铜材的切削液选择和维护
铜材切削液
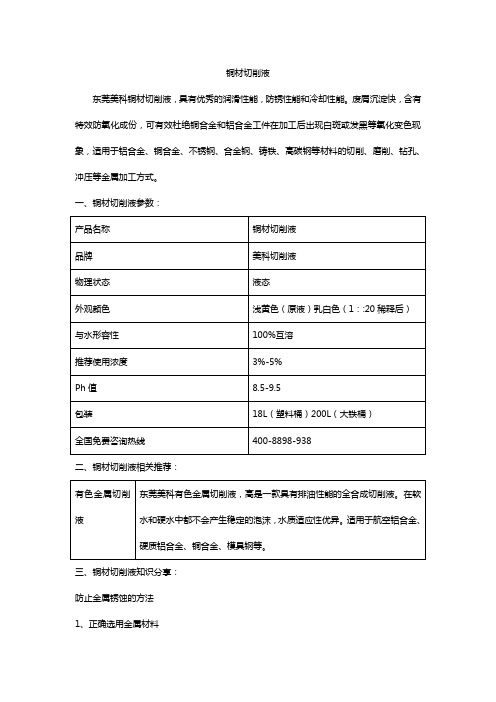
铜材切削液
东莞美科铜材切削液,具有优秀的润滑性能,防锈性能和冷却性能。
废屑沉淀快,含有特效防氧化成份,可有效杜绝铜合金和铝合金工件在加工后出现白斑或发黑等氧化变色现象,适用于铝合金、铜合金、不锈钢、合金钢、铸铁、高碳钢等材料的切削、磨削、钻孔、冲压等金属加工方式。
一、铜材切削液参数:
二、铜材切削液相关推荐:
三、铜材切削液知识分享:
防止金属锈蚀的方法
1、正确选用金属材料
2、在金属表面预制防护层或覆盖层例如渗氮、磷化、电镀、搪瓷等。
3、电化学法防蚀
4、控制环境法防蚀。
切削液的更换、使用与维护

17
pH 试纸
• • • • • *
将切削液表面的离散油去除 将 pH 试纸快速浸入液体中 从液体中取出 等候一分钟 与试纸包装盒上的图表相对比 pH 试纸 会由于放置时间较长而受潮
18
检测与记录
斯徒尔特金属加工液状态监测表
斯图尔特金属加工液名称 推荐使用浓度(%) 机床编号 日期 浓度(%) pH值(8.2~9.5) 添加量(升) 添加液的浓度(%) 备注 日常维护原则 1、浓度保持在推荐的使用浓度;2、pH值保持在8.2~9.5; 3、每周末撇去冷却液表面的浮油; 4、用稀释好的冷却液添加,不能直接加水或浓缩液
切削液更鲜冷却液重新填充机床或系统前,必须保证 机器已得到正确的清洗; • 按2.5%浓度将斯图尔特Dasco Kleen 06238机床清洗 液注入机床的切削液液箱; • 48小时后放干机床内所有的切削液; • 将机床内所有的切屑,垃圾等杂物清理干净; • 将机床台面和液箱擦洗干净; • 用清水在系统内循环15分钟; • 排干系统内的清水; • 把按推荐浓度配制好的稀释后的切削液注入系统; • 立即开动机床以循环切削液至系统各个部位。
3
千万注意
• 永远是将切削液原液倒入水中, 永远是将切削液原液倒入水中, 严禁将水倒入切削液原液之中; 严禁将水倒入切削液原液之中; 尽可能使用自动混合器调配乳化 液
4
日常监测指标与频率
维持推荐的使用浓度,每天至少一次 维持正常的pH值:8.5-9.2,每周至少两次 每周五下班前撇去切削液液箱内的浮油 定期用稀释后的切削液对系统进行添加以持正 常的浓度和维液面,始终保持切削液液箱的液 味在80%左右
8
折光仪的使用-检测浓度
• 擦干水滴 • 在折射镜上滴三滴干净的切削液, 必须 将分离油和金属切削屑去除 • 从目镜中读数 • 用折光系数转换为浓度百分比
切削液的选用与维护
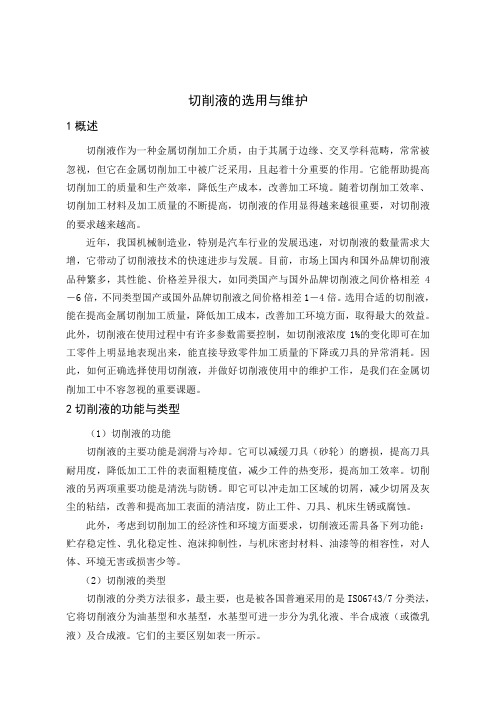
切削液的选用与维护1概述切削液作为一种金属切削加工介质,由于其属于边缘、交叉学科范畴,常常被忽视,但它在金属切削加工中被广泛采用,且起着十分重要的作用。
它能帮助提高切削加工的质量和生产效率,降低生产成本,改善加工环境。
随着切削加工效率、切削加工材料及加工质量的不断提高,切削液的作用显得越来越很重要,对切削液的要求越来越高。
近年,我国机械制造业,特别是汽车行业的发展迅速,对切削液的数量需求大增,它带动了切削液技术的快速进步与发展。
目前,市场上国内和国外品牌切削液品种繁多,其性能、价格差异很大,如同类国产与国外品牌切削液之间价格相差4-6倍,不同类型国产或国外品牌切削液之间价格相差1-4倍。
选用合适的切削液,能在提高金属切削加工质量,降低加工成本,改善加工环境方面,取得最大的效益。
此外,切削液在使用过程中有许多参数需要控制,如切削液浓度1%的变化即可在加工零件上明显地表现出来,能直接导致零件加工质量的下降或刀具的异常消耗。
因此,如何正确选择使用切削液,并做好切削液使用中的维护工作,是我们在金属切削加工中不容忽视的重要课题。
2切削液的功能与类型(1)切削液的功能切削液的主要功能是润滑与冷却。
它可以减缓刀具(砂轮)的磨损,提高刀具耐用度,降低加工工件的表面粗糙度值,减少工件的热变形,提高加工效率。
切削液的另两项重要功能是清洗与防锈。
即它可以冲走加工区域的切屑,减少切屑及灰尘的粘结,改善和提高加工表面的清洁度,防止工件、刀具、机床生锈或腐蚀。
此外,考虑到切削加工的经济性和环境方面要求,切削液还需具备下列功能:贮存稳定性、乳化稳定性、泡沫抑制性,与机床密封材料、油漆等的相容性,对人体、环境无害或损害少等。
(2)切削液的类型切削液的分类方法很多,最主要,也是被各国普遍采用的是ISO6743/7分类法,它将切削液分为油基型和水基型,水基型可进一步分为乳化液、半合成液(或微乳液)及合成液。
它们的主要区别如表一所示。
切削液使用和维护须知

中石油金属加工液版本号:WX-GY200515昆仑KL GRC2622全合成切削液使用和维护须知1、排放、清洗和配液1)换液前必须对过滤器和其管路进行清洗,去除设备管路内的杂质、污垢、各类菌皮;提前两天在工作液箱内添加杀菌剂,进行16-48小时循环后,彻底排干净液槽内废液。
2)排放后用机械方法去除箱底沉淀物、顽垢和金属屑等。
3)加水到液槽,使循环泵工作。
添加清洗剂浓度0.5-1%左右,系统循环1小时后排放废液,人工去除液箱内残余物。
4)加水到液槽,使循环泵工作,配液用水的硬度以不大于200ppm 为宜,在循环同时缓慢加入原液至目标控制浓度。
2、指标监控表1-工作液控制指标及检测频率检测项目控制指标检测频率浓度(折光仪)数控车床加工中心(钻孔、攻丝)加工中心(精镗、铰孔)2.0%-4.0%3.0%-5.0%5.0%-8.0%每天一次泡沫微弱或无每天一次pH8.5-9.5每月一次杂油< 2.0%每月一次防锈性<2级每月一次测菌<106每月一次硬度<500ppm每月一次注:当控制指标发生超差时,应及时采取调整浓度、添加各类添加剂或换液等措施。
浓度等控制指标仅做参考,特殊工艺要求可视加工情况进行修正。
3、日常维护1)检测浓度并做记录,根据工艺要求调整并复测,直至符合控制指标。
2)检查液位,如液位低,则需补充原液和水。
3)泡沫超标时,添加消泡剂。
4)pH 值超出控制范围,适当添加pH 调节剂。
5)杂油大于2.0%时,建议人工撇除杂油。
6)防锈性下降时,添加防锈剂。
7)细菌超标时,添加杀菌剂。
8)硬度超标时,添加去离子水,持续两周不能改善,建议换液。
9)定期清理液槽中金属屑,金属屑与沉积物的混合易引起细菌的滋生,从而导致加工液的变质。
10)长时间停工前需撇除杂油,有条件的情况下每天循环工作液1-2小时。
4、存储说明1)避免直接暴露在阳光下,产品应放置在通风阴凉(4℃至40℃)室内存储。
切削液的使用、管理与机床腐蚀的防护范本

切削液的使用、管理与机床腐蚀的防护范本随着制造业的发展,切削液在机床加工中起着非常重要的作用。
切削液的正确使用和管理,不仅可以提高切削加工的效率和质量,还可以延长机床的使用寿命。
同时,机床的腐蚀防护也是非常重要的,它可以降低机床的维护成本,保证机床的正常运行。
本文将从切削液的使用、管理和机床腐蚀防护方面进行介绍。
一、切削液的使用1. 选择切削液选择合适的切削液是确保切削过程稳定进行的关键。
切削液的选择应根据加工材料、切削方式、刀具类型和机床类型等因素进行。
常见的切削液有油基切削液、水基切削液和乳化液等。
2. 切削液的配制和调整在使用切削液之前,需要将其配制成适当的浓度。
切削液的浓度过高或过低都会影响切削液的性能。
当切削液的浓度过高时,易导致切削液的粘度过大,降低切削液的冷却和润滑效果;当切削液的浓度过低时,易导致切削液的润滑效果不佳,增加切削过程的摩擦。
3. 切削液的使用注意事项在使用切削液时,需要注意以下几点:- 切削液应定期更换,并且在更换之前应进行切削液的清洁。
- 在使用切削液时,应注意切削液与工件表面的接触情况,以确保切削液能够充分润滑工件表面。
- 使用切削液时,应根据切削液的要求进行调整,以确保切削液能够发挥最佳性能。
二、切削液的管理1. 切削液的储存和保管切削液应储存在干燥、阴凉的地方,避免阳光直射。
切削液的容器应密封良好,以防止切削液的挥发和污染。
切削液的储存区域应定期清洁和消毒,以防止细菌和其他有害物质的滋生。
2. 切削液的过滤和回收切削液在使用过程中会受到切屑、油脂等杂质的污染,因此需要定期对切削液进行过滤和回收。
切削液的过滤可以减少切屑和杂质对刀具的磨损,并有效延长切削液的使用寿命。
切削液的回收可以降低成本,并且对环境友好。
3. 切削液的定期检测和维护切削液的性能随着使用时间的推移而发生变化,因此需要定期进行切削液的检测和维护。
切削液的检测可以通过测量切削液的酸碱度、粘度、浓度等指标来判断切削液是否需要更换或调整。
切削液的使用与维护细则
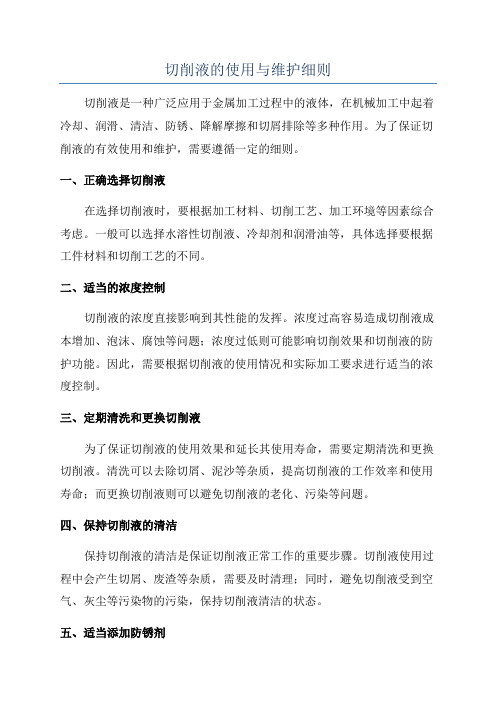
切削液的使用与维护细则切削液是一种广泛应用于金属加工过程中的液体,在机械加工中起着冷却、润滑、清洁、防锈、降解摩擦和切屑排除等多种作用。
为了保证切削液的有效使用和维护,需要遵循一定的细则。
一、正确选择切削液在选择切削液时,要根据加工材料、切削工艺、加工环境等因素综合考虑。
一般可以选择水溶性切削液、冷却剂和润滑油等,具体选择要根据工件材料和切削工艺的不同。
二、适当的浓度控制切削液的浓度直接影响到其性能的发挥。
浓度过高容易造成切削液成本增加、泡沫、腐蚀等问题;浓度过低则可能影响切削效果和切削液的防护功能。
因此,需要根据切削液的使用情况和实际加工要求进行适当的浓度控制。
三、定期清洗和更换切削液为了保证切削液的使用效果和延长其使用寿命,需要定期清洗和更换切削液。
清洗可以去除切屑、泥沙等杂质,提高切削液的工作效率和使用寿命;而更换切削液则可以避免切削液的老化、污染等问题。
四、保持切削液的清洁保持切削液的清洁是保证切削液正常工作的重要步骤。
切削液使用过程中会产生切屑、废渣等杂质,需要及时清理;同时,避免切削液受到空气、灰尘等污染物的污染,保持切削液清洁的状态。
五、适当添加防锈剂切削液使用过程中容易引发金属工件的锈蚀问题,为了减少锈蚀的发生,可以适当添加一些防锈剂。
防锈剂的添加可以提高切削液的防锈性能,延长切削液的使用寿命。
六、定期测量和调整PH值切削液的PH值直接影响到其对金属的腐蚀性和防锈性。
因此,定期测量和调整切削液的PH值是非常重要的。
一般来说,切削液的PH值应在正常范围内,过高或者过低都会对切削液的使用产生不良影响。
七、注意切削液的储存和使用环境切削液的储存和使用环境对其性能的发挥影响很大。
首先,要选择干燥、通风、避光的环境进行切削液的储存;其次,在使用过程中要避免切削液受到灰尘、杂质等污染;最后,在加工过程中要保持切削液的温度适宜,避免过高或者过低。
总之,正确使用和维护切削液对金属加工过程的顺利进行至关重要。
切削液的选用

不能使用水基切削液,以免引起燃烧
刀具材料
高速钢刀具
热硬性差,一般应使用切削液
硬质合金刀具
热硬性好,耐热、耐磨,一般不用切削液,必要时可使用低浓度的乳化液或合成切削液,但必须连续、充分浇注,以免刀片因冷热不均匀,产生较大内应力而导致破裂
加工方法
钻孔(尤其是钻深孔)、铰孔、攻螺纹、拉削等加工
因工具与已加工表面的摩擦严重,宜采用乳化液、极压乳化液、极压切削油,并充分浇注
使用螺纹刀具、齿轮刀具及成形刀具切削
刀具价格较贵,刃磨困难,要Байду номын сангаас刀具寿命高,宜采用极压切削油、硫化切削油等
磨削
因其加工时温度很高,且会产生大量的细屑及脱落的磨粒,容易堵塞砂轮和使工件烧伤,要选用冷却作用好、清洁能力强的切削液,如合成切削液和低浓度乳化液
磨削不锈钢、高温合金
应选用润滑性能较好的极压型合成切削液和极压乳化液
切削液的选用
选用依据
加工条件
切削液选用原则
工件材料
切削钢等塑性材料
需用切削液
切削铸铁等脆性材料
因使用切削液的作用不明显,且会弄脏工作场地和使碎屑黏附在机床导轨与滑板间造成阻塞和擦伤,故一般不使用切削液
切削高强度钢、高温合金等难切削材料
选用极压切削油或极压乳化液
切削铜、铝及其合金
因硫对其有腐蚀作用,故不能使用含硫的切削液
加工要求
粗加工
金属切除量大,切削温度高,应选用冷却作用好的切削液
精加工
为保证加工质量,宜选用润滑作用好的极压切削液
切削液的保养维护

切削液的保养维护
切削液的维护工作主要包括以下几项:
⑴确保液体循环线路的畅通及时排除循环线路的金属屑、金属粉末、霉菌粘液、切削液本身的分解物、砂轮灰等,以免造成堵塞。
⑵在切削液的使用过程中,要定期检查细菌含量,及时采取相应措施。
⑶净化要及时除掉切削液中的金属粉末等切屑及飘浮油,消除细菌滋生环境。
⑷定时检查PH值,有较大变化,及时采取相应措施。
⑸及时补加切削液,由于切削液在循环使用过程中因飞溅、雾化、蒸发以及加工材料和切屑的携带,会不断消耗,因此要及时补加新液,以满足系统的循环液总量不变。
- 1、下载文档前请自行甄别文档内容的完整性,平台不提供额外的编辑、内容补充、找答案等附加服务。
- 2、"仅部分预览"的文档,不可在线预览部分如存在完整性等问题,可反馈申请退款(可完整预览的文档不适用该条件!)。
- 3、如文档侵犯您的权益,请联系客服反馈,我们会尽快为您处理(人工客服工作时间:9:00-18:30)。
铜是人类最早使用的金属。
铜被广泛应用于电力、家用电器、汽车、建筑、电子仪器仪表、国防、交通运输、海洋工程等行业。
铜加工业(铜产品制造业)是国民经济的重要部门,根据产品形状可细分为铜管材、铜板带材、铜箔材、铜棒材、铜型材、铜线材等子行业,其中铜管材、铜棒材均属于铜产品制造业中发展较快的细分行业。
铜加工有加工硬化的特性,就是随着加工率的增加,其塑性降低,强度增加,变形难度增加,理论上黄铜每次退火之间加工率可达80%以上,紫铜可以达到90%以上,但是要达到这么大的加工率其轧制力将增加很大,设备效率降低,通常采用每次软化退火之间加工率黄铜60%-70%,紫铜可以大些,达90%,利用其塑性较好时,可以大加工率加工,其加工效率比较高,对设备投资较小,同时加工率大边部破裂也会增加,板形控制难度也会增加;所以必须进行再结晶软化退火,提高材料塑性(可加工性),来继续进行深加工。
综合上面所述,铜及其合金切削液的选择非常重要,必须保证良好的润滑性、冷却性、过滤性和防锈性,因此可用于铜及其合金加工的切削液与普通的切削液有所不同,选择一款合适的切削液是十分必要的。
铜材切削液的选择
根据加工条件和加工精度的要求不同应选择不同的切削液。
对于高速加工可产生大量的热量,如高速切削、钻孔等,如果产生的热量不能及时的被切削液带走,将会发生粘刀现象,严重的会出现积屑瘤,将严重的影响到工件的加工精糙度和刀具的使用寿命,同时热量也可
使工件发生变形,严重影响到工件的精度。
因此切削液的选择既要考虑到其本身的润滑性也要考虑其冷却性能,对于精加工易选择乳化型减摩切削液或低粘度的切削油,如联诺化工的乳化型切削液SCC101和切削油NC600,对于半精加工和粗加工可选择低浓度的乳化型减摩切削液或半合成减摩切削液等具有良好冷却性能的切削液如联诺化工的乳化型切削液SCC102和半合成切削液SCC618。
对于磨削加工来说,磨削下来的磨屑非常细小,而且在磨削过程中会产生大量的热量,因此选择切削液时既要考虑润滑和冷却性能外还要考虑到切削液的过滤性,如选择的切削粘稠度过大,切屑不能及时沉积降下去或被过滤出去,那么就会随切削液循环到加工区而划伤工件表面而影响加工表面的光洁度。
因此对于精磨或超精磨易选用低粘度减摩磨削油或半合成减磨切削液,如联诺化工的半合成切削液SCC638,对于半精磨或粗磨可选用低浓度度的半合成切削液或全合成切削液,如联诺化工的半合成切削液SCC638A和全合成切削液SCC750A。
在切削液的选择方面除了要考虑切削液的润滑性、冷却性等性能外,还要考虑切削液的防锈性、成本和易维护等方面的性能。
切削油易选用粘度相对较低的基础油加入减磨添加剂,这样既可达到润滑减摩,也可有很好冷却和易过虑性。
但是切削油存在的问题是闪点低,在高速切削时烟雾较重,闪点低,危险系数较高,而且挥发快,用户使用成本相应变高,因此在条件允许的景况下尽量选用水溶性切削液。
对于水性切削液,更重要的是要考虑其防锈性。
现在常用的水性铝
防锈剂有硅酸盐和磷酸脂,对于工序间存放时间较长的工件,在加工时易选用具有磷酸脂型防锈剂的切削液,因为硅类物质与铝材长时间接触会发生腐蚀产生黑色的“硅斑”。
切削液的pH值多保持在8-10之间,如果防锈性不好,铜材在这种碱性条件下很容易被腐蚀。
因此水溶性切削液一定要有良好的防锈性能。
铜材切削液的使用与维护
铜及其合金切削液的配制和使用与普通切削液的配制和使用基本相同,只是在稀释水的选择上要更加严格,因为水中的许多离子对铜都会产生腐蚀作用,如果这些离子含量过多就会降低切削液的防锈性能,尤其是在工序间防锈上,例如氯离子、硫酸根离子、重金属离子等。
另外一些离子还会与切削液中的防锈剂发生产反应而降低切削液的防锈性和稳定性,如钙、镁离子等。
因此尽量选择硬度较小的稀释水,或经过离子交换软化后的稀释水,以保证切削液的使用效果和使用寿命。
铜及其合金切削液的维护除了需要像普通切削液的日常维护外还要注意以下几点:
1. 过滤。
因为铜及其合金在碱性条件下易发生反应生成铝皂,破坏切削液的稳定性。
因此切削下来的铜屑应立即将其过滤出去,避免铜屑与切削液发生产反应而影响到切削液的使用效果与使用寿命。
在磨削加工过程中磨现来的铜屑既细小又轻,很难沉淀下去,如不进行过滤或过滤的不充分,铜屑就会随切削液循环系统被带到加工区而影响到加工区而划伤工作面,影响加工表面的光泽度。
2. pH值。
因为铜材对切削液的pH值非常敏感,因此要经常性的对铜及其合金切削液pH值进行检测,如发现异常应及时进行调整,使用pH控制在8-9之间,以免pH值过高腐蚀工件或pH值过低使细菌大量繁殖而影响切削液的稳定和使用性能。
3. 定时补加新液。
既保证切削液的良好润滑,也保证了切削液良好的防锈性能和杀菌防腐性能,以延长工作液的使用寿命。
结论
铜及其合金切削液的选择是非常重要的,既要保证切削液良好的润滑性、防锈性,还要有良好的稳定性、过虑性和易维护性,只有这样才能在加工出符合要求的产品,也最大限度的降低切削液的使用成本。