6炼钢的基本原理
炼钢生产过程以及流程图详解(全)
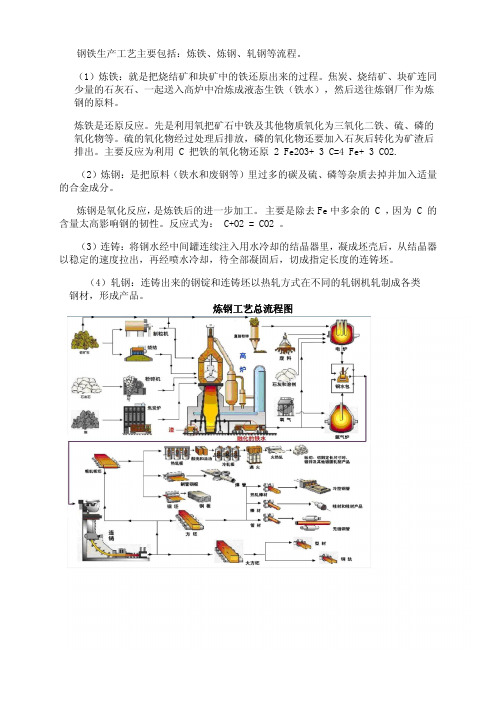
钢铁生产工艺主要包括:炼铁、炼钢、轧钢等流程。
(1)炼铁:就是把烧结矿和块矿中的铁还原出来的过程。
焦炭、烧结矿、块矿连同少量的石灰石、一起送入高炉中冶炼成液态生铁(铁水),然后送往炼钢厂作为炼钢的原料。
炼铁是还原反应。
先是利用氧把矿石中铁及其他物质氧化为三氧化二铁、硫、磷的氧化物等。
硫的氧化物经过处理后排放,磷的氧化物还要加入石灰后转化为矿渣后排出。
主要反应为利用 C 把铁的氧化物还原 2 Fe2O3+ 3 C=4 Fe+ 3 CO2.(2)炼钢:是把原料(铁水和废钢等)里过多的碳及硫、磷等杂质去掉并加入适量的合金成分。
炼钢是氧化反应,是炼铁后的进一步加工。
主要是除去Fe中多余的 C ,因为 C 的含量太高影响钢的韧性。
反应式为: C+O2 = CO2 。
(3)连铸:将钢水经中间罐连续注入用水冷却的结晶器里,凝成坯壳后,从结晶器以稳定的速度拉出,再经喷水冷却,待全部凝固后,切成指定长度的连铸坯。
(4)轧钢:连铸出来的钢锭和连铸坯以热轧方式在不同的轧钢机轧制成各类 钢材,形成产品。
炼钢工艺总流程图炼焦生产流程:炼焦作业是将焦煤经混合,破碎后加入炼焦炉内经干馏后产生热焦碳及粗焦炉气之制程。
烧结生产流程:烧结作业系将粉铁矿,各类助熔剂及细焦炭经由混拌、造粒后,经由布料系统加入烧结机,由点火炉点燃细焦炭,经由抽气风车抽风完成烧结反应,高热之烧结矿经破碎冷却、筛选后,送往高炉作为冶炼铁水之主要原料。
还原气体,还原铁矿石,产生熔融铁水与熔渣之炼铁制程。
转炉生产流程:炼钢厂先将熔铣送前处理站作脱硫脱磷处理,经转炉吹炼后,再依订单钢种特性及品质需求,送二次精炼处理站(RH真空脱气处理站、Ladle Injection盛桶吹射处理站、VOD真空吹氧脱碳处理站、STN搅拌站等)进行各种处理,调整钢液成份,最后送大钢胚及扁钢胚连续铸造机,浇铸成红热钢胚半成品,经检验、研磨或烧除表面缺陷,或直接送下游轧制成条钢、线材、钢板、钢卷及钢片等成品。
《钢冶金学》_第6章 氧气底吹转炉和顶底复合吹炼转炉炼钢

钢冶金学重庆科技学院王宏丹◆氧气底吹转炉炼钢氧气底吹转炉炼钢OBM法和LWS法吹炼高磷铁水时的成分变化Q-BOP法吹炼过程中钢水和炉渣成分的变化Q-BOP法吹炼过程炉渣成分的变化吹炼终点[C]和[O]的关系图终点[C]和[Mn]的关系Q-BOP和LD炉内渣中(FeO)6.2.1 顶底复吹转炉炼钢工艺类型6.2 顶底复合吹炼转炉的冶金特点6.2.2 顶底复吹转炉的底吹供气和供气元件6.2.3 顶底复吹转炉内的冶金反应6.2.4 冶金效果氧气顶底复吹转炉炼钢在复吹转炉中,了解和掌握底吹气体的性质、冶金行为、合理地确定底吹气体比例,选择和控制底吹供气强度,是复吹转炉获得良好的技术经济指标的重要因素。
底吹气体的冶金行为主要表现在三个方面: 强化熔池搅拌,使钢水成分,温度均匀;加速炉内反应,使渣钢反应界面增大,元素间化学反应和传质过程更加趋于平衡;冷却保护供气元件,使供气元件使用寿命延长。
底吹气体底吹O:需用冷却介质来保护供气元件,会与熔2池中碳发生反应,产生较大的搅拌力。
:可不用冷却剂,会与熔池中碳发生反 底吹CO2应搅拌力较强的气体;会使熔池CO分压增加,不利于超低碳钢冶炼。
、Ar和CO:属中性或惰性气体,供入铁 底吹N2水中不参与熔池内的反应,只起搅拌作用。
底吹气体比例在复吹转炉中,底吹气体量的多少决定熔池内搅拌的强弱程度。
,其底吹 在冶炼超低碳钢种时,即使用底吹O2供气量也要达20%左右;对一些具有特殊功能的复吹工艺(如喷石灰粉、煤粉等),其底吹供气量可达40%。
就一般复吹转炉而言,为了保证脱硫、脱气和渣-钢间反应趋于平衡,在吹炼结束前,也要采用较大的底吹供气来搅拌熔池。
底吹供气强度获得最佳搅拌强度,使熔池混合最均匀。
大量实验研究表明,熔池的混匀程度与搅拌强度有关,而搅拌强度受供气量和底吹元件布置影响。
根据吹炼过程调节供气强度。
复吹转炉的特点是能有效地把熔池搅拌与炉渣氧化性有机统一起来,而实现手段就是控制底吹供气强度。
6 炼钢的基本原理
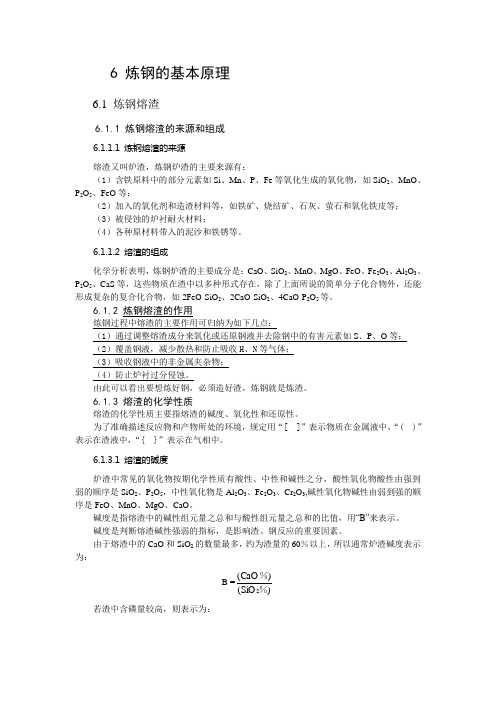
6 炼钢的基本原理6.1 炼钢熔渣6.1.1 炼钢熔渣的来源和组成6.1.1.1 炼钢熔渣的来源熔渣又叫炉渣,炼钢炉渣的主要来源有:(1)含铁原料中的部分元素如Si 、Mn 、P 、Fe 等氧化生成的氧化物,如SiO 2、MnO 、P 2O 5、FeO 等;(2)加入的氧化剂和造渣材料等,如铁矿、烧结矿、石灰、萤石和氧化铁皮等;(3)被侵蚀的炉衬耐火材料;(4)各种原材料带入的泥沙和铁锈等。
6.1.1.2 熔渣的组成化学分析表明,炼钢炉渣的主要成分是:CaO 、SiO 2、MnO 、MgO 、FeO 、Fe 2O 3、Al 2O 3、P 2O 5、CaS 等,这些物质在渣中以多种形式存在,除了上面所说的简单分子化合物外,还能形成复杂的复合化合物,如2FeO·SiO 2、2CaO·SiO 2、4CaO·P 2O 5等。
6.1.2 炼钢熔渣的作用 炼钢过程中熔渣的主要作用可归纳为如下几点:(1)通过调整熔渣成分来氧化或还原钢液并去除钢中的有害元素如S 、P 、O 等;(2)覆盖钢液,减少散热和防止吸收H 、N 等气体;(3)吸收钢液中的非金属夹杂物;(4)防止炉衬过分侵蚀。
由此可以看出要想炼好钢,必须造好渣,炼钢就是炼渣。
6.1.3 熔渣的化学性质熔渣的化学性质主要指熔渣的碱度、氧化性和还原性。
为了准确描述反应物和产物所处的环境,规定用“[ ]”表示物质在金属液中,“( )”表示在渣液中,“{ }”表示在气相中。
6.1.3.1 熔渣的碱度炉渣中常见的氧化物按期化学性质有酸性、中性和碱性之分,酸性氧化物酸性由强到弱的顺序是SiO 2、P 2O 5,中性氧化物是Al 2O 3、Fe 2O 3、Cr 2O 3,碱性氧化物碱性由弱到强的顺序是FeO 、MnO 、MgO 、CaO 。
碱度是指熔渣中的碱性组元量之总和与酸性组元量之总和的比值,用“B”来表示。
碱度是判断熔渣碱性强弱的指标,是影响渣、钢反应的重要因素。
材料加工原理第6章-材料加工过程中的化学冶金

Cn H 2 n+2 nC + (n + 1)H 2 →
18
二、液态金属与气体的反应
N2、H2、O2是对金属作用 最大(有害) 最大(有害)的三种气 体。
1、氮 Nitrogen (1)氮在金属中的溶解 (1)氮在金属中的溶解 N2↔2[N] 2[N] 即: 1/2N [N] 1/2N2↔[N]
1 2 3 4 5
F2=F+F + H2=H+H + H2=H+H++e + O2=O+O + N2=N+N +
-270 -433.9 -1745 -489.9 -711.4
6 7 8 9 10
CO2=CO+1/2O2 + H2O=H2+1/2O2 = H2O=OH+1/2H2 = + H2O=H2+O = H2O=2H+O = +
13
4、气体的分解
简单气体( 等双原子气体) 简单气体(指N2、H2、O2、F2等双原子气体)的分解 ; 复杂气体( 复杂气体(指CO2和H2O等)的分解,分解产物在高温下 等 的分解, 还可进一步分解和电离。 还可进一步分解和电离。
编 号 反应式
∆H
° 298 /kJ.mol
编 号
反应式
° ∆H 298 /kJ.mol
6
(3)熔池反应区 (3)熔池反应区
焊接化学冶金反应的最后阶段。 焊接化学冶金反应的最后阶段。 特点: 特点: 平均温度较低: 16001)平均温度较低: 1600-1900℃ 前后部温差大,反应方向不同。 前后部温差大,反应方向不同。 比表面积小,但存在(反应)时间较长。 2)比表面积小,但存在(反应)时间较长。 熔池中金属、熔渣不断更新(renewing) (renewing)。 3)熔池中金属、熔渣不断更新(renewing)。
转炉炼钢
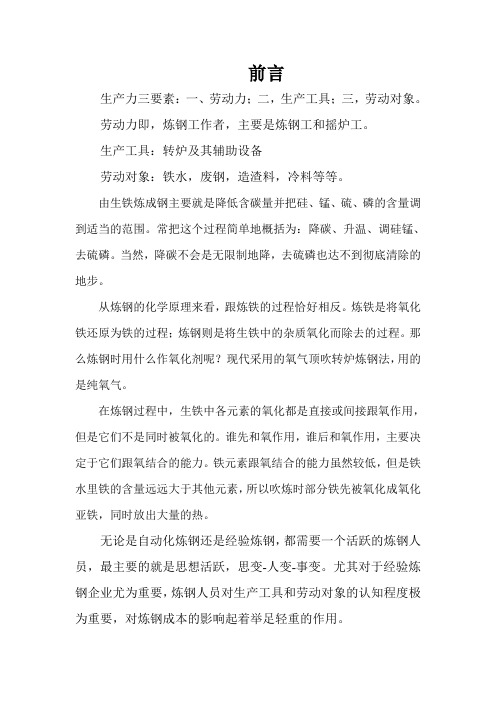
前言生产力三要素:一、劳动力;二,生产工具;三,劳动对象。
劳动力即,炼钢工作者,主要是炼钢工和摇炉工。
生产工具:转炉及其辅助设备劳动对象:铁水,废钢,造渣料,冷料等等。
由生铁炼成钢主要就是降低含碳量并把硅、锰、硫、磷的含量调到适当的范围。
常把这个过程简单地概括为:降碳、升温、调硅锰、去硫磷。
当然,降碳不会是无限制地降,去硫磷也达不到彻底清除的地步。
从炼钢的化学原理来看,跟炼铁的过程恰好相反。
炼铁是将氧化铁还原为铁的过程;炼钢则是将生铁中的杂质氧化而除去的过程。
那么炼钢时用什么作氧化剂呢?现代采用的氧气顶吹转炉炼钢法,用的是纯氧气。
在炼钢过程中,生铁中各元素的氧化都是直接或间接跟氧作用,但是它们不是同时被氧化的。
谁先和氧作用,谁后和氧作用,主要决定于它们跟氧结合的能力。
铁元素跟氧结合的能力虽然较低,但是铁水里铁的含量远远大于其他元素,所以吹炼时部分铁先被氧化成氧化亚铁,同时放出大量的热。
无论是自动化炼钢还是经验炼钢,都需要一个活跃的炼钢人员,最主要的就是思想活跃,思变-人变-事变。
尤其对于经验炼钢企业尤为重要,炼钢人员对生产工具和劳动对象的认知程度极为重要,对炼钢成本的影响起着举足轻重的作用。
如今,大多数钢铁企业还处在经验炼钢或者半经验炼钢阶段,炼钢操作人员还没有实现高学历化。
大多数企业对炼钢人员的培养都是传帮带,由于人员素质的不同,导致很多好的经验、好的方法在传承的过程当中失传,对于一个企业来说造成的损失不可估量,即使一些企业对炼钢工作者进行一些相关的培训工作,也只是单纯的理论培训,照本宣科,起不到实质性的作用。
基于此,企业老板本着对企业的可持续发展,管理者本着达到企业制定的的工作目标,炼钢工作人员本着更好的完成工作目标,就需要理论和实践的有机结合,达到可持续,动态化的炼钢生产,最大程度的降低炼钢成本,实现企业效益的最大化。
劳动对象一、铁水C;二、Mn;三、S;四、P;五、Si;六、Fe七、废钢,八、造渣料,石灰,轻烧白云石,烧结矿,石灰石等九、冷料,矿石,铁皮球,炼钢成本最大的一块就是转炉的钢铁料消耗,故钢铁料消耗应该是我们的重点研究对象。
炼钢工艺
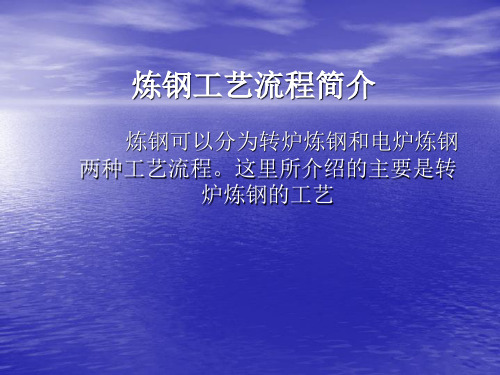
这是利用辊道输送至冷床。这是铸坯 在运输辊道上的场景。
★铸坯的收集(冷床,推钢)
连铸坯通过步进式翻转冷床冷却,然后由推钢 机收集。这就是步进式冷床场景。
★向混铁炉兑入铁水
混铁炉是一种贮存铁水的容器,通过 多包铁水混兑可以均匀铁水温度和成分, 为转炉冶炼创造更好的原料条件。此外由 于混铁炉容量较大,它还是调节高炉和转 炉生产节奏的缓冲器。
这就是向混铁炉兑入铁水的场景。
★混铁炉出铁
根据转炉生产的需要,混铁炉随时可提供一定量的铁 水。这是混铁炉出铁的场景。出铁量通过铁水车上的电子 秤称量并在大屏幕上显示。
二次除尘为干法除尘,采用长袋脉冲反吹除尘 器。
B、循环水泵房 循环水泵房其间数十台水泵可将处理后的冷
却水源源不断地送往炼钢、连铸各个系统,并实 现水的循环使用。
这 散是 烟转 囱炉 的一 画次 面除 。尘
放
这是转炉二次除尘设备的除尘器画面。
这是循环水泵房场景。
这是转炉一次除尘斜板沉淀池的画面。
★向转炉兑铁水
转炉炼钢所需要的主原料是铁水,这是向转炉 加入铁水的场景。
★转炉加废钢
废钢是转炉炼钢除铁水外又一种重要 的原材料。根据工艺要求配加一定量的废 钢。一是为了降温,实现冶炼过程中热平 衡,二是在铁水量一定的情况下增加钢的 产量。
这是向转炉加废钢的场景。
★转炉加石灰及其他辅料,地下料仓
★测温取样
每炉钢出钢前必须符合工艺规定的温 度和化学成分的要求,因此冶炼到一定阶 段需要倒炉进行测温取样。温度在现场大 屏幕和主控室计算机上均有显示,试样则 需送到炉前化验室经直读光谱仪分析再报 出结果。
转炉炼钢-绪论
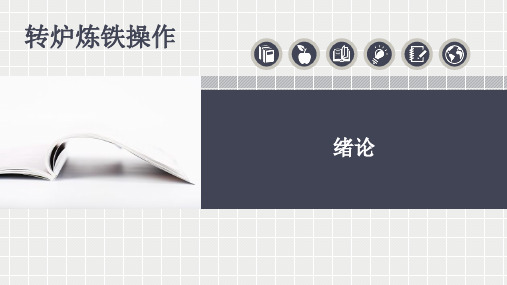
相关知识
七、转炉一炉钢的基本冶炼过程 顶吹转炉冶炼一炉钢的操作过程 (1)上炉出钢、倒渣,检查炉衬和倾动设备等进行必要的修补和修理。 (2)倾炉,加废钢、兑铁水,摇正炉体(至垂直位置)。 (3)降枪开吹,同时加入第一批渣料(起初炉内噪声较大,从炉口冒
出赤色烟雾,随后喷出暗红的火焰;3~5min后硅锰氧化接近结束,碳氧反应 逐渐激烈,炉口的火焰变大,亮度随之提高;同时渣料熔化,噪声减弱)。
(4) 3~5min后加入第二批渣料继续吹炼(随吹炼进行钢中碳逐渐降 低,约12min后火焰微弱,停吹)。
(5)倒炉,测温、取样,并确定补吹时间或出钢。 (6)出钢,同时(将计算好的合金加入钢包中)进行脱氧合金化。
相关知识
八、转炉炼钢三个阶段及任务 • 吹炼前期———硅锰氧化期
任务:化好渣、早化渣,以利P、S的去除。同时注意造渣,以减少炉渣 对炉衬的侵蚀。 • 吹炼中期———碳氧化期
相关知识
四、炼钢的基本任务 • 炼钢的基本任务是脱碳、脱磷、脱硫、脱氧,去除有害气体和非金属夹
杂物,提高温度和调整成分。 “四脱”(碳、氧、磷和硫),“二去”(去气和去夹杂),“二调整” (成分和温度)。 • 采用的主要技术手段为:供氧,造渣,升温,加脱氧剂和合金化操作。
பைடு நூலகம்
相关知识
五、钢的分类 1、按化学成分分:
—兑铁水——装废钢——下枪——加渣料(石灰、铁皮)——点火—— 熔池升温——脱P、Si、Mn——降枪脱碳。 • 看炉口的火,听声音,看渣稠不稠。看火亮度——加第二批(渣料)— —倒炉——取样 测温。 • 根据分析取样结果——决定出钢(或补吹)——合金化。技术水平高的 炉长,一次命中率高。不要补吹的就是通常说的一次命中。
转炉炼铁操作
炼钢过程的物理化学基础

炼钢过程的物理化学基础
炼钢是将生铁或生铁合金通过冶炼、熔炼和精炼等过程,去除杂质和调整合金元素含量,制得具有一定化学成分和性能的钢材。
这个过程涉及多种物理和化学原理,其中一些重要的物理化学基础包括:
1.熔炼原理:
熔融与溶解:高温条件下金属原料被熔化,形成熔体。
在熔体中,不同金属元素能够相互溶解,形成合金体系。
相平衡与相图:钢铁冶炼中考虑不同金属之间的相平衡关系,例如铁碳相图,用于预测在不同温度下金属间的相变情况,指导生产实践。
2.去除杂质与精炼原理:
氧化还原反应:在炼钢过程中,通过氧化还原反应去除杂质。
例如,将氧气通过熔融金属,氧气与不纯净金属反应生成氧化物,再被去除,使金属中杂质减少。
渗碳原理:通过加入碳源(如石墨、焦炭等)来调整钢铁的碳含量,使其满足特定的技术要求。
3.结晶与晶体生长:
凝固过程:当熔体冷却至凝固温度以下时,金属开始凝固成晶体结构。
晶体的形成和排列方式直接影响钢材的力学性能。
晶粒粗化与细化:控制熔体冷却速率,可以影响晶粒的尺寸和形态,从而调节钢材的组织结构和性能。
4.热力学与动力学:
热力学平衡:针对炼钢过程中的温度、压力和化学反应等参数,
进行热力学平衡分析,确保炉内反应能够朝着预期的方向进行。
动力学控制:炼钢过程中,不仅需要考虑热力学平衡,还需考虑动力学控制,即控制熔体的流动和传热,以便有效地去除杂质、调整合金成分。
炼钢过程是一个复杂的物理化学过程,其中涉及多种物质相互作用和反应过程。
理解这些物理化学基础是确保钢铁冶炼过程高效、稳定和品质可控的关键。
- 1、下载文档前请自行甄别文档内容的完整性,平台不提供额外的编辑、内容补充、找答案等附加服务。
- 2、"仅部分预览"的文档,不可在线预览部分如存在完整性等问题,可反馈申请退款(可完整预览的文档不适用该条件!)。
- 3、如文档侵犯您的权益,请联系客服反馈,我们会尽快为您处理(人工客服工作时间:9:00-18:30)。
6炼钢的基本原理6.1炼钢熔渣6.1.1炼钢熔渣的来源和组成6.1.1.1炼钢熔渣的来源熔渣又叫炉渣,炼钢炉渣的主要来源有:(1)含铁原料中的部分元素如Si、Mn、P、Fe等氧化生成的氧化物,如SQ2、MnO、P2O5、FeO 等;(2)加入的氧化剂和造渣材料等,如铁矿、烧结矿、石灰、萤石和氧化铁皮等;(3)被侵蚀的炉衬耐火材料;(4)各种原材料带入的泥沙和铁锈等。
6.1.1.2熔渣的组成化学分析表明,炼钢炉渣的主要成分是:CaO、Si。
?、MnO、MgO、FeO、Fe2O3、AI2O3、P2O5、CaS 等,这些物质在渣中以多种形式存在,除了上面所说的简单分子化合物外,还能形成复杂的复合化合物,如2FeO・SiO2、2CaOSiO2、4CaORO5等。
6.1.2炼钢熔渣的作用炼钢过程中熔渣的主要作用可归纳为如下几点:(1)通过调整熔渣成分来氧化或还原钢液并去除钢中的有害元素如S、P、O等;(2)覆盖钢液,减少散热和防止吸收H N等气体;(3)吸收钢液中的非金属夹杂物;(4)防止炉衬过分侵蚀。
由此可以看出要想炼好钢,必须造好渣,炼钢就是炼渣。
6.1.3熔渣的化学性质熔渣的化学性质主要指熔渣的碱度、氧化性和还原性。
为了准确描述反应物和产物所处的环境,规定用“[]”表示物质在金属液中,“()”表示在渣液中,“ { } ”表示在气相中。
6.1.3.1熔渣的碱度炉渣中常见的氧化物按期化学性质有酸性、中性和碱性之分,酸性氧化物酸性由强到弱的顺序是SiO2、P2O5,中性氧化物是AI2O3、Fe2O3、Cr2O3,碱性氧化物碱性由弱到强的顺序是FeO、MnO、MgO、CaO。
碱度是指熔渣中的碱性组元量之总和与酸性组元量之总和的比值,用“ B'来表示。
碱度是判断熔渣碱性强弱的指标,是影响渣、钢反应的重要因素。
由于熔渣中的CaO和SiO2的数量最多,约为渣量的60%以上,所以通常炉渣碱度表示为:(CaO%)(SiO2%)若渣中含磷量较高,则表示为:B =(SiO2% ) (P2O5%)6.1.3. 2熔渣的氧化性炉渣的氧化性是指熔渣氧化金属熔池中杂质元素的能力。
FeO能同时存在于炉渣和钢液中,并在渣一钢之间建立一种平衡(FeO)=[ FeO],所以认为渣中的氧通过FeO传递到钢液中。
(FeO) = [ FeO],=(FeO)[FeO]在一定温度下L o唯一常数,称为氧在熔渣和金属液中的分配系数。
因此渣中FeO的含量可代表炉渣所具备的氧化能力的大小,渣中FeO的含量越高,炉渣氧化性越强。
另外,炉渣碱度对炉渣的氧化性影响也很大,当渣中FeO的含量相同时,炉渣碱度等于约等于2时,炉渣氧化性最强。
渣中FeO的含量多少对造渣过程影响也很大。
渣中FeO的含量过低过低时,造渣困难,炉渣的反应能力低。
渣中FeO的含量过高时,转炉易造成喷溅,增加金属损失和炉衬侵蚀。
因此,渣中氧化铁的含量应适当,在转炉冶炼过程中,一般控制在10〜20%。
6.1.3.3熔渣的还原性熔渣的还原性与氧化性是炉渣同一种化学性质的两种不同说法,即炉渣从金属熔池中夺取氧的能力。
在碱性电弧炉还原期操作中,要求炉渣具有高碱度、低氧化铁、好的流动性,以达到钢液脱氧、脱硫和减少合金元素烧损的目的。
炉外精炼造渣也往往如此。
6.1.4熔渣的物理性质6.1.4. 1熔渣的粘度粘度是表示炉渣内部相对运动时各层之间的内摩擦力的大小。
粘度与流动性正好相反,粘度低则流动性好。
冶炼时,若熔渣粘度过大,质点在熔渣中的移动缓慢,不利于钢、渣之间快速反应;但若粘度过小,又会加剧炉衬的侵蚀。
所以在炼钢时希望炉渣粘度适当。
影响炉渣粘度的主要因素是炉渣成分、温度及未熔质点。
凡能降低炉渣熔点的成分均可以改变熔渣的流动性,降低渣的粘度;熔池温度越高,渣的粘度越小,流动性越好;渣中未熔质点越多,渣的粘度越大。
实际操作中,炉渣粘度主要靠控制渣中的FeO含量、碱度及加入萤石的方法进行调节。
6.1.4.2熔渣的密度密度是熔渣的重要性质之一,它影响着液滴和介质间的相对运动速度,也决定了熔渣所占的体积。
液态熔渣的密度比钢液密度小得多,,一般只有3000kg/m3。
6.2铁、硅、锰的氧化6.2.1熔池内氧的来源熔池内氧的来源主要三个方面第一,向熔池吹入氧气。
它是炼钢过程最主要的供氧方式。
氧气顶吹转炉炼钢,通过 炉口上方插入的水冷氧枪吹入高压纯氧。
电炉通过炉门口吹氧管(或氧枪) 、炉壁氧枪插入熔池供氧。
第二,向熔池中加入铁矿石和氧化铁皮。
铁矿石的主要成分是 Fe 2O 3(赤铁矿)和Fe 3O 4(磁铁矿),氧化铁皮的主要成分是 FeO 。
第三,炉气向熔池供氧。
6.2.2铁的氧化和杂质的氧化方式6.2.2.1铁的氧化1[Fe] + — {0 2} = ( FeO )2 12( FeO ) +{O 2} =( Fe 2O 3)6.2.2.2杂质氧化方式炼钢熔池中除铁以外的各种元素的氧化方式有两种:直接氧化和间接氧化。
直接氧化是指气相中的氧与熔池中的除铁以外的各种元素直接发生氧化反应。
如:1[Mn] +{O 2} = (MnO )2间接氧化是指氧首先和铁发生反应,生成( FeO ),然后(FeO )扩散并溶解于钢中,钢中其他元素与溶解的氧发生氧化反应。
[C] + ( FeO ) = {CO} + [Fe]或 [C] + [O] = {CO}各种元素的氧化以间接氧化为主。
6.2.3硅的氧化6.2.3.1硅的氧化反应式在碱性炼钢法中,Si 的氧化对成渣过程和炉衬的侵蚀有重要的影响。
直接氧化:[Si] + {O 2} = ( SiO 2) 放热间接氧化:[Si] + 2 (FeO ) = (SiO 2) +[Fe]放热Si 的氧化产物SiO 2只溶于炉渣,不溶于钢液。
6.2.3.2硅氧化反应的主要特点 Si 氧化反应的特点如下:(1) 由于Si 与氧的亲和力很强,所以在冶炼初期,钢中的硅就能基本氧化完毕。
同时由于硅的氧化产物 SiO 2在碱性渣中完全与碱性氧化物如 CaO 结合,无法被还原出来,氧化很完全彻底;(2) 硅的氧化是一个强放热反应,低温有利于反应迅速进行。
硅是转炉吹炼过程中重 要的发热元素,铁和氧的亲和力小于 所以铁最先被氧化。
Si 、Mn 、P ,但由于金属液中铁的浓度最大(质量分数为 90%),但硅高会增加渣量,增大热损失。
6.2.4锰的氧化6.241锰硅的氧化反应式直接氧化:间接氧化:[Mn] + ( FeO ) = ( MnO ) + [Fe] 放热Mn 的氧化产物只溶于炉渣,不溶于钢液。
6.2.3.2锰氧化反应的主要特点 Mn 氧化反应的特点如下:(1) Mn 与氧的亲和力很强, 并且Mn 的氧化是强放热反应, 故Mn 的氧化也是在冶炼 初期进行; (2) 由于Mn 的氧化产物MnO 是碱性氧化物,故碱性渣不利于Mn 的氧化,Mn 的氧 化不象Si 的氧化那样完全;(3) 当温度升高后,Mn 的氧化反应会逆向进行, 发生Mn 的还原,即发生 回锰现象”, 使钢中余锰”增加。
6.3碳的氧化6.3.1碳氧反应的意义碳氧反应是炼钢过程中最重要的一个反应。
一方面,把钢液中的碳含量降到了所炼钢 种的规格范围内。
另一方面,碳氧反应时产生的大量CO 气泡从熔池中逸出时,引起熔池的剧烈沸腾和搅拌,对炼钢过程起到了极为重要的作用,具体如下:(1) 加速了熔池内各种物理化学反应的进行; (2) 强化了传热过程;(3) CO 气泡的上浮有利于钢中气体[H]、[N]和非金属夹杂物的去除;(4) 促进了钢液和熔渣温度和成分的均匀,并大大加速成渣过程; (5) 大量的CO 气泡通过渣层,有利于形成泡沫渣。
6.3.2碳的氧化反应6.3.2.1氧气流股与金属液间的 C — O 反应在氧气炼钢中,金属中一少部分碳可以受到直接氧化。
1[C] + {O 2} = {CO}+136000J2该反应放出大量的热,是转炉炼钢的重要热源。
在氧射流的冲击区及电炉炼钢采用吹 氧管插入钢液吹氧脱碳时,氧气流股直接作用于钢液,均会发生此类反应。
脱碳示意图分别如图6-1和图6-2所示。
流股中的气体氧与钢液中的碳原子直接接触,反应生成气体产物一 氧化碳,脱碳速度受供氧强度的直接影响,供氧强度越大,脱碳速度越快。
[Mn] +1尹2}=(MnO )放热6.3.2.2金属熔池内部的C —O 反应金属熔池中大部分的碳是同溶解在金属中的氧相作用而被间接氧化。
[C] + [O] = {CO} 该反应微弱放热反应,温度降低有利于反应的进行。
在转炉和电炉炼钢吹氧脱碳时,气体氧会使熔池内的铁原子大量氧化成(Fe0), 或由加入矿石或氧化铁皮在钢、渣界面上还原形成(FeO),然后(FeO)扩散并溶解于钢中,钢中[C]溶解的[O]发生作用。
6.3.2.3金属液与渣液界面的C—O 反应当渣中(FeO)含量较高时,渣中的(FeO), 一方面会向钢液中扩散,发生第二类反应,另一方面也会直接发生界面反应,如下:[C] + (FeO) = {CO} + [Fe]6.4 脱磷在大多数情况下,磷对钢的质量是有害的。
随着钢中磷含量的增加,使钢的塑性和韧性降低,特别是低温冲击韧性降低,称为“冷脆” 。
6.4.1脱磷的基本反应和基本条件脱磷的基本反应为:2[P] + 5 (FeO) + 4 (CaO) = (4 CaOP2O5) + 5[Fe] 放热综合脱磷反应式可以得到脱磷的基本条件为:(1)炉渣碱度适当高(B=2.5〜3.0最好);(2)渣中的氧化铁适当高(15〜20%);(3)适当的低温(1450〜1500C);(4)大渣量电炉炼钢采用自动流渣、放旧渣造新渣的方法;( 5)炉渣流动性好。
6.4.2回磷磷从炉渣重新返回钢液的现象称为“回磷” 。
一般认为回磷现象的产生与以下因素有关:钢液温度过高,脱氧剂的加入使渣中( FeO)大大降低,脱氧产物和耐火材料中SiO2的溶入使炉渣碱度降低等。
生产中抑制回磷的常用方法是:出钢前向炉内加入石灰使终渣变稠;挡渣出钢;出钢过程中向钢包中加入石灰粉稠化钢包内渣,保持碱度,减弱渣的反应能力;控制出钢温度不要太高等。
6.5 脱硫硫是钢中的有害元素,主要使钢在进行热加工时产生裂纹甚至断裂,称为“热脆”。
钢中硫含量高时,还使钢的横向机械性能和焊接性能下降。
6.5.1脱硫的基本反应和基本条件脱硫的基本反应为:(FeS + (CaO) = (CaS) + (FeO) 吸热综合脱硫反应式可以得到脱硫的基本条件为:(1)炉渣碱度适当高(B=3.0〜3.5最好)。
(2)渣中的氧化铁低渣中的氧化铁低对脱硫有利;但氧气转炉为改善炉渣流动性,促进石灰快速成渣,形成高碱度炉渣,使用(FeO)含量(15〜20%)炉渣也能脱硫,但效果远不如碱性的还原渣。