安全带校核
安全带设计指南00
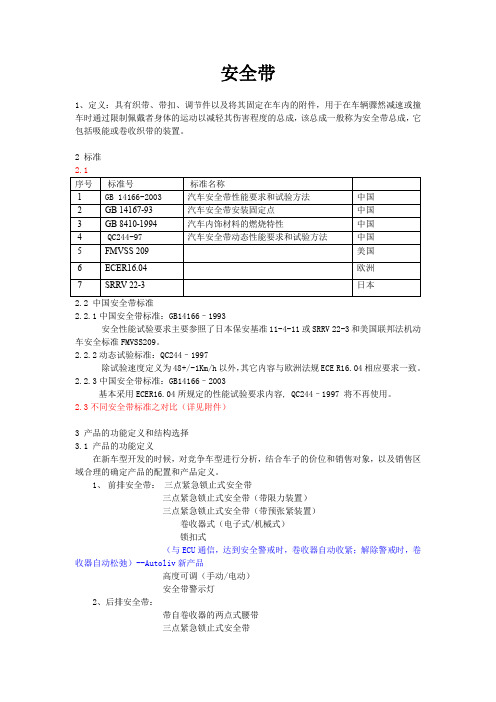
安全带1、定义:具有织带、带扣、调节件以及将其固定在车内的附件,用于在车辆骤然减速或撞车时通过限制佩戴者身体的运动以减轻其伤害程度的总成,该总成一般称为安全带总成,它包括吸能或卷收织带的装置。
2 标准2.12.2.1中国安全带标准:GB14166–1993安全性能试验要求主要参照了日本保安基准11-4-11或SRRV 22-3和美国联邦法机动车安全标准FMVSS209。
2.2.2动态试验标准:QC244–1997除试验速度定义为48+/-1Km/h以外,其它内容与欧洲法规ECE R16.04相应要求一致。
2.2.3中国安全带标准:GB14166–2003基本采用ECER16.04所规定的性能试验要求内容, QC244–1997 将不再使用。
2.3不同安全带标准之对比(详见附件)3 产品的功能定义和结构选择3.1 产品的功能定义在新车型开发的时候,对竞争车型进行分析,结合车子的价位和销售对象,以及销售区域合理的确定产品的配置和产品定义。
1、前排安全带:三点紧急锁止式安全带三点紧急锁止式安全带(带限力装置)三点紧急锁止式安全带(带预张紧装置)卷收器式(电子式/机械式)锁扣式(与ECU通信,达到安全警戒时,卷收器自动收紧;解除警戒时,卷收器自动松弛)--Autoliv新产品高度可调(手动/电动)安全带警示灯2、后排安全带:带自卷收器的两点式腰带三点紧急锁止式安全带三点紧急锁止式安全带(带预张紧装置)3、中间安全带:两点式腰带带自卷收器的两点式腰带三点紧急锁止式安全带3.2产品结构选择尽量在现有的产品结构中选择需要的产品。
比如:卷收器、锁舌、锁扣、导向件、高度调节器、紧固件(螺栓、螺母、螺钉、调整滚子)。
其他紧固件用垫圈、螺钉等尽量采用汽标件。
Autoliv的产品详见附页,可以在其中进行选择合适的产品结构。
3.3安装固定点螺孔尺寸按照GB14167-93的要求:安装固定点螺孔尺寸为7/16″-20UNF2A或2B。
安全带检验方法共7页

安全带检验方法本标准适用于高处围杆,悬挂和攀登作业。
安全带各部件和整体要做负荷试验。
分静负荷和冲击试验两部分。
1 静负荷试验和要求1.1 安全带各部件(包括带、绳、金属配件和使用的缝线)和围杆带、绳整体做静负荷试验,按GB6095—85《安全带》的规定进行,合格后才准组装成安全带。
整体围杆带或绳做4412.7N(450kgf)静负荷测试,合格后,才能批量生产。
1.2 试验设备49000N(5t)拉力试验机1台;980.6N(100kg)拉力试验机1台;试验架一座;0.5t卷扬机1台;整体静负荷试验装置一套如图10。
1.3 各部件检验情况1.3.1 安全带、绳的试件结构尺寸见图1、图2。
绳的两端应插成3~4道的花的绳环。
1―缝线;2―铆钉;3―带图1 带的试件尺寸1―绳环;2―编结花;3―绳图2 绳的试件尺寸1.3.2 金属配件的试件结构尺寸应符合设计要求。
1.3.3 安全钩静负荷试验连接形式,见图3、图4、图5、图6、图7。
1―夹具;2―扁钢钩;A、B―加力处图3 扁钢钩测试图1―夹具;2―圆钢钩;A、B―加力处图4 圆钢钩测试图]1―绳;2―自锁钩;3―夹具;A、B―加力处图5 封闭式自锁钩测试图1―绳;2―开启式自锁钩;3―挂钩;4―夹具;A、B―加力处图6 开启式自锁钩测试图1、4―夹具;2―挂钩框;3―攀登钩;A、B―加力处图7 攀登挂钩测试图1.3.4 各种连接环静负荷试验的连接形式,见图8。
1―板构夹具;2―半圆环;3―U型环夹具;4―圆环;5―三角环;6―品字环;7―8字环图8 连接环或试验用具图1.3.5 安全带卡子静负荷试验连接形式,见图9。
1、3―夹具;2―腰带扣;A、B―加力处图9 腰带扣测试图围杆带或绳做整体测试的连接形式,见图10。
1―夹具;2―安全带;3―半圆环;4―钩;5―三角环;6―围杆带或围杆绳;7―木轮;A―加力处;B―固定端图10 围杆带或绳整体静负荷试验图1.5 缝线试验将线栓在夹具上做拉力试验,要求破断负荷为156.8N(16kgf),拉断速度100mm/min。
汽车安全带固定点
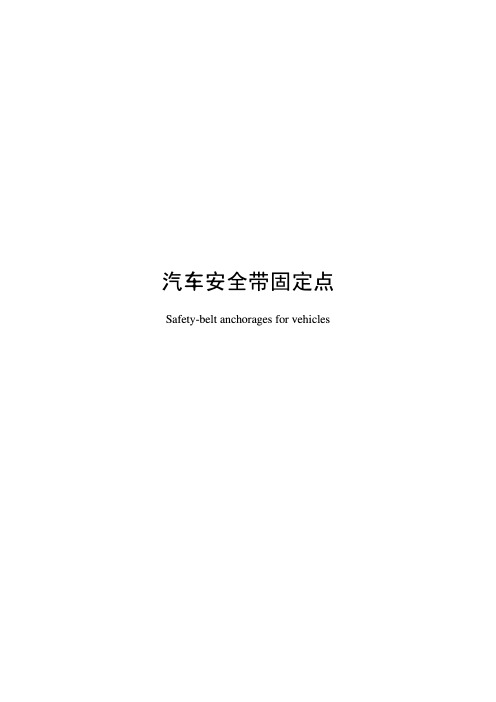
汽车安全带固定点
1 范围
本标准规定了汽车安全带安装固定点的位置、 强度要求和试验方法。 本标准适用千本公司生产的M1类和N类汽车上前向和后向座椅成年乘员用安全带固定点。
2 规范性引用文件
下列文件对千本文件的应用是必不可少的。凡是注日期的引用文件,仅所注日期的版本适用千本文 件。 凡是不注日期的引用文件, 其最新版本(包括所有的修改单)适用千本文件。
时 Qz 杖沪 土1沪
',
j j.
「
'I j
丿l f
I Ii /
j'
,f .
!lJ Ll丰帝扣
fl. l
伪O
J
J
r ·} ”
I
I L
v / ,.
L上
万
j f
( l, .
ll 丰扣纠
气•.
图1
4.3.2.3 如图2所示, 后排座椅安全带下有效固定点的角度: a) 对千M1类车辆的后排座椅, QI (非带扣侧)和a 2 C带扣一侧)应在30° �so 0 。 如果后排座 椅是可调的, 则在所有正常移动位置, 上述要求均有效; b) 对千N类车辆的长条座椅和带有调节机构且靠背小千 20° 的座椅, 以及正常使用位置上的其 他后排座椅, QI (非带扣侧)和a 2 C带扣一侧)允许在 20° �so 0 之间。
4
注4: CY 平面的定义:过 C 点的水平面为 CY 平面。 C 点位于 R 点垂直上方 450 mm 处, 即 CR=450 mm; 如果 s;,,:zso mm
时且用 BR= 260 mm+O. 8 XS 计算, 则 CR=500 mm。 注5: S 值是安全带上有效固定点至 P 平面的距离, S 值不得小千 140 mm。 注6: p平面的定义: P 平面是平行于车辆纵向中心平面的平面。 如果乘坐位置是由座椅的形状确定的, 则 P 平面为
车辆总布置人机工程设计的一般步骤
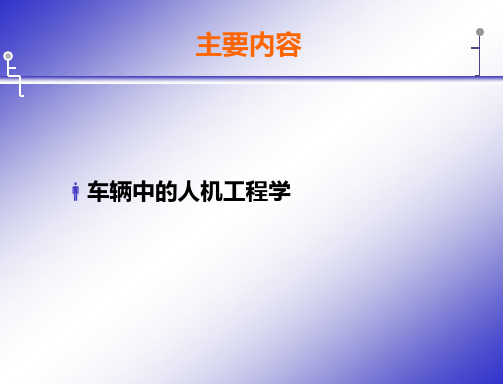
眼椭圆
眼椭圆
驾驶员眼椭圆与视野设计
驾驶员的手伸及界面及操作件的合理布置
足蹬力 手操舵力 手柄的设计 坐姿下驾驶员双手对方向盘的手操舵力与方向盘倾角 (侧视图上方向盘平面与水平之间的夹角)有密切的 关系。方向盘平面越接近水平即倾角越小,手操舵力 越大。但是可以转动方向盘的角度值变小,如图2-5所 示。此时对应的座椅靠背也比较垂直,驾驶员坐姿相 应地也比较平直。
驾驶员眼椭圆与视野设计
眼椭圆应用之轿车仪表板盲区 汽车行驶过程中,驾驶员需要经 常观察仪表板上的信息。在观察 时,驾驶员的视线会受到方向盘 的阻挡,方向盘的轮毂、轮辐和 轮缘在仪表板上形成相应的盲区 称之为仪表板盲区
驾驶员眼椭圆与视野设计
轿车驾驶员的前方视野
驾驶员的手伸及界面及操作件的合理布置
驾驶员的手伸及界面及操作件的合理布置
驾驶员手伸及范围的 分区 基准平面:指与汽车 纵向对称平面平行的 与座椅参考点(设计 时采用的H点)左右相 距50mm的两平面。
驾驶员的手伸及界面及操作件的合理布置
1区:位于参考平面左侧,由下列表面形成的区域: A)平行于方向盘平面且向上相距20mm的平面; B)平行于方向盘平面且向下相距170mm的平面; C)沿方向盘轮圈外缘向外扩展100mm的圆柱面。 该圆柱面的中心线与方向盘轴线共线。 D)通过方向盘轴线的两垂直相交平面。两垂直相交平面与 参考平面之间的夹角分别为40º,130º。
驾驶员的手伸及界面及操作件的合理布置
安全带法规校核
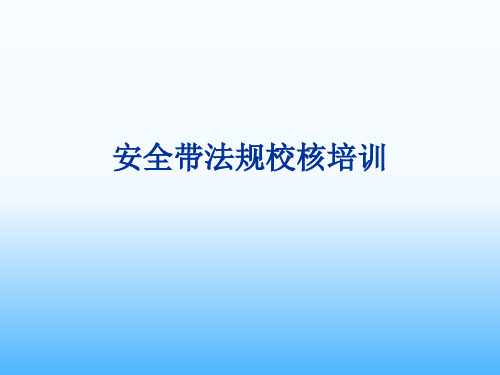
按照法规步骤作出上下固定点要求的角度、距离等画出规定区域
与法规相关要求值作比较,确定是否满足法规要求
安全带上部安装固定点区域
(说明:对于高度可调的安全带固定点,暂时没有相关的法规要求,有 待今后进一步的研究)
国标规定上部固定点区域
安全带法规校核培训
安全带简介
❖ 安全带定义:具有织带、带扣、调节件以及将其固定在车内的附件,用于在车辆骤然减速或撞车时通过 限制佩戴者身体的运动以减轻其伤害程度的总成,该总成一般称为安全带总成,它包括吸能或卷收织带 的装置。
❖ 1885年,安全带已经出现并使用在马车上,目的是防止乘客从马车中甩下去。1902年5月20日,美国 纽约举行汽车竞赛。参加竞赛的人中,有一位叫沃尔特·贝克的工程师,驾驶一辆鱼雷牌电动汽车,车 上除他外,还有一位技工。贝克在座位上钉上了一根带子套在身上以防不测,竞赛开始后,正在高速飞 驰的“鱼雷”碰到一根露出路面的钢轨,腾空而起,然后闯入人群,当场压死2人,伤数十人,可贝克 和那位技工却安然无恙。当时报纸报道了车辆带来惨重伤亡,却没有注意车上人是怎样幸免遇难的。
安全带的功能原理与分类
❖ 安全带的功能
安全带主要有两个方面的功能: ❖ 1、在车辆发生安全事故时,将因惯性前冲的乘客拦截下来,并将乘客受力的时间延长,
从而分散瞬间的受力。 ❖ 2、将乘客束缚在一定的空间里,有效的减少乘客与室内其他可能对其造成伤害的部件的
可能性,主要有仪表板、方向盘、前风挡玻璃,还包括座椅边缘。
紧急锁止式安全带(ELR)
简易式安全带
* 简易式安全带没有自动锁止功能,可允许织带自由拉出,扣上带扣时乘客必须
安全带固定点法规符合性校核

500; • D点的确定:DR=315mm+1.8S,但当S≤200 mm时,DR=675 mm
; • B点的确定:BR=260mm+S。但当S≥280 mm时,制造商可选用BR
=260mm+0.8S; • 躯干基准线的确定:对M1与N1类车辆,使与RC线成25º的一条直线
• 2.正确佩戴时安全带应无滑脱的危险; • 3.织带与车辆或座椅构架上凸出零件接触应无损伤织带的
危险; • 4.对于可改变位置的固定点(该固定点既便于乘员进人车
辆,且能约束乘员),本标准中的规定应适用于处于有效 约束位置时的固定点。
安全带固定点的最低数量
• 1.所有前向和后向座椅处的安全带固定点最低数量应符合下表的规定;
安全带固定点法规符合性校核
安全带总成的定义
• 具有织带、带扣、调节件以及将其固定在车内的附件,用于在车辆骤 然减速或撞车时通过限制佩戴者身体的运动以减轻其伤害程度的总成 ,该总成一般称为安全带总成,它包括吸能或卷收织带的装置。
目的 对安全带固定点进行法规符合性分析,确保设计满足企
业、行业、国家法规要求。
长120mm的线段;
•
XJ1:从X点沿垂直于RZ和ZX确定的平面的直线,向前截取长
60mm的线段。
•
J2点与J1点相对于过躯干线的纵向铅垂平面对称,该躯干线为安
放在座椅上的人体模型的躯干线。当用双开门为前后座椅提供通道,
且上定点在B柱上时,固定点系统应不妨碍乘员上下车;
安全带固定点的位置
3.2 安全带上有效固定点应位于垂直于座椅纵向中心面并与躯干线成 65°角的FN平面下方。对于后排座椅,此夹角可减小至60°。FN 平面与躯干线相交于D点,此时须保证DR=315mm+1.8S,但当 S≤200 mm时,DR=675 mm; 3.3 安全带上有效固定点应在垂直于座椅纵向中心面并与躯干线成 120°角且相交于B点的FK平面后方,此时须保证BR=260mm+S。 但当S≥280 mm时,制造商可选用BR=260mm+0.8S; 3.4 S值不得小于140 mm; 3.5 安全带上有效固定点应位于通过R点并垂直于车辆纵向中心平面 的铅垂平面之后; 3.6 安全带上有效固定点应在通过C点的水平面上方。
王云-座椅舒适性校核2015.10.21

(°)
脚角
(°)
表1 驾驶员坐姿推荐值
第4页/共44页
舒适参考范围 250~405 20~30 95~115 100~145 87~110
五、校核步骤
前排乘客舒适坐姿推荐值,见表2:
符号
尺寸名称
舒适参考范围
H31 R点到踵点的垂直距离 (mm)
127~405
A41 靠背角
(°)
20~75
A43 躯干与大腿夹角
L53-2 R点到踵点的水平距离 (mm)
A40-2 靠背角
(°)
A42-2 躯干与大腿夹角
(°)
A57-2 大腿与水平面夹角 (°)
A44-2 膝角
(°)
L46-2 脚角
5.2 软件分析校核步骤
表3后排乘客(舒°适)坐姿推荐值
舒适参考范围 127~405 —— 20~75 90~115 —— 90~145 95~130
5.3.3 后排乘员布置 依据硬点报告中相关硬点,按5.3.1方法操作,其中人体类型选择“乘员”,后排脚底面 与地毯成0度,测量所做假人坐姿角度是否满足表3要求。 注:SAE人体皆按5.3.1中步骤进行建立。 5.3.4 国标5%女性乘员布置 5.3.3.1中国国标5%假人与SAE假人人体坐姿的不同之处为在UG软件中“人体模型尺寸” 选择“自定义”,然后按照GBT 15759-1995进行尺寸的输入,输入R点位GB 5%女性人 体R点坐标值,如图7所示:
5.1 输入数据
数模:油门踏板(1108分组),地毯数模(5109分组)
硬点及参数:各排座椅R点、靠背角、踵点AHP、踏板角PRP(或踏板点)、方向盘中
心点、方向盘最大外径、方向盘倾角。
5.2 标准要求
QJM J01077-2018 安全带有效固定点法规校核规范

Q/JM J01077-2018安全带有效固定点法规校核规范1 目的和范围本规范规定了本公司车辆安全带有效固定点法规校核的一般要求。
本规范适用于本公司所有研发车辆的安全带有效固定点设计及校核。
2 引用文件下列文件对于本文件的应用是必不可少的。
凡是注日期的引用文件,仅注日期的版本适用于本文件。
凡是不注日期的引用文件,其最新版本(包括所有的修改单)适用于本文件。
GB 14167-2013 汽车安全带安装固定点、ISOFIX固定点系统及上拉带固定点EEC-R 14 关于机动车安全带安装固定点认证的统一规定76/115/EEC 机动车辆安全带固定点3 技术要求3.1 M1类车辆的前排座椅。
M1类车辆的a1(非带扣侧)应在30°~80°范围内,a2(带扣侧)应在45°~80°范围内。
前排座椅所有可正常移动的位置,角度要求同上。
在所有正常乘坐位置,a1和a2中至少有一个是恒定值时(如固定点在座椅上),其值应为60°±10°。
3.2 M1类车辆后排座椅。
对M1类车辆,所有后排座椅的a1和a2应在30°~80°范围内;如果后排座椅是可调的,则在所有正常移动位置,上述要求均有效。
3.3分别通过同一安全带的两个下固定点L1、L2且平行于车辆纵向中心平面的两个垂直平面间的距离不得小于350mm。
对M1和N1类车辆的后排中央乘坐位置,若相对其他乘坐位置是不可移位的,则上述距离不可小于240mm。
座椅的纵向中心平面应在L1和L2点之间,且距离至少为120mm。
3.4安全带上有效固定点应在垂直于座椅纵向中心面并与躯干线成65°角的FN平面下方。
对于后排座椅,此夹角可减小至60°。
FN平面与躯干线相较于D点,此时须保证DR=315mm+1.8S,但当S≤200mm 时,DR=675mm。
见图1。
3.5 安全带上有效固定点应该在垂直于座椅纵向中心面并与躯干线成120°角且相交于B点的FK平面后方,此时须保证BR=260mm+S。
- 1、下载文档前请自行甄别文档内容的完整性,平台不提供额外的编辑、内容补充、找答案等附加服务。
- 2、"仅部分预览"的文档,不可在线预览部分如存在完整性等问题,可反馈申请退款(可完整预览的文档不适用该条件!)。
- 3、如文档侵犯您的权益,请联系客服反馈,我们会尽快为您处理(人工客服工作时间:9:00-18:30)。
3. 安全带布置设计要求Biblioteka 3.1 安全带下有效固定点位置
3.1.1 M1类车辆的前排座椅
M1类车辆的α1(非带扣侧)应在30°-80°范围内,α2(带扣侧)应在45°-80 范围内。前排座椅所有可正常移动的位置,角度要求同上。在所有正常乘坐位 置,α1和α2中至少有一个是恒定值时(如固定点在座椅上),其值应为60±10° 。对于带有调节机构的可调座椅,当靠背角小于20°时,α1可以低于以上规定 的最小值(30°),但在任何正常使用位置均不得小于20°,参见图1、2。
图1 安全带下侧固定点(非带扣侧) 1.2 安全带下侧固定点(带扣侧,带扣固定于座椅上)
图2 安全带下侧固定点(带扣侧)
2.3 后排中间座椅安全带两固定点距离车辆纵向对称平面不得小于120mm且分列于 车辆纵向对称平面两侧,两者之间的距离不得小于350mm,如图3。
图3 后排中央座椅位置校核 1.4 前排安全带上有效固定点位置
安全带位置校核设计指南
一、 目的
为统一各车型安全带布置校核程序及输出结果,特制定本规范。
二、 适用范围
适用于乘用车研究院内各车型安全带位置的校核。
三、 规范内容
1. 规范引用标准
汽车安全带安装固定点报批稿
2. 相关定义
2.1 L1和L2点:同一安全带的两个下部有效固定点位置。
2.2
1和 2:分别为通过R点、L1点和R点、L2点,且垂直于车辆纵向中心
R-II长轴距安全带位置校核 1. R-II安全带固定点位置校核 1.1 安全带下侧固定点(非带扣侧)
R-II安全带下侧固定点(非带扣侧)均在车身上,且前排和中排座椅可调、第 三排座椅固定,因此对R-II而言,前排及中排座椅在所有正常移动位置时及第三 排座椅,α1应在30°-80°范围内,法规允许的安全带下侧固定点区域(非带扣侧) 如图1所示:
图3 安全带上有效固定点范围(俯视图) 4. 校核步骤 4.1前排座椅下固定点校核:按照3.1.1和3.1.3条中的要求作出法规允许的安全带 固定点区域,检查安全带实际固定点是否在允许的区域内以判断安全带固定点是 否满足要求。 4.2后排座椅下固定点校核:按照3.1.2和3.1.4条中的要求作出法规允许的安全带 固定点区域,检查安全带实际固定点是否在允许的区域内以判断安全带固定点是 否满足要求。 4.3后排中央座椅的下固定点校核:按照3.1.5条中的要求进行校核,判断是否满 足法规要求。
面的平面与水平面之间的夹角,如图1所示。
2.3 P平面的位置规定如下:
2.3.1 如果乘坐位置是由座椅形状确定的,P平面即为座椅的中心平面;
2.3.2 在不能确定乘坐位置的情况下:
2.3.2.1 对于驾驶员座椅,P平面为通过的方向盘中心且平行于汽车纵向中心面的 铅垂平面(可调式方向盘应位于正中位置)。
图4 前排安全带上固定点
图6 后排安全带上固定点 2.结论 由于CAS数据中缺少安全带固定点的具体位置,本文档给出了其布置的大致范围。
3.1.2 M1类车辆后排座椅
对M1类车辆,所有后排座椅的α1和α2应在30°-80°范围内;如果后排座椅是可调 的,则在所有正常移动位置,上述要求均有效。
3.1.3 M1类以外车辆的前排座椅
对M1类以外车辆的前排座椅的所有正常移动位置,α1和α2应在30°-80°之 间;对于最大总质量不超过3500kg车辆的前排座椅的所有正常使用位置,α1和α 2中至少有一个是恒定值时(如固定点在座椅上),其值应为60±10°。 3.1.4 M1类以外车辆后排座椅和特殊前排或后排座椅
2.3.2.2 对于前排外侧乘员座椅,P平面应为与驾驶员座椅的P平面相对称平面。
2.3.2.3 对于后排外侧乘员位置的P平面,应为车辆纵向平面的距离为A的平面, 由制造商按下述条件确定: 若长条座椅仅用于乘坐两人时,A>200mm; 若长条座椅乘坐超过两人时,A>300mm。 2.4 S为安全带上有效固定点至平行于车辆纵向中心平面的基准平面P的距 离,单位为mm。
4.4 按照3.2.2、3.2.3、3.2.5以及3.2.6条的要求作出相应的四个平面,检查安 全带实际的上有效固定点是否在允许的范围内以判断安全带固定点是否满足法规 要求。若安全带有附加固定点,则按照3.2.1和3.2.7条中的要求进行校核并判断 是否满足法规要求。 5. 结论
针对4.1至4.4项的校核结果,判断车辆安全带的上下实际固定点是否满足法 规要求。 附件1:安全带固定位置校核实例
3.2.2 安全带上有效固定点应位于垂直于座椅纵向中心面并与躯干线成65°角 的FN平面下方。对于后排座椅,此夹角可减小至60°。FN平面与躯干线相交于D 点,此时须保证DR=315mm+1.8S,但当S≤200mm时,DR=675mm。 3.2.3 安全带上有效固定点应在垂直于座椅纵向中心面并与躯干线成120°角 且相交于B点的FK平面后方,此时须保证BR=260mm+S。但当S≥280mm时,制造商可 选用BR=260mm+0.8S。 3.2.4 S值不得小于140mm。 3.2.5 安全带上有效固定点应位于通过R点并垂直于车辆纵向中心平面的铅垂 平面之后,如图1所示。 3.2.6 安全带上有效固定点应在通过2.5条规定的C点的水平面上方。 3.2.7 除3.2.1条规定的上有效固定点外,若满足下述条件之一,可以装备另 外的附加上有效固定点: 3.2.7.1 附加固定点应符合3.2.1至3.2.6的要求。 3.2.7.2 无需借助工具应能使用附加固定点。该固定点应符合3.2.5和3.2.6的 要求,并处于图1所示沿铅垂方向上下各80mm所确定的区域内。 3.2.7.3 符合3.2.6规定要求的全背带式安全带的固定点应位于通过躯干线的横 向平面之后,并处于下述位置: 3.2.7.3.1 对于单固定点,位于通过3.2.1规定的J1和J2点的两个铅垂面夹角内, 其水平截面见图3。 3.2.7.3.2 对于两个固定点, 固定点可位于上述二点之一的夹角内,同时其中一 固定点是另一个固定点相对于2.3中规定的座椅的P平面的对称点,且二者间的距 离不大于50mm。
图1 安全带有效固定点范围(侧视图)
图2 安全带有效固定点范围(俯视图) 3.2 安全带上有效固定点位置 3.2.1 如果因采用织带导向件或类似装置而影响安全带上有效固定点位置 时,应根据织带纵向中心线通过J1点时固定点的位置的情况来确定有效固定点位 置。从R点开始,用下述三条线段确定J1点: RZ: 从R点向上沿躯干线截取长530mm的线段; ZX: 从Z点沿垂直于汽车纵向中心面的直线,向固定点方向截取长120mm的线 段; X J1:从X点沿垂直于RZ和ZX确定的平面的直线,向前截取长60mm的线段。 J2点与J1点相对于过人体模型躯干线的纵向铅垂平面对称,当用双开门为前后座 椅提供通道,且上固定点在B柱上时,固定点系统应不妨碍乘员上下车。
其中前排安全带上固定点与前排座椅(单侧)中心线的Y向距离按原Refine 安全带的位置选取,S=267mm,大于标准要求的140mm。按照3.2.2、3.2.3、3.2.5 及3.2.6条的规定作出相应的四个平面,如图6中红色阴影区域所示。由于R-II前 排座椅安全带配备有高度调节器,属于附加固定点,因此按照3.2.7条的要求作出 附加固定点法规要求区域,如图4中蓝色阴影区域所示。