圆盘剪的设计与参数选择知识分享
圆盘式剪板机的设计

圆盘式剪板机的设计圆盘剪板机通常设置在精整作业线上,用来将运动着的钢板的纵向边缘切齐或切成窄带钢。
根据其用途可分为两种类型:剪切板边的圆盘剪和剪切带钢的圆盘剪。
本文中对圆盘剪板机的设计计算是从材料力学、动力学和经济学的角度出发,对圆盘剪板机的主传动系统,压下系统、侧间隙调整机构进行了设计。
重点包括电动机的计算选取、轴和齿轮的设计,以及其他传动装置和执行机构的设计等,同时对部分主要零部件进行了强度校核。
本次设计的改进点:首先,在径向间隙调整机构连杆机构,其二,侧向间隙调整增加自锁装置。
其三,宽度调整采用行星齿轮减速机。
最后增加了测速机构。
本圆盘剪板机可普遍用于横切机组、酸洗机组等。
1 前言1.1 选题的背景和目的剪板机各种类型,平刃剪、斜刃剪、圆盘剪和飞剪。
平刃剪用于剪板方坯,斜刃剪用于剪板板材,而圆盘剪广泛用于纵向剪切厚度小于20~30毫米的钢板及薄带钢。
而飞剪用于剪切运动着的轧件,其剪刃有平刃、斜刃和圆盘式飞剪。
圆盘式剪板机由于刀片是旋转的圆盘,因而可连续纵向剪切运动钢板和带钢。
圆盘式剪板机通常设置在精整作业线上用于将运动着的钢板纵向边缘切齐和剪切或者切成窄带钢,根据其用途可分为剪切板边的圆盘剪和剪切带钢的圆盘剪。
上刀片固定在刀架上,下刀片固定在下床面上,工作台上安装有托料球,以便于板料的送进移动和板料在上面滑动时不被划伤,后挡料板用于板料定位,位置由调位电机销进行调节。
液压压料筒用于压紧板料,以防止板料在剪切时翻转和防止板料在剪切时移动。
棚板是安全装置,以防止发生工伤事故。
回程一般 靠氮气,速度快,冲击小。
调整前挡板把后挡板靠紧下刀口,再把样板靠紧后挡板,将前挡板靠紧样板并固定。
松开后挡板,去掉样板,装上板料,进行剪切。
调整后挡板将样板托平对齐下刀口,再把后挡板靠紧样板并固定,去掉样板,再装上板料进行剪切。
调整角挡板先将样板放在台面上对齐下刀口,调整角挡板并固定,再根据样板调整后挡板,剪切过程中同时利用角挡板和后挡板以定位.查 机械原理[1]%1002312001200⨯+=A 1.2 圆盘式剪板机国内外的发展现状圆盘剪板机有下列几个机构组成:刀盘旋转传动系统,刀盘径向调整和刀片的侧向调整,剪切宽度的调整等。
高速圆盘锯的设计与优化

高速圆盘锯的设计与优化高速圆盘锯是一种常用于木材加工和金属切割的切割工具。
它采用圆盘状切割刀具,在高速旋转的同时,通过切削物体来实现切割作业。
为了提高切割效率和质量,高速圆盘锯的设计与优化是至关重要的。
首先,高速圆盘锯的设计需要考虑切削刀具的选择。
切削刀具的材料和形状直接影响切削效果和使用寿命。
通常,高硬度的硬质合金材料是制作切削刀具的常见选择,因为它具有高耐磨性和耐热性。
同时,切削刀具的形状应该能够在高速旋转时有效地将切削力传递给工件,并降低振动和噪音。
其次,高速圆盘锯的设计需要考虑切削参数的优化。
切削速度、进给速度和切削深度是影响切削效率和切削质量的关键参数。
切削速度过高可能导致切削刀具过早磨损,而切削速度过低则会降低切削效率。
进给速度的选择应该根据不同的工件和切削刀具,以保证切削过程中既能保持稳定的切削力,又能获得满意的切削表面质量。
切削深度的选择应该平衡切削效果和切削刀具的使用寿命,以避免过度磨损或切削力过大引起振动和噪音。
另外,高速圆盘锯的设计还需要考虑切削润滑和冷却系统的优化。
切削润滑和冷却是提高切削效果和切削刀具寿命的重要手段。
常见的切削润滑和冷却方法包括涂层剂、喷雾系统和冷却剂。
切削润滑和冷却系统的设计应该考虑切削材料的性质和加工条件,以确保切削过程中切削刀具保持良好的润滑和冷却效果。
此外,高速圆盘锯的设计还需要考虑安全性和人机工程学因素。
切削过程中可能产生的飞溅和切削粉尘对操作者的安全和健康构成潜在威胁。
因此,设计应包括安全防护装置和合理的工作环境,以减少操作者受伤风险。
此外,人机工程学的考虑应该确保高速圆盘锯的设计符合人体工程学原理,使操作者能够方便、安全地操作设备。
最后,高速圆盘锯的设计还需要考虑设备的稳定性和耐用性。
设备结构的稳定性可以通过合理的机身设计和选用高强度材料来实现。
耐用性的考量包括材料的使用寿命、易损件的更换和设备的维修保养等。
合理的设计和优化可以延长设备的使用寿命,降低维修成本。
中板圆盘剪传动机构设计

中板圆盘剪传动机构设计一、中板圆盘剪传动机构的工作原理在工作过程中,需要保证两个圆盘之间的压力不会过大,否则会导致机构的堵塞和故障。
因此,在设计中需要考虑适当的尺寸、材料、传动比等因素。
二、中板圆盘剪传动机构的设计要点1.传动比的确定:在进行设计时,需要确定合适的传动比。
传动比的选择会影响到机构的性能和工作效率。
一般情况下,传动比越大,工作效率越高,但是对机构的要求也越高,需要考虑到材料强度和使用寿命等因素。
2.圆盘材料的选择:由于中板圆盘在工作时需要承受较大的剪切力,因此需要选择合适的材料。
常见的材料有钢、铝合金等。
在选择材料时需要考虑到强度、硬度、耐磨性等因素。
3.圆盘尺寸的确定:圆盘的尺寸对机构的工作性能有着重要的影响。
大圆盘可以提供较大的剪切力,但机构体积会增大;小圆盘可以减小机构体积,但提供的剪切力较小。
因此,需要根据实际需求确定合适的圆盘尺寸。
4.传动轴的设计:传动轴是连接驱动圆盘和中板圆盘的关键部件。
在设计传动轴时,需要考虑到强度、刚性、耐磨性等因素。
一般情况下,传动轴需要经过热处理来增强其硬度和强度。
5.调整装置的设计:为了保证机构的正常工作,需要设计一个调整装置来调整两个圆盘之间的间隙和压力。
调整装置一般包括调整螺丝、调整垫片等。
通过调整装置可以实现机构的灵活调整和维护。
三、中板圆盘剪传动机构设计实例以设计一个中板圆盘剪传动机构为例,假设工作要求为:工作圆盘直径为200mm,剪切板厚度为5mm,材料为优质钢,要求剪切力为1000N。
1.传动比的确定:经过计算,传动比取1:42.圆盘材料的选择:根据材料强度要求,材料选择优质钢。
3. 圆盘尺寸的确定:根据工作圆盘直径为200mm,剪切板厚度为5mm,计算得出大圆盘和小圆盘的直径分别为200mm和50mm。
4.传动轴的设计:选择优质钢作为传动轴材料,经过热处理提高其硬度和强度。
5.调整装置的设计:设计一个调整螺丝和垫片调整装置,通过调整螺丝的松紧程度来达到调整圆盘间隙和压力的目的。
圆盘剪

酸洗机组圆盘剪调整工艺一、圆盘剪的功能采用一定的剪切工艺对带钢的边部进行剪切,消除热轧钢带的边部缺陷,和满足用户的需求。
二、主要技术性能剪切速度:30~180m/min刀片直径: 350~400 mm刀头开口度: 700~1350 mm刀片厚度: 35~ 40 mm刀片材质: 6CrW2Si刀轴材质: 42CrMo切边量: Min 5mm且大于1.5倍带钢厚度;Max 35mm (单边)剪切带钢厚度: 1.5~ 5mm刀片重叠量调整精度: ±0.2mm刀片侧隙调整精度: ±0.1mm三、圆盘剪的剪切机理圆盘剪由上下错位的、垂直的两片圆形刀片组合而成,调取一定的间隙及重叠量对通过两刀片之间的带钢进行剪切。
带钢通过两刀片之间时,刀片给带钢施以一定的剪切力,使带钢与刀片接触区域产生变形,随着咬入深度的增加,带钢的变形量也随之增加,当变形量达到一定程度时(一般为带钢厚度的1/4~3/4),受压的部分就从原板上断裂。
下刀片装在内侧主要起支撑作用,上刀片装在外侧主要起剪切作用。
上刀片机组中钢带心线边丝下刀片四、剪切不良的常见缺陷及成因分析1. 毛刺1.1原因毛刺的根本原因是刀片自身的平面度、上下刀片的相对平行度及刀片平面与剪切后钢带边缘的平行度存在偏差所至,导致上刀片与带钢边缘进行二次剪切;常见原因为刀片承担剪切面的边缘有缺口、烧伤或粘结、装刀时刀片侧面粘有异物、或者刀片修磨后未作消磁处理,导致刃口部位粘上铁屑。
1.2对策对各规格带钢剪切时按照正确的调整工艺进行调整;为了减少刀片自身的平面度、上下刀片的相对平行度偏差所带来的影响调整时可适当的将刀片的间隙放大,使剪切后钢带的横截面成倒梯形,以减少二次剪切面积;安装时保证刀片平面与机组中心线的平行度,同时使刀片出口侧的间距略大于入口侧的间距(0~1mm);及时更换刀片后作业;保证新刀片及修磨后刀片的精度,对修磨后的刀片作消磁处理。
2. 剪切不断2.1原因剪切不断的根本原因是刀片的间隙过大或重叠量过小;常见原因为刀片崩刃、刀片过钝、刀片的内孔过大导致剪切时重叠量的波动较大、压靠盘的直径与刀片直径的匹配不合理。
圆盘剪刀轴加工技术

l:
Ol 0 } O0 3
3 选 择合适 的加 工设备 .
这类零件通常选择精度高的机床加 工 ,但 各公
司 设 备 不 尽 相 同 ,设 备 与 设 备 之 间精 度 也 有 所 差 异 。现 有 的 高端 设备 主 要 有 数 控车 床 、数 控 磨床 。 受 资 源 的 限 制 ,公 司主 要 利 用 了数 控 车 床 及 普通 磨 床 来 实 现 产 品加 工要 求 , 因而 对设 备 精 度 的 确认 尤
承 内孔配磨。该 产品的形位公差要求相当高 ,需要 磨 削才能最终达 到精度要求 ,而 整体加工难度就在
于 如 何 保证 这 些 要 求 。
齐或切成窄带钢 ,去除带钢边部缺 陷。通过上下 刀 片的旋转 剪切运动以获得精确的钢板宽度和 良好 的
边 部 成形 。 圆盘 剪设 备 精 度 高 ,用于 剪 切 的 钢板 比 较 薄 ,剪 刀 的 间 隙 约 为00 mm, 刀盘 轴 向 圆跳 动 .2
进行检测并进行调整 ,保证磨床在轴向运行过程 中
轨 道的 直 线 度 ;并 通过 做 砂轮 动平 衡 ,来 保 证 砂轮
的径 向和 轴 向方 向上 的 圆跳 动 。 ②磨 削各 挡 外 圆 ,
选择适 当的进给量 ,随时检测各挡外 圆尺寸 。③对 于轴 向圆跳动 ,磨削采用 了拉刀式的方法 ,利用金
了 公司 圆盘 剪 刀轴 加 工 的成 熟 工艺 。MW ( 收稿 日期 :2 1 2 7 0 l 0) 1
用 图2 示方法进行检测 ,工件旋转 在等高V 铁 所 形
上 ,轴 向使 用钢 珠 固定 ,依 据 产 品形 状位 置 公 差 检 测 规 范操 作 来检 测 圆度 、轴 向 圆跳动 。
圆盘剪讲义精编版

圆盘剪讲解一工艺原理作用:使用两对旋转刀片切掉钢带边部,确定带钢的预定的宽度。
∙切边宽度:最小5mm(每边),最大40mm(每边);∙切边速度:出口线速度;∙缝隙调节装置:机构包括一个预加载微调螺钉,由一个双止推轴承定位。
范围: 0.04~0.6mm ;精度: ± 5µm ;∙重叠量调节装置:通过一个安装在微调螺钉末端的特殊步进电机进行调节。
范围: ﹢2~﹣1.6mm ;精度:±0.01mm ;∙角向头部开度调节装置:确保两个切割面的平行度的精确调节,从而能容易地调节一个小的开度既便于切割,又减小刀具的磨损。
两个丝杆能调节头部± 1°的范围。
∙刀片:使用时间:在两次更换之间约120km ;每次磨削量:0.3至0.5mm ;刀片寿命:约磨削20次;二工作状态1圆盘剪的旋转刀刃允许在不停线的情况下进行更换,对于剪刃有专用的设备允许在对薄带进行剪切时进行调整剪刃的机械间隙。
2两个电动系统允许边部的剪刃在修剪的水平和垂直方向的独自的进行调整间隙。
更换圆盘剪的剪刃简单而且大约需要1分钟(操作员在两侧)。
易拆/ 更换刀片是可能由液压螺母进行,也使用传动轴承两边剪切下来的废料直接进入废料箱3详细(1)两个旋转圆盘剪刃(2)位于旋转圆盘剪端部的去毛刺机(标准布置)(3)位于旋转圆盘剪端部的去毛刺机在圆盘剪的外壳上有一个极其紧凑布置,距离简短所以在圆盘剪剪刃与废料箱之间有安全导卫装置可移动、旋转的移动刀架可以保证刀刃的连续工作设备调整和锁住刀刃的进出纵向辅助设施上叶片中心,从而让更多的真正的废料流出如果没有叠层量的存在,在入口处应用硬质合金刀片,材质的使用寿命较长在使用固定的无间隙较低的剪刃时要预先加载去毛刺机剪刃的外壳和移动的锁定是通过液压活塞来完成的锥形滚珠丝杆的安装调整为宽刀的头上。
滚珠丝杠主轴得到安装过载滑离合器。
与安装一个电子的位置精度很高的调整编码器可以获得的远程控制修剪隔间。
木材圆盘切割锯设计

木材圆盘切割锯设计木材圆盘切割锯是一种广泛应用于木材加工行业的切割设备,能够将木材圆盘进行快速、准确的切割,提高生产效率和产品质量。
在设计木材圆盘切割锯时,需要考虑以下几个主要方面:切割精度、安全性、自动化程度和易维护性。
首先,切割精度是设计木材圆盘切割锯时最重要的考虑因素之一、切割精度决定了木材切割后的尺寸精度和平整度。
为了提高切割精度,可以采用高精度的导轨、高速度的切割刀片、稳定的传动装置和精确的定位系统。
此外,可以加入自动计数和自动校正功能,提高切割的准确性。
其次,安全性是设计木材圆盘切割锯时不可忽视的重要因素。
木材切割锯是一种较为危险的设备,如果操作不当可能会发生意外伤害。
为了保证操作人员的安全,应在设计中考虑安全装置,如切割刀片防护罩、切割区域警示灯、应急停止按钮等。
此外,应提供相应的培训和操作指南,以确保操作人员了解正确的操作方法。
第三,自动化程度是现代木材圆盘切割锯设计的一个重要趋势。
通过引入自动化控制系统,可以提高生产效率和切割精度。
例如,可以采用数控系统来实现切割参数的自动调整,根据不同的木材尺寸和切割要求进行自动切割。
同时,可以采用自动送料装置和自动卸料装置,减少人工操作。
最后,易维护性是设计木材圆盘切割锯时需要考虑的另一个方面。
由于木材切割锯需要长时间连续运行,因此需要保证设备的稳定性和可靠性。
为了方便维护,可以采用模块化设计,将设备分解成若干子系统,方便日常维护和故障排除。
此外,应提供操作手册和维护手册,以指导用户正确操作和维护设备。
总之,设计木材圆盘切割锯需要兼顾切割精度、安全性、自动化程度和易维护性。
通过合理设计和创新,可以提高木材加工行业的生产效率和产品质量。
同时,还应不断关注行业的技术发展和用户需求的变化,不断更新和改进木材圆盘切割锯的设计,以适应市场需求的不断变化。
圆盘剪
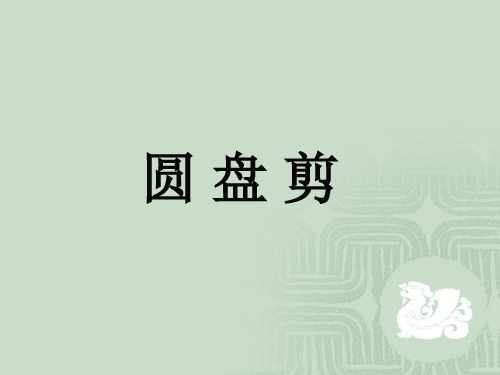
圆盘剪刀架宽度调整系统
适应剪切宽度的变化,设备上装有宽度调整 装置,由电机通过滚珠丝杠调整机架的开口 度,以满足高精度调宽的要求
剪刃间隙调整的特点
过去制造的剪边机大多是人工手动调整剪 刃间隙,因此将剪刃间隙调整到某个给定值时 需要较长时间;剪切不同厚度尺寸的钢板每次 就要停机重新调整一次剪刃间隙,这样大大增 加了停机时间,减少了机组的产量。
双头回转式圆盘剪停机时间很短,首先它 通过电脑了解了下一卷带钢的规格尺寸,并在 线外自动调整好备用刀盘的参数;换规格时只 需将备用刀盘转动到工作位置,便可继续剪切。 每对刀盘上都装有一套剪刃间隙调整装置。
Sห้องสมุดไป่ตู้
S
板厚/mm 圆盘刀片重叠量S 、侧向间隙 与被切钢板厚度h的关系
1850酸轧线圆盘剪技术参数值
剪刃直径: 剪刃的宽度: 剪刃的材料:
400 mm 43 - 25 mm HRC 58-60,合金钢
圆盘剪机架旋转机构
装有两套机架旋转双速齿轮电机,由双速齿 轮电机直接传动机架旋转机构,在旋转机构 上装有一个锁紧液压缸,当机架旋转到位后, 锁紧液压缸驱动一个凸状楔形块,将楔形块 插入机架上的楔形凹槽内,将机架锁紧定位。 需要换刀时,只需一分钟就可将机架及备用 刀盘一起旋转180度,并可准确定位在工作位 置上。
多对刀盘的圆盘剪用于板卷的纵切机组,将 板卷分切成窄带钢,其多对刀盘一般固定在 两个公用的轴上。
圆盘剪切机主要参数
圆盘刀片直径 与板带厚度h,刀片重叠量 S和最大咬入角1
有下列关系
D hS
1 cos1
咬入角1=10-15 ,则圆盘刀片通常在下列范围:
D (40 125h)
圆盘剪切机主要参数
圆盘刀片厚度
- 1、下载文档前请自行甄别文档内容的完整性,平台不提供额外的编辑、内容补充、找答案等附加服务。
- 2、"仅部分预览"的文档,不可在线预览部分如存在完整性等问题,可反馈申请退款(可完整预览的文档不适用该条件!)。
- 3、如文档侵犯您的权益,请联系客服反馈,我们会尽快为您处理(人工客服工作时间:9:00-18:30)。
圆盘剪的设计与参数选择圆盘剪的设计与参数选择【摘要】本文结合实际工程,介绍了推拉式酸洗线上圆盘剪的结构特点,刀具侧向间隙及刀盘重合度调整的方法等。
并给出了剪切力、驱动功率的计算公式和实际例子。
本圆盘剪已在华美推拉式酸洗线上使用。
【关键词】圆盘剪设计参数目录:1.圆盘剪概述2.圆盘剪主要技术性能3.圆盘剪结构3.1机架3.2调宽装置3.3刀刃侧向间隙调整装置3.4刀盘重合度调整装置4.有关参数的选择和计算4.1刀盘直径和厚度的选择4.2刀盘重合度和侧向间隙的选择4.3剪切力的计算4.4剪切力矩的计算4.5剪切电机功率校核5.结束语参考文献1.圆盘剪概述带钢在轧制过程中,有时边部会产生细小的裂缝等缺陷,如不及时切掉,极可能在后续加工过程中产生断带事故。
所以在酸洗机组中均设置圆盘剪,以便去掉边缘损伤,并使成品带钢达到要求的宽度。
另外圆盘剪还广泛用在冶金带钢生产线的其它机组中,如横切机组、纵剪机组、重卷机组、拉矫机组、镀锡机组及焊接机组等。
圆盘剪按其用途和构造可分为两大类:带两对刀盘和多对刀盘.两对刀盘的圆盘剪只用来剪切带材的边部,故称切边圆盘剪或切边剪;多对刀盘的圆盘剪在剪切带材边部的同时并将带材纵切成多条较窄的带材,故称分条圆盘剪或分条剪。
圆盘剪按其传动方式又分为拉剪和动力剪;所谓拉剪,即刀盘没有传动装置,直接由机后的张力辊及卷取机等设备将带钢拉过圆盘剪进行剪切.本文介绍的圆盘剪是用在推拉式酸洗线上。
它的特点是传动系统中装有超越离合器,当机组速度低于穿带速度时,圆盘剪按动力剪状态工作;当机组速度超过穿带速度时,离合器将脱开传动系统,圆盘剪按拉剪状态工作。
为了使切边时不产生毛刺,并保持最小的宽度公差。
必须用防跑偏装置加以控制,以使带钢对中和无冲击地进入圆盘剪。
因此,在圆盘剪的入口侧布置了一套夹送辊纠偏装置。
2.圆盘剪主要技术性能带钢厚度: 1.8~4.0mm带钢宽度:700~1350mm带钢强度极限:σb≤610Mpa机组速度:酸洗出口(圆盘剪):最大 120m/min穿带速度:最大 60m/min剪刃直径:φ350mm剪刃厚度:30mm最大工作间距:1590mm最小工作间距:630mm切边精度:0~+1mm3.圆盘剪结构圆盘剪由左右机架、上下刀轴、机架调宽机构、传动装置、刀盘重合度调整装置、刀刃侧向间隙调整装置、固定底座等组成。
详见图(1)、(2)。
图1 圆盘剪1.底座2.左机架3.右机架4.调宽装置5.刀刃侧向间隙调整装置图2 圆盘剪1.机架2.废边导向溜槽3.刀盘4.刀刃侧向间隙调整装置5.刀盘传动装置3.1 机架图3 圆盘剪(左)机架装配1.刀盘 2,机架 3.芯套 4.下刀轴 5.叠簧 6.超越离合器 7.刀盘驱动齿轮箱 8.上刀轴9.刀刃侧向间隙调整装置 10.刀盘重合度调整装置 11.偏心套圆盘剪两个机架左右对称布置,上下刀轴、刀盘、刀盘重合度调整装置、刀刃侧向间隙调整装置均装在机架上。
机架为箱形焊接结构,刀轴为悬臂式。
上下刀轴为圆盘剪的主要部件,详见图(3)。
其上安装有刀盘、压辊、圆锥滚子轴承、圆柱滚子轴承、芯套(下刀轴)、偏心套(上刀轴)、叠簧、液压螺母等。
由力的分析可以知道,在剪切时,上下刀盘有向上下方向倾翻的趋势,这将使刀盘重合度减小及刀刃侧向间隙增大。
直接的后果就是剪切质量下降,毛边产生,严重的可能导致剪不断,造成生产事故。
为避免上述现象发生,我们在上下刀轴上安装单列圆锥滚子轴承(成对安装)不允许刀轴窜动。
3.2 调宽装置为剪切不同宽度的带钢,圆盘剪的机架安装有调宽装置,用以调整两对刀盘的开口度。
调宽要求准确,由一个安装有编码器的齿轮电机驱动两根左右旋向的螺杆,带动固定在左右机架下方的螺母,实现左右机架的同时开合。
3.3 刀刃侧向间隙调整装置图4 刀刃侧向间隙调整装置1.侧向间隙调整齿轮电机2.蜗杆3.蜗轮4.芯套5.下刀轴刀刃侧向间隙调整时,上刀盘不动,由下刀盘轴向移动来实现。
通过齿轮电机驱动蜗杆,带动蜗轮。
蜗轮与下刀盘上的芯套用螺纹联接。
通过结构上的设计,保证蜗轮在芯套轴向上不能移动。
蜗轮的旋转运动经芯套转化为刀盘的轴向移动。
安装在下刀盘芯套尾部的有预紧力的碟簧,使装在下刀轴芯套上的蜗轮始终与装在机架上的挡块压紧。
将刀刃侧向间隙调小时,如图(3)所示,齿轮电机驱动蜗杆,带动蜗轮,使芯套带动下刀轴向左移动。
反之则可调大间隙。
齿轮电机尾部安装有旋转编码器,可以精确控制刀刃侧向间隙。
3.4 刀盘重合度调整装置图5 刀盘重合度调整装置1.刀盘重合度调整齿轮电机2.蜗杆3. 蜗轮4.偏心套5. 上刀轴刀盘重合度调整时,下刀轴固定不动,用上刀轴绕偏心套旋转来控制。
通过齿轮电机驱动蜗杆,带动蜗轮。
蜗轮与上刀轴上的偏心套用键联接。
由于上刀轴和偏心套有25mm的偏心量,偏心套的旋转,将使上刀盘的垂直位置发生变化,从而调整上下刀盘的重合度。
齿轮电机安装有旋转编码器,可以对重合度精确调整。
4.有关参数的选择和计算圆盘剪的基本参数是剪切力、重合量、侧向间隙、刀盘厚度、刀盘直径等。
4.1 刀盘直径和厚度的选择刀盘形状是薄圆柱体,主要几何尺寸是刀盘直径D和厚度b。
刀盘直径D主要取决于板带的厚度h,刀盘重合量S和最大咬入角α1。
参考类似的机组数据,我们选择刀盘直径为350mm。
选择刀盘的厚度b应使刀盘具有足够的刚度,一般选取b=(0.06~0.10)D,本刀盘选取b=30mm。
刀盘的材质应具备强度大、韧性好和硬度高的性能。
剪刃性能与制造工艺密切相关,制造性能好的剪刃,必须选用优质材料,精心锻造,合理热处理。
材料选用Cr12MoV,表面淬火硬度HRC≥58,表面粗糙度0.8~0.4μm,端面跳动6μm。
4.2 刀盘重合度和侧向间隙的选择刀盘重合量s和侧向间隙∆与被剪切的带钢厚度有关,如图6所示。
图6 圆盘剪刀盘重合量s和侧向间隙∆与被剪钢板厚度h的关系曲线由图可见,随着钢板厚度的增加,刀盘重合量s减小。
当钢板厚度>5mm时,重合量为负值。
剪切时,如重合量不够,会引起机械超负荷和带材局部弯曲;若重合量太大,则引起带材“竖立”现象。
为了避免圆盘剪剪刃之间的磨损,在两个剪刃侧向之间,应该有一定的间隙。
确定该间隙时,要考虑被切带钢的厚度和强度。
根据生产实践,冷剪时,侧向间隙∆可取被切带钢厚度的14~17%。
如果侧向间隙设置得不合理,对剪切面和设备均有很大的影响。
当剪刃之间的间隙过大时,剪切面出现不整齐,因为在剪切面附近会产生塑性变形,该断口不是被剪断的,而是以揉搓形式产生的撕裂现象。
这种剪断口,在剪切较厚而软的低碳钢板时较容易见到。
当剪刃之间的间隙过小时,又会导致设备超载,而且易使上下移动的剪刃面擦伤而过早损坏,其结果将使带钢的剪切面产生毛刺而不整齐。
左右机架上的剪刃重合量要一致,如果重合量不一致,则两机架上的剪刃受力不等,带钢两边受力亦不等,结果会导致带钢向侧面串动,发生跑偏现象。
侧向间隙小,剪切进行得快些,反之则慢一些。
所以,如果左右机架上的剪刃侧向间隙不一致,带钢两侧一边剪得快,一边剪得慢,带钢两边受力不等,必然产生跑偏现象。
4.3 剪切力的计算剪切过程一般由两个阶段组成:压入变形阶段和滑移阶段。
剪切力是随着切入深度Z的变化而变化的,当剪刃刚接触并逐渐压入带钢时,剪切力由零逐渐增大。
在整个压入阶段,在剪切断面上产生的剪切力小于带钢本身的抗剪能力,带钢只产生局部压缩塑性变形,这时带钢将产生偏转。
随着剪刃的逐渐压入,剪切力继续增加,当剪切力产生的剪应力等于带钢的抗剪能力时,带钢的的转角不再增加。
当剪切力稍大于此值时,在剪切断面上的剪应力就大于了带钢的抗剪能力,这时带钢便沿整个断面产生了相对滑移。
在滑移阶段,剪切断面逐渐减小,剪切力也随着不断减小,直至剪断带钢,剪切力为零。
在圆盘剪上剪切金属时,作用在单个圆盘剪剪刃上的总剪切力由两部分组成:P=P1十P2式中 Pl——纯剪切力;P2——钢板被剪掉部分的弯曲力,是由于剪切伴随着钢板的复杂弯曲而产生的,如图(7)。
图7 圆盘剪切机剪切板边示意图剪切力的计算方法较多,下面分别采用两种公式来计算:方法一:由上述可知,作用在单个剪刃上的总剪切力由两部分组成:P=P1十P2纯剪切力P1的确定在原则上与斜刀剪类似,参见图(8)。
图8 在圆盘剪上剪切金属时的压力图假定实际剪切面积只局限于弧AB 及CD 之间,因为在BD 线之外剪切的相对切入深度大于ε0,即剪切过程已彻底完成了。
其次,将弧AB 和CD 视为弦。
作用于宽度为dx 的微小面积上的剪切力为dP1=qxdx=τhdx式中 qx ——作用在接触弧AB 水平投影单位长度上的剪切力。
qx=τh 式中 τ——剪切应力 MPa h ——板厚 mm 相对切入深度由下式计算:hx αεtan 2=微分后得εαd hdx tan 2=式中 α——弦AB 与CD 间夹角的一半。
所以纯剪切力为a h d h hdx P αετατtan 2tan 2221===⎰⎰式中 a ——单位剪切功,⎰=ετd a 。
在圆盘剪上冷剪时,a 值可按下式求得5521δσδσb b K K a ==式中 K 1、K 2——换算系数,取 K 1 K 2=1b σ 、δ——被剪切钢板的强度极限(MPa)和延伸率。
P 2——钢板被剪掉部分的弯曲力,由下式计算:δαtan 112Z P P =总剪切力计算公式为)tan 1(1112δαZ P p p P +=+=系数Z l 决定于被剪掉的板边宽度与板厚的比值d /h ,参见图(9)。
图9 被剪切钢板的相对宽度d/h与系数Z1的关系由图中可知,当d/h≥15时,Z l的数值趋近于渐近线Z l=1.4。
假设合力P的作用点在弦AB和CD中间,则α可按下式求得sDDEF-=+αcos或DEFs+-=1cosα式中 s——刀片重叠量。
又hEF)21(0ε-=Dhs)21(1cosεα-+-=以板厚h=4mm,2/60mmkgb=σ为例:根据图(6),取s=0.3mm根据表(1),取ε0=0.33表(1)相对延伸率5δ和相对剪切率ε的对应值9896.03504)233.01(3.01cos=⨯-+-=α︒=271.8α由表(1),取26.05=δ,则6.15826.06105=⨯==δσb a (N ·mm/mm 3)所以纯剪切力为N a h P 87296.158271.8tan 24tan 2221=⨯︒⨯==α 总剪切力NZ P P 15561)26.0271.8tan 4.11(8729)tan 1(11=︒⨯+⨯=+=δα方法二:圆盘剪的剪切力,一般还可按诺沙里公式进行计算。
即)tan 1(tan 21552z h P b δαδσα+=对于圆盘剪可建议取525.1δε=,系数取z 1=1.4,则上式简化为:)7.04.0tan (2+=αεσb h P图10 圆盘剪刀盘上的作用力简图由图(10)可知,)21(22εε-=-=-=h h h z h GF 。