72塑料制品的成型工艺分析
塑料成型工艺及塑料制件的结构工艺性

塑料成型工艺及塑料制件的结构工艺性塑料成型工艺主要有注塑成型、挤塑成型、吹塑成型、压塑成型等。
注塑成型是通过在注塑机加热并熔化塑料,然后通过射出装置将熔化塑料注入模具腔中,随后冷却硬化成型的方法。
这是最常用、最广泛应用的塑料加工方法之一、挤塑成型是通过从挤出机中将熔化后的塑料挤出成型,逐步冷却硬化的方法。
吹塑成型是通过将熔化的塑料吹入膨胀的模具腔中,并通过高压气体使其充分膨胀,最终形成所需的形状。
压塑成型是通过将熔化后的塑料放入模具中,并施加一定的压力,使其在模具中充分流动并冷却硬化。
在进行塑料制件的结构设计时,首先要考虑制品的功能要求和使用要求。
基于这些要求,需要选择适合的塑料材料,并设计合适的结构形式和尺寸。
在设计结构时,需要考虑制品的强度、刚度、韧度、耐热性、耐候性等性能要求,并选择合适的结构形式来满足这些要求。
例如,对于要求强度和刚度较高的制品,可以采用加强筋、壁厚增加等方法来增强结构的强度和刚度。
对于要求耐热性较高的制品,可以采用具有较高耐热性的塑料材料,或者采用增加空气孔洞、降低制品厚度等方法来改善结构的耐热性。
在制造过程中,还需要考虑塑料制件的工艺性。
工艺性是指在制造过程中,塑料制件的形状和尺寸的复杂程度,以及制造工艺的难易程度。
一般来说,制造过程中,塑料制件的形状和尺寸越简单,工艺性越好;相反,形状和尺寸越复杂,工艺性越差。
因此,在进行结构设计时,需要尽量简化制品的形状和尺寸,减少材料的浪费,并提高制造的效率和质量。
此外,还需要考虑到塑料的收缩性和变形性。
塑料在冷却过程中会发生收缩,导致制品的尺寸变小。
因此,在设计结构时,需要根据塑料材料的收缩性进行适当的补偿,以保证制品的尺寸符合要求。
在制造过程中,还需要考虑到塑料的变形性,避免塑料制件在制造过程中因为受到应力而产生变形。
总之,塑料成型工艺及塑料制件的结构工艺性是塑料制品生产过程中不可忽视的重要因素。
通过合理选择成型工艺和进行结构设计,可以有效地提高制品的质量,降低成本,满足用户需求。
塑料制品的制造工艺与成型方法
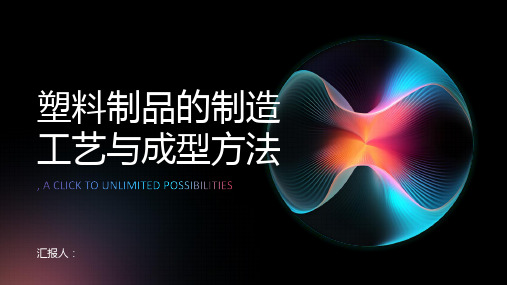
塑料门窗:轻便、耐用、隔音效果好
塑料管道:耐腐蚀、抗老化、使用寿命长
塑料防水材料:防水效果好、施工方便
塑料装饰材料:色彩丰富、造型多样、易于清洁
汽车行业
汽车内饰:塑料制品可用于制作汽车内饰,如座椅、门板、仪表板等。
汽车外饰:塑料制品可用于制作汽车外饰,如保险杠、后视镜、车灯等。
汽车零部件:塑料制品可用于制作汽车零部件,如发动机罩、空气滤清器、油箱等。
医疗行业:塑料医疗器械、耗材、包装等
THANK YOU
汇报人:
混合:将各种原料按照配方比例混合均匀,形成混合料
塑料的成型工艺
塑料的二次加工
热成型:将塑料片材加热至软化,通过模具成型
挤出成型:将塑料熔融后通过挤出机挤出,冷却成型
注射成型:将塑料熔融后通过注射机注射,冷却成型
吹塑成型:将塑料熔融后通过吹塑机吹塑,冷却成型
塑料制品的质量控制
原材料选择:选择优质、稳定的原材料供应商
浇注成型
工艺流程:塑料熔化→浇注系统→模具→冷却固化→脱模
原理:将塑料熔体通过浇注系统注入模具中,冷却固化后得到制品
特点:适用于大型、复杂、薄壁制品的生产
浇注系统:包括浇注口、流道、浇口等,设计合理可以提高生产效率和产品质性,通过模具成型
应用:广泛应用于汽车、电子、医疗等领域
原理:利用压缩空气将熔融的塑料吹入模具,形成中空制品
缺点:产品质量受模具和工艺参数的影响较大
应用:广泛应用于生产饮料瓶、化妆品瓶等塑料制品
压延成型
定义:将塑料通过压延机加工成片材或薄膜的成型方法
优点:生产效率高,产品质量好,适用于大规模生产
工艺流程:喂料→塑化→压延→冷却→卷取
应用领域:广泛应用于包装、建筑、汽车等行业
塑料制品制作工艺

塑料制品制作工艺塑料制品是我们日常生活中不可或缺的一部分,从日常用品到工业产品,塑料制品无处不在。
塑料制品的制作工艺经过多年的发展和改进,变得越来越精密和高效。
在本文中,我们将深入探讨塑料制品的制作工艺,了解其主要步骤和关键技术。
首先,塑料制品的制作工艺通常包括以下几个主要步骤:原料准备、塑料熔化、模具注塑、冷却固化、脱模、后处理等。
每个步骤都至关重要,影响着最终产品的质量和性能。
在原料准备阶段,需要准备好所需的塑料原料,通常为塑料颗粒或颗粒。
不同的塑料原料具有不同的性能和特点,选择合适的原料对最终产品的质量至关重要。
在这个阶段,还需要对原料进行配料、混合和干燥等处理,确保原料的质量和稳定性。
塑料熔化是制作塑料制品的关键步骤之一。
在塑料熔化过程中,将塑料原料加热至熔化状态,使其成为流动状,便于进一步加工。
常见的塑料熔化方法包括挤出、注塑、吹塑等,根据不同的产品要求和生产规模选择合适的熔化方法。
模具注塑是制作塑料制品的核心工艺。
在模具注塑过程中,将熔化的塑料原料注入模具中,经过一定的压力和温度,使塑料填充模具腔体,形成产品的外形和结构。
模具的设计和制造至关重要,直接影响着产品的质量和成型效果。
冷却固化是模具注塑后的一个重要步骤。
在冷却固化过程中,待成型的塑料制品在模具中冷却,塑料逐渐固化和变硬,成为具有一定强度和稳定性的制品。
冷却固化的速度和方式对产品的性能和外观有着重要影响,需要合理控制和调节。
脱模是塑料制品制作工艺的最后一步,也是最关键的一步。
在脱模过程中,将冷却固化的塑料制品从模具中取出,通常需要采用一定的脱模装置和方法,确保产品的完整和光滑。
脱模的质量和效率直接影响着生产的速度和产品的质量,需要严格控制和操作。
除了以上的主要制作步骤,塑料制品制作工艺还包括一系列的后处理工艺,如去毛刺、热处理、喷涂等,以提高产品的表面质量和功能性。
这些后处理工艺的选择和操作需要根据具体产品的要求和应用领域进行合理设计和实施。
塑料制品成型工艺流程的产品外观质量控制
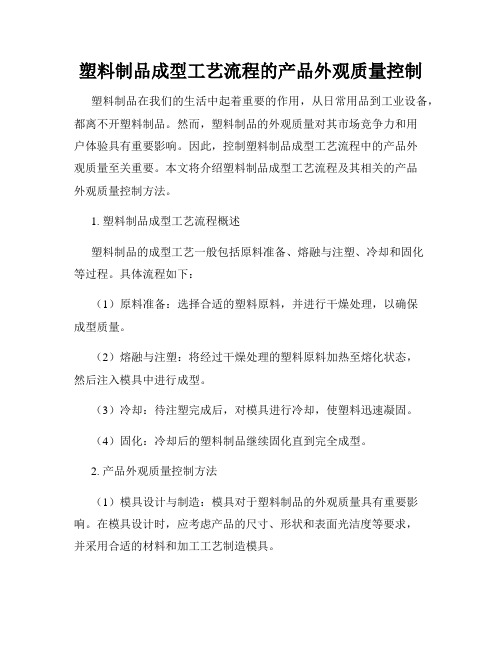
塑料制品成型工艺流程的产品外观质量控制塑料制品在我们的生活中起着重要的作用,从日常用品到工业设备,都离不开塑料制品。
然而,塑料制品的外观质量对其市场竞争力和用户体验具有重要影响。
因此,控制塑料制品成型工艺流程中的产品外观质量至关重要。
本文将介绍塑料制品成型工艺流程及其相关的产品外观质量控制方法。
1. 塑料制品成型工艺流程概述塑料制品的成型工艺一般包括原料准备、熔融与注塑、冷却和固化等过程。
具体流程如下:(1)原料准备:选择合适的塑料原料,并进行干燥处理,以确保成型质量。
(2)熔融与注塑:将经过干燥处理的塑料原料加热至熔化状态,然后注入模具中进行成型。
(3)冷却:待注塑完成后,对模具进行冷却,使塑料迅速凝固。
(4)固化:冷却后的塑料制品继续固化直到完全成型。
2. 产品外观质量控制方法(1)模具设计与制造:模具对于塑料制品的外观质量具有重要影响。
在模具设计时,应考虑产品的尺寸、形状和表面光洁度等要求,并采用合适的材料和加工工艺制造模具。
(2)塑料原料控制:选择优质的塑料原料是保证产品外观质量的基础。
应确保原料的纯净度和物理化学性能符合要求,并避免杂质和颜色偏差对成型品质量的影响。
(3)熔融与注塑参数控制:熔融与注塑过程中,需要控制熔融温度、注射速度和压力等参数。
合理的参数设置可以保证塑料在模具中充分填充,并避免成型品出现熔断、气泡和痕迹等缺陷。
同时,注塑过程中应避免过快或过慢的注射速度,以及过高或过低的压力,以免影响外观质量。
(4)冷却与固化控制:冷却过程中,应保持合适的冷却速度和温度,以避免塑料制品的收缩和变形。
固化过程中,可以采用加热或冷却处理,以确保产品的结构稳定性和尺寸精度。
(5)后续处理:塑料制品成型后,还需要进行修整、打磨、清洗和表面处理等后续工序。
这些工序对于产品外观质量的最终呈现起着重要作用。
应确保操作准确并使用适当的工具和材料,以避免划痕、变色和其他损伤。
3. 检测与检验方法为了确保塑料制品成型工艺流程中的产品外观质量,常用的检测与检验方法包括:(1)外观检查:通过目测外观,检查产品是否存在缺陷、瑕疵、变形或颜色偏差等。
塑件成型工艺分析
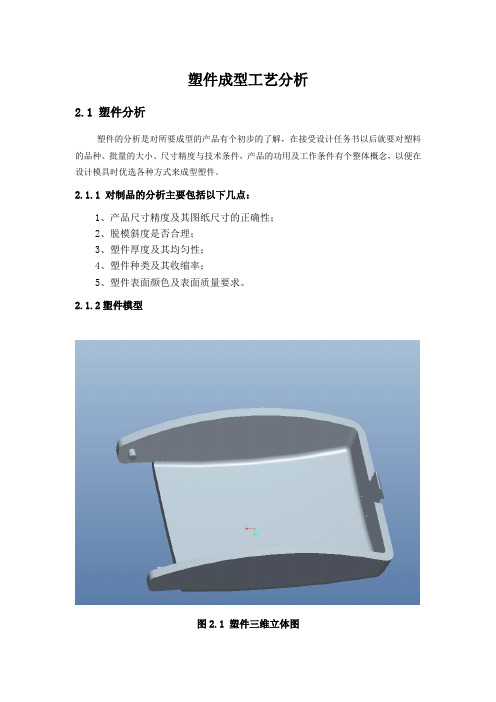
塑件成型工艺分析2.1 塑件分析塑件的分析是对所要成型的产品有个初步的了解,在接受设计任务书以后就要对塑料的品种、批量的大小、尺寸精度与技术条件,产品的功用及工作条件有个整体概念,以便在设计模具时优选各种方式来成型塑件。
2.1.1 对制品的分析主要包括以下几点:1、产品尺寸精度及其图纸尺寸的正确性;2、脱模斜度是否合理;3、塑件厚度及其均匀性;4、塑件种类及其收缩率;5、塑件表面颜色及表面质量要求。
2.1.2塑件模型图2.1 塑件三维立体图485图2.2 塑件平面图2.1.3 塑料 ABS(Acrylonitrile-butadiene-styrene 丙烯腈-丁二烯-苯乙烯) 2.1.4 塑料件质量10.715237(g ) 2.1.5 塑料件体积10.204987(cm ³) 2.1.6 色条 半透明2.1.7 生产纲领:大批量生产 2.1.8工艺结构分析 (1)结构分析塑件结构复杂程度一般,对塑件表面质量有一定的要求。
如上图所示,塑件的内部有突出的小圆柱,外侧有倒扣因而需要考虑侧向分型抽芯机构的设置。
其他结构部分用一般的成型结构即可。
该是塑件比较薄,投影面积较大,需要六个顶杆来顶出。
(2)精度等级选用的尺寸精度等级一般为4 级, 根据GB/ T 14486 - 1993 标准,公差为0.74 mm 。
(3)脱模斜度从表查得ABS 塑件的脱模斜度, 型腔为30′~1°30′, 型芯35′~1°。
脱模斜度取决于塑件的形状、壁厚、及塑料的收缩率。
成型型芯越长或型腔越深,则斜度应取偏小值;反之可选用偏大值。
(塑件内孔以型芯小端为准,塑件外形以型腔大端为准)一般情况下,脱模斜度不包括在塑件的公差范围内。
当要求开模后塑件留在型腔内时,塑件内表面的脱模斜度应不大于塑件外表面的脱模斜度。
2.2 ABS成型特性与工艺参数2.2.1 塑料ABS成型特性(1)名称ABS,中文名,丙烯腈-丁二烯-苯乙烯,英文名,Acrylonitrile-butadiene-styrene。
塑件成型工艺性分析
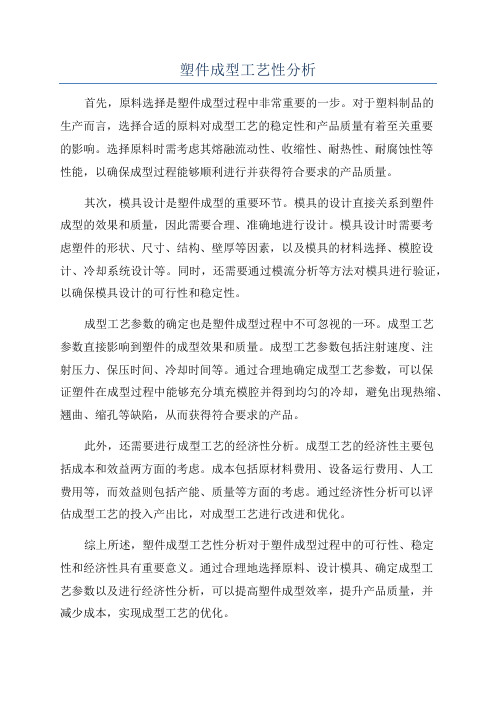
塑件成型工艺性分析首先,原料选择是塑件成型过程中非常重要的一步。
对于塑料制品的生产而言,选择合适的原料对成型工艺的稳定性和产品质量有着至关重要的影响。
选择原料时需考虑其熔融流动性、收缩性、耐热性、耐腐蚀性等性能,以确保成型过程能够顺利进行并获得符合要求的产品质量。
其次,模具设计是塑件成型的重要环节。
模具的设计直接关系到塑件成型的效果和质量,因此需要合理、准确地进行设计。
模具设计时需要考虑塑件的形状、尺寸、结构、壁厚等因素,以及模具的材料选择、模腔设计、冷却系统设计等。
同时,还需要通过模流分析等方法对模具进行验证,以确保模具设计的可行性和稳定性。
成型工艺参数的确定也是塑件成型过程中不可忽视的一环。
成型工艺参数直接影响到塑件的成型效果和质量。
成型工艺参数包括注射速度、注射压力、保压时间、冷却时间等。
通过合理地确定成型工艺参数,可以保证塑件在成型过程中能够充分填充模腔并得到均匀的冷却,避免出现热缩、翘曲、缩孔等缺陷,从而获得符合要求的产品。
此外,还需要进行成型工艺的经济性分析。
成型工艺的经济性主要包括成本和效益两方面的考虑。
成本包括原材料费用、设备运行费用、人工费用等,而效益则包括产能、质量等方面的考虑。
通过经济性分析可以评估成型工艺的投入产出比,对成型工艺进行改进和优化。
综上所述,塑件成型工艺性分析对于塑件成型过程中的可行性、稳定性和经济性具有重要意义。
通过合理地选择原料、设计模具、确定成型工艺参数以及进行经济性分析,可以提高塑件成型效率,提升产品质量,并减少成本,实现成型工艺的优化。
塑料制品的塑胶模具与成型工艺
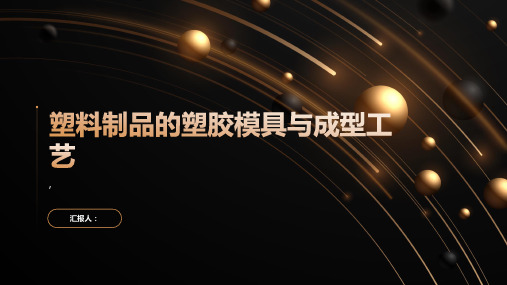
冷却时间:根据 塑胶种类和模具 结构确定
固化过程:塑胶 在模具中逐渐冷 却、硬化,形成 最终形状
脱模:塑胶冷却 固化后,从模具 中取出,完成塑 胶成型过程
清洗方法:使用专用清洗剂 清洗塑胶制品表面
后处理方法:包括清洗、打 磨、喷漆等
脱模过程:从模具中取出塑 胶制品
打磨方法:使用砂纸或磨砂 机对塑胶制品表面进行打磨
模具强度和刚度: 保证模具在生产过 程中不变形、不损 坏
模具冷却系统:合 理设计冷却系统, 保证模具温度均匀, 提高生产效率
模具排气系统:合 理设计排气系统, 保证模具内部气体 顺利排出,避免产 生气泡和烧焦现象
模具材料选择:根 据产品材质和生产 需求选择合适的模 具材料,提高模具 使用寿命和生产效 率
塑胶原料的选择:根据产品 用途、性能要求、成本等因
素进行选择
塑胶原料的处理:干燥、混 合、塑化等,确保原料的质
量和性能
塑胶熔融:将塑胶颗粒加热至熔点以上,使其成为熔融状态 塑胶注射:将熔融的塑胶通过注射机注入到模具中 塑胶冷却:在模具中冷却,使塑胶固化成型 塑胶脱模:将成型的塑胶制品从模具中取出
冷却方式:水冷、 风冷、油冷等
的钢材
钢材的处理:热处理、表面 处理等,以提高钢材的性能
和寿命
优点:重量轻、强度高、耐腐 蚀性好
缺点:成本较高、加工难度较 大
应用:广泛应用于汽车、电子、 家电等行业
选型:根据产品性能要求、成 本预算等因素综合考虑
锌合金的特点:具有良好的耐磨性、耐腐蚀性和抗冲击性 锌合金的应用:广泛应用于塑胶模具制造,如注塑模具、压铸模具等 锌合金的优点:易于加工、成本低、使用寿命长 锌合金的缺点:硬度较低,不适合用于高精度模具制造
塑料成型技术分析(1)

塑料成型技术分析一、塑模温度控制【一】温度控制必要性(1)温度控制对成形性之目的及作为成形品外观,材料物理性质,成形循环等,受模仁温度之影响,颇为显著。
一般成型情况,模仁温度保持于较低,可以提高射出次数较为理想,但与成形品形状(模仁构造)及成品材料种类有关之成形循环亦寄赖于必需提高模仁充填之温度。
(2)为防止应力作温度控制此为成形品材料问题,此项要求唯有※冷却速度。
入冷确时间短,即使有一部份硬化一部份尚软之场合,仍能避免由于不均一收缩引起应力。
亦即适当之温度控制能对冷却应力性质改良。
(3)成形材料之结晶化程度调整之做之温度控制聚硫氨(尼龙),聚醋酸数脂,聚丙烯等结晶材料对结晶化程度调节,及机械性质改良,一般需要较高模仁温度。
【二】技术问题(1)温度控制所需之热传面积模仁热传面积之计算式为t1:成形材之熔融温度t0:成形品取出时温度cp:成形材料之比热sh:每小时射出成形次数移动热量Q=shx*cp*(t1-t0)kacl /hrhw:冷却管路侧之表膜热传系数d:冷却孔直径(m)u:粘度(kg/m ses)μ:流速(m/ses)λ :冷媒之热传导率(kcal/m2hrc)ΔT:模型及冷(热)媒间之平均温度差则Hw:λd(dug/μ)x8.0(cp u /λ)2hr℃)(kcal/m所需之热传面积可由下式求得之A=Q/hwx T (m2)此际对外界空气之放热、型模板、喷嘴等之热传俱行略去不计。
图1 热传路径图2温度变化曲线(2)冷却管路之分布成形循环时间缩短虽有种种因素,但冷却效果卓越之模型制造为重大之问题。
冷却不均一,实行急遽冷却,将使成形品内部产生应力,发生变形及龟裂。
所以必需相应穴形状及肉厚,考虑模仁构造,使能有实施均一而高效率之冷却性能。
再者,就模型管路加工场合综合考虑,选定管路之数量与大小。
例如图1所示,相同成形品面积之场合,模仁(a)有5条较大管路,型模(b)有2条较小管路互作比较,依照热传路径略图所示,型模(a)之型穴表面几乎有相等热传,有均一之冷却效果,较为适用。
- 1、下载文档前请自行甄别文档内容的完整性,平台不提供额外的编辑、内容补充、找答案等附加服务。
- 2、"仅部分预览"的文档,不可在线预览部分如存在完整性等问题,可反馈申请退款(可完整预览的文档不适用该条件!)。
- 3、如文档侵犯您的权益,请联系客服反馈,我们会尽快为您处理(人工客服工作时间:9:00-18:30)。
线状成型法 ——人造纤维
板状成型法 ——薄板材料或片状材料(胶 片薄板、塑料薄膜)
立体状成型法(模塑成型法) ——把塑料模塑成
工
具
为几何形状、尺寸精度、物理性
塑料模具 能等符合使用要求的制品。
模塑成型法
压缩模 压棍(模) 真空成型模
压注模
注射模
流动性差:如聚碳酸酯、硬聚氯乙烯、聚苯醚、氟塑料等。
2.流动性
影响流动性的主要因素:
温度 料温高则流动性增大,但不同塑料也各有差异。如PS(聚苯乙
烯)、PA(尼龙) 、PMMA聚甲基丙烯酸甲脂(丙烯)、ABS (丙烯腈-丁二烯-苯乙烯共聚物)、PC(聚碳酸醋)。
压力 注射压力增大则熔体受剪切作用大,流动性也增大。 如PE
吹塑成型 真空及压缩空气成型 气辅成型
2.按成型过程中物理状态不同分 : 熔融成型
压缩成型压机
压缩模具
压缩成型产品
2.按成型过程中物理状态不同分 :
压注成型压机
压注原理 熔融成型
压注成型产品
2.按成型过程中物理状态不同分 :
注射成型压机
熔融成型
注射原理
注射成型产品
2.按成型过程中物理状态不同分 : 熔融成型
塑料成型理论的进展
温度分析
温度分析
模具冷却系统设计分析 气辅—气体穿透分析
流道优化设计分析
二 塑料模塑成型及模具技术的发展动向
1.塑料成型技术的发展 塑料成型理论的进展(各种流变行为的研究 ) 塑料成型方法的革新(针对新型塑料和具有特殊要求的塑件 ) 制品的精密化、微型化和超大型化
2.产品市场的发展
⑵塑件结构 :塑件的形状、尺寸、壁厚、有无嵌件、 嵌件数量及其分布均影响收缩率的大小。塑件的形 状复杂、尺寸较小、壁薄、有嵌件、嵌件数量多且 对称分布,其收缩率小。
三 热塑性塑料成型的工艺性能
1.收缩性
影响收缩的基本因素:
⑶模具结构:模具的分型面、浇口形式及尺寸等因 素直接影响料流方向、密度分布、保压补缩作用及 成型时间。浇口大,收缩小,各向异性大,沿料流 方向收缩小,垂直料流方向收缩大。浇口小,浇口 凝结收缩得不到补充,收缩大。
(聚乙烯) 、PP(聚丙烯)、POM(聚氧甲烯)。
模具结构 凡促使熔体降低温度,增加流动性阻力的则流动性就降
低。
三 热塑性塑料成型的工艺性能
3.结晶性
所谓结晶现象即为塑料由熔融状态到冷凝时,
分子由独立移动,完全处于无次序状态,变成分子 停止自由运动,按略微固定的位置,并有一个使分 子排列成为正规模型的倾向的一种现象。
结晶型塑料 非结晶型(又称无定形)塑料
三 热塑性塑料成型的工艺性能
3.结晶性
一般结晶性塑料为不透明或半透明
一般非结晶型塑料(无定形料)为透 明(如有机玻璃等)
例外:
聚(4)甲基戍烯为结晶型塑料却有高透明性 ABS为无定形塑料但却并不透明
三 热塑性塑料成型的工艺性能
3.结晶性
结晶型塑料在模具设计及选择注塑机时的要求
塑料成型工基础
心灵纯洁的人, 生活充满甜蜜和喜悦
——列夫·托尔斯泰
7-2 塑料制品的成型工艺
基本内容: 1.了解塑料制品的成型方法; 2.掌握塑料成型的工艺特性。
重点难点: 1.重点:塑料成型的工艺特性 2.难点:对概念的理解,如收缩性、流动性
7-2 塑料制品的成型工艺
挤出机头
挤出成型产品
挤出成型过程
2.按成型过程中物理状态不同分 : 固相成型
吹塑成型压机
吹塑原理
吹塑成型产品
2.按成型过程中物理状态不同分 : 固相成型
真空成型模具
真
空
成
型
产
品
2.按成型过程中物理状态不同分 : 固相成型
气辅成型塑件
气辅模具
气针装置
气辅模具
模具配置气针装置, 由气体产生器(惰性气 体)向气针装置供气, 以实现气辅。
塑料成型方 法及其模具
挤出模 吹塑模
彩印模
搪塑模
发泡模 热压印模
2.按成型过程中物理状态不同分 :
熔融成型 —— 把塑料加热至熔点以上(使之处 于熔融态),对其进行成型加工的一种方法。
注射成型 挤出成型 压缩成型 压注成型
固相成型 —— 塑料处在熔融温度以下(至少 低于熔点10-20℃ ),塑料尚处于软化状态 时进行的一种成型方法。
⑷成型条件:模温高,熔体冷却慢,则塑件密度低, 收缩大。压力高,时间长则收缩小,方向性大。料 温高,收缩大,方向性小。
三 热塑性塑料成型的工艺性能
1.收缩性
收缩率的计算:
ab S实 b
式中: S实── 实际收缩率(%) S计── 计算收缩率(%)
a ── 塑件在成型温度时的尺寸(mm) b —— 塑件在室温下的尺寸(mm) c —— 塑模在室温下的尺寸(mm)
3.塑料模具发展趋势(大型化 、高精度、多功能复 合模、热流道模具)
随着塑料工业的蓬勃发展,塑料成型加工技术 也不断推陈出新。我们在学习本课程时,还要注 意学习国内外的新技术、新工艺、新经验,为使 我国塑料成型加工技术赶超世界先进水平作出贡 献。
三 热塑性塑料成型的工艺性能
1.收缩性 塑件从模具中取出冷却到室温后,塑件的各部分
三 热塑性塑料成型的工艺性能
2.流动性
塑料熔体在一定温度与压力下填充型腔的能力称为流 动性。
常用塑料根据它的流动性可分为三类: 流动性好:如聚乙烯、聚丙烯、聚苯乙烯等。 流动性中等:如改性聚苯乙烯、ABS(丙烯腈-丁二烯-苯 乙烯共聚物 )、AS(丙烯腈-苯乙烯树脂 )、聚甲基丙烯 酸甲酯、聚甲醛、氯化聚醚等。
及注意事项: 料温上升到成型温度所需的热量多,要用塑化 能力大的设备。 冷凝时放出热量大,要充分冷却。
三 热塑性塑料成型的工艺性能
4.热敏性及水敏性
热敏性(热稳定性) —— 对热较为敏感,在高温下受热
时间较长或进料口截面过小而致剪切作用增大使料温增高,
易出现变色、降解、分解的倾向。这种性能称为热敏性。
尺寸都比原来在模具中的尺寸有所缩小,这种性能称
为收缩性。 成型收缩的形式:
(1)塑件的尺寸收缩 (2)收缩方向性 (3)后处理收缩
三 热塑性塑料成型的工艺性能
1.收缩性
影响收缩的基本因素:
⑴塑料品种 :塑料品种不同,收缩率也不同。同种 塑料如各种组分的比例不同,分子量大小不同,则 收缩率也不相同。树脂的相对分子质量高、含量多、 含有机填料,则收缩率大。
如PVC(聚氯乙烯) 、POM (聚氧甲烯)等