轴承疲劳测试标准
lq1020轴承状态检测仪判定标准

lq1020轴承状态检测仪判定标准LQ1020轴承状态检测仪是一种常用的设备,用于判定轴承的状态。
它可以通过检测轴承的振动、噪音、温度等参数来判断轴承的磨损程度、故障类型以及剩余寿命。
下面将根据实际情况,提供一些参考内容,用于判定轴承状态的标准。
1. 振动检测标准:- 轴承振动速度:正常轴承振动速度一般不超过15mm/s,如果超过此值,说明轴承已经损坏。
- 轴承振动频率:通过测量轴承振动频率的变化,可以判断是否存在不平衡、共振或其它异常情况。
- 轴承振动的时间趋势:观察测量结果的时间趋势,如果振动持续增加,则说明轴承可能存在问题。
2. 噪音检测标准:- 正常轴承的噪音水平一般在70dB以下,如果超过此值,则说明轴承存在异常。
- 噪音的频率和类型:通过分析噪音的频率和类型,可以判断轴承是否存在滚珠脱落、内外圈磨损等问题。
3. 温度检测标准:- 轴承温度的上限:正常轴承温度一般不超过80℃,如果超过此值,则说明轴承存在异常。
- 温度的分布情况:通过观察轴承不同部位的温度分布情况,可以判断是否存在摩擦、磨损等问题。
4. 其他判定参考内容:- 外观检查:通过观察轴承的外观,检查是否存在裂纹、锈蚀等问题。
- 润滑情况:检查轴承的润滑情况,如果润滑油少或污染严重,可能导致轴承异常。
- 工作环境:考察轴承工作环境,包括温度、湿度、振动等因素,这些因素都可能影响轴承的工作寿命。
以上是一些常见的参考内容,用于判定LQ1020轴承状态检测仪的测量结果。
需要注意的是,这些标准只是一些常见的判别参考,实际应用中应结合具体的情况进行综合判断。
在使用LQ1020轴承状态检测仪时,操作者应熟悉设备的使用方法和各项测量参数的正常范围,以便更准确地判定轴承的状态。
同时,在实际应用中,对于有关轴承状态的标准和参考内容,也可根据实际情况进行适当调整和补充。
JB/T 10510-2005《滚动轴承材料接触疲劳试验方法》标准介绍
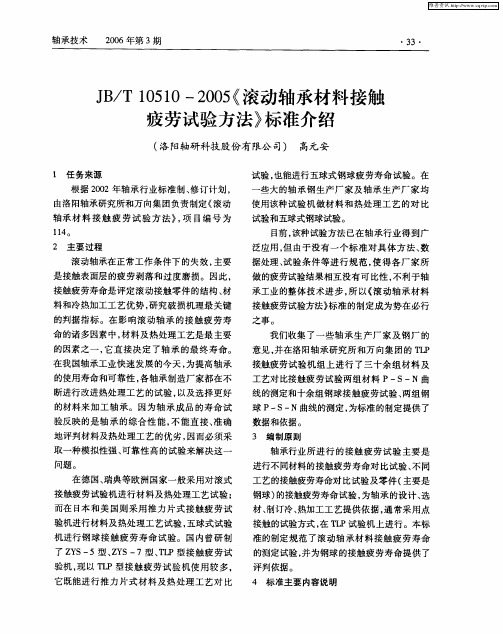
N×1 次 0 应 力
5o 6 oMPa
50 9 0MPa
60 2 0MPa
1 2 3 4
1 78 0 . 3 2. 33 93 3. 9 3 7 0 4. 7 0 66
1 2 92 .7 1 9 4O .4 33 7 . 41 4. 8 6 15
537 .3 5
6. 5 4 O6 6. 78 71 7. 6 9 5 7 8. 4 2 14 9. 5 7 0 8 1 3 8 0. 9 8 1 84 2. 7 2 1 19 6. 4 2 1 7 4 9. 62 2 2 6 4. 5 6
4. 1 5 87
4. 2 9 22 5. 73 5 3 6. 8 31 7 7. 7 3 5 0 9. 4 2 07 9. 8 3 72 1 .8 8 14 5 1 6 4 3. O2 1 O 3 5. 36 1 41 3 9. 7
的判 据 指 标 。在 影 响滚 动 轴 承 的 接 触 疲 劳 寿
承工业的整体技术进 步, 以《 所 滚动轴承材料
接触疲劳试验方法》 标准的制定成为势在必行 理工艺是最主要
的因素之一 , 它直接决定 了轴 承的最终寿命 。
在我 国轴承 工业 快 速发 展 的今 天 , 提高 轴 承 为
一
根 据 20 02年 轴 承行 业标 准 制 、 订计 划 , 修 由洛 阳轴 承研 究所 和万 向集 团 负责 制定 《 动 滚 轴 承 材 料 接 触 疲 劳 试 验 方 法 》, 目编 号 为 项
I 4。 1
些大的轴承钢生产厂家及轴承生产厂家均
使 用该种 试 验 机 做 材 料 和 热 处 理 工 艺 的 对 比 试 验和 五球 式钢 球试验 。 目前 , 该种 试验方 法 已在轴 承行 业得 到 广
‘滑动轴承’的国内外标准

‘滑动轴承’检测标准滑动轴承(sliding bearing),在滑动摩擦下工作的轴承。
滑动轴承工作平稳、可靠、无噪声。
在液体润滑条件下,滑动表面被润滑油分开而不发生直接接触,还可以大大减小摩擦损失和表面磨损,油膜还具有一定的吸振能力。
但起动摩擦阻力较大。
轴被轴承支承的部分称为轴颈,与轴颈相配的零件称为轴瓦。
为了改善轴瓦表面的摩擦性质而在其内表面上浇铸的减摩材料层称为轴承衬。
轴瓦和轴承衬的材料统称为滑动轴承材料。
滑动轴承应用场合一般在低速重载工况条件下,或者是维护保养及加注润滑油困难的运转部位。
‘滑动轴承’的国内外标准较多,所以只列了80个国内的国标及行业标准和地台湾地方标准。
CNS 5694-1980 滚动轴承组成零附件及球面滑动轴承总则CNS 8210-1982 连座滑动轴承CNS 8213-1982 滑动轴承用卷制轴承衬(尺度)CNS 8214-1983 滑动轴承用卷制轴承衬检验法(外径及内径)CNS 8468-1982 径向滑动轴承运转试验通则CNS 8556-1982 滑动轴承中耐摩擦金属摩擦状态之特性CNS 8769-1982 滑动轴承用卷制轴衬之润滑孔、润滑槽、润滑坑CNS 8770-1982 滑动轴承用卷制轴衬之材料CNS 8922-1982 滑动轴承用轴衬(驱动组件)CNS 8923-1982 滑动轴承用抗摩合金衬料CNS 9062-1982 托架滑动轴承?总成及外壳CNS 9063-1982 托架滑动轴承?轴承衬CNS 9064-1982 托架滑动轴承?润滑环CNS 9065-1982 托架滑动轴承?轴承油封、轴承盖片及组合尺寸CNS 9066-1982 止推滑动轴承?轴衬式止推轴承之组合尺寸CNS 9067-1982 止推滑动轴承?止推轴承环之组合尺寸CNS 9068-1982 滑动轴承之配合CNS 9348-1982 滑动轴承轴衬?烧结材料制CNS 9349-1982 滑动轴承轴衬?铜合金制整件CNS 9350-1982 滑动轴承轴衬?有润滑孔及润滑槽CNS 9351-1982 滑动轴承轴衬?碳精制CNS 9352-1982 滑动轴承轴衬?热硬性树脂制CNS 9353-1982 热硬性树脂制滑动轴承轴衬检验法CNS 9354-1982 滑动轴承轴衬?热塑性塑料制CNS 11203-1985 铁路车辆滑动轴承之轴箱用防尘板CNS 11204-1985 铁路车辆用滑动轴承GB/T 2688-1981 滑动轴承粉末冶金轴承技术条件GB/T 2889.1-2008 滑动轴承术语、定义和分类第1部分:设计、轴承材料及其性能GB/T 7308-2008 滑动轴承有法兰或无法兰薄壁轴瓦公差、结构要素和检验方法GB/T 10445-1989 滑动轴承整体轴套的轴径GB/T 10446-2008 滑动轴承整圆止推垫圈尺寸和公差GB/T 10447-2008 滑动轴承半圆止推垫圈要素和公差GB/T 12613.1-2002 滑动轴承卷制轴套第1部分;尺寸GB/T 12613.2-2002 滑动轴承卷制轴套第2部分;外径和内径的检测数据GB/T 12613.3-2002 滑动轴承卷制轴套第3部分;润滑油孔、润滑油槽和润滑油穴GB/T 12613.4-2002 滑动轴承卷制轴套第4部分;材料GB/T 12948-1991 滑动轴承双金属结合强度破坏性试验方法GB/T 12949-1991 滑动轴承覆有减摩塑料层的双金属轴套GB/T 14910-1994 滑动轴承厚壁多层轴承衬背技术要求GB/T 16748-1997 滑动轴承金属轴承材料的压缩试验GB/T 18323-2001 滑动轴承烧结轴套的尺寸和公差GB/T 18324-2001 滑动轴承铜合金轴套GB/T 18325.1-200 滑动轴承流体动压润滑条件下试验机内和实际应用的滑动轴承疲劳强度GB/T 18326-2001 滑动轴承薄壁滑动轴承用金属多层材料GB/T 18327.1-2001 滑动轴承基本符号GB/T 18327.2-2001 滑动轴承应用符号GB/T 18329.1-2001 滑动轴承多层金属滑动轴承结合强度的超声波无损检验GB/T 18330-2001 滑动轴承薄壁轴瓦和薄壁轴套的壁厚测量GB/T 18331.1-2001 滑动轴承卷制轴套外径的检测GB/T 18844-2002 滑动轴承损坏和外观变化的术语、特征及原因GB/T 21466.1-2008 稳态条件下流体动压径向滑动轴承.圆柱滑动轴承.第1部分:计算过程GB/T 21466.2-2008 稳态条件下流体动压径向滑动轴承圆形滑动轴承第2部分:计算过程中所用函数GB/T 21466.3-2008 稳态条件下流体动压径向滑动轴承.圆形滑动轴承.第3部分:许用的运行参数HG/T 2121-1991 可倾瓦径向滑动轴承技术条件JB/T 743-2000 电机用Z系列座式滑动轴承JB/T 2560-2007 整体有衬正滑动轴承座型式与尺寸JB/T 2561-2007 对开式二螺柱正滑动轴承座型式与尺寸JB/T 2562-2007 对开式四螺柱正滑动轴承座型式与尺寸JB/T 2563-2007 对开式四螺柱斜滑动轴承座型式与尺寸JB/T 2564-2007 滑动轴承座技术条件JB/T 5888.1-2000 电机用DQ系列端盖式滑动轴承.技术条件JB/T 5888-2005 电机用DQ系列滑动轴承结构与尺寸JB/T 5985-1992 滑动轴承.水润滑热固性塑料轴承JB/T 7920-1995 滑动轴承薄壁轴瓦周长的检验方法JB/T 7921-1995 滑动轴承单层和多层轴承用铸造铜合金JB/T 7922-1995 滑动轴承单层轴承用锻造铜合金JB/T 7923-1995 滑动轴承单层轴承用铝基合金JB/T 7925.1-1995 滑动轴承单层轴承减摩合金硬度检验方法JB/T 7925.2-1995 滑动轴承多层轴承减摩合金硬度检验方法JJG(机械) 86-1992 滑动轴承薄壁轴承互校准模检定规程LY/T 1501-1999 森林铁路车辆无导框滑动轴承铸钢轴箱体技术条件MT/T 643-1996 滚筒采煤机用三层复合材料滑动轴承TB/T 2875-1998 滑动轴承几何特性和材料质量特性的质量控制技术和检验TB/T 2876-1998 滑动轴承.薄壁轴瓦和薄壁筒形轴承的壁厚测量TB/T 2958-1999 滑动轴承. 薄壁轴瓦周长检验TB/T 2959-1999 滑动轴承. 金属多层滑动轴承粘结层的超声波无损检验TB/T 2984-2000 滑动轴承.金属多层滑动轴承渗透无损检测TB/T 3020-2001 滑动轴承.薄壁轴承用多层材料TB/T 3033-2002 滑动轴承损坏和外观变化的术语、特征及原因YB/T 5364-2006 滑动轴承用铝锡合金-钢复合带。
608轴承疲劳极限载荷

608轴承疲劳极限载荷
608轴承是一种标准的深沟球轴承,通常用于滚簧板、滑板、滚球鞋和其他小型机械设备。
608轴承的疲劳极限载荷是指在标准测试条件下,轴承能够承受的循环载荷次数,通常是在轴承失效之前的次数。
这个参数是衡量轴承的寿命和耐久性的关键指标。
608轴承的疲劳极限载荷通常以动载荷(Dynamic Load Rating)来表示,单位是牛顿(N)或千牛顿(kN)。
疲劳极限载荷的值取决于轴承的尺寸、材料和设计。
要了解608轴承的具体疲劳极限载荷,您需要查阅该轴承型号的技术规格表或相关的制造商文档。
通常,这些规格表会提供有关轴承的各种性能参数,包括动载荷、静载荷、最高转速等信息。
这些规格表通常会列出不同轴承型号和尺寸的性能参数。
请注意,608轴承的疲劳极限载荷是经过严格测试和标准化程序测定的,以确保可靠性和性能。
在实际应用中,疲劳极限载荷将受到外部因素(如润滑、轴承装配、工作条件等)的影响,因此轴承的实际使用寿命可能会有所不同。
对于具体的应用和设计,建议咨询制造商或工程师以确保选用的608轴承满足所需的寿命和性能要求。
疲劳试验标准

疲劳试验标准疲劳试验是评价材料、零部件及构件在交变应力作用下的疲劳性能的重要手段,也是确定材料寿命和安全可靠性的关键方法之一。
疲劳试验的标准化对于保证产品质量、提高产品可靠性具有重要意义。
本文将介绍疲劳试验标准的相关内容,以便于广大工程技术人员更好地了解和应用疲劳试验标准。
1. 疲劳试验标准的概述。
疲劳试验标准是制定和规范疲劳试验的技术文件,包括试验方法、试验条件、试验设备、试验程序、试验数据处理和分析等内容。
疲劳试验标准的制定是为了保证疲劳试验的科学性、准确性和可比性,为产品设计、制造和使用提供可靠的数据支持。
2. 疲劳试验标准的分类。
根据不同的试验对象和试验条件,疲劳试验标准可分为金属材料疲劳试验标准、非金属材料疲劳试验标准、零部件疲劳试验标准等。
其中,金属材料疲劳试验标准包括拉伸-疲劳试验、弯曲-疲劳试验、扭转-疲劳试验等;非金属材料疲劳试验标准包括塑料材料疲劳试验、复合材料疲劳试验等;零部件疲劳试验标准包括轴承疲劳试验、焊接接头疲劳试验、螺栓连接疲劳试验等。
3. 疲劳试验标准的应用。
疲劳试验标准的应用范围涉及到航空航天、汽车、船舶、轨道交通、机械制造、电子电气、建筑工程等多个领域。
通过遵循疲劳试验标准,可以评价材料和构件在实际工作条件下的疲劳性能,为产品的设计、选材和使用提供科学依据,有助于提高产品的可靠性和安全性。
4. 疲劳试验标准的发展趋势。
随着科学技术的不断发展和进步,疲劳试验标准也在不断完善和更新。
未来,疲劳试验标准将更加注重多学科交叉融合,推动疲劳试验技术与先进制造技术、数字化技术、材料基因工程等领域的深度融合,为实现高效、精准、智能的疲劳试验提供更加可靠的技术支持。
5. 结语。
疲劳试验标准是疲劳试验工作的基础和指导,对于提高产品质量、保障产品安全具有重要意义。
各行各业的工程技术人员应当重视疲劳试验标准的学习和应用,不断提升疲劳试验技术水平,为推动工程技术的发展和进步做出更大的贡献。
JB/T 10510-2005《滚动轴承材料接触疲劳试验方法》介绍

表 1 术 语及 定 义
●
名 称 接触应力 接触疲劳 接触疲劳寿命 特 寿命 额定寿命 中值 寿命
符 号 S
定
义
接触物体之问集 中于局部接触区的相互压力而产牛 的应力 试样 的局部接触区在循 环接触应力作用下产牛疲劳裂纹 ,经一定循环 次数后 ,接触表
面 、浅层或深层发生接触疲劳剥落失效 时所承受 的应力循 环次数 服从韦布尔分布 ,破坏概率为 6 . %时子样 的接 触疲劳寿命 32
L0 l L0 5
服从韦布尔分布 ,破坏概率为 1%时子样的接触疲劳寿命 0 服从韦布尔分布 ,破坏概率为 5 %时子样的接触疲劳寿命 0
— —
试验 机在 每 次试 验前 应 进 行 调试 ,使 其 符
冷却油的进 口温度为 5 4 o c 0C; c一 工作 载荷应 不大于 16 9N,误差不应 超过
合试验要求。载荷 系统应每年校验一次。
c )试 验机 的 润滑
— —
—
—
±1 : %
应采用 N 2 3 油润滑 ;
2 标准 中涉及 的术 语 及定 义见 表 1 ) 。
轴承行业所进行的接触疲劳试验主要是进行不 同材料 的接触疲劳寿命对 比试验 、不 同工艺的接触
疲劳 寿命对 比试 验及零 件 ( 主要 是钢 球 ) 的 接触 疲
劳寿命试验 ,以为轴承的设计 、选材 、制定冷、热 加工工艺提供依据 ,通常采用 点接触 的试验 方式, 在 T J试验机上进行。J/ 0 1 I P B T 150规范了滚动轴
维普资讯
料 耪 舷 癍 劳试 验 茄 法 喻 绍
由中国机械工业联合会提 出,全 国滚动轴承标 准化技术委员会 (A / 9 )归 口,洛 阳轴承研究 S C T8 所 、万 向集 团 技 术 中心 负 责 起 草 的 J / 150 B T 0 1— 承材料及零件接触疲劳寿命 的测定试验方法 ,并为 钢球 的接触疲劳寿命提供了评判依据。
关节轴承疲劳试验大纲

关节轴承疲劳试验大纲
摘要:
1.关节轴承简介
2.疲劳试验的背景和重要性
3.关节轴承疲劳试验的目的和方法
4.关节轴承疲劳试验的结果和分析
5.关节轴承疲劳试验的应用和展望
正文:
1.关节轴承简介
关节轴承是一种广泛应用于各种机械设备的关键部件,它能够承受较大的径向和轴向载荷,同时具有较高的旋转精度和稳定性。
关节轴承的主要失效模式包括磨损、疲劳、腐蚀等,其中疲劳失效是最为常见的一种。
2.疲劳试验的背景和重要性
疲劳试验是一种模拟关节轴承在实际工况下承受循环载荷的过程,通过测试关节轴承在特定条件下的寿命,以此来评估其抗疲劳性能。
疲劳试验在关节轴承的研发、生产和应用中具有重要意义,能够为关节轴承的设计、选型和使用提供重要的参考依据。
3.关节轴承疲劳试验的目的和方法
关节轴承疲劳试验的主要目的是评估关节轴承在实际工况下的抗疲劳性能,以此来提高关节轴承的使用寿命和可靠性。
关节轴承疲劳试验通常采用专用的疲劳试验机进行,通过模拟关节轴承在实际工况下的载荷和转速,测试其在一定循环次数下的寿命。
4.关节轴承疲劳试验的结果和分析
关节轴承疲劳试验的结果通常包括疲劳寿命、疲劳强度和疲劳裂纹等指标。
通过对这些指标的分析,可以评估关节轴承的抗疲劳性能,并为其设计和选型提供参考。
5.关节轴承疲劳试验的应用和展望
关节轴承疲劳试验在关节轴承的研发、生产和应用中具有重要作用,能够为关节轴承的设计、选型和使用提供重要的参考依据。
高速超精密轴承尺寸稳定性与疲劳寿命试验
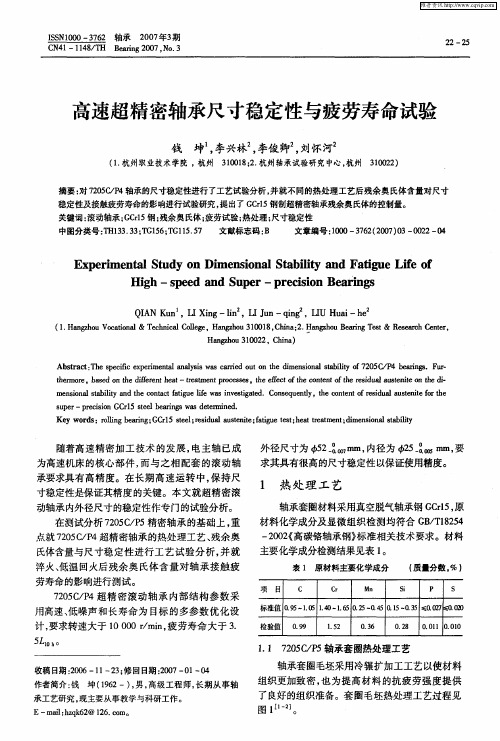
中图分 类号 :H133 ;G 5 ;G 1 .7 T 3 .3 T 16 T 155 文献标志码 : B 文章编号 :0 0— 7 2 20 ) 3 0 2 0 10 3 6 (0 7 0 — 02— 4
E p rm e t lS u y o m e so a t b l y a d F t u ie o x e i n a t d n Di n i n lS a i t n a i e L f f i g
- 1、下载文档前请自行甄别文档内容的完整性,平台不提供额外的编辑、内容补充、找答案等附加服务。
- 2、"仅部分预览"的文档,不可在线预览部分如存在完整性等问题,可反馈申请退款(可完整预览的文档不适用该条件!)。
- 3、如文档侵犯您的权益,请联系客服反馈,我们会尽快为您处理(人工客服工作时间:9:00-18:30)。
轴承疲劳测试标准
常见的用于轴承疲劳测试的标准包括以下几个:
1. ISO 281:这是国际标准化组织(ISO)发布的轴承动载荷评定标准,其中包括了轴承疲劳寿命的计算方法和寿命评定。
2. ASTM F347/F347M:这是美国材料和试验协会(ASTM)发布的标准,涵盖了金属轴承和轴承合金的疲劳性能测试。
3. DIN 26281:这是德国国家标准(DIN)的疲劳测试标准,该标准提供了用于滚动轴承疲劳寿命评定的测试方法。
4. GB/T 307.2:这是中国国家标准(GB)的一部分,其中包括滚动轴承疲劳寿命的测试和计算方法。
这些标准是行业中广泛采用的,提供了轴承疲劳寿命测试的指导和评定方法。
标准中通常包括了测试设备、样品准备、加载条件、测试过程以及数据处理和结果评估等方面的要求。
需要注意的是,在进行轴承疲劳测试时,应根据具体的应用要求和规范选择适当的标准,并确保按照标准要求进行测试。
此外,如果您在特定行业或应用领域工作,可能会有行业标准或公司内部标准需要遵循。
建议查阅相关的行业规范、标准文献或咨询专业的工程师或设备制造商以获取更准
确的信息和指导。