热管技术在荒煤气余热回收上的应用
热管技术在荒煤气余热回收上的应用
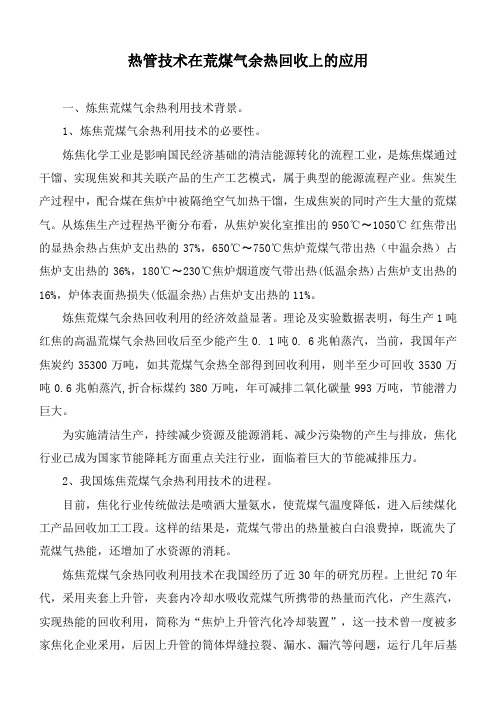
热管技术在荒煤气余热回收上的应用一、炼焦荒煤气余热利用技术背景。
1、炼焦荒煤气余热利用技术的必要性。
炼焦化学工业是影响国民经济基础的清洁能源转化的流程工业,是炼焦煤通过干馏、实现焦炭和其关联产品的生产工艺模式,属于典型的能源流程产业。
焦炭生产过程中,配合煤在焦炉中被隔绝空气加热干馏,生成焦炭的同时产生大量的荒煤气。
从炼焦生产过程热平衡分布看,从焦炉炭化室推出的950℃〜1050℃红焦带出的显热余热占焦炉支出热的37%,650℃〜750℃焦炉荒煤气带出热(中温佘热)占焦炉支出热的36%,180℃〜230℃焦炉烟道废气带出热(低温余热)占焦炉支出热的16%,炉体表面热损失(低温余热)占焦炉支出热的11%。
炼焦荒煤气余热回收利用的经济效益显著。
理论及实验数据表明,每生产1 吨红焦的高温荒煤气余热回收后至少能产生0. 1吨0. 6兆帕蒸汽,当前,我国年产焦炭约35300万吨,如其荒煤气余热全部得到回收利用,则半至少可回收3530万吨0.6兆帕蒸汽,折合标煤约380万吨,年可减排二氧化碳量993万吨,节能潜力巨大。
为实施清洁生产,持续减少资源及能源消耗、减少污染物的产生与排放,焦化行业已成为国家节能降耗方面重点关注行业,面临着巨大的节能减排压力。
2、我国炼焦荒煤气余热利用技术的进程。
目前,焦化行业传统做法是喷洒大量氨水,使荒煤气温度降低,进入后续煤化工产品回收加工工段。
这样的结果是,荒煤气带出的热量被白白浪费掉,既流失了荒煤气热能,还增加了水资源的消耗。
炼焦荒煤气余热冋收利用技术在我国经历了近30年的研究历程。
上世纪70年代,采用夹套上升管,夹套内冷却水吸收荒煤气所携带的热量而汽化,产生蒸汽,实现热能的回收利用,简称为“焦炉上升管汽化冷却装置”,这一技术曾一度被多家焦化企业釆用,后因上升管的筒体焊缝拉裂、漏水、漏汽等问题,运行几年后基本停用。
后来经过改进,有的企业把冷却水换成了导热油,导热油与高温荒煤气间接换热,被加热的高温导热油用于煤焦油蒸馏、干燥入炉煤、蒸氨等。
热管在工业废热和余热回收中的应用
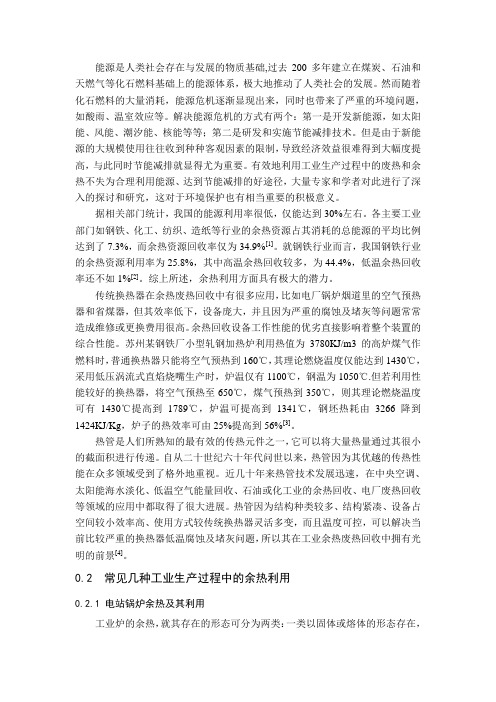
能源是人类社会存在与发展的物质基础,过去200多年建立在煤炭、石油和天燃气等化石燃料基础上的能源体系,极大地推动了人类社会的发展。
然而随着化石燃料的大量消耗,能源危机逐渐显现出来,同时也带来了严重的环境问题,如酸雨、温室效应等。
解决能源危机的方式有两个:第一是开发新能源,如太阳能、风能、潮汐能、核能等等;第二是研发和实施节能减排技术。
但是由于新能源的大规模使用往往收到种种客观因素的限制,导致经济效益很难得到大幅度提高,与此同时节能减排就显得尤为重要。
有效地利用工业生产过程中的废热和余热不失为合理利用能源、达到节能减排的好途径,大量专家和学者对此进行了深入的探讨和研究,这对于环境保护也有相当重要的积极意义。
据相关部门统计,我国的能源利用率很低,仅能达到30%左右。
各主要工业部门如钢铁、化工、纺织、造纸等行业的余热资源占其消耗的总能源的平均比例达到了7.3%,而余热资源回收率仅为34.9%[1]。
就钢铁行业而言,我国钢铁行业的余热资源利用率为25.8%,其中高温余热回收较多,为44.4%,低温余热回收率还不如1%[2]。
综上所述,余热利用方面具有极大的潜力。
传统换热器在余热废热回收中有很多应用,比如电厂锅炉烟道里的空气预热器和省煤器,但其效率低下,设备庞大,并且因为严重的腐蚀及堵灰等问题常常造成维修或更换费用很高。
余热回收设备工作性能的优劣直接影响着整个装置的综合性能。
苏州某钢铁厂小型轧钢加热炉利用热值为3780KJ/m3的高炉煤气作燃料时,普通换热器只能将空气预热到160℃,其理论燃烧温度仅能达到1430℃,采用低压涡流式直焰烧嘴生产时,炉温仅有1100℃,钢温为1050℃.但若利用性能较好的换热器,将空气预热至650℃,煤气预热到350℃,则其理论燃烧温度可有1430℃提高到1789℃,炉温可提高到1341℃,钢坯热耗由3266降到1424KJ/Kg,炉子的热效率可由25%提高到56%[3]。
热管是人们所熟知的最有效的传热元件之一,它可以将大量热量通过其很小的截面积进行传递。
热管换热器在烟道气余热回收中的应用_刘纪福
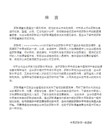
热水器遇到的主要危险是露点腐蚀,因其壁温
太低;而热管余热锅炉遇到的主要问题是传热
温差过低,管子根数过多,使其经济性和投资回
收年限加长;而热管空气预热器基本上能满足
各项要求。所以,对于低温烟气的余热回收,采
范围内工作,这就要求相应改变热管的工质,遗
憾的是,在200一500℃的温度范围内,除了水
之外,目前尚没有非常理想的工质可供大规模
地选用。这还是一个正在研究的课题。
3.露点腐蚀在烟道气中总会含有一定量
的硫酸蒸气,当热管的表面温度低于硫酸蒸气
的露点时,硫酸蒸气将在壁面上凝结成液体(硫
酸)而形成对壁面的腐蚀。称为露点腐蚀。露
现冷热流体的纯逆向流动,而一般的预热器则
不能。
(3)结构紧凑。金属消耗量少,占地面积
小o
(钓热管换热器的传热元件具有单根可拆
换性。
(5)热管换热器具有较高的抗露点腐蚀能
力。
(6)热管换热器中的冷热流体都是管外换
热,便于清理和维护。
热管换热器在烟道气余热回收中的应用主
要有三种:
最最高管内温度度3邪℃℃190℃℃210℃℃
月月曰启口合目J民J‘‘140℃℃110℃℃190七七,,曰.一、】旧月又,卒卒卒卒卒
管管壁沮度度度度度
换换热器型式式气一气气气一液液气~汽汽
(((((空气预热器)))(热水器)))(余热锅护)))
冷冷流体进出口口空气气水水蒸气气
温温度度0℃一250℃℃0℃一100℃℃250℃(40巴)))
传传热温差差420℃℃500℃℃29000
热热管根数数12000800012000
热管在锅炉烟气余热回收中的节能应用

热管在锅炉烟气余热回收中的节能应用
余热回收再利用,是将生产过程中排出的具有高于环境温度的物质所带有的热能,通过热管热回收装置进行回收并加以利用。
当高温烟气经过排烟入口进入换热设备中,热管中的工质受热发生相变变为气态,将烟气中的热量带走,同时烟气温度降低,工质在压力差作用下从蒸发端到冷凝端;当气态工质到达冷凝端后,释放热量再变成液态,在重力作用下回流到蒸发端,如此往复,就完成了热量的传递。
热管因为具有热流密度可变性,从而能够以较大的传热面积输入流量、以较小的冷却面输出热量,在热传递的过程中比较高效灵活。
热管在锅炉烟气余热回收中的节能应用主要体现在以下几个方面:
1. 高效吸收烟气余热:热管是一种高效传热元件,能够快速吸收烟气的余热,使烟气的温度降低,从而减少燃料的消耗。
2. 烟气处理:热管可以有效地处理烟气,降低烟气的排放温度和烟气中的有害物质,符合环保要求。
3. 节能改造:热管技术可以用于锅炉的节能改造,提高锅炉的热效率,减少能源的浪费。
4. 自动控制:热管回收系统可以与锅炉控制系统相结合,实现自动控制,保证锅炉的正常运行和能源的有效利用。
5. 减少环境污染:热管技术可以有效地气中的余热,减少能源的浪费和废气的排放,降低环境污染。
总的来说,热管在锅炉烟气余热回收中的应用,能够提高锅炉的热效率,减少能源的浪费和废气的排放,实现节能减排的目标,符合环保要求和社会经济发展的需要。
热管及其换热器在烟气余热回收中的应用_王斌斌
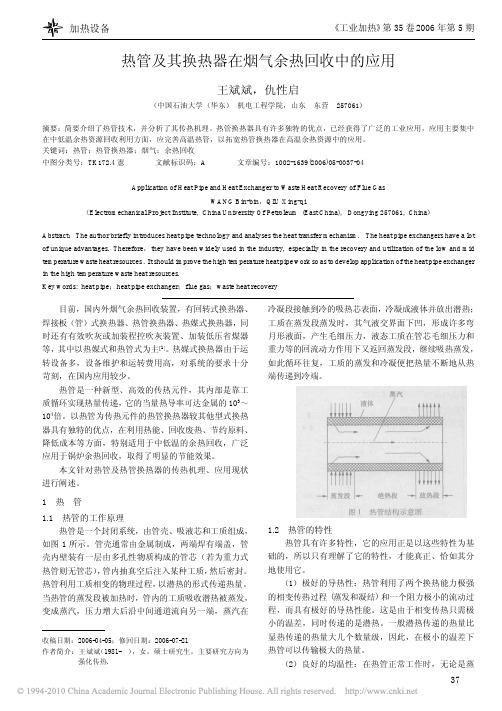
利用热管能够方便地在热源与冷源间实现热传递, 把 若干支路热管组装成一体,中间用隔板把热管的蒸发段 和凝结段隔开,形成了冷、热介质的流道,把热源中的 热量源源不断地传给冷源,这种热管元件的组装体就是 热管换热器。 典型的热管换热器,其外形一般为长方体,主要部 件为热管管束、外壳、隔板。热管的蒸发段和凝结段被
2 2.1
热管换热器的结构和基本特性 热管换热器的结构 热管换热器是常见的结构,如图 2 所示。
图2
热管换热器结构图
严格, 冷热流体不能相互污染的情况下进行热交换时, 热 管换热器自然是理想的换热设备。 (4) 热管换热器有较高的防积灰堵灰能力:热管是烟 气在管外壁流动横掠换热,烟气的扰动性加强。再加上 热管壁温高,管壁壁温高,管外始终呈干燥状态,因此, 也就不会结焦不易粘附烟灰, 因而它就能有效地防止堵塞。 (5) 热管换热器有较高的抗低温腐蚀能力:烟气进入 低温受热面后,其中的水蒸汽可能由于烟温降低或在接 触温度较低的受热面时发生凝结。烟气中水蒸汽开始凝
1= 1
ln
1
1 1 1 1
式中: 为烟气的放热量: =
38
加热设备
结的温度称为水露点。水露点一般比较低,所以一般不 易在低温受热面发生结露,但如果凝结时可能使受热面 金属产生氧腐蚀。 当燃用含硫燃料时,硫燃烧后形成二氧化硫,其中 一部分会进一步氧化成三氧化硫。三氧化硫与烟气中水 蒸汽结合成硫酸蒸汽。烟气中硫酸蒸汽的凝结温度称为 酸露点。它比水露点要高很多。烟气中三氧化硫含量愈 多,酸露点就愈高。烟气中硫酸蒸汽本身对受热面的工 作影响不大。但当它在壁温低于酸露点的受热面上凝结 下来时,就会对受热面金属产生严重腐蚀作用。这种由 于金属壁低于酸露点而引起的腐蚀称为低温腐蚀。强烈 的低温腐蚀通常发生在低温级空气预热器中空气和烟气 温度最低的区域。烟气对受热面低温腐蚀常用酸露点的 高低来表示。露点愈高,腐蚀范围愈广,腐蚀也愈严重。 其腐蚀速度与金属壁面温度有很大关系,如图 3 所示。 由图 3 可见,随着金属壁面温度的降低,出现了两 个严重腐蚀区和两个相对安全区。对于一定的煤种及运 行方式,腐蚀曲线也是一定的。对于一般的管式空气预 热器采用诸如提高排烟温度和热风再循环以及暖风机提 高入口风温等措施,可以避开第一个严重腐蚀区,但是, 第一个严重腐蚀区是难以避免的。而对于热管空气预热 器,在设计中,可根据锅炉工况特点调整热管加热段和 冷凝段的长度,以及调整低温处热管冷、热两段翅片的 间距、数量等办法来调整烟气侧与空气侧的热阻比,从 而达到控制热管壁温。使烟气侧壁温高于运行工况酸露 点温度,而避开硫酸蒸汽的结露。 所以 = 式中:
热管技术在余热回收上的应用

双良节能系统股份有限公司换热器事业部
双良节能系统股份有限公司换热器事业部
热管用途 热管
余热回收
保持温度
均
温
热管冷热两端都可 热管具有单向传热 以进行强化传热处 能力,可让物体保 理,比普通高效管 持一定温度。青藏 式换热器具有更大 高原铁路就应用了 的传热系数,往往 热管技术保持冻土 用于余热回收领域。 温度。
维护方便。模块化设计,在不影响生 产的情况下可更换热管。
双良节能系统股份有限公司换热器事业部
焦炉废气余热回收效益简单分析
以年产90万吨焦炭二联并列焦炉为例,烟气流量 220000Nm3/h,烟气温度250℃计算,效益收入如下:
已知: 蒸汽产量: 年生产时间: 煤气锅炉燃料消耗量: 煤气价格: 软水价格: 工业用电价格: 那么: 蒸汽总产量: 节约煤气量: 节约煤气效益: 煤气锅炉折旧: 总收益: 软水支出费用: 电费支出费用: 毛收益: 系统投资回收期: 11×7000=77000t 163×77000=12551000m3 12551000×1÷10000=1255.1万元/年 15万元/年 1255.1+15=1270.1万元/年 11×10×7000=77万元/年 200kW×7000×0.8=112万元/年 1270.1-77-112=1081.1万元/年 <2年 11t/h, 7000h 163m3/(t· h) 3 1元/m 软水10元/t 0.8元/度
双良节能系统股份有限公司换热器事业部
90万吨/年焦炉废气余热回收系统基本参数
焦炉产量 燃料 烟气 流量 温度 阻力 蒸汽 压力 产量 设备主体尺寸 设备主体重量 0.6MPa 11t/h 长9.4m×宽4m×高9m 174t 220000Nm3/h 进250℃,出162℃ 1100Pa 90万吨/年×2 焦炉自产煤气
热管在余热资源回收再利用中的作用

热管在余热资源回收再利用中的作用根据定义,余热是指受历史、技术、理念等因素的局限性,在已投运的工业企业耗能装置中,原始设计未被合理利用的显热和潜热。
它包括高温废气余热、冷却介质余热、废汽废水余热、高温产品和炉渣余热、化学反应余热、可燃废气废液和废料余热等。
余热回收利用是指将工业过程中产生的余热,通过一定的技术再次回收并重新利用。
余热回收的过程,其实也是将原本要排放到大气中的热能进行再次集成的过程。
通过余热回收再利用,可达到降低能源成本投入、减少碳排放,提高能源效率,增加对环境的保护。
1、余热的产生:在工业领域,余热资源是非常常见也是浪费严重的一种热资源。
余热的产生是伴随生产工序的进行而产生的,如烘干工序,在对物料进行烘干时,要将新空气进行加热到合适的温度后进行烘干。
在烘干过程中,物料中的湿气蒸发出来,空气含湿量增加,而新风的相对湿度较低,为保持烘干炉内空气的湿度,需要时时保持新风的进入。
有进入就要有排出,排出的空气温度要高与外界,如不加以回收利用,那这部分热能就白白的浪费了。
2、余热的回收要求:余热产生的形式其实是有很多的,如高温烟气、蒸汽、固体废热、液体废热等,产生的形式不同,在对余热进行回收时所使用的设备、技术也不同。
如当烟气中含尘量过大或具有腐蚀性物质时,就对余热回收技术和设备有了一定的要求,既要保障设备的正常运转,也要保障设备的使用寿命。
3、余热回收后的用途:余热回收后,可直接用于工序生产中,也可以用于生活中。
如在生产工序中,回收的余热可用于新风的预热,可以降低能源成本的投入;在生活中,回收的余热可用于暖气供暖、热水等使用中;可根据实际情况来使用。
热管技术,近几年来发展迅速,以热管技术为核心而制作的热管换热器,在诸多领域的余热回收中得到应用。
热管其内部为真空状态并充满工作介质。
在热管的两端,受热的一端为蒸发端,受冷的一端为冷凝端。
在工作时,当热管的一端与热流体接触(即蒸发端),管内工作介质吸热蒸发后,沿管流向冷凝端,蒸汽状态的工作介质在冷凝端遇冷放热,凝结为液体状态后,在管芯毛细作用下,回落到蒸发端。
热管式锅炉在烟气余热回收中的应用分析
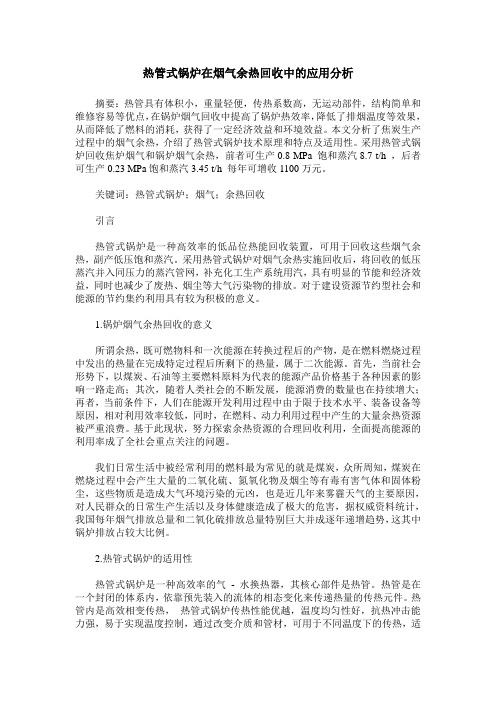
热管式锅炉在烟气余热回收中的应用分析摘要:热管具有体积小,重量轻便,传热系数高,无运动部件,结构简单和维修容易等优点,在锅炉烟气回收中提高了锅炉热效率,降低了排烟温度等效果,从而降低了燃料的消耗,获得了一定经济效益和环境效益。
本文分析了焦炭生产过程中的烟气余热,介绍了热管式锅炉技术原理和特点及适用性。
采用热管式锅炉回收焦炉烟气和锅炉烟气余热,前者可生产0.8 MPa 饱和蒸汽8.7 t/h ,后者可生产0.23 MPa饱和蒸汽3.45 t/h 每年可增收1100万元。
关键词:热管式锅炉;烟气;余热回收引言热管式锅炉是一种高效率的低品位热能回收装置,可用于回收这些烟气余热,副产低压饱和蒸汽。
采用热管式锅炉对烟气余热实施回收后,将回收的低压蒸汽并入同压力的蒸汽管网,补充化工生产系统用汽,具有明显的节能和经济效益,同时也减少了废热、烟尘等大气污染物的排放。
对于建设资源节约型社会和能源的节约集约利用具有较为积极的意义。
1.锅炉烟气余热回收的意义所谓余热,既可燃物料和一次能源在转换过程后的产物,是在燃料燃烧过程中发出的热量在完成特定过程后所剩下的热量,属于二次能源。
首先,当前社会形势下,以煤炭、石油等主要燃料原料为代表的能源产品价格基于各种因素的影响一路走高;其次,随着人类社会的不断发展,能源消费的数量也在持续增大;再者,当前条件下,人们在能源开发利用过程中由于限于技术水平、装备设备等原因,相对利用效率较低,同时,在燃料、动力利用过程中产生的大量余热资源被严重浪费。
基于此现状,努力探索余热资源的合理回收利用,全面提高能源的利用率成了全社会重点关注的问题。
我们日常生活中被经常利用的燃料最为常见的就是煤炭,众所周知,煤炭在燃烧过程中会产生大量的二氧化硫、氮氧化物及烟尘等有毒有害气体和固体粉尘,这些物质是造成大气环境污染的元凶,也是近几年来雾霾天气的主要原因,对人民群众的日常生产生活以及身体健康造成了极大的危害,据权威资料统计,我国每年烟气排放总量和二氧化硫排放总量特别巨大并成逐年递增趋势,这其中锅炉排放占较大比例。
- 1、下载文档前请自行甄别文档内容的完整性,平台不提供额外的编辑、内容补充、找答案等附加服务。
- 2、"仅部分预览"的文档,不可在线预览部分如存在完整性等问题,可反馈申请退款(可完整预览的文档不适用该条件!)。
- 3、如文档侵犯您的权益,请联系客服反馈,我们会尽快为您处理(人工客服工作时间:9:00-18:30)。
热管技术在荒煤气余热回收上的应用一、炼焦荒煤气余热利用技术背景。
1、炼焦荒煤气余热利用技术的必要性。
炼焦化学工业是影响国民经济基础的清洁能源转化的流程工业,是炼焦煤通过干馏、实现焦炭和其关联产品的生产工艺模式,属于典型的能源流程产业。
焦炭生产过程中,配合煤在焦炉中被隔绝空气加热干馏,生成焦炭的同时产生大量的荒煤气。
从炼焦生产过程热平衡分布看,从焦炉炭化室推出的950℃〜1050℃红焦带出的显热余热占焦炉支出热的37%,650℃〜750℃焦炉荒煤气带出热(中温佘热)占焦炉支出热的36%,180℃〜230℃焦炉烟道废气带出热(低温余热)占焦炉支出热的16%,炉体表面热损失(低温余热)占焦炉支出热的11%。
炼焦荒煤气余热回收利用的经济效益显著。
理论及实验数据表明,每生产1 吨红焦的高温荒煤气余热回收后至少能产生0. 1吨0. 6兆帕蒸汽,当前,我国年产焦炭约35300万吨,如其荒煤气余热全部得到回收利用,则半至少可回收3530万吨0.6兆帕蒸汽,折合标煤约380万吨,年可减排二氧化碳量993万吨,节能潜力巨大。
为实施清洁生产,持续减少资源及能源消耗、减少污染物的产生与排放,焦化行业已成为国家节能降耗方面重点关注行业,面临着巨大的节能减排压力。
2、我国炼焦荒煤气余热利用技术的进程。
目前,焦化行业传统做法是喷洒大量氨水,使荒煤气温度降低,进入后续煤化工产品回收加工工段。
这样的结果是,荒煤气带出的热量被白白浪费掉,既流失了荒煤气热能,还增加了水资源的消耗。
炼焦荒煤气余热冋收利用技术在我国经历了近30年的研究历程。
上世纪70年代,采用夹套上升管,夹套内冷却水吸收荒煤气所携带的热量而汽化,产生蒸汽,实现热能的回收利用,简称为“焦炉上升管汽化冷却装置”,这一技术曾一度被多家焦化企业釆用,后因上升管的筒体焊缝拉裂、漏水、漏汽等问题,运行几年后基本停用。
后来经过改进,有的企业把冷却水换成了导热油,导热油与高温荒煤气间接换热,被加热的高温导热油用于煤焦油蒸馏、干燥入炉煤、蒸氨等。
因导热油稳定性好,运行效果有了较大改善。
用热管回收荒煤气带出热量,效果也不错。
将管内水变成蒸汽,沿着热管上升加热管外的水产生蒸汽,单个上升管产蒸汽压力1.6兆帕,平均蒸汽流量66公斤/小时,热管换热后降至500℃。
冷却流程改进。
使脱硫贫液与高温荒煤气间接换热,脱硫贫液换热后通过闪蒸装置产生蒸汽,作为脱硫液再生热源,这种工艺可使年产200万吨焦炭企业年节约低压蒸汽26万吨,相当于回收利用了25%荒煤气带出热。
此外,我国焦化工作者还设计了用锅炉回收荒煤气带出热、用半导体温差发电技术回收荒煤气余热等方案和技术。
二、热管技术在荒煤气余热回收上的应用简介。
1、热管回收余热技术。
(1)热管技术是1963年美国LosAlamos国家实验室的G.M.Grover发明的一种称为“热管”的传热元件,它充分利用了热传导原理与致冷介质的快速热传递性质,透过热管将发热物体的热量迅速传递到热源外,其导热能力超过任何已知金属的导热能力。
热管技术目前已广泛应用于宇航、军工、钢铁、机械等行业。
(2)工作原理:热管是一种新型高效的传热元件,按较精确的定义应称之为“封闭的两相传热系统”,即在一个抽成真空的封闭的体系内,依赖装入内部的流体的相态变化(液态变为汽态和汽态变为液态)来传递热量的装置。
热管放在热源部分的称之为蒸发段(热端),放在冷却部分的称之为冷凝段(冷端)。
当蒸发段吸热把热量传递给工质后,工质吸热由液体变成汽体,发生相变,吸收汽化潜热。
在管内压差作用下,汽体携带潜热由蒸发段流到冷凝段,把热量传递给管外的冷流体,放出凝结潜热,管内工质又由汽体凝为液体,在重力作用下,又回到蒸发段,继续吸热汽化。
如此周而复始,将热量不断地由热流体传给冷流体。
(3)热管优点①金属、非金属材料本身的导热速率取决于材料的导热系数、温度梯度、正交于温度梯度的截面面积。
以金属银为例,其值为415W/m2٠K左右,经测定,热管的导热系数是银的几百倍到上千倍,故热管有热超导体之称。
②由于热管内的传热过程是相变过程,而且工质的纯度很高,因此热管内蒸汽温度基本上保持恒温,经测定:热管两端的温差不超过5℃,与其它传热元件相比,热管具有良好的等温性能。
③热管能适应的温度范围与热管的具体结构、采用的工作流体及热管的环境工作温度有关。
目前,热管能适应的温度范围一般为-200℃~2000℃,这也是其它传热元件所难以达到的。
(4)热管式余热回收装置①原理:热管式余热回收装置的核心部件是热管。
基本结构:热管蒸汽发生器是由若干根特殊的热管元件组合而成。
热管的受热段置于热流体风道内,热风横掠热管受热段,热管元件的放热段插在水—汽系统内。
由于热管的存在使得该水—汽系统的受热及循环完全和热源分离而独立存在于热流体的风道之外,水—汽系统不受热流体的直接冲刷。
工作原理:热流体的热量由热管传给水套内的饱和水(饱和水由下降管输入),并使其汽化,所产蒸汽(汽、水混合物)经蒸汽上升管达到汽包,经集中分离以后再经蒸汽主控阀输出(汽包内的水由104℃除氧水经水预热器加热至175℃后供给)。
这样由于热管不断将热量输入水套,通过外部汽—水管道的上升及下降完成基本的汽—水循环,达到将热流体降温,并转化为蒸汽的目的。
②优点:热管换热设备较常规换热设备更安全、可靠,可长期连续运行;传热效率高,启功速度快,热管的冷、热侧均可根据需要采用缠绕翅片来增加传热面积;有效的防止积灰,换热器设计时能够采用变截面形式,保证流体通过热管换热器时等流速流动,达到自清灰的目的;结构紧凑,占地面积小;热流密度可变性,热管可以独立改变蒸发段和冷凝段的加热面积,这样可以控制管壁温度以避免出现露点结灰或酸腐蚀。
(5)热管技术在荒煤气余热回收上的应用。
热管安装在荒煤气上升管内,整个装置包括热管换热器,热风引入设备、氨水喷淋器、气液分离罐以及循环水罐和水泵等。
荒煤气仍由上升管下部引入,通过热管换热器换热降温至500℃,然后用喷洒氨水冷却至80~85℃。
根据余热回收装置的工作温度范围,选用金属钾为工质,采取不锈钢丝网吸液芯附于热管内壁。
热管的蒸发段安装在上升管内,冷凝段安装在废热锅炉内,其位置略高于蒸发段。
通过以上工艺,热管技术在荒煤气余热回收方面取得了很好的应用。
2、热管技术在国内荒煤气余热利用方面的应用研究。
传统炼焦工艺:即炼焦煤由备煤车间送至煤塔,再由除尘装煤车装入碳化室内,煤料在碳化室内经过高温干馏成为焦炭,同时产生荒煤气(温度850-950℃、流量70000m3/h)。
汇集到碳化室顶部空间的荒煤气在经过桥管送至煤气净化工序的过程中,荒煤气在桥管内通过氨水喷洒进行冷却,以便荒煤气在煤气净化工序进行焦油的脱除。
采用氨水喷洒对荒煤气进行冷却的方式虽然能够迅速降低高温荒煤气温度,但该工艺流程比较复杂,同时荒煤气中所含有的大量热能在与氨水热交换过程中被冷却氨水带走,冷却后的氨水通过蒸发脱氨而后排放,在消耗大量氨水增加生产成本的同时,荒煤气余热资源无法回收而损失掉。
在本次焦炉荒煤气余热回收研讨与实验中,作了传热分析与模拟计算,并以此为依据进行了焦炉上升管热量回收实验系统与装置等设计,开展了329小时的试验,实验表明对焦炉荒煤气的余热回收,本项目所采用的方案基本是可行的。
(1)设计方案:我们设计了两套余热回收装置,第一种方案是高温热管荒煤气余热回收装置;第二种方案是分离式热管荒煤气余热回收装置。
①高温热管荒煤气余热回收方案本方案应用高温热管技术回收焦炉荒煤气余热,从炭化室出来的800℃左右的荒煤气进入上升管,通过辐射换热将热量传给高温钾热管,温度降至500℃左右离开上升管,上升管内的钾热管吸收辐射热,并将热量传给上升管外部的冷凝端,使联箱中的水汽化并放出热量。
联箱中的水汽化后通过汽水上升管进入锅炉,进行汽水分离,满足用户需求。
本方案优点:采用高温热管,能够保证热管壁温在荒煤气焦油露点之上,不会产生结焦问题;而且高温钾热管安全可靠,即使热管破坏,钾蒸汽量小,不会像水夹套那样导致整个汽包中的汽水混合物漏入炭化室,不会造成安全事故,能够保证焦炉的安全运行。
本方案缺点:高温热管造价相对较高。
②分离式热管荒煤气余热回收方案本方案应用分离式热管技术回收焦炉荒煤气余热,从炭化室出来的800℃左右的荒煤气进入上升管,通过辐射换热将热量传给炭钢—水热管,温度降至500℃左右离开上升管;上升管内的数根热管吸收辐射热,热管内的水蒸发成蒸汽,沿热管上升至上联箱汇集,然后一起通过汽水上升管送入汽包进行汽水分离,满足用户需求。
给水通过下降管送入下联箱,分配给各个热管。
本方案优点:采用分离式热管,布置方便,通过提高产汽压力,可以保证热管壁温在荒煤气焦油露点之上,不会产生结焦问题;分离式热管同高温热管一样,即使热管破坏,水蒸汽量小,不会像水夹套那样导致整个汽包中的汽水混合物漏入炭化室,不会造成事故,能够保证焦炉的安全运行。
此外,造价相对较低,经济合理。
本方案缺点:由于要防止荒煤气结焦,必须提高热管管壁温度和热管管内工作温度,这就必须提高热管管内蒸汽压力,而碳钢-水热管最高工作温度和承压能力都有一定限制,因此对于热管安全运行提出的条件较高。
综合考虑后确定采用第二方案。
(2)焦炉上升管热量回收实验系统与装置设计:热力系统:从炭化室出来的800℃左右的荒煤气仍由上升管下部引入,通过辐射换热将热量传给布置在上升管壳体内壁的分离式热管的受热端管束,温度降至500℃左右离开上升管,经氨水喷淋冷却后进入集气管;上升管内的受热端管束吸收辐射热后,管内的水蒸发成蒸汽,上升至管束的上联箱处汇集,然后一起通过汽水上升管送入布置在汽包内的分离式热管放热端,将汽包内的水加热并产生蒸汽;管束内的蒸汽冷凝成水后通过给水下降管送回至受热端管束的下联箱后分配给各个热管继续蒸发。
如此往复循环进行,从而完成热量由受热段到放热段的输送,达到回收荒煤气显热并产生蒸汽供用户使用的目的。
由于焦炉结构布置紧凑,没有太大的剩余空间来安置较大换热装置,本次实验也不宜对原焦炉进行较大的改造,故决定利用原焦炉上升管外壳体,将上升管内部耐火砖打掉,把分离式热管的受热端管束紧贴着上升管壳体内壁布置,将分离式热管的放热端管束浸入汽包液面以下,通过外联上升、下降管路实现受热端与放热端间的热量循环传输。
(3)实验过程及数据:在实验期间,为确保实验的安全性,同时为了防止本次实验给厂区附近带来噪音污染,将产汽压力调整为0.1MPa。
实验期间测定的部分数据如下:根据现场采集的数据可以看出,在实验初期,设备的运行状况与理论计算值基本吻合,实验进行了约3-4天后,荒煤气的出口温度较设计值偏高,换热管表面出现了焦油冷凝结焦的现象,导致换热效率下降。