铝合金铸件的铸造工艺分析
铝合金的铸造方法
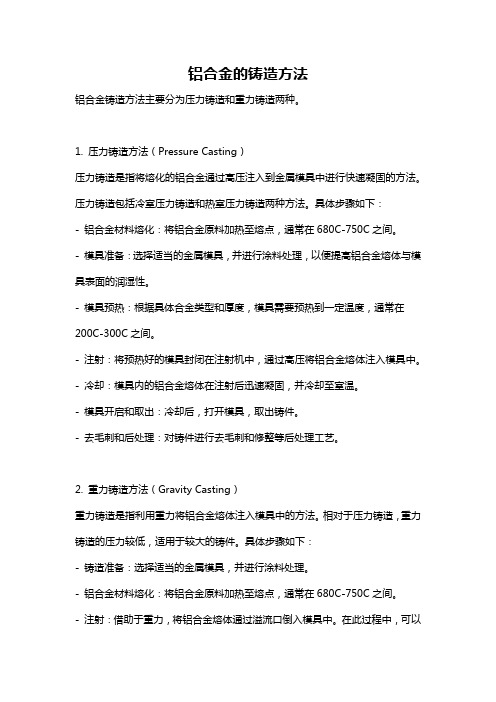
铝合金的铸造方法铝合金铸造方法主要分为压力铸造和重力铸造两种。
1. 压力铸造方法(Pressure Casting)压力铸造是指将熔化的铝合金通过高压注入到金属模具中进行快速凝固的方法。
压力铸造包括冷室压力铸造和热室压力铸造两种方法。
具体步骤如下:- 铝合金材料熔化:将铝合金原料加热至熔点,通常在680C-750C之间。
- 模具准备:选择适当的金属模具,并进行涂料处理,以便提高铝合金熔体与模具表面的润湿性。
- 模具预热:根据具体合金类型和厚度,模具需要预热到一定温度,通常在200C-300C之间。
- 注射:将预热好的模具封闭在注射机中,通过高压将铝合金熔体注入模具中。
- 冷却:模具内的铝合金熔体在注射后迅速凝固,并冷却至室温。
- 模具开启和取出:冷却后,打开模具,取出铸件。
- 去毛刺和后处理:对铸件进行去毛刺和修整等后处理工艺。
2. 重力铸造方法(Gravity Casting)重力铸造是指利用重力将铝合金熔体注入模具中的方法。
相对于压力铸造,重力铸造的压力较低,适用于较大的铸件。
具体步骤如下:- 铸造准备:选择适当的金属模具,并进行涂料处理。
- 铝合金材料熔化:将铝合金原料加热至熔点,通常在680C-750C之间。
- 注射:借助于重力,将铝合金熔体通过溢流口倒入模具中。
在此过程中,可以通过控制溢流口的大小和位置来控制铸件的形状和尺寸。
- 冷却:待铝合金熔体在模具中凝固,冷却至室温。
- 模具开启和取出:冷却后,打开模具,取出铸件。
- 去毛刺和后处理:对铸件进行去毛刺和修整等后处理工艺。
值得注意的是,上述方法仅列举了最常用和基本的铝合金铸造方法,实际生产中还有其他特殊的铸造方法,如砂芯铸造、低压铸造等。
具体方法的选择会根据铸件形状、尺寸和要求等因素进行灵活确定。
铸铝件工艺流程
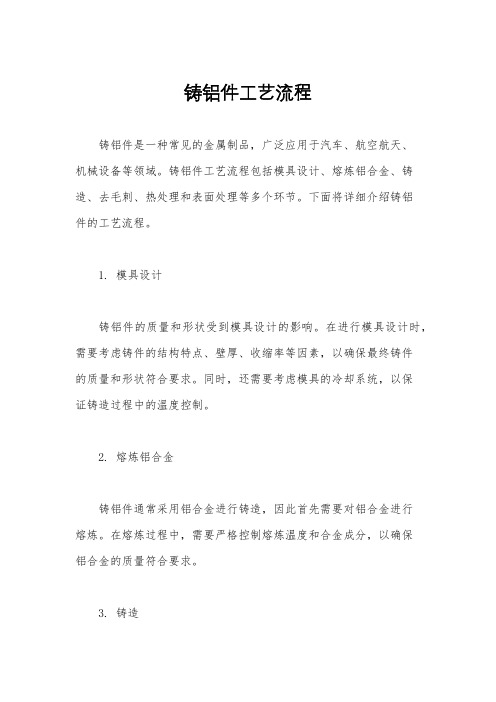
铸铝件工艺流程铸铝件是一种常见的金属制品,广泛应用于汽车、航空航天、机械设备等领域。
铸铝件工艺流程包括模具设计、熔炼铝合金、铸造、去毛刺、热处理和表面处理等多个环节。
下面将详细介绍铸铝件的工艺流程。
1. 模具设计铸铝件的质量和形状受到模具设计的影响。
在进行模具设计时,需要考虑铸件的结构特点、壁厚、收缩率等因素,以确保最终铸件的质量和形状符合要求。
同时,还需要考虑模具的冷却系统,以保证铸造过程中的温度控制。
2. 熔炼铝合金铸铝件通常采用铝合金进行铸造,因此首先需要对铝合金进行熔炼。
在熔炼过程中,需要严格控制熔炼温度和合金成分,以确保铝合金的质量符合要求。
3. 铸造铸造是铸铝件工艺流程中的关键环节。
在铸造过程中,需要将熔化的铝合金倒入预先设计好的模具中,然后等待铸件冷却凝固。
在此过程中,需要注意控制浇注速度、温度和压力,以避免产生气孔、夹杂等缺陷。
4. 去毛刺铸造完成后,铸件表面通常会留有一些毛刺和氧化皮。
因此,需要对铸件进行去毛刺处理,以提高表面质量和加工性能。
5. 热处理铸铝件通常需要进行热处理,以消除残余应力、改善组织结构和提高硬度。
常见的热处理工艺包括时效处理、固溶处理和淬火处理等。
6. 表面处理最后,铸铝件还需要进行表面处理,以提高其耐腐蚀性和装饰性。
常见的表面处理工艺包括阳极氧化、喷涂、电镀等。
总结铸铝件工艺流程包括模具设计、熔炼铝合金、铸造、去毛刺、热处理和表面处理等多个环节。
每个环节都对最终铸铝件的质量和性能有着重要影响。
因此,在生产过程中需要严格控制每个环节,以确保铸铝件的质量符合要求。
铝合金铸造工艺简介
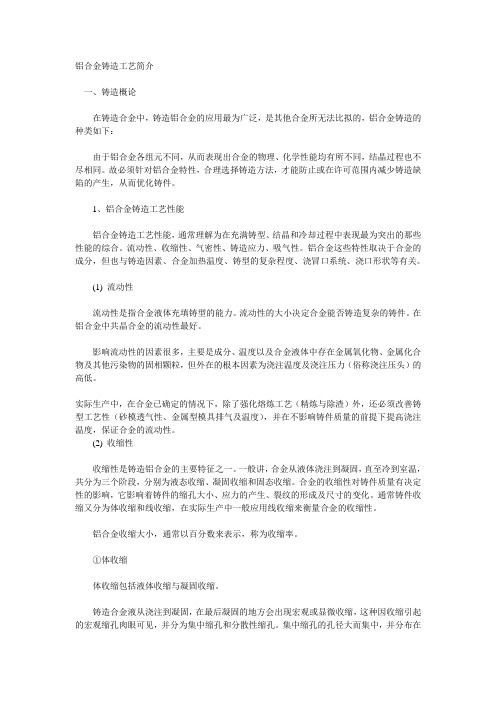
铝合金铸造工艺简介一、铸造概论在铸造合金中,铸造铝合金的应用最为广泛,是其他合金所无法比拟的,铝合金铸造的种类如下:由于铝合金各组元不同,从而表现出合金的物理、化学性能均有所不同,结晶过程也不尽相同。
故必须针对铝合金特性,合理选择铸造方法,才能防止或在许可范围内减少铸造缺陷的产生,从而优化铸件。
1、铝合金铸造工艺性能铝合金铸造工艺性能,通常理解为在充满铸型、结晶和冷却过程中表现最为突出的那些性能的综合。
流动性、收缩性、气密性、铸造应力、吸气性。
铝合金这些特性取决于合金的成分,但也与铸造因素、合金加热温度、铸型的复杂程度、浇冒口系统、浇口形状等有关。
(1) 流动性流动性是指合金液体充填铸型的能力。
流动性的大小决定合金能否铸造复杂的铸件。
在铝合金中共晶合金的流动性最好。
影响流动性的因素很多,主要是成分、温度以及合金液体中存在金属氧化物、金属化合物及其他污染物的固相颗粒,但外在的根本因素为浇注温度及浇注压力(俗称浇注压头)的高低。
实际生产中,在合金已确定的情况下,除了强化熔炼工艺(精炼与除渣)外,还必须改善铸型工艺性(砂模透气性、金属型模具排气及温度),并在不影响铸件质量的前提下提高浇注温度,保证合金的流动性。
(2) 收缩性收缩性是铸造铝合金的主要特征之一。
一般讲,合金从液体浇注到凝固,直至冷到室温,共分为三个阶段,分别为液态收缩、凝固收缩和固态收缩。
合金的收缩性对铸件质量有决定性的影响,它影响着铸件的缩孔大小、应力的产生、裂纹的形成及尺寸的变化。
通常铸件收缩又分为体收缩和线收缩,在实际生产中一般应用线收缩来衡量合金的收缩性。
铝合金收缩大小,通常以百分数来表示,称为收缩率。
①体收缩体收缩包括液体收缩与凝固收缩。
铸造合金液从浇注到凝固,在最后凝固的地方会出现宏观或显微收缩,这种因收缩引起的宏观缩孔肉眼可见,并分为集中缩孔和分散性缩孔。
集中缩孔的孔径大而集中,并分布在铸件顶部或截面厚大的热节处。
分散性缩孔形貌分散而细小,大部分分布在铸件轴心和热节部位。
铝铸件工艺
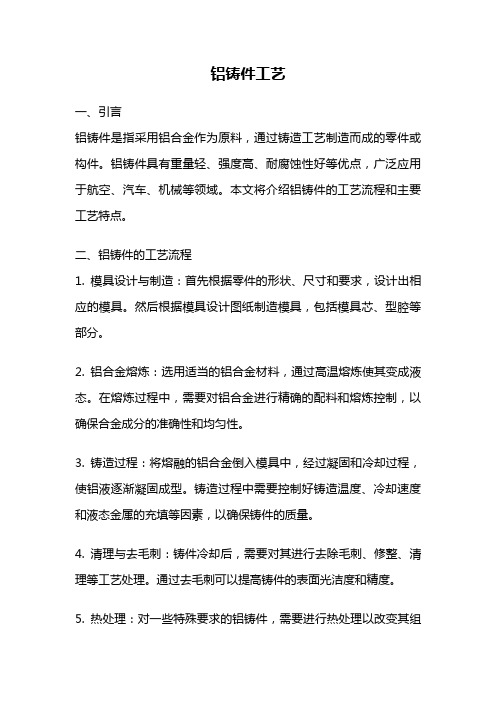
铝铸件工艺一、引言铝铸件是指采用铝合金作为原料,通过铸造工艺制造而成的零件或构件。
铝铸件具有重量轻、强度高、耐腐蚀性好等优点,广泛应用于航空、汽车、机械等领域。
本文将介绍铝铸件的工艺流程和主要工艺特点。
二、铝铸件的工艺流程1. 模具设计与制造:首先根据零件的形状、尺寸和要求,设计出相应的模具。
然后根据模具设计图纸制造模具,包括模具芯、型腔等部分。
2. 铝合金熔炼:选用适当的铝合金材料,通过高温熔炼使其变成液态。
在熔炼过程中,需要对铝合金进行精确的配料和熔炼控制,以确保合金成分的准确性和均匀性。
3. 铸造过程:将熔融的铝合金倒入模具中,经过凝固和冷却过程,使铝液逐渐凝固成型。
铸造过程中需要控制好铸造温度、冷却速度和液态金属的充填等因素,以确保铸件的质量。
4. 清理与去毛刺:铸件冷却后,需要对其进行去除毛刺、修整、清理等工艺处理。
通过去毛刺可以提高铸件的表面光洁度和精度。
5. 热处理:对一些特殊要求的铝铸件,需要进行热处理以改变其组织和性能。
常见的热处理方法包括时效处理、固溶处理等。
6. 机械加工:对于需要进行精密加工的铝铸件,如钻孔、铣削、车削等,需要进行相应的机械加工工艺。
7. 表面处理:根据产品要求和应用领域的不同,可以对铝铸件进行表面处理,如喷涂、阳极氧化、电镀等,以提高其防腐蚀性和美观度。
8. 检测与质量控制:通过各种检测方法对铝铸件进行质量检验,包括外观检查、尺寸测量、力学性能测试等。
确保铝铸件符合设计要求和使用要求。
三、铝铸件工艺的特点1. 模具成本低:与其他铸造工艺相比,铝铸件的模具成本较低,制造周期较短,能够快速满足不同产品的需求。
2. 产品形状复杂:铝铸件工艺适用于各种复杂形状的产品制造,可以生产出具有复杂内部结构和外观形状的零件。
3. 高材料利用率:铝铸件工艺具有较高的材料利用率,废料少,可以有效降低成本。
4. 材料性能优良:铝铸件具有优良的物理性能和机械性能,强度高、刚性好、耐腐蚀性强。
铝合金真空压铸技术

铝合金真空压铸技术铝合金真空压铸技术是一种高效、精密的铝合金铸造工艺,通过在真空环境中进行压铸,可以有效避免铸件表面氧化、气孔等缺陷,提高铸件的质量和性能。
以下是关于铝合金真空压铸技术的详细介绍,包括其工艺流程、优势、应用领域等方面。
一、铝合金真空压铸技术概述铝合金真空压铸技术是一种在真空环境下进行的高压铸造工艺。
其主要步骤包括:模具封闭,抽真空,充填铝液,施加高压,保压定型,冷却固化,开模取件。
整个过程在真空条件下进行,以确保铸件表面无气孔、氧化等缺陷,同时通过高压实现铝液的充分充填,提高铸件的密度和机械性能。
二、铝合金真空压铸技术的工艺流程模具设计和制造:根据产品的形状和尺寸,设计并制造合适的压铸模具,确保模具具有足够的强度和耐磨性。
模具封闭:将设计好的模具封闭,形成一个密封的腔室,以准备进行真空铸造。
真空抽气:在模腔封闭后,通过真空泵将模腔内的空气抽出,创造真空环境。
真空状态有助于减少铝液中气体的溶解,防止气孔的生成。
铝液充填:在真空状态下,将预热至一定温度的铝液注入模腔,确保铝液在模腔中均匀充填。
施加高压:在铝液充填后,施加高压,使铝液充分充填模腔,提高铸件的密度和机械性能。
保压定型:在高压作用下,保持一段时间,使铝液定型成型。
冷却固化:在定型后,通过冷却系统将模腔内的铝液迅速冷却,固化成为铝合金铸件。
开模取件:冷却固化后,打开模具,取出成型的铝合金铸件,进行后续的处理和加工。
三、铝合金真空压铸技术的优势减少氧化和气孔:在真空环境下进行铸造可以有效减少铸件表面的氧化,同时通过真空抽气减少气体的溶解,避免气孔的生成,提高铸件的表面质量。
提高密度和机械性能:高压充填和保压定型能够使铝液充分充填模腔,提高铝合金铸件的密度和机械性能。
精密铸造:铝合金真空压铸技术可以实现更精密的铸造,适用于复杂形状、高精度要求的铝合金零件生产。
高生产效率:由于真空压铸工艺的高压和高速度,可以实现较短的充填时间和较快的冷却速度,提高生产效率。
铝合金重力浇铸与高压铸造
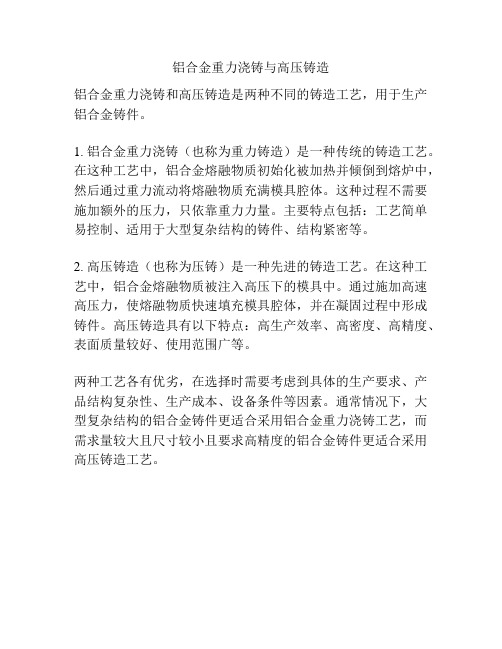
铝合金重力浇铸与高压铸造
铝合金重力浇铸和高压铸造是两种不同的铸造工艺,用于生产铝合金铸件。
1. 铝合金重力浇铸(也称为重力铸造)是一种传统的铸造工艺。
在这种工艺中,铝合金熔融物质初始化被加热并倾倒到熔炉中,然后通过重力流动将熔融物质充满模具腔体。
这种过程不需要施加额外的压力,只依靠重力力量。
主要特点包括:工艺简单易控制、适用于大型复杂结构的铸件、结构紧密等。
2. 高压铸造(也称为压铸)是一种先进的铸造工艺。
在这种工艺中,铝合金熔融物质被注入高压下的模具中。
通过施加高速高压力,使熔融物质快速填充模具腔体,并在凝固过程中形成铸件。
高压铸造具有以下特点:高生产效率、高密度、高精度、表面质量较好、使用范围广等。
两种工艺各有优劣,在选择时需要考虑到具体的生产要求、产品结构复杂性、生产成本、设备条件等因素。
通常情况下,大型复杂结构的铝合金铸件更适合采用铝合金重力浇铸工艺,而需求量较大且尺寸较小且要求高精度的铝合金铸件更适合采用高压铸造工艺。
铝合金铸造工艺
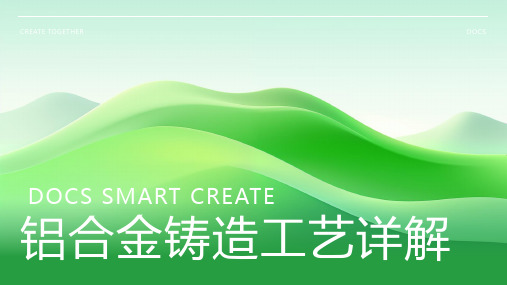
和应用
铝02合金铸造工艺的分类及
特点
重力铸造工艺及特点
重力铸造工艺是将熔融铝倒入模具中,依靠重力作 用使铝液充满模具并凝固成型的一种工艺
• 重力铸造工艺简单、投资成本低,适 用于中小型铸件的生产 • 重力铸造工艺对模具的要求较低,模 具使用寿命较长
学性能
• 挤压铸造工艺适用于对力学性能要求 较高的铸件生产,如汽车制造领域的零 部件 • 挤压铸造工艺对模具和挤压设备的要 求较高,投资成本较大
铝03合金铸造工艺的主要原
材料与辅助材料
铝合金铸造原料的选择及特点
铝合金铸造原料主要包括铝合金锭、合金元素、精炼剂等
• 铝合金锭是铝合金铸造的主要原料,根据不同的性能要求,可以选择不同的铝合 金牌号 • 合金元素用于调整铝合金的成分,改善其性能,如镁、硅、铜等 • 精炼剂用于改善铝合金熔炼过程中的气体含量和杂质含量,提高铸件的质量
铝合金铸造模具的设计需要考虑铸件的形状、尺寸、壁厚等因素
• 模具设计应满足铸件的成型要求,保证铸件的尺寸精度和表面质量 • 模具设计应考虑铸造过程中的温度、压力、时间等参数,确保铸件的质量
铝合金铸造工具的种类及用途
铝合金铸造工具主要包括铸造工具、测量工具、清理工具等
• 铸造工具用于成型铝合金铸件,如压铸工具、重力铸造工具、低压铸造工具等 • 测量工具用于检测铸件的尺寸、形状、质量等,如卡尺、千分尺、投影仪等 • 清理工具用于清理铸件表面的杂质、氧化皮等,如砂轮机、抛光机、喷砂机等
其他铝合金铸造工艺及特点
真空铸造工艺:在真空条件下进行铸造,可以降低 熔融铝中的气体含量,提高铸件的质量
• 真空铸造工艺适用于对气密性要求较 高的铸件生产,如航空航天领域的零部 件 • 真空铸造工艺对设备要求较高,投资 成本较大
铝合金熔铸工艺及常见的缺陷
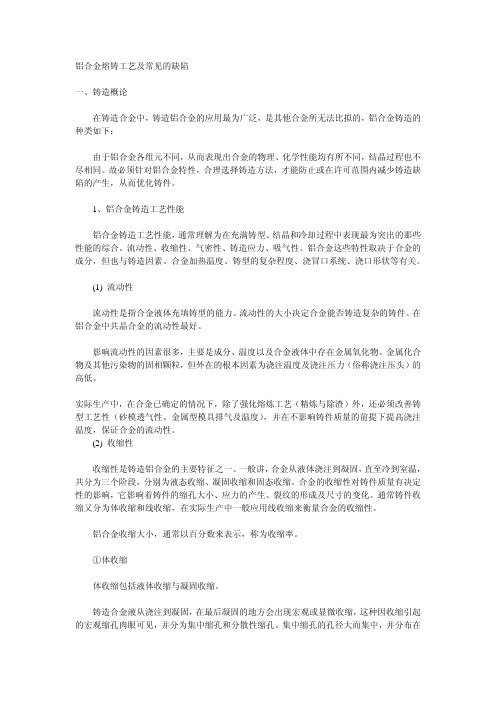
铝合金熔铸工艺及常见的缺陷一、铸造概论在铸造合金中,铸造铝合金的应用最为广泛,是其他合金所无法比拟的,铝合金铸造的种类如下:由于铝合金各组元不同,从而表现出合金的物理、化学性能均有所不同,结晶过程也不尽相同。
故必须针对铝合金特性,合理选择铸造方法,才能防止或在许可范围内减少铸造缺陷的产生,从而优化铸件。
1、铝合金铸造工艺性能铝合金铸造工艺性能,通常理解为在充满铸型、结晶和冷却过程中表现最为突出的那些性能的综合。
流动性、收缩性、气密性、铸造应力、吸气性。
铝合金这些特性取决于合金的成分,但也与铸造因素、合金加热温度、铸型的复杂程度、浇冒口系统、浇口形状等有关。
(1) 流动性流动性是指合金液体充填铸型的能力。
流动性的大小决定合金能否铸造复杂的铸件。
在铝合金中共晶合金的流动性最好。
影响流动性的因素很多,主要是成分、温度以及合金液体中存在金属氧化物、金属化合物及其他污染物的固相颗粒,但外在的根本因素为浇注温度及浇注压力(俗称浇注压头)的高低。
实际生产中,在合金已确定的情况下,除了强化熔炼工艺(精炼与除渣)外,还必须改善铸型工艺性(砂模透气性、金属型模具排气及温度),并在不影响铸件质量的前提下提高浇注温度,保证合金的流动性。
(2) 收缩性收缩性是铸造铝合金的主要特征之一。
一般讲,合金从液体浇注到凝固,直至冷到室温,共分为三个阶段,分别为液态收缩、凝固收缩和固态收缩。
合金的收缩性对铸件质量有决定性的影响,它影响着铸件的缩孔大小、应力的产生、裂纹的形成及尺寸的变化。
通常铸件收缩又分为体收缩和线收缩,在实际生产中一般应用线收缩来衡量合金的收缩性。
铝合金收缩大小,通常以百分数来表示,称为收缩率。
①体收缩体收缩包括液体收缩与凝固收缩。
铸造合金液从浇注到凝固,在最后凝固的地方会出现宏观或显微收缩,这种因收缩引起的宏观缩孔肉眼可见,并分为集中缩孔和分散性缩孔。
集中缩孔的孔径大而集中,并分布在铸件顶部或截面厚大的热节处。
分散性缩孔形貌分散而细小,大部分分布在铸件轴心和热节部位。
- 1、下载文档前请自行甄别文档内容的完整性,平台不提供额外的编辑、内容补充、找答案等附加服务。
- 2、"仅部分预览"的文档,不可在线预览部分如存在完整性等问题,可反馈申请退款(可完整预览的文档不适用该条件!)。
- 3、如文档侵犯您的权益,请联系客服反馈,我们会尽快为您处理(人工客服工作时间:9:00-18:30)。
铝合金铸件的铸造工艺分析
摘要:本文作者结合工作经验,对铸造工艺设计的几个控制要点、铸造工艺设计以及零件的浇注系统设计进行重点分析。
以期参考交流。
关键词:铝合金;筒体;铸造;
中图分类号:ts912+.3文献标识码: a 文章编号:
1、铸件的基本信息
筒体铸件最大轮廓尺寸为准900 mm×850 mm,最大壁厚137 mm,铸件净重约650 kg,属于典型厚壁件,铸件表面全部加工,铸件结构如图1。
筒体铸件虽然我单位生产很多,但此铸件结构与常年生产的筒类铸件结构不同,不同之处在于:在准900 mm的平面上高出
准280 mm×150 mm的圆柱体,正是由于高出的圆柱体给工艺设计和生产操作,带来很大的麻烦。
图1 筒体铸件结构图
2、铸造工艺设计的几个控制要点
2.1 铸件的补缩
对于壁厚较大的铝合金铸件,在铸造工艺设计过程中合金的补缩是十分重要的,如果补缩的作用不够,铸件的最后凝固处易产生缩松,甚至可能产生集中缩孔,造成铸件报废。
在筒体铸件中,φ900 mm处壁厚137 mm (不包括加工量),φ450 mm内腔壁厚125 mm (不包括加工量),对于此类厚壁铸件,因浇注
中型腔热容量大,凝固收缩比较缓慢,后期要求冒口提供的金属液补缩较大,故必须对整体采用强有力的补缩措施,以避免产生缩孔、缩
松等铸造缺陷。
2.2 铸件的冷却
因铸件使用过程中对气密性要求很高,故加大厚大铸件的凝固速度,以获得较细的金相组织,使其铸件表面有一层较细的致密层,是提高其气密性和力学性能重要技术措施。
故对于筒体铸件的内腔厚大部位,必须采用冷铁加强冷却。
2.3 准280 mm×150 mm圆柱体的成型及尺寸控制
如果选择调整铸件壁厚形成准280 mm×150 mm的圆柱体,虽然工艺设计简单,但不可避免将产生以下缺点:
1)为了适应铝合金顺序凝固原则,在准900 mm平面上必须增加很大的工艺补贴及加工量,给后续机加工带来很大麻烦。
2)在很大尺寸范围内改变了铸件结构。
3)产品尺寸及重量大,本以接近单位铸造铝合金生产的极限,如果选择调整铸件壁厚,势必在原来铸件重量的基础上额外再增加重量,进一步增加了熔化操作难度和安全生产隐患。
如果选择砂芯结合实样块形成准280 mm×150 mm的圆柱体,虽然工艺设计相对要复杂,但是可以避免以上缺点。
3、零件铸造工艺设计
3.1 模型及砂芯设计
为了节约成本,模型决定采用3块刮板造型,其中2块刮板形成铸件的轮廓尺寸,1块刮板形成冒口外轮廓尺寸。
冒口内轮廓尺寸由砂芯形成,砂芯中要求作出准280 mm×150 mm的圆柱体实样块;砂芯采用吊芯,且要求有芯骨,以方便砂芯吊装和搬运,以及合箱时测量铸件壁厚的均匀。
3.2 冒口设计
按照铝合金冒口的设计原则,冒口必须将其设置于铸件最高最厚之处,最后凝固,设计冒口必须考虑以下工艺因素。
分析认为在φ900 mm大平面放置冒口,有利于比被补缩的厚大部位晚凝固。
同时可以提高合金液的压头,提高补缩效果。
由于有高出的φ280 mm×150 mm的圆柱体,筒体的冒口设计与以往的冒口设计不一样:冒口补缩压头比以往要高,否则会由于补缩压头不够使φ280 mm平面产生缩孔;冒口根部尺寸设计除了考虑根部尺寸必须大于被补缩热节处尺寸,保证具有足够大小的补缩通道外,还必须考虑砂芯的结构尺寸,否则根部尺寸过大,易使砂芯强度不够,浇注时易冲砂;反之根部尺寸过小,易使补缩通道狭窄,最终在大平面上产生缩孔。
综合以上因素,冒口设计为环形,冒口结构与尺寸如图2,砂芯底部尺寸定为75 mm。
图 2 环形冒口
4、加工量设计
φ900 mm大平面和φ280 mm侧面加工余量均设计为9 mm,其目的是解决φ900 mm大平面的夹渣、气孔缺陷,同时避免由于合箱时
误差,造成φ280 mm尺寸偏差。
φ280 mm平面加工余量为12 mm,其目的是解决铸件最高处最易产生的缩孔缺陷。
铸件的其余表面尺寸加工余量均设计为7 mm。
5、浇注系统设计
采用开放式浇注系统,各组元截面之比为:f直∶ f横∶f内=1 ∶3 ∶ 5。
考虑到铸件的高度较大,直浇道在浇注过程中容易使液流速度过快而形成紊流。
为了控制液流速度,保证充型平稳,采用双层分流方式浇注系统:上层主直浇道1根;下层分流直浇道2根,双向横浇道,内浇道8个。
这种设计的优点可以尽量减少氧化渣被卷入型腔,浇注系统的分布如图3。
(a)上层浇注系统示意图(b)下层浇注系统示意图
图 3 浇注系统示意图
6、冷铁设计
设计1#,2#和3#冷铁,1#为平面代用冷铁,2#和3#为成型冷铁,考虑其可操作性,2#冷铁作成6块变壁厚冷铁,冷铁之间间隙取14 mm,3#冷铁为整体冷铁。
由于2#和3#冷铁的激冷作用直接作用于铸件的使用面上,加快了铸件外层的凝固速度,使铸件表层组织致密,解决内腔气密性问题,与冒口配合使用,进一步增强冒口的补缩效果。
铸件浇注温度控制在695~705 ℃。
7、零件工艺设计图
筒体铸件铸造工艺设计总图如图4。
图 4 筒体铸造工艺图
结论
铝合金筒类铸件为常用铸铝件,此类铸件特点是尺寸大,壁厚,重量大,使用过程中对气密性要求高,其内腔不允许有气孔、夹渣及裂纹等缺陷。
经过上述工艺措施连续生产,铸件内外未发现表面夹渣、气孔和缩孔,内腔加工后表面光洁,使用中未发现漏气现象,满足使用要求。
生产证明:对于大型厚壁筒类铝合金铸件铸造工艺设计,采用环形冒口、冷铁、砂芯及合理制定浇注系统等工艺措施,对解决铸件夹渣、补缩、提高内腔气密性问题是切实可行的。
在工艺设计时需综合考虑众多的影响因素,且生产过程需要采取特殊的工艺控制措施,才能保证铸件的质量。
参考文献:
[1]姜希尚. 铸造手册第五卷铸造工艺[m]. 北京:机械工业出版社,1994.
[2]全国铸造标准化技术委员会编. 最新铸造标准应用手册[m]. 北京:机械工业出版社,1994.
[3]吴定涛 . 某大型框架式铝合金铸件工艺改进[j]. 铸造技术,2011,32(11):1 058-1 060.。