切削过程中的物理现象分析
切削过程
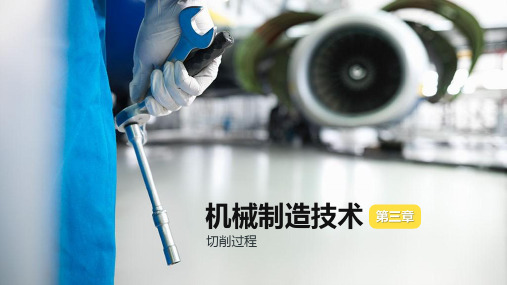
机械制造技术切削过程切削过程切削过程是刀具从工件表面上切除多余材料,从切屑形成开始到已加工表面形成为止的完整过程。
一、切屑的形成过程在刀具的作用下,切削层金属经过一个复杂的过程变成切屑。
在这一过程中,切削层的形态发生了变化。
产生这一变化的根本原因是切削层金属在刀具的作用下产生老变形,这就是切削过程中的变形。
伴随切削过程的变形,出现一系列的物理现象,如切削力、切削热、切削温度、刀具磨损、积屑瘤等。
切削过程的变形是研究切削过程的基础。
图1 塑性金属材料的剪切破坏 削过程三个变形区图1所示模型说明了切削过程的变形。
塑性金属材料在刀具的作用下,沿与作用力成45o 的方向产生剪切滑移变形,当变形达到一定极限值时,就会沿着变形方向产生剪切滑移破坏。
若刀具连续运动,虚线以上的材料就会在刀具的作用下与下方材料分离。
金属切削过程与上述过程基本相似。
如图2所示,在刀具的作用下,切削层金属经过复杂的变形后与工件基体材料分离形成了切屑。
这一过程中产生的变形可以划分为三个区域,即三个变形区,它们是位于切削刃前OAM之间的第I变形区、靠近前刀面的第II变形区和位于后刀面附近的第III变形区。
图2 切削过程三个变形区(1) 第一(Ⅰ)变形区切削层金属从开始塑性变形到剪切滑移基本完成的过程区,也就是图3所示OA与OM之间的区域就是第一(Ⅰ)变形区。
图3 金属切削过程的三个变形区金属材料在OA线以左发生弹性变形。
在OA线上,材料的剪应力达到屈服强度τs,开始塑性变形,产生滑移,OA称为始滑移线。
随着刀具的连续移动,原来处于滑移线上的金属不断向刀具靠拢,应力和变形也逐渐增大,达到OM线时,应力和变形达到最大值。
超过OM线,切削层金属将沿前刀面流出,形成切屑,完成切离。
OM线称为终滑移线。
OA线和OM线之间的区域是塑性变形区域。
第一变形区是金属切削变形过程中最大的变形区,在这个区域内,金属将产生大量的切削热,并消耗大部分功率。
此区域较窄,宽度仅0.02~0.2mm。
金属切削原理

金属切削原理一、引言金属切削是一种重要的加工方法,广泛应用于机械制造、航空航天、汽车制造等领域。
金属切削的原理是将金属材料通过刀具的切削力和磨擦力进行去除,从而得到所需形状和尺寸的工件。
本文将详细介绍金属切削的原理。
二、金属材料的物理特性金属材料具有高强度、高硬度、高塑性等特点。
在进行切削加工时,需要考虑到这些特性对加工过程和结果的影响。
1.硬度硬度是指材料抵抗外界力量侵蚀和破坏的能力。
在进行金属切削时,硬度会影响到刀具对材料的切削深度和速度。
硬度越大,材料越难被去除,需要采用更高强度和更耐磨损的刀具。
2.韧性韧性是指材料抵抗断裂和变形的能力。
在进行金属切削时,韧性会影响到刀具对材料的变形程度和断裂情况。
韧性越大,材料越容易被刀具弯曲和拉伸,需要采用更大的切削力和更耐磨损的刀具。
3.塑性塑性是指材料在受到外力作用下发生变形的能力。
在进行金属切削时,塑性会影响到材料的变形程度和表面质量。
塑性越大,材料越容易被切削并留下较光滑的表面。
三、切削力的产生金属切削过程中,主要有三种力对工件进行去除:正向切削力、侧向切削力和径向切削力。
这些力产生的原因如下:1.正向切削力正向切削力是指沿着工件表面方向施加在主轴上的推进力。
它是由于主轴上旋转的刀具与工件之间产生了摩擦而引起的。
2.侧向切削力侧向切削力是指垂直于工件表面方向施加在主轴上的推进力。
它是由于主轴上旋转的刀具与工件之间产生了摩擦而引起的。
3.径向切削力径向切削力是指垂直于工件表面方向施加在主轴上的推进力。
它是由于主轴上旋转的刀具与工件之间产生了摩擦而引起的。
四、切削过程中的热效应金属切削过程中,由于摩擦和变形,会产生大量的热量。
这些热量会对材料和刀具造成影响。
1.材料的热变形在金属切削过程中,由于高速旋转的刀具与工件之间产生了摩擦,会使得材料表面温度升高。
当温度达到一定值时,材料就会发生热变形,导致尺寸和形状发生变化。
2.材料的热软化在金属切削过程中,由于高速旋转的刀具与工件之间产生了摩擦,会使得材料表面温度升高。
3-2切削力

生产中,为了分析切削力对工件、 生产中,为了分析切削力对工件、刀具和机床的 影响,通常把总切削力 分解为三个分力。如图3-15 总切削力F分解为三个分力 影响,通常把总切削力 分解为三个分力。如图 所示。其中: 所示。其中: 也称主切削力, 切削力 ——也称主切削力,车外圆时,又称切向力。 也称主切削力 车外圆时,又称切向力。 它是总切削力在主运动方向的分力, 切削速度的方向 它是总切削力在主运动方向的分力,与切削速度的方向 主运动方向的分力 一致。消耗90﹪以上的切削功率,是计算刀具强度、 一致。消耗 ﹪以上的切削功率,是计算刀具强度、机 床功率的主要依据。 床功率的主要依据。
2.切削用量
(1)背吃刀量和进给量 )
ap
f
背吃刀量和进给量f加大, 背吃刀量和进给量 加大,均使切削力增大,但两 加大
者的影响程度不同。见表3-1。 者的影响程度不同。见表 。
f
ap
进给量不变背吃刀量增加一倍,切削力也增大一倍。 进给量不变背吃刀量增加一倍,切削力也增大一倍。
不变,进给量增大一倍时,切削力不成正比例增加, 不变,进给量增大一倍时,切削力不成正比例增加,增 大0.7~0.8倍。上述影响反映在切削力实验公式中指数, 倍
vc
vc
率,又使切削力减小。 又使切削力减小。
3.刀具几何参数 (1)前角 γ o ) γ 切削塑性材料时, 增大,变形减小, 切削塑性材料时, o 增大,变形减小,切削力
Fc、Fp、Ff降低。如图 、 、 降低 如图3-18所示。 降低。 所示。 所示 切削脆性材料时,由于变形小,摩擦小, 切削脆性材料时,由于变形小,摩擦小,前角对 切削力的影响不明显。 切削力的影响不明显。 负倒棱使切削刃变钝,切削力增加。 (2)负倒棱 负倒棱使切削刃变钝,切削力增加。 ) (3)主偏角 ) r 由图3-20可知,主偏角的变化,改变背向力和进给力的比 可知, 由图 可知 主偏角的变化, 主偏角增大,背向力减少, 例,主偏角增大,背向力减少,进给力增大。生产 车细长轴时 系统刚性差, 中,车细长轴时,系统刚性差,止工件在背向力 ° ° 甚至大于90°),以防止工件在背向力 腰鼓形工件 作用下变形而加工出腰鼓形工件。 作用下变形而加工出腰鼓形工件。
第二章第三节 金属切削过程及其物理现象
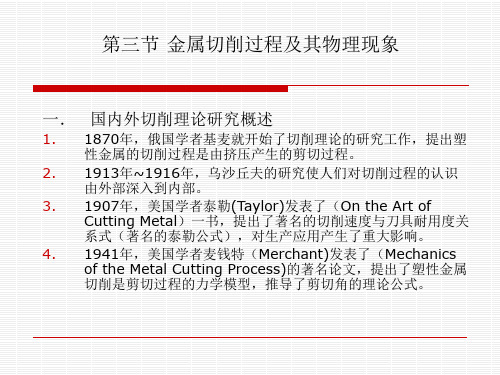
五.变形程度的表示方法
1. 剪切角 2. 相对滑移或剪应变 3. 变形系数 a / l
六. 前刀面的挤压与摩擦及其对切屑变形的影响
特征:使切屑底层靠近前刀面处纤维化,流动速度 减慢,甚至滞留在前刀面上; 切屑弯曲; 由摩擦产生的热量使切屑与刀具接触面温度升高。
1. 2. 3. 4.
七. 积屑瘤的形成及其对切削过程的影切 屑的情况下,加工一般钢料或其他 塑性材料时,常常在刀具前刀面粘 着一块剖面有时呈三角形的硬块。 它的硬度很高,通常是工件材料的 2~3倍,在处于比较稳定的状态时, 能够代替切削刃进行切削。这块冷 焊在前刀面上的金属就叫积屑瘤。
第三节 金属切削过程及其物理现象
一. 国内外切削理论研究概述
1. 2. 3. 1870年,俄国学者基麦就开始了切削理论的研究工作,提出塑 性金属的切削过程是由挤压产生的剪切过程。 1913年~1916年,乌沙丘夫的研究使人们对切削过程的认识 由外部深入到内部。 1907年,美国学者泰勒(Taylor)发表了(On the Art of Cutting Metal)一书,提出了著名的切削速度与刀具耐用度关 系式(著名的泰勒公式),对生产应用产生了重大影响。 1941年,美国学者麦钱特(Merchant)发表了(Mechanics of the Metal Cutting Process)的著名论文,提出了塑性金属 切削是剪切过程的力学模型,推导了剪切角的理论公式。
4.
5.
6.
在Merchant之后,诸多学者对剪切角的理论推导,剪切角与变形 的关系以及切削速度对切屑变形的影响进行了广泛的研究。如美国 学者李-谢弗、苏联学者佐列夫、澳大利亚学者奥克斯利、日本学 者中山一雄、日本学者臼井英治、华裔学者赵佩之、美国学者阿尔 伯莱特等都各自做出了一定的贡献。 1981年起,在刘培德教授的带领下,大连理工大学机械系金属切 削原理与刀具教研室的多位老师开展了切削理论的研究。取得的成 果有: 提出了正交切削时刃前区应力分析的新模型(带弯矩的切削力学模 型) 证明了切削过程中存在弯矩,弯矩的存在使切屑发生弯曲。通过一 定手段控制弯矩的大小及正负控制切屑的卷曲与折断,从而发展了 断屑理论。解决了诸多生产难题,如上海宝钢无缝钢管厂在西德产 数控车床上螺纹加工的断屑问题。
刀具切削的工作原理

刀具切削的工作原理刀具切削是现代工业中常见的加工方式之一,它广泛应用于各个行业,如机械制造、汽车制造、航空航天等等。
本文将详细介绍刀具切削的工作原理,并分点列出其重要的方面。
一、切削工具与刀具材料1. 切削工具:包括刀具刀片、钻头、铣刀等。
它们的形状、尺寸和材料的选择直接影响到切削加工的效果。
2. 刀具材料:常见的刀具材料包括硬质合金、高速钢、陶瓷等。
不同材料具有不同的硬度、韧性和耐磨性,能够应对不同材料的切削需求。
二、切削原理1. 花削原理:切削刀具在工件上作圆周运动,通过将切屑削掉的方式实现切削。
适用于外圆、内圆等工件的加工。
2. 铣削原理:切削刀具以较高速度旋转,通过将工件上一层或多层金属削下来的方式实现切削。
适用于直线、曲线等多种形状的加工。
3. 钻削原理:切削刀具以旋转的方式进入工件内部,通过刮削或削下的方式实现切削。
适用于孔加工。
4. 切下原理:切削刀具削下工件上的金属,如钻孔、车削等。
适用于各种形状的加工。
三、切削过程的物理现象1. 切削力:切削过程中,切削刀具对工件施加一定的力。
切削力的大小和方向会影响切削刀具和工件的磨损、加工精度等。
切削力分为切削力和切向力两个方向。
2. 切削热:切削过程中,由于切削力和摩擦力的作用,会产生大量的热量。
高温会导致刀具变软、变形,也会对工件表面造成损伤。
因此,切削过程需要保持适当的冷却和润滑。
3. 切削震动:切削过程中,由于刀具和工件的摩擦以及其它因素,会产生切削震动。
切削震动会导致切削失准、加工表面质量差等问题。
因此,需要采取措施来减小切削震动。
四、切削参数的选择1. 切削速度:切削速度是指切削刀具和工件之间的相对速度。
选择合适的切削速度可以提高生产效率,同时也要考虑刀具材料的耐磨性。
2. 进给量:进给量是指刀具单位时间内移动的距离。
合理的进给量能够控制加工负荷和加工精度。
3. 切削深度:切削深度是指刀具在一次切削过程中进入工件的深度。
切削深度的选择与切削力、切削热等因素密切相关。
第一章 金属切削过程中的基本规律讲解
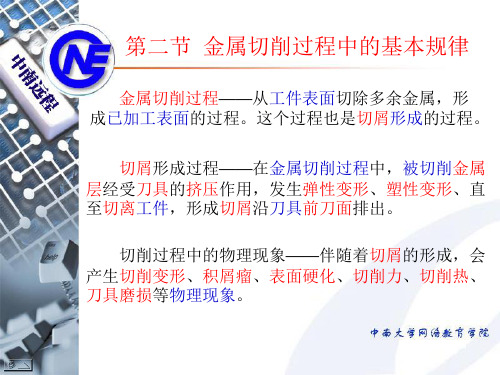
②增大前角 积屑瘤具有30°左右的前角。
③增大切削厚度 切削厚度增大了ΔhD。
④增大已加工表面粗糙度
原因:积屑瘤不规则的形状和非周期性的生成与脱 落、可能引起的振动、积屑瘤碎片残留在已加工表面 上。
积屑瘤
(3)影响积屑瘤的主要因素
在滑动区内的摩擦为外摩擦,该处的剪应力τy 由τs 逐渐减小到零。
正应力σγ 在刀刃处最大,离切削刃越远,前刀面上 的正应力越小,并逐渐减小到零。
刀-屑接触面上的摩擦特性
刀-屑接触面上的摩擦特性
前刀面上的摩擦系数μ是变化的,其计算公式如下:
s av
式中 τs ——工件材料的剪切屈服强度,随温度升 高而略有下降
响比较明显,前角γ0 对切削力的影响最大。
切削热的产生和传出
(1)切削热的产生 切削加工中,切削变形与摩擦所消耗的能量几乎全 部转换为热能,因此三个变形区就是三个发热源。如 下图所示。
切削热的产生和传出
(2)切削热的传出 由切屑、刀具、工件、周围介质传导出去。
车削钢料时,切削热被切屑带走约50% ~ 86%,传入 刀具的约占10% ~ 40%,传入工件的约为3% ~ 9%,传入 周围介质的约占1%。
相对滑移ε
切削层中m´n´线滑移至m˝n˝ ,瞬时位移为∆y , 滑移量为∆s 。
cos o
sin cos( o )
增大前角γo 和剪切角φ,则
相对滑移ε减小,即切削
变形减小。
变形系数ξ
将切削时形成的切屑与切削层尺寸比较,可知切 屑的长度缩短而厚度增加。 变形系数就是切屑厚度和 切削层厚度的比值,或者是切削层长度和切屑长度的 比值。
金属切削过程中的物理现象
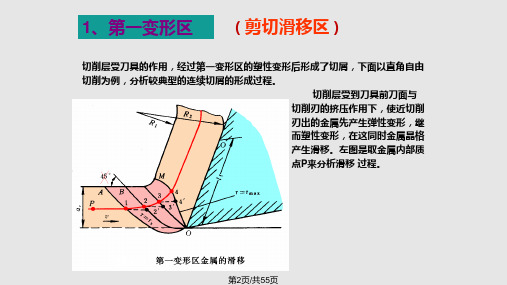
第20页/共55页
2)切削速度的影响
切削塑性材料,切削速度的影响分为两个阶段: 有积屑瘤和无积屑瘤两个阶段。
切削塑性材料时
第21页/共55页
切削速度是通过影响切削变形程度来影 响切削力,切削变形大,则切削力大。
第22页/共55页
切削铸铁等脆性材料时,被切材料 的塑性变形及它与前刀面的摩擦均比 较小。υc对切削力没有显著影响。
在材料的强度、硬度相近的情况下,材料的塑性越大。韧性越大,则切削力 越大。 ◆塑性大的材料在切削过程中将产生较大的塑性变形和加 工硬化,且切削与前 刀面的接触时间长,故切削力较大; ◆韧性大的材料,使之发生变形或破坏需消耗较多的能量,故切削力较大。
切削脆性材料时,一般皆为崩脆切削,从而切削与前刀面的摩擦都比较小, 故其切削力相对较小。
第14页/共55页
3.总切削力的几何分力
F F F F F F
2
c
2
N
2 2 2
C
P
f
Fp=FNcosKr;
Ff =FNsinkr
一般情况下,Fc最大,Fp和Ff小一些
第15页/共55页
主切削力Fc:切削合力F在主运动方向的分力,又称切向分力。它与切削速度 方向一致,在切削过程中做功最多,占总切削功率的90%以上。Fc是计算机 床动力、设备的强度及刚度的基本数据。
切削过程中消耗的功将绝大部分转化成 (约 99%)转换为热量,即切削热。
切削热 Q≈Fzvc
第30页/共55页
切削热传出: (1)通过工件传出Qg,使工件温度升高 (2)通过切屑传出Qx,使切屑温度升高 (3)通过刀具传出Qd,使刀具温度升高 (4)通过周围介质传出Qj
Q=Qg+Qx+Qd+Qj 对车、铣、刨削加工,50~86%由切屑带走,10~40%传入刀具,3~9%传入 工件,1%传入空气 ; 钻削时,28%由切屑带走,15%左右传给工件,50%左右传给刀具,其余由周围 介质带走; 磨削时,大部分热量传给工件(84%),传给砂轮12%,而极小比例的热量传给磨 屑,因此会使工件温升很高,甚至烧伤工具表面。
第2章 金属切削过程的物理现象
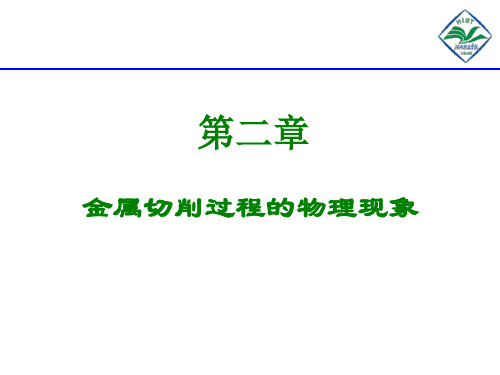
4.崩碎切屑
切削脆性材料(如灰铸铁)时,由于材料的塑性很小,抗
拉强度较低刀具切入后,切削层内靠近切削刃和前面的 局部金属,几乎不经过塑性变形就被挤裂,或在拉应力 状态下脆断,形成大小不等、形状各异的碎块状切屑。
2.2.2 切屑与前刀面的摩擦和积屑瘤
1.切屑与前刀面的摩擦
切屑与前刀面间的这种摩擦与一般金属接触面间的摩擦 不同。如图2-5所示,切屑与前刀面接触去分为粘结区 和滑动区两部分。
1.带状切屑
这是一种最常见的切屑形状。当切屑内剪应力小于材 料的强度极限时,剪切滑移变形较小,切屑连绵不断,
没有裂纹,就形成了带状切屑
2.节状切屑
当切屑内剪应力在局部地方达到了材料的破裂极限,
会形成节状切屑。
2.2.1 切屑的种类
3.粒状切屑
当切屑内部剪应力超过了材料的破裂强度,切屑将沿
剪切面完全断开,形成粒状切屑。
图2-1 金属切削的三个变形区域
图2-2 第一变形区金属的滑移
2.1.2切削层的变形
1.第一变形区(剪切变形区)
如图2-2所示从OA线开始发生塑性变形,到OM线晶粒
的剪切滑移基本完成,这个区域叫第一变形区。
2.第二变形区(挤压变形区)
当切屑从刀具的前倾面排出时,受刀具前面的推挤和摩 擦,必将发生进一步变形,这就是第二变形区的变形。 这一变形主要集中在切屑底面一薄层金属里,使靠近刀 具前倾面的金属纤维基本上与前倾面平行,离刀具前面 愈远,影响愈小。
由于进给功率相对切削功率Pc很小(<1%~2%),可 忽略不计。所以,工作功率P,可以用切削功率Pc近似 代替。 在计算机床电机功率Pm 时,还应考虑机床的传动效率 ηm(一般取0.75~0.85),则:
- 1、下载文档前请自行甄别文档内容的完整性,平台不提供额外的编辑、内容补充、找答案等附加服务。
- 2、"仅部分预览"的文档,不可在线预览部分如存在完整性等问题,可反馈申请退款(可完整预览的文档不适用该条件!)。
- 3、如文档侵犯您的权益,请联系客服反馈,我们会尽快为您处理(人工客服工作时间:9:00-18:30)。
一般在常温下加工,并且不引起工件 的化学 或物相 变化﹐ 称冷加 工。一 般在高 于或低 于常温 状态的 加工﹐ 会引起 工件的 化学或 物
相变化﹐称热加工。冷加工按加工方 式的差 别可分 为切削 加工和 压力加 工。热 加工常 见有热 处理﹐ 煅造﹐ 铸造和 焊接。
机械加工 另外装配时常常要用到冷热处理。例 如:轴 承在装 配时往 往将内 圈放入 液氮里 冷却使 其尺寸 收缩, 将外圈 适当加 热使其 尺寸放 大
近转化为热,称为切削热。 (2)切削热的主要来源
是被切削金属的变形、切屑与前刀面的摩擦和工件 与刀具后面的摩擦。 (3)切削温度
切削区域的平均温度。 (4)切削热的传散
切削热通过切屑、工件、刀具以及周围介质传散。 (5)减少切削热,降低切削温度的措施
增大刀具前角,减小主偏角;优先采用大的背吃刀量 和进给量,再确定合理的切削速度;使用切削液都能减少 和带走切削热,降低切削温度。
1-11
课程教学模块五:金属切削的基本理论与应用 ——课题4
5.4.5 刀具的磨损和耐用度
在切削过程中,刀具在高压、高温和强烈摩擦条件 下工作,切削刃由锋利逐渐变钝以至失去正常切削能力。 刀具磨损超过允许值后,须及时刃磨,否则会引起振动 并使加工质量下降。
1.刀具的磨损 刀具正常磨损时,按磨损部位不同,可分为主后面 磨损、前刀面磨损、前刀面和主后面同时磨损三种 形式。
5.4.2 滞流层和积屑瘤
切削塑性材料时,由于切屑底面与前刀面的挤压和剧烈 摩擦,使切屑底层的流动速度低于上层的流动速度,形成滞流 层。当滞流层金 属与前刀面之间的摩擦力超过切屑本身分 子间结合力时,滞流层的部分新鲜金属就会粘附在刀刃附近, 形成楔形的积屑瘤。
1-8
课程教学模块五:金属切削的基本理论与应用 ——课题4
2.刀具耐用度 刀具两次刃磨之间实际切削的时间,称为刀具的
耐用度。
1-12
课程教学模块五:金属切削的基本理论与应用 ——课题4
5.4.5 刀具的磨损和耐用度
1-13
机械加工是一种用加工机械对工件的 外形尺 寸或性 能进行 改变的 过程。 按被加 工的工 件处于 的温度 状态﹐ 分为冷 加工和 热加工 。
机械产品 1959年,Richard P Feynman(1965年诺贝尔 物理奖 获得者) 就提出 了微型 机械的 设想。 1962年 第一个 硅微型 压力传 感器问 世,其
,然后再将其装配在一起。火车的车 轮外圈 也是用 加热的 方法将 其套在 基体上 ,冷却 时即可 保证其 结合的 牢固性 (此种 方法现 在
依旧应用于某些零部件的转配过程中 )。
机械加工包括:灯丝电源绕组、激光切 割、重 型加工 、金属 粘结、 金属拉 拔、等
离子切割、精密焊接、辊轧成型、金 属板材 弯曲成 型、模 锻、水 喷射切 割、精 密焊接 等。
切屑的背面呈锯齿形,底面有时出现裂纹。 (3 )崩碎切屑
切削铸铁等脆性材料时,切削层产生弹性变形后,一 般不经过塑性变形就突然崩碎,形成不规则的碎块状屑片, 称为崩碎切屑。
1-6
课程教学模块五:金属切削的基本理论与应用 ——课题4
5.4.1 切削加工概述
1-7
课程教学模块五:金属切削的基本理论与应用 ——课题4
1-9
课程教学模块五:金属切削的基本理论与应用 ——课题4
5.4.3 切削力
(2)背向力Fp 总切削力在垂直于工作平面上的分力。 (3)进给力 总切削力在进给运动方向上的分力(正投影)。
1-10
课程教学模块五:金属切削的基本理论与应用 ——课题4
5.4.4 切削热与切削温度
(1)切削热 金属切削过程中所消耗的功,绝大部分在切削刃附
1-5
课程教学模块五:金属切削的基本理论与应用 ——课题4
5.4.1 切削加工概述
2)切屑的种类 切削时,由于被加工材料性能与切削条件的不同,切削
层金属将产生不同程度的变形,从而形成不同类型的切屑。 常见的切屑有以下三种。 (1 )带状切屑
外形连绵不断,与前刀面接触的面很光滑,背面呈毛 茸状。 (2 )节状切屑
5.4.3 切削力
在切削过程中,刀具上所有参与切削的各切削部分 所产生的总切削力的合力称为刀具的总 切削力。
(1)切削力Fc 总切削力在主运动方向上的正投影,旧称垂直切削分 力Fv。切削力的大小约占总切削力的 90%以上。 Fc是计算机床动力、设计主传动系统的零件、夹具 强度和刚度的主要依据;也是计算刀柄、刀体强度和选择 切削用量的依据。
机械加工:广意的机械加工就是
指能用机械手段制造产品的过程;狭 意的是 用车床 (Lathe Machine)、铣床(Milling Machine)、钻床(Driling Machine)、磨
床(Grinding Machine)、冲压机、压铸机机等专用机 械设备 制作零 件的过 程。 编辑本段微型机械加工技术的国外发 展现状
1-4
课程教学模块五:金属切削的基本理论与应用 ——课题4
5.4.1 切削加工概述
随着刀具连续切入,原来处于始滑移面 OA 上的金属 不断向刀具靠近,当滑移过程进入终滑移面 OE 位置时,应 力应变达到最大值,若切应力超过材料的强度极限时,材 料被挤裂。越过 OE 面后切削层脱离工件,沿着前刀面流 出而形成切屑。
课程教学模块五:金属切削的基本理论与应用 ——课题4
切削过程 中的物理现象分析
1-1
Байду номын сангаас
课程教学模块五:金属切削的基本理论与应用 ——课题4
课程教学模块五:金属切削的基本理论与应用 ——课题4
课程教学模块五:金属切削的基本理论与应用 ——课题4
5.4.1 切削加工概述
1、切屑的形成与种类
金属切削加工方式很多,一般可分为车削加工、铣削 加工、钻削加工、镗削加工、刨削加工、磨削加工、齿 轮加工及钳工等。 1)切屑的形成