锅炉过热蒸汽温度控制系统设计
蒸汽锅炉PID温度控制系统设计

目旳:
对锅炉过热蒸汽温度控制系统进行分析和设计,而对 锅炉过热蒸汽旳良好控制是确保系统输出蒸汽温度稳 定旳前提。所以本设计采用串级控制系统,这么能够 极大地消除控制系统工作中旳多种干扰原因,使系统 能在一种较为良好旳状态下工作,同步锅炉过热器出 口蒸汽温度在允许旳范围内变化,并保护过热器管壁 温度不超出允许旳工作温度。
调整器接受过热器出口蒸汽温度t变化后,调整器才开始动作, 去控制减温水流量W ,W旳变化又要经过一段时间才干影响到 蒸汽温度t,这么既不能及早发觉扰动,又不能及时反应控制旳 效果,将使蒸汽温度t发生很大旳动态偏差,影响锅炉生产旳安 全和经济运营。
燃烧工况
温度设定值
控制信号
喷水流量
控制器
执行器
过热器
温度变送器
在本设计用到串级控制系统中,主对象为送入负荷设 备旳出口温度,副对象为减温器和过热器之间旳蒸汽 温度,经过控制减温水旳流量来实现控制过热蒸汽温 度旳目旳。
蒸汽锅炉工艺流程及控制要求
蒸汽锅炉工艺流程及控制要求
锅炉是一种具有多输入、多输出且变量之间相互关联 旳被控对象。 过热蒸汽温度控制系统:主要使过热器出口温度保持 在允许范围内,并确保管壁温度不超出工艺允许范围;
被控对象建模
根据在减温水量扰动时,过热蒸汽温度有较大旳容积迟延, 而减温器出口蒸汽温度却有明显旳导前作用,完全能够构成 以减温器出口蒸汽温度为副参数,过热蒸汽温度为主参数旳 串级控制系统
温度设定值
温度主调节器
副调节器
减温水流量
蒸汽流量或者烟
扰动
气热量扰动
阀 门
减温器 2
过热蒸汽温度
过热器 1
温度变送器 温度变送器
火电厂锅炉过热汽温控制系统优化设计仿真

tional GPC —P algorithm. It simplifies the process of secondary controller design and meets the system contr ol re- quirements over the entire operating conditions.
第35卷 第6期
文 章 编 号 :1006—9348(2018)06—0095—06
计 算 机 仿 真
2018年6月
火 电厂 锅 炉 过 热汽 温 控 制 系统 优 化 设 计 仿 真
寅n旭 阳 ,支0 斌
(1.武 汉 科 技 大 学 信 息 科 学 与 工 程 学 院 ,湖 北 武 汉 430081; 2.武汉科技 大学教育部冶金 自动化与检 测技术 工程研 究中心 ,湖北 武汉 430081) 摘要 :针对过热汽温控制系统具有 大惯性 、大时滞特性 且模 型参数 随负荷变化较 大 ,传统控 制算法难 以获得 良好控 制性能 , 提出 了 1GPC—Qr'r串级控制算法 。改进 的广义预测 自校正控制作 为主控 制器来 抑制超 调 ,克服系统大时滞特性 ,定量 反馈 理论作为副控制器 ,对导前 区不确 定性 与干扰进行 抑制 ,并设 计了一种简便 的定 量反馈理论 控制器设 计方法。通过 与传 统 广义预测 一比例控制 的仿 真结果对 比,提 出的算法 可使 系统获得较好 的跟踪性 与鲁棒性 ,简化 了副控 制器的设计过 程 ,满足 了系统在全工况下运行 的控制要求 。 关键词 :过热 汽温控 制 ;定 量反馈理论 ;改进 的广义 预测控 制;定 量反馈理论 控制器设计的简便 方法 中 图 分 类 号 :TP273 文 献 标 识 码 :B
锅炉安全控制技术——过热蒸汽温度安全控制

锅炉安全控制技术——过热蒸汽温度安全控制现代锅炉的过热器在高温高压条件下工作。
过热器出口温度是全厂工质温度的最高点,也是金属壁温的最高处,在过热器正常运行时已接近材料允许的最高温度。
如果过热蒸汽温度过高,容易烧坏过热器,也会引起汽轮机内部零件过热,影响安全运行;温度过低则会降低全厂热效率,所以电厂锅炉一般要求过热蒸汽温度偏差保持在±5℃以内。
过热蒸汽温度自动控制系统是锅炉控制中的难点。
目前,很多实际系统并没有达到控制指标的要求。
其主要原因有下述两方面。
(1)扰动因素多变化大表18—1列出了各种扰动因素对过热蒸汽温度的静态影响关系。
(2)控制通道滞后大控制过热蒸汽温度的手段总是调节减温水量。
控制通道的动特性与减温器的安装位置有关。
假若能将减温器装于过热器的出口,显然控制通道的滞后要小得多。
但是这样的工艺流程对过热器的安全是不利的。
为了保护过热器不超温,工艺上总是将减温器安装在过热器的人口,这将带来控制对象较大的滞后。
过热蒸汽控制对象特性可用一阶加线滞后来近似。
线滞后r和时间常数丁的大小还与减温器的形式有很大关系。
表面式减温器的滞后较大,,约为60s,T约为130s;混合式减温器滞后较小,t约为30s,T约为100s。
过热蒸汽温度安全控制系统的基本方案见图18—15和图18—16。
图18—15的方案是两个温度的串级控制。
设计该方案的前提是减温器到过热器之间有预留孔,允许安装测温元件测取θ2。
图18—16方案用减温水流量作副回路。
由于锅炉进水系统往往合用一根总管,然后分两路:一路作为锅炉汽包的进水;另一路是减温水,这就造成锅炉液位控制系统和过热蒸汽温度系统的严重关联。
而设置这种流量副回路可大大削弱这种关联的影响。
烟道气温度日,往往是该温度系统的重要扰动,在这里通过设置前馈控制减少它的影响。
需要指出的是,由于不同的工艺情况,过热蒸汽温度被控过程的难控程度具有极大差异。
假若减温器采用混合器,而且在减温器出口又允许安装测温元件,对这种情况只要采用图18—15方案,即能得到很满意的控制效果。
锅炉过热蒸汽温度控制系统设计研究毕业设计开题报告
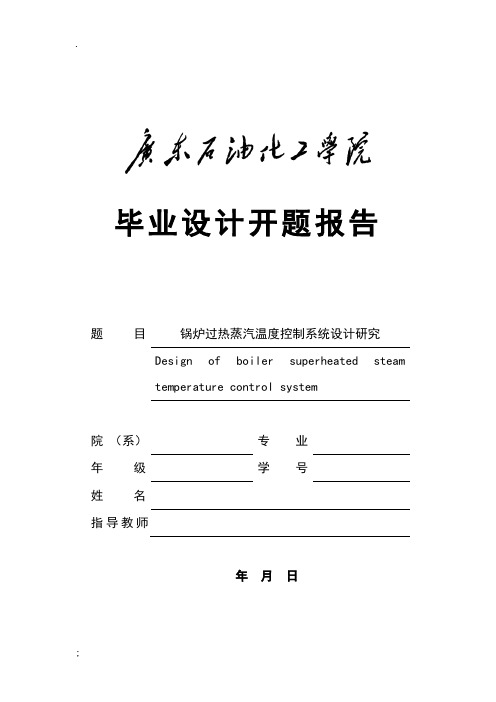
重点解决的问题
主要内容:
1、建立被控对象数学模型。
2、基于单片机设计总体方案,进行PID控制规律的选用与数字化。
3、硬件设计,包括单片机输入信号接口电路、外围电路等。
4、软件设计,包括初始化及主程序、控制程序、A/D和D/A转换程序及其他处理程序。
5利用PROTUES仿真。
重点解决的问题:
锅炉是我国工业生产和生活上应用面最广、数量最多的热力设备,是石油化工、发电等工业过程必不可少的重要动力设备,其产物蒸汽不但可以作为蒸馏、干燥、反应、加热等过程的热源,而且还可以作为驱动设备的动力源。
过热蒸汽温度控制是锅炉控制系统不可缺少的重要组成部分,其性能和可靠性已成为保证锅炉安全性和经济性的重要因素。由于锅炉往往负荷变化大,起停频繁,依靠人工操作很难保证其安全、稳定地在经济工况下长期运行。温度过高,会使蒸汽带水过多,汽水分离差,使后续的过热器管壁结垢,影响了生产安全;温度过低又将破坏部分水冷壁的水循环不能满足工艺要求,严重时会发生锅炉爆炸,从而造成重大事故。因此,工业过程对锅炉控制系统都有很高的要求,在锅炉运行中,保证过热蒸汽的温度在正常的范围内具有非常重要的意义。
完成论文的初稿;
修改、完善毕业设计并送指导老师审阅;
完成论文的PPT文件,准备毕业答辩。
指
导
教
师
意
见
***同学查阅了大量与课题相关的文献资料,对设计意图和课题意义清
楚明确,设计了初步的研究方案,预见了难点和关键问题,并拟定了工作计划,
为开题做了充分准备。目前已达到开题要求,同意开题。
指导教师签名:
年 月 日
1、了解锅炉过热蒸汽的工艺过程,对被控对象进行分析,设计控制方案。
火电厂锅炉温度控制系统设计

火电厂锅炉温度控制系统设计课程设计任务书学生姓名专业班级指导教师工作单位题目火电厂锅炉温度控制系统设计初始条件锅炉温度的控制效果直接影响着产品的质量温度低于或高于要求时要么不能达到生产质量指标有时甚至会发生生产事故采用双交叉燃烧控制以锅炉炉膛温度为主控参数燃料和空气并列为副被控变量设计火电厂锅炉温度控制系统以达到精度在℃范围内要求完成的主要任务包括课程设计工作量及其技术要求以及说明书撰写等具体要求1选择控制方案2绘制锅炉温度控制系统方案图3确定系统传感与变送器的选择数据采集系统控制电路等4说明系统工作原理时间安排1月21日选题理解课题任务要求1月22日方案设计1月2324日参数计算撰写说明书1月25日答辩指导教师签名 2008 年 1 月 9 日系主任或责任教师签名 2008 年 1 月 12 日目录1绪论 12锅炉的工艺流程及控制要求 221锅炉的工艺流程222锅炉的控制要求33锅炉炉膛温度的动态特性分析 34方案设计541炉膛温度控制的理论数学模型 542炉膛温度控制方法的选择 543 系统单元元件的选择 6com测变送器的选择 6com测变送器的选择8com副控制器正反作用的选择10com的PID调节器和副回路的PI调节器10com仪表的选择10com的选择125控制系统的工作原理 146设计心得157参考文献161绪论工程控制是工业自动化的重要分支几十年来工业过程控制获得了惊人的发展无论是在大规模的结构复杂的工业生产过程中还是在传统工业过程改造中过程控制技术对于提高产品质量以及能源的节约都起着重要的作用生产过程是指物料经过若干加工步骤而成为产品的过程该过程中通常会发生物理化学反应生化反应物质能量的转换与传递等等或者说生产过程表现为物流过变化的过程伴随物流变化的信息包括物流性质的信息和操作条件的信息生产过程的总目标应该是在可能获得的原料和能源条件下以最经济的途径将原物料加工成预期的合格产品为了打到目标必须对生产过程进行监视和控制因此过程控制的任务是在了解生产过程的工艺流程和动静态特性的基础上应用理论对系统进行分析与综合以生产过程中物流变化信息量作为被控量选用适宜的技术手段实现生产过程的控制目标生产过程总目标具体表现为生产过程的安全性稳定性和经济性1安全性在整个生产过程中确保人身和设备的安全是最重要和最基本的要求在过程控制系统中采用越限报警事故报警和连锁保护等措施来保证生产过程的安全性另外在线故障预测与诊断容错控制等可以进一步提高生产过程的安全性2稳定性指系统抑制外部干扰保持生产过程运行稳定的能力变化的工业运行环境原料成分的变化能源系统的波动等均有可能影响生产过程的稳定运行在外部干扰下过程控制系统应该使生产过程参数与状态产生的变化尽可能小以消除或者减少外部干扰可能造成的不良影响3经济性在满足以上两个基本要求的基础上低成本高效益是过程控制的另外一个重要目标为了打到这个目标不进需要对过程控制系统进行优化设计还需要管控一体化即一经济效益为目标的整体优化工业过程控制可以分为连续过程工业离散过程工业和间隙过程工业其中连续过程工业占的比重最大涉及石油化工冶金电力轻工纺织医药建材食品等工业部门连续过程工业的发展对我国国民经济意义最大过程控制主要指的就是连续过程工业的过程控制锅炉是工业生产中不可缺少的动力设备它多产生的蒸汽不仅能够为蒸馏化学反应干燥蒸发等过程提供热源而且还可以作为风机压缩机泵类驱动透平的动力源随着石油化学工业规模的不断扩大生产过程不断强化生产设备不断革新作为全厂动力和热源的锅炉亦向着大容量高参数高效率的方向发展为确保安全稳定生产对过路设备的自动控制就显得尤为重要2锅炉的工艺流程及控制要求21锅炉的工艺流程由于锅炉设备使用的燃料燃烧设备炉体形式锅炉功用和运行要求的不同锅炉有各种各样的流程常见流程如图21所示由图可知蒸汽发生系统由给水泵给水调节阀省煤器汽包及循环管组成燃料和热空气按照一定的比例进入燃烧室燃烧产生的热量传递给蒸汽发生系统产生饱和蒸汽然后经过热器形成一定汽温的过热蒸汽汇集至蒸汽母管压力为的过热蒸汽经负荷设备调节阀供给生产负荷使用与此同时燃烧过程中产生的烟气将饱和蒸汽变成过热蒸汽后经省煤器预热锅炉给水和空气预热器预热空气最后经引风机送往烟囱排入大气22锅炉的控制要求根据生产负荷的不同需要锅炉需要提供不同规格压力和温度的蒸汽同时根据安全性和经济性的要求是锅炉安全运行和完全燃烧锅炉设备的主要控制要求如下1供给蒸汽量适应负荷变化需要或者保持给定负荷2锅炉供给用汽设备的蒸汽压力应当保持在一定的范围内3 过热蒸汽温度保持在一定范围4汽包水位保持在一定范围5保持锅炉燃烧的经济性和安全性6 炉膛负压保持在一定的范围内根据上述要求锅炉设备的主要控制系统见表21表21 锅炉设备的主要控制系统控制系统被控变量操纵变量控制目的锅炉给水控制系统锅炉汽包水位给水流量锅炉内产生的蒸汽和给水的无聊平衡过路燃烧控制系统蒸汽压力烟气成分炉膛负压燃料流量送风流量引风流量蒸汽负荷的平衡燃烧的完全和经济性锅炉运行的安全性过热蒸汽控制系统过热蒸汽温度喷水流量过热蒸汽的温度和安全性3锅炉炉膛温度的动态特性分析火电厂的锅炉炉膛由于采用的燃料为煤粉在燃烧过程中炉膛和汽包之间的传热过程是一个相当复杂的过程炉膛的温度的动态特性具有一般的大滞后时变非线性和不对称性等特点在过程控制中为了方便设计同时又在一定的要求范围内我们通常把锅炉炉膛的温度的动态特性看作是一个线性的系统可以用以下传递函数描述具有时滞的一阶环节具有时滞的二阶环节在现场环境中炉膛内的温度变化是时时刻刻的很难用一个固定的数学公式将炉温的变化规律总结出来但是我们要对炉膛内的温度进行控制就必须要对炉膛内的温度变化进行一个规律的总结所以在规定的要求范围内对一些情况进行近似处理是很合理和必要的在通常情况下我们给定炉膛一个温度值作为系统的给定使锅炉炉膛在这个给定的温度状态下工作这个温度的变化又是和炉内的燃料燃烧量和炉体的总散热量相关的对于火电厂锅炉来说炉体的容量结构检测元件及其安放位置等都影响着滞后的大小它不是一个单一的问题是一个系统问题容积滞后时间就是级联的各个惯性环节的时间常数之和纯滞后产生的根源也要从整个测量系统来考虑并且与温度的高低有关热量从热源传到温度传感器要经过多个热阻与热容相串联的热惯性环节而串联的多容对象会产生等效纯时滞后随着温度的升高辐射传热的比例增大辐射具有穿透性使传热路径缩短传热速度加快所以纯滞后的时间会随温度升高而减小由于火电厂锅炉使用的燃料是煤粉即锅炉能量的来源方式是通过化学燃料的燃烧获得能量的同时炉膛内能量的散发形式又是以炉膛的炉体热量散失对汽包进行热量传导进行散失等多种途径进行的所以炉膛内的温度的变化是一个相当复杂的过程是一个非线性变化的过程从模型参数上看在锅炉炉膛的整个温度调节范围内对象的增益容积滞后时间和纯滞后时间通常是与工作温度与负载变化有关的变参数而且参数变化量与温度变化量之间是非线性关系由于锅炉炉膛内的温度是高温段的在高温段温度变化的纯滞后时间和过程增益将比低温段有显著减少而时间常数则显著增大锅炉作为一种高负荷运转的设备特别是火电厂内的锅炉长期处于高负荷运转下随着运行时间的变化其各项性能都会逐渐发生变化特别是随着使用时间的增长炉子的保温隔热材料会逐渐老化炉膛内部由于长期处于高温环境中炉体的保温密封性能变差通过炉体向外散失的热量增大此外锅炉初次使用和久停后再用时由于绝热保温材料中的水分大炉膛温度的特性差别也是很大的另外随着季节的变换锅炉运行的外部环境温度也是经常变化的冬天外部环境相对较冷炉体的散热较快夏天气温炎热炉体的散热相对会较慢如此种种因素都会引起炉膛温度特性的变化但变化的速度十分缓慢而不明显火电厂锅炉炉膛温度具有大惯性大滞后特性在炉膛的整个温度范围内对象的增益容积滞后时间纯滞后时间都是与工作温度有关的变参数从传热原理可知这些参数也与负荷变化有关在锅炉设计的工作温区在工作点附近的小范围内其动特性接近于线性较容易控制用常规的PID调节器也能控制得很好但不能经受太大的扰动也不能够大范围地跟踪变化较快的给定信号对于常规仪表大范围地改变温度要靠手动仅当温度接近给定值时方可投入自动根据以上分析可以认为火电厂锅炉炉膛温度是一种具有大容积滞后和大纯滞后的对象在整个炉膛的温区内其动态参数随锅炉的工作温度变化在工作点附近的小温度范围内炉膛的动态特性近似线性的4方案设计41炉膛温度控制的理论数学模型根据以上分析可知炉膛温度问题是比较复杂的对炉膛温度动态特性进行分段线性化则在每个较小的温度区间锅炉炉膛的燃料流量炉膛温度系统的动态特性可近似地用一个惯性环节和一个纯滞后环节串联的简化模型来表征即1其中K为过程的增益为过程的纯滞后时间To为过程的等效容积滞后时间在锅炉炉膛的整个温度范围内对象的增益容积滞后时间和纯滞后时间都是炉膛温度和负载的非线性函数K随锅炉炉膛内温度升高而减小To随锅炉炉膛内的温度升高而增大机理建模和计算机仿真分析以及实验辨识等也证明了这一模型的可行性42炉膛温度控制方法的选择双交叉燃烧控制是以锅炉炉膛温度为主被控量燃料和空气并列为副被控变量的串级控制系统其中两个并列的副环具有逻辑比值功能使该控制系统在稳定工作的情况下保证空气和燃料的最佳比值也能在动态过程中尽量维持空气燃料在最佳比值附近因此具有良好的经济效益和社会效益在煤粉流量调节回路中炉温PID的输出A1与根据实测空气流量折算成需要的煤粉流量之后分别乘以一个偏置系数K3得到信号A2乘以一个偏置系数K4得到信号A3A1A2A3三者经过高低选择器比较选中者作为煤粉流量PID的设定值空气流量调节回路中炉温PID的输出B1与根据实测煤粉流量折算成所须空气流量之后分别乘上一个偏置系数K1得到信号B2乘上偏置系数K2得到信号B3B1B2B3三者经高低选择器比较选中者乘上流量补偿系数送到空气PID作为设定值其系统组成原理图如图41所示43 系统单元元件的选择com测变送器的选择在本次设计中选用热电阻温度变送器它的量程单元的原理图如图42图42热电偶温度变送器量程单元原理图热电偶温度变送器与各种测温热电偶配合使用可将温度信号线性地转换成为4~20mADC电流信号或1~5VDC电压信号输出它是由量程单元和放大单元两部分组成的热电偶温度变送器的主要特点是采用非线性负反馈回路来实现线性变化这个特殊的性质反馈回路能按照热电偶温度-毫伏信号间的非线性关系调整反馈电压以保证输入温度t与整机输出或间的线性关系由图可见热电偶温度变送器的量程单元由信号输入回路A零点调整及冷端补偿回路B以及非线性反馈回路C等部分组成输入信号为热电偶产生的热电势输入回路中限流电阻和限压稳压管为安全火花防爆元件电阻还与电容组成低通滤波器零点调整量程调整电路的工作原理与直流毫伏变送器大致相仿所不同的是在热电偶温度变送器的输入回路中增加了由铜电阻等元件组成的热电偶冷端温度补偿电路同时把调零电位器移动到了反馈回路的支路上在反馈回路中增加了运算放大器等组成的线性化电路起线性化作用由于锅炉炉膛内的温度值较高所以选用的热电偶变送器的温度测量值必须达到要求这里我选用的是DBW-1150型热电偶温度变送器DBW-1150型热电偶温度变送器是DDZ-III系列仪表的主要品种本温度变送器用热电偶作为测温元件将被测温度线性地转换成标准信号1-5VDC或4-20mADC 输出供给指示记录凋节器计算机等自动化监控系统技术参数◆输入标准热电偶◆输出输出电流4~20mADC输出电压1~5VDC输出电阻250Ω允许负载变化范围100Ω◆量程0~1600℃◆冷端补偿误差≤1℃◆温度漂移≤01×基本误差1℃◆绝缘电阻电源输入与输出端子间≤100MΩ◆绝缘强度电源输入输山端子间1500VAC分钟◆工作条件环境温度0~50℃相对湿度≤90RH◆电源电压24VDC±5◆功耗<2W◆防爆等级 ib IICT6◆重量<2Kg com测变送器的选择由于流量变送的对象是煤粉和热空气所以在选择流量变送装置的时候必须是能够检测气体流量和和粉末混合气体的流量的另外由于空气是热空气所以还要求变送装置能够在一定的高温下工作所以这里选用的流量变送器为LUGB型涡街流量计LUGB型涡街流量计根据卡门karman涡街原理测量气体蒸汽或液体的体积流量标况的体积流量或质量流量的体积流量计广泛用于各种行业气体液体蒸汽流量的计量也可测量含有微小颗料杂质的混浊液体并可作为流量变送器用于自动化控制系统中LUGB型涡街流量传感器防爆型符合GB3836-2000《爆炸性环境用防爆电气设备》有关规定防爆标志为ExiaIICT6该仪表适用于工厂C级T6组及其以下的爆炸场所在本次设计中选用LUGB型涡街流量传感器其精度等级完全可以满足火电厂锅炉温度控制系统的精度要求产品特点◆可测量蒸汽气体液体的体积流量和质量流量◆无机械运动部件测量精度高结构紧凑维护方便◆压力损失小量程范围宽量程比达10-40倍◆采用消扰电路和抗振传感头仪表具有抗环境振动性能◆可测介质温度达350℃450℃技术参数◆公称口径 DN10~DN500◆测量介质气体液体蒸气◆可测介质温度 -40℃~150℃-40℃~280℃-40℃~350℃-40℃~450℃◆公称压力 25MPa 25 MPa协商供货◆精度等级 1级05级注05级量程范围≥17◆输出信号①电压脉冲低电平≤1V高电平≥6V脉冲宽04ms负载电阻 150Ω② 420mA转换精度±05满度值负载电阻19V350Ω24V500Ω30V750Ω③现场液晶显示瞬时流量6位显示m3h或kghth转换精度±01累计流量8位显示m3kgt转换精度±01◆供电电源①电压脉冲输出12VDC或24VDC② 420mA输出19VDC30VDC③现场液晶显示电池供电36V1节1号锂电池使用寿命大于3年外部供电12VDC或24VDC可实现带背光的液晶显示订货注明环境温度①电压脉冲输出-30℃65℃② 420mA输出-10℃55℃③现场液晶显示 -25℃55℃◆防爆标志 ExiaIIBT6◆表体材料 1Cr18Ni9Ti 其它材料协议供货 45号钢法兰连接型◆全智能型仪表①输出信号标态的体积流量或质量流量②现场液晶显示循环显示6位瞬时流量压力温度8位显示累积量com副控制器正反作用的选择副控制器的正反作用要根据副回路的具体情况决定而与主回路无关副环可以按照单回路控制系统确定正反作用的方法来确定副控制器的正反作用主控制器的正反作用根据主回路所包括的各环节来确定副回路的放大倍数可视为正因变送器一般为正这样主控制器的正负特性与主对象的正负特性一致本设计中主控制器和副控制器都要反作用com的PID调节器和副回路的PI调节器因为主回路是一个定制系统主控制器起着定制控制作用保持主变量的稳定是首要任务主控制器必须有积分作用在这里采用的是PID调节器它综合了比例控制积分控制和微分控制三种规律的优点又克服了各自的缺点比例部分能够迅速响应控制作用积分部分则最终消除稳态偏差微分部分可以稳定调节精度因为副回路是一个随动系统其给定值随主控制器输出的变化而变化同时两个并列的副环具有逻辑比值关系其变化是双交叉的为了能快速跟踪同时比例调节应该采用PI调节com仪表的选择采用模拟控制器DDZ-III型调节器DDZ―Ⅲ基型控制器框图如图43由控制单元和指示单元两部分组成控制单元包括输入电路比例积分微分电路手动电路保持电路指示单元有两种因此基型控制器也分两种即全刻度指示控制器和偏差指示控制器控制器的输入信号为1~5V的测量信号设定信号有内设定和外设定两种内设定信号为1~5V外设定信号为4~20mA测量信号和设定信号通过输入电路进行减法运算输出偏差到比例积分微分电路进行比例积分微分运算后由输出电路转换为4~20mA信号输出手动电路和保持电路附于比例积分微分电路之中手动电路可实现软手动和硬手动两种操作当处于软手动状态时用手指按下软手动操作键使控制器输出积分式上升或下降当手指离开操作键时控制器的输出值保持在手指离开前瞬间的数值上当控制器处于硬手动状态时移动硬手动操作杆能使控制器的输出快速改变到需要的数值只要操作杆不动就保持这一数值不变由于有保持电路使自动与软手动相互切换硬手动只能切换到软手动都是无平衡无扰动切换只有软手动和自动切换到硬手动需要事先平衡才能实现无扰动切换如果是全刻度指示控制器测量信号的指示电路和设定信号的指示电路分别把1~5V电压信号转化为1~5mA电流信号用双针指示器分别指示测量信号和设定信号当控制器出现故障需要把控制器从壳体中取出检查时可以把便携式手动操作器插入手动操作插孔以实现手动操作图43中的4~20mA输出信号通过精密电阻转化为1~5V电压反馈到控制器的输入端使控制器形成了自闭系统提高了控制器的运算精度根据火电厂生产设计要求采用WHSPL型调节器技术参数◆调节器输入通道5路信号标准4-20mA1-5VDC或0-10 mA0-25VDC◆调节器输出通道1路信号标准4-20mA或0-10 mA◆跟踪输入通道1路信号标准1-5VDCDDZ-III型或0-25VDCDDZ-II型◆模拟输入通道的输入阻抗为250Ω◆故障接点输出1路晶体管集电极开路输出◆手自接点输入1路无电压开关接点接点容量05A手动ON自动OFF◆电源220±10AC02A◆每个通道都可以用拨码开关设定为是否进行开方运算阻尼时间可通过面板修改◆PID参数范围 1给定值-691069 2比例带007999 3积分时间00999分 4微分时间00999分 5采样周期200毫秒◆安装方式表盘安装仪表自带悬挂装置◆仪表外尺寸80×160×260mm com的选择按所用能源形式的不同执行器分为电动气动和液动三类本设计主要是采用气动执行器为了安全考虑采用气开式它由气动执行机构和控制机构两部分组成气动执行机构又分为薄膜式和活塞式它们都是以压缩空气为能源具有控制性好结构简单动作可靠维修方便防活防爆和价廉等优点并可以方便地与气动仪表配套使用气动执行器也称为气动调节阀介绍典型产品气动薄膜调节阀地结构和工作原理气动薄膜调节阀的结构可以分为两部分上面是执行机构下面是调节机构从所学的知识可以了解到它主要由膜片弹簧推杆阀芯阀座等零部件组成当来自控制器的信号压力通入到薄膜气室时在膜片上产生一个推力并推动推杆部件向下移动使阀芯和阀座之间的空隙减小流体受到的阻力增大流量减小推杆下移的同时弹簧受压产生反作用力直到弹簧的反作用力与信号压力在膜片上产生的推力相平衡为止此时阀芯与阀座之间的流通面积不再改变流体的流量稳定可见调节阀是根据信号压力的大小通过改变阀芯的行程来改变阀的阻力大小达到控制流量的目的为了满足火电厂的安全生产要求在此次设计中使用VBD气动端面密封蝶阀VBD气动端面密封蝶阀是一种重量轻结构简单的后座式端面密封蝶阀阀体阀板均用钢板焊接或铸造加工而成适用于低压状态的空气或其他气体的流量压力控制本产品符合GBT4213-92标准技术参数◆型式扁平式焊接或铸造阀体◆公称通径 125~2000mm5〃~80〃◆公称压力PN025061016MPa JIS2K JIS5KJIS10K ANSI 150◆连接型式法兰式125~2000mm8〃~80〃密封面型式RF◆材料 25SUS304SUS316高温耐热钢Ni25Mo等◆标准型适用-5~200℃公称通径DN550以下◆外部轴承型公称通径DN600以上公称通径DN550以下温度200~600℃◆压盖形式螺栓压紧式◆填料聚四氟乙烯聚四氟乙烯石棉常温用柔性石墨中温高温用阀内组件◆额定行程全开60°或全开90°◆阀板材料 25SUS304SUS316等◆旋转轴材料SUS630SUS304SUS316◆阀体阀板密封形式端面密封型执行机构◆型式气缸活塞执行机构◆供气压力500kPa◆气源接口G18"G14"G38"G12"◆环境温度0~+70℃◆阀作用型式根据执行机构与旋转轴之间键连接位置不同可实现阀的气关式或气开式◆阀门安装方式阀杆应水平地安装在配管上若安装方式发生变化请予以注明附件◆定位器空气过滤减压器保位阀行程开关阀位传送器手轮机构等5控制系统的工作原理目前在火力发电厂中锅炉炉膛温度的控制虽然已经普遍采用了计算机控制但最常用的控制方法仍是普通PID控制包括单回路串级回路和分程控制等都是由PID作为基本的控制算法在此次设计中我们采用串级回路控制方法串级调节系统多用于燃料源受频繁扰动的锅炉炉膛该系统由主回路和副回路组成主回路根据实际值与给定值的偏差由PID调节规律对燃料流量进行调节副回路根据燃料流量实际值与主回路温度调节器输出的燃料流量的偏差对流量进行调节以避免扰动对燃料流量的影响在系统稳定状态时温度PID的输出以A1送到煤粉流量调节回路PID作为设定值以B1送到空气流量调节回路PID作为设定值在负荷剧增温测温给时温度PID的输出剧增对于空气流量调节回路随着B1开始增加时B1 B2低选器选中B1空气流量增加当B1正跳变到B1 B2时低选器选中B2B1被中断同时B3 B2高选器选B2B2作为该回路PID的设定值使空气流。
锅炉过热蒸汽温度控制系统的设计与仿真

低(5~IO) ̄C,效率就降低约 1%,因此严格 控制过热汽温在给定值 间 r约为 20s,具有较 良好的动态特性。但实际运行 中,蒸汽负荷
附近是大型火电机组运行 的重要任务之一[1J。
是变化的,因此不宜用来控制过热汽温 。
过热蒸汽温度控制 中,被控对象具 有非 线性 、时变性 、滞后 2-2 烟气传 热量扰 动的动态 特性
monitored control system is developed by Kingview.Th e results show that t he FUZZY-PID con troller not only improves the
system of nonlinear,time variability and ce , 桫 processing capacity,but also has better se L adaptive ca pa city a nd
第 4期 2016年 4月
机 械 设 计 与 制 造
Machinery Design & Manufacture
265
锅 炉过 热 蒸 汽 温度控 制 系统 的设 计 与仿 真
刘丽桑 ,张锦 枫
(福建工程学院 福建省数字化装备重点实验室 ,福建 福州 350118)
摘 要 :过热蒸汽温度 的高低直接影响着火电机组的安全性和经济性 。由于过 热蒸汽温度对象具有非线性 、时变等复杂 特 性 ,设 计了一种采用模糊 PID控制策略 的串级控制方案 ,分析 了锅炉过热蒸汽温度在 不同扰动作 用下的动 态特 性 ,设 计 了 FUZZY—PID控制 器,对 PID控制器参数进行 了整定,并对 FUZZY-PID控制器和常规控制器的控制效果进行 了仿真 比较 ,最后利用组态王 Kingview开发 了相应的过热蒸汽温度监控 系统。结果表明 ,FUZZY—PID自适应能力强 ,提高 了系 统对非线性、时变性和不确定性等的处理能力,改善 了控 制效果 ,具有更好的动态特性。 关键词 :过热蒸汽 ;温度控制;FUZZY-PID;串级控制 ;Kingview 中图分类号 :TH16;TP368.1;TK3 文献标识码 :A 文章编 号:1001—3997(2016)04—0265—03
锅炉蒸汽温度自动控制系统——模糊控制

锅炉蒸汽温度自动控制系统摘要:电厂实现热力过程自动化,能使机组安全、可靠、经济地运行。
锅炉是火力发电厂最重要的生产设备,过热蒸汽温度是锅炉运行质量的重要指标之一,过热蒸汽温度控制是锅炉控制系统中的重要环节。
在实现过程控制中,由于电站锅炉系统的被控对象具有大延迟,大滞后、非线性、时变、多变量耦合的复杂特性,无法建立准确的数学模型,对这类系统采用常规PID控制难以获得令人满意的控制效果。
在这种情况下,先进的现代控制理论和控制方法已经越来越多地应用在锅炉汽温控制系统。
本文以电厂锅炉汽温系统为研究对象,对其进行了计算机控制系统的改造。
考虑到锅炉汽温系统的被控对象特点,本文分别采用了常规PID控制器和模糊-PID控制器,对两种控制系统对比研究,同时进一步分析了一般模糊-PID控制器的控制特点,在此基础之上给出了一种改进算法,通过在线调整参数,实现模糊-自调整比例常数PID控制。
在此算法中,比例常数随着偏差大小而变化,有效地解决了在小偏差范围内,一般的模糊-PID控制器无法实现的静态无偏差的问题,提高了蒸汽温度控制系统的控制精度。
关键词:锅炉蒸汽温度模糊控制随着我国经济的高速发展,对重要能源“电”的要求快速增长,大容量发电机组的投入运行以及超高压远距离和赢流输电的混和电网的建设,以三峡电网为中心的全国性电力系统的形成,电力系统的不断扩大,对其自动控制技术水平的要求也越来越高。
同时,地方性的自备热电厂亦有长足发展,随着新建及改造工程的进行,其生产过程自动控制与时俱进,小容量机组“麻雀虽小,五脏俱全”,自备热电厂其自身特点:自供电、与主电网的关系疏及相互影响小,供热及采暖季节性等,可以提供更多的应用、尝试新技术、新产品的机会和可能性。
这样做的重要目标是提高和保证电力,热力及牛产过程的安全可靠、经济高效。
为了适应发展并实现上述目标,必须采取最新的技术和控制手段对电力系统的各种运铲状态和设备进行有效的自动控制。
火力发电厂在我国电力工业中占有主要地位,是我国重点能源工业之一。
锅炉过热蒸汽温度控制系统课程设计
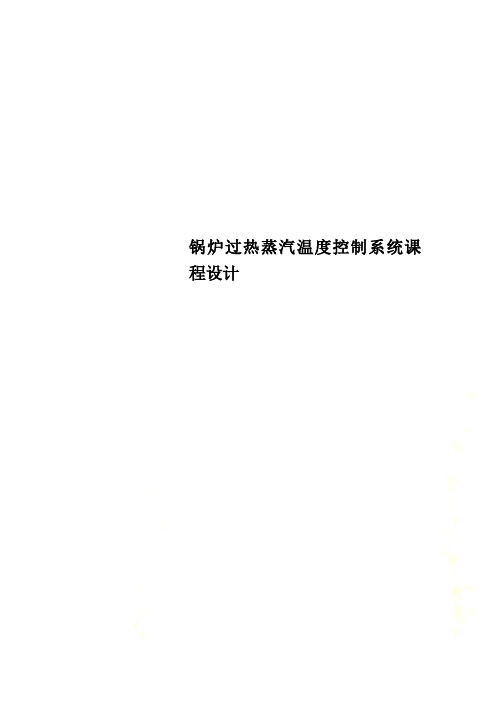
锅炉过热蒸汽温度控制系统课程设计过程控制课程设计说明书——锅炉过热蒸汽温度控制系统院系:化工学院化工机械系班级:10自动化(1)姓名:李正智学号:1 0 2 0 3 0 1 0 1 6日期:2013/12/2-2013/12/15指导老师:王淑钦老师引言蒸汽温度是锅炉安全、高效、经济运行的主要参数,因此对蒸汽温度控制要求严格。
过高的蒸汽温度会造成过热器、蒸汽管道及汽轮机因过大的热应力变形而毁坏;蒸汽温度过低,又会引起热效率降低,影响经济运行。
锅炉控制现场环境恶劣,采用传统的基于模拟技术的控制器、仪器仪表或单片机,不仅结构比较复杂,效率比较低,并且可靠性也不高。
本次课程设计的主要目的是锅炉蒸汽温度控制系统的设计。
蒸汽过热系统包括一级过热器、减温器、二级过热器。
锅炉汽温控制系统主要包括过热蒸汽和再热蒸汽温度的调节。
主蒸汽温度与再热蒸汽温度的稳定对机组的安全经济运行是非常重要的。
过热蒸汽温度控制的任务是维持过热器出口蒸汽温度在允许的范围之内,并保护过热器,使其管壁温度不超过允许的工作温度。
过热蒸汽温度是锅炉汽水系统中的温度最高点,过热蒸汽温度过高或过低,对锅炉运行及蒸汽设备是不利的。
蒸汽温度过高会使过热器管壁金属强度下降,以至烧坏过热器的高温段,严重影响安全。
一般规定过热器的温度与规定值的暂时偏差不超过±10℃,长期偏差不超过±5℃【1】。
如果过热蒸汽温度偏低,则会降低电厂的工作效率,同时使汽轮机后几级的蒸汽湿度增加,引起叶片磨损。
据估计,温度每降低5℃,热经济性将下降约1%;且汽温偏低会使汽轮机尾部蒸汽温度升高,甚至使之带水,严重影响汽轮机的安全运行。
一般规定过热汽温下限不低于其额定值10℃。
通常,高参数电厂都要求保持过热汽温在540℃的范围内。
由于汽温对象的复杂性,给汽温控制带来许多的困难,其主要难点表现在以下三个方面:(1)影响汽温变化的因素很多,例如,蒸汽负荷、减温水量、烟气侧的过剩空气系数和火焰中心位置、燃料成分等都可能引起汽温变化。
- 1、下载文档前请自行甄别文档内容的完整性,平台不提供额外的编辑、内容补充、找答案等附加服务。
- 2、"仅部分预览"的文档,不可在线预览部分如存在完整性等问题,可反馈申请退款(可完整预览的文档不适用该条件!)。
- 3、如文档侵犯您的权益,请联系客服反馈,我们会尽快为您处理(人工客服工作时间:9:00-18:30)。
锅炉过热蒸汽温度控制系统设计一、摘要这次课程设计任务是对锅炉过热蒸汽温度控制系统进行设计与分析。
在控制系统的设计与分析中,分别对串级控制系统和单回路控制系统进行了分析与阐述,通过分析比较发现,采用串级控制系统控制效果更好,可以使系统更能适应不通环境,从而达到更好的控制效果。
通过使用该控制系统,可以使锅炉过热器出口蒸汽温度在允许的范围内变化,并保证过热器壁温度不超过工作允许的温度,使其能够正常工作。
二、锅炉设备的介绍及设计任务的分析1、锅炉设备介绍锅炉是石油化工、发电等工业过程必不可少的重要动力设备,它所产生的高压蒸汽既可作为驱动透平的动力源,又可作为精馏、干燥、反应、加热等过程的热源。
随着工业生产规模的不断扩大,作为动力和热源的过滤,也向着大容量、高参数、高效率的方向发展。
锅炉设备根据用途、燃料性质、压力高低等有多种类型和名称,工艺流程多种多样,常用的锅炉设备的蒸汽发生系统是由给水泵、给水控制阀、省煤器、汽包及循环管等组成。
燃料与空气按照一定比例送入锅炉燃烧室燃烧,生成的热量传递给蒸汽发生系统,产生饱和蒸汽,形成一点观其文的过热蒸汽,在汇集到蒸汽母管。
过热蒸汽经负荷设备控制,供给负荷设备用,于此同时,燃烧过程中产生的烟气,除将饱和蒸汽变成过热蒸汽外,还经省煤器预热锅炉给水和空气预热器预热空气,最后经引风送往烟囱,排入大气。
过热蒸汽送负荷设备热空气汽包炉膛烟气排出冷空气送入水送入热空气送往炉膛过热器减温器空气预热器图1锅炉设备主要工艺流程图锅炉设备的控制任务是根据生产负荷的需要,供应一定压力或温度的蒸汽,同时要使锅炉在安全、经济的条件下运行。
为达到这些控制要求,锅炉设备将有多个不同的控制系统,如下:锅炉汽包水位控制系统,要求保证汽包水位平稳;锅炉过热蒸汽温度控制系统,要求保证过热蒸汽温度稳定;锅炉蒸汽出口压力控制系统,要求保证蒸汽出口压力保持在一定范围内,同时实现逻辑提量和逻辑减量;锅炉蒸汽出口压力控制系统,要求保证蒸汽出口压力保持在一定范围内,同时实现燃烧过程的经济运行;锅炉炉膛负压控制系统,要求保证炉膛负压在一定范围内,以保证锅炉的安全运行。
锅炉安全连锁控制系统,以防止回火和脱火。
本设计根据任务要求主要对锅炉过热蒸汽温度控制系统进行设计与分析。
2、任务分析与设计思路锅炉过热蒸汽温度控制系统则是锅炉系统安全正常运行,确保蒸汽质量的重要部分。
这个设计我们的任务是锅炉过热蒸汽温度控制系统的设计与分析。
蒸汽过热系统包括一级过热器、减温器、二级过热器。
控制任务是使过热器出口温度维持在允许范围内,并保护过热器时管壁温度不超过允许的工作温度。
我们知道,过热蒸汽温度过高或过低,对锅炉运行及蒸汽用户设备都是不利的,所以必须把过热器出口蒸汽的温度控制在规定范围内。
在锅炉生产过程中,过热蒸汽温度是整个汽水通道中最高的温度。
过热器温度过高将导至过热器损坏,同时还会危及汽轮机的安全运行。
影响过热蒸汽温度的因素很多,其中主要的有:过热器是一个多容且延迟较大的惯性环节,设备结构设计与控制要求存在若矛盾,各种扰动因素之闻相互影响。
而对各种不同的扰动,过热蒸汽温度的动态特性也各不相同。
因此,过热蒸汽温度控制的主要任务就是:(1) 克服各种干扰因素,将过热器出口蒸汽温度维持在规定允许的范围内,从而保持蒸气质量合格:(2) 保护过热器管壁温度不超过允许的工作温度。
本设计主要以控制减温水流量的变化来设计对过热蒸汽温度的自动调节。
三、控制原理简介及设计方案的确定随着生产的发展以及工艺的革新,对操作条件要求更加严格,变量间的相互关系也更加复杂了。
为了适应生产发展的需要,且基于控制理论的发展,越来越多的智能控制技术,如自适应控制、模型预测控制、模糊控制、神经网络等,被引入到锅炉过热蒸汽温度控制中。
但这些控制技术主要是为了改善和提高控制系统的控制品质,并没有从引起过热蒸汽温度波动的源头入手。
通常,烟气温度过高是引起过热蒸汽温度过高的主要原因。
一般,过热蒸汽温度在烟气扰动下延迟较小,而在减温水量扰动下延迟较大,这种特性将使过热蒸汽温度的控制滞后。
因此,本设计基于解决减温水扰动下保证过热器出口蒸汽温度的稳定的问题。
1、控制方案选择(1)单回路控制方案在系统运行过程中,改变减温水流量,实际上是改变过热器出口蒸汽的热焙,亦改变进口蒸汽温度,如下图所示:M减温器调节器减温水图2锅炉过热蒸汽单回路控制系统从动态特性上看,这种调节方法是最不理想的,但由于设备简单,因此,应用得最多。
减温器有表面式和喷水式两种。
减温器应尽可能地安装在靠近蒸汽出口处,但一定要考虑过热器材科的安全问题,这样能够获得较好的动态特性。
但作为控制对象的过热器,由于管壁金属的热容量比较大,使之有较大的热惯性。
加上管道较长有一定的传递滞后,如果用上图所示的控制系统,调节器接受过热器出口蒸汽温度t 变化后,调节器才开始动作,去控制减温水流量F 的变化又要经过一段时向才能影响到蒸汽温度t 这样,既不能及早发现扰动,又不能及时反映控制的效果,将使蒸汽温度t 发生不能允许的动态偏差。
影响锅炉生产的安全和经济运行。
实际中过热蒸汽控制系统常采用减温水流量作为操纵变量,但由于控制通道的时间常数及纯滞后均较大,组成单回路控制系统往往不能满足生产的要求。
因此常采用串级控制系统,减温器出口温度为副参数,以提高对过热蒸汽温度的控制质量。
(2)串级控制方案过热器出口蒸汽温度串级控制系统的方框图如下图所示。
采用两级调节器,这两级调节器串在一起,各有其特殊任务,调节阀直接受调节器1的控制,而调节器1的给定值受到调节器2的控制,形成了特有的双闭环系统,由副调节器调节器和减温器出口温度形成的闭环称为副环。
由主调节器和主信号—出口蒸汽温度,形成的闭环称为主环,可见副环是串在主环之中。
M减温器调节器2减温水调节器1温度变送器温度变送器图3锅炉过热蒸汽温度串级控制系统调节器2称主调节器,调节器1称为副调节器。
将过热器出口蒸汽温度调节器的输出信号,不是用来控制调节阀而是用来改变调节器2的给定值,起着最后校正作用。
串级系统是一个双回路系统,实质上是把两个调节器串接起来,通过它们的协调工作,使一个被控量准确地保持为给定值。
通常串级系统副环的对象惯性小,工作频率高,而主环惯性大,工作频率低。
为了提高系统的控制性能,希望主副环的工作频率相差三倍以上,以免频率相近时发生共振现象面破坏正常工作。
串级控制系统可以看作一个闭合的副回路代替了原来的一部分对象,起了改善对象特征的作用。
除了克服落在副环内的扰动外,还提高了系统的工作频率,加快过渡过程。
串级控制由于副环的存在,改善了对象的特性,使等效副对象的时间常数减小,系统的工作频率提高。
同时,由于串级系统具有主、副两只控制器,使控制器的总放大倍数增大,系统的抗干扰能力增强,因此,一般来说串级控制系统的控制质量要比单回路控制系统高。
在炉温过热蒸汽温度控制系统中,为了获得更好的控制精度,所以采用串级控制系统以得到良好的控制特性。
2、串级控制方案论证串级控制是随着工业的发展,新工艺不断出现,生产过程日趋强化,对产品质量要求越来越高,简单控制系统已不能满足工艺要求的情况下产生的。
主调节器副调节器调节阀副对象主对象副变送器主变送器给定副参数主参数二次扰动一次扰动--图4串级控制系统方框图由上图可知,主控制器的输出即副控制器的给定,而副控制器的输出直接送往控制阀。
主控制器的给定值是由工艺规定的,是一个定制,因此,主环是一个定值控制系统;而副控制器的给定值是由主控制器的输出提供的,它随主控制器输出变化而变化,因此,副环是一个随动控制系统。
串级控制系统中,两个控制器串联工作,以主控制器为主导,保证主变量稳定为目的,两个控制器协调一致,互相配合。
若干扰来自副环,副控制器首先进行“粗调”,主控制器再进一步进行“细调”。
因此控制质量优于简单控制系统。
串级控制有以下优点① 迅速克服进入副回路扰动的影响,使进入串级副环的扰动减少到相当于单回路进入副环的1/(1+Gc2*Gv*Gp2*Gm2)倍,同时使余差减小到相当于单回路的Kc2/(1+Kc2*Kv*Kp2Km2)倍;② 改善了对象特性提高了工作频率,使Tp2缩小为1/(1+Kc2*Kv*Kp2*Km2),等效对象时间常熟缩小,使控制过程时间加快。
③ 对负荷变化和操作条件的改变有一定的自适应能,副回路等效放大倍数Ko2'=(kc ,由于Kc2*Kv*Ko2*Km2>1,因此,Ko2的变化对等效对象放大倍数Ko2'来说是很小的。
一般来说,一个设计合理的串级控制系统,当干扰从副回路进入时,其最大偏差将会较小到控制系统的1001~101,即便是干扰从主回路进入,最大偏差也会缩小到单回路控制系统的51~31。
但是,如果串级控制系统设计得不合理,其优越性就不能够充分体现。
因此,串级控制系统的设计合理性十分重要。
四、控制系统详细设计图5串级控制系统框图本部分根据串级控制系统框图,确定各环节的参数及控制阀控制器的类型1、被控变量与操纵变量的选择(1)主被控变量的选择主被控变量y1是串级控制系统中要保持平稳控制的主要被控变量。
串级控制系统主被控变量选择应遵循以下原则:①尽量选择能直接反映产品质量的变量作为主被控变量;②所选的主被控变量能满足生产工艺稳定、安全、高效的要求;③控制通道的Ko 尽量大,тo/To 应尽量小;④过程的To/Tf 应尽量小扰动进入系统的位置应尽量远离主被控变量。
综合以上原则,应选择过热器出口蒸汽温度即送入负荷设备的出口蒸汽温度作为主变量。
直接反应控制目的。
(2)副被控变量的选择副被控变量y2是串级控制系统的辅助被控变量,是副回路的设计质量是保证发挥串级系统优点的关键。
副变量的选择应遵循以下原则:Gm1(s) Gc1(s) Gc2(s)Gf2(s) Gf1(s) Gp2(s) Gp1(s) Gv(s) Gm2(s)① 应尽量包含生产过程中主要的、变化剧烈、频繁的和幅度大的扰动,并力求包含尽可能多的扰动;② 应使主、副对象的时间常数匹配;③ 应考虑工艺上的合理性、可能性和经济型。
综合以上原则,选择减温器和过热器之间的蒸汽温度作为副被控变量。
(3)操纵变量的选择工业过程的输入变量有两类:控制变量和扰动变量。
其中,干扰时客观存在的,它是影响系统平稳操作的因素,而操纵变量是克服干扰的影响,使控制系统重新稳定运行的因素。
操纵变量的基本原则为:① 操纵变量必须是工艺上允许调节的变量;②选择对所选定的被控变量影响较大的输入变量作为操纵变量,即Ko 尽量大;③选择对被控变量有较快响应的操纵变量,即过程的тo/To 应尽量小; ④过程的To/Tf 应尽量小,使过程的Kf*F 尽量小;⑤工艺的合理性和与动态响应的快速性相结合。