状和位置偏差范围,用于描述零件的形状和位置与设计要求之间的偏差。
形位公差在三维空间中描述了零件的尺寸、位置和形状之间的关系。
例如,图纸上标注的圆心位置为(0,0),形位公差为0.2mm,表示允许圆心位置在圆心(0,0)的半径为0.2mm的圆内。
尺寸公差和形位公差的关系尺寸公差和形位公差之间存在一定的关系,它们相互制约和影响,需要综合考虑才能确保产品的精度和合格性。
以下是尺寸公差和形位公差的关系原则:1. 尺寸公差对形位公差的影响当尺寸公差增大时,形位公差的容差范围也会相应增大。
简单来说,尺寸公差越大,形位公差的要求就越宽松,制造难度也就相对较低。
然而,要注意的是,尺寸公差的增大也可能会导致产品的功能性能受到一定影响,因此需要在满足产品功能要求的前提下,合理确定尺寸公差和形位公差的关系。
2. 形位公差对尺寸公差的影响形位公差是描述零件形状和位置偏差的指标,它可以限制零件的尺寸变化范围。
形位公差较小,一般意味着允许的尺寸公差范围也较小;形位公差较大,允许的尺寸公差范围也相应增大。
因此,形位公差的大小直接影响了尺寸公差的限制范围。
3. 综合考虑尺寸公差和形位公差为了确保产品的质量和合格性,需要综合考虑尺寸公差和形位公差的关系。
在设计过程中,可以通过优化尺寸公差和形位公差的组合,来实现既满足产品功能要求,又提高零件的制造可行性和成本控制。
形位公差的公差原则
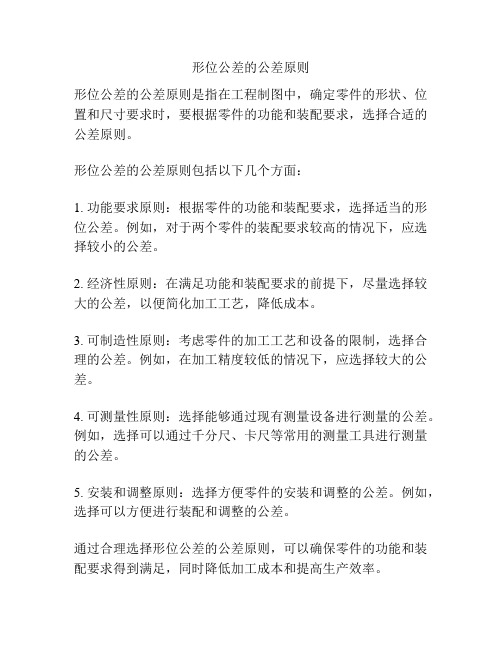
形位公差的公差原则
形位公差的公差原则是指在工程制图中,确定零件的形状、位置和尺寸要求时,要根据零件的功能和装配要求,选择合适的公差原则。
形位公差的公差原则包括以下几个方面:
1. 功能要求原则:根据零件的功能和装配要求,选择适当的形位公差。
例如,对于两个零件的装配要求较高的情况下,应选择较小的公差。
2. 经济性原则:在满足功能和装配要求的前提下,尽量选择较大的公差,以便简化加工工艺,降低成本。
3. 可制造性原则:考虑零件的加工工艺和设备的限制,选择合理的公差。
例如,在加工精度较低的情况下,应选择较大的公差。
4. 可测量性原则:选择能够通过现有测量设备进行测量的公差。
例如,选择可以通过千分尺、卡尺等常用的测量工具进行测量的公差。
5. 安装和调整原则:选择方便零件的安装和调整的公差。
例如,选择可以方便进行装配和调整的公差。
通过合理选择形位公差的公差原则,可以确保零件的功能和装配要求得到满足,同时降低加工成本和提高生产效率。
形位公差的标注及公差原则
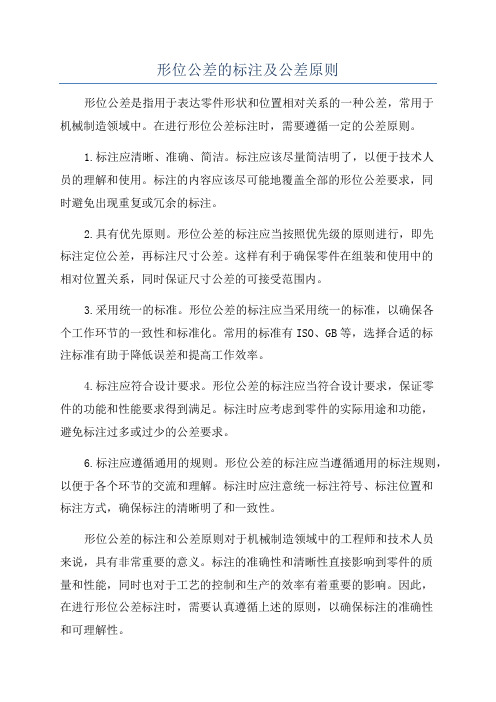
形位公差的标注及公差原则形位公差是指用于表达零件形状和位置相对关系的一种公差,常用于机械制造领域中。
在进行形位公差标注时,需要遵循一定的公差原则。
1.标注应清晰、准确、简洁。
标注应该尽量简洁明了,以便于技术人员的理解和使用。
标注的内容应该尽可能地覆盖全部的形位公差要求,同时避免出现重复或冗余的标注。
2.具有优先原则。
形位公差的标注应当按照优先级的原则进行,即先标注定位公差,再标注尺寸公差。
这样有利于确保零件在组装和使用中的相对位置关系,同时保证尺寸公差的可接受范围内。
3.采用统一的标准。
形位公差的标注应当采用统一的标准,以确保各个工作环节的一致性和标准化。
常用的标准有ISO、GB等,选择合适的标注标准有助于降低误差和提高工作效率。
4.标注应符合设计要求。
形位公差的标注应当符合设计要求,保证零件的功能和性能要求得到满足。
标注时应考虑到零件的实际用途和功能,避免标注过多或过少的公差要求。
6.标注应遵循通用的规则。
形位公差的标注应当遵循通用的标注规则,以便于各个环节的交流和理解。
标注时应注意统一标注符号、标注位置和标注方式,确保标注的清晰明了和一致性。
形位公差的标注和公差原则对于机械制造领域中的工程师和技术人员来说,具有非常重要的意义。
标注的准确性和清晰性直接影响到零件的质量和性能,同时也对于工艺的控制和生产的效率有着重要的影响。
因此,在进行形位公差标注时,需要认真遵循上述的原则,以确保标注的准确性和可理解性。
尺寸公差和形位公差关系的公差原则

尺寸公差和形位公差关系的公差原则尺寸公差和形位公差是机械制造中非常重要的两个概念,它们在保证产品质量、提高生产效率、降低成本等方面都起到了关键作用。
本文将从尺寸公差和形位公差的基本概念入手,深入探讨它们之间的关系,总结出尺寸公差和形位公差关系的公差原则。
一、尺寸公差和形位公差的基本概念1. 尺寸公差尺寸公差是指零件各个尺寸之间允许的最大偏离量。
通俗地说,就是指零件实际尺寸与设计要求之间的偏离量。
一般来说,尺寸公差包括上限偏差和下限偏差两种。
2. 形位公差形位公差是指零件各个特定点之间允许的最大偏移量或旋转角度。
通俗地说,就是指零件实际位置与设计要求之间的偏移量或旋转角度。
形位公差可以分为平面形位公差和轴向形位公差两种。
二、尺寸公差和形位公差的关系尺寸公差和形位公差在机械制造中都是非常重要的概念。
它们之间的关系可以从以下几个方面来分析。
1. 形位公差对尺寸公差的影响形位公差可以对零件的尺寸公差产生影响。
一般来说,如果一个零件的形位公差比较大,那么它所允许的偏移量或旋转角度也就比较大,这就会导致其尺寸公差变大。
因此,在进行机械制造时,需要根据设计要求合理设置形位公差,以保证零件的尺寸精度。
2. 尺寸公差对形位公差的影响尺寸公差也可以对零件的形位精度产生影响。
一般来说,如果一个零件的尺寸公差比较大,那么它所允许的偏移量或旋转角度也就比较大,这就会导致其形位精度变低。
因此,在进行机械制造时,需要根据设计要求合理设置尺寸公差,以保证零件的形位精度。
3. 尺寸和形位之间的综合考虑在进行机械制造时,需要综合考虑尺寸公差和形位公差,以确定最终的公差要求。
一般来说,如果一个零件的形位精度要求比较高,那么其尺寸公差就要比较小;反之,如果一个零件的形位精度要求比较低,那么其尺寸公差就可以适当放大。
因此,在进行机械制造时,需要根据具体情况灵活设置尺寸公差和形位公差。
三、尺寸公差和形位公差关系的公差原则根据以上分析,可以总结出以下几个原则:1. 形位精度要求高的零件应该设置较小的尺寸公差。
形位公差3(公差原则)

最大实体要求标注
Φ0.1 M Φ0.015 M AM
A 用于被测要素时 用于被测要素和基准要素时
最大实体要求的应用(被测要素)
应用:适用于中心要素。主要用于只要求可装配性的 零件,能充分利用图样上给出的公差,提高零件的合 格率。 边界:最大实体要求应用于被测要素,被测要素遵守 最大实体实效边界。即:体外作用尺寸不得超出最大 实体实效尺寸,其局部实际尺寸不得超出最大实体尺 寸和最小实体尺寸。 最大实体实效尺寸:MMVS=MMS±t t—被测要素的形位公差,“+”号用于轴,“-”号用于 孔。
零形位公差举例
如图所示孔的轴线对A的垂直度公差,采用最大实体要求的零形 位公差。该孔应满足下列要求: 实际尺寸在ø 49.92mm~ ø 50.13mm内; 实际轮廓不超出关联最大实体边界,即其关联体外作用尺寸不小 于最大实体尺寸D=49.92mm。 当该孔处在最大实体状态时,其轴应与基准A垂直;当该孔尺寸 偏离最大实体尺寸时,垂直度公差可获得补偿。当孔处于最小实 体尺寸时,垂直度公差可获得最大 补偿值0.21mm。 ø50+0.13 –0.08
-0.013 -0.028
图例
G
G基准平面
Φ0.01 G
90°
关联体外作用尺寸
B
体内作用尺寸
在被测要素的给定 长度上,与实际内 表面(孔)体内相 接的最小理想面, 或与实际外表面 (轴)体内相接的 最大理想面的直径 或宽度,称为体内 作用尺寸。
最大实体状态(尺寸、边界)
最大实体状态(MMC):实际要素在 给定长度上具有最大实体 最大实体时的状态。 最大实体 最大实体尺寸(MMS):实际要素在 最大实体状态下的极限尺寸。 (轴的最大极限尺寸dmax,孔的最小 极限尺寸Dmin) 边界:由设计给定的具有理想形状的 极限包容面。 最大实体边界:尺寸为最大实体尺寸 的边界。
- 1、下载文档前请自行甄别文档内容的完整性,平台不提供额外的编辑、内容补充、找答案等附加服务。
- 2、"仅部分预览"的文档,不可在线预览部分如存在完整性等问题,可反馈申请退款(可完整预览的文档不适用该条件!)。
- 3、如文档侵犯您的权益,请联系客服反馈,我们会尽快为您处理(人工客服工作时间:9:00-18:30)。
三、相关要求
• 定义——图样上给定的形位公差与尺寸公差相互
有关的公差要求。
(一)包容要求 1.定义:包容要求是要求实际要素应遵守其最大
实体边界(MMB),其局部实际尺寸不得超出最小 实体尺寸的一种公差要求。
2.标注方法:当采用包容要求时,应在被测要素
的尺寸极限偏差或公差带代号后加注“ E ”符号。
体外作用尺寸与最大实体实效尺寸的区别:
体外作用尺寸是由实际尺寸和形位误差综合形成 的,一批零件中各不相同,是一个变量,但就每 个实际的轴或孔而言,作用尺寸却是唯一的。 最大实体实效尺寸是由最大实体尺寸和形位公差 综合形成的,对一批零件而言是一定量。实效尺 寸可以视为作用尺寸的允许极限值。
4.理想边界
直线度/mm
19.7(dL)
0.4
0.4 0.3 0.2 0.1
20.1(dMV)
19.7(dL)
0.3 0.2 0.1 0
实际尺寸/mm
20(dM) 20.1(dMV)
4)实际尺寸必须在最大实体尺寸和最小实体尺寸之间。
第六节 形位公差的选择
1.形位公差项目的选择原则
1)选择时应尽量用综合控制的公差项目,以减少 形位公差项目。 2)确定公差项目必须与检测条件相结合,考虑现 有条件检测的可能性与经济性。
Dfe
Da1
Da2
Da3
da1
da2
da3
dfe
a) 实际轴
b) 实际孔
实际尺寸和体外作用尺寸
Dfi
dfi
3. 最大实体实效状态、尺寸
• (1) 最大实体实效状态(MMVC) 在给定长度上,实际轮廓要素处于最大实体状态 且其中心要素的形状或位置误差等于给出的形位 公差值时的综合极限状态。 • (2) 最大实体实效尺寸(DMV、dMV) 最大实体实效 状态下的体外作用尺寸。 dfe=da + f dMV =dM + t =dmax + t Dfe=Da-f DMV==DM–t =Dmin- t
• (1)理想边界 由设计给定的具有理想形 状的极限包容面。 • (2)最大实体边界(MMB) 尺寸为最大实 体尺寸的边界。 • (3)最大实体实效边界(MMVB) 尺寸为最 大实体实效尺寸的边界。
二、独立原则
1.定义 尺寸公差与形位公差单独保证,没有关联。 2.标注方法
0.02
0 20 -0.033
第五节 公差原则
定义:机械零件的同一被测要素既有尺寸公差要求,
又有形位公差要求,处理两者之间关系的原则,称 为公差原则。
一、有关术语及定义
1. 局部实际尺寸(简称实际尺寸da、Da)
2. 体外作用尺寸 体外作用尺寸(dfe、Dfe) 在被测要素的给定长 度上,与实际轴外接的最小理想孔或与实际孔内接 的最大理想轴的直径。对于关联要素,该理想孔 (或轴)的中心线(或轴线)必须与基准保持图样 给定的几何关系。 dfe=da+f Dfe=Da-f
19.97(dL)
标注
直线度/mm
0.03
0.02
0.03
0.01 0
20(dM)
19.97(dL) 20(dM)
实际尺寸/mm
最大实体边界
直线度误差的动态变动范围
包容要求
实际尺寸及允许的误差
被测要素实际尺寸 允许的直线度误差
20
0
19.99
19.98 19.97
0.01
1) 被测要素遵守最大实体实效边界,即被测要素的体 外作用尺寸不超过最大实体实效尺寸。
20(dM)
2) 被测要素的实际尺寸为最大实体尺寸时, 形位误差为图样上给定的形位公差值。
20.1(dMV)
0.1
3) 当被测要素的实际尺寸偏离最大实体尺寸时,其 偏离量可补偿给形位误差,允许的形位误差等于图样 上给定的形位公差值与偏离量之和。
2.形位公差等级(公差值)的选择
形位公差等级的选择原则与尺寸公差选用原则相 同,即在满足零件使用要求的前提下,尽量选用低的 公差等级。 (1) 形位公差和尺寸公差的关系 T形状<T位置<T尺寸 (2) 形状公差与表面粗糙度的关系 表面粗糙度的Ra值约占形状公差值的20%~25%。 (3) 凡有关标准已对形位公差作出规定的,应按相应 的标准确定。 如与滚动轴承相配的轴和壳主要用于尺寸精度和形位精度要求都较
严,且需要分别满足要求。
•包容要求:主要用于需严格保证配合性质的场合。 •最大实体要求:主要用于中心要素,保证可装配
性的场合。
0.02 0.03
(二)最大实体要求(MMR) 1.定义:最大实体要求是要求被测要素的实际
轮廓应遵守其最大实体实效边界(MMVB),当其 实际尺寸偏离最大实体尺寸时,允许其形位误差 值超出在最大实体状态下给出的公差值的一种公 差要求。
2.标注方法:
0.1 M 20h8
•最大实体要求的特点如下: