冲压模具课程设计——盖第一次拉深模具设计
冲压模课程设计--微电机外壳首次拉深模具设计

课题:微电机外壳首次拉深模具设计摘要本次设计是微电机外壳冲压模具设计,根据零件的尺寸、材料、技术要求等,分析零件的成形工艺、制订工艺方案、设计模具结构、毛坯尺寸计算、工艺参数计算。
其中工艺参数计算主要有确定排样和裁板,计算冲压压力,初选压力机,计算凸、凹模刃口尺寸和公差,最后设计选用零、部件,对压力机进行校核。
最后绘制模具装配总图。
在结构设计中,主要对凸模、凹模、凸凹模、定位制件、卸料与出件装置、模架、冲压设备、紧固件等进行了设计,对于部分零部件选用的是标准件,这样可以节约时间课程、难度等,并且在结构设计的同时,对部分零部件进行了加工工艺分析。
此次的微电机外壳工序为落料→拉深(带压边4次)→冲孔+修边→切口。
主要说明的是首次拉深模的设计,解决首次拉深的计算问题同时对相关的模具的零件给以详细的设计。
生成装配工程图和相关的零件图,最终完成这次课程设计。
关键词:落料首次拉深单排修边切口目录第1章概论 (1)1.1冲压模具在制造业的地位 (1)第2章工艺方案分析及确定 (2)2.1 冲压件工艺分析 (2)2.2冲压工艺方案的确定 (3)第 3章拉深件工艺计算 (4)3.2排样 (4)3.3 各工序尺寸计算 (5)3.4 压力计算与设备选择 (7)3.5拉深模工作零件设计与计算 (8)3.6弹性装置的选用与计算 (9)第4章模具结构的确定 (10)4.1 模具的形式 (10)4.2 定位装置 (10)4.3 导向零件 (11)4.4 模架 (11)第5章模具零件加工工艺过程 (11)第6章模具结构图 (13)第7章首次拉深模具装配图、零件图(见附图) (15)第8章总结 (16)第9章参考文献 (17)第1章概论1.1冲压模具在制造业的地位由于冷冲压加工具节省材料、良好的互换性、成产效率高、操作简单、可以加工薄壁形状复杂表面质量好刚性好的零件、生产成本低的优点。
因此在生产中得到广泛应用,在汽车、拖拉机、电机、电器、仪表和日用生产品种,已占据十分重要的低位。
课程设计之拉深模
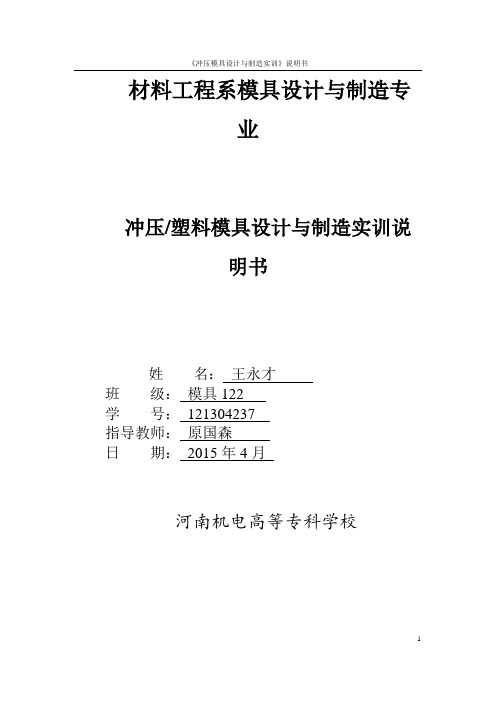
材料工程系模具设计与制造专业冲压/塑料模具设计与制造实训说明书姓名:王永才班级:模具122学号:121304237指导教师:原国森日期:2015年4月河南机电高等专科学校目录第一章绪论1.1 国内外模具的现状和发展趋势1.2 深圆筒拉深件模具设计与制造方面第二章圆筒冲压工艺的分析2.1 拉深件工艺分析2.2 拉深工艺计算和工艺方案2.2.1 工艺方案的确定2.2.2 计算毛坯尺寸2.2.3 确定是否用压边圈2.2.4 拉深次数的确定2.2.5 排样及相关的计算2.3 压力、压力中心计算及压力机的选用2.3.1 压力计算2.3.2 压力机的选用第3章模具的结构设计3.1 模具工作部分的计算3.1.1 拉深模的间隙3.1.2 拉深模的圆角半径3.1.3 凸凹模工作部分的尺寸和公差3.1.4 选用模架、确定闭合高度及总体尺寸3.2 模具零件的结构设计3.2.1 拉深凹模3.2.2 拉深凸模3.2.3 打料块3.2.4 压边圈3.2.5 导柱、导套3.2.6 其他零件3.3模具总装图第一章绪论1.1模具设计的重要性与现状目前我国模具工业与发达国家相比还相当落后。
主要原因是我国在模具标准化,模具制造工艺及设备等方面与工业发达国家相比差距很大。
我国模具近年来发展很快,据不完全统计,2003年我国模具生产厂点约有2万多家,从业人员约50多万人,2004年模具行业的发展保持良好势头,模具企业总体上订单充足,任务饱满,2004年模具产值530亿元。
进口模具18.13亿美元,出口模具4.91亿美元,分别比2003年增长18%、32.4%和45.9%。
进出口之比2004年为3.69:1,进出口相抵后的进净口达13.2亿美元,为净进口量较大的国家。
在2万多家生产厂点中,有一半以上是自产自用的。
在模具企业中,产值过亿元的模具企业只有20多家,中型企业几十家,其余都是小型企业。
近年来,模具行业结构调整和体制改革步伐加快,主要表现为:大型、精密、复杂、长寿命中高档模具及模具标准件发展速度快于一般模具产品;专业模具厂数量增加,能力提高较快;"三资"及私营企业发展迅速;国企股份制改造步伐加快等虽然说我国模具业发展迅速,但远远不能适应国民经济发展的需要。
冲压工艺及模具设计经教材-冲压工艺及模具设计-第8章拉深模具设计

8.6.6 压力机选择
根据标称压力,滑块行程,及模具闭合高度,确定选择型号 为JC23—35型开式双柱可倾压力机。
校核过程如下:确定所选型号压力机的滑块许用负荷图,设 备参数和模具工艺力确定模具工作过程中对应的落料拉深力曲 线,
若落料拉深力曲线处于许用负荷曲线之下,则所选设备符合 工作要求;
若落料拉深力曲线超出许可范围(见图8.25),则需选择标称 压力更大型号的压力机,继续以上校核过程。
凸缘处的圆角半径满足拉深工艺性要求;尺寸为IT12级, 08 钢拉深性能较好。
8.6.2 工艺方案确定
1. 计算坯料直径
根据零件尺寸查表7-5得切边余量; 凸缘直径59.8mm。
8.6.2 工艺方案确定 1. 计算坯料直径; 2. 判断可否一次拉深成形; 3. 确定首次拉深工序件尺寸; 4. 计算以后各次拉深的工序件尺寸 5. 工艺方案
8.3.4 落料拉深压形模
图8.17 落料拉深压形复合模 落料拉深压形复合模的上模下行时,落料拉深凸凹模与落料凹模完成落料。 上模继续下行,落料拉深凸凹模与拉深凸模完成拉深。在上模行程的终了阶段, 压形凸模和拉深压形凸凹模镦压制件,进行压形。
8.3.5 落料拉深冲孔模
图8.18 落料拉深冲孔复合
8.3.1 凸缘制件的落料拉深模
图8.13 带凸缘制件落料拉深 复合 模
带凸缘零件的落料拉深复合模如图8.13所示。这类模具 要注意设计成先落料后拉深,因此拉深凸模低于落料凹模。
8.3.2 球形制件落料拉深模
图8.14 球形制件落料拉深复合 模
球形零件落料拉深复合模。落料拉深凸凹模的外缘是落料凸模 刃口,内孔是拉深凹模。模具采用固定卸料板卸料。为减小拉深时 起皱趋势,在落料拉深凸凹模的凸模刃口处设计了一个锥面。
拉深模具设计说明书
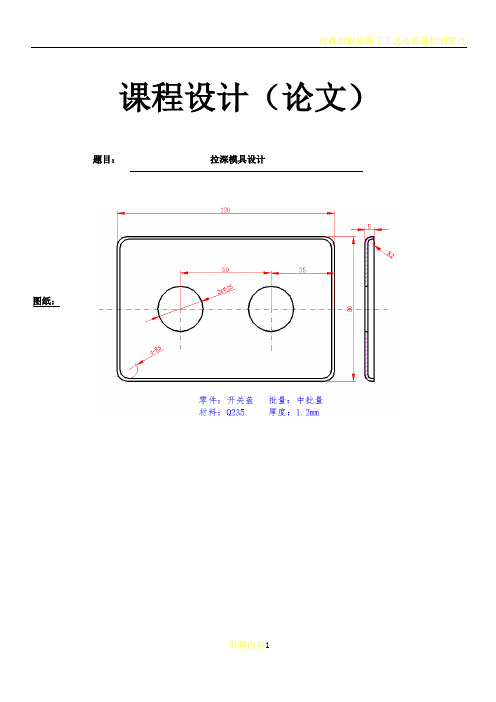
课程设计(论文)题目:拉深模具设计图纸:目录课程设计(论文) (1)前言 (4)1. 冲裁件工艺性分析 (5)1.1材料选择 (5)1.2工件结构形状 (5)1.3尺寸精度 (5)2. 冲裁工艺方案的确定 (5)3. 模具结构形式的确定 (6)4.模具总体结构设计 (6)4.1模具类型的选择 (7)4.2操作与定位方式 (7)4.3部分零部件的设计 (7)4.3.1凸模的设计 (7)4.3.2卸料部分的设计 (7)4.3.3推件装置的设计 (8)4.3.4模架的设计 (8)4.3.5模架的选用 (9)4.3.6上、下模座的选用 (9)4.4工作零件材料的选用 (9)5.模具工艺参数确定 (9)5.1排样设计与计算 (9)5.2搭边值的确定 (10)5.3材料利用率的计算 (10)5.4凸、凹模刃口尺寸的计算 (11)5.4.1刃口尺寸计算的基本原则 (11)5.4.2刃口尺寸的计算 (11)6.计算冲压力与压力机的初选 (12)F的计算 (13)(3)顶件力q2F+1q F+2q F (13)根据模具结构总的冲压力F=P7. 模具压力中心的确定 (13)8.冲压设备的选择 (14)通过校核,选择开式双柱可倾式压力机J23—80能满足使用要求。
其主要技术参数如下: (14)9.模具零件图 (14)10.模具总装图 (15)模具总装图的零件间的装配配合要求按下表选用: (16)总结 (18)参考文献 (20)前言冲压加工是现代机械制造业中先进高效的加工方法之一。
冲压加工的应用十分广泛,不仅可以加工金属材料,而且可以加工非金属材料。
在现代制造业,比如汽车、拖拉机、农业机械、电机、电器、仪表、化工容器、玩具以及日常生活用品的生产方面,都占有十分重要的地位。
当然,冲压加工在我国也存在着一些问题和不足。
如机械化、自动化程度低、生产集中度低、冲压板材自给率不足、品种规格不配套、科技成果转化慢、先进工艺推广慢、专业人才缺乏、大、精模具依赖进口等,因此,我们将还有很长的路要走。
冲压工艺与模具设计第4章 拉深
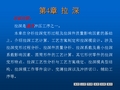
2.筒壁的拉裂
主要取决于:
一方面是筒壁传力区中的拉应力; 另一方面是筒壁传力区的抗拉强度。 当筒壁拉应力超过筒壁材料的抗拉强度时,拉深件就会在 底部圆角与筒壁相切处——“危险断面”产生破裂。
防止拉裂:
一方面要通过改善材料的力学性能,提高筒壁抗拉强度;
另一方面通过正确制定拉深工艺和设计模具,降低筒壁所 受拉应力。
1.等重量法 :已有拉深件样品时,使用等重量法来求毛 坯直径会非常方便。 2.等体积法 :适用于变薄拉深件。
3.等面积法:不变薄拉深工序用来计算毛坯尺寸的依据。
4.3.2 修边余量
修边余量:拉深件口部或凸缘周边不整齐;特别是经过多 次拉深后的制件,口部或凸缘不整齐的现象更为显著;因 此必须增加制件的高度或凸缘的直径,拉深后修齐增加 的部分即为修边余量。
4.凸模圆角部分 5.筒底部分 坯料各区的应力与应变是很不均匀的。
拉深过程中零件应力与应变状态
4.2.3 拉深变形过程中凸缘变形区的应力分布
圆筒件拉深时凸缘
变形区应力分布图
4.2.4 拉深件主要质量问题
拉深过程中的质量问题:Fra bibliotek主要是凸缘变形区的起皱和筒壁传力区的拉裂。
凸缘区起皱: 由于切向压应力引起板料失去稳定而产生弯曲; 传力区拉裂: 由于拉应力超过抗拉强度引起板料断裂。
毛坯尺寸的计算必须将加上了修边余量后的制件尺寸作 为计算的依据。 表4-5为无凸缘圆筒件的修边余量; 表4-6为带凸缘圆筒件的修边余量。
4.3.3 简单旋转体拉深件毛坯尺寸计算
1.将拉深件划分为若干个简单的几何体; 2.分别求出各简单几何体的表面积; 3.把各简单几何体面积相加即为零件总面积; 4.根据表面积相等原则,求出坯料直径。
课程设计带凸缘筒形件首次拉深的拉深模设计
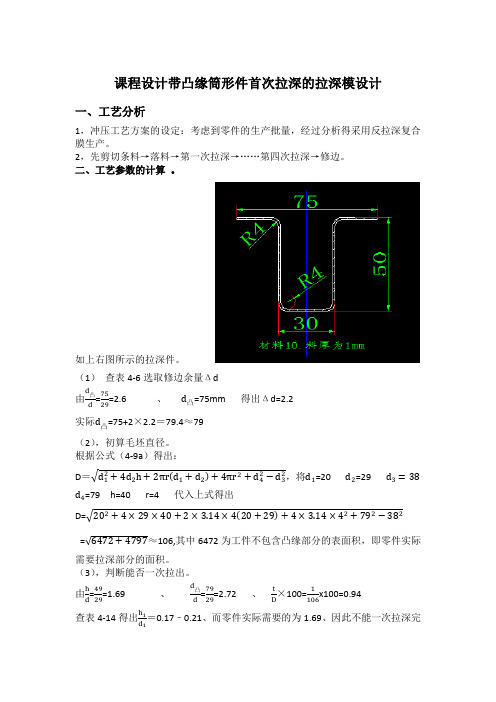
课程设计带凸缘筒形件首次拉深的拉深模设计一、工艺分析1,冲压工艺方案的设定:考虑到零件的生产批量,经过分析得采用反拉深复合膜生产。
2,先剪切条料→落料→第一次拉深→……第四次拉深→修边。
二、工艺参数的计算 。
如上右图所示的拉深件。
(1) 查表4-6选取修边余量Δd 由d 凸d=7529=2.6 、 d 凸=75mm 得出Δd=2.2实际d 凸=75+2×2.2=79.4≈79 (2),初算毛坯直径。
根据公式(4-9a )得出:D =√d 12+4d 2h +2πr (d 1+d 2)+4πr 2+d 42−d 32,将d 1=20 d 2=29 d 3=38d 4=79 h=40 r=4 代入上式得出D=√202+4×29×40+2×3.14×4(20+29)+4×3.14×42+792−382 =√6472+4797≈106,其中6472为工件不包含凸缘部分的表面积,即零件实际需要拉深部分的面积。
(3),判断能否一次拉出。
由h d =4929=1.69 、d 凸d=7929=2.72 、 t D ×100=1106x100=0.94查表4-14得出h1d 1=0.17﹣0.21、而零件实际需要的为1.69、因此不能一次拉深完成。
(4),计算拉深次数及各工序的拉深直径。
,因此需要用试凑法计算利用表4-14来进行计算,但由于有两个未知数m和d td1拉深直径。
下面用逼近法来确定第一的拉深直径。
的值为由于实际拉深系数应该比极限拉伸系数稍大,才符合要求,所以上表中d td11.5、1.6、1.7的不合适。
因为当d t的值取1.4的时候,实际拉深系数与极限拉深系数接近。
故初定第一次d1拉深直径d1=56.因以后各次拉深,按表4-8选取。
故查表4-8选取以后各次的拉深系数为当m2=0.77时d2=d1×m2=56×0.77=43mm当m2=0.79时d3=d2×m3=43×0.79=34mm当m3=0.81时d4=d3×m4=34×0.81=27mm<29mm因此以上各次拉程度分配不合理,需要进行如下调整。
拉深模设计实例(课程设计)(毕业设计)
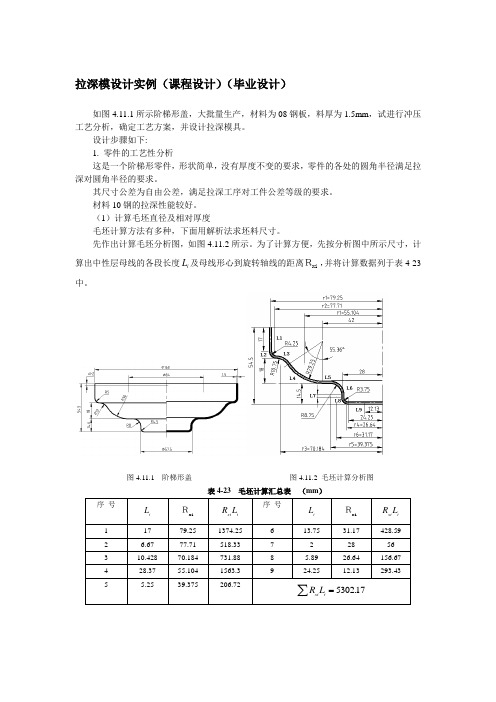
拉深模设计实例(课程设计)(毕业设计)如图4.11.1所示阶梯形盖,大批量生产,材料为08钢板,料厚为1.5mm ,试进行冲压工艺分析,确定工艺方案,并设计拉深模具。
设计步骤如下:1. 零件的工艺性分析这是一个阶梯形零件,形状简单,没有厚度不变的要求,零件的各处的圆角半径满足拉深对圆角半径的要求。
其尺寸公差为自由公差,满足拉深工序对工件公差等级的要求。
材料10钢的拉深性能较好。
(1)计算毛坯直径及相对厚度毛坯计算方法有多种,下面用解析法求坯料尺寸。
先作出计算毛坯分析图,如图4.11.2所示。
为了计算方便,先按分析图中所示尺寸,计算出中性层母线的各段长度i L 及母线形心到旋转轴线的距离xi R,并将计算数据列于表4-23中。
图4.11.1 阶梯形盖 图4.11.2 毛坯计算分析图表4-23 毛坯计算汇总表 (mm )根据公式(4-11)计算得毛坯直径:D 206mm坯料的尺寸也可以根据拉深前后表面积不变,借助pro/E 等CAD 软件求出。
过程如下:(1) 先在pro/E 软件中进行造型, 如图4.11.3所示,因为零件的内、外表面积的不同,造型过程要注意,把零件的中间层设为实体的外表面或内表面,以便于测量;(2) 复制曲面,点击菜单中分析→ 测量;(3) 选择类型为“面积”,曲线/边为“面组”,投影方向选择为“无”,即可计算出被选中曲面的表面积,如图4.11.4所示。
由图4.11.4可知,零件的表面积A=33434.8mm 2,坯料的直径:206mm D ==≈计算相对厚度: 1.52060.72%t D == (2)确定拉深次数54.557.50.95n h d ==;根据公式(4-21),查表4-11,得拉深次数为2。
(3)计算第一次拉深工序尺寸 为了计算第一次拉深工序尺寸,利用等面积法,求出第一次拉深后工序件的直径和深度。
由于参与第二次拉深变形的区域是从图4.11.2中的L 5开始,因此以L 5开始计算面积,并求出相应的直径。
冲压模具课程设计——盖第一次拉深模具设计
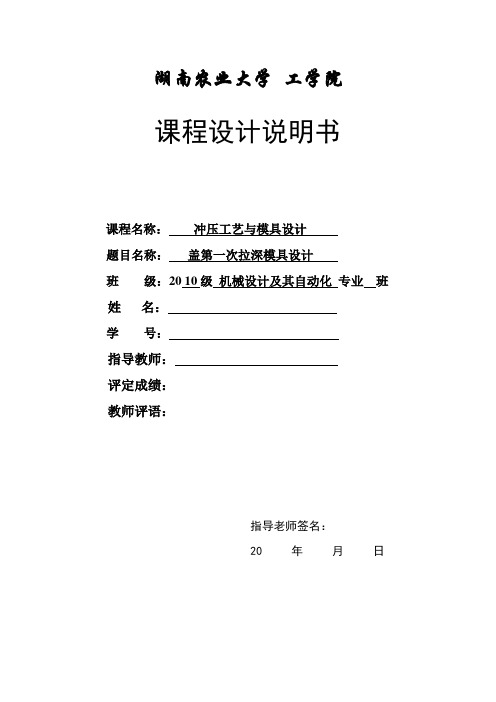
三、拉深工艺方案的确定............................2
四、主要设计计算....................................2
4.1毛坯尺寸计算. ................. ......2
——拉深凹模的圆角半径,mm,此处取
代入数据计算得:
4.5.6总冲压力的计算
故总冲裁力为:
4.6压力中心的确定
由于该零件既关于X轴对称,也关于Y轴对称,所以其压力中心,就在冲压工件的几何中心,即圆心上。
4.7工作零件刃口尺寸的计算
4.7.1拉深刃口尺寸计算
对于拉深部分,工件未注公差,按IT12级计,则拉深件尺寸为 mm。
加工工件料厚1mm,相对单薄,冲裁后箍在凸模上的工艺废料用弹压性的卸料板卸料。工件采用下出件方式,即压入凹模内的工件利用凹模下方的顶件块顶出工件。
6.3导向方式的选择
该模具的位置精度要求比较高,最好采用四导柱模架,但考虑到该模具较小,所以采用中间导柱模架。
6.5弹性材料的选择与计算
为了得到较平整的工件,此模具采用弹压式卸料结构,使条料在拉深过程中始终处在一个稳定的压力之下,从而改善毛坯的稳定性,避免材料在切向应力的作用下起皱。卸料采用橡胶为弹性元件。
生产批量:大批量
材料:Q235
材料厚度:1mm
设计要求:第一次拉深模的设计
二、冲压件的工艺分析
2.1冲压件的结构分析
此工件的工序包括:落料和拉深,其中第一次的拉深模的设计的成形工件如图2-1所示,材料为Q235,料厚为2mm,具有良好的冲裁性能。工件结果简单,盖的外沿尺寸为 69mm,为未注公差,属于自用尺寸,Q235钢材的力学性能: , , 。
- 1、下载文档前请自行甄别文档内容的完整性,平台不提供额外的编辑、内容补充、找答案等附加服务。
- 2、"仅部分预览"的文档,不可在线预览部分如存在完整性等问题,可反馈申请退款(可完整预览的文档不适用该条件!)。
- 3、如文档侵犯您的权益,请联系客服反馈,我们会尽快为您处理(人工客服工作时间:9:00-18:30)。
7.1.2拉深凸模尺寸
拉深凸模的基本结构由安装固定部分和工作部分两大部分组成,凸模和凸模固定板的配合间隙均为H7/m6,拉深圆孔凸模结构尺寸为:
(7-2)
式中: ——凸模固定板的厚度,一般为凹模厚度的60%-80%,此次取30mm;
——卸料板的厚度,此处取18mm;
——导料板的厚度,此处取10mm;
凸、凹模的制造公差可采用IT8级精度,查表可得 。
拉深凸模和凹模的单边间隙查表按 ,则可求得拉深凸模和凹模的刃口尺寸为:
五、冲压设备的选择
5.1拉深压力机标称压力的确定
为使压力机能安全工作,取 ,故选型号为JC23-35开式双柱固定台式压力机。其主要技术参数如下表5-1所示:
表5-1
规格
数值
规格
数值
(4-5)
式中: ——卸料力系数,查表可得
代入数据计算得:
4.5.3顶件力 的计算
的计算按下式公式计算:
(4-6)
式中: ——卸料力系数,查表可得
代入数据计算得:
4.5.4拉深力 的计算
对于圆筒形件首次拉深的拉深力 为:
(4-7)
式中: ——拉深力,N
d——拉深工序件直径,mm
t——板料的厚度,mm
图2-1盖
三、冲压工艺的确定
该工件为圆形拉深件,拉深高度不大。工件材料为Q235钢,易于拉深成形。出于本设计任务的要求,采用首次拉深模对工件进行加工。经综合分析论证,采用落料、拉深模,一套模具完成此工件的第一次拉深模的加工。
四、主要设计计算
4.1毛坯尺寸计算
该工件为无凸缘圆筒形件,根据等面积原则,用解析法求毛坯直径。如图4-1所示,
湖南农业大学 工学院
课程设计说明书
课程名称:冲压工艺与模具设计
题目名称:盖第一次拉深模具设计
班 级:2010级机械设计及其自动化专业班
姓 名:
学号:
指导教师:
评定成绩:
教师评语:
指导老师签名:
20 年 月 日
一、设计任务书............................................. 1
——增加长度0.5mm,作为首次刀磨量;
——橡胶的装配高度;
t——材料的厚度,为1mm;
代入数据计算得:
,去通气孔的尺寸为 ,则凸模的结构尺寸如下:
图7-2 凸模
7.2工作零件力学性能的校核
冲压力学性能校核主要是凸模的断面接触应力 和凸模失稳前的最大长度 。
7.2.1承压能力的校核
凸模的承压应力: (7-3)
——拉深件材料的抗拉刚度,其中 MPa,此处取
K——修正系数,与拉深系数有关,此处取0.5
代入数据计算得:
4.5.5压边力 的计算
在模具设计师,压料力可按下列经验公式计算:
圆筒形件首次拉深 (4-8)
式中: ——压料力,N
p——单位面积压料力,MPa,此处取p=2.5MPa
D——坯料直径,mm
d——拉深工序件的直径,mm
4.5冲压力的计算..............5
4.5.1冲裁力的计算..............5
4.5.2卸料力的计算..............5
4.5.3顶件力的计算..............6
4.5.4拉深力的计算..............6
4.5.5压边力的计算..............6
6.4弹性材料的选择与计算.............. 8
6.4.1弹性卸料板上橡胶高度的计算.............. 8
6.4.2顶杆上的橡胶高度的计算..............9
七、主要零部件的设计.................... ...............9
7.1工作零件.............9
7.4卸料零件的设计..............11
7.5模架及其它部件..............11
7.6模具闭合高度校核..............12
7.7模具安装尺寸校核..............12
八、模具总装图.........................12
九、模具工作过程......................................13
加工工件料厚1mm,相对单薄,冲裁后箍在凸模上的工艺废料用弹压性的卸料板卸料。工件采用下出件方式,即压入凹模内的工件利用凹模下方的顶件块顶出工件。
6.3导向方式的选择
该模具的位置精度要求比较高,最好采用四导柱模架,但考虑到该模具较小,所以采用中间导柱模架。
6.5弹性材料的选择与计算
为了得到较平整的工件,此模具采用弹压式卸料结构,使条料在拉深过程中始终处在一个稳定的压力之下,从而改善毛坯的稳定性,避免材料在切向应力的作用下起皱。卸料采用橡胶为弹性元件。
4.5.6总冲压力的计算..............6
4.6压力中心的确定..............7
4.7工作零件刃口尺寸的计算..............7
4.7.1拉深刃口尺寸计算..............7
五、冲压设备的选择及拉深功的计算...................................7
生产批量:大批量
材料:Q235
材料厚度:1mm
设计要求:第一次拉深模的设计
二、冲压件的工艺分析
2.1冲压件的结构分析
此工件的工序包括:落料和拉深,其中第一次的拉深模的设计的成形工件如图2-1所示,材料为Q235,料厚为2mm,具有良好的冲裁性能。工件结果简单,盖的外沿尺寸为 69mm,为未注公差,属于自用尺寸,Q235钢材的力学性能: , , 。
分别把上式代入可计算得:D 88.688mm,取D=89mm
(3)确定是否需要压边圈:
根据坯料相对厚度: (4-2)
式中 t —坯料厚度,mm
D—毛坯直径,mm
所以,需要压边圈。
4.2确定拉深次数
根据工件的相对高度(h/d)和坯料的相对厚度( )的大小查表确定拉深次数。
根据相对厚度查表确定出圆筒形件(带压边圈)极限拉深系数 =0.50~0.53,而工件的拉深系数为d/D=69/89=0.78> ,则可一次拉成。
5.1拉深压力机标称压力的确定..............7
5.2拉深功的计算.............. 8
六、模具结构选择.............................8
6.1模具类型的选择.............. 8
6.2卸料、出件方式的选择.............. 8
6.3导向方式的选择.............. 8
7.1.1拉深凹模尺寸..............9
7.1.2拉深凸模尺寸..............10
7.2工作零件力学性能的校核..............11
7.2.1承压能力的校核..............11
7.2.2稳定性的校核..............11
7.3固定零件..............11
十、总结......................................14
参考文献................................14
盖第一次拉深模设计
学 生:曾志平
(湖南农业大学工学院机械10-4班级,学号************)
一、设计任务书
图1-1盖
零件名称:盖
4.5冲压力的计算
4.5.1冲裁力F的计算
用一般的平刃冲裁是,其冲裁力F可按下式计算:
(4-4)
式中:F——冲裁力,N;
K——安全系数,K=1.3;
t——板料厚度,mm;
——材料的抗剪强度,MPa,Q235钢 ,取 ;
L——冲裁周边的总长,mm;
代入数据计算得:
4.5.2卸料力 的计算
的计算按下式公式计算:
6.5.1弹性卸料板上的橡胶高度计算
橡胶的自由高度: (6-1)
式中 —橡胶的自由高度,mm;
—工作行程与模具修磨量或调整量(4~6mm)之和,mm, 。
代入数据计算可得: ,取自由高度
橡胶的装配高度: (6-2),取装配高度
6.5.2顶杆上的橡胶高度计算
橡胶的自由高度:
式中 —橡胶的自由高度,mm;
4.3凸、凹模的圆角半径
4.3.1凹模圆角半径
第一次拉深的凹模圆角半径可按以下经验公式计算:
(4-3)
式中: ——凹模圆角半径;
D——坯料直径;
d——凹模内径;
t——材料厚度;
代入数据可得:
4.3.2凹模圆角半径
一般 ,单次拉深或多次拉深的第一次拉深的可取:
4.4排样方式的确定及其计算
由于首次拉深拉入凹模的材料面积比零件实际需要的面积多5%,即要对坯料的直径进行修正。即 ,则修正后的坯料直径D 92mm。考虑到要使操作方便,则采用单排排样的方法,如图4-2所示;
二、冲压件工艺性分析...................................1
三、拉深工艺方案的确定............................2
四、主要设计计算....................................2
4.1毛坯尺寸计算. ................. ......2
公称压力
350
工作台尺寸
前后
380
滑块行程
130
左右
610
滑块行程次数
50
工作台孔尺寸
前后
200
最大封闭高度
280
左右