再生胶 橡胶制品生产工艺
废旧橡胶生产再生胶技术

废旧橡胶生产再生胶技术
再生胶以废旧橡胶制品为原料,具有生胶的一些性能,但比生胶能节约费用,还能改善产品的耐酸、耐碱及耐老化等性能,原料来源广,工艺简单。
生产方法如下:一、整理废旧的橡胶
1.把废旧的橡胶分成外胎、内胎、胶鞋和其它橡胶制品四类,同时把天然橡胶与合成胶分开。
2.选择再生剂,油法生产再生胶要选用液体再生剂,天然胶选用松节油作再生剂;合成胶选用煤焦油;用于浅色制品的再生剂选用氧化松节油,对颜色没有要求而对物理机械性要求较高的选用松节油。
二、生产工艺
1.粉碎:把洗涤后的废橡胶用小钢磨粉碎过筛,外胎胶粉细度要求达26-28目,胶鞋才杂类胶粉细度要求达24-28目。
2.拌油:把胶粉放入拌油机内,使温度达70-80摄氏度,与油温合均匀,一般油的用量为胶粉的8%-15%
3.脱硫:净加油后的胶粉盛于铁盘中,然后放入卧式加热器内加热,在150-180摄氏度下10小时左右,废橡胶分子才能分裂而转化成再生胶砖。
4.压炼:把脱硫后的再生胶片入在精炼机上精炼,液温掌握在80-90度之间,直到合乎标准为止。
下片后再在开放式炼胶机上压成一定厚度的胶片就是再生胶。
红色精细再生橡胶的生产方法
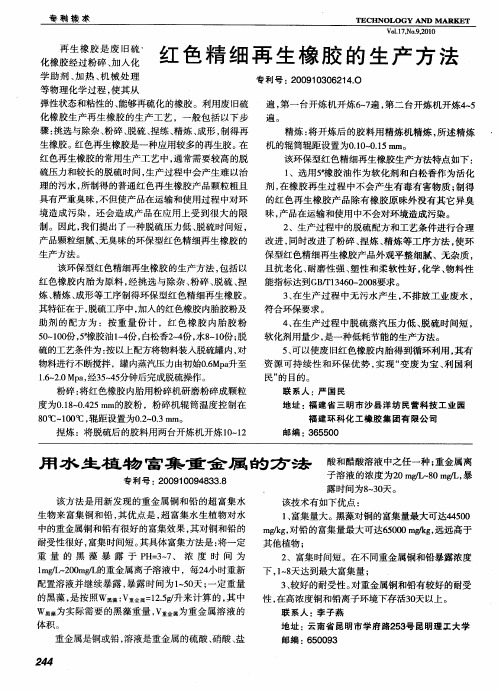
捏 炼 :将脱硫 后 的胶 料用 两 台开 炼机 开炼 1 2 0 1
用 水 生 植 物 富 集 重 金 属 的 方 法 酸 醋 溶 中 任 种;金 离 和 酸 液 之 一 重 属
专 利号 : 0 9 0 9 8 38 2 0 1 0 4 3 . 子溶 液 的浓度 为 2 /-0m /, 0mg 8 g 暴 L L
w黑 为实 际需 要 的黑 藻 重量 , 重 属 重 金 属溶 液 的 藻 V金为
体积 。
联 系人 :李子 燕
地址 : 南省 昆明市 学府 路2 3 昆明理 工大学 云 5号
重金 属是铜 或铅 , 溶液 是重金 属 的硫 酸 、 酸 、 硝 盐
2 4 4
邮编 : 5 0 3 6 0 9
5 可 以使 废 旧红色 橡胶 内胎 得到循 环 利用 , 、 其有 资源 可 持 续 性 和 环保 优 势 , 现 “ 废 为 宝 、 国利 实 变 利
民” 目的 。 的
联 系人 : 国 民 严 地 址 :福建省 三 明市沙 县洋 坊 民营 科技 工业 园 福建环 科化 工橡胶 集 团有 限公 司
能指 标达 到G / 14 0 2 0 要 求 。 BT 3 6 — 0 8
3 在 生产 过程 中无 污水 产 生 , 排放 工 业废 水 , 、 不 符合环保要求。
4 在生产过程 中脱硫蒸汽压力低 、 、 脱硫时间短 , 软化剂 用量少 , 一种低 耗节 能 的生产方 法 。 是
遍。
骤 : 选与 除杂 、 挑 粉碎 、 硫 、 练 、 脱 捏 精炼 、 形 , 得再 成 制 生橡 胶 。 色再生 橡胶是 一种 应用较 多 的再生胶 。 红 在 红色再 生橡胶 的常用生产 工艺 中 , 通常需 要 较高 的脱
特种再生橡胶的生产工艺及配方

特种再生橡胶的生产工艺及配方董诚春(北京橡胶工业研究设计院)摘要:本文主要论述了再生橡胶目前通用的分类方法,以及工艺和配方。
关键词:再生橡胶;分类;工艺;配方;性能通常所说再生橡胶是以废轮胎等通用橡胶制品为原料制成的再生橡胶,而以废特种橡胶制品为原料制成的再生橡胶称特种再生橡胶,特种再生橡胶包括彩色再生橡胶、乳胶再生橡胶、香味再生橡胶、精细再生橡胶、丁基再生橡胶、丁腈再生橡胶、三元乙丙再生橡胶及硅橡胶再生橡胶、氟橡胶再生橡胶、液体再生橡胶等分述如下:1、彩色再生橡胶在废橡胶制品中除轮胎等黑色橡胶制品外,还有不少彩色橡胶制品废料,这些废料可用于生产彩色再生橡胶,彩色再生橡胶的质量虽然不如轮胎再生胶,但利润高,今将其生产工艺简介如下:1.1 原料分类1.1.1 在废橡胶制品中按红色、蓝色、黄色、绿色、白色等分类,然后分类进行清洗,应防止污染。
1.1.2 软化剂应选用浅色类非污染型的软化剂,例如:白油、机油、油酸、石蜡油等。
1.2 粉碎不少彩色废料用双辊粉碎机粉碎到30目可能很困难,建议滚刀式粉碎机粗碎,再用磨盘式粉碎机细碎。
1.3 脱硫由于彩色再生橡胶产量不大,宜用小规格的专用脱硫设备,例如小规格时电加热动态脱硫罐,脱硫配方及工艺与生产轮胎再生胶相近,只是要用浅色无污染型的软化剂及活化剂,例如810、910等都是无污染型活化剂。
脱硫时间比生产轮胎再生胶短-点。
1.4 捏炼、精炼彩色再生橡胶-般通过捏炼出薄片即可,如用精炼出片,必须是强度较好的再生胶,否则,易断片,难成块状再生胶。
2、乳胶再生橡胶乳胶再生橡胶是最受欢迎的再生橡胶,因含胶率高,可代替生胶使用,其原料是乳胶厂的结皮废乳胶、废乳胶手套、废乳胶气球、废乳胶管等制品,它难生产,原因是粉碎困难,过去用油法生产,也不粉碎,有的不加软化剂,在蒸汽压作者简介:董诚春(1936),男,武汉市人,北京橡胶工业研究设计院高级工程师(已退休),从事轮胎等橡胶制品及废橡胶综合利用的研究开发工作,在橡胶专业期刊上发表论文有五十余篇,参加合编了六本橡胶专业书籍的有关章节,独自编著了《废橡胶资源综合利用》及《废轮胎回收加工利用》。
再生胶生产工艺3

脱硫配方及实例脱硫是再生胶生产过程中一个主要环节,是影响再生胶产品质量的一个关键工序。
脱硫不是把硫黄从橡胶分子中脱出来,而是通过加热、氧化及再生剂的作用,使硫化胶中的8———9—8交联键断裂,发生降解,导致硫化胶从弹性状态变成塑性状态,以利于后期加工处理。
(一)脱硫配方脱硫配方是关系到再生胶脱硫效果好坏和后期加工难易的一个关键技术。
制定配方要根据胶粉的种类、脱硫工艺条件、后期机械加工条件等综合因素,选择适宜软化剂、活化剂品种和用量。
脱硫配方由胶粉、软化剂和活化剂等组成。
确定软化剂及其用量要考虑三个因素。
!"胶粉种类及细度胶粉有外胎胶粉、胶鞋胶粉、杂胶胶粉三类,每类又分若干品种(详见本章第四节)。
由于每种胶粉的胶质、含胶量及所含的配合剂不同,在选择软化剂时要首先考虑适应性。
(!)非极性软化剂(饱和烷烃或环烷烃成分)与极性橡胶分子互容性差,在渗透后只使分子溶胀,分子间距离增大,削弱分子间的作用力,使橡胶分子易于滑动变形,这类软化剂得到的再生胶塑性大,拉伸强度低。
(#)有一定极性并含双键或活性基的软化剂,由于与极性橡胶分子中的活性基有近似结构,互容性好,在极性作用下产生相互诱导力,使分于间的作用力加强,这类软化剂得到的再生胶,其物理机械性能和工艺性能较好。
($)极性强、化学性活泼、含有双键的环状化合物作软化剂,除使极性橡胶分子溶胀外,它还吸附在橡胶分子上,其结构中的!电子云与橡胶分子双键中的!电子云相重叠,而产生结合力,同时在极性作用下产生较强的取向力和诱导力。
虽然由于渗透作用,在一定程度上削弱了橡胶分子间的作用力,但在极性作用下(结合力、诱导力、取向力)却使橡胶分子保持较高的相互作用力,此时再生胶具有较高的物理机械性能。
胶粉的细度一般要求在#%&$#目,胶粉细度越大,软化剂用量越少,否则反之。
软化剂用量不足,将有一部分胶粉得不到膨胀,影响脱硫效果。
用量过多,使工艺操作困难,产品质量下降。
再生胶配方

再生胶配方再生胶配方是制造再生胶产品的关键。
再生胶是指由废旧橡胶制成的一种材料,可以再次使用和生产各种橡胶制品。
再生胶被广泛应用于橡胶工业,例如橡胶底板、汽车胎和橡胶管等。
本文将介绍一种常见的再生胶配方,包括原料及其比例、加工过程和产品特性等。
1. 原料及其比例再生胶的原料主要包括废橡胶和添加剂。
废橡胶通常来自废旧轮胎、橡胶制品或橡胶加工废料等。
添加剂是为了提高再生胶的物理性能和加工性能而加入的,常见的添加剂包括硫化剂、防老剂和增塑剂等。
以下是一种常见的再生胶配方示例:- 废橡胶:60%- 硫化剂:3%- 防老剂:1%- 增塑剂:2%- 其他添加剂:4%- 橡胶粉:30%上述比例仅供参考,实际配方可能因产品用途、性能要求和生产工艺的不同而有所变化。
2. 加工过程再生胶的生产过程分为四个主要阶段:破碎、造粒、混合和硫化。
首先,废橡胶经过破碎处理,将废旧橡胶制品或废料破碎成小颗粒状。
然后,将破碎后的橡胶颗粒进行造粒,即通过高温和高压将颗粒进行加热和挤压,使其形成固体颗粒。
接下来,将造粒后的再生橡胶与添加剂进行混合。
混合的过程需要借助橡胶混炼机,将再生橡胶和添加剂均匀混合,确保添加剂充分分散在再生橡胶中。
最后,混合后的胶料经过硫化处理,即在一定的温度和时间条件下进行硫化反应。
硫化剂起到交联橡胶分子的作用,使其形成弹性体。
3. 产品特性再生胶的性能取决于原料的质量和配方的比例。
再生胶的主要特性和性能包括以下几个方面:- 耐磨性:再生胶具有较高的耐磨性,适用于制造汽车胎和工业橡胶制品等高磨损性的产品。
- 弹性:再生胶具有良好的弹性,可以有效地吸收震动和减少噪音。
- 耐候性:再生胶具有较好的耐候性,能够抵抗日晒、雨淋等外部环境的影响。
- 加工性能:再生胶易于加工成型,可以通过挤出、压延、模压等工艺制造不同形状和规格的产品。
然而,与原料橡胶相比,再生胶在某些性能方面可能存在一定的差异。
例如,再生胶的耐热性、抗拉强度和耐油性等性能通常较原料橡胶略差。
再生橡胶加工新工艺
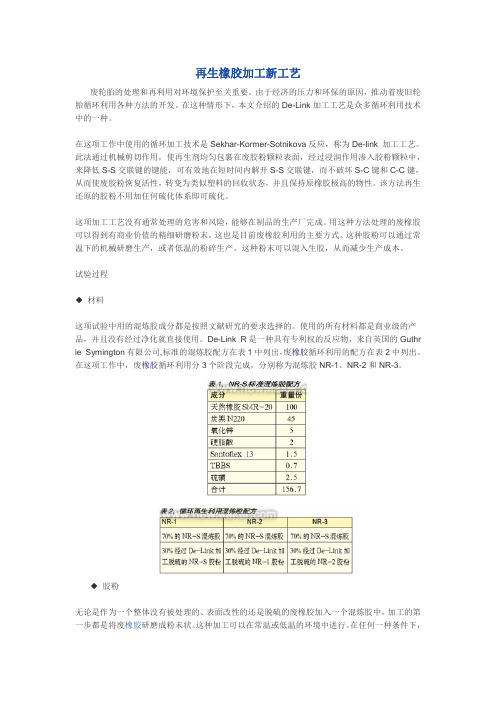
再生橡胶加工新工艺废轮胎的处理和再利用对环境保护至关重要。
由于经济的压力和环保的原因,推动着废旧轮胎循环利用各种方法的开发。
在这种情形下,本文介绍的De-Link加工工艺是众多循环利用技术中的一种。
在这项工作中使用的循环加工技术是Sekhar-Kormer-Sotnikova反应,称为De-link 加工工艺。
此法通过机械剪切作用,使再生剂均匀包裹在废胶粉颗粒表面,经过浸润作用渗入胶粉颗粒中,来降低S-S交联键的键能,可有效地在短时间内解开S-S交联键,而不破坏S-C键和C-C键,从而使废胶粉恢复活性,转变为类似塑料的回收状态,并且保持原橡胶极高的物性。
该方法再生还原的胶粉不用加任何硫化体系即可硫化。
这项加工工艺没有通常处理的危害和风险,能够在制品的生产厂完成。
用这种方法处理的废橡胶可以得到有商业价值的精细研磨粉末,这也是目前废橡胶利用的主要方式。
这种胶粉可以通过常温下的机械研磨生产,或者低温的粉碎生产。
这种粉末可以混入生胶,从而减少生产成本。
试验过程◆材料这项试验中用的混炼胶成分都是按照文献研究的要求选择的。
使用的所有材料都是商业级的产品,并且没有经过净化就直接使用。
De-Link R是一种具有专利权的反应物,来自英国的Guthr ie Symington有限公司,标准的混炼胶配方在表1中列出,废橡胶循环利用的配方在表2中列出。
在这项工作中,废橡胶循环利用分3个阶段完成,分别称为混炼胶NR-1、NR-2和NR-3。
◆胶粉无论是作为一个整体没有被处理的、表面改性的还是脱硫的废橡胶加入一个混炼胶中,加工的第一步都是将废橡胶研磨成粉末状。
这种加工可以在常温或低温的环境中进行。
在任何一种条件下,生产非常精细的胶粉都是必要的。
正如R.Kohler和J.O′Neill描述的,没有被处理的碎屑填充物粒径必须至少在40~60筛孔,或者更细。
R.Kohler和J.O′Neill经过实验证明,胶粉粒子的大小对混炼胶拉伸强度几乎没有影响,但是使用较小粒径的胶粉能改进胶料扯断伸长率和门尼粘度。
(完整版)再生胶、橡胶制品生产工艺

再生胶、橡胶板加工工艺流程简介1、再生橡胶生产工艺图2-1 再生胶加工工艺流程图主要流程说明:分拣:将废轮胎等进行分类,便于后续加工。
2、切胶:将废轮胎剪切成需要的尺寸,便于下道工序加工。
3、清洗:因废轮胎与地面接触夹带泥沙,需要进行清洗。
一方面是为了防止在粉碎过程中产生粉尘,另一方面是为了防止夹带泥沙,影响产品质量。
清洗废水经沉淀后循环使用,泥沙作为固体废物处理,对环境没有影响。
4、粉碎:利用粉碎机进行粉碎,得到需要的废橡胶颗粒。
粉碎中产生的颗粒物经集气罩收集、袋式除尘器除尘,并且经常清理除尘器,将收集的废橡胶颗粒再次回用。
5、风选、磁选:粉碎后的废橡胶颗粒由输送器送入旋风分离器和磁选装置将帘布等纤维杂质和轮胎中的钢丝分离出来。
废帘布、废钢丝作为固体废物由物回部门回收再利用,对环境没有影响。
6、过筛:经振动筛使合格的胶粉从筛网漏下,不合格的胶粉单独收集重新粉碎。
过筛过程中还会有少量废帘布、钢丝被分离出来。
7、脱硫:过筛合格的胶粉采用动态脱硫法进行脱硫。
脱硫是生产再生胶的关键环节,在脱硫罐中将一定比例的胶粉、软化剂、活化剂、水混合,通过加热、加压、氧化等破坏其分子的网状结构,使其从弹性状态变成塑性状态,便于后期加工。
脱硫过程中产生非甲烷总烃、恶臭,脱硫过程中产生的废气经废橡胶动态脱硫尾气系统净化装置进行净化后排放,脱硫尾气处理过程中所用的喷淋水、冷却水在自然冷却后循环使用。
8、冷却:脱硫后的胶粉需要马上进行冷却,防止着火碳化。
冷却方式是由夹套中通冷却水的螺旋输送器输送到冷却场地,由人工摊开冷却到30-40℃。
冷却水循环使用。
9、精炼:经过脱硫后的胶料可塑性低、含有杂质和尚未完全脱硫的硬颗粒,精炼的目的就是利用剪切力使胶料分子进一步断裂、分离杂质和碾碎尚未完全脱硫的硬颗粒。
精炼过程中胶料生热产生低浓度工艺废气,经集气罩收集处理后排放。
10、出片:从精炼机下来的胶片通过重量控制,由自动切割刀将胶片割开取下,即成为再生胶成品。
再生胶生产工艺

再生胶生产工艺
再生胶是指通过对废旧轮胎和废胶制品进行回收、再加工,制造出具有再生利用价值的橡胶材料,并用于再生橡胶制品的生产过程。
再生胶生产工艺主要包括废胶破碎、除钢线、粉碎、橡胶颗粒化、胶粉质量改性、胶粉工艺设计等环节。
首先,废胶破碎是再生胶生产的第一步。
在废旧轮胎回收过程中,采用机械或化学方法将轮胎进行切割、切碎,得到废胶块。
然后,废胶破碎后,需要进行除钢线的工艺。
除钢线主要通过磁选和振动筛分两种方式进行。
磁选主要是利用磁铁对钢丝进行吸附,使其与废胶分离。
振动筛分则是通过震动筛将废胶和钢丝分离开来,得到纯净的废胶颗粒。
接下来,废胶颗粒化是再生胶生产的关键环节。
废胶颗粒化主要是将废胶颗粒经过高温加热,使其软化,然后通过挤出机或压机将其压制成形,得到橡胶颗粒。
在橡胶颗粒化后,还需要对胶粉进行质量改性。
质量改性主要是通过添加剂、活性剂等对橡胶颗粒进行处理,改变其性能特征,提高再生胶的使用价值。
最后,再生胶生产还需要进行胶粉工艺设计。
胶粉工艺设计主要是根据再生胶的使用需求,进行胶粉的配方设计,确定胶粉的比例、成分和加工工艺。
总的来说,再生胶生产工艺是一个复杂而精细的过程。
从废胶
的破碎、除钢线到胶粉质量改性,再到胶粉工艺设计,每一步都需要认真细致的操作和科学合理的设计。
通过再生胶生产工艺的完善,可以使废旧轮胎和废胶制品得到有效的回收利用,减少对自然资源的消耗,降低环境污染。
再生胶的广泛应用,也推动了可持续发展的愿景。
- 1、下载文档前请自行甄别文档内容的完整性,平台不提供额外的编辑、内容补充、找答案等附加服务。
- 2、"仅部分预览"的文档,不可在线预览部分如存在完整性等问题,可反馈申请退款(可完整预览的文档不适用该条件!)。
- 3、如文档侵犯您的权益,请联系客服反馈,我们会尽快为您处理(人工客服工作时间:9:00-18:30)。
再生胶、橡胶板加工工艺流程简介
1、再生橡胶生产工艺
主要流程说明:
分拣:将废轮胎等进行分类,便于后续加工。
2、切胶:将废轮胎剪切成需要的尺寸,便于下道工序加工。
3、清洗:因废轮胎与地面接触夹带泥沙,需要进行清洗。
一方面是为了防止在粉碎过程中产生粉尘,另一方面是为了防止夹带泥沙,影响产品质量。
清洗废水经沉淀后循环使用,泥沙作为固体废物处理,对环境没有影响。
4、粉碎:利用粉碎机进行粉碎,得到需要的废橡胶颗粒。
粉碎中产生的颗粒物经集气罩收集、袋式除尘器除尘,并且经常清理除尘器,将收集的废橡胶颗粒再次回用。
5、风选、磁选:粉碎后的废橡胶颗粒由输送器送入旋风分离器和磁选装置将帘布等纤维杂质和轮胎中的钢丝分离出来。
废帘布、废钢丝作为固体废物由物回部门回收再利用,对环境没有影响。
6、过筛:经振动筛使合格的胶粉从筛网漏下,不合格的胶粉单独收集重新粉碎。
过筛过程中还会有少量废帘布、钢丝被分离出来。
7、脱硫:过筛合格的胶粉采用动态脱硫法进行脱硫。
脱硫是生产再生胶的关键环节,在脱硫罐中将一定比例的胶粉、软化剂、活化剂、水混合,通过加热、加压、氧化等破坏其分子的网状结构,使其从弹性状态变成塑性状态,便于后期加工。
脱硫过程中产生非甲烷总烃、恶臭,脱硫过程中产生的废气经废橡胶动态脱硫尾气系统净化装置进行净化后排放,脱硫尾气处理过程中所用的喷淋水、冷却水在自然冷却后循环使用。
8、冷却:脱硫后的胶粉需要马上进行冷却,防止着火碳化。
冷却方式是由夹套中通冷却水的螺旋输送器输送到冷却场地,由人工摊开冷却到30-40℃。
冷却水循环使用。
9、精炼:经过脱硫后的胶料可塑性低、含有杂质和尚未完全脱硫的硬颗粒,精炼的目的就是利用剪切力使胶料分子进一步断裂、分离杂质和碾碎尚未完全脱硫的硬颗粒。
精炼过程中胶料生热产生低浓度工艺废气,经集气罩收集处理后排放。
10、出片:从精炼机下来的胶片通过重量控制,由自动切割刀将胶片割开取下,即成为再生胶成品。
11、检验、包装:经检验合格的再生胶中间涂上隔离剂即成为再生胶成品。
2
1、混炼:将原料橡胶、配合剂等按一定比例投入密炼设备中进行混炼加工,混炼的目的就是使配合剂完全均匀分散在橡胶中,并尽可能不降低橡胶的机械强力。
混炼是在密炼机中按照工艺要求进行炼制,一般情况下工艺温度在130℃。
2、返炼:返炼是在开炼机中按照工艺要求进行炼制,一般情况下工艺温度在80℃. 返炼过程中也会产生一定量的炼胶废气,主要为臭气浓度。
3、压延:根据产品要求加工出厚度、宽度符合要求的胶板半成品。
压延过程产生一定的异味气体。
4、硫化:硫化过程温度控制在130℃左右,在压力和温度的作用下,使橡胶具备了定伸强度、弹性、硬度、拉伸强度等一系列物理机械性能。
5、裁边:在长案上展开胶板,用钢板尺按成品规格截取宽度及长度,顺纹理裁剪两边。
裁边过程中的固体废物为橡胶板下脚料,收集后作为再生胶的原料。
6、检验包装:按产品的质量标准验收把关,用塑料薄膜包好并贴好产品标志。
7、入库:最终产品入库待售。
加工过程中产生的工艺废气通过设备上方设置的集气设施收集后集中排放。