润滑油生产装置简介和重点部位及设备简易版
润滑油生产装置说明与危险因素及防范措施
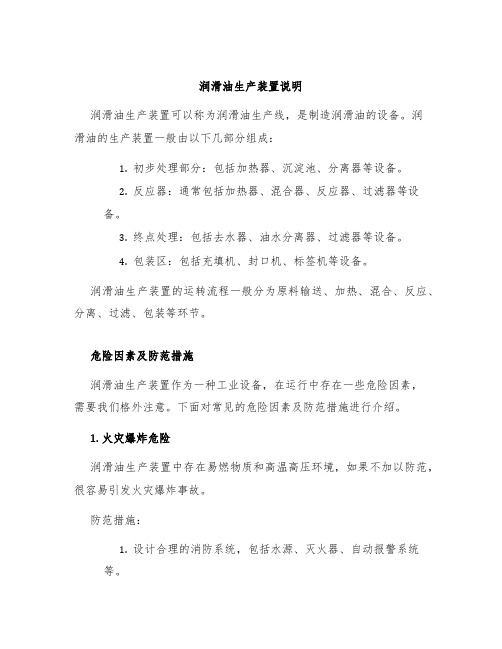
润滑油生产装置说明润滑油生产装置可以称为润滑油生产线,是制造润滑油的设备。
润滑油的生产装置一般由以下几部分组成:1.初步处理部分:包括加热器、沉淀池、分离器等设备。
2.反应器:通常包括加热器、混合器、反应器、过滤器等设备。
3.终点处理:包括去水器、油水分离器、过滤器等设备。
4.包装区:包括充填机、封口机、标签机等设备。
润滑油生产装置的运转流程一般分为原料输送、加热、混合、反应、分离、过滤、包装等环节。
危险因素及防范措施润滑油生产装置作为一种工业设备,在运行中存在一些危险因素,需要我们格外注意。
下面对常见的危险因素及防范措施进行介绍。
1. 火灾爆炸危险润滑油生产装置中存在易燃物质和高温高压环境,如果不加以防范,很容易引发火灾爆炸事故。
防范措施:1.设计合理的消防系统,包括水源、灭火器、自动报警系统等。
2.加强对设备的维护,保证设备正常运行、减少漏油、防止油气泄漏等事故的发生。
3.对员工进行消防安全培训,提高员工火灾意识并指导消防知识。
2. 化学危害润滑油生产装置中的原材料、半成品和成品都有可能对人体产生化学危害,比如吸入、接触等。
防范措施:1.严格执行润滑油生产装置操作规程,如佩戴好防护装备,避免接触有毒有害物质。
2.定期进行环境监测,及时发现问题并采取措施处理。
3.做好现场危险品管理工作,明确危险品种类、数量、存放位置和应急处置措施,提高应变能力。
3. 机械伤害润滑油生产装置中操作人员可能接触到高速旋转机械、高温区域等危险区域,极易发生机械伤害事故。
防范措施:1.严格遵守操作规程,佩戴好防护装备,确保工人人身安全。
2.在机器旁设置相应的安全带、安全脚踏板等安保设施。
3.强化对员工的安全教育培训,提高员工的安全意识。
综上所述,润滑油生产装置的安全生产工作十分重要。
我们要加强安全生产意识,提高危险预判和控制能力,遵守操作规程,做好健康、安全、环保的生产工作。
润滑油生产装置简介
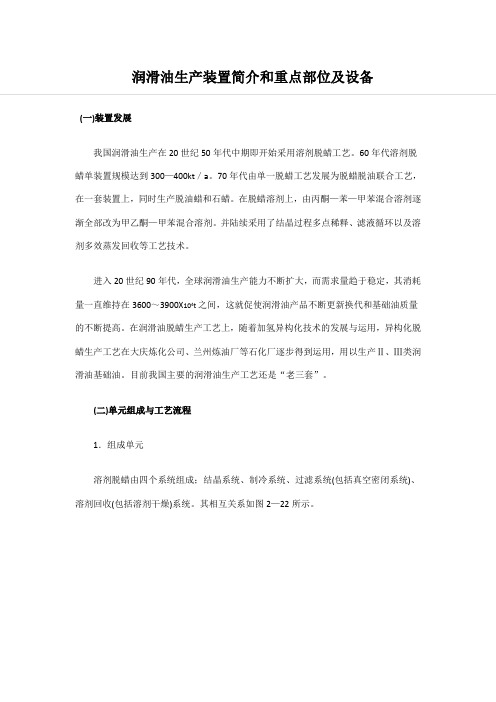
润滑油生产装置简介和重点部位及设备(一)装置发展我国润滑油生产在20世纪50年代中期即开始采用溶剂脱蜡工艺。
60年代溶剂脱蜡单装置规模达到300—400kt/a。
70年代由单一脱蜡工艺发展为脱蜡脱油联合工艺,在一套装置上,同时生产脱油蜡和石蜡。
在脱蜡溶剂上,由丙酮—苯—甲苯混合溶剂逐渐全部改为甲乙酮—甲苯混合溶剂。
并陆续采用了结晶过程多点稀释、滤液循环以及溶剂多效蒸发回收等工艺技术。
进入20世纪90年代,全球润滑油生产能力不断扩大,而需求量趋于稳定,其消耗量一直维持在3600~3900X104t之间,这就促使润滑油产品不断更新换代和基础油质量的不断提高。
在润滑油脱蜡生产工艺上,随着加氢异构化技术的发展与运用,异构化脱蜡生产工艺在大庆炼化公司、兰州炼油厂等石化厂逐步得到运用,用以生产Ⅱ、Ⅲ类润滑油基础油。
目前我国主要的润滑油生产工艺还是“老三套”。
(二)单元组成与工艺流程1.组成单元溶剂脱蜡由四个系统组成;结晶系统、制冷系统、过滤系统(包括真空密闭系统)、溶剂回收(包括溶剂干燥)系统。
其相互关系如图2—22所示。
2.工艺流程典型原则工艺流程见图2—23、图2—24。
工艺流程说明如下:(1)结晶系统结晶系统的流程为:原料油与预稀释溶剂(重质原料时用,轻质原料时不用)混合后,经水冷却后进人换冷套管与冷滤液换冷,使混合溶液冷却到冷点,在此点加入经预冷过的一次稀释溶剂,进入氨冷套管进行氨冷。
在一次氨冷套管出口处加人过滤机高部真空滤液或二段过滤的滤液做二次稀释,再经过二次氨冷套管进行氨冷,使温度达到工艺指标。
在二次氨冷套管出口处再加人经过氨冷却的三次稀释溶剂,进人过滤机进料罐。
图2—23溶剂脱蜡的典型工艺流程(结晶、过滤、真空密闭、制冷部分)I一原料油;Ⅱ一滤流;Ⅲ一蜡液;Ⅳ一溶剂1一换冷套管结晶器;2、3一氨冷套管结晶器;4--溶剂氨冷套管结晶器;5一一段真空过滤机;6——二汇段真空过滤机;7一滤机进料罐;8——段蜡液罐;9——二段蜡液罐;10——段滤液罐;11——二段滤液罐;12——低压氨分离罐;13——氨压缩机;14——中间冷却器;15——高压氨分液罐;16——氨冷凝冷却器;17——液氨储罐;18--低压氨储罐;19——真空罐;20——分液罐;2l——安全气罐图2—24溶剂脱蜡的典型工艺流程(溶剂回收、溶剂干燥部分)I一滤液;Ⅱ一蜡液;Ⅲ—溶剂;Ⅳ一脱蜡油;V一含油蜡1一滤液低压蒸发塔;2--滤液高压蒸发塔;3一滤液低压蒸发塔;4--脱蜡油汽提塔;5—蜡液低压蒸发塔;6——蜡液高压蒸发塔;7--蜡液低压蒸发塔;8--含油蜡汽提塔;9---溶剂干燥塔;10--酮脱水塔;11一滤液加热炉;12—蜡液加热炉;13一溶剂罐;14--湿溶剂分水罐(2)过滤和真空密闭系统过滤系统是使固、液两相分离。
润滑精制装置简介和重点部位及设备
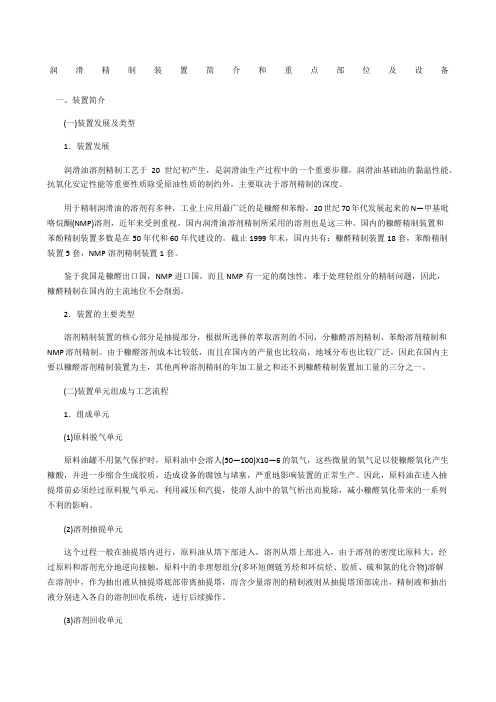
润滑精制装置简介和重点部位及设备一、装置简介(一)装置发展及类型1.装置发展润滑油溶剂精制工艺于20世纪初产生,是润滑油生产过程中的一个重要步骤,润滑油基础油的黏温性能、抗氧化安定性能等重要性质除受原油性质的制约外,主要取决于溶剂精制的深度。
用于精制润滑油的溶剂有多种,工业上应用最广泛的是糠醛和苯酚,20世纪70年代发展起来的N—甲基吡咯烷酮(NMP)溶剂,近年来受到重视,国内润滑油溶剂精制所采用的溶剂也是这三种。
国内的糠醛精制装置和苯酚精制装置多数是在50年代和60年代建设的。
截止1999年末,国内共有:糠醛精制装置18套,苯酚精制装置5套,NMP溶剂精制装置1套。
鉴于我国是糠醛出口国,NMP进口国,而且NMP有一定的腐蚀性,难于处理轻组分的精制问题,因此,糠醛精制在国内的主流地位不会削弱。
2.装置的主要类型溶剂精制装置的核心部分是抽提部分,根据所选择的萃取溶剂的不同,分糠醛溶剂精制、苯酚溶剂精制和NMP溶剂精制。
由于糠醛溶剂成本比较低,而且在国内的产量也比较高,地域分布也比较广泛,因此在国内主要以糠醛溶剂精制装置为主,其他两种溶剂精制的年加工量之和还不到糠醛精制装置加工量的三分之一。
(二)装置单元组成与工艺流程1.组成单元(1)原料脱气单元原料油罐不用氮气保护时,原料油中会溶人(50—100)X10—6的氧气,这些微量的氧气足以使糠醛氧化产生糠酸,并进一步缩合生成胶质,造成设备的腐蚀与堵塞,严重地影响装置的正常生产。
因此,原料油在进入抽提塔前必须经过原料脱气单元,利用减压和汽提,使溶人油中的氧气析出而脱除,减小糠醛氧化带来的一系列不利的影响。
(2)溶剂抽提单元这个过程一般在抽提塔内进行,原料油从塔下部进入,溶剂从塔上部进入,由于溶剂的密度比原料大,经过原料和溶剂充分地逆向接触,原料中的非理想组分(多环短侧链芳烃和环烷烃、胶质、硫和氮的化合物)溶解在溶剂中,作为抽出液从抽提塔底部带离抽提塔,而含少量溶剂的精制液则从抽提塔顶部流出,精制液和抽出液分别进入各自的溶剂回收系统,进行后续操作。
润滑油高压加氢装置总体概况

润滑油高压加氢装置总体概况1.1装置简介本装置是由中国石化总公司北京设计院设计,年加工能力为30万吨的润滑油加氢装置。
全装置共有设备144台,装置总投资64000万元,位置处于石化公司生产区内制氢装置以东,空分装置以南,占地面积11610m2,1999年4月破土动工,于2000年12月投产,各项主要技术指标均已达到设计要求。
1.1.1装置特点克石化30万吨/年润滑油高压加氢装置是属于高温、高压、临氢催化工艺过程的一套装置。
通过采用高压催化加氢对润滑油料进行加氢改质、临氢降凝和加氢补充精制,通过选择催化剂、工艺条件、原料可生产出不同粘度等级的润滑油基础油。
可调制优质的变压器油、冷冻机油和橡胶填充油等,其质量水平达到国际先进水平,轻脱油还可生产出优质的HVIW120BS和HVIW150BS光亮油(指标中粘度指数除外)。
该工艺过程具有良好的原料适应性和产品的灵活性。
本装置采用北京石油化工科学研究院三段加氢工艺,第一段加氢处理采用较苛刻的加氢条件,对润滑油料进行加氢改质;第二段临氢降凝采用专门的催化剂,在临氢状况下,降低基础油的凝点;第三段加氢补充精制用来改善基础油的氧化安定性和光安定性,反应条件较缓和。
装置工艺流程具有如下特点:1、30万吨/年润滑油高压加氢装置采用北京石科院提供的专项技术。
工艺流程为加氢处理—→常压汽提—→临氢降凝—→加氢补充精制—→常减压分馏。
是国内第一套全部采用国内技术的润滑油高压加氢装置。
2、四台反应器均为热壁式反应器,其中R-101是专门针对克石化厂原料中重金属含量较高的情况而设的保护反应器,保证装置长周期平稳运行。
3、新氢压缩机K-101A/B和降凝循环氢压缩机K-201A/B各共用一台电机。
4、四台加热炉全部采用对流-辐射型卧管立式炉。
由于原料变化频繁且工况复杂,因此加热炉设计弹性较大。
由于减压炉汽化量较大,为了减小压力降避免炉管内超临界速度出现,减压炉出口炉管进行适当扩径。
润滑精制装置简介和重点部位及设备

润滑精制装置简介和重点部位及设备1. 润滑精制装置概述润滑精制装置是一种利用化学物质和机械设备进行加工处理的工业设备,用于生产各种润滑油和脂肪。
润滑精制装置通过不断地加工和洗涤、分离、脱色、去异味等工艺流程,将原始的粗糙油脂制成符合各种要求的润滑油和脂肪。
润滑精制装置广泛应用于汽车、冶金、航空、化工、食品、医药等诸多领域。
2. 润滑精制装置重点部位2.1 脱酸器脱酸器是润滑精制装置中的一个主要部件,用于去除油脂中的游离酸,防止酸腐蚀或损坏设备。
脱酸器的结构和工作原理简单,其主要组成部分有加热装置、旋转桶、底座、进出料口等。
2.2 分离器分离器是润滑精制装置中的另一个重要部件,用于将掺杂在油脂中的杂质进行分离。
一般分离器根据工作原理不同可划分为离心式、沉淀式、过滤式、吸附式等。
离心式分离器利用离心力将杂质分离出来,沉淀式分离器则是利用沉淀原理,将杂质沉淀至底部分离等等。
2.3 脱色器脱色器是润滑精制装置中的关键部位之一,主要用来去除油脂中的色素和其他有机物。
脱色器主要具有两种结构形式:一种是采用物理吸附型的脱色剂,另一种则是采用化学还原法。
具体的脱色工艺则是要看不同的脱色剂而有所不同,但总体上都是采用反复冲洗的方式进行脱色的。
3. 润滑精制装置设备3.1 加热设备加热装置是润滑精制装置中的一项非常重要的设备,用于将原料油或是脂肪升温至加工需要的温度。
加热设备应选用低温升温方式,以免油被加热过度从而破坏其结构性能。
加热设备的形式有很多种,可以选用电加热管、蒸汽加热、导热油加热等方式。
3.2 搅拌设备搅拌设备用于将油料搅拌均匀并促进化学反应。
搅拌器的形式有螺旋式、叶片式、锚式等,在不同的工艺流程中应该选择不同的搅拌方式。
3.3 反应釜反应釜用于进行润滑油脱酸、脱色、脱臭、精制等工艺过程中的反应加工。
反应釜应该具有三个基本线性,即压力容器、加热器和搅拌器,在实际的应用中可以改变反应釜的容积、形状等维度,以适应不同流程的反应需求。
润滑油净化装置介绍

润滑油净化装置介绍1. 设备安装位置油净化装置布置在汽机房零米层。
2. 使用条件润滑油系统运行时,待处理油介质特性:润滑油牌号:L-TSA32号透平油油质标准:GB11120-89运动粘度〔40℃〕:28.8~35.2 mm2/s闪点:≥180℃酸值:> 0.2 mgKOH/g机械杂质:9级〔NAS〕水分:0.2 %破乳化时间:超过60分钟防锈性能:轻锈润滑油处理装置的运行方式:每台机组配置1台汽轮机主机润滑油处理装置,2台给水泵汽轮机润滑油处理装置,可连续运行,油质合格后处于备用状态。
运行油温: 20-70℃,工作压力: <0.5MPa。
3. 技术条件3.1 参数、容量/能力、用途及型式本期工程共配置2台汽轮机润滑油处理装置,4台给水泵汽轮机润滑油处理装置,可连续运行,油质合格后处于备用状态。
汽轮机油箱最大容量约3,油净化装置容量为:>3/h;给水泵汽轮机润滑油箱总容量约3,有效容积3.8 m3,油净化装置容量为:>1.22 m3/h;处理后润滑油质的要求:润滑油系统的滤油精度:≤ 5 μm油质水分: 含水量低于 0.01 %油质外状: 透明运动粘度〔40℃〕: 28.8~35.2 mm2/s闪点: ≥180℃机械杂质: 符合NAS 6级酸值: ≤油净化装置运行方式: 连续或连续、正压或负压均可运行油净化除渣方式: 手动用途:将润滑油系统的润滑油进展循环处理,从而起到对润滑油除水、除杂质、除酸和破除乳化的目的,以保证汽轮机的正常运行。
型式:聚结别离3.2 性能要求润滑油处理装置为集装式组合净化装置,能够滤除润滑油中的水份、颗粒杂质等污染物,破除乳化相,保证润滑油再生,并能适合机组各种运行工况下对润滑油质产生的影响,自动连续运行。
该装置设有进、出油口管接头以及有关油位、油压、差压检测仪表和保护装置等。
润滑油处理装置能够可靠地别离水份、颗粒杂质等污染物,破除乳化相,卖方在协议文件中详细说明产品别离水分的原理及脱水系统设备的参数、构造特点。
小机润滑油系统介绍要点
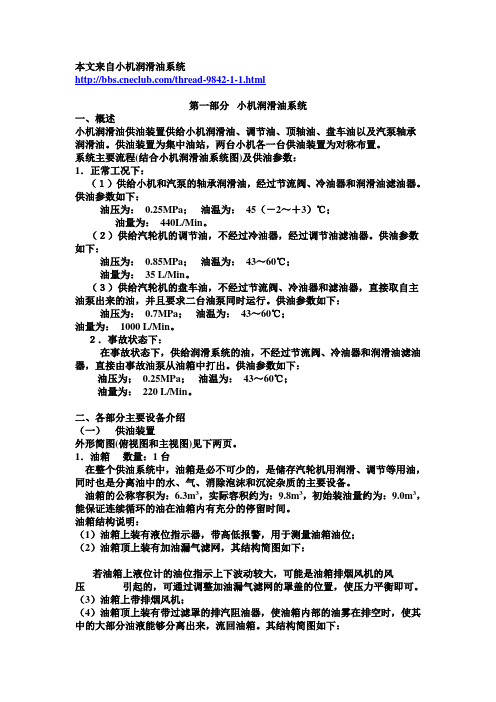
本文来自小机润滑油系统/thread-9842-1-1.html第一部分小机润滑油系统一、概述小机润滑油供油装置供给小机润滑油、调节油、顶轴油、盘车油以及汽泵轴承润滑油。
供油装置为集中油站,两台小机各一台供油装置为对称布置。
系统主要流程(结合小机润滑油系统图)及供油参数:1.正常工况下:(1)供给小机和汽泵的轴承润滑油,经过节流阀、冷油器和润滑油滤油器。
供油参数如下:油压为:0.25MPa;油温为:45(-2~+3)℃;油量为:440L/Min。
(2)供给汽轮机的调节油,不经过冷油器,经过调节油滤油器。
供油参数如下:油压为:0.85MPa;油温为:43~60℃;油量为:35 L/Min。
(3)供给汽轮机的盘车油,不经过节流阀、冷油器和滤油器,直接取自主油泵出来的油,并且要求二台油泵同时运行。
供油参数如下:油压为:0.7MPa;油温为:43~60℃;油量为:1000 L/Min。
2.事故状态下:在事故状态下,供给润滑系统的油,不经过节流阀、冷油器和润滑油滤油器,直接由事故油泵从油箱中打出。
供油参数如下:油压为;0.25MPa;油温为:43~60℃;油量为:220 L/Min。
二、各部分主要设备介绍(一)供油装置外形简图(俯视图和主视图)见下两页。
1.油箱数量:1台在整个供油系统中,油箱是必不可少的,是储存汽轮机用润滑、调节等用油,同时也是分离油中的水、气、消除泡沫和沉淀杂质的主要设备。
油箱的公称容积为:6.3m3,实际容积约为:9.8m3,初始装油量约为:9.0m3,能保证连续循环的油在油箱内有充分的停留时间。
油箱结构说明:(1)油箱上装有液位指示器,带高低报警,用于测量油箱油位;(2)油箱顶上装有加油漏气滤网,其结构简图如下:若油箱上液位计的油位指示上下波动较大,可能是油箱排烟风机的风压引起的,可通过调整加油漏气滤网的罩盖的位置,使压力平衡即可。
(3)油箱上带排烟风机;(4)油箱顶上装有带过滤罩的排汽阻油器,使油箱内部的油雾在排空时,使其中的大部分油液能够分离出来,流回油箱。
常用油润滑装置

常用油润滑装置一、手工给油装置:手工给油润滑是由操作工人用油壶或油枪向润滑点的油孔、油嘴及油杯加油,主要用于低速、轻载和间歇工作的滑动面、开式齿轮、链条以及其他单个摩擦副。
加油量依靠工人感觉与经验加以控制。
(1)油孔、油嘴及油杯:一般在位置受到限制时只能采用带喇叭口的油孔,油孔内可填充毛毡或毛绳,使之起储油和过滤的作用。
(2)油壶和油枪:油壶和油枪是常用的供油装置,种类繁多,选择时主要看它的出油处能否与用油孔、油嘴、油杯相适应,使用方便可靠即可。
二、滴油润滑:滴油润滑主要使用油杯向润滑点供油润滑。
通常的油杯有:针阀式注油杯、压力作用滴油油杯、跳针式油杯、连续压注油杯、活塞式滴油油杯等。
油杯多用铝和铝合金等轻金属制成骨架,杯壁和检查孔多用透明的塑料或玻璃制造,以便观察其内部油位。
(1)针阀式油杯:这种注油杯的滴油量受针阀的控制,油杯中油位的高低可直接影响通过针阀环间隙的滴油量。
(2)压力作用滴油油杯:这种油杯的底面有一个针阀,其阀杆通过油杯上的操作缸伸出外部,连接调节螺母。
这是装在透平式压缩机上的滴油杯,阀的起闭由压缩机的排气通过弹簧压着的活塞加以控制,并可用阀杆上的螺母来调节油杯的滴油量。
(3)跳针式润滑油杯:这种油杯还能由摩擦副的温度变化来控制。
摩擦副中的温度变化通过油杯的金属管传到油杯的上腔使其中的空气膨胀或收缩。
当空气膨胀时,油杯上面空腔内的气压增大,强迫少量润滑油流出油杯送入摩擦副;而在空气收缩时,油流停止,如是连续不断地动作。
这种油杯在某些要求先加油然后起动的摩擦副上不能应用。
(4)连续压注油杯:这种连续压注油杯由于其下面储油器能保持着不变的油压,所以能保证自动均匀的给油。
(5)均匀滴油油杯:润滑油从上面储油器经过连在浮标上的阀,补充到下面的储油器,其送往摩擦副的油量靠针阀来调节。
(6)活塞式滴油油杯:它的滴油量可通过杯上的杠杆机构来调节。
三、油绳和油垫润滑:主要使用油绳、毡垫等浸在润滑油中,应用虹吸管和毛细管作用吸油。
- 1、下载文档前请自行甄别文档内容的完整性,平台不提供额外的编辑、内容补充、找答案等附加服务。
- 2、"仅部分预览"的文档,不可在线预览部分如存在完整性等问题,可反馈申请退款(可完整预览的文档不适用该条件!)。
- 3、如文档侵犯您的权益,请联系客服反馈,我们会尽快为您处理(人工客服工作时间:9:00-18:30)。
In Order To Simplify The Management Process And Improve The Management Efficiency, It Is Necessary To Make Effective Use Of Production Resources And Carry Out Production Activities.编订:XXXXXXXX20XX年XX月XX日润滑油生产装置简介和重点部位及设备简易版润滑油生产装置简介和重点部位及设备简易版温馨提示:本安全管理文件应用在平时合理组织的生产过程中,有效利用生产资源,经济合理地进行生产活动,以达到实现简化管理过程,提高管理效率,实现预期的生产目标。
文档下载完成后可以直接编辑,请根据自己的需求进行套用。
(一)装置发展我国润滑油生产在20世纪50年代中期即开始采用溶剂脱蜡工艺。
60年代溶剂脱蜡单装置规模达到300—400kt/a。
70年代由单一脱蜡工艺发展为脱蜡脱油联合工艺,在一套装置上,同时生产脱油蜡和石蜡。
在脱蜡溶剂上,由丙酮—苯—甲苯混合溶剂逐渐全部改为甲乙酮—甲苯混合溶剂。
并陆续采用了结晶过程多点稀释、滤液循环以及溶剂多效蒸发回收等工艺技术。
进入20世纪90年代,全球润滑油生产能力不断扩大,而需求量趋于稳定,其消耗量一直维持在3600~3900X10的4次方(原多次方位置应该标在右上位置,但word格式不支持)t之间,这就促使润滑油产品不断更新换代和基础油质量的不断提高。
在润滑油脱蜡生产工艺上,随着加氢异构化技术的发展与运用,异构化脱蜡生产工艺在大庆炼化公司、兰州炼油厂等石化厂逐步得到运用,用以生产Ⅱ、Ⅲ类润滑油基础油。
目前我国主要的润滑油生产工艺还是“老三套”。
(二)单元组成与工艺流程1.组成单元溶剂脱蜡由四个系统组成;结晶系统、制冷系统、过滤系统(包括真空密闭系统)、溶剂回收(包括溶剂干燥)系统。
其相互关系如图2—22所示。
2.工艺流程典型原则工艺流程见图2—23、图2—24。
工艺流程说明如下:(1)结晶系统结晶系统的流程为:原料油与预稀释溶剂(重质原料时用,轻质原料时不用)混合后,经水冷却后进人换冷套管与冷滤液换冷,使混合溶液冷却到冷点,在此点加入经预冷过的一次稀释溶剂,进入氨冷套管进行氨冷。
在一次氨冷套管出口处加人过滤机高部真空滤液或二段过滤的滤液做二次稀释,再经过二次氨冷套管进行氨冷,使温度达到工艺指标。
在二次氨冷套管出口处再加人经过氨冷却的三次稀释溶剂,进人过滤机进料罐。
图2—23溶剂脱蜡的典型工艺流程(结晶、过滤、真空密闭、制冷部分) I一原料油;Ⅱ一滤流;Ⅲ一蜡液;Ⅳ一溶剂1一换冷套管结晶器;2、3一氨冷套管结晶器;4--溶剂氨冷套管结晶器;5一一段真空过滤机;6——二汇段真空过滤机;7一滤机进料罐;8——段蜡液罐;9——二段蜡液罐;10——段滤液罐;11——二段滤液罐;12——低压氨分离罐;13——氨压缩机;14——中间冷却器;15——高压氨分液罐;16——氨冷凝冷却器;17——液氨储罐;18--低压氨储罐;19——真空罐;20——分液罐;2l——安全气罐图2—24溶剂脱蜡的典型工艺流程(溶剂回收、溶剂干燥部分)I一滤液;Ⅱ一蜡液;Ⅲ—溶剂;Ⅳ一脱蜡油;V一含油蜡1一滤液低压蒸发塔;2--滤液高压蒸发塔;3一滤液低压蒸发塔;4--脱蜡油汽提塔;5—蜡液低压蒸发塔;6——蜡液高压蒸发塔;7--蜡液低压蒸发塔;8--含油蜡汽提塔;9---溶剂干燥塔;10--酮脱水塔;11一滤液加热炉;12—蜡液加热炉;13一溶剂罐;14--湿溶剂分水罐(2)过滤和真空密闭系统过滤系统是使固、液两相分离。
由若干台并联旋转式鼓形真空过滤机组成,连续运转操作。
冷却后含结晶蜡溶液自动流入过滤机底槽内,过滤机转鼓内抽真空,在滤布内外形成压”差,油和溶剂通过滤布进入中间储罐,即为滤液。
滤布上的蜡饼经过喷淋溶剂洗涤和吸干后,用反吹气和刮刀从滤布上刮落,进入蜡液罐。
滤液与原料油换冷,换冷后的滤液和蜡液分别去溶剂回收系统。
(3)制冷系统制冷系统是独立的,它提供原料油、溶剂、安全气冷却时的冷量,达到脱蜡所要求的温度,使去蜡油的凝点达到质量指标。
以氨为冷冻剂,采用往复式、螺杆式或离心式冷冻机。
一般采用高、低两段蒸发操作,根据工艺需要确定氨的蒸发温度。
(4)溶剂回收与干燥系统滤液和蜡液中的溶剂通过蒸发回收,循环使用。
滤液和蜡液溶剂回收系统均采用双效或三效蒸发。
在双效蒸发中,第一蒸发塔为低压操作,热量由与第二蒸发塔顶溶剂蒸气换热提供:第二蒸发塔为高压操作,热量由加热炉提供:第三蒸发塔为降压闪蒸塔,最后在汽提塔内用蒸汽吹出残留的溶剂,得到含溶剂量和闪点合格的去蜡油和含油蜡。
三效蒸发的流程与双效蒸发基本相同,只是在低压蒸发塔与高压蒸发塔之间,增加了一个中压蒸发塔,使热量得到充分利用。
各蒸发塔顶回收的溶剂经换热、冷凝、冷却后进人干、湿溶剂罐。
汽提塔顶含溶剂蒸汽经冷凝、冷却后进人湿溶剂分水罐。
溶剂干燥系统是从含水湿溶剂中脱除水分,使溶剂干燥,以及从含溶剂水中回收溶剂,脱除装置系统的水。
湿溶剂罐内分为两层,上层为含饱和水的溶剂,下层为含少量溶剂的水层。
含水溶剂经换热后,送入干燥塔,塔底用重沸器加热,酮与水形成低沸点共沸物,由塔顶蒸出,干燥溶剂从塔底排出,冷却后进人干溶剂罐。
湿溶剂罐下层含溶剂的水经换热后,进入脱酮塔,用蒸汽直接吹脱溶剂,塔顶的含溶剂蒸汽经过冷凝冷却后,回到湿溶剂分水罐。
水由塔底排出,含酮量控制在0.01%以下。
(三)主要操作条件及工艺技术特点1.主要操作条件对于不同的润滑油溶剂脱蜡装置,其工艺操作条件有所不同,燕山石化酮苯装置主要操作条件如下:(1) 结晶单元(2) 过滤单元(3)制冷系统制冷系统在各润滑油溶剂脱蜡装置中差别比较大,从安全生产角度考虑,以燕山石化酮苯脱蜡装置为例,制冷系统主要工艺控制指标如表2—69所示。
(4) 溶剂回收及干燥系统2.工艺技术特点(1)采用多点稀释并控制冷点温度结晶系统稀释溶剂分3—4次加入。
第一次稀释溶剂的加入点,从原来的原料油泵出口移至原料油冷却到比其凝点低15-20℃的温度处。
其余各次溶剂亦根据不同原料油控制加入点温度,为蜡结晶生成及成长提供适宜条件。
采用多点稀释和控制冷点温度,除可以改善蜡的结晶状态提高过滤速度外,还可以提高油蜡收率。
(2)采用二段过滤和滤液循环工艺我国生产润滑油的原油多数是含蜡多的原油。
润滑油脱蜡时,蜡膏量一般为原料油的45%—52%。
为了降低蜡膏中的油含量以提高脱蜡油收率,一般采两段过滤及滤液循环工艺。
其工艺流程是将第一段过滤得的含油蜡膏加入一定数量的溶剂再稀释,在比第一段温度稍高3-5℃或相同温度下,进行第二段过滤。
第二段滤液与第一、二段过滤高部真空抽出的滤液共同作为结晶系统的二次及三次稀释溶剂。
采用二段过滤和滤液循环工艺较一段过滤提高脱蜡油收率8%—10%,同时还降低装置能耗。
(3)采用脱蜡—脱油联合及过滤三段逆流循环工艺我国润滑油原料中含量很高的蜡是生产石蜡的宝贵资源。
因此,在溶剂脱蜡装置上,除了采用二段过滤和滤液循环工艺外,目前多数溶剂脱蜡装置还增加了溶剂脱油部分,构成溶剂脱油—脱蜡联合工艺流程。
在原料油脱蜡的同时进行蜡膏脱油,同时得到脱蜡油和脱油石蜡。
脱蜡—脱油联合工艺流程采用部分滤液循环工艺,包括一段脱蜡两段脱油。
滤液三段逆流循环是将二段脱油滤液全部作为一段脱油稀释溶剂,将一段脱油的滤液大部分作为脱蜡稀释溶剂,而小部分去蜡下油溶剂回收系统。
(四)混合溶剂及氨1.混合溶剂及氨的作用润滑油溶剂脱蜡的混合溶剂是丁酮、甲苯按一定比例混合组成。
溶剂脱蜡是含蜡原料油在选择性溶剂存在条件下,降低温度使蜡形成固体结晶,并通过溶剂对油溶解而对蜡不溶或少溶的特性,形成固液两相,经过滤而达到蜡、油分离的过程。
混合溶剂在系统中,除起选择溶解作用外,还起降低油液黏度、为结晶的形成和过滤分离创造有利条件作用。
氨在润滑油溶剂脱蜡装置中作为制冷剂,利用液氨在低温下即可在氨蒸发器内蒸发(汽化),蒸发中吸收大量热量的性质来冷却原料、溶剂、安全气,实现制冷。
气、液态氨的转换是通过氨压缩机增压及与外界环境换热、减压节流实现的。
2.混合溶剂及氨的主要物化性质、安全性质混合溶剂及氨的物化性、安全性质见表2—71。
(五)原料及产品性质1.原料性质原料性质如表2—72所示。
2.产品性质(1)脱蜡油脱蜡油性质如表2—73所示(2)脱油蜡脱油蜡性质如表2—74所示二、重点部位及设备(一)重点部位1.溶剂回收系统溶剂回收系统的二次蒸发塔属于高压塔,其安全阀定压在0.5—0.55Mpa,由于实际生产操作中存在满塔、前塔换热器换热效果差等原因,造成高压塔安全阀跳,致使塔内大量溶剂喷出,极易造成火灾、爆炸等事故的发生。
2.制冷系统冷冻系统的分离器、中膨器的液位因液氨夹带等原因,容易致使冷冻机抽液氨,使冷冻机剧烈震动,损坏冷冻机叶片和轴瓦。
循环化套管、用蒸汽处理套管等,若处理不当,造成套管憋压,而崩裂套管前后大盖。
(二)重点设备1.套管结晶器套管结晶器在工艺过程中分为换冷和氨冷两种。
前者为夹套内以冷滤液作冷却剂取热,后者为夹套内以氨液作冷却剂取热,其结构形式基本相同。
氨冷套管结晶器的上面设液氨罐,用罐内液面调节器控制液体氨流人结晶器夹套内的氨量,罐内的压力和相应的液氨蒸发温度用氨气排出口的控制阀门调节。
套管结晶器内蒸发后的氨气进入液氨罐的上部空间,分离夹带的液体氨后,经控制阀去氨压缩机。
2.真空过滤机真空过滤机为一连续工作设备,通过压缩机以惰性气为介质提供动力,包括四个基本组成部分:①下部壳体,为冷却了的原料溶液容器;②顶盖,用法兰与下部壳体相连接,连接处要保证绝对密封;③滤鼓,位于壳体内部;④自动分配装置。
该位置可填写公司名或者个人品牌名Company name or personal brand name can be filled in this position。