关于加氢裂化催化剂失活的原因分析
关于加氢裂化催化剂失活的原因分析
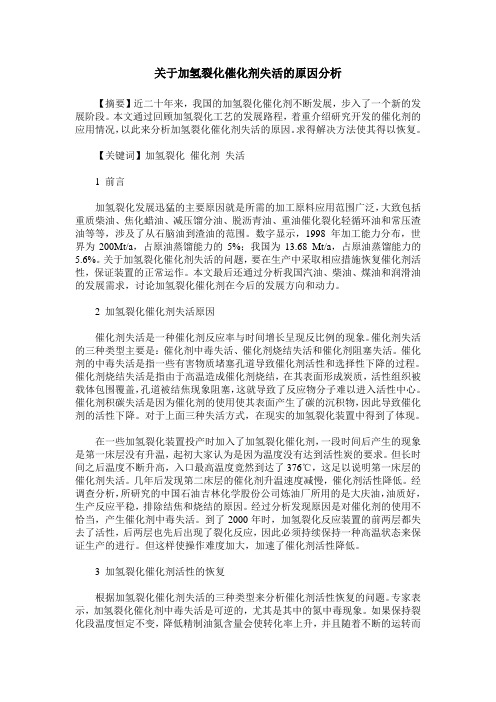
关于加氢裂化催化剂失活的原因分析【摘要】近二十年来,我国的加氢裂化催化剂不断发展,步入了一个新的发展阶段。
本文通过回顾加氢裂化工艺的发展路程,着重介绍研究开发的催化剂的应用情况,以此来分析加氢裂化催化剂失活的原因。
求得解决方法使其得以恢复。
【关键词】加氢裂化催化剂失活1 前言加氢裂化发展迅猛的主要原因就是所需的加工原料应用范围广泛,大致包括重质柴油、焦化蜡油、减压馏分油、脱沥青油、重油催化裂化轻循环油和常压渣油等等,涉及了从石脑油到渣油的范围。
数字显示,1998年加工能力分布,世界为200Mt/a,占原油蒸馏能力的5%;我国为13.68 Mt/a,占原油蒸馏能力的5.6%。
关于加氢裂化催化剂失活的问题,要在生产中采取相应措施恢复催化剂活性,保证装置的正常运作。
本文最后还通过分析我国汽油、柴油、煤油和润滑油的发展需求,讨论加氢裂化催化剂在今后的发展方向和动力。
2 加氢裂化催化剂失活原因催化剂失活是一种催化剂反应率与时间增长呈现反比例的现象。
催化剂失活的三种类型主要是:催化剂中毒失活、催化剂烧结失活和催化剂阻塞失活。
催化剂的中毒失活是指一些有害物质堵塞孔道导致催化剂活性和选择性下降的过程。
催化剂烧结失活是指由于高温造成催化剂烧结,在其表面形成炭质,活性组织被载体包围覆盖,孔道被结焦现象阻塞,这就导致了反应物分子难以进入活性中心。
催化剂积碳失活是因为催化剂的使用使其表面产生了碳的沉积物,因此导致催化剂的活性下降。
对于上面三种失活方式,在现实的加氢裂化装置中得到了体现。
在一些加氢裂化装置投产时加入了加氢裂化催化剂,一段时间后产生的现象是第一床层没有升温,起初大家认为是因为温度没有达到活性炭的要求。
但长时间之后温度不断升高,入口最高温度竟然到达了376℃,这足以说明第一床层的催化剂失活。
几年后发现第二床层的催化剂升温速度减慢,催化剂活性降低。
经调查分析,所研究的中国石油吉林化学股份公司炼油厂所用的是大庆油,油质好,生产反应平稳,排除结焦和烧结的原因。
加氢裂化反应影响因素
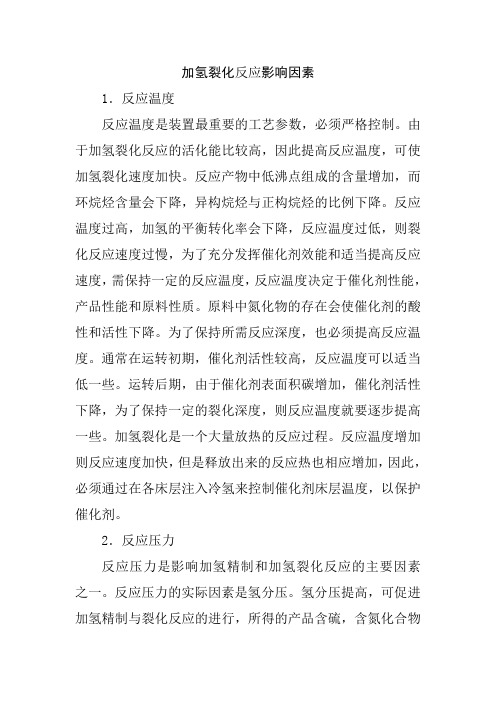
加氢裂化反应影响因素1.反应温度反应温度是装置最重要的工艺参数,必须严格控制。
由于加氢裂化反应的活化能比较高,因此提高反应温度,可使加氢裂化速度加快。
反应产物中低沸点组成的含量增加,而环烷烃含量会下降,异构烷烃与正构烷烃的比例下降。
反应温度过高,加氢的平衡转化率会下降,反应温度过低,则裂化反应速度过慢,为了充分发挥催化剂效能和适当提高反应速度,需保持一定的反应温度,反应温度决定于催化剂性能,产品性能和原料性质。
原料中氮化物的存在会使催化剂的酸性和活性下降。
为了保持所需反应深度,也必须提高反应温度。
通常在运转初期,催化剂活性较高,反应温度可以适当低一些。
运转后期,由于催化剂表面积碳增加,催化剂活性下降,为了保持一定的裂化深度,则反应温度就要逐步提高一些。
加氢裂化是一个大量放热的反应过程。
反应温度增加则反应速度加快,但是释放出来的反应热也相应增加,因此,必须通过在各床层注入冷氢来控制催化剂床层温度,以保护催化剂。
2.反应压力反应压力是影响加氢精制和加氢裂化反应的主要因素之一。
反应压力的实际因素是氢分压。
氢分压提高,可促进加氢精制与裂化反应的进行,所得的产品含硫,含氮化合物减少,更重要的是可减少结焦,保持催化剂活化,提高催化剂的稳定性。
反应器中的氢分压等于油汽加上循环氢的总压与氢气占全部气体分子数的乘积。
本装置补充氢纯度确定为99.9%。
从经济角度出发,不采用提高补充氢纯度的办法来提高氢分压。
3.氢油比氢油体积比有两种,其一是反应器入口的氢油比,其二是总冷氢油比。
反应器入口氢油比是每小时通过反应器内氢气(循环氢气+新氢)体积与每小时通过的原料油体积之比。
(单位为Nm3 /m3)。
总冷氢油体积比是每小时通入反应器的总冷氢气体积总和与每小时通过的原料油体积之比。
在加氢反应器中只有一部分氢气起反应。
大部分氢气仍以自由状态存在。
采用高氢油比,可提高氢分压,有利于传质和加氢反应的进行,在一定范围内防止油料在催化剂表面结焦。
加氢裂化技术问题研究报告

加氢裂化技术问题研究报告加氢裂化技术问题研究报告摘要:加氢裂化技术在石油化工工业中具有重要地位,但在实际应用中也存在一些问题。
本文针对加氢裂化技术存在的问题进行了深入分析和研究,探讨了其产生的原因,并给出了相应的解决方法和建议。
一、引言加氢裂化技术是一种重要的石油化工技术,它可以将重质石油馏分转化为轻质石化产品。
然而,在实际应用中,我们发现加氢裂化技术存在一些问题,包括产物选择性、催化剂失活、设备结焦等。
本文将对这些问题进行详细研究,以期为加氢裂化技术的进一步发展提供参考。
二、问题一:产物选择性在加氢裂化过程中,产物选择性是一个很重要的指标。
目前存在的问题是,由于催化剂表面存在一些缺陷,导致裂解反应选择性较低。
为了解决这个问题,我们采用了活性组分的改性方法,通过表面改性提高催化剂的选择性。
三、问题二:催化剂失活加氢裂化催化剂是实现反应的关键。
然而,在长时间使用后,催化剂会发生失活,导致反应效果下降。
我们的研究发现,催化剂失活主要是由于金属杂质的存在和随时间的积累所导致的。
因此,我们提出了一种定期热解和再生催化剂的方法,可以保持催化剂的活性和稳定性。
四、问题三:设备结焦加氢裂化设备中常常会出现结焦问题,严重影响了反应的进行。
造成设备结焦主要是因为反应温度过高、进料中含有杂质和反应气氛失控等原因。
为了解决这个问题,我们可以通过优化反应温度控制、改变进料组分和研究最佳反应气氛等措施,减少设备结焦的发生,提高设备稳定性。
五、问题四:环境污染加氢裂化技术在使用过程中产生的废气和废水对环境造成了一定的污染。
为了减少环境污染,我们提出了一种废气净化和废水处理的方法,通过物理和化学方法去除废气中的有害物质,并对废水进行深度处理,以达到排放标准。
六、结论与展望通过对加氢裂化技术问题的研究,我们发现了其产生的原因,并提出了相应的解决方法和建议,以期解决加氢裂化技术存在的问题,提高其效率和可靠性。
未来,我们将进一步研究和改进加氢裂化技术,推动其在石油化工领域的发展。
催化剂失活的原因和解决措施
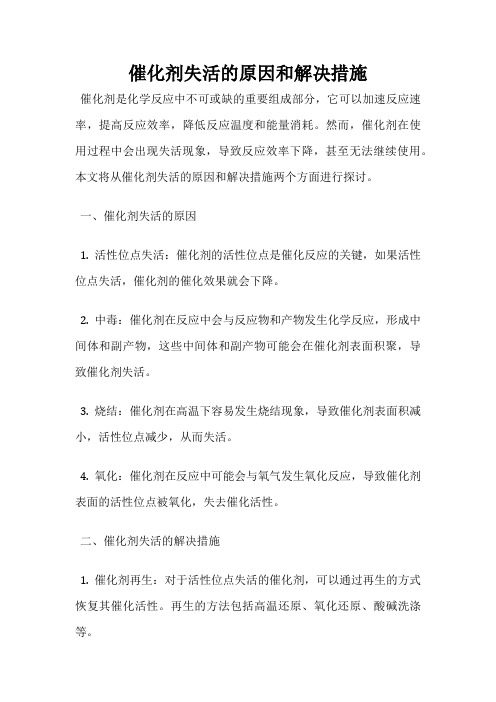
催化剂失活的原因和解决措施催化剂是化学反应中不可或缺的重要组成部分,它可以加速反应速率,提高反应效率,降低反应温度和能量消耗。
然而,催化剂在使用过程中会出现失活现象,导致反应效率下降,甚至无法继续使用。
本文将从催化剂失活的原因和解决措施两个方面进行探讨。
一、催化剂失活的原因1. 活性位点失活:催化剂的活性位点是催化反应的关键,如果活性位点失活,催化剂的催化效果就会下降。
2. 中毒:催化剂在反应中会与反应物和产物发生化学反应,形成中间体和副产物,这些中间体和副产物可能会在催化剂表面积聚,导致催化剂失活。
3. 烧结:催化剂在高温下容易发生烧结现象,导致催化剂表面积减小,活性位点减少,从而失活。
4. 氧化:催化剂在反应中可能会与氧气发生氧化反应,导致催化剂表面的活性位点被氧化,失去催化活性。
二、催化剂失活的解决措施1. 催化剂再生:对于活性位点失活的催化剂,可以通过再生的方式恢复其催化活性。
再生的方法包括高温还原、氧化还原、酸碱洗涤等。
2. 催化剂改性:对于容易中毒的催化剂,可以通过改性的方式增强其抗中毒能力。
改性的方法包括添加助剂、改变催化剂结构等。
3. 催化剂保护:对于容易烧结和氧化的催化剂,可以通过保护的方式延长其使用寿命。
保护的方法包括降低反应温度、控制反应气氛、添加稳定剂等。
4. 催化剂替换:对于失活严重的催化剂,只能通过替换的方式来解决。
替换的催化剂应具有更好的稳定性和催化活性。
催化剂失活是催化反应中不可避免的问题,但可以通过再生、改性、保护和替换等方式来解决。
在实际应用中,需要根据具体情况选择合适的解决措施,以保证催化反应的高效进行。
催化装置催化剂失活与破损原因分析及解决措施
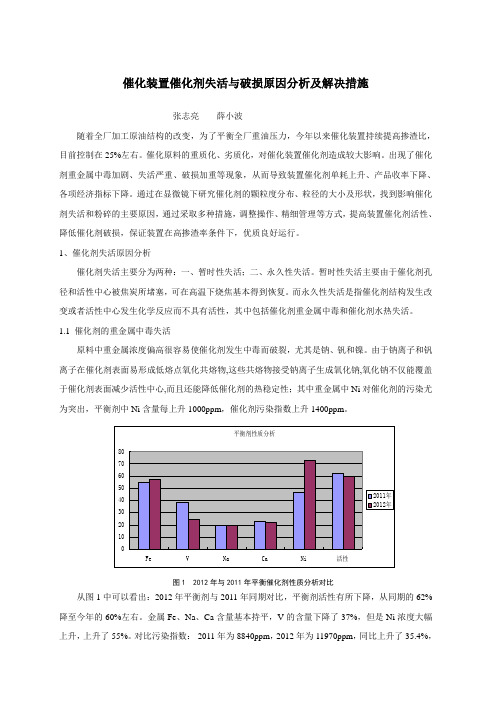
催化装置催化剂失活与破损原因分析及解决措施张志亮薛小波随着全厂加工原油结构的改变,为了平衡全厂重油压力,今年以来催化装置持续提高掺渣比,目前控制在25%左右。
催化原料的重质化、劣质化,对催化装置催化剂造成较大影响。
出现了催化剂重金属中毒加剧、失活严重、破损加重等现象,从而导致装置催化剂单耗上升、产品收率下降、各项经济指标下降。
通过在显微镜下研究催化剂的颗粒度分布、粒径的大小及形状,找到影响催化剂失活和粉碎的主要原因,通过采取多种措施,调整操作、精细管理等方式,提高装置催化剂活性、降低催化剂破损,保证装置在高掺渣率条件下,优质良好运行。
1、催化剂失活原因分析催化剂失活主要分为两种:一、暂时性失活;二、永久性失活。
暂时性失活主要由于催化剂孔径和活性中心被焦炭所堵塞,可在高温下烧焦基本得到恢复。
而永久性失活是指催化剂结构发生改变或者活性中心发生化学反应而不具有活性,其中包括催化剂重金属中毒和催化剂水热失活。
1.1 催化剂的重金属中毒失活原料中重金属浓度偏高很容易使催化剂发生中毒而破裂,尤其是钠、钒和镍。
由于钠离子和钒离子在催化剂表面易形成低熔点氧化共熔物,这些共熔物接受钠离子生成氧化钠,氧化钠不仅能覆盖于催化剂表面减少活性中心,而且还能降低催化剂的热稳定性;其中重金属中Ni对催化剂的污染尤为突出,平衡剂中Ni含量每上升1000ppm,催化剂污染指数上升1400ppm。
图1 2012年与2011年平衡催化剂性质分析对比从图1中可以看出:2012年平衡剂与2011年同期对比,平衡剂活性有所下降,从同期的62%降至今年的60%左右。
金属Fe、Na、Ca含量基本持平,V的含量下降了37%,但是Ni浓度大幅上升,上升了55%。
对比污染指数:2011年为8840ppm,2012年为11970ppm,同比上升了35.4%,从而导致催化剂活性下降了2~3个百分点。
因此,目前催化剂活性下降的重要原因是Ni含量大幅上升。
加氢催化剂再生技术的研究进展

加氢催化剂再生技术的研究进展发布时间:2022-07-15T06:42:40.581Z 来源:《科学与技术》2022年第5期3月作者:孙亮[导读] 加氢催化剂再生技术的原理与催化剂失活的原因之间存在紧密的关联孙亮中国石油玉门油田分公司炼油化工总厂加氢车间甘肃玉门 735200摘要:加氢催化剂再生技术的原理与催化剂失活的原因之间存在紧密的关联。
而催化剂失活的原因可分为中毒性失活、烧结及热失活、结焦和堵塞失活。
高温加氢汽化再生催化剂技术是当前应用最广泛的技术,本文对此进行介绍,供参考。
关键词:加强氢催化剂再生;失活原因;高温气化引言:加强氢催化剂是指化合物与氢进行加成反应时添加的催化剂,主要用于产品生产、原料净化、产物精制等。
制备加氢催化剂时,原料来源至关重要。
比如在炼油化工领域,进行原油提炼的过程中会产生大量废催化剂,即失活催化剂。
有资料显示,针对废催化剂进行科学、合理处理可以对炼油行业的经济效益产生正面影响,是实践可持续发展理念的重要举措。
除此之外,由于加氢催化剂占炼油废催化剂的比例较大,故围绕加氢催化剂再生技术进行开发对相关行业的发展均具有重要意义。
1.催化剂的失活形式与再生原理分析催化剂再生技术在一定程度上决定催化剂的采购成本,对相关领域的企业而言,若掌握催化剂再生技术,可有效降低成本支出,达到提高利润空间的目的[1]。
提及催化剂的再生技术,首先需要明确催化剂的“失活”与“再生”相关的原理。
从化学和分子学角度来看,催化剂的失活可根据“能否有效恢复活性”分为“暂时性失活”及“永久性失活”两种形式。
导致催化剂失活的原因可分为中毒性失活、烧结及热失活、结焦和堵塞引起的失活。
具体而言:①中毒引起的失活。
可进一步分为暂时性中毒(可逆中毒,有毒成分在活性中心上进行吸附和化合,生成的键去强度相对较弱,通过特定的方法去除毒性成分后,便可恢复催化剂的活性,其原本的性质不会受到影响)、永久中毒(不可逆中毒,有毒物质与催化剂内的活性组分发生了不可逆的相互作用,生成的化学键强度极大,常规方法无法恢复催化剂原本的性状,强行恢复后也失去原有性能)、选择性中毒(催化剂接触某类有毒物质之后,其原先具备的某种性能,即对某种反应的催化能力会失去,但却保留其他催化能力)。
固定床渣油加氢催化剂失活的原因分析及对策
固定床渣油加氢催化剂失活的原因分析及对策曾松【摘要】固定床渣油加氢技术是重油改质的重要手段,是优化重油催化裂化装置原料的主要措施,而固定床渣油加氢装置催化剂的价格昂贵、使用周期短且不具再生使用性,因此探讨固定床渣油加氢催化剂失活的原因并采取相应的对策,对延长催化剂的使用周期有积极的意义.通过对固定床渣油加氢装置催化剂末期运行的现象、废旧催化剂化学组成等方面的分析,发现导致固定床渣油加氢装置催化剂失活的主要原因是积炭和金属沉积.同时分析催化剂级配装填的比例、催化剂硫化、原料油的性质和反应温度的分布等因素对固定床渣油加氢催化剂失活的影响,提出了采用抗积炭和容垢能力高的催化剂,进行合理的催化剂级配装填,控制好原料的性质,调整各床层反应温度的匹配分布和控制好催化剂开工条件等措施,可有效延长催化剂的使用寿命.%Fixed-bed residue hydrogenation is an important process to upgrade heavy oil and a major measure to optimize feedstock of heavy oil fluidized catalytic cracking units. However, the catalysts for the said process are expensive in addition to the short service life as well as the non-regenerative nature, which makes it worthy to study the causes of fixed-bed residue hydrogenation catalyst deactivation and to take corresponding countermeasures to extend the catalysts life. The analysis of EOR performances of fixed-bed residue hydrotreating catalysts and chemical compositions of spent catalysts has found out that the main causes of cata lyst deactivation are carbon and metal depositions. The impacts of proportion of catalyst graded loading, cata lyst pre-sulfiding, feedstock properties and distribution of reaction temperatures on catalystdeactivation are studied. The use of coke-deposition-resistant catalystswith good deposition capacity, appropriate graded load ing of catalysts, good control of feedstocks, good adjustment of bed temperature distribution and good control of catalyst start-up conditions are recommended to extend the service life of catalysts.【期刊名称】《炼油技术与工程》【年(卷),期】2011(041)009【总页数】5页(P39-43)【关键词】渣油加氢;催化剂;失活;级配;硫化【作者】曾松【作者单位】中国石油化工股份有限公司茂名分公司,广东省茂名市525011【正文语种】中文随着原油日益重质化、劣质化和轻油需求量的不断增加,提高原油加工深度已是企业提高经济效益的必由之路。
加氢裂化操作因素变化的分析
操作参数对反应过程的影响主要讨论反应温度、压力、氢油比及空速等操作参数对加氢裂化转化深度、产品分布以及产品质量的影响。
讨论的前提:反应器物流近似于活塞流且径向温差很小(不存在沟流、返混)。
一.反应温度1.CAT、CAT1、CAT2、BAT11、BAT12、BAT13、BAT21、BAT22、BAT23、BAT24介绍CAT(Catalyzer Average Temperature)为一个反应器中催化剂的平均温度,其值等于该反应器中每一床层温度和该床层的催化剂在反应器总催化剂中所占体积百分数乘积之和(加权平均温度)。
BAT(Bed Average Temperature)为床层的平均温度,其值等于某一床层入口温度和出口温度的算术平均值。
温度分布是指每个反应器所有床层从上到下每个床层出入口温度所形成的曲线图。
一般要求在同一反应器中每个床层进出口温度是相同的,这样所形成的温度分布为“平坦的”。
相对于平坦的温度分布曲线,有上升的温度曲线和下降的温度曲线,两相比较,有相同的转化率下,平坦的温度分布曲线使催化剂有较均匀的工作条件使催化剂寿命延长。
反应温度对反应过程的影响机理简述。
反应器中的反应主要分加氢精制反应和加氢裂化反应。
精制反应器中以加氢精制反应为主,伴有加氢裂化反应,裂化反应器中以加氢裂化反应为主,伴有加氢精制反应。
前面花主任在讲《加氢裂化过程的化学反应》时对加氢裂化过程中涉及到的各类化学反应讲得比较详细。
从反应动力学和反应热力学两个角度综合分析,得出的结论是提高反应温度有利于精制反应和裂化反应的进行。
2.反应温度对转化率的影响转化率:加氢裂化是重质烃/非烃复杂混合物轻质化的过程,过程的裂化转化率理论上指的是通过反应生成进料中原来未含有的轻馏分产率。
但有两种情况需要说明:1)由于进料往往为很宽的馏分油,进料本身就含有一部分轻质产品组分,它并非由裂化产生;2)进料中最重的部分通过轻微裂化变成较小的分子,但其沸点范围仍在原料范围之中而未进入轻质产品,还是比我们需要的产品重。
加氢工艺异常问题分析
加氢工艺异常问题分析引言催化加氢指有机化合物中一个或几个不饱和的官能团在催化剂作用下与氢气加成。
催化加氢在炼油化工和有机化工中有十分广泛的应用。
在石油加工过程中,催化加氢对于提高原油加工深度、合理利用石油资源、改善产品质量、提高轻质油收率以及减少大气污染都具有重要意义。
尤其随着原油日益变重变劣,催化加氢更显重要。
目前石油工业中的加氢过程主要有加氢裂化、加氢精制、临氢降凝、润滑油加氢等。
在有机化工中,合成氨、合成甲醇、丁二烯、苯乙烯的制取等,都是催化加氢过程。
此外,催化加氢还用于许多化工产品的精制过程。
1 催化剂安全理论催化加氢反应分为多相催化加氢反应和均相催化加氢反应两种。
常用加氢工艺催化剂主要有以下几种:Ⅷ族过渡金属元素的金属催化剂,如铂、钯、镍载体催化剂及骨架镍等,用于烯烃选择加氢,油脂加氢等;金属氧化物催化剂,如氧化铜-亚铬酸铜、氧化铝-氧化锌-氧化铬催化剂等,用于醛、酮、酯、酸及CO等的加氢;金属硫化物催化剂,如镍-钼硫化物等,用于石油炼制中的加氢精制等;络合催化剂用于均相液相加氢。
催化剂的活性对于反应过程起到至关重要的作用。
一旦催化剂失活,将对加氢过程产生致命影响。
引起加氢催化剂失活的原因主要有:碳沉积、金属沉积、杂质污染、碱性中毒、金属形态变化。
碱性物质如碱性氮化合物吸附在加氢催化剂的酸性中心上引起中毒,影响裂化反应。
原料中的杂质,如焦粉等固体颗粒堵塞催化剂孔口,覆盖活性中心。
上游装置腐蚀所带入的铁,造成床层堵塞压降增大;硫化铁具有强的脱氢活性,促进生焦;正常生产中催化剂的积碳、结焦引起活性下降,这个问题可以再生解决;催化剂内进水,易造成催化剂颗粒破损床层超温引起催化剂金属和载体形态破坏失活。
催化剂再生是指利用含氧气体烧除催化剂表面上的积碳,来恢复催化剂的活性,即氧化再生。
催化剂的再生可以分为器内再生和器外再生两种方式。
所用介质一般为蒸汽-空气介质或氮气-空气介质。
催化剂再生不仅为生产节约资金,也避免了废催化剂掩埋处理时对环境污染,更重要的是将社会资源得到充分利用。
加氢裂化催化剂效率与寿命的影响因素与提升对策探讨
加氢裂化催化剂效率与寿命的影响因素与提升对策探讨在加氢装置的使用过程中,其主要的成本来源于催化剂,通过延长催化剂的寿命,提升催化剂的效率可以获得显著的经济效益。
立足于现状,首先介绍了加氢裂化催化剂的定义与特征,其次对影响加氢裂化催化剂效率与寿命的因素进行了解析,并在最后提出了相应的加氢裂化催化剂寿命、效率的优化对策,希望可以有效延长使用寿命,取得良好的运行成果。
标签:加氢裂化催化剂;效率;寿命;影响因素引言加氢裂化反应主要包括加氢脱硫脱氮以及脱氧等环节。
在设备运行过程中,选择合适的催化剂来参与生产将决定生产的效率与经济效益。
某生产厂家选择FR1、481-2催化剂,生产能力仅为国外的三分之一,效率不及国外同等规模企业的一半。
为了解决这个问题,企业进行了技术研讨,取得了相应的成果。
为了进一步介绍加氢裂化催化剂寿命延长策略,现就其基本定义介绍如下。
一、加氢裂化催化剂概述加氢裂化催化剂在工业生产中主要扮演催化助力的角色。
从整个反应过程上来看,加氢精制要求脱除掉各种油品的杂质,整个过程中烃分子的结构不应出现较大的变化,所以需要尽可能保持缓和的工作状态。
在加氢精制的过程中,除了基本的反应温度控制,还需要做好操作压力控制、氢蜡比控制等等,而最为关键的就是加氢裂化催化剂的选择。
通过选择合适的加氢裂化催化剂,可以有效促进反应向着正反应的方向进行,同时自身的活性条件也决定了运行的效率。
但是,由于加氢裂化反应的环境十分复杂,不同类型的加氢裂化催化剂在寿命、效率的平衡方面难以处理好,所以很多情况下还是需要通过大量的实验验证后才能够得出结论。
二、加氢裂化催化剂效率与寿命的影响因素1.催化剂自身条件加氢裂化催化剂自身条件是其效率与寿命影响最大的因素之一。
在使用过程中,催化剂主要在相对缓和的运行状态下进行反应,所以可以通过适当的酸性物质来满足活性需求,但是这并不是说就不需要考虑到高质量的问题。
实际上,大多数企业都认为加氢裂化催化剂的质量是最终效率与寿命的决定性因素,而事实上也正是如此。
- 1、下载文档前请自行甄别文档内容的完整性,平台不提供额外的编辑、内容补充、找答案等附加服务。
- 2、"仅部分预览"的文档,不可在线预览部分如存在完整性等问题,可反馈申请退款(可完整预览的文档不适用该条件!)。
- 3、如文档侵犯您的权益,请联系客服反馈,我们会尽快为您处理(人工客服工作时间:9:00-18:30)。
关于加氢裂化催化剂失活的原因分析
【摘要】近二十年来,我国的加氢裂化催化剂不断发展,步入了一个新的发展阶段。
本文通过回顾加氢裂化工艺的发展路程,着重介绍研究开发的催化剂的应用情况,以此来分析加氢裂化催化剂失活的原因。
求得解决方法使其得以恢复。
【关键词】加氢裂化催化剂失活
1 前言
加氢裂化发展迅猛的主要原因就是所需的加工原料应用范围广泛,大致包括重质柴油、焦化蜡油、减压馏分油、脱沥青油、重油催化裂化轻循环油和常压渣油等等,涉及了从石脑油到渣油的范围。
数字显示,1998年加工能力分布,世界为200Mt/a,占原油蒸馏能力的5%;我国为13.68 Mt/a,占原油蒸馏能力的5.6%。
关于加氢裂化催化剂失活的问题,要在生产中采取相应措施恢复催化剂活性,保证装置的正常运作。
本文最后还通过分析我国汽油、柴油、煤油和润滑油的发展需求,讨论加氢裂化催化剂在今后的发展方向和动力。
2 加氢裂化催化剂失活原因
催化剂失活是一种催化剂反应率与时间增长呈现反比例的现象。
催化剂失活的三种类型主要是:催化剂中毒失活、催化剂烧结失活和催化剂阻塞失活。
催化剂的中毒失活是指一些有害物质堵塞孔道导致催化剂活性和选择性下降的过程。
催化剂烧结失活是指由于高温造成催化剂烧结,在其表面形成炭质,活性组织被载体包围覆盖,孔道被结焦现象阻塞,这就导致了反应物分子难以进入活性中心。
催化剂积碳失活是因为催化剂的使用使其表面产生了碳的沉积物,因此导致催化剂的活性下降。
对于上面三种失活方式,在现实的加氢裂化装置中得到了体现。
在一些加氢裂化装置投产时加入了加氢裂化催化剂,一段时间后产生的现象是第一床层没有升温,起初大家认为是因为温度没有达到活性炭的要求。
但长时间之后温度不断升高,入口最高温度竟然到达了376℃,这足以说明第一床层的催化剂失活。
几年后发现第二床层的催化剂升温速度减慢,催化剂活性降低。
经调查分析,所研究的中国石油吉林化学股份公司炼油厂所用的是大庆油,油质好,生产反应平稳,排除结焦和烧结的原因。
经过分析发现原因是对催化剂的使用不恰当,产生催化剂中毒失活。
到了2000年时,加氢裂化反应装置的前两层都失去了活性,后两层也先后出现了裂化反应,因此必须持续保持一种高温状态来保证生产的进行。
但这样使操作难度加大,加速了催化剂活性降低。
3 加氢裂化催化剂活性的恢复
根据加氢裂化催化剂失活的三种类型来分析催化剂活性恢复的问题。
专家表示,加氢裂化催化剂中毒失活是可逆的,尤其是其中的氮中毒现象。
如果保持裂化段温度恒定不变,降低精制油氮含量会使转化率上升,并且随着不断的运转而
持续升高。
这是因为低氮油对有机氮化物有吸附作用,而刚好这些有机氮化物吸附在催化剂活性中心位置上。
对于催化剂的中毒现象,提高裂化段入口的温度,这也是分离氮化物和催化剂的方法,使得较少的催化剂中毒。
并且这种方法还可以激活催化剂活性,恢复催化剂在高温下的活性。
知道了这些原理,在以后的生产中要注意减低加氢精致生成油的氮含量,如果催化剂的活性依然很低,这表明单纯的依靠降低氮含量来减少中毒现象的作用并不够。
经过实例,将加氢裂化装置的前两床层催化剂的入口温度最大限度的提高使其到达380℃,经过几十天两个床层的温度提高,激活催化剂,使催化剂活性开始恢复。
但是如果只依靠升温是不够的,还应该加强降低氮含量。
将这两个方法相结合使用,经过长时间的运转,催化剂的活性逐渐恢复。
4 我国汽、柴、煤等能源的现状
汽油、柴油、煤油等均属于二次非可再生能源,我国的原油偏重,含蜡量偏高。
与国外相比我国的汽油柴油等油馏分收率低。
数字显示,汽油低了8%以上但不高于17%,柴油低在5%到12%之间。
我国60%的重油深度加工多采用催化裂化,加氢裂化却只占到10%左右。
我国柴油迅速增长,但是由于需求量过大,难以满足消费需求。
柴油中加氢精制油只占到20%左右,硫含量高且颜色差。
因此要着重提高柴油质量和柴汽比,应该做到发展加氢过程,提高加氢改质、加氢精制、加氢裂化等等。
煤油在我国主要是航空煤油占到85%左右,虽然产量有些低,但是通过加氢裂化和直馏方式获得可以满足市场消费需求。
5 加氢裂化催化剂发展的展望
随着经济的不断发展,在经济发展的同时越来越注重环境的保护,这就需要更多的清洁能源、石油化工原料等等清洁的燃料。
在今后的发展中,加氢裂化以柴油为重点,扩大馏分油加氢精制和缓和加氢裂化等都成了今后发展的重点。
加氢裂化经过几十年的发展,技术手段已经日趋成熟,但是为满足产品的需求,加氢裂化催化剂的更新换代很快,所以要着重开发新型的粘度高的加氢裂化催化剂和脱氮精致催化剂。
对于加氢预精致催化剂发展主要是要提高脱氮的性能,可通过采用二元化合物来减少结焦,延长装置的使用时间。
使用新型的催化材料,如金属碳化物、杂多酸化合物和金属氮化物等,改进设备来扩大生产力,增加收益,减低成本。
在未来加氢裂化技术将会保持很好的发展势头,并通过科学方法不断提高加氢裂化催化剂的活性。
6 结束语
催化剂因可以增加工业反映速率而被广泛应用于工业生产中,但是在催化剂的操作中会产生失活现象。
通过本文得知催化剂失活是因为原料中碱性氮过高产生中毒、积碳和烧结等现象。
因此,在生产中可以采取减低原料油中氮含量和升高催化剂温度等方法来增加催化剂的活性,延长生产周期,降低成本,提高经济效益。
通过对加氢裂化催化剂发展前景的展望,可以使企业走上一条更适合自己发展的道路,更加关注催化剂的再生和前景,将化工与科技相结合,提高加氢裂
化催化剂的活性,使其更适合工业的发展。
参考文献
[1] 王从梁.蜡油加氢裂化装置反应器飞温原因分析及对策[J].广东化工,2011,12(3):84-86
[2] 潘琦琨,张维.360×104t/a加氢裂化装置运行分析[J].中外能源,2012,5(7):44-46
[3] 姚春峰,王辉.Ⅱ套加氢裂化装置产品重石脑油总硫含量控制[J].中外能源,2012,8(9):175-178
[4] 陈尊仲.加氢裂化催化剂湿法硫化的工业应用[J].炼油技术与工程,2012,3(1):190-192。