滚动轴承磨加工工艺流程与过程控制
滚动轴承制造工艺
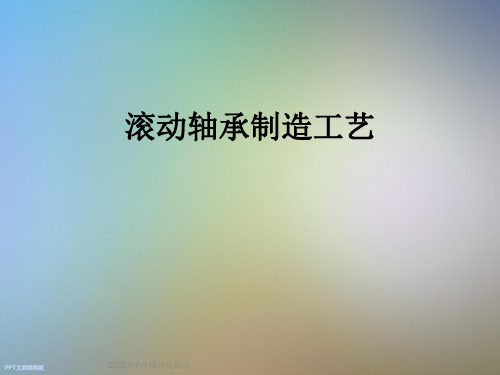
滚动轴承制造工艺
①退火棒料:材料利用率低(26%以下),车削 工作量大,只适用于小型套圈;
②管料:材料利用率比较高(50%以上),车削 工作量小,生产效率高,只适用于大批量生产中 小型轴承套圈的自动线上;
③锻件:目前车削套圈的主要毛坯,材料利用率 比较高(40%以上),适用于大批量生产中大型 轴承套圈。
外圈:挤压成形压平→
加热→镦粗→分套→
辗扩→整径
内圈:料芯→镦粗→
挤压成形→冲孔压
平→辗扩→整径
滚动轴承制造工艺
滚动轴承制造工艺
④清理:毛刺、氧化皮等。 ⑤退火:降低硬度,便于车加工。 4、锻造设备: (1)燃料:①固体燃料:煤;②液体燃料:汽
油、煤油、柴油、重油;③气体燃料:天然气 、煤气、石油气等。 (2)加热炉:①燃煤加热炉;②燃气加热炉; ③燃油加热炉;④电加热炉;⑤感应加热炉( 工频50Hz、中频50~10000Hz、高频10000以上)
滚动轴承制造工艺
降低劳动强度等都有重要的影响。 2、轴承套圈车削加工的目的和任务: ①对一般锻件毛坯,去除表面坚硬的氧化变质层
(黑皮); ②对棒料、管料,去除多余的金属量; ③经济取得车加工的形状、尺寸和位置精度; ④对待加工表面均匀地留有一定深度的流量; ⑤加工好辅助表面(倒角、沟、槽等); 3、轴承套圈毛坯的类型:
滚动轴承制造工艺
(2)代表我国锻造技术水平的是高速镦锻。 其工艺采用感应加热至始锻温度,在高速镦锻 机上完成切料、镦饼、成形、切底分离等工序 。一般适应与外径φ30~105mm的大批量生产 ,生产效率高,尺寸精度高,表面质量好,其 留量为:外径1~1.5mm、内径1.2~2mm、高度 1.2~2mm,公差:内径0.4~0.6mm 外径 0.3~0.4mm高度0.4~0.6mm,材料利用率可达 60%以上。
轴承制造工艺及装配ppt课件

ZYS·TCC 车削加工
车削加工
车削加工是轴承套圈的半成品加工,也可以说是成型加工。
车削加工的主要目的是:
1 使加工后的套圈与最终产品形状完全相同。
2 为后面的磨削加工创造有利条件。
车削 加工
集中工序法:在一台设备上完成所有的车削工序 小批量生产 分散工序法:在一台设备上完成某一种车削工序
大批量生产
ZYS·TCC 车削加工
套圈车削加工过程示意图
毛坯
内径 端面
外径 端面
磨削 端面
外圈
倒角 车沟 车槽
磨削
外径
精车
内径 内圈
倒角
车沟
设备一般都是轴承专用车床,按分散工序法的工序流程布置
ZYS·TCC 热处理
热处理
热处理是提高轴承内在质量的关键加工工序
热处理的主要目的是:
1 通过热处理使材料组织转变,提高材料机械性能。 2 提高轴承内在质量(耐磨性、强韧性),从而提高轴承使用寿命。
2 消除金属内在缺陷,改善金属组织,使金属流线分布合理,金 属紧密度好,从而提高轴承的使用寿命。
锻造 加工
热锻 —— 金属加热到再结晶温度以上
冷锻 —— 金属在室温下变形 温锻 —— 介于热锻与冷锻之间的金属变形
大量使用
很少采用 试验阶段
ZYS·TCC 锻造加工
锻造加工
外 圈
钢材
加热 下料
1050℃~1150 ℃
等终检 装配
等终检 装配
设备一般都是数控轴承专用磨床,按分散工序法的工序流 程布置
ZYS·TCC 轴承装配
轴承装配
轴承装配是轴承生产过程中的最后工序,对轴承性能具 有重要的影响。
轴承装配的主要目的是:
圆锥滚子轴承制造的生产工艺流程

圆锥滚子轴承制造的生产工艺流程圆锥滚子轴承是一种常用的滚动轴承,广泛应用于机械设备中。
它具有承载能力高、转速高、摩擦损失小等优点,因此在工业领域得到了广泛的应用。
下面我们来介绍一下圆锥滚子轴承的生产工艺流程。
一、原材料准备圆锥滚子轴承的主要原材料是高品质的轴承钢。
首先需要对这些轴承钢进行化学成分分析和机械性能测试,确保其符合产品标准要求。
然后将轴承钢进行切割和加热处理,得到符合尺寸要求的轴承圆棒。
二、车削加工将加热处理后的轴承圆棒进行车削加工,包括车外圆、车内圆和车端面等工序。
通过车削加工,可以使轴承圆棒的尺寸精度和表面光洁度达到要求。
车削加工是圆锥滚子轴承制造过程中的重要环节,对产品质量起着决定性作用。
三、热处理经过车削加工后的圆锥滚子轴承,需要进行热处理。
热处理可以改善轴承的组织结构和机械性能,提高其硬度和耐磨性。
热处理工艺包括淬火和回火两个步骤,通过控制加热温度和保温时间,使轴承达到理想的硬度和韧性。
四、磨削加工经过热处理的圆锥滚子轴承需要进行磨削加工,以进一步提高其尺寸精度和表面质量。
磨削加工包括外圆磨削、内圆磨削和端面磨削等工序。
通过磨削加工,可以使轴承的圆度、圆柱度和表面粗糙度达到产品标准的要求。
五、装配和调试经过磨削加工的各个零部件,需要进行装配和调试。
装配过程中,需要安装滚子、保持架、内外圈等零部件,并进行润滑。
调试过程中,需要检查轴承运转是否灵活、噪音是否正常等,确保轴承的质量和性能符合要求。
六、清洗和包装经过装配和调试的圆锥滚子轴承需要进行清洗和包装。
清洗过程中,使用清洗液将轴承表面的油污和金属屑清除干净。
包装过程中,将清洗后的轴承进行适当的防锈处理,并采用适合的包装材料进行包装,以确保轴承在运输和储存过程中不受损坏。
以上就是圆锥滚子轴承的生产工艺流程。
通过精细的加工和严格的质量控制,可以生产出高质量的圆锥滚子轴承,满足各种机械设备的使用需求。
圆锥滚子轴承的生产工艺流程是一个复杂而精细的过程,需要专业的设备和技术,并且在每个环节都需要进行严格的质量检查,以确保产品的质量和性能。
滚动轴承磨加工工艺流程与过程控制
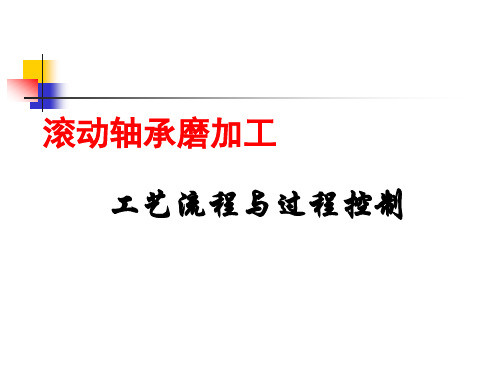
T
端面工序
端面磨分单面磨端面和双端面磨(原理) 端面磨质量要求
平行差(VBS,VCS):内外套圈宽度变动量 (V ): 尺寸 (△BS, △CS):套圈宽度尺寸偏差 粗糙度(Ra): 外观:啃伤、烧伤、碰伤、磨纹、擦伤(原因 由自己去总结,烧伤是砂轮选择不当、进给量 不均匀切削液不足或变质等
内圆(内径) 内圆(内径)
1、内径工序质量控制项
尺寸(A) 椭圆度 锥度 垂直差 粗糙度 外观 2、内径工序常见问题 a、尺寸超差:测规调整不当或故障、磨削量选择不合适、切 削液不足温差大、上工序外径偏差大(微型) b、圆度:主轴径向摆动大、上工序圆度不好复映开内径面 上、砂轮不好或磨钝,支承调整不当、进给量过大 c、锥度:磨架角度未调好、砂轮没修好成锥形、工件中心和 砂轮中心不等高、上工序质量不好(微型) d、垂直差:工件主轴有轴向窜动、工件端面尺寸偏差太大、 靠山未修平 e、磨内径引起了沟道碰伤:主要是由支承边角未修磨好、机 械手磨损严重碰到沟道、料道没调好。
无心工序
外圆磨质量问题
尺寸:可能引起的原因有1、导轮不圆、2、导轮旋转时有 跳动 3、磨削轮磨钝4、磨削轮轴振动 圆度:椭圆度、棱圆度1、工件中心高不合适、斜角过大、 磨削余量过大、磨削轮不平衡等 振纹:磨削轮不平衡、磨削轮磨钝、托板太薄或斜角过大、 工件中心过高等 粗糙度:磨粒太粗或金刚石笔磨钝、导板位置没有调好、 工件纵向速度太快、导轮速度过高。0.32um 外观:烧伤、啃伤、擦伤三角形磨伤、倒角磨伤、沟式磨伤、垫伤 锥度:工件间靠的不紧、托板磨损严重、火花没有调好、不均匀前 后导板的位置不正确。
端面工序对下工序的影响
工艺流程与过程控制
A 磨 内 径 磨 小 沟
轴承外圈加工工艺流程

轴承外圈加工工艺流程英文回答:The manufacturing process for the outer ring of a bearing involves several steps to ensure its accuracy and quality. Here is a general overview of the process:1. Material Selection: The first step is to select the appropriate material for the outer ring. Common materials used for bearing rings include steel, stainless steel, and brass.2. Forging or Casting: The selected material is then either forged or cast into the desired shape of the outer ring. Forging involves heating the material and shaping it using mechanical force, while casting involves pouring molten metal into a mold and allowing it to solidify.3. Rough Machining: After the forging or casting process, the outer ring undergoes rough machining to removeexcess material and bring it close to its final shape. This is typically done using CNC machines or other precision machining tools.4. Heat Treatment: The rough-machined outer ring is then subjected to a heat treatment process to improve its mechanical properties. This usually involves heating the ring to a specific temperature and then cooling it rapidly to achieve the desired hardness and toughness.5. Precision Machining: Once the heat treatment is complete, the outer ring undergoes precision machining to achieve its final dimensions and surface finish. This includes operations such as turning, grinding, and honing to achieve the required tolerances and surface smoothness.6. Surface Treatment: Depending on the application requirements, the outer ring may undergo additional surface treatments such as plating, coating, or heat treatment to enhance its corrosion resistance, wear resistance, or other properties.7. Inspection and Quality Control: Throughout the manufacturing process, the outer ring undergoes rigorous inspection and quality control measures to ensure its dimensional accuracy, surface finish, and overall quality. This includes non-destructive testing, dimensional measurement, and visual inspection.8. Assembly: Once the outer ring is deemed to be within the specified tolerances and quality standards, it is ready for assembly with other bearing components, such as theinner ring, rolling elements, and cage, to form a complete bearing assembly.中文回答:轴承外圈的加工工艺流程包括多个步骤,以确保其精度和质量。
轴承的制作方法和步骤
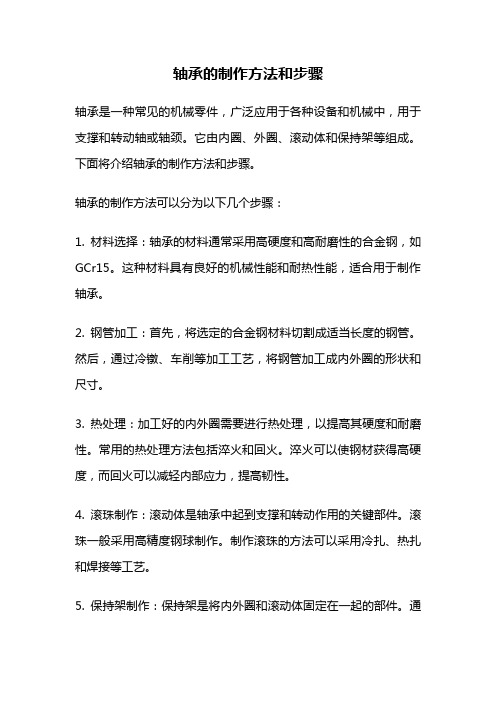
轴承的制作方法和步骤轴承是一种常见的机械零件,广泛应用于各种设备和机械中,用于支撑和转动轴或轴颈。
它由内圈、外圈、滚动体和保持架等组成。
下面将介绍轴承的制作方法和步骤。
轴承的制作方法可以分为以下几个步骤:1. 材料选择:轴承的材料通常采用高硬度和高耐磨性的合金钢,如GCr15。
这种材料具有良好的机械性能和耐热性能,适合用于制作轴承。
2. 钢管加工:首先,将选定的合金钢材料切割成适当长度的钢管。
然后,通过冷镦、车削等加工工艺,将钢管加工成内外圈的形状和尺寸。
3. 热处理:加工好的内外圈需要进行热处理,以提高其硬度和耐磨性。
常用的热处理方法包括淬火和回火。
淬火可以使钢材获得高硬度,而回火可以减轻内部应力,提高韧性。
4. 滚珠制作:滚动体是轴承中起到支撑和转动作用的关键部件。
滚珠一般采用高精度钢球制作。
制作滚珠的方法可以采用冷扎、热扎和焊接等工艺。
5. 保持架制作:保持架是将内外圈和滚动体固定在一起的部件。
通常采用金属材料或塑料材料制作。
金属保持架可以采用钢带冲压成形,而塑料保持架可以通过注塑成型制作。
6. 装配:将加工好的内外圈、滚动体和保持架进行装配。
首先,将滚动体均匀分布在内外圈之间,然后使用保持架将其固定在一起。
装配时需要注意保持极其清洁,避免杂质进入轴承内部。
7. 润滑:装配好的轴承需要进行润滑,以减少摩擦和磨损。
常用的润滑方法包括油润滑和脂润滑。
油润滑适用于高速轴承,而脂润滑适用于低速高负荷轴承。
8. 检测:制作完毕的轴承需要进行严格的检测,以确保其质量和性能符合要求。
常用的检测方法包括外观检查、尺寸测量、硬度测量和性能测试等。
通过以上步骤,轴承的制作过程基本完成。
最后,制作好的轴承可以用于各种机械设备中,起到支撑和转动的作用。
轴承的制作需要严格遵循工艺要求和质量控制标准,以确保轴承具有良好的性能和可靠性。
总结起来,轴承的制作方法和步骤包括材料选择、钢管加工、热处理、滚珠制作、保持架制作、装配、润滑和检测。
滚动轴承套圈加工工艺
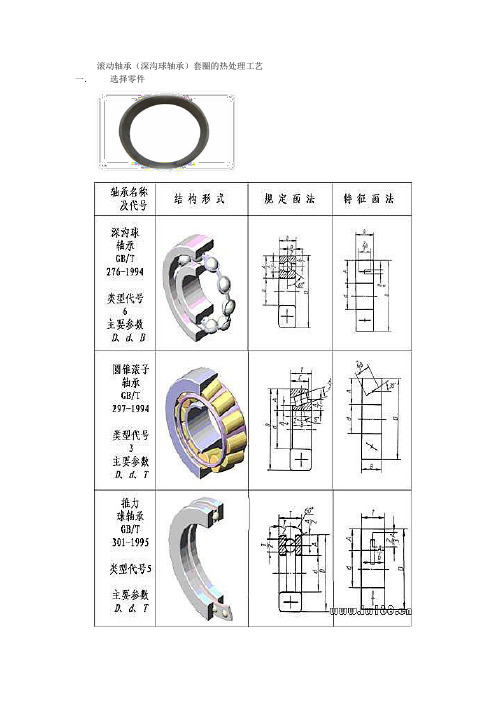
套圈的冷却一般在30~80℃的10号、20号机油中冷却。冷却方法使用分级淬火:在正常奥氏体化温度后,再投入120~170℃的10号机油中冷却2~5分钟,再放入30~60℃10号机油中冷却,为减少残余奥氏体的稳定性,分级淬火后应立即进行冷处理和回火。
5.回火
回火的目的
消除内应力,稳定组织和尺寸,提高圈套的综合机械性能。回火是热处理淬火后必不可少的工序,是决定零件内在质量的关键工序。
四.加工工艺
棒料→锻制→正火→球化退火→车削加工→去应力退火→淬火→冷处理→低温回火→粗磨→补加回火→精磨→成品
1.正火
正火的目的
(1)消除网状碳化物及线条状组织
(2)返修退火的不合格品
(3)为满足特殊性能的需要
(4)为退火做组织准备
加热温度
正火加热温度主要依据正火目的和正火前组织状态来决定。此处正火主要是为了消除或减少粗大网状碳化物,所以正火温度选在930~950℃之间。如果一次正火不能消除粗大网状碳化物,可以以相同温度二次正火。
综上所诉,要求套圈要有1)高的接触疲劳强度2)高的耐磨性3)高的弹性极限4)适宜的硬度5)一定的韧性6)良好的尺寸稳定性7)良好的防锈能力8)良好的工艺性能
三.材料选择
套圈的材料选择一般有6种GCr4 ,GCr15 ,GCr15SiMn ,GCr15SiMo ,GCr18Mo
牌号
C
Si
Mn
Cr
Mo
P
7.热处理设备
7.1.中温箱式电阻炉
此次生产所要的最高温度为950℃。900℃以下的为低温箱式电阻炉,1300℃以上的为高温箱式电阻炉,为节约成本选用中温箱式电阻炉。中温箱式电阻炉适用于中小型钢制机件的淬火、退火、正火热处理。
汽车轴承加工工艺流程

汽车轴承加工工艺流程
1. 原材料准备
- 选择合适的钢材或其他金属材料作为轴承材料。
- 检查材料质量,确保无缺陷。
2. 锻造或铸造
- 根据轴承的设计要求,采用锻造或铸造工艺将原材料加工成粗坯。
- 锻造可提高材料的致密度和力学性能。
3. 热处理
- 对粗坯进行适当的热处理,如淬火、回火等,以获得所需的硬度和强度。
- 热处理可改善材料的组织结构和力学性能。
4. 粗加工
- 使用车床、铣床等机床对粗坯进行粗加工,去除多余材料,获得接近最终尺寸的半成品。
- 粗加工可提高后续精加工的效率。
5. 精加工
- 采用精密加工设备,如精密车床、磨床等,对半成品进行精加工。
- 确保轴承表面光洁度、几何精度和尺寸公差符合要求。
6. 超精加工(可选)
- 对于一些高精度轴承,可进行超精加工,如滚动磨床加工、抛光等,
以获得更高的表面质量。
7. 装配
- 将加工完成的轴承内、外圈、滚动体等部件进行清洗和装配。
- 注意保持装配过程的清洁度,避免污染。
8. 检测
- 对装配后的轴承进行全面检测,包括尺寸、运动精度、噪音、振动等,确保满足质量标准。
9. 包装和入库
- 对合格的轴承进行标识、包装,防止在运输和存储过程中受损。
- 将轴承入库,待后续装配到汽车上。
以上是汽车轴承加工的一般工艺流程,具体流程可能因轴承类型、材料和要求而有所调整。
在整个加工过程中,需要严格控制质量,确保轴承的可靠性和使用寿命。