紧密赛络纺装置在国产细纱机的改造建议及工艺探讨_王亚芳
紧密赛络纺纱技术在棉纺中的应用探讨

Y 12 G 7 A纱线毛羽测试仪 , 试验次 数 l管 X0 测试速度 3 / i, 0 1 次, 0m mn
片断长 度 1 0m;
锭细纱机的同一牵伸机构 , 以平行 状态同时被牵伸 , 从前罗拉夹持点
出来 后 进 入气 动集 聚 区 。在 每 个 纺纱 部 位 开 有双 槽 且 内部 处 于 负 压状 态 的异型 管表 面 套有 网格 圈 ,
国 际纺织 导报 2 0 0 6年 第 1 0期
维普资讯
纺
一
条 干 测 试 仪 : 岭 纺 电 长
Y 3 G 条 干 仪 ,测 试 速 度 G15 40m mi, 试 时 间 0 0 , 试 0 / n测 10”测
次数 1 0次 ;
一
Ui no n公 司 生 产 的 D 3视 Z
观结构( 放大倍数为 30 , 图 2 5 )如
所示。
起, 纱线受控程度增强 , 纤维束 松 散程 度减弱 , 边缘 纤 维 受到 了有
一
从 图 2中可 以看 出 , 密赛 络 紧 纺纱 线 的 表面 及外 观 可 与 紧 密 纺
效的集聚。所 以紧密赛络纺纱 的
毛羽少 , 强力 高 , 磨性好 。 耐
维普资讯
纺
紧密赛络纺纱技术在棉纺中的应用探讨
杨丽 丽 谢春萍 王 兰兰 黄 晶全 江 南大 学 纺 织服装 学 院( 中国)
的 精梳纯 棉粗纱 。 纺纱 机 :J 2 K细 纱 机 ( E M18 装
摘 要 : 绍 了紧密赛络 纺技 术的原理 及其特点。将 自行研制 的具 有不同吸风双槽 的 介
图 2 三种 纱 线 外观 结 构
频变焦显微镜 ; 测试 环境 : 度 2 。 相 对湿 温 2 c,
紧密赛络纺装置在国产细纱机的改造建议及工艺探讨

摇架压力要求较高;3输出胶辊直径 比前上胶辊 ()
稍大, 两个胶 辊之 间通过 中间齿轮传 动 , 对不 同 且
纤维存在不同的牵伸 比, 机构复杂;4 配有不同 () 狭槽长度和倾斜角度的吸管,适纺不同原料 的纱 支 ;5 负压 控制 系 统采 用分 单元 控 制技 术 , 2 () 每 4 锭为一组 , 每组 由一个吸风机提供负压 , 负压吸风 单 元 的风速集 中调节控 制 ,保证 每个 吸风单元 的
2 国 内紧密赛 络 纺纱装 置的研 制现 状及 性 能对 比
从 2 0 年起 ,国内对 紧密纺 的研究就 已经起 00
步, 现在 紧密赛络 纺结构 形式尽管 有多种 形式 , 但 主要还是 集 中在 气流集 聚装置上 ,而气流 集聚装
置又分为两种 :一种是仿绪森式 ,一种是仿丰 田 式。 它们的集聚原理相同, 都是在原来的细纱牵伸
系统前加 一个气 动集 聚区 ,采用 网格 圈将 凝 聚须 条送 至加 捻 点 , 因此 , 它们 的集 聚效 果也 差 不 多 ,
所不 同的 只是 日常 消耗 和维 护管理 的复杂性 大相
径庭 。
1 紧 密 赛 络 纺 改 善 毛 羽 、 强 力 机 理
分 析
传统 的环锭纺尽 管 自诞 生 以来 一直保 持着纱 线 生 产 的统 治 地 位 ,但 其 存 在 着 不 可 克 服 的 弱
维普资讯
紧密赛络纺装置在 国产细纱机的改造建议及工艺探讨
王 亚芳
( 南通 市 中等专 业 学校 南通 260 ) 20 1
[ 要】 摘 紧密 赛络 纺是 紧密 纺和赛 络 纺相 结合 的 一种 组合 纺 纱 法 。本 文 通过 两种 紧密 赛络装 置 的成 纱质 量及 器材 消耗 的对 比分 析 ,对 国产 细纱机 紧密赛 络 纺 改造3 试验对 比分析 。 231质量对 比( 。. 见表 1 )
紧密赛络纺成纱机理及.

(二)纱线对比研究
加捻纱线的纵向结构分析(350倍)
紧密塞络纺棉纱
紧密纺棉纱
赛络纺棉纱
普通环锭纺棉纱
退捻后纱线的纵向结构(100倍)
紧密赛 络纱 赛络纱 紧密纱 传统环 锭纱
紧密赛 络纱 赛络纱 紧密纱 传统环 锭纱
小结
自制紧密赛络纺纱装置结合了集聚与合股的 双重作用,可有效减小加捻三角区,成纱毛 羽明显减少,尤其是长毛羽可基本消除;纱 线的同向同步加捻,使其结构更加清晰紧密, 表面纤维排列整齐顺直,截面形状也更圆, 退捻后有明显的双股结构;成纱强伸性能和 条干得到了较好的改进。与普通环锭纺单纱、 赛络纱、紧密纱相比,紧密赛络纱突显其优 越性。
10 310 335 360 385 410 捻系数
粗细节和棉结/个
30 25 20 15 10
5 0
310 335 360 385 410 捻系数
断裂强力/cN
吸风负压对纱线性能的影
440 430 420 410 400 390 380
1500
2100 2700 吸风负压/Pa
断裂伸长率/%
5.4 5.2
14.5×2/29
80 70 60 50 40 30 20 10 0
14.5×2/29
9.7×2/19.4 纱线细度/tex
9.7×2/19.4 纱线细度/tex
7.3×2/14.6 7.3×2/14.6
紧密赛 络纱 赛络纱
紧密纱
传统环 锭纱
9.7×2/19.4 纱线细度/tex
紧密纺_赛络纺纺纱经验及其探讨_王方水

紧密纺、赛络纺纺纱经验及其探讨王方水,郭 恒,贾云辉(鲁泰纺织股份有限公司,山东淄博 255100)摘要:介绍了紧密纺、赛络纺等新型纺纱技术原理及紧密纺纱线在色织面料方面的应用;分析紧密纺、赛络纺技术的优点及不足,并将其与普通纺进行对比,指出紧密纺、赛络纺技术生产的纱线质量好、强力高、毛羽少、条干均匀以及下游工序产品质量可进一步提高;加强对设备的日常维护、保养、保持器材部件清洁、运转正常,对充分发挥新型纺纱技术的优势至关重要,但企业要充分考虑其成本因素,应加速研发具有自己特色和自主知识产权,纺织企业能够接受的整机型和改造型的紧密纺细纱机及装置,以提高企业的竞争力。
关键词:紧密纺;塞络纺;优势;不足;器材配置;日常维护;竞争力中图分类号:TS104.7 文献标识码:A 文章编号:1001-9634(2009)03-0057-04收稿日期:2008-10-28作者简介:王方水(1961 ),男,山东淄博人,工程师,主要从事纺纱色织布的研究。
1 紧密纺等新型纺纱自1999年巴黎国际纺织机械展览会,立达(R-ieter )、青泽(Zinser )、绪森(Suessen)等国外纺机公司推出生产紧密纱的环锭细纱机以来,紧密纺纱技术迅速风靡整个纺织界。
紧密纺纱技术对改善纱线品质、提高成纱强力、减少毛羽等方面已经由实践证实,得到了快速发展。
欧洲计划用5a~10a 以紧密纺纱机全部替代普通环锭纺纱机,更有专家预言,未来属于紧密纺。
1.1 紧密纺纱原理紧密纺纱系统多数采用空气动力学原理,在纺纱三角区位置,通过一组集聚元件,使牵伸后的松散纤维须条经过负压吸聚管表面时,利用空气导向作用使纤维紧密地抱合在一起,经导向胶辊输出加捻成纱,纺纱过程中加捻三角区变得很小,基本消失,大大减少浮游外露纤维(即毛羽)的数量。
还有一种紧密纺纱系统不采用吸风而采用机械-磁铁原理工作,如瑞士罗托卡夫特公司生产的罗卡斯(Ro Co S)紧密纺系统装置,其前胶辊和引纱胶辊置于前下罗拉之上,磁性紧密器置于两个胶辊之间,共同形成紧密区。
紧密赛络纺纱技术在细纱工艺中的应用探讨_王晓丽
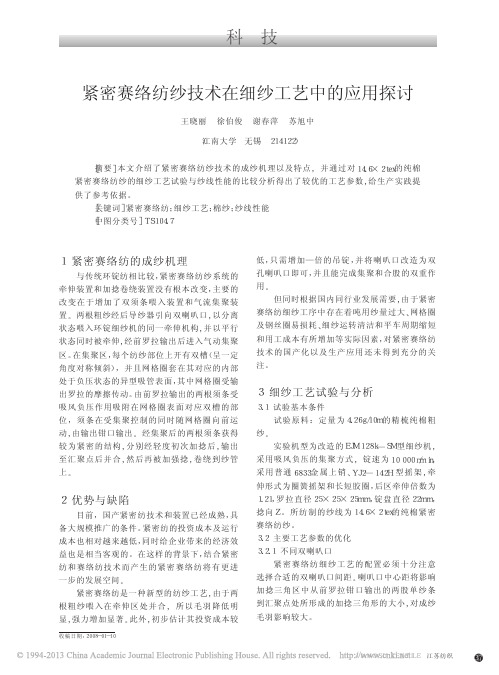
科技紧密赛络纺纱技术在细纱工艺中的应用探讨王晓丽徐伯俊谢春萍苏旭中(江南大学无锡214122)[摘要]本文介绍了紧密赛络纺纱技术的成纱机理以及特点,并通过对14.6×2tex的纯棉紧密赛络纺纱的细纱工艺试验与纱线性能的比较分析得出了较优的工艺参数,给生产实践提供了参考依据。
[关键词]紧密赛络纺;细纱工艺;棉纱;纱线性能[中图分类号]TS104.71紧密赛络纺的成纱机理与传统环锭纺相比较,紧密赛络纺纱系统的牵伸装置和加捻卷绕装置没有根本改变,主要的改变在于增加了双须条喂入装置和气流集聚装置。
两根粗纱经后导纱器引向双喇叭口,以分离状态喂入环锭细纱机的同一牵伸机构,并以平行状态同时被牵伸,经前罗拉输出后进入气动集聚区。
在集聚区,每个纺纱部位上开有双槽(呈一定角度对称倾斜),并且网格圈套在其对应的内部处于负压状态的异型吸管表面,其中网格圈受输出罗拉的摩擦传动。
由前罗拉输出的两根须条受吸风负压作用吸附在网格圈表面对应双槽的部位,须条在受集聚控制的同时随网格圈向前运动,由输出钳口输出。
经集聚后的两根须条获得较为紧密的结构,分别经轻度初次加捻后,输出至汇聚点后并合,然后再被加强捻,卷绕到纱管上。
2优势与缺陷目前,国产紧密纺技术和装置已经成熟,具备大规模推广的条件。
紧密纺的投资成本及运行成本也相对越来越低,同时给企业带来的经济效益也是相当客观的。
在这样的背景下,结合紧密纺和赛络纺技术而产生的紧密赛络纺将有更进一步的发展空间。
紧密赛络纺是一种新型的纺纱工艺,由于两根粗纱喂入在牵伸区处并合,所以毛羽降低明显,强力增加显著。
此外,初步估计其投资成本较低,只需增加—倍的吊锭,并将喇叭口改造为双孔喇叭口即可,并且能完成集聚和合股的双重作用。
但同时根据国内同行业发展需要,由于紧密赛络纺细纱工序中存在着吨用纱量过大、网格圈及钢丝圈易损耗、细纱运转清洁和平车周期缩短和用工成本有所增加等实际因素,对紧密赛络纺技术的国产化以及生产应用还未得到充分的关注。
国产细纱机长车紧密纺改造的应用实践

( hn ogJ n oTxi n hmi l ru o ,t. Sa dn i a eteadC e c opC . Ld ) m l aG
Y h ui eS o j
( hn o gD zo n esy S adn ehuU i ri ) v t
10mm; 速 机 同步 带 加 长 10mi。根 据设 计 3 减 3 l l 要求 , 更换 车头 牵伸 密封 板 、 防护 罩 。
12 车中部分的改造 .
1 E M1 8 L J 3 J C型细纱机主要部件 的改造
紧密 纺纱 技 术是 传 统纺 纱 技 术 的进 步 , 能 它 够 显著减 少成 纱 毛羽 , 提高成 纱 强力 和耐磨 性 , 在 同等配棉 条件 下 , 普 通 环锭 纺 纱 相 比具 有 明 显 与 的质 量优 势 。我 公 司 为 提 高产 品质 量 , 应 市 场 适 的需 求 , 20 于 07年 年 底 对 E Ml8 J 3儿c型 细 纱 机 ( 0 108锭/ , 台 并带 有集 体 落纱 装 置 ) 行 了紧 密 进 纺装 置改造 。运 行 至今 , 经多 品种试 验 , 品质量 产 指标稳 定 , 设备运 行 可靠 , 满足 了后 工序 的质 量要 求 , 到 了改造 紧密 纺 的 目的 。 达
Ab ta t T ntl d met o a tsinn e iei o si J 1 8 L pn igf me o 0 8 s ide sr c oisal o si cmp c pn igd vc nd met E M 3 J C sinn a f1 0 pn ls, c c l
密 纺改造 的原理 , 体改造 措施 如 下 。 具
1 1 车 头部 分 的改 造 .
紧密纺纱的性能与应用

紧密纺纱的性能与应用王方水王美荣司志奎(鲁泰纺织股份有限公司)摘要:紧密纺纱技术成功地解决了环锭纺纱产生的毛羽及飞花,提高了纱线的强力和耐磨强度,纱线外观及物理性能都有很大提高和改善,与普通环锭纺纱相比,在纱的质量和产量方面都具有明显优势,为提高后续织造等工序的效率,改善面料的强度、手感、外观质量等方面提供了可靠保证。
瑞士立达公司、德国绪森公司、青泽公司、日本丰田公司等都相继推出了紧密环锭纺纱机。
文章对紧密环锭纺纱技术和紧密纺纱在色织、针织方面的使用情况作了介绍。
2002年4月份,鲁泰纺织股份有限公司投资1.2亿人民币从瑞士立达公司全程引进K44紧密纺纱2万锭,到今年5月底全部投入生产,基本上达到了预期的目的。
其工艺流程如下:A11自动抓棉机一B11轴流开棉机一B7/3多仓混棉机一UNIFLEXB60开棉机一C51梳棉机一SB2预并条机一E32条并卷联合机一E62精梳机一RSB-D30并条机一FLl00粗纱机一K44—21C细络联。
主要生产纯棉CM40一CM40支纱,经过一年多的生产实践,产、质量达到了设计要求,现介绍如下。
1 Compact纺纱机理及特点概述卡摩纺纱是英文Compact yarn的简译音,意思是紧密纺纱。
最早在1999年巴黎展览会上展出了该紧密环锭纺纱机,它是欧洲主要机械制造商如瑞士立达、德国绪森和青泽公司研究出的纺纱设备,其中以瑞士立达公司制造K44 Comforspin的设备较有代表性。
Compact 纺纱与传统环锭纺纱前、后纺设备相同,只是细纱机不同。
1.1 Compact纱的形成机理传统环锭纺纱的方法是纤维由前罗拉和前皮辊的握持钳口输出,在加捻三角区被集聚到纱线结构中,但加捻三角区不可能集聚所有的纤维。
这就意味着许多边缘纤维或者丢失掉形成飞花,或者以某种不规则的形式捻合到纱线中,它们对强力的贡献很小,并且影响条干和粗细节、毛羽。
而Compact纱则克服传统环锭纺的不足,它是将传统环锭纺中前罗拉用一个带孔的抽吸滚筒代替,并且在滚筒内部安装一个特殊的不运动的斜管,以便气流通过,在滚筒的里面有一个产生负压的抽气系统,从而使气流从外面流人滚筒里面。
紧密赛络纺技术的特点及在牛仔纱生产中的应用

紧密赛络纺技术的特点及在牛仔纱生产中的应用随着消费者对牛仔服装的热爱和生活水平不断提高,牛仔布面料的要求也越来越高,新的纺纱原料和纺纱方法正逐渐应用在生产实践中。
一、前言1、赛络纺是在传统环锭细纱机上纺出类似于股线结构的纱线的一种纺纱方法。
赛络纺技术最早在毛纺上得到应用,后逐步应用到棉纺上。
赛络纺纱是采用两根粗纱从喇叭口喂入,在前后牵伸区仍然保持两根须条的分离状态,从前钳口输出一定长度后合并,并由同一个锭子加捻,形成有双股结构特征的赛络纱。
赛络纺的同向同步加捻使其纱线具有特殊的结构,赛络纺纱表面纤维排列整齐,纱线结构紧密,毛羽少,抗起毛起球好。
赛络纺织物和股线织物相比,手感柔软,比较平滑。
赛络纺纱可用于机织物及针织物,也可替代股线用于高支高密织物。
2、紧密纺技术是基于传统环锭纺的一种新型环锭纺纱技术。
简单地说就是使细纱机牵伸后输出的纤维致密化的纺纱技术,即通过在须条加捻前增加吸风装置,通过负压的控制,使松散纤维集聚、抱合,纤维在受控制区域内充分伸直,缩小传统纺纱机上的加捻三角区,便纤维在平行紧密的状态下实现加捻。
由于须条中各纤维受力均匀,抱合紧密,使成纱结构和质量得到全面提升,毛羽、强力、条干,耐磨性,纱线外观有了显著的改善。
3、紧密赛络纺是紧密纺和赛络纺相结合的一种组合工艺纺纱方法,该技术所纺制的纱线,结合了两种纺纱法的优异特性和品质,与传统环锭纺单纱及赛络纱相比,紧密赛络纱毛羽更少,强力更高,更具有赛络纺合股的效果,是纺制高档织物的理想原料,具有良好的发展前景。
二、我国牛仔布的起源及发展现状牛仔以其粗犷、豪放、洒脱大方、自然的风格以及结构紧密厚实,穿着柔软,质地耐磨结实的特点,广受人们的青睐。
我国作为牛仔布生产的大国,年产能力已达15亿平方米以上,但并非产销强国,其产品主要是以量取胜的传统大路货品种,其品牌,价格在国际上普遍缺乏竞争力。
提升产品的质量档次,开发出更多高附加值的新产品是产业升级的重要方法。
- 1、下载文档前请自行甄别文档内容的完整性,平台不提供额外的编辑、内容补充、找答案等附加服务。
- 2、"仅部分预览"的文档,不可在线预览部分如存在完整性等问题,可反馈申请退款(可完整预览的文档不适用该条件!)。
- 3、如文档侵犯您的权益,请联系客服反馈,我们会尽快为您处理(人工客服工作时间:9:00-18:30)。
紧密赛络纺装置在国产细纱机的改造建议及工艺探讨王亚芳(南通市中等专业学校南通226001)[摘要]紧密赛络纺是紧密纺和赛络纺相结合的一种组合纺纱法。
本文通过两种紧密赛络装置的成纱质量及器材消耗的对比分析,对国产细纱机紧密赛络纺改造提出了一定的建议,同时对影响紧密赛络纱的几个关键工艺参数进行了认真的分析。
[关键词]紧密赛络纺;质量;消耗;改造;工艺配置[中图分类号]TS103.27紧密赛络纺是紧密纺和赛络纺相结合的一种组合纺纱法,该技术所纺制的纱线秉承了两种纺纱法的优异特性和品质,与传统环锭纺单纱及赛络纱、紧密纺纱相比,紧密赛络纱毛羽更少,强力更高,更具有赛络纺合股的效果,是纺制高档织物的理想原料,具有良好的发展前景。
1紧密赛络纺改善毛羽、强力机理分析传统的环锭纺尽管自诞生以来一直保持着纱线生产的统治地位,但其存在着不可克服的弱点———加捻三角区。
由于加捻三角区的存在,致使加捻区纤维应力应变分布不均匀,纤维发生内外转移,伸直平行度较差,从而毛羽增加,强力降低以及飞花散失,所以,消灭加捻三角区是使传统环锭纺达到更加完善的关键。
紧密赛络纺则是针对影响强力、毛羽的加捻三角区进行的创新,它采用创新方式,增设了机构彻底地解决了加捻三角区问题。
它不仅利用气流对纤维积极控制减少三角区,而且还利用了股线减少毛羽提高强力的机理,通过两根或多个单纱之间加捻过程中对长毛羽的捕捉,使长毛羽卷入纱线的内部,变成较短的毛羽,从而达到减少毛羽,提高强力的目的。
尽管在紧密赛络纺系统中,双须条的喂入会形成一定的加捻三角区,但由于两根须条先进行了集聚,结构紧密,不会发生纤维从纱条中偏离出来的现象,且两纱条间的距离保持很小,在控制罗拉钳口处,低捻区范围相当小,其对毛羽的影响微乎其微,因此,紧密赛络纺对毛羽、强力的改善相当明显。
2国内紧密赛络纺纱装置的研制现状及性能对比从2000年起,国内对紧密纺的研究就已经起步,现在紧密赛络纺结构形式尽管有多种形式,但主要还是集中在气流集聚装置上,而气流集聚装置又分为两种:一种是仿绪森式,一种是仿丰田式。
它们的集聚原理相同,都是在原来的细纱牵伸系统前加一个气动集聚区,采用网格圈将凝聚须条送至加捻点,因此,它们的集聚效果也差不多,所不同的只是日常消耗和维护管理的复杂性大相径庭。
2.1仿丰田式紧密赛络装置特点仿丰田式紧密赛络装置主要定位在现有设备的改造,并能够兼顾现有各个厂家的新机配套。
传动形式采用了网格圈积极传动方式,在异型截面负压吸管内加装一根带齿小罗拉,带齿小罗拉的转动通过过桥齿轮由带齿前罗拉传动,网格圈的运动是通过小罗拉和紧密纺胶辊的钳口夹持而积极运动,从结构上形成了一个四罗拉牵伸装置。
主要特点是:(1)结构简单,安装维护简便;(2)网格圈积极传动对摇架压力要求不高,减少能耗;(3)前胶辊与紧密纺胶辊之间无传动关系,两个胶辊可互换,减轻维护工作量;(4)网格圈积极传动寿命长于摩擦传动,降低维护成本;(5)负压控制系统风管采用了流量控制技术,确保车头和车尾的负压差控制在极小范围内。
2.2仿绪森式紧密赛络装置特点仿绪森紧密赛络装置是目前在国际上应用较多的紧密纺系统之一,它既能用于整机,也能用于普通细纱机的改造。
其主要特点是:(1)原牵伸机收稿日期:2008-04-10构不作任何变动,只在前罗拉前增加一套紧密纺系统装置,改造比较方便;(2)网格圈消极传动,对摇架压力要求较高;(3)输出胶辊直径比前上胶辊稍大,两个胶辊之间通过中间齿轮传动,且对不同纤维存在不同的牵伸比,机构复杂;(4)配有不同狭槽长度和倾斜角度的吸管,适纺不同原料的纱支;(5)负压控制系统采用分单元控制技术,每24锭为一组,每组由一个吸风机提供负压,负压吸风单元的风速集中调节控制,保证每个吸风单元的负压乃至每个锭位的负压均匀一致。
2.3试验对比分析2.3.1质量对比(见表1)试验条件:同锭同组纱试验机型:FA506改道试验支别:19.7tex人棉紧密赛络纺表1:不同紧密赛络纺质量对比从测试数据分析,仿丰田式与仿绪森式质量上无明显差异。
2.3.2锭速对比(见表2)试验条件同上表2:不同紧密赛络装置锭速试验从测试数据分析,仿丰田装置可适当提高车速,增加产量,提升效益。
2.4易损件消耗易损件消耗主要是网格圈和胶辊消耗、过桥齿轮损耗以及张力架的非正常损耗,仿绪森装置多小风机损耗,仿丰田式多个小罗拉损耗。
网格圈损耗是紧密赛络装置的最大损耗。
从说明书上看,两种形式的网格圈寿命均为5至6个月,基本差不多,主要损耗是非正常损耗。
从实际运行看,由于传动形式的不同,一种是消极传动,一种是积极传动。
因此,仿丰田式网格圈非正常损耗小得多,经统计折合每锭每年损耗2.5只,单价按4.5元计算,共计价格11.25元,而仿绪森式由于装置的缺陷以及对摇架压力的较高要求,易堵塞网格圈非正常损耗相当严重,经测算,折合每锭每年损耗4.5只,同样按4.5元计算,共计价格20.25元,两相比较,仿丰田式每锭每年少损耗9元。
胶辊损耗则是紧密赛络装置的又一大损耗,由于该装置取消了动程,因此,对胶辊的要求相当高,必须高弹性、高耐磨,但是,由于设计的差异,两种装置在胶辊的消耗上相差较大。
仿丰田装置由于集聚胶辊和前皮辊规格尺寸相同,两者之间互换性好,前皮辊正常情况下一般磨砺周期应为2.5 ̄3个月,每次磨砺直径0.2mm,加上非正常损耗每年磨砺5次,皮辊直径从φ30mm磨到φ28mm需要2年时间,集聚胶辊和前皮辊互换使用寿命则增加至4年,每只皮辊单价以3.8元计算,则每锭每年消耗1.9元,但实际上皮辊磨砺到φ28以下还可以调至后档使用,所以皮辊消耗还要比估算值小一些,仿绪森装置由于采取的是大小胶辊结构,且二者必须具备一定的牵伸比,因此,回磨次数受到限制,回磨周期和每次磨砺尺寸假定与仿丰田一致,但由于欠伸比的存在皮辊只能用1.5年时间,且价格大于正常胶辊,平均每只4元计算,则每锭5.3元,事实上考虑到生活的难易,非正常损耗还要增加。
其它因素忽略不计,仿丰田式比仿绪森式每锭胶辊每年少损耗3.4元。
过桥齿轮和中间齿轮损耗也是紧密纺的常见损耗。
仿丰田式装置配备的过桥齿轮每6锭一只,使用寿命2年,平均单价22元,则每年每锭损耗应为1.83元。
仿绪森式装置配置的中间齿轮每2锭一只,正常使用寿命6个月,每只单价一元,则每年每锭损耗为0.83元,但往往是非正常损耗较多,因此,每年每锭损耗实际上大于0.83元,以1元计比仿丰田式节约0.83元/锭。
其它损耗主要是张力架的非正常损耗,一般在正常寿命时间内每年以5%结算,两种装置均有损耗也接近,大约每年每锭0.18元。
综上所述,仿丰田式装置每年每锭损耗为15.16元,仿绪森式每年每锭损耗26.56元,相差11.4元。
2.5电能耗用仿丰田装置每台增加一台4KW的电机,由于使用变频器拖动,实际能耗小于4KW,现以4KW计算,每台车每年耗电量为34560KW.h,每台车408锭,则每锭每年消耗电能为84.71KW.h。
仿绪森装置每台增加一台6.2KW的电机,几乎是满负荷运行,现以6KW计算,每台车每年耗电量为51840KW.h,每台车408锭,则每锭每年消耗电能为127.06KW.h。
两相比较,仿丰田装置比仿绪森装置每锭每年少消耗电能42.35KW.h。
2.6维护管理仿丰田装置前皮辊和集聚胶辊无传动关系,两个皮辊可互换,减轻了皮辊磨削和管理的工作量。
仿绪森装置则采取大小胶辊结构,且两者之间必须有牵伸比,因此,皮辊维修及中间齿轮维护工作量大。
另外,仿绪森装置采用单元吸风系统,马达轴承及风机轴承消耗大、维修不便。
2.7品种适应性仿丰田装置皮辊互换性强,锭速范围大,能适应从16支到150支的纱线生产,而仿绪森装置由于张力牵伸限制,各种原料牵伸比的不一致,且更换胶辊工作量大,故品种适应性不强,尽管理论上能适应各种纤维各种纱支的生产,但需更换胶辊及不同槽形的吸风管,因此,实际可操作性不强。
2.8改造建议综上所述,仿绪森式紧密赛络纺系统质量较稳定,但能耗大,器材损耗严重,实际品种适应性差,维修管理工作量大,一般适应于品种结构单一且稳定,质量水平要求高、产品附加值高,管理水平较高的企业改造,而仿丰田式装置尽管质量稍逊,但器材消耗少,管理难度相对较小,比较适应品种更换频繁,管理质量要求中上水平的企业改造。
3工艺配置紧密赛络纺纱技术的优越性源于其装置结构的合理设计和精良制造,但仅此还不能生产出优质的紧密纱,还需要配套的紧密赛络工艺。
尽管紧密赛络纱结合了两种新型纺纱方法,但它并不是简单的叠加,而是有自己的特殊性,即使是同样的气流聚集装置,但由于机构设计的差异,也存在自己的独特特点,因此,在工艺配置上,不能简单照搬原来环锭纺,赛络纺的纺纱工艺,而应根据各自装置的特点,选用纤维的特性以及器材的选用等方面全面考虑。
3.1负压值的优选(见表3与表4)适当的负压值是气集聚型紧密纺减少毛羽的必备条件,一般来讲,负压气流流速加快,对纱条表面的作用增强,纱线指标明显好转,但是,负压值也不是越大越好,太大不仅能耗增大,而且由于不同特性的纤维适应不同的负压值,负压值太大效果反而不好。
实验表明,棉纤维的纤维长度短,短绒相对较多,必须采用较大的负压值,而对纤维素纤维来说,整齐度好,强力大,负压值一般偏小掌握。
表3:纤维素纤维负压值优选试验表4:棉纤维负压值优选试验3.2粗纱间距的优选(见表5与表6)粗纱间距是指经过牵伸的两根粗纱在离开前罗拉钳口时的距离。
对紧密赛络纺工艺来说,粗纱间距是一个十分重要的参数,它将直接影响加捻三角区中从前罗拉钳口输出的两股单纱条到汇聚点处所形成的加捻三角形的大小以及汇聚点上侧单纱条上的捻度多少,从而直接影响纱条的强力和毛羽,尽管紧密赛络纱加捻三角区很小,但它对成纱质量还是有影响的。
一般来说,粗纱喂入间距加大加剧了纤维翻滚集聚的作用,有利于成纱强力和毛羽的改善,但过大会影响纤维的排列和均匀分布,条干CV%值有恶化趋势。
另外,由于捻陷作用,不同长度的纤维其粗纱间距也不相同,实践证明,棉纤维粗纱间距应选4.0mm左右,而纤维素纤维则为5.5mm ̄6.5mm为宜。
表5:纤维素纤维粗纱间距优选表6:棉纤维粗纱间距优选对紧密赛络纱来说,粗纱间距的选择主要是异形管槽间间距以及双口嗽叭口的间距选择,关键是二者必须密切配合,不能出现喇叭口间距大而槽间间距小或槽间间距大而喇叭口间距小的现象,它们都将影响成纱效果。
3.3钢领钢丝圈的优选(见表7)钢领、钢丝圈是细纱加捻卷绕的专件,在环锭细纱中,它不仅利用它们的速度差使细纱获得所需的捻度,而且对于减少毛羽,降低细纱断头至关重要。
在紧密纺工艺中,其装置设计主要在加捻三角区,致力于在加捻之前,消除纱线毛羽,提高纱线强力,似于钢领钢丝圈的加捻卷绕无关,但紧密纱少有的毛羽因无力提供滑润保护作用而导致了加捻卷绕元件钢领钢丝圈寿命的缩短,因此,紧密赛络纱对钢领钢丝圈提出了更高的要求,钢领要耐磨,钢丝圈则不仅要耐磨,而且要优选圈形,其纺纱通道必须能承受超大的摩擦力,否则会造成大量断头和飞圈。