车削加工程序编制
数控机床程序编制的一般步骤和手工编程

数控机床程序编制的一般步骤和手工编程数控机床程序编制〔又称数控编程〕是指编程者〔程序员或数控机床操作者〕根据零件图样和工艺文件的要求,编制出可在数控机床上运行以完成规定加工任务的一系列指令的过程。
具体来说,数控编程是由分析零件图样和工艺要求开始到程序检验合格为止的全部过程。
一般数控编程步骤如下〔见图19-22〕。
图19-22 一般数控编程顺序图1.分析零件图样和工艺要求分析零件图样和工艺要求的目的,是为了确定加工方法、制定加工方案,以及确认与生产组织有关的问题,此步骤的内容包括:1〕确定该零件应安排在哪类或哪台机床上进行加工。
2〕采用何种装夹具或何种装卡位方法。
3〕确定采用何种刀具或采用多少把刀进行加工。
4〕确定加工路线,即选择对刀点、程序起点〔又称加工起点,加工起点常与对刀点重合〕、走刀路线、程序终点〔程序终点常与程序起点重合〕。
5〕确定切削深度和宽度、进给速度、主轴转速等切削参数。
6〕确定加工过程中是否需要提供冷却液、是否需要换刀、何时换刀等。
2.数值计算根据零件图样几何尺寸,计算零件轮廓数据,或根据零件图样和走刀路线,计算刀具中心〔或刀尖〕运行轨迹数据。
数值计算的最终目的是为了获得编程所需要的所有相关位置坐标数据。
3.编写加工程序单在完成上述两个步骤之后,即可根据已确定的加工方案〔或方案〕及数值计算获得的数据,按照数控系统要求的程序格式和代码格式编写加工程序等。
编程者除应了解所用数控机床及系统的功能、熟悉程序指令外,还应具备与机械加工有关的工艺知识,才能编制出正确、实用的加工程序。
4.制作控制介质,输入程序信息程序单完成后,编程者或机床操作者可以通过CNC机床的操作面板,在EDIT方式下直接将程序信息键入CNC系统程序存储器中;也可以根据CNC系统输入、输出装置的不同,先将程序单的程序制作成或转移至某种控制介质上。
控制介质大多采用穿孔带,也可以是磁带、磁盘等信息载体,利用穿孔带阅读机或磁带机、磁盘驱动器等输入〔输出〕装置,可将控制介质上的程序信息输入到CNC系统程序存储器中。
数控车削加工工艺

数控车削加工工艺随着现代制造业的不断发展,数控车削加工技术成为了制造业中不可或缺的一部分。
数控车削加工是一种高效、高精度、高质量的加工方式,可以实现复杂零件的大规模生产。
本文将介绍数控车削加工的基本工艺,制造过程及其优点。
一、数控车削加工的基本工艺数控车削加工是指使用数控车床进行加工的一种加工过程。
数控车床是一种基于计算机控制系统的机械设备,通过预置的数字程序控制车床的运动来完成自动化的加工。
数控车床包括自动进给机构、主轴箱、刀架和工件旋转机构等部分。
数控车削加工基本工艺流程包括以下几个方面:1.数控加工合理设计:在进行数控加工前,需要进行CAD (计算机辅助设计)和CAM(计算机辅助制造)前期工作。
首先,根据产品的零件图纸,进行CAD绘制出三维模型图。
然后,通过CAM软件将三维模型转化为加工程序,并导出G代码程序。
2.加工参数设置:在进行数控加工前,需要设置加工参数,包括刀具的半径、旋转速度、进给速度、加工深度和加工时间等。
根据不同的零件特点,进行合理的加工参数设计,以保证加工效果和效率。
3.设备准备:在进行数控加工前,需要对设备进行准备,包括安装好相应的刀具和工件,并对设备进行调试和检测。
确保设备运行正常状态下,以保证加工效果和效率。
4.数控加工操作:在进行数控加工时,需要通过预置的数字程序控制车床的运动轨迹和刀具的进给速度等参数,按照设定好的程序进行加工操作。
同时,需要对加工过程进行监控,及时处理加工过程中出现的问题。
二、数控车削加工的制造流程数控车削加工的制造流程包括数控程序编制、预处理、机床设备准备、加工和后处理等阶段。
下面简要介绍一下制造流程中的各个阶段:1.数控程序编制:这是数控车削加工的基础工作,需要经过CAD/CAM软件完成。
利用CAD软件绘制三维模型,然后通过CAM软件转化为数控程序并生成容易理解的G代码。
2.预处理:在数控程序发送给机床之前,需要进行预处理。
预处理的任务是将G代码程序转换成机床识别的M代码和G代码,并在验证程序的形式、语法等方面进行检查和纠正。
零件数控车床加工程序的编制

现 以上 图酒 杯 的数 控 车削 为 例 ,分 析怎 样 制 定 加工 工艺 及如 何编 制其 加工 程序 的方 法 。
一
、
分 析 零 件 图
/ ■, / , j 0 ,
零 件 图是 加 工零 件 要严 格遵 守 的技术 文 件 ,分
析零 件 图是 我 们 工 艺 准 备 中首 当其 冲 的重 要 工 作 。
图纸 识读 的准 确 与否 ,将 直 接影 响零 件程 序 编 制及
加工 的结 果 。 件 图上 的尺 寸公 差要 求 ,以确 定 控 制其
尺寸 精度 的加 工工 艺 , 比如 刀具 的选 择及 切 削 用量
图2
的确 定 。分 析 图 中形 状 和位 置公 差 要 求 :在 数 控 车 切 削加 工 中 ,影 响零 件 的形 状 和位 置 度 的主 要 因素 该 加 工路 线是 先用 G 7 5指令 在 径 向迅 速先 切 除 图示 区域 内大 的加 工余 量 ,其 各 点坐 标 可借 助 计 算 机 辅 助计 算 ,很 快捷 。再 用 G 7 3指 令加 工 。这样 可
法 ,则是极 为重要 的一项 工作 。
关 键词 :数 控 车床 ;走 刀路 线 ;程序 编 制
在 数 控 车 削 加 工 中 ,编 制 一 个 零 件 的数 控 程 序 ,其 加 工 路线 的选择 、程序 功 能指 令 的选 择 往 往 举 棋不 定 ,甚 至 同一 个 零 件 已经 加工 完 成 多个 ,尚
低成 本之 目的 。
1 0 /
零 件表 面粗 糙 度 、材 料 与热 处理 、其 它特 殊 处 理及 毛 坯 的要 求 ,件 数 。该 零件 为 铝件 ,粗糙 度 全
部 为R a 3 . 2。这 些都 是不 可忽 视 的参 数 。
铁路货车车轴车削数控加工程序的编制

( )机 壳 采 用 阻 燃 性 塑 料 制 8 品, 有效 地 防止 了静 电 的产生 和 放 电现象 , 确保 安全 。
制 输 出 电 路 隔 离 ,无 直 接 电气 耦
合。
( )控 制 电 路 输 出 为 机 械 接 6 点 , 局部 电源 与检 测 控制 电路 无 使
电气 连接 。
3 mA的十分 之一 。 此 电路 的接 人 0 故 对 轨 道 电 路 电气 特 性 几 乎 无 任 何
影响。
( )输 出继 电器 采 用 O O 7 MR N 的产 品 , 电器 机 械寿 命 可达 10 继 5o
万次 以上 。
子 监 控 防 护 盒 已通 过 了 铁 道 部 的
动 和动作 的机床。其加工原理是先对 被加工零件图纸进行工艺分析 ,将零 规 定 的代 码 和格 式 编 写成 程 序 , 然 后 将 加工 程 序输 入 数 控装 置 , 照 按
一 酣 ~ ~ 一 一
Y
Y
Y・ X X
直 线 插 补
图1 数控 原 理 图
圆 弧 插 补
 ̄¥圆弧插补指令 、9 蠢 - - I G 证线速度一
致命令 , 7 循环 指令 等等 。 及G 3
211 确定 车轴 的装卡 方法 .. R2 E C型 车轴 重 量 为 4 0 g 长 4k ,
工 聪
1 编 程 方 法 和数 控 系 统
11 数 控 编程 基本 方法 .
达 216 因此 在 数控 车 床 中 部装 . m, 6
有托架 。车轴 装夹 以车轴两 端 中心 数 控 编 程基本方 法有手工 编程 和 自动编程两种 ,手工编程是 自动编 程的基础 。手工编程是指从零件图样 分析工艺处理、数据计算 、编写程序
编制数控车削加工工艺的基本步骤
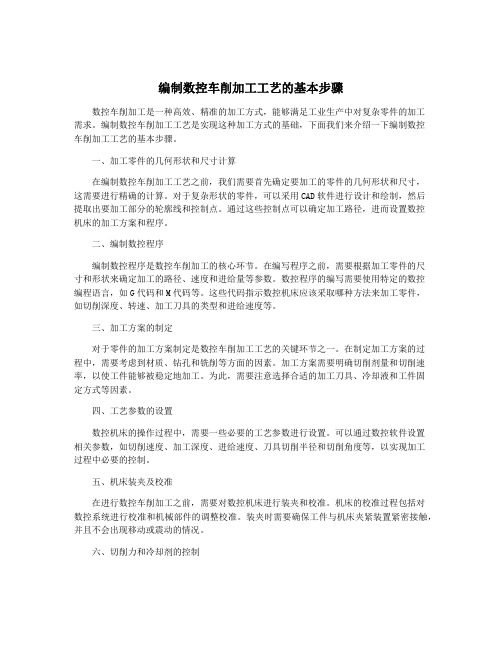
编制数控车削加工工艺的基本步骤数控车削加工是一种高效、精准的加工方式,能够满足工业生产中对复杂零件的加工需求。
编制数控车削加工工艺是实现这种加工方式的基础,下面我们来介绍一下编制数控车削加工工艺的基本步骤。
一、加工零件的几何形状和尺寸计算在编制数控车削加工工艺之前,我们需要首先确定要加工的零件的几何形状和尺寸,这需要进行精确的计算。
对于复杂形状的零件,可以采用CAD软件进行设计和绘制,然后提取出要加工部分的轮廓线和控制点。
通过这些控制点可以确定加工路径,进而设置数控机床的加工方案和程序。
二、编制数控程序编制数控程序是数控车削加工的核心环节。
在编写程序之前,需要根据加工零件的尺寸和形状来确定加工的路径、速度和进给量等参数。
数控程序的编写需要使用特定的数控编程语言,如G代码和M代码等。
这些代码指示数控机床应该采取哪种方法来加工零件,如切削深度、转速、加工刀具的类型和进给速度等。
三、加工方案的制定对于零件的加工方案制定是数控车削加工工艺的关键环节之一。
在制定加工方案的过程中,需要考虑到材质、钻孔和铣削等方面的因素。
加工方案需要明确切削剂量和切削速率,以使工件能够被稳定地加工。
为此,需要注意选择合适的加工刀具、冷却液和工件固定方式等因素。
四、工艺参数的设置数控机床的操作过程中,需要一些必要的工艺参数进行设置。
可以通过数控软件设置相关参数,如切削速度、加工深度、进给速度、刀具切削半径和切削角度等,以实现加工过程中必要的控制。
五、机床装夹及校准在进行数控车削加工之前,需要对数控机床进行装夹和校准。
机床的校准过程包括对数控系统进行校准和机械部件的调整校准。
装夹时需要确保工件与机床夹紧装置紧密接触,并且不会出现移动或震动的情况。
六、切削力和冷却剂的控制数控车削加工中需要控制切削力和冷却剂的使用。
切削力过大会导致刀具的过早磨损和加工表面粗糙,因此需要控制加工的深度和进给速度等参数;而冷却剂的使用可以有效降低加工温度,从而减少刀具的磨损和工件的形变。
《计算机辅助制造》课大作业--编程说明书

《计算机辅助制造》综合作业一、数控车削加工程序编制应用MasterCAM软件编写如下图所示的零件的数控车削加工程序。
1、零件图2、毛坯图该零件车削加工取用的毛坯尺寸为外径60mm,内径15mm,长度135mm的管件。
3、工艺分析序号工步内容刀具号主轴转速(r/min)进给转速(mm/min)背吃刀量(mm)备注1 粗车端面T01 550 100 22 精车端面T01 800 60 0.53 粗车外圆(不含圆弧)T02 550 80 24 粗车R16圆弧面T02 550 80 25 精车外圆T02 800 50 0.56 切外退刀槽T03 350 307 车外螺纹T04 2008 粗镗内孔T05 300 40 19 精镗内孔T05 400 30 0.510 切内退刀槽T06 200 2511 车内螺纹T07 1004、绘制零件轮廓线运用SolidWorks三维造型软件绘制零件草图,并在MasterCAM软件打开以*.IGES格式保存的文件,零件轮廓线如下图所示。
零件轮廓线5、设定工件坐标系(以右端面为例)按键盘上的<F9>键,图形会出现两条棕色的直线,其交点即为当前工件坐标的原点。
工件原点移动的方法:点击菜单<转换>→<平移>,然后全选“图形区域所有线段”按回车确认,在弹出的<平移>对话框中,选择<移动>,<从一点到另一点>,然后选择图形上要平移的点,回车确认。
工件坐标系设定6、机床类型选择及毛坯定义机床类型选择:点击菜单<机床类型>→<车床>→<默认>毛坯定义:在软件页面左侧<操作管理>中,点击<属性>→<材料设置>→<信息内容>,在弹出的<机床组件材料>对话框中,对毛坯进行参数设置。
毛坯参数设置7、刀具路径生成及参数设置(因该零件加工为调头件加工,所以刀具路径分为左右两部分)a、右半部分:1)粗车端面点击<刀具路径>→<车端面>,具体参数设置如下图所示。
数控车床的程序编制步骤
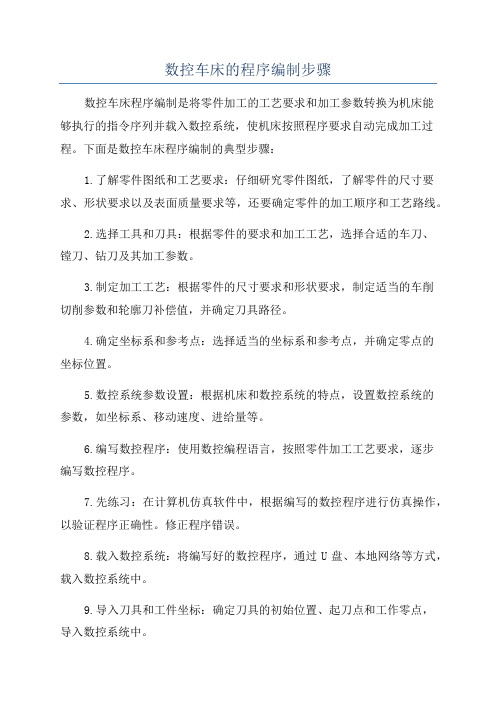
数控车床的程序编制步骤数控车床程序编制是将零件加工的工艺要求和加工参数转换为机床能够执行的指令序列并载入数控系统,使机床按照程序要求自动完成加工过程。
下面是数控车床程序编制的典型步骤:1.了解零件图纸和工艺要求:仔细研究零件图纸,了解零件的尺寸要求、形状要求以及表面质量要求等,还要确定零件的加工顺序和工艺路线。
2.选择工具和刀具:根据零件的要求和加工工艺,选择合适的车刀、镗刀、钻刀及其加工参数。
3.制定加工工艺:根据零件的尺寸要求和形状要求,制定适当的车削切削参数和轮廓刀补偿值,并确定刀具路径。
4.确定坐标系和参考点:选择适当的坐标系和参考点,并确定零点的坐标位置。
5.数控系统参数设置:根据机床和数控系统的特点,设置数控系统的参数,如坐标系、移动速度、进给量等。
6.编写数控程序:使用数控编程语言,按照零件加工工艺要求,逐步编写数控程序。
7.先练习:在计算机仿真软件中,根据编写的数控程序进行仿真操作,以验证程序正确性。
修正程序错误。
8.载入数控系统:将编写好的数控程序,通过U盘、本地网络等方式,载入数控系统中。
9.导入刀具和工件坐标:确定刀具的初始位置、起刀点和工作零点,导入数控系统中。
10.设置工件坐标系:根据图纸和实际加工需求,设置工件坐标系和坐标偏移。
11.调试程序:使用手动操作或自动操作,对数控系统进行调试,确保程序的安全性和准确性。
12.加工实践:进行实际加工操作,监控加工过程中各项参数的变化,并及时调整。
13.检验零件:完成加工后,根据图纸要求进行零件的测量和检验,确保零件质量满足要求。
14.优化程序:根据实际加工情况,调整和优化数控程序,提高加工效率和质量。
15.存档和备份:将编写好的数控程序进行保存和备份,以备后续使用。
总结起来,数控车床程序编制是一项精细的工作,需要熟悉机床、工具和数控系统的基本原理,同时要具备良好的图纸分析和数控编程能力。
通过以上步骤的严格执行,可以确保数控车床加工过程的准确性和安全性。
车削加工循环指令

数控加工的程序编制——车削加工循环1、单一外形固定循环指令G90、G92、G94。
①外径、内径车削循环指令G90。
②螺纹车削循环指令G92。
③端面车削循环指令G94。
2、复合固定循环指令。
①外径、内径粗加工循环指令G71。
②端面粗加工循环指令G72。
③固定形状粗车循环指令G73。
外径、内径车削循环指令G901、圆柱面车削循环的编程格式:G90 X(U)Z(W) F ;圆锥面车削循环的编程格式:G90 X(U)Z(W)R F ;2、R表示快速进给,F为指定速度进给。
3、用增量坐标编程时地址U、W的符号由轨迹1、2的方向决定,沿负方向移动为负号,反之为正号。
4、用增量坐标编程时要注意R的符号,确定方法是锥面起点坐标大于终点坐标时为正,反之为负。
圆柱面车削循环(左)、圆锥面车削循环(右)螺纹车削循环指令G921、值螺纹车削循环的编程格式:G92 X(U)Z(W) F ;圆锥螺纹车削循环的编程格式:G92 X(U)Z(W)R F ;2、X(U)、Z(W)为终点坐标,F为螺纹的导程,R为螺纹大小端的差值,当X向切削起点坐标小于切削终点坐标时R为负,反之为正。
端面车削循环指令G941、值螺纹车削循环的编程格式:G92 X(U)Z(W) F ;圆锥螺纹车削循环的编程格式:G92 X(U)Z(W)R F ; 各地址代码的用法同G94。
螺纹车削循环,圆锥螺纹(a)、直螺纹(b)直端面车削循环(左)、圆锥面车削循环(右)外径、内径粗加工循环指令G711、格式:G71 U∆d Re;G71 P ns Q nf U∆u W∆w F;2、式中,ns 为精加工第一个程序段的顺序号;nf为精加工最后一个程序段的顺序号;∆u 为X轴方向的精加工余量;∆w 为Z轴方向的精加工余量;∆d为粗加工每次切削的被吃刀量;e为每次切削循环的退刀量。
端面粗加工循环指令G72格式:G71 U∆d Re;G71 P ns Q nf U∆u W∆w F;固定形状粗车循环指令G73格式:G71 U∆d Re;G71 P ns Q nf U∆u W∆w F;外径粗加工循环(左)、端面粗加工循环(右)固定形状粗车循环。
- 1、下载文档前请自行甄别文档内容的完整性,平台不提供额外的编辑、内容补充、找答案等附加服务。
- 2、"仅部分预览"的文档,不可在线预览部分如存在完整性等问题,可反馈申请退款(可完整预览的文档不适用该条件!)。
- 3、如文档侵犯您的权益,请联系客服反馈,我们会尽快为您处理(人工客服工作时间:9:00-18:30)。
2、常用编程指令:
刀尖半径补偿指令: G40、G41、 G42 循环指令:单一固定循环指令(G70 、 G77、G78) 复合固定循环指令( G71 、G72、 G73 、G76 ) 子程序指令 直径编程方式 ,半径编程方式 恒速切削和恒转速切削指令 进给速度和恒进给量切削速度
3、常用编程指令举例
3)恒进给速度与恒进给量指令 (G94 G95)
ISO标准:
G94:恒进给速度(mm/min) G95:恒进给量(mm/r) 格式: G94 ( G95) F___
华中I系统标准
G98:恒进给速度(mm/min) G99:恒进给量(mm/r) 格式: G98 ( G99) F___ 举例: G98 F100 :
车削加工程序编制
1、零件加工特点:
主要为轴类、盘类等回转体零件。 主要加工表面为内外圆柱面、圆锥面、成形表面、螺纹和端面,以 及还需要做车槽、倒角、切断、钻孔、扩孔、铰孔等工作。 可在一次装夹中完成更多的加工工序,提高加工精度和生产效率。 X方向分直径和半径,直径是回转零件常用的标注方式。 切削需要多次吃刀。
I-5 F2
3)端面切削循环
(平面端面切削循环)
…… G00 X85 Z5 G94 X30 Z-5 F0.2 Z-10 Z-15 .....
编程格式 G94 X(U)~ Z(W)~ F~ 式中:X、Z- 端面切削的 终点坐标值; U、W-端面切削的终点相 对于循环起点的坐标。
举例: G01 X65 Z2 G90 X60 Z-35 I-5 F0.2 X50 G00 X100 Z200
3)螺纹切削循环指令(G78)
螺纹切削循环指令把“切入-螺纹切削-退刀-返回”四个动作作为一个循环,用一个 程序段来指令。
编程格式
G78 X(U)~ Z(W)~ I~ F~ 式中:X(U)、 Z(W) - 螺纹切削的终点 坐标值; I - 螺纹部分半径之差,即螺纹切削起 始点与切削终点的半径差。加工圆柱 螺纹时,I=0。加工圆锥螺纹时,当X 向切削起始点坐标小于切削终点坐标 时,I为负,反之为正。 (X坐标值依据《机械设计手册》查表确 定) F - 螺纹导程。
G77圆柱面切削循环指令举例
N10 G50 X200 Z200 T0101 N20 M03 S1000 N30 G00 X55 Z4 M08 N40 G01 G96 Z2 F2.5 S150 N50 G77 X45 Z-25 F0.2 N60 X40 N70 X35 N80 G00 X200 Z200 N90 M30
注意:其他系统常用的螺纹的加工为:G33、G92、G82
圆柱螺纹的加工程序编写举例
(螺纹导程4mm,升速进刀段δ 1=3mm,降速退刀段 δ 2=1.5mm,螺纹深度2.165 mm 大径=60mm)。
螺纹的加工程序。
…… G00 X115.67 Z84.5 G78 X58.5 X57.5 X56.5 X56 X55.77 …… Z10.7 F4
(恒进给速度100mm/min)
应用:
G95恒进给量用于加工螺纹。
G99 F0.3
(恒进给量0.3mm/r)
4、单一固定循环
单一固定循环可以将一系列连续加工动作,如“切入-切 削-退刀-返回”,用一个循环指令完成,从而简化程序。
圆柱面或圆锥面切削循环
平面端面切削循环
包括
端面切削循环
锥面端面切削循环
2)圆锥面单一固定循环(G77)
编程格式 G77 X(U)~ Z(W)~ I~ F~ 式中:X、Z- 圆锥面切削的终 点坐标值; U、W-圆柱面切削的终点相对 于循环起点的坐标; I- 圆锥面切削的起点相对于 终点的半径差。如果切削起点 的X向坐标小于终点的X向坐标,
I值为负,反之为正。
I=(D1-D2)/2
螺纹切削循环
1)圆柱面单一固定循环(G77)
编程格式 G77 X(U)~ Z(W)~ F~ 式中:X、Z- -圆柱面切削的 终点坐标值; U、W--圆柱面切削的终点相 对于循环起点坐标分量。 F - -切削进给量
华中I型:G80 X(U)~ Z(W)~ F~ FUNAC:G90 00 X35 Z104 G78 X29.2 Z53 F1.5 X28.6 X28.2 X28.04 G00 X200 Z200
圆锥螺纹的加工程序编写
…… G00 X80 Z62 G78 X49.6 Z12 X48.7 X48.1 X47.5 X47 G00 X200 Z200 ……
1)刀尖圆弧半径自动补偿指令G40、G41、 G42举例 2)恒速切削G96与恒转速切削G97指令举例 3)恒进给速度G94与恒进给量G95指令举例 4)固定循环指令举例 (1)单一固定循环指令举例 (G70 、 G77、G78指令) (2)复合固定循环指令举例 (G71、 G72、 G73、 G74 指令) 7) 调用子程序举例
加工图所示零件
2)恒速切削与恒转速切削指令 (G96 G97)
ISO标准:
G96恒速切削指令(最大线速度m/min) G97恒转速切削指令(转速r/min) 格式: G96 ( G97) S___ 应用:G96常用与精加工和半精加工 G97常用与粗加工或半径变化不大的工件. 举例: G96 S180(恒速切削 最大线速度180 m/min) ) G97 S2500(恒转速切削 转速2500r/min)
1)、刀尖圆弧半径自动补偿指令 G40、G41、 G42举例
刀尖位置编码:3 N10 G50 X200 Z175 T0101 N20 M03 S1500 N30 G00 G42 X58 Z10 M08 N40 G96 S200 N50 G01 Z0 F1.5 N60 X70 F0.2 N70 X78 Z-4 N80 X83 N85 Z-15 N90 X85 Z-5 N100 G02 X91 Z-18 R3 F0.15 N110 G01 X94 N120 X97 Z-19.5 N130 X100 N140 G00 G40 G97 X200 Z175 S1000 N150 M30