拉伸试验的作用及试样的形状及尺寸
材料力学性能拉伸试验报告

材料力学性能拉伸试验报告材化08李文迪40860044. . .[试验目的]1. 测定低碳钢在退火、正火和淬火三种不同热处理状态下的强度与塑性性能。
2. 测定低碳钢的应变硬化指数和应变硬化系数。
[试验材料]通过室温拉伸试验完成上述性能测试工作,测试过程执行GB/T228-2002:金属材料室温拉伸试验方法:1.1试验材料:退火低碳钢,正火低碳钢,淬火低碳钢的R4标准试样各一个。
1.2热处理状态及组织性能特点简述:1.2.1退火低碳钢:将钢加热到Ac3或Ac1以上30-50℃,保温一段时间后,缓慢而均匀的冷却称为退火。
特点:退火可以降低硬度,使材料便于切削加工,并使钢的晶粒细化,消除应力。
1.2.2正火低碳钢:将钢加热到Ac3或Accm以上30-50℃,保温后在空气中冷却称为正火。
特点:许多碳素钢和合金钢正火后,各项机械性能均较好,可以细化晶粒。
1.2.3淬火低碳钢:对于亚共析钢,即低碳钢和中碳钢加热到Ac3以上30-50℃,在此温度下保持一段时间,使钢的组织全部变成奥氏体,然后快速冷却(水冷或油冷),使奥氏体来不及分解而形成马氏体组织,称为淬火。
特点:硬度大,适合对硬度有特殊要求的部件。
1.3试样规格尺寸:采用R4试样。
参数如下:1.4公差要求[试验原理].. ..1.原理简介:材料的机械性能指标是由拉伸破坏试验来确定的,由试验可知弹性阶段卸荷后,试样变形立即消失,这种变形是弹性变形。
当负荷增加到一定值时,测力度盘的指针停止转动或来回摆动,拉伸图上出现了锯齿平台,即荷载不增加的情况。
当屈服到一定下,试样继续伸长,材料处在屈服阶段。
此时可记录下屈服强度ReL 程度后,材料又重新具有了抵抗变形的能力,材料处在强化阶段。
此阶段:强化后的材料就产生了残余应变,卸载后再重新加载,具有和原材料不同的性质,材料的强度提高了。
但是断裂后的残余变形比原来降低了。
这种常温下经塑性变形后,材料强度提高,塑性降低的现象称为冷作硬化。
2拉伸试验
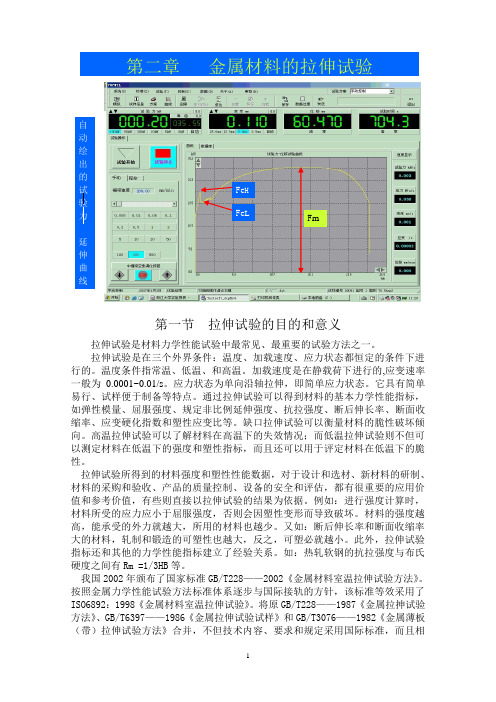
物体因外力作用产生变形,其内部各部分之间因相对位置的变化而引起的相互作用称为内力.众所周知,即使不受外力,物体各质点间也存在相互作用力.我们所称的内力,是在外力作用下,上述各作用力的变化量,随着该变化量的逐渐加大,物体内部发生一系列的物理变化,当到达某一极限时,物体就会被破坏,该极限与物体的强度有直接关系.
第二阶段为屈服阶段(cd段),即试样屈服于外力产生较大塑性变形阶段。此时试样伸长急剧增加,但载荷却在很小的范围内波动,若忽略这一微小的波动,F- 曲线上该段可见一水平线段,该段对应的外力Fs以表示,这是由弹性变形阶段到塑性变形阶段的分界点。
第三阶段为强化阶段(de)(均匀塑性变形阶段)。试样屈服变形阶段结束后,要使之继续变形,就要继续施加外力,克服试样内部不断增加的抗变形力。因为材料本身在塑性变形中会产生强化,也称为加工硬化。该阶段的塑性变形比弹性变形大得多,所以曲线上可见 有很大增加。由d点开始,屈服结束,试样某部位产生塑性变形,截面变小,但加工硬化使该部位抗变形力增加,这样,下一步变形就转移到试样的其它部位。由此,在de段试样各部位产生较均匀的塑性变形之间近似遵循直线关系,且此直径gh与弹性现阶段内直线oa近似平行。由此可见,试样的变形包括了弹性变形 e和塑性变形 p。如卸载时的载荷,此后原则上遵循着原来的拉伸曲线。
Lo 试样原始标距。试验前,测量试样伸长所标记的标距长度。
Lu 试样断后标距。试样拉断后,将断口对接在一起时试样的标距长度。
Le 引伸计标距。用引伸计测量试样延伸所使用的试样部分的长度。
So 试样平行长度部分的原始横截面积
Su 试样拉断后缩颈处的最小横截面积
(一)圆截面试样
Lc≥Lo+d/2仲裁试验Lo+2d Lo=5d,10d或定标距 r≥0.75d粗糙度≤0.8µm
塑料橡胶 拉伸试验步骤(目的原理步骤结果处理)
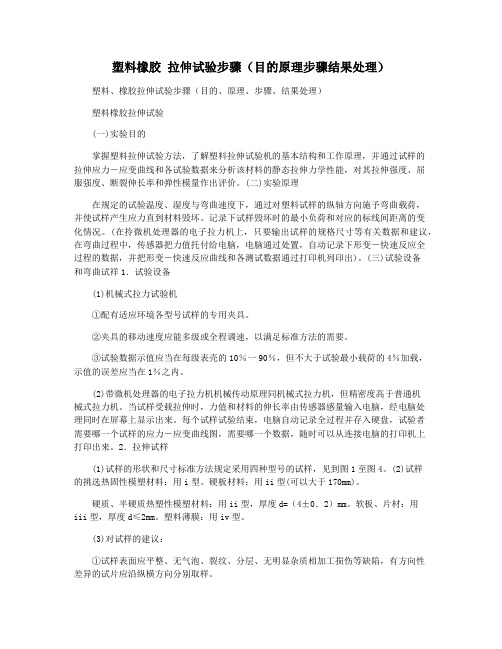
塑料橡胶拉伸试验步骤(目的原理步骤结果处理)塑料、橡胶拉伸试验步骤(目的、原理、步骤、结果处理)塑料橡胶拉伸试验(一)实验目的掌握塑料拉伸试验方法,了解塑料拉伸试验机的基本结构和工作原理,并通过试样的拉伸应力―应变曲线和各试验数据来分析该材料的静态拉伸力学性能,对其拉伸强度、屈服强度、断裂伸长率和弹性模量作出评价。
(二)实验原理在规定的试验温度、湿度与弯曲速度下,通过对塑料试样的纵轴方向施予弯曲载荷,并使试样产生应力直到材料毁坏。
记录下试样毁坏时的最小负荷和对应的标线间距离的变化情况。
(在拎微机处理器的电子拉力机上,只要输出试样的规格尺寸等有关数据和建议,在弯曲过程中,传感器把力值托付给电脑,电脑通过处置,自动记录下形变―快速反应全过程的数据,并把形变―快速反应曲线和各测试数据通过打印机列印出)。
(三)试验设备和弯曲试祥1.试验设备(1)机械式拉力试验机①配有适应环境各型号试样的专用夹具。
②夹具的移动速度应能多级或全程调速,以满足标准方法的需要。
③试验数据示值应当在每级表壳的10%一90%,但不大于试验最小载荷的4%加载,示值的误差应当在1%之内。
(2)带微机处理器的电子拉力机机械传动原理同机械式拉力机,但精密度高于普通机械式拉力机。
当试样受载拉伸时,力值和材料的伸长率由传感器感量输入电脑,经电脑处理同时在屏幕上显示出来。
每个试样试验结束,电脑自动记录全过程并存入硬盘,试验者需要哪一个试样的应力―应变曲线图,需要哪一个数据,随时可以从连接电脑的打印机上打印出来。
2.拉伸试样(1)试样的形状和尺寸标准方法规定采用四种型号的试样,见到图1至图4。
(2)试样的挑选热固性模塑材料:用i型。
硬板材料:用ii型(可以大于170mm)。
硬质、半硬质热塑性模塑材料:用ii型,厚度d=(4±0.2)mm。
软板、片材:用iii型,厚度d≤2mm。
塑料薄膜:用iv型。
(3)对试样的建议:①试样表面应平整、无气泡、裂纹、分层、无明显杂质相加工损伤等缺陷,有方向性差异的试片应沿纵横方向分别取样。
拉伸试验规程
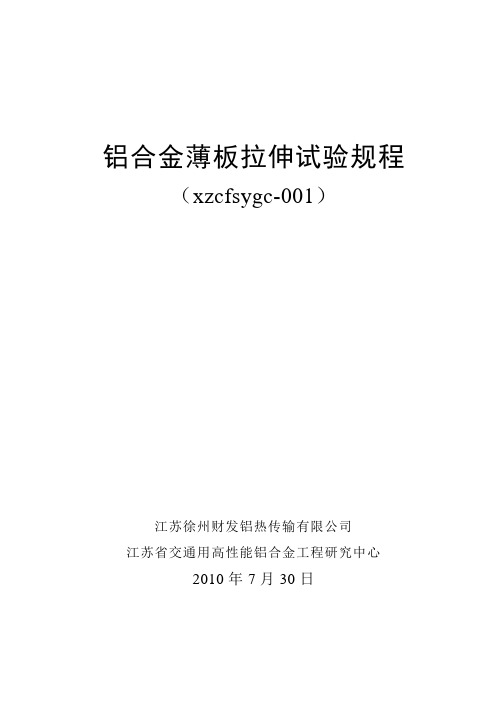
铝合金薄板拉伸试验规程(xzcfsygc-001)江苏徐州财发铝热传输有限公司江苏省交通用高性能铝合金工程研究中心2010年7月30日铝合金薄板拉伸试样加工和试验按GB/T 5027-1999,GB/T 5028-1999和GB/T 228-2002规定执行。
1 拉伸试样1.1 取样取样部位、方向和数量应符合相关产品标准要求或经双方协商确定。
1.2 试样形状通常情况下采用图示带肩试样。
通过协商,也可以采用平行边试样(不带肩试样)。
1.3 试样尺寸1.3.1 平行长度应不小于L0+b0/2。
仲裁试验时,平行长度应为L0+2b0。
1.3.2 宽度不大于20mm的不带肩试样,夹头间的自由长度应不小于L0+3b0。
表两种非比例试样的尺寸mm1.4 试样制备1.4.1试样毛坯必须单个切取。
试样均须进行机加工以消除加工硬化影响。
对于极薄试样,将切取的等宽毛坯用油纸逐片分隔,在两外侧夹上等宽度的较厚板一起加工,直至达到要求的试样。
1.4.2 试样原始标距内宽度两侧不平行度尽可能小,最大宽度与最小宽度之差不应大于标距内测量宽度平均值的0.1%(试样1为0.01mm,试样2为0.02mm)。
1.4.3 除非另有规定,试样厚度应是产品全厚度。
在试样标距内,任意两处的厚度值之差应不大于0.01mm;当厚度小于1.0mm时,应不大于公称厚度的1%。
1.4.4 试样表面不应有划伤等缺陷。
2 常规室温拉伸性能试验常规室温拉伸性能试验指在室温下对上述试样进行拉伸试验操作,主要测定材料的抗拉强度(破断强度)、屈服强度、延伸率和断面收缩率等。
2.1 试验要求2.1.1 试验设备的准确度试验机应按GB/T 16825进行检验,并应为1级或优于1级准确度。
2.1.2 试验速率(1)测定屈服极限(R eH、R eL)的试验速率。
试验速率取决于材料特性。
铝的拉伸弹性模量为70GPa,所以在弹性范围直至上屈服点,应力速率应为2~20MPa/s,在试样平行长度的屈服期间应变速率应在0.00025/s~0.0025/s之间。
拉伸性能测试

拉伸性能测试(静态)拉伸性能测试主要确定材料的拉伸强度,为研究、开发、工程设计以及质量控制和标准规范提供数据。
在拉伸测试中,薄的薄膜会遇到一定困难。
拉伸试样的切边必须没有划痕或裂缝,避免薄膜从这些地方开始过早破裂。
对于更薄的薄膜,夹头表面是个问题。
必须避免夹头发滑、夹头处试样破裂。
任何防止夹头处试样发滑和破裂,而且不干扰试样测试部分的技术如在表面上使用薄的橡胶涂层或使用纱布等都可以接受。
从拉伸性能测试中可以得到拉伸模量、断裂伸长率、屈服应力和应变、拉伸强度和拉伸断裂能等材料性能。
ASTM D 638 (通用)[4]和ASTM D 882 [5](薄膜)中给出了塑料的拉伸性能(静态)。
拉伸强度拉伸强度是用最大载荷除以试样的初始截面面积得到的,表示为单位面积上的力(通常用MPa为单位)。
屈服强度屈服强度是屈服点处的载荷除以试样的初始截面面积得到的.用单位面积上的力(单位MPa)表示,通常有三位有效数字。
拉伸弹性模量拉伸弹性模量(简称为弹性模量,E)是刚性指数,而拉伸断裂能(TEB,或韧性)是断裂点处试样单位体积所吸收的总能量。
拉伸弹性模量计算如下:在载荷-拉伸曲线上初始线性部分画一条切线,在切线上任选一点,用拉伸力除以相应的应变即得(单位为MPa),实验报告通常有三位有效数字。
正割模量(应力-应变间没有初始线性比值时)定义为指定应变处的值。
将应力-应变曲线下单位体积能积分得到TEB,或者将吸收的总能量除以试样原有厚度处的体积积分。
TEB表示为单位体积的能量(单位为MJ/m3),实验报告通常有两位有效数字。
拉伸断裂强度拉伸断裂强度的计算与拉伸强度一样,但要用断裂载荷,而不是最大载荷。
应该注意的是,在大多数情况中,拉伸强度和拉伸断裂强度值相等。
断裂伸长率断裂伸长率是断裂点的拉伸除以初始长度值。
实验报告通常有两位有效数字。
屈服伸长率屈服伸长率是屈服点处的拉伸除以试样的初始长度值,实验报告通常有两位有效数字。
拉伸试验

Stress
Strain
1、材料的局部破坏为主要原因;
2、设备的不完善;
Y
X Z
关于泊松比
问题与难点:
-在拉伸条件下,纤维聚合物复合材料的泊松比并非不变值,而是随着载荷的增 加而减小,有时会出现负的泊松比。 -分析其主要原因:泊松比的符号取决于增强纤维的铺设方向和顺序,反映在边 缘效应上。因此,对增强纤维的横向相对应变进行测量时困难;
解决办法:
-取厚与宽相同的承均质叠层的试样上测定泊松比,且由单向材料的试样测量, 并加载水平给予说明。
根据试验的目的不同 选择不同形状、尺寸的 试件。 要测定弹性常数该选 哪一种呢?
强度呢?
板样试件的加载
各向异性杆的变形特征 -对于各向异性材料,受轴向拉伸的杆不仅沿加载方向延伸,沿横向收 缩,而且在所有平行于坐标平面的面上受剪。与各向同性材料相反。
-在约束变形条件下,出 拉伸应力外,还产生弯曲 力和剪切力,从而导致变 形不均匀。 -此时,弯曲和剪切的影 响不仅取决于被测试材料 的弹性常数,而且取决于 试样的长宽比。
lL : 试样在基长lT 上的纵向变形;
i i 式中: lL / lL L和-lT / lT T 可直接用电阻应变片测量;
破坏模式
-纤维聚合物的破坏模式主要是由于增强叠层形式、各组分的材料的力学 性能及组分间的作用,工艺缺陷(空隙、纤维波纹度等)、以及试样尺寸 所决定。
几种破坏模式:
然而,当 时,试件破坏的层间剪应力 可能超过材料 的极限值。由于弯曲的结果,内层受载,而外层载荷不足。
拉伸试验的作用及试样的形状及尺寸
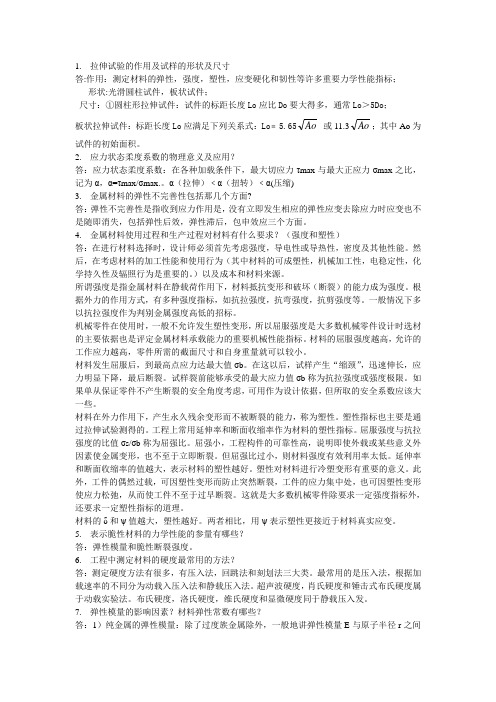
1.拉伸试验的作用及试样的形状及尺寸答:作用:测定材料的弹性,强度,塑性,应变硬化和韧性等许多重要力学性能指标;形状:光滑圆柱试件,板状试件;尺寸:①圆柱形拉伸试件:试件的标距长度Lo应比Do要大得多,通常Lo>5Do;板状拉伸试件:标距长度Lo应满足下列关系式:Lo﹦5.65Ao或11.3Ao;其中Ao为试件的初始面积。
2.应力状态柔度系数的物理意义及应用?答:应力状态柔度系数:在各种加载条件下,最大切应力τmax与最大正应力σmax之比,记为α,α=τmax/σmax.。
α(拉伸)﹤α(扭转)﹤α(压缩)3.金属材料的弹性不完善性包括那几个方面?答:弹性不完善性是指收到应力作用是,没有立即发生相应的弹性应变去除应力时应变也不是随即消失,包括弹性后效,弹性滞后,包申效应三个方面。
4.金属材料使用过程和生产过程对材料有什么要求?(强度和塑性)答:在进行材料选择时,设计师必须首先考虑强度,导电性或导热性,密度及其他性能。
然后,在考虑材料的加工性能和使用行为(其中材料的可成塑性,机械加工性,电稳定性,化学持久性及辐照行为是重要的。
)以及成本和材料来源。
所谓强度是指金属材料在静载荷作用下,材料抵抗变形和破坏(断裂)的能力成为强度。
根据外力的作用方式,有多种强度指标,如抗拉强度,抗弯强度,抗剪强度等。
一般情况下多以抗拉强度作为判别金属强度高低的招标。
机械零件在使用时,一般不允许发生塑性变形,所以屈服强度是大多数机械零件设计时选材的主要依据也是评定金属材料承载能力的重要机械性能指标。
材料的屈服强度越高,允许的工作应力越高,零件所需的截面尺寸和自身重量就可以较小。
材料发生屈服后,到最高点应力达最大值σb。
在这以后,试样产生“缩颈”,迅速伸长,应力明显下降,最后断裂。
试样裂前能够承受的最大应力值σb称为抗拉强度或强度极限。
如果单从保证零件不产生断裂的安全角度考虑,可用作为设计依据,但所取的安全系数应该大一些。
拉伸性能测试

拉伸性能测试(静态)拉伸性能测试主要确定材料的拉伸强度,为研究、开发、工程设计以及质量控制和标准规范提供数据。
在拉伸测试中,薄的薄膜会遇到一定困难。
拉伸试样的切边必须没有划痕或裂缝,避免薄膜从这些地方开始过早破裂。
对于更薄的薄膜,夹头表面是个问题。
必须避免夹头发滑、夹头处试样破裂。
任何防止夹头处试样发滑和破裂,而且不干扰试样测试部分的技术如在表面上使用薄的橡胶涂层或使用纱布等都可以接受。
从拉伸性能测试中可以得到拉伸模量、断裂伸长率、屈服应力和应变、拉伸强度和拉伸断裂能等材料性能。
ASTM D 638 (通用)[4]和ASTM D 882 [5](薄膜)中给出了塑料的拉伸性能(静态)。
拉伸强度拉伸强度是用最大载荷除以试样的初始截面面积得到的,表示为单位面积上的力(通常用MPa为单位)。
屈服强度屈服强度是屈服点处的载荷除以试样的初始截面面积得到的.用单位面积上的力(单位MPa)表示,通常有三位有效数字。
拉伸弹性模量拉伸弹性模量(简称为弹性模量,E)是刚性指数,而拉伸断裂能(TEB,或韧性)是断裂点处试样单位体积所吸收的总能量。
拉伸弹性模量计算如下:在载荷-拉伸曲线上初始线性部分画一条切线,在切线上任选一点,用拉伸力除以相应的应变即得(单位为MPa),实验报告通常有三位有效数字。
正割模量(应力-应变间没有初始线性比值时)定义为指定应变处的值。
将应力-应变曲线下单位体积能积分得到TEB,或者将吸收的总能量除以试样原有厚度处的体积积分。
TEB表示为单位体积的能量(单位为MJ/m3),实验报告通常有两位有效数字。
拉伸断裂强度拉伸断裂强度的计算与拉伸强度一样,但要用断裂载荷,而不是最大载荷。
应该注意的是,在大多数情况中,拉伸强度和拉伸断裂强度值相等。
断裂伸长率断裂伸长率是断裂点的拉伸除以初始长度值。
实验报告通常有两位有效数字。
屈服伸长率屈服伸长率是屈服点处的拉伸除以试样的初始长度值,实验报告通常有两位有效数字。
- 1、下载文档前请自行甄别文档内容的完整性,平台不提供额外的编辑、内容补充、找答案等附加服务。
- 2、"仅部分预览"的文档,不可在线预览部分如存在完整性等问题,可反馈申请退款(可完整预览的文档不适用该条件!)。
- 3、如文档侵犯您的权益,请联系客服反馈,我们会尽快为您处理(人工客服工作时间:9:00-18:30)。
1.拉伸试验的作用及试样的形状及尺寸
答:作用:测定材料的弹性,强度,塑性,应变硬化和韧性等许多重要力学性能指标;
形状:光滑圆柱试件,板状试件;
尺寸:①圆柱形拉伸试件:试件的标距长度Lo应比Do要大得多,通常Lo>5Do;
板状拉伸试件:标距长度Lo应满足下列关系式:Lo﹦5.65Ao或11.3Ao;其中Ao为
试件的初始面积。
2.应力状态柔度系数的物理意义及应用?
答:应力状态柔度系数:在各种加载条件下,最大切应力τmax与最大正应力σmax之比,记为α,α=τmax/σmax.。
α(拉伸)﹤α(扭转)﹤α(压缩)
3.金属材料的弹性不完善性包括那几个方面?
答:弹性不完善性是指收到应力作用是,没有立即发生相应的弹性应变去除应力时应变也不是随即消失,包括弹性后效,弹性滞后,包申效应三个方面。
4.金属材料使用过程和生产过程对材料有什么要求?(强度和塑性)
答:在进行材料选择时,设计师必须首先考虑强度,导电性或导热性,密度及其他性能。
然后,在考虑材料的加工性能和使用行为(其中材料的可成塑性,机械加工性,电稳定性,化学持久性及辐照行为是重要的。
)以及成本和材料来源。
所谓强度是指金属材料在静载荷作用下,材料抵抗变形和破坏(断裂)的能力成为强度。
根据外力的作用方式,有多种强度指标,如抗拉强度,抗弯强度,抗剪强度等。
一般情况下多以抗拉强度作为判别金属强度高低的招标。
机械零件在使用时,一般不允许发生塑性变形,所以屈服强度是大多数机械零件设计时选材的主要依据也是评定金属材料承载能力的重要机械性能指标。
材料的屈服强度越高,允许的工作应力越高,零件所需的截面尺寸和自身重量就可以较小。
材料发生屈服后,到最高点应力达最大值σb。
在这以后,试样产生“缩颈”,迅速伸长,应力明显下降,最后断裂。
试样裂前能够承受的最大应力值σb称为抗拉强度或强度极限。
如果单从保证零件不产生断裂的安全角度考虑,可用作为设计依据,但所取的安全系数应该大一些。
材料在外力作用下,产生永久残余变形而不被断裂的能力,称为塑性。
塑性指标也主要是通过拉伸试验测得的。
工程上常用延伸率和断面收缩率作为材料的塑性指标。
屈服强度与抗拉强度的比值σs/σb称为屈强比。
屈强小,工程构件的可靠性高,说明即使外载或某些意义外因素使金属变形,也不至于立即断裂。
但屈强比过小,则材料强度有效利用率太低。
延伸率和断面收缩率的值越大,表示材料的塑性越好。
塑性对材料进行冷塑变形有重要的意义。
此外,工件的偶然过载,可因塑性变形而防止突然断裂,工件的应力集中处,也可因塑性变形使应力松弛,从而使工件不至于过早断裂。
这就是大多数机械零件除要求一定强度指标外,还要求一定塑性指标的道理。
材料的δ和ψ值越大,塑性越好。
两者相比,用ψ表示塑性更接近于材料真实应变。
5.表示脆性材料的力学性能的参量有哪些?
答:弹性模量和脆性断裂强度。
6.工程中测定材料的硬度最常用的方法?
答:测定硬度方法有很多,有压入法,回跳法和刻划法三大类。
最常用的是压入法,根据加载速率的不同分为动载入压入法和静载压入法。
超声波硬度,肖氏硬度和锤击式布氏硬度属于动载实验法。
布氏硬度,洛氏硬度,维氏硬度和显微硬度同于静载压入发。
7.弹性模量的影响因素?材料弹性常数有哪些?
答:1)纯金属的弹性模量:除了过度族金属除外,一般地讲弹性模量E与原子半径r之间
存在下列关系:E=k/rm,式中K与m均为常数,m>1。
这表明E随原子半径增大而减小,亦即随原子间距离增大而减小。
过度族金属的弹性模量较大,并且d层电子数等于6时弹性模量具有最大值;
2)合金元素的影响:化学成分的重大改变和具有高弹性模量的第二相质点可以使弹性模量发生显著的变化。
3)温度,通常温度升高是原子间距离增大,原子间结合力减弱。
因此弹性模量总是随温度升高而降低。
4)加载速率。
金属的弹性变形速度很快,远远超过一般的加载速率,因此,一般工程技术中的加载速率不会影响金属的弹性模量。
5)冷变形。
冷变形稍稍降低金属的弹性模量。
材料的弹性常数有:正弹性模量E和切变模量G,泊松比υ也是弹性常数,但他与E,G有下列关系E=2(1+υ)G
8.断裂按照断裂机制分为哪几大类?
答:解理断裂,沿晶断裂,微孔聚合型的延性断裂。
9.理论断裂强度的应用范围?
答:晶体结构比较完整的晶体
10.断裂力学主要用来处理哪方面的问题?
答:断裂力学市是研究裂纹体强度与寿命特别是裂纹扩展规律的科学,是固体力学的一门新分支,又称裂纹力学,与损伤力学成为姊妹学科,共成为破坏力学。
研究对象:裂纹体。
研究目标:主要预防控制低应力脆性断裂。
研究内容:裂纹的萌生机制,扩展规律,闭合理论以及动态起始与传播-止裂等。
研究任务:求的各类材料的断裂韧度,建立物体的断裂判据,研究裂纹的扩展规律,研究载荷与腐蚀共同作用下的断裂问题。
11.多晶体金属塑性变形的特点?
答:多晶体金属塑性具有如下一些特点:
1)各晶体变形的不同时性和不均匀性
2)各晶体变形的相互协调性
12.脆性端口和延性端口的特点?
答:脆性断裂的断裂面一般与正应力垂直,断口平齐而光亮,常呈放射状或结晶状;延性断裂的断裂面一般平行于最大切应力并与主应力成45°.用肉眼或放大镜观察时,端口呈纤维状,灰暗色。
13.裂纹体变形的形式?最危险的形式?
答:裂纹体的三种变形模式
1)Ⅰ型或张开型(最危险) 外加拉应力与断裂面垂直,使裂纹张开,即为Ⅰ型或张开型
2)Ⅱ型或滑开型外加应力平行于裂纹面并垂直于裂纹前缘线,即为Ⅱ型或滑开型3)Ⅲ型或撕开型外加应力即平行于裂纹面又垂直于裂纹前缘线,即为Ⅲ型或撕开型14.材料脆性——韧性转变影响因素?
答:1.应力状态及其柔度系数
应力状态可以用切应力和正应力表示,只有切应力引起材料塑性变形,简单的讲切应力促进塑性变形,对塑性变形有利;拉应力促进断裂,不利于塑性和韧性。
且柔度系数越大,应力状态越柔,越易变形而较不易开裂,越处于韧性状态
2.温度和加载速率的影响
温度对屈服强度影响很大,因为温度有助于激活F-R位错运动,使滑移易于进行。
随温度升高,断裂应力σc变化不大,而屈服强度σs变化很大,两者交点为韧脆转变温度,低于此温度为脆断,高于此温度为韧断。
加载速率的提高,而相对变形速率增加,超过某一限度时会限制塑性变形发展,提高形变抗力,增加脆性倾向
3.材料的微观结构影响
a.各晶类型影响面心立方晶格金属,一般不出现韧脆转换而处于韧性状态,没有韧脆转变;体心立方晶格韧脆转变受温度及加载速率影响很大,易发生解理断裂。
b.成分影响含碳质量分数增加,塑性变形抗力增加,不仅冲击韧性降低,而且韧性转变温度明显提高
c.晶粒大小的影响晶粒细,滑移距离短,在障碍前塞积的位错数目少,相应的应力集中较小,需要消耗更多能量;晶界对裂纹扩展有阻碍作用。
晶粒愈细化,愈易处于韧性状态,降低了韧脆转变温度,提高了韧性和塑性。
15.。