催化裂化3
催化裂化工艺介绍

1。
0催化裂化催化裂化是原料油在酸性催化剂存在下,在500℃左右、1×105~3×105Pa 下发生裂解,生成轻质油、气体和焦炭的过程.催化裂化是现代化炼油厂用来改质重质瓦斯油和渣油的核心技术,是炼厂获取经济效益的重要手段。
催化裂化的石油炼制工艺目的:1)提高原油加工深度,得到更多数量的轻质油产品;2)增加品种,提高产品质量。
催化裂化是炼油工业中最重要的一种二次加工工艺,是重油轻质化和改质的重要手段之一,已成为当今石油炼制的核心工艺之一。
1。
1催化裂化的发展概况催化裂化的发展经历了四个阶段:固定床、移动床、流化床和提升管。
见下图:固定床移动床流化床提升管(并列式)在全世界催化裂化装置的总加工能力中,提升管催化裂化已占绝大多数。
1。
2催化裂化的原料和产品1。
2。
0原料催化裂化的原料范围广泛,可分为馏分油和渣油两大类。
馏分油主要是直馏减压馏分油(VGO),馏程350—500℃,也包括少量的二次加工重馏分油如焦化蜡油等,以此种原料进行催化裂化称为馏分油催化裂化。
渣油主要是减压渣油、脱沥青的减压渣油、加氢处理重油等。
渣油都是以一定的比例掺入到减压馏分油中进行加工,其掺入的比例主要受制于原料的金属含量和残炭值.对于一些金属含量低的石蜡基原有也可以直接用常压重油为原料。
当减压馏分油中掺入渣油使通称为RFCC。
以此种原料进行催化裂化称为重油催化裂化。
1。
2.1产品催化裂化的产品包括气体、液体和焦炭。
1、气体在一般工业条件下,气体产率约为10%-20%,其中含干气和液化气。
2、液体产物1)汽油,汽油产率约为30%-60%;这类汽油安定性较好。
2)柴油,柴油产率约为0—40%;因含较多芳烃,所有十六烷值较低,由重油催化裂化得到的柴油的十六烷值更低,这类柴油需经加氢处理。
3)重柴油(回炼油),可以返回到反应器内,已提高轻质油收率,不回炼时就以重柴油产品出装置,也可作为商品燃料油的调和组分。
4)油浆,油浆产率约为5%—10%,从催化裂化分馏塔底得到的渣油,含少量催化剂细粉,可以送回反应器回炼以回收催化剂。
催化裂化原理
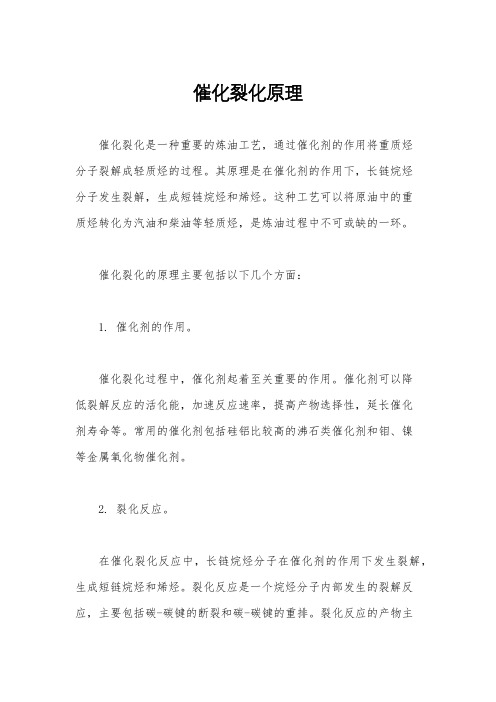
催化裂化原理催化裂化是一种重要的炼油工艺,通过催化剂的作用将重质烃分子裂解成轻质烃的过程。
其原理是在催化剂的作用下,长链烷烃分子发生裂解,生成短链烷烃和烯烃。
这种工艺可以将原油中的重质烃转化为汽油和柴油等轻质烃,是炼油过程中不可或缺的一环。
催化裂化的原理主要包括以下几个方面:1. 催化剂的作用。
催化裂化过程中,催化剂起着至关重要的作用。
催化剂可以降低裂解反应的活化能,加速反应速率,提高产物选择性,延长催化剂寿命等。
常用的催化剂包括硅铝比较高的沸石类催化剂和钼、镍等金属氧化物催化剂。
2. 裂化反应。
在催化裂化反应中,长链烷烃分子在催化剂的作用下发生裂解,生成短链烷烃和烯烃。
裂化反应是一个烷烃分子内部发生的裂解反应,主要包括碳-碳键的断裂和碳-碳键的重排。
裂化反应的产物主要是烷烃、烯烃和芳烃。
3. 反应条件。
催化裂化的反应条件包括温度、压力、催化剂种类和用量等。
通常情况下,催化裂化反应需要在较高的温度下进行,以提高反应速率和产物选择性。
此外,适当的压力和催化剂的选择也对裂化反应的效果有重要影响。
4. 产物分离。
催化裂化反应产生的混合气体需要进行分离和纯化,以得到所需的轻质烃产品。
通常采用的分离技术包括精馏、萃取、吸附等,以获得高纯度的汽油和柴油产品。
5. 催化剂再生。
在催化裂化过程中,催化剂会因受到焦炭和烃类物质的污染而失活,需要进行再生。
催化剂再生是通过热氧化或化学氧化等方法将焦炭烧除,恢复催化剂的活性和选择性,延长催化剂的使用寿命。
总的来说,催化裂化是一种重要的炼油工艺,通过催化剂的作用将重质烃分子裂解成轻质烃,可以提高原油的利用率,生产出更多的汽油和柴油产品。
催化裂化的原理涉及催化剂的作用、裂化反应、反应条件、产物分离和催化剂再生等多个方面,需要综合考虑和控制,以实现高效、稳定的生产过程。
催化裂化第三级旋风分离器

是20世纪70年代设计、引进和建设投产的,以后由于多管式三旋
的引进并被我国当时确定为发展方向,因此没有再建造和引进布
埃尔式三旋和旋流式三旋。我国从20世纪70年代后期开始研究催
化裂化能量回收系统多管式第三级旋风分离器(以下简称“三
旋”)。从最初的引进吸收、消化国外技术为主,到后来的自主开
Hale Waihona Puke 发研制,从80年代的EPVC旋风管到现在的PDC、PSC、PST、VAS、
谢谢!
目前我国多管式三旋运转中出现的主要问题
(1)各种类型单管在冷态试验时单根管的分离效率普遍很高(95%以上),但是实际 工业应用中单管不是单独使用,而是并联使用,并联后的整体效率高才是我 们追求的目标。在实际应用中单管组合后的整体效率并不理想。理论分析、 冷态试验和工业应用都证明:造成单管效率与组合效率相差较大的原因就在 于目前的单管抗返混能力差,组合后由于各单管压降不均匀或不一致,造成 部分单管不工作、失效、甚至返混,从而导致组合效率严重下降。造成各单 管压降不均匀或不一致的主要原因是由单管的加工、制造和安装精度产生的。 另一原因是由于安装单管的隔板太大,需现场拼焊,大隔板成型和加工精度 都较差,单管与隔板焊接变形,组装后单管的同轴度和其他精度很难达到要 求。而装置开工后,在高达700℃以上的操作温度下工作,装置运行一段时间 后,隔板的适量变形是无法避免的,而单管的强度和刚度根本无法抵抗由于 上述原因引起的自身变形。隔板的比较小的变形,将使单管产生很大的变形。 另外从操作方面讲,泄气量小,集尘室粉尘太多,排尘不畅,造成集尘室与 进气室压差太小,一部分单管在泄气率正常状态下工作,另一部分单管则在 偏小泄气率甚至不泄气或返混状态下工作。在长期连续工作中,压降小的单 管流量大、流速快、磨损严重,压降会变得更小。压降大的单管流量小、流 速慢、磨损小,或基本不磨损,单管压降基本不变,这就使各单管压降不均 匀性日趋严重,所以返混也越来越严重。
催化裂化计算公式
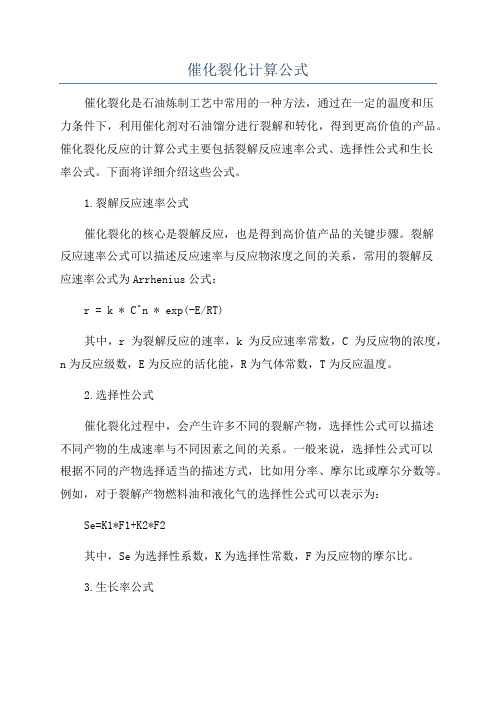
催化裂化计算公式催化裂化是石油炼制工艺中常用的一种方法,通过在一定的温度和压力条件下,利用催化剂对石油馏分进行裂解和转化,得到更高价值的产品。
催化裂化反应的计算公式主要包括裂解反应速率公式、选择性公式和生长率公式。
下面将详细介绍这些公式。
1.裂解反应速率公式催化裂化的核心是裂解反应,也是得到高价值产品的关键步骤。
裂解反应速率公式可以描述反应速率与反应物浓度之间的关系,常用的裂解反应速率公式为Arrhenius公式:r = k * C^n * exp(-E/RT)其中,r为裂解反应的速率,k为反应速率常数,C为反应物的浓度,n为反应级数,E为反应的活化能,R为气体常数,T为反应温度。
2.选择性公式催化裂化过程中,会产生许多不同的裂解产物,选择性公式可以描述不同产物的生成速率与不同因素之间的关系。
一般来说,选择性公式可以根据不同的产物选择适当的描述方式,比如用分率、摩尔比或摩尔分数等。
例如,对于裂解产物燃料油和液化气的选择性公式可以表示为:Se=K1*F1+K2*F2其中,Se为选择性系数,K为选择性常数,F为反应物的摩尔比。
3.生长率公式催化裂化反应中,一些分子会通过生长过程生成更大的分子,这些生长过程可以通过生长率公式描述。
一般来说,生长率公式可以基于碳原子的增长数量表示。
G=A*C^m其中,G为生长率,A为生长常数,C为反应物的浓度,m为生长度。
需要注意的是,上述公式只是催化裂化反应计算中的常用公式,实际应用中还需要结合具体的反应机理和实验数据进行修正和拟合。
此外,催化裂化反应过程中还涉及到反应器设计、催化剂选择、操作参数优化等多方面的问题,需要综合考虑才能得到准确的计算结果。
催化裂化机理及特点

催化裂化机理及特点催化裂化是一种通过加热和催化剂的作用将长链烃分子裂解为短链烃分子的重要工艺。
催化裂化机理及特点主要包括以下几个方面:一、催化裂化机理1.构造反应:长链烃分子在裂化过程中首先发生构造反应,通过裂解碳-碳键,形成相对较短的碳链碳烃和烯烃。
2.重排反应:长链烃分子中的骨架碳骨架会经历一系列重排反应,使得产物中更多的是相对稳定的异构体和环状化合物。
3.脱氢反应:重排反应过程中,长链分子中的烃基可能失去氢原子,从而形成烯烃,增加了催化裂化的产物中烯烃的含量。
4.脱氢裂解反应:在高温高压下,部分碳链碳烃可以发生脱氢裂解反应,形成更短的链长烃烃烃烃、烯烃和芳香烃。
二、催化裂化特点1.催化裂化具有高选择性:在催化剂的影响下,催化裂化反应主要发生在长链烃分子中的弱键和缺陷位置,使得产物中的碳链长度相对较短,同时产生更多的异构体和环状化合物。
2.催化裂化反应速度快:催化剂的存在提高了反应活性,使得裂化反应可以在相对低的温度和压力下进行,加快了反应速度。
3.催化裂化可以产生高附加值的产品:催化裂化使得重质燃料油转化为轻质烃类产品,其中包括汽油、炼厂气、润滑油基础油等,这些产品有较高的附加值。
4.催化裂化可以降低能源消耗:通过催化裂化将重质原油转化为较轻质产品,如汽油和炼厂气,不仅提供了更多的高附加值产品,还减少了对原油的需求,降低了能源消耗。
5.催化裂化可以调节产品分布:通过不同的催化剂组合和反应条件,可以调节催化裂化产物的碳链长度分布,以满足市场需求,提高产品经济效益。
总之,催化裂化是一种高效、高选择性的炼油工艺,通过加热和催化剂的作用,将长链烃分子裂解为短链烃分子,产生高附加值产品,并降低能源消耗。
催化裂化机理和特点的深入研究对于提高炼油工艺的效率和降低能源消耗具有重要意义。
催化裂化的工艺特点及基本原理

催化裂化的工艺特点及基本原理催化裂化是一种重要的石油加工工艺,其开发和应用对于提高石油产业发展水平具有重要的意义。
催化裂化工艺的特点和基本原理如下:一、工艺特点:1.高选择性:催化裂化工艺可以将石油馏分中的大分子烃化合物按照其碳数分解为较低碳数的烃化合物,其中可选择的烃化合物主要是汽油和液化气。
因此,催化裂化可以提高汽油和液化气产率,达到更好的操作经济效益。
2.产物分布广:催化裂化反应不仅可以生成汽油和液化气,还可以生成较低碳数的烃化合物,如乙烯、丙烯等。
因此,催化裂化反应可以提供多种不同碳数的烃化合物,满足不同需求。
3.增塔体积积极:催化裂化工艺采用固定床反应器,反应器内填充了催化剂颗粒,因此反应器体积较大。
大体积的反应器可以增加催化裂化反应的容量,提高石油裂解速率,并且还可以增加反应过程的稳定性和可控性。
4.废气利用:催化裂化反应产生的废气中含有非常丰富的烃化合物和能量,可以通过适当的处理和回收利用,从而得到更好的经济效益,并减少对环境的污染。
二、基本原理:催化裂化反应是通过催化剂的作用来进行的,其基本原理如下:1.裂解反应:石油中的长链烃化合物在催化剂的作用下发生热裂解反应,将大分子烷烃分解成较小分子的烃化合物。
这种反应是一个链状反应过程,会生成一系列的短链烃化合物和碳氢烃中间体。
2.重排反应:短链烃化合物和碳氢烃中间体在催化剂的作用下发生重排反应,重新组合成不同碳数的烃化合物。
3.芳构化反应:在催化裂化过程中,由于催化剂特殊的性质,烃化合物还会发生芳构化反应,生成芳烃类化合物,如苯、甲苯等。
4.积碳反应:由于裂化过程产生的碳元素会在催化剂表面析出,形成碳黑,导致催化剂失活。
因此,催化裂化还需要定期对催化剂进行再生,以保持其活性。
综上所述,催化裂化工艺具有高选择性、广泛的产物分布、增塔体积积极和废气利用等特点。
其基本原理包括裂解反应、重排反应、芳构化反应和积碳反应。
催化裂化工艺的开发和应用有助于提高石油产业的经济效益和环境可持续性。
3号催化裂化装置的提升管喷汽油试验

类似 终止 剂 的作 用 , 品分 布 以汽 油 和液 化 气 为 产
芳构 化 反应 加强 。
此工艺的焦 碳和干 气收 率有 上升 , 作 成本有 操
( 20 年 1 1 按 01 月 9日检 尺数据 )根据等 比例跑损的 ,
计算 ,ⅡC 0  ̄ _50约 占总藏量 7 %。 0
由于装 置 正 处 于 开 工 状态 , 不影 响 正 常 生 为
所上升 , 置能耗 有负 面影 响 ; 从 产品 收率看 , 对装 但 使用提升管喷汽油后 , 柴油和液 态烃 收率上升 , 经济 效益方面估计 是有利 的。该技 术对提高装 置的柴汽 比亦有帮助 。 目前 由于装置设 备 上 的问题 , 料油 原
20 0 1年 1月 以来 , 态烃 丙 烯 含 量 和烷 烯 比都 有 液
柴油 的需求 日益增 长 , 油厂 在 3号 催化 裂化装 置 炼
上进行多产液化气 和柴油 的试验。其核心是部分 粗 汽油返 回提 升管 , 通过在 提 升管 的不 同部 位进 料 并 来控制不同 的反应 苛 刻度 , 以达到改 善产 品分布 和
主, 柴油 有减 少 。而 从 预 提 升 段 进 汽 油 就 对 柴 油
收率 的上 升起 作用 , 别是 在 汽油 量大 的情 况下 。 特
而 由于装 置 F 1 3量程 仅 为 2 th 所 以不 再进 C10 0/ , 行更 大 流量 汽 油 的试 验 。从 液 态 烃 成 绩 看 ,0 0 20 年 1 2月 由于 ML - 5 0在 系 统 藏 量 中 的 比例 上 C 0 升 , 态 烃 的 丙 烯 含 量 和 烷 烯 比 都 在 下 降 。 而 液
催化裂化的基本工艺流程
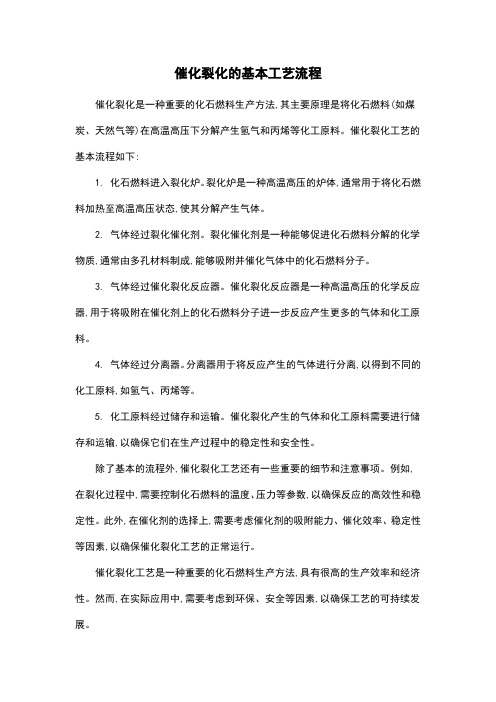
催化裂化的基本工艺流程
催化裂化是一种重要的化石燃料生产方法,其主要原理是将化石燃料(如煤炭、天然气等)在高温高压下分解产生氢气和丙烯等化工原料。
催化裂化工艺的基本流程如下:
1. 化石燃料进入裂化炉。
裂化炉是一种高温高压的炉体,通常用于将化石燃料加热至高温高压状态,使其分解产生气体。
2. 气体经过裂化催化剂。
裂化催化剂是一种能够促进化石燃料分解的化学物质,通常由多孔材料制成,能够吸附并催化气体中的化石燃料分子。
3. 气体经过催化裂化反应器。
催化裂化反应器是一种高温高压的化学反应器,用于将吸附在催化剂上的化石燃料分子进一步反应产生更多的气体和化工原料。
4. 气体经过分离器。
分离器用于将反应产生的气体进行分离,以得到不同的化工原料,如氢气、丙烯等。
5. 化工原料经过储存和运输。
催化裂化产生的气体和化工原料需要进行储存和运输,以确保它们在生产过程中的稳定性和安全性。
除了基本的流程外,催化裂化工艺还有一些重要的细节和注意事项。
例如,在裂化过程中,需要控制化石燃料的温度、压力等参数,以确保反应的高效性和稳定性。
此外,在催化剂的选择上,需要考虑催化剂的吸附能力、催化效率、稳定性等因素,以确保催化裂化工艺的正常运行。
催化裂化工艺是一种重要的化石燃料生产方法,具有很高的生产效率和经济性。
然而,在实际应用中,需要考虑到环保、安全等因素,以确保工艺的可持续发展。
- 1、下载文档前请自行甄别文档内容的完整性,平台不提供额外的编辑、内容补充、找答案等附加服务。
- 2、"仅部分预览"的文档,不可在线预览部分如存在完整性等问题,可反馈申请退款(可完整预览的文档不适用该条件!)。
- 3、如文档侵犯您的权益,请联系客服反馈,我们会尽快为您处理(人工客服工作时间:9:00-18:30)。
0.098)(带经验式4314,0.0996)
17
9.4催化裂化催化剂失活与再生
已知烟气分析数据和进入再生器的主风流量,可以按 以下方法计算烧焦量,焦碳中H/C比。
再生器烧焦量: Ch=V1(3.78+0.242CO2+0.313CO-0.18O2)/[100(CO2+CO+O2)] (kg/h)
(1792m3/min)多算几遍
15
9.4催化裂化催化剂失活与再生
例题3:已知干烟气组成:CO2=9.2%,CO=8.0%
,O2=1.4%(均为体积百分数),干烟气流量为
44800标m3/h,新鲜原料量为75t/h,干空气中
O2/N2=21/79(体积比)。
求:1)理论氧气量; 2)烧焦产生的水量; 3)
10
9.4催化裂化催化剂失活与再生
这种计算方法实际上是把焦炭看成是碳和氢的混合物
,实际计算中还须从总热效应中扣除某一个数值以对 燃烧热作出修正
常见的修正方法如 ESSO 法 (焦炭脱附热的数值为总热
效应的 11.5%) 、 PACE 法 ( 从总热效应中扣除 5 ~ 10% 的
水脱附热)等
催化剂含炭量沿提升管高度的变化并不是单调增加的。 裂化催化剂的活性变化规律是沿提升管高度催化剂活性先 下降然后上升到一最高点,然后又下降。
6
9.4催化裂化催化剂失活与再生
二、裂化Cat.的再生
1、再生方法 烧去Cat.上所沉积的焦炭。 恢复Cat.的活性和选择性,为反应过程提供热量。
催化剂失活后,可以通过再生而恢复由于结焦而丧失
积比)为1.5,求烧焦放热为多少?
(36553*104KJ/h)
14
焦炭燃烧所需主风量(湿空气量)
例题2:已知烟气中氧含量为0.5%(V),
CO2/CO(体积比)为1.5。焦中H/C(质量比)
=10/90,烧焦量为11.4t/h,空气中水蒸汽与干空
气的质量比为0.01,计算燃烧所需要的空气量。
u<umf umf<u<ut u>ut
为固定床 为流化床 稀相输送
在固定床阶段,粒子之间的空隙形成了许多曲曲弯弯的小通道。气体 流过这些小通道时因摩擦阻力而产生压降,摩擦阻力与气体的流速的平
方成正比,因此气体流速越大,产生的床层压力降越大。
28
分析:流化床的压降不随气速的变化而改变?
当气速增大到B点,作用于床层的各力达到平衡,整个床层被悬浮
焦炭是一种缩合产物,主要成分是C和H。
8
9.4催化裂化催化剂失活与再生
焦炭的经验分子式为(CHn)m,n=0.5~1.0。
③再生反应 催化剂再生反应就是用空气中的氧烧去沉积的焦炭, 即焦炭中的C和H被空气中的O2燃烧的氧化反应,再生反 应的产物是CO2、CO和H2O。
9
9.4催化裂化催化剂失活与再生
12
9.4催化裂化催化剂失活与再生
通常在计算再生热时,是根据元素碳和元素氢的燃烧
发热值并结合焦炭的H/C以及烟气中的CO2/CO来计算再 生反应热,此计算值为再生反应的总热效应 。
13
9.4催化裂化催化剂失活与再生
##例题1:某催化裂化装置烧焦炭量为11.4t/h,焦
中H/C(质量比)=8/92,再生烟气中CO2/CO(体
④再生反应热(P376)
再生反应是放热反应,热效应相当大,足以提供本装 置热平衡所需的热量。 把焦炭看作是C和H单质的混合物,分别计算燃烧热, 再计算总和。
C O2 CO2 33873 kJ / kg C
C 0.5O2 CO 10258kJ / kg C
H 2 0.5O2 H 2O 119890 kJ / kg H
(1)影响烧碳反应速率的主要因素
21
9.4催化裂化催化剂失活与再生
(1)再生温度
(2)氧分压:操作压力与再生气体中氧分子浓度 (进入再生器的空气和出再生器的烟气中氧含量的对数 平均值)的乘积。 一般烟气中氧含量控制在0.5%左右;完全再生烟气
中氧含量通常在3%以上。
22
Cat.含C量、Cat.的类型等。
耗风指标:燃烧1kg焦炭所需要的干空气量。
19
9.4催化裂化催化剂失活与再生
计算干烟气的组成:
CO%=(8.93-0.425O2)/[(1+a)H/C+0.425a+0.257] CO2%=aCO%
20
9.4催化裂化催化剂失活与再生
4、再生反应动力学
再生反应速率直接影响Cat.的活性、选择性和装置生 产能力。 再生反应速率决定于焦炭中碳的燃烧速率。由烧碳本 征反应动力学方程式看出
粒开始流化,此后继续增大气速,床层继续膨胀,固体运动也愈激烈,但床 层压基本不变。(如图BC段) 气速再增大到某个数值,如C点固体颗粒被气流带走,床层压降下降,气体 再继续增大,被带出的粒子越多。
27
9.5流态化基本原理
临界流化速度umf (又叫起始流化速度):相当于B点的气速;
终端速度ut(速度):相当于C点的气速
焦炭产率。
16
9.4催化裂化催化剂失活与再生
例题4:某催化裂化装置进入再生器的总的空气
量为1050Nm3/min,再生烟气中的CO为
0.08838%,O2为5.9762%,CO2为12.1632%,空
气中水蒸汽与干空气的分子比为0.012,试计算总
烧焦量,总焦碳中H/C比是多少?( 4321kg/h,
11
9.4催化裂化催化剂失活与再生
烧焦放热中有11.5%消耗在焦炭脱附过程中,故
可利用热=总热-焦炭脱附热 或 Q用=Q总-Q脱=Q总×(100-11.5)% ⑤影响再生反应热的主要因素 反应热的数值与焦炭中的H/C和烟气中CO2/CO有关。 若H/C比值↗,放热↗; CO2/CO比值↗,放热↗。
3
9.4催化裂化催化剂失活与再生
③毒物引起的失活
裂化Cat.的毒物主要是重金属(Fe、Ni、Cu、V)、钠和 碱性氮化合物。 (2)Cat.的平衡活性 新鲜Cat.的活性不能反映装置中实际的Cat.活性。
在实际生产中,用“平衡活性”来表示装置中Cat.活
性。
4
9.4裂化催化剂的失活与再生
影响Cat.平衡活性的因素主要有:
25
9.5流态化基本原理
26
9.5流态化基本原理
实验将发生如下现象:当气速U较小时,床层内的催化剂颗粒不活动,处
于堆紧状态,即处于固定床,只是随气体流速的增大,床层压将增加图 AB段。
气速增大到一定程度时,床层开始膨胀,一些细粒在有限的范围内运动。
当层速再增高时,固体粒子被气流悬浮起来,并做不规则的运动,即固体颗
V1—进入再生器的干空气量Nm3/h,V1=V2/(1+e)
V2—湿空气量Nm3/h; e—水蒸气和干空气的分子比。
CO2,CO,O2----分别为在干烟气中的体积分数。
18Байду номын сангаас
焦碳中H/C比
H/C=[8.93-0.425( CO2+O2)-0.257CO]/ (CO2+CO) 主风单耗=湿空气量/烧焦量 (Nm3/kg)
2
9.4催化裂化催化剂失活与再生
②结焦失活:焦炭沉积在Cat.的表面上,覆盖在Cat.的活性
中心,使其活性和选择性↙。 工业催化裂化所产生的焦炭包括:
催化焦:烃类在催化剂活性中心上反应时生成的焦炭 附加焦:原料中的焦炭前身物(稠环芳烃)在催化剂表面上
吸附、经缩合反应生成的。
可汽提焦:重质烃类 污染焦:重金属沉积造成的
起来而固体颗粒自由运动,即
床层压降*床层截面积=床中固体重-固体所受浮力
△P×F=V×(1-ε) ×ρs- V×(1-ε) × ρg
上式可近似写作:△P×F=V×(1-ε) ×ρs
即床层压降等于单位面积床层重量(床层静压)。利用这个原理,
在实验室或工业装置中可以通过测定流化床中不同高度的两点压差 来计算床层中固体藏量或床层密度。
第九章 催化裂化 Chapter 9 Catalytic Cracking
1
9.4 催化裂化催化剂失活与再生
一、催化剂的失活
催化剂的失活*:在反应-再生过程中,Cat.的活性和选 择性不断下降的现象。 (1)催化裂化Cat.失活性的原因* ①水热失活 在高温和水蒸气作用下,裂化Cat.的比表面积↙、孔 容↙,分子筛晶体结构破坏。
①Cat.的水热失活速率:再生器的操作条件 ②Cat.的置换速率 ③Cat.的重金属污染 ④其它因素:原料油的性质、Cat.的流失率、新鲜Cat. 的活性及稳定性等。
5
工业提升管反应器内催化剂失活规律
石油大学的徐春明利用在线取样分析系统对工业提升管反 应器内催化剂失活规律进行了研究,结果表明:
再生时间=藏量/催化剂循环量
烧焦强度=烧焦量/藏量
(2)再生器工艺数学模型
在实际生产过程中,结焦催化剂的再生是在流化床中进行的,流化状
态对反应物的浓度有影响,进而对再生反应速率有影响。在高气速流 化床中,烧碳反应速率高。
23
9.5 流态化基本原理
一、流化床的形成与流化域 1、流化床的形成
24
9.5流态化基本原理
的活性,但不能恢复由于结构变化及金属污染引起的失 活。
7
9.4催化裂化催化剂失活与再生
①待生剂:在工业上把经反应沉积了焦炭的催化剂。
②再生剂:再生除去部分焦炭的催化剂。 2、再生要求 无定型的硅酸铝Cat.:再生后含碳量为0.3~0.5%; 分子筛Cat.:再生后含碳量<0.2%以下。 3、再生反应和反应热* ①焦炭分子式