注塑车间质量控制流程
注塑车间质量控制流程

注塑车间质量控制流程注塑车间质量控制流程概述注塑车间质量控制流程是指在注塑车间中,为了保证产品的质量,制定的一系列质量控制措施和流程。
该流程旨在规范注塑车间的操作,减少产品缺陷率和不合格品率,提高产品的质量稳定性和生产效率。
流程步骤步骤一:准备工作在开始注塑车间质量控制流程之前,需要进行一些准备工作,包括以下内容:- 确认注塑机设备的状态是否正常,是否具备开机条件。
- 确认注塑原料的充足性和质量问题。
- 检查模具设备的完好性和可用性。
步骤二:设备开机1. 打开注塑机电源,按照设备启动流程启动注塑机。
2. 检查注塑机温度控制装置是否正常工作,确保温度在正常范围内。
3. 注入注塑原料,并确保原料投入正常。
步骤三:质量控制1. 注塑车间质量控制人员在每个生产周期开始前,对注塑机进行检查,并记录相关数据。
2. 注塑机开始工作后,质量控制人员定期抽样检查产品尺寸和重量,并记录结果。
3. 使用工装夹具进行产品检查,确保产品的外观质量符合要求。
4. 定期进行产品外观检查,对产品进行分类评估,及时发现并解决质量问题。
5. 定期进行产品性能,以确保产品符合技术规范和客户要求。
6. 若发现质量问题,立即停止生产,排除质量问题,并记录问题产生原因和相应的改善措施。
步骤四:记录和分析1. 质量控制人员将每个生产周期的质量检查结果记录下来,并整理成报告。
2. 对于质量问题的分析,质量控制人员通过查看记录的质量数据和分析相关工艺参数,找出问题的原因,并提出相应的改善措施。
3. 质量控制人员根据记录和分析的结果,出相应的改进建议,并向注塑车间管理人员汇报。
步骤五:改进措施1. 注塑车间管理人员根据质量控制报告和改进建议,制定改进计划,并进行实施。
2. 针对不同的质量问题,采取相应的纠正措施和预防措施,防止类似问题发生。
注塑车间质量控制流程是一个保证产品质量的关键步骤,它能够帮助注塑车间避免质量问题,提高产品的合格率和质量稳定性。
注塑车间质量控制流程

注塑车间质量控制流程一、引言注塑车间是制造企业中至关重要的环节之一,质量控制流程的严谨性和有效性对产品质量的稳定性和客户满意度有着重要影响。
本文将详细介绍注塑车间质量控制流程,包括质量控制的目标、流程步骤、关键控制点以及质量数据分析等内容。
二、质量控制目标1. 提高产品的质量稳定性和一致性,确保产品符合客户要求。
2. 减少次品率和返工率,提高生产效率和产品利润率。
3. 降低客户投诉率,增强企业的品牌形象和市场竞争力。
三、质量控制流程步骤1. 原材料检验a. 根据产品要求,对原材料进行抽样检验,包括外观、尺寸、物理性能等指标。
b. 检验结果记录并与供应商进行反馈,及时处理不合格材料。
2. 注塑设备调试a. 根据产品要求,对注塑设备进行调试,确保设备运行稳定。
b. 确认注塑设备的参数设置,包括温度、压力、速度等。
3. 注塑模具检验a. 对注塑模具进行定期检查和维护,确保模具的完好性和准确性。
b. 检查模具尺寸、表面质量等指标,确保模具满足产品要求。
4. 注塑工艺控制a. 根据产品要求,设定注塑工艺参数,如注射速度、保压时间等。
b. 对注塑过程中的关键参数进行实时监控和调整,确保工艺参数的稳定性。
5. 注塑产品检验a. 从注塑生产线上抽样,对产品进行外观检验、尺寸测量等。
b. 对产品的物理性能进行测试,如强度、硬度等。
c. 检验结果记录并与产品要求进行比对,及时处理不合格产品。
6. 注塑产品包装a. 对合格产品进行包装,包括外包装和内包装的检查。
b. 根据客户要求,确保产品的标识、数量等信息准确无误。
四、关键控制点1. 原材料的质量检验是质量控制的第一道关卡,确保注塑过程中使用的原材料符合要求。
2. 注塑设备的调试和维护是保证注塑工艺稳定性的关键,设备运行异常会直接影响产品质量。
3. 注塑模具的检验和维护是保证产品尺寸和外观质量的关键,模具损坏或不准确会导致产品缺陷。
4. 注塑工艺参数的控制是保证产品质量稳定性的关键,工艺参数的偏差会导致产品尺寸不一致或性能不达标。
注塑车间质量控制流程

注塑车间质量控制流程一、原料入库检验核对数量:对采购的原料进行数量清点,确保数量准确。
检查外观:观察原料有无明显的破损、污渍、杂质等不良现象。
性能测试:抽取部分原料进行物理性能测试,如拉伸强度、冲击强度等,确保符合生产要求。
记录存档:对入库原料的检验结果进行详细记录,并存档备查。
不合格处理:对不合格原料进行标识、隔离,并通知采购部门进行处理。
二、生产过程监控工艺参数监控:对注塑机的温度、压力、时间等工艺参数进行实时监控,确保在工艺范围内。
半成品检验:对生产的半成品进行外观、尺寸、性能等方面的检验,防止不良品流入下道工序。
过程记录:对生产过程中的关键参数、检验结果等进行详细记录,以便追溯和改进。
不良品处理:对生产过程中出现的不良品进行标识、隔离,并分析原因,采取措施防止再次发生。
监控结果反馈:定期将生产过程监控的结果反馈给相关部门,以便及时调整和优化生产过程。
三、产品出库检测抽样检验:按照规定的抽样方案对即将出库的产品进行抽样检验。
外观检查:对产品的外观进行详细检查,确保无明显缺陷。
性能测试:对产品的物理性能进行测试,如抗冲击、抗老化等性能。
不合格处理:对不合格产品进行标识、隔离,并进行返工或报废处理。
出库记录:对出库产品的数量、质量等信息进行详细记录,以便追溯。
四、设备维护与保养日常保养:定期对设备进行清洁、润滑、紧固等保养工作,确保设备正常运行。
定期检查:对设备的运行状态、磨损情况进行定期检查,及时发现并处理问题。
维修记录:对设备的维修、保养情况进行详细记录,以便分析设备状况和制定保养计划。
维修流程:制定详细的设备维修流程,确保维修工作顺利进行。
备件管理:对设备备件进行妥善保管,确保备件充足且无损坏。
五、环境与安全卫生环境:保持注塑车间的整洁卫生,防止产品受到污染。
安全防护:确保注塑车间具备完善的安全防护设施,如防爆、防火设施等。
安全生产:制定并执行安全生产规章制度,确保员工的人身安全和企业的财产安全。
注塑车间质量控制流程
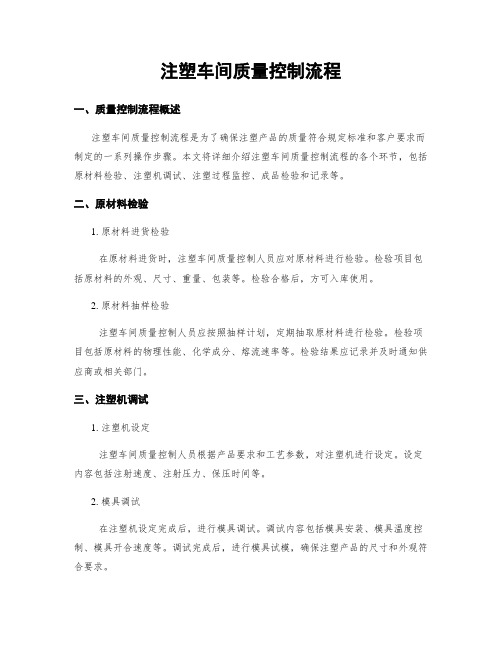
注塑车间质量控制流程一、质量控制流程概述注塑车间质量控制流程是为了确保注塑产品的质量符合规定标准和客户要求而制定的一系列操作步骤。
本文将详细介绍注塑车间质量控制流程的各个环节,包括原材料检验、注塑机调试、注塑过程监控、成品检验和记录等。
二、原材料检验1. 原材料进货检验在原材料进货时,注塑车间质量控制人员应对原材料进行检验。
检验项目包括原材料的外观、尺寸、重量、包装等。
检验合格后,方可入库使用。
2. 原材料抽样检验注塑车间质量控制人员应按照抽样计划,定期抽取原材料进行检验。
检验项目包括原材料的物理性能、化学成分、熔流速率等。
检验结果应记录并及时通知供应商或相关部门。
三、注塑机调试1. 注塑机设定注塑车间质量控制人员根据产品要求和工艺参数,对注塑机进行设定。
设定内容包括注射速度、注射压力、保压时间等。
2. 模具调试在注塑机设定完成后,进行模具调试。
调试内容包括模具安装、模具温度控制、模具开合速度等。
调试完成后,进行模具试模,确保注塑产品的尺寸和外观符合要求。
四、注塑过程监控1. 注塑工艺参数监控注塑车间质量控制人员应定期检查注塑机的工艺参数是否正常。
包括注射速度、注射压力、保压时间等。
如有异常,应及时调整。
2. 注塑产品外观检验注塑车间质量控制人员应定期对注塑产品进行外观检验。
检验项目包括产品的色泽、表面平整度、气泡、瑕疵等。
如发现问题,应及时调整注塑机的参数或模具。
五、成品检验1. 尺寸检验注塑车间质量控制人员应对注塑产品的尺寸进行检验。
检验项目包括长度、宽度、高度、壁厚等。
检验方法可以采用量具、投影仪等。
2. 功能性能检验注塑车间质量控制人员应对注塑产品的功能性能进行检验。
检验项目包括产品的承载能力、耐磨性、耐腐蚀性等。
检验方法可以采用试验机、实际使用等。
六、记录与报告1. 注塑过程记录注塑车间质量控制人员应对注塑过程进行记录,包括注塑机的设定参数、模具调试参数、注塑产品的外观检验结果等。
记录内容应真实可靠,以备后续分析和追溯。
注塑车间质量控制流程

注塑车间质量控制流程引言概述:注塑车间作为创造行业中一个重要的环节,其质量控制流程对于产品的质量和客户满意度具有至关重要的作用。
本文将从五个大点来阐述注塑车间质量控制流程,包括原材料检验、注塑工艺参数控制、模具检查、注塑产品检验和记录与分析。
正文内容:1. 原材料检验1.1 原材料外观检查:包括颜色、光泽度、表面是否有异物等。
1.2 原材料尺寸检查:对原材料的长度、宽度、厚度等进行测量,确保符合要求。
1.3 原材料性能检查:通过物理性能测试和化学成份分析,确保原材料的质量稳定。
2. 注塑工艺参数控制2.1 温度控制:确保注塑机的熔融温度、模具温度等参数在合适的范围内。
2.2 压力控制:调整注射压力、保压时间等参数,保证产品的成型质量。
2.3 注塑速度控制:根据产品的形状和尺寸调整注塑速度,避免产生瑕疵。
3. 模具检查3.1 模具外观检查:检查模具表面是否有损坏、划痕等问题。
3.2 模具尺寸检查:对模具的尺寸进行测量,确保其与产品要求一致。
3.3 模具装配检查:检查模具的装配是否正确,避免产生漏料、死料等问题。
4. 注塑产品检验4.1 外观检验:检查产品的表面光滑度、色差、划痕等问题。
4.2 尺寸检验:对产品的尺寸进行测量,确保其与设计要求一致。
4.3 功能性检验:根据产品的用途进行相应的功能性测试,确保产品的可靠性和稳定性。
5. 记录与分析5.1 记录数据:将原材料检验、注塑工艺参数、模具检查和产品检验的结果进行记录,建立数据档案。
5.2 分析数据:通过对数据的统计和分析,找出问题的原因,并采取相应的改进措施。
5.3 持续改进:根据数据分析的结果,对质量控制流程进行持续改进,提高产品的质量和生产效率。
总结:注塑车间的质量控制流程是保证产品质量的关键环节。
通过原材料检验、注塑工艺参数控制、模具检查、注塑产品检验和记录与分析,可以有效地发现和解决质量问题,提高产品的质量稳定性和客户满意度。
持续改进是质量控制流程的核心,惟独不断改进和优化,才干适应市场需求的变化,保持竞争力。
注塑车间质量控制流程

注塑车间质量控制流程1. 质量控制目标在注塑车间中,质量控制是非常重要的环节。
其主要目标是保证最终产品的质量符合标准要求,提高客户满意度,降低不良品率,提高生产效率。
2. 质量控制流程2.1 原材料检验在注塑车间开始生产之前,需要对原材料进行检验。
主要检查原料的质量是否合格,包括外观、尺寸、密度等。
只有经过检验合格的原材料才能被使用。
若发现原材料质量存在问题,应立即通知供应商,并选用其他合格的原材料。
2.2 模具安装和调试注塑车间的模具需要经过安装和调试,确保其能正常运行。
在安装过程中需要检查模具的结构是否完整,是否存在损坏或磨损的情况。
调试过程中需要调整模具的温度、压力等参数,以确保注塑产品的质量。
2.3 调整注塑机参数在正式生产之前,需要根据产品的要求调整注塑机的参数。
这包括注塑速度、注射压力、保压时间等。
通过不断调整和测试,使注塑机能够稳定地运行,并生产出符合质量要求的产品。
2.4 生产过程监控在注塑车间的生产过程中,需要对生产情况进行监控。
主要监控产品的尺寸、外观、密度等质量指标。
这可以通过使用专业的检测设备来实现,如投影仪、计量仪等。
若发现产品质量存在问题,及时调整生产参数,并通知相关人员进行处理。
2.5 产品检验生产出的产品需要进行全面的检验。
在注塑车间中,常用的检验方法有外观检查、尺寸测量、物理性能测试等。
只有通过检验合格的产品才能被送到下一个工序,否则需要进行返工或报废。
2.6 不良品处理在注塑车间中,不可避免地会产生一定数量的不良品。
及时处理这些不良品是非常重要的。
一般来说,不良品的处理包括返工、报废和分拣。
返工是指对不良品进行修复,使其符合质量要求;报废是指将不良品直接销毁;分拣是将不良品分类,以便进行进一步处理。
2.7 数据分析和改进通过对质量控制过程中的数据进行分析,可以发现一些潜在的问题,并采取相应的措施进行改进。
这可以包括改进生产参数、优化工艺流程、提供员工培训等。
通过不断地改进,注塑车间的质量控制可以不断提升。
注塑车间质量控制流程

注塑车间质量控制流程引言概述注塑车间是制造企业中非常重要的一个环节,质量控制是确保注塑产品质量稳定的关键。
本文将详细介绍注塑车间的质量控制流程,包括原材料检验、注塑加工过程控制、成品检验、异常处理和质量记录等五个部分。
一、原材料检验1.1 原材料外观检验在注塑车间进行原材料检验时,首先需要对原材料的外观进行检验。
检验员需要仔细观察原材料的颜色、光泽度、表面是否有明显的瑕疵等,确保原材料的外观符合要求。
1.2 原材料物理性能测试除了外观检验外,注塑车间还需要对原材料进行物理性能测试。
这些测试包括原材料的硬度、拉伸强度、熔融指数等。
通过这些测试,可以确保原材料的质量符合注塑产品的要求。
1.3 原材料化学成分分析原材料的化学成分对注塑产品的质量也有重要影响。
因此,在注塑车间的原材料检验流程中,还需要对原材料的化学成分进行分析。
常见的化学成分分析方法包括红外光谱分析、X射线荧光光谱分析等。
二、注塑加工过程控制2.1 注塑机参数控制在注塑加工过程中,注塑机的参数设置对产品质量起着至关重要的作用。
注塑车间需要确保注塑机的温度、压力、速度等参数设置合理,以确保产品的尺寸、外观等质量指标符合要求。
2.2 模具调试与维护模具是影响注塑产品质量的另一个重要因素。
注塑车间需要进行模具的调试和维护工作,确保模具的尺寸精度、表面光洁度等符合要求。
同时,还需要定期检查模具的磨损情况,及时进行维修或更换。
2.3 注塑工艺参数记录为了确保注塑加工过程的稳定性和可追溯性,注塑车间还需要记录注塑工艺参数。
这些参数包括注射速度、射胶压力、保压时间等。
通过记录这些参数,可以在出现质量问题时进行分析和排查。
三、成品检验3.1 外观检验成品的外观是判断产品质量的重要指标之一。
注塑车间需要对成品进行外观检验,包括检查产品的颜色、表面是否有瑕疵、是否有气泡等。
只有通过外观检验合格的产品才能进入下一道工序。
3.2 尺寸检验除了外观检验外,注塑车间还需要对成品的尺寸进行检验。
注塑车间质量控制流程
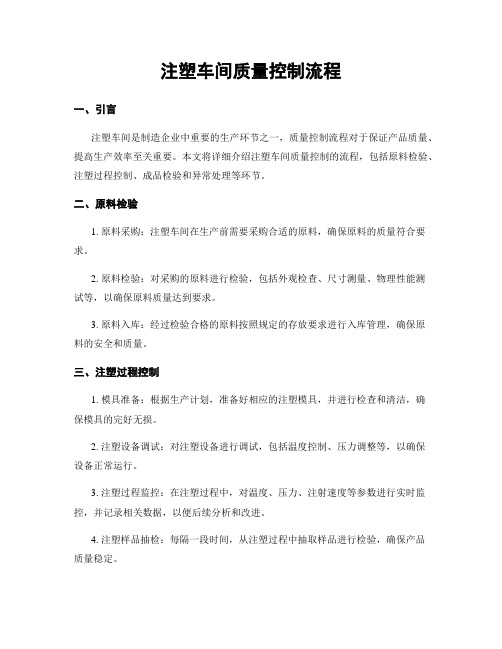
注塑车间质量控制流程一、引言注塑车间是制造企业中重要的生产环节之一,质量控制流程对于保证产品质量、提高生产效率至关重要。
本文将详细介绍注塑车间质量控制的流程,包括原料检验、注塑过程控制、成品检验和异常处理等环节。
二、原料检验1. 原料采购:注塑车间在生产前需要采购合适的原料,确保原料的质量符合要求。
2. 原料检验:对采购的原料进行检验,包括外观检查、尺寸测量、物理性能测试等,以确保原料质量达到要求。
3. 原料入库:经过检验合格的原料按照规定的存放要求进行入库管理,确保原料的安全和质量。
三、注塑过程控制1. 模具准备:根据生产计划,准备好相应的注塑模具,并进行检查和清洁,确保模具的完好无损。
2. 注塑设备调试:对注塑设备进行调试,包括温度控制、压力调整等,以确保设备正常运行。
3. 注塑过程监控:在注塑过程中,对温度、压力、注射速度等参数进行实时监控,并记录相关数据,以便后续分析和改进。
4. 注塑样品抽检:每隔一段时间,从注塑过程中抽取样品进行检验,确保产品质量稳定。
四、成品检验1. 外观检查:对注塑成品进行外观检查,包括表面平整度、色差、划痕等方面的评估,以确保产品外观符合要求。
2. 尺寸测量:对注塑成品进行尺寸测量,使用合适的测量工具和设备,确保产品尺寸精确度符合要求。
3. 功能测试:对注塑成品进行功能测试,验证产品的性能是否符合设计要求。
4. 批量抽检:从生产批次中抽取一定数量的样品进行检验,以确保产品质量的稳定性和一致性。
五、异常处理1. 异常记录:对于发现的异常情况,及时记录并进行分类、整理,以便后续分析和改进。
2. 异常分析:对异常情况进行原因分析,找出问题根源,并采取相应的纠正措施。
3. 纠正措施:根据异常分析结果,采取相应的纠正措施,包括调整参数、修复设备等,以确保异常不再发生。
4. 效果验证:对纠正措施的效果进行验证,确保问题得到解决并不再出现。
六、总结注塑车间质量控制流程是保证产品质量的重要环节,通过原料检验、注塑过程控制、成品检验和异常处理等环节的有效管理,可以提高产品质量稳定性,提高生产效率,并为客户提供高质量的产品。