特种陶瓷_整理版
特种陶瓷简介

10.2.1.1 氧化铝陶瓷
• 是以α-Al2O3为主晶相的陶瓷材料,其Al2O3含量一般 在75-99%之间,并习惯以配料中Al2O3含量分类。 Al2O3含量在75%左右为“75瓷”,含量在85%为“85 瓷”,含量在95%的为“95瓷”,含量在99%的为“99 瓷”。 • 氧化物陶瓷用途最广的是氧化铝。它是唯一以单晶形式 广泛使用的氧化物陶瓷。然而以多晶氧化铝的用途占压 倒多数。以质量计算氧化铝基材料的主要市场为:
(4)气氛烧结
• 对在空气中很难烧结的制品,为防止其氧化,可在炉膛内通入一
定量的某种气体,在这种特定气氛下进行烧结称为气氛烧结。
(5)反应烧结
• 通过多孔坯体同气相或液相发生化学反应,使坯体质量增加,空 隙减少,并烧结成具有一定强度和尺寸精度的成品的一种烧结工艺。
(6)化学气相沉积法
• 将准备在其表面沉积一层瓷质薄膜的物质置于真空室中,加热至 一定温度后,然后将欲被覆涂料的气态化合物通过加热载体的表面。
一般不需要加工
炊具、餐具、陈设品
10.1 特种陶瓷工艺特点 10.2 高温结构陶瓷简介
10.3 发展中的特种陶瓷
10.1特种陶瓷工艺特点
• 主要从粉体制备、成型和烧结三方面来简述其工艺特点。
10.1.1粉体制备
制取方法有两大类:
机械破碎法,只占从属地位,不作介绍
物理化学法:通常包括固相法、液相法、气相法。
(3)流延法成型
• 将准备好的粉料内加粘结剂、增塑剂、分散剂、溶剂,然后进行混合,再将 料浆放入流延机料斗中,料浆从料斗下部流至流延机薄膜载体(传送带)上。 用刮刀控制厚度,再经红外线加热等方法烘干,得到膜坯,连同载体一起卷 轴待用。
料浆 刮刀 剥离成型薄膜 干燥炉
特种陶瓷

特种陶瓷,又称精细陶瓷,按其应用功能分类,大体可分为高强度、耐高温和复合结构陶瓷及电工电子功能陶瓷两大类。
在陶瓷坯料中加入特别配方的无机材料,经过1360度左右高温烧结成型,从而获得稳定可靠的防静电性能,成为一种新型特种陶瓷,通常具有一种或多种功能,如:电、磁、光、热、声、化学、生物等功能;以及耦合功能,如压电、热电、电光、声光、磁光等功能。
目录分类1.氧化物陶瓷2.氮化物陶瓷3.碳化物陶瓷4.硼化物陶瓷5.硅化物陶瓷6.氟化物陶瓷7.硫化物陶瓷8.其他制作工艺1.成形方法与结合剂的选择2.陶瓷注射成形和成形用结合剂3.陶瓷挤压成形和成形用结合剂发展新动向1.重要地位2.技术新发展3.应用新发展4.研究开发重点发展前景分类1.氧化物陶瓷2.氮化物陶瓷3.碳化物陶瓷4.硼化物陶瓷5.硅化物陶瓷6.氟化物陶瓷7.硫化物陶瓷8.其他制作工艺1.成形方法与结合剂的选择2.陶瓷注射成形和成形用结合剂3.陶瓷挤压成形和成形用结合剂发展新动向1.重要地位2.技术新发展3.应用新发展4.研究开发重点发展前景展开分类特种陶瓷特种陶瓷是二十世纪发展起来的,在现代化生产和科学技术的推动和培育下,它们"繁殖"得非常快,尤其在近二、三十年,新品种层出不穷,令人眼花缭乱。
按照化学组成划分有:氧化物陶瓷氧化物陶瓷:氧化铝、氧化锆、氧化镁、氧化钙、氧化铍、氧化锌、氧化钇、二氧化钛、二氧化钍、三氧化铀等。
氮化物陶瓷氮化物陶瓷:氮化硅、氮化铝、氮化硼、氮化铀等。
碳化物陶瓷碳化物陶瓷:碳化硅、碳化硼、碳化铀等。
硼化物陶瓷硼化物陶瓷:硼化锆、硼化镧等。
硅化物陶瓷硅化物陶瓷:二硅化钼等。
氟化物陶瓷氟化物陶瓷:氟化镁、氟化钙、三氟化镧等。
硫化物陶瓷硫化物陶瓷:硫化锌、硫化铈等。
其他还有砷化物陶瓷,硒化物陶瓷,碲化物陶瓷等。
除了主要由一种化合物构成的单相陶瓷外,还有由两种或两种以上的化合物构成的复合陶瓷。
例如,由氧化铝和氧化镁结合而成的镁铝尖晶石陶瓷,由氮化硅和氧化铝结合而成的氧氮化硅铝陶瓷,由氧化铬、氧化镧和氧化钙结合而成的铬酸镧钙陶瓷,由氧化锆、氧化钛、氧化铅、氧化镧结合而成的锆钛酸铅镧(PLZT)陶瓷等等。
特种陶瓷

特种陶瓷复习资料第一章特种陶瓷的定义:采用人工合成的高纯度无机化合物为原料,在严格控制的条件下经成型、烧结和其他处理而制成具有微细结晶组织的无机材料——特种陶瓷。
这类陶瓷又称为先进陶瓷或精细陶瓷。
分类:按化学成分:氧化物和非氧化物陶瓷按功能分:结构陶瓷和功能陶瓷结构陶瓷:利用力学和热学性能应用于制造发动机,切削工具和轴承等领域功能陶瓷:利用电光磁声化学等功能性,应用于检测,控制,以及生物医学领域等。
按性能:工程陶瓷,热功能,电功能,磁学功能,光学功能,化学功能,放射性功能,声学功能,生物医学功能。
第三章弹性模量的定义:在工程意义上,弹性模量是表征材料对弹性变形的抵抗能力。
在应力应变关系意义上,弹性模量代表着单位应力作用下原子间距的变化率。
陶瓷材料弹性模量的特点比金属大得多;压缩时比拉伸时大(金属相等)1 抗弯强度定义:材料抵抗抗弯曲不断裂的能力。
测试方法:三点弯曲 :四点弯曲断裂韧性K 1C 的定义和测定方法断裂韧性:表征材料抵抗其内部裂纹扩展能力的性能指标K 1C —裂纹尖端的临界应力强度因子. 3 断裂韧性K 1C 的测定方法硬度的概念:硬度是材料抵抗外来异物压入时产生永久变形的能力 ()232/3t PL b ωσ=()232/3t PL b ωσ=()232/3t PL b ωσ=()232/3t PL b ωσ=影响因素表面原子或离子填充密度;弹性模量、强度、裂纹的方向、塑性变形程度等。
疲劳断裂在交变负荷产生的交变应力作用下,材料内部显微组织发生变化,最后导致的断裂。
称为疲劳断裂这样的变化过程称为材料的疲劳(或交变应力损伤)热学性质包括:热容量,热导率,热膨胀、耐热冲击性能等性质;3.4 陶瓷的增强和增韧1.细晶强化增韧2.晶界增强增韧3.相变增强增韧4.复合增强增韧1.2.晶界增强增韧原理通过改变晶相组成和烧结后的热处理,使晶界玻璃相结晶成高强度的晶界相来提高强度改变晶相组成• 3.相变增韧原理•利用晶态不同变体发生晶型转变时产生的体积变化使材料内部形成应力场,当材料断裂时,应力的释放阻止裂纹的扩张,只有增加外力做功,才能使裂纹继续扩展,于是材料的强度和韧性都得到了提高。
特种陶瓷整理版
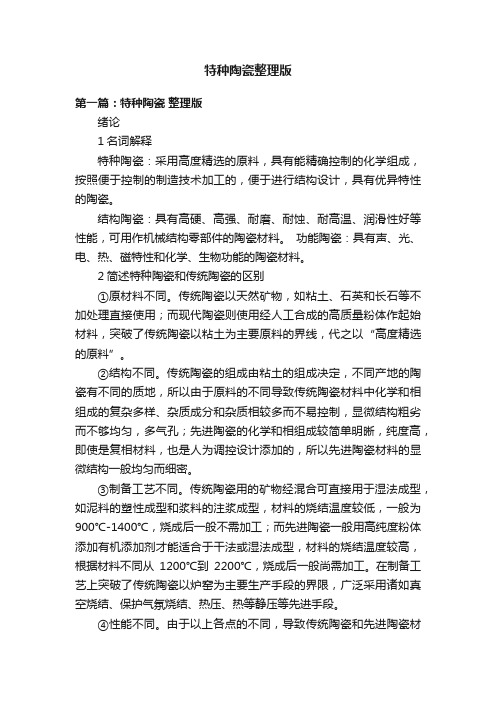
特种陶瓷整理版第一篇:特种陶瓷整理版绪论1名词解释特种陶瓷:采用高度精选的原料,具有能精确控制的化学组成,按照便于控制的制造技术加工的,便于进行结构设计,具有优异特性的陶瓷。
结构陶瓷:具有高硬、高强、耐磨、耐蚀、耐高温、润滑性好等性能,可用作机械结构零部件的陶瓷材料。
功能陶瓷:具有声、光、电、热、磁特性和化学、生物功能的陶瓷材料。
2简述特种陶瓷和传统陶瓷的区别①原材料不同。
传统陶瓷以天然矿物,如粘土、石英和长石等不加处理直接使用;而现代陶瓷则使用经人工合成的高质量粉体作起始材料,突破了传统陶瓷以粘土为主要原料的界线,代之以“高度精选的原料”。
②结构不同。
传统陶瓷的组成由粘土的组成决定,不同产地的陶瓷有不同的质地,所以由于原料的不同导致传统陶瓷材料中化学和相组成的复杂多样、杂质成分和杂质相较多而不易控制,显微结构粗劣而不够均匀,多气孔;先进陶瓷的化学和相组成较简单明晰,纯度高,即使是复相材料,也是人为调控设计添加的,所以先进陶瓷材料的显微结构一般均匀而细密。
③制备工艺不同。
传统陶瓷用的矿物经混合可直接用于湿法成型,如泥料的塑性成型和浆料的注浆成型,材料的烧结温度较低,一般为900℃-1400℃,烧成后一般不需加工;而先进陶瓷一般用高纯度粉体添加有机添加剂才能适合于干法或湿法成型,材料的烧结温度较高,根据材料不同从1200℃到2200℃,烧成后一般尚需加工。
在制备工艺上突破了传统陶瓷以炉窑为主要生产手段的界限,广泛采用诸如真空烧结、保护气氛烧结、热压、热等静压等先进手段。
④性能不同。
由于以上各点的不同,导致传统陶瓷和先进陶瓷材料性能的极大差异,不仅后者在性能上远优于前者,而且特种陶瓷材料还发掘出传统陶瓷材料所没有的性能和用途。
传统陶瓷材料一般限于日用和建筑使用,而特种陶瓷具有优良的物理力学性能,高强、高硬、耐磨、耐腐蚀、耐高温、抗热震,而且在热、光、声、电、磁、化学、生物等方面具有卓越的功能,某些性能远远超过现代优质合金和高分子材料。
特种陶瓷及其功能应用简介

5、溶剂蒸发法(Solvent Evaporation)
• 酒精干燥法(Alchol Drying) • 冷冻干燥法(Freeze Drying) • 热石油干燥法(Hot-Petrol Drying) • 喷雾干燥法(Spray Drying)
9.2.2 成型
• 特种陶瓷的成形技术和方法对于制备 性能优良的制品具有重要意义。特种 陶瓷的成形技术与方法比起传统陶瓷 来说更加丰富、更加广泛,而且具有 不同的特点。特种陶瓷成形方法的选 择,是根据制品的性能要求、形状、 大小、厚薄、产量和经济效益等综合 确定的。
软模压制成形麻花钻 头的示意图
1-钢模模冲;2-钢模套; 3-塑料垫片;4-塑料模 具;5-硬质合金粉末;
6-模垫
3、热等静压
• 热等静压是一项有前景的技术,为陶瓷粉料的致密化提供了 最有效的方法,可用于生产高性能和高可靠型的净尺寸陶瓷。 它也可用于陶瓷和陶瓷之间、陶瓷与金属之间的固体-固体, 固体-粉料,粉料-粉料间的连接。
1、固相法:
• 化合或还原-化合法
– 直接化合的通式为: Me+X=MeX – 或用MeO代替Me, MeO+2X=MeX+XO↑ – 可以生产多种碳化物、硅化物、氮化物和氧化物粉
末。
• 制取硼化物的碳化硼法
– 4MeO+B4C+3C=4MeB+4CO – 或加入B2O3以降低反应产品中碳的含量: – 2MeO+B2O3+5C=2MeB+5CO – 或用金属还原剂代替碳: – 3MeO+3 B2O3+8Al(Mg,Ca,Si)=3MeB2+
9.2 特种陶瓷的基本制备工艺
• 9.2.1 粉末制备 • 9.2.2 成型 • 9.2.3 烧结 • 9.2.4 加工与精加工技术
特 种 陶 瓷

2012-12-16
2ቤተ መጻሕፍቲ ባይዱ12-12-16
陶瓷发动机
发动机使用陶瓷材料有如下优点: 1、提高发动机热效率 发动机燃烧室采用陶瓷隔热零件并取消冷却系统 后,会降低热量损失,增加工作的循环平均温度,从而使循环热效率得 到提高。 2、减少辅助功率消耗,发动机结构简化 当燃烧室采用陶瓷隔热技术后, 可以部分取消或完全取消冷却系统。使发动机不再需要水管、水泵、风 扇、散热器等一系列零部件,结构上也可以取消水套。这样,整机结构 简化,质量、体积减小,原来用于驱动水泵、风扇的辅助工作亦被取消, 输出功率增加。在使用上可摆脱冷却系统故障所带来的麻烦,并几乎不 受恶劣气候的影响,其军事用途尤为明显。 3、适应多种燃料的燃烧 陶瓷发动机的燃烧室壁温显著升高,有利于燃 料的蒸发、着火和燃烧。陶瓷材料抗化学腐蚀性强,可使用质量较差的 燃油。 4、降低发动机的噪声,减少排气污染 取消或部分取消冷却系统,使风 扇噪声降低。另外,由于燃烧室燃烧温度高(最高1370℃),燃烧完全, 可减少对环境的污染。 5、减轻质量 陶瓷材料比金属轻60%左右,可减轻发动机的质量。 6、资源丰富 陶瓷材料资源丰富,可减少对Co、Ni、Cr等战略物资的依 赖。
2012-12-16
2.1 结构陶瓷
所谓结构陶瓷,是指能作为工程结构材料使 用的陶瓷。是陶瓷材料的重要分支,约占整个陶 瓷市场的25%左右。结构陶瓷以耐高温、高强度、 超硬度、耐磨、抗腐蚀等机械力学性能为主要特 征,因此在冶金、宇航、能源、机械、光学等领 域有重要的应用。在这些应用领域用非金属代替 金属是总的趋势。结构陶瓷大致分为氧化物系、 非氧化物系和结构用的陶瓷基复合材料。
2012-12-16
2012-12-16
n 陶瓷刹车盘不会因水浸而降低 性能,而且减速非常快,其制 动碟表面的摩擦系数在制动初 段比铸铁碟高25%,这样在急 制动时,车子就无需额外的制 动辅助技术,单靠制动器便能 迅速提供充足的制动力。陶瓷 制动器采用6活塞的制动卡钳, 在活塞与制动片之间,装有陶 瓷隔热体,用以防止制动时产 生的高热传人液压组件和制动 液,这套刹车系统更可以在 800℃高温下正常工作。 n 保时捷、奔驰等跑车均已采用 这类陶瓷制动器
特种陶瓷总结

脆性差
高硬度,耐磨 高熔点,耐高温 高强度 高化学稳定性 比重小,约为金属1/3
原因:
化学键差异造成的。 金属:金属键,没有方向性,塑性变形性能好 陶瓷:离子键和共价键,方向性强,结合能大,很难塑性形 变,脆性大,裂纹敏感性强
第一章 粉体性能及制备
特种陶瓷粉体要求
1) 化学成分纯度高,均匀性好 2) 相组成均匀,准确 3) 粒度小于1um,粒度分布范围窄 4) 颗粒形状为球形式自形晶形 5) 团聚程度低 6) 粉体流动性好
绪
论
2、特种陶瓷分类
⑴ 结构陶瓷
以耐高温、高强度、超硬度、耐磨损、抗腐蚀等机械力学性 能为主要特征。
⑵ 功能陶瓷
以电、磁、光、热和力学等性能及其相互转换为主要特征, 在通信电子、自动控制、集成电路、计算机、信息处理等方面 的应用日益普及。
⑶ 陶瓷基复合材料
陶瓷材料的最大缺点是韧性低,使用时会产生不可预测的突 然性断裂,陶瓷基复合材料主要是为了改善陶瓷韧性。
对于固定体 系E是固定的
吸 附 层
扩 散 层
可通过塑化 剂或者解凝 剂调整
当粒子和介质固定时,ζ和扩散层厚度成正比; 而ζ电位的增高,可提高团粒间的斥力,有助于克服范德华力和和 布朗运动,获得良好的悬浮性。
以Al203为例, Al203用盐酸处理后,在粒子表面生成三氯化铝 (AlCl3),三氯化铝立即水解,生成AlCl2+和AlCl2+离子,犹如Al203 粒子表面吸附了一层阳离子,使其成为一个带正电荷的胶粒,然后 胶粒吸附OH-而形成一个庞大的胶团。
相变增韧对多晶转变有什么要求?
相变增韧的多晶转变要求 ①高温相转变为低温相的体积膨胀要大 ②多晶转变可以通过改变晶体粒度、加入稳定 剂或增加压力等手段使之在室温下不能进行 ③相变速度要快 ④晶体本身要有高强度 ZrO2由四方相到单斜相的变化属于马氏体相变, 满足上述条件,因此不仅用在本身,也在其他 陶瓷有明显的效果。
特种陶瓷、先进陶瓷的16种成型工艺、应用简介及优缺点总结

特种陶瓷、先进陶瓷的16种成型工艺、应用简介及优缺点总结01特种陶瓷特种陶瓷也称为先进陶瓷、现代陶瓷、新型陶瓷、高性能陶瓷、高技术陶瓷和精细陶瓷,突破了传统陶瓷以黏土为主要原料的界限,主要以氧化物、炭化物、氮化物、硅化物等为主要原料,有时还可以与金属进行复合形成陶瓷金属复合材料,是一种采用现代材料工艺制备的、具有独特和优异性能的陶瓷材料。
特种陶瓷分类及应用02特种陶瓷成型方法及特点陶瓷成型就是将陶瓷原料按照实际生产的要求制作成具有规定形状、尺寸及一定强度的生坯,成型过程取决于陶瓷原料的性能和成型工艺方法。
造就陶瓷制品形状的方法也是多种多样的,但总的来说,可以分为干法成型和湿法成型。
干法成型包括干压成型、等静压成型、超高压成型、粉末电磁成型等方法。
湿法成型大致可分为塑性成型和胶态浇注成型两大类。
塑性成型也称湿压法,是指将已制成塑性的物料在刚性模具中压制成型的一种成型方法,包括挤压成型、注射成型、轧膜成型(压延成型)等几种。
胶态浇注成型是将具有流动性的浆料制成可自我支撑形状的一种成型方法。
该法利用浆料的流动性,使物料干燥并固化后得到一定形状的成型体。
主要包括注浆成型、注凝成型、流延成型、直接凝固成型、胶态振动注模成型等。
陶瓷材料及部件的主要成型工艺2.1干压成型干压成型就是在陶瓷粉料中加入一定量的有机添加剂(粘结剂、润滑剂、可塑剂、消泡剂、减水剂等),在外界压力的作用下,使其在模具中成型。
优点:易于实现自动化,所以在工业生产中得到较大的应用。
缺点:在成型过程中,常会因为径向、轴向的压力分布不均而引起坯体的分层,开裂、密度不均等现象也会经常发生。
2.2等静压成型等静压成型是通过施加各项同性压力而使粉料一边压缩一边成型的方法。
根据成型温度的不同,等静压成型又分为热等静压成型和冷等静压成型。
冷等静压是在常温下对工件进行成型的等静压法。
热等静压是在指在高温高压下对工件进行等压成型烧结的等静压法。
陶瓷球坯模压-等静压成型工艺过程陶瓷球坯直接等静压成型工艺过程优点:能压制具有凹形、空心、细长件以及其他复杂形状的零件;摩擦损耗小,成型压力低;压力从各个方面传递,压坯密度分布均匀、压坯强度高,模具制作方便,寿命长,成本较低。
- 1、下载文档前请自行甄别文档内容的完整性,平台不提供额外的编辑、内容补充、找答案等附加服务。
- 2、"仅部分预览"的文档,不可在线预览部分如存在完整性等问题,可反馈申请退款(可完整预览的文档不适用该条件!)。
- 3、如文档侵犯您的权益,请联系客服反馈,我们会尽快为您处理(人工客服工作时间:9:00-18:30)。
1名词解释特种陶瓷:采用高度精选的原料,具有能精确控制的化学组成,按照便于控制的制造技术加工的,便于进行结构设计,具有优异特性的陶瓷。
粉体颗粒:指在物质的本质结构不发生改变的情况下,分散或细化而得到的固态基本颗粒。
团聚体:由一次颗粒通过表面力吸引或化学键键合形成的颗粒,它是很多一次颗粒的集合体。
胶粒:即胶体颗粒。
胶粒尺寸小于100nm,并可在液相中形成稳定胶体而无沉降现象。
6什么是固相法、气相法、液相法,简述工艺流程固相法就是以固态物质为出发原料,通过一定的物理与化学过程来制备陶瓷粉体的方法。
固相原料——配料——混合——合成——粉碎——粉体气相法是直接利用气体或者通过各种手段将物质变成气体,使之在气体状态下发生物理变化或化学反应,最后在冷却过程中凝聚长大形成粉体的方法。
蒸发-凝聚法(PVD):原料——高温气化——急冷——粉体蒸发-凝聚法是将原料加热至高温(用电弧或等离子流等加热),使之气化,接着在电弧焰和等离子焰与冷却环境造成的较大温度梯度条件下急冷,凝聚成微粒状物料的方法。
气相化学反应法(CVD):金属化合物蒸气——化学反应——粉体气相化学反应法是挥发性金属化合物的蒸气通过化学反应合成所需物质的方法。
液相合成法也称湿化学法或溶液法。
溶液法从均相的溶液出发,将相关组分的溶液按所需的比例进行充分的混合,再通过各种途径将溶质与溶剂分离,得到所需要组分的前驱体,然后将前驱体经过一定的分解合成处理,获得特种陶瓷粉体,可以细分为脱溶剂法、沉淀法、溶胶-凝胶法、水热法等。
溶液制备——溶液混合——脱水——前驱体——分解合成——粉体7常用的气相法有哪些,各有何特点(3个)一种是系统中不发生化学反应的蒸发-凝聚法(PVD),另一种是气相化学反应法(CVD)。
第三章特种陶瓷成型工艺1.简述烧结过程烧结前,陶瓷粉料在外部压力作用下,形成一定形状的、具有一定机械强度的多孔坯体。
在烧结前期,陶瓷生坯中一般含有百分之几十的气孔,颗粒之间只有点接触。
在表面能减少的推动力下,物质通过不同的扩散途径向颗粒间的颈部和气孔部位填充,使颈部渐渐长大,并逐步减少气孔所占的体积,细小的颗粒之间开始逐渐形成晶界,并不断扩大晶界的面积,使坯体变得致密化。
在这个相当长的过程中,连通气孔不断缩小;两个颗粒之间的晶界与相邻晶界相遇,形成晶界网络;晶界移动,晶粒逐步长大。
其结果是气孔缩小,致密化程度提高,直至气孔相互不再连通,形成孤立的气孔分布于几个晶粒相交的位置。
这时坯体的密度达到理论密度的90%以上。
接着进入烧结后期阶段,孤立的气孔扩散填充,使致密化继续进行,同时晶粒继续均匀长大,一般气孔随晶界一起移动,直至致密化,得到致密的陶瓷材料。
2.常用的烧结方法,各有何特点1、低温烧结这种方法可以降低能耗,使产品价格降低。
2、热压烧结如果加热粉体的同时进行加压,那么烧结主要取决于塑性流动,而不是扩散。
对于同一材料而言,压力烧结与常压烧结相比,烧结温度低得多,而且烧结体中气孔率也低。
另外,由于在较低的温度下烧结,就抑制了晶粒成长,所得的烧结体致密,且具有较高的强度(晶粒细小的陶瓷,强度较高)。
3、气氛烧结对于空气中很难烧结的制品(如透光体或非氧化物),为防止其氧化等可采用气氛烧结。
4、其他烧结方法(1)电场烧结(可获得有压电性的陶瓷样品(2) 超高压烧结其特点是,不仅能够使材料迅速达到高密度,具有细晶粒(小于1μm),而且使晶体结构甚至原子、电子状态发生变化,从而赋予材料在通常烧结或热压烧结工艺下所达不到的性能。
而且可以合成新型的人造矿物。
此工艺比较复杂,对模具材料、真空密封技术以及原料的细度和纯度均要求较高。
(3) 活化烧结它具有降低烧结温度,缩短烧结时间、改善烧结效果等优点。
(4) 活化热压烧结是一种高效率的热压技术。
3.烧结过程易出现的主要问题应力集中,裂纹,收缩,塌陷,气孔,结石4.试述烧结过程中的物质传递机理在高温过程中,由于表面曲率不同,必然在系统的不同部位有不同的蒸气压,于是通过气相有一种传质趋势,这种传质过程仅仅在高温下蒸气压较大的系统内进行,如氧化铅、氧化铍和氧化铁的烧结。
物质将从蒸气压高的凸形颗粒表面蒸发,通过气相传递而凝聚到蒸气压低的凹形颈部,从而使颈部逐渐被填充。
蒸发-凝聚传质的特点是烧结时颈部区域扩大,球的形状改变为椭圆,气孔形状改变,但球与球之间的中心距不变,也就是在这种传质过程中坯体不发生收缩。
气孔形状的变化对坯体一些宏观性质有可观的影响,但不影响坯体密度。
气相传质过程要求把物质加热到可以产生足够蒸气压的温度。
对于几微米的粉末体,要求蒸气压最低为10~1Pa,才能看出传质的效果。
而烧结氧化物材料往往达不到这样高的蒸气压,如A1203在1200℃时蒸气压只有10-41Pa,因而一般硅酸盐材料的烧结中这种传质方式并不多见。
在高温下挥发性小的陶瓷原料,其物质主要通过表面扩散和体积扩散进行传递,烧结是通过扩散来实现的。
目前主要的扩散机理:(1)直接交换。
相邻同种离子交换位置。
由于这种扩散的活化能大,一般情况下很难发生。
(2)空穴迁移。
靠近空穴的离子,移动到空穴位置,相当于空穴沿相反方向移动。
(3)间隙迁移。
在间隙位置的离子,通过空的间隙位置进行移动。
(4)准间隙迁移。
间隙离子把正常位置的离子推到其它的间隙位置,占据正常的晶格位置。
(5)循环移动。
离子作为一个集团同时移动,由于引起点阵畸变小,扩散活化能也小。
在扩散传质中要达到颗粒中心距离缩短必须有物质向气孔迁移,气孔作为空位源,空位进行反向迁移。
颗粒点接触处的应力促使扩散传质中物质的定向迁移。
颗粒不同部位空位浓度不同,颈表面张应力区空位浓度大于晶粒内部,受压应力的颗粒接触中心空位浓度最低。
空位浓度差是自颈到颗粒接触点大于颈至颗粒内部。
系统内不同部位空位浓度的差异对扩散时空位的漂移方向是十分重要的。
扩散首先从空位浓度最大部位(颈表面)向空位浓度最低的部位(颗粒接触点)进行。
其次是颈部向颗粒内部扩散。
空位扩散即原子或离子的反向扩散。
因此,扩散传质时,原子或离子由颗粒接触点向颈部迁移,达到气孔充填的结果。
扩散可以沿颗粒表面进行,也可以沿着两颗粒之间的界面进行或在晶粒内部进行,我们分别称为表面扩散、界面扩散和体积扩散。
不论扩散途径如何,扩散的终点是颈部。
当晶格内结构基元(原子或离子)移至颈部,原来结构基元所占位置成为新的空位,晶格内其它结构基元补充新出现的空位,就这样以“接力”方式物质向内部传递而空位向外部转移。
空位在扩散传质中可以在以下三个部位消失:自由表面、内界面(晶界)和位错。
随着烧结进行,晶界上的原子(或离子)活动频繁,排列很不规则,因此晶格内空位一旦移动到晶界上,结构基元的排列只需稍加调整空位就易消失。
随着颈部填充和颗粒接触点处结构基元的迁移出现了气孔的缩小和颗粒中心距逼近。
表现在宏观上则气孔率下降和坯体的收缩。
液相烧结的基本原理与固相烧结有类似之处,推动力仍然是表面能。
不同的是烧结过程与液相量、液相性质、固相在液相中的溶解度、润湿行为有密切关系。
因此,液相烧结动力学的研究比固相烧结更为复杂。
(1)粘性流动在液相含量很高时,液相具有牛顿型液体的流动性质,这种粉体的烧结比较容易通过粘性流动而达到平衡。
除有液相存在的烧结出现粘性流动外,弗仑克认为,在高温下晶体颗粒也具有流动性质,它与非晶体在高温下的粘性流动机理是相同的。
在高温下物质的粘性流动可分为两个阶段:第一阶段,物质在高温下形成粘性流体,相邻颗粒中心互相逼近,增加接触面积,接着发生颗粒间的粘合作用和形成一些封闭气孔;第二阶段,封闭气孔的粘性压紧,即小气孔在玻璃相包围压力作用下,由于粘性流动而密实化。
而决定烧结致密化速率主要有三个参数:颗粒起始粒径、粘度、表面张力。
原料的起始粒度与液相粘度这两项主要参数是相互配合的,它们不是孤立地起作用,而是相互影响的。
为了使液相和固相颗粒结合更好,液相粘度不能太高,若太高,可用加入添加剂降低粘度及改善固-液相之间的润湿能力。
但粘度也不能太低,以免颗粒直径较大时,重力过大而产生重力流动变形。
也就是说,颗粒应限制在某一适当范围内,使表面张力的作用大于重力的作用,所在液相烧结中,必须采用细颗粒原料且原料粒度必须合理分布。
(2)塑性流动在高温下坯体中液相含量降低,而固相含量增加,这时烧结传质不能看成是牛顿型流体,而是属于塑性流动的流体,过程的推动力仍然是表面能。
为了尽可能达到致密烧结,应选择尽可能小的颗粒、粘度及较大的表面能。
在固-液两相系统中,液相量占多数且液相粘度较低时,烧结传质以粘性流动为主,而当固相量占多数或粘度较高时则以塑性流动为主。
实际上,烧结时除有不同固相、液相外,还有气孔存在,因此实际情况要复杂得多。
塑性流动传质过程中纯固相烧结中同样也存在,可以认为晶体在高温、高压作用下产生流动是由于晶体晶面的滑移,即晶格间产生位错,而这种滑移只有超过某一应力值才开始。
在烧结时固、液两相之间发生如下传质过程:细小颗粒(其溶解度较高)以及一般颗粒的表面凸起部分溶解进入液相,并通过液相转移到粗颗粒表面(这里溶解度较低)而沉淀下来。
这种传质过程发生于具有下列条件的物系中:有足量的液相生成;液相能润湿固相;固相在液相中有适当的溶解度。
而传质过程是以下列方式进行的:首先,随着烧结温度提高,出现足够量液相。
固相颗粒分散在液相中,在液相毛细管的作用下,颗粒相对移动,发生重新排列,得到一个更紧密的堆积,结果提高了坯体的密度。
这一阶段的收缩量与总收缩的比取决于液相的数量。
当液相数量大于35%(体积)时,这一阶段是完成坯体收缩的主要阶段,其收缩率相当于总收缩率的60%左右。
第二,被薄的液膜分开的颗粒之间搭桥,在接触部位有高的局部应力导致塑性变形和蠕变。
这样促进颗粒进一步重排。
第三,是通过液相的重结晶过程。
这一阶段特点是细小颗粒和固体颗粒表面凸起部分的溶解,通过液相转移并在粗颗粒表面上析出。
在颗粒生长和形状改变的同时,使坯体进一步致密化。
颗粒之间有液相存在时颗粒互相压紧,颗粒间有压力作用下又提高了固体物质在液相中的溶解度。
如:Si3N4是高度共价键结合的化合物,共价键程度约占70%,体扩散系数(bulk diffu-sion coefficient)不到10-7cm2/s,因此纯Si3N4很难进行固相烧结,而必须加入添加剂,如MgO,Y2O3,Al2O3等,这样在高温时它们和α-Si3N4颗粒表面的SiO2形成硅酸盐液相,并能润湿和溶解α-Si3N4,在烧结温度下,析出β- Si3N4。
外加剂(添加剂)对烧结有何影响外加剂与烧结主体形成固溶体、成液相、化合物、外加剂阻止多晶转变、外加剂起到扩大烧结范围的作用。