回转窑除尘脱硫方案
回转窑窑尾烟气SDS干法脱硫除尘的优化分析

第46卷第3期回转窑窑尾烟气SDS干法脱硫除尘的优化分析周英贵(江苏世清环保科技有限公司,南京210012)摘要:镁钙砂煅烧用回转窑窑尾排烟温度在180~220益之间,烟气中含有二氧化硫和粉尘等污染物。
针对回转窑窑尾烟气对环境造成污染问题,配置了高效碳酸氢钠干粉喷射SDS干法脫硫除尘系统。
本文阐述了SDS脫硫技术原理、流程和影响因素分析,并在实际项目中探究了镁钙砂回转窑烟气中二氧化硫和粉尘的去除效果。
结果表明,在实际运行中采用SDS干法脫硫+布袋除尘工艺处理后,烟气能够达到超低排放要求,即二氧化硫排放浓度臆35mg/m3,粉尘排放浓度臆10mg/m3遥该项目投运后所产生的脫硫畐庐物可综合回收利用作为水泥添加剂辅料。
该技术已成功推广应用到其他回转窑、焦炉和水泥窑烟气脫硫项目中,并取得了较好的应用效果。
关键词:回转窑;SDS干法脫硫;布袋除尘;超低排放中图分类号:TQ175.653.6文献标识码:A文章编号:1673-7792(2021)03-0005-05Optimization analysis of SDS dry desulfurization and dedustingof flue gas from rotary kiln tailZhou Yinggui(Jiangsu Slean Environmental ProtectionTechnology Co.,Ltd.,Nanjing210012,China)Abstract:The temperature of flue gas from the rotary kiln is about180益to220益,and the flue gas contains pollutants such as sulfur dioxide and dust.In view of the environmental pollution caused by the flue gas from the kiln tail,an efficient sodium bicarbonate dry powder spray SDS dry desulfurization and dust removal system is equipped.This paper describes the principle,process and influencing factors of SDS desulfurization technology,and explores the removal effect of SO and dust from flue gas of calcium magnesiun sand rotary kiln in a project.The results show that the flue gas can meet the requirements of ultra-low emission,that is,the emission concentration of sulfur dioxide belows35m財m3,the emission concentration of dust belows10mg/m3.After the project is put into operation,the main component of desulfurization by-product can be recycled as cement additive.The technology has been successfully applied to other flue gas desulfurization projects of rotary kiln,coke oven and cement kiln,and achieved good application results.Key words:Rotary kiln;SDS dry desulfurization;Bag filter;Ultra-low emission1前言随着国家对大气污染的环保排放要求越来越严格,烟气治理污染物排放力度也不断加大,钢铁冶金行业的烟气治理越来越受到重视。
回转窑除尘脱硫方案

回转窑除尘脱硫方案回转窑是一种常用的水泥生产设备,其生产过程中会产生大量的粉尘和废气,其中包含很高的二氧化硫含量。
为了减少环境污染,回转窑需要配备除尘和脱硫设备。
下面是一种针对回转窑的除尘脱硫方案。
一、除尘方案1.利用静电除尘器:将回转窑产生的烟气通过静电除尘器进行除尘。
静电除尘器是一种高效的除尘设备,通过电场作用使粉尘颗粒带电并沉降到集尘板上。
这种方式适用于颗粒直径在0.1-100微米的细颗粒。
2.安装布袋除尘器:静电除尘器可以有效去除微细颗粒,但对于较大颗粒的除尘效果较差。
因此,可以再设置布袋除尘器进行更彻底的除尘。
布袋除尘器利用滤袋的孔隙大小和过滤速度将烟气中的粉尘截留在滤袋上,清洁的气体经过滤袋排出。
3.设置湿式电除尘器:湿式电除尘器是一种利用水雾将颗粒截留的除尘设备。
将回转窑的烟气通过湿式电除尘器,烟气中的颗粒会被水雾截留下来,从而达到除尘的效果。
二、脱硫方案1.使用石灰石脱硫:石灰石脱硫是一种常用的脱硫方法。
将石灰石喷入烟气中,石灰石与二氧化硫发生反应生成石膏,从而达到脱硫的效果。
这种方法具有成本低、效果好的优点。
2.采用湿法脱硫:湿法脱硫是一种高效的脱硫方法。
通过喷洒液体吸收剂(如石灰浆或海藻酸钠溶液)使二氧化硫被吸收,并与吸收剂反应生成固体废物。
这种方法脱硫效果好,但操作和维护成本较高。
以上是一种针对回转窑的除尘脱硫方案。
根据实际情况,可以根据生产工艺和环境要求进行调整和优化。
同时,还需要及时监测和维护除尘脱硫设备,确保其正常运行和高效除尘脱硫。
回转窑除尘脱硫方案
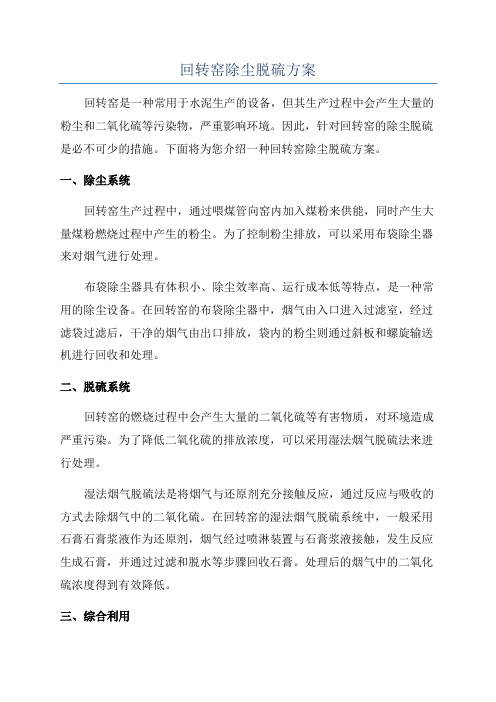
回转窑除尘脱硫方案回转窑是一种常用于水泥生产的设备,但其生产过程中会产生大量的粉尘和二氧化硫等污染物,严重影响环境。
因此,针对回转窑的除尘脱硫是必不可少的措施。
下面将为您介绍一种回转窑除尘脱硫方案。
一、除尘系统回转窑生产过程中,通过喂煤管向窑内加入煤粉来供能,同时产生大量煤粉燃烧过程中产生的粉尘。
为了控制粉尘排放,可以采用布袋除尘器来对烟气进行处理。
布袋除尘器具有体积小、除尘效率高、运行成本低等特点,是一种常用的除尘设备。
在回转窑的布袋除尘器中,烟气由入口进入过滤室,经过滤袋过滤后,干净的烟气由出口排放,袋内的粉尘则通过斜板和螺旋输送机进行回收和处理。
二、脱硫系统回转窑的燃烧过程中会产生大量的二氧化硫等有害物质,对环境造成严重污染。
为了降低二氧化硫的排放浓度,可以采用湿法烟气脱硫法来进行处理。
湿法烟气脱硫法是将烟气与还原剂充分接触反应,通过反应与吸收的方式去除烟气中的二氧化硫。
在回转窑的湿法烟气脱硫系统中,一般采用石膏石膏浆液作为还原剂,烟气经过喷淋装置与石膏浆液接触,发生反应生成石膏,并通过过滤和脱水等步骤回收石膏。
处理后的烟气中的二氧化硫浓度得到有效降低。
三、综合利用除尘和脱硫过程中产生的废水、固体废物等需要进行处理和综合利用。
例如,湿法除尘过程中产生的废水可以进行沉淀和澄清后,用于冲洗系统和循环利用。
而脱硫过程中产生的石膏可以作为水泥生产过程中的掺合材料使用,达到资源的综合利用。
综上所述,回转窑除尘脱硫方案主要包括布袋除尘器和湿法烟气脱硫系统。
通过这些装置,可以有效地控制回转窑生产过程中产生的粉尘和二氧化硫等污染物的排放,达到环境保护的目的。
同时,对除尘和脱硫过程中产生的废水和固体废物进行处理和综合利用,可以实现资源的循环利用,进一步减少对环境的负面影响。
带余热锅炉回转窑烟气治理方案

带余热锅炉回转窑烟气治理方案带余热锅炉通过充分利用烟气中的余热,将其转化为热水或蒸汽供热,达到节能减排的目的。
然而,带余热锅炉在运行中会产生烟气排放,其中含有大量的污染物。
为了有效治理带余热锅炉回转窑烟气,以下是一种可能的治理方案:1.减少烟气排放:通过优化燃烧工艺,控制燃烧温度和燃料供应量,减少燃烧产生的污染物。
采用低氮燃烧技术,减少氮氧化物的生成,安装烟气脱硫装置,减少硫化物的排放量。
通过定期维护和清洁燃烧设备,确保燃烧效率和排放符合相关标准。
2.烟气净化处理:采用干法除尘技术,如静电除尘器或布袋除尘器,去除烟气中的颗粒物。
通过电场和滤料的作用,将颗粒物吸附、捕集和分离。
同时,可以添加除尘剂,增加除尘效果。
针对烟气中的有机污染物和重金属等有害物质,可采用活性炭吸附或催化氧化等方法,以进一步净化烟气。
3.余热利用:带余热锅炉通过烟气中的余热产生热水或蒸汽供热,因此需要设置余热回收装置,将烟气中的余热转化为有用能源。
可以采用换热器进行热量交换,将烟气中的高温热量传递给水或蒸汽,提高能源利用率。
同时,还可以将余热用于制冷、发电等方面,增加其综合利用效益。
4.监测与管理:建立监测系统,对烟气排放进行实时监测和数据记录。
通过监测设备和传感器,对烟气中的污染物进行监测和分析,及时发现和解决问题。
同时,制定管理措施,加强运行管理和维护保养,保证设备正常运行和效果稳定。
5.宣传与培训:对工作人员进行环保意识和技能的培训,提高其对带余热锅炉回转窑烟气治理的认识和操作技能。
加强企业内部宣传,使员工和各相关部门都能够积极参与和支持治理工作,形成企业内部良好的环境保护氛围。
综上所述,带余热锅炉回转窑烟气治理方案主要包括减少烟气排放、烟气净化处理、余热利用、监测与管理以及宣传与培训等方面的措施。
通过综合运用这些措施,可以有效治理带余热锅炉回转窑烟气,达到节能减排的目的,提高企业的环保水平。
氧化锌法脱硫技术在回转窑烟气处理中的应用

氧化锌法脱硫技术在回转窑烟气处理中的应用摘要:回转窑烟气采用氧化锌工艺处理,无需外购脱硫剂,可使用厂内生产中产生的烟尘脱硫产物可返回其他工艺以回收锌,与常规冶炼流程相结合,不外排废弃物,副产品能在厂内循环利用,无二次污染。
基于此,本文重点论述了氧化锌法脱硫技术在回转窑烟气处理中的应用。
关键词:氧化锌法脱硫;回转窑;烟气湿法炼锌中产生的浸出渣在回转窑中进行处理,生产中排放的烟气SO2浓度符合《大气污染物综合排放标准》(GB16297)中960mg/m3限值。
因窑龄过长,系统设备老化严重,目前尚无烟气脱硫设施,此外,现有多膛炉脱氟氯系统,烟气仅配备除尘设备,自新标准《铅锌工业污染物排放标准》(GB25466)实施以来,回转窑尾气SO2排放量不能满足新标准400mg/m3限值要求。
随着环保管理的日益严格,烟气治理至关重要。
回转窑系统迫切需提高装备水平,配备新的烟气脱硫系统,以满足最新国家烟气排放标准。
一、烟气脱硫工艺1、石灰石-石膏法。
这是一种广泛使用的脱硫方法,被许多冶炼厂采用。
其吸收剂来源广泛,可实现较高的脱硫效率,通常为95%。
需外购石灰石粉(大于250目)或石灰现场配浆,当前该方法的主要问题是副产石膏的去向,一般销路有限,因此要考虑石膏的储存和二次污染问题。
2、氧化锌法。
吸收剂氧化锌粉通常来自铅锌厂的氧化锌烟尘。
副产品硫酸锌溶液送至湿法系统,产生的一定量过滤渣为未完全反应的氧化锌及亚硫酸锌,可与锌精矿一起送至焙烧系统,回收锌及SO2。
当过程渣产量较大时,废电解液也可用于处理过滤渣以回收SO2,SO2返回硫酸系统再使用。
该方法特别适用于铅锌冶炼企业,可与厂内冶炼系统有机结合,无需外购原料,脱硫产物可直接返回厂内系统,实现资源的综合利用。
二、氧化锌法脱硫工艺1、工艺原理。
回转窑烟气中SO2在吸收塔内和一定浓度ZnO浆液发生以下主反应:SO2溶解于水中反应机理:SO2+H2O→HSO3-+H+HSO3-→SO2-3+H+ZnO溶解于水中反应机理为:ZnO+2H+→Zn2++H2OSO2在吸收塔内与一定浓度ZnO浆液反应机理:Zn2++SO2-3→ZnSO3Zn2++HSO3-→Zn(HSO3)2ZnO+SO2+H2O→ZnSO3·H2O亚硫酸属于二元酸反应过程,会生成两种盐,若ZnO过剩则生成中性盐ZnSO3,若SO2过剩则生成酸性盐Zn(HSO3)2。
回转窑烟气半干法净化技术方案(7.18)

Φ3.0×60m回转窑脱硫脱硝除尘烟气治理技术文件山东凯瑞环保科技有限公司日期:2019年7月第一章工程概述贵公司拟新建现有两条φ3.0×60m回转窑,用于煅烧陶粒砂,窑炉用焦化煤气作为燃料,窑炉的燃烧温度为1450℃—1550℃。
窑炉在燃烧的过程中产生一定的SO2、NOx以及粉尘,会对周围的大气环境造成一定的污染,根据国家环保排放标准和当地环保部门的要求进行进一步烟气治理,确保窑炉尾部排放SO2、颗粒物、NO X按照国家和当地环保排放要求达标排放。
本期工程方案为窑炉烟气治理工程脱硫、除尘、脱硝一体化系统的设计、制造、安装调试、达标运行,针对业主方的现场特点,结合我司的工艺技术和工程经验,从工艺技术、安全运行、排放指标、经济指标等各方面进行了细致的论证,提出以以蜂窝体催化剂为载体氨水作为还原剂的SCR选择性催化还原法脱硝;CaOH为脱硫剂的半干法脱硫;余热利用;低压脉冲长布袋除尘器除尘,最终达标排放的工艺路线。
本技术方案在给定设计条件下,颗粒物≤10mg/Nm³;SO2≤50mg/Nm³;NO X ≤100mg/Nm³(折算基准氧含量为18%)的排放指标进行整体设计。
技术方案包括脱硫、脱硝、除尘系统正常运行所必须具备的工艺系统设计、设备选型、采购或制造、运输、土建(构)筑物设计、施工及全过程的技术指导、安装督导、调试督导、试运行、考核验收、人员培训和最终的交付投产。
第二章设计说明2.1设计原则按照新建工程考虑,环保要求依据国家相关环保标准,确定如下设计原则:(1)脱硫采用以CaOH为吸收剂的循环流化床法半干法,脱硫后SO2≤50mg/Nm³;除尘采用低压脉冲长布袋除尘的方式,确保粉尘≤10mg/Nm³达标排放,脱硝采用蜂窝体催化剂为载体,18~20%氨水作为还原剂的SCR脱硝。
(2)确保烟气治理系统的安全、稳定运行。
(3)系统设备按照规范、紧凑、合理、美观的原则布置,最大限度地提高场地利用率。
回转窑除尘方案范文

回转窑除尘方案范文回转窑是一种常见的烧结设备,广泛应用于建材行业,但其生产过程中也会产生大量的尘埃污染,给环境造成严重的影响。
为了保护环境、改善空气质量,回转窑除尘方案成为必要的选择。
下面将介绍一种常见的回转窑除尘方案。
首先,回转窑除尘方案的基本原理是通过吸尘器或除尘器对回转窑排放的烟气进行过滤,将其中的尘埃物质捕捉并净化,使其排放出来的烟气符合环境排放标准。
其次,回转窑除尘方案的主要设备包括:旋风分离器、静电除尘器、布袋除尘器等。
其中旋风分离器是最常用的一种,其工作原理是利用离心力将尘埃颗粒分离出来,适用于直径大于10微米的粗颗粒。
静电除尘器则利用电场力使尘埃带电并吸附在带电电极上,适用于直径小于10微米的细颗粒。
布袋除尘器的工作原理则是利用滤料将尘埃物质截留在布袋上,适用于颗粒直径在1-5微米之间的超细粉尘。
再次,回转窑除尘方案的工作流程分为两个阶段:预处理和深度处理。
预处理阶段主要是对粗颗粒尘埃的捕捉和分离,常用的方法是利用旋风分离器进行预处理。
深度处理阶段则是对细颗粒尘埃的捕捉和净化,常用的方法是通过静电除尘器和布袋除尘器进行处理。
最后,回转窑除尘方案的优点在于操作简单、投资成本低、占地面积小等。
同时,针对不同的工况和污染物种类,还可以进行组合使用,使除尘效果更加理想。
此外,还可以通过排放废气进行回收利用,减少资源浪费。
总的来说,回转窑除尘方案是一种有效的控制尘染的措施,具有很高的实用性和经济性。
在实际应用中,还需要根据具体的工况和环境要求进行调整和优化,以确保除尘效果和节能减排的目标能够得到最大程度的实现。
以此为目标,我们可以进一步推动环保事业的发展,保护环境、改善生态。
水泥窑脱硝、脱硫改造技术方案

4000t/d新型干法回转窑窑尾配套SNCR+SC脱硝、湿法脱硫(超低排放改造)工程技术方案XXX日期:2019年7月-、工程概况 (5)1、项目实施的意义和必要性 (5)2、国外技术现状分析 (7)3、窑尾烟气参数 (7)4、方案思路 (7)二、设计依据 (7)1、基本依据 (7)2、基本原则 (8)3、设计标准 (8)三、SNCR+SCR硝工艺设计 (9)1、S NCR兑硝利旧。
(9)2、公用系统主要参数 (9)2、S NCRE艺及设备描述 (9)3、选择性催化还原(SCR脱硝技术 (10)四、湿法脱硫方案 (14)1、S O2吸收系统 (14)2、烟气系统 (16)3、吸收剂供应与制备系统 (18)4、脱硫装置供水及排放系统 (18)5、箱体和容器 (19)6、仪表及控制 (19)7、脱硫岛电气 (20)&石灰一石膏湿法烟气脱硫工艺 (22)五、 ..................................... 技术服务及质量保证251、现场技术服务 (25)2、技术培训 (26)3、售后服务保证 (26)4、设计联络 (27)六、 ................................................. 供货围271、S CR兑硝系统供货围 (27)2、脱硫供货围 (28)一、工程概况1、项目实施的意义和必要性2018年我国水泥总产量已突破20亿吨,NOx排放量已成为火电之后的第二大工业领域。
“十二五”时期,水泥行业是NOx减排的重点行业。
2012年在《水泥工业“十二五”发展规划》指出,到2015年末,NOx排放总量降低10%新建生产线必须配套建设效率不低于60%勺烟气脱硝装置,二氧化硫排放总量降低8% 等目标,“两会”期间,温家宝总理在政府工作报告中也提出要加快燃煤机组脱硝设施建设,加强水泥行业NOX的治理等要求,而同期环保部正在研究相当严格的水泥工业新的NOx排放标准。
- 1、下载文档前请自行甄别文档内容的完整性,平台不提供额外的编辑、内容补充、找答案等附加服务。
- 2、"仅部分预览"的文档,不可在线预览部分如存在完整性等问题,可反馈申请退款(可完整预览的文档不适用该条件!)。
- 3、如文档侵犯您的权益,请联系客服反馈,我们会尽快为您处理(人工客服工作时间:9:00-18:30)。
**化工有限公司回转窑脱硫方案技术文件泊头市实恒除尘设备有限公司技术科提供常经理:传真:第一章总述工程概况公司现有2座回转窑,工况烟气量分别为45000m³/h和80000m³/h(温度为90℃)。
根据国家环保对粉尘及硫化物总量控制要求,该锅炉需配备相应的除尘脱硫装置,使烟尘和二氧化硫排放浓度达到环保标准后方可排放。
根据实际情况及我公司在大气污染治理方面的经验,决定采用脱硫塔脱硫,脱硫方法采用双碱法。
、设计思想及原则1、确保除尘脱硫装置不影响锅炉运行,通过对含硫尾气进行治理,使污染物排放浓度符合业主及当地环保部门的要求。
2、投资省、效果好。
选择合理的治理工艺在有效治理废气的同时,应尽量降低设备的投资和运行成本。
3、脱硫副产品无二次污染,易于处理。
4、除尘脱硫装置能在工况烟气温度加10℃(150℃)的条件下安全连续行。
5充分结合厂方现有的客观条件,因地制宜,制定具有针对性的技术方案。
6、系统平面布置要求紧凑、合理、美观,实现功能分区,方便运行管理。
7、采用钠钙双碱法脱硫工艺,技术成熟、脱硫效率高、运行安全、操作简便。
8、烟气除尘脱硫系统具有应付紧急停机的有效措施。
设计依据《工业炉窑大气污染物排放标准》 GB9078-1996《锅炉大气污染物排放标准》 GB13271-1991《锅炉烟尘测试方法》 GB/T5468-91《工业企业噪声控制设计规范》 GBJ78-85《钢结构设计规范》 GB50205-2001《袋式除尘器安装技术要求与验收规范》 JB/T8471-96《袋式除尘器用滤料及滤袋技术条件》 GB12625-90《除尘机组技术性能及测试方法》 GB/T11653-89《脉冲喷吹类袋式除尘器》 GB/T8532-1997《电器装置安装工程施工技术条件》 GBJ232-82《建筑抗震设计规范》 BJ11-89《固定式钢斜梯》《固定式工业钢平台》《火力发电厂热力设备和管道保温油漆设计技术规定》 DGJ59-84《袋式式除尘器用滤袋框架技术条件》 JB/T5917-91《袋式式除尘器用电磁脉冲阀》 JB/T5916-2004《电气装置安装工程及验收规程》 GBJ232-82《低压分配和电路设计规范》 GBJ54-83《湿式烟气脱硫除尘装置》 HCRJO40—1999《一般工业固体废物贮存、处置场污染控制标准》 GB18599-2001《优质碳素结构钢技术条件》 GB699-88《优质碳素结构钢热轧厚钢板技术条件》 GB711-85《优质碳素结构钢薄钢板和钢带技术条件》 GB710-88《碳钢焊条技术条件》 GB3087-82当地环保部门的有关规定和要求业主提供的烟气参数及相关数据设计范围本设计范围包括烟气除尘脱硫系统工艺、系统结构等专业的设计,工程设计范围:从布袋除尘器至脱硫塔烟气出口之间的脱硫装置和相应配套的附属设施。
包括:§脱硫剂制备系统§除尘系统§SO2吸收系统§脱硫液再生循环系统和脱硫渣处理系统设计参数(1)45000m³/h风量回转窑脱硫设备设计参数(2)80000m³/h风量回转窑脱硫设备设计参数设计要求第二章 脱硫工艺的选择脱硫系统材质性能比较目前国内脱硫塔常用材质一般有:不锈钢、玻璃钢、碳钢内衬玻璃鳞片、麻石。
选择脱硫方案需考虑的因素 (1)原料、燃料的性质和含硫量;(2)当地环保部门对脱硫率的要求、建成后征收的SO2排放费用; (3)烟气脱硫方案技术的成熟性、初投资、将来的运行维护费用; (4)脱硫剂来源、价格及副产品的处理销售; (5)脱硫装置占地;(6)脱硫装置对原设备运行的影响;(7)如果是在原有设施基础上增设脱硫装置,则在选择脱硫方案时尚需考虑由此而引起的拆迁、改建、停产时间,以及整个脱硫工程的经济性、施工工期等方面因素。
工艺选择目前国内外脱硫技术应用最广泛的是湿式石灰石—石膏法,但该技术工程投资大、运行成本高,设备和管路系统易磨损和堵塞。
双碱法是先用可溶性的碱性清液作为吸收剂吸收SO 2,然后再用石灰乳或石灰对吸收液进行再生,由于在吸收和吸收液处理中,使用了不同类型的碱,故称为双碱法。
钠钙双碱法是以碳酸钠或氢氧化钠溶液为第一碱吸收烟气中的SO 2,然后再用石灰或熟石灰作为第二碱,处理吸收液,再生后的吸收液送回吸收塔循环使用。
由于采用钠碱液作为吸收液,不存在结垢和浆料堵塞问题,且钠盐吸收速率比钙盐速率快,所需要的液气比低很多,可以节省动力消耗。
因此,本工程采用钠钙双碱法脱硫工艺。
钠钙双碱法工艺反应原理钠钙双碱法烟气脱硫技术是利用氢氧化钠溶液作为启动脱硫剂,配制好的氢氧化钠溶液直接打入脱硫塔洗涤脱除烟气中SO2来达到烟气脱硫的目的,然后脱硫产物经脱硫剂再生池还原成氢氧化钠再打回脱硫塔内循环使用。
脱硫工艺主要包括5个部分:(1)吸收剂制备与补充;(2)吸收剂浆液喷淋;(3)塔内雾滴与烟气接触混合;(4)再生池浆液还原钠基碱;(5)石膏脱水处理。
钠钙双碱法烟气脱硫工艺同石灰石/石灰等其他湿法脱硫反应机理类似,主要反应为烟气中的SO2先溶解于吸收液中,然后离解成H+和HSO3-;使用Na2CO3或NaOH液吸收烟气中的SO2,生成HSO32-、SO32-与SO42-,反应方程式如下:脱硫反应Na2SO3+SO2→NaSO3+CO2↑(1)2NaOH+SO2→Na2SO3+H2O(2)Na2SO3+SO2+H2O→2NaHSO3(3)其中:式(1)为启动阶段Na2CO3溶液吸收SO2的反应;式(2)为再生液pH值较高时(高于9时),溶液吸收SO2的主反应;式(3)为溶液pH值较低(5~9)时的主反应。
氧化过程(副反应)Na2SO3+1/2O2→Na2SO4(4)NaHSO3+1/2O2→NaHSO4(5)再生过程Ca(OH)2+Na2SO3→2NaOH+CaSO3(6)Ca(OH)2+2NaHSO3→Na2SO3+CaSO3·1/2H2O+3/2H2O(7)氧化过程CaSO3+1/2O2→CaSO4(8)式(6)为第一步反应再生反应,式(7)为再生至pH>9以后继续发生的主反应。
脱下的硫以亚硫酸钙、硫酸钙的形式析出,然后将其用泵打入石膏脱水处理系统,再生的NaOH可以循环使用。
最初的双碱法一般只有一个循环水池,NaOH、石灰和脱硫过程中捕集的飞灰同在一个循环池内混合。
在清除循环池内的灰渣时,烟灰、反应生成物亚硫酸钙、硫酸钙及石灰渣和未反应的石灰同时被清除。
为克服传统双碱法的缺点,对其进行了改进。
主要工艺过程是,清水池一次性加入氢氧化钠制成脱硫液,用泵打入吸收塔进行脱硫。
三种生成物均溶于水,在脱硫过程中,烟气夹杂的飞灰同时被循环液湿润而捕集,从吸收塔排出的循环浆液流入沉淀池。
灰渣经沉淀定期清除,可回收利用。
第三章脱硫系统脱硫塔烟气通过布袋除尘器后,%的尘埃被除去,由卸灰器排出;烟气在引风机的作用下,进入脱硫塔筒体,流速为17m/s的气流高速冲击塔内液面而产生密集气泡,使细微尘埃落入循环液中,部分SO2气体与碱液发生中和反应;烟气在旋流板的作用下旋转上升,以延长烟气在塔内的滞留时间;密集型强雾化置在塔内形成全雾化气幕,使烟气与碱液充分接触,完成完全的中和反应,达到高效脱硫的目的。
被水雾湿润的尘粒流到脱硫塔底部,从溢流孔排走。
在筒体底部封底并设有水封槽以防止烟气从底部漏出,有清理孔便于进行筒体底部清理。
脱硫后废水由底部溢流孔排出进入沉淀池,沉淀中和,循环使用。
带水烟气上升至上层除雾器时,部分湿润烟气由于除雾器的作用,产生气水分离,洁净烟气进入烟囱排入大气。
本装置具有以下优点:1、在塔身采用Q235钢板不锈钢内衬玻璃鳞片制作,有效地防止了酸气腐蚀,并具有足够的耐磨性能,延长设备使用寿命。
而且设备制作周期短,可以现场成套安装,施工时间大大缩短。
2.采用前置风机,避免了风机的带湿带水问题,延长风机使用寿命。
3、采用液膜吸附式液气分离原理制作而成的除雾器,能把微小的小液滴从烟气中分离出来,使系统耗水量降低,以节约运行成本。
4、运用旋流技术、射流技术、压力雾化技术和冲击装置技术,使烟气和脱硫液充分接触,达到理想的脱硫效果。
5、脱硫液循环使用,有PH监测仪和控制系统联动,确保脱硫液的PH值控制在9-12。
6、塔内无运动件,塔体整体制作,降低了漏风率,有效地减少维修几率。
除雾器除雾器可安装在吸收塔上部,以分离净烟气夹带的雾滴。
除雾器出口烟气湿度不大于75mg/Nm3,分为两级布置在脱硫塔上部,设置两级四通道平板式除雾器,一层粗除雾,一层精除雾。
除雾器型式能够保证其具有较高的可利用性和良好的去除液滴效果,且保证脱硫后的烟气以一定流速均匀通过除雾器,防止发生二次携带,堵塞除雾器。
除雾器系统的设计考虑了脱硫装置入口的飞灰浓度的影响。
该系统还包括去除除雾器沉积物的冲洗和排水系统,运行时根据给定或可变化的程序,既可进行自动冲洗,也可进行人工冲洗。
设计了合理的冲洗时间和冲洗水量,既能冲洗干净除雾器,又防止生成二次携带。
位于下面的第一级除雾器是一个大液滴分离器,叶片间隙稍大,用来分离上升烟气所携带的较大液滴。
上方的第二级除雾器是一个细液滴分离器,叶片距离较小,用来分离上升烟气中的微小浆液液滴和除雾器冲洗水滴。
烟气流经除雾器时,液滴由于惯性作用,留在挡板上。
由于被滞留的液滴也含有固态物,因此存在挡板上结垢的危险,同时为保证烟气通过除雾器时产生的压降不超过设定值,需定期进行在线清洗。
为此,设置定期运行的清洁设备,包括喷嘴系统。
冲洗介质为工业水。
喷雾系统(1)喷淋层在本脱硫系统中,为了达到良好的吸收效果,吸收塔设计成逆流式喷淋塔,设置2层的喷淋层,每层喷淋层由若干个高效雾化实心喷嘴组成,而每个喷嘴自成体系统,可单独开启与关闭并可调节其喷液量。
吸收液由喷嘴喷出,喷嘴均匀布置塔内横截面上,喷射出来的成实心锥型的浆液可以覆所需的比表面积的同时,该技术把喷淋造成的压力损失减少到最小。
盖整个横截面,在满足吸收SO2传质吸收时间为2-3秒。
喷嘴是本净化装置最关键的部件,它具有以下特点:①国内雾化喷嘴由于受到国内加工工艺、材料的限制,根本无法与进口的相比拟,为提高脱硫液的雾化程度及雾化的均匀性,我公司引进原装316L高效雾化喷嘴。
②原装高效雾化喷嘴雾化程度好,雾化粒径小,脱硫剂的比表面积大,再加上喷嘴的科学合理布置,使得在预处理区形成无漏洞、重叠少的吸收液雾化区段,与国内技术相比成百、上千倍地提高了烟气与脱硫液接触机会,同时喷液可大幅减少,由此带来烟气温降与脱硫剂之间反应剧烈、反应速度快,这小,由于烟气温度高、气液接触面积大,SO2是保证脱硫效率高的一个主要因素,也给烟尘的成球提供了良好的条件。