甲基丙烯酸甲酯生产工艺及技术经济比较
任务二 甲基丙烯酸甲酯生产工艺

2.MMA聚合 . 聚合 PMMA可用自由基型本体、溶液、悬浮、乳液 聚合进行生产,其中本体聚合采用最多。主要 用于生产板、棒、管状有机玻璃;悬浮聚合, 均聚合或与苯乙烯共聚合生产相应粒料,以用 于注塑成型、挤塑成型及牙托粉的生产。溶液 聚合生产涂料但应用少。乳液聚合生产皮革和 织物处理剂。
二、PMMA本体浇铸聚合法—有机玻璃板 材生产工艺
1.模具浇铸有机玻璃是PMMA聚合的典型产品, 其工艺主要有制浆、制膜、聚合、脱膜及其它辅 助工序和操作。生产流程如示意图4-2-2。
2.流程说明(参见附图) .流程说明(参见附图) (1)预聚合: 在装有搅拌器的预聚合釜内,加入引发剂过氧化苯甲酰、脱模剂―硬脂酸、邻苯 二甲酸二丁酯(增塑荆)和甲基丙烯酸甲酯,搅拌加热,控制一定反应温度进行 聚合,反应完毕后,料液冷却至30℃,放入贮槽。制备有色有机玻璃,还应溶入 所需的颜料,搅拌均匀。 (2)制模 将普通平板硅玻璃清洗,用酒精揩干,四周按要求厚度垫以包有玻璃纸的像胶或 PVC 垫条,并糊好封闭,留出浇料口。然后干燥。 (3)浇料 通过计量的甲基丙烯酸甲酯预聚合体料液灌入模内,倾斜模具,排出气体,并封 合。 (4)后聚合 封合后的模具用吊片架进入水箱中进行后聚合。至反应成型后,用热水脱模,成 品经检验分级、划线、切边后包装出厂。
7.脱模 聚合后的模子,用模具刀插入缝中微加压力 . 即可脱模,若有困难可用温水加热有助于脱模。脱模 后的片状物经修边、裁剪、检验、分级后即可包装入 库。 PMMA悬浮聚合是以水为介质,过氧化二苯甲酰为引 发剂、分散剂聚乙烯醇,滑石粉等反应在釜式反应, 温度在80~120℃,2小时后完成产物经洗涤、干燥、 造粒获得各种色泽的粒料。悬浮聚合控制,并获得分 子量较低,可进行注塑、挤压等成型加工。
甲基丙烯酸甲酯(MMA)工艺技术进展及技术经济分析

甲基丙烯酸甲酯(MMA )是一种重要的基础有机化工原料,广泛应用于汽车、建筑、医学、电子电气、纺织印染、涂料、胶黏剂、皮革处理化学品、树脂加工等诸多领域[1],其中最主要的用途为生产聚甲基丙烯酸甲酯(PMMA )、聚氯乙烯加工抗冲助剂丙烯酸酯类共聚物(ACR )、甲基丙烯酸甲酯-丁二烯-苯乙烯三元共聚物(MBS )及用作腈纶第二单体等,是国民经济发展不可或缺的重要化工原料。
近年来,受MMA 市场驱动影响,我国众多企业纷纷进入MMA 行业,国际国内竞争压力持续加大。
201—2019年我国MMA 产能进入集中爆发期,2019年为135.5万t/a ,相对于2014年底的58.3万t/a ,5年内产能扩张一倍。
不考虑2019年底新投产的江苏斯尔邦石化有限公司二期和重庆奕翔化工有限公司一期,整体产能利用率不足七成。
未来几年,受我国丙烯腈产业发展的带动,仍有大量MMA 在建、拟建装置,据初步统计,2020—2022年在建和规划产能达到118.5万t/a ,整个行业的竞争格局将愈加严峻;而另一方面,我国MMA 还存在大量进口,2019年进口量21.7万t ,净进口16.8万t ,主要进口来源为沙特阿拉伯,占我国进口总量的41%,其次是中国台湾(17%)和新加坡(14%),进口货源对国内市场仍存在巨大的冲击。
目前,全球MMA 产品已形成了C2路线、C3路线和C4路线等多样化工艺技术路线[2],在激烈市场竞争中,企业需要紧紧结合自身资源和技术优势,选择一条最合适的工艺路线,持续加强技术进步和提升,确保长期健康稳定发展。
为此,本文对MMA 不同工艺路线的进展和技术经济情况分别作了分析。
1MMA 工艺技术进展自1933年罗门哈斯公司建成世界上第一套MMA 工业化装置以来,不同公司对MMA 生产工艺路线进行了大量的尝试与探索,形成了C2、C3、C4多种工艺路线并行发展的格局。
1.1C2工艺路线C2路线以乙烯为原料,通过不同工艺转化成丙醛、丙酸或丙酸甲酯,再经过水解、酯化形成MMA ,目前已经产业化的工艺路线包括丙醛路线(BASF 法)、丙酸甲酯路线(Alpha 工艺)。
MMA生产工艺技术的比较

MMA生产工艺技术的比较摘要:对甲基丙烯酸甲酯(MMA)主要生产方法进行了分析和比较,重点阐述MMA的几种主流生产工艺丙酮氰醇法、乙烯法、改进丙酮氰醇法,异丁烯氧化法,并对各类装置的物料消耗、投资、成本进行了对比,提出可采取异丁烯直接甲基化工艺代替传统的工艺生产。
关键词:甲基丙烯酸甲酯;对比;异丁烯1. 丙酮氰醇法(ACH法)[1]丙酮氰醇法是生产MMA的主要方法之一,该技术由英国ICI公司开发,于1937年实现工业化。
以丙酮和氢氰酸为原料在碱催化剂作用下发生氰化反应,生成丙酮氰醇,ACH再与浓硫酸反应生成甲基丙烯酰胺硫酸盐,甲基丙烯酰胺硫酸盐再和甲醇水溶液反应生成MMA。
[2]我国已掌握了ACH法生产MMA的工艺技术,目前2 家最大的 MMA 生产企业吉林石化和黑龙江龙新化工均采用此工艺。
其优势是有效利用了石油化工丙烯腈装置的副产物氢氰酸,MMA 收率高,生产技术成熟;但缺点是反应使用大量的浓硫酸,对设备材质要求较高,且每吨 MMA 产品要副产 1. 2 t 的硫酸氢铵,需要配套建设昂贵的耐酸设备以回收硫酸氢铵。
另外,原料氢氰酸受丙烯腈装置开工率及价格的影响,采购成本较高;而建设氢氰酸合成装置则受到技术、原料和环保等多方面条件的限制,而且贮运和使用过程中也要求采取严格的防护措施。
[3]2.乙烯法(BASF法)乙烯法由德国BASF公司开发并于1988年建成投产3.6万t/a 的 MMA 生产装置。
该技术以乙烯和合成气(CO +H2)为原料,二者首先在Rh-Pt 络合物催化剂的作用下经过氢甲酰化合成丙醛,丙醛再与甲醛在仲胺催化剂的作用下进行缩合反应生成甲基丙烯醛(MAL),再经空气氧化生成 MAA,MAA 经分离提纯后与甲醇进行酯化反应生成 MMA。
乙烯法开辟了用煤化工原料替代石油原料的新路线,对充分利用煤资源、缓解油气紧缺的局面起到了重要的作用,且该技术有效降低了生产成本,原料优势明显,整个工艺无废水、废渣排放,是一条绿色清洁的工艺。
甲基丙烯酸甲酯的生产工艺

甲基丙烯酸甲酯的生产工艺甲基丙烯酸甲酯(Methyl Methacrylate,简称MMA)是一种重要的有机合成中间体,广泛应用于塑料、油墨、涂料、粘合剂等领域。
下面简要介绍甲基丙烯酸甲酯的生产工艺。
甲基丙烯酸甲酯的生产工艺主要包括原料准备、酯化反应、分离纯化和产品后处理等步骤。
首先,原料准备。
甲基丙烯酸甲酯的原料主要包括甲醇和丙烯酸甲酯。
甲醇通过蒸汽加热解和精馏处理来获得高纯度的甲醇。
丙烯酸甲酯可以通过丙烯腈的加氢反应或通过甲基丙烯酸的酯化反应来合成。
其次,酯化反应。
甲基丙烯酸甲酯的合成主要通过甲醇与丙烯酸甲酯的酯化反应进行。
该反应在酸性催化剂(如硫酸、磷酸等)存在下进行。
反应温度和反应时间的控制对产品质量有着重要的影响。
反应后生成的甲基丙烯酸甲酯和副产物经过分离纯化后即可获得高纯度的甲基丙烯酸甲酯。
然后,分离纯化。
酯化反应后的产物需要经过分离纯化来去除杂质和副产物。
分离纯化主要包括蒸馏、结晶等步骤。
首先,采用等温蒸馏来除去产物中的低沸点组分,如甲醛、丙烯酸等。
然后,采用减压蒸馏来除去高沸点组分,如高聚物和其他杂质。
最后,通过结晶来得到高纯度的甲基丙烯酸甲酯。
最后,产品后处理。
生产过程结束后,还需要进行产品的后处理工序。
常见的后处理工序包括质量检验、贮存包装等。
质量检验主要包括甲基丙烯酸甲酯的物理性质、化学性质、含量检测等。
贮存包装的目的是保持产品的稳定性和安全性。
以上是甲基丙烯酸甲酯的生产工艺的简要介绍。
生产过程中需要合理设计反应条件、控制生产过程和设备的选用,以确保产品的质量和产品的安全性。
甲基丙烯酸甲酯工艺流程比较
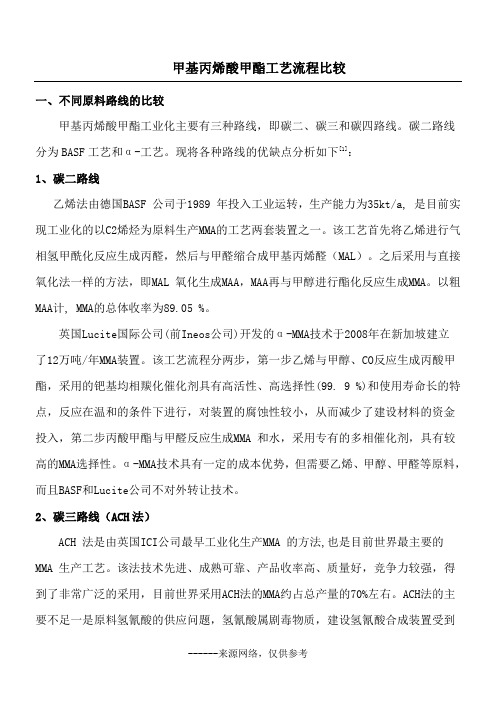
甲基丙烯酸甲酯工艺流程比较
一、不同原料路线的比较
甲基丙烯酸甲酯工业化主要有三种路线,即碳二、碳三和碳四路线。
碳二路线分为BASF工艺和α-工艺。
现将各种路线的优缺点分析如下[1]:
1、碳二路线。
以粗MAA计
了12
高的
而且
2、碳三路线(ACH法)
ACH 法是由英国ICI公司最早工业化生产MMA 的方法,也是目前世界最主要的MMA 生产工艺。
该法技术先进、成熟可靠、产品收率高、质量好,竞争力较强,得到了非常广泛的采用,目前世界采用ACH法的MMA约占总产量的70%左右。
ACH法的主要不足一是原料氢氰酸的供应问题,氢氰酸属剧毒物质,建设氢氰酸合成装置受到
技术、原料和环保等多方面条件的限制。
氢氰酸比较经济合理的来源是丙烯腈装置副产,但这将使MMA生产受到丙烯腈装置开工率的影响。
二是设备投资大,由于使用硫酸等强腐蚀物质,需要采用钛材、哈氏合金等材料。
三是废液处理问题,。
与其他工艺相比,ACH法需配套建设价格昂贵的酸性残液处理回收装置,回收硫铵。
因此采用ACH法的MMA生产装置须具有较大的规模才能保持较强的竞争力。
针对ACH法的这
3
至
区
4、比较和结论
中国大陆地区最近5年新建装置中碳四氧化法产能超过了70%。
下表是各种路线生产MMA的成本比较。
MMA各种工艺生产成本比较[2]
技术套。
[1]
[2]。
全球及中国甲基丙烯酸甲酯行业供需现状分析

全球及中国甲基丙烯酸甲酯行业供需现状分析一、MMA的基本性质甲基丙烯酸甲酯是一种有机化合物,又称MMA,简称甲甲酯,是典型的不饱和羧酸酯。
具有低温固化,快速固化,超强抗紫外线及耐磨性、耐候性、耐高低温差(-20-+70℃)等优点。
其主要物理性质为:MMA的化学性质主要有:(1)易挥发,易燃,与空气形成爆炸性混合物;(2)受光、热和催化作用易聚合;(3)易进行加成、卤化、亲核取代和酯交换反应;(4)毒性较小。
二、全球MMA行业市场现状分析世界MMA生产能力地区分布如下:亚洲为313.4万t/a,占世界总生产能力的59.9%;北美为97.8万t/a,占世界总生产能力的18.7%;西欧为66.1万t/a,占世界总生产能力的12.6%;中东为34万t/a,占世界总生产能力的6.5%;其他地区占世界总生产能力的2.3%。
中国大陆是世界上最大的MMA生产国,生产能力为128.5万t/a,占世界总生产能力的24.6%;其次为美国,生产能力为95.3万t/a,占世界总生产能力的18.2%;第三位是日本,生产能力为54.7万t/a,占世界总生产能力的10.5%。
三、中国MMA行业市场现状分析MMA作为一种重要的基础有机化工原料,近年来我国MMA生产能力逐年增长,据统计,截至2019年我国MMA产能达到128.5万t/年,同比2018年增长至38.5万t/年。
产量方面,据统计,截至2019年我国MMA产量为80.1万吨,同比增长44%,平均开工负荷率约在77%,较2018年大幅提高约15%。
2019年国内MMA市场行情整体处于低位,国内化工产品现货市场年内最高价为1月初的16000元/t,最低价至7月上旬10200元/t。
第1季度,MMA市场在需求低迷下重心持续下滑,3月小幅反弹;第2季度,MMA国内市场再次因终端需求持续疲软,一路下跌创近年来新低;第3季度由于工厂检修,加之上半年跌幅较大,现阶段现货趋紧形势下,触底反弹,市场重心回暖;第4季度是传统需求淡季,需求平平,市场显弱势。
浅谈生产甲基丙烯酸甲酯的新工艺

浅谈生产甲基丙烯酸甲酯的新工艺浅谈生产甲基丙烯酸甲酯的新工艺摘要:生产甲基丙烯酸甲酯的方法中最有经济性的是以异丁烯为原料通过直接氧化酯化法来得到,该工艺方法在工业化生产中很有竞争力。
本文介绍了用该方法生产甲基丙烯酸甲酯(MMA)的工艺过程以及生产的条件。
该项新工艺不同于一般的工艺方法,具有无污染、绿色环保、经济性等很多优点。
关键词:甲基丙烯酸甲酯;生产方法;新工艺;中图分类号:D412.64文献标识码: A 文章编号:1 引言用丙酮-氰醇法进行生产甲基丙烯酸甲酯是以前比较常用的方法,通过实验分析,该生产方法存在很多缺陷:生产过程中产生如亚硫酸氢钠等很多有害的副产品和对环境有危害的废水。
通过人们最近几年对国内外关于生产MMA方面的文献和技术资料进行分析,经过研究可以表明由混合C4经水合得到异丁烯,通过直接氧化酯化法来合成MMA,使得C4资源得到高价值的利用,是一条新工艺的技术路线。
用异丁烯催化氧化法―一种新工艺方法来生产甲基丙烯酸甲酯,可以避免出现丙酮-氰醇法所出现的问题,能够节约资源,降低生产成本,并且无废水产生。
截止到目前,只有日本领先于世界其它国家完成了该项新技术的工业化试验。
而中国通过近几年的科研,已经成功的研发出以异丁烯通过直接氧化酯化方法生产甲基丙烯酸甲酯的清洁工艺技术。
使得我国C4 资源取得最优利用这一课题从根本上得到了解决,改变了落后的生产甲基丙烯酸甲酯的工艺状况。
2 甲基丙烯酸甲酯新工艺研究2.1 工艺流程在多管式的第一反应器内加入叔丁醇、空气、蒸汽,催化剂同样也放入管中,用冷却剂进行循环冷却。
第二反应器的设备结构与第一反应器相同,反应后的流出物和剩余的异丁烯醛一同进入第二反应器,并在其内发生内反应。
反应结束后流出物含有MMA和未参加反应的异丁烯醛,将其放入甲基丙烯酸洗涤器内。
在甲基丙烯酸洗涤器内,用水溶液冷却气体用来收取甲基丙烯酸。
洗涤器内的排气被异丁烯醛吸收塔回收,在催化剂燃烧炉内进行燃烧,其内的部分气体作为惰气用于第一反应器和异丁烯醛气提塔,而异丁烯醛被吸收后用以惰气再返回到第二反应器。
甲基丙烯酸甲酯的生产工艺

甲基丙烯酸甲酯的生产工艺甲基丙烯酸甲酯的生产工艺金丰富王成(浙江卫星控股集团研究中心,浙江嘉兴314004)喃鞫甲基丙烯酸甲酯是一种重要的有机化工原料’主要应用于生产有机玻璃硬有机玻璃模塑料及其它工程塑料产品、PV C踟l生荆、胶粘剂、表面涂料等,市场前景十分广泛。
鹾搠】甲基丙烯酸甲酯;M M A;生产工艺甲基丙烯酸甲醋是一种重要的有机化工原料,主要应用于生产有机玻璃及有机玻璃模塑料及其它工程塑料产品、P V C改性剂、胶粘剂、表面涂料等,市场前景十分广泛。
1甲基丙烯酸甲酯的合成1.1C一3路线11.1丙酮氰醇法A CH此法是1934年I C I公司发明,1937年工业化,世界上80%的甲基丙烯酸甲酯用这个工艺合成。
丙酮氰醇和硫酸反应生成甲基丙烯酸硫酸盐,然后再和甲醇反应,生成甲基丙烯酸甲鸶。
丙酮氰醇是由氢氰酸和丙酮反应而成。
硫酸用量为1.4~1.8m ol/m ol A C H,硫酸既作为反应物,也作为溶剂。
首先生成甲基丙烯酰胺硫酸盐,副产物是a一羟基异丁烯酰胺硫酸盐(有水的情况下生成),而a一羟基异丁烯酰胺硫酸盐在比较高的温度和比较长的时间会生成甲基丙烯酰胺硫酸盐。
整个反应需要加入阻聚剂。
第一步反应80~100度,然后快速升高120~160度,整个反应时间1小时,这步转化率一般(按A C H算)是94%。
接下来用甲醇和水醋化甲基丙烯酸酰胺硫酸盐。
这个反应温度是100~150度,压力是7a t m,反应时间是1小时,一步转化率是(以甲基丙烯酰胺算)82%,甲醇和甲基丙烯酸循环反应,最终甲基丙烯酸甲酯的转化率接近90%。
生成的废水可以高温处理生成硫酸重复利用,也可以加入液氨,制成硫铵。
改进的A C H工艺是不用硫酸,最终转化率(按A C H算)84%。
第一步是丙酮氰醇制备a一羟基异丁酰胺,这个反应是丙酮氰醇和水在M n02催化作用下60度反应,转化率接近98%,然后再和甲醇在甲醇钠和离子交换树脂的催化作用下生成甲基丙烯酸甲酯,反应温度小于100度,这步转化率接近65%。
- 1、下载文档前请自行甄别文档内容的完整性,平台不提供额外的编辑、内容补充、找答案等附加服务。
- 2、"仅部分预览"的文档,不可在线预览部分如存在完整性等问题,可反馈申请退款(可完整预览的文档不适用该条件!)。
- 3、如文档侵犯您的权益,请联系客服反馈,我们会尽快为您处理(人工客服工作时间:9:00-18:30)。
甲基丙烯酸甲酯生产工艺及技术经济比较摘要从技术性和经济性角度评述了甲基丙烯酸甲酯的生产工艺, 包括丙酮氰醇(ACH) 法、异丁烯/叔丁醇法、乙烯法和异丁烷氧化法, 认为异丁烯直接氧化工艺具有原料来源广泛、收率高、环境污染小的特点。
关键词甲基丙烯酸甲酯, 生产工艺, 技术经济比较甲基丙烯酸甲酯(MMA)是一种重要的有机化工原料, 可在光热或催化剂存在下自聚或与其他单体共聚生成甲基丙烯酸甲酯树脂和塑料, 如聚甲基丙烯酸甲酯(PMMA)、MMA -苯乙烯(MS)树脂、MMA -丁二烯-苯乙烯(MBS)树脂等。
聚合产品具有透明度高、耐候性好、光学性能优良等特点, 广泛用作广告牌、照明材料、建筑材料、汽车零件等。
近来, 这些聚合产品在IT 行业相关领域如液晶显示屏光导板、DVD 光盘等的需求也快速增长。
在物理性质上, MMA 具有低毒性, 且可以回收, 因而是有利于环保的材料。
据统计, 2002 年全球MMA 生产能力为2 477 kt/a , 其中北美765 kt/a ,占30 .9 %;南美29 kt/a , 占1 .1 %;东欧50 kt/a , 占2 .0 %;西欧705 kt/a ,占28 .5 %;日本535 kt/a , 占21 .6 %;不包括日本的亚洲其他地区393 kt/a ,占15 .9 %[1]。
同年全球MMA消费量共1970 kt ,其中北美占35 %,欧洲占27 %,日本占19 %, 亚洲其他地区占15 %, 世界其他地区占4 %。
预计至2006 年全球MMA 年均需求增长率为3 %~ 3.5 %,其中亚洲增长强劲, 为4 %, 北美为3 .1 %, 欧洲为2 .4 %[2]。
2002年我国MMA生产能力约120 kt/a ,实际产量约90kt。
同年中国MMA 消费量约150 kt ,其中65 %用于有机玻璃的生产, 12 %用于塑料化工助剂, 11 %用于表面涂料, 12 %用于其他领域。
预计未来5 年中国MMA 发展的主要市场仍是有机玻璃、水性涂料和聚氯乙烯改性剂等[3]。
1 传统MMA 生产工艺及其改进丙酮氰醇(ACH)法是MMA 生产的传统工艺。
1982 年日本开发了以异丁烯为原料的直接氧化法工艺以来, 已开发出多种生产工艺, 其中有的已实现工业化,有的则尚在开发改进之中。
MMA 主要合成路线如图1 所示[4]。
目前在工业上,MMA 主要有5 种生产工艺。
由于采取不同的原料,合成MMA 的催化反应收率也有高有低。
各工艺装置的规模效益也不一样, 任何一项工艺没有绝对的优势。
全球MMA 生产能力中80 %采用ACH 工艺。
在MMA 三大生产地区, 北美、西欧主要采用传统的ACH 工艺,日本主要采用以C4 烃为原料的工艺。
本文从技术和经济性两方面评述了MMA 生产工艺。
1.1 ACH法ACH法以苯酚副产的丙酮和丙烯腈副产的氢氰酸为原料,生成ACH后在浓硫酸中加热生成甲基丙烯酰胺硫酸盐,再与甲醇进行酯化反应生成MMA。
该工艺的特点是有效利用了石油化工副产物, 且MMA 收率高, 无论以丙酮或氢氰酸计收率均超过97 %。
但由于过程中浓硫酸过量, 且生成大量硫酸氢铵副产物, 每生成1 t 的MMA ,副产1.2t硫酸氢铵, 因此增加了后续处理费用。
另外该工艺装置必须采用耐酸设备, 且原料氢氰酸具有剧毒。
为达到10 %的投资回报率, 该工艺装置还必须具有一定规模的生产能力和较高的开工率才有经济性。
Chem System s 对采用该工艺的MMA 生产装置进行了分析, 结果表明在生产能力为22 .7 ~272 .4 kt/a 、且装置满负荷运行时,MMA 产品生产成本随生产能力的增加以12 .2 %的速率递减;当生产能力固定为136 .1 kt/a , 而开工率在50 %~ 117 %变化时, MMA 产品生产成本随开工率的增加而以39 .2 %的速率递减, 从而表明了装置规模与生产成本之间的直接关系。
目前全球该工艺装置的生产能力多在100 kt/a 左右。
随着全球石化行业对环保要求越来越严格,该工艺固有的环境污染问题促使人们对其进行改进, 或开发新的MMA 生产技术。
1.2 新ACH法日本三菱瓦斯化学原采用ACH 工艺的MMA装置生产能力为6 000 t/a 。
由于酸性废弃物的处理问题以及氢氰酸原料供应不足, 限制了装置的扩能, 因此该公司对原工艺进行了改造。
1997 年三菱瓦斯将41 kt/a 新ACH 法工业化装置投入运行。
在该工艺中, 第一步(与传统ACH 法一样)丙酮与氢氰酸反应生成ACH 。
下一步将ACH 进行水合反应生成α-羟基异丁酰胺, 再与甲酸反应生成α-羟基异丁酸甲酯和甲酰胺, 然后α-羟基异丁酸甲酯脱水生成MMA , 而甲酰胺则分解成水和氢氰酸, 并将大部分氢氰酸进行循环, 以保证原料供应。
过程中避免使用硫酸, 因而不副产硫酸氢铵, 所以无需对废酸进行处理, 这样便使传统ACH 工艺开始向清洁化工艺发展。
然而该工艺MMA 总收率低, 约为93 %;另外过程中副产较多, 且由于氢氰酸需要循环, 能耗也较高, 因而在一定程度上制约了新ACH 工艺的进一步推广应用。
1.3 异丁烯/叔丁醇直接氧化法由于丙烯腈催化剂性能的改进, 副产氢氰酸生成量减少。
为此日本生产商研究开发了以C4 烃为原料的MMA 生产工艺。
1982 年三菱人丝和日本MMA 单体公司以异丁烯或其水合物叔丁醇(TBA)为初始原料, 经气相氧化与酯化两步反应制得MMA , 并将该工艺实现了工业化。
之后,亚洲地区基于该项C4 烃利用技术的新建装置迅速增加, 至2002 年末生产能力已达435 kt/a , 约占该地区MMA 总生产能力的46 %[4]。
直接氧化工艺首先必须对异丁烯进行分离。
原料异丁烯可从炼厂FCC 装置以及蒸汽裂解装置的副产C4 物流中获得, 例如石脑油裂解装置C4 物流经抽提分出丁二烯后, 抽余液中异丁烯含量为40 %~45 %[5]。
但异丁烯沸点(-6 .9 ℃)与1 -丁烯(-6 .3 ℃)非常接近, 很难分离。
因此三菱人丝采用强酸性离子交换树脂、旭化成采用高浓度杂多酸水溶液, 将异丁烯进行选择性水合反应生成TBA (沸点为82 .9 ℃), 以达到分离的目的。
另外住友化学还将含异丁烯的C4 烃物流与甲醇反应制得甲基叔丁基醚(MTBE) , 然后在固体催化剂上将MTBE 分解成异丁烯和甲醇, 甲醇可循环使用。
以异丁烯或TBA 为原料合成MMA 工艺的第一步氧化反应采用丙烯氧化制丙烯酸的Mo -Bi 系催化剂, 在反应温度350 ℃、空速1 000 h-1 下,甲基丙烯醛(MAL)和甲基丙烯酸(MAA)收率之和为90 .2 %。
第二步MAL 氧化制MAA 反应采用磷钼酸催化剂, 并添加碱金属以增加催化剂的热稳定性、调节活性及增加表面积。
在300 ~ 310℃、空速1 100 h-1下, MAL 单程转化率为89 %,MAA 选择性为86 %。
最后MMA 用液液抽提或共沸抽提等方式提纯后, 在硫酸存在下与甲醇在70 ~100 ℃下进行酯化反应, 生成MMA 的收率为80 %~ 90 %。
与ACH 工艺相比, 异丁烯或TBA 直接氧化法避免使用极毒原料氢氰酸, 同样也避免了废酸的生成以及设备腐蚀等问题, 但不足之处是收率较低。
因而目前正在继续开发性能好且使用寿命长的催化剂。
在投资回报率一定的情况下, 采用该工艺的MMA 装置产品生产成本主要受C4 烃原料成本以及副产MAA 收益的影响。
1.4 直接甲基化法日本旭化成公司于1984 年将以TBA 为原料经氨氧化制甲基丙烯腈(MAN)、然后与硫酸水合、再酯化的工艺实现了工业化, 生产能力为50 kt/a 。
该工艺虽然不使用氢氰酸, 但生成MAN 以后的过程与ACH 法大致相同, 仍存在废酸处理问题, 同时MMA 收率也不比直接氧化法高, 因此1999 年改造成直接甲基化法装置。
直接甲基化工艺将异丁烯或TBA 氧化得到的MAL 用甲醇与氧气进行氧化酯化反应, 可直接制得MMA 。
将异丁烯/空气/蒸汽以摩尔比1/11 .46/7 .53 送入转换器, 在350 ℃、空速1000 h-1 下,MAL 收率约86 .2 %。
然后MAL 溶解在过量甲醇中, 与气态氧在负载钯或铅的固体催化剂下进行氧化酯化反应, MAL 单程转化率为51 %, MMA选择性为94 %。
目前旭化成公司采用该工艺的装置生产能力为100 kt/a 。
近年来, 通过开发钯-铅系催化剂, 即使在甲醇/MAL 摩尔比降低的情况下,也可得到较高的转化率与选择性, 从而降低了甲醇回收费用[6]。
这项不经过MAA的简单工艺比直接氧化法的MMA 收率高, 但缺点是采用价格昂贵的贵金属Pd 催化剂, 故初期投资费用较高。
此外, 虽然与MMA 沸点相近的甲基丙烯酸副产减少, 但回收过剩甲醇又使公用工程费用有所上升。
1.5 乙烯法乙烯法由德国BASF 公司于1989 年投入工业运转, 生产能力为35 kt/a , 是目前惟一一项实现工业化的以C2 烯烃为原料生产MMA 的工艺。
该工艺首先将乙烯进行气相氢甲酰化反应生成丙醛, 然后与甲醛缩合成MAL 。
之后采用与直接氧化法一样的方法, 即MAL 氧化生成MAA ,MAA 再与甲醇进行酯化反应生成MMA 。
以粗MAA 计, MMA 的总体收率为89 .05 %。
BASF 在丙醛生产时利用了其原有设备, 但如果新建一套采用该工艺的装置的话, 投资费用过高, 因此之后没有新装置建设。
该工艺同直接氧化法一样,需要对MAL 氧化催化剂进行改进。
2 MMA 新工艺的开发近年来MMA 生产商除对传统工艺进行改进外, 还对基于乙烯、丙炔、丙烯和异丁烷的新工艺进行了技术开发。
与现有工业化技术相比, 这些新工艺大多数具有一定的成本优势及特有的技术优势。
2.1 Lucite 公司α-MMA 工艺英国Lucite 国际公司(前Ineos 公司) 开发的α-MMA 技术已经通过了中试鉴定, 即将建造100 kt/a MMA 工业装置[7]。
该工艺流程分两步,第一步乙烯与甲醇、CO 反应生成丙酸甲酯, 采用的钯基均相羰化催化剂具有高活性、高选择性(99 .9 %)和使用寿命长的特点, 反应在温和的条件下进行, 对装置的腐蚀性较小, 从而减少了建设材料的资金投入;第二步丙酸甲酯与甲醛反应生成MMA 和水, 采用专有的多相催化剂, 具有较高的MMA 选择性。
然后采用分馏法将MMA 从反应产物中分离出来。
工艺流程如图2 所示。
图2 Lucite α-MMA 工艺流程图α-MMA 工艺是继BASF 法之后, 最有可能实现工业化, 其最大的优点是可摆脱传统ACH 法和异丁烯氧化法的不足, 即无需酸回收装置, 且因工艺条件温和而无需采用特殊的制造材料。