冲压模具设计与制造实例
冲压模具设计和制造实例
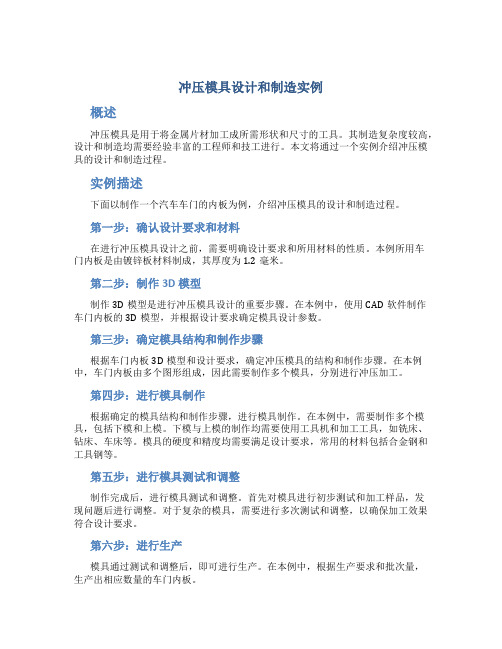
冲压模具设计和制造实例概述冲压模具是用于将金属片材加工成所需形状和尺寸的工具。
其制造复杂度较高,设计和制造均需要经验丰富的工程师和技工进行。
本文将通过一个实例介绍冲压模具的设计和制造过程。
实例描述下面以制作一个汽车车门的内板为例,介绍冲压模具的设计和制造过程。
第一步:确认设计要求和材料在进行冲压模具设计之前,需要明确设计要求和所用材料的性质。
本例所用车门内板是由镀锌板材料制成,其厚度为1.2毫米。
第二步:制作3D模型制作3D模型是进行冲压模具设计的重要步骤。
在本例中,使用CAD软件制作车门内板的3D模型,并根据设计要求确定模具设计参数。
第三步:确定模具结构和制作步骤根据车门内板3D模型和设计要求,确定冲压模具的结构和制作步骤。
在本例中,车门内板由多个图形组成,因此需要制作多个模具,分别进行冲压加工。
第四步:进行模具制作根据确定的模具结构和制作步骤,进行模具制作。
在本例中,需要制作多个模具,包括下模和上模。
下模与上模的制作均需要使用工具机和加工工具,如铣床、钻床、车床等。
模具的硬度和精度均需要满足设计要求,常用的材料包括合金钢和工具钢等。
第五步:进行模具测试和调整制作完成后,进行模具测试和调整。
首先对模具进行初步测试和加工样品,发现问题后进行调整。
对于复杂的模具,需要进行多次测试和调整,以确保加工效果符合设计要求。
第六步:进行生产模具通过测试和调整后,即可进行生产。
在本例中,根据生产要求和批次量,生产出相应数量的车门内板。
冲压模具的设计和制造是一项复杂精细的工作,需要技术水平和经验。
本例通过一个车门内板的制作过程,展示了冲压模具设计和制造的详细步骤,包括确认设计要求和材料、制作3D模型、确定模具结构和制作步骤、进行模具制作、进行模具测试和调整以及进行生产。
这些步骤都需要严密的操作和高水平的技术,以确保最终的产品质量。
冲压模具实例

冲压模具实例例8.2.1冲裁模设计与制造实例工件名称:手柄工件简图:如图8.2.1所示。
生产批量:中批量材料:Q235-A钢材料厚度:1.2mm1.冲压件工艺性分析此工件只有落料和冲孔两个工序。
材料为Q235-A钢,具有良好的冲压性能,适合冲裁。
工件结构相对简单,有一个φ8mm的孔和5个φ5mm的孔;孔与孔、孔与边缘之间的距离也满足要求,最小壁厚为3.5mm(大端4个φ5mm的孔与φ8mm孔、φ5mm的孔与R16mm外圆之间的壁厚)。
工件的尺寸全部为自由公差,可看作IT14级,尺寸精度较低,普通冲裁完全能满足要求。
2.冲压工艺方案的确定该工件包括落料、冲孔两个基本工序,可有以下三种工艺方案:方案一:先落料,后冲孔。
采用单工序模生产。
方案二:落料-冲孔复合冲压。
采用复合模生产。
方案三:冲孔-落料级进冲压。
采用级进模生产。
方案一模具结构简单,但需两道工序两副模具,成本高而生产效率低,难以满足中批量生产要求。
方案二只需一副模具,工件的精度及生产效率都较高,但工件最小壁厚3.5mm接近凸凹模许用最小壁厚3.2mm,模具强度较差,制造难度大,并且冲压后成品件留在模具上,在清理模具上的物料时会影响冲压速度,操作不方便。
方案三也只需一副模具,生产效率高,操作方便,工件精度也能满足要求。
通过对上述三种方案的分析比较,该件的冲压生产采用方案三为佳。
3.主要设计计算(1)排样方式的确定及其计算图8.2.1手柄工件简图(2)冲压力的计算该模具采用级进模,拟选择弹性卸料、下出件。
冲压力的相关计算见表图8.2.2手柄排样图8.2.1。
根据计算结果,冲压设备拟选J23-25。
(3)压力中心的确定及相关计算计算压力中心时,先画出凹模型口图,如图8.2.3所示。
在图中将某oy坐标系建立在图示的对称中心线上,将冲裁轮廓线按几何图形分解成L1~L6共6组基本线段,用解析法求得该模具的压力中心C点的坐标(13.57,11.64)。
有关计算如表8.2.2所示。
冲压模具设计与制造实例
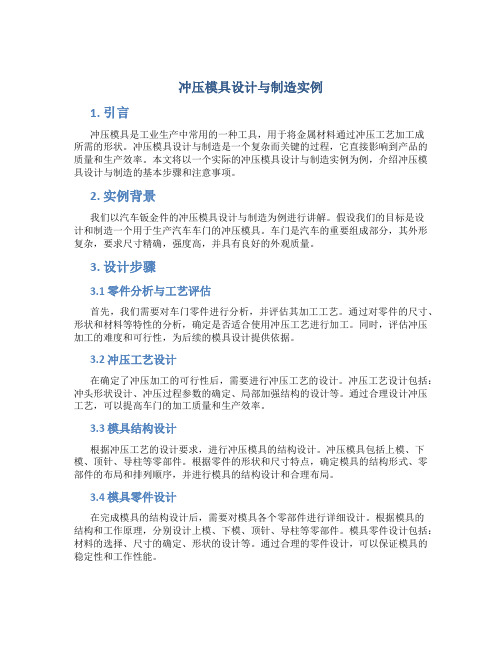
冲压模具设计与制造实例1. 引言冲压模具是工业生产中常用的一种工具,用于将金属材料通过冲压工艺加工成所需的形状。
冲压模具设计与制造是一个复杂而关键的过程,它直接影响到产品的质量和生产效率。
本文将以一个实际的冲压模具设计与制造实例为例,介绍冲压模具设计与制造的基本步骤和注意事项。
2. 实例背景我们以汽车钣金件的冲压模具设计与制造为例进行讲解。
假设我们的目标是设计和制造一个用于生产汽车车门的冲压模具。
车门是汽车的重要组成部分,其外形复杂,要求尺寸精确,强度高,并具有良好的外观质量。
3. 设计步骤3.1 零件分析与工艺评估首先,我们需要对车门零件进行分析,并评估其加工工艺。
通过对零件的尺寸、形状和材料等特性的分析,确定是否适合使用冲压工艺进行加工。
同时,评估冲压加工的难度和可行性,为后续的模具设计提供依据。
3.2 冲压工艺设计在确定了冲压加工的可行性后,需要进行冲压工艺的设计。
冲压工艺设计包括:冲头形状设计、冲压过程参数的确定、局部加强结构的设计等。
通过合理设计冲压工艺,可以提高车门的加工质量和生产效率。
3.3 模具结构设计根据冲压工艺的设计要求,进行冲压模具的结构设计。
冲压模具包括上模、下模、顶针、导柱等零部件。
根据零件的形状和尺寸特点,确定模具的结构形式、零部件的布局和排列顺序,并进行模具的结构设计和合理布局。
3.4 模具零件设计在完成模具的结构设计后,需要对模具各个零部件进行详细设计。
根据模具的结构和工作原理,分别设计上模、下模、顶针、导柱等零部件。
模具零件设计包括:材料的选择、尺寸的确定、形状的设计等。
通过合理的零件设计,可以保证模具的稳定性和工作性能。
4. 制造步骤4.1 模具加工在完成模具设计后,需要进行模具的加工制造。
模具加工包括:材料采购、加工设备的选择、加工工艺的制定等。
根据模具的设计要求,选择适合加工模具的机床设备,进行模具零部件的加工。
加工过程中,需要严格控制尺寸和精度。
4.2 零部件组装模具零部件加工完成后,需要进行零部件的组装。
冲压磨具结构设计的十大经典案例

冲压磨具结构设计的十大经典案例案例一:汽车车身冲压件的多工位磨具汽车车身冲压件的磨具设计具有独特的特点和挑战。
为了提高生产效率和质量,设计师通常需要设计多工位磨具。
多工位磨具可以在一次夹紧的情况下完成多个冲压工序,大大提高了冲压生产线的效率。
案例二:飞机翼罩冲压模具飞机翼罩是航空领域中关键的部件之一,其冲压模具设计要求非常高。
翼罩的形状复杂且精度要求高,需要考虑到翼罩的强度、刚度和表面光洁度等因素。
设计师经过精心的磨具结构设计,保证了飞机翼罩的质量和性能。
案例三:家电外壳冲压磨具家电外壳冲压磨具的设计要求外壳的造型美观,同时要满足耐用性和制造成本的要求。
设计师通过合理的冲压工艺和磨具结构设计,实现了家电外壳的高效生产和质量控制。
案例四:电子产品金属外壳冲压模具电子产品金属外壳的冲压模具设计要考虑到外壳的精度、尺寸稳定性和表面处理要求。
设计师通过合理的模具结构设计和冲压工艺,实现了电子产品外壳的高质量和高效生产。
案例五:手机壳冲压模具手机壳的冲压模具设计要考虑到外观要求,如曲面和切割边缘的处理。
设计师通过创新的磨具结构设计和冲压工艺,实现了手机壳的设计复杂性和高质量要求。
案例六:钢铁行业冲压磨具设计钢铁行业的冲压磨具设计要考虑到材料的硬度和可加工性。
设计师通过合理的磨具结构设计和冲压工艺,提高了钢铁行业的生产效率和产品质量。
案例七:航天器零部件冲压模具航天器零部件的冲压模具设计要求非常高,需要考虑到零部件的材料性能、结构复杂度和重量要求等因素。
设计师通过优化的磨具结构设计和精细的制造工艺,实现了航天器零部件的高质量和可靠性。
案例八:新能源汽车零部件冲压模具新能源汽车零部件的冲压模具设计要考虑到其特殊材料和结构要求。
设计师通过创新的磨具结构设计和精细的制造工艺,实现了新能源汽车零部件的高质量和可靠性。
案例九:家具五金件冲压模具家具五金件的冲压模具设计要考虑到五金件的形状复杂度和表面质量要求。
设计师通过合理的磨具结构设计和冲压工艺,实现了家具五金件的高质量和高效生产。
冲压模具设计和制造实例

冲压模具设计和制造实例冲压模具是指在金属板材冲压加工过程中使用的一种专业加工工具。
它是将板材经过模具的加工,使其按照设定的形状和尺寸进行变形或者分割的过程。
下面将为大家介绍一个冲压模具设计和制造的实例。
该实例是针对手机外壳的冲压模具设计和制造。
手机外壳是指手机整机的外部保护壳。
它起到保护手机内部电子元器件的作用,同时也是消费者对手机外观的第一印象。
因此,制造外观精美、质量可靠的手机外壳对手机制造商来说非常重要。
在这个实例中,冲压模具设计和制造的大致步骤如下:1.确定模具结构和尺寸:根据手机外壳的设计图纸,确定模具的结构和尺寸。
模具结构可以分为上模、下模和顶出模组成。
上模和下模通过导柱进行定位,保证模具的稳定性。
通过翻转上模和下模可以实现对外壳内外表面的冲压。
顶出模是用于排出冲压件的模块。
2.模具材料选择:根据冲压工件的材料和厚度,选择适合的模具材料。
常用的模具材料有工具钢和硬质合金。
工具钢具有良好的热处理性能和可磨削性,适合制造形状复杂的模具。
硬质合金具有高硬度和抗磨损性能,适合制造耐磨性能要求高的模具。
3.绘制模具零件图纸:根据模具结构和尺寸,绘制模具零件的图纸。
主要包括上模、下模、顶出模的轮廓形状和孔位等。
根据零件图纸可以制造模具的零件。
C加工模具零件:使用数控加工设备,根据模具的零件图纸进行加工。
零件加工包括铣削、钻孔和螺纹加工等。
通过CNC加工可以保证模具的精度和质量。
5.模具装配和调试:将加工好的模具零件进行装配和调试。
根据模具装配图纸进行模具组装,同时通过调试模具使其达到冲压工艺要求。
6.冲压试产:将手机外壳材料放入模具中,进行试产。
通过试产可以检验模具的设计和制造是否合理,以及工件的质量和尺寸是否符合要求。
如果不符合要求,需要进行修改和调整。
7.产品化生产:在通过冲压试产验证无误后,可以开始进行产品化生产。
根据市场需求和订单量,确定冲压模具的加工数量,进行批量生产。
通过以上的步骤,一个手机外壳的冲压模具设计和制造就完成了。
冲压模具设计与制造实例

冲压模具设计与制造实例冲压模具是工业生产中常用的一种模具类型,它主要用于冲压加工金属材料,实现金属板材的成型、剪切、翻边等工艺。
下面我们将给出一个冲压模具设计与制造的实例,以便更好地理解冲压模具的工作原理和制造流程。
实例:汽车车门冲压模具设计与制造1.设计工作开始前,需要对车门的设计图纸进行详细的分析和理解,确定车门的形状、尺寸、材料等信息。
同时,还需要参考汽车厂商提供的标准和要求,确保设计的模具能够满足实际生产的需要。
2.根据车门的设计和要求,制定出冲压模具的设计方案。
这包括模具结构、构成零部件、动力系统、导向系统等方面的设计。
例如,我们可以采用单步冲压模具结构,由上下模具、导向柱、导向套等部件组成。
3.根据设计方案,进行具体的零部件的设计。
这包括上下模的设计、导向柱、导向套、挡块、压力座以及弹簧等部件的设计。
这些部件的设计需要考虑到材料的选择、尺寸的确定以及工艺要求等。
4.根据零部件的设计,进行各个部件的加工制造。
这包括零部件的加工、热处理、装配等工艺过程。
例如,上下模具可以采用精密数控机床进行加工,导向柱、导向套可以采用热处理进行强化处理。
5.在模具制造完成后,进行模具的调试和试产。
这包括模具的安装、调整、模具的正常运行以及质量检查等工作。
例如,我们可以采用冲压机进行模具的试产,调整模具的参数和位置,确保生产出的车门符合设计要求。
6.在模具试产成功后,批量生产汽车车门。
这包括模具投入生产、调整生产过程、质量检查等工作。
同时,还需要制定模具的保养和维护计划,确保模具能够长期稳定地运行。
冲压模具设计与制造是一个复杂的工作,需要设计师具备较高的专业知识和技能。
同时,还需要进行大量的试验和实践,通过实际的生产验证设计和制造的可行性,确保模具的质量和性能。
只有设计与制造出高质量的冲压模具,才能保证汽车车门的质量和使用寿命。
以上是一个汽车车门冲压模具设计与制造的实例,通过详细的设计和制造过程,我们可以更好地了解冲压模具的工作原理和制造流程,加深对冲压模具的理解和掌握。
冲压模具设计和制造实例之欧阳引擎创编
冲压模具设计与制造实例欧阳引擎(2021.01.01)例:图1所示冲裁件,材料为A3,厚度为2mm ,大批量生产。
试制定工件冲压工艺规程、设计其模具、编制模具零件的加工工艺规程。
零件名称:止动件 生产批量:大批 材料:A3 材料厚度:t=2mm一、 冲压工艺与模具设计1.冲压件工艺分析①材料:该冲裁件的材料A3钢是普通碳素钢,具有较好的可冲压性能。
②零件结构:该冲裁件结构简单,并在转角有四处R2圆角,比较适合冲裁。
③尺寸精度:零件图上所有未注公差的尺寸,属自由尺寸,可按IT14级确定工件尺寸的公差。
孔边距12mm 的公差为-0.11,属11级精度。
查公差表可得各尺寸公差为:零件外形:65 mm24 mm30 mm R30 mm R2 mm-0.74 0-0.52 0-0.52 0-0.52 0-0.52 +0.36 0零件内形:10 mm 孔心距:37±0.31mm 结论:适合冲裁。
2.工艺方案及模具结构类型该零件包括落料、冲孔两个工序,可以采用以下三种工艺方案:①先落料,再冲孔,采用单工序模生产。
②落料-冲孔复合冲压,采用复合模生产。
③冲孔-落料连续冲压,采用级进模生产。
方案①模具结构简单,但需要两道工序、两套模具才能完成零件的加工,生产效率较低,难以满足零件大批量生产的需求。
由于零件结构简单,为提高生产效率,主要应采用复合冲裁或级进冲裁方式。
由于孔边距尺寸12 mm 有公差要求,为了更好地保证此尺寸精度,最后确定 用复合冲裁方式进行生产。
工件尺寸可知,凸凹模壁厚大于最小壁厚,为便于操作,所以复合模结构采用倒装复合模及弹性卸料和定位钉定位方式。
3.排样设计查《冲压模具设计与制造》表2.5.2,确定搭边值: 两工件间的搭边:a=2.2mm-0.11工件边缘搭边:a1=2.5mm步距为:32.2mm条料宽度B=D+2a1=65+2*2.5=70确定后排样图如2所示一个步距内的材料利用率η为:η=A/BS×100%=1550÷(70×32.2)×100%=68.8%查板材标准,宜选900mm×1000mm的钢板,每张钢板可剪裁为14张条料(70mm×1000mm),每张条料可冲378个工件,则η为:η=nA1/LB×100%=378×1550/900×1000×100%=65.1%即每张板材的材料利用率为65.1%4.冲压力与压力中心计算⑴冲压力落料力 F总=1.3Ltτ=1.3×215.96×2×450=252.67(KN)其中τ按非退火A3钢板计算。
冷冲压模具设计与制造实例
例8.2.1冲裁模设计与制造实例工件名称:手柄工件简图:如图8.2.1所示。
生产批量:中批量材料:Q235-A钢材料厚度:1.2mm1.冲压件工艺性分析此工件只有落料和冲孔两个工序。
材料为Q235-A钢,具有良好的冲压性能,适合冲裁。
工件结构相对简单,有一个φ8mm的孔和5个φ5mm的孔;孔与孔、孔与边缘之间的距离也满足要求,最小壁厚为3.5mm(大端4个φ5mm的孔与φ8mm孔、φ5mm的孔与R16mm外圆之间的壁厚)。
工件的尺寸全部为自由公差,可看作IT14级,尺寸精度较低,普通冲裁完全能满足要求。
2.冲压工艺方案的确定该工件包括落料、冲孔两个基本工序,可有以下三种工艺方案:方案一:先落料,后冲孔。
采用单工序模生产。
方案二:落料-冲孔复合冲压。
采用复合模生产。
方案三:冲孔-落料级进冲压。
采用级进模生产。
方案一模具结构简单,但需两道工序两副模具,成本高而生产效率低,难以满足中批量生产要求。
方案二只需一副模具,工件的精度及生产效率都较高,但工件最小壁厚3.5mm接近凸凹模许用最小壁厚3.2mm,模具强度较差,制造难度大,并且冲压后成品件留在模具上,在清理模具上的物料时会影响冲压速度,操作不方便。
方案三也只需一副模具,生产效率高,操作方便,工件精度也能满足要求。
通过对上述三种方案的分析比较,该件的冲压生产采用方案三为佳。
3.主要设计计算(1)排样方式的确定及其计算设计级进模,首先要设计条料排样图。
手柄的形状具有一头大一头小的特点,直排时材料利用率低,应采用直对排,如图8.2.2所示的排样方法,设计成隔位冲压,可显著地减少废料。
隔位冲压就是将第一遍冲压以后的条料水平方向旋转180°,再冲第二遍,在第一次冲裁的间隔中冲裁出第二部分工件。
搭边值取2.5mm和3.5mm,条料宽度为135mm,步距离为53 mm,一个步距的材料利用率为78%(计算见表8.2.1)。
查板材标准,宜选950mm×1500mm的钢板,每张钢板可剪裁为7张条料(135mm×1500mm),每张条料可冲56个工件,故每张钢板的材料利用率为76%。
冲压模具设计和制造实例
冲压模具设计和制造实例冲压模具是一种用于加工金属产品的工具,通过压力将金属材料加工成所需形状的工具。
下面,我将介绍两个冲压模具设计和制造的实例。
实例一:汽车车门冲压模具设计和制造汽车车门是汽车的一个重要部件,它通常由多个金属板件组成,需要通过冲压来制造。
车门冲压模具的设计和制造需要考虑以下几个方面:1.车门的形状和结构:车门通常由多个金属板件组成,包括外板、内板、框架等。
模具的设计需要根据车门的结构设计成相应的多工位冲模,以便一次完成多个工序的冲压操作。
2.材料选择:考虑到车门需要具备一定的强度和耐腐蚀能力,通常选择高强度钢板作为材料。
模具的设计和制造需要根据材料的性质和特点来选择合适的模具材料,确保模具具有足够的硬度和耐磨性。
3.工艺流程:冲压车门需要经过多道工序,包括剪切、成形、冲孔、弯曲等。
模具的设计需要根据车门的工艺流程,分解各个工序,确定模具的结构和工作方式。
4.精度和尺寸控制:冲压车门需要保证尺寸的准确性和表面的光洁度。
模具的设计和制造需要考虑到尺寸控制和表面质量的要求,采取相应的控制措施,如安装导向装置、调整模具的工作间隙等。
实例二:家用电器外壳冲压模具设计和制造家用电器外壳通常由金属材料制成,冲压是常用的制造工艺。
下面是家用电器外壳冲压模具的设计和制造实例:1.外壳结构和形状:家用电器外壳通常具有盒状结构,需要通过冲压来成形。
模具的设计需要根据外壳的尺寸和形状,设计成相应的单工位或多工位冲模。
2.材料选择:外壳通常采用不锈钢或者冷轧钢板作为材料,以保证外壳的强度和耐腐蚀能力。
模具的设计和制造需要选用适当的模具材料,以确保模具具有足够的硬度和耐磨性。
3.工艺流程:外壳冲压通常包括剪切、成形、冲孔、折弯等工序。
模具的设计需要分解各个工序,确定模具的结构和工作方式,以便一次完成所有工序。
4.精度和表面质量:外壳冲压需要保证尺寸的准确性和表面的光洁度。
模具的设计和制造需要考虑到尺寸控制和表面质量的要求,采取相应的控制措施,如安装导向装置、选用合适的冲头等。
冲压模具设计与制造实例教材(PDF 31页)
1. 冲压件工艺分析2. 工艺方案及模具结构类型3. 排样设计4.冲压力与压力中心计算5.工作零件刃口尺寸计算落料部分以落料凹模为基准计算 ,落料凸模按间隙值配制;冲孔部分以冲孔凸模为基准计算,冲孔凹模按间隙值配制。
既以落料凹模、冲孔凸模为基准,凸凹模按间隙值配制。
刃口尺寸计算见表1。
表 1 刃口尺寸计算6.工作零件结构尺寸7.其它模具零件结构尺寸根据倒装复合模形式特点: 凹模板尺寸并查标准JB/T-6743.1-94,确定其它模具模板尺寸列于表2:根据模具零件结构尺寸 ,查标准GB/T2855.5-90选取后侧导柱125×25标准模架一副。
8.冲床选用根据总冲压力 F总=352KN,模具闭合高度,冲床工作台面尺寸等,并结合现有设备,选用J23-63开式双柱可倾冲床,并在工作台面上备制垫块。
其主要工艺参数如下:公称压力: 630KN滑块行程: 130mm行程次数: 50 次∕分最大闭合高度: 360mm连杆调节长度: 80mm工作台尺寸(前后×左右):480mm × 710mm9.冲压工艺规程10.模具总装配图图 4 模具装配图11.模具零件图图 5 凸凹模图 6 冲孔凸模图 7 落料凹模板图 8 上模座板图 9 下模座板图 10 上垫板图 11 下垫板图 12 凸模固定板图 13 空心垫板图 14 推件块图 15 卸料板图 16 凸凹模固定板1. 主要模具零件加工工艺过程落料凹模加工工艺过程材料 :Gr12 硬度 : 60 ~ 64 HRC冲孔凸模加工工艺过程材料: T10A 硬度: 56 ~ 60HRC凸凹模加工工艺过程材料 :Gr12 硬度 : 60 ~ 64 HRC凸模固定板加工工艺过程材料 :45# 硬度 : 24 ~ 28 HRC凸凹模固定板加工工艺过程材料 :45# 硬度 : 24 ~ 28 HRC卸料板加工工艺过程材料 :45# 硬度 : 24 ~ 28 HRC上垫板加工工艺过程材料 :T8A 硬度 : 54 ~ 58 HRC下垫板加工工艺过程材料 :T8A 硬度 : 54 ~ 58 HRC空心垫板加工工艺过程材料 :45# 硬度 : 24 ~ 28 HRC上模座加工工艺过程材料 :HT200下模座加工工艺过程材料: HT200推件块加工工艺过程材料 :45# 硬度 : 24 — 28 HRC2. 加工过程:详见素材资源库中的视频。
- 1、下载文档前请自行甄别文档内容的完整性,平台不提供额外的编辑、内容补充、找答案等附加服务。
- 2、"仅部分预览"的文档,不可在线预览部分如存在完整性等问题,可反馈申请退款(可完整预览的文档不适用该条件!)。
- 3、如文档侵犯您的权益,请联系客服反馈,我们会尽快为您处理(人工客服工作时间:9:00-18:30)。
图1所示冲裁件,材料为Q235,厚度为1mm,大批量生产。
试制定工件冲压工艺规程、设计其模具、编制模具零件的加工工艺规程。
零件名称:1#件
生产批量:中批量
材料:Q235
1. 冲压件工艺分析
2. 工艺方案及模具结构类型
3. 排样设计
4.冲压力与压力中心计算
工件如图找到坐标计算得
24*12+60*0+24*12+14.5*24+38.6*27.97+14.5*24+31.4*12+31.4*12
Y= ——————————————————————————————=2.5 24+60+24+14.5+38.5+14.5+34.1+31.4
X=8.3
5.工作零件刃口尺寸计算
落料部分以落料凹模为基准计算 ,落料凸模按间隙值配制;冲孔部分以冲孔凸模为基准计算,冲孔凹模按间隙值配制。
既以落料凹模、冲孔凸模为基准,凸凹模按间隙值配制。
刃口尺寸计算见表1。
表 1 刃口尺寸计算
6.工作零件结构尺寸
7.其它模具零件结构尺寸
根据倒装复合模形式特点: 凹模板尺寸并查标准JB/T-6743.1-94,确定其它模具模板尺寸列于表2:
根据模具零件结构尺寸 ,查标准GB/T2855.5-90选取后侧导柱125×25标准模架一副。
8.冲床选用
根据总冲压力 F总=352KN,模具闭合高度,冲床工作台面尺寸等,并结合现有设备,选用J23-63开式双柱可倾冲床,并在工作台面上备制垫块。
其主要工艺参数如下:公称压力:1630KN
滑块行程: 120mm
行程次数: 60 次∕分
最大闭合高度: 140mm
连杆调节长度: 50mm
工作台尺寸(前后×左右): 63*63
9.冲压工艺规程
切料63*25的板料。