机械加工过程中的振动讲解
强迫振动现象分析资料讲解
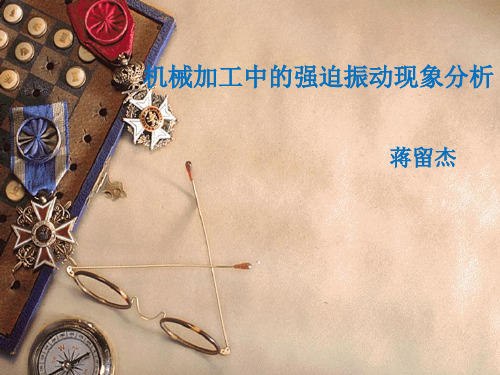
蒋留杰
机械加工过程中 ,在工件和刀具之间常产 生振动 。 产生振动时 ,工艺系 统的正常 切削 过程便受到干扰和破坏 ,从而零件 加工表面出现振纹 ,降低了 零件的加工 精度和表面质量 。机械加工过程中 产生 的振动 ,按其产生的原因来分 ,可分为自 由 振动 、强迫振动 和 自 激振动 三大 类 。 自由振动往往是由于切削力的突然 变化或其他外力的冲击等原因所引 起的 。 这种振动一般可以迅速衰减 ,因此对机械 加工过程中 的影响较小 。 而强迫振动 和自激振动都是不能自 然衰减而且危害 较大的振动 。
(2) 隔振 :即在振动的路线中安放具有弹性性 能的隔振装置 ,使振源所产生的大部分振动由 隔振装置来吸收 ,以减小振源对加工过程中 的干扰 。 如将机床安置在防振地基上及在振 源与刀具和工件之间设置弹簧或橡皮垫片等 。
(3) 提高工艺系统的刚度及增大阻尼 ,其目 的是使强迫振动的频率远离系统的固有频率 。 如使其避开共振区 ,使在λ≤0 (干扰力的频 率与系统固有频率的比值) 或λ ≥0 的情况 下加工 ,采用刮研接触面来提高部件的刚度 。
Байду номын сангаас
1 . 4 外部振源
由邻近设备 (如冲压设备 、龙门 刨等) 工作时的强烈振动通过地基传来 ,使工艺 系统产生相同 (或整倍数) 频率的强迫振 动。
3
减小强迫振动的措施和途径
(1) 减少或消除振源的激振力 :例如精确平衡 各回转零件、部件 ,对电动机的转子和砂轮不 但要进行静平衡 ,而且要进行动平衡。 轴承 的制造精度以及装配和调试质量常常对减小强 迫振动有较大的影响 。
1 .2 机床传动系统中的误差
机床传动系统中的齿轮 ,由于制造和装配误 差而产生周期性的激振力 。此外 ,皮带接 缝 ,轴承滚动体尺寸差和液压传动中油液脉 动等各种因素均可能引起工艺系统强迫振 动。
机械加工过程中机械振动的原因及对策分析
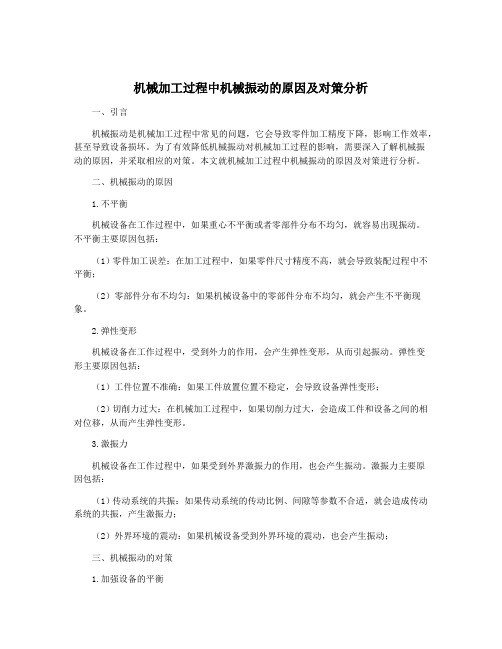
机械加工过程中机械振动的原因及对策分析一、引言机械振动是机械加工过程中常见的问题,它会导致零件加工精度下降,影响工作效率,甚至导致设备损坏。
为了有效降低机械振动对机械加工过程的影响,需要深入了解机械振动的原因,并采取相应的对策。
本文就机械加工过程中机械振动的原因及对策进行分析。
二、机械振动的原因1.不平衡机械设备在工作过程中,如果重心不平衡或者零部件分布不均匀,就容易出现振动。
不平衡主要原因包括:(1)零件加工误差:在加工过程中,如果零件尺寸精度不高,就会导致装配过程中不平衡;(2)零部件分布不均匀:如果机械设备中的零部件分布不均匀,就会产生不平衡现象。
2.弹性变形机械设备在工作过程中,受到外力的作用,会产生弹性变形,从而引起振动。
弹性变形主要原因包括:(1)工件位置不准确:如果工件放置位置不稳定,会导致设备弹性变形;(2)切削力过大:在机械加工过程中,如果切削力过大,会造成工件和设备之间的相对位移,从而产生弹性变形。
3.激振力机械设备在工作过程中,如果受到外界激振力的作用,也会产生振动。
激振力主要原因包括:(1)传动系统的共振:如果传动系统的传动比例、间隙等参数不合适,就会造成传动系统的共振,产生激振力;(2)外界环境的震动:如果机械设备受到外界环境的震动,也会产生振动;三、机械振动的对策1.加强设备的平衡对于不平衡造成的振动,可以采取以下对策:(1)提高零件加工精度:在零件加工过程中,应严格控制尺寸精度,避免误差导致的不平衡;(2)调整零部件分布:改变零部件的位置,使得机械设备的重心分布更加均匀。
2.增加刚度对于弹性变形引起的振动,可以采取以下对策:(1)稳定工件位置:通过改进夹具结构,提高工件的抓紧力,稳定工件的位置,减少弹性变形;(2)优化切削参数:通过调整切削速度、切削深度等参数,降低切削力,减少工件和设备之间的相对位移,减小弹性变形。
3.减少激振力对于激振力引起的振动,可以采取以下对策:(1)改善传动系统的设计:优化传动系统的传动比例、间隙等参数,避免传动系统的共振;(2)加强设备的隔振措施:通过在机械设备底部安装隔振装置,降低设备受外界环境震动的影响。
机械加工中振动的产生机理以及防治措施

机械加工中振动的产生机理以及防治措施一、机械加工过程中振动的危害振动会在工件加工表面出现振纹,降低了工件的加工精度和表面质量,低频振动时会产生波度;振动会引起刀具崩刃打刀现象并加速刀具或砂轮的磨损;振动使机床夹具连接部分松动,影响运动副的工作性能,并导致机床丧失精度;产生噪声污染,危害操作者健康;影响生产效率;二、机械加工过程中振动的类型机械加工过程中振动的类型:自由振动、强迫振动、自激振动。
1.自由振动工艺系统受到初始干扰力而破坏了其平衡状态后,系统仅靠弹性恢复力来维持的振动称为自由振动。
由于系统中存在阻尼,自由振动将逐渐衰弱,对加工影响不大。
2.强迫振动由稳定的外界周期性的干扰力(激振力)作用引起;除了力之外,凡是随时间变化的位移、速度和加速度,也可以激起系统的振动;强迫振动振源:机外+机内。
机外:其他机床、锻锤、火车、卡车等通过地基把振动传给机床机内:1)回转零部件质量的不平衡(旋转零件的质量偏心)2)机床传动件的制造误差和缺陷(如齿轮啮合时的冲击、皮带轮圆度误差及皮带厚度不均引起的张力变化,滚动轴承的套圈和滚子尺寸及形状误差)3)切削过程中的冲击(如往复部件的冲击;液压传动系统的压力脉动;断续切削时的冲击振动)强迫振动的特征:频率特征:与干扰力的频率相同,或是干扰力频率整倍数幅值特征:与干扰力幅值、工艺系统动态特性有关。
当干扰力频率接近或等于工艺系统某一固有频率时,产生共振相角特征:强迫振动位移的变化在相位上滞后干扰力一个φ角,其值与系统的动态特性及干扰力频率有关强迫振动的运动方程:图示:内圆磨削振动系统a) 模型示意图b)动力学模型c)受力图3.自激振动在没有周期性外力(相对于切削过程)作用下,由系统内部激发反馈产生的周期性振动;自激振动过程可用传递函数概念说明;切削过程本身能引起某种交变切削力,而振动系统能通过这种力的变化,从不具备交变特性的能源中周期性的获得补充能量,从而维持住这个振动。
机械加工中机械振动的原因解析与应对

机械加工中机械振动的原因解析与应对随着工业技术的不断发展,机械加工已成为现代生产中不可或缺的重要环节。
然而在机械加工过程中,经常会遇到机械振动的问题,这不仅会影响加工质量,还有可能引发安全事故。
了解机械振动的原因和有效应对是非常重要的。
一、机械振动的原因解析1.不稳定的加工条件在机械加工过程中,如果加工条件不稳定,比如切削速度、切削深度、进给速度等参数没有得到合理控制,就会引起机床工作状态的不稳定,从而产生振动。
2.机床结构设计不合理机床是机械加工的主要设备,如果机床的结构设计不合理,会导致刚性不足、固定件松动等问题,使得在加工过程中产生振动。
3.切削刀具磨损切削刀具是机械加工中常用的工具,如果刀具磨损严重或者安装不良,就会引起加工过程中的振动。
4.工件材料变形在加工过程中,由于工件材料自身性能的变化,也有可能引起机械振动。
5.进给系统问题进给系统的性能不稳定、传动链条出现松动等问题,会导致机床在工作时的振动。
刀具在加工时,间歇切削会引起刀具的振动,影响加工质量。
二、机械振动的应对措施1.合理选择切削工艺参数在机床的结构设计上,要注重刚性的设计和加强工装的固定,确保机床在加工过程中稳定性。
加强机床的维护保养工作,及时发现并解决机床结构问题。
3.切削刀具的选择和维护合理选择切削刀具,并确保刀具的安装正确、刃磨合适,定期进行刀具的维护和更换工作。
选择质量稳定的工件材料,对材料性能进行精密测试和处理,以减少因材料变形引起的机械振动。
对进给系统进行定期的检查和维护工作,确保传动链条、导轨等部件的稳定性和耐磨性。
6.刀具间歇切削的解决方法对于刀具间歇切削引起的问题,可以采用提高刀具速度、增加刀具的刚度等方法来减少刀具的振动。
三、结语在机械加工中,机械振动是一个常见问题,如果不能得到及时合理的处理,会对加工质量和安全性造成很大影响。
加强对机械振动原因的分析和应对措施的研究非常重要。
通过合理选择加工条件、加强机床结构设计和维护、切削刀具的选择和维护、工件材料处理、进给系统的维护以及解决刀具间歇切削等措施,可以有效减少机械振动的发生,提高机械加工的质量和效率。
机械加工中的振动类型分类

了解振动要先从振动的类型开始,振动从不同的角度来划分,可以分为很多类型,有强迫型、自激型、自由型等,每种类型都有各自的特点,都对机械生产过程会产生不同的影响,下面我们就具体来看看吧。
1自激振动的概念及类型分析
自激振动是振动的另一种类型,自激振动从某种意义上说是一种自发振动。
因为这种振动是不受外力干扰,而自动引起的自发性振动,在振动的过程中,受交变力的影响会引起持续的运动,持续且有规律性,机械设备在工作时,齿轮和部件相互交织在一起,而产生一定的磨擦导致这种自激振动产生。
2自由振动的概念及类型分析
振动中还有最后一种类型,是自由振动类型。
这种振动类型对机械加工的影响相对不是很大。
由于机械运转过程中,激振力对系统不断作用,从而机械设备的平衡就被破坏,我们把能对激振力,进行约束的方式称为自由振动。
3强迫振动的概念及类型分析
强迫振动类型,是在外力有规律的作用下产生的振动。
例如,在我们经常见到的,削、切、磨的过程中,由于机械设备的带动,像电动机械,砂轮、皮带等的带动下,都会产生振动。
这其中因为皮带或长或短,或厚或薄,油泵不稳定等因素的影响,从不同程度上都会促使振动的发生,这种振动现象就是强迫振动,这种振动会对加工产品的精密准确度产生影响,
从而影响加工产品的圆度、加工产品的粗糙度等。
一些回转动的机械设备,振动对回转精度也会产生影响。
机械加工中机械振动的原因解析与应对

机械加工中机械振动的原因解析与应对
机械加工中的机械振动指的是机器在运行过程中的震动和共振现象。
机械振动不仅会影响产品的加工精度和质量,还会对机器本身造成损伤,因此必须引起足够的重视。
以下是机械振动的原因解析与应对措施。
一、机械振动的原因
1.不平衡:机械零件中存在不平衡现象时,发动机转动时会由于离心力产生横向或纵向的振动。
2.共振:当机器设备的固有频率与强制振动频率接近或相等时,就会出现共振现象,引起机器的强烈振动。
3.摩擦和磨损:机械零件的摩擦和磨损会导致运动不平稳,引起机器的振动。
4.不稳定结构:机器结构不够稳定,机械零件的振动会自我放大。
5.加工精度:由于零件加工误差、装配不良等原因,会导致机械零件在运行时振动加剧。
二、机械振动的应对措施
1.动平衡处理:对于不平衡现象严重的零件,应采取动平衡处理,通过在转子上安装调节重量来消除不平衡,降低振动的影响。
2.增加阻尼:在机械设备中增加阻尼器,可以有效地减小机械振动的幅度和频率。
3.改变固有频率:对于因共振引起的振动,可以通过改变机器的结构和材料,改变固有频率,避免共振的出现。
4.加强润滑:保持机器设备的良好润滑状态,减少磨损和摩擦,可以降低机械振动的程度。
5.改善加工质量:严格控制零件加工误差,加强装配质量,提高机器的运行精度,从而减轻机械振动的影响。
综上所述,机械振动是机械加工中必须面对的一个问题。
只有全方位的应对措施,才能保证机器的正常运行,同时也能保证产品加工的质量和精度。
补充:机械加工过程中的振动
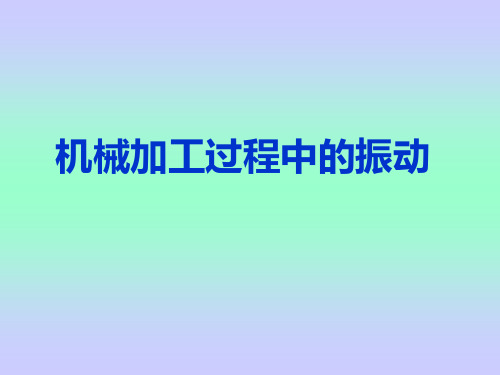
机械加工过程中产生的振动,是一种十 分有害的现象,这是因为:
1)刀具相对于工件振动会使加工表面 产生波纹,这将严重影响零件的使用性能。
2)刀具相对于工件振动,切削截面、 切削角度等将随之发生周期性变化,工艺系 统将承受动态载荷的作用,刀具易于磨损 (有时甚至崩刃),机床的连接特性会受到 破坏,严重时甚至使切削加工无法进行。
再生型切削颤振:这种由于切削厚度变化效 应(简称再生效应)而引起的自激振动称为再 生型切削颤振。
图4-49 再生型颤振的产生过程
切削过程一般都是部分地或完全地在有 振纹(波纹)的表面上进行的,车削、铣削、 刨削、钻削、磨削等均不例外,由振纹再生 效应引发的再生型切削颤振是机床切削的主 要形态。
产生再生型颤振的条件:
3)为了避免发生振动或减小振动,有 时不得不降低切削用量,致使机床、刀具的 工作性能得不到充分发挥,限制了生产效率 的提高。
综上分析可知,机械加工中的振动对于 加工质量和生产效率都有很大影响,须采取 措施控制振动。
一、机械加工过程中的强迫振动 强迫振动:机械加工过程中的强迫振动
是指在外界周期性于扰力的持续作用下,振 动系统受迫产生的振动。
机械加工过程中的强迫振动与一般机械 振动中的强迫振动没有本质上的区别。机械 加工过程中的强迫振动的频率与干扰力的频 率相同或是其整数倍;当干扰力的频率接近 或等于工艺系统某一薄弱环节固有频率时, 系统将产生共振。
强迫振动的振源有来自于机床内部的机 内振源和来自机床外部的机外振源。
机外振源甚多,但它们都是通过地基传给 机床的,可以通过加设隔振地基来隔离外部 振源,消除其影响。
2.增大工艺系统的阻尼 增大工艺系统中的阻尼,可通过多种方 法实现。例如,使用高内阻材料制造零件, 增加运动件的相对摩擦,在床身、立柱的封 闭内腔中充填型砂,在主振方向安装阻振器 等。 (三)采用减振装置 常用的减振装置有动力式减振器、摩擦 式减振器和冲击式减振器等三种类型。
机械加工过程中振动产生的原因

机械加工过程中振动产生的原因2.1自然振动由于机械的构造非常复杂,在通电之后,机械会受到电力驱使进行运作。
由于机械内部的机械零部件非常多,在使用过程中机械零件急速运转,不同零件受空气阻力,进而产生振动。
可以说,自然振动是机械运转中不可避免的.振动问题,也是最常见、原理最为简单的振动类型。
同时,自然振动还包括外部因素影响,生产地不平、风力因素等影响。
通常情况下,机械各个运作零件都有一个磨合期,在刚刚接通电流时会产生明显振动,随着不同零件正常运转,起振动力机会逐渐削弱。
总之,自然振动是受技术、环境的影响,是不可避免的振动问题,对机械整体运作不会产生明显影响。
2.2自激振动有关调查研究显示,自然振动虽然是一种不可控问题,但如果不加以限制即会产生自激振动。
自激振动相比自然振动来说,就会对机械主体产生一定的伤害,轻则运作零部件松动、重则造成机械短路烧毁电线以及零件破损。
自激振动即是机械主体颤振,机械在正常加工中出现高频率振动,严重影响工业生产。
机械加工产生颤动的原因主要表现在以下几点:(1)机械在加工过程中,由于加工主体硬度突然变化,刀具运作频率突然改变,进而发生刀崩问题后,即会因为内部零件运作不协调而产生自激振动。
(2)机械中的各个零部件在生产中,由于刀具与零件之间契合度不足或生产规格不规范,而产生运作冲突,进而产生自激振动。
(3)机械刀具质量不过关,刚性较差,在生产过程中刀杆振动,进而带动机械整体振动。
(4)在机械生产过程中,由于生产刀具与产品生产规格相冲突,导致切削量无法满足标准,进而出现自激振动。
总体来说自激振动主要是由机械内部因素所引起的问题,主要是机械刀具或零部件之间的问题而产生的自激振动。
但是在自激振动中,振动周期会出现一定变化。
2.3强迫振动强迫振动与自激振动不同,强迫振动通常受外界因素与内部因素所产生的振动问题。
其内部因素主要是指:机械加工生产中,会由于机械各个部门零件所产生的离心振动,继而导致机械整体振动。
- 1、下载文档前请自行甄别文档内容的完整性,平台不提供额外的编辑、内容补充、找答案等附加服务。
- 2、"仅部分预览"的文档,不可在线预览部分如存在完整性等问题,可反馈申请退款(可完整预览的文档不适用该条件!)。
- 3、如文档侵犯您的权益,请联系客服反馈,我们会尽快为您处理(人工客服工作时间:9:00-18:30)。
再生型切削颤振:这种由于切削厚度变化效 应(简称再生效应)而引起的自激振动称为再 生型切削颤振。
图4-49 再生型颤振的产生过程
切削过程一般都是部分地或完全地在有 振纹(波纹)的表面上进行的,车削、铣削、 刨削、钻削、磨削等均不例外,由振纹再生 效应引发的再生型切削颤振是机床切削的主 要形态。
2.消除或减弱产生自激振动的条件 (1)减小重叠系数 再生型颤振是由于 在有波纹的表面上进行切削引起的,如果本 转(次)切削不与前转(次)切削振纹相重 叠,就不会有再生型颤振发生。重叠系数越 小,就越不容易产生再生型颤振。重叠系数 值大小取决于加工方式、刀具的几何形状及 切削用量等。适当增大刀具的主偏角和进给 量,均可使重叠系数减小。
综上分析可知,机械加工中的振动对于 加工质量和生产效率都有很大影响,须采取 措施控制振动。
一、机械加工过程中的强迫振动 强迫振动:机械加工过程中的强迫振动
是指在外界周期性于扰力的持续作用下,振 动系统受迫产生的振动。
机械加工过程中的强迫振动与一般机械 振动中的强迫振动没有本质上的区别。机械 加工过程中的强迫振动的频率与干扰力的频 率相同或是其整数倍;当干扰力的频率接近 或等于工艺系统某一薄弱环节固有频率时, 系统将产生共振。
2)刀具相对于工件振动,切削截面、 切削角度等将随之发生周期性变化,工艺系 统将承受动态载荷的作用,刀具易于磨损 (有时甚至崩刃),机床的连接特性会受到 破坏,严重时甚至使切削加工无法进行。
3)为了避免发生振动或减小振动,有 时不得不降低切削用量,致使机床、刀具的 工作性能得不到充分发挥,限制了生产效率 的提高。
绩80% ❖ 授课教师:赵斌(机电工程学院) ❖ 联系方式(手机):18203671508 ❖ 电子邮箱:zhaobin978@ ❖ QQ:49588976
第五节 机械加工过程中的振动
机械加工过程中产生的振动,是一种十 分有害的现象,这是因为:
1)刀具相对于工件振动会使加工表面 产生波纹,这将严重影响零件的使用性能。
❖ 选用教材:机械制造技术基础.于骏一,邹青主编.机械工业出 版社
❖ 参考书: 1. 谢家赢.机械制造技术.机械工业出版社 2. 冯之敬主编.《机械制造工程原理》. 清华大学出版社 3. 张福润 徐鸿本 刘延林.《机械制造技术基础》.华中科技
大学出版社 4. 卢秉恒主编.《机械制造技术基础》.机械工业出版社 5. 杨叔子主编.《机械制造技术基础》.机械工业出版社 ❖ 考核方式:平时成绩(平时、作业、论文)的比例20%,期末成
强迫振动的振源有来自于机床内部的机 内振源和来自机床外部的机外振源。机外振 源甚多,但它们都是通过地基传给机床的, 可以通过加设隔振地基来隔离外部振源,消 除其影响。机内振源主要有:机床上的带轮、 卡盘或砂轮等高速回转零件因旋转不平衡引 起的振动;机床传动机构的缺陷引起的振动; 液压传动系统压力脉动引起的振动;由于断 续切削引起的振动等。
效地提高机床加工系统的稳定性。提高各结 合面的接触刚度,对主轴支承施加预载荷, 对刚性较差的工件增加辅助支承等都可以提 高工艺系统的刚度。
2.增大工艺系统的阻尼 增大工艺系统中的阻尼,可通过多种方 法实现。例如,使用高内阻材料制造零件, 增加运动件的相对摩擦,在床身、立柱的封 闭内腔中充填型砂,在主振方向安装阻振器 等。 (三)采用减振装置 常用的减振装置有动力式减振器、摩擦 式减振器和冲击式减振器等三种类型。
如果确认机械加工过程中发生的是强迫 振动,就要设法查找振源,以便消除振源或 减小振源对加工过程的影响。
二、机械加工过程中的自激振动(颤振) 1.机械加工过程中的自激振动 与强迫振动相比,自激振动具有以下特
征: l)机械加工中的自激振动是指在没有
周期性外力(相对于切削过程而言)干扰下 产生的振动运动。
重叠系数:
(2)减小切削刚度 减小切削刚度可以 减小切削力,可以降低切削厚度变化效应 (再生效应)和振型耦合效应的作用。改善 工件材料的可加工性、增大前角、增大主偏 角和适当提高进给量等,均可使切削刚度下 降。
(3)合理布置振动系统小刚度主轴的位 置。
(二)改善工艺系统的动态特性 1.提高工艺系统刚度 提高工艺系统薄弱环节的刚度,可以有
2.振型耦合原理 实际振动系统一般都是多自由度系统。
四、控制机械加工振动的途径 (一)消除或减弱产生振动的条件 1.消除或减弱产生强迫振动的条件 (1)消除或减小内部振源 机床上的高
速回转零件必须满足动平衡要求;提高传动 元件及传动装置的制造精度和装配精度,保 证传动平稳;使动力源与机床本体分离。
(2)调整振源的频率 通过改变传动比, 使可能引起强迫振动的振源频率远离机机床加 工系统薄弱环节的固有频率,避免产生共振。
(3)采取隔振措施 使振源产生的部分振 动被隔振装置所隔离或吸收。隔振方法有两种, 一种是主动隔振,阻止机内振源通过地基外传; 另一种是被动隔振,阻止机外干扰力通过地基 传给机床。常用的隔振材料有橡皮、金属弹簧、 空气弹簧、矿渣棉、木屑等。
2)自激振动的频率接近于系统某一薄 弱振型的固有频率。
三、自激振动的激振机理 1.振纹再生原理 在刀具进行切削的过程中,若受到一个瞬
时的偶然扰动力的作用,刀具与工件便会产生 相对振动(属自由振动),振动的幅值将因系 统阻尼的存在而逐渐衰减。但该振动会在已加 工表面上留下一段振纹。当工件转过一转后, 刀具便会在留有振纹的表面上进行切削,切削 厚度时大时小,这就有动态切削力产生。如果 机床加工系统满足产生自激振动的条件,振动 便会进一步发展到持续的振动状态。
产生再生型颤振的条件,一般说,本转 (次)切削的振纹与前转(次)切削的振纹 总不会完全同步,它们在相位上有一个差值。 设本转(次)切削的振动运动为:
yt An cost
则上转(次)切削的振动运动为
yt T An1 cost
式中 T-工件转一转的时间;
-振动源频率;
An -本转(次)切削的振动振幅; An1 -上转(次)切削的振动幅值。