毛刺产生和消除
毛刺的消除
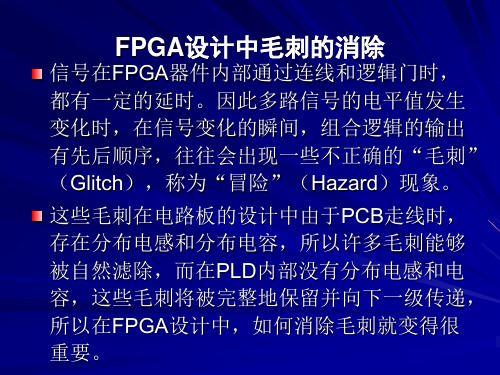
毛刺
时序仿真输出波形
引入了D 引入了D触发器的长帧同步时钟的产生
module longframe2(clk,strb); parameter DELAY=8; input clk; output strb; reg[7:0] counter; reg temp,strb; always@(posedge clk) begin if(counter==255) counter<=0; else counter<=counter+1; end always@(posedge clk) begin strb<=temp;end //引入触发器 //引入触发器 always@(counter) begin if(counter<=(DELAY-1)) temp<=1; else temp<=0; if(counter<=(DELAYend endmodule
消除毛刺后的时序仿真输出波形
延时方式去毛刺
延时方式去毛刺
逻辑方式去毛刺
逻辑方式去毛刺
定时方式去毛刺
定时方式去毛刺
跨时钟域设计
module metastable(clka,clkb,ina,outb); input clka,clkb,ina; output outb; reg outb,outa; always @(posedge clka) outa=ina; always @(posedge clkb) outb=outa; outa outb~reg0 endmodule
FPGA设计中毛刺的消除 FPGA设计中毛刺的消除
信号在FPGA器件内部通过连线和逻辑门时, 信号在FPGA器件内部通过连线和逻辑门时, 都有一定的延时。因此多路信号的电平值发生 变化时,在信号变化的瞬间,组合逻辑的输出 有先后顺序,往往会出现一些不正确的“毛刺” 有先后顺序,往往会出现一些不正确的“毛刺” (Glitch),称为“冒险”(Hazard)现象。 Glitch),称为“冒险” Hazard)现象。 这些毛刺在电路板的设计中由于PCB走线时, 这些毛刺在电路板的设计中由于PCB走线时, 存在分布电感和分布电容,所以许多毛刺能够 被自然滤除,而在PLD内部没有分布电感和电 被自然滤除,而在PLD内部没有分布电感和电 容,这些毛刺将被完整地保留并向下一级传递, 所以在FPGA设计中,如何消除毛刺就变得很 所以在FPGA设计中,如何消除毛刺就变得很 重要。
电路中如何消除方波跳变时产生的尖刺

电路中如何消除方波跳变时产生的尖刺?解释一:在组合逻辑中,由于门的输入信号通路中经过了不同的延时,导致到达该门的时间不一致叫竞争。
产生毛刺叫冒险。
如果布尔式中有相反的信号则可能产生竞争和冒险现象。
解决方法:一是添加布尔式的(冗余)消去项,但是不能避免功能冒险,二是在芯片外部加电容。
三是增加选通电路。
在组合逻辑中,由于多少输入信号变化先后不同、信号传输的路径不同,或是各种器件延迟时间不同(这种现象称为竞争)都有可能造成输出波形产生不应有的尖脉冲(俗称毛刺),这种现象成为冒险。
解释二:竞争与冒险是数字电路中存在的一种现象。
由于元器件质量和设备工艺已达到相当高的水平,因而数字电路的故障往往是竞争与冒险引起的,所以要研究它们。
在一个复杂的数字电路的设计阶段,就完全预料电路中的竞争与冒险是困难的,有一些要通过实验来检查。
下面将说明组合数字电路中竞争与冒险的基本概念和确定消除它的一些基本方法。
竞争:在组合电路中,信号经由不同的途径达到某一会合点的时间有先有后,这种现象称为竞争。
冒险:由于竞争而引起电路输出发生瞬间错误现象称为冒险。
表现为输出端出现了原设计中没有的窄脉冲,常称其为毛刺。
竞争与冒险的关系:有竞争不一定会产生冒险,但有冒险就一定有竞争。
在组合逻辑中,由于门的输入信号通路中经过了不同的延时,导致到达该门的时间不一致叫竞争。
产生毛刺叫冒险。
如果布尔式中有相反的信号则可能产生竞争和冒险现象。
解决方法:一是添加布尔式的消去项,二是在芯片外部加电容。
当组合逻辑电路存在冒险现象时,可以采取修改逻辑设计,增加选通电路,增加输出滤波等多种方法来消除冒险现象。
当一个门的输入有两个或两个以上的变量发生改变时,由于这些变量是经过不同路径产生的,使得它们状态改变的时刻有先有后,这种时差引起的现象称为竞争(Race)。
数字电路毛刺消除问题

数字电路⽑刺消除问题参考博⽂:和1. ⽑刺的产⽣原因:冒险和竞争使⽤分⽴元件设计电路时,由于PCB在⾛线时,存在分布电容和电容,所以在⼏ns内⽑刺被⾃然滤除,⽽在PLD内部没有分布电感和电容,所以在PLD/FPGA设计中,竞争和冒险问题⽐较重要。
信号在FPGA器件内部通过连线和逻辑单元时,都有⼀定的延时。
延时的⼤⼩与连线的长短和逻辑单元的数⽬有关,同时还受器件的制造⼯艺、⼯作电压、温度等条件的影响。
信号的⾼低电平转换也需要⼀定的过渡时间。
由于存在这两⽅⾯因素,多路信号的电平值发⽣变化时,在信号变化的瞬间,组合逻辑的输出有先后顺序,并不是同时变化,往往会出现⼀些不正确的尖峰信号,这些尖峰信号称为"⽑刺"。
如果⼀个组合逻辑电路中有"⽑刺"出现,就说明该电路存在"冒险"。
可以概括的讲,只要输⼊信号同时变化,(经过内部⾛线)组合逻辑必将产⽣⽑刺。
将它们的输出直接连接到时钟输⼊端、清零或置位端⼝的设计⽅法是错误的,这可能会导致严重的后果。
所以我们必须检查设计中所有时钟、清零和置位等对⽑刺敏感的输⼊端⼝,确保输⼊不会含有任何⽑刺。
存在逻辑冒险的电路:仿真波形:2. 判断是否存在冒险关于冒险的知识,数电书上有详细的说明,当时没有认真学,只了解个⼤概,现在⼜要重新看...还记得当年画卡诺图时的痛苦冒险按照产⽣⽅式分为静态冒险 & 动态冒险两⼤类。
静态冒险指输⼊有变化,⽽输出不应该变化时产⽣的窄脉冲;动态冒险指输⼊变化时,输出也应该变化时产⽣的冒险。
动态冒险是由静态冒险引起的,所以,存在动态冒险的电路也存在静态冒险。
静态冒险根据产⽣条件不同,分为功能冒险和逻辑冒险两种。
当有两个或两个以上的输⼊信号同时变化时,在输出端有⽑刺,称为功能冒险;如果只有⼀个输⼊变量变化时,出现的冒险称为逻辑冒险。
因为动态冒险是由静态冒险引起的,所以消除了静态冒险,也就消除了动态冒险。
去毛刺作业规范

文件编号:IQMS/JLW-JS-066A去毛刺作业规范(试行)编制:审核:批准:日期:北京纵横机电技术开发公司技术中心工艺技术部(中国铁道科学研究院机车车辆研究所)一、主题内容及适用范围本规范规定了机械、电子、电气零部件去毛刺作业的一般通用要求。
本规范与产品图样和相关技术要求文件配合使用。
本规范适用于北京纵横机电技术开发公司所有自制件产品,对于外协产品也具有指导意义。
由于产品的特殊性,不适用本标准的,允许制定相应作业指导书。
二、引用标准JB 4129 冲压件毛刺高度DIN 6784 各种工件的棱边标注GB/T 4127.13 立式砂轮机用去毛刺和荒磨砂轮三、去毛刺定义及方法分类1、去毛刺定义广义去毛刺流程如图1所示,是包含从设计去毛刺、机加工去毛刺、过程去毛刺、专门去毛刺到清洗工艺的一个完整过程。
狭义去毛刺工艺主要指专门去毛刺工序。
图1、广义去毛刺流程2、去毛刺方法分类2.1无毛刺或少毛刺设计和加工零部件经过加工后在其相交棱边处会产生大小不同的毛刺,通过改变设计结构和加工工艺,可以达到零件无或少毛刺,从而提高生产效率、减少成本和人工去毛刺强度。
因此,无毛刺或少毛刺设计及加工是一种主动去毛刺方法。
表1为无或少毛刺设计及加工典型实例。
表1 无毛刺或少毛刺设计及加工序号典型结构说明1增加倒角,去除毛刺。
加工螺纹前,在螺纹入口处加工90°至120°倒角,使得螺纹入口处无毛刺。
2增加退刀槽,去除毛刺。
在内外螺纹根部,加工退刀槽,去除螺纹外圆和内控交界处毛刺。
3改进结构,减少毛刺产生外圆或螺纹A与直槽交接处,应设计成阶梯轴,铣槽时,外圆或螺纹工作面A不会有毛刺。
4改进结构,减少毛刺影响改进焊接零件设计,减少和消除焊缝对装配使用的影响。
5 增加槽边缘倒角,去除毛刺。
在挡圈槽和阶梯轴处加工倒角,倒角15°或30°最佳,可以去除挡圈槽与内孔交接处棱角以及阶梯轴交汇处棱角的毛刺。
压铸件去毛刺方法大全

压铸件去毛刺的方法
机器人去毛刺相关要素
机器人本体: •刚性 •位置重复精度 •自由度(轴数)
利用数据库和输入,选择最佳工艺,输入: •加工质量要求 •材质 •尺寸 •毛刺大小位置等加工信息
压铸件去毛刺的方法
三、振磨
借助冲击振动/摩擦去除毛刺。
特点: • 效率一般。 • 毛刺不是全部被去除,而有些会折
2、专用的去毛刺工具 根据工件去毛刺强度及难度可选择不同形式。
适合曲面和内孔
砂片
砂带
压铸件去毛刺的方法
一、人工去毛刺
压铸件去毛刺的方法
人工去毛刺
工具方式: •纯人力 •气动 •电动
人工方式特点:
•良品率低,质量得不到保证 •效率低 •人工成本高 •工人易疲劳导致不良上升和安全隐患 •工件靠摩擦折弯(去料的除外),后期可 能反弹
压铸件去毛刺的方法
四、磨粒流加工(AFM)技术
常规的振磨,对于孔洞类的毛刺难于应付,AFM技术对此比较适合: •可处理0.35mm的微孔毛刺。 •无二次毛刺产生。 •流体特性可以处理复杂位置毛刺。
压铸件去毛刺的方法
五、热能去毛刺(TEM)技术
将需要加工的零件置于充满天然气和氧气混合气体的封闭燃烧 腔内,用火花塞 将混合气体点燃,产生高强度热量,这样便 可彻底将毛刺燃烧掉,而对工件本 身不产生任何损害。适合 精度要求高、多孔洞的产品。
人力资源: •手工去毛刺需要大量的人力,单独招这些人成本不低,可以 考虑外包方式。
压铸件去毛刺的方法
二、机器人去毛刺
压铸件去毛刺的方法
机器人去毛刺
原理类似于人工去毛刺,只是将动力变为机器人。 得到编程技术以及力控技术的支持,实现柔性打磨 (压力与速度的变换),机器 人去毛刺优势凸显。
常见冲压质量问题及解决之冲裁件的常见缺陷及原因分析

常见冲压质量问题及解决之冲裁件的常见缺陷及原因分析冲裁件的常见缺陷及原因分析冲裁是利用模具使板料分离的冲压工序。
冲裁件常见缺陷有:毛刺、制件表面翘曲、尺寸超差。
1、毛刺在板料冲裁中,产生不同程度的毛刺,一般来讲是很难避免的,但是提高制件的工艺性,改善冲压条件,就能减小毛刺。
产生毛刺的原因主要有以下几方面:1.1 间隙冲裁间隙过大、过小或不均匀均可产生毛刺。
影响间隙过大、过小或不均匀的有如下因素:a 模具制造误差-冲模零件加工不符合图纸、底板平行度不好等;b 模具装配误差-导向部分间隙大、凸凹模装配不同心等;c 压力机精度差—如压力机导轨间隙过大,滑块底面与工作台表面的平行度不好,或是滑块行程与压力机台面的垂直度不好,工作台刚性差,在冲裁时产生挠度,均能引起间隙的变化;d 安装误差—如冲模上下底板表面在安装时未擦干净或对大型冲模上模的紧固方法不当,冲模上下模安装不同心(尤其是无导柱模)而引起工作部分倾斜;e 冲模结构不合理-冲模及工作部分刚度不够,冲裁力不平衡等;d 钢板的瓢曲度大-钢板不平。
1.2 刀口钝刃口磨损变钝或啃伤均能产生毛刺。
影响刃口变钝的因素有:a 模具凸、凹模的材质及其表面处理状态不良,耐磨性差;b 冲模结构不良,刚性差,造成啃伤;c 操作时不及时润滑,磨损快;d 没有及时磨锋刃口。
1.3 冲裁状态不当如毛坯(包括中间制件)与凸模或凹模接触不好,在定位相对高度不当的修边冲孔时,也会由于制件高度低于定位相对高度,在冲裁过程中制件形状与刃口形状不服帖而产生毛刺。
1.4 模具结构不当1.5 材料不符工艺规定材料厚度严重超差或用错料(如钢号不对)引起相对间隙不合理而使制件产生毛刺。
1.6 制件的工艺性差-形状复杂有凸出或凹入的尖角均易因磨损过快而产生毛刺。
小结:毛刺的产生,不仅使冲裁以后的变形工序由于产生应力集中而容易开裂,同时也给后续工序毛坯的分层带来困难。
大的毛刺容易把手划伤;焊接时两张钢板接合不好,易焊穿,焊不牢;铆接时则易产生铆接间隙或引起铆裂。
电路中如何消除方波跳变时产生的尖刺.doc

电路中如何消除方波跳变时产生的尖刺?解释一:在组合逻辑中,由于门的输入信号通路中经过了不同的延时,导致到达该门的时间不一致叫竞争。
产生毛刺叫冒险。
如果布尔式中有相反的信号则可能产生竞争和冒险现象。
解决方法:一是添加布尔式的(冗余)消去项,但是不能避免功能冒险,二是在芯片外部加电容。
三是增加选通电路。
在组合逻辑中,由于多少输入信号变化先后不同、信号传输的路径不同,或是各种器件延迟时间不同(这种现象称为竞争)都有可能造成输出波形产生不应有的尖脉冲(俗称毛刺),这种现象成为冒险。
解释二:竞争与冒险是数字电路中存在的一种现象。
由于元器件质量和设备工艺已达到相当高的水平,因而数字电路的故障往往是竞争与冒险引起的,所以要研究它们。
在一个复杂的数字电路的设计阶段,就完全预料电路中的竞争与冒险是困难的,有一些要通过实验来检查。
下面将说明组合数字电路中竞争与冒险的基本概念和确定消除它的一些基本方法。
竞争:在组合电路中,信号经由不同的途径达到某一会合点的时间有先有后,这种现象称为竞争。
冒险:由于竞争而引起电路输出发生瞬间错误现象称为冒险。
表现为输出端出现了原设计中没有的窄脉冲,常称其为毛刺。
竞争与冒险的关系:有竞争不一定会产生冒险,但有冒险就一定有竞争。
在组合逻辑中,由于门的输入信号通路中经过了不同的延时,导致到达该门的时间不一致叫竞争。
产生毛刺叫冒险。
如果布尔式中有相反的信号则可能产生竞争和冒险现象。
解决方法:一是添加布尔式的消去项,二是在芯片外部加电容。
当组合逻辑电路存在冒险现象时,可以采取修改逻辑设计,增加选通电路,增加输出滤波等多种方法来消除冒险现象。
当一个门的输入有两个或两个以上的变量发生改变时,由于这些变量是经过不同路径产生的,使得它们状态改变的时刻有先有后,这种时差引起的现象称为竞争(Race)。
竞争的结果若导致冒险或险象(Hazard)发生(例如毛刺),并造成错误的后果,那么就称这种竞争为临界竞争。
液压铝阀块毛刺的主动控制和去除

103中国设备工程C h i n a P l a n t E n g i n e e r i ng中国设备工程 2020.08 (下)液压元件从最初的管式阀发展到板式阀和插装式阀,伴随着液压元件的发展,液压系统集成也相应地有了变化,液压系统集成管式阀只需要按照要求把各种阀用管路连接就可以,但集成板式阀和插装阀就需要用集成阀块来实现各种阀的油路连通,集成各种阀的阀体也变得较为复杂,对制造工艺的要求越来越高,集成阀块的特点是孔系密度大、孔的长径比大、孔规格多、螺纹多、交叉孔多、沟通孔多、阀孔精度高,所以集成阀块就面临如何加工才能满足液压系统要求的问题。
液压系统对集成阀块的主要要求是三个“度”:尺寸精度、表面粗糙度和清洁度。
为了解决漏油和渗油的问题,板式阀和插装阀对安装面有尺寸精度和表面粗糙度的要求;为了解决液压元件卡阀和磨损的问题,对清洁度提出了更高的要求,清洁度最关键的就是清除加工过程中产生的毛刺、切屑及其杂质,于是,在制造过程中如何去除毛刺保证液压阀块的清洁度,成了决定液压产品质量的关键技术。
液压集成铝阀块在机械加工的过程中常常伴随着毛刺和切屑的产生,毛刺和切屑是在刀具和阀体相对运动过程中产生的,在切削力作用下产生晶粒剪切滑移、塑性变形,使材料被挤压、撕裂,导致阀体与面的切割线或孔与孔、孔与螺纹交接处出现的各种尖边、毛边等多余材料和表面极细小的金属颗粒,特别容易产生于如铝合金类延展性好的材质。
液压阀块中毛刺和切屑的存在,轻者损坏零件,重则造成整个设备报废。
因此,加工流程中需要增加工序,以消除毛刺和切屑。
去毛刺和切屑工序的工时约占总加工工时的5%~10%,去毛刺和切屑成本占总加工成本的10%左右,这还没有考虑由于毛刺和切屑造成的损失,由此可见,去毛刺和切屑成为降低成本的重要因素。
1 铝阀块加工工艺流程在液压系统中,铝阀块有很多应用,阀块充当液液压铝阀块毛刺的主动控制和去除于良振 (上海楷液流体技术有限公司,上海 201209)摘要:液压铝阀块在液压系统中广泛应用,阀块中的毛刺和铝屑会对液压系统造成严重危害,控制液压铝阀块的清洁度成为产品质量的关键技术。
- 1、下载文档前请自行甄别文档内容的完整性,平台不提供额外的编辑、内容补充、找答案等附加服务。
- 2、"仅部分预览"的文档,不可在线预览部分如存在完整性等问题,可反馈申请退款(可完整预览的文档不适用该条件!)。
- 3、如文档侵犯您的权益,请联系客服反馈,我们会尽快为您处理(人工客服工作时间:9:00-18:30)。
数字逻辑基础
LOGO
毛刺产生及消除
传播延迟不仅限制电路工作的速度,它们也会在输出端引起不期望的多余跳变。
这些多余的跳变,称为“毛刺”。
⏹这将导致当其中一个信号发生改变时,给信号提供了两条或更多的流过电路的路径,并且其中一条路径的延迟时间比其他路径长。
⏹当信号路径在输出门重组时,这个在一条路径上增加的时间延迟会产生毛刺。
毛刺产生及消除
当一个输入信号通过两条路径或多条路径驱动的一个输出,其中一条路径有反相器而另外一条没有时,通常会出现非对称的延迟。
包含反相器会产生毛刺的组合逻辑结构
毛刺产生及消除
毛刺生成逻辑结构和时序分析
毛刺产生及消除
当一个输入用于两个积项(或者和之积方程式的两个和
项),以及反相器在其中一项中有而另一项中没有时,将会产生毛刺。
在该卡诺图中,两个圆圈决定了最小逻辑表达式。
B·C 独立于A 。
当B 变化时,两种不同的积项必须在输出时重组以保持输出为高,
这就是引起毛刺的原因。
产生毛刺的电路
毛刺
该设计保存在\eda_verilog\glitch 目录下
毛刺产生及消除
电路产生毛刺可以通过它原理图、卡诺图或者是逻辑等式验证。
⏹在原理图中,输入后面有多条到达输出的路径,并且其中一条有反相器而其他路径没有就会产生毛刺。
⏹在卡诺图中,假如画的圈是相邻的但不重叠,那么那些没有被圈圈住的相邻项将有可能产生短时脉冲干扰。
毛刺产生及消除
可能的毛刺没有毛刺没有毛刺
毛刺产生及消除
对于毛刺的产生,一个逻辑电路必须对驱动所有输入到适当的水平的耦合变量“很敏感”,这样就只有耦合变量可以影响输出。
在一个SOP 电路中,这意味着除了耦合输入外的所有的输入必须被驱动到“1”,这样它们对第一级与门的输出就不会产生影响。
这种情况为逻辑电路消除毛刺提供了一个直观的方法:将所有多余的输入信号组合到一个新的第一级的逻辑输入(例如,SOP 电路的与门),并将这个新增加的门添加到电路中。
毛刺产生及消除
逻辑表达式:
耦合项是A ,多余项可以组合成项的形式,将这项添加到电路组成方程式。
原等式是最小逻辑表达式,为了不产生毛刺,在最小逻辑表达式中添加了一个冗余项。
毛刺产生及消除
原始的SOP 表达式画圈并没有重叠,这就是毛刺潜在的特点。
当增加了冗余项的圈时,每个圈至少重叠其他一项,那就不会产生毛刺。
消除毛刺的电路
添加一项
该设计保存在\eda_verilog\glitch_remove 目录下。