注射成型的工艺参数
注射成型不锈钢粉末工艺参数

注射成型不锈钢粉末工艺参数
注射成型是一种常见的制造工艺,用于生产复杂形状的零件。
在注射成型不锈钢粉末的工艺中,有一些关键的参数需要考虑,包
括粉末特性、成型压力、温度控制和后续处理等。
以下是一些可能
需要考虑的工艺参数:
1. 粉末特性,粉末的粒度、形状和化学成分对成型过程至关重要。
粉末应具有适当的流动性和压实性,以确保成型零件的密实度
和表面质量。
2. 成型压力,成型压力是指注射成型机对粉末进行压实的力度。
压力的选择应该考虑到粉末的特性以及最终零件的要求。
过高的压
力可能导致粉末结构破坏,而过低的压力则可能导致零件密实度不足。
3. 注射温度,温度对于粉末的流动性和成型过程中的烧结效果
至关重要。
通常情况下,需要根据具体的不锈钢粉末类型和成型设
备来确定最佳的注射温度范围。
4. 模具设计,合适的模具设计可以确保成型零件的准确性和表
面质量。
模具的表面光洁度和耐磨性对最终产品的质量有重要影响。
5. 烧结工艺,注射成型后的零件通常需要进行烧结处理,以提
高密实度和力学性能。
烧结工艺参数包括烧结温度、保温时间和冷
却速度等。
总的来说,注射成型不锈钢粉末的工艺参数需要综合考虑材料
特性、设备性能和最终产品要求。
通过合理的工艺参数选择和精细
的工艺控制,可以实现高质量的不锈钢粉末注射成型零件的生产。
pa12注塑工艺参数
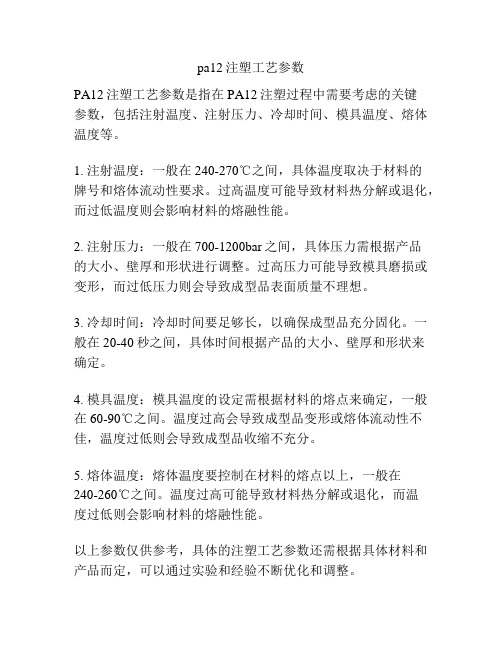
pa12注塑工艺参数
PA12注塑工艺参数是指在PA12注塑过程中需要考虑的关键
参数,包括注射温度、注射压力、冷却时间、模具温度、熔体温度等。
1. 注射温度:一般在240-270℃之间,具体温度取决于材料的
牌号和熔体流动性要求。
过高温度可能导致材料热分解或退化,而过低温度则会影响材料的熔融性能。
2. 注射压力:一般在700-1200bar之间,具体压力需根据产品
的大小、壁厚和形状进行调整。
过高压力可能导致模具磨损或变形,而过低压力则会导致成型品表面质量不理想。
3. 冷却时间:冷却时间要足够长,以确保成型品充分固化。
一般在20-40秒之间,具体时间根据产品的大小、壁厚和形状来
确定。
4. 模具温度:模具温度的设定需根据材料的熔点来确定,一般在60-90℃之间。
温度过高会导致成型品变形或熔体流动性不佳,温度过低则会导致成型品收缩不充分。
5. 熔体温度:熔体温度要控制在材料的熔点以上,一般在
240-260℃之间。
温度过高可能导致材料热分解或退化,而温
度过低则会影响材料的熔融性能。
以上参数仅供参考,具体的注塑工艺参数还需根据具体材料和产品而定,可以通过实验和经验不断优化和调整。
常用注塑工艺参数

常用注塑工艺参数注塑工艺参数是指在注塑成型过程中需要设置的各项参数,包括料筒温度、注塑压力、注射速度、保压时间、冷却时间等。
这些参数的设置将直接影响到注塑成型的质量和效率。
下面是一些常用的注塑工艺参数。
1.料筒温度:注塑过程中需保持一定的料筒温度,一般分为上料区、加热区和冷却区。
上料区用于将塑料原料加热至熔融状态,一般设置较低的温度,避免原料在上料过程中过度熔化或变质。
加热区用于将熔融状态的塑料加热至合适的注射温度,一般设置较高的温度。
冷却区用于降低热塑性塑料的温度,避免注射后的产品变形或变色。
2.注塑压力:注塑压力是指注射机在注塑成型过程中对塑料熔融物体所施加的压力。
注塑压力既影响塑料的熔融和注射速度,也影响充填过程中的背压。
一般情况下,注塑压力应根据产品的尺寸、结构和塑料的性质进行调整,以保证产品的充填性能和尺寸精度。
3.注射速度:注射速度是指注射机将塑料熔融物体注射到模具中的速度。
注射速度的快慢将直接影响到产品的充填性能和尺寸精度。
一般情况下,注射速度应根据产品的尺寸、壁厚和注塑机的规格进行调整,以保证产品的充填性能和表面质量。
4.保压时间:保压时间是指在注射和充填完成后,继续对模具施加一定的保压力和时间,使产品保持充填状态直到冷却和固化完全。
保压时间一般根据产品的尺寸、壁厚和注塑机的规格进行调整,以保证产品的密实度和尺寸精度。
5.冷却时间:冷却时间是指产品在模具中冷却和固化的时间。
冷却时间应根据产品的尺寸、壁厚和冷却条件进行调整,以保证产品冷却和固化完全,并避免产品变形和缩水现象的发生。
6.模具温度:模具温度是指模具加热系统对模具进行加热的温度。
模具温度应根据产品的尺寸、壁厚和塑料的性质进行调整,以保证产品的表面质量和尺寸精度。
7.射胶量:射胶量是指每次注射时注塑机所注入模具中的塑料量。
射胶量一般根据产品的尺寸、壁厚和注塑机的规格进行调整,以保证产品的充填性能和表面质量。
8.背压:背压是指在注射过程中,注塑机对塑料熔融物体施加的压力。
PVC电线电缆注射成型工艺参数
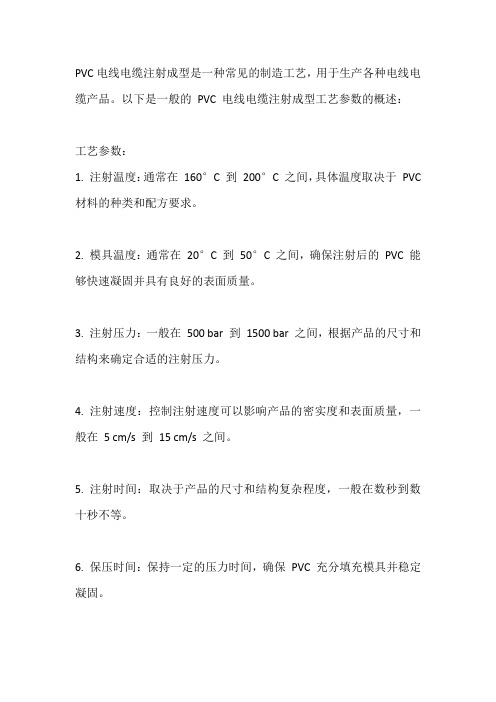
PVC电线电缆注射成型是一种常见的制造工艺,用于生产各种电线电缆产品。
以下是一般的PVC 电线电缆注射成型工艺参数的概述:
工艺参数:
1. 注射温度:通常在160°C 到200°C 之间,具体温度取决于PVC 材料的种类和配方要求。
2. 模具温度:通常在20°C 到50°C 之间,确保注射后的PVC 能够快速凝固并具有良好的表面质量。
3. 注射压力:一般在500 bar 到1500 bar 之间,根据产品的尺寸和结构来确定合适的注射压力。
4. 注射速度:控制注射速度可以影响产品的密实度和表面质量,一般在5 cm/s 到15 cm/s 之间。
5. 注射时间:取决于产品的尺寸和结构复杂程度,一般在数秒到数十秒不等。
6. 保压时间:保持一定的压力时间,确保PVC 充分填充模具并稳定凝固。
注意事项:
-确保PVC 材料质量符合要求,避免含水量过高或杂质过多。
-注射机的调试要求精准,确保稳定的注射温度、压力和速度。
-模具设计要合理,避免产生气泡、短注等缺陷。
-对注射设备进行定期维护和保养,确保设备运行稳定。
以上工艺参数和注意事项仅供参考,实际生产中还需根据具体产品的要求和生产情况进行调整和优化。
通过合理的工艺参数设置和严格的生产管理,可以生产出质量稳定、性能优良的PVC 电线电缆产品。
注射成型不锈钢粉末工艺参数
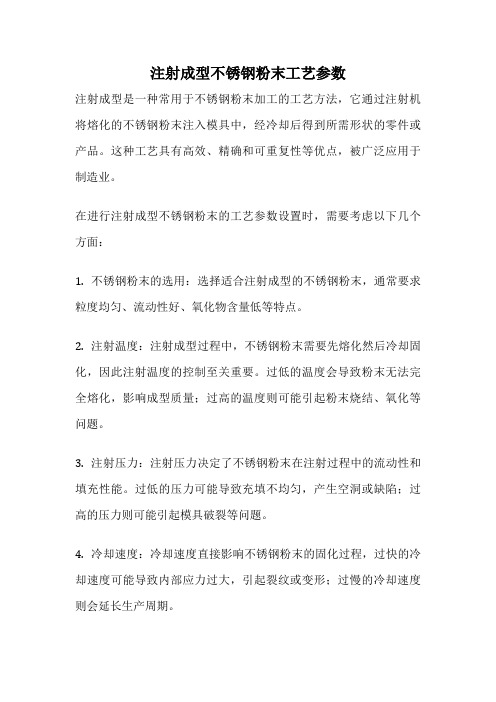
注射成型不锈钢粉末工艺参数
注射成型是一种常用于不锈钢粉末加工的工艺方法,它通过注射机将熔化的不锈钢粉末注入模具中,经冷却后得到所需形状的零件或产品。
这种工艺具有高效、精确和可重复性等优点,被广泛应用于制造业。
在进行注射成型不锈钢粉末的工艺参数设置时,需要考虑以下几个方面:
1. 不锈钢粉末的选用:选择适合注射成型的不锈钢粉末,通常要求粒度均匀、流动性好、氧化物含量低等特点。
2. 注射温度:注射成型过程中,不锈钢粉末需要先熔化然后冷却固化,因此注射温度的控制至关重要。
过低的温度会导致粉末无法完全熔化,影响成型质量;过高的温度则可能引起粉末烧结、氧化等问题。
3. 注射压力:注射压力决定了不锈钢粉末在注射过程中的流动性和填充性能。
过低的压力可能导致充填不均匀,产生空洞或缺陷;过高的压力则可能引起模具破裂等问题。
4. 冷却速度:冷却速度直接影响不锈钢粉末的固化过程,过快的冷却速度可能导致内部应力过大,引起裂纹或变形;过慢的冷却速度则会延长生产周期。
5. 模具温度:模具温度的控制可以影响注射成型的充填性能和成品的表面质量。
过低的温度可能导致粉末凝固不完全,产生毛刺或瑕疵;过高的温度则可能引起粉末烧结或氧化。
6. 固化时间:固化时间是指不锈钢粉末在模具中冷却固化所需的时间。
固化时间过短可能导致产品未完全固化,无法保持所需形状;固化时间过长则会增加生产周期。
在实际操作中,需要根据具体的不锈钢粉末材料和产品要求进行工艺参数的优化调整。
通过合理的工艺参数设置,可以实现不锈钢粉末注射成型工艺的高效、精确和稳定性,为制造业提供优质的不锈钢零件和产品。
注射成形工艺参数优化
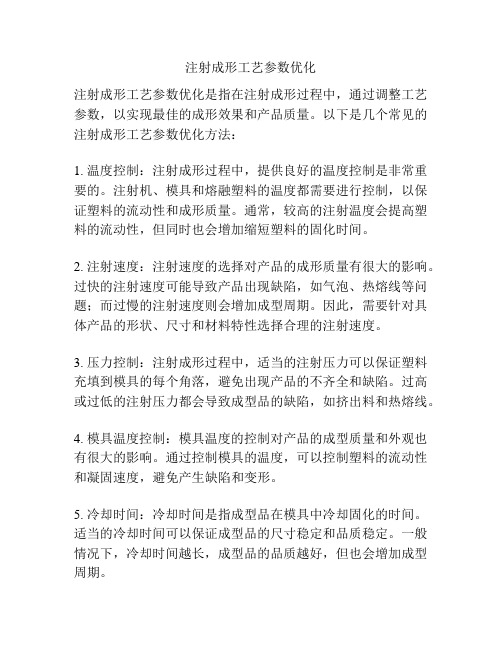
注射成形工艺参数优化注射成形工艺参数优化是指在注射成形过程中,通过调整工艺参数,以实现最佳的成形效果和产品质量。
以下是几个常见的注射成形工艺参数优化方法:1. 温度控制:注射成形过程中,提供良好的温度控制是非常重要的。
注射机、模具和熔融塑料的温度都需要进行控制,以保证塑料的流动性和成形质量。
通常,较高的注射温度会提高塑料的流动性,但同时也会增加缩短塑料的固化时间。
2. 注射速度:注射速度的选择对产品的成形质量有很大的影响。
过快的注射速度可能导致产品出现缺陷,如气泡、热熔线等问题;而过慢的注射速度则会增加成型周期。
因此,需要针对具体产品的形状、尺寸和材料特性选择合理的注射速度。
3. 压力控制:注射成形过程中,适当的注射压力可以保证塑料充填到模具的每个角落,避免出现产品的不齐全和缺陷。
过高或过低的注射压力都会导致成型品的缺陷,如挤出料和热熔线。
4. 模具温度控制:模具温度的控制对产品的成型质量和外观也有很大的影响。
通过控制模具的温度,可以控制塑料的流动性和凝固速度,避免产生缺陷和变形。
5. 冷却时间:冷却时间是指成型品在模具中冷却固化的时间。
适当的冷却时间可以保证成型品的尺寸稳定和品质稳定。
一般情况下,冷却时间越长,成型品的品质越好,但也会增加成型周期。
6. 注射压力和速度的曲线控制:不同的产品形状和材料特性需要不同的注射压力和速度曲线来保证产品的品质。
通过合理的曲线控制,可以避免在注射过程中出现缺陷,提高产品的成型质量。
总之,注射成形工艺参数优化是一个复杂的过程,需要综合考虑材料特性、产品形状和尺寸、模具结构等因素,并通过试验和实践进行优化调整,以实现最佳的成型效果和产品质量。
tpr注塑成型工艺参数
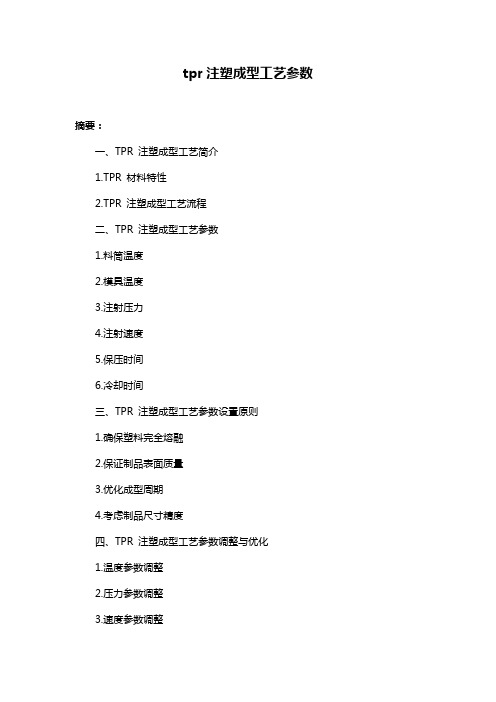
tpr注塑成型工艺参数摘要:一、TPR 注塑成型工艺简介1.TPR 材料特性2.TPR 注塑成型工艺流程二、TPR 注塑成型工艺参数1.料筒温度2.模具温度3.注射压力4.注射速度5.保压时间6.冷却时间三、TPR 注塑成型工艺参数设置原则1.确保塑料完全熔融2.保证制品表面质量3.优化成型周期4.考虑制品尺寸精度四、TPR 注塑成型工艺参数调整与优化1.温度参数调整2.压力参数调整3.速度参数调整4.时间参数调整正文:TPR 注塑成型工艺是一种将热塑性弹性体(TPR)通过注塑机进行加工制造的工艺。
TPR 材料具有优异的弹性和耐磨性,广泛应用于汽车、电子、家电等领域。
本文将详细介绍TPR 注塑成型工艺的参数设置及优化方法。
一、TPR 注塑成型工艺简介TPR 材料是一种具有橡胶与塑料特性的材料,具有较高的弹性、强度和耐磨性。
TPR 注塑成型工艺流程包括:原料准备、注塑机调试、模具安装、注射成型、制品取出、冷却定型等步骤。
二、TPR 注塑成型工艺参数1.料筒温度:料筒温度是影响TPR 材料熔融的重要参数。
适当的料筒温度可以确保塑料完全熔融,避免因温度过低导致塑料不能完全熔融,或因温度过高导致塑料降解。
2.模具温度:模具温度会影响制品的表面质量和尺寸精度。
适当的模具温度可以降低制品的内应力,提高制品的表面质量。
3.注射压力:注射压力是影响TPR 注塑成型工艺的关键参数。
合适的注射压力可以保证制品的密度和强度,避免制品出现缺陷。
4.注射速度:注射速度过快或过慢都会影响制品的质量。
合适的注射速度可以保证制品的尺寸精度,避免出现熔接痕、气泡等缺陷。
5.保压时间:保压时间过长或过短都会影响制品的质量。
合适的保压时间可以保证制品的密度和强度,避免出现缺陷。
6.冷却时间:冷却时间过长或过短都会影响制品的尺寸和性能。
合适的冷却时间可以保证制品的尺寸精度,避免制品变形或破裂。
三、TPR 注塑成型工艺参数设置原则1.确保塑料完全熔融:料筒温度、注射压力和注射速度等参数需相互配合,确保塑料能够完全熔融,避免出现缺料、熔接痕等缺陷。
注射成型工艺参数简单版.
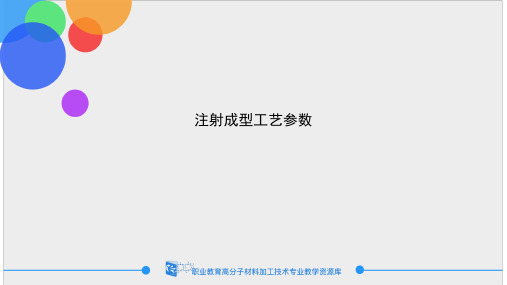
注射成型工艺参数
温度
压力
时间 (成型周期)
1.温度Βιβλιοθήκη ①料筒温度:在Tf(Tm)~Td之间(图3-9) ,保证塑料熔体正常流 动,不发生变质分解; 料筒后端温度最低,喷嘴前端最高;
当Tf(Tm)~Td范围窄时,料筒温度取偏低值。
②喷嘴温度:
略低于料筒最高温度:防止熔料在喷嘴处产生“流涎” 现象;但温度也不能太低,否则易堵塞喷嘴。
3.成型时间
成型周期或总周期 —— 完成一次注射模塑过程
所需的时间。 注射时间
保压时间
充模时间
成型周期
闭模冷却时间
其它时间
思考与练习:
1.模塑前准备及过程(填写工艺流程图) 2.螺杆式及柱塞式注射机的不同特点?
问题:
1.注射过程分为哪几个阶段?
2.注射成型工艺条件有哪些?
③模具温度:
温度过高 —— 成型周期长,脱模后翘曲变形,影响尺寸精度; 温度太低 —— 产生较大内应力,开裂,表面质量下降。
2.压力
①塑化压力:
又称背压(螺杆头部熔体在螺杆转动后退时所受到的压 力),由液压系统溢流阀调整大小。(补充概念)
②注射压力:
柱塞或螺杆头部对塑料熔体施加的压力。注射压力的大 小一般为40~130MPa,它的作用是克服熔体的流动阻力,保 证一定的充模速率。 注射压力与塑料品种、注射机类型、模具浇注系统结构尺 寸、塑件壁厚流程大小等因素有关。
- 1、下载文档前请自行甄别文档内容的完整性,平台不提供额外的编辑、内容补充、找答案等附加服务。
- 2、"仅部分预览"的文档,不可在线预览部分如存在完整性等问题,可反馈申请退款(可完整预览的文档不适用该条件!)。
- 3、如文档侵犯您的权益,请联系客服反馈,我们会尽快为您处理(人工客服工作时间:9:00-18:30)。
§4.3 注射成型的工艺参数
为避免熔料在料筒中过热降解—— 必须控制熔料在料筒内的滞留时间。 (2)喷嘴温度 喷嘴温度一般略低于料筒的最高温度。 喷嘴温度太高: 熔料在喷嘴处产生流涎现象,塑料易产生热分 解现象。 喷嘴温度太低: 易产生冷块或僵块,使熔体产生早凝,其结果 是凝料堵塞喷嘴,或是将冷料注入模具型腔,导 致成品缺陷。
§4.3 注射成型的工艺参数
但对结晶性塑料来说,使用这种方法成型周期 不一定增长,因为压实压力大时可以提高塑料的 熔点。 ——如聚甲醛,如果压力加大到50 MPa,则其 熔点可提高90℃,脱模可以提前。
2)保压大小也会对成型过程产生影响,保压压 力太高,易产生溢料、溢边,增加塑件的应力; 保压压力太低,会造成成型不足。
§4.3 注射成型的工艺参数
(3)保压时间 保压时间: 是指型腔充满后继续施加压力的时间(柱塞或 螺杆停留在前进位臵的时间),一般为20—25s, 特厚塑件可高达5~10min。 保压时间过短: 塑件不紧密,易产生凹痕,塑件尺寸不稳定; 保压时间过长: 加大塑件的应力,产生变形、开裂,脱模困难。 保压时间的长短不仅与塑件的结构尺寸有关,而 且与料温、模温以及主流道和浇口的大小有关。
§4.3 注射成型的工艺参数
3.时间(成型周期) 成型周期: 完成一次注射成型过程所需的时间。 成型周期的组成: 合模时间 注射时间 保压时间 模内冷却时间 其他时间
§4.3 注射成型的工艺参数
(1)合模时间 合模时间: 是指注射之前模具闭合的时间。 ——合模时间太长,则模具温度过低,熔料在 料筒中停留时间过长; ——合模时间太短,模具温度相对较高。 (2)注射时间 注射时间: 是指注射开始到充满模具型腔的时间(柱塞或 螺杆前进时间)。
§4.3 注射成型的工艺参数
降低模具温度的优点: 能缩短冷却时间,提高生产率。 降低模具温度的缺点: 过低时,熔体在模具型腔内的流动性能会变 差,使塑件产生较大的应力和明显的熔接痕等缺 陷。 模具温度较低: 对降低塑件的表面粗糙度值、提高塑件的表面 质量有利。
§4.3 注射成型的工艺参数
降低模具温度的措施: 采用定温的冷却介质或制冷装臵来控制; 提高模具温度的措施: 用加热装臵对模具加热来保持模具的温度。 ——对塑料熔体,注射过程都是冷却过程。 为了使塑料成型和顺利脱模,模具的温度应低 于塑料的玻璃化温度θg或工业上常用的热变形 温度。
——会使得模腔中塑料内外冷却不一致,塑件 易产生应力和凹痕。 ——熔料的温度高,流动性好,易产生溢料、 溢边等缺陷。
§4.3 注射成型的工艺参数
2.料筒温度太低 ——熔体流动性差,易产生熔接痕、充填不足、 波纹等缺陷。 ——塑料冷却时易产生应力,塑件容易产生变 形或开裂等现象。 3.料筒的温度分布原则 采用前高后低的原则。 ——即料筒的加料口(后段)处温度最低,喷嘴 处的温度最高。 料筒后段温度应比中段、前段温度低5~10℃。
§4.3 注射成型的工艺参数
在生产过程中,模具温度的确定原则: 需要根据塑料品种和塑件的复杂程度确定。 满足注射过程要求的温度下,采用尽可能低 的模具温度,以加快冷却速度,缩短冷却时间;
模具温度保持在比热变形温度稍低的状态下, 使塑件在比较高的温度下脱模,然后自然冷却, 可以缩短塑件在模内的冷却时间。 ABS塑料成型中小型塑件的温度参数选择: 预热干燥温度: 80~85℃;
§4.3 注射成型的工艺参数
(4)模内冷却时间 模内冷却时间: 是指塑件保压结束至开模以前所需的时间(柱 塞后撤或螺杆转动后退的时间均在其中)。 影响冷却时间的因素: 塑件的厚度 塑料的热性能 结晶性能 模具温度
§4.3 注射成型的工艺参数
冷却时间的长短: 应以脱模时塑件不引起变形为原则,冷却时间 一般在30~120 s之间。 冷却时间过长: 不仅延长生产周期,降低生产效率,对复杂塑 件还将造成脱模困难、易变形、结晶度高等; 冷却时间过短: 塑件易产生变形等缺陷。
§4.3 注射成型的工艺参数
——高粘度塑料: 流动性差和充模能力弱,为了获得致密的组 织结构,必须采用较高的模具温度; ——对于粘度较小、流动性好的塑料: 可采用较低的模具温度,这样可缩短冷却时 间,提高生产效率。 ——对于壁厚大的制件: 充模和冷却时间较长,温度过低,易使塑件内 部产生真空泡和较大的应力,不宜采用较低的模 具温度。
§4.3 注射成型的工艺参数
生产中塑化压力的选择原数值随所用塑料的品种而定。 一般为6~20MPa。
1)注射聚甲醛: 较高的塑化压力会使塑件的表面质量提高; 但可能使塑料变色、塑化速率降低和流动性下 降。
§4.3 注射成型的工艺参数
2)注射聚酰胺: 塑化压力必须降低,否则塑化速率将很快降 低。 ——因为螺杆中逆流和漏流增加的缘故。 ——如需增加料温,则应采用提高料筒温度的 方法。 3)聚乙烯: 热稳定性较高,提高塑化压力不会有降解的危 险,这有利于混料和混色,不过塑化速率会随之 降低。
§4.3 注射成型的工艺参数
注射压力太高: 塑料的流动性提高,易产生溢料、溢边,塑料 在高压下强迫冷凝,易产生应力,塑件易粘模, 脱模困难,塑件容易变形,但不易产生气泡。 注射压力太低: 塑料的流动性下降,成型不足,产生熔接痕 迹,不利于气体从熔料中溢出,易产生气泡,冷 却中补缩差,会产生凹痕和波纹等缺陷。
§4.3 注射成型的工艺参数
影响注射成型工艺的重要参数: 温度、压力和时间是。 1.温度 成型过程中需控制的温度种类: 料筒温度 喷嘴温度 模具温度 ——料筒温度、喷嘴温度主要影响塑料的塑化 和流动。 ——模具温度则影响塑料的流动和冷却定型。
§4.3 注射成型的工艺参数
(1)料筒温度 料筒温度的选择原则: 与塑料的品种、特性有关。 ——不同的塑料具有特定的粘流态温度或熔 点。 ——为保证塑料熔体的正常流动,不使物料发 生过热分解。 料筒最适合的温度范围: 在粘流温度或熔点温度θf(或θm)和热分解温 度θd之间。
§4.3 注射成型的工艺参数
(3)模具温度 模具温度的影响: 对熔体的充模流动能力 塑件的冷却速度 成型后的塑件性能
模具温度选择原则: 根据塑料的分子结构特点、塑件的结构及性能 要求和其他成型工艺条件(熔体温度、注射速度、 注射压力和模塑周期等)。
§4.3 注射成型的工艺参数
提高模具温度的优点: 改善熔体在模具型腔内的流动性 增加塑件的密度和结晶度 减小充模压力和塑件中的应力 提高模具温度的缺点: 冷却时间会延长,冷却速度慢, 产生粘模现象 收缩率大和脱模后塑件的翘曲变形会增加 降低生产率
§4.3 注射成型的工艺参数
影响注射压力的大小的因素: 注射机的类型 塑料的品种 模具浇注系统的结构、尺寸与表面粗糙度 模具温度 塑件的壁厚 流程的大小 ——目前难以作出具有定量关系的结论。 ——在相同条件下,柱塞式注射机的注射压力 应比螺杆式注射机的注射压力大。
§4.3 注射成型的工艺参数
影响塑料流动阻力的因素: 1.注射压力的大小。 2.塑料与模具浇注系统及型腔之间的摩擦系数和 塑料自身的熔融粘度。 ——摩擦系数和熔融粘度越大,注射压力应越 高。 ——同一种塑料流动时其与模具的摩擦系数和 熔融粘度是随料筒温度和模具温度而变动的。 3.是否加有润滑剂有关。
§4.3 注射成型的工艺参数
(5)其他时间 其他时间: 是指开模、脱模、喷涂脱模剂、安放嵌件等时 间。 塑化时间: 是指螺杆开始转动至预塑结束所需的时间。 ——塑化是在保压结束后就开始的,已经包含 在模内冷却时间内,因此不能重复计算在成型周 期内。
§4.3 注射成型的工艺参数
——螺杆转速快,剪切热加大,塑化时间缩 短; ——螺杆转速慢,剪切热减少,塑化时间增长。 模具的成型周期的影响: 直接影响到生产率和注射机使用率,因此,生 产中在保证质量的前提下应尽量缩短成型周期中 各个阶段的有关时间。 整个成型周期中,以注射时间和冷却时间最重 要,他们对塑件的质量均有决定性影响。
§4.3 注射成型的工艺参数
——平均相对分子质量偏高、温度分布范围较 窄的塑料: ——选择较高的料筒温度(玻璃纤维增强塑体)。 ——用柱塞式塑化装臵的塑料和注射压力较低、 塑件壁厚较小时: ——应选择较高的料筒温度。 反之,则选择较低的料筒温度。
§4.3 注射成型的工艺参数
注意问题: 1.料筒温度太高 ——塑料易产生低分子化合物和分解成气体, 使塑料表面变色,产生气泡、银丝及斑纹,导致 性能下降。
§4.3 注射成型的工艺参数
(3)保压压力 保压压力: 型腔充满后,继续对模内熔料施加的压力。 保压压力的作用: 是使熔料在压力下固化,并在收缩时进行补 缩,从而获得健全的塑件。 保压压力等于或小于注射时注射压力的原因: 1)注射和压实时的压力相等,则往往可以使塑 件的收缩率减小,并且它们的尺寸稳定性较好。 缺点是会造成脱模时的残余压力过大和成型周 期过长。
(3)保压时间 保压时间: 是指型腔充满后继续施加压力的时间(柱塞或 螺杆停留在前进位臵的时间),一般为20—25s, 特厚塑件可高达5~10min。 保压时间过短: 塑件不紧密,易产生凹痕,塑件尺寸不稳定; 保压时间过长: 加大塑件的应力,产生变形、开裂,脱模困难。 保压时间的长短不仅与塑件的结构尺寸有关,而 且与料温、模温以及主流道和浇口的大小有关。 (4)模内冷却时间 模内冷却时间是指塑件保
§4.3 注射成型的工艺参数
§4.3 注射成型的工艺参数
注射中,影响塑化压力大小的因素: 螺杆的设计 塑件质量的要求 塑料的种类 增加塑化压力的优点: ——三个因素和螺杆的转速都不变。 增加塑化压力会提高熔体的温度,并使熔体的 温度均匀、色料混合均匀并排除熔体中的气体。 增加塑化压力的缺点: 降低塑化速率,延长成型周期,甚至可能导致 塑料的降解。
§4.3 注射成型的工艺参数
料筒温度: 后段150~170℃; 中段165~180℃; 前段180~200℃; 喷嘴温度: 170~180℃; 模具温度: 50~80℃; 后处理温度: 70℃。