注塑产品缺陷分析及解决方案
注塑工艺与产品缺陷解决方案100例

注塑工艺与产品缺陷解决方案注塑工艺是一种常见的制造方法,用于生产各种塑料制品。
然而,在注塑过程中可能会出现一些产品缺陷。
以下是一些常见的注塑产品缺陷及其解决方案:1. 短射(Short Shot):指塑料注射不完整,导致产品部分或全部空洞。
解决方案包括:- 检查模具温度和压力,确保足够的塑料流动。
- 检查塑料熔融温度和压力,确保充分熔融。
- 检查模具设计,确保填充均匀。
2. 气泡(Air Traps):在产品内部形成气泡,影响外观和强度。
解决方案包括:- 调整注射速度和压力,以减少气体陷阱的形成。
- 优化模具通道和冷却系统,确保塑料充分流动并迅速冷却。
3. 热胀冷缩(Warping):产品在冷却后变形或扭曲。
解决方案包括:- 优化模具温度和冷却系统,确保均匀冷却。
- 调整注射速度和压力,避免内部应力积累。
- 使用合适的塑料材料,具有较低的热胀冷缩性能。
4. 流痕(Flow Marks):产品表面出现纹理或痕迹。
解决方案包括:- 调整注射速度和压力,确保塑料流动顺畅。
- 优化模具设计,减少填充阻力。
- 提高模具温度,增加塑料流动性。
5. 毛刺(Flash):产品边缘出现额外的塑料。
解决方案包括:- 检查模具关闭力,确保模具严密闭合。
- 检查模具设计,减少模具间隙。
- 控制注射速度和压力,避免过多的塑料溢出。
6. 熔接线(Weld Lines):由于塑料流动不畅导致的界面线。
解决方案包括:- 调整注射速度和压力,以减少熔接线形成。
- 优化模具设计,减少填充阻力。
- 提高模具温度,增加塑料流动性。
以上只是一些常见的注塑产品缺陷及其解决方案,具体解决方案还需要根据具体情况进行调整和优化。
为了确保产品质量,注塑过程中的工艺参数、模具设计以及塑料材料的选择都非常重要。
注塑缺陷原因分析与解决方案
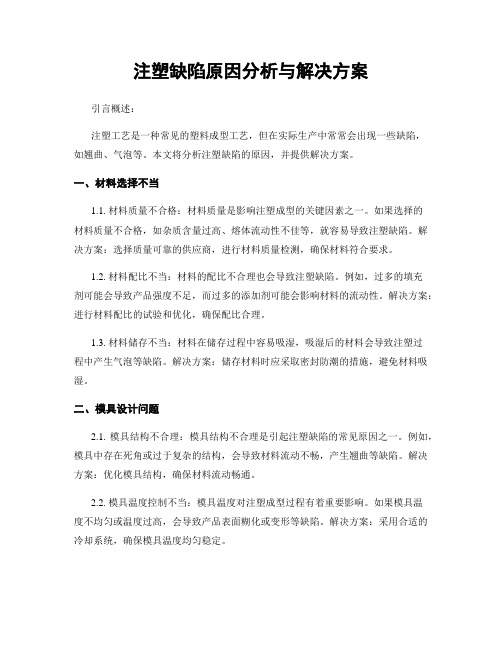
注塑缺陷原因分析与解决方案引言概述:注塑工艺是一种常见的塑料成型工艺,但在实际生产中常常会出现一些缺陷,如翘曲、气泡等。
本文将分析注塑缺陷的原因,并提供解决方案。
一、材料选择不当1.1. 材料质量不合格:材料质量是影响注塑成型的关键因素之一。
如果选择的材料质量不合格,如杂质含量过高、熔体流动性不佳等,就容易导致注塑缺陷。
解决方案:选择质量可靠的供应商,进行材料质量检测,确保材料符合要求。
1.2. 材料配比不当:材料的配比不合理也会导致注塑缺陷。
例如,过多的填充剂可能会导致产品强度不足,而过多的添加剂可能会影响材料的流动性。
解决方案:进行材料配比的试验和优化,确保配比合理。
1.3. 材料储存不当:材料在储存过程中容易吸湿,吸湿后的材料会导致注塑过程中产生气泡等缺陷。
解决方案:储存材料时应采取密封防潮的措施,避免材料吸湿。
二、模具设计问题2.1. 模具结构不合理:模具结构不合理是引起注塑缺陷的常见原因之一。
例如,模具中存在死角或过于复杂的结构,会导致材料流动不畅,产生翘曲等缺陷。
解决方案:优化模具结构,确保材料流动畅通。
2.2. 模具温度控制不当:模具温度对注塑成型过程有着重要影响。
如果模具温度不均匀或温度过高,会导致产品表面糊化或变形等缺陷。
解决方案:采用合适的冷却系统,确保模具温度均匀稳定。
2.3. 模具磨损严重:模具长时间使用后会出现磨损,磨损严重的模具会导致产品尺寸不准确或表面粗糙等缺陷。
解决方案:定期检查和维护模具,及时更换磨损严重的模具部件。
三、注塑工艺参数设置不当3.1. 注射压力过高或过低:注射压力是影响注塑成型的关键参数之一。
如果注射压力过高,会导致产品变形或开裂,而注射压力过低则会导致产品表面光洁度不高。
解决方案:根据产品要求和材料特性,合理设置注射压力。
3.2. 注射速度不合理:注射速度对产品的充填和冷却过程有着重要影响。
如果注射速度过快,会导致产品内部产生气泡或短射,而注射速度过慢则会导致产品表面瑕疵。
注塑制品缺陷的原因分析与解决措施

环境湿度变化大,影响塑料的稳定性和制品的外观。
空气污染
空气中存在灰尘、油雾等污染物,影响制品的外观和 质量。
03
注塑制品缺陷的解决措施
优化模具设计
模具设计合理化
确保模具设计符合产品要求,避免出现倒扣、 侧扣等设计不合理的地方。
避免模具损伤
提高模具的耐用性,避免使用过程中出现磨损 、断裂等问题。
优化浇口设计
合理设计浇口位置和大小,确保塑料能够均匀流入模具型腔。
把关原料质量
严格控制原料成分
确保原料中不含有杂质、异物等不良成分。
定期检测原料性能
对原料的性能进行定期检测,以确保其符合 生产要求。
加强原料存储管理
避免原料在存储过程中受潮、污染等问题。
调整工艺参数
合理调整注塑温度
根据塑料的性质和产品要求,合理调整注塑温度。
201 4
案例三:注塑制品出现银纹的原因及解决方法
原因分析
1. 塑料中含有水分或挥发性物质,导致银纹产 生。
2. 模具温度过低,导致塑料无法完全流动,出 现银纹。
案例三:注塑制品出现银纹的原因及解决方法
• 注射速度过快或压力过低,导致塑料在模具中流动不均匀,出现银纹。
案例三:注塑制品出现银纹的原因及解决方法
注塑制品缺陷的原因
分析与解决措施
汇报人:
日期:
• 注塑制品缺陷概述 • 注塑制品缺陷的原因分析 • 注塑制品缺陷的解决措施 • 注塑制品缺陷案例分析
目录
01
注塑制品缺陷概述
注塑制品常见缺陷
01 02 03 04
翘曲变形 缩痕 气泡 烧焦
注塑制品常见缺陷
01 02
溢边 裂纹
颜色差异
注塑缺陷原因分析与解决方案
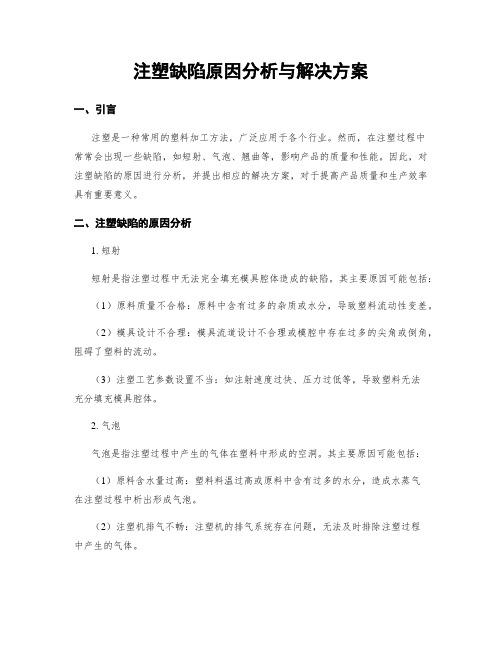
注塑缺陷原因分析与解决方案一、引言注塑是一种常用的塑料加工方法,广泛应用于各个行业。
然而,在注塑过程中常常会出现一些缺陷,如短射、气泡、翘曲等,影响产品的质量和性能。
因此,对注塑缺陷的原因进行分析,并提出相应的解决方案,对于提高产品质量和生产效率具有重要意义。
二、注塑缺陷的原因分析1. 短射短射是指注塑过程中无法完全填充模具腔体造成的缺陷。
其主要原因可能包括:(1)原料质量不合格:原料中含有过多的杂质或水分,导致塑料流动性变差。
(2)模具设计不合理:模具流道设计不合理或模腔中存在过多的尖角或倒角,阻碍了塑料的流动。
(3)注塑工艺参数设置不当:如注射速度过快、压力过低等,导致塑料无法充分填充模具腔体。
2. 气泡气泡是指注塑过程中产生的气体在塑料中形成的空洞。
其主要原因可能包括:(1)原料含水量过高:塑料料温过高或原料中含有过多的水分,造成水蒸气在注塑过程中析出形成气泡。
(2)注塑机排气不畅:注塑机的排气系统存在问题,无法及时排除注塑过程中产生的气体。
(3)注塑工艺参数设置不当:如注射速度过快、压力过高等,造成塑料内部气体无法顺利排出。
3. 翘曲翘曲是指注塑制品在冷却后出现变形的现象。
其主要原因可能包括:(1)模具温度不均匀:模具温度不均匀导致注塑制品冷却不均匀,从而引起翘曲。
(2)注塑过程中的应力积累:注塑过程中,塑料在注射后会受到冷却和收缩的影响,如果释放不及时,会导致应力积累引起翘曲。
(3)注塑工艺参数设置不当:如注射速度过快、冷却时间过短等,造成塑料冷却不充分,引起翘曲。
三、注塑缺陷的解决方案1. 短射的解决方案(1)优化原料质量:选择质量合格的原料,避免杂质和水分的存在。
(2)优化模具设计:合理设计模具流道,避免尖角和倒角的存在,保证塑料的顺畅流动。
(3)优化注塑工艺参数:合理设置注射速度和压力,确保塑料能够充分填充模具腔体。
2. 气泡的解决方案(1)控制原料含水量:确保塑料料温适宜,原料中的水分含量符合要求。
注塑缺陷及其解决方法
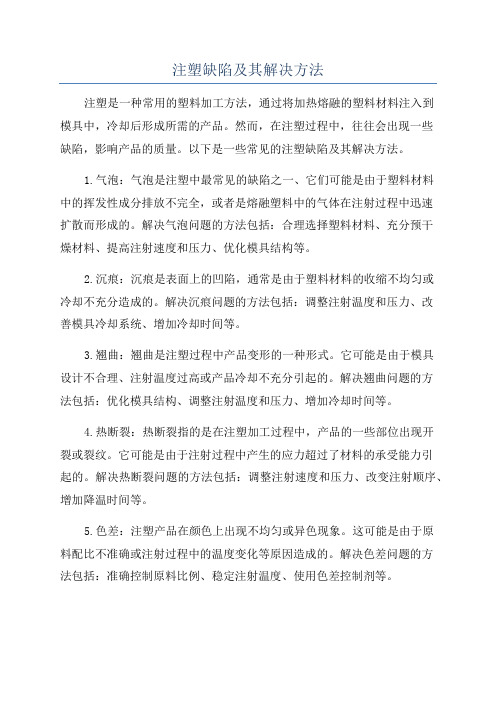
注塑缺陷及其解决方法注塑是一种常用的塑料加工方法,通过将加热熔融的塑料材料注入到模具中,冷却后形成所需的产品。
然而,在注塑过程中,往往会出现一些缺陷,影响产品的质量。
以下是一些常见的注塑缺陷及其解决方法。
1.气泡:气泡是注塑中最常见的缺陷之一、它们可能是由于塑料材料中的挥发性成分排放不完全,或者是熔融塑料中的气体在注射过程中迅速扩散而形成的。
解决气泡问题的方法包括:合理选择塑料材料、充分预干燥材料、提高注射速度和压力、优化模具结构等。
2.沉痕:沉痕是表面上的凹陷,通常是由于塑料材料的收缩不均匀或冷却不充分造成的。
解决沉痕问题的方法包括:调整注射温度和压力、改善模具冷却系统、增加冷却时间等。
3.翘曲:翘曲是注塑过程中产品变形的一种形式。
它可能是由于模具设计不合理、注射温度过高或产品冷却不充分引起的。
解决翘曲问题的方法包括:优化模具结构、调整注射温度和压力、增加冷却时间等。
4.热断裂:热断裂指的是在注塑加工过程中,产品的一些部位出现开裂或裂纹。
它可能是由于注射过程中产生的应力超过了材料的承受能力引起的。
解决热断裂问题的方法包括:调整注射速度和压力、改变注射顺序、增加降温时间等。
5.色差:注塑产品在颜色上出现不均匀或异色现象。
这可能是由于原料配比不准确或注射过程中的温度变化等原因造成的。
解决色差问题的方法包括:准确控制原料比例、稳定注射温度、使用色差控制剂等。
6.熔接线:熔接线是由于注塑模具的设计和操作问题导致两个或多个熔融塑料部分相互连接而形成的。
解决熔接线问题的方法包括:调整模具结构,避免部件交汇点过多,调整注射速度和压力等。
总之,注塑缺陷的解决方法主要包括调整材料配比、优化模具结构、控制注射温度和压力、增加冷却时间等。
同时,及时调整机器参数、进行模具维护和清洁,以保证注塑过程的稳定性和可靠性。
通过以上的措施,可以有效减少注塑缺陷,提高产品质量。
注塑缺陷描述及解决方案

注塑缺陷描述及解决方案注塑是一种常用的塑料加工方法,通过将熔融的塑料材料注入模具中,然后冷却成型,最终得到所需的产品。
然而,在注塑过程中,可能会出现一些缺陷,如气泡、短射、毛刺等,这些缺陷会降低产品质量,影响生产效率。
因此,及时发现并解决注塑缺陷是非常重要的。
首先,气泡是注塑中常见的缺陷之一、气泡通常由以下原因引起:塑料材料中含有水分、注塑机压力不稳定、模具排气不畅等。
为解决气泡缺陷,可以采取以下措施:在使用塑料材料之前对其进行干燥处理,确保材料中不含水分;调整注塑机的压力和速度,保持稳定的注塑过程;对模具进行排气孔设计,确保顺畅排气。
其次,短射是另一种常见的注塑缺陷。
短射通常是由于塑料材料流动性不好、充型不足或注塑机压力不足等原因引起的。
为解决短射问题,可以采取以下措施:选用流动性好的塑料材料,例如增加流动助剂;优化模具的设计,确保充型顺畅;调整注塑机的压力和速度,保证充型充分。
此外,毛刺也是一种常见的注塑缺陷。
毛刺通常是由于模具接缝不严、射出速度过快、注塑机压力过高等原因引起的。
为解决毛刺问题,可以采取以下措施:检查和调整模具接缝,确保接缝紧密;调整射出速度和注塑机压力,控制流动状态,减少毛刺的产生。
此外,还可能出现其他一些注塑缺陷,如烧焦、变色等。
对于这些缺陷,可以通过调整注塑工艺参数、改进模具设计、使用优质的塑料材料等方法加以解决。
总之,注塑缺陷的解决需要综合考虑塑料材料的选择、注塑机的调整以及模具设计等因素。
通过合理的工艺控制和改进,可以有效降低注塑缺陷的发生,提高产品质量和生产效率。
同时,及时发现和解决注塑缺陷也需要经验丰富的操作人员进行实时监控和调整。
注塑产品常见缺陷

注塑产品常见缺陷注塑产品常见缺陷及其原因分析注塑产品在生产过程中可能会遇到各种缺陷,这些缺陷可能源于产品设计、模具制造、材料选择、注塑工艺等多个因素。
以下是一些常见的注塑产品缺陷及可能的原因分析:1.填充不足(缺料)这可能是由于注塑压力不足、注射时间过短、模具排气不良、浇口设计不合理等原因造成的。
解决这个问题的方法包括增加注塑压力、延长注射时间、优化模具排气设计、改进浇口位置等。
2.溢料(毛边)溢料通常是由于注射压力过高、浇口设计不当、模具磨损等原因造成的。
解决溢料问题的方法包括降低注塑压力、优化浇口设计、修复模具磨损等。
3.气泡(气孔)气泡可能是由于塑料在模具中未完全填满、气体未完全排出、注射速度过快等原因造成的。
解决气泡问题的方法包括降低注射速度、增加冷却时间、优化模具设计等。
4.变形变形可能是由于产品结构不合理、冷却不均匀、模具温度波动等原因造成的。
解决变形问题的方法包括优化产品结构设计、改善冷却条件、稳定模具温度等。
5.银纹(流纹)银纹可能是由于塑料流动不均匀、模具温度过低、注射速度过快等原因造成的。
解决银纹问题的方法包括优化注射条件、提高模具温度、降低注射速度等。
6.裂纹(龟裂)裂纹可能是由于产品结构设计不合理、材料韧性不足、注射压力过高等原因造成的。
解决裂纹问题的方法包括优化产品结构设计、更换韧性更好的材料、降低注射压力等。
7.翘曲(扭曲)翘曲可能是由于产品结构设计不合理、模具温度不均匀、注射压力过低等原因造成的。
解决翘曲问题的方法包括优化产品结构设计、改善冷却条件、提高注射压力等。
8.冷块(冷凝物)冷块可能是由于塑料在冷却过程中速度过快、模具温度过低等原因造成的。
解决冷块问题的方法包括降低冷却速度、提高模具温度等。
9.喷射痕迹(蛇形纹)喷射痕迹可能是由于注射速度过快、浇口设计不当等原因造成的。
解决喷射痕迹问题的方法包括降低注射速度、优化浇口设计等。
10.颜色分布不均(色差)颜色分布不均可能是由于材料混合不均匀、注塑条件不稳定等原因造成的。
注塑缺陷描述及解决方案

注塑缺陷描述及解决方案一、缺陷描述在注塑过程中,可能会浮现各种缺陷,这些缺陷会影响产品的质量和外观。
以下是常见的注塑缺陷描述:1. 气泡缺陷:在注塑制品表面或者内部浮现气泡,影响产品的美观度和强度。
2. 热胀冷缩缺陷:注塑制品在冷却过程中,由于热胀冷缩不均匀,导致产品尺寸不许确或者变形。
3. 短射缺陷:注塑模具中的塑料未能充满模腔,导致产品浮现不完整或者部份缺失。
4. 毛刺缺陷:注塑制品表面浮现细小的毛刺,影响产品的外观质量。
5. 沉痕缺陷:注塑制品表面浮现凹陷或者凸起的痕迹,影响产品的美观度。
6. 热裂缺陷:注塑制品在冷却过程中,由于塑料内部应力过大,导致浮现裂纹。
7. 毛躁缺陷:注塑制品表面浮现粗糙的纹理或者颗粒,影响产品的触感和外观。
二、解决方案针对以上注塑缺陷,可以采取以下解决方案:1. 控制注塑工艺参数:合理调整注塑机的注射速度、压力、温度等参数,确保塑料充满模腔,避免短射温和泡缺陷的发生。
2. 优化模具设计:对于容易浮现热胀冷缩缺陷的产品,可以通过优化模具结构和冷却系统设计,平衡热胀冷缩过程,减少尺寸偏差和变形。
3. 选择合适的塑料材料:根据产品的要求和使用环境,选择适合的塑料材料,以提高产品的强度和耐用性,减少热裂和毛刺缺陷的发生。
4. 加工后处理:对于浮现毛刺、沉痕和毛躁等缺陷的产品,可以采用打磨、抛光、喷涂等后处理方法,改善产品的外观质量。
5. 增加注塑模具的维护保养:定期清洁和保养注塑模具,确保模具表面光滑,减少缺陷的发生。
6. 引入质量控制措施:建立完善的质量控制体系,通过检测和测试,及时发现和解决注塑缺陷问题,确保产品质量符合要求。
总结:注塑缺陷的描述及解决方案是为了匡助生产企业更好地理解和解决注塑过程中可能浮现的问题。
通过合理调整工艺参数、优化模具设计、选择合适的材料、加工后处理和加强质量控制,可以有效地解决注塑缺陷问题,提高产品质量和客户满意度。
- 1、下载文档前请自行甄别文档内容的完整性,平台不提供额外的编辑、内容补充、找答案等附加服务。
- 2、"仅部分预览"的文档,不可在线预览部分如存在完整性等问题,可反馈申请退款(可完整预览的文档不适用该条件!)。
- 3、如文档侵犯您的权益,请联系客服反馈,我们会尽快为您处理(人工客服工作时间:9:00-18:30)。
3:提高射出速度、调整加工温度。
4:选用高融指、高流动性材料。
黑点
(杂质)
1:熔体温度过高、分解,螺杆结碳。
2:材料在混合、输送时受到污染。
3:材料本身有黑点。
1:降低熔体温度、清洗螺杆。
2:严格控制混合、输送时的标准作业流程。
3:换材料。
变形
(翘曲)
1:材料的尺寸稳定不好、异向收缩。
2:适当提高注射压力、速度及时间。
3:加点流道及浇口尺寸、提高模温。
4:加开排气,保证排气顺畅。
5:尝试使用较高融指的材料。
6:选用合适的加工温度。
飞边
(披锋)
1:模具精密度不够,分型面有间隙。
2:机台锁模力不够、失效。
3:注射速度、压力过大。
4:熔体温度、模具温度过高。
1:重新配合分型面间隙。
2:选用足够锁模力的机台,检测锁模系统是否正常。
2:工艺不合理。
3:产品结构受限、设计不合理。
1:选用尺寸稳定材料或者无定型塑料。
2:优化工艺。
3:优化合理设计、对变形产品进行整形。
光泽度不好
1:模具表面抛光不够,模具温度过低。
2:射出速度、压力过低,熔体未贴紧模具表面,熔体温度不合理。
1:模具表面重新抛光,提高模具温度。
2:提高射出速度、压力,优化熔体温度。
缺陷
产生缺陷原因
解决措施
凹痕
(缩痕)
(缩水)
由于塑料加热后,熔体进入模具,会有冷却过程,冷却的同时会伴随收缩的过程,而这个过程必须提供足够的熔体填充,如果冷却过快,无法提供足够的补偿,会造成缩痕、凹痕。
要想保证足够的熔体补偿,预防熔体过快冷却:
1:流道系统必须足够大(浇口厚度大于产品厚度一半)
2:有足够高的模具温度,延长冷凝时间。
凹痕
(缩痕)
(缩水)
缺料
欠注
飞边
(披锋)
银纹
银丝
水花
气痕
浮纤
色差纹
雾纹
熔接线
(熔接痕)
黑点
杂质
变形
(翘曲)
光泽度不好
3:有足够长的填充时间、压力。
4:要保证有足够的料垫。
缺料
(欠注)
1:机台的容量是否过小,螺杆止逆阀是否磨损。
2:机台的压力速度是否过低,填充时间太短。
3:模具流道是否过小、模温是否过低。
4:模具是否困气(排气不良)。
5:材料熔体是否过低(流动性不好)。
6:加工温度是否过低。
1:选用足够大容量机台,检测螺杆止逆阀。
5:降低射出速度。
浮纤
1:模具温度过低。
2:熔体温度过低。
3:射出速度过慢。
1:提高模具温度。
2:提高熔体温度。
3:提高注射速度。
色差纹
(云雾纹)
1:色母、色粉分散不够均匀,螺杆剪切不够。
2:色母、色粉分散性不好。
3:材料与色母在搅拌时未搅拌均匀。
4:加工温度过高或过低。
5:螺杆未清洗干净。
1:提高储料背压、提高螺杆转速,增加储料量。
3:适当优化注射速度、压力。
4:适当降低熔体及模具温度。
银纹
(银丝)
(水花)
(气痕)
1:材料干燥不彻底。
2:熔体温度Leabharlann 高。3:储料(溶胶)背压过低,溶胶速度过快。
4:模具排气不良、浇口过细。
5:射速过快。
1:彻底干燥材料。
2:适当调整熔体温度。
3:适当加高背压、降低溶胶速度。
4:增加模具排气、加大浇口尺寸。
2:提高色母、色粉的分散性,可以通过增加分散剂或者选用好的分散剂实现。
3:延长材料混合时间,适当调整加工温度。
4:充分清洗螺杆。
熔接线
(熔接痕)
1:模具温度过低、流道系统太小。
2:模具排气不良、结构不合理。
3:射出速度过低、加工温度偏低。
4:材料融指过低,流动性太差。
1:提高模具温度、加大流道系统尺寸。