冲压模具外文英语文献翻译
冲压模具英文参考文献(精选120个最新)
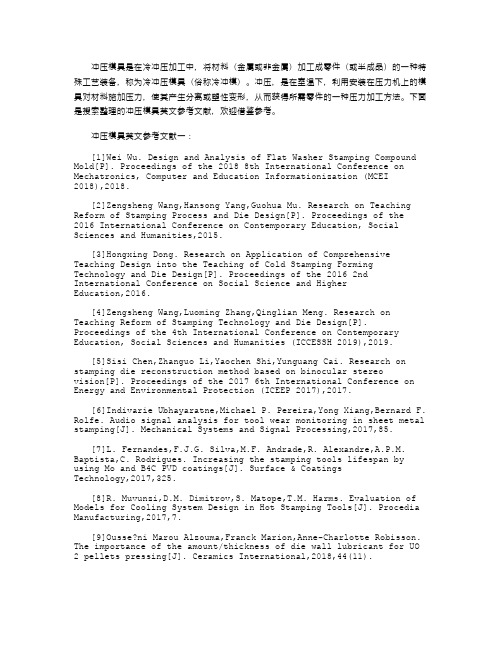
冲压模具是在冷冲压加工中,将材料(金属或非金属)加工成零件(或半成品)的一种特殊工艺装备,称为冷冲压模具(俗称冷冲模)。
冲压,是在室温下,利用安装在压力机上的模具对材料施加压力,使其产生分离或塑性变形,从而获得所需零件的一种压力加工方法。
下面是搜索整理的冲压模具英文参考文献,欢迎借鉴参考。
冲压模具英文参考文献一: [1]Wei Wu. Design and Analysis of Flat Washer Stamping Compound Mold[P]. Proceedings of the 2018 8th International Conference on Mechatronics, Computer and Education Informationization (MCEI 2018),2018. [2]Zengsheng Wang,Hansong Yang,Guohua Mu. Research on Teaching Reform of Stamping Process and Die Design[P]. Proceedings of the 2016 International Conference on Contemporary Education, Social Sciences and Humanities,2015. [3]Hongxing Dong. Research on Application of Comprehensive Teaching Design into the Teaching of Cold Stamping Forming Technology and Die Design[P]. Proceedings of the 2016 2nd International Conference on Social Science and HigherEducation,2016. [4]Zengsheng Wang,Luoming Zhang,Qinglian Meng. Research on Teaching Reform of Stamping Technology and Die Design[P]. Proceedings of the 4th International Conference on Contemporary Education, Social Sciences and Humanities (ICCESSH 2019),2019. [5]Sisi Chen,Zhanguo Li,Yaochen Shi,Yunguang Cai. Research on stamping die reconstruction method based on binocular stereovision[P]. Proceedings of the 2017 6th International Conference on Energy and Environmental Protection (ICEEP 2017),2017. [6]Indivarie Ubhayaratne,Michael P. Pereira,Yong Xiang,Bernard F. Rolfe. Audio signal analysis for tool wear monitoring in sheet metal stamping[J]. Mechanical Systems and Signal Processing,2017,85. [7]L. Fernandes,F.J.G. Silva,M.F. Andrade,R. Alexandre,A.P.M. Baptista,C. Rodrigues. Increasing the stamping tools lifespan by using Mo and B4C PVD coatings[J]. Surface & CoatingsTechnology,2017,325. [8]R. Muvunzi,D.M. Dimitrov,S. Matope,T.M. Harms. Evaluation of Models for Cooling System Design in Hot Stamping Tools[J]. Procedia Manufacturing,2017,7. [9]Ousse?ni Marou Alzouma,Franck Marion,Anne-Charlotte Robisson. The importance of the amount/thickness of die wall lubricant for UO 2 pellets pressing[J]. Ceramics International,2018,44(11). [10]Kailun Zheng,Yangchun Dong,Hanshan Dong,JonathanFernandez,Trevor A Dean. Investigation of the lubrication performance using WC: C coated tool surfaces for hot stampingAA6082[J]. Procedia Engineering,2017,207. [11]Ersyzario Edo Yunata,Tatsuhiko Aizawa,Kenji Tamaoki,Masao Kasugi. Plasma Polishing and Finishing of CVD-Diamond Coated WC (Co) Dies for Dry Stamping[J]. Procedia Engineering,2017,207. [12]L. Fernandes,F.J.G. Silva,M.F. Andrade,R. Alexandre,A.P.M. Baptista,C. Rodrigues. Improving the punch and die wear behavior in tin coated steel stamping process[J]. Surface & Coatings Technology,2017,332. [13]Xiaochuan Liu,Mohammad M. Gharbi,Oualid Manassib,Omer El Fakir,LiLiang Wang. Determination of the interfacial heat transfer coefficient between AA7075 and different forming tools in hot stamping processes[J]. Procedia Engineering,2017,207. [14]Li-Wei Chen,Ming-Jhe Cai. Development of a hot stamping clinching tool[J]. Journal of Manufacturing Processes,2018,34. [15]Xiaochuan Liu,Omer El Fakir,Mohammad M. Gharbi,LiLiang Wang. Effect of tool coating on interfacial heat transfer coefficient in hot stamping of AA7075 aluminium alloys[J]. ProcediaManufacturing,2018,15. [16]Yuki Nakagawa,Ken-ichiro Mori,Tomoyoshi Maeno,Yoshitaka Nakao. Reduction in holding time at bottom dead centre in hot stamping by water and die quenching[J]. ProcediaManufacturing,2018,15. [17]Tomoki Hasegawa,Tatsuhiko Aizawa,Tadahiko Inohara,Kenji Wasa,Masahiro Anzai. Hot mold stamping of optical plastics and glasses with transcription of super-hydrophobic surfaces[J]. Procedia Manufacturing,2018,15. [18]Chunping Cao,Meng Li,Yu Li,Yu Sun. Intelligent fault diagnosis of hot die forging press based on binary decision diagram and fault tree analysis[J]. Procedia Manufacturing,2018,15. [19]Shiva Shankar Mangalore Babu,Stuart Berry,Michael Ward,Michal Krzyzanowski. Numerical investigation of key stamping process parameters influencing tool life and wear[J]. Procedia Manufacturing,2018,15. [20]Y. Pascal,D. Labrousse,M. Petit,S. Lefebvre,F. Costa. Experimental investigation of the reliability of Printed Circuit Board (PCB)-embedded power dies with pressed contact made of metal foam[J]. Microelectronics Reliability,2018,88-90. [21]Enrico Armentani,Angelo Mattera,Raffaele Sepe,LucaEsposito,Francesco Naclerio,Gian Filippo Bocchini. Dies for pressingmetal powders to form helical gears[J]. Procedia Structural Integrity,2018,12. [22]Ping Chen,Xiaojie Liu,Mingji Huang,Zhe Shi,Bin Shan. Numerical simulation and experimental study on tribological properties of stamping die with triangular texture[J]. Tribology International,2018. [23]Xiaochuan Liu,Omer El Fakir,Yang Zheng,Mohammad M.Gharbi,LiLiang Wang. Effect of tool coatings on the interfacial heat transfer coefficient in hot stamping of aluminium alloys under variable contact pressure conditions[J]. International Journal of Heat and Mass Transfer,2019,137. [24]P. Vishnu,R. Raj Mohan,E. Krishna Sangeethaa,S. Raghuraman,R. Venkatraman. A review on processing of aluminium and its alloys through Equal Channel Angular Pressing die[J]. Materials Today: Proceedings,2019. [25]Liang Ying,Tianhan Gao,Minghua Dai,Ping Hu,Luming Shen. Investigation of convection heat transfer coefficient of circular cross-section short pipes in hot stamping dies[J]. Applied Thermal Engineering,2018,138. [26]Patrik Schwingenschl?gl,Philipp Niederhofer,Marion Merklein. Investigation on basic friction and wear mechanisms within hot stamping considering the influence of tool steel and hardness[J]. Wear,2019,426-427. [27]Yan-hong Mu,Bao-yu Wang,Jing Zhou,Xu Huang,Jun-ling Li. Influences of hot stamping parameters on mechanical properties and microstructure of 30MnB5 and 22MnB5 quenched in flat die[J]. Journal of Central South University,2018,25(4). [28]Q. Y. Jiang,H. Y Zhao,H. F. Yang. Numerical Simulation of the Thermomechanical Behavior of a Hot Stamping Die[J]. Strength of Materials,2018,50(1). [29]Xiaoyong Qiao,Aiguo Cheng,Xin Nie,Minqing Ning. A study on die wear prediction for automobile panels stamping based on dynamic model[J]. The International Journal of Advanced Manufacturing Technology,2018,97(5-8). [30]Mohd Fawzi Zamri,Ahmad Razlan Yusoff. Heuristic design of U-shaped die cooling channel for producing ultra-high strength steel using hot press forming[J]. The International Journal of Advanced Manufacturing Technology,2018,97(9-12). 冲压模具英文参考文献二: [31]Hangyan Wang,Hui Xie,Qiming Liu,Yunfei Shen,PinjianWang,Licheng Zhao. Structural topology optimization of a stampingdie made from high-strength steel sheet metal based on loadmapping[J]. Structural and MultidisciplinaryOptimization,2018,58(2). [32]N. Demazel,H. Laurent,J. Co?r,M. Carin,P. Masson,J. Favero,R. Canivenc,H. Salmon-Legagneur. Investigation of the progressive hot die stamping of a complex boron steel part using numerical simulations and Gleeble tests[J]. The International Journal of Advanced Manufacturing Technology,2018,99(1-4). [33]Csaba Pléh. A Review of Olivier Morin: How traditions live and die. Oxford: Oxford University Press, xvi + 300 pp, 2016, paper. Foundations of Human Interaction Series, ?25.99[J]. Evolutionary Psychological Science,2017,3(3). [34]Guo-Zheng Quan,Zhi-hua Zhang,Xuan Wang,Yong-le Li,An Mao,Yu-feng Xia. Parameter optimization of cooling system in U-shape hot stamping mold for high strength steel sheet based on MOPSO[J]. The International Journal of Advanced ManufacturingTechnology,2017,90(1-4). [35]Kailun Zheng,Denis J. Politis,Jianguo Lin,Trevor A. Dean. An experimental and numerical investigation of the effect of macro-textured tool surfaces in hot stamping[J]. International Journal of Material Forming,2017,10(2). [36]Pabitra Palai,N. Prabhu,B. P. Kashyap. Effect of Solid Die Equi-Channel Pressing Angle on β-Mg 17 Al 12 Phase Morphology and Mechanical Behavior of AZ80 Mg alloy[J]. Journal of Materials Engineering and Performance,2017,26(4). [37]I. N. Stepankin. Consideration of contact wear regularitiesof the surface layers of stamping tools in order to increase resistance[J]. Journal of Friction and Wear,2017,38(3). [38]Gui Li,Xiaoyu Long,Min Zhou,Hegen Xiong,Wensheng Wang. A geometric feature-based design system of full parametric association modeling of standard cam for automotive stamping dies[J]. The International Journal of Advanced ManufacturingTechnology,2017,92(9-12). [39]S. N. Lezhnev,I. E. Volokitina,A. V. Volokitin. Evolution of microstructure and mechanical properties of steel in the course of pressing–drawing[J]. Physics of Metals andMetallography,2017,118(11). [40]Alexander Kalies,Hüseyin ?zcoban,Claudia S. Leopold. Performance Characteristics of a Novel Vibration Technique for the Densification of a Powder Bed within a Die of a Rotary Tablet Press — a Proof of Concept[J]. AAPS PharmSciTech,2019,20(4). [41]Gui Li,Xiaoyu Long,Min Zhou. A new design method based on feature reusing of the non-standard cam structure for automotive panels stamping dies[J]. Journal of IntelligentManufacturing,2019,30(5). [42]Gui Li,Peng Yang,Zhongkai Liang,Saisai Cui. Intelligent design and group assembly of male and female dies for hole piercing of automotive stamping dies[J]. The International Journal of Advanced Manufacturing Technology,2019,103(1-4). [43]Long Chen,Wei Chen,Fan Xu,Yinxia Zhu,Yitao Zhu. A pre-design method for drilled cooling pipes in hot stamping tool based on pipe parameter window[J]. The International Journal of Advanced Manufacturing Technology,2019,103(1-4). [44]Rolinski, E,Woods, M,Damirgi, T,Sharp, G. Improving Performance of Stamping Dies with Ion/Plasma Nitriding[J].Industrial Heating,2015,83(11). [45]Jianwei Liu,Xinyu Liu,Lianfa Yang,Huiping Liang.Investigation of tube hydroforming along with stamping of thin-walled tubes in square cross-section dies[J]. Proceedings of the Institution of Mechanical Engineers,2016,230(1). [46]Sarah D Phillips. Dying Unneeded: The Cultural Context of the Russian Mortality Crisis by Michelle A. Parsons. Nashville: Vanderbilt University Press, 2014. 224 pp.[J]. American Anthropologist,2016,118(1). [47]Anonymous. Big Mill Masters Large Progressive StampingDies[J]. Manufacturing Engineering,2016,156(6). [48]. Materials Engineering; Reports Outline Materials Engineering Findings from Iran University of Science and Technology (Die Design Modification to Improve Workability during Equal Channel Angular Pressing)[J]. Journal of Engineering,2016. [49]Eric I Karchmer. Fighting for Breath: Living Morally and Dying of Cancer in a Chinese Village by Anna Lora-Wainwright. Honolulu: University of Hawai'i Press, 2013. 343 pp.[J]. American Anthropologist,2016,118(4). [50]. T.H.T. Presses, Inc.; Researchers Submit Patent Application, "Thermally Directed Die Casting Suitable for Making Hermetically Sealed Disc Drives", for Approval (USPTO20170136529)[J]. Chemicals & Chemistry,2017. [51]. Toyota Boshoku Kabushiki Kaisha; "Press Die" in Patent Application Approval Process (USPTO 20180154423)[J]. Energy Weekly News,2018. [52]Sarah D Phillips. Dying Unneeded: The Cultural Context of the Russian Mortality Crisis by Michelle A. Parsons. Nashville: Vanderbilt University Press, 2014. 224 pp.[J]. American Anthropologist,2016,118(1). [53]. GM Global Technology Operations LLC; Patent Application Titled "Die Assembly For A Stamping Press" Published Online (USPTO 20180221934)[J]. Energy Weekly News,2018. [54]. BOBST Mex SA; "Foil Reel Mounting Device, Supporting Module, Stamping Machine, Handling Tool And Method For Loading And Unloading A Reel Of Stamping Foil" in Patent Application Approval Process (USPTO 20180257366)[J]. Electronics Business Journal,2018. [55]Eric I Karchmer. Fighting for Breath: Living Morally and Dying of Cancer in a Chinese Village by Anna Lora-Wainwright. Honolulu: University of Hawai'i Press, 2013. 343 pp.[J]. American Anthropologist,2016,118(4). [56]. Nanotechnology - Micromachines; Data on Micromachines Reported by Researchers at Polytechnic of Porto (Study of Tialn Pvd Coating On Stamping Dies Used In Tinplate Food PackageProduction)[J]. Food Weekly News,2019. [57]Klass Dennis. Griffith, L. M., & Wallace, C. (Eds.). (2016). Grave matters: Death and dying in Dublin 1500 to the presentGriffith L. M. & Wallace C. (Eds.). ( 2016 ). Grave matters: Death and dying in Dublin 1500 to the present . Dublin, Ireland : Four Courts Press . 226 pp. 22.45. ISBN: 978-1-84682-601-6 (paperback)..[J]. Omega,2018,76(3). [58]Cann Candi K. Malkowski, J. (2017). Dying in Full Detail: Mortality and Digital Documentary Malkowski J. ( 2017 ). Dying in Full Detail: Mortality and Digital Documentary. Durham, NC: Duke University Press. 264 pp. ISBN 978-0-8223-6315-6. $23.95 (paperback).[J]. Omega,2017. [59]Fernandes Liliana,Silva Francisco J G,Alexandre Ricardo. Study of TiAlN PVD Coating on Stamping Dies Used in Tinplate Food Package Production.[J]. Micromachines,2019,10(3). [60]Kalies Alexander,?zcoban Hüseyin,Leopold Claudia S. Performance Characteristics of a Novel Vibration Technique for the Densification of a Powder Bed within a Die of a Rotary Tablet Press - a Proof of Concept.[J]. AAPS PharmSciTech,2019,20(4). 冲压模具英文参考文献三: [61]Cantin Yann. L'éducation de l'écolier sourd. Histoire d'une orthopédie. 1822 à 1910 par Didier Séguillon L'éducation del'écolier sourd. Histoire d'une orthopédie. 1822 à 1910 DidierSéguillon Nanterre : Presses universitaires de Paris Nanterre , 2017 , 364 p., 22 ?.[J]. Canadian bulletin of medical history=Bulletin canadien d'histoire de la medecine,2018,35(1). [62]Fanciulli C,Coduri M,Boldrini S,Abedi H,Tomasi C,FamengoA,Ferrario A,Fabrizio M,Passaretti F. Structural Texture Induced inSnSe Thermoelectric Compound via Open Die Pressing.[J]. Journal of nanoscience and nanotechnology,2017,17(3). [63]Zahari Taha,M A Hanafiah Shaharudin. Estimation of Thermal Contact Conductance between Blank and Tool Surface in Hot Stamping Process[J]. IOP Conference Series: Materials Science and Engineering,2016,114(1). [64]A Zakaria,M A Abidin,M S N Ibrahim,A Senin. Numerical Validation of an Optimized Cooling System for Hot Stamping Die[J]. Journal of Physics: Conference Series,2016,734(3). [65]Nan Zhang,Fadi Abu-Farha. Modeling and Simulating Material Behavior during Hot Blank - Cold Die (HB-CD) Stamping of Aluminium Alloy Sheets[J]. Journal of Physics: Conference Series,2016,734(3). [66]Johan Pilthammar,Mats Sigvant,Sharon Kao-Walter. Including die and press deformations in sheet metal forming simulations[J]. Journal of Physics: Conference Series,2016,734(3). [67]W Wei?,M Koplenig,M Alb,J Graf. Virtual method for the determination of an optimum thermal design of hot stamping tools[J]. IOP Conference Series: Materials Science andEngineering,2016,159(1). [68]I Valls,A Hamasaiid,A Padré. High Thermal Conductivity and High Wear Resistance Tool Steels for cost-effective Hot Stamping Tools[J]. Journal of Physics: Conference Series,2017,896(1). [69]V. Vignesh Shanbhag,P. Michael Pereira,F. Bernard Rolfe,N Arunachalam. Time series analysis of tool wear in sheet metal stamping using acoustic emission[J]. Journal of Physics: Conference Series,2017,896(1). [70]F Medea,G Venturato,A Ghiotti,S Bruschi. Tribological performances of new steel grades for hot stamping tools[J]. Journal of Physics: Conference Series,2017,896(1). [71]Lars Penter,Steffen Ihlenfeldt,Norbert Pierschel. Compensation for tool deformation and expansion in virtual try-outs of hot stamping tools[J]. IOP Conference Series: Materials Science and Engineering,2018,418(1). [72]Vignesh V Shanbhag,Bernard F Rolfe,N Arunachalam,Michael P Pereira. Understanding the source of acoustic emission signalsduring the wear of stamping tools[J]. IOP Conference Series: Materials Science and Engineering,2018,418(1). [73]S E Pratiwi,W Haris,I Miftakhul. Analysis of progressive dies metal stamping components for yoke a plate to maximize age ofwear[J]. IOP Conference Series: Materials Science andEngineering,2018,453(1). [74]Shand Lynda. Caring for the Dying: The Doula Approach to a Meaningful Death by Fersko-Weiss, H. (2017) Fersko-Weiss H. ( 2017 ). Caring for the Dying: The Doula Approach to a Meaningful Death. Newburyport, MA: Conari Press. 222 pp. $24.95 (hardback). ISBN: 9781573246965.[J]. Omega,2018,77(2). [75]Hill. Tell me why my children died: rabies, indigenous knowledge, and communicative justice , by Charles L. Briggs andClara Mantini-Briggs, Durham, NC, Duke University Press, 2016, 344 pp., US$26.95 (paperback), ISBN 978-0-8223-6124-4[J]. Canadian Journal of Latin American and Caribbean Studies / Revue canadienne des études latino-américaines et cara?bes,2018,43(2). [76]Andre Shihomatsu,Sergio Tonini Button,Iris Bento daSilva,Patrick De Baets. Tribological Behavior of Laser Textured Hot Stamping Dies[J]. Advances in Tribology,2016,2016. [77]Maider Muro,Garikoitz Artola,Anton Gorri?o,CarlosAngulo,Akihiko Kimura. Wear and Friction Evaluation of DifferentTool Steels for Hot Stamping[J]. Advances in Materials Science and Engineering,2018,2018. [78]Andre Shihomatsu,Sergio Tonini Button,Iris Bento da Silva. Tribological Behavior of Laser Textured Hot Stamping Dies[J]. Advances in Tribology,2016,2016. [79]Yung-Chou Hung,Yuan-Jen Chang,Chia-Lung Kuo,Jin-ChenHsu,Chao-Ching Ho. Comparison between Laser and Stamping without Die (SWD) for Micro Tapered Hole Forming[J]. Applied Sciences,2016,6(3). [80]Magdalena Cortina,Jon I?aki Arrizubieta,Amaia Calleja,Eneko Ukar,Amaia Alberdi. Case Study to Illustrate the Potential of Conformal Cooling Channels for Hot Stamping Dies Manufactured Using Hybrid Process of Laser Metal Deposition (LMD) and Milling[J]. Metals,2018,8(2). [81]Norman Domeier. Geheime Fotos. Die Kooperation von Associated Press und NS-Regime (1942–1945)[J]. ZeithistorischeForschungen,2017,14 (2017)(2). [82]Robertus Suryo Bisono. STUDI BANDING PELAPISAN MATERIAL SKD11 DENGAN METODE PHYSICAL VAPOUR DEPOSITION DAN THERMAL DIFUSION PADA KOMPONEN INSERT DIES MESIN STAMPING PRESS[J]. Jurnal TeknikMesin,2017,6(1). [83]He Bin,Si Yanglei,Ying Liang,Hu Ping. Research onoptimization design of conformal cooling channels in hot stamping tool based on response surface methodology and multi-objective optimization[J]. MATEC Web of Conferences,2016,80. [84]A.R. Zulhishamuddin, S.N. Aqida. An overview of high thermal conductive hot press forming die material development[J]. Journal of Mechanical Engineering and Sciences,2015,9. [85]NISHINO Souichiro. Damage Evaluation of Coatings for Press Forming Die[J]. JOURNAL OF JAPANESE SOCIETY OFTRIBOLOGISTS,2017,62(8). [86]. Martin Franz, Sebastian Henn und J?rg Weingarten (Hrsg.): BRIC-Investitionen in Deutschland. Chancen und Risiken für Unternehmen und Arbeitnehmer. Forschung aus der Hans-B?ckler-Stiftung 186. Bielefeld: Transcript (2016), 229 S., 24,99 ?.<break> Ulrich Jürgens und Martin Krzywdzinski: New Worlds of Work:Varieties of Work in Car Factories in the BRIC Countries. Oxford: Oxford University Press (2016), 345 pp., 85,24 ?, auch erschienen in deutscher Sprache: Neue Arbeitswelten: Wie sich die Arbeitsrealit?t i[J]. Zeitschrift für Wirtschaftsgeographie,2016,60(3).</break> [87]Ulrich Wyrwa. Dietz Bering, ?War Luther Antisemit?“ Das deutsch-jüdische Verh?ltnis als Trag?die der N?he. Berlin, Berlin University Press 2014[J]. Historische Zeitschrift,2016,302(3). [88]A.W. Or?owicz,M. Mróz,M. Tupaj,A. Trytek,B. Kupiec,M. Korzeniowski,K. Sondej,L. Kozak. The Effect of Carbides Orientation in NC11 Steel on Scratch Susceptibility of Die Inserts Used to Press Stampings for Refractory Shapes[J]. Archives of Foundry Engineering,2016,16(2). [89]. Lutz Musner, Die verletzte Trommel. Der Krieg imslowenisch-triestinischen Karst 1915–1917. Wien, new academic press 2015[J]. Historische Zeitschrift,2017,304(1). [90]Martin Rink. Douglas Porch, Counterinsurgency. Exposing the Myths of the New Way of War, Cambridge [u. a.]: Cambridge University Press 2013, XIII, 434 S., ? 19.99 [ISBN 978-1-107-0738-1] Lukas von Krshiwoblozki, Asymmetrische Kriege. Die Herausforderung für die deutsche Sicherheitspolitik im 21. Jahrhundert, Marburg: Tectum 2015, 796 S., EUR 49,95 [ISBN 978-3-8288-3513-9][J]. Militaergeschichtliche Zeitschrift,2017,76(2). 冲压模具英文参考文献四: [91]Georg Wurzer. Alexander W. Hoerkens, Unter Nazis? Die NS-Ideologie in den abgeh?rten Gespr?chen deutscher Kriegsgefangener in England 1939–1945. Waco, Baylor University Press 2014[J].Historische Zeitschrift,2017,304(2). [92]Martin Moll. Thomas R. Grischany, Der Ostmark treueAlpens?hne. Die Integration der ?sterreicher in die gro?deutsche Wehrmacht, 1938–45, G?ttingen: V&R unipress; Wien: Vienna University Press 2015, 327 S. (=Zeitgeschichte im Kontext, 9), EUR 49,99 [ISBN 978-3-8471-0377-6][J]. MilitaergeschichtlicheZeitschrift,2016,75(2). [93]Eric I. Karchmer. Fighting for Breath : Living Morally and Dying of Cancer in a Chinese Village by Anna Lora‐Wainwright .Honolulu : University of Hawai‘i Press , 2013 . 343 pp.[J]. American Anthropologist,2016,118(4). [94]M. James. Amy Appleford : Learning to Die in London, 1380–1540 . Philadelphia : University of Pennsylvania Press , 2015 ; pp. 336.[J]. Journal of Religious History,2016,40(1). [95]Mohsen Torabi,Ali Reza Eivani,Hamidreza Jafarian,Mohammad Taghi Salehi. Die Design Modification to Improve Workability during Equal Channel Angular Pressing[J]. Advanced EngineeringMaterials,2016,18(8). [96]Sarah D. Phillips. Dying Unneeded : The Cultural Context of the Russian Mortality Crisis by Michelle A. Parsons . Nashville : Vanderbilt University Press , 2014 . 224 pp.[J]. American Anthropologist,2016,118(1). [97]Cassandra Hartblay. Living and Dying in the Contemporary World: A Compendium . Veena Das and Clara Han , eds., Berkeley : University of California Press , 2016 , 896 pp.[J]. Medical Anthropology Quarterly,2017,31(3). [98]WENDY VOGT. The Land of Open Graves: Living and Dying on the Migrant Trail . Jason De Léon , Oakland, CA : University of California Press , 2015 , 384 pp .[J]. City & Society,2017,29(2). [99]MINDY J. MORGAN. Thank You for Dying for Our Country: Commemorative Texts and Performances in Jerusalem . Chaim Noy . New York : Oxford University Press , 2015 . 274 pp.[J]. American Ethnologist,2016,43(4). [100]John Morton. The Aranda's Pepa: An Introduction to Carl Strehlow's Masterpiece Die Aranda‐ und Loritja‐St?mme in Zentral Australien (1907–1920) By Anna Kenny Canberra : ANU E Press . 2013 Pp xix + 310 Price: US$28.00 (paper); free download[J].Oceania,2015,85(2). [101]Stephan Hafenstein,Ewald Werner,Jens Wilzer,WernerTheisen,Sebastian Weber,Christina Sunderk?tter,Mischa Bachmann. Influence of Temperature and Tempering Conditions on Thermal Conductivity of Hot Work Tool Steels for Hot StampingApplications[J]. steel research international,2015,86(12). [102]Jessica Robbins‐Ruszkowski. Dying Unneeded: The Cultural Context of the Russian Mortality Crisis . Michelle A. Parsons , Nashville : Vanderbilt University Press , 2014 , 209 pp.[J]. Medical Anthropology Quarterly,2015,29(3). [103]G. Rosales‐Marín,J. A. Delgadillo,E. T. Tuzcu,C. A.Pérez‐Alonso. Prediction of a piston–die press product using batch population balance model[J]. Asia‐Pacific Journal of Chemical Engineering,2016,11(6). [104]Indivarie Ubhayaratne,Michael P. Pereira,Yong Xiang,Bernard F. Rolfe. Audio signal analysis for tool wear monitoring in sheet metal stamping[J]. Mechanical Systems and Signal Processing,2017,85. [105]A. Ghiotti,S. Bruschi,F. Medea,A. Hamasaiid. Tribological behavior of high thermal conductivity steels for hot stampingtools[J]. Tribology International,2016,97. [106]R. Muvunzi,D.M. Dimitrov,S. Matope,T.M. Harms. Evaluation of Models for Cooling System Design in Hot Stamping Tools[J]. Procedia Manufacturing,2016,7. [107]A. V. Vlasov. Thermomechanical fatigue of dies for hot stamping[J]. Steel in Translation,2016,46(5). [108]In-Kyu Lee,Myeong-Sik Jeong,Sang-Kon Lee,Yong-Jae Cho,Jae-Wook Lee,Pan-Ki Seo,Dae-Cheol Ko,Kyung-Hun Lee,Byung-Min Kim. Wear and fatigue characteristics of new stamping die material for ultra-high-strength steel sheet[J]. International Journal of Precision Engineering and Manufacturing,2015,16(11). [109]Ghasem Azamirad,Behrooz Arezoo. Structural design of stamping die components using bi-directional evolutionary structural optimization method[J]. The International Journal of Advanced Manufacturing Technology,2016,87(1-4). [110]Huiping Li,Lianfang He,Chunzhi Zhang,Hongzhi Cui. Solutionof boundary heat transfer coefficients between hot stamping die and cooling water based on FEM and optimization method[J]. Heat and Mass Transfer,2016,52(4). [111]Cox Alyson. Lydia Dugdale (ed.): Dying in the twenty-first century: toward a new ethical framework for the art of dying well : MIT Press, 2015, XII + 224 pp, $35.00 (hardcover), ISBN: 9780262029124.[J]. Theoretical medicine and bioethics,2016,37(5). [112]Sachin Salunkhe,Deepak Panghal,Shailendra Kumar,H M A Hussein. An expert system for process planning of sheet metal parts produced on compound die for use in stamping industries[J].Sādhanā,2016,41(8). [113]Vitor L. Sordi,Anibal A. Mendes Filho,Gustavo T.Valio,Phillip Springer,Jose B. Rubert,Maurizio Ferrante. Equal-channel angular pressing: influence of die design on pressure forces, strain homogeneity, and corner gap formation[J]. Journal of Materials Science,2016,51(5). [114]Hongxun Wang,Peng Jiang,Weifang Zhang,Yaozhong Zhang,Tong Song. Failure analysis of large press die holder[J]. Engineering Failure Analysis,2016,64. [115]Ping Hu,Bin He,Liang Ying. Numerical investigation oncooling performance of hot stamping tool with various channel designs[J]. Applied Thermal Engineering,2016,96. [116]Bin He,Liang Ying,Xianda Li,Ping Hu. Optimal design of longitudinal conformal cooling channels in hot stamping tools[J]. Applied Thermal Engineering,2016,106. [117]Jens Fruhstorfer,Stefan Barlag,Martin Thalheim,Leandro Sch?ttler,Christos G. Aneziris. Upright die pressing of refractory hollowware for steel ingot casting with reduced clay content[J]. Ceramics International,2016,42(2). [118]Huiping Li,Lianfang He,Chunzhi Zhang,Hongzhi Cui. Research on the effect of boundary pressure on the boundary heat transfer coefficients between hot stamping die and boron steel[J]. International Journal of Heat and Mass Transfer,2015,91. [119]Dekuan Liu,Shuang Jin,Hu Xu. Humanoid Based Intelligence Control Strategy of Plastic Cement Die Press Work-Piece Forming Process for Polymer Plastics[J]. Journal of Materials Science and Chemical Engineering,2016,04(06). [120]Russell David. Closing the gaps on efforts to improve healthcare quality at the end-of-life A review of Dying in America: Improving Quality and Honoring Individual Preferences Near the Endof Life by the Committee on Approaching Death: Addressing Key End of Life Issues. Washington, DC: National Academies Press, 2014. 638 pages. (ISBN: 978-0309303101). $74.95 for print copy; available free online (see References).[J]. Death studies,2016,40(1). 以上就是关于冲压模具英文参考文献,希望对你有所帮助。
冲压模具外文文献教程文件
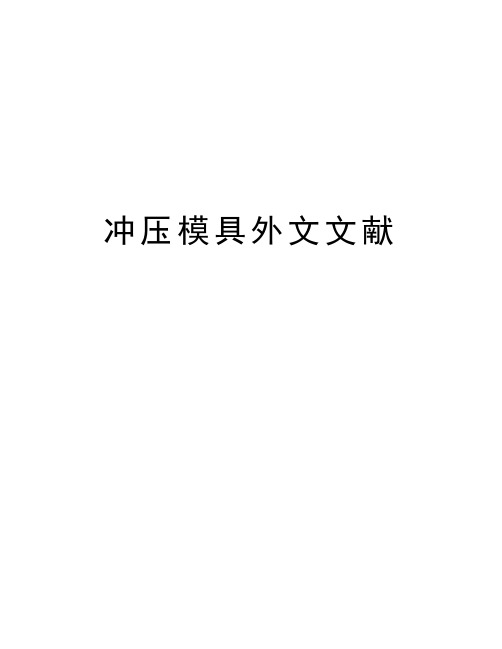
冲压模具外文文献Progressive DieProgressive die has the following advantages1) Class into the module is multi-process dies, in a mold can include punching, bending, forming and drawing a variety of multi-pass process, with a higher than the compound die labor productivity, but also can produce quite complex stampings;2) Progressive Die Operation Security, because staff do not have to enter the danger zone;3) Class Progressive Die Design, The process can be distributed. Do not focus on one station , there is no Compound Dies "Minimum wall thickness" problem. Therefore relatively high mold strength, longer life expectancy.4) Progressive Die Easy Automation That is easy to Automaticfeeding ,Autoout of parts Automatic lamination;5) Class Progressive die can be High-speed press production, because the workpiece can be directly down the drain and waste;6) Use Class Progressive die can be Reduce the presses, semi-finished products to reduce transport. Workshop area and storage space can be greatly reduced.Progressive Dies The disadvantage is that complex structure, manufacturing of high precision, long life cycle and high costs. Because of progressive die is a To the workpiece, the shape of successive out, each punch has a positioning error, is more difficult to maintain stability in the workpiece, the relative position of the one-off appearance. However, high precision parts, not all contours of all, the shape relative position requirements are high, you can be washed in the shape of the same station, on the relative position of demanding the same time, out of this part of the profile, thus ensuring precision parts.First, process pieces of carry approachProcesses and the determination of nesting is of the progressive die design a very important link. In considering the processes and nesting, we must first consider the process method of carriage parts.Bending parts there are two main ways to carry:1) Blanking station in the upper and lower pressure, so that after blanking process pieces and re-pressed into the material inside. Generally only about access to material thickness of thel/3, but has enough to process pieces with the material sent to the next process, within the workpiece in the working procedure have all been pressed into the material inside the remnant. Beyond that, after process pieces are washed curved shape, until the last escape from the Strip. The drop in this way conveying pairs of thick material is very effective, because the thin material easy to bagging, wrinkles, or bent, thus blanking out the flat blank song, not with the advance of material and stops in a station caused the accident.Simple blanking progressive die, sometimes in order to ensure that the workpiece is flat and has also taken off after the re-feed materials putpressure on people within the approach, in the latter process to workpiece pushed. Because blanking after being re-pressed into the workpiece can not be material in the thickness direction all entered the hole, so in the blanking die station after the plane, to the corresponding lower.2) Rush to need to bend some of the surrounding material, the rest of the parts remain in the article (Volume)Materials, there is no separation. As the hub of to the material, You may need to spend a long Progress in distance delivery.Second, the principle of work arrangements1)Blanking the workpiece to avoid the use of complex shapes convex mode. Rather more than the increase a process to simplify the convex mode shapes.2)"U"-shaped pieces can be divided into two out, as Figure7--76As shown in order to avoid material stretched, out of Workpiece dimensions vary.Figure7--76 U shaped pieces of curved process3)In the asymmetric bending, the workpiece slide easily can be shown in Figure7—77shown with teeth inserts were inserts into the bend Convex Mold and roof in order to prevent the workpiece sliding. The main disadvantage of this method is the a)After the procedure b)pre-process workpiece plane with prints. Also available on the heat treatment before Convex Mold and roof pre-perforated, after tryout after the sheet metal through the tryout will be two holes without sliding inlay Ping . If sliding is used tooth inserts.Figure7--77 To prevent the sheet metal bending generated when sliding1- Bending Convex Die 2- Cut off Convex Die 3- Roof 4- With teeth inserts 4) Bending or deep drawing of the workpiece, high-quality plastic surgery procedures should be added.5) Waste, such as continuous, should increase the cutting process, using waste cutter cut. Automatic press itself, as some waste cutter, you do not have to die to consider.6) Can be countersunk head hole punching. Figure7—78 shows the first hole punching of the workpiece . When clamping the punch die Xiaoping Tou both plane and concave hole stretch of artificial parts, and contact with each other in order to prevent inward deformation of holes. Clamping direction due to the strict size requirements, so the punch assembly when subject to a high degree of repair potential. Also can be used as shown in Figure 7-79 height adjustment body punch. The upper punch 3 face, contact with the slider 2. Slider right-hand side has opened a T-shaped slot to accommodate the screw 5 in the head. Rotating screw 5, then move along the slider 2. As the slider 2 and the mold base 4 in order to ramp contact with each other, while the punch 3 in the fixed plate is sliding in with l, consequent punch in the direction of the location of mold can be adjusted. Adjusted with the nut 6 fixed.Figure7--78 Stamp shen head hole1—Convex Die 2- DieFigure7--79 Punch height adjustment body1- Fixed Plate 2-Slider 3- Punch 4- On the mold base 5- Screw6- Nut7) There are strict requirements of local relative position within the shape, should consider the possibility of the same station on the out, in order to maintain accuracy. If there are really difficult to be broken down into two working bits. Be better placed in two adjacent stations.Third, the principle of stamping operations sequencing1)For pure blanking progressive dies, in principle, the first ,punch, followed by re-punching shape I expected, the final and then washed down from the Strip on the integrity of the workpiece. Carrier should be maintained of material of sufficient strength, can be accurate when sent to press.2)For the blanking bending progressive die should be washed before cut off part of the hole and bend the shape I expected, and then bending, and finally washed near the curved edge holes and the side hole-bit accuracy of the sidewall holes. Washed down by the final separation of parts.3) Drawing for the progressive die stamping , first make arrangement to cut processes, further drawing, the final washed down from the article on the workpiece material.4)For with the deep drawing, bending stamping parts, the first drawing, then I punched the surrounding material, followed by bending plus.5)For stamping with a stamping parts, in order to facilitate the metal flow and reduce the stamping force, stamping parts of neighboring I expected to be an appropriate resection, and then arrange stamping. The final re -Precision Die-Cut materials .If there are holes on the embossing position, in principle, should be embossed after the punching.6)For with the stamping, bending and stamping workpiece, in principle, is the first imprint ,And then punching Yu Liu, And then bending process.Fourth, nesting layout1) Nesting mapping, you can start with plane launch fig start, right designed to blanking station, left the design forming station. Step by step according to the actual situation after the amendment.2) Consider increasing the intensity to be an empty station molds. Continuous drawing more frequently when the first drawing after being a backup space industry in order to increase the number of drawing. High precision, complex shape of the workpiece should be less to set an empty station. Step away from the mold is greater than 16mm When more than set up an empty station. Interval accuracy The poor should not be easily added an empty station.3) Decided to process pieces of carry approach.4) Note that material rolling direction. Rolling direction affects not only the economic effects of nesting, but also affect the performance of the workpiece.5) Burr bending parts should be located in inside.6) Thin material used Guide is being sold, But do not side edge trimming. For thick material or heavy section materials, in order to avoid guide is being sold off the need to side edge trimming.7) According to the workpiece dimensions and the scale of production to determine a shape one pieces two documents or four parts, or more pieces.8) Stamping process does not allow any scattered debris left on the die surface.9) Residual material on the press to consider the possibility of other parts.。
冲压模具成型外文翻译参考文献
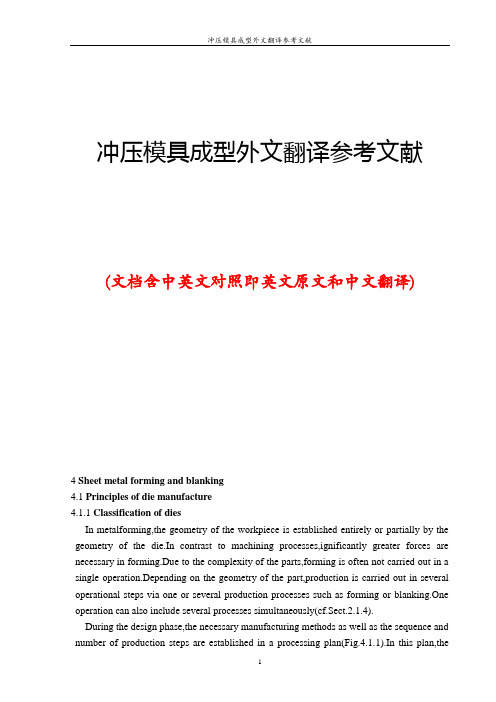
冲压模具成型外文翻译参考文献(文档含中英文对照即英文原文和中文翻译)4 Sheet metal forming and blanking4.1 Principles of die manufacture4.1.1 Classification of diesIn metalforming,the geometry of the workpiece is established entirely or partially by the geometry of the die.In contrast to machining processes,ignificantly greater forces are necessary in forming.Due to the complexity of the parts,forming is often not carried out in a single operation.Depending on the geometry of the part,production is carried out in several operational steps via one or several production processes such as forming or blanking.One operation can also include several processes simultaneously(cf.Sect.2.1.4).During the design phase,the necessary manufacturing methods as well as the sequence and number of production steps are established in a processing plan(Fig.4.1.1).In this plan,theavailability of machines,the planned production volumes of the part and other boundary conditions are taken into account.The aim is to minimize the number of dies to be used while keeping up a high level of operational reliability.The parts are greatly simplified right from their design stage by close collaboration between the Part Design and Production Departments in order to enable several forming and related blanking processes to be carried out in one forming station.Obviously,the more operations which are integrated into a single die,the more complex the structure of the die becomes.The consequences are higher costs,a decrease in output and a lower reliability.Fig.4.1.1 Production steps for the manufacture of an oil sumpTypes of diesThe type of die and the closely related transportation of the part between dies is determined in accordance with the forming procedure,the size of the part in question and the production volume of parts to be produced.The production of large sheet metal parts is carried out almost exclusively using single sets of dies.Typical parts can be found in automotive manufacture,the domestic appliance industry and radiator production.Suitable transfer systems,for example vacuum suction systems,allow the installation of double-action dies in a sufficiently large mounting area.In this way,for example,the right and left doors of a car can be formed jointly in one working stroke(cf.Fig.4.4.34).Large size single dies are installed in large presses.The transportation of the parts from oneforming station to another is carried out mechanically.In a press line with single presses installed one behind the other,feeders or robots can be used(cf.Fig.4.4.20 to 4.4.22),whilst in large-panel transfer presses,systems equipped with gripper rails(cf.Fig.4.4.29)or crossbar suction systems(cf.Fig.4.4.34)are used to transfer the parts.Transfer dies are used for the production of high volumes of smaller and medium size parts(Fig.4.1.2).They consist of several single dies,which are mounted on a common base plate.The sheet metal is fed through mostly in blank form and also transported individually from die to die.If this part transportation is automated,the press is called a transfer press.The largest transfer dies are used together with single dies in large-panel transfer presses(cf.Fig.4.4.32).In progressive dies,also known as progressive blanking dies,sheet metal parts are blanked in several stages;generally speaking no actual forming operation takes place.The sheet metal is fed from a coil or in the form of metal ing an appropriate arrangement of the blanks within the available width of the sheet metal,an optimal material usage is ensured(cf.Fig.4.5.2 to 4.5.5). The workpiece remains fixed to the strip skeleton up until the laFig.4.1.2 Transfer die set for the production of an automatic transmission for an automotive application-st operation.The parts are transferred when the entire strip is shifted further in the work flow direction after the blanking operation.The length of the shift is equal to the center line spacing of the dies and it is also called the step width.Side shears,very precise feeding devices or pilot pins ensure feed-related part accuracy.In the final production operation,the finished part,i.e.the last part in the sequence,is disconnected from the skeleton.A field of application for progressive blanking tools is,for example,in the production of metal rotors or stator blanks for electric motors(cf.Fig.4.6.11 and 4.6.20).In progressive compound dies smaller formed parts are produced in several sequential operations.In contrast to progressive dies,not only blanking but also forming operations areperformed.However, the workpiece also remains in the skeleton up to the last operation(Fig.4.1.3 and cf.Fig.4.7.2).Due to the height of the parts,the metal strip must be raised up,generally using lifting edges or similar lifting devices in order to allow the strip metal to be transported mechanically.Pressed metal parts which cannot be produced within a metal strip because of their geometrical dimensions are alternatively produced on transfer sets.Fig.4.1.3 Reinforcing part of a car produced in a strip by a compound die setNext to the dies already mentioned,a series of special dies are available for special individual applications.These dies are,as a rule,used separately.Special operations make it possible,however,for special dies to be integrated into an operational Sequence.Thus,for example,in flanging dies several metal parts can be joined together positively through the bending of certain metal sections(Fig.4.1.4and cf.Fig.2.1.34).During this operation reinforcing parts,glue or other components can be introduced.Other special dies locate special connecting elements directly into the press.Sorting and positioning elements,for example,bring stamping nuts synchronised with the press cycles into the correct position so that the punch heads can join them with the sheet metal part(Fig.4.1.5).If there is sufficient space available,forming and blanking operations can be carried out on the same die.Further examples include bending,collar-forming,stamping,fine blanking,wobble blanking and welding operations(cf.Fig.4.7.14 and4.7.15).Fig.4.1.4 A hemming dieFig.4.1.5 A pressed part with an integrated punched nut4.1.2 Die developmentTraditionally the business of die engineering has been influenced by the automotive industry.The following observations about the die development are mostly related to body panel die construction.Essential statements are,however,made in a fundamental context,so that they are applicable to all areas involved with the production of sheet-metal forming and blanking dies.Timing cycle for a mass produced car body panelUntil the end of the 1980s some car models were still being produced for six to eight years more or less unchanged or in slightly modified form.Today,however,production time cycles are set for only five years or less(Fig.4.1.6).Following the new different model policy,the demands ondie makers have also changed prehensive contracts of much greater scope such as Simultaneous Engineering(SE)contracts are becoming increasingly common.As a result,the die maker is often involved at the initial development phase of the metal part as well as in the planning phase for the production process.Therefore,a muchbroader involvement is established well before the actual die development is initiated.Fig.4.1.6 Time schedule for a mass produced car body panelThe timetable of an SE projectWithin the context of the production process for car body panels,only a minimal amount of time is allocated to allow for the manufacture of the dies.With large scale dies there is a run-up period of about 10 months in which design and die try-out are included.In complex SE projects,which have to be completed in 1.5 to 2 years,parallel tasks must be carried out.Furthermore,additional resources must be provided before and after delivery of the dies.These short periods call for pre-cise planning,specific know-how,available capacity and the use of the latest technological and communications systems.The timetable shows the individual activities during the manufacturing of the dies for the production of the sheet metal parts(Fig.4.1.7).The time phases for large scale dies are more or less similar so that this timetable can be considered to be valid in general.Data record and part drawingThe data record and the part drawing serve as the basis for all subsequent processing steps.They describe all the details of the parts to be produced. The information given in theFig.4.1.7 Timetable for an SE projectpart drawing includes: part identification,part numbering,sheet metal thickness,sheet metal quality,tolerances of the finished part etc.(cf.Fig.4.7.17).To avoid the production of physical models(master patterns),the CAD data should describe the geometry of the part completely by means of line,surface or volume models.As a general rule,high quality surface data with a completely filleted and closed surface geometry must be made available to all the participants in a project as early as possible.Process plan and draw developmentThe process plan,which means the operational sequence to be followed in the production of the sheet metal component,is developed from the data record of the finished part(cf.Fig.4.1.1).Already at this point in time,various boundary conditions must be taken into account:the sheet metal material,the press to be used,transfer of the parts into the press,the transportation of scrap materials,the undercuts as well as thesliding pin installations and their adjustment.The draw development,i.e.the computer aided design and layout of the blank holder area of the part in the first forming stage–if need bealso the second stage–,requires a process planner with considerable experience(Fig.4.1.8).In order to recognize and avoid problems in areas which are difficult to draw,it is necessary to manufacture a physical analysis model of the draw development.With this model,theforming conditions of the drawn part can be reviewed and final modifications introduced,which are eventually incorporated into the data record(Fig.4.1.9).This process is being replaced to some extent by intelligent simulation methods,through which the potential defects of the formed component can be predicted and analysed interactively on the computer display.Die designAfter release of the process plan and draw development and the press,the design of the die can be started.As a rule,at this stage,the standards and manufacturing specifications required by the client must be considered.Thus,it is possible to obtain a unified die design and to consider the particular requests of the customer related to warehousing of standard,replacement and wear parts.Many dies need to be designed so that they can be installed in different types of presses.Dies are frequently installed both in a production press as well as in two different separate back-up presses.In this context,the layout of the die clamping elements,pressure pins and scrap disposal channels on different presses must be taken into account.Furthermore,it must be noted that drawing dies working in a single-action press may be installed in a double-action press(cf.Sect.3.1.3 and Fig.4.1.16).Fig.4.1.8 CAD data record for a draw developmentIn the design and sizing of the die,it is particularly important to consider the freedom of movement of the gripper rail and the crossbar transfer elements(cf.Sect.4.1.6).These describe the relative movements between the components of the press transfer system and the die components during a complete press working stroke.The lifting movement of the press slide,the opening and closing movements of the gripper rails and the lengthwise movement of the whole transfer are all superimposed.The dies are designed so that collisions are avoided and a minimum clearance of about 20 mm is set between all the moving parts.4 金属板料的成形及冲裁4. 模具制造原理4.1.1模具的分类在金属成形的过程中,工件的几何形状完全或部分建立在模具几何形状的基础上的。
冲压模具成型外文翻译参考文献
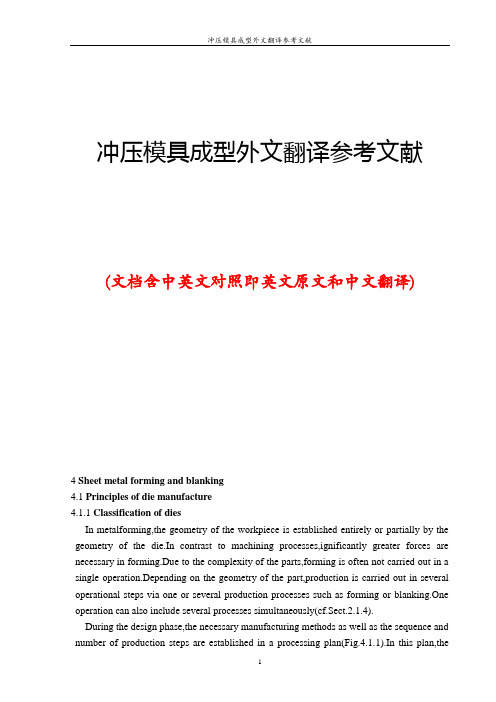
冲压模具成型外文翻译参考文献(文档含中英文对照即英文原文和中文翻译)4 Sheet metal forming and blanking4.1 Principles of die manufacture4.1.1 Classification of diesIn metalforming,the geometry of the workpiece is established entirely or partially by the geometry of the die.In contrast to machining processes,ignificantly greater forces are necessary in forming.Due to the complexity of the parts,forming is often not carried out in a single operation.Depending on the geometry of the part,production is carried out in several operational steps via one or several production processes such as forming or blanking.One operation can also include several processes simultaneously(cf.Sect.2.1.4).During the design phase,the necessary manufacturing methods as well as the sequence and number of production steps are established in a processing plan(Fig.4.1.1).In this plan,theavailability of machines,the planned production volumes of the part and other boundary conditions are taken into account.The aim is to minimize the number of dies to be used while keeping up a high level of operational reliability.The parts are greatly simplified right from their design stage by close collaboration between the Part Design and Production Departments in order to enable several forming and related blanking processes to be carried out in one forming station.Obviously,the more operations which are integrated into a single die,the more complex the structure of the die becomes.The consequences are higher costs,a decrease in output and a lower reliability.Fig.4.1.1 Production steps for the manufacture of an oil sumpTypes of diesThe type of die and the closely related transportation of the part between dies is determined in accordance with the forming procedure,the size of the part in question and the production volume of parts to be produced.The production of large sheet metal parts is carried out almost exclusively using single sets of dies.Typical parts can be found in automotive manufacture,the domestic appliance industry and radiator production.Suitable transfer systems,for example vacuum suction systems,allow the installation of double-action dies in a sufficiently large mounting area.In this way,for example,the right and left doors of a car can be formed jointly in one working stroke(cf.Fig.4.4.34).Large size single dies are installed in large presses.The transportation of the parts from oneforming station to another is carried out mechanically.In a press line with single presses installed one behind the other,feeders or robots can be used(cf.Fig.4.4.20 to 4.4.22),whilst in large-panel transfer presses,systems equipped with gripper rails(cf.Fig.4.4.29)or crossbar suction systems(cf.Fig.4.4.34)are used to transfer the parts.Transfer dies are used for the production of high volumes of smaller and medium size parts(Fig.4.1.2).They consist of several single dies,which are mounted on a common base plate.The sheet metal is fed through mostly in blank form and also transported individually from die to die.If this part transportation is automated,the press is called a transfer press.The largest transfer dies are used together with single dies in large-panel transfer presses(cf.Fig.4.4.32).In progressive dies,also known as progressive blanking dies,sheet metal parts are blanked in several stages;generally speaking no actual forming operation takes place.The sheet metal is fed from a coil or in the form of metal ing an appropriate arrangement of the blanks within the available width of the sheet metal,an optimal material usage is ensured(cf.Fig.4.5.2 to 4.5.5). The workpiece remains fixed to the strip skeleton up until the laFig.4.1.2 Transfer die set for the production of an automatic transmission for an automotive application-st operation.The parts are transferred when the entire strip is shifted further in the work flow direction after the blanking operation.The length of the shift is equal to the center line spacing of the dies and it is also called the step width.Side shears,very precise feeding devices or pilot pins ensure feed-related part accuracy.In the final production operation,the finished part,i.e.the last part in the sequence,is disconnected from the skeleton.A field of application for progressive blanking tools is,for example,in the production of metal rotors or stator blanks for electric motors(cf.Fig.4.6.11 and 4.6.20).In progressive compound dies smaller formed parts are produced in several sequential operations.In contrast to progressive dies,not only blanking but also forming operations areperformed.However, the workpiece also remains in the skeleton up to the last operation(Fig.4.1.3 and cf.Fig.4.7.2).Due to the height of the parts,the metal strip must be raised up,generally using lifting edges or similar lifting devices in order to allow the strip metal to be transported mechanically.Pressed metal parts which cannot be produced within a metal strip because of their geometrical dimensions are alternatively produced on transfer sets.Fig.4.1.3 Reinforcing part of a car produced in a strip by a compound die setNext to the dies already mentioned,a series of special dies are available for special individual applications.These dies are,as a rule,used separately.Special operations make it possible,however,for special dies to be integrated into an operational Sequence.Thus,for example,in flanging dies several metal parts can be joined together positively through the bending of certain metal sections(Fig.4.1.4and cf.Fig.2.1.34).During this operation reinforcing parts,glue or other components can be introduced.Other special dies locate special connecting elements directly into the press.Sorting and positioning elements,for example,bring stamping nuts synchronised with the press cycles into the correct position so that the punch heads can join them with the sheet metal part(Fig.4.1.5).If there is sufficient space available,forming and blanking operations can be carried out on the same die.Further examples include bending,collar-forming,stamping,fine blanking,wobble blanking and welding operations(cf.Fig.4.7.14 and4.7.15).Fig.4.1.4 A hemming dieFig.4.1.5 A pressed part with an integrated punched nut4.1.2 Die developmentTraditionally the business of die engineering has been influenced by the automotive industry.The following observations about the die development are mostly related to body panel die construction.Essential statements are,however,made in a fundamental context,so that they are applicable to all areas involved with the production of sheet-metal forming and blanking dies.Timing cycle for a mass produced car body panelUntil the end of the 1980s some car models were still being produced for six to eight years more or less unchanged or in slightly modified form.Today,however,production time cycles are set for only five years or less(Fig.4.1.6).Following the new different model policy,the demands ondie makers have also changed prehensive contracts of much greater scope such as Simultaneous Engineering(SE)contracts are becoming increasingly common.As a result,the die maker is often involved at the initial development phase of the metal part as well as in the planning phase for the production process.Therefore,a muchbroader involvement is established well before the actual die development is initiated.Fig.4.1.6 Time schedule for a mass produced car body panelThe timetable of an SE projectWithin the context of the production process for car body panels,only a minimal amount of time is allocated to allow for the manufacture of the dies.With large scale dies there is a run-up period of about 10 months in which design and die try-out are included.In complex SE projects,which have to be completed in 1.5 to 2 years,parallel tasks must be carried out.Furthermore,additional resources must be provided before and after delivery of the dies.These short periods call for pre-cise planning,specific know-how,available capacity and the use of the latest technological and communications systems.The timetable shows the individual activities during the manufacturing of the dies for the production of the sheet metal parts(Fig.4.1.7).The time phases for large scale dies are more or less similar so that this timetable can be considered to be valid in general.Data record and part drawingThe data record and the part drawing serve as the basis for all subsequent processing steps.They describe all the details of the parts to be produced. The information given in theFig.4.1.7 Timetable for an SE projectpart drawing includes: part identification,part numbering,sheet metal thickness,sheet metal quality,tolerances of the finished part etc.(cf.Fig.4.7.17).To avoid the production of physical models(master patterns),the CAD data should describe the geometry of the part completely by means of line,surface or volume models.As a general rule,high quality surface data with a completely filleted and closed surface geometry must be made available to all the participants in a project as early as possible.Process plan and draw developmentThe process plan,which means the operational sequence to be followed in the production of the sheet metal component,is developed from the data record of the finished part(cf.Fig.4.1.1).Already at this point in time,various boundary conditions must be taken into account:the sheet metal material,the press to be used,transfer of the parts into the press,the transportation of scrap materials,the undercuts as well as thesliding pin installations and their adjustment.The draw development,i.e.the computer aided design and layout of the blank holder area of the part in the first forming stage–if need bealso the second stage–,requires a process planner with considerable experience(Fig.4.1.8).In order to recognize and avoid problems in areas which are difficult to draw,it is necessary to manufacture a physical analysis model of the draw development.With this model,theforming conditions of the drawn part can be reviewed and final modifications introduced,which are eventually incorporated into the data record(Fig.4.1.9).This process is being replaced to some extent by intelligent simulation methods,through which the potential defects of the formed component can be predicted and analysed interactively on the computer display.Die designAfter release of the process plan and draw development and the press,the design of the die can be started.As a rule,at this stage,the standards and manufacturing specifications required by the client must be considered.Thus,it is possible to obtain a unified die design and to consider the particular requests of the customer related to warehousing of standard,replacement and wear parts.Many dies need to be designed so that they can be installed in different types of presses.Dies are frequently installed both in a production press as well as in two different separate back-up presses.In this context,the layout of the die clamping elements,pressure pins and scrap disposal channels on different presses must be taken into account.Furthermore,it must be noted that drawing dies working in a single-action press may be installed in a double-action press(cf.Sect.3.1.3 and Fig.4.1.16).Fig.4.1.8 CAD data record for a draw developmentIn the design and sizing of the die,it is particularly important to consider the freedom of movement of the gripper rail and the crossbar transfer elements(cf.Sect.4.1.6).These describe the relative movements between the components of the press transfer system and the die components during a complete press working stroke.The lifting movement of the press slide,the opening and closing movements of the gripper rails and the lengthwise movement of the whole transfer are all superimposed.The dies are designed so that collisions are avoided and a minimum clearance of about 20 mm is set between all the moving parts.4 金属板料的成形及冲裁4. 模具制造原理4.1.1模具的分类在金属成形的过程中,工件的几何形状完全或部分建立在模具几何形状的基础上的。
冲压模具冷冲压加工毕业论文中英文对照资料外文翻译文献
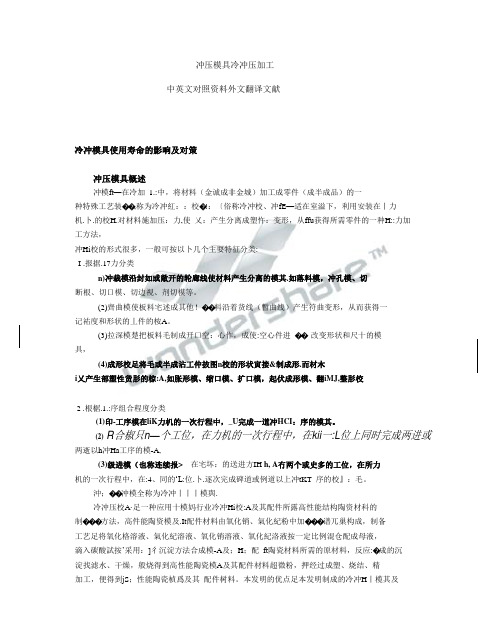
冲压模具冷冲压加工中英文对照资料外文翻译文献冷冲模具使用寿命的影响及对策冲压模具概述冲模ft—在冷加_1.:中,将材料(金诚成非金城)加工成零件(成半成品)的一种特殊工艺装��,称为冷冲紅::校�!:〔俗称冷冲校、冲fE—适在室溢下,利用安装在丨力机.卜.的校H.对材料施加压:力,使_乂:产生分离成塑忤:变形,从ffu获得所需零件的一种H::力加工方法,冲Hi校的形式很多,一般可按以卜几个主耍特征分类:I .报据.17力分类n)冲裁模沿封如或敞开的轮廊线使材料产生分离的模其.如落料模,冲孔模、切断根、切口模、切边視、剂切模等。
(2)齊曲模使板料宅述成其他!��料沿着货线(暫曲线)产生符曲变形,从而获得一记祐度和形状的丄件的桉A。
(3)拉深模楚把板料毛制成开口空:心作,成使:空心件进_��_改变形状和尺十的模具,(4)成形校足将毛或半成沾工仲抜图n校的形状寅接&制成形.而材木i乂产生部塑性货肜的椋:A,如胀形模、缩口模、扩口模,起伏成形模、翻iMJ,整肜校2 .根椐.1.:序组合程度分类(1)印-工序模在liK力机的一次行程中,_U完成一道冲HCI:序的模其。
(2) R合椒只n—个工位,在力机的一次行程中,在kii一:L位上同时完成两进或两逝以h冲Ha工序的模-A,(3)级进模(也称连续报>在宅坏:的送进方IH h, A冇两个或史多的工位,在所力机的一次行程中,在:4、同的‘L:位.卜.逐次完成碑道或例道以上冲tKT_序的校』:毛。
沖;��冲模全称为冷冲丨丨丨模與.冷冲压校A·足一种应用十模妈行业冷冲Hi校:A及其配件所露高性能结构陶资材科的制���方法,高件能陶资模及.It配件材料由氧化销、氣化紀粉中加���谱兀巢构成,制备工艺足将氧化格溶液、氣化紀溶液、氧化销溶液、氧化紀洛液按一定比例混仓配成母液,滴入碳酸試按’采用:]彳沉淀方法合成模-A及;H;配_ft陶瓷材料所需的原材料,反应:�成的沉淀找滤水、干燥,般烧得到高性能陶瓷模A及其配件材料超微粉,押经过成塑、烧结、精加工,便得到jS;性能陶瓷楨爲及其_配件树料。
冲压模具外文英语文献翻译
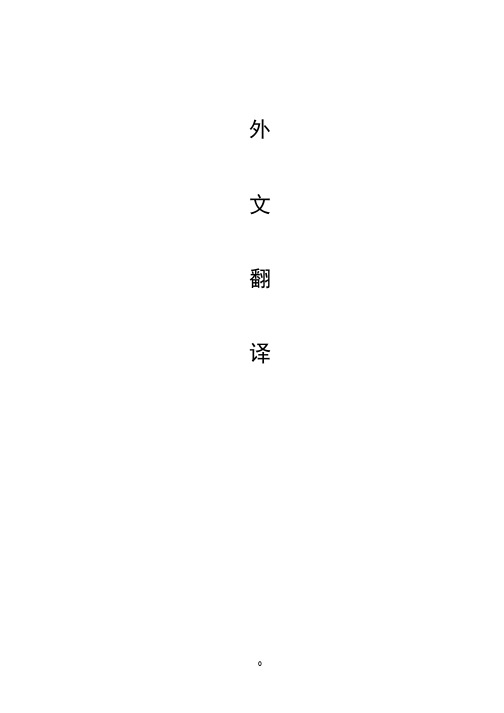
外文翻译Heat Treatment of Die and Mould Oriented Concurrent Design LI Xiong,ZHANG Hong-bing,RUAN Xue —yu,LUO Zhong —hua,ZHANG YanTraditional die and mould design,mainly by experience or semi —experience ,is isolated from manufacturing process.Before the design is finalized ,the scheme of die and mould is usually modified time and again ,thus some disadvantages come into being,such as long development period,high cost and uncertain practical effect.Due to strong desires for precision,service life,development period and cost,modern die and mould should be designed and manufactured perfectly.Therefore more and more advanced technologies and innovations have been applied,for example,concurrent engineering,agile manufacturing virtual manufacturing,collaborative design,etc.Heat treatment of die and mould is as important as design,manufacture and assembly because it has a vital effect on manufacture ,assembly and service life .Design and manufacture of die and mould have progressed rapidly ,but heat treatment lagged seriously behind them .As die and mould industry develops ,heat treatment must ensure die and mould there are good state of manufacture ,assembly and wear —resistant properties by request. Impertinent heat treatment can influence die and mould manufacturing such as over —hard and —soft and assembly .Traditionally the heat treatment process was made out according to the methods and properties brought forward Abstract:Many disadvantages exist in the traditional die design method which belongsto serial pattern. It is well known that heat treatment is highly important to thedies. A new idea of concurrent design for heat treatment process of die andmould was developed in order to overcome the existent shortcomings of heattreatment process. Heat treatment CAD/CAE was integrated with concurrentcircumstance and the relevant model was built. These investigations canremarkably improve efficiency, reduce cost and ensure quality of R and D forproducts.Key words:die design; heat treatment; mouldby designer.This could make the designers of die and mould and heat treatment diverge from each other,for the designers of die and mould could not fully realize heat treatment process and materials properties,and contrarily the designers rarely understood the service environment and designing thought. These divergences will impact the progress of die and mould to a great extent. Accordingly,if the process design of heat treatment is considered in the early designing stage,the aims of shortening development period,reducing cost and stabilizing quality will be achieved and the sublimation of development pattern from serial to concurrent will be realized.Concurrent engineering takes computer integration system as a carrier,at the very start subsequent each stage and factors have been considered such as manufacturing,heat treating,properties and so forth in order to avoid the error.The concurrent pattern has dismissed the defect of serial pattern,which bring about a revolution against serial pattern.In the present work.the heat treatment was integrated into the concurrent circumstance of the die and mould development,and the systemic and profound research was performed.1 Heat Treatment Under Concurrent CircumstanceThe concurrent pattern differs ultimately from the serial pattern(see Fig.1).With regard to serial pattern,the designers mostly consider the structure and function of die and mould,yet hardly consider the consequent process,so that the former mistakes are easily spread backwards.Meanwhile,the design department rarely communicates with the assembling,cost accounting and sales departments.These problems certainly will influence the development progress of die and mould and the market foreground.Whereas in the concurrent pattern,the relations among departments are close,the related departments all take part in the development progress of die and mould and have close intercommunion with purchasers.This is propitious to elimination of the conflicts between departments,increase the efficiency and reduce the cost.Heat treatment process in the concurrent circumstance is made out not after blueprint and workpiece taken but during die and mould designing.In this way,it is favorable to optimizing the heat treatment process and making full use of the potential of the materials.2 Integration of Heat Treatment CAD/CAE for Die and MouldIt can be seen from Fig.2 that the process design and simulation of heat treatment are the core of integration frame.After information input via product design module and heat treatment process generated via heat treatment CAD and heat treatment CAE module will automatically divide the mesh for parts drawing,simulation temperature field microstructure analysis after heat—treatment and the defect of possible emerging (such as overheat,over burning),and then the heat treatment process is judged if the optimization is made according to the result reappeared by stereoscopic vision technology.Moreover tool and clamping apparatus CAD and CAM are integrated into this system.The concurrent engineering based integration frame can share information with other branch.That makes for optimizing the heat treatment process and ensuring the process sound.2.1 3-D model and stereoscopic vision technology for heat treatmentThe problems about materials,structure and size for die and mould can be discovered as soon as possible by 3-D model for heat treatment based on the shape of die and mould.Modeling heating condition and phase transformation condition for die and mould during heat treatment are workable,because it has been broken through for the calculation of phase transformation thermodynamics,phase transformation kinetics,phase stress,thermal stress,heat transfer,hydrokinetics etc.For example,3-D heat—conducting algorithm models for local heating complicated impression and asymmetric die and mould,and M ARC software models for microstructure transformation was used.Computer can present the informations of temperature,microstructure and stress at arbitrary time and display the entire transformation procedure in the form of 3-D by coupling temperature field,microstructure field and stress field.If the property can be coupled,various partial properties can be predicted by computer.2.2 Heat treatment process designDue to the special requests for strength,hardness,surface roughness and distortion during heat treatment for die and mould,the parameters including quenching medium type,quenching temperature and tempering temperature and time,must be properlyselected,and whether using surface quenching or chemical heat treatment the parameters must be rightly determined.It is difficult to determine the parameters by computer fully.Since computer technology develops quickly in recent decades,the difficulty with large—scale calculation has been overcome.By simulating and weighing the property,the cost and the required period after heat treatment.it is not difficult to optimize the heat treatment process.2.3 Data base for heat treatmentA heat treatment database is described in Fig.3.The database is the foundation of making out heat treatment process.Generally,heat treatment database is divided into materials database and process database.It is an inexorable trend to predict the property by materials and process.Although it is difficult to establish a property database,it is necessary to establish the database by a series of tests.The materials database includes steel grades,chemical compositions,properties and home and abroad grades parallel tables.The process database includes heat treatment criterions,classes,heat preservation time and cooling velocity.Based on the database,heat treatment process can be created by inferring from rules.2.4 Tool and equipment for heat treatmentAfter heat treatment process is determined,tool and equipment CAD/CAE systemtransfers the information about design and manufacture to the numerical control device.Through rapid tooling prototype,the reliability of tool and the clamping apparatus can be judged.The whole procedure is transferred by network,in which there is no man—made interference.3 Key Technique3.1 Coupling of temperature,microstructure,stress and propertyHeat treatment procedure is a procedure of temperature-microstructure—stress interaction.The three factors can all influence the property (see Fig.4).During heating and cooling,hot stress and transformation will come into being when microstructure changes.Transformation temperature-microstructure and temperature—microstructure—and stress-property interact on each other.Research on the interaction of the four factors has been greatly developed,but the universal mathematic model has not been built.Many models fit the test nicely,but they cannot be put into practice.Difficulties with most of models are solved in analytic solution,and numerical method is employed so that the inaccuracy of calculation exists.Even so,comparing experience method with qualitative analysis,heat treatment simulation by computer makes great progress.3.2 Establishment and integration of modelsThe development procedure for die and mould involves design,manufacture,heat treatment,assembly,maintenance and so on.They should have own database and mode1.They are in series with each other by the entity—relation model.Through establishing and employing dynamic inference mechanism,the aim of optimizing design can be achieved.The relation between product model and other models was built.The product model will change in case the cell model changes.In fact,it belongs to the relation of data with die and mould.After heat treatment model is integrated into the system,it is no more an isolated unit but a member which is close to other models in the system.After searching,calculating and reasoning from the heat treatment database,procedure for heat treatment,which is restricted by geometric model,manufacture model for die and mould and by cost and property,is obtained.If the restriction is disobeyed,the system will send out the interpretative warning.All design cells are connected by communication network.3.3 Management and harmony among membersThe complexity of die and mould requires closely cooperating among item groups.Because each member is short of global consideration for die and mould development,they need to be managed and harmonized.Firstly,each item group should define its own control condition and resource requested,and learn of the request of up- and-down working procedure in order to avoid conflict.Secondly,development plan should be made out and monitor mechanism should be established.The obstruction can be duly excluded in case the development is hindered.Agile management and harmony redound to communicating information,increasing efficiency,and reducing redundancy.Meanwhile it is beneficial for exciting creativity,clearing conflict and making the best of resource.4 Conclusions(1) Heat treatment CAD/CAE has been integrated into concurrent design for die and mould and heat treatment is graphed,which can increase efficiency,easily discover problems and clear conflicts.(2)Die and mould development is performed on the same platform.When the heat treatment process is made out,designers can obtain correlative information and transfer self-information to other design departments on the platform.(3)Making out correct development schedule and adjusting it in time can enormously shorten the development period and reduce cost.References:[1] ZHOU Xiong-hui,PENG Ying-hong.The Theory and Technique of Modern Die and Mould Design and Manufacture[M].Shanghai:Shanghai Jiaotong University Press 2000(in Chinese).[2] Kang M,Park& Computer Integrated Mold Manufacturing[J].Int J Computer Integrated Manufacturing,1995,5:229-239.[3] Yau H T,Meno C H.Concurrent Process Planning for Finishing Milling and Dimensional Inspection of Sculptured Surface in Die and Mould Manufacturing[J].Int J Product Research,1993,31(11):2709—2725.[4] LI Xiang,ZHOU Xiong-hui,RUAN Xue-yu.Application of Injection Mold Collaborative Manufacturing System [J].JournaI of Shanghai Jiaotong University,2000,35(4):1391-1394.[5] Kuzman K,Nardin B,Kovae M ,et a1.The Integration of Rapid Prototyping and CAE in Mould Manufacturing[J].J Materials Processing Technology,2001,111:279—285.[6] LI Xiong,ZHANG Hong—bing,RUAN Xue-yu,et a1.Heat Treatment Process Design Oriented Based on Concurrent Engineering[J].Journal of Iron and Steel Research,2002,14(4):26—29.文献出处:LI Xiong,ZHANG Hong-bing,RUAN Xue—yu,LUO Zhong—hua,ZHANG Yan.Heat Treatment of Die and Mould Oriented Concurrent Design[J].Journal of Iron and Steel Research,2006,13(1):40- 43,74模具热处理及其导向平行设计李雄,张鸿冰,阮雪榆,罗中华,张艳摘要:在一系列方式中,传统模具设计方法存在许多缺点。
冲压模具设计毕业外文翻译 中英文翻译 外文文献翻译

冲压模具设计毕业外文翻译中英文翻译外文文献翻译毕业设计(论文)外文资料翻译系部:专业:姓名:学号:外文出处: The Pofessional English of DesignManufacture for Dies & Moulds附件: 1.外文资料翻译译文,2.外文原文。
指导教师评语:签名:年月日附件1:外文资料翻译译文冲压模具设计对于汽车行业与电子行业,各种各样的板料零件都是有各种不同的成型工艺所生产出来的,这些均可以列入一般种类“板料成形”的范畴。
板料成形(也称为冲压或压力成形)经常在厂区面积非常大的公司中进行。
如果自己没有去这些大公司访问,没有站在巨大的机器旁,没有感受到地面的震颤,没有看巨大型的机器人的手臂吧零件从一个机器移动到另一个机器,那么厂区的范围与价值真是难以想象的。
当然,一盘录像带或一部电视专题片不能反映出汽车冲压流水线的宏大规模。
站在这样的流水线旁观看的另一个因素是观看大量的汽车板类零件被进行不同类型的板料成形加工。
落料是简单的剪切完成的,然后进行不同类型的加工,诸如:弯曲、拉深、拉延、切断、剪切等,每一种情况均要求特殊的、专门的模具。
而且还有大量后续的加工工艺,在每一种情况下,均可以通过诸如拉深、拉延与弯曲等工艺不同的成形方法得到所希望的得到的形状。
根据板料平面的各种各样的受应力状态的小板单元体所可以考虑到的变形情形描述三种成形,原理图1描述的是一个简单的从圆坯料拉深成一个圆柱水杯的成形过程。
图1 板料成形一个简单的水杯拉深是从凸缘型坯料考虑的,即通过模具上冲头的向下作用使材料被水平拉深。
一个凸缘板料上的单元体在半径方向上被限定,而板厚保持几乎不变。
板料成形的原理如图2所示。
拉延通常是用来描述在板料平面上的两个互相垂直的方向被拉长的板料的单元体的变形原理的术语。
拉延的一种特殊形式,可以在大多数成形加工中遇到,即平面张力拉延。
在这种情况下,一个板料的单元体仅在一个方向上进行拉延,在拉长的方向上宽度没有发生变化,但是在厚度上有明确的变化,即变薄。
【毕业设计】冲压模具毕业设计外文翻译

【关键字】毕业设计冲压模具毕业设计外文翻译篇一:模具外文文献及翻译The mold designing and manufacturingThe mold is the manufacturing industry important craft foundation, in our country,the mold manufacture belongs to the special purpose equipment manufacturingindustry. China although very already starts to make the mold and the use mold, but long-term has not formed the industry. Straight stabs 0 centuries 80's later periods, the Chinese mold industry only then drives into the development speedway. Recent years, not only the state-owned mold enterprise had the very big development, the threeinvestments enterprise, the villages and towns (individual) the mold enterprise'sdevelopment also rapid quietly.Although the Chinese mold industrial development rapid, but compares with thedemand, obviously falls short of demand, its main gap concentrates precisely to,large-scale, is complex, the long life mold domain. As a result of in aspect and so on mold precision, life, manufacture cycle and productivity, China and the international average horizontal and the developed country still had a bigger disparity, therefore, needed massively to import the mold every year .The Chinese mold industry must continue to sharpen the productivity, from now on will have emphatically to the profession internal structure adjustment and thestate-of-art enhancement. The structure adjustment aspect, mainly is the enterprise structure to the specialized adjustment, the product structure to center the upscale mold development, to the import and export structure improvement, center theupscale automobile cover mold forming analysis and the structure improvement, the multi-purpose compound mold and the compound processing and the laser technology in the mold design manufacture application, the high-speed cutting, the superfinishing and polished the technology, the information direction develops .The recent years, the mold profession structure adjustment and the organizationalreform step enlarges, mainly displayed in, large-scale, precise, was complex, the long life, center the upscale mold and the mold standard letter development speed is higher than the common mold product; The plastic mold and the compression casting mold proportion increases; Specialized mold factory quantity and its productivity increase;"The three investments" and the private enterprise develops rapidly; The joint stock system transformation step speeds up and so on. Distributes from the area looked,take Zhejiang Delta and Yangtze River delta as central southeast coastal areadevelopment quickly to mid-west area, south development quickly to north. Atpresent develops quickest, the mold produces the most centralized province isGuangdong and Zhejiang, places such as Jiangsu, Shanghai, Anhui and Shandong also has a bigger development in recent years.Although our country mold total quantity had at present achieved the suitable scale, the mold level also has the very big enhancement, after but design manufacture horizontal overall rise and fall industry developed country and so on Yu De, America, date, France, Italy many. The current existence question and the disparity mainly display in following several aspects:(1) The total quantity falls short of demandDomestic mold assembling one rate only, about 70%. Low-grade mold, centerupscale mold assembling oneself rate only has 50% about.(2) the enterprise organizational structure, the product structure, the technical structure and the import and export structure does not gatherin our country mold production factory to be most is from the labor mold workshop which produces assembles oneself (branch factory), from produces assembles oneself the proportion to reach as high as about 60%, but the overseas mold ultra 70% is the commodity mold. The specialized mold factory mostly is "large and complete","small and entire" organization form, but overseas mostly is "small but", "is specially small and fine". Domestic large-scale, precise, complex, the long life mold accountsfor the total quantity proportion to be insufficient 30%, but overseas in 50% aboveXX years, ratio of the mold import and export is 3.7:1, the import and exportbalances the after net import volume to amount to 1.32 billion US dollars, is world mold net import quantity biggest country .(3) The mold product level greatly is lower than the international standardThe production cycle actually is higher than the international water broad productlevel low mainly to display in the mold precision, cavity aspect and so on surface roughness, life and structure.(4) Develops the ability badly, economic efficiency unsatisfactory our countrymold enterprise technical personnel proportion lowThe level is lower, also does not take the product development, and is frequent inthe passive position in the market. Our country each mold staff average year creation output value approximately, ten thousand US dollars, overseas mold industry developed country mostly 15 to10, 000 US dollars, some reach as high as 25 to10,000 US dollars, relative is our country quite part of molds enterprises also continuesto use the workshop type management with it, truly realizes the enterprise which the modernized enterprise manages fewTo create the above disparity the reason to be very many, the mold long-term hasnot obtained the value besides the history in as the product which should have, as well as the most state-owned enterprises mechanism cannot adapt the market economy, butalso has the following several reasons: .(1) Country to mold industry policy support dynamics also insufficientlyAlthough the country already was clear about has promulgated the mold profession industrial policy, but necessary policy few, carried out dynamics to be weak. Atpresent enjoyed the mold product increment duty enterprise nation 185; the majority enterprise still the tax burden is only overweight. The mold enterprise carries on the technological transformations introduction equipment to have to pay the considerable amount the tax money, affects the technology advancement, moreover privately operated enterprise loan extremely difficult.(2) Talented person serious insufficient, the scientific research development and the technical attack investment too urinemold profession is the technology, the fund, the work crowded industry, along withthe time progress and the technical development, grasps the talented person which and skilled utilizes the new technology exceptionally short, the high-quality mold fitterand the enterprise management talent extremely is also anxious. Because the mold enterprise benefit unsatisfactory and takes insufficiently the scientific research development and the technical attack, the scientific research unit and the universities, colleges and institutes eye stares at is creating income, causes the mold profession invests too few in the scientific research development and the technical attack aspect, causes the mold technological development step doe not to be big, progresses does not be quick.(3) The craft equipment level is low, also is not good, the using factor is low.Recent years ,our country engine bed profession progressed quickly, has been able to provide the quite complete precision work equipment, but compared with the overseas equipment, still had a bigger disparity. Although the domestic many enterprises have introduced many overseas advanced equipment, but the overall equipment level low are very more than the overseas many enterprises. As a result of aspect the and so on system and fund reason, introduces the equipment not necessary, the equipment and the appendix not necessary phenomenon are extremely common, the equipment utilization rate low question cannot obtain the comparatively properly solution for a long time .(4) Specialization, standardization, commercialized degree low, the cooperationabilityBecause receives "large and complete" "small and entire" the influence since long ago, mold specialization level low, the specialized labor division is not careful, the commercialized degree is low. At present domestic every year produces mold, commodity mold minister 40% about, other for from produce uses for oneself. Between the molds enterprise cooperates impeded, completes the comparativelylarge-scale mold complete task with difficulty. Mold standardization level low, mold standard letter use cave rare is low also to the mold quality, the cost has a more tremendous influence, specially has very tremendous influence.(5) To the mold manufacture cycle) the mold material and the mold correlationtechnology fallThe mold material performance, the quality and the variety question often canaffect the mold quality, the life and the cost, the domestically produced molding toolsteel and overseas imports the steel products to compare has a bigger disparity. Plastic, plate, equipment energy balance, also direct influence mold level enhancement.At present, our country economy still was at the high speed development phase, onthe international economical globalization development tendency is day by dayobvious, this has provided the good condition and the opportunity for the our countrymold industry high speed development. On the one hand, the domestic mold marketwill continue high speed to develop, on the other hand, the mold manufacture also gradually will shift as well as the transnational group to our country carries on themold purchase trend to our country extremely to be also obvious. Therefore, will takea broad view the future, international, the domestic mold market overall development tendency prospect will favor, estimated the Chinese mold will obtain the high speed development under the good market environment, our country not only can becomethe mold great nation, moreover certainly gradually will make the powerful nation tothe mold the ranks to make great strides forward. "15" period, the Chinese moldindustry level not only has the very big enhancement in the quantity and the archerytarget aspect, moreover the profession structure, the product level, the development innovation ability, enterprise's system and the mechanism as well as the technology advancement aspect also can obtain a bigger development .The mold technology has gathered the machinery, the electron, chemistry, optics,the material, the computer, the precise monitor and the information network and so on many disciplines, is a comprehensive nature multi-disciplinary systems engineering.The mold technology development tendency mainly is the mold product tolarger-scale, precise, more complex and a more economical direction develops, themold product technical content unceasingly enhances, the mold manufacture cycle unceasingly reduces, the mold production faces the information, is not having thechart, is fine, the automated direction develops, the mold enterprise to the technical integration, the equipment excellent, is producing approves the brand, themanagement information, the management internationalization direction develops.Mold profession in "十15" period needs to solve the key essential technologyshould be the mold information, the digitized technology and precise, ultra fine, high speed, the highly effective manufacture technology aspect breakthroughAlong with thenational economy total quantity and the industry product technologyunceasing development, all the various trades and occupations to the mold demandquantity more and more big, the specification more and more is also high.Although mold type many, but its development should be with emphasis both canmeet the massive needs, and has the comparatively high-tech content, specially atpresent domestic still could not be self-sufficient, needs the massive imports the moldand can represent the development direction large-scale, precise, is complex, the long篇二:冲压模具设计毕业设计开题报告题目:院系:专业:学生:学号:指导老师:毕业设计开题报告冲压工艺分析与弯曲冲孔模具的设计三峡大学机械与材料学院机械设计制造及其自动化三峡大学机械与材料学院冲压工艺分析与弯曲冲孔模具的设计开题报告一、课题的来源课题来源于生产实际,探讨冲压加工中较常见零件的工艺方法和结构设计。
- 1、下载文档前请自行甄别文档内容的完整性,平台不提供额外的编辑、内容补充、找答案等附加服务。
- 2、"仅部分预览"的文档,不可在线预览部分如存在完整性等问题,可反馈申请退款(可完整预览的文档不适用该条件!)。
- 3、如文档侵犯您的权益,请联系客服反馈,我们会尽快为您处理(人工客服工作时间:9:00-18:30)。
外文翻译Heat Treatment of Die and MouldOriented Concurrent DesignLI Xiong,ZHANG Hong-bing,RUAN Xue-yu,LUOZhong—hua,ZHANG YanAbstract:Many disadvantages exist in the traditional die design methodwhich belongs to serial pattern。
It is well known that heattreatment is highly important to the dies. A new idea of concurrentdesign for heat treatment process of die and mould was developedin order to overcome the existent shortcomings of heat treatmentprocess. Heat treatment CAD/CAE was integrated with concurrentcircumstance and the relevant model was built. Theseinvestigations can remarkably improve efficiency,reduce costand ensure quality of R and D for products.Key words:die design; heat treatment;mouldTraditional die and mould design,mainly by experience or semi—experience,is isolated from manufacturing process。
Before the design is finalized,the scheme of die and mould is usually modified time and again,thus some disadvantages come into being,such as long development period,high cost and uncertain practical effect。
Due to strong desires for precision,service life,development period and cost,modern die and mould should be designed and manufactured perfectly。
Therefore more and more advanced technologies and innovations have been applied,for example,concurrent engineering,agile manufacturing virtual manufacturing,collaborative design,etc.Heat treatment of die and mould is as important as design,manufacture and assembly because it has a vital effect on manufacture,assembly and service life.Design and manufacture of die and mould have progressed rapidly,but heat treatment lagged seriously behind them.As die and mould industry develops,heat treatment must ensure die and mould there are goodstate of manufacture,assembly and wear-resistant properties by request。
Impertinent heat treatment can influence die and mould manufacturing such as over—hard and-soft and assembly.Traditionally the heat treatment process was made out according to the methods and properties brought forward by designer.This could make the designers of die and mould and heat treatment diverge from each other,for the designers of die and mould could not fully realize heat treatment process and materials properties,and contrarily the designers rarely understood the service environment and designing thought。
These divergences will impact the progress of die and mould to a great extent。
Accordingly,if the process design of heat treatment is considered in the early designing stage,the aims of shortening development period,reducing cost and stabilizing quality will be achieved and the sublimation of development pattern from serial to concurrent will be realized.Concurrent engineering takes computer integration system as a carrier,at the very start subsequent each stage and factors have been considered such as manufacturing,heat treating,properties and so forth in order to avoid the error.The concurrent pattern has dismissed the defect of serial pattern,which bring about a revolution against serial pattern.In the present work.the heat treatment was integrated into the concurrent circumstance of the die and mould development,and the systemic and profound research was performed.1 Heat Treatment Under Concurrent CircumstanceThe concurrent pattern differs ultimately from the seri al pattern(see Fig.1)。
With regard to serial pattern,the designers mostly consider the structure and function of die and mould,yet hardly consider the consequent process,so that the former mistakes are easily spread backwards.Meanwhile,the design department rarely communicates with the assembling,cost accounting and sales departments.These problems certainly will influence the development progress of die and mould and the market foreground.Whereas in the concurrent pattern,the relations among departments are close,the related departments all take part in the development progress of die and mould and have close intercommunion with purchasers.This is propitious to eliminationof the conflicts between departments,increase the efficiency and reduce the cost.Heat treatment process in the concurrent circumstance is made out not after blueprint and workpiece taken but during die and mould designing.In this way,it is favorable to optimizing the heat treatment process and making full use of the potential of the materials.2 Integration of Heat Treatment CAD/CAE for Die and MouldIt can be seen from Fig.2 that the process design and simulation of heat treatment are the core of integration frame.After information input via product design module and heat treatment process generated via heat treatment CAD and heat treatment CAE module will automatically divide the mesh for parts drawing,simulation temperature field microstructure analysis after heat-treatment and the defect of possible emerging (such as overheat,over burning),and then the heat treatment process is judged if the optimization is made according to the result reappeared by stereoscopic visiontechnology.Moreover tool and clamping apparatus CAD and CAM are integrated into this system.The concurrent engineering based integration frame can share information with other branch.That makes for optimizing the heat treatment process and ensuring the process sound.2.1 3—D model and stereoscopic vision technology for heat treatmentThe problems about materials,structure and size for die and mould can be discovered as soon as possible by 3-D model for heat treatment based on the shape of die and mould.Modeling heating condition and phase transformation condition for die and mould during heat treatment are workable,because it has been broken through for the calculation of phase transformation thermodynamics,phase transformation kinetics,phase stress,thermal stress,heat transfer,hydrokinetics etc.For example,3—D heat—conducting algorithm models for local heating complicated impression andasymmetric die and mould,and M ARC software models for microstructure transformation was used.Computer can present the informations of temperature,microstructure and stress at arbitrary time and display the entire transformation procedure in the form of 3—D by coupling temperature field,microstructure field and stress field.If the property can be coupled,various partial properties can be predicted by computer.2。