浅谈瓦楞纸板塌楞故障处理方法
浅谈瓦楞纸板塌楞故障处理方法

浅谈瓦楞纸板塌楞故障处理方法在瓦楞纸板包装和印刷中,瓦楞纸板塌楞(一般均为局部塌楞)对产品包装质量的影响很大,这种不合格的瓦楞纸板,不但无法确保瓦楞纸箱的抗压强度、环压强度,不能保证包装产品贮运的安全,而且影响整个产品包装外观质量,此外,在包装印刷中也会因塌楞等原因使印刷的图文不清,严重影响产品的销售。
由于在瓦楞纸板生产过程中,对瓦楞纸板的技术参数、工艺设计、质量检测等几个方面要求非常严格,生产线结构比较复杂,生产时使用材料和影响质量的因素较多,如要求瓦楞原纸、温度、胶粘剂、速度等同步进行,只要有一个环节控制不好,就不可避免地发生质量问题。
因此,要保证生产出合格的瓦楞纸板除了要求设备精良,材料、环境符合要求外,熟悉生产工艺,掌握高超的操作技术和故障处理的技巧也是关键所在,下面就谈谈瓦楞纸板生产中出现局部塌楞故障的处理方法.供同行们参考。
瓦楞纸板塌楞的危害和特点在瓦楞纸板生产中,发生局部塌楞是其常见的故障之一.发生局部塌楞的类型主要有4种,即两个瓦楞塌楞、多个瓦楞塌楞和一个至多个瓦楞塌楞(如图1)。
在大批量生产中,瓦楞纸板产生这种局部塌楞的现象将会严重影响产品质量,造成大量次废品,导致制造成本大幅度增加,企业深受其害。
此外,发生塌楞的三层、五层或七层瓦楞纸板,必然会产生其脱胶面积之和大于国标每平方米20cm2,边压强度大大降低,纸板厚度低于标准,印刷图案、文字模糊发虚等次废品,严重影响纸箱产品的整体质量.这样的纸板不但根本无法应用于中、高档的产品包装,就是在低档次的包装中,对包装产品的质量、外观、销售等也都会产生不良的影响。
仔细观察分析瓦楞纸板产生塌楞的现象,可以归纳出如下瓦楞纸板生产中出现局部塌楞的主要特点:(1)塌楞面积变化大,以每平方米计,存在塌楞面积少至几平方厘米,多至上千平方厘米;(2)塌楞具有周期性,沿着单面机的生产方向,瓦楞纸板上出现周期性而不完全相同的塌楞;(3)塌楞面积沿瓦楞横向中间大两头小,楞形塌落呈不规则状态;(4)塌楞面积内明显脱胶,瓦楞纸板局部厚度明显减薄,有的仅为相应标准厚度的30%,单面、三层、五层瓦楞纸板局部塌楞。
瓦楞纸板出现变形现象的原因和解决方法
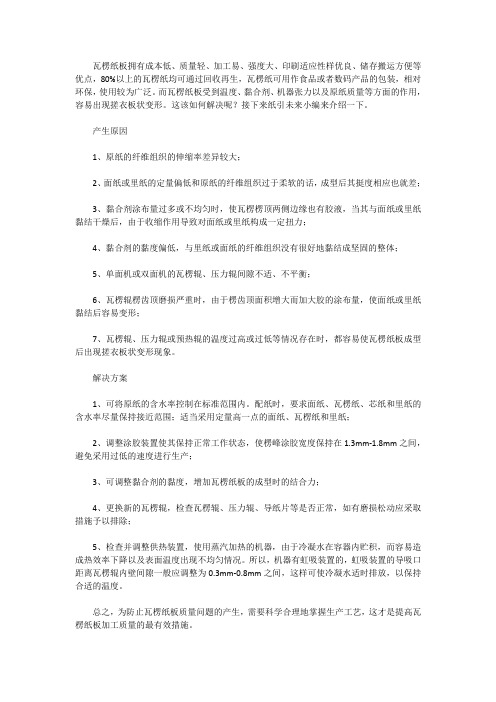
瓦楞纸板拥有成本低、质量轻、加工易、强度大、印刷适应性样优良、储存搬运方便等优点,80%以上的瓦楞纸均可通过回收再生,瓦楞纸可用作食品或者数码产品的包装,相对环保,使用较为广泛。
而瓦楞纸板受到温度、黏合剂、机器张力以及原纸质量等方面的作用,容易出现搓衣板状变形。
这该如何解决呢?接下来纸引未来小编来介绍一下。
产生原因1、原纸的纤维组织的伸缩率差异较大;2、面纸或里纸的定量偏低和原纸的纤维组织过于柔软的话,成型后其挺度相应也就差;3、黏合剂涂布量过多或不均匀时,使瓦楞楞顶两侧边缘也有胶液,当其与面纸或里纸黏结干燥后,由于收缩作用导致对面纸或里纸构成一定扭力;4、黏合剂的黏度偏低,与里纸或面纸的纤维组织没有很好地黏结成坚固的整体;5、单面机或双面机的瓦楞辊、压力辊间隙不适、不平衡;6、瓦楞辊楞齿顶磨损严重时,由于楞齿顶面积增大而加大胶的涂布量,使面纸或里纸黏结后容易变形;7、瓦楞辊、压力辊或预热辊的温度过高或过低等情况存在时,都容易使瓦楞纸板成型后出现搓衣板状变形现象。
解决方案1、可将原纸的含水率控制在标准范围内。
配纸时,要求面纸、瓦楞纸、芯纸和里纸的含水率尽量保持接近范围;适当采用定量高一点的面纸、瓦楞纸和里纸;2、调整涂胶装置使其保持正常工作状态,使楞峰涂胶宽度保持在1.3mm-1.8mm之间,避免采用过低的速度进行生产;3、可调整黏合剂的黏度,增加瓦楞纸板的成型时的结合力;4、更换新的瓦楞辊,检查瓦楞辊、压力辊、导纸片等是否正常,如有磨损松动应采取措施予以排除;5、检查并调整供热装置,使用蒸汽加热的机器,由于冷凝水在容器内贮积,而容易造成热效率下降以及表面温度出现不均匀情况。
所以,机器有虹吸装置的,虹吸装置的导吸口距离瓦楞辊内壁间隙一般应调整为0.3mm-0.8mm之间,这样可使冷凝水适时排放,以保持合适的温度。
总之,为防止瓦楞纸板质量问题的产生,需要科学合理地掌握生产工艺,这才是提高瓦楞纸板加工质量的最有效措施。
瓦楞纸板常见质量问题和产生原因及解决办法辩析

适度控制张力系统
表十三
质量问题
产生原因
解决办法
面纸压破裂
1.双面机热量过大
2.原纸质量不好
3.上、下压线轮相对位置不正
4.原纸含水太小
5.压线轮间隙调整不合适,间隙过小,压线太深,使面纸承压过大;间隙过大,压线太轻,在弯折时,面纸受力过大而破裂
降低热量,提高车速
更换原纸
修正和调整上、下压线轮位置
简易修复或更换瓦楞辊
增大予热器包角、降低车速、提高粘合剂质量
适当修正和调整
双向翘曲
原纸水分分布不均衡
帆布带横向张力不均衡
里、面原纸张力过大或过小
予热器浮动辊工作不正常
过纸天桥、予热器、涂胶机中心线不正
喷淋或予热控制
保持清洁和干燥,适当调整张力系统
加紧或放松刹车、控制张力
检查或修正运转部分零件、保证水平工作
提高车速或人为降低热板
适当投放重量辊
表五
质量问题
产生原因
解决办法
纵向向上翘曲
1.原纸张力不够
2.原纸含水不均衡
3.予热包角调控不平衡
4.过纸天桥过多堆积
5.过纸天桥输出瓦楞纸板张力过大
适当加大张力系统的控制力度
适当予热或喷水后予热
检查并修整传动装置,保证运转平行
减少堆积
适当减小输出张力控制
纵向向下翘曲
7.导纸板带脏、磨损或位置不正
8.涂胶辊和单面瓦楞纸板在运行中的速度不适应
9.瓦楞原纸张力过大
10.面纸、芯纸、瓦原纸含水不均衡
清除瓦楞辊表面脏物
检查冷凝水排放情况
调整粘合剂的制作,检查各种原料质量
修正和调整涂胶间隙、减小着胶量
包装印刷瓦楞问题产生的原因及解决办法
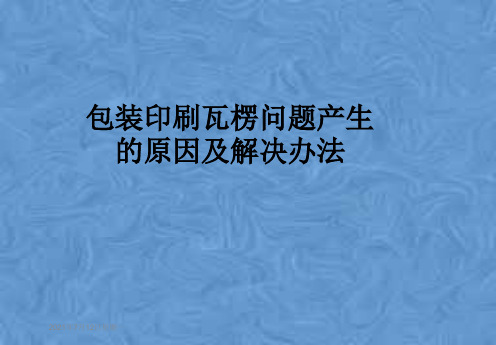
解决办法
调整、修正瓦楞辊的平行度
修正上、下瓦楞辊的贴合间隙
降低控制器的张力 检查、修正两者的调整装置
适当控制压辊的位 置并检查平衡度 加大原纸预热器
包角和双面机热量
调节传动带的松紧
三 塌楞
产生原因
瓦楞辊表面不清洁 瓦楞辊热量不均衡 瓦楞辊面磨损、 变形或调节不良
瓦楞辊配合压力不合适
胶黏剂的黏度太低
解决办法
充分发挥预热器 和预调器的作用
更换纸卷
减少胶黏剂的附着量
提高胶黏剂的黏度
二 面纸折皱
产生原因
箱纸板本身质量问题 面纸含水不均衡 原纸两端边过紧
解决办法
加大喷湿量、加大 张力或更换纸卷
加大预热包角或喷水增湿
适当加大张力的预热
三 纸板表面有折皱
产生原因
面纸张力不够 压力辊中高不够 纸箱板水分不 均匀、质量不好
调整、重置压辊 检查并排除热量不足的因素
产生原因
热量过高、淀粉过早凝合 胶黏剂形成团块 ,上胶不均匀 面纸张力太大
面纸、芯纸水分过大 胶黏剂附着量小 胶黏剂质量不好
解决办法
适当减少预热 提高胶黏剂的质量 调整刹车装置,减少摩擦力 加大预热力度或换纸 加大胶黏剂附着量
修正胶黏剂质量
二 部分脱胶
产生原因
更换瓦楞原纸或提高预热器效果
六 楞折皱
产生原因
瓦楞辊平行度不好 瓦楞辊磨损
瓦楞原纸质量不 好或水分不均衡 瓦楞原纸张力太小
解决办法
修正、调整瓦楞辊的平行度
修复或更换瓦楞辊
更换瓦楞原纸或 改善预热器效果
适当调整张力控 制系统,加大张力
七 瓦楞横切断、纵裂断
常见的瓦楞纸板缺陷及其解决方法
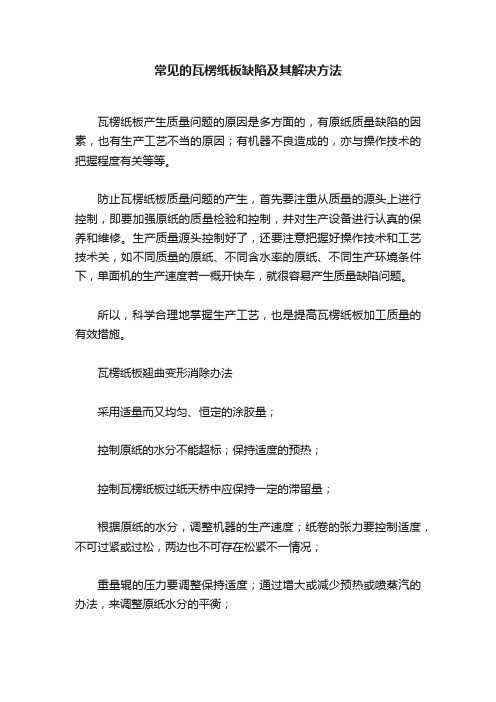
常见的瓦楞纸板缺陷及其解决方法瓦楞纸板产生质量问题的原因是多方面的,有原纸质量缺陷的因素,也有生产工艺不当的原因;有机器不良造成的,亦与操作技术的把握程度有关等等。
防止瓦楞纸板质量问题的产生,首先要注重从质量的源头上进行控制,即要加强原纸的质量检验和控制,并对生产设备进行认真的保养和维修。
生产质量源头控制好了,还要注意把握好操作技术和工艺技术关,如不同质量的原纸、不同含水率的原纸、不同生产环境条件下,单面机的生产速度若一概开快车,就很容易产生质量缺陷问题。
所以,科学合理地掌握生产工艺,也是提高瓦楞纸板加工质量的有效措施。
瓦楞纸板翘曲变形消除办法采用适量而又均匀、恒定的涂胶量;控制原纸的水分不能超标;保持适度的预热;控制瓦楞纸板过纸天桥中应保持一定的滞留量;根据原纸的水分,调整机器的生产速度;纸卷的张力要控制适度,不可过紧或过松,两边也不可存在松紧不一情况;重量辊的压力要调整保持适度;通过增大或减少预热或喷蒸汽的办法,来调整原纸水分的平衡;控制单面机或双面机生产环境保持稳定的温湿度;瓦楞辊、压力辊、活动辊和预热辊要调整保持平衡状态;对使用磨损厉害的瓦楞辊应更换新辊;切忌将含水率高低悬殊过大的瓦楞纸、面纸或里纸(箱板纸)进行配套成型加工。
瓦楞纸板出现搓衣板状变形的原因瓦楞纸板由于受到温度、黏合剂和机器张力和原纸质量等方面的作用,就容易出现搓衣板状变形。
产生原因:1、原纸的纤维组织的伸缩率差异较大;2、面纸或里纸的定量偏低和原纸的纤维组织过于柔软的话,成型后其挺度相应也就差;3、黏合剂涂布量过多或不均匀时,使瓦楞楞顶两侧边缘也有胶液,当其与面纸或里纸黏结干燥后,由于收缩作用导致对面纸或里纸构成一定扭力;4、黏合剂的黏度偏低,与里纸或面纸的纤维组织没有很好地黏结成坚固的整体;5、单面机或双面机的瓦楞辊、压力辊间隙不适、不平衡;6、瓦楞辊楞齿顶磨损严重时,由于楞齿顶面积增大而加大胶的涂布量,使面纸或里纸黏结后容易变形;7、瓦楞辊、压力辊或预热辊的温度过高或过低等情况存在时,都容易使瓦楞纸板成型后出现搓衣板状变形现象。
瓦楞纸板生产线中起楞过程中的常见故障及排除方法
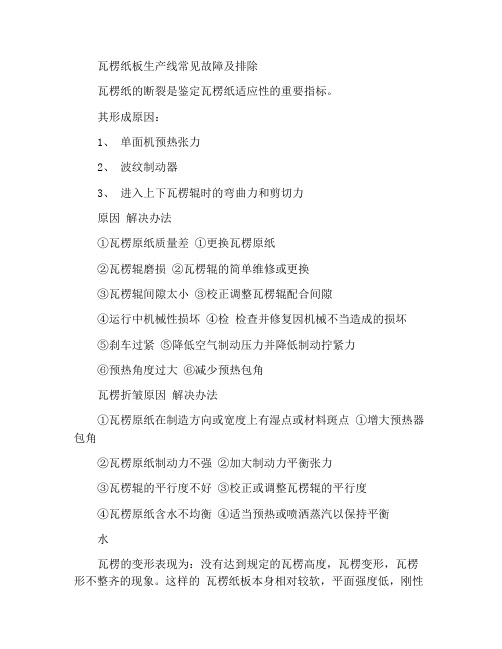
瓦楞纸板生产线常见故障及排除瓦楞纸的断裂是鉴定瓦楞纸适应性的重要指标。
其形成原因:1、单面机预热张力2、波纹制动器3、进入上下瓦楞辊时的弯曲力和剪切力原因解决办法①瓦楞原纸质量差①更换瓦楞原纸②瓦楞辊磨损②瓦楞辊的简单维修或更换③瓦楞辊间隙太小③校正调整瓦楞辊配合间隙④运行中机械性损坏④检检查并修复因机械不当造成的损坏⑤刹车过紧⑤降低空气制动压力并降低制动拧紧力⑥预热角度过大⑥减少预热包角瓦楞折皱原因解决办法①瓦楞原纸在制造方向或宽度上有湿点或材料斑点①增大预热器包角②瓦楞原纸制动力不强②加大制动力平衡张力③瓦楞辊的平行度不好③校正或调整瓦楞辊的平行度④瓦楞原纸含水不均衡④适当预热或喷洒蒸汽以保持平衡水瓦楞的变形表现为:没有达到规定的瓦楞高度,瓦楞变形,瓦楞形不整齐的现象。
这样的瓦楞纸板本身相对较软,平面强度低,刚性也低,做成的纸箱抗压强度也低,戳穿强度也小。
此种原因在流水线上有发生,在制箱过程中也有发生。
原因解决办法①强度低的瓦楞原纸抗压强度不足①更换高强度瓦楞纸②如果瓦楞原纸的含水量过低或过高,则很容易变形②加大预热包角或喷雾均衡水分③上、当下部瓦片辊之间的压力不足时,波纹成形不好③调整合适压力④瓦楞辊磨损,降低了瓦楞高度④更换垫辊和压辊⑤双面机器上涂布辊和压载辊之间的间隙调整不当⑤调节合适间隙达到正常合适⑥加热和冷却部件中的称重辊压力不当会导致破碎⑥调整加大压辊间隙高度⑦由于水分过高或热板温度不足,瓦楞纸板无法成型⑦增加蒸汽压力,将温度升高到适当的温度,或检查导致温度不好的原因以解决⑧横切机压辊调节太重,导致压溃瓦楞⑧通过调整重辊铊的间隙距离,可以解决波纹的倾斜问题:瓦楞向纸板运动方向倾斜,但还没倒塌。
原因解决方法①纸天桥张力过大①减低控制器的张力②双面机重力辊压力太大②正确控制重力辊的间隙并检查平衡③压纸辊和送纸辊之间的间隙不合适③调节间隙到适合④羊毛带打滑引起的上下速度差不同④调节毛布带的松紧到正常五)、瓦楞高低不平表现为:相邻波纹板和粘合表面之间的高度差很小,使纸板表面高低不平,并可降低抗压强度。
瓦楞纸板生产线故障与对策

瓦楞纸板生产线故障与对策在制造瓦楞纸板时会产生很多故障,其中有原材料问题,粘合剂问题,机械本身问题,操作技术问题及熟练程度的问题,在当今市场需求尤其在生产过程控制特别要求尽量尽快减少。
由上述故障引出的质量问题造成的报废数量和频率是重中之重。
经公司研究决定,由技术部编写本对策以解决生产急需达到降低控制成本之目的。
一、瓦楞纸断裂这是鉴别瓦楞纸适应性的重要指标。
其形原因:1、单面机预热张力2、瓦楞纸刹车器3、在进入上下瓦楞辊时受到的弯曲与剪切力产生原因解决办法①瓦楞原纸质量不好①更换瓦楞原纸②瓦楞辊磨损②进行简易修复或更换瓦楞辊③瓦楞辊间隙太小③修正和调整瓦楞辊的贴合间隙④运行中机械性损坏④检查并修复机械性不当造成的损伤⑤刹车过紧⑤降低气刹压力减少刹车紧力⑥预热包角过大⑥减少预热包角二、瓦楞折皱产生原因解决办法①瓦楞原纸在抄造或抄宽方向上有湿斑或料斑①增大预热器包角②瓦楞原纸的制动力不强②加大制动力平衡张力③瓦楞辊的平行度不好③修正或调整瓦楞辊的平行度④瓦楞原纸含水平不均衡④适当预热或喷蒸气使其保持平衡的含水三、瓦楞的变形表现为:没有达到规定的瓦楞高度,瓦楞变形,瓦楞形不整齐的现象。
这样的瓦楞成形的纸板本身比较软,平面强度低,刚性也低,做成的纸箱抗压强度也低,戳穿强度也小。
此种原因在流水线上有发生,在制箱过程中也有发生。
产生原因解决办法①使用了低强度的瓦楞原纸本身抗压强度不够①更换高强度瓦楞纸②瓦楞原纸水分过低或过高易变形②加大预热包角或喷雾均衡水分③上、下瓦辊间压力不足时瓦楞成型不好③调整合适压力④瓦楞辊磨损,降低了瓦楞高度④更换瓦辊和压力辊可解决⑤双面机上涂胶辊和压载辊的间隙调节不当⑤调节合适间隙达到正常合适⑥加热部和冷却部的加重辊压力不适当导致压溃⑥调整加大压辊间隙高度⑦瓦楞纸板水分高或热板温度不够不能使其定型⑦加大蒸气压力使温度升高到合适温度,或检查导致温度不好的原因以解决⑧横切机压辊调节太重,导致压溃瓦楞⑧调节重辊铊的间隙距离可解决四、瓦楞的倾斜表现为:瓦楞向纸板运动方向倾斜,但还没倒塌。
瓦楞纸板常见质量问题和产生原因及解决办法课件

大,压线太轻,在弯折时,面纸受
合间隙
过大而破裂
PPT文档演模板
瓦楞纸板常见质量问题和产生原因及 解决办法
3rew
演讲完毕,谢谢听讲!
再见,see you again
PPT文档演模板
2024/8/1
瓦楞纸板常见质量问题和产生原因及 解决办法
• 检查并重新制作粘合剂
• 瓦楞原纸含水不均衡张力小 • 适当予热并加大张力控制
• 过纸天桥张力不均衡
瓦楞纸板常见质量问题和产生原因及 解决办法
质量问题
楞倾斜
楞不均
PPT文档演模板
产生原因
解决办法
涂胶辊和浮动辊不平行 •
双面机重量辊位置不当或压 •
力大
过纸天桥张力太大
•
瓦楞原纸含水过高
•
瓦楞辊不平行
适当修正和调整
原纸水分分布不均衡
喷淋或予热控制
帆布带横向张力不均衡
保持清洁和干燥,适当调整
张力系统
里、面原纸张力过大或过小 加紧或放松刹车、控制张力
预热器浮动辊工作不正常
检查或修正运转部分零件、
保证水平工作
过纸天桥、予热器、涂胶机中心 如安装失误应重新修正、部
线不正
分偏斜加以调整
瓦楞纸板常见质量问题和产生原因及 解决办法
•瓦楞辊贴合间隙太小• Nhomakorabea瓦楞辊表面有脏物
•
检查和修正二者的调整 装置
适当控制重量辊的投放 并检查平衡度 减低控制器的张力
加大予热器包角和双面 机热量
调整和修正瓦楞辊的平 行度
修正瓦楞辊的贴合间隙 清理瓦楞表面异物
瓦楞辊贴合间隙大
• 修正瓦楞辊的贴合间隙
瓦画辊贴合间隙不平衡 •
- 1、下载文档前请自行甄别文档内容的完整性,平台不提供额外的编辑、内容补充、找答案等附加服务。
- 2、"仅部分预览"的文档,不可在线预览部分如存在完整性等问题,可反馈申请退款(可完整预览的文档不适用该条件!)。
- 3、如文档侵犯您的权益,请联系客服反馈,我们会尽快为您处理(人工客服工作时间:9:00-18:30)。
浅谈瓦楞纸板塌楞故障处理方法
在瓦楞纸板包装和印刷中,瓦楞纸板塌楞(一般均为局部塌楞)对产品包装质量的影响很大,这种不合格的瓦楞纸板,不但无法确保瓦楞纸箱的抗压强度、环压强度,不能保证包装产品贮运的安全,而且影响整个产品包装外观质量,此外,在包装印刷中也会因塌楞等原因使印刷的图文不清,严重影响产品的销售。
由于在瓦楞纸板生产过程中,对瓦楞纸板的技术参数、工艺设计、质量检测等几个方面要求非常严格,生产线结构比较复杂,生产时使用材料和影响质量的因素较多,如要求瓦楞原纸、温度、胶粘剂、速度等同步进行,只要有一个环节控制不好,就不可避免地发生质量问题。
因此,要保证生产出合格的瓦楞纸板除了要求设备精良,材料、环境符合要求外,熟悉生产工艺,掌握高超的操作技术和故障处理的技巧也是关键所在,下面就谈谈瓦楞纸板生产中出现局部塌楞故障的处理方法。
供同行们参考。
瓦楞纸板塌楞的危害和特点
在瓦楞纸板生产中,发生局部塌楞是其常见的故障之一。
发生局部塌楞的类型主要有4种,即两个瓦楞塌楞、多个瓦楞塌楞和一个至多个瓦楞塌楞(如图1)。
在大批量生产中,瓦楞纸板产生这种局部塌楞的现象将会严重影响产品质量,造成大量次废品,导致制造成本大幅度增加,企业深受其害。
此外,发生塌楞的三层、五层或七层瓦楞纸板,必然会产生其脱胶面积之和大于国标每平方米20cm2,边压强度大大降低,纸板厚度低于标准,印刷图案、文字模糊发虚等次废品,严重影响纸箱产品的整体质量。
这样的纸板不但根本无法应用于中、高档的产品包
装,就是在低档次的包装中,对包装产品的质量、外观、销售等也都会产生不良的影响。
仔细观察分析瓦楞纸板产生塌楞的现象,可以归纳出如下瓦楞纸板生产中出现局部塌楞的主要特点:(1)塌楞面积变化大,以每平方米计,存在塌楞面积少至几平方厘米,多至上千平方厘米;(2)塌楞具有周期性,沿着单面机的生产方向,瓦楞纸板上出现周期性而不完全相同的塌楞;(3)塌楞面积沿瓦楞横向中间大两头小,楞形塌落呈不规则状态;(4)塌楞面积内明显脱胶,瓦楞纸板局部厚度明显减薄,有的仅为相应标准厚度的30%,单面、三层、五层瓦楞纸板局部塌楞。
引起塌楞故障的主要原因和解决方法
在日常瓦楞纸板产生中,出现局部塌楞现象的纸板多数为导爪式单面机生产的瓦楞纸板,因此,下面就主要针对这种塌楞故障进行分析,归纳起来,主要有三个方面。
第一,导爪工作面圆弧半径与下瓦楞辊外径之间间隙过大。
如下瓦楞辊峰已经磨损使外径减小或下瓦楞辊楞型经反复修磨后外径减小等,仍然使用原
有的导爪其间隙就必然过大。
第二,导爪安装位置不当,导爪的工作面圆弧半径与下瓦楞辊外径之间上、下间隙不一致。
如导爪安装未到位,导爪上端或下瓦楞辊间隙太大,距离压力辊太远,使得工作面未起到导纸的功能。
第三,导爪在使用中已局部磨损,部分工作面不能正常导纸。
瓦楞原纸在单面瓦楞机轧制过程中,一旦经过受力点(上、下瓦楞辊楞齿啮合点),它就受到瓦楞辊运转产生的离心力作用和烘烤后散发水分的气压作用,会使成型的瓦楞纸脱离辊表面,这时主要靠导爪将成型的瓦楞纸紧紧托住,使其紧附在下瓦楞辊的表面运转。
若导爪工作面圆弧半径与下瓦楞辊外径之间间隙过大或不一致(除涂胶处之外),就不能起到应有导纸功能,瓦楞纸在径向就会处于自由状态,脱离瓦楞辊楞峰表面,产生楞形峰谷错位,运转中当下瓦楞辊与压力辊压紧时,错位了的瓦楞纸楞形受到下瓦楞辊楞峰的挤压,使得瓦楞纸已涂上胶水的楞峰不规则地与里纸粘合,形成单面瓦楞纸板局部塌楞。
因此,在瓦楞辊正常的情况下,解决瓦楞纸板局部塌楞,关键是要保持导爪工作面与下瓦楞辊外径之间间隙的合理性和一致性。
此外,由于影响瓦楞纸板生产质量的因素很多,如温度不足、瓦楞原纸水分过高、胶粘剂质量等多种因素都会引起塌楞现象。
主要有:涂胶辊的单面瓦楞纸板运行中的速度不适应;瓦楞原纸张力过大;面纸、芯纸、瓦楞原纸含水不均衡或瓦楞原纸水分过多;上瓦楞原辊的夹紧压力不合适;瓦楞辊面有污物,磨根、变形或调节不良;瓦楞辊热量不均衡;胶粘剂粘度不够或附着量太大;帆布带污染,透气性不好;双面机热板表面有异物。
根据上述原因,应仔细观察分析故障的现象,采用合适的解决方法。
首先,
要测量或检查导爪工作面圆弧半径与下瓦楞辊外径是否配套(如图2)。
若导爪工作面出现局部非正常磨损或磨损太多,则应立即调换导爪。
当下瓦楞辊的楞型经过反复修磨后外径减小或下瓦楞辊的楞峰明显磨损使外径减小时,则根据下瓦楞外径减小量重新加工导爪工作面圆弧半径。
根据实践经验,导爪半径的配制为:
导爪工作面圆弧半径=下瓦楞辊实际外径÷2+瓦楞原纸厚度×修正值
对于不同类型的瓦楞纸,选取的修正值(一般为1.5~1.9)有所差异,一般来说,E型楞取1.5,B型楞取1.6,C型楞取1.8,A型楞取1.9。
此外,为了便于楔入导向,导爪工作面上方10~20mm范围内的圆弧半径可另加0.2~0.4mm。
其次,导爪安装的位置要保证合适,导爪工作面圆弧半径与下瓦楞辊外径的配合间隙要根据不同类型的瓦楞纸板控制,一般为(1.5~1.9)×瓦楞原纸厚度,并要调整到上、下间隙一致,导爪的平面要与下瓦楞辊轴线保持垂直。
第三,必须注意检查导爪两端位置是否合适,上、下端能不能顶住,并观察其承托瓦楞功能是否正常,若有误差应进行调整、磨削或重新制造。
瓦楞辊、导爪工作面上有粘附物等,也会影响正常导纸,应及时清理。
至于因温度不足、瓦楞原纸水分过高、胶粘剂质量等因素引起的塌楞,也应根据塌楞的具体情况,对症下药地排除故障。
如因涂胶辊的单面瓦楞纸板运行中的速度不适应,则应加大过纸天桥的张力控制系统,增大或减小张力;若瓦楞原纸张力过大,就要减小张力系统的摩擦;对于面纸、芯纸、瓦楞原纸含水不均衡或瓦楞原纸水分过多,则应充分预热或更换面纸、芯纸、瓦楞原纸;检查调试合适的上瓦楞原辊的夹紧压力,并使之稳定;看看瓦楞辊面是否存在污物并加以清理;检查瓦楞辊面是否磨损、变形或调节不良,对辊筒进行调校;对于瓦楞辊热量不均衡的现象,则应检查冷凝水排放情况;看看是否胶粘剂粘度不够或附着量太大,若是,则应检查各种原料质量,调整胶粘剂制作或修正和调整涂胶间隙、减少着胶量;若因帆布带污染,透气性不好引起的塌楞,就必须清洗和烘干帆布带;检查双面机热板表面有脏污,应及时清除污物,并保持表面洁净。
总之,对于瓦楞纸板生产中出现局部塌楞的现象,应根据塌楞的位置、形状等外观现象,分析机械设备、材料、环境、技术等方面的因素,不断调试排除处理,并不断总结经验,避免成本损耗,提高纸板合格率。