塑件结构工艺性分析
注塑件设计要点——结构设计
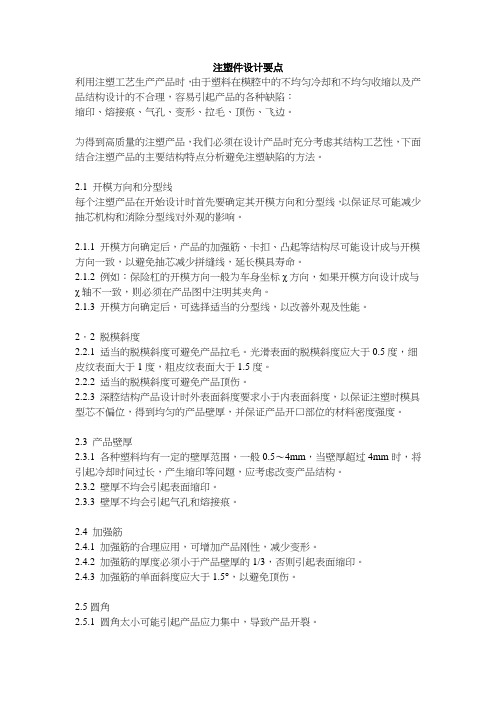
注塑件设计要点利用注塑工艺生产产品时,由于塑料在模腔中的不均匀冷却和不均匀收缩以及产品结构设计的不合理,容易引起产品的各种缺陷:缩印、熔接痕、气孔、变形、拉毛、顶伤、飞边。
为得到高质量的注塑产品,我们必须在设计产品时充分考虑其结构工艺性,下面结合注塑产品的主要结构特点分析避免注塑缺陷的方法。
2.1 开模方向和分型线每个注塑产品在开始设计时首先要确定其开模方向和分型线,以保证尽可能减少抽芯机构和消除分型线对外观的影响。
2.1.1 开模方向确定后,产品的加强筋、卡扣、击起等结构尽可能设计成与开模方向一致,以避免抽芯减少拼缝线,延长模具寿命。
2.1.2 例如:保险杠的开模方向一般为车身坐标χ方向,如果开模方向设计成与χ轴不一致,则必须在产品图中注明其夹角。
2.1.3 开模方向确定后,可选择适当的分型线,以改善外观及性能。
2〃2 脱模斜度2.2.1 适当的脱模斜度可避免产品拉毛。
光滑表面的脱模斜度应大于0.5度,细皮纹表面大于1度,粗皮纹表面大于1.5度。
2.2.2 适当的脱模斜度可避免产品顶伤。
2.2.3 深腔结构产品设计时外表面斜度要求小于内表面斜度,以保证注塑时模具型芯不偏位,得到均匀的产品壁厚,并保证产品开口部位的材料密度强度。
2.3 产品壁厚2.3.1 各种塑料均有一定的壁厚范围,一般0.5~4mm,当壁厚超过4mm时,将引起冷却时间过长,产生缩印等问题,应考虑改变产品结构。
2.3.2 壁厚不均会引起表面缩印。
2.3.3 壁厚不均会引起气孔和熔接痕。
2.4 加强筋2.4.1 加强筋的合理应用,可增加产品刚性,减少变形。
2.4.2 加强筋的厚度必须小于产品壁厚的1/3,否则引起表面缩印。
2.4.3 加强筋的单面斜度应大于1.5°,以避免顶伤。
2.5圆角2.5.1 圆角太小可能引起产品应力集中,导致产品开裂。
2.5.2 圆角太小可能引起模具型腔应力集中,导致型腔开裂。
2.5.3 设置合理的圆角,还可以改善模具的加工工艺,如型腔可直接用R刀铣加工,而避免低效率的电加工。
模具设计-塑件的结构工艺性

一般模具表面粗糙度要比塑件的要求高 1~2级。
三、塑件的几何形状
1.塑件的壁厚 (1)塑件壁厚设计原则:
①满足塑件结构和使用性能要求下取小壁厚; ②能承受推出机构等的冲击和振动; ③制品连接紧固处、嵌件埋入处等具有足够的厚度; ④保证贮存、搬运过程中强度所需的壁厚; ⑤满足成型时熔体充模所需的壁厚,见P74表3.14、3.15 ;
二、塑件的尺寸、精度和表面粗糙度
1.塑件的尺寸
(1)塑件的尺寸是指塑件的总体尺寸。 (2)塑件的尺寸受下面两个因素影响:
①塑料的流动性(大而薄的塑件充模困难) ②设备的工作能力(注射量、锁模力、工作台面)
2.塑件的精度
(1)塑件的尺寸精度是指所获得的塑件尺寸与产品图中尺寸的符合程度, 即所获塑件尺寸的准确度。 (2)影响塑件尺寸精度的因素:
塑件公差等级的选用见P70表3.10。
(3)塑件尺寸精度的确定(续)
对于塑件上孔的公差可采用基准孔,可取表中数值冠以(+)号。 对于塑件上轴的公差可采用基准轴,可取表中数值冠以(-)号。 一般配合部分尺寸精度高于非配合部分尺寸精度。
模具尺寸精度比塑件尺寸精度高2-3级。
3.塑件的表面质量
表面质量
表面粗糙度、光亮程度 色彩均匀性 表面缺陷:缩孔、凹陷 推杆痕迹 对拼缝、熔接痕、毛刺等
2.塑料原料选择方法:
使用环境: 不同的温度、湿度及介质条件、不同的受力类型选择不同的塑料;
使用对象: 使用塑料制品的国别、地区、民族和具体使用者的范围、国家不同,其
标准规格也不同。
按用途进行分类: 按应用领域分类,如汽车运输工业用、家用电气设备用、机械工业用、
建筑材料用、宇航和航空用等;按应用功能分类,如结构材料、低摩擦擦 材料、受力机械零件材料、耐热、耐腐蚀材料、电绝缘材料、透光材料等。
水杯的塑件结构工艺性分析

水杯的塑件结构工艺性分析
针对水杯的塑件结构,其工艺性分析主要包括以下几个方面:
1.材料选择:水杯塑料件的材料选择对工艺性影响很大,要考虑其熔体流动性、热稳定性、耐久性等特性。
通常选择聚乙烯、聚丙烯、ABS、PVC等塑料材料。
2.模具设计:水杯塑件的模具设计要考虑到结构复杂程度、尺寸精度、成型效率等因素,以确保生产出的产品具有稳定的尺寸和质量。
同时,设计时还要注重模仁布置、冷却系统等工艺细节。
3.注塑工艺:注塑工艺参数包括模温、射出速度、射出压力、保压时间等。
不同的塑料材料和产品要求会对这些参数产生影响,需要根据实际情况进行调整以保证质量和速度。
4.后处理工艺:水杯塑件在成型后需要进行后处理,包括精修、气孔处理、油漆喷涂等环节。
这些工艺都需要有相应的技能和经验,对于成品质量和外观效果的影响也很大。
总之,对于水杯塑件结构工艺性的分析需要综合考虑材料、模具设计、注塑工艺和后处理等多个方面。
这些因素的优化与协调可以大大提高产品的生产效率和质量,降低不良率和生产成本。
塑料注塑性能工艺概括
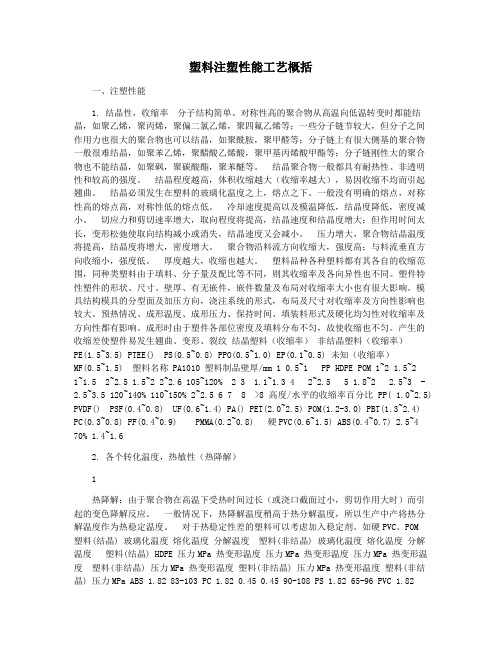
塑料注塑性能工艺概括一、注塑性能1. 结晶性,收缩率分子结构简单、对称性高的聚合物从高温向低温转变时都能结晶,如聚乙烯,聚丙烯,聚偏二氯乙烯,聚四氟乙烯等;一些分子链节较大,但分子之间作用力也很大的聚合物也可以结晶,如聚酰胺,聚甲醛等;分子链上有很大侧基的聚合物一般很难结晶,如聚苯乙烯,聚醋酸乙烯酸,聚甲基丙烯酸甲酯等;分子链刚性大的聚合物也不能结晶,如聚砜,聚碳酸酯,聚苯醚等。
结晶聚合物一般都具有耐热性、非透明性和较高的强度。
结晶程度越高,体积收缩越大(收缩率越大),易因收缩不均而引起翘曲。
结晶必须发生在塑料的玻璃化温度之上,熔点之下。
一般没有明确的熔点,对称性高的熔点高,对称性低的熔点低。
冷却速度提高以及模温降低,结晶度降低,密度减小。
切应力和剪切速率增大,取向程度将提高,结晶速度和结晶度增大;但作用时间太长,变形松弛使取向结构减小或消失,结晶速度又会减小。
压力增大,聚合物结晶温度将提高,结晶度将增大,密度增大。
聚合物沿料流方向收缩大,强度高;与料流垂直方向收缩小,强度低。
厚度越大,收缩也越大。
塑料品种各种塑料都有其各自的收缩范围,同种类塑料由于填料、分子量及配比等不同,则其收缩率及各向异性也不同。
塑件特性塑件的形状、尺寸、壁厚、有无嵌件,嵌件数量及布局对收缩率大小也有很大影响。
模具结构模具的分型面及加压方向,浇注系统的形式,布局及尺寸对收缩率及方向性影响也较大。
预热情况、成形温度、成形压力、保持时间、填装料形式及硬化均匀性对收缩率及方向性都有影响。
成形时由于塑件各部位密度及填料分布不匀,故使收缩也不匀。
产生的收缩差使塑件易发生翘曲、变形、裂纹结晶塑料(收缩率)非结晶塑料(收缩率)PE(1.5~3.5) PTEE() PS(0.5~0.8) PPO(0.5~1.0) EP(0.1~0.5) 未知(收缩率)MF(0.5~1.5) 塑料名称 PA1010 塑料制品壁厚/mm 1 0.5~1 PP HDPE POM 1~2 1.5~21~1.5 2~2.5 1.5~2 2~2.6 105~120% 2 3 1.1~1.3 4 2~2.5 5 1.8~2 2.5~3 - 2.5~3.5 120~140% 110~150% 2~2.5 6 7 8 >8 高度/水平的收缩率百分比 PP( 1.0~2.5) PVDF() PSF(0.4~0.8) UF(0.6~1.4) PA() PET(2.0~2.5) POM(1.2-3.0) PBT(1.3~2.4) PC(0.3~0.8) PF(0.4~0.9) PMMA(0.2~0.8) 硬PVC(0.6~1.5) ABS(0.4~0.7) 2.5~4 70% 1.4~1.62. 各个转化温度,热敏性(热降解)1热降解:由于聚合物在高温下受热时间过长(或浇口截面过小,剪切作用大时)而引起的变色降解反应。
塑料模具设计说明书(参考)
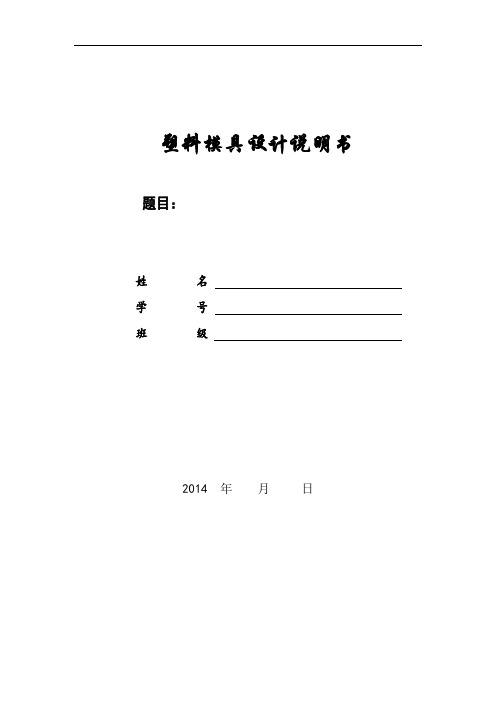
塑料模具设计说明书题目:姓名学号班级2014 年月日目录第一章塑件的工艺分析1.1 任务要求1.2 原料ABS的成型特性和工艺参数1.3 塑件的结构工艺性第二章注射设备的选择2.1 注射成型工艺条件2.2 选择注射机第三章型腔布局与分型面的选择3.1 塑件的布局3.2 分型面的选择第四章浇注系统的设计4.1主流道和定位圈的设计4.2 分流道设计4.3 浇口的设计4.4冷料穴的设计4.5 排气系统的分析第五章主要零部件的设计计算5.1 型芯、型腔结构的确定5.2 成型零件的成型尺寸第六章成型设备的校核6.1、注射成型机注射压力校核6.2、注射量的校核6.3、锁模力的校核相关零件图第一章塑件的工艺分析1.1 任务要求图1 盒盖1.2原料ABS的成型特性和工艺参数ABS是目前产量最大、应用最广的工程塑料。
ABS是不透明非结晶聚合物,无毒、无味,密度为 1.02~1.05 g/cm3。
ABS 具有突出的力学性能,坚固、坚韧、坚硬;具有一定的化学稳定性和良好的介电性能;具有较好尺寸稳定性,易于成型和机械加工,成型塑件表面有较好光泽,经过调色可配成任何颜色,表面可镀铬。
其缺点是耐热性不高,连续工作温度约为70℃,热变形温度约为93℃,但热变形温度比聚苯乙烯、聚氯乙烯、尼龙等都高;耐候性差,在紫外线作用下易变硬发脆。
可采用注射、挤出、压延、吹塑、真空成型、电镀、焊接及表面涂饰等多种成型加工方法。
ABS的成型特性:(1)ABS易吸水,成型加工前应进行干燥处理,表面光泽要求高的塑件应长时间预热干(2)流动性中等,溢边值0.04 mm左右。
(3)壁厚、熔料温度对收缩率影响极小,塑件尺寸精度高。
(4)ABS比热容低,塑化效率高,凝固也快,故成型周期短。
(5)ABS的表观黏度对剪切速率的依赖性很强,因此模具设计中大都采用点浇口形式。
(6)顶出力过大或机械加工时塑件表面会留下白色痕迹,脱模斜度宜取2°以上。
(7)易产生熔接痕,模具设计时应注意尽量减少浇注系统对料流的阻力。
塑料模具毕业,课程设计说明任务书,圆盖注塑模设计与制造(好东西)
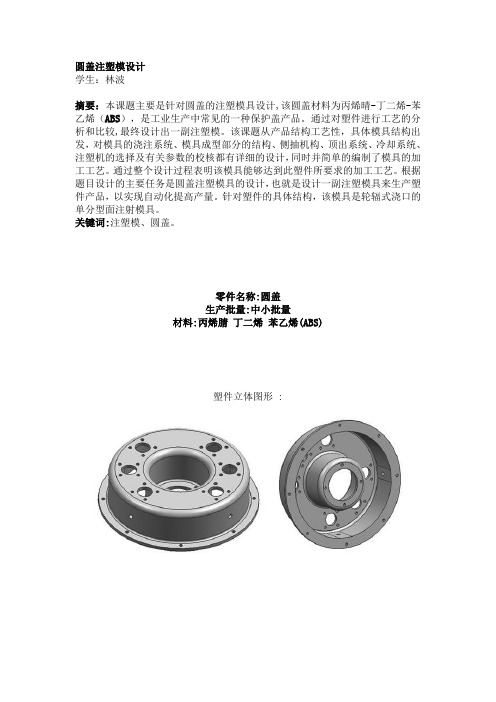
圆盖注塑模设计学生:林波摘要:本课题主要是针对圆盖的注塑模具设计,该圆盖材料为丙烯晴-丁二烯-苯乙烯(ABS),是工业生产中常见的一种保护盖产品。
通过对塑件进行工艺的分析和比较,最终设计出一副注塑模。
该课题从产品结构工艺性,具体模具结构出发,对模具的浇注系统、模具成型部分的结构、侧抽机构、顶出系统、冷却系统、注塑机的选择及有关参数的校核都有详细的设计,同时并简单的编制了模具的加工工艺。
通过整个设计过程表明该模具能够达到此塑件所要求的加工工艺。
根据题目设计的主要任务是圆盖注塑模具的设计,也就是设计一副注塑模具来生产塑件产品,以实现自动化提高产量。
针对塑件的具体结构,该模具是轮辐式浇口的单分型面注射模具。
关键词:注塑模、圆盖。
零件名称:圆盖生产批量:中小批量材料:丙烯腈丁二烯苯乙烯(ABS)塑件立体图形 :一、塑件的工艺性分析塑件的工艺性分析包括:塑件的原材料分析、塑件的尺寸精度分析、塑件表面质量和塑件的工艺性分析,其具体分析如下:1、塑件的原材料分析:塑料品种结构特点使用温度化学稳定性性能特点成型特点丙烯腈、丁二烯、苯乙烯(ABS),属于热塑性塑料非结晶态树脂,不透明小于85-110℃,脆化温度未-18℃有较良好的耐化学试剂性,不耐浓的氧化性酸及醛、酮、酯、氧化烃等不透明,具有良好的综合物理力学性能,耐热、耐腐、耐磨及良好的抗蠕变性,介电性能好,吸水性较强熔融温度高(超过250℃时才出现分解),熔体粘度不太高,流动性中等(溢边值为0.04mm),与流动性和压力有关,对压力更敏感,冷却速度较快,成型收缩小结论: ①熔融温度较高,熔体黏度中等,一般采用螺杆注射机成型,模具温度可控制在60-80℃②吸湿性强,含水量应小于0.3%,必须充分干燥③易发生熔接熔接痕,应注意选择进料口位置形式,顶出力过大或机械加工时塑件表面呈现“白色痕迹”(但在热水中加热可消失),脱模斜度应取2°以上2、塑件的结构工艺性分析:⑴ 从图纸上分析,该塑件的外形为回转体,壁厚均匀,都为3.5mm,且符合最小壁厚要求.⑵ 塑件型腔较大,有尺寸不等的孔,如:36-Ф3.5 、6-Ф16,它们均符合最小孔径要求.⑶ 在塑件侧壁有四个Ф5mm的孔,因此成型后塑件不易取出,需要考虑侧抽装置.3 、塑件的尺寸精度分析:该塑件的未注公差按MT5级公差要求,其余公差要求按制件的制件图所示公差要求塑件的外形尺寸: ФФ内形尺寸: Ф孔尺寸: ФФФФ空心距尺寸: ФФФФ4、塑件表面质量分析:该塑件为工业用圆盖塑料,对其表面质量没有什么高的要求,粗糙度可取Ra3.2um ,塑件内部也不需要较高的表面粗糙度要求,所以内外表面的粗糙度都3取Ra3.2um.结论:该塑件可采用注射成型加工,且加工性能较好,但成型以后需要设置侧抽芯机构才能将塑件顺利脱出.二、成型设备选择与模塑工艺规程编制1、计算塑件的体积:+2、注塑机的初步选择塑件成型所需的注射总量应小于所选注塑机的注射容量.注射容量以容积()表示时,塑件体积(包括浇注系统)应小于注塑机的注塑容量,其关系是:式中- 塑件与浇注系统的体积()- 注射机注射容量()0.8- 最大注射容量利用系数根据塑件的原材料分析,查相关手册①得知该塑件的原材料所需的注射压力为60-100 ,由于塑件的尺寸较大,型芯较多,所以选择较大的注射压力.模具所需的注射压力应小于或等于注射机的额定注射压力,其关系按下式:式中- 塑件成型是所需的压力()- 所选注射机的额定注射压力()模具所需的最大锁模力应小于或等于注射机的额定锁模力,其关系式如下:式中- 模具型腔压力,取45MPa- 塑件与浇注系统在分型面上的投影面积()- 注射机额定锁模力(N)再根据塑件形状及尺寸采用一模一件的模具结构,由以上数据,相关资料②初选螺杆式注塑机:XS-ZY-250.它的注射容量为250,注塑压力为130MPa,锁模力为1800KN,均满足以上条件.3、塑件模塑成型工艺参数的确定ABS注射成型工艺参数见下表,试模时,可根据实际情况作适当调整工艺参数规格工艺参数规格预热和干燥温度t/℃: 80-95成型时间/s 注射时间0-5时间/h: 4-5保压时间15-30料筒温度t/℃ 后段150-170 冷却时间15-30 中段165-180 总周期40-70 前段180-200螺杆转速n/()30-60喷嘴温度t/℃ 170-180后处理方法红外线灯烘箱模具温度t/℃ 50-80 温度t/℃ 70 注射压力p/Mpa 60-100时间/h2-4三、注射模的结构设计注射模结构设计主要包括: 分型面的选择、模具型腔数目的确定及型腔的排列、浇注系统设计、型芯、型腔结构的确定、推件方式、侧抽芯机构的设计、模具结构零件设计等内容.1、分型面的选择该塑件为工业用圆盖塑料,对其表面质量没有什么高的要求,只要求外径没有明显的斑点及熔接痕.在选择分型面时,根据分型面的选择原则,考虑不影响塑件的外观以及成型后能够顺利取出制件如图所示,塑件留动模,塑件的脱模容易实现,且模具的加工相对以上方案简单,方便. 所以,通过对以上几种分型面的考虑以及塑件的外观的要求,选择大端底平面作为分型面的方案较合适.2、型腔数目的确定及型腔的排列由于该塑件采用一模一件成型,所以,型腔布置在模具的中间.这样也有利于浇注系统的排列和模具的平衡.3、浇注系统的设计(1)主流道设计主流道是指浇注系统中从注射机喷嘴与模具接触处开始到分流道为止的塑料熔体的流动通道,是熔体最先流经模具的部分,它的形状与尺寸对塑料熔体的流动速度和充模时间有较大的影响,因此,必须使熔体的温度降和压力损失最小。
塑件的结构工艺性
塑料成型制件的结构工艺性l塑料制件的设计是在满足使用要求的前提下,根据选用塑料的类型及其成型加工特点,确定相应而合理的成型工艺,并根据该成型工艺的特性而设计出相适应的塑料结构件。
l由于塑料有其特殊的物理机械性能,因此设计塑件时必须充分发挥其性能上的优点,避免或补偿其缺点,在满足使用要求的前提下,塑件形状应尽可能地做到简化模具结构,符合成型工艺特点。
l对于模具设计者来说,在考虑塑件的结构及有关使用要求时,还必须与成型该塑件的成型模具的相应结构结合起来考虑,既要使塑料制件能按使用要求加工出来,保证制件的质量,而又要使模具结构合理、经济。
在塑件结构工艺性设计时,应考虑以下几方面的因素:(1)塑料的各项性能特点;(2)在保证各项使用性能的前提下,塑件结构形状力求简单,且有利于充模流动、排气、补缩和高效冷却硬化(热塑性塑料制件)或快速受热固化(热固性塑料制件);(3)模具的总体结构应使模具零件易于制造,特别是抽芯和脱模机构。
一、塑料制件的选材二、塑料制件的尺寸和精度三、塑料制件的表面质量四、塑料制件的结构设计表面粗糙度表观质量形状、壁厚、斜度、加强筋、支撑面、圆角、孔、螺纹、齿轮、嵌件、铰链、标记、符号和文字等一、塑料制件的选材塑料制品的选材应考虑如下几个方面,以判断其是否能够满足使用要求。
1)塑料的力学性能,如强度、刚性、韧性、弹性、弯曲性能、冲击性能以及对应力的敏感性。
2)塑料的物理性能,如对环境温度变化的适应性、光学特性、绝热或电气绝缘的程度、精加工和外观的完满程度等。
3)塑料的化学性能,如对接触物(水、溶剂、油、药品)的耐性、卫生程度以及使用上的安全性等。
4)必要的精度,如收缩率的大小以及各向收缩率的差异。
5)成型工艺性,如塑料的流动性、结晶性、热敏性等。
对于塑料材料的这些要求往往是通过塑料的特性表进行选择和比较的。
下表列出常用塑料的特性,以供参考。
二、塑料制件的尺寸和精度1. 塑件的尺寸–总体尺寸主要取决于塑料品种的流动性Ø在一定的设备和工艺条件下,流动性好的塑料可以成型较大尺寸的塑件;反之,成型出的塑件尺寸较小。
塑件结构工艺性分析
塑件结构工艺性分析一、材料选用塑料是目前广泛应用于各行各业的一种材料,其在结构设计中的应用也越来越广泛。
材料的选择对塑件的结构工艺性有着重要影响。
首先,要考虑塑件的使用环境和功能要求。
例如,如果塑件需要承受较大的载荷和压力,就需要选择具有较高强度和刚度的材料。
如果塑件需要抗紫外线或耐高温,就需要选择具有耐候性或耐高温性能的材料。
其次,要考虑材料的加工性能。
不同的塑料在加工过程中有着不同的性能,如流动性、收缩率、熔体粘度等。
这些性能会直接影响到塑件的成型效果和尺寸稳定性。
最后,要考虑成本和可持续发展。
选择成本较低且可回收再利用的材料有助于降低生产成本和减少环境污染。
二、结构设计塑件的结构设计要考虑到材料的特性和加工工艺的要求,以确保塑件在生产加工过程中能够顺利进行。
首先,要合理设计塑件的形状和尺寸。
过于复杂的形状和过小的尺寸会增加成型难度,导致成型效果不佳。
同时,还应保证塑件的结构设计符合模具的规范要求,以便于模具的设计和制造。
其次,要考虑到塑件的组装和装配工艺。
例如,对于需要进行拼装的塑件,要确保其接口的设计合理,以便于拼装完成后的塑件具有足够的稳定性和可靠性。
最后,还应考虑到塑件的成型和冷却等工艺要求。
合理设计成型孔、冷却孔和浇口等结构,有利于塑件的快速成型和降低成型过程中的内应力,从而提高产品质量和生产效率。
三、加工工艺塑件的加工工艺包括模具设计、塑料注射成型、相关配套工艺等,其中模具设计是塑件结构工艺性的重要环节。
首先,模具的设计和制造要符合塑件的结构设计要求。
模具的结构应简单、密封性好、易于脱模,以便于塑件的成型和脱模。
其次,要根据不同材料的特性确定合适的注射工艺参数。
不同材料的熔体粘度和流动性不同,因此注射温度、注射压力和注射时间等参数需要进行合理调整,以确保塑件的成型效果和尺寸稳定性。
最后,要对塑件进行后续处理。
例如,塑料件常常需要进行去毛刺、修边、抛光、喷涂等处理,以提高产品的表面质量和装饰效果。
注塑件的工艺结构设计
筋与柱子联合使用
柱子基本设计守则
自攻螺钉柱 通过预制孔自钻出螺纹实现胶壳的结合,下图为常用自攻螺
钉及预制孔的选择参照供参考:
加强筋基本设计守则
加强筋有效地增加产品的刚性和 强度而无需大幅增加产品截面面 积
加强筋更可充当内部流道,有助 模腔充填,对帮助塑料流入部件 的支节部份的作用很大。
加强筋的长度可与产品的长 度一致,两端相接产品的外 壁,或只占据产品部份的长 度,用以局部增加产品某部 份的刚性。要是加强筋没有 接上产品外壁的话,末端部 份亦不应突然终止,应该渐 次地将高度减低,直至完结, 从而减少出现困气、填充不 满及烧焦痕等问题 。
聚碳酸酯(PC) 0.95
1.80
2.30 3.00~4.50
有机玻璃 (PMMA)
0.80
2.20 4.00~6.50
壁厚基本设计守则
图例
图例
出模角基本设计守则
取斜度的方向 一般内孔以小端为准,符合图样,斜度由扩大方向取得;外形以
大端为准,符合图样,斜度由缩小方向取得。如左图。
加强筋一般的设计
加强筋基本设计守则
长方形的加强筋必须改变形状使生产更容易,加强筋的两边必须 加上出模角(1~5 °)以减低脱模顶出时的摩擦力,底部相接产 品的位置必须加上圆角以消除应力过份集中的现象,圆角的设计 亦给与流道渐变的形状使模腔充填更为流畅。
加强筋基本设计守则
为防止缩水缺陷及保证加强筋强度,加强筋的宽度一般取壁厚的 1/2~2/3;
具体的咬花深度而定,一般的晒纹版上已清楚例出可供作参考之用的 要求出模角。咬花深度越深,脱模斜度应越大.推荐值为 1°+H/0.0254°(H为咬花深度). 插穿面和枕位面斜度一般为1°~3°。
塑料材料工艺特性
目录1、塑料制品成型机理 (1)1.1结晶效应 (1)1.2取向效应 (2)1.2.1取向机理 (2)1.2.2取向对制品性能的影响 (2)1.3内应力 (2)1.3.1内应力产生 (2)1.3.2影响内应力的工艺因素 (2)1.4 成型原理 (3)2、塑料的工艺特性 (3)2.1 收缩率 (3)2.2 流动性 (4)2.3 硬化速度 (4)3、主要加工方法 (4)3.1 压缩成型 (5)3.1.1成型特点 (5)3.1.2 压塑成型过程和操作方法 (5)3.1.3 压塑成型过程中的控制因素 (5)3.1.4 压缩成型用的设备 (6)3.2 注塑成型 (6)3.2.1 注塑成型的工艺过程 (6)3.2.2 注塑成型的优点 (6)3.2.3 热固性塑料注射成型与热塑性塑料注射成型的比较 (6)3.3.4 热塑性塑料注射成型过程中的控制因素 (7)3.3.5 塑料制品的热处理和调湿处理 (7)3.3.6注塑成型用设备 (8)4、其他成型方法简介 (8)4.1 挤出成型 (8)4.2 中空吹塑成型 (8)4.3 真空成型 (8)5、塑料制品的结构工艺要求 (9)尺寸精度 (9)脱模斜度 (9)壁厚 (9)加强筋 (10)支承面 (10)圆角 (11)孔 (11)嵌件 (11)6、模具设计的工艺性 (12)塑料制件在工业中的应用日趋普遍,这主要是因为它们具有一系列特定的优点。
塑料制件主要优点有:1)塑料密度小、质量轻,这是“以塑代钢”的优点;2)塑料的绝缘性能好,介电损耗低,是电子工业不可缺少的原材料;3)塑料的化学稳定性高,对酸、碱和许多化学药品有良好的耐腐蚀能力;4)塑料减摩、耐磨、减震、隔音等等性能也较好塑料已从代替部分金属、木材、皮革及无机材料发展成为各个部门不可缺少的一种化学材料,并跻身于金属、纤维材料和硅盐酸三大传统材料之列。
1、塑料制品成型机理1.1结晶效应结晶定义:评定聚合物结晶相同的标准是晶体形状、大小及结晶度。
- 1、下载文档前请自行甄别文档内容的完整性,平台不提供额外的编辑、内容补充、找答案等附加服务。
- 2、"仅部分预览"的文档,不可在线预览部分如存在完整性等问题,可反馈申请退款(可完整预览的文档不适用该条件!)。
- 3、如文档侵犯您的权益,请联系客服反馈,我们会尽快为您处理(人工客服工作时间:9:00-18:30)。
•
•图1-1 灯座二维图形
书山有路勤为径, 学海无涯苦作舟
•图1-13 电流线圈架零件图
•
二、相关知识
•(一)塑件设计基本原则
•1、塑料制件的尺寸
指塑料制件的总体尺寸: 塑料流动性 现有的成型设备规格、参数
•2、塑料制件的尺寸精度
为满足塑料制件的装配要求和零件的互换性要求 模具的制造误差 塑料材料的成型收缩率波动 模具在使用过程中的磨损 飞边厚薄的变化 型腔的变形模具零件相互之间的安装定位误差 模具的结构(浇口尺寸和位置、分型面位置、模具的拼合方式) 成型后的条件(测量误差、存放条件)
书山有路勤为径, 学海无涯苦作舟
•
二、相关知识
•(一)塑件设计基本原则
•4.脱模斜度
• 塑料在模腔中冷却收缩,便包紧型芯或型腔中的 凸起部分,为了便于脱模和抽拔,避免脱模和抽拔时 塑件产生划痕、拉毛、变形等缺陷,设计塑件时,沿 脱模和抽拔方向其内外表面均需有一定的斜度。称为
脱模斜度。一般斜度取 30 ′~ 1˚ 30 ′。
推荐值:热固性塑料制品——参见表3-5 热塑性塑料制品——参见表3-6
书山有路勤为径, 学海无涯苦作舟
•
二、相关知识
•(二)塑件局部结构设计
•1.加强筋与防变形机构
设计原则:
为了提高塑件的强度和刚度,不能仅仅采用增大壁厚的方法,而常采用改 变塑件的结构、增设加强筋的方法来满足其强度、刚度的要求。
采用增设加强筋的方法优点
书山有路勤为径, 学海无涯苦作舟
•
二、相关知识
•(二)塑件局部结构设计
•5.螺纹的设计
设计原则:
塑件上的螺纹可以在模塑时直接成型,也可在模塑后用机械切削方式加工,对经常装拆和受力 较大的螺纹,可使用金属的螺纹嵌件。
塑件的面与面之间一般均采用圆弧过渡,这样不仅可避免塑件 尖角处的应力集中,提高塑件强度、而且可改善物料的流动状态, 降低充模阻力,便于充模。另外可便于模具的加工制造及模具强度 的提高,避免模具在淬火或使用时应力开裂。
书山有路勤为径, 学海无涯苦作舟
•
二、相关知识
•(二)塑件局部结构设计
•4.孔的设计 设计原则:
书山有路勤为径, 学海无涯苦作舟
•
二、相关知识
•(一)塑件设计基本原则 •5.壁厚
设计原则: 塑件的壁厚应根据塑件的使用要求来确定。尽量做到壁厚均匀,一
般为1~4mm范围
壁厚 材料消耗增大,成型效率降低,使塑件成本提高。而且还容易 过厚 产生气泡、缩孔、翘曲等缺陷
壁厚 易脱模变形或破裂,不能满足使用要求,且难以充满,成型困 过薄 难——最小壁厚(见经验表格 )
书山有路勤为径, 学海无涯苦作舟
•
二、相关知识
•(一)塑件设计基本原则 •2.塑件的表面质量及表面粗糙度
选择原则:
塑件的表面粗糙度值大小,主要取决于模具型腔(凸凹模)的表面粗 糙度。一般模具型腔的表面粗糙度应比塑件的表面粗糙度值小1~2级。
从塑件的外观和塑件的充模流动角度考虑:
通常应小于Ra 0.8 , 有时需小于Ra 0.1。
根据使用要求(固定、装配)塑件一常需设有孔。孔的位置,应不至 影响塑件的强度,故孔与孔之间、孔与边缘之间应留一定的距离。为了便于 成型及满足孔的质量要求,直接成型的孔的深度不能过大。
•塑件上的固定孔与其它受力孔的周围应采用凸边予以加强。
•成型塑件孔的型芯的 安装方式通常有三种: • 通孔 • 盲孔(注射 h<4d) • 特殊孔
书山有路勤为径, 学海无涯苦作舟
•
二、相关知识
•(二)塑件局部结构设计
•2.支承面
设计原则:
当塑件需有一个支承面时,不能用整个底面作为支承面,因为稍许的 翘曲或变形就会使整个底面不平。设计塑件时通常采用凸边或几个凸起的支 脚作为支承面。当底部有加强筋时,支承面的高度应略高于加强筋。
•3.圆角 设计原则:
•
影响因素众多,设计塑件时需综合考虑
•
塑件的尺寸公差GB/T14486-1993
书山有路勤为径, 学海无涯苦作舟
•
二、相关知识
•(一)塑件设计基本原则
•2. 塑料制件的尺寸精度
•塑件尺寸公差代号MT,分7级, • 每一级分A、B两部分: • A为不受模具活动影响的尺寸公差;B为受模具活动影响的尺寸公差 • 每一种塑料分3个精度等级 • 表中只规定了公差值,上、下偏差可根据塑件的配合性质来分配。 •通常偏差根据“凸负凹正,中心对正”
改变侧孔形状,避免 侧抽芯机构
避免侧孔或 侧凹
改变侧孔斜度,避免 侧抽芯机构
改变塑件角度,避免 侧抽芯机构
菱形纹改为直条纹, 避免瓣合模机构
有侧凸、侧 凹的强 制脱模的
条件
1.塑件具有足够的弹性 (如PE、PP、POM等塑料) 2. ( A-B )/ B ≤ 5 %或 ( A - B ) /C ≤ 5 % 否则用侧向分型抽芯等结构
•设计脱模斜度遵循原则:
• ( 1 )塑料的收缩率大,壁厚,斜度应取偏大值 • ( 2 )塑件结构复杂,斜度应取偏大值 • ( 3 )型芯长或深型腔为了便于脱模,在满足制件的使用和尺寸公差要求的前提下斜度值 取大值 • ( 4 ) 一般外表面的斜度小于内表面的 • ( 5 )热固性塑料小于热塑性塑料
塑件结构工艺性分析
书山有路勤为径, 学海无涯苦作舟
2020年4月10日星期五
项目3 分析塑件结构工艺性
•一
• 项目导入
•二
•相关知识
•三
•项目实施
书山有路勤为径, 学海无涯苦作舟
•
一、 项目引入
灯座(如图1-1所示)塑件和电流线圈架(如图1-13所示)的结 构工艺性能是否合理,并能对塑件的结构不合理的地方进行修改 。
为便于加工(降低加工成本):
对于非透明的塑件,可将外观要求不高的内侧表面粗糙度值取大些。而 透明的塑件,内、外侧表面粗糙度值应相同。
书山有路勤为径, 学海无涯苦作舟
•
二、相关知识
•(一)塑件设计基本原则
•3.塑料制品的形状
设计原则:
塑件的几何形状除应满足使用要求外,还应尽可能使其所对应的模具 结构简单便于加工。(避免侧抽芯机构、避免瓣合模机构)
1、 有时还能降低物料的充模阻力 2、 保证塑件的强度、刚度,而且还避免了塑件壁厚的不均匀
加强筋布置的注意事项
1、 加强筋应设在受力大,易变形的部位,其分布尽量均匀 2、 避免设加强筋后塑件局部壁厚过大 3、 尽量沿着塑料流向布置。以降低充模阻力 4、 设计成球面、或拱面,也可有效增加刚性和防止变形