工业控制系统可靠性评估方法探讨
浅谈PLC控制系统的可靠性措施
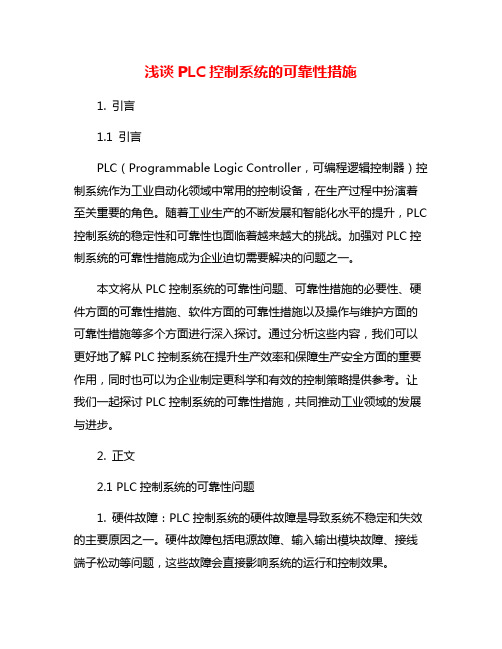
浅谈PLC控制系统的可靠性措施1. 引言1.1 引言PLC(Programmable Logic Controller,可编程逻辑控制器)控制系统作为工业自动化领域中常用的控制设备,在生产过程中扮演着至关重要的角色。
随着工业生产的不断发展和智能化水平的提升,PLC 控制系统的稳定性和可靠性也面临着越来越大的挑战。
加强对PLC控制系统的可靠性措施成为企业迫切需要解决的问题之一。
本文将从PLC控制系统的可靠性问题、可靠性措施的必要性、硬件方面的可靠性措施、软件方面的可靠性措施以及操作与维护方面的可靠性措施等多个方面进行深入探讨。
通过分析这些内容,我们可以更好地了解PLC控制系统在提升生产效率和保障生产安全方面的重要作用,同时也可以为企业制定更科学和有效的控制策略提供参考。
让我们一起探讨PLC控制系统的可靠性措施,共同推动工业领域的发展与进步。
2. 正文2.1 PLC控制系统的可靠性问题1. 硬件故障:PLC控制系统的硬件故障是导致系统不稳定和失效的主要原因之一。
硬件故障包括电源故障、输入输出模块故障、接线端子松动等问题,这些故障会直接影响系统的运行和控制效果。
2. 软件故障:PLC控制系统的软件故障也是一个重要的可靠性问题。
软件bug、编程错误、程序逻辑混乱等问题都可能导致系统的误操作和失效,进而影响设备的正常运行。
3. 通信故障:PLC控制系统通常会涉及到不同模块之间的通信,如果通信出现故障,会导致系统无法正常工作。
通信故障可能是由于网络问题、通信线路故障、通信协议不兼容等原因造成的。
4. 环境因素:PLC控制系统通常安装在工业环境中,在恶劣的环境条件下运行。
高温、湿度、电磁干扰等外部环境因素会对系统的稳定性和可靠性造成影响。
5. 人为误操作:操作人员的操作错误、维护不当等问题也可能导致PLC控制系统的故障和失效。
PLC控制系统的可靠性问题是一个综合性的难题,需要从硬件、软件、通信、环境和人为因素多方面加以考虑和解决。
控制系统中的可靠性分析与可靠性设计

控制系统中的可靠性分析与可靠性设计在现代社会中,控制系统扮演着至关重要的角色。
无论是工业生产、交通运输,还是能源供应等领域,控制系统的稳定运行都是其高效运作的基础。
然而,随着技术的不断发展,控制系统面临着越来越复杂的挑战,其中一个重要的方面就是可靠性。
本文将讨论控制系统中的可靠性分析与可靠性设计。
一、可靠性分析可靠性是指控制系统在给定条件下实现所需功能的能力。
进行可靠性分析是为了识别控制系统中存在的潜在问题,从而提前采取相应的措施来预防故障发生。
下面将介绍可靠性分析的两种常用方法。
1.1 故障树分析故障树分析(FTA)是一种以事件为节点,使用逻辑门进行组合的方法。
它可以清楚地展示在控制系统中各种事件之间的因果关系,并通过定量的方式评估整个系统的可靠性。
在进行故障树分析时,需要考虑到各种可能的故障模式和他们之间的关联。
通过不断细化和扩展故障树,可以找到最重要的故障模式,并为其设计相应的解决方案。
1.2 可靠性块图分析可靠性块图(RBD)是一种图形表示方法,用于描述控制系统中各个子系统之间的可靠性关系。
通过将系统分解成多个子系统,并使用不同类型的块代表系统元素,可靠性块图能够直观地显示系统的结构和可靠性交互。
通过对可靠性块图进行分析,可以计算得出整个系统的可靠性参数,如可用性、失效概率等。
二、可靠性设计可靠性设计是在可靠性分析的基础上,采取相应的措施来提高控制系统的可靠性。
下面将介绍一些常见的可靠性设计方法。
2.1 多元冗余设计多元冗余设计是指在控制系统中引入多个冗余元素,以提高系统的容错性和可靠性。
常见的多元冗余设计包括冗余传感器、冗余执行器和冗余通信链路等。
通过多个冗余元素的互相监测和备份,可以实现对单个元素故障的快速检测与切换,从而提高整个系统的可靠性。
2.2 容错控制算法容错控制算法是指在控制系统中采用一种特殊的算法,能够检测和纠正可能的错误。
常见的容错控制算法包括冗余数据传输、恢复性检测和纠正算法等。
工业控制系统的安全风险评估与防范

工业控制系统的安全风险评估与防范工业控制系统是现代工业生产的核心技术之一,通过计算机软件控制各种物理过程,实现自动化、智能化生产。
工控系统具有稳定性、安全性、可靠性等优点,但也面临着安全威胁,一旦受到攻击,将会给生产企业造成巨大的经济损失。
因此,如何进行有效的安全风险评估与防范控制,对于保障工业生产安全至关重要。
一、工业控制系统安全的现状与威胁目前,全球工业控制系统遭受网络攻击已成为一个常见现象。
据报告显示,2019年,全球工业控制系统遭受的网络攻击数量同比增加了41%,而攻击手段也越来越复杂,形式多样,既有网络钓鱼、木马攻击,也有严重破坏行为如勒索软件和恶意软件。
工业控制系统的一个主要安全问题是缺乏合适的安全措施来保护工业生产网络。
由于工业控制系统在设计时往往会忽视安全因素,一旦网络受到攻击,将会导致生产中断、数据泄露等各种问题,严重影响生产的安全性和质量,并对企业造成不可估量的经济损失。
二、工业控制系统安全风险评估为了避免工业控制系统被攻击,企业必须了解当前的安全风险和可持续的威胁。
以网站未经授权访问为例,以下是一些基本的风险评估步骤:1. 确定需要评估的系统工业控制系统分为多个不同的部分,每个部分都有其特定的网络需要评估。
它们包括控制器、传感器、运动控制器、通信模块和网络接口。
2. 了解威胁要评估安全威胁,必须首先了解每种威胁所需的技术和攻击手段。
攻击者可能会利用漏洞、恶意软件、拒绝服务攻击、社交工程等多种方式进行攻击。
3. 安全漏洞评估评估网络漏洞的目的是确定检测到的目标系统中与安全可用性和完整性有关的漏洞。
评估的方式包括对扫描结果进行潜在与漏洞区别和分类、漏发的目标和漏洞发生的频率、代价等进行评估。
三、工业控制系统安全防范1. 安全意识教育培训企业内部安全培训将有助于员工了解网络安全的重要性。
通过相关的工业控制系统安全漏洞监控系统实现对员工的常识和安全操作的教育和培训,将有助于防止对时间、资金、资源和生产线带来的损失.2. 加强访问控制管理网络管理员应根据实际要求,保护工业控制系统。
工业控制系统的安全评估与风险防护指南及实践案例

工业控制系统的安全评估与风险防护指南及实践案例随着工业控制系统的广泛应用和互联互通趋势的增强,工业控制系统的安全问题日益凸显。
为了保证工业控制系统的正常运行、确保工业生产的可靠性和行业信息的安全性,对工业控制系统进行安全评估并采取相应的风险防护措施变得尤为重要。
本文将为您介绍工业控制系统的安全评估与风险防护指南,并提供一些实践案例供参考。
一、工业控制系统的安全评估1.评估目标确定在进行工业控制系统的安全评估时,首先需要明确评估的目标。
评估可以是全面的,包括硬件设备、软件程序和网络架构等方面的安全性。
也可以是针对特定的系统、部分系统或特定的组件进行的局部评估。
2.风险分析与评估通过对工业控制系统的风险进行分析与评估,可以识别潜在的威胁和漏洞,并评估其对系统安全性的影响程度。
风险分析与评估主要包括:威胁分析、脆弱性分析、风险度量、风险评估和风险通信等过程。
3.安全策略制定根据风险评估的结果,制定相应的安全策略和安全控制措施。
安全策略应综合考虑技术、管理和法规等方面的要求,以确保工业控制系统的安全性。
安全控制措施包括逻辑访问控制、身份认证与授权、数据加密、网络隔离等。
4.安全评估报告撰写综合以上步骤的分析结果和控制措施,撰写工业控制系统的安全评估报告。
报告应包括系统概述、安全评估目标与方法、风险分析与评估结果、安全策略与控制措施等内容,并提出改进建议和风险防范措施。
二、工业控制系统的风险防护指南1.物理安全防护确保工业控制系统的物理安全是保障系统稳定运行的基本前提。
包括建立适当的访问控制措施、视频监控系统、入侵报警系统和物理隔离措施等,以防止未经授权的人员进入控制区域,避免非法接触和破坏控制设备。
2.网络安全防护工业控制系统的网络安全是防止恶意攻击和未授权访问的重要环节。
需要建立网络防火墙、入侵检测系统、流量监控和分析系统等,对网络通信进行监控和审计,及时发现并阻止潜在的网络攻击。
3.安全意识与培训提高工作人员的安全意识和相关知识能力,可以有效减少内部安全漏洞的风险。
控制系统性能评估
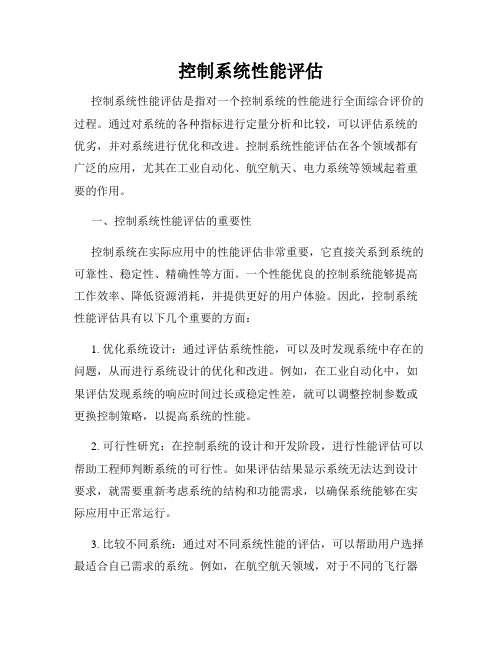
控制系统性能评估控制系统性能评估是指对一个控制系统的性能进行全面综合评价的过程。
通过对系统的各种指标进行定量分析和比较,可以评估系统的优劣,并对系统进行优化和改进。
控制系统性能评估在各个领域都有广泛的应用,尤其在工业自动化、航空航天、电力系统等领域起着重要的作用。
一、控制系统性能评估的重要性控制系统在实际应用中的性能评估非常重要,它直接关系到系统的可靠性、稳定性、精确性等方面。
一个性能优良的控制系统能够提高工作效率、降低资源消耗,并提供更好的用户体验。
因此,控制系统性能评估具有以下几个重要的方面:1. 优化系统设计:通过评估系统性能,可以及时发现系统中存在的问题,从而进行系统设计的优化和改进。
例如,在工业自动化中,如果评估发现系统的响应时间过长或稳定性差,就可以调整控制参数或更换控制策略,以提高系统的性能。
2. 可行性研究:在控制系统的设计和开发阶段,进行性能评估可以帮助工程师判断系统的可行性。
如果评估结果显示系统无法达到设计要求,就需要重新考虑系统的结构和功能需求,以确保系统能够在实际应用中正常运行。
3. 比较不同系统:通过对不同系统性能的评估,可以帮助用户选择最适合自己需求的系统。
例如,在航空航天领域,对于不同的飞行器控制系统,可以通过评估其性能指标来选择最佳的控制系统,以保证飞行器的安全和稳定。
二、控制系统性能评估的指标控制系统性能评估的指标取决于具体的应用领域和系统需求。
以下列举一些常见的性能指标:1. 响应时间:指系统对输入信号的快速响应能力。
响应时间越短,说明系统对外界变化的处理速度越快,适合对变化要求较高的应用。
2. 稳定性:指系统在输入变化时的稳定性能。
稳定性好的系统能够快速达到稳定状态,并保持在稳定状态下工作。
3. 精确度:指系统输出与期望值的偏差大小。
精确度高的系统能够准确地控制输出,并保持在可接受范围内。
4. 鲁棒性:指系统在外部干扰或参数变化时的稳定性能。
鲁棒性好的系统能够抵抗干扰,保持稳定工作。
控制系统的可靠性与安全性分析方法
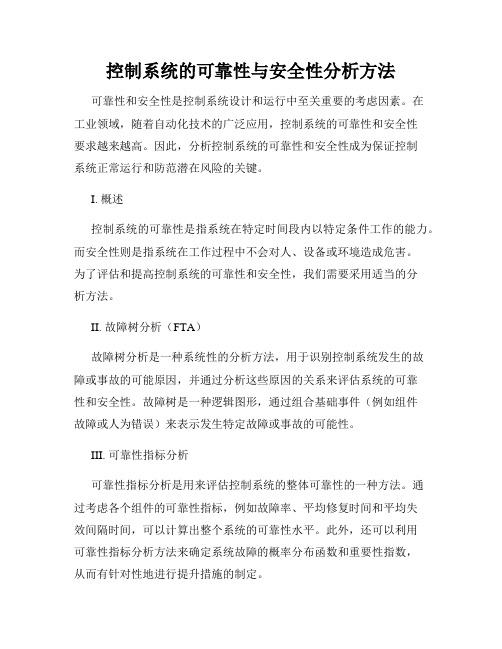
控制系统的可靠性与安全性分析方法可靠性和安全性是控制系统设计和运行中至关重要的考虑因素。
在工业领域,随着自动化技术的广泛应用,控制系统的可靠性和安全性要求越来越高。
因此,分析控制系统的可靠性和安全性成为保证控制系统正常运行和防范潜在风险的关键。
I. 概述控制系统的可靠性是指系统在特定时间段内以特定条件工作的能力。
而安全性则是指系统在工作过程中不会对人、设备或环境造成危害。
为了评估和提高控制系统的可靠性和安全性,我们需要采用适当的分析方法。
II. 故障树分析(FTA)故障树分析是一种系统性的分析方法,用于识别控制系统发生的故障或事故的可能原因,并通过分析这些原因的关系来评估系统的可靠性和安全性。
故障树是一种逻辑图形,通过组合基础事件(例如组件故障或人为错误)来表示发生特定故障或事故的可能性。
III. 可靠性指标分析可靠性指标分析是用来评估控制系统的整体可靠性的一种方法。
通过考虑各个组件的可靠性指标,例如故障率、平均修复时间和平均失效间隔时间,可以计算出整个系统的可靠性水平。
此外,还可以利用可靠性指标分析方法来确定系统故障的概率分布函数和重要性指数,从而有针对性地进行提升措施的制定。
IV. 安全性评估方法在控制系统设计和运行过程中,安全性评估是至关重要的。
一种常用的安全性评估方法是风险评估和风险分析。
通过识别可能的风险和事故,并评估其潜在的影响和发生概率,可以采取相应的措施来降低风险。
此外,还可以使用安全完整性级别(SIL)评估方法对控制系统进行定量的安全性评估,以确保系统满足特定的安全性要求。
V. 故障模式与效果分析(FMEA)故障模式与效果分析是一种通过识别系统中的潜在故障模式,并分析其可能的影响来评估系统可靠性和安全性的方法。
通过定性和定量分析系统中故障模式的发生概率和影响程度,可以制定相应的预防和纠正措施来提高系统的可靠性和安全性。
VI. 系统安全保障措施除了分析方法之外,还需要采取适当的安全保障措施来提高控制系统的可靠性和安全性。
DCS系统的安全性与可信度评估

DCS系统的安全性与可信度评估DCS系统是指分布式控制系统,它在工业自动化领域发挥着重要作用。
然而,随着网络技术的不断发展,DCS系统也面临着安全性与可信度的挑战。
本文将就这一问题展开探讨,并对DCS系统的安全性与可信度评估进行深入分析。
一、DCS系统的安全性评估1.1 定义安全需求在进行DCS系统的安全性评估之前,首先需要明确安全需求。
安全需求包括物理安全、网络安全和数据安全等方面。
物理安全确保DCS系统的硬件设备和控制设备受到保护,防止未经授权的访问和破坏。
网络安全保障DCS系统的通信网络的安全性,防止攻击者通过网络入侵系统。
数据安全确保DCS系统中的敏感数据受到保护,防止数据泄露和篡改。
1.2 评估系统的脆弱性评估DCS系统的脆弱性是评估其安全性的重要环节。
通过对系统进行渗透测试、漏洞扫描和安全演练等手段,可以发现系统中的潜在漏洞和脆弱性,并采取相应的措施进行修补和加固。
1.3 设计安全策略在评估了DCS系统的脆弱性后,需要制定相应的安全策略来提高系统的安全性。
安全策略可以包括防火墙的设置、加密算法的应用、访问控制的管理等方面。
通过合理的安全策略可以有效地减少系统遭受攻击的风险。
二、DCS系统的可信度评估2.1 确定可信度要素要评估DCS系统的可信度,首先需要确定可信度的要素。
可信度要素包括系统的可用性、可靠性和可检测性。
可用性指系统能够按照预定要求进行工作的能力;可靠性指系统在给定时间内能够按照要求提供服务的能力;可检测性指系统能够及时、准确地检测出异常行为和故障的能力。
2.2 评估系统的性能评估DCS系统的性能是评估其可信度的重要环节。
通过对系统的吞吐量、响应时间和资源利用率等性能指标进行评估,可以了解系统的性能状况,判断系统是否能够满足实际应用要求。
2.3 进行故障分析在评估了系统的性能后,需要进行故障分析,找出系统的潜在故障点和问题所在,并采取相应的措施进行修复和增强。
故障分析可以通过故障树分析、故障模式与影响分析等方法进行。
自动控制系统的安全性与可靠性分析
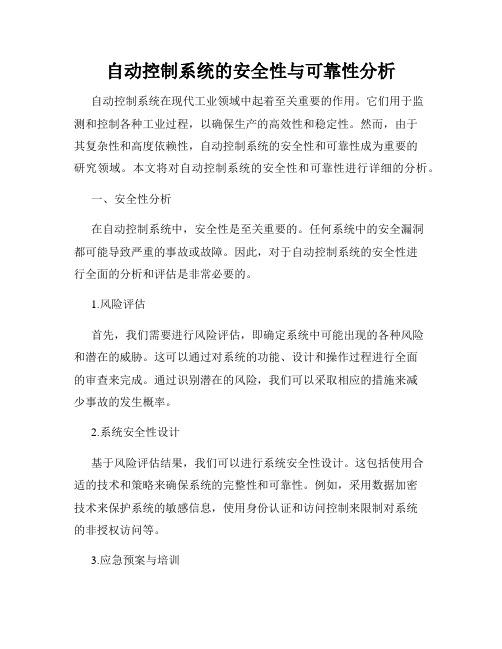
自动控制系统的安全性与可靠性分析自动控制系统在现代工业领域中起着至关重要的作用。
它们用于监测和控制各种工业过程,以确保生产的高效性和稳定性。
然而,由于其复杂性和高度依赖性,自动控制系统的安全性和可靠性成为重要的研究领域。
本文将对自动控制系统的安全性和可靠性进行详细的分析。
一、安全性分析在自动控制系统中,安全性是至关重要的。
任何系统中的安全漏洞都可能导致严重的事故或故障。
因此,对于自动控制系统的安全性进行全面的分析和评估是非常必要的。
1.风险评估首先,我们需要进行风险评估,即确定系统中可能出现的各种风险和潜在的威胁。
这可以通过对系统的功能、设计和操作过程进行全面的审查来完成。
通过识别潜在的风险,我们可以采取相应的措施来减少事故的发生概率。
2.系统安全性设计基于风险评估结果,我们可以进行系统安全性设计。
这包括使用合适的技术和策略来确保系统的完整性和可靠性。
例如,采用数据加密技术来保护系统的敏感信息,使用身份认证和访问控制来限制对系统的非授权访问等。
3.应急预案与培训除了系统安全性设计,制定应急预案也非常重要。
在系统发生故障或事故时,应急预案可以帮助我们迅速采取措施以最小化损失。
同时,为系统操作员和维护人员提供培训以增强其对系统安全性的认识和应对能力。
二、可靠性分析除了安全性,自动控制系统的可靠性也是一个关键的参数。
可靠性表示系统在规定的时间内,以规定的准确度和可用性来执行其功能或任务的能力。
1.可靠性评估可靠性评估是判断系统性能和可靠性的主要方法之一。
通过对系统的各个组件和子系统进行评估,我们可以确定系统在给定条件下的可靠性水平。
这涉及到对系统的故障率、失效模式分析、故障诊断和纠正等方面的研究。
2.容错设计为增强自动控制系统的可靠性,容错设计是一个常用的策略。
容错设计可以使系统在故障情况下保持部分功能,并能够进行相应的故障诊断和修复。
例如,使用冗余组件来代替可能发生故障的组件,以确保系统的连续运行。
- 1、下载文档前请自行甄别文档内容的完整性,平台不提供额外的编辑、内容补充、找答案等附加服务。
- 2、"仅部分预览"的文档,不可在线预览部分如存在完整性等问题,可反馈申请退款(可完整预览的文档不适用该条件!)。
- 3、如文档侵犯您的权益,请联系客服反馈,我们会尽快为您处理(人工客服工作时间:9:00-18:30)。
经典方法是基于系统及其组成设备的试验信息进行 可靠性综合评估的统计方法。如:L M 方法、M M L 方法和W C F 展开方法。其中 L M 方法由成败型单元构成的串联系统, MML 方法适用于由成败型单元构成的系统,WCF 方法适用于 由成败型或指数型单元构成的系统。由于篇幅的限制,本 文只对L M 方法进行防真。
记 nB=29 及 备 B 的等效试验数据。
,则(nB ,rB)=(29,7.076)为设
4.3 贝叶斯统计方法仿真
假设组成上述工业控制系统中的设备 A 服从指数分
布,该设备MTBF 的点估计为11100h,在置信度为90% 的情况
下,M T B F 下限是5 0 0 0 小时,在现场使用了一年以后,出现
在组成系统设备试验数据齐全的情况下采用经典方 法;目前国内外比较统一的经典方法有W C F、LM 和M M L。其 中 L M 方法的评估结果偏保守,M M L 方法在小子样情形时, 评估结果也会有较大偏差。W C F 展开方法的评估结果相对 最精确。经典方法的缺陷是输入信息仍局限于设备的寿命 试验信息,因此在实际应用过程中存在数据利用不充分问 题。
分布。
贝叶斯方法是基于系统及其组成设备的先验信息和
试验信息进行系统可靠性综合评估的方法。其评估的基本
框架如图1 。
图1 贝叶斯统计评估方法
贝 叶 斯 统 计 方 法 与 经 典 统 计 方 法 相 比 ,其 最 大 的 优 点是除了利用系统组成设备的试验信息以外,还可以利用 组成设备的先验信息进行系统可靠性综合评估。
x2 —可查 x2 分布下侧分位数表。 双侧区间表示为: c)置信水平为80% 时的平均寿命 的单侧下限估计值: 对应的单侧置信水平 c=90%,a=10% 求单侧下限估计值: 根据公式:
单侧下限表示为:
测定试验估计结论:该系统MTBF 的真值落在( 1645.8 ~16466.2)小时区间的概率为80%,同样也表明有90% 的概 率使该系统MTBF 真值大于或等于1645.8 小时,但也可能 有10% 的系统MTBF 真值小于1645.8 小时。 4.2 经典方法仿真(LM方法)
5 结 论 经典方法以及贝叶斯统计方法的数学计算比较复杂,
数据量比较大,手动计算难于实现。一般情况下,借助于 软件实现,本单位正在致力于相关软件的开发。
参考文献
[1] 潘茂庆,张有来.贝叶斯法在继电器可靠性评估中的应用[J] .中 国电力资源网,2002.
[2] 夏 洪,甘诚智.电视机可靠性指标的贝叶斯估计方法[J].南昌 大学学报,2000.
3 方法的实用性分析 本主作者对三种评估方法在工业控制系统可靠性评
《自动化与仪器仪表》2011 年第 1 期(总第 153 期)
估领域的运用进行大量研究和实例分析,结论如下: 工 业 控 制 系 统 可 靠 性 评 估 过 程 中 ,在 组 成 系 统 设 备
先验信息丰富且准确的情况下,采用贝叶斯方法。但是其 评估结果的精确度取决于先验信息的准确性。
精确方法要求数据样本量较大,对于目前的可靠性 要求高、研制周期短的系统适用性不强,只有在整机试验 或使用数据完备的情况下采用精确方法。
复杂工业控制系统的可靠性评估往往要综合利用以 上方法。在工业控制系统中,工控机一般是采购比较成熟 的计算机,这类设备的先验信息比较丰富,所以适合采用 贝叶斯方法,而过程控制站大多属于新研产品,在研制过 程中进行了大量的工程试验,在试验数据齐全的情况下, 适合采用经典方法,而针对研制周期较长,试验数据和现 场使用数据丰富的情况下,适合采用精确方法。 4 实例仿真
某工业控制系统由工控机、过程控制站、通信网络和 现场仪表四个寿命指数型设备组成串联系统,其可靠性模 型如图 2 ,投入现场使用一年,期间出现故障次数为 2 次, 失效时间为1200h ,4800h,估计该种产品平均寿命的点估 计值和在置信水平为8 0 % 时,平均寿命的双侧区间估计和 单侧区间估计值。可靠性框图如图 2 所示。
了一次故障,估计该工控机的 M T B F 。
计算先验分布数:r0 ,T0,由公式
图2 工业控制系统可信水平的选择
如选择使用方风险
,则选用 8 0 % 的置信区间,
其单侧置信水平为 9 0 % ; 如选择使用方风险
,则选
用 6 0 % 的置信区间,其单侧置信水平为 8 0 % 。
L M 方法是将系统看做二项分布,并且为由成败型单
收稿日期: 2 0 1 0 - 1 1 - 2 7 作者简介: 桑毅( 1 9 8 3 - ) , 男, 助理工程师, 主要从事可靠性相 关理论的研究, 参与制定国家标准、行业标准等工作。
122
元构成的串联系统,利用系统本身的试验数据(n . , r )和由设 备得到的等效系统试验数据(ns ,rs),根据二项分布,计算系 统的可靠性特征量。
2 工业控制系统可靠性评估概述 工业控制系统可靠性评估技术是工业控制系统领域
一个重要的研究方向。国内外需要统计学家及可靠性工程 师作了大量的研究工作。可靠性综合评估方法有如下三种 类型:精确方法、经典方法和贝叶斯方法。 2.1 精确方法
精确方法是利用工业控制系统在实验室或现场使用 的准确数据运用统计学方法来评估系统的可靠性,并给出 系统可靠性特征量的点估计和区间估计的方法。它包括现 场 数 据 统 计 分 析 法 、可 靠 性 验 证 试 验 、可 靠 性 测 定 试 验 等;其可靠性特征量采用的数学模型是:MTBF=T/r,MTBF 为平均故障间隔时间、T 为工业控制系统总试验时间、r 是 在工业控制系统在试验过程中出现的故障数; 2.2 经典方法
[3] 钟强晖,张志华,董 理.鱼雷装载可靠度的评估方法[J].舰船 科学技术,2010.
[4] 金泉辉. 一类可修系统贮存可靠性评估的 LM 法[D].延边大学, 2009.
123
1 研究背景 随着科学技术的高速发展,工业自动化水平日益提
高,应用于生产过程的工业控制系统已成为企业生产的重 要硬件设施,在生产中起着越来越重要的作用。一套工业 控制系统就好比一个人的大脑,指挥着整个生产装置的运 行,因此工业控制系统可靠性非常重要。但是如何评估工 业控制系统的可靠性,国际上工业控制系统可靠性研究始 于 2 0 世纪 5 0 年代,而国内开展的比较晚,目前国内还没有 一个统一的标准。本文通过比较国内外比较统一的算法和 适用范围进行探讨。
假设组成上述工业控制系统中的设备 B 是由 B1,B2,B3, B4 四个单元组成的串联系统S,B1,B2,B3,B4 是成败型设备,其 试验数据为(n1 ,r1)=(30,3),(n2 ,r2)=(30,2),(n3 ,r3)=(30,1),(n4 ,r4)=(29, 2)。
设备 B 可靠度的点估计:
4 . 1 . 2 可靠性测定试验评估方法
统计分析:
试验时间T=1 ×365 ×24=8760h
a ) 平均寿命 MTBF 的点估计值:
b ) 置信水平为 8 0 % 时的平均寿命 M T B F 双侧区间估计 值,根据公式:
得 代入上式得 r0=3,x2 —可查 x2 分布分位数表:T0=r0 ×MTBF0=11100× 3=33300h 由此可得M T B F 的平均值为
工业控制系统可靠性评估方法探讨 桑 毅,等
工业控制系统可靠性评估方法探讨
桑 毅,隆 萍,刘兴莉 (重庆工业自动化仪表研究所 重庆,4 0 1 1 2 1 )
摘 要:工业控制系统的可靠性评估方法种类繁多,目前没有统一。本文对几种比较统一的方法进行重点分 析,并通过实例仿真的方式对各种方法进行比较,得出结论,供同行参考。
对θ规定一个先验分布,它是在进行推断时不可或缺的一
个要素。贝叶斯学派把先验分布解释为在抽样前就有的关
于θ的先验信息的概率表述,先验分布不必有客观的依
据,它可以部分地或完全地基于主观信念。利用贝叶斯分
布方法进行可靠性综合评估时,评估结果的精确度取决于
先验信息的准确性。在可靠性综合评估过程中,通常是将
不同类型的先验信息转换成设备可靠度或失效率的先验
假定系统的M 个设备的试验数据分别为:(n1 ,r1)……(nM,
rM) ;这时系统可靠度的点估计为:
;记
及 的等效试验数据。
,我们称(ns ,rs)为系统
2.3 贝叶斯方法
贝 叶 斯 统 计 的 根 本 观 点 ,是 认 为 在 关 于 θ 的 任 何 统
计推断问题中,除了使用样本 X 所提供的信息外,还必须