催化装置催化剂失活与破损原因分析及解决措施
催化装置脱硫脱硝设备的运行问题及对策

催化装置脱硫脱硝设备的运行问题及对策催化装置是一种用于降低工业生产过程中废气中有害气体含量的设备,其中脱硫脱硝是其主要功能之一。
在实际运行中,催化装置脱硫脱硝设备也会遇到一些问题,影响设备的正常运行。
本文将针对催化装置脱硫脱硝设备的运行问题进行分析,并提出相应的对策,以期达到更好的设备运行效果。
一、运行问题分析1. 催化剂失活催化剂的失活是催化装置运行中常见的问题之一。
主要表现为催化剂的活性降低,导致脱硫脱硝效率下降。
失活的原因主要有:化学性质的改变、受到污染等。
这些因素都会导致催化剂的性能下降,影响脱硫脱硝效果。
2. 温度波动催化装置在运行过程中,温度波动是不可避免的。
当温度波动过大时,会影响催化剂的活性,降低脱硫脱硝效率。
3. 供气不稳定催化装置的运行需要稳定的气体供应,当供气不稳定时,会导致催化剂的性能受到影响,进而影响脱硫脱硝效果。
4. 污染物浓度过高工业生产过程中产生的废气中含有多种有害气体,其中的污染物浓度过高会对催化装置的运行造成影响,降低脱硫脱硝效果。
二、对策建议1. 定期更换催化剂为了避免催化剂失活造成的影响,建议定期更换催化剂。
在更换催化剂时,应当选择优质的催化剂,并在更换后进行严格的检测和试运行,确保新的催化剂可以正常运行。
2. 加强温度控制针对温度波动过大的问题,可以采取加强温度控制的措施,例如增加温度监测装置,加强对温度变化的监控和调节,确保催化剂运行在适宜的温度范围内。
3. 稳定气体供应为了解决供气不稳定的问题,可以加强对气体供应系统的管理,确保气体供应的稳定性。
可以采取增加备用供气装置、定期检查气体供应管道等措施,保障催化装置的正常运行。
4. 废气预处理对于废气中污染物浓度过高的情况,可以考虑增加废气预处理设备,将废气中的污染物浓度降低到催化装置可接受的范围内,以提高脱硫脱硝效果。
催化装置脱硫脱硝设备的运行问题是一项复杂的工作,需要全面的技术和管理支持。
通过加强对设备的监测和调节、定期维护和保养、人员培训等措施,可以有效地解决设备运行中出现的问题,确保设备能够高效、稳定地运行,达到清洁生产的目的。
MTBE装置催化剂失活的原因分析

MTBE装置催化剂失活的原因分析1、原料性质对催化剂的影响原料性质对催化剂的影响大致可以从以下几个方面分析:⑴原料中水对催化剂的影响如果原料中含有水,则水可以使树脂中的磺酸根脱落,也可以和磺酸根以氢键相结合,从而造成树脂催化剂失活。
此外,水还可以和异丁烯生成TBA聚集在催化剂的表面,使催化剂的反应面积减少,影响催化剂的催化效果。
原料带水来源于两个渠道:①C4原料中携带。
一般情况下原料中不可能携带大量游离水,这是由于碳四原料来源于气体分馏装置的脱丙烷塔底,液化气中的水分均通过共沸作用至塔顶,况且每个班的液化气脱水都比较彻底,所以可以排除混合碳四中携带水的可能性。
②甲醇带水。
回收甲醇以及进装置的新鲜甲醇都经过化验室分析,水含量基本控制在不大于1%,所以可以看出甲醇携带的水是微量的,但也不可以忽视甲醇回收系统的精心操作,尽量把水对催化剂的影响降到最低。
⑵金属离子及碱性物质对催化剂的影响根据催化剂厂家对失活催化剂的研究和化验分析,70%的催化剂失活是由于阳离子的原因。
因为阳离子置换了催化剂中的氢离子,再加上碱性物质中和了催化剂中的酸性,都会使树脂的酸性释放不出来,从而不能充分发挥其催化作用。
由于我公司液化气采用碱洗+水洗的脱硫工艺,因此MTBE装置原料混合碳四中不可避免将携带大量金属离子和碱性物质。
分析和控制原料中金属离子含量、防止液态烃带碱对MTBE催化剂寿命至关重要。
为了最大限度地降低金属离子和碱性物质的含量,建议实行以下措施:①加强脱硫醇的操作,防止液态烃带碱;增加水洗量,使用除盐水;②减少上游装置停工检修次数,减少铁离子含量;③加强液化气罐区脱水;④必要时在MTBE装置前增加离子过滤器。
⑶碳五烃类对催化剂的影响原料中碳五组分的存在严重威胁催化剂的使用寿命,包括硫化物失活、生成TAME堵塞催化剂孔道。
原料中硫化物主要是硫醚对MTBE催化剂影响最大,二甲基硫醚主要性质与碳五相似,因此在碳五中含量较多,虽然其总量微小,但是影响显著,与磺酸根结合形成盐类,从而使催化剂损失。
MTBE装置催化剂失活原因分析及解决方案
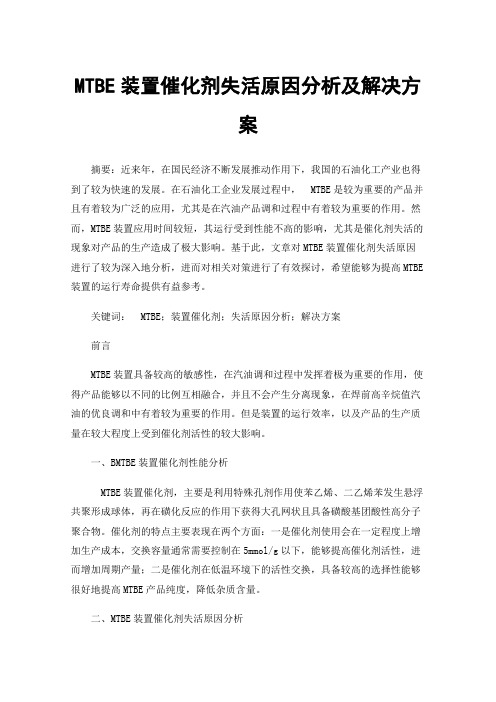
MTBE装置催化剂失活原因分析及解决方案摘要:近来年,在国民经济不断发展推动作用下,我国的石油化工产业也得到了较为快速的发展。
在石油化工企业发展过程中,MTBE是较为重要的产品并且有着较为广泛的应用,尤其是在汽油产品调和过程中有着较为重要的作用。
然而,MTBE装置应用时间较短,其运行受到性能不高的影响,尤其是催化剂失活的现象对产品的生产造成了极大影响。
基于此,文章对MTBE装置催化剂失活原因进行了较为深入地分析,进而对相关对策进行了有效探讨,希望能够为提高MTBE 装置的运行寿命提供有益参考。
关键词:MTBE;装置催化剂;失活原因分析;解决方案前言MTBE装置具备较高的敏感性,在汽油调和过程中发挥着极为重要的作用,使得产品能够以不同的比例互相融合,并且不会产生分离现象,在焊前高辛烷值汽油的优良调和中有着较为重要的作用。
但是装置的运行效率,以及产品的生产质量在较大程度上受到催化剂活性的较大影响。
一、BMTBE装置催化剂性能分析MTBE装置催化剂,主要是利用特殊孔剂作用使苯乙烯、二乙烯苯发生悬浮共聚形成球体,再在磺化反应的作用下获得大孔网状且具备磺酸基团酸性高分子聚合物。
催化剂的特点主要表现在两个方面:一是催化剂使用会在一定程度上增加生产成本,交换容量通常需要控制在5mmol/g以下,能够提高催化剂活性,进而增加周期产量;二是催化剂在低温环境下的活性交换,具备较高的选择性能够很好地提高MTBE产品纯度,降低杂质含量。
二、MTBE装置催化剂失活原因分析(一)原料污染碳四组是MTBE产品生产不可或缺因素,而碳四组分主要是液态烃脱硫、液气分离所得,其过程极易混入含氮化合物,从而影响催化剂使用寿命。
同时混入的金属离子也会对MTBE 装置催化剂造成不良影响,使催化剂受到较为严重污染而降低催化剂活性。
催化剂生产过程中,FCC脱氧醇工艺的应用会涉及低浓度氢氧化钠溶液,导致大量金属钠离子混入催化剂原料中而使得催化剂受到污染。
催化装置脱硫脱硝设备的运行问题及对策

催化装置脱硫脱硝设备的运行问题及对策催化装置脱硫脱硝设备是用于去除燃料气体中的硫化物和氮氧化物的重要设备。
在实际运行中,可能会出现一些问题,影响设备的正常运转。
本文将针对这些问题进行分析,并提出相应的对策。
一、催化剂失活问题催化装置脱硫脱硝设备中的催化剂是关键的部件,直接影响设备的脱硫脱硝效果。
在运行过程中,催化剂可能会因为多种原因失活,导致脱硫脱硝效果下降。
1. 催化剂中毒:催化剂可以被硫化物和氮氧化物中的某些成分所吸附,导致催化剂中毒。
常见的中毒物质包括硫化氢、二氧化硫和氮氧化物。
当这些物质吸附在催化剂表面时,会阻塞活性位点,降低催化剂的活性。
对策:定期对催化剂进行再生或更换。
通过加热或者用其他气体进行冲洗,可以将吸附在催化剂上的中毒物质去除,恢复催化剂的活性。
2. 催化剂结焦:在高温条件下,催化剂可能会发生结焦现象,表面形成焦炭物质,降低催化剂的活性。
对策:采取适当的操作措施,控制催化剂的温度,避免过高的温度导致结焦。
定期进行催化剂的清洗和再生,可以去除结焦物质,恢复催化剂的活性。
催化装置脱硫脱硝设备中的催化剂的选择直接关系到设备的脱硫脱硝效果。
不同类型的催化剂适用于不同的工况条件。
1. 催化剂的反应活性不高:选用的催化剂反应活性不高,不能有效地去除燃料气体中的硫化物和氮氧化物。
对策:根据具体工况条件选择合适的催化剂。
可以通过实验室的筛选实验来评估不同催化剂的反应活性,并选择活性较高的催化剂。
2. 催化剂的寿命较短:选用的催化剂寿命较短,需要频繁更换,增加了设备的运营成本。
三、操作问题1. 温度控制不当:温度是影响催化剂活性的重要因素之一。
如果温度过低,催化反应的活性会降低;如果温度过高,可能导致催化剂结焦或失活。
对策:合理控制催化装置的温度,保持在适宜的范围内。
2. 气体流速过大:气体流速过大会导致气体在催化剂上停留时间短,不利于催化反应的进行。
对策:调整气体流速,使气体在催化剂上停留时间适宜。
MTBE装置催化剂失活原因分析及对策研究
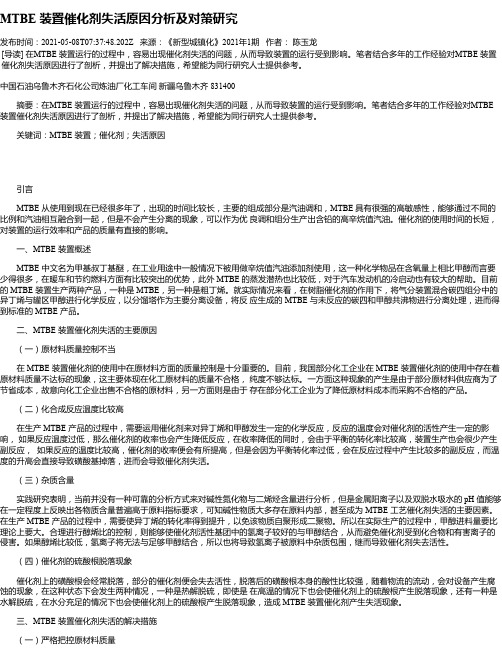
MTBE 装置催化剂失活原因分析及对策研究发布时间:2021-05-08T07:37:48.202Z 来源:《新型城镇化》2021年1期作者:陈玉龙[导读] 在MTBE 装置运行的过程中,容易出现催化剂失活的问题,从而导致装置的运行受到影响。
笔者结合多年的工作经验对MTBE 装置催化剂失活原因进行了剖析,并提出了解决措施,希望能为同行研究人士提供参考。
中国石油乌鲁木齐石化公司炼油厂化工车间新疆乌鲁木齐 831400摘要:在MTBE 装置运行的过程中,容易出现催化剂失活的问题,从而导致装置的运行受到影响。
笔者结合多年的工作经验对MTBE 装置催化剂失活原因进行了剖析,并提出了解决措施,希望能为同行研究人士提供参考。
关键词:MTBE 装置;催化剂;失活原因引言MTBE 从使用到现在已经很多年了,出现的时间比较长,主要的组成部分是汽油调和,MTBE 具有很强的高敏感性,能够通过不同的比例和汽油相互融合到一起,但是不会产生分离的现象,可以作为优良调和组分生产出含铅的高辛烷值汽油。
催化剂的使用时间的长短,对装置的运行效率和产品的质量有直接的影响。
一、MTBE 装置概述MTBE 中文名为甲基叔丁基醚,在工业用途中一般情况下被用做辛烷值汽油添加剂使用,这一种化学物品在含氧量上相比甲醇而言要少得很多,在暖车和节约燃料方面有比较突出的优势,此外 MTBE 的蒸发潜热也比较低,对于汽车发动机的冷启动也有较大的帮助。
目前的 MTBE 装置生产两种产品,一种是 MTBE,另一种是粗丁烯。
就实际情况来看,在树脂催化剂的作用下,将气分装置混合碳四组分中的异丁烯与罐区甲醇进行化学反应,以分馏塔作为主要分离设备,将反应生成的 MTBE 与未反应的碳四和甲醇共沸物进行分离处理,进而得到标准的 MTBE 产品。
二、MTBE 装置催化剂失活的主要原因(一)原材料质量控制不当在 MTBE 装置催化剂的使用中在原材料方面的质量控制是十分重要的。
化学技术中催化剂失活原因的分析与预防

化学技术中催化剂失活原因的分析与预防引言:催化剂在各个化学领域中扮演着至关重要的角色。
然而,在催化过程中,难免会遇到催化剂失活的问题。
催化剂失活不仅导致产率下降和反应效率降低,还会增加生产成本。
因此,分析催化剂失活的原因并采取预防措施是一项重要的研究课题。
一、物理失活物理失活是指催化剂中的物理性质发生变化,导致活性降低。
其中,主要原因包括沉积物堵塞、颗粒聚集和金属中毒。
1. 沉积物堵塞催化反应中的沉积物是一种常见的导致催化剂失活的因素。
沉积物可以来自于反应物中的杂质或副产物。
当沉积物堆积在催化剂表面时,会阻碍反应物与催化剂之间的接触,从而减少催化剂的活性。
2. 颗粒聚集颗粒聚集是指催化剂颗粒之间的物理吸附或化学键结合。
当颗粒聚集导致催化剂的比表面积减少时,活性也会随之降低。
3. 金属中毒金属中毒是指催化剂中的金属元素与金属反应物或其他杂质发生反应,生成具有毒性的金属化合物。
金属中毒不仅导致催化剂活性降低,还可能造成催化剂的变质。
二、化学失活化学失活是指催化剂的化学性质发生变化,导致活性降低或完全失效。
常见的化学失活原因包括化学反应、水蒸气和酸碱性条件。
1. 化学反应化学反应是指催化剂与反应物或其他物质之间发生化学反应,导致催化剂结构的破坏。
例如,催化剂与氧气反应会发生氧化反应,导致表面结构损坏,进而使催化剂失活。
2. 水蒸气水蒸气是一种常见的催化剂失活因素。
在某些催化反应中,水蒸气可以与催化剂表面发生氧化还原反应,导致催化剂的活性降低。
3. 酸碱性条件酸碱性条件是指催化剂所处环境的酸碱度。
当催化剂暴露在酸性或碱性介质中时,会导致催化剂表面的活性位点被破坏或改变,从而引起催化剂失活。
三、预防措施为了降低催化剂失活的风险,可以采取一些预防措施。
1. 优化反应条件调整反应条件,例如温度、反应物浓度和反应物比例等,可以降低催化剂失活的可能性。
通过优化反应条件,可以减少催化剂与有害物质的接触,延缓催化剂的失活速度。
化学催化剂的失活与再生
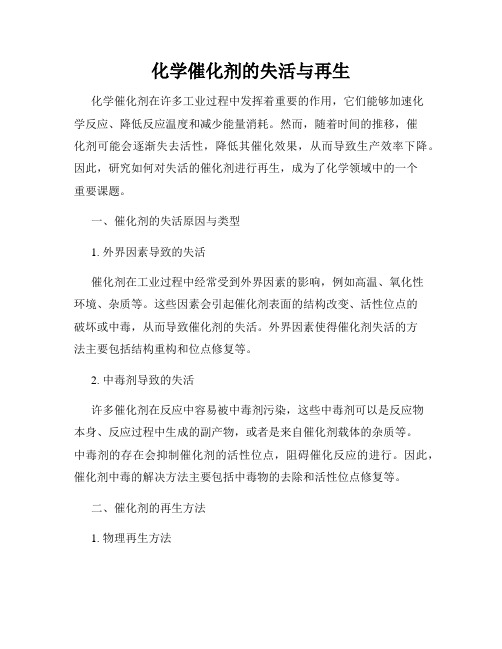
化学催化剂的失活与再生化学催化剂在许多工业过程中发挥着重要的作用,它们能够加速化学反应、降低反应温度和减少能量消耗。
然而,随着时间的推移,催化剂可能会逐渐失去活性,降低其催化效果,从而导致生产效率下降。
因此,研究如何对失活的催化剂进行再生,成为了化学领域中的一个重要课题。
一、催化剂的失活原因与类型1. 外界因素导致的失活催化剂在工业过程中经常受到外界因素的影响,例如高温、氧化性环境、杂质等。
这些因素会引起催化剂表面的结构改变、活性位点的破坏或中毒,从而导致催化剂的失活。
外界因素使得催化剂失活的方法主要包括结构重构和位点修复等。
2. 中毒剂导致的失活许多催化剂在反应中容易被中毒剂污染,这些中毒剂可以是反应物本身、反应过程中生成的副产物,或者是来自催化剂载体的杂质等。
中毒剂的存在会抑制催化剂的活性位点,阻碍催化反应的进行。
因此,催化剂中毒的解决方法主要包括中毒物的去除和活性位点修复等。
二、催化剂的再生方法1. 物理再生方法物理再生方法主要采用物理手段对失活的催化剂进行处理,以恢复其催化活性。
其中的一个方法是煅烧,即将失活的催化剂放入高温炉中进行加热。
煅烧能够去除催化剂表面的积碳物质或挥发性杂质,从而恢复催化活性。
另一个物理再生方法是超声波清洗,通过超声波的作用,将附着在催化剂表面的污染物颗粒震掉。
超声波清洗简单且高效,可在不破坏催化剂的情况下去除污染物。
2. 化学再生方法化学再生方法主要利用化学反应使失活的催化剂得到再生。
催化剂在反应中被还原或氧化,以去除中毒物质或修复被破坏的活性位点。
举个例子,对于一些贵金属催化剂,如铂、钯等,可以通过浸渍法将音化物质重新沉积在催化剂表面,从而恢复其活性。
此外,酸碱洗涤、化学溶解和还原等方法也常用于修复失活催化剂。
三、催化剂失活与再生的案例研究1. 催化剂失活与再生的案例研究许多学者对催化剂失活与再生进行了深入研究,旨在寻找更有效的再生方法。
例如,研究人员发现,当镍基催化剂在CO2氛围中失活时,可以通过还原和氧化处理来修复催化剂,使其再次活化。
MTBE装置催化剂的失活原因分析及解决措施

M T B E 装置催化剂的失活原因分析及解决措施徐丹凤杨丰华(中海石油宁波大榭石化有限公司,浙江宁波315812)摘要:甲基叔丁基醚(MTBE )产品由于其辛烷值彳艮高,是生产含氧、无铅和高辛烷值汽油的理想组分,也可作为后续装置生产高纯 度异丁烯的原料。
为了获取高纯度的M T B E 产品,除了严格控制操作条件外,保证反应所需催化剂的高活性也至关重要。
催化剂的 使用寿命一般为一年,随着装置运行时间的增长,催化剂的活性会越来越低,但是由于原料组分、操作条件等原因,会导致催化剂 提前或过早的不正常失活,不能达到使用寿命,给公司带来由M T B E 产品纯度降低以及换剂所造成的经济损失,所以如何避免催化 剂的不正常失活成为M T B E 装置操作人员必须要探究解决的问题。
关键词:M T B E ;催化剂;失活1 M T B E 反应基本原理气体分馏装置来混合碳四中的异丁烯与甲醇,在温度 35 ~75X :,压力(K 5 ~0.9MPa (g )操作条件及大孔强酸性离 子交换树脂催化剂的作用下合成MTBE 。
在主反应的同时还存在以下副反应:① 原料中的水与异丁烯反应生成叔丁醇(TBA ),② 异丁烯自聚反应生成异丁烯二聚物(DIB ):异丁烯二聚 是在进料中醇烯比不足时才发生,二聚物(DIB )过多不仅影 响MTBE 产品纯度,而且DIB 会堵塞催化剂细孔、使反应器床 层超温等,造成催化剂失活,是必须要严格限制的情况。
③ 甲醇缩合合成二甲醚(DME):温度要求较高,80X :以上 时甲醇缩合反应才可发生。
④ 正丁烯与甲醇反应合成甲基仲丁基醚(MSBE )。
为了获取高纯度的MTBE ,要尽量避免副反应的发生。
2催化剂失活机理 2.1磺酸根脱落磺酸根为催化剂提供酸性活性中心,因此横酸根在催化剂 表面吸附的牢固程度就关系到催化剂活性的高低。
当反应温度 过高时,磺酸根会脱落,导致催化剂失活,脱落的磺酸根具有很 强的酸性,会随着物料的流动而对设备造成腐蚀。
- 1、下载文档前请自行甄别文档内容的完整性,平台不提供额外的编辑、内容补充、找答案等附加服务。
- 2、"仅部分预览"的文档,不可在线预览部分如存在完整性等问题,可反馈申请退款(可完整预览的文档不适用该条件!)。
- 3、如文档侵犯您的权益,请联系客服反馈,我们会尽快为您处理(人工客服工作时间:9:00-18:30)。
催化装置催化剂失活与破损原因分析及解决措施张志亮薛小波随着全厂加工原油结构的改变,为了平衡全厂重油压力,今年以来催化装置持续提高掺渣比,目前控制在25%左右。
催化原料的重质化、劣质化,对催化装置催化剂造成较大影响。
出现了催化剂重金属中毒加剧、失活严重、破损加重等现象,从而导致装置催化剂单耗上升、产品收率下降、各项经济指标下降。
通过在显微镜下研究催化剂的颗粒度分布、粒径的大小及形状,找到影响催化剂失活和粉碎的主要原因,通过采取多种措施,调整操作、精细管理等方式,提高装置催化剂活性、降低催化剂破损,保证装置在高掺渣率条件下,优质良好运行。
1、催化剂失活原因分析催化剂失活主要分为两种:一、暂时性失活;二、永久性失活。
暂时性失活主要由于催化剂孔径和活性中心被焦炭所堵塞,可在高温下烧焦基本得到恢复。
而永久性失活是指催化剂结构发生改变或者活性中心发生化学反应而不具有活性,其中包括催化剂重金属中毒和催化剂水热失活。
1.1 催化剂的重金属中毒失活原料中重金属浓度偏高很容易使催化剂发生中毒而破裂,尤其是钠、钒和镍。
由于钠离子和钒离子在催化剂表面易形成低熔点氧化共熔物,这些共熔物接受钠离子生成氧化钠,氧化钠不仅能覆盖于催化剂表面减少活性中心,而且还能降低催化剂的热稳定性;其中重金属中Ni对催化剂的污染尤为突出,平衡剂中Ni含量每上升1000ppm,催化剂污染指数上升1400ppm。
图1 2012年与2011年平衡催化剂性质分析对比从图1中可以看出:2012年平衡剂与2011年同期对比,平衡剂活性有所下降,从同期的62%降至今年的60%左右。
金属Fe、Na、Ca含量基本持平,V的含量下降了37%,但是Ni浓度大幅上升,上升了55%。
对比污染指数:2011年为8840ppm,2012年为11970ppm,同比上升了35.4%,从而导致催化剂活性下降了2~3个百分点。
因此,目前催化剂活性下降的重要原因是Ni含量大幅上升。
1.2催化剂的水热失活在高温条件下,特别是有水蒸汽存在的条件下,催化剂表面结构会发生裱花,比表面积减小,孔容减小,分子筛的晶体结构发生破坏,从而导致催化剂的活性和选择性下降。
通过查阅大量的资料并将本装置与其他装置进行数据分析、对比研究发现:(1)分子筛催化剂在环境温度<650℃时催化剂失活较慢,在环境温度<720℃时失活并不严重,但当环境温度>730℃时失活就比较突出;(2)装置发生水热失活的地方主要是密相床层和一、二提升管底部;(3)目前装置烧焦量达到7.0~8.0%,燃烧后生成大量水蒸气携带入密相床层,同时现有再生器为快速床+湍流床的完全再生形式,湍流床层中设置了主风分布环管,催化剂在高氧含量、高温(690~700℃)、高水蒸汽分压及长停留时间的共同作用下,不仅会生成V2O5,使催化剂晶体结构发生破坏,产生较多的超细粉,发生水热失活。
2、催化剂的破损原因分析系统内平衡催化剂在受原料中重金属污染后,其骨架结构和性质发生破坏,最终在催化剂与催化剂颗粒之间、催化剂与设备之间相互摩擦,从而发生催化剂破损,形成更小的催化剂颗粒和大量催化剂细粉。
这里从这两方面展开分析,一是高速部位对催化剂破碎的影响,二是掺渣率对催化剂破碎的影响。
2.1 高速部位对催化剂破碎的影响通过计算高速部位线速,研究是否存在线速超高的状况。
计算结果见下表:稀相线速m/s 0.73 0.79密相线速m/s 1.037 1.19从表1中装置各主要部位线速和参考值的对比中可以看出:大部分高速部位线速都在设计和参考范围之内,但是中环风分布管线速和二密风分布管线速比参考值略高。
2.2 掺渣率对催化剂破碎的影响表2 2012年1~3掺渣率与平衡剂中细粉含量统计表项目掺渣率,%比表面积m2/g粒度0-20μm%(v/v)粒度20-40μm%(v/v)粒度40-60μm%(v/v)粒度60-80μm%(v/v)粒度80-111μm%(v/v)粒度>111μm%(v/v)2012.1 18.64 96 0.2 17.1 26.4 21.5 20 14.8 2012.2 19.78 90 0.7 17.4 26.7 21.5 19.7 14 2012.3 22.19 92 0.2 18.8 28.1 22 19.2 11.7 装置在1~3月份,随着掺渣率的上升,平衡催化剂中0~40μm%(v/v)的含量逐渐上升,平衡催化剂的比表面积也呈下降的趋势,说明掺渣率上升,平衡催化剂的破碎程度增加。
2.3 显微镜下催化剂形态学观察采集装置上平衡催化剂和新鲜催化剂在再高倍显微镜下观察分析,其表面光滑程度、粒度大小以及粒度分布情况都能较好的辨识出来。
如下图所示:平衡催化剂新鲜催化剂图3 显微镜下平衡催化剂与新鲜催化剂形态对比从图3明显可以看出,绝大多数平衡催化剂颗粒表面比较光滑,棱角比较分明的较少,催化剂粒度分布较好,细小颗粒少,与平衡催化剂反馈数据较为一致,说明目前装置内平衡催化剂破损很大程度上是由于长时间在系统内循环最终磨损所致。
新鲜催化剂细粉较少,通过催化裂化反应在水蒸气的作用下,平衡催化剂中大颗粒减少,小颗粒增多,原来很多形态较好的颗粒因颗粒之间相互碰撞或与设备冲刷、破碎变得形态各异。
3、解决措施3.1 LDO-75型催化剂在装置上的优化应用LDO-75型催化剂是兰州石化催化剂厂研制的一种高活性、高稳定性的分子筛催化剂,采用了多空基质材料、重金属捕集技术、和ZSM-5改性技术,已在多家炼油厂使用。
LDO-75催化剂执行LSZB094-2009标准,具体如下:装置在2011年5月份之前一直使用CDC和LV-23两种催化剂,自2011年5月3日开始使用LDO-75型催化剂。
2012年1~9月装置共加入催化剂1027.4吨,催化剂单耗完成1.68 Kg/t,催化剂活性维持在58~62%之间。
为做好LDO-75催化剂的使用工作,使其达到最佳使用效果,与生产厂家进行技术交流。
进一步改善催化剂的性能,主要从以下几方面入手:①使出厂新鲜催化剂17小时的活性稳定在64~65%;②提高催化剂的水热稳定性;③控制催化剂的磨损指数不能太高。
3.2优化车间进料,严格控制掺渣率由于催化原料中减压渣油中重金属含量远远高于裂化料中的含量,其中Ni含量为裂化料中的3~4倍,V的含量为裂化料的2~3倍,所以控制掺渣率能够有效控制原料中(Ni+V)的含量。
查阅资料显示,在催化掺渣率控制在25%以内,系统内平衡催化剂上(Ni+V)含量基本维持在8000μg/g 左右,能够有效控制催化剂的重金属中毒。
3.3 降低回炼比由于油浆和回炼油系统中重金属含量远远高于原料中重金属含量,所以通过停用二提油浆回炼,适当外排油浆,降低回炼比等措施能够有效降低催化剂的重金属中毒。
装置回炼油回炼量由45t/h降至40t/h,外排油浆量控制在4~5t/h,回炼比控制在0.4左右。
3.4 改变预提升段的预提升介质为了降低高温催化剂遇低温水蒸汽发生水热失活现象,将一提预提升段预提升介质由蒸汽改为干气。
3.5 调整预提升段的预提升介质流量根据设计要求,在满足催化剂在提升管底部预提升段正常流化条件下,尽量降低与提升段流化介质流量,减少催化剂发生水热失活的条件,项目小组进行了调整:一提预提升干气由1200Kg/h 降至1000Kg/h,二提预提升蒸汽流量由1.7t/h降至1.6t/h。
3.6 调整反再区蒸汽松动点由于反再系统部分松动点分布较紧密,在保证催化剂正常流化条件下,一方面为了节约蒸汽,另一方面为了降低高温催化剂与低温蒸汽直接接触的几率。
关闭了部分分布紧密的松动点,只保证催化剂正常流化。
3.7 降低催化剂总藏量为了减少平衡催化剂在再生器的停留时间,降低平衡催化剂在再生器密相的水热失活几率。
根据装置的实际情况,保证装置正常流化的前提下,当系统内催化剂藏量较高时采取及时卸催化剂,目前催化剂总藏量由160吨左右降低至140吨左右。
3.8 调节分布主风量针对再生器内中环风分布管线速和二密风分布管线速略高的情况,对主风分布进行了调整:二密床层的进口风量由6800Nm3/h降至200Nm3/h,一二提雾化蒸汽流量控制在3~3.5%之间,控制VQS出口线速在设计范围内。
合理调节主风分布、雾化蒸汽量等操作参数,使线速控制在设定值的范围之内,尽量降低催化剂在高速部位的磨损。
4、效果评价4.1 催化剂活性稳步上升通过采取以上措施,项目小组对装置2012年1~8月份平衡催化剂活性进行统计,结果如下:2012年装置1~8月份催化剂活性趋势57.4058.9057.1059.0059.2061.2062.2061.0056.0057.0058.0059.0060.0061.0062.0063.002011-12-232012-02-112012-04-012012-05-212012-07-102012-08-29日期活性%*图中数据来自催化剂长岭分公司2012年1~8月份玉门平衡剂数据报告图2 2012年装置1~8月份催化剂活性分布图从图2中明显可以看出,通过采取多种措施,装置催化剂活性呈直线上升曲线,从1月份的57%上升到8月份的61%,说明以上措施对于减少平衡催化剂的水热失活有明显的效果。
4.2 催化剂单耗有效降低项目小组对2012年1~9月份的催化剂使用情况进行了统计,结果如下:表4 2012年1~9月份与去年同期催化剂使用情况对比项目 处理量 t 掺渣量 t 掺渣率 % 催化剂加入量t催化剂单耗Kg/t催化剂活性% 2012年1~9月 610112 149635 23.50 1078.2 1.77 57~62 2011年1~9月511245 10522120.581016.51.9960~63从表4可以看出:在掺渣率上升 2.92个百分点,催化剂活性变化不大的情况下,催化剂单耗下降了0.22Kg/t ,说明在采取上述一系列措施以后,催化剂的重金属中毒失活状况有所好转。
4.3 催化剂破损程度下降图4 装置2012年1~9月份掺渣率与0~40μm催化剂细粉含量走势曲线从图4可以看出,通过采取以上减少催化剂失活和破损的措施(见3.2、3.3和3.8),虽然1~9月份进料掺渣率逐步提高,但是4月份开始系统内平衡催化剂0-40μm%(v/v)的含量平缓下降,说明通过以上措施,有效的减少了催化剂发生破损几率。
5、结论(1)2012年1~9月份,装置掺渣率为23.50%,较去年同期提高2.92个百分点,催化剂单耗为1.77Kg/t(控制在2.0 Kg/t以内),较去年同期下降了0.22 Kg/t,使车间的生产成本降低。
(2)催化剂活性较1、2月份上升了2~3个百分点,平衡催化剂中0~40μm的筛分组成维持在14~18%(v/v),催化剂粒度分布较好。