铁水预处理工艺方法及原理
铁水预处理

计算中心
王丽 丽
8 铁水预处理
铁水预处理是指铁水兑入炼钢炉之前进行的各种处理。 铁水预处理是指铁水兑入炼钢炉之前进行的各种处理。 普通铁水预处理包括:铁水脱硫、铁水脱硅和铁水脱磷。 普通铁水预处理包括:铁水脱硫、铁水脱硅和铁水脱磷。 8.1 铁水预脱硫 脱硫剂:石灰粉(CaO)、电石粉( )、电石粉 和金属镁。 1、脱硫剂:石灰粉(CaO)、电石粉(CaC2)和金属镁。 石灰粉: 1)石灰粉: 2CaO(S)+ [S] + 1/2[Si] =(CaS)(S) + 1/2(Ca2SiO4) ) 电石粉: 2)电石粉: CaC2(S)+ [S] ==(CaS)(S) + 2[C] ) 2(S) 电石粉需要以惰性气体密封保存和运输。 电石粉需要以惰性气体密封保存和运输。 金属镁: 3)金属镁: Mg+ [S]=MgS(S) 金属镁活性高,极易氧化,易燃易爆, 金属镁活性高,极易氧化,易燃易爆,所以镁粒必须表面 钝化后才能安全的运输、储存和使用。 钝化后才能安全的运输、储存和使用。
镁在铁水温度下与硫有较强的亲和力。特别是在低温下 镁在铁水温度下与硫有较强的亲和力。 镁脱硫效率极高。用镁脱硫铁水温降小, 镁脱硫效率极高。用镁脱硫铁水温降小,渣量及铁损均 少且不损坏处理罐内衬,也不影响环境。 少且不损坏处理罐内衬,也不影响环境。因而铁水包喷 镁脱硫工艺获得了迅猛的发展。 镁脱硫工艺获得了迅猛的发展。 镁价格昂贵,保存时须防止吸潮。 镁价格昂贵,保存时须防止吸潮。 2、脱硫方法——喷吹法 脱硫方法——喷吹法 —— 此法是用喷枪以惰性气体为载体, 此法是用喷枪以惰性气体为载体,将脱硫剂与气体混合 吹入铁水深部, 吹入铁水深部,以搅动铁水与脱硫剂充分混合的脱硫方 该法可以在鱼雷罐车或铁水包内处理铁水。 法。该法可以在鱼雷罐车或铁水包内处理铁水。
炼钢第二讲(1)铁水预处理

17
脱磷剂
氧化剂――――氧气、氧化铁、轧钢铁皮、连铸铁皮等 将铁水中的磷氧化 固定剂――――CaO,Na2CO3; 5NaCO3+4[P]=5(Na2O)+2(P2O5)+5C
3(Na2O)+(P2O5)=(3NaO· P2O5)
使磷稳定地结合在炉渣中 助熔剂――――CaF2,CaCl2。 生产低熔点的化合物,溶于渣中。 18
搅拌能 低 高
供氧 速率 低 高
氧气 比率 低 高
废钢比 低 高
建设投资 低 高
24
脱硫
脱硫原理
钢铁冶炼脱硫,就是要形成稳定的硫化物,并
能与钢或铁水顺利分离。
脱硫基本反应方程式如下:
Mg(g)+[S]=MgS(s) ΔGΘ=- 427367+180.67 T
25
脱硫剂
苏打灰(Na2CO3) 石灰粉(CaO) 电石粉(CaS) 金属镁
铁水“三脱”工艺
铁水三脱预处理( ORP法 )工艺流程
50
49
总用量大约为吨铁水35公斤。配比:CaO42%-Fe2O346%-CaF212%。
预脱磷方法
在高炉出铁沟或出铁槽内进行脱磷; 在铁水包或鱼雷罐车中进行预脱磷; 在专用转炉内进行铁水预脱磷。
19
铁水包喷吹法 优点: 铁水罐混合容易, 浸入 反应动力学条件好 缺点:
吹炼时间长,温降大 渣多
被铁水内部进行脱硫反应,从而达到脱硫的目的。
优点:脱硫效率高、脱硫剂耗量少、金属损耗低等。
38
非卷入型机械搅拌法
特点:在钢包内只设一个简单
的倒T字形耐火材料搅拌棒, 旋转搅拌棒使脱硫剂与铁水混合
进行脱硫。但脱硫时间长,
铁水预处理工艺
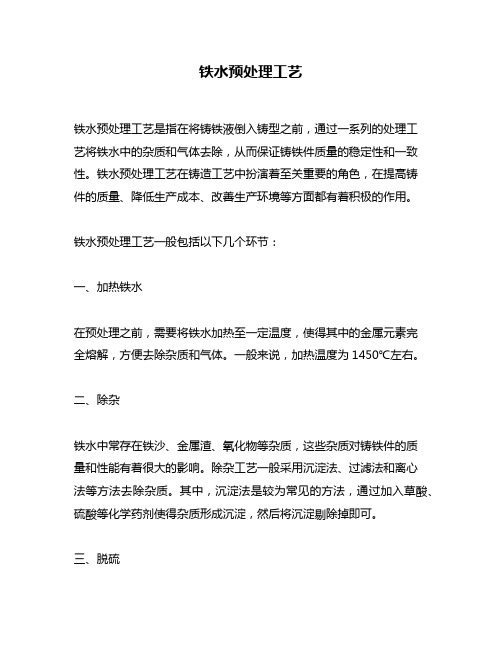
铁水预处理工艺铁水预处理工艺是指在将铸铁液倒入铸型之前,通过一系列的处理工艺将铁水中的杂质和气体去除,从而保证铸铁件质量的稳定性和一致性。
铁水预处理工艺在铸造工艺中扮演着至关重要的角色,在提高铸件的质量、降低生产成本、改善生产环境等方面都有着积极的作用。
铁水预处理工艺一般包括以下几个环节:一、加热铁水在预处理之前,需要将铁水加热至一定温度,使得其中的金属元素完全熔解,方便去除杂质和气体。
一般来说,加热温度为1450℃左右。
二、除杂铁水中常存在铁沙、金属渣、氧化物等杂质,这些杂质对铸铁件的质量和性能有着很大的影响。
除杂工艺一般采用沉淀法、过滤法和离心法等方法去除杂质。
其中,沉淀法是较为常见的方法,通过加入草酸、硫酸等化学药剂使得杂质形成沉淀,然后将沉淀剔除掉即可。
三、脱硫铁水中含有一定量的硫,会影响铁水的流动性、凝固分析等性能。
脱硫工艺主要采用氧气吹炼法,将氧气引入铁水中,使得硫气氧化成SO2并排出,从而达到脱硫的目的。
四、脱碳铸铁中碳含量的多少与铁水中碳含量有着密切的关系,因此脱碳工艺对于决定铸铁件的硬度和韧性有着重要的作用。
脱碳工艺一般采用灌碳剂或者双氧水等方法,将其中的碳元素去除掉。
五、脱气铁水中通常还含有大量的气体,如氢、氧、氮等,这些气体都会在铸造过程中释放出来,导致铸件内部产生气孔、夹杂等缺陷。
因此,脱气工艺也是铁水预处理中不可或缺的一个环节。
脱气一般采用真空除气、加压除气等方法,将其中的气体去除掉。
铁水预处理工艺在现代铸造工业中已经得到广泛应用,能够显著提高铸铁件的质量和性能,减少铸件的废品率和生产成本,对于推动铸造行业的发展和升级有着重要的意义。
铁水预处理的目的以及预处理工艺法

铁水预处理的目的以及预处理工艺法铁水预处理的目的铁水预处理是指铁水在进入转炉炼钢之前,为了去除某些有害成分或回收有益成分的处理过程。
针对炼钢而言,主要是使铁水中的硅、硫、磷含量降低到所要求的范围,以简化炼钢过程,提高钢材的质量。
在铁和钢的生产过程中,硫之所以成为主要脱除或控制的元素之一,是因为它对钢的性能有着多方面的影响。
(1)热脆:硫在铁液中以FeS形式存在,1600℃硫在铁液巾能无限溶解,但其溶解度随温度的降低而减小,在固态铁中的溶解度很小。
在钢液凝固过程中,低熔点(1193℃)的FeS将浓聚于液相中,并将与Fe形成低熔点共晶(988℃),最后凝固时形成网状组够分布于铁晶粒周界上。
当钢在热加工的加热过程中,温度超过1100℃左右时,富集于晶界的低熔点硫化物将使晶界成脆性或熔融状态,在轧制或锻造时,即出现裂纹,这种现象称为“热脆”。
(2)疲劳断裂:钢材的疲劳断裂是由于使用过程中钢材内部显微裂纹不断扩展的结果。
当硫含量偏高时产生晶界裂纹,这就是由于硫高而导致疲劳断裂的原因。
(3)力学性能:硫化物夹杂对钢材力学性能的影响,主要是由于硫化物夹杂在钢材加工中易变成长条状和片状,因此使钢材横向抗拉强度及塑性大大下降,同时冲击韧性也下降。
(4)抗蚀、焊接和切削性能:钢中硫化物夹杂还会引起坑蚀现象。
在钢的焊接过程中,钢中的硫化锰夹杂能引起热撕裂。
硫对钢还有一种很好的影响,即它能改善钢的切削性能。
铁水预处理工艺方法铁水预处理是对炼钢用铁水进行脱硅、脱磷和脱硫处理(简称为“三脱”),主要在出铁沟、鱼雷式混铁车、铁水包和混铁炉中进行。
铁水预处理工艺方法有:铁水沟连续处理法(铺撒法)、铁水罐喷吹法、机械搅拌法、专用炉法、摇包法、转鼓法、钟罩法以及喷雾法等。
铁水沟连续处理法:此法是一种最简易的铁水预处理方法,可分为上置法和喷吹法两种。
前者只需将预处理剂铺撒在铁水沟适当的位置,预处理剂即随铁水流下,靠铁流的搅动和冲击使预处理剂和铁水发生反应而脱出有关杂质元素;而后者则需在铁水沟上设置喷吹搅拌枪或喷粉枪,使预处理剂经喷吹搅拌强化与铁水的接触。
铁水预处理工艺方法及原理

铁水预处理工艺方法及原理铁水预处理是指铁水兑入炼钢炉前对其进行脱除杂质元素的一种处理工艺。
常用的工艺方法有:铁沟散料法、铁水罐内喷吹法、铁水罐内机械搅拌法等。
(1)铁沟散料法:高炉出铁时,在铁沟内的铁水上散入工业纯碱(Na2CO3)或复合脱硫剂(由Na2CO3 、CaO、CaCO3、CaF2、C粉等配合而成),利用铁水流动时的冲击湍流运动使铁水与脱硫剂搅拌混合,促进脱硫反应,达到脱硫目的。
该法简便易行,但脱硫效率波动大(约为20—60%)、环境污染大、恢硫多。
已基本不用。
(2)铁水罐内喷吹法:如右图所示:在送去转炉的铁路线上设立喷吹脱硫站,喷枪的铁管外复合有耐火材料浇注料,可插入铁水内一定深度,以空气为载体,喷入粉状脱硫剂,进行脱硫,而后耙除脱硫渣,防止恢硫(脱硫渣如果不去掉,在后续过程中,脱硫渣中的硫又会返回铁水中,造成恢硫)。
由于该法使脱硫剂与铁水接触良好,脱硫效率较高,还可脱除部分硅和碳。
常用的脱硫剂:a、钝化石灰粉(不含钝化剂的石灰,存放时间稍长,吸水到一定程度,就会堵塞喷吹系统)。
优点:成本较低、脱硫效率较高。
缺点:环保较差、铁水温降较大。
b、复合脱硫剂(由Na2CO3 、CaO、CaCO3、CaF2、C粉等配合而成)。
优点:成本较低、脱硫效率较高、比钝化石灰粉较易耙渣。
缺点:环保较差、铁水温降较大。
c、钝化镁粒(金属镁粒需钝化,否则存放时易氧化,同时载体需改为氮气)。
金属镁粒喷入铁水后,会迅速气化,与铁水接触条件更好,脱硫率很高。
优点:脱硫率很高、喷吹设备和操作很简单、环保较好、铁水温降很小、脱硫渣量很小。
缺点:成本高。
d、钝化镁粒与钝化石灰混喷(结合了金属镁粒脱硫率很高和钝化石灰成本低的优点,还可根据铁水含硫量和所炼钢种,来调节钝化镁粒(0—100%)与钝化石灰的配比,从而达到最佳成本与脱硫率的配合。
优点:脱硫率很高且可调、环保较好、铁水温降较小、脱硫渣量较小、成本较低且可调。
缺点:喷吹设备投资较大、操作较复杂。
铁水预处理
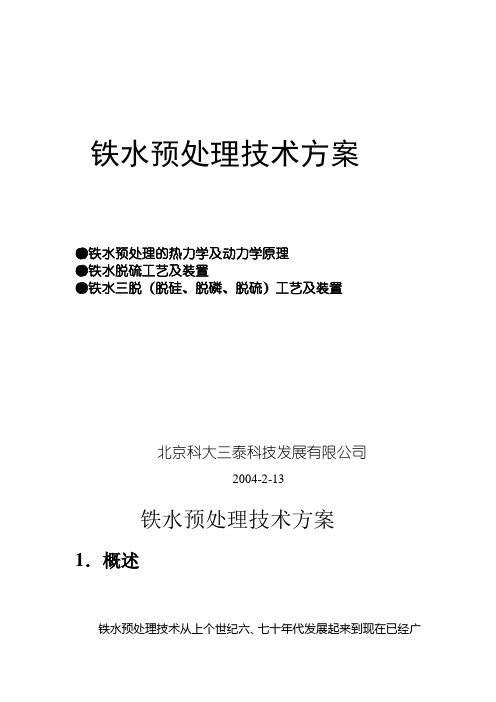
铁水预处理技术方案●铁水预处理的热力学及动力学原理●铁水脱硫工艺及装置●铁水三脱(脱硅、脱磷、脱硫)工艺及装置北京科大三泰科技发展有限公司2004-2-13铁水预处理技术方案1.概述铁水预处理技术从上个世纪六、七十年代发展起来到现在已经广泛地应用于各国,用于提高铁水质量,其技术也已经得到迅速的发展,目前可以用于铁水预处理的技术不下二、三十种。
铁水预处理工艺方法主要有:(1)机械搅拌法,有代表性的是日本开发的KR法;(2)吹气搅拌法,包括顶吹喷粉法和底吹法,目前顶吹喷粉法得到最广泛的应用,如ATH、TDS、IRSID、ISIDD等法;(3)喂丝法近年来开始得到应用。
铁水预处理的主要工艺目标是:(1)脱硫;(2)脱磷;(3)脱硅、磷、硫(俗称三脱);(4)其它。
从处理熔剂的选择来看有:主要是石灰系、碳化钙系、镁系三类脱硫剂,可以单独使用,可以复合应用,往往可以取得更好的冶金效果。
顶吹喷粉法近年发展了更多的工艺形成:产生了混合喷吹法和复合喷吹法以及分步喷吹法等。
从控制模型方面看:近年来更加重视建立较高精度的预处理粉剂喷吹量的控制模型。
还有一些不同的分类方法,但是无论怎样分类,每个企业选择的原则都是一样的,那就是从自己企业近期和长远规划来考虑,结合企业能力、产品目标、市场、经济效益等具体情况选择最适合自己的,最有利的方案。
本技术方案——从三个方面介绍科大三泰公司向用户推荐并可提供的技术装备:(1)(1)铁水罐顶喷纯化镁脱硫;(2)(2)铁水罐采用镁加钙系脱硫剂分步或复合喷吹脱硫(即所谓混喷);(3)(3)铁水罐采用镁加钙系或者单纯钙系脱硫剂分步或者复合喷吹三脱(脱硫、脱磷、脱硅);是较高精度顶吹喷粉法;脱硫剂选用钝化镁粒或镁系的;喷吹工艺形式采用单系统喷吹或分步复合喷吹;为了提高镁的利用率,降低喷粉生产成本,同时达到目标硫数值,达到喷粉目的,采用具有较高精度的脱硫剂喷吹量的控制模型(可选择的和可即时调控的);采用高技术喷射器系统;带气化室的喷枪;采用PLC 全程程控和计算机操作等。
(铁水预处理)炼钢工艺学

水含硫又高的小钢铁厂,还经常被采用。
机械搅拌法
靠旋转沉入铁水中的搅拌器或转动盛铁水的容器使铁水 与脱硫剂搅拌混合。
采用搅拌器和采用转动容器机械搅拌法,均可控制铁水 与脱硫剂的搅拌时间和搅拌强度,用CaC2作脱硫剂能得到 >90%的脱硫效率(单向摇包法搅拌混合较差,脱硫率比双向 摇包法约低10%),可以把铁水中的硫稳定地降低到<0.010%。
1、铁水预脱磷的基本原理
铁水中的磷首先氧化成P2O5,然后与强碱性氧化物结合成 稳定的磷酸盐而去除。
在铁水预脱磷过程中,首先要有适当的氧化剂将溶解于 铁水中的磷氧化,然后采用强有力的固定剂,使被氧化 的磷牢固地结合在炉渣中。
4.4 铁水预脱磷工艺
2、铁水预脱磷方法 ◆ 在高炉出铁沟或出铁槽内进行脱磷 ◆ 在铁水包或鱼雷罐车中进行预脱磷 ◆ 在专用转炉内进行铁水预脱磷
武钢旋转实心搅拌器的KR机械搅拌法,铁水的含硫量 可从0.06%降低到0.005%。实践证明,此类脱硫设备可以用 价廉的石灰进行有效的脱硫。设备最简单,脱硫效率高。
转动容器的回转炉法和摇包法,由于设备复杂,维修费用高 和难于大型化,发展前途不大。
搅拌器法
旋转实心搅拌器的 搅拌法(KR法)
旋转空心搅拌器的搅 拌法(DORA法)
4.5 铁水“三脱”工艺
铁水三脱工艺特点 o 优点: ▪ 可实现转炉少渣冶炼(渣量< 30 kg/t)。 ▪ 铁水脱硫有利于冶炼高碳钢、高锰钢、低磷钢、特殊钢
(如轴承钢、不锈钢)等。 ▪ 可提高脱碳速度,有利于转炉高速冶炼。 ▪ 转炉吹炼终点时钢水锰含量高,可用锰矿直接完成钢水合
金化。 o 缺点: ▪ 铁水中发热元素减少,转炉的废钢加入量减少。 转炉少渣炼钢工艺——铁水预处理将S、P(脱P需先脱Si )
1-铁水预处理工艺

3.2 铁水脱磷装置示意图
四、转炉双联法脱磷工艺
日本和歌山制铁所炼钢厂工艺布置示意图
4.1 脱磷转炉
脱磷炉加15%废钢(尺寸稍小些) 脱碳炉加2%废钢(尺寸稍大些) 脱磷炉:废钢与脱碳炉渣一起从料槽加入。 BOFd[p]:[C]:4.7%~3.7% 吹氧时间9min [P]:从0.1%(1000ppm)→降到0.01% (100ppm)周期时间20min 炉龄: 25000炉,炉渣R:≤2,渣量 ~35kg/t,脱磷炉供氧强度是脱碳炉的1/4~1/2。 脱磷炉加入造渣料:BOFd[C]返渣(约占脱碳 炉渣总量的1/2)+石灰 脱磷炉渣:由于碱度≤2,可直接用于筑路 等 半钢温度1300℃左右, 回收煤气,流量为 35000~40000m3/h
五、铁水预处理对纯净钢的意义
铁水含磷、硫可降到低或超低含量水平。 提高转炉生产率、降低成本、节约能耗。 极低碳钢的清洁度。钢中T[O]、[N]、[H]含
量降低。 有利于复吹转炉冶炼高碳钢时的“保碳出钢 技术”。 有效地提高铁、钢、材系统的综合经济效益。
二、铁水脱Si(120t转炉)
铁水脱Si的重要意义: 铁水脱磷的必要条件 利于减少石灰加入量和渣量
铁水脱Si的工艺方法铁水罐脱硅 转炉脱硅
2.1 脱Si剂、脱Si原理
脱硅剂: 氧化剂:氧气,氧化铁皮,精矿粉,烧结矿粉,氧 化铁烟尘 溶剂:石灰,萤石 铁水脱Si化学反应: [Si]+O2(g)=SiO2 [Si]+(2/3)Fe2O3(s)=SiO2(s)+(4/3)Fe [Si]+(1/2)Fe3O4(s)=SiO2(s)+(3/2)Fe [Si]+2(FeO)=SiO2(s)+2Fe
- 1、下载文档前请自行甄别文档内容的完整性,平台不提供额外的编辑、内容补充、找答案等附加服务。
- 2、"仅部分预览"的文档,不可在线预览部分如存在完整性等问题,可反馈申请退款(可完整预览的文档不适用该条件!)。
- 3、如文档侵犯您的权益,请联系客服反馈,我们会尽快为您处理(人工客服工作时间:9:00-18:30)。
铁水预处理工艺方法及原理
铁水预处理是指铁水兑入炼钢炉前对其进行脱除杂质元素的一种处理工艺。
常用的工艺方法有:铁沟散料法、铁水罐内喷吹法、铁水罐内机械搅拌法等。
(1)铁沟散料法:高炉出铁时,在铁沟内的铁水上散入工业纯碱(Na2CO3)
或复合脱硫剂(由Na2CO3 、CaO、CaCO3、CaF2、C粉等配合而成),利用铁水流动时的冲击湍流运动使铁水与脱硫剂搅拌混合,促进脱硫反应,达到脱硫目的。
该法简便易行,但脱硫效率波动大(约为20—60%)、环境污染
大、恢硫多。
已基本
不用。
(2)铁水罐内喷吹
法:如右图所示:在
送去转炉的铁路线
上设立喷吹脱硫站,
喷枪的铁管外复合
有耐火材料浇注料,
可插入铁水内一定深度,以空气为载体,喷入粉状脱硫剂,进行脱硫,而后耙除脱硫渣,防止恢硫(脱硫渣如果不去掉,在后续过程中,脱硫渣中的硫又会返回铁水中,造成恢硫)。
由于该法使脱硫剂与铁水接触良好,脱硫效率较高,还可脱除部分硅和碳。
常用的脱硫剂:
a、钝化石灰粉(不含钝化剂的石灰,存放时间稍长,吸水到
一定程度,就会堵塞喷吹系统)。
优点:成本较低、脱硫效率较高。
缺点:环保较差、铁
水温降较大。
b、复合脱硫剂(由Na2CO3 、CaO、CaCO3、CaF2、C粉等
配合而成)。
优点:成本较低、脱硫效率较高、比钝化石
灰粉较易耙渣。
缺点:环保较差、铁水温降较大。
c、钝化镁粒(金属镁粒需钝化,否则存放时易氧化,同时载体需改
为氮气)。
金属镁粒喷入铁水后,会迅速气化,与铁水接触条
件更好,脱硫率很高。
优点:脱硫率很高、喷吹设备和操作很简单、环保较好、铁水
温降很小、脱硫渣量很小。
缺点:成本高。
d、钝化镁粒与钝化石灰混喷(结合了金属镁粒脱硫率很高和
钝化石灰成本低的优点,还可根据铁水含硫量和所炼钢种,来调节钝化镁粒(0—100%)与钝化石灰的配比,从而达到最佳成本与脱硫率的配合。
优点:脱硫率很高且可调、环保较好、铁水温降较小、脱硫渣
量较小、成本较低且可调。
缺点:喷吹设备投资较大、操作较
复杂。
应用厂家:唐钢一钢轧采用是单喷颗粒镁工艺进行铁水脱硫。
(3)铁水罐内机械搅拌法:
(具有代表是KR法,如右
示意图)在送去转炉的铁路
线上设立机械搅拌脱硫站,
机械搅拌器插入铁水内一定
深度进行铁水搅拌,从而把
粒状或粉状脱硫剂卷入铁水
内部,进行脱硫,而后耙除
脱硫渣,防止恢硫。
由于该法使脱硫剂与铁水接触良好,脱硫效率较高,此法不能脱除硅和碳。
常用的脱硫剂:
a、粒状石灰(1—6mm或5—30mm)。
优点:成本较低、脱硫效率较高、环保较好。
缺点:铁水温降较大。
b、复合脱硫剂(由Na2CO3、CaO、CaCO3、CaF2、C粉等配合而成)。
优点:成本较低、环保较好、脱硫效率更高一些、比石灰粒较易耙渣。
缺点:铁水温降较大。
应用厂家:首钢首迁200吨3台、曹妃甸京唐钢铁300吨3台,采用KR法脱硫。
工艺流程为:。