304不饱和聚酯树脂大生产工艺
不饱和聚酯树脂生产工艺的危险、有害因素分析
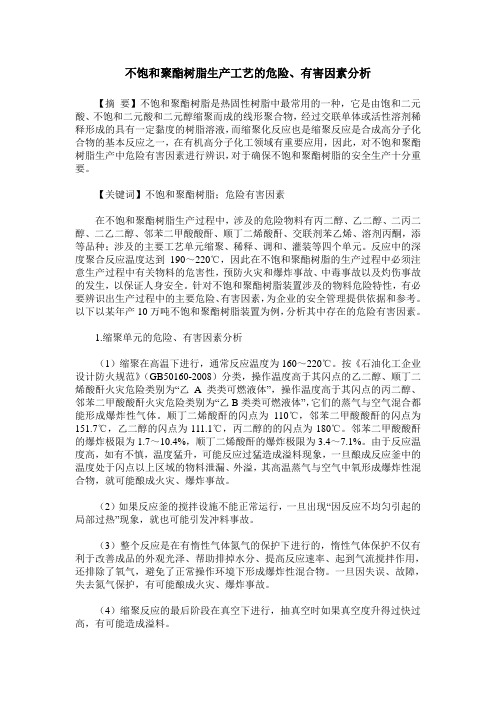
不饱和聚酯树脂生产工艺的危险、有害因素分析【摘要】不饱和聚酯树脂是热固性树脂中最常用的一种,它是由饱和二元酸、不饱和二元酸和二元醇缩聚而成的线形聚合物,经过交联单体或活性溶剂稀释形成的具有一定黏度的树脂溶液,而缩聚化反应也是缩聚反应是合成高分子化合物的基本反应之一,在有机高分子化工领域有重要应用,因此,对不饱和聚酯树脂生产中危险有害因素进行辨识,对于确保不饱和聚酯树脂的安全生产十分重要。
【关键词】不饱和聚酯树脂;危险有害因素在不饱和聚酯树脂生产过程中,涉及的危险物料有丙二醇、乙二醇、二丙二醇、二乙二醇、邻苯二甲酸酸酐、顺丁二烯酸酐、交联剂苯乙烯、溶剂丙酮,添等品种;涉及的主要工艺单元缩聚、稀释、调和、灌装等四个单元。
反应中的深度聚合反应温度达到190~220℃,因此在不饱和聚酯树脂的生产过程中必须注意生产过程中有关物料的危害性,预防火灾和爆炸事故、中毒事故以及灼伤事故的发生,以保证人身安全。
针对不饱和聚酯树脂装置涉及的物料危险特性,有必要辨识出生产过程中的主要危险、有害因素,为企业的安全管理提供依据和参考。
以下以某年产10万吨不饱和聚酯树脂装置为例,分析其中存在的危险有害因素。
1.缩聚单元的危险、有害因素分析(1)缩聚在高温下进行,通常反应温度为160~220℃。
按《石油化工企业设计防火规范》(GB50160-2008)分类,操作温度高于其闪点的乙二醇、顺丁二烯酸酐火灾危险类别为“乙A类类可燃液体”,操作温度高于其闪点的丙二醇、邻苯二甲酸酸酐火灾危险类别为“乙B类类可燃液体”,它们的蒸气与空气混合都能形成爆炸性气体。
顺丁二烯酸酐的闪点为110℃,邻苯二甲酸酸酐的闪点为151.7℃,乙二醇的闪点为111.1℃,丙二醇的的闪点为180℃。
邻苯二甲酸酸酐的爆炸极限为1.7~10.4%,顺丁二烯酸酐的爆炸极限为3.4~7.1%。
由于反应温度高,如有不慎,温度猛升,可能反应过猛造成溢料现象,一旦酿成反应釜中的温度处于闪点以上区域的物料泄漏、外溢,其高温蒸气与空气中氧形成爆炸性混合物,就可能酿成火灾、爆炸事故。
不饱和聚酯树脂的固化

不饱和聚酯树脂的固化 Company number:【0089WT-8898YT-W8CCB-BUUT-202108】不饱和聚酯树脂的固化机理引言不饱和聚酯树脂(UPR)的固化似乎是从理论和实践上已研究得十分透彻的问题,但是因为影响固化反应的因素相当复杂,而在UPR的各种应用领域中,制品所出现的质量瑕疵在很大程度上几乎都与“固化”有关。
所以,我们有对UPR的固化进行较深入探讨的必要。
(探讨不饱和聚酯树脂的固化,首先应该了解与不饱和聚酯树脂固化有关的一些概念和定义)。
2.与不饱和聚酯树脂固化有关的概念和定义固化的定义液态UPR在光、热或引发剂的作用下可以通过线型聚酯链中的不饱和双键与交联单体的双键的结合,形成三向交联的不溶不熔的体型结构。
这个过程称为UPR的固化。
固化剂不饱和聚酯树脂的固化是游离基引发的共聚合反应,如何能使反应启动是问题的关键。
单体一旦被引发,产生游离基,分子链即可以迅速增长而形成三向交联的大分子。
饱和聚酯树脂固化的启动是首先使不饱和C—C双键断裂,由于化学键发生断裂所需的能量不同,对于C—C键,其键能E=350kJ/mol,需350-550℃的温度才能将其激发裂解。
显然,在这样高的温度下使树脂固化是不实用的。
因此人们找到了能在较低的温度下即可分解产生自由基的物质,这就是有机过氧化物。
一些有机过氧化物的O—O键可在较低的温度下分解产生自由基。
其中一些能在50-150℃分解的过氧化物对树脂的固化很有利用价值。
我们可以利用有机过氧化物的这一特性,选择其中的一些作为树脂的引发剂,或称固化剂。
固化剂的定义:不饱和聚酯树脂用的固化剂,是在促进剂或其它外界条件作用下而引发树脂交联的一种过氧化物,又称为引发剂或催化剂。
这里所说的“催化剂”与传统意义上的“催化剂”是不同的。
在传统的观念上,“催化剂”这个术语是为反应物提供帮助的,它们在促进反应的同时,本身并没有消耗。
而在UPR固化反应中,过氧化物必须在它“催化”反应以前,改变它本身的结构,因此对于用于UPR固化的过氧化物来说,一个较合适的名字应该叫做“起始剂”或“引发剂”。
不饱和聚酯树脂生产工艺分析

不饱和聚酯树脂生产工艺分析发布时间:2021-07-27T14:46:15.773Z 来源:《基层建设》2021年第13期作者:李丁[导读] 摘要:本文对不饱和聚酯树脂的生产工艺进行了分析,主要分为两个部分内容。
天津渤化环境修复股份有限公司天津市 300041摘要:本文对不饱和聚酯树脂的生产工艺进行了分析,主要分为两个部分内容。
其一为概述生产工艺,包括通用型生产工艺简介、生产工艺流程以及产品质量指标。
其二为原材料对不饱和聚酯树脂性能影响状况的分析。
关键词:不饱和聚酯;树脂;生产工艺随着玻璃钢行业的蓬勃发展,我国对不饱和聚酯树脂的需求量亦呈不断扩大的趋势。
生产不饱和聚酯树脂,需要生产者较为准确地把握生产工艺的各个环节,并透彻了解各类因素可能对不饱和聚酯树脂性能的影响,以此探索出高质量聚酯树脂的生产技术。
本文即由此入手展开了对不饱和聚酯树脂生产工艺的分析,希望能够为相关生产实践提供一定的借鉴参考。
1 不饱和聚酯树脂生产工艺概述1.1 通用型生产工艺简介通用型不饱和聚酯树脂主要由丙二醇、苯酐、顺酐等按照科学的配比,并在特定的温度(160~210℃之间)进行缩聚制得,随机再向其中加入阻聚剂、石蜡、苯乙烯、光稳定剂等,让它们在70~80℃的温度下混溶,由此而得到的具备一定粘度的液体树脂成品。
此类树脂的耐温性与耐腐蚀性较强,可以在工业生产的很多领域得到应用。
1.2 生产工艺流程生产工艺控制参数的具体情况如下表1所示:表1 生产工艺控制参数1.3 产品质量指标产品质量指标的具体数据如下:外观方面主要呈淡黄色,属于较为透明的液体;酸值方面,具体参数为27~37mgKOH/g;粘度方面,此处以25℃条件为标准,具体参数为2~5p;胶凝时间方面,此处仍以25℃为准,具体参数为12~30min;固体含量方面,具体参数为59%~67%;热稳定性方面,若处在80℃以下主要是24h,若处在25℃以下则为6个月。
2 原材料对不饱和聚酯树脂性能的影响2.1 二元酸对不饱和聚酯树脂性能的影响(1)不饱和二元酸(酐),顺丁烯二酸酐、反丁烯二酸属于工业中较为常见的类型,此类不饱和二元酸可以将不饱和双键提供给聚酯,如此便可在一定条件下使之同苯乙烯单体进行交联共聚。
不饱和聚酯树脂的固化过程(血脂)

2019/10/29
医学知识
4
2.不饱和聚酯树脂的固化特征
固化过程中的三个阶段
A阶
B阶
C阶
可溶、可熔 凝胶阶段
不溶、不熔
2019/10/29
医学知识
5
固化树脂的网络结构表征
固化产物是具有网络结构的体型聚合物,网络结构有两个 重要参数:
(1)两个线型不饱和聚酯分子交联点间苯乙烯的重复单元 数;平均为1~3个。
真空袋压法成型 压力袋成型 树脂注射和树脂传递成型 喷射成型 手糊成型-湿法铺层成型 真空辅助树脂注射成型 夹层结构成型 模压成型
2019/10/29
注射成型
挤出成型
纤维缠绕成型
拉挤成型
连续板材成型
层压或卷制成型
热塑性片状模塑料热冲击成型
离心浇铸成型
来排出。 • 固化成型压力:层压工艺:10-20Mpa,模压30-50Mpa,胶接工艺
1Mpa • 酸固化 • 加入无机酸或有机酸可以常温固化,固化反应与酸催化下,热塑性酚
醛树脂的合成反应相似。,仅仅用于浇注树脂。自发泡(酚醛泡沫塑 料) • 复合材料中的热固性酚醛树脂都是采用加热加压的方法制备,这种固 化的树脂固化充分、耐热性、机械性能、耐溶剂性均比酸固化的要高 许多。
2019/10/29
医学知识
23
抑制剂与缓聚剂在本质上没有任何差别,仅是kz / kp的比 值 大小不同而已。 kz / kp的比值 叫做阻聚常数,用τz表示, 其值越大,阻聚效果越好。
2019/10/29
医学知识
24
例如,对苯乙烯聚合时,其阻聚常数如下:
苯醌(对苯二酚) τ z = 500
不饱及聚酯树脂的固化过程
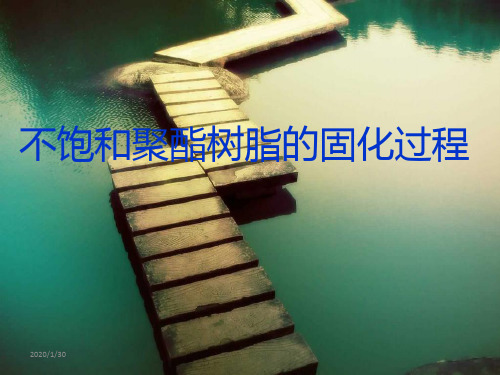
1.1 不饱和聚酯树脂的固化过程:
• 1 固化的含义: • 粘流态→交联→不溶不熔的体型网络 • 2 不饱和聚酯树脂的固化特征 • 凝胶阶段(A阶):失去流动性 • 硬化(定型)阶段(B阶):具有硬度和形状 • 熟化阶段(C阶):具有力学性能可供选择
2020/1/30
2.不饱和聚酯树脂的固化特征
不饱和聚酯树脂的固化过程
2020/1/30
课前回顾
1、什么是UPR的固化?通常分为哪几个阶段? 2、UPR的固化机理与特点分别是什么? 3、固化树脂的网络结构如何表征?
2020/1/30
outline
• 1.1 不饱和聚酯树脂的固化过程 • 1.2 不饱和聚酯树脂的固化原理
1.2.1 固化剂的选择 1.2.2 凝胶与固化 • 1.3 不饱和聚酯用引发剂 • 1.4 不饱和聚酯用阻聚剂 • 1.5 树脂的制备 • 1.6 聚合物基复合材料成型加工技术
2020/1/30
• 理论上恒配比苯乙烯用量为57mol.% • 实际上通用不饱和聚酯树脂中苯乙烯含量为33-40 wt%, 苯
乙烯与不饱和聚酯双键摩尔比为1.8:1,苯乙烯占64-70mol.%
2020/1/30
• (3)链终止 • 双基偶合终止为主 • 共聚到一定程度,形成三维网络,出现凝胶现象(双基终
2020/1/30
• 叔胺(二甲基苯胺)+有机过氧化物(BPO)
• 环烷酸钴+过氧化甲乙酮
2020/1/30
叔胺类促进剂
用于促进过氧化物引发剂,如BPO,使之能在 常温下固化,并且凝胶时间与固化时间都很短, 是室温快速固化体系常用促进剂。
最常用的是N,N’- 二甲基苯胺、 N,N’- 二乙 基苯胺与N,N’- 二甲基对甲苯胺,一般使用10% 的溶液,用量1%~4%。
不饱和聚酯树脂的合成工艺

对原料进行过滤、干燥、脱气等处理, 以确保原料的纯净度和避免在后续反 应中产生气泡。
聚合反应
聚合温度
控制聚合温度在一定范围内,使原料充分反应。
聚合压力
保持一定的聚合压力,有助于提高产品的分子量和粘度。
聚合时间
根据反应进程和产品要求,确定合适的聚合时间。
固化与后处理
固化
通过加入固化剂或加热等方式,使不饱和聚酯树脂从液态转 变为固态。
结构调控与改性
通过分子结构设计、共聚改性等方法,改善不饱和聚 酯树脂的加工性能、力学性能和耐热性能。
高性能化的研究
探索不饱和聚酯树脂的高性能化途径,如增强增韧、 阻燃、耐腐蚀等方面的研究。
环保与可持续发展
01
绿色合成工艺
研究开发环境友好的合成工艺,降低生产过程中的能耗和废弃物产生。
02
废弃不饱和聚酯树脂的回收利用
04
02
不饱和聚酯树脂的合成原理
缩聚反应原理
01
缩聚反应是一种或多种含有多 官能团的单体之间发生反应, 生成高分子化合物的聚合反应 。
02
在不饱和聚酯树脂的合成中, 通常使用二元醇和二元酸作为 单体,通过缩聚反应生成聚酯 。
03
缩聚反应过程中,单体分子中 的官能团之间相互反应,不断 脱去小分子副产物(如水或醇 ),形成高分子链。
总结词
01
产品性能不稳定会影响树脂的应用范围和可靠性。
详细描述
02
原因可能是由于合成过程中的杂质或副产物过多,或者后处理
过程中的热历史、加工条件等控制不当。
解决方案
03
加强原料的纯度控制和后处理工艺,优化热历史和加工条件,
以及采用稳定剂或抗氧剂等添加剂来提高产品的稳定性。
不饱和聚酯树脂涂料

设备选型与布局规划
设备选型
反应釜、搅拌器、研磨机、过滤器、包装机等。
布局规划
根据工艺流程和设备特点,合理规划设备布局,确保生产顺畅、安全。
04
质量控制与检测标准
原材料质量控制
原材料选择
原材料储存
选用优质的不饱和聚酯树脂、固化剂、 稀释剂等原材料,确保来源可靠、品 质稳定。
原材料应储存在干燥、阴凉、通风的 仓库中,避免阳光直射和高温,防止 原材料变质。
02
不饱和聚酯树脂涂料特性
物理化学性质
固化方式
不饱和聚酯树脂涂料通过引发剂 的作用,可在常温下固化,也可
加热固化。
粘度
不饱和聚酯树脂涂料的粘度适中, 易于施工,可喷涂、刷涂或滚涂。
颜色与光泽
不饱和聚酯树脂涂料颜色丰富,光 泽度高,可满足不同装饰需求。
耐候性、耐化学品腐蚀性
耐候性
不饱和聚酯树脂涂料具有良好的耐候性,能抵抗紫外线、氧化和大气污染物的 侵蚀,长期保持颜色和光泽。
高性能化趋势
为了满足高端市场和特定应用场 景的需求,不饱和聚酯树脂涂料 需要不断提高其性能,如耐候性、 耐化学品性、耐磨性等。同时, 还需要关注涂料的施工性能和装 饰效果等方面的提升。
创新驱动因素探讨
要点一
技术创新
通过研发新的合成技术、改性技术和 涂装技术等,提高不饱和聚酯树脂涂 料的性能和质量,降低生产成本和环 境污染。
应用领域与市场需求
应用领域
不饱和聚酯树脂涂料广泛应用于家具、 建筑装修、汽车零部件、船舶、管道等 领域。其中,木器涂装是不饱和聚酯树 脂涂料的主要应用领域之一,具有优异 的装饰性、保护性和耐久性。
VS
市场需求
随着消费者对环保和健康的关注度不断提 高,对不饱和聚酯树脂涂料的环保性能要 求也越来越高。同时,市场对于高性能、 多功能的不饱和聚酯树脂涂料的需求也在 不断增加。为了满足市场需求,涂料企业 需要不断研发创新,提高产品的环保性能 、施工性能和装饰性能。
不饱和聚酯树脂生产操作规程

不饱和聚酯树脂生产操作规程一.投料根据配方,先将乙二醇、丙二醇、二乙二醇等液态原料抽入反应釜后,启动反应釜搅拌,再进行邻苯二甲酸酐、顺丁烯二酸酐等固态原料投料。
再加入必要的抗氧剂、阻聚剂、消泡剂等小料。
关闭反应釜投料口,关闭反应釜上所有阀门,打开废水受槽上平衡管阀门、回流管阀门的放空阀门。
二.升温根据冷热油系统操作规程升温系统操作。
当反应温度升到160-170℃时,开始出水,这时应严格控制馏头温度在100-103℃,具体操作办法是用立冷冷却水大小来控制馏头温度,如果馏头温度过高,则会把反应釜内醇原料带走,馏头温度过低,则会影响出水。
一般每小时升温6-8℃,具体操作方法是由热油进阀门来控制升温速度。
三.保温当反应温度达到工艺要求后(205-210℃),应采取保温3小时左右,具体见冷热油系统操作规程中保温系统操作。
四.测酸值当出水量很少时,就可以测酸值,正常应在57左右。
五.抽真空减压酯化。
当酸值达到工艺要求后,就可以抽真空,具体操作方法见真空操作规程。
关闭废水受槽上的平衡管阀门,关闭受槽底部的排污阀门,慢慢关闭废水受槽上的放空阀门,使真空度控制在-0.05MPa,这时应看反应釜内原料的沸腾状态,慢慢提高真空度,使真空度达到-0.08MPa以上,一般为2个小时左右。
六.再测酸值关闭真空泵,打开废水受槽上的放空阀门,解除反应釜的真空度来进行取样,具体操作方法见上面测酸值,酸值根据品种不同由工艺定,一般为27左右。
七.降温具体操作见操作规程,温度降到180℃左右时,加入阻聚剂、石腊等小料。
继续降温到155准备兑稀。
八.在稀释釜内抽入配方量的苯乙烯,加入阻聚剂TBC 搅拌好准备兑稀。
九.兑稀启动真空泵。
打开反应釜上出料阀门,打开稀释釜上进料阀门,关闭稀释釜上不相关阀门。
打开苯乙烯受槽上进真空阀门,关闭苯乙烯受槽上放空阀门和底部的排污阀门,当真空达到-0.05MPa以上时,反应釜内的聚酯即不断地抽到稀释釜内。