各种冲压模具结构形式与设计
冲压模具设计与制作配套案例库:案例09 冲模结构与设计

案例九冲模结构与设计冲模是冲压生产的主要工艺设备,冲模结构设计对冲压件品质、生产率及经济效益影响很大。
因此,了解冲模结构,研究和提高冲模的各项技术指标,对冲模设计和发展冲压技术是十分必要的。
8. 1冲模分类及其特点按不同的特征对冲模进行分类,其分类方法主要有:(1)按冲压工序性质可分为冲裁模、拉深模、翻边模、胀形模、弯曲模……。
习惯上把冲裁模当作所有分离工序模的总称,包括落料模、冲孔模、切断模、切边模、半精冲模、精冲模及整修模等。
(2)按冲压工序的组合方式可分为单工序模、级进模和复合模。
1)单工序模在压力机一次冲压行程内,完成一道冲压工序的模具。
2)级进模在压力机一次冲程内,在模具不同工位上完成多道冲压工序的模具。
3)复合模在压力机一次行程内,在模具一个工位上完成两道以上冲压工序的模具。
(4)按进料、出件及排除废料方式可分为手动模、半自动模、自动模。
(5)按模具零件组合通用程度可分为专用模(包括简易模)和组合冲模。
(6)按凸、凹模材料可分钢模、硬质合金模、钢结硬质合金模、聚氨酯模、低熔点合金模等。
(7)按模具轮廓尺寸可分为大型模、中型模、小型模等。
8.2冲模零部件分类及功能各种类型冲模复杂程度不同,所含零件各有差异,但根据其作用都可归纳为如下五种类型:(1)工作零件工作零件直接使被加工材料变形、分离,而成为工件,如凸模、凹模、凸凹模等。
(2)定位零件定位零件控制条料的送进方向和送料进距,确保条料在冲模中的正确位置,有挡料销、导正销、导尺、定位销、定位板、导料板、侧压板和侧刃等。
(3)压料、卸料与顶料零件压料、卸料与顶料零件包括冲裁模的卸料板、顶出器、废料切刀、拉深模中的压边圈等。
卸料与顶料零件在冲压完毕后,将工件或废料从模具中排出,以使下次冲压工序顺利进行;拉深模中的压边圈的作用是防止板料毛坯发生失稳起皱。
(4)导向零件导向零件的作用是保证上模对下模相对运动精确导向,使凸模与凹模之间保持均匀的间隙,提高冲压件品质。
各种冲压模具结构形式与设计

各种冲压模具结构形式与设计各种冲压模具结构形式与设计普通冲模的结构形式与设计凹模结构尺⼨1.凹模厚度H和壁厚C 凹模厚度H可按下式计算:式中 F——最⼤冲裁⼒(N)。
但H必须⼤于10mm,如果冲裁轮廓长度⼤于51mm,则上式计算值再乘以系数1.1~1.4。
凹模壁厚按下式确定:C=(1.5~2)H (mm)2.凹模刃⼝间最⼩壁厚⼀般可参照表1。
表1 凹模刃⼝间最⼩壁厚(mm)常⽤凸模形式冲裁凹模的刃壁形式凹模和凸模的镶拼结构主要⽤于⼤型冲模和刃⼝形状复杂以及个别部分容易损坏的⼩型冲模。
镶块的分块要点如表1。
表1 镶块的分块要点对于中、⼩型镶拼模,镶块的固定可采⽤框套螺钉固定法,圆形镶拼模可采⽤框套热压法。
对于⼤中型镶块的分段固定法如表2。
表2 ⼤、中型镶块的分段固定法常见的凸模固定形式冲裁模的结构形式与设计落料模落料模是沿封闭的轮廓将制件或⼯序件与板料分离的冲模。
图1所⽰为冲制锁垫的落料模。
该模具有导柱、导套导向,因⽽凸、凹模的定位精度及⼯作时的导向性都较好。
导套内孔与导柱的配合要求为H6/h5。
凸模断⾯细弱,为了增加强度和刚度,凸模上部放⼤。
凸模与固定板紧配合,上端带台肩,以防拉下。
凹模刃壁带有斜度,冲件不易滞留在刃孔内,同时减轻对刃壁的磨损,⼀次刃磨量较⼩。
刃⼝尺⼨随刃磨变化。
凹模刃⼝的尺⼨决定了落料尺⼨。
凸模和凹模间有刃⼝间隙。
图1 落料模1-模柄 2-垫板 3-凸模固定板 4-凸模 5-卸料板6-定位销 7-凹模 8-导柱 9-导套在条料进给⽅向及其侧⾯,装有定位销,在条料进给时确定冲裁位置。
⼯件从凹模的落料孔中排出,条料由卸料板卸下,这种⽆导向弹压卸料板⼴泛⽤于薄材料和零件要求平整的落料、冲孔、复合模等模具上的卸料,弹压元件可⽤弹簧或硬橡胶板,卸料效果好,操作⽅便。
冲孔模冲孔模是在落料板材或成形冲件上,沿封闭的轮廓分离出废料得到带孔制件的冲模。
1.冲单孔的冲孔模其结构⼤致与落料模相同。
冲孔模的凸模、凹模类似于落料模。
冷冲模冷冲压模具的结构与设计1课件

工作零件
工艺零件 定位零件
冲裁模零部件
卸料与推件零部件
结构零件 导向零件 连接与固定零件
其它零件
二、模具零件的结构与设计
1、凸模组件及其结构设计 2、凹模设计 3、定位零件 4、卸料与推件零件 5、模架
1、凸模组件及其结构设计
凸模组件:凸模、凸模固定板、垫板和防转销、 上模座、螺钉、销钉固定
倒装模凸凹模的最小壁厚: 查p.102表4-4
3、定位零件
横向定位装置:使条料由正确的送进方向
导料销、导料板及侧压装置
纵向定位装置:控制条料在冲裁中送进步距
挡料销、导正销、侧刃
定位板和定位钉
横向定位装置
导料销
导料销两个,位于条料的同侧
导料板
两导料板之间距离L=条料最大宽度+间隙值 导料板厚度H=材料厚度t或挡料销高度+(2∽8) 整体式导料板其长度和宽度与凹模板外形尺寸
缺点:模具结构复杂,材料有额外消耗,定位 精度不高。
连续模排样
连续模排样设计:
1、零件精度对排样要求:
精度要求高——尽量减少工位数 孔距公差较小——尽量同一工位冲出
2、模具结果对排样要求:
零件较大或较小但工位多——采用连续复合排样
3、模具强度对排样要求:
孔距小——分布冲 工位间凹模壁厚小——增设空工位 外形复杂——分布冲
动力由压力机传递给 模具
相关链接:动力
第一节 冲压模的分类
一、按工序组合程度分 二、按上下模导向方式分 三、按凹模位置分 四、按自动化程度分
一、按工序组合程度分
1、单工序模(简单模)
单工序模是指压力机在一次行程中只完成一道工序的冲裁模
2在、一多副模工具中序,模在模具的同一位置上能同时完成数种 工序的模具 (在压力机的一次行程中,在模具的同一位置上同时 完成A几、道连工序续的模冲(模)级进模、跳步模) 在一副模具中,材料在模具的不同位置上能同时完成各 自工(B序是、指复压合力机模在一次行程中依次在几个不同的位置上 同时完成多道工序的冲模)
冲压模具的结构组成
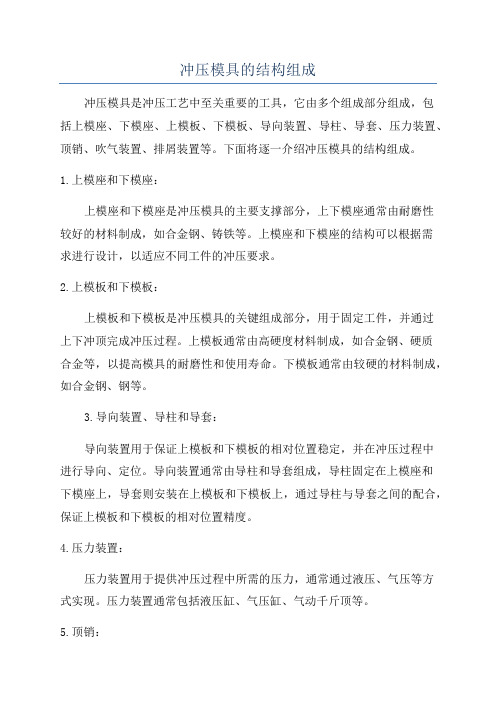
冲压模具的结构组成冲压模具是冲压工艺中至关重要的工具,它由多个组成部分组成,包括上模座、下模座、上模板、下模板、导向装置、导柱、导套、压力装置、顶销、吹气装置、排屑装置等。
下面将逐一介绍冲压模具的结构组成。
1.上模座和下模座:上模座和下模座是冲压模具的主要支撑部分,上下模座通常由耐磨性较好的材料制成,如合金钢、铸铁等。
上模座和下模座的结构可以根据需求进行设计,以适应不同工件的冲压要求。
2.上模板和下模板:上模板和下模板是冲压模具的关键组成部分,用于固定工件,并通过上下冲顶完成冲压过程。
上模板通常由高硬度材料制成,如合金钢、硬质合金等,以提高模具的耐磨性和使用寿命。
下模板通常由较硬的材料制成,如合金钢、钢等。
3.导向装置、导柱和导套:导向装置用于保证上模板和下模板的相对位置稳定,并在冲压过程中进行导向、定位。
导向装置通常由导柱和导套组成,导柱固定在上模座和下模座上,导套则安装在上模板和下模板上,通过导柱与导套之间的配合,保证上模板和下模板的相对位置精度。
4.压力装置:压力装置用于提供冲压过程中所需的压力,通常通过液压、气压等方式实现。
压力装置通常包括液压缸、气压缸、气动千斤顶等。
5.顶销:顶销用于在冲压过程中对工件施加顶压力,以保证工件在冲裁过程中的精度和质量。
顶销通常由合金钢等材料制成,其结构形式也因具体情况而异,如弹簧顶销、气动顶销等。
6.吹气装置:吹气装置用于在冲裁过程中吹松工件与模具之间的摩擦力,以便于工件的顺利脱模。
吹气装置通常包括喷嘴、风管等,通过气压将空气导入模具中。
7.排屑装置:排屑装置用于清除冲压过程中产生的屑铁、碎屑等废料。
排屑装置通常包括排屑孔、排屑板等。
冲压模具课程设计--带凸缘无底筒形件

冲压模具设计课程设计学院:姓名:寒冰色手学号:专业:11机制目录1零件冲压工艺分析---------------------------------------------03 1.1 制件介绍---------------------------------------------------03 1.2 产品结构形状分析-------------------------------------------032.零件冲压工艺方案的确定--------------------------------------033冲模结构的确定-----------------------------------------------044.零件冲压工艺计算--------------------------------------------044.1零件毛坯尺寸计算-------------------------------------------044.2 排样------------------------------------------------------064.3 拉深工序的拉深次数和拉深系数的确定------------------------064.4 冲裁力、拉深力的计算--------------------------------------074.5 拉深间隙的计算--------------------------------------------094.6 拉深凸、凹模圆角半径的计算--------------------------------09 4.7 计算模具刃口尺寸------------------------------------------094.8 计算模具--------------------------------------------------105. 选用标准模架----------------------------------------------125.1 模架的类型------------------------------------------------125.2 模架的尺寸------------------------------------------------126. 选用辅助结构零件------------------------------------------136.1 导向零件的选用--------------------------------------------136.2 模柄的选用------------------------------------------------136.3 卸料装置--------------------------------------------------146.4 推件、顶件装置--------------------------------------------146.5 定位装置--------------------------------------------------147 参考文献--------------------------------------------------141零件冲压工艺分析1.1 制件介绍零件名称:心子隔套材料:08钢料厚:1.0mm批量:大批量1.2 产品结构形状分析由图1可知该零件为圆筒件经过翻遍处理,翻边处有过渡圆弧,且半径为R=2.5mm故非常适合用模具拉深或翻边进行处理,故要对毛坯进行计算。
冲压模具结构

冲裁可分为冲孔和落料 。 定义:用冲模沿封闭轮廓曲线冲切,封闭线内是制件,封闭线外是废料的工艺,叫落料;反之 是 冲孔。 冲裁模分类:1.工序组合的形式:单工序冲裁模、复合冲裁模和连续冲裁模。 2.按工序分类:落料模、冲孔模、切断模和切边模等。 8.1.1 落料模 . 1)敞开模 特点:结构简单,制造容易,模具的均匀间隙不易保证,安装调试复杂,冲裁制件 精 度低 2)导板模 特点:精度较高,模具寿命长,模具间隙由模具制造精度决定,但制造复杂
8.2 复合冲裁模
复合模( 复合模 多工序冲裁模)
定义:冲床一次行程中,在模具同一位置上能完成几个不同冲裁工序的模具。 结构特点:一副模具有一个凸凹模。 分类:①正(顺)装式复合模 ②倒装式复合模。 8.2.1 正装式复合模 适用:制件平直度要求较高或冲裁时易弯曲的大而薄的制件。 缺点:操作不方便,也不安全,不适用于多孔制件的冲裁。 • • 8.2.2倒装式复合模 倒装式复合模 • 特点:操作方便、安全 • 应用:平直度要求不高,多孔厚板制件的冲裁。 • 复合冲裁模的特点: • 1)制件形位尺寸精度较高。 • 2)制件冲孔与落料的毛刺同在一侧。 • 3)可以节省材料。 • 4)模具的体积较小,模具结构紧凑。 • 5)制件内外形尺寸直接影响凸凹模强度。 • 6)生产效率高。 • 由于凸凹模的壁厚受到限制,复合模适宜冲裁生产批量大,精度要求高、厚度不 • 大• • • • • • • 3)导柱模 • 特点:精度高,模具寿命长,使用安装方便,但是模具规模大、 • 8.1. 2.冲孔模 • 冲小孔模具,必须考虑凸模的强度和刚度,以及快速更换凸模的结构。 • 1) 侧壁冲孔模 • 2) 小孔冲孔模 模具结构采用缩短凸模长度的方法(防止弯曲变形而折断) 特点:制造比较容易,凸模使用寿命也较长。
冲压模具零部件设计

靠用标准,选择模架的依据。
凹 模 形 式 及 固 定
3.凸凹模 复合模中同时具有落料凸模和冲孔凹模作用的工作零件。 凸凹模的最小壁厚: 正装复合模,内孔不积存废料,胀力小,最小壁厚可以小些; 倒装复合模, 若内孔为直筒形刃口形式,且采用下出料方 式,则内孔积存废料,胀力大,故最小壁厚 应大些。 倒装复合模的凸凹模最小壁厚见表。 正装复合模的凸凹模最小壁厚可比倒装的小些。
3.导柱和导套零件导向装置
(1)导柱 (2)导套
导柱导套的配合间隙:必须小于冲裁间隙 冲裁间隙小的一般应 按H6/h5配合;间隙较大的按H7/h6配合。 导柱导套的长度:据模具闭合高度,一般应符合相关要求。 导柱导套制造、安装要求:采用H7/r6压入模座的安装孔; 材料:20钢表面渗碳,淬火硬度58~62HRC
工作原理:
特点:推件力大,工作可靠
刚性推件装置
1-打杆 2-推板 3-连接推杆 4-推件块
推板
1-打杆 2-模柄 3-推板 4-推杆 5-卸料螺钉 6-凸凹模 7-卸料板 8-落料凹模 9-顶件块 10-带肩顶杆 11-冲孔凸模 12-挡料销 13-导料销
正装式复合模
动画
弹 性 推 件 装 置
1-橡胶 2-推板 3-连接推杆 4-推件块
(2)顶件装置 组成:顶杆、顶件块和装在下模底下的弹顶器 特点:顶件力容易调节,工作可靠,冲件平直度较高 制造、装配要求:①模具处于开启状态时,必须顺利复位,工作 面高出凹模平面,以便继续冲裁; ②模具处于闭合状态时,其背后有一定空间, 以备修磨和调整的需要;
级进模
配合使用: 与挡料销或与侧刃配合使用
后者粗定位,前者精定位
结构组成
导入部分:圆锥形的头部 导正部分:圆柱形的
(完整版)几种典型冲压模具结构

几种典型冲压模具结构设计的冷冲压模具的结构是否合理,是否好用,对能否生产出合格的工件,开发的新产品能否成功,是至关重要的一套模具,结构简单的不过几十个零部件组成。
但是,在刚开始设计时,是选何种模具结构形式,是选正装模具结构(即凹模安装在下模座上)呢?还是倒(反)装模具结构(即凸模安装在下模座上)?是选单工序模具结构呢?还是选复合模具结构?这是一个非常值得深入探讨的话题。
1何时选用正装模具结构(由于加精度要求不高,生产批量不大的工件,在很多生产企业都普遍存在。
故只讨论无导向装置的单工序模)1.1正装模具的结构特点正装模具的结构特点是凹模安装在下模座上。
故无论是工件的落料、冲孔,还是其它一些工序,工件或废料能非常方便的落入冲床工作台上的废料孔中。
因此在设计正装模具时,就不必考虑工件或废料的流向。
因而使设计出的模具结构非常简单,非常实用。
1.2正装模具结构的优点(1)因模具结构简单,可缩短模具制造周期,有利于新产品的研制与开发。
(2)使用及维修都较方便。
(3)安装与调整凸、凹模间隙较方便(相对倒装模具而言)。
(4)模具制造成本低,有利于提高企业的经济效益。
5)由于在整个拉伸过程中,始终存在着压边力,所以适用于非旋转体件的拉抻(参看五金科技,1997;6:42 〜44)。
1.3正装模具结构的缺点(1)由于工件或废料在凹模孔内的积聚,增加了凹模孔内的小组涨力。
因此凹必须增加壁厚,以提高强度。
(2)由于工件或废料在凹模孔内的积聚,所以在一般情况下,凹模刃口就必须要加工落料斜度。
在有些情况下,还要加工凹模刃口的反面孔(出料孔)。
因而即延长了模具的制作周期,又啬了模具的加工费用。
1.4正装模具结构的选用原则综上所述可知,我们在设计冲模时,应遵循的设计原则是:应优先选用正装模具结构。
只有在正装模具结构下能满足工件技术要求时,才可以考虑采用其它形式的模具结构。
2何时选用倒(反)装模具结构2.1倒装模具的结构特点倒装模具的结构特点是凸模安装在下模座上,故我们就必须采用弹压卸料装置将工件或废料从凸模上卸下。
- 1、下载文档前请自行甄别文档内容的完整性,平台不提供额外的编辑、内容补充、找答案等附加服务。
- 2、"仅部分预览"的文档,不可在线预览部分如存在完整性等问题,可反馈申请退款(可完整预览的文档不适用该条件!)。
- 3、如文档侵犯您的权益,请联系客服反馈,我们会尽快为您处理(人工客服工作时间:9:00-18:30)。
各种冲压模具结构形式与设计普通冲模的结构形式与设计凹模结构尺寸1.凹模厚度H和壁厚C 凹模厚度H可按下式计算:式中 F——最大冲裁力(N)。
但H必须大于10mm,如果冲裁轮廓长度大于51mm,则上式计算值再乘以系数1.1~1.4。
凹模壁厚按下式确定:C=(1.5~2)H (mm)2.凹模刃口间最小壁厚一般可参照表1。
表1 凹模刃口间最小壁厚(mm)常用凸模形式冲裁凹模的刃壁形式凹模和凸模的镶拼结构主要用于大型冲模和刃口形状复杂以及个别部分容易损坏的小型冲模。
镶块的分块要点如表1。
表1 镶块的分块要点对于中、小型镶拼模,镶块的固定可采用框套螺钉固定法,圆形镶拼模可采用框套热压法。
对于大中型镶块的分段固定法如表2。
表2 大、中型镶块的分段固定法常见的凸模固定形式冲裁模的结构形式与设计落料模落料模是沿封闭的轮廓将制件或工序件与板料分离的冲模。
图1所示为冲制锁垫的落料模。
该模具有导柱、导套导向,因而凸、凹模的定位精度及工作时的导向性都较好。
导套内孔与导柱的配合要求为H6/h5。
凸模断面细弱,为了增加强度和刚度,凸模上部放大。
凸模与固定板紧配合,上端带台肩,以防拉下。
凹模刃壁带有斜度,冲件不易滞留在刃孔内,同时减轻对刃壁的磨损,一次刃磨量较小。
刃口尺寸随刃磨变化。
凹模刃口的尺寸决定了落料尺寸。
凸模和凹模间有刃口间隙。
图1 落料模1-模柄 2-垫板 3-凸模固定板 4-凸模 5-卸料板6-定位销 7-凹模 8-导柱 9-导套在条料进给方向及其侧面,装有定位销,在条料进给时确定冲裁位置。
工件从凹模的落料孔中排出,条料由卸料板卸下,这种无导向弹压卸料板广泛用于薄材料和零件要求平整的落料、冲孔、复合模等模具上的卸料,弹压元件可用弹簧或硬橡胶板,卸料效果好,操作方便。
冲孔模冲孔模是在落料板材或成形冲件上,沿封闭的轮廓分离出废料得到带孔制件的冲模。
1.冲单孔的冲孔模其结构大致与落料模相同。
冲孔模的凸模、凹模类似于落料模。
但冲孔模所冲孔与工件外缘或工件原有孔的位置精度是由模具上的定位装置来决定的。
常用的定位装置有定位销、定位板等。
2.冲多孔的冲孔模图1是印制板冲孔模,用于冲裁印制板小孔,孔径为φ1.3mm,材料为复铜箔环氧板,厚1.5mm。
为得到较大的压料力,防止孔壁分层,上模采用六个矩形弹簧。
导板材料为CrWMn,并淬硬至50~54HRC,凸模3采用弹簧钢丝,拉好外径后切断、打头,即可装入模具中使用。
凸模与固定板动配合。
下模为防止废料胀死,漏料孔扩大,工件孔距较近时,漏料孔可以相互开通。
图1 印制板冲孔模1-矩形弹簧 2-导板 3-凸模4-凸模固定板 5-凹模3.深孔冲模当孔深化t/D(料厚/孔径)≥1,即孔径等于或小于料厚时,采用深孔冲模结构。
图2是凸模导向元件在工作过程中的始末情况,该结构给凸模以可靠的导向。
主要的特点是导向精度高,凸模全长导向以及在冲孔周围先对材料加压。
图2 凸模导向元件在工作行程中的始末情况a)冲孔开始 b)冲孔结束压力中心一副冲模的压力中心就是指这副冲模各个冲压部分的冲压力的合力作用点。
冲模的压力中心,应尽可能通过模具中心并与压力机滑块中心重合,以避免偏心载荷使模具歪斜,间隙不均,从而加速压力机和模具的导向部分及凸、凹模刃口的磨损。
冲裁模压力中心计算的步骤和公式见表1。
表1 冲裁模压力中心计算的步骤和公式冲裁级进模冲裁级进冲模是在条料的送料方向上,具有两个以上的工位,并在压力机一次行程中,在不同的工位上完成两道或两道以上的冲压工序的冲模。
对孔边距较小的工件,采用复合模有困难,往往采取落料后冲孔,由两副模具来完成,如果采用级进模冲裁则可用一副模具来完成。
为了保证冲裁零件形状间的相对位置精度,常采用定距侧刃和导正销定距的结构。
1.定距侧刃(图1)在条料的侧边冲切一定形状缺口,该缺口的长度等于步距,条料送进步距就以缺口定距。
图1 侧刃定距1-落料凸模 2-冲孔凸模 3-侧刃2.导正销定距(图2)导正销在冲裁中,先进入预冲的孔中,导正材料位置,保证孔与外形的相对位置,消除送料误差。
图2 导正销定距1-落料凸模 2-导正销 3-冲孔凸模在图2中,冲裁时第一步送料用手按压始用挡料销抵住条料端头,定位后进行第一次冲制,冲孔凸模在条料上冲孔。
第一次冲裁后缩回始用挡料销,以后冲压不再使用。
第二步把条料向前送至模具上落料的位置,条料的端头抵住固定挡料钉初步定位,此时在第一步所冲的孔已位于落料的位置上,当第二次冲裁时,落料凸模下降,装于落料凸模工作端的导正销首先播进原先冲好的孔内,将条料导正到准确的位置,然后冲下一个带孔的工作,同时冲孔凸模又在条料上预冲好孔,以后各次动作均与第二次同。
冲裁复合模冲裁复合模是只有一个工位,并在压力机的一次行程中,同时完成落料与冲孔两道冲压工序,见图1。
图1 复合模1-打棒 2-打板 3-冲孔凸模 4-落料凹模5-卸料板 6-凸凹模 7-推块 8-推杆凸凹模既是落料凸模又是冲孔凹模,因此能保证冲件内外形之间的形状位置。
压料装置在单动压力机上常用的拉深模压料装置见表1。
表1 拉深模的压料装置定位装置及导料装置表1 定位装置表2 导料装置表3 切边后条料与导料板间空隙(mm)表4 条料与导料板间空隙 (mm)导正销导正销导正材料位置的方式有两种,即利用冲件孔直接导正及利用条料上另外设置的工艺孔间接导正。
导正销的结构形式见表1。
导正销和孔间的空隙见表2。
导正销工作高度见表3。
表1 导正销的结构形式表2 导正销和孔间的空隙(双向) (mm)表3 导正销工作高度 (mm)常见的卸料板结构形式冲裁模与压力机的关系为了合理设计模具和正确选用压力机,就必需进行冲裁力计算。
选择压力机吨位时,应将冲裁力乘以安全系数,其值一般取1.3。
冲模与压力机的闭合高度也有一定的配合关系,即(Hmax -h1)-5≥h≥(Hmin-h1)+10 (mm)式中 Hmax——压力机的最大闭合高度 (mm);Hmin——压力机的最小闭合高度 (mm);h1——压力机垫板厚度(mm);h——模具的闭合高度(mm)。
冲裁模结构设计注意事项弯曲模的结构形式与设计弯曲件的工序安排对弯曲件安排弯曲工序时,应仔细分析弯曲件的具体形状、精度和材料性能。
特点小的工件,尽可能采用一次弯曲成形的复杂弯曲模,这样有利于定位和操作。
当弯曲件本身带有单面几何形状,在模具结构上采用成对弯曲,这样既改善模具的受力状态,又可防止弯曲毛料的滑移(表1)。
表1 弯曲件的工序安排弯曲模结构形式弯曲模结构有简易弯曲模,斜楔弯曲模,滚轮弯曲模,精弯模等。
1.简易弯曲模(表1)表1 简易弯曲模2.斜楔弯曲模适用于弯曲零件的弯角小于90°,图2是示例。
先由凸模下降,坯料弯曲成90°,然后斜楔推动活动凹模(滑块)弯曲零件。
图2 斜楔弯曲模1-凸模 2-斜楔3.滚轮弯曲模图3示滚轮式弯曲模,使零件在弯曲过程中具有良好的变形条件,从而得到形状正确的零件。
图3 滚轮式弯曲模1-滚轮弯曲模结构设计注意事项弯曲凸、凹模圆角半径与凹模深度1.凸模圆角半径一般情况下,凸模圆角半径取等于或略小于工件内侧的圆角半径R,对于工件圆角半径较大(R/t>10),而且精度较高时,则应进行回弹计算。
2.凹模进口圆角半径当凹模进口圆角半径过小时,弯矩的力臂减小,坯料沿凹模圆角滑进时的阻力增大,从而增加弯曲力,并使毛坯表面擦伤。
在生产中,可按材料厚度,决定凹模圆角半径(表1)。
表1 凹模进口圆角半径R A(mm)3.凹模深度凹模深度查表2。
凹模深度过小,毛坯两边自由部分太多,弯曲件回弹大,不平直。
但凹模深度增大,消耗模具钢材多,且需要压力机有较大的工作行程。
表2 凹模深度l (mm)拉深模的结构形式与设计拉深模的结构形式与设计拉深模是把坯料拉压成空心体,或者把空心体拉压成外形更小而板厚没有明显变化的空心体的冲模。
拉深模结构形式1.第一次拉深工序的模具(表1)2.后续拉深工序的模具(表2)表1第一次拉深工序的模具表2 后续拉深工序的模具3.反拉深模将工序件按前工序相反方向进行拉深,称为反拉深。
反拉深把工序件内壁外翻,工序件与凹模接触面大,材料流动阻力也大,因而可不用压料圈。
图1是反拉深示例。
图2示反拉深模,凹模的外径小于工序件的内径,因此反拉深的拉深系数不能太大,太大则凹模壁厚过薄,强度不足。
4.变薄拉深模变薄拉深与一般拉深不同,变薄拉深时工件直径变化很小,工件底部厚度基本上没有变化,但是工件侧面壁厚在拉深中加以变薄,工件高度相应增加。
变薄拉深凹模的形式见表3。
变薄拉深凸模的形式见表4。
图3示变薄拉深模,凸模下冲时,经过凹模(两件),对坯件进行二次变薄拉深,凸模上升时,卸料圈拼块把拉深件从凸模上卸下。
表3 变薄拉深凹模的形式表4 变薄拉深凸模的形式图3 变薄拉深模1-凸模 2-定位圈 3、4-凹模 5-卸料圈拼块拉深模间隙、圆角半径与压料筋1.拉深模间隙拉深模凸、凹模间隙过小时,使拉深力增大,从而使材料内应力增大,甚至在拉深时可能产生拉深件破裂。
但当间隙过大时,在壁部易产生皱纹。
拉深模在确定其凸、凹模间隙的方向时,主要应正确选定最后一次拉深的间隙方向,在中间拉深工序中,间隙的方向是任意的。
而最后一次拉深的间隙方向应按下列原则确定:当拉深件要求外形尺寸正确时,间隙应由缩小凸模取得,当拉深件要求内形尺寸正确时,间隙应由扩大凹模取得。
矩形件拉深时,由于材料在拐角部分变厚较多,拐角部分的间隙应较直边部分间隙大0.1t(t——拉深件材料厚度)。
拉深时,凸模与凹模间每侧的间隙Z/2可按下式计算:——材料的最大厚度(mm);式中 tmaxK——系数,见表1;t——材料的公称厚度(mm)。
表1 拉深模间隙系数K注:1.对于强度高的材料,K取较小值。
2.精度要求高的拉深件,建议最后一道采用拉深系数m=0.9~0.95的整形拉深。
2.圆角半径凸模圆角半径增大,可减低拉深系数极限值,应该避免小的圆角半径。
过小的圆角半径显然将拉加拉应力,使得危险剖面处材料发生很大的变薄,在后续拉深工序中,该变薄部分将转移到侧壁上,同时承受切向压缩,因而导致形成具有小折痕的明显的环形圈。
凹模圆角半径对拉深力和变形情况有明显的影响。
增大凹模圆角半径,不仅降低了拉深力,而且由于危险剖面的应力数值降低,增加了在一次拉深中可能的拉深深度,亦即可以减低拉深系数的极限值。
但过大的圆角半径,将会减少毛坯在压料圈下的面积,因而当毛料外缘离开压料圈的平面部分后,可能导致发生皱折。
多道拉深的凸模圆角半径,第一道可取与凹模半径相同的数值,以后各道可取工件直径减小值的一半。
末道拉深凸模的圆角半径值,决定于工件要求,如果工件要求的圆角半径小时,需增加整形模,整小圆角。
拉深凹模的圆角半径——坯料直径或上一次拉深件直径(mm);式中 dd——本次拉深件直径(mm);t——材料厚度(mm)。