机械英文文献翻译
机械专业外文文献翻译

翻译部分英文原文High-speed machining and demand for the development ofHigh-speed machining is contemporary advanced manufacturing technology an important component of the high-efficiency, High-precision and high surface quality, and other features. This article presents the technical definition of the current state of development of China's application fields and the demand situation.High-speed machining is oriented to the 21st century a new high-tech, high-efficiency, High-precision and high surface quality as a basic feature, in the automobile industry, aerospace, Die Manufacturing and instrumentation industries gained increasingly widespread application, and has made significant technical and economic benefits. contemporary advanced manufacturing technology an important component part.HSC is to achieve high efficiency of the core technology manufacturers, intensive processes and equipment packaged so that it has a high production efficiency. It can be said that the high-speed machining is an increase in the quantity of equipment significantly improve processing efficiency essential to the technology. High-speed machining is the major advantages : improve production efficiency, improve accuracy and reduce the processing of cutting resistance.The high-speed machining of meaning, at present there is no uniform understanding, there are generally several points as follows : high cutting speed. usually faster than that of their normal cutting 5 -10 times; machine tool spindle speed high, generally spindle speed in -20000r/min above 10,000 for high-speed cutting; Feed at high velocity, usually 15 -50m/min up to 90m/min; For different cutting materials and the wiring used the tool material, high-speed cutting the meaning is not necessarily the same; Cutting process, bladed through frequency (Tooth Passing Frequency) closer to the "machine-tool - Workpiece "system the dominant natural frequency (Dominant Natural Frequency), can be considered to be high-speed cutting. Visibility high-speed machining is a comprehensive concept.1992. Germany, the Darmstadt University of Technology, Professor H. Schulz in the 52th on the increase of high-speed cutting for the concept and the scope, as shown in Figure 1. Think different cutting targets, shown in the figure of the transition area (Transition), to be what is commonly called the high-speed cutting, This is also the time of metal cutting process related to the technical staff are looking forward to, or is expected to achieve the cutting speed.High-speed machining of machine tools, knives and cutting process, and other aspects specific requirements. Several were from the following aspects : high-speed machining technology development status and trends.At this stage, in order to achieve high-speed machining, general wiring with high flexibility of high-speed CNC machine tools, machining centers, By using a dedicated high-speed milling, drilling. These equipment in common is : We must also have high-speed and high-speed spindle system feeding system, Cutting can be achieved in high-speed process. High-speed cutting with the traditional cutting the biggest difference is that "Machine-tool-workpiece" the dynamic characteristics of cutting performance is stronger influence. In the system, the machine spindle stiffness, grip or form, a long knife set, spindle Broach, torque tool set, Performance high-speed impact are important factors.In the high-speed cutting, material removal rate (Metal Removal Rate, MRR), unit time that the material was removed volume, usually based on the "machine-tool-workpiece" whether Processing System "chatter." Therefore, in order to satisfy the high-speed machining needs, we must first improve the static and dynamic stiffness of machine spindle is particularly the stiffness characteristics. HSC reason at this stage to be successful, a very crucial factor is the dynamic characteristics of the master and processing capability.In order to better describe the machine spindle stiffness characteristics of the project presented new dimensionless parameter - DN value, used for the evaluation of the machine tool spindle structure on the high-speed machining of adaptability. DN value of the so-called "axis diameter per minute speed with the product." The newly developed spindle machining center DN values have been great over one million. To reduce the weight bearing, but also with an array of steel products than to the much more light ceramic ball bearings; Bearing Lubrication most impressive manner mixed with oil lubrication methods. In the field of high-speed machining. have air bearings and the development of magnetic bearings and magnetic bearings and air bearings combined constitute the magnetic gas / air mixing spindle.Feed the machine sector, high-speed machining used in the feed drive is usually larger lead, multiple high-speed ball screw and ball array of small-diameter silicon nitride (Si3N4) ceramic ball, to reduce its centrifugal and gyroscopic torque; By using hollow-cooling technology to reduce operating at high speed ball screw as temperature generated by the friction between the lead screw and thermal deformation.In recent years, the use of linear motor-driven high-speed system of up to'' Such feed system has removed the motor from workstations to Slide in the middle of all mechanical transmission links, Implementation of Machine Tool Feed System of zero transmission. Because no linear motor rotating components, from the role of centrifugal force, can greatly increase the feed rate. Linear Motor Another major advantage of the trip is unrestricted. The linear motor is a very time for a continuous machine shop in possession of the bed. Resurfacing of the very meeting where avery early stage movement can go, but the whole system of up to the stiffness without any influence. By using high-speed screw, or linear motor can greatly enhance machine system of up to the rapid response. The maximum acceleration linear motors up to 2-10G (G for the acceleration of gravity), the largest feed rate of up to 60 -200m/min or higher.2002 world-renowned Shanghai Pudong maglev train project of maglev track steel processing, Using the Shenyang Machine Tool Group Holdings Limited McNair friendship company production plants into extra-long high-speed system for large-scale processing centers achieve . The machine feeding system for the linear guide and rack gear drive, the largest table feed rate of 60 m / min, Quick trip of 100 m / min, 2 g acceleration, maximum speed spindle 20000 r / min, the main motor power 80 kW. X-axis distance of up to 30 m, 25 m cutting long maglev track steel error is less than 0.15 mm. Maglev trains for the smooth completion of the project provided a strong guarantee for technologyIn addition, the campaign machine performance will also directly affect the processing efficiency and accuracy of processing. Mold and the free surface of high-speed machining, the main wiring with small cut deep into methods for processing. Machine requirements in the feed rate conditions, should have high-precision positioning functions andhigh-precision interpolation function, especially high-precision arc interpolation. Arc processing is to adopt legislation or thread milling cutter mold or machining parts, the essential processing methods. Cutting Tools Tool Material developmenthigh-speed cutting and technological development of the history, tool material is continuous progress of history. The representation ofhigh-speed cutting tool material is cubic boron nitride (CBN). Face Milling Cutter use of CBN, its cutting speed can be as high as 5000 m / min, mainly for the gray cast iron machining. Polycrystalline diamond (PCD) has been described as a tool of the 21st century tool, It is particularly applicable to the cutting aluminum alloy containing silica material, which is light weight metal materials, high strength, widely used in the automobile, motorcycle engine, electronic devices shell, the base, and so on. At present, the use of polycrystalline diamond cutter Face Milling alloy, 5000m/min the cutting speed has reached a practical level. In addition ceramic tool also applies to gray iron of high-speed machining; Tool Coating : CBN and diamond cutter, despite good high-speed performance, but the cost is relatively high. Using the coating technology to make cutting tool is the low price, with excellent mechanical properties, which can effectively reduce the cost. Now high-speed processing of milling cutter, with most of the wiring between the Ti-A1-N composite technology for the way of multi-processing, If present in the non-ferrous metal or alloy material dry cutting, DLC (Diamond Like Carbon) coating on thecutter was of great concern. It is expected that the market outlook is very significant;Tool clamping system : Tool clamping system to support high-speed cutting is an important technology, Currently the most widely used is a two-faced tool clamping system. Has been formally invested as a commodity market at the same clamping tool system are : HSK, KM, Bigplus. NC5, AHO systems. In the high-speed machining, tool and fixture rotary performance of the balance not only affects the precision machining and tool life. it will also affect the life of machine tools. So, the choice of tool system, it should be a balanced selection of good products.Process ParametersCutting speed of high-speed processing of conventional shear velocity of about 10 times. For every tooth cutter feed rate remained basically unchanged, to guarantee parts machining precision, surface quality and durability of the tool, Feed volume will also be a corresponding increase about 10 times, reaching 60 m / min, Some even as high as 120 m / min. Therefore, high-speed machining is usually preclude the use of high-speed, feed and depth of cut small cutting parameters. Due to the high-speed machining cutting cushion tend to be small, the formation of very thin chip light, Cutting put the heat away quickly; If the wiring using a new thermal stability better tool materials and coatings, Using the dry cutting process for high-speed machining is the ideal technology program. High-speed machining field of applicationFlexible efficient production lineTo adapt to the needs of new models, auto body panel molds andresin-prevention block the forming die. must shorten the production cycle and reduce the cost of production and, therefore, we must make great efforts to promote the production of high-speed die in the process. SAIC affiliated with the company that : Compared to the past, finishing, further precision; the same time, the surface roughness must be met, the bending of precision, this should be subject to appropriate intensive manual processing. Due to the extremely high cutting speed, and the last finishing processes, the processing cycle should be greatly reduced. To play for machining centers and boring and milling machining center category represented by the high-speed machining technology and automatic tool change function of distinctions Potential to improve processing efficiency, the processing of complex parts used to be concentrated as much as possible the wiring process, that is a fixture in achieving multiple processes centralized processing and dilute the traditional cars, milling, boring, Thread processing different cutting the limits of technology, equipment and give full play to the high-speed cutting tool function, NC is currently raising machine efficiency and speed up product development in an effective way. Therefore, the proposed multi-purpose tool of the new requirements call for a tool to complete different partsof the machining processes, ATC reduce the number of ATC to save time, to reduce the quantity and tool inventory, and management to reduce production costs. More commonly used in a multifunctional Tool, milling, boring and milling, drilling milling, drilling-milling thread-range tool. At the same time, mass production line, against the use of technology requires the development of special tools, tool or a smart composite tool, improve processing efficiency and accuracy and reduced investment. In the high-speed cutting conditions, and some special tools can be part of the processing time to the original 1 / 10 below, results are quite remarkable. HSC has a lot of advantages such as : a large number of materials required resection of the workpiece with ultrafine, thin structure of the workpiece, Traditionally, the need to spend very long hours for processing mobile workpiece and the design of rapid change, short product life cycle of the workpiece, able to demonstrate high-speed cutting brought advantages.中文译文高速切削加工的发展及需求高速切削加工是当代先进制造技术的重要组成部分,拥有高效率、高精度及高表面质量等特征。
机械外文翻译外文文献英文文献机械臂动力学与控制的研究

外文出处:Ellekilde, L. -., & Christensen, H. I. (2009). Control of mobile manipulator using the dynamical systems approach. Robotics and Automation, Icra 09, IEEE International Conference on (pp.1370 - 1376). IEEE.机械臂动力学与控制的研究拉斯彼得Ellekilde摘要操作器和移动平台的组合提供了一种可用于广泛应用程序高效灵活的操作系统,特别是在服务性机器人领域。
在机械臂众多挑战中其中之一是确保机器人在潜在的动态环境中安全工作控制系统的设计。
在本文中,我们将介绍移动机械臂用动力学系统方法被控制的使用方法。
该方法是一种二级方法, 是使用竞争动力学对于统筹协调优化移动平台以及较低层次的融合避障和目标捕获行为的方法。
I介绍在过去的几十年里大多数机器人的研究主要关注在移动平台或操作系统,并且在这两个领域取得了许多可喜的成绩。
今天的新挑战之一是将这两个领域组合在一起形成具有高效移动和有能力操作环境的系统。
特别是服务性机器人将会在这一方面系统需求的增加。
大多数西方国家的人口统计数量显示需要照顾的老人在不断增加,尽管将有很少的工作实际的支持他们。
这就需要增强服务业的自动化程度,因此机器人能够在室内动态环境中安全的工作是最基本的。
图、1 一台由赛格威RMP200和轻重量型库卡机器人组成的平台这项工作平台用于如图1所示,是由一个Segway与一家机器人制造商制造的RMP200轻机器人。
其有一个相对较小的轨迹和高机动性能的平台使它适应在室内环境移动。
库卡工业机器人具有较长的长臂和高有效载荷比自身的重量,从而使其适合移动操作。
当控制移动机械臂系统时,有一个选择是是否考虑一个或两个系统的实体。
在参考文献[1]和[2]中是根据雅可比理论将机械手末端和移动平台结合在一起形成一个单一的控制系统。
流体 机械 外文翻译 外文文献 英文文献
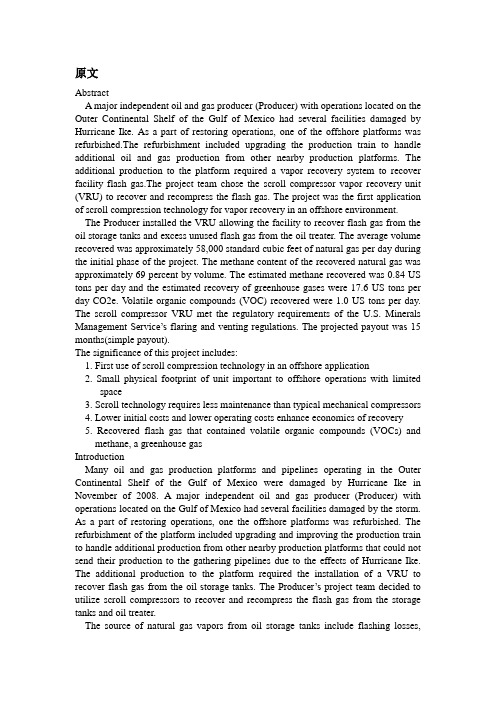
原文AbstractA major independent oil and gas producer (Producer) with operations located on the Outer Continental Shelf of the Gulf of Mexico had several facilities damaged by Hurricane Ike. As a part of restoring operations, one of the offshore platforms was refurbished.The refurbishment included upgrading the production train to handle additional oil and gas production from other nearby production platforms. The additional production to the platform required a vapor recovery system to recover facility flash gas.The project team chose the scroll compressor vapor recovery unit (VRU) to recover and recompress the flash gas. The project was the first application of scroll compression technology for vapor recovery in an offshore environment.The Producer installed the VRU allowing the facility to recover flash gas from the oil storage tanks and excess unused flash gas from the oil treater. The average volume recovered was approximately 58,000 standard cubic feet of natural gas per day during the initial phase of the project. The methane content of the recovered natural gas was approximately 69 percent by volume. The estimated methane recovered was 0.84 US tons per day and the estimated recovery of greenhouse gases were 17.6 US tons per day CO2e. V olatile organic compounds (VOC) recovered were 1.0 US tons per day. The scroll compressor VRU met the regulatory requirements of the U.S. Minerals Management Service’s flaring and venting regulations. The projected payout was 15 months(simple payout).The significance of this project includes:1. First use of scroll compression technology in an offshore application2. Small physical footprint of unit important to offshore operations with limitedspace3. Scroll technology requires less maintenance than typical mechanical compressors4. Lower initial costs and lower operating costs enhance economics of recovery5. Recovered flash gas that contained volatile organic compounds (VOCs) andmethane, a greenhouse gasIntroductionMany oil and gas production platforms and pipelines operating in the Outer Continental Shelf of the Gulf of Mexico were damaged by Hurricane Ike in November of 2008. A major independent oil and gas producer (Producer) with operations located on the Gulf of Mexico had several facilities damaged by the storm. As a part of restoring operations, one the offshore platforms was refurbished. The refurbishment of the platform included upgrading and improving the production train to handle additional production from other nearby production platforms that could not send their production to the gathering pipelines due to the effects of Hurricane Ike. The additional production to the platform required the installation of a VRU to recover flash gas from the oil storage tanks. The Producer’s project team decided to utilize scroll compressors to recover and recompress the flash gas from the storage tanks and oil treater.The source of natural gas vapors from oil storage tanks include flashing losses,working losses and breathing losses. Flashing for a pressure vessel (e.g., separator, heater treater) or oil storage tank occurs when the crude oil or condensate with dissolved gases moves from a higher pressure to a lower pressure. As the pressure of the oil drops some of the lighter components dissolved in the oil are released or “flashed.” Working losses are due to displacement of the natural gas vapors within the storage tank vapor space as a tank is filled. Breathing losses are due to displacement of natural gas vapor within the storage tank vapor space due to changes in the tank temperature and pressure throughout the day. For this paper we refer to the vent gas from the oil storage tanks collectively as flash gas.Often flash gases from offshore production platforms are either vented directly to the atmosphere or burned by a flare. Historically VRUs have been used to recover flash gas when there is sufficient quantity to justify the investment and to meet air emission standards. The typical type of vapor recovery compressors used for vent flash gas has been natural gas driven rotary screw compressors and rotary vane compressors.The United States Minerals Management Service (MMS) is the regulatory agency with jurisdiction over venting of natural gas in the central and western areas of the Gulf of Mexico. MMS regulations require a facility to recover natural gas volumes over 50,000 standard cubic feet per day rather than venting directly to the atmosphere or burning in a flare. For offshore production platforms, deck space requirements are a significant consideration for vapor recovery units. To accommodate this limitation, the scroll compressor package has a footprint one-third the size of a traditional VRUs used. In addition, lower overall maintenance costs were a significant factor in the decision to utilize scroll compressor technology. The scroll compressor requires oil changes once per year compared to quarterly for the typical mechanical compressor. Equipment used in the offshore environment required capital upgrades to the typical onshore compression package due to the saltwater corrosive environment and additional safety controls required for operating offshore. For this project the standard onshore VRU was upgraded to meet specifications for the offshore conditions and regulations.Description and Application of Equipment and ProcessesScroll Compression Technology.Scroll compression technology is a positive displacement machine that uses two interleaved spiral-shaped scrolls to compress natural gas. With scroll compression technology, one of the scrolls is fixed, while the other orbits eccentrically, thereby trapping and pumping or compressing gas between through successively smaller scroll volume “pockets” until the gas reaches maximum pressure at the center. At the center, the gas is released through a discharge point in the fixed scroll. Compression is continuous since during orbit of the orbiting scroll, multiple gas pockets are compressed simultaneously.The driver for the compressor is an electric motor. The scroll compressor is a hermetic compressor designed for use with high-pressure refrigerants. It has a broad range of operation and is intrinsically leak free. Scroll compressor technology has been widely used in cooling system applications.The scroll compressor VRU installed had a horizontal design that has a low profile, low noise, low vibration, and uses variable speed control motors. Depending on the application, the range of inlet pressures of gas to the scroll compressor VRUs may vary from -10.4 to 101.3 pounds per square inch gage and the discharge pressures can range from 43.5 to 363 pounds per square inch gage. The compression ratio ranges from 3 to 15.Scroll compression technology has been used in oil and gas vapor recovery applications since 2004.Application of Scroll Technology.In May of 2009, COMM and the Producer began working together to modify a typical onshore scroll compressor VRU for the platform that was damaged and being refurbished.The scroll compressor VRU consisted of two stacked modules each 8-foot long by 4-foot wide by 4-foot high steel skids each with an inlet gas scrubber. Each module contained two 15-horsepower scroll compressors and an aftercooler. Each module also included a control panel with Programmable Logic Control (PLC) and variable frequency drive (VFD). The design recovery capacity of this twin module package used was 200,000 standard cubic feet per day.A suction line connected to the oil storage tanks’ common vent and to the oil treater (i.e., heater treater) vent was installed to the inlet scrubber of the scroll compressor VRU. The suction line to the oil treater was used to collect excess gas from the oil treater that was not used as platform fuel gas. A flow meter was placed on the suction line prior to the inlet of the scroll compressor VRU to measure the amount of natural gas recovered. The discharge of the scroll compressor package was piped to the suction separator/scrubber of the onsite main compressor. This main compressor compresses natural gas for ultimate injection into the sales pipeline.A purge gas system was installed and used to recycle gas through the scroll compressor VRU when there is insufficient pressure from flash gas in the storage tanks. The purpose of the purge gas system is to keep VRU operating to maintain the scroll compressor’s oil temperature at a minimum of 235 degrees Fahrenheit. By maintaining the oil temperature at or above 235 degrees F, the flash gas will remain in a gas phase.As a safety measure, a blanket gas system was installed on the storage tanks to maintain approximately 0.5 ounce per square inch of pressure on the tanks to keep oxygen from entering the tanks.Figure 1 contains a simplified process flow for the VRU.The control panels with VFD’s were located in the motor control center (MCC) and wiring was run to the scroll compressor VRU which was located on a lower deck of the platform.Functionally, the scroll compressor operates normally in the recycle mode at 2400 revolutions per minute (rpm). When the pressure builds in the oil storage tanks, a pressure transmitter sends a signal enabling the speed of the compressor to increase to 4800 rpms and the flash gas is recovered and compressed. Once the flash gas from the storage tanks is recovered and the pressure drops in the storage tanks, the VFD rampsthe compressor speed down to 2400 rpms. Then the VRU is in recycle mode again. Any liquids recovered by the gas scrubber are pumped back to the oil storage tanks. Modifications to VRU Package.To meet offshore specification, the structural components of the scroll compressor package were already hot dipped galvanized and suitable for offshore installation but other components required refinishing to withstand the corrosive saltwater environment. The compressors and several other components were removed from the modules and specially coated with a three part epoxy coating to withstand the corrosive environment.In addition to the special coatings needed for offshore, there was a number of safety system modifications needed to make the scroll compressor VRU compliant with the United States Minerals Management Service (MMS) regulations. Offshore operators are required to abide by the American Petroleum Institute (API) Recommended Practices 14C (RP 14C). API RP 14C contains the criteria for designing, installing and testing a safety system on an offshore platform. It identifies each undesirable event that could affect a process component and discusses safety device selection criteria for each component type.Failure to meet RP 14C requirements can result in fines to the operators and in some cases, require an interruption of production which could result in losses of income to the operator until compliance is restored.Specifically, the modifications in response to RP-14C were:1. Installation of test circuit for monthly testing of high level alarm/shutdown on the gas scrubber2. Installation of test circuit for monthly testing of high discharge pressurealarm/shutdown on compressor discharge line3. Installation of test circuit for monthly testing of low pressure alarm/shutdown on oil storage tanks4. Addition on redundant oil storage tank pressure transmitter. Installation of test circuit for monthly testing of high pressure alarm/shutdown on oil storage tanks. Additionally, the Producer’s offshore specifications required the repla cement of several valves to steel construction rather than brass.The scroll compressor VRU was shipped to the platform in July 2009. The interconnecting piping to and from the scroll compressor VRU was completed in August 2009. Once the installation was completed and the platform was placed into operation, the scroll compressor VRU was brought into operation.Presentation of Data and ResultsFor this installation, the scroll compressor VRU had an average recovery of tank flash gas over the initial operating period of 58,000 standard cubic feet per day. Thepeak flowrate documented was 215,000 standard cubic feet of flash gas per day. A sample of the recovered flash gas that was chemically analyzed had a molecular weight of 26.6 and contained approximately 69 percent by volume of methane. V olatile organic compounds (nonmethane, nonethane hydrocarbons) amounted to approximately 29 percent by volume. The higher heating value was approximately 1540 British Thermal Units (BTU) per standard cubic feet.The hydrogen sulfide content of the flash gas was considered de minimus based on the facility processing sweet natural gas.The calculated simple payout of this scroll compressor VRU based on the average recovery and gas price of USD 5/MMBTU is 15 months.The estimated methane emissions recovered were 0.84 US tons per day and the estimated recovery of greenhouse gases were 17.6 US tons per day CO2e. V olatile organic compound (VOC) emissions recovered were 1.0 US tons per day.The Producer is in the process of modifying the scroll compressor VRU control system. These modifications include the installation of a single programmable logic controller (PLC) to control both modules, replacement of pressure switches with transmitters and the installation of a touch screen control panel next to the VRU. The modifications are needed to meet the Producer’s operating standards. The cost of this modification will result in an extra initial cost of USD 8,000.ConclusionsThe application of scroll based compression technology in the harsh offshore environment is a cost effective and most efficient solution for vapor recovery. By utilizing scroll compression technology for vapor recovery, offshore operators can meet regulatory requirements to reduce emissions, improve their carbon footprint and economically recover flash gas.AcknowledgmentsOur sincerest thanks go to Mr. James Welsh and Mr. Ron Damron for their expertise and diligence in making this project successful.Reference List1. Emerson Climate Technologies. April 2008. A Hermetic Scroll Compressor For Application To High Heat-Of-Compression Gases,/oil_gas/PDF/HermeticScrollCompressorWhitePap er.pdf.2. RP 14C, Recommended Practice for Analysis, Design, Installation and Testing of Basic Surface Safety Systems on Offshore Production Platforms, sixth edition. March 1998. Washington, DC: API.第一篇:在海上生产平台上使用滚动压缩技术回收储存罐内闪发气体G.B.(比尔)施耐德,SPE, 布莱恩E. 博耶,SPE,马克A.古德伊尔,商科工程摘要位于墨西哥湾外大陆架的一个独立的石油天然气生产操作遭到飓风艾克的袭击并损坏了一些设施。
Manufacturing Engineering and Technology(机械类英文文献+翻译)

Manufacturing Engineering and Technology—MachiningSerope kalpakjian;Steven R.Schmid机械工业出版社2004年3月第1版20.9 MACHINABILITYThe machinability of a material usually defined in terms of four factors:1、Surface finish and integrity of the machined part;2、Tool life obtained;3、Force and power requirements;4、Chip control.Thus, good machinability good surface finish and integrity, long tool life, and low force And power requirements. As for chip control, long and thin (stringy) cured chips, if not broken up, can severely interfere with the cutting operation by becoming entangled in the cutting zone.Because of the complex nature of cutting operations, it is difficult to establish relationships that quantitatively define the machinability of a material. In manufacturing plants, tool life and surface roughness are generally considered to be the most important factors in machinability. Although not used much any more, approximate machinability ratings are available in the example below.20.9.1 Machinability Of SteelsBecause steels are among the most important engineering materials (as noted in Chapter 5), their machinability has been studied extensively. The machinability of steels has been mainly improved by adding lead and sulfur to obtain so-called free-machining steels.Resulfurized and Rephosphorized steels. Sulfur in steels forms manganese sulfide inclusions (second-phase particles), which act as stress raisers in the primary shear zone. As a result, the chips produced break up easily and are small; this improves machinability. The size, shape, distribution, and concentration of these inclusions significantly influence machinability. Elements such as tellurium and selenium, which are both chemically similar to sulfur, act as inclusion modifiers inresulfurized steels.Phosphorus in steels has two major effects. It strengthens the ferrite, causing increased hardness. Harder steels result in better chip formation and surface finish. Note that soft steels can be difficult to machine, with built-up edge formation and poor surface finish. The second effect is that increased hardness causes the formation of short chips instead of continuous stringy ones, thereby improving machinability.Leaded Steels. A high percentage of lead in steels solidifies at the tip of manganese sulfide inclusions. In non-resulfurized grades of steel, lead takes the form of dispersed fine particles. Lead is insoluble in iron, copper, and alumin um and their alloys. Because of its low shear strength, therefore, lead acts as a solid lubricant (Section 32.11) and is smeared over the tool-chip interface du ring cutting. This behavior has been verified by the presence of high concentra tions of lead on the tool-side face of chips when machining leaded steels.When the temperature is sufficiently high-for instance, at high cutting spee ds and feeds (Section 20.6)—the lead melts directly in front of the tool, acting as a liquid lubricant. In addition to this effect, lead lowers the shear stress in the primary shear zone, reducing cutting forces and power consumption. Lead can be used in every grade of steel, such as 10xx, 11xx, 12xx, 41xx, etc. Le aded steels are identified by the letter L between the second and third numeral s (for example, 10L45). (Note that in stainless steels, similar use of the letter L means “low carbon,”a condition that improves their corrosion resistance.)However, because lead is a well-known toxin and a pollutant, there are se rious environmental concerns about its use in steels (estimated at 4500 tons of lead consumption every year in the production of steels). Consequently, there is a continuing trend toward eliminating the use of lead in steels (lead-free ste els). Bismuth and tin are now being investigated as possible substitutes for lea d in steels.Calcium-Deoxidized Steels. An important development is calcium-deoxidize d steels, in which oxide flakes of calcium silicates (CaSo) are formed. These f lakes, in turn, reduce the strength of the secondary shear zone, decreasing tool-chip interface and wear. Temperature is correspondingly reduced. Consequently, these steels produce less crater wear, especially at high cutting speeds.Stainless Steels. Austenitic (300 series) steels are generally difficult to mac hine. Chatter can be s problem, necessitating machine tools with high stiffness. However, ferritic stainless steels (also 300 series) have good machinability. M artensitic (400 series) steels are abrasive, tend to form a built-up edge, and req uire tool materials with high hot hardness and crater-wear resistance. Precipitati on-hardening stainless steels are strong and abrasive, requiring hard and abrasio n-resistant tool materials.The Effects of Other Elements in Steels on Machinability. The presence of aluminum and silicon in steels is always harmful because these elements com bine with oxygen to form aluminum oxide and silicates, which are hard and a brasive. These compounds increase tool wear and reduce machinability. It is es sential to produce and use clean steels.Carbon and manganese have various effects on the machinability of steels, depending on their composition. Plain low-carbon steels (less than 0.15% C) c an produce poor surface finish by forming a built-up edge. Cast steels are mor e abrasive, although their machinability is similar to that of wrought steels. To ol and die steels are very difficult to machine and usually require annealing pr ior to machining. Machinability of most steels is improved by cold working, w hich hardens the material and reduces the tendency for built-up edge formation.Other alloying elements, such as nickel, chromium, molybdenum, and vana dium, which improve the properties of steels, generally reduce machinability. T he effect of boron is negligible. Gaseous elements such as hydrogen and nitrog en can have particularly detrimental effects on the properties of steel. Oxygen has been shown to have a strong effect on the aspect ratio of the manganese sulfide inclusions; the higher the oxygen content, the lower the aspect ratio an d the higher the machinability.In selecting various elements to improve machinability, we should consider the possible detrimental effects of these elements on the properties and strengt h of the machined part in service. At elevated temperatures, for example, lead causes embrittlement of steels (liquid-metal embrittlement, hot shortness; see Se ction 1.4.3), although at room temperature it has no effect on mechanical prop erties.Sulfur can severely reduce the hot workability of steels, because of the fo rmation of iron sulfide, unless sufficient manganese is present to prevent such formation. At room temperature, the mechanical properties of resulfurized steels depend on the orientation of the deformed manganese sulfide inclusions (aniso tropy). Rephosphorized steels are significantly less ductile, and are produced so lely to improve machinability.20.9.2 Machinability of Various Other MetalsAluminum is generally very easy to machine, although the softer grades te nd to form a built-up edge, resulting in poor surface finish. High cutting speed s, high rake angles, and high relief angles are recommended. Wrought aluminu m alloys with high silicon content and cast aluminum alloys may be abrasive; they require harder tool materials. Dimensional tolerance control may be a pro blem in machining aluminum, since it has a high thermal coefficient of expans ion and a relatively low elastic modulus.Beryllium is similar to cast irons. Because it is more abrasive and toxic, t hough, it requires machining in a controlled environment.Cast gray irons are generally machinable but are. Free carbides in castings reduce their machinability and cause tool chipping or fracture, necessitating to ols with high toughness. Nodular and malleable irons are machinable with hard tool materials.Cobalt-based alloys are abrasive and highly work-hardening. They require sharp, abrasion-resistant tool materials and low feeds and speeds.Wrought copper can be difficult to machine because of built-up edge form ation, although cast copper alloys are easy to machine. Brasses are easy to ma chine, especially with the addition pf lead (leaded free-machining brass). Bronz es are more difficult to machine than brass.Magnesium is very easy to machine, with good surface finish and prolong ed tool life. However care should be exercised because of its high rate of oxi dation and the danger of fire (the element is pyrophoric).Molybdenum is ductile and work-hardening, so it can produce poor surfac e finish. Sharp tools are necessary.Nickel-based alloys are work-hardening, abrasive, and strong at high tempe ratures. Their machinability is similar to that of stainless steels.Tantalum is very work-hardening, ductile, and soft. It produces a poor surf ace finish; tool wear is high.Titanium and its alloys have poor thermal conductivity (indeed, the lowest of all metals), causing significant temperature rise and built-up edge; they can be difficult to machine.Tungsten is brittle, strong, and very abrasive, so its machinability is low, although it greatly improves at elevated temperatures.Zirconium has good machinability. It requires a coolant-type cutting fluid, however, because of the explosion and fire.20.9.3 Machinability of Various MaterialsGraphite is abrasive; it requires hard, abrasion-resistant, sharp tools.Thermoplastics generally have low thermal conductivity, low elastic modul us, and low softening temperature. Consequently, machining them requires tools with positive rake angles (to reduce cutting forces), large relief angles, small depths of cut and feed, relatively high speeds, and proper support of the work piece. Tools should be sharp.External cooling of the cutting zone may be necessary to keep the chips f rom becoming “gummy”and sticking to the tools. Cooling can usually be achi eved with a jet of air, vapor mist, or water-soluble oils. Residual stresses may develop during machining. To relieve these stresses, machined parts can be an nealed for a period of time at temperatures ranging from to ( to ), and then cooled slowly and uniformly to room temperature.Thermosetting plastics are brittle and sensitive to thermal gradients during cutting. Their machinability is generally similar to that of thermoplastics.Because of the fibers present, reinforced plastics are very abrasive and are difficult to machine. Fiber tearing, pulling, and edge delamination are significa nt problems; they can lead to severe reduction in the load-carrying capacity of the component. Furthermore, machining of these materials requires careful rem oval of machining debris to avoid contact with and inhaling of the fibers.The machinability of ceramics has improved steadily with the development of nanoceramics (Section 8.2.5) and with the selection of appropriate processi ng parameters, such as ductile-regime cutting (Section 22.4.2).Metal-matrix and ceramic-matrix composites can be difficult to machine, d epending on the properties of the individual components, i.e., reinforcing or wh iskers, as well as the matrix material.20.9.4 Thermally Assisted MachiningMetals and alloys that are difficult to machine at room temperature can be machined more easily at elevated temperatures. In thermally assisted machinin g (hot machining), the source of heat—a torch, induction coil, high-energy bea m (such as laser or electron beam), or plasma arc—is forces, (b) increased too l life, (c) use of inexpensive cutting-tool materials, (d) higher material-removal rates, and (e) reduced tendency for vibration and chatter.It may be difficult to heat and maintain a uniform temperature distribution within the workpiece. Also, the original microstructure of the workpiece may be adversely affected by elevated temperatures. Most applications of hot machi ning are in the turning of high-strength metals and alloys, although experiment s are in progress to machine ceramics such as silicon nitride.SUMMARYMachinability is usually defined in terms of surface finish, tool life, force and power requirements, and chip control. Machinability of materials depends n ot only on their intrinsic properties and microstructure, but also on proper sele ction and control of process variables.20.9 可机加工性一种材料的可机加工性通常以四种因素的方式定义:1、分的表面光洁性和表面完整性。
机械手臂外文文献翻译、中英文翻译、外文翻译

外文出处:《Manufacturing Engineering and Technology—Machining》附件1:外文原文ManipulatorRobot developed in recent decades as high-tech automated production equipment. I ndustrial robot is an important branch of industrial robots. It features can be program med to perform tasks in a variety of expectations, in both structure and performance a dvantages of their own people and machines, in particular, reflects the people's intellig ence and adaptability. The accuracy of robot operations and a variety of environments the ability to complete the work in the field of national economy and there are broad p rospects for development. With the development of industrial automation, there has be en CNC machining center, it is in reducing labor intensity, while greatly improved lab or productivity. However, the upper and lower common in CNC machining processes material, usually still use manual or traditional relay-controlled semi-automatic device . The former time-consuming and labor intensive, inefficient; the latter due to design c omplexity, require more relays, wiring complexity, vulnerability to body vibration inte rference, while the existence of poor reliability, fault more maintenance problems and other issues. Programmable Logic Controller PLC-controlled robot control system for materials up and down movement is simple, circuit design is reasonable, with a stron g anti-jamming capability, ensuring the system's reliability, reduced maintenance rate, and improve work efficiency. Robot technology related to mechanics, mechanics, elec trical hydraulic technology, automatic control technology, sensor technology and com puter technology and other fields of science, is a cross-disciplinary integrated technol ogy.First, an overview of industrial manipulatorRobot is a kind of positioning control can be automated and can be re-programmed to change in multi-functional machine, which has multiple degrees of freedom can be used to carry an object in order to complete the work in different environments. Low wages in China, plastic products industry, although still a labor-intensive, mechanical hand use has become increasingly popular. Electronics and automotive industries thatEurope and the United States multinational companies very early in their factories in China, the introduction of automated production. But now the changes are those found in industrial-intensive South China, East China's coastal areas, local plastic processin g plants have also emerged in mechanical watches began to become increasingly inter ested in, because they have to face a high turnover rate of workers, as well as for the workers to pay work-related injuries fee challenges.With the rapid development of China's industrial production, especially the reform and opening up after the rapid increase in the degree of automation to achieve the wor kpiece handling, steering, transmission or operation of brazing, spray gun, wrenches a nd other tools for processing and assembly operations since, which has more and mor e attracted our attention. Robot is to imitate the manual part of the action, according to a given program, track and requirements for automatic capture, handling or operation of the automatic mechanical devices.In real life, you will find this a problem. In the machine shop, the processing of part s loading time is not annoying, and labor productivity is not high, the cost of producti on major, and sometimes man-made incidents will occur, resulting in processing were injured. Think about what could replace it with the processing time of a tour as long a s there are a few people, and can operate 24 hours saturated human right? The answer is yes, but the robot can come to replace it.Production of mechanical hand can increase the automation level of production and labor productivity; can reduce labor intensity, ensuring product quality, to achieve saf e production; particularly in the high-temperature, high pressure, low temperature, lo w pressure, dust, explosive, toxic and radioactive gases such as poor environment can replace the normal working people. Here I would like to think of designing a robot to be used in actual production.Why would a robot designed to provide a pneumatic power: pneumatic robot refers to the compressed air as power source-driven robot. With pressure-driven and other en ergy-driven comparison have the following advantages: 1. Air inexhaustible, used late r discharged into the atmosphere, does not require recycling and disposal, do not pollu te the environment. (Concept of environmental protection) 2. Air stick is small, the pipeline pressure loss is small (typically less than asphalt gas path pressure drop of one-thousandth), to facilitate long-distance transport. 3. Compressed air of the working pre ssure is low (usually 4 to 8 kg / per square centimeter), and therefore moving the mate rial components and manufacturing accuracy requirements can be lowered. 4. With th e hydraulic transmission, compared to its faster action and reaction, which is one of th e advantages pneumatic outstanding. 5. The air cleaner media, it will not degenerate, n ot easy to plug the pipeline. But there are also places where it fly in the ointment: 1. A s the compressibility of air, resulting in poor aerodynamic stability of the work, resulti ng in the implementing agencies as the precision of the velocity and not easily control led. 2. As the use of low atmospheric pressure, the output power can not be too large; i n order to increase the output power is bound to the structure of the entire pneumatic s ystem size increased.With pneumatic drive and compare with other energy sources drive has the followin g advantages:Air inexhaustible, used later discharged into the atmosphere, without recycling and disposal, do not pollute the environment. Accidental or a small amount of leakage wo uld not be a serious impact on production. Viscosity of air is small, the pipeline pressu re loss also is very small, easy long-distance transport.The lower working pressure of compressed air, pneumatic components and therefor e the material and manufacturing accuracy requirements can be lowered. In general, re ciprocating thrust in 1 to 2 tons pneumatic economy is better.Compared with the hydraulic transmission, and its faster action and reaction, which is one of the outstanding merits of pneumatic.Clean air medium, it will not degenerate, not easy to plug the pipeline. It can be saf ely used in flammable, explosive and the dust big occasions. Also easy to realize auto matic overload protection.Second, the composition, mechanical handRobot in the form of a variety of forms, some relatively simple, some more complic ated, but the basic form is the same as the composition of the , Usually by the implem enting agencies, transmission systems, control systems and auxiliary devices composed.1.Implementing agenciesManipulator executing agency by the hands, wrists, arms, pillars. Hands are crawlin g institutions, is used to clamp and release the workpiece, and similar to human finger s, to complete the staffing of similar actions. Wrist and fingers and the arm connecting the components can be up and down, left, and rotary movement. A simple mechanical hand can not wrist. Pillars used to support the arm can also be made mobile as needed .2. TransmissionThe actuator to be achieved by the transmission system. Sub-transmission system c ommonly used manipulator mechanical transmission, hydraulic transmission, pneuma tic and electric power transmission and other drive several forms.3. Control SystemManipulator control system's main role is to control the robot according to certain p rocedures, direction, position, speed of action, a simple mechanical hand is generally not set up a dedicated control system, using only trip switches, relays, control valves a nd circuits can be achieved dynamic drive system control, so that implementing agenc ies according to the requirements of action. Action will have to use complex program mable robot controller, the micro-computer control.Three, mechanical hand classification and characteristicsRobots are generally divided into three categories: the first is the general machinery does not require manual hand. It is an independent not affiliated with a particular host device. It can be programmed according to the needs of the task to complete the oper ation of the provisions. It is characterized with ordinary mechanical performance, also has general machinery, memory, intelligence ternary machinery. The second category is the need to manually do it, called the operation of aircraft. It originated in the atom, military industry, first through the operation of machines to complete a particular job, and later developed to operate using radio signals to carry out detecting machines suc h as the Moon. Used in industrial manipulator also fall into this category. The third cat egory is dedicated manipulator, the main subsidiary of the automatic machines or automatic lines, to solve the machine up and down the workpiece material and delivery. T his mechanical hand in foreign countries known as the "Mechanical Hand", which is t he host of services, from the host-driven; exception of a few outside the working proc edures are generally fixed, and therefore special.Main features:First, mechanical hand (the upper and lower material robot, assembly robot, handlin g robot, stacking robot, help robot, vacuum handling machines, vacuum suction crane, labor-saving spreader, pneumatic balancer, etc.).Second, cantilever cranes (cantilever crane, electric chain hoist crane, air balance th e hanging, etc.)Third, rail-type transport system (hanging rail, light rail, single girder cranes, doubl e-beam crane)Four, industrial machinery, application of handManipulator in the mechanization and automation of the production process develo ped a new type of device. In recent years, as electronic technology, especially comput er extensive use of robot development and production of high-tech fields has become a rapidly developed a new technology, which further promoted the development of ro bot, allowing robot to better achieved with the combination of mechanization and auto mation.Although the robot is not as flexible as staff, but it has to the continuous duplication of work and labor, I do not know fatigue, not afraid of danger, the power snatch weig ht characteristics when compared with manual large, therefore, mechanical hand has b een of great importance to many sectors, and increasingly has been applied widely, for example:(1) Machining the workpiece loading and unloading, especially in the automatic lat he, combination machine tool use is more common.(2) In the assembly operations are widely used in the electronics industry, it can be used to assemble printed circuit boards, in the machinery industry It can be used to ass emble parts and components.(3) The working conditions may be poor, monotonous, repetitive easy to sub-fatigue working environment to replace human labor.(4) May be in dangerous situations, such as military goods handling, dangerous go ods and hazardous materials removal and so on..(5) Universe and ocean development.(6), military engineering and biomedical research and testing.Help mechanical hands: also known as the balancer, balance suspended, labor-saving spreader, manual Transfer machine is a kind of weightlessness of manual load system, a novel, time-saving technology for material handling operations booster equipment, belonging to kinds of non-standard design of series products. Customer application ne eds, creating customized cases. Manual operation of a simulation of the automatic ma chinery, it can be a fixed program draws ﹑ handling objects or perform household to ols to accomplish certain specific actions. Application of robot can replace the people engaged in monotonous ﹑ repetitive or heavy manual labor, the mechanization and a utomation of production, instead of people in hazardous environments manual operati on, improving working conditions and ensure personal safety. The late 20th century, 4 0, the United States atomic energy experiments, the first use of radioactive material ha ndling robot, human robot in a safe room to manipulate various operations and experi mentation. 50 years later, manipulator and gradually extended to industrial production sector, for the temperatures, polluted areas, and loading and unloading to take place t he work piece material, but also as an auxiliary device in automatic machine tools, ma chine tools, automatic production lines and processing center applications, the comple tion of the upper and lower material, or From the library take place knife knife and so on according to fixed procedures for the replacement operation. Robot body mainly b y the hand and sports institutions. Agencies with the use of hands and operation of obj ects of different occasions, often there are clamping ﹑ support and adsorption type of care. Movement organs are generally hydraulic pneumatic ﹑﹑ electrical device dri vers. Manipulator can be achieved independently retractable ﹑ rotation and lifting m ovements, generally 2 to 3 degrees of freedom. Robots are widely used in metallurgic al industry, machinery manufacture, light industry and atomic energy sectors.Can mimic some of the staff and arm motor function, a fixd procedure for the capture, handling objects or operating tools, automatic operation device. It can replace hum an labor in order to achieve the production of heavy mechanization and automation th at can operate in hazardous environments to protect the personal safety, which is wide ly used in machinery manufacturing, metallurgy, electronics, light industry and nuclea r power sectors. Mechanical hand tools or other equipment commonly used for additio nal devices, such as the automatic machines or automatic production line handling an d transmission of the workpiece, the replacement of cutting tools in machining centers , etc. generally do not have a separate control device. Some operating devices require direct manipulation by humans; such as the atomic energy sector performs household hazardous materials used in the master-slave manipulator is also often referred to as m echanical hand.Manipulator mainly by hand and sports institutions. Task of hand is holding the wor kpiece (or tool) components, according to grasping objects by shape, size, weight, mat erial and operational requirements of a variety of structural forms, such as clamp type, type and adsorption-based care such as holding. Sports organizations, so that the com pletion of a variety of hand rotation (swing), mobile or compound movements to achie ve the required action, to change the location of objects by grasping and posture. Robot is the automated production of a kind used in the process of crawling and mo ving piece features automatic device, which is mechanized and automated production process developed a new type of device. In recent years, as electronic technology, esp ecially computer extensive use of robot development and production of high-tech fiel ds has become a rapidly developed a new technology, which further promoted the dev elopment of robot, allowing robot to better achieved with the combination of mechani zation and automation. Robot can replace humans completed the risk of duplication of boring work, to reduce human labor intensity and improve labor productivity. Manipu lator has been applied more and more widely, in the machinery industry, it can be use d for parts assembly, work piece handling, loading and unloading, particularly in the a utomation of CNC machine tools, modular machine tools more commonly used. At pr esent, the robot has developed into a FMS flexible manufacturing systems and flexibl e manufacturing cell in an important component of the FMC. The machine tool equipment and machinery in hand together constitute a flexible manufacturing system or a f lexible manufacturing cell, it was adapted to small and medium volume production, y ou can save a huge amount of the work piece conveyor device, compact, and adaptabl e. When the work piece changes, flexible production system is very easy to change wi ll help enterprises to continuously update the marketable variety, improve product qua lity, and better adapt to market competition. At present, China's industrial robot techno logy and its engineering application level and comparable to foreign countries there is a certain distance, application and industrialization of the size of the low level of robo t research and development of a direct impact on raising the level of automation in Ch ina, from the economy, technical considerations are very necessary. Therefore, the stu dy of mechanical hand design is very meaningful.附件1:外文资料翻译译文机械手机械手是近几十年发展起来的一种高科技自动化生产设备。
机械手臂应用领域的外文文献以及翻译

机械手臂应用领域的外文文献以及翻译1. Introduction机械手臂是一种用于执行各种任务的自动化设备,其应用领域广泛。
本文档提供了一些关于机械手臂应用领域的外文文献,并附有简要的翻译。
2. 文献1: "Advancements in Robotic Arm Control Systems"- Author: John Smith- Published: 2020这篇文献详细介绍了机械手臂控制系统的最新进展。
作者讨论了各种控制算法、传感器和执行器的应用,以提高机械手臂的性能和精确度。
3. 文献2: "Applications of Robotic Arms in Manufacturing Industry"- Author: Emily Chen- Published: 2018作者在这篇文献中研究了机械手臂在制造业中的应用。
她列举了多个实例,包括机械手臂在装配、焊接和搬运等任务中的应用,以及通过使用机械手臂能够提高生产效率和质量的案例。
4. 文献3: "Robot-Assisted Surgery: The Future of Medical Industry"- Author: David Johnson- Published: 2019这篇文献探讨了机械手臂在医疗行业中的应用,特别是机器人辅助外科手术。
作者解释了机械手臂在手术过程中的优势,包括更小的切口、更高的精确度和减少术后恢复时间等方面。
5. 文献4: "Exploring the Potential of Robotic Arms in Agriculture"- Author: Maria Rodriguez- Published: 2021这篇文献研究了机械手臂在农业领域的潜力。
作者探讨了机械手臂在种植、收割和除草等农业任务中的应用,以及如何通过机械化技术改善农业生产的效率和可持续性。
机械工程专业外文文献及翻译
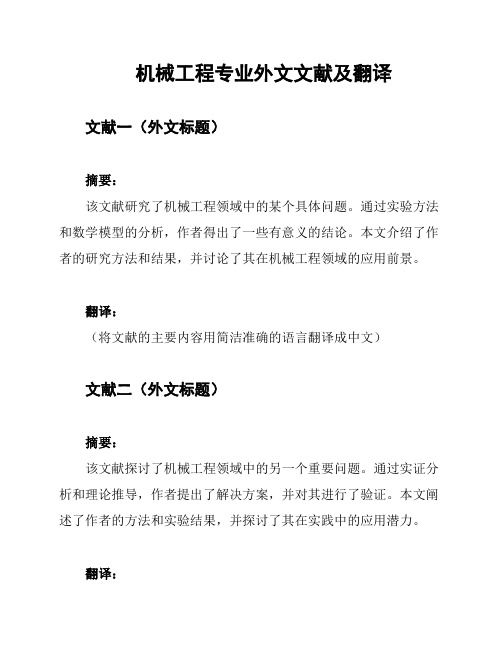
机械工程专业外文文献及翻译文献一(外文标题)
摘要:
该文献研究了机械工程领域中的某个具体问题。
通过实验方法和数学模型的分析,作者得出了一些有意义的结论。
本文介绍了作者的研究方法和结果,并讨论了其在机械工程领域的应用前景。
翻译:
(将文献的主要内容用简洁准确的语言翻译成中文)
文献二(外文标题)
摘要:
该文献探讨了机械工程领域中的另一个重要问题。
通过实证分析和理论推导,作者提出了解决方案,并对其进行了验证。
本文阐述了作者的方法和实验结果,并探讨了其在实践中的应用潜力。
翻译:
(将文献的主要内容用简洁准确的语言翻译成中文)
文献三(外文标题)
摘要:
该文献研究了机械工程领域中的另一个新颖课题。
作者通过数
值模拟和实验验证,得出了一些有趣的发现。
本文介绍了作者的研
究过程和结果,并讨论了其对机械工程领域的影响。
翻译:
(将文献的主要内容用简洁准确的语言翻译成中文)
总结
本文档介绍了三篇机械工程专业的外文文献,包括摘要和翻译。
这些文献都对机械工程领域中的不同问题进行了研究,并提出了相
关的解决方案和发现。
希望这些文献能为机械工程专业的学生和研
究人员提供有价值的参考和启发。
机械专业外文文献翻译

利用CAD / CAM/ CAE系统开发操纵机器人H.S.李*,S.E.张华为技术学院,电力机械工程,云林,台湾,中国摘要在这项研究中,需要开发用于机器人操作臂的CAD/CAE/CAM集成系统。
通过变换矩阵,利用D-H坐标系变换方法对机器人的位姿进行分析,我们使用MATAB软件对其进行计算。
一般来说,利用PRO/E对机械臂的参数进行实体化建模,用Pro / Mechanical软体模拟动态仿真和工作空间,MasterCAM用来实现切削模拟仿真,而最终的模型用CNC数控铣床制造出来。
这样,一个用于机器人操作臂的CAD/CAE/CAM集成系统便开发出来了。
我们用一个范例来验证这种设计,分析以及制造的结果的正确性。
该集成系统不仅促进机器人的生产自动化功能,而且还简化了机械臂的CAD / CAE / CAM的分析过程。
这种集成系统是用于开发一个实用的计算机辅助机构设计课程的教学辅助工具。
©2003由Elsevier B.V.出版关键词:CAD / CAE/ CAM;机械臂;Denavit,Hartenberg坐标系变换引言许多研究已涉及到的CAD / CAE/ CAM集成系统的原理。
吕[1]讨论了平面五杆受电弓的运动学分析并设计制造了基于此弓的机械手。
通过研究五杆受电弓的运动性能,设计出一款简单的控制器来对机械手进行控制。
李某和陈某[2]描述了一个自动升降轮椅固定装置内的全尺寸货车的开发。
开发的过程中,包括机制的概念设计,运动仿真,工程分析,原型开发和测试。
周[3]使用参数化CAD系统的实体模型表达设计理念。
首先开发的是模具,其次是基于CAM系统的模型。
通过与产业界的合作,对试模调整,粉末形成,烧结,烧结后处理在专业的粉末冶金工厂进行了实验。
徐[4]在UG2通用CAD / CAM系统的基础上通过将注塑模具的CAD/CAM软件与注塑模具CAE软件集成建立了一个注塑用CAD / CAE/ CAM系统。
- 1、下载文档前请自行甄别文档内容的完整性,平台不提供额外的编辑、内容补充、找答案等附加服务。
- 2、"仅部分预览"的文档,不可在线预览部分如存在完整性等问题,可反馈申请退款(可完整预览的文档不适用该条件!)。
- 3、如文档侵犯您的权益,请联系客服反馈,我们会尽快为您处理(人工客服工作时间:9:00-18:30)。
英文原文Extending Blender: Development of a Hepatic Authoring Tool Abstract -In this paper, we present our work to extend a well known 3D graphic modeler -Blender -to support hepatic modeling and rendering. The extension tool is named HAMLAT (hepatic Application Markup Language Authoring Tool). We describe the modifications and additions to the Blender source code which have been used to create HAMLAT Furthermore, we present and discuss the design decisions used when developing HAMLAT, and also an implementation "road map" which describes the changes to the Blender source code. Finally, we conclude with discussion of our future development and research avenues.Keywords Hepatics HAML Graphic Modelers Blender Virtual Environments.I. IntroductionA. MotivationThe increasing adoption of hepatic modality in human-computer interaction paradigms has led to a huge demand for new tools that help novice users to author and edit hepatic applications. Currently, the hepatic application development process is a time consuming experience that requires programming expertise. The complexity of hepatic applications development rises from the fact that the hepatic application components (such as the hepatic API, the device, the hepatic rendering algorithms, etc.) need to interact with the graphic components in order to achieve synchronicity. Additionally, there is a lack of application portability as the application is tightly coupled to a specific device that necessitates the use of its corresponding API. Therefore, device and API heterogeneity lead to the fragmentation and disorientation of both researchers and developers. In view of all these considerations, there is a clear need for an authoring tool that can build hepatic applications while hiding programming details from the application modeler (such as API, device, or virtual model).This paper describes the technical development of the hepatic Application Markup Language Authoring Tool (HAMLAT). It is intended to explain the design decisions used for developing HAMLAT and also provides an implementation "road map", describing the source code of the project.B. BlenderHAMLAT is based on the blender [1] software suite, which is an open-source 3D modeling package with a rich feature set. It has a sophisticated user interface which is noted for its efficiency and flexibility, as well as its supports for multiple file formats, physics engine, modem computer graphic rendering and many other features.Because of blender's open architecture and supportive community base, it was selected as the platform of choice for development of HAMLAT. The open-source nature of Blender means HAMLAT can easily leverage its existing functionality and focus on integrating hepatic features which make it a complete hap to-visual modeling tool, since developing a 3D modeling platform from scratch requires considerable development time and expertise in order to reach the level of functionality of blender. Also, we can take advantage of future improvements to blender by merging changesfrom its source code into the HAMLAT source tree.HAMLAT builds on existing Blender components, such as the user-interface and editing tools, by adding new components which focus on the representation, modification, and rendering of hepatic properties of objects in a 3D scene. By using Blender as the basis for HAMLAT, we hope to develop a 3D hepatic modeling tool which has the maturity and features of Blender combined with the novelty of hepatic rendering.C. Project GoalsAs previously stated, the overall goal for the HAMLAT project is to produce a polished software application which combines the features of a modem graphic modeling tool with hepatic rendering techniques. HAMLAT has the "look and feel" of a 3D graphical modeling package, but with the addition of features such as hepatic rendering and hepatic property descriptors. This allows artists, modelers, and developers to generate realistic 3D hippo-visual virtual environments. A high-level block diagram of HAMLAT is shown in Figure 1. It illustrates the flow of data in the hepatic modeling. HAMLAT assists the modeler, or application developer, in building hap to-visual applications which may be stored in a database for later retrieval by another hepatic application. By hippo-visual application we refer to any software which displays a 3D scene both visually andhectically to a user in a virtual setting. An XML file format, called HAML [2], is used to describe the 3D scenes and store the hippo-visual environments built by a modeler for later playback to an end user.Traditionally, building hippo-visual environments has required a strong technical and programming background. The task of hectically rendering a 3D scene is tedious since hepatic properties must be assigned to individual objects in the scene and currently there are few high-level tools for accomplishing this task. HAMLAT bridges this gap by integrating into the HAML framework and delivering a complete solution for development of hippo visual applications requiring no programming knowledge.The remainder of the paper is organized as follows: in Section 2, we present the proposed architecture extensions and discuss design constraints. Section 3 describes the implementation details and how hepatic properties are added and rendered within the blender framework. In section 4 we discuss related issues and future work avenues.II. SYSTEMOVERVIEWANDARCHITECTUREThe blender design philosophy is based on three main tasks: data storage, editing, and visualization. According to the legacy documentation [3], it follows a data visualize-edit development cycle for the 3D modelingA 3D scene is represented using data structures within the Blender architecture. The modeler views the scene, makes changes using the editing interface which directly modifies the underlying data structures, and then the cycle repeats.To better understand this development cycle, consider the representation of a 3D object in Blender. A 3D object may be represented by an array of vertices which have been organized as a polygonal mesh. Users may choose to operate on any subset of this data set. Editing tasks may include operations to rotate, scale, and translate thevertices, or perhaps a re-meshing algorithm to "cleanup" redundant vertices and transform from a quad to a triangle topology. The data is visualized using a graphical 3D rendered which is capable of displaying the object as a wireframe or as a shaded, solid surface. The visualization is necessary in order to see the effects of editing on the data. In a nutshell, this example defines the design philosophy behind blender's architecture.In blender, data is organized as a series of lists and base data types are combined with links between items in each list, creating complex scenes from simple structures. This allows data elements in each list to be reused, thus reducing the overall storage requirements. For example, a mesh may be linked by multiple scene objects, but the position and orientation may change for each object and the topology of the mesh remains the same. A diagram illustrating the organization of data structures and reuse of scene elements is shown in Figure 2. A scene object links to three objects, each of which link to two polygonal meshes. The meshes also share a common material property. The entire scene is rendered on one of several screens, which visualizes the scene.We adopt the Blender design approach for our authoring tool. The data structures which are used to represent objects in a 3D scene have been augmented to include fields for hepatic properties (e.g., stiffness, damping); user interface components (e.g., button panels) which allow the modeler to change object properties have also been updated to include support for modifying the hepatic properties of an object. Additionally, an interactive hippo-visual rendered has been implemented to display the 3D scene graphically and hectically, providing themodeler or artist with immediate feedback about the changes they make to the scene.A class diagram outlining the changes to the blender frame work is shown in Figure 3. Components which are pertinent to HAMLAT are shaded in gray. HAMLAT builds on existing blender sub-systems by extending them for hepatic modeling purposes. The tactile and kinesthetic cues, which are displayed due to interaction with virtual objects, are typically rendered based on the geometry of the mesh. in this data type. Other scene components such as lamps, cameras, or lines are not intuitively rendered using force feedback hepatic devices and are therefore not of current interest of chaotic rendering.An augmented version of the mesh data structure is shown in Figure 4. It contains fields for vertex and face data, plus some special custom data fields which allow data to be stored to/retrieved from disk and memory. We have modified this data type to include a pointer to a hepatics data structure, which stores hepatic properties such as stiffness, damping, and friction for the mesh elements (Figure 5).Similarly to the built-in graphical rendered, HAMLAT uses a custom rendered for displaying 3Ds scenes graphical and hap call, and is in end of the connectivity is given in the next section.IMPLEMENTATIONData StructureBlender uses many different data structures to represent the various types of objects in a 3D scene a polygonal mesh contains the location and topology of vertices;a lamp contains color and intensity values; and a camera object contains intrinsic viewing parameters.The Mesh data structure is used by the blenderBlender rendered. This component is developed independently since heretical and graphical rendering must be performed simultaneously and synchronously. A simulation loop is used to update hepatic rendering forces at a rate which maintains stability and quality.Where the force feedback vector which is displayed to the user is computed using the stiffness coefficient (variable name stiffness) for the object and x the |penetration depth (displacement) of the hepatic proxy into an object. The stiffness coefficient has a range of [0,1],where 0 represents no resistance to deformation and 1 represents the maximum stiffness which may be rendered by the hepatic device. The damping of an object defines its resistance to the rate of deformation due to some applied strut Hepatices force. It is typically rendered using the force equation:Hepatic PropertiesIn this section we'll briefly discuss the hepatic properties which may currently be modeled using HAMLAT. It is important for the modeler to understand these properties and their basis for use in hepatic rendering.The stiffness of an object defines how resistant it is to deformation by some applied force. Hard objects, such as a rock or table, have very high stiffness; soft objects, such as rubber ball, have low stiffness. The hardness-softness of an object is typically rendered using the spring-force equation: range of [0,1] and may be used to model viscous behavior of a material. It also increases the stability of the hepatic rendering loop ford stiff materials.The static friction (variable name striation) and dynamic friction (variable name direction) coefficient are used to model the frictional forces experienced while exploring the surface of a 3D object. Static friction is experienced when the proxy is not moving over the object's surface, and an initial force must be used to overcome static friction. Dynamic friction is felt when the proxy moves across the surface, rubbing against it. Frictional coefficients also have a range of /0,1], with a value of 0 making the surface of a 3D object feel "slippery" and a value of 1 making the object feel very rough.B. EditingBlender uses a set of non-overlapping windows called spaces to modify various aspects of the 3D scene and its objects. Each space is divided into a set of areas and panels which are context aware. That is, they provide functionality based on the selected object type. For example, if a camera is selected the panel will display components which allow the modeler to change the focal length and viewing angle of the camera, but these components will not appear if an object of another type is selected.Figure 6 shows a screen shot of the button space which is used to edit properties for a hepatic mesh. It includes user-interface panels which allow a modeler to change the graphical shading properties of the mesh, perform simple re-meshing operations, and to modify the hepatic properties of the selected mesh.HAMLAT follows the context-sensitive behavior of Blender by only displaying the hepatic editing panel when a polygonal mesh object is selected. In the future, this panel may be duplicated to support hepatic modeling for other object types, such as NURB surfaces.The blender framework offers many user-interface components (e.g., buttons, sliders, pop-up menus) which may be used to edit the underlying data structures. The hepatic properties for mesh objects are editable using sliders or by entering a float value into a text box located adjacent to the slider. When the value of the slider/text box is changed, it triggers an event in the blender windowing a unique identifier indicates he first pass renders the scene graphically, and the second pass renders it hectically. The second pass is required because the Open Hepatics toolkit intercepts commands send to the OpenGL pipeline and uses them to display the scene using hepatic rendering techniques. In this pass, the hepatic properties of each mesh object are used much in the same way color and lighting are used by graphical rendering they define the type of material for each object. To save CPU cycles, the lighting and graphical material properties are excluded from the hepatic rendering pass.Figure 7 shows source code which is used to apply the material properties during the hepatic rendering pass. The hepatic rendered is independent from the Blender framework in that it exists outside the original source code. However, it is still heavily dependent on Blender data structures and types.D. ScriptingThe Blender Python (By) wrapper exposes many of the internal data structures, giving the internal Python scripting engine may access them. Similar to the data structures used for representing mesh objects in the native Blender framework, wrappers allow user defined scripts to access and modify the elements in a 3D scene.An import script allows 3D scenes to be read from a HAML file and reproduced in the HAMLAT application; an export script allows 3D scenes to be written to a HAML file, including hepatic properties, and used in other HAML applications.The By wrappers also expose the Blender windowing system. Figure 9 shows a panel which appears when the user exports a 3D scene to the HAML file format. It allows the user to specify supplementary information about the application such as a description, target hardware, and system requirements. These are fields defined by the HAML specification [2] and are included with the authored scene as part of the HAML file format. User-interface components displayed on this panel are easily extended to agree with the future revisions of HAML.Currently, HAMLAT supports basic functionality for modeling and rendering hippo-visual applications. Scenes may be created, edited, previewed, and exported as part of a database for use in by other hap to-visual applications, such as the HAML player [6]. However, there is room for growth and in there are many more ways we can continue leveraging existing blender functionality. As per future work, we plan to extend HAMLAT to include support for other hepatic platforms and devices. Currently, only the PHANTOM series of devices is supported since the interactive rendered is dependent on the Open Hepatics toolkit [5]. In order to support other devices, a cross-platform library such as Chai3D or hatpin may be used to performrendering. These libraries support force rendering for a large range of hepatic hardware. Fortunately, due to the modularity of our implementation, only the interactive hepatic rendering component need be altered for these changes. In addition to support multiple hardware platforms, a user interface component which allows the selection and configuration of hepatic devices will be important. Most likely, this will be added as part of the user preferences panel in blender.Adding support for hepatic devices as part of editing tasks is also a planned feature. This will allow the modeler to modify the shape, location, and other properties on in-scene objects. For example, the sculpting mode in Blender allows a user to manipulate the geometry of a 3D object using natural interface, similar to reshaping a piece of clay. HAMLAT will build on this technology by allowing the modeler to manipulate the virtual clay using high DOF hepatic interfaces.中文译文延长搅拌机:摘要-在本文中,我们目前的工作是拓展一个众所周知的三维图形建模-搅拌机,来支持触觉建模和绘制。