2020年橡胶产品基本缺陷产生原因及解决措施参照模板
橡胶基础知识及常见缺陷改善对策

橡胶基础知识及常见缺陷改善对策原料-配方-工艺-设备-生产经验一、橡胶次品类别、原因分析及解决办法类别产生废品的原因解决办法责任人(单位)半成品规格、形状不合格. 调整半成品规格,形状至合格。
预成型。
隔离剂浓度太浓。
稀释隔离剂浓度或减少使用班长,操作工。
硫化工加压太猛,不当。
量。
操作工。
流痕、沟设备不保压或压力不足。
缓慢加压改变原操作方法。
机修工。
槽硫化排气次数太少。
修理设备使设备保压。
操作工。
半成品胶料重量不足。
增加排气次数。
预成型。
增加半成品重量。
原材料本身有杂质或污染。
原材料进行检查,过滤并防污材料部.炼胶,成型工人为造杂质或污染。
材料部,预成型。
染。
胶料不准落地,容器使用前清操作工。
硫化工对胶料管理不当带入杂洗干净。
操作工。
杂质、老质。
胶料用专用器具盛装,上料时材料部,预成型。
化胶(特模具不清洁或模具上废边未清严防污染。
别是有色除干净。
模具在使用前清洗干净,脱模产品) 混炼焦烧,老化,造成产品表后将废边清除干净。
面有老化胶。
加强胶料管理,(特别是有色胶)开炼机挡板两边胶料清楚干净。
欠硫:A硫化温度低,B硫化时严格按工艺生产,制定合理的工艺科,硫化工。
间短。
硫化工艺。
机修工。
2.硫化压力不足或不保压。
增加硫化压力或维修设备。
材料部。
气泡、发3.胶料或原材料含水分太大。
进行干燥处理,将水分蒸发。
预成型。
孔(不饱4.预成型件中混有杂胶或塑料重新混炼,过虑后使用。
材料部。
满) 袋。
提高其温度至合格为止。
5.密炼,热炼或成型时温度不够。
模脏或模具锈蚀清洗模具或沙光。
洗模工。
胶料污染严重或胶料表面气重新成型,更换胶料。
预成型孔。
增加单耗,使达到合格。
预成型砂眼成型件重量不足。
提高胶料流动性,加强胶料的材料部,预成型胶料流动性差或胶料老化。
管理。
材料部,预成型胶料杂质过多. 胶料过滤处理.压力不足或不饱压调整压力或维修设备。
机修工焦烧时间太短,胶料强度不够调整配方或提高胶料强度。
材料室缩裂或硬度太低检查,修理模具。
橡胶制品的常见缺陷与解决方案

橡胶制品的缺陷与解决方案
件之间有一个从软到硬的渐进。 ( stiffness gradients 橡胶截面弹性与刚性比的有益渐 进) ;
1、改进配方以保证有充足的焦烧时间; 2、改进制品模具和配方,保证胶料以最快的速 度到达金属嵌件的粘结部位; 3、尽量采用普通、半有效硫化体系(不同硫化 体系的耐疲劳性和耐热氧老化等性能有明显差 异,一般硫化体系中随着促进剂与硫黄比率由 小到大的变化,硫化体系由普通硫化体系过渡 到半有效硫化体系,至有效硫化体系。硫化胶 4.配方不合理,胶料 网络结构则由多硫交联键为主转变为多硫键、 硫化速度与胶浆硫化 双硫键和单硫键并存的分布,最后全硫化体系 速度不一致 (配方泛指 变为单硫键和双硫键为主的脆性结构。一般橡 胶料配方和胶浆配方) 胶制品的物理和化学性能,在前两种硫化体系 中能较好适应于生产使用。 ) , 提高硫黄用量 (相 对而言,不是越多越好) ,以实现多硫交联键; 4、改进硫化条件(温度、时间和压力) ; 5、减少易喷霜物和增塑剂的使用,防止其硫化 时迁移到橡胶表面,从而影响粘结; 6、胶料停放时间过长,与空气接触产生一定的 物理化学反应,造成胶料硫化失效。需改用新
3/9
橡胶制品的缺陷与解决方案
2.橡胶- 金属粘接不良 会引起粘结部位残留 大量气体, 加压时气体 收缩。一旦撤去压力, 按上述一橡胶-金属粘接不良中所述方法解决; 气体扩散, 橡胶层较薄 且面积较大的橡胶和 金属之间会出现气泡 1、增加模具合模后放气次数; 2、对模具进行抽真空; 3、提高混炼胶的温度; 4、采用门尼粘度较高的橡胶;(门尼粘度用门 尼粘度计测量, 门尼粘度计是一个标准的转子, 3.有气体裹入胶料, 气 以恒定的转速(一般 2 转/分),在密闭室的试 体不易排除, 随胶料一 样中转动。转子转动所受到的剪切阻力大小与 起硫化, 从而在制品表 试样在硫化过程中的粘度变化有关,可通过测 面出现气泡 力装置显示在以门尼为单位的刻度盘上,以相 同时间间隔读取数值可作出门尼硫化曲线,当 门尼数先降后升,从最低点起上升 5 个单位时 的时间称门尼焦烧时间,从门尼焦烧点再上升 30 个单位的时间称门尼硫化时间。
橡胶制品常见问题及解决方法

不管是何种产品,其实都是有缺陷。
自然橡胶制品也不例外,那该产品比较常见的问题及解决方案有哪些呢吗,下边为您解答。
1、橡胶产品撕裂
原因分析:启模太快,受力不均匀;模具棱角、倒角不合理;隔离剂过多或是过少;胶料流动性差,半成品粘接性差;。
解决方案:启模时制品均匀受力,减小胶料的门黏度,改进模具设计,合理使用隔离剂。
2、橡胶产品缺胶
原因分析:胶料没有充分流动;半成品单耗不足或装胶量不足;模具排气性能差;模温太高。
解决方案:减慢模具上升速度并反复放气;从新制定模具装胶量;改善模具设计,降低模温。
3、橡胶产品出现卷边、抽边、缩边
原因分析:胶料加工性能差。
解决方案:采用铸压、注射法生产降低胶料的门尼黏度。
4、橡胶产品过于粗糙
原因分析:模具表面粗糙,没清洗干净;混炼胶焦烧时间过短。
解决方案:清洗模具;延长焦烧时间。
5、橡胶产品胶边过厚,以至于产品超重
原因分析:模具装胶料过多;平板压力不足;模具没有相应的余胶槽。
解决方案:严格控制半成品单耗;增大平板压力;改进模具设计。
6、橡胶产品有气泡
原因分析:配合剂中含有硫化分解加工时出现窝气;模腔中的空气没有排干净;模具无排气线。
解决方案:模具上增加排气线;生产合模前反复放气,配方中加适量氧化钙
7、橡胶产品出现裂纹
原因分析:胶料有脏物混入;隔离剂添加过多;胶料焦烧不够。
解决方案:保证胶料清洁无污染;合理使用隔离剂;延长焦烧时间。
综上就是橡胶制品常见7大问题及解决方法的介绍,希望对大家进一步的了解有所帮助,同时,如想了解更多有关橡胶制品信息可咨询巩义市鑫业供水材料有限公司。
塑胶件常见不良状况及形成原因、改善对策
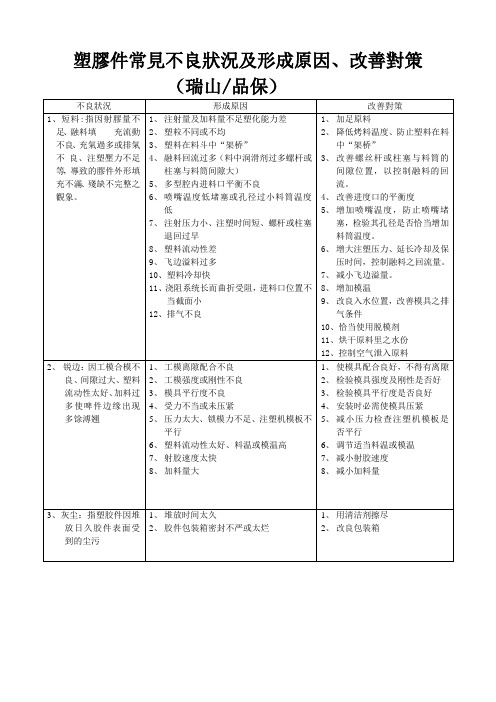
1、模具设计不合理,胶件出模时受力不当
2、胶件因冷却及保压时间不够而引起的收缩性变形
3、包装方式不当或包装胶袋及纸箱不合理保存时间太长或堆放不合理而引起的变形
1、改良模具设计,使之合理
2、延长冷却及保压时间即延长啤塑周期
3、改良包装材料(纸箱胶袋)改善合理的包装方式
6、调节适当料温或模温
7、减小射胶速度
8、减小加料量
3、灰尘:指塑胶件因堆放日久胶件表面受到的尘污
1、堆放时间太久
2、胶件包装箱密封不严或太烂
1、用清洁剂擦尽
2、改良包装箱
4、油垢:指工模防锈油污及脱模剂所致的油污,表现为黄色或黑色斑,一般可用布擦掉
1、工模因停机时所加防锈油及脱模剂在开啤尚时未洗干净
塑膠件常見不良狀況及形成原因、改善對策
(瑞山/品保)
不良狀況
形成原因
改善對策
1、短料:指因射膠量不足、融料填充流動不良、充氣過多或排氣不良、注塑壓力不足等,導致的膠件外形填充不滿、殘缺不完整之觀象。
1、注射量及加料量不足塑化能力差
2、塑粒不同或不均
3、塑料在料斗中“架桥”
4、融料回流过多(料中润滑剂过多螺杆或柱塞与料筒间隙大)
5、模具排气不良
6、模温低
7、注塑时间速度太快
8、模具型腔内有水分,油脂或脱模剂不当
9、加料端空气混入
10、料气死角
1、烤干原料里水分
2、降低料温
3、加大压力
4、螺杆不得过早退回
5、改善模具之排气条件
6、增加模温
7、减小注塑速度
8、保证模具型腔不得有水分,油脂。使用适当脱模剂
9、禁止加料端空气泄入
橡胶模压制品常见缺陷及解决方法

橡胶模压制品常见缺陷及解决方法橡胶模压制品常见缺陷及解决方法 :::::::::::::::缺陷产生原因解决方法起泡 (又叫 '困气', '包风')模压料固化不完全空气没有排清提高模温或延长保温时间增加排气次数模温过高,使物料中某种成分气化或分解降低模温模具配合间隙过大或溢料孔太大缺料脱模剂用量太多操作太慢或太快调整模具配合公差和溢料孔尺寸调节适当的合模温度和加压时机烧焦模具温度过高,橡胶在合模过程中还没来得及充分流动就已经部分硫化失去融合能力适当降低模温改善固化条件固化不完全翘曲出模工艺不当温度偏高导致过硫化重新设计模具,使顶出装置合理. 适当降低模温或缩短硫化时间模温过高或过低表面无光泽粘模调整模温,一般适当降低模温使用合适的脱模剂模具表面粗糙提高模具表面光洁度,应镀铬模压料未加内脱模剂或加入不当粘模通过试验加入适量的有效的内脱模剂提高模具表面光模具表面粗糙或新模未经研洁度,可用压塑粉试模磨使用后再压制玻璃钢压制压力过高适当降低压力模具过热斑驳表面颜料因过热而分解降低模温喷霜混炼胶或硫化胶内部的液体或固体配合剂因迁移而在橡胶制品表面析出形成云雾状或白色粉末物质的现象.这是由于硫,石蜡,某些防老剂,软化剂的使用量超出了它们在橡胶中的溶解度而引起的.为防止喷霜,上述各种配合剂用量要适当,对常见的硫黄喷霜可采用不溶性硫黄加以防止.在橡胶中适当加入松焦油,液体古马隆等可增加胶料对上述配合剂的溶解度,以减少喷霜现象. 喷霜-定义和由来喷霜又名喷出(blooming),是橡胶加工过程中常见的质量问题,它是指未硫化胶或硫化胶中所含的配合剂迁移到表面并析出的现象.有时,这种喷出物呈霜状结晶物,故习惯上称'喷霜'.较多见的喷霜物为硫,因为硫黄是通用橡胶中应用最广泛的硫化剂,且在橡胶中的溶解度低因而容易产生喷霜.其实从喷出物外观来看,也未必都呈霜状,也有呈油状(软化剂,增塑剂)或粉粒状(多为填充剂, 防老剂,促进剂等)的物质喷出,甚至炭黑喷出也有所见. 喷霜-防霜剂硅胶也会有喷霜现象,采用双二四硫化剂(通常用在挤出成型工艺)高温分解后会产生低分子量的酸性物质,其与硅橡胶不相容,在存放过程中会转移到硅胶表面结晶从而出现喷霜.防霜剂主要成分为碱性物质,通过酸碱中和反应来达到防霜的目的. 高硬度的硅胶往往加入比较多的内脱模剂,遇水也会喷白,水的酸性对此有遏制作用硅橡胶模具制作方法及注意事项模具是快速模具里的一种最为简单的方法,一般是用硅胶将RP 原型进行复模,但寿命很短,只有 10-30 件左右!他具有很好的弹性和复制性能,用硅橡胶复制模可不用考虑拔模斜度,不会影响尺寸精度,有很好的分割性,不用分上下模可直接进行整体浇注.再沿预定的分模线进行切割取出母模就可以了!室温硫化硅橡胶又分为加成型和缩合型两种! 室温硫化硅橡胶又分为加成型和缩合型两种! 原料及配方采用专用模具硅橡胶,该品系以双包装形式出售,A 组份是胶料,B 组份是催化剂.配制时要考虑室温,模具的强度和硬度,以此来确定AB 组份的重量配制比例.室温在20-25 度时,A:B=100:1.5.室低时(但不能低于 10 度)则适当增加 B 组份 0.1-0.3 份.室温偏高则减少 B 组 0.1-0.3 份.具体方法是依据模具体积确定总用量,然后将A,B 组份按比例称量准确, 置于器皿中搅拌均匀,即成. 制模: 将调配好的材料, 倒入待仿制的清洁的实物上即可. 为了节省材料, 制得较薄的模具, 也可分次涂刷. 为增加模具的拉力可糊纱布之类. 在室温20 度条件下 2 小时就能固化为弹性体, 一天后就可使用. 硅橡胶模具制作注意事项:1,B 组份是催化剂,易受潮水解,故用后应将盖子盖严.2,A, B 组一经混合,化学反应;立即开始,粘度逐渐上升,无法中止,为避免浪费,应根据用量,随用随配,配好后应立即使用,不可延误.3,A,B 组的配合比,关系到化学反应的速度和模具的性能.B 组份越多,反应越快,制品的强度和硬度越高,但韧度随之降低.因此,称量要求精确. 4,配制前,应将 A 组份料上下搅拌均匀,再称量.5,浇注法适宜于浮雕类,涂刷法适用于立体类模具的制作.浇注浮雕类的模具应先制作长宽都大于原雕长宽各 4-6CM 的边框.边框要平正, 内面要光滑. 浇注时将边框放置在干净的玻璃板上, 再将原件放在框中, 每边留出 2-3CM 的间隙. (硅橡胶 61 元/KG) 硅橡胶模具制作注意事项:制作过程中有气泡解决办法:1,改进飞边槽与排气系统的设计 2,增大压机的压力 3,减少脱模剂的用量,并均匀喷洒 4,材料控制水份........5,可以试着加些消泡剂6,使用冷流道.7,用真空机真空抽气,模具上可以增加排气操.1,天然橡胶(NR) 以橡胶烃(聚异戊二烯)为主,含少量蛋白质,水分,树脂酸, 糖类和无机盐等.弹性大,定伸强度高,抗撕裂性和电绝缘性优良,耐磨性和耐旱性良好, 加工性佳,易于其它材料粘合,在综合性能方面优于多数合成橡胶.缺点是耐氧和耐臭氧性差,容易老化变质;耐油和耐溶剂性不好,第抗酸碱的腐蚀能力低;耐热性不高.使用温度范围:约-60℃~+80℃. 制作轮胎,胶鞋,胶管,胶带,电线电缆的绝缘层和护套以及其他通用制品. 特别适用于制造扭振消除器, 发动机减震器, 机器支座, 橡胶-金属悬挂元件, 膜片,模压制品.2,丁苯橡胶(SBR) 丁二烯和苯乙烯的共聚体. 性能接近天然橡胶,是目前产量最大的通用合成橡胶,其特点是耐磨性,耐老化和耐热性超过天然橡胶,质地也较天然橡胶均匀.缺点是:弹性较低,抗屈挠,抗撕裂性能较差;加工性能差,特别是自粘性差,生胶强度低.使用温度范围:约-50℃~+100℃. 主要用以代替天然橡胶制作轮胎,胶板,胶管, 胶鞋及其他通用制品.3,顺丁橡胶(BR) 是由丁二烯聚合而成的顺式结构橡胶. 优点是:弹性与耐磨性优良,耐老化性好, 耐低温性优异, 在动态负荷下发热量小, 易于金属粘合. 缺点是强度较低, 抗撕裂性差,加工性能与自粘性差.使用温度范围:约-60℃~+100℃. 一般多和天然橡胶或丁苯橡胶并用,主要制作轮胎胎面,运输带和特殊耐寒制品.4,异戊橡胶(IR) 是由异戊二烯单体聚合而成的一种顺式结构橡胶. 化学组成,立体结构与天然橡胶相似,性能也非常接近天然橡胶,故有合成天然橡胶之称.它具有天然橡胶的大部分优点,耐老化由于天然橡胶,弹性和强力比天然橡胶稍低,加工性能差,成本较高.使用温度范围:约-50℃~+100℃ 可代替天然橡胶制作轮胎,胶鞋,胶管,胶带以及其他通用制品.5,氯丁橡胶(CR) 是由氯丁二烯做单体乳液聚合而成的聚合体. 这种橡胶分子中含有氯原子,所以与其他通用橡胶相比:它具有优良的抗氧,抗臭氧性,不易燃,着火后能自熄,耐油,耐溶剂, 耐酸碱以及耐老化,气密性好等优点; 其物理机械性能也比天然橡胶好, 故可用作通用橡胶,也可用作特种橡胶.主要缺点是耐寒性较差,比重较大,相对成本高, 电绝缘性不好,加工时易粘滚,易焦烧及易粘模.此外,生胶稳定性差,不易保存.使用温度范围:约-45℃~+100℃. 主要用于制造要求抗臭氧,耐老化性高的电缆护套及各种防护套,保护罩;耐油,耐化学腐蚀的胶管,胶带和飞机衬里;耐燃的地下采矿用橡胶制品, 以及各种模压制品,密封圈,垫,粘结剂等.6,丁基橡胶(IIR) 是异丁烯和少量异戊二烯或丁二烯的共聚体. 最大特点是气密性好, 耐臭氧,耐老化性能好,耐热性较高, 长期工作温度可在130℃以下;能耐无机强酸 (如硫酸, 硝酸等)和一般有机溶剂, 吸振和阻尼特性良好,电绝缘性也非常好.缺点是弹性差, 加工性能差,硫化速度慢,粘着性和耐油性差.使用温度范围:约-40℃~+120℃. 主要用作内胎,水胎,气球,电线电缆绝缘层,飞机设备衬里及防震制品,耐热运输带,耐热老化的胶布制品.7,丁晴橡胶(NBR) 丁二烯和丙烯晴的共聚体. 特点是耐汽油和脂肪烃油类的性能特别好,仅次于聚硫橡胶,丙烯酸酯和氟橡胶,而优于其他通用橡胶.耐热性好,气密性, 耐磨及耐水性等均较好,粘结力强.缺点是耐寒及耐臭氧性较差,强力及弹性较低,耐酸性差,电绝缘性不好,耐极性溶剂性能也较差.使用温度范围:约-30℃~+100℃. 主要用于制造各种耐油制品,如胶管,密封制品等.8, 氢化丁晴橡胶 (HNBR) 丁二烯和丙烯晴的共聚体. 它是通过全部或部分氢化NBR 的丁二烯中的双键而得到的.其特点是机械强度和耐磨性高,用过氧化物交联时耐热性比NBR 好,其他性能与丁晴橡胶一样.缺点是价格较高.使用温度范围:约-30℃~+150℃. 主要用于耐油,耐高温的密封制品.9,乙丙橡胶(EPM\\EPDM) 乙烯和丙烯的共聚体,一般分为二元乙丙橡胶和三元乙丙橡胶. 特点是抗臭氧,耐紫外线,耐天候性和耐老化性优异,居通用橡胶之首.电绝缘性,耐化学性,冲击弹性很好,耐酸碱,比重小,可进行高填充配合.耐热可达150℃,耐极性溶剂-酮,酯等,但不耐脂肪烃和芳香烃,其他物理机械性能略次于天然橡胶而优于丁苯橡胶.缺点是自粘性和互粘性很差,不易粘合.使用温度范围:约-50℃~+150℃. 主要用作飞机设备衬里,电线电缆包皮,蒸汽胶管,耐热运输带,汽车用橡胶制品及其他工业制品.10,硅橡胶(Q) 为主链含有硅,氧原子的特种橡胶,其中起主要作用的是硅元素. 其主要特点是既耐高温(最高300℃)又耐低温(最低-100℃) ,是目前最好扥艾寒,耐高温橡胶;同时电绝缘性优良,对热氧化和臭氧的稳定性很高,化学惰性大.缺点是机械强度较低,耐油,耐溶剂和耐酸碱性差,较难硫化,价格较贵.使用温度:-60℃~+200℃. 主要用于制作耐高低温制品(胶管,密封件等) ,耐高温电线电缆绝缘层,由于其无毒无味, 还用于食品及医疗工业.11,氟橡胶(FPM) 是由含氟单体共聚而成的有机弹性体. 其特点耐温高可达300℃, 耐酸碱,耐油性是耐油橡胶中最好的,抗辐射,耐高真空性能好;电绝缘性,机械性能,耐化学腐蚀性,耐臭氧,耐大气老化性均优良.缺点是加工性差,价格昂贵耐寒性差,弹性透气性较低.使用温度范围:-20℃~+200℃. 主要用于国防工业制造飞机,飞机上的耐真空,耐高温,耐化学腐蚀的密封材料,胶管或其他零件及汽车工业.12,聚氨酯橡胶(AU\\EU) 有聚酯(或聚醚)与二异氰酸酯类化合物聚合而成的弹性体. 其特点是耐磨性好,在各种橡胶中是最好的;强度高,弹性好,耐油性优良.耐臭氧, 耐老化,气密性等也优异. 缺点是耐温性能较差,耐水和耐碱性差, 耐芳香烃, 氯化烃及酮, 酯,醇类等溶剂性较差.使用温度范围:约-30℃~+80℃. 制作轮胎紧挨由零件,垫圈, 防震制品,以及耐磨,高强度和耐油的橡胶制品.13,丙烯酸酯橡胶(ACM\\AEM) 它是丙烯酸乙酯或丙烯酸丁酯的聚合物. 其特点是兼有良好的耐热, 耐油性能, 在含有硫, 磷,氯添加剂的润滑油中性能稳定.同时耐老化, 耐氧和臭氧,耐紫外线,气密性优良. 缺点是耐寒性差,不耐水, 不耐蒸汽及有机和无机酸,碱.在甲醇,乙二醇,酮酯等水溶性溶液内膨胀严重.同时弹性和耐磨性差,电绝缘性差, 加工性能较差.使用温度范围:约-25℃~+150℃. 可用于制造耐油,耐热,耐老化的制品,如密封件,胶管,化工衬里等.14,氯磺化聚乙烯橡胶(CSM) 它是聚乙烯经氯化和磺化处理后,所得到具有弹性的聚合物. 耐臭氧紧挨老化优良,耐候性优于其它橡胶.阻燃,耐热,耐溶剂性及耐大多数化学药品和耐酸碱性能较好. 电绝缘性尚可, 耐磨性与丁苯橡胶相似. 缺点是抗撕裂性能差, 加工性能不好.使用温度范围:约-20℃~+120℃. 可用作臭氧发生器上的密封材料,制造耐油密封件,电线电缆包皮以及耐油橡胶制品和化工衬里.15,氯醚橡胶(CO\\ECO) 由环氧氯丙烷均聚或由环氧氯丙烷与环氧乙烷共聚而成的聚合物. 特点是耐脂肪烃及氯化烃溶剂,耐碱,耐水,耐老化性能极好,耐臭氧性,弹性较差,电绝缘性不良.可用作胶管,密封件,薄膜和容器衬里,油箱,胶辊,制造油封,水封等.16,氯化聚乙烯橡胶(CM 或 CPE) 是聚乙烯通过氯取代反应制成的具有弹性的聚合物. 性能与氯磺化聚乙烯橡胶接近,其特点是流动性好,容易加工;有优良的耐天候性, 耐臭氧性和耐电晕性,耐热,耐酸碱,耐油性良好.缺点是弹性差,压缩变形较大,电绝缘性较低.使用温度范围:约-20℃~+120℃. 电线电缆护套,胶管,胶带,胶辊化工衬里等.橡胶产品表面有气泡. 1.有水份 (混炼时加点氧化钙) 2.未充分硫化,不熟看起来有气泡. 3.硫化剂杂质较多,小分子的杂质提前变成分解,气泡残留制品中 4.模具本身排气设计不合理,胶料冲线时气不能及时排出!5.分散不良.6.胶料塑炼时间长.产品硫化时也有气泡.。
橡胶产品不合格处置方案

橡胶产品不合格处置方案在生产过程中,有时会出现橡胶产品的不合格情况。
这种情况需要及时处理,避免不良影响。
本文将介绍橡胶产品不合格的处置方案。
不合格橡胶产品的定义不合格橡胶产品是指未能达到相关标准要求的产品。
这些产品可能存在缺陷,或未通过相关检测标准。
如不同型号、规格、客户要求不符合等。
处置方案1. 橡胶产品质量纠正措施当发现橡胶产品存在不合格情况时,首先需要进行质量纠正措施,以保障客户利益和公司形象。
质量纠正措施包括但不限于:•零部件更新或更换•采取隔离措施•重新制造2. 不合格橡胶产品的处理方法如果无法进行质量纠正措施,则需要进行不合格橡胶产品的处理方法。
处理方法包括:2.1 报废处理对于严重的不合格橡胶产品,应直接予以报废处理。
以下是报废处理的具体步骤:•首先对有问题的橡胶产品进行记录,并进行初步的缺陷分析。
•确认不合格产品的具体数量和品种,测量记录各项指标和数据,并将其填写入不合格统计表中,以便于管理和监督。
•在报废处置方案确认后,对不合格产品进行标识,以便于区别已报废的产品和未报废的产品。
并尽快将其报废,并进行记录。
2.2 重制或改制处理橡胶制品的特性决定了可再生利用率高。
如果有可能实现再生利用,也就降低了产品的浪费和环境污染,具有 very positive 的成本效益。
更具体地说,建议采取以下方案:•返修:重做或修改被建议,修改后应再次进行检查合格,确认达到客户目的和质量标准。
•二次加工:细整、混合等工序,如适用。
•破碎:将不合格橡胶产品破碎重新制品,如方砖、O形圈用素片等,消化产库,减小库存量,增加利用率。
3. 橡胶产品质量控制措施为更好的控制橡胶制品生产质量,以达到提高市场地位、保障用户利益,应建立完善的制品质量跟踪计划和质量检测点,具体建议如下:•全面检查生产工艺流程。
•采用层层把关的质量检测制度和检验标准对关键的环节、关键的部位的检验要求、和对方案的复核。
•对从库存进料到出厂检验全程跟踪,确保随时发现、追溯不合格品、是时有针对性的纠正问题。
橡胶产品基本缺陷产生原因及解决措施

3. 排气时模具排不开,气体在型腔内 无法散出。
解决措施
1.根据具体问题重新制定工艺 2.调整注射压力及流量。 3.调整排气的停留时间和排气 次数。
五、产品缺陷、4M原因分析、措施
缺陷名称:裂 口
定 义:产品胶体裂
开,在自然
状态下往往
呈闭合状态
,受力变形
后可以看出
解决措施
1.进行现场培训,提高员工技 能和质量意识及自检意识。
2.员工严格按工艺规定、作业 指导书生产。 3.生产时,保持型腔清洁。
五、产品缺陷、4M原因分析、措施
烂泡4M分析:机(machine)
主要生产原因 1.热板温度不正常、设备不保压。 2.模板不平造成型腔受热不均。 3.模具排气不畅或无排气孔。 4.模具型腔粗糙度差。 5.抽真空设备出现异常或密封条损坏
11、如待骨架或计划完成换模停机,应及时排空螺 杆和射料管内的胶料,以免胶料在螺杆及射料 管内老化,造成射料管胶料堵塞;
12、下班前要停机清扫设备,保持清洁。
四、常见硫化违反工艺操作形式: 1、硫化三要素未按工艺执行。 2、生产时操作工未戴白手套或戴布手套上骨架造成骨
架表面粘合剂污染。 3、操作工生产时将骨架上入型腔定位后在清理流道废
边。 4、操作工生产时在出模/进模时清理流道废边。 5、操作工未按工艺要求每二小时检测一次模温,并
未在温度点检表上做记录。
安徽中鼎减震橡胶技术有限公司
6、生产时有脱模器不用,用骨架顶取产品。 7、操作工未按工艺要求自检。 8、就餐时将产品超时压在模具中,造成产品过
硫。 9、烫坏骨架未按要求做标识进行隔离,造成混
接影响硫化速度和产品质量。硫化温度和硫化时间是 相互制约的,硫化温度高,硫化速度快;硫化温度低 ,硫化速度慢。提高硫化温度可以缩短硫化时间,提 高生产效率。但也要考虑其他方面的因素,也不是温 度越高越好。
橡胶制品外观缺陷及解决方案

橡胶制品外观缺陷及解决方案预览说明:预览图片所展示的格式为文档的源格式展示,下载源文件没有水印,内容可编辑和复制橡胶制品外观缺陷及解决方案篇一:橡胶模压制品常见缺陷及解决方法喷霜混炼胶或硫化胶内部的液体或固体配合剂因迁移而在橡胶制品表面析出形成云雾状或白色粉末物质的现象。
这是由于硫、石蜡、某些防老剂、软化剂的使用量超出了它们在橡胶中的溶解度而引起的。
为防止喷霜,上述各种配合剂用量要适当,对常见的硫黄喷霜可采用不溶性硫黄加以防止。
在橡胶中适当加入松焦油,液体古马隆等可增加胶料对上述配合剂的溶解度,以减少喷霜现象。
喷霜-定义和由来喷霜又名喷出(blooming),是橡胶加工过程中常见的质量问题,它是指未硫化胶或硫化胶中所含的配合剂迁移到表面并析出的现象。
有时,这种喷出物呈霜状结晶物,故习惯上称“喷霜”。
较多见的喷霜物为硫,因为硫黄是通用橡胶中应用最广泛的硫化剂,且在橡胶中的溶解度低因而容易产生喷霜。
其实从喷出物外观来看,也未必都呈霜状,也有呈油状(软化剂、增塑剂)或粉粒状(多为填充剂、防老剂、促进剂等)的物质喷出,甚至炭黑喷出也有所见。
喷霜-防霜剂硅胶也会有喷霜现象,采用双二四硫化剂(通常用在挤出成型工艺)高温分解后会产生低分子量的酸性物质,其与硅橡胶不相容,在存放过程中会转移到硅胶表面结晶从而出现喷霜。
防霜剂主要成分为碱性物质,通过酸碱中和反应来达到防霜的目的。
高硬度的硅胶往往加入比较多的内脱模剂,遇水也会喷白,水的酸性对此有遏制作用硅橡胶模具制作方法及注意事项模具是快速模具里的一种最为简单的方法,一般是用硅胶将RP原型进行复模,但寿命很短,只有10-30 件左右!他具有很好的弹性和复制性能,用硅橡胶复制模可不用考虑拔模斜度,不会影响尺寸精度,有很好的分割性,不用分上下模可直接进行整体浇注。
再沿预定的分模线进行切割取出母模就可以了!室温硫化硅橡胶又分为加成型和缩合型两种!原料及配方采用专用模具硅橡胶,该品系以双包装形式出售,A 组份是胶料,B组份是催化剂。
- 1、下载文档前请自行甄别文档内容的完整性,平台不提供额外的编辑、内容补充、找答案等附加服务。
- 2、"仅部分预览"的文档,不可在线预览部分如存在完整性等问题,可反馈申请退款(可完整预览的文档不适用该条件!)。
- 3、如文档侵犯您的权益,请联系客服反馈,我们会尽快为您处理(人工客服工作时间:9:00-18:30)。
5.注射模料嘴与闷头间隙大,注料时 跑料, 模具球面压坏。
五、产品缺陷、4M原因分析、措施
缺料4M分析:材料(material)
主要生产原因
解决措施
1.胶料焦烧,混炼不均匀,成型件停 1. 调整配方,改善流动性,将
放期太短、胶料流动性太好、硬度低 硬度控制在中上限。
。
2. 严格按相关工艺进行加工,
2.轻微模板不平,可垫砂纸,严 重的应更换模板。
3.模具型腔结垢严重,胶料流动阻力 大或者是设备之间有误差,每台设备 储存量不一样。
4.结构设计不合理:型腔高度不一致 ,模具配合间隙过大或小,注料点太 粗糙及注料孔尺寸不正确,模具老化 。
1.清洗模具或擦模。 2.模具修理或报废。 3.修理设备后保持一致或增加 流量,保证型腔填满。
入合格骨架内生产。
五、产品缺陷、4M原因分析、措施
缺陷名称:缺 料
定 义:胶料流动时,型腔 没有完全充满, 失去应有的形状 导致产品外形不 完整。
缺料
五、产品缺陷、4M原因分析、措施
缺料4M分析:人(man )
主要生产原因
1.硫化人员不按作业指导书要求操作 ,没有得到有效培训或操作工技能不 熟练:如:上料不到位(上错、上偏) 、初压过大、排气次数过少、脱模剂 使用不当:如临时选用其它脱模剂或 不同浓度的同类脱模剂、喷涂不均匀 。
3.上料方法不合理。
根据具体问题重新制定合理工 艺。途径:由班长/工序质控 员以《硫化工艺完善记录》形 式提出更改,或工艺员主动更 改。
4.脱模剂选用不当,浓度大,未规定 喷涂位置、喷涂次数。
5.胶料从上模流道板溢出造成产品缺 料。
增加压力,减小注射压力流量 ,检查增压时间和模具行程。
五、产品缺陷、4M原因分析、措施
❖ 硫化时间的作用:
硫化时间是完成硫化反应过程的条件,它由胶料配方 、硫化温度和压力决定,对于特定胶料来说,在一定的硫 化温度和硫化条件下,有一最适宜的硫化时间(既正硫化 时间)。当时间超过这一时间时,橡胶制品就会产生过硫 ,时间没有达到时,橡胶制品就会欠硫。过硫、欠硫都会 导致品性能严重下降。
硫化的四个阶段: 诱导期、热硫化期、正硫化期、过硫期
三、硫化操作时应注意事项 1、不允许超压使用设备,不准空机上升加压; 2、 操作工不准擅自调节液压系统有关压力和流量,不
允许调节压力表上的压力指针,以防损坏设备; 3、不准用铁铲、铜棒等坚硬物敲击设备; 4、设备在工作时严禁将身体的任何部位进入其运动区
域; 5、合模时要检查模具与上模板导柱是否对齐,防止压
缺陷名称:烂 泡 定 义:产品表面有明
显的凸起且呈 蜂窝状,烂泡 部位产品疏松。
烂泡
五、产品缺陷、4M原因分析、措施
烂泡4M分析:人(man )
苏州美隆 橡塑制品有限公司
1
目录
一、培训目的 二、硫化知识 三、硫化操作时应注意事项
四、常见硫化违反工艺操作形式 五、产品缺陷、4M原因分析、措施
2
一、培训目的
为了让员工了解产品的外观缺 陷,运用所学的知识制定出解决措 施,提高操作工的生产技能和质量 意识。让员工了解生产上的质量异 常、掌握质量控制的基本方法,确 保生产过程受控稳定,最终达到提 升生产效率和合格率,减少成本损 失,以保证产品质量满足客户要求。
接影响硫化速度和产品质量。硫化温度和硫化时间是 相互制约的,硫化温度高,硫化速度快;硫化温度低 ,硫化速度慢。提高硫化温度可以缩短硫化时间,提 高生产效率。但也要考虑其他方面的因素,也不是温 度越高越好。
5
❖ 硫化压力的作用: 1、可以防止橡胶制品在硫化过程中产生气泡,提高胶料 的致密性;
2、可使胶料易于流动和充满模腔; 3、提高胶料与骨架的附着力; 4、可有助于提高硫化胶的物理机械性能。
解决措施
1.进行现场培训,提高操作工 技能和质量意识及自检意识。 2.如中夜班脱模剂短缺急用时 ,应做好验证工作。
五、产品缺陷、4M原因分析、措施
缺料4M分析:机(machine)
主要生产原因
解决措施
1.设备漏油、掉压。
2.受压面不平、模板不平、极限压力 达不到工艺要求 。
1.设备维修或换机台生产。
2.成型件未按工艺要求成型:单耗小 使成型件符合工艺要求。
、规格不符 。
3.胶料流动性差,注射速度慢造成产 3.将胶料退予成型翻练后再生产 品缺料。
五、产品缺陷、4M原因分析、措施
缺料4M分析:方法(method)ຫໍສະໝຸດ 主要生产原因解决措施
1.工艺要求成型件规格不合理:单耗 偏小,材料利用率过高。 2.初压偏大、加压过快、压力偏小 。
3
苏州美隆橡塑制品有限公司
二、硫化知识: ❖ 1、硫化定义:
硫化是在一定的温度、压力和时间条件下,通 过一系列的物理化学反应,使线型橡胶分子结构变 成空间立体网状橡胶分子结构的过程。 ❖ 2、何为硫化三要素?各起什么作用?
硫化温度、硫化时间、硫化压力称硫化三要素
4
❖ 硫化温度的作用: 硫化温度是橡胶发生硫化反应的基本条件,它直
边。 4、操作工生产时在出模/进模时清理流道废边。 5、操作工未按工艺要求每二小时检测一次模温,并
未在温度点检表上做记录。
安徽中鼎减震橡胶技术有限公司
6、生产时有脱模器不用,用骨架顶取产品。 7、操作工未按工艺要求自检。 8、就餐时将产品超时压在模具中,造成产品过
硫。 9、烫坏骨架未按要求做标识进行隔离,造成混
坏模具;
6、设备一旦出现异常,如异味、漏油、漏电、 部件变形、超压等故障时,要立即关机电 源,待排除故障后使用;
7、模具应放在压机加热板正中间部位; 8、每次填料和上骨架时都要彻底清除型腔内
飞边并检查; 9、上完骨架必须检查有无多放、少放、放反,
放置位置是否正确;
安徽中鼎减震橡胶技术有限公司
10、领料时要检查成型件,骨架编号是否与工艺相 符合,如有异常可以退料,并向班长、值班人 员反映;
11、如待骨架或计划完成换模停机,应及时排空螺 杆和射料管内的胶料,以免胶料在螺杆及射料 管内老化,造成射料管胶料堵塞;
12、下班前要停机清扫设备,保持清洁。
四、常见硫化违反工艺操作形式: 1、硫化三要素未按工艺执行。 2、生产时操作工未戴白手套或戴布手套上骨架造成骨
架表面粘合剂污染。 3、操作工生产时将骨架上入型腔定位后在清理流道废