应用GT-POWER进行发动机进气系统噪声仿真(2007)
基于GT-Power软件的BL1.6L发动机排气噪声优化研究
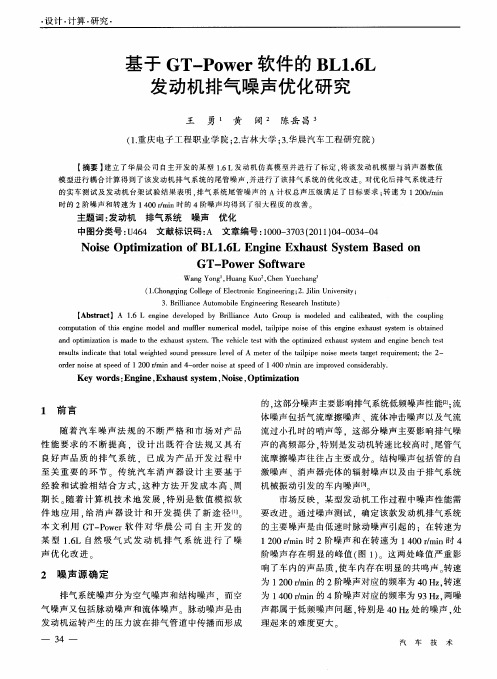
【 s at . L egn ee p d b rl ne A t Go p i m dl n a ba d i h opig Abt c】A 1 nie dvl e y Bii c uo ru s o e d a d cl rt ,wt te cu l r 6 o la e i e h n
模 型 进 行 耦 合计 算 得 到 了该 发 动 机 排 气 系 统 的尾 管 噪声 . 进 行 了该 排 气 系 统 的优 化 改 进 对优 化 后 排 气 系 统 进 行 并 的实 车 测 试 及 发 动 机 台架 试 验 结 果 表 明 . 气 系 统 尾 管 噪 声 的 A计 权 总声 压 级 满 足 了 目标 要 求 : 速 为 12 0 mi 排 转 0 d n 时 的 2阶 噪 声 和 转速 为 1 0 m n时 的 4阶 噪声 均 得 到 了 很 大 程 度 的改 善 0/i 4 r
r s h n ia e t a oa e g td s u d p e s r e e o t ro e t i i e n i es t r e e u r me t t e 2 e u si d c t h t tlw i h e o n r su e l v l fA mee ft al p os me t ag tr q i t h p e e n; h - o d r os ts e d o 0 mi n - r e os ts e d o 4 0rmi r mp o e o sd r by r e i a p e f12 0 r n a d 4 o d rn ie a p e f1 0 n e / / n a e i r v d c n i ea l .
基于GT-Power的汽车排气系统噪声优化设计

基于GT-Power的汽车排气系统噪声优化设计张利;胡光辉;汤海娟;左炜晨;严鑫映;丁吉民【摘要】文章基于GT-Power软件建立发动机和消声器模型,同时建立消声器的传递损失仿真模型和与发动机耦合仿真模型,经计算得到消声器的压力损失,仿真结果与试验结论基本一致,验证了模型的准确性.在保证压力损失目标要求下,对消声器结构进行优化改进,仿真结果具有较好的传递损失,试验结果验证了此方案具有较好的尾管总噪声和阶次噪声,满足NVH设计要求.文章可对汽车消声器设计起到参考作用.【期刊名称】《汽车实用技术》【年(卷),期】2017(000)012【总页数】5页(P224-228)【关键词】GT-Power;消声器;传递损失;尾管噪声;仿真分析【作者】张利;胡光辉;汤海娟;左炜晨;严鑫映;丁吉民【作者单位】安徽江淮汽车集团股份有限公司,安徽合肥 230601;安徽江淮汽车集团股份有限公司,安徽合肥 230601;安徽江淮汽车集团股份有限公司,安徽合肥230601;安徽江淮汽车集团股份有限公司,安徽合肥 230601;安徽江淮汽车集团股份有限公司,安徽合肥 230601;安徽江淮汽车集团股份有限公司,安徽合肥 230601【正文语种】中文【中图分类】U467.4+93随着汽车工业的快速发展,汽车噪声问题日益突出,相应的环境噪声法规也对汽车噪声要求越来越严格。
发动机排气噪声是汽车的主要噪声源,因此,开发消声性能良好、结构可靠、成本低廉的排气消声系统成为汽车企业的重要任务之一。
传统的消声器设计是基于经验和试验相结合的方法进行,在设计前期未能进行最优设计,整车验证阶段要浪费较长周期进行优化整改[1]。
随着计算机技术和数值分析法的发展,各种CAE软件可以较为准确的耦合发动机与消声器进行噪声分析,这为消声器的设计与开发提供了新的途径[2]。
本文基于 GT-Power软件的声学模块对某轿车排气消声器进行了原始方案设计与优化,在满足排气压力损失的情况下,消除车内共鸣音,降低尾管怠速噪声,同时满足 NVH噪声性能指标[3]。
采用仿真软件GT-Power和Fluent的消声器声学和流场分析
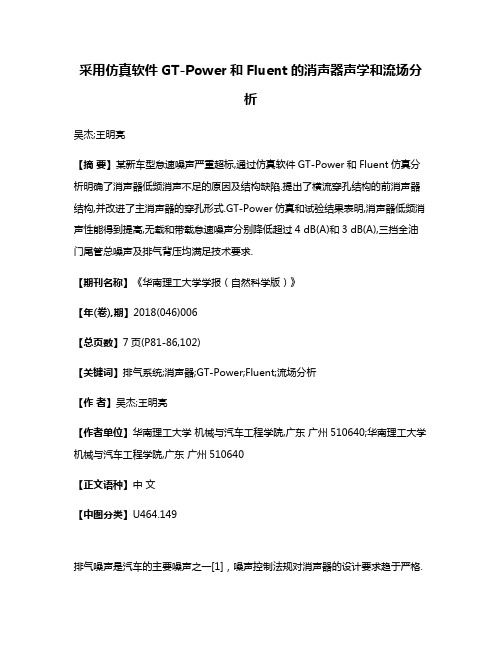
采用仿真软件GT-Power和Fluent的消声器声学和流场分析吴杰;王明亮【摘要】某新车型怠速噪声严重超标,通过仿真软件GT-Power和Fluent仿真分析明确了消声器低频消声不足的原因及结构缺陷.提出了横流穿孔结构的前消声器结构,并改进了主消声器的穿孔形式.GT-Power仿真和试验结果表明,消声器低频消声性能得到提高,无载和带载怠速噪声分别降低超过4 dB(A)和3 dB(A),三挡全油门尾管总噪声及排气背压均满足技术要求.【期刊名称】《华南理工大学学报(自然科学版)》【年(卷),期】2018(046)006【总页数】7页(P81-86,102)【关键词】排气系统;消声器;GT-Power;Fluent;流场分析【作者】吴杰;王明亮【作者单位】华南理工大学机械与汽车工程学院,广东广州510640;华南理工大学机械与汽车工程学院,广东广州510640【正文语种】中文【中图分类】U464.149排气噪声是汽车的主要噪声之一[1],噪声控制法规对消声器的设计要求趋于严格.计算机仿真技术的发展大幅度降低了消声器的开发成本,缩短了开发周期.侯献军等[2]利用GT-Power声学软件设计消声器并验证了软件仿真的有效性.李洪亮等[3]利用Fluent研究了消声器压力损失产生原因并指导消声器结构优化.张德满等[4]利用计算流体力学方法对消声器内部结构进行了分析优化,消声器压力损失得到明显降低.邓兆祥等[5]基于计算流体力学方法研究了结构参数和气流速度对穿孔管消声器再生噪声的影响,揭示了再生噪声的产生机理.康钟旭等[6- 7]通过建立计算流体力学模型计算了结构参数和掠过流马赫数对消声器穿孔板声阻抗的影响,计算结果表明,掠过流对穿孔板的声阻抗和穿孔管消声器的消声性能有明显影响.某在线开发轿车实车测试的空调关闭、开启状态下尾管怠速噪声超标3~5 dB(A).文中首先利用GT-Power软件对消声器初始方案进行声学性能仿真并分析了怠速噪声偏高的原因,进而利用Fluent软件对初始方案进行流场性能仿真,分析了消声器内部结构缺陷.结合消声器消声性能和流场性能分析给出了优化方案并进行试验验证.1 初始方案声学及流场仿真1.1 初始方案尾管噪声仿真GT-Power声学软件以一维流体动力学模型为基础,采用有限体积法进行计算.根据实际测量发动机进气系统参数和排气岐管系统参数,分别建立发动机的进气系统和排气岐管系统模型,根据主机厂给定的发动机参数(如表1所示)建立发动机箱体系统模型,将建立好的三大系统连接建立发动机GT-Power模型并根据试验数据修正模型,修正后模型数值对比如表2所示.从表2可以看出,额定功率(6 000 r/min)和峰值扭矩(4 500 r/min)的相对误差均低于5%,模型精度满足排气系统性能计算的精度要求.表1 发动机参数表Table 1 Engine parameters table参数数值参数数值排放标准国V缸径/mm75排量/L1.5行程/mm84.8工作方式自然吸气冲程4节气门电子气门额定功率/(kW·r-1·min-1)84/6000点火线圈笔式×4最大扭矩/(N·m·r-1·min-1)143/4000汽缸数4每缸气门数/个4压缩比10.5燃料形式汽油表2 发动机额定功率及峰值扭矩的仿真与实验值对比Table 2 Comparison of simulational and experimental engine rated power and peak torque功率和扭矩额定功率/kW峰值扭矩/(N·m)实验值84143仿真值82.71142.57误差/%-1.54-0.3根据生产厂家提供的两套初始方案的排气系统结构参数(前消声器相同),运用GT-Power软件建立发动机和排气系统的耦合仿真模型,如图1所示.图1 发动机与排气系统的GT-Power耦合仿真模型Fig.1 Coupled GT-Power simulation model of engine and exhaust system 图2为在三挡全油门(3WOT)加速工况下,利用耦合仿真模型计算得到的初始方案尾管噪声总值及各阶次噪声变化曲线.由图2可知,发动机低转速的排气噪声主要是由各阶次噪声引起,当发动机转速达到3 000 r/min以上时,气流再生噪声对尾管总噪声影响较大[8].初始方案1空调关闭,开启的怠速噪声分别为64.82dB(A)、68.46 dB(A);初始方案2空调关闭,开启的怠速噪声分别为65.62 dB(A) 、69.24 dB(A),均超出了主机厂要求的61 dB(A)(空调关)、65 dB(A)(空调开).图2 3WOT工况下初始方案尾管噪声Fig.2 Tailpipe noise of the original scheme at 3WOT case1.2 初始方案传递损失传递损失TL是表征消声器本身消声性能的重要特征.一般地,消声器的传递损失越大消声性能越好.传递损失表明声波经过消音元件后声波能量的衰减,即入射声功率级LWi和透射声功率级LWt的差值[8]:(4)式中,Wi为入射声功率,Wt为透射声功率.根据两负载法传递矩阵原理[9]在GT-Power中建立消声器传递损失仿真模型,计算得到传递损失变化曲线,如图3所示.图3 消声器传递损失变化曲线Fig.3 Change curve of transmission loss of the mufflers由图3(a)可知,初始方案前消声器中、高频消声性能较好,但200 Hz以下的传递损失低于9 dB(A),消声性能差.方案1后消声器在高于200 Hz时传递损失数值超过30 dB(A),但是低于120 Hz时传递损失低于18 dB(A),最小传递损失数值为12.5 dB(A),消声性能较差.方案2后消声器在170~910 Hz范围内传递损失超过25 dB(A),但是在低于170 Hz和高于910 Hz时传递损失数值均低于25 dB(A),在100 Hz以下的传递损失低至0 dB(A),消声性能差.由图3(b)可知,两套初始方案消声器总传递损失在100 Hz低频范围内均低于18 dB(A),这是造成尾管怠速噪声偏高的主要原因之一.1.3 初始方案内部流场仿真低频传递损失不足的主要原因在于消声器内部结构对低频声波的衰减不足,下面主要分析消声器的低速流场,分析低频传递损失不足的原因以指导结构优化.消声器的三维几何模型如图4所示.图4 初始消声器三维几何模型Fig.4 3D models of the initial mufflers为了分析消声器低速流场,设置消声器入口速度为20 m/s(对应发动机1 500r/min以下低转速工况).图5为前消声器内部速度矢量云图.由图5可知,只有少量气流流入吸音棉腔(高频消音腔)和共振腔,绝大部分气流直接排出消声器,这种前消声器高频吸音棉腔和高频共振腔直通管结构不利于衰减波长较长的低频段声波,低频消声效果较差[8].图5 前消声器速度矢量云图Fig.5 Velocity vector contour plot of the front muffler图6、图7为前消声器内部湍动能云图和再生噪声云图.可以看出,气流再生噪声云图和湍动能云图数值变化趋势相对应,表明气流速度剧烈变化是引起再生噪声的主要原因之一.由图7可知,再生噪声基本在60 dB(A)以下,说明发动机低转速时的气流再生噪声对尾管噪声影响不大,并非引起尾管怠速噪声偏高的原因.图6 前消声器湍动能云图Fig.6 Turbulent kinetic energy contour plot of the front muffler图7 前消声器再生噪声云图Fig.7 Regenerated noise contour plot of the front muffler综合上述分析,发动机低转速时前消声器的二次噪声数值较低、低频消声性能不足的主要原因在于前消声器结构简单、声阻抗较低、吸音棉腔和共振腔消声频率偏高,因此,需要优化调整前消声器内部结构以增加低频消声性能.后消声器内部结构复杂,需要对后消声器内部二维流场平面进行选择性分析,初始方案1和初始方案2的3个选择面如图8所示,特征见图4.图9为两套初始方案主消声器的速度迹线云图.1—隔板穿孔;2—入口管;3—出口管图8 后消声器剖面图Fig.8 Cross-section drawn of the rear mufflers图9 后消声器速度迹线云图Fig.9 Velocity track contour plot of the rear muffler由图9可知,初始方案1最后一腔隔板穿孔共振腔,仅有小部分气流流入,主要衰减中、高频率声波,对低频段声波衰减贡献较小.当气流从消声器入口腔流入第3腔时,气流向各个方向发散并没有形成明显涡流,进入第2腔时也没有形成明显涡流.当气流从第2腔流入第1腔,气流以较高的流速直接冲击到端盖,经过180°反转流入出口管,消声器抗性结构复杂,有利于衰减低频声波.初始方案2最后一腔出口管穿孔并填充吸音棉,主要衰减特定高频声波,对低频声波衰减贡献很小.消声器的第1、2腔单个腔体容积明显大于方案1的第1、2、3腔单个腔体容积,当气流从消声器入口腔流入第2腔时,虽然有部分气流直接流入第1腔,但是部分气流在第2腔内形成明显的涡流,会增加消声器的压力损失.气流流入第1腔时,因为腔内容积较大,部分气流直接流入出口管,虽然这样可以减小气流阻力损失,但也减小了消声器声阻抗,不利于衰减声波.图10给出了两套初始方案处理后消声器剖面速度矢量云图.图10 两套后消声器剖面速度矢量云图Fig.10 Velocity vector contour plot at the cross-section drawn of the two rear mufflers从图10(a)、图10(b)可以看出,在直径相同、气流入口流速相同的情况下,方案1比方案2入口管产生的射流粗且距离短,有利于高速气流与低速气流的冲击碰撞,能够进一步改变声波的传播规律以及入口管截面的声阻抗[10- 11].同时也会减小对隔板的冲击,降低排气阻力损失以及高频冲击噪声.方案1的最后隔板穿孔比方案2的不穿孔在降低气流冲击噪声和降低排气阻力方面有较大优势.由图10(c)、图10(d)可知,气流穿过隔板3.5 mm圆孔时,产生的射流范围小,不会冲击到正对隔板,并且圆孔之间距离较小,流场分布相对均匀,不易产生较大的再生噪声.对比图10(e)、图10(f)可以看出,隔板穿孔直径越大,气流穿过隔板时产生的射流范围越大、距离越长,且对穿孔位置正对隔板处产生冲击,易产生冲击噪声和射流噪声.图11给出了两套初始方案后消声器剖面湍动能云图.从图11可知,方案1的湍动能数值比方案2的大,且数值最大处位于第3隔板大圆孔(直径21 mm)正对的第2隔板小圆孔穿孔处.结合图10(e)可以看出,大圆孔穿孔处形成速度高、距离长的射流,高速射流直接冲击到第2隔板,使得第2隔板小圆孔穿孔处速度急剧变化,产生较大的湍动能.由图11(e)可知,在大圆孔处形成了数值大、范围广的湍流,且流场分布不均匀,不仅会产生较大的再生噪声,还会增大气流摩擦损失,增加排气阻力.与图11(b)、图11(d)和图11(f)相比较可以看出,小圆孔穿孔则无此现象.因此,从流场性能方面考虑,隔板穿孔选择小圆孔更好.图11 两套后消声器剖面湍动能云图Fig.11 Turbulent kinetic energy contour plot at the cross-section drawn of the two rear mufflers2 消声器优化方案前消声器采用横流穿孔以增加消声器抗性结构,从而增加消声器的中、低频降噪性能.在保证主机厂要求的离地间隙前提下,为增加消声器容积,选择前消声器截面为三角形形状.后消声器取消大圆孔隔板穿孔,用直径3.5 mm的小圆孔代替,将初始方案1的前3个消声腔与初始方案2的最后两个消声腔组合,并将最后一个隔板开3.5 mm圆孔,设计成与初始方案截面相同的5腔结构后消声器.前、后消声器优化方案二维结构示意图见图12.后消声器第1至第5腔长度分别为150、110、185、180、75 mm,第5腔填充玻璃纤维350 g.第1、2、3隔板各穿孔166个直径3.5 mm的圆孔,第4隔板穿孔266个直径3.5 mm的圆孔.进气管直径42.6 mm,出气管直径70 mm.距离出气管第1隔板20 mm处穿孔48个直径3.5 mm的圆孔,距离第4隔板7.5 mm处穿孔240个直径3 mm的圆孔.前消声器参数为:第1至第3腔长度分别为145、100、155 mm,第3腔填充玻璃纤维130 g.第1、2隔板分别穿孔32个直径10 mm的圆孔、100个直径3 mm的圆孔.进气管直径48 mm,出气管直径65 mm,出气管穿孔390个直径3 mm的圆孔.图3中给出了消声器优化方案的传递损失,在200 Hz范围内,前消声器、后消声器传递损失均较初始方案有较大幅度提高,表明采用GT-Power声学仿真结合Fluent流场分析的优化方法是有效的.图12 消声器优化方案Fig.12 Optimization scheme of muffler图13为3WOT工况下初始方案与优化方案尾管总体噪声和2阶次噪声仿真结果对比图,可以看出,在1 500 r/min以下时,优化方案尾管噪声下降明显,怠速噪声有较大幅度降低.优化方案尾管2阶次噪声在发动机转速低于4 200 r/min时降低明显,怠速2阶次噪声比初始方案降低2.1dB(A)左右;2 000 r/min 2阶次噪声较初始方案1降低4.02 dB(A),较初始方案2降低6.27 dB(A).优化方案也消除了初始方案在发动机2 500 r/min时的2阶次噪声峰值,较初始方案1降低6.74dB(A),较初始方案2降低10.27 dB(A),优化方案的阶次噪声改善明显.图13 3WOT工况下初始和优化方案的尾管仿真噪声Fig.13 Simulated tailpipe noise of the original and the optimized scheme at 3WOT case3 试验验证制作优化方案样件并安装到带有半消声室的试验台架,测量排气压力.总体布置及实物安装如图14所示,图中点1、点2为压力传感器安装位置.测量发动机从怠速到5 500 r/min过程中点1、点2的全压值,5 500 r/min时,排气系统点1背压为45 kPa,满足技术要求.为验证优化效果,进行实车测试,空调关闭、开启状态下怠速噪声分别降低至60.64 dB(A)和64.98 dB(A),满足了技术要求.图15为实车试验测得的发动机转速1 000~5 000 r/min范围内的3挡全油门尾管噪声总值以及2阶次噪声值,均满足要求.图14 实验室总体布置及实物图Fig.14 Layout and material object drawings of the laboratory图15 整车3挡全油门试验尾管噪声图Fig.15 Experimental tailpipe noise map of the vehicle at 3WOT case4 结语消声器进气管正对隔板穿孔比不穿孔好,能够降低气流对隔板冲击、降低冲击噪声以及排气阻力.隔板大圆孔(直径21 mm)穿孔,产生射流较大,流场分布不均匀,穿孔附近湍动能增加易引起较大再生噪声.隔板小圆孔(直径3.5 mm)穿孔比大圆孔穿孔好,产生的射流和湍动能更小,流场分布更加均匀.横流穿孔管结构前消声器低频消声性能更好.文中的仿真分析与设计方法及给出的横流消声器子结构也可为其它消声结构的优化设计提供借鉴.参考文献:【相关文献】[1] 马大猷.噪声与振动控制工程手册 [M].北京:机械工业出版社,2002.[2] 侯献军,王天田,田翠翠,等.基于GT-Power的乘用车消声器设计 [J].北京理工大学学报,2010,30(2):161- 165.HOU Xian-jun,WANG Tian-tian,TIAN Cui-cui,et al.Design of Passenger Vehicle Muffler Based on GT-Power [J].Transaction of Beijing Institute of Technology,2010,30(2):161- 165.[3] 李洪亮,谷芳,程魁玉,等.某轿车消声器性能的数值模拟 [J].汽车工程,2008,30(10):885- 888,897.LI Hong-liang,GU Fang,CHENG Kui-yu,et al.Acoustic analysis of automobile engine exhaust system based on CFD [J].Automotive Engineering,2008,30(10):885- 888,897. [4] 张德满,李舜酩,门秀花.单缸发动机消声器压力损失的CFD研究 [J].华南理工大学学报(自然科学版),2010,38(3):129- 132.ZHANG De-man,LI Shun-ming,MEN Xiu-hua.CFD investigation in to pressure loss of single-cylinder engine muffler [J].Journal of South China University of Technology(Natural Science Edition),2010,38(3):129- 132.[5] 邓兆祥,赵海军,赵世举,等.穿孔管消声单元气流再生噪声产生机理 [J].内燃机学报,2009,27(5):452- 457.DENG Zhao-xiang,ZHAO Hai-jun,ZHAO Shi-ju,et al.Producing mechanism of flow noise generation from perforated duct muffler element [J].Transaction of CSICE,2009,27(5):452- 457.[6] 康钟旭,季振林,连小眠,等.掠过流作用下穿孔板的声阻抗 [J].声学学报,2011,36(1):51- 59.KANG Zhong-xu,JI Zhen-lin,LIAN Xiao-mian,et al.Acoustic impedance of perforate plate with grazing flow [J].ACTA ACUSTICA,2011,36(1):51- 59.[7] 康钟旭,郑四发,连小眠,等.穿孔管消声器有流声学性能的数值预测 [J].内燃机工程,2011,32(5):7- 10.KANG Zhong-xu,ZHENG Si-fa,LIAN Xiao-mian,et al.Numerical prediction on acoustic characteristics of perforate tube silence with flow [J].Chinese Internal Combustion Engine Engineering,2011,32(5):7- 10.[8] 庞剑,谌刚,何华.汽车噪声与振动:理论与应用 [M].北京:北京理工大学出版社,2006:198- 203.[9] 徐航手,康钟绪,季振林.排气消声器传递损失的实验测量分析 [J].噪声与振动控制,2009,29(4);128- 131.XU Hang-shou,KANG Zhong-xu,JI Zhen-lin.Experimental measurement and analysis of transmission loss of exhaust silencers [J].Noise and Vibration Control,2009,29(4):128- 131.[10] 刘晨,季振林,胡志龙.高温气流对穿孔管消声器声学性能的影响[J].汽车工程,2008,30(4):331- 334.LIU Chen,JI Zhen-lin,HU Zhi-long.The effect of high temperature gas flow on the acoustic attenuation perfor-mance of perforated tube mufflers [J].Automotive Engineering,2008,30(4):331- 334.[11] 郭立新,范威.基于计算流体力学计算结果的穿孔管消声器声学性能研究 [J].机械工程学报,2017,53(1):79- 85.GUO Li-xin,FAN Wei.Acoustic attenuation performance of perforated tube silencer based on computational fluid dynamics results [J].Journal of Mechanical Enginee-ring,2017,53(1):79- 85.。
基于GT-Power软件的BL1
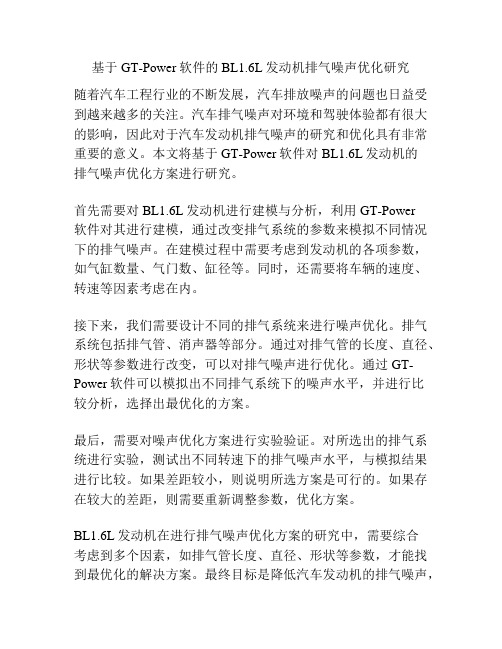
基于GT-Power软件的BL1.6L发动机排气噪声优化研究随着汽车工程行业的不断发展,汽车排放噪声的问题也日益受到越来越多的关注。
汽车排气噪声对环境和驾驶体验都有很大的影响,因此对于汽车发动机排气噪声的研究和优化具有非常重要的意义。
本文将基于GT-Power软件对BL1.6L发动机的排气噪声优化方案进行研究。
首先需要对BL1.6L发动机进行建模与分析,利用GT-Power软件对其进行建模,通过改变排气系统的参数来模拟不同情况下的排气噪声。
在建模过程中需要考虑到发动机的各项参数,如气缸数量、气门数、缸径等。
同时,还需要将车辆的速度、转速等因素考虑在内。
接下来,我们需要设计不同的排气系统来进行噪声优化。
排气系统包括排气管、消声器等部分。
通过对排气管的长度、直径、形状等参数进行改变,可以对排气噪声进行优化。
通过GT-Power软件可以模拟出不同排气系统下的噪声水平,并进行比较分析,选择出最优化的方案。
最后,需要对噪声优化方案进行实验验证。
对所选出的排气系统进行实验,测试出不同转速下的排气噪声水平,与模拟结果进行比较。
如果差距较小,则说明所选方案是可行的。
如果存在较大的差距,则需要重新调整参数,优化方案。
BL1.6L发动机在进行排气噪声优化方案的研究中,需要综合考虑到多个因素,如排气管长度、直径、形状等参数,才能找到最优化的解决方案。
最终目标是降低汽车发动机的排气噪声,提高驾驶体验,为环保事业做出贡献。
BL1.6L发动机排气噪声优化研究的目的是通过GT-Power软件建模和仿真,进行不同排气系统的参数优化,以找到最优的排气噪声优化方案。
在研究中需要对排气管长度、直径、形状及消声器进行优化,以达到降低汽车发动机的排气噪声的目的。
在进行模拟分析过程中,还需要考虑到尾气温度、流量、压力以及噪声的发生机理等因素。
这些因素之间相互影响,生产出不同的噪声频率和振幅。
通过GT-Power软件进行模拟和比较,可确定排气系统的最优设计方案。
基于GT-Power某MPV进气噪声优化设计

10.16638/ki.1671-7988.2017.17.080基于GT-Power某MPV进气噪声优化设计何延刚,张鹤,祝文举,麻金贺(安徽江淮汽车集团股份有限公司,安徽合肥230601)摘要:文章对某MPV进气系统进行优化,通过试验和分析该段噪声的特性及产生的机理,通过对空滤器出气管出气管的优化设计降低这显著噪声,改善了整车NVH性能,提高了产品竞争力。
关键词:波长管;低频噪声;插入损失;扩张腔中图分类号:U462.1 文献标识码:A 文章编号:1671-7988 (2017)17-217-04The optimization of a MPV's intake noise by GT-PowerHe Yangang, Zhang He, Zhu Wenju, Ma Jinhe( Anhui jianghuai automobile group co., LTD., Anhui Hefei 230601 )Abstract: Through experiment and analysis methods, this paper has carried out a research on a MPV's intake system noise. By optimizing the outlet pipes of the air filter, the level of noise decreased obviously. For the improvement of the MPV's NVH character increased, the competitive power of the car increased.Keywords: Wavelength of the tube; Low frequency noise; Insertion loss; The expansion of the cavityCLC NO.: U462.1 Document Code: A Article ID: 1671-7988 (2017)17-217-04前言进气噪声是汽车五大噪声源之一,非增压发动机的进气噪声比机械噪声高出5~10dB(A),仅次于排气噪声。
基于gt-power 的排气消声器数值仿真设计

国内外研究表明,排气噪声是发动机的主要噪声源之一,消声器是降低发动机排气噪声的重要部件,其性能好坏直接影响发动机的噪声大小和功率损耗。
本文主要叙述如何运用GT-POWER 对的排气消声器数值进行仿真设计。
1 消声器的主要评价指标 (1)传递损失:112210log w w w TLL L w ==−即消声器进口处的入射声功率级和出口处的透射声功率级之差。
(2)插入损失IL :定义为安装消声器前后在某固定测点处测得的计数声级或总声压值之差。
由于插入损失便于现场测量,非常实用。
在测量未安装消声器的排气噪声时应在排气管口加装一段与消声器等长的空管,以保证在安装消声器前后测点不变。
(3)功率损失比: 121100%NNe Ne R Ne −=×内燃机在标定工况下不安装消声器时的功率与安装消声器时的功率之差和不安装消声器时功率的百分比。
2 某型原消声器结构分析图1 原消声器结构如图1所示,采用单腔加两段穿孔管、一块穿孔隔板结构,容积比为3.2,扩张比为8.3。
从结构上分析,原件的设计存在以下不合理的地方: (1)容积小,空间利用不足。
容积比、扩张比都较小,而消声量很大程度上取决于这两个参数。
(2)采用穿孔管和穿孔板结构:穿孔声学元件的降噪量主要与穿孔率、小孔孔径有关。
穿孔率越小、孔径越小,消声量越大。
但穿孔率过小、气流的流动阻力损失则越大,功率损失亦大,经济性能变差。
因此,要提高消声量必须减小孔径, 要降低排气阻力又必须增大通流截面系数,该消声器这两项难以同时满足,我们认为在这种情况下采用小孔喷注结构是不理想的。
3 新消声器的设计 传统的消声器设计法存在着不足:实验周期长,人力物力消耗严重但仍不能取得好的效果,不能适应企业开发周期最小化的需要。
随着计算机软件技术的发展,发动机性能仿真技术也得到了快速发展并逐渐成熟。
GT-POWER 就是其中优秀的仿真软件之一,它的使用大大缩短了产品的开发周期,提高了企业的竞争力。
发动机进气系统性能仿真及降噪优化
一
损 失 、 气 口噪声 、 入 损 失进 行 评价 ; 体 动 力 性 进 插 气 能采 用压 力损 失进 行 评价 。本文 主 要通 过进 气 口 噪声 、 入损 失和压 力损 失来评 价消 声元件 性 能 。 插
个模 型里 完成 。 进 气 口噪 声 模 型 在 进 气 口位 置添 加 一个 麦 克
英 国汽 车 工业 研 究 协会 的研 究发 现 , 车 噪声 汽 中 以发 动机 噪 声 为 最大 u 。降低 汽 车 噪 声 , 从 降 要
放 标准 和 噪 声标 准 的 日益严 格 , 考 虑排 气系 统 噪 只 声 优化 已经 不 能满足 限值要 求 , 因此 有必 要对 发 动
声。
4 3
直 管长度 定义 。 24 消声 元件性 能评 价模 型 .
对进 气 消 声 元 件 的评 价 指 标 主 要 包 括 两 个 方
面 : 声性 能 和气 体 动 力性 能 。消 声性 能采 用 传 递 消
分别 将 22 23中的消 声 元件 与发 动 机耦 合 , .、 - 建 立 性 能评价 模 型 , 进气 口噪声 、 将 压力损 失 的计算 在
步优化 。
lO O 9 O
最 大 功 率 (W/ / n) k (mi r ) 最 大 扭矩 ( m ( mi) N./ / n) r 气 缸 点火 顺 序
基于GT-Power软件的汽车排气系统消声器的设计
基于GT-Power软件的汽车排气系统消声器的设计
马雪皎
【期刊名称】《机械工程与自动化》
【年(卷),期】2011(000)006
【摘要】介绍了一种新的发动机性能仿真软件GT- Power,它是以一维模型计算为基础,采用有限容积法对流体进行模拟运算的软件.综述了排气消声器的几种常用的研究方法,介绍了各种方法的优点和缺点,井分析了不同参数对各种消声器消声效果的影响.
【总页数】3页(P64-65,68)
【作者】马雪皎
【作者单位】中北大学机电工程学院,山西太原 030051
【正文语种】中文
【中图分类】U464.134+.4
【相关文献】
1.基于GT-Power软件的内燃机消声器设计与分析方法 [J], 钟绍华;金国栋;谢田峰
2.基于GT-Power的某汽车排气系统消声器改进 [J], 麻金贺;张鹤;朱帅;吴孟兵;何延刚;杨德银
3.基于gt-power软件的某汽车排气系统消声器改进 [J], 黄东洋;宋晓琳
4.基于GT-Power软件的排气消声器优化设计 [J], 江洪;白云
5.GT-Power软件的微型车消声器设计与优化 [J], 颜伏伍;杨伦;刘志恩;黄恒
因版权原因,仅展示原文概要,查看原文内容请购买。
gtpower排气声学仿真发展趋势
gtpower排气声学仿真发展趋势GTPower排气声学仿真是一种重要的技术手段,可以用来模拟和优化发动机排气系统的声学性能。
随着汽车工业的不断发展,排气声学仿真在汽车设计和制造中的作用越来越重要。
本文将探讨GTPower排气声学仿真的发展趋势。
GTPower排气声学仿真在汽车行业中的应用前景广阔。
随着尾气排放标准的不断提高,对发动机排气系统的噪声控制要求也越来越严格。
通过GTPower排气声学仿真,可以预测和评估不同排气系统设计对噪声产生的影响,从而指导发动机和排气系统的优化设计。
这对于汽车制造商来说是非常重要的,可以帮助他们提高产品的竞争力。
GTPower排气声学仿真的技术水平不断提高。
随着计算机硬件和软件的不断发展,声学仿真的计算能力和精度都得到了大幅提升。
现在的GTPower排气声学仿真软件可以模拟复杂的发动机排气系统,包括进气管、排气管、消声器等部件的声学特性。
同时,声学仿真软件还可以考虑流动效应、温度效应等因素对声学性能的影响,使得仿真结果更加准确和可靠。
GTPower排气声学仿真在新能源汽车领域的应用也越来越重要。
随着电动汽车的快速发展,电动汽车的噪声控制也成为一个重要的问题。
通过GTPower排气声学仿真,可以优化电动汽车的排气系统设计,减少电动汽车的噪声污染,提高驾驶舒适性。
GTPower排气声学仿真还可以与其他仿真技术相结合,实现更全面的性能评估。
例如,可以将GTPower排气声学仿真与流体力学仿真、热力学仿真等技术相结合,共同评估发动机排气系统的性能。
这种多物理场耦合仿真能够更真实地模拟发动机排气系统的工作状态,为优化设计提供更全面的参考。
GTPower排气声学仿真在汽车行业中具有广阔的应用前景。
随着技术的不断发展,GTPower排气声学仿真的计算能力和精度将进一步提高。
同时,GTPower排气声学仿真与其他仿真技术的结合也将成为未来的发展方向。
通过不断创新和研究,GTPower排气声学仿真将为汽车制造商提供更可靠、高效的排气系统设计方案,进一步推动汽车工业的发展。
GT—POWER在内燃机设计中的应用
GT—POWER在内燃机设计中的应用作者:张杰来源:《电脑知识与技术》2013年第25期摘要:在计算机技术发展越来成熟的今天,利用计算机辅助工程人员进行设计能大大提高工程人员的工作效率,该文主要对GT-POWER在内燃机设计方面的应用进行介绍。
在GT-Power中建立了一台涡轮增压发动机的仿真模型,并对仿真模型进行了校验,以对进气岐管的优化和不同压缩比对发动机性能的影响为例进行了简单探索。
关键词: GT-POWER;内燃机;仿真;应用中图分类号: TP391.9 文献标识码:A 文章编号:1009-3044(2013)25-5780-03传统的内燃机研究模式,主要是根据设计的图纸制造原型机,在试验台上进行不同机构参数的分析,根据实验结果进行对比改进,不断的实验才能得到用于生产的机型。
但这种传统的实验方法要耗费大量的人力、物力、财力资源,而且周期长,已经不能满足现代经济与科技快速发展的需要。
近几十年,主要随着计算机技术的发展,流体力学,化学反应动力学及相关的学科完善,采用计算机数值模拟的方法解决内燃机工程技术上的相关问题已经是大势所趋[1]。
在内燃机的研究与开发应用过程中,计算机数值模拟仿真技术已成为十分重要而且非常实用的辅助手段,国内外的各大厂商及科研机构都在加大这方面的研究和开发。
现在的内燃机的研究方法主要是实验法与计算机数值模拟法两种结合。
实验法是利用相关的实验技术在试验机上进行研究,是理论研究的前提和基础,而仿真却是减小实验范围和预测实验结果的最好工具。
GT-POWER是内燃机工作过程模拟计算软件,是一款由美国Gamma Technologies公司开发的具有内燃机工业标准的模拟仿真工具,市场占有率最高,被世界上大多数发动机和汽车制造厂家及供应商使用。
该软件采用有限体积法进行流体的计算,计算步长自动可调,有强大的辅助建模前处理工具,自带有优化设计功能,能进行直接优化设计[2]。
在发动机开发过程中,利用GT-POWER软件可以进行以下几个方面的仿真计算和优化设计:1)发动机的性能计算,包括经济性、动力性及相关的污染物排放,在特定的设计目标下,进行多种参数优化设计。
- 1、下载文档前请自行甄别文档内容的完整性,平台不提供额外的编辑、内容补充、找答案等附加服务。
- 2、"仅部分预览"的文档,不可在线预览部分如存在完整性等问题,可反馈申请退款(可完整预览的文档不适用该条件!)。
- 3、如文档侵犯您的权益,请联系客服反馈,我们会尽快为您处理(人工客服工作时间:9:00-18:30)。
应用GT-POWER进行发动机进气系统噪声仿真
Noise Simulation of Engine Intake System
by GT-POWER
张小燕
(长安汽车工程研究院 重庆 401120)
摘要:本文以进气系统的设计为例,介绍了用GT-POWER计算进气系统的模拟过程和进气系统的设计方法和过程,验证了几种主要的消声结构对进气系统噪声的影响,说明了GT-POWER软件在进气系统开发中发挥的主要作用。
关键词: 进气系统 设计 噪声 GT-POWER
Abstract:the paper introduced the intake system simulation and design by GT-POWER, verified the effect of some anechoic structure and showed the main function of GT-POWER in intake system development.
Key words: Intake system design noise GT-POWER
1、前言
发动机的进气系统的主要功能除了为发动机提供充足的,干净的空气外,还要有很好的降噪作用。
进气系统是汽车最主要的噪声源之一,进气口的噪声是影响整车通过噪声的一项重要的因素,所以进气系统的降噪设计也是非常重要的。
进气系统的噪声降低与进气系统的压力损失两者之间是一对矛盾。
如果进气管道截面积越大,空气流通就越顺畅,压力损失越小,发动机功率就越大,但同时进气口噪声也就越高。
在设计中就必须平衡这对矛盾。
本文研究项目是在发动机现有的进气系统基础上进行设计改进,将发动机进气口的噪声控制在目标值之内。
本文应用发动机热力学计算分析软件GT-POWER建立发动机热力学和声学分析模型,计算出发动机进气口的噪声总压值。
通过不断的增加消声结构,逐步降低进气口的噪声,直到满足控制目标。
2、进气系统消声设计步骤
1)首先不采用任何消声措施,只用一根管道与发动机相连接,分析进气口噪声变化,将结
果与目标噪声比较,得到所需要的消声曲线。
2)设计空气滤清器。
根据安装空间设计空气滤清器本体。
空气滤清器容积应该尽可能的大,这样传递损失大而且覆盖的频带宽。
图一 常用空滤器结构
空滤器的进入管和输出管有时会插入到空滤器中,插入的长度对传递损失有影响,不
同的插入长度都能够提高空滤器的传递损失,但插入管会带来较大的功率损失,其功率损失要比减小管道截面积带来的损失还要大。
空滤器的传递损失为:
)2cos()2cos()L 2sin(
(1m (25.01[10lg TL 2λπλπλπb a L L m −+= (1) La 为进入管在空滤器中的长度;L 为空滤器本体长度;
Lb 为输出管在空滤器中的长度;m 为扩张比。
3)确定空滤器进出管的管径,减小空滤器进、出管管径对降低噪声有好处,但是会增加
进气系统的压力损失,降低发动机的进气量,影响发动机的性能。
在设计时要权衡两
方面的得失。
4)根据增加了空气滤清器之后的进气口噪声来确定需要增加的消声结构。
常用的消声结
构如下:
A 赫姆霍兹消声器一般是针对低频的,传递损失与消声容积的形状没有关系。
赫姆霍兹消声器的共振频率为:
c
c Vl S c f π22= (2) 传递损失为:
]2/(1lg[102f
f S l V S TL r
r m c
c −+= (3) V 为空滤器容积;Lc 为连接管长度;Sc 为连接管截面积;Sm 为主管道截面积
B 1/4波长管一般用来消除高频噪声,如果要用1/4波长管消除低频噪声,波长管必须
做得很长。
1/4波长管的共振频率为:
L
c n f 4)12(−= (4) 1/4波长管的传递损失为:
]2tan *(411lg[102λ
πL m TL += (5)
3、GT-POWER 在进气系统设计应用的实例
GT-POWER 软件能够模拟发动机的气体流动情况,通过建立发动机的模型、进气系统
噪声分析模型及设置麦克风信号采集信息,可以得到进气口的噪声总压。
将进气口的噪声总压控制在目标值之下,能够很好的降低发动机的进气噪声。
发动机原机的进气系统的空滤器容积为8.7L,空滤器进管直径为76mm,出管直径为68mm ,与现在的发动机匹配,由于空间限制进气系统的空滤器容积必须减小。
根据现状态的空间尺寸设计空气滤清器本体为5.8L,空滤器进管直径为76mm,出管直径为68mm。
首先计算新状态进气系统的进气口噪声水平,结果如图二:
图二 新旧进气系统噪声比较
由计算结果可以看出,新状态的空滤器由于体积减小,导致进气口噪声增加,不能达到控制目标,必须增加其它消声结构,降低进气口噪声。
下面分几步优化新状态进气口的噪声,使其满足控制目标。
第一步:减小空滤器进管的直径由原来的76mm减小为60mm。
减小进管管径,能够提高扩张比,降低进气口噪声。
减小空滤器进管的管径能够有效的降低进气口的噪声,但需要同时关注发动机进气系统的压力损失增加情况,不能因为噪声降低引起发动机功率损失太大。
图三 空滤器进管直径对进气系统噪声比较
第二步:在第一步的基础上将进管进口部的直径由原来的60mm减小为50mm。
图四 空滤器进管进口直径对进气系统噪声比较
将空滤器进管进口改为缩管的形式,能够适当降低进气口的噪声总压。
第三步:在空滤器进管的中间增加四个小孔,小孔的作用是用来消除驻波影响的。
图五 空滤器进管小孔对进气系统噪声影响比较
4个小孔对于降低发动机进气口的噪声在整个发动机转速范围内都有明显的作用。
发动机进气口的噪声在2000rpm-3000rpm之间的噪声水平仍然高于控制目标。
第四步:第三种状态进气口各阶的噪声如图六所示:
图六 进气口各阶噪声分布曲线
由图六可以看出,影响进气口的噪声主要为二阶噪声。
在2000rpm-3000rpm之间,主要的噪声为二阶,在2500rpm时出现噪声峰值。
可以采用增加谐振腔降低2500rpm的噪声。
2500rpm的二阶频率为83Hz,所以建议增加83Hz的谐振腔来降低2000-3000rpm的噪声。
增加83Hz谐振腔后的计算结果如图七:
图七 空滤器谐振腔对进气系统噪声影响比较
计算结果表明83Hz谐振腔能够有效的降低2000rpm-3000rpm的噪声并使整个转速范围内的噪声降低到了控制目标之内。
第五步:验证进气系统对发动机性能降低的影响。
一般发动机不带进气系统与带进系统,在额定转速点的功率损失要求低于5%。
经过计算6000rpm时,不带进气系统时,发动机的功率为108.4kW,带进气系统时,发动机的功率为106.0kW,功率降低为2.2%,小于5%,满足设计要求。
经过分步模拟计算,得到与发动机匹配且满足噪声要求的进气系统初步结构和设计尺寸,根据此数据进行进气系统的详细设计。
4、小结
GT-POWER软件能够预测发动机进气口的噪声,能够对各种降噪结构的降噪效果进行预测,同时能够兼顾分析进气系统改变对发动机性能的影响。
GT-POWER软件能够很好的为发动机进气系统的前期开发提供快速有效的指导。
参考文献
1、庞剑 谌刚 何华等 汽车噪声与振动,北京理工出版社,2003年
2、何渝生,汽车噪声控制,机械工业出版社,1995年。