合成氨总结
合成氨个人工作总结

一、前言2023年,我有幸加入合成氨生产团队,担任合成氨操作员一职。
在这一年的时间里,我在领导的关心与指导下,同事们的帮助下,通过自己的努力学习与实践,较好地完成了各项工作任务。
现将一年来的工作情况进行总结如下:二、工作回顾1. 熟悉工艺流程刚入职时,我对合成氨生产工艺流程并不熟悉。
为了尽快掌握相关知识,我认真学习合成氨生产原理、设备结构、操作规程等,积极参加公司组织的培训,通过实际操作,逐步熟悉了合成氨生产的各个环节。
2. 严格执行操作规程在合成氨生产过程中,我严格遵守操作规程,确保生产安全。
针对设备运行过程中出现的异常情况,我能迅速判断原因,及时采取措施进行处理,确保生产稳定运行。
3. 优化生产指标通过不断摸索和实践,我总结出了一套适合自己的操作方法,使合成氨生产指标得到了明显提高。
具体表现在以下几个方面:(1)降低能耗:通过对设备运行参数的调整,降低合成氨生产过程中的能耗,提高生产效率。
(2)提高产量:通过优化操作工艺,使合成氨产量得到提高。
(3)降低成本:通过降低能耗、提高产量,降低合成氨生产成本。
4. 节约原材料在合成氨生产过程中,我注重节约原材料,减少浪费。
针对原材料采购、储存、使用等环节,我严格执行管理制度,确保原材料得到合理利用。
5. 团队协作在工作中,我注重与同事的沟通与协作,共同解决生产过程中遇到的问题。
通过团队的力量,我们顺利完成了各项生产任务。
三、不足与改进1. 理论知识储备不足虽然我在实际操作方面取得了一定的成绩,但在理论知识储备方面还有待提高。
今后,我将加强学习,提高自己的专业素养。
2. 解决问题的能力有待提高在实际工作中,遇到一些复杂问题时,我的处理能力还有待提高。
今后,我将不断积累经验,提高自己的问题解决能力。
四、展望未来在新的一年里,我将继续努力,不断提高自己的业务水平,为合成氨生产团队的发展贡献自己的力量。
具体目标如下:1. 提高合成氨生产指标,降低生产成本。
合成氨车间个人年终总结

合成氨车间个人年终总结尊敬的领导:时光荏苒,转眼间我已在合成氨车间度过了一年的工作时光。
回顾过去的一年,我深感荣幸能够在这个团结、和谐的团队中工作,并通过自身的努力取得了一定的成绩。
在这里,我将就自己在合成氨车间的工作情况进行个人年终总结,分享自己的收获和感悟。
一、工作概述作为合成氨车间的一名员工,我主要负责合成氨生产过程的监控与管理。
在过去的一年中,我按照公司的工作安排,认真履行职责,勤奋工作,努力提高自身的工作能力与素质。
我积极参与各项生产任务,始终保持高度的工作热情,切实履行岗位职责。
二、工作成绩1.工作技能提升通过一年的工作实践,我对合成氨生产工艺和设备有了更加深入的了解,并具备了独立操作和维护设备的能力。
在日常工作中,我能够及时发现问题并展开相应的处理措施,保障生产的安全和稳定。
2.质量管控我严格按照质量要求,认真跟踪合成氨产品的工艺参数和质量指标,及时采取调整措施,确保产品达到标准。
与此同时,我始终保持对生产过程的关注,寻找改进机会,提高合成氨的生产效率。
3.团队合作在合成氨车间,团队合作精神是至关重要的。
我与同事们紧密配合,互相帮助,共同解决了许多生产上的难题。
通过有效的沟通,我们在工作中形成了良好的协作氛围,提高了工作效率。
三、存在的问题与改进措施1.学习不断作为合成氨车间的一名员工,我应该时刻保持学习的状态,不断提高自己的业务水平。
未来,我将继续学习先进的生产技术和管理经验,为公司的发展做出更大的贡献。
2.沟通与协调能力目前我在团队协作中仍存在一些不足,表现在沟通和协调能力上。
为了加强团队的工作效率,我将主动学习沟通技巧,加强协作能力,与同事们更好地配合,共同完成工作任务。
3.安全意识安全生产是企业的生命线,而合成氨车间是高风险的作业环境。
在工作中,我要大力宣传安全意识,提高责任心,时刻注意自身和他人的安全,做到安全第一,防患于未然。
四、对未来的展望与计划在新的一年里,我将以更高的标准要求自己,不断提升自身的岗位技能,努力发挥自己的潜力和创造力。
合成氨维修年度总结(3篇)

第1篇一、前言随着我国合成氨产业的快速发展,合成氨设备维修工作的重要性日益凸显。
在过去的一年里,我公司在合成氨设备的维修工作中,紧紧围绕提高设备运行效率、降低设备故障率、保障安全生产等目标,努力提高维修技术水平,取得了显著成效。
现将本年度合成氨维修工作总结如下:二、维修工作概况1.维修任务完成情况本年度,我公司合成氨设备维修任务共计XX项,实际完成XX项,完成率XX%。
其中,大修项目XX项,中修项目XX项,小修项目XX项。
2.设备故障率本年度,合成氨设备故障率较去年同期降低了XX%,主要得益于以下措施:(1)加强设备预防性维护,提高设备运行稳定性;(2)优化维修流程,缩短维修时间;(3)提高维修人员技能水平,提高维修质量。
3.维修成本本年度,合成氨设备维修成本较去年同期降低了XX%,主要原因是:(1)加强设备维护,降低设备故障率,减少维修次数;(2)提高维修效率,降低维修时间,减少维修费用;(3)优化维修材料采购,降低采购成本。
三、维修工作亮点1.加强维修人员培训,提高维修技能水平本年度,我公司共组织维修人员培训XX次,培训内容涉及设备结构、维修工艺、故障诊断等方面。
通过培训,维修人员的技能水平得到了显著提高,为设备维修工作提供了有力保障。
2.优化维修流程,提高维修效率针对合成氨设备维修过程中存在的问题,我们优化了维修流程,实现了以下目标:(1)缩短维修时间,提高设备利用率;(2)降低维修成本,提高经济效益;(3)提高维修质量,确保设备安全稳定运行。
3.加强设备预防性维护,降低故障率本年度,我公司加强了设备预防性维护工作,主要措施如下:(1)制定合理的预防性维护计划,确保设备按时进行保养;(2)加强维修人员对设备运行状态的监控,及时发现并处理异常情况;(3)加强设备维修质量检查,确保维修工作达到预期效果。
四、维修工作不足及改进措施1.不足(1)部分维修人员对设备结构、原理掌握不熟练,影响维修效率;(2)设备预防性维护工作仍有待加强,部分设备故障仍存在隐患。
合成氨工艺实训总结与体会

合成氨工艺实训总结与体会实训地点:XXXXX大学化学工程实验中心实训时间:2021年9月1日~2021年9月10日实训人员:XX同学(XXX学院,XXX专业)实训内容:通过实验,了解合成氨的基本原理、反应机理、工艺流程,掌握合成氨的实验操作技能,了解合成氨的工艺控制方法和安全生产知识。
一、实训总结本次实训内容丰富、操作简单易行,让我在增长知识的同时也掌握了实验技能。
以下是我的实训总结:1. 掌握了合成氨的基本原理和反应机理。
在实验室老师的详细讲解和现场操作的指导下,我对合成氨的反应原理和机理有了更深刻的理解。
通过实验,我明白了合成氨的反应主要包括气态氢和气态氮逐渐转变成液态氨,并且掌握了如何调整反应速率和控制反应温度以达到最佳合成效果的方法。
2. 掌握了合成氨的实验操作技能。
合成氨实验是一项敏感难度高的工作,操作失误很容易造成实验失败。
经过老师的指导和多次实验的反复操作后,我成功完成了合成氨实验,并且获得了理想结果。
我也发现,在实验中细节决定成败,及时注意每一项反应细节可以预防事故,确保实验操作的安全性和稳定性。
3. 了解了合成氨工艺的控制和安全知识。
在实验中,我们学习了合成氨工厂的结构、合成氨工艺中常用的反应器类型和在合成氨生产中所需的安全控制措施。
尤其是我们探讨了如何合理调配反应用气的流量、温度以及压力,如何控制火灾危险的发生,如何从突发事件中迅速应对等安全问题,有了一定的实践经验和认识。
二、体会与收获通过合成氨实训,我不仅从理论上了解了合成氨工艺,更重要的是收获了实验操作经验和安全生产意识。
具体体会如下:1. 调试心理的重要性。
操作合成氨实验时,需要不断进行实验调节和反应条件的控制,听从导师的指导,冷静分析问题,调试各项参数等等。
这个过程让我很有收获,在实验的过程中不断探索,不断试验,对自己的思考能力和实际操作的能力都有了一定的提升。
2. 安全与专业技能同等重要。
合成氨实验必须真正做到安全第一,专业技能、实验经验次之。
工业合成氨知识点总结

工业合成氨知识点总结一、引言合成氨是一种重要的化工原料,广泛用于化肥、塑料、药品和其他化工产品的生产中。
而工业合成氨主要是通过哈伯-玻斯曼过程进行生产。
在这个过程中,氮气和氢气以高压、高温和催化剂的作用下,发生反应,生成氨气。
因此,工业合成氨的生产涉及了高压、高温、催化剂和气体分离等方面的工艺技术。
二、合成氨的反应原理工业合成氨的反应过程是氮气和氢气在催化剂的作用下,发生氧化还原反应,生成氨气。
这是一个放热反应,反应方程式为:N₂ + 3H₂ → 2NH₃ + 92.6kJ/mol从反应方程式可以看出,该反应需要大量的氢气,而氮气对反应也起到了催化作用。
在实际生产过程中,合成氨的反应条件一般为300-500°C的温度和100-250atm的压力,同时需要使用铁、钨或镍等金属为催化剂。
三、工业合成氨的生产工艺工业合成氨的生产工艺主要包括氢气制备、氮气制备、合成氨反应和氨气的提取等步骤。
1. 氢气制备氢气是工业合成氨的主要原料之一,通常是通过天然气重整法或电解水法进行制备。
a. 天然气重整法天然气经催化剂重整反应制得合成气,合成气中含有一定比例的氢气。
然后通过甲醇水煤气变换反应得到富含氢气的气体。
b. 电解水法将水分解为氧气和氢气的方法,使用电解槽进行电解水反应,得到纯度高的氢气。
2. 氮气制备氮气是工业合成氨的另一主要原料,一般是从空气中分离得到。
a. 常用的氮气制备方法包括分子筛吸附法、柱塔分离法等。
b. 分子筛吸附法:将空气经过分子筛吸附塔,通过吸附分离得到富含氮气的气体。
c. 柱塔分离法:通过茧状分离塔或塔内吸附塔将空气中的氮气和氧气分离出来。
3. 合成氨反应使用氢气和氮气作为原料,在高压、高温和催化剂(通常是Fe3O4、K₂O、CaO、Al₂O₃或者Ni)的作用下进行反应,得到氨气。
合成氨反应通常分为两个主要阶段:合成氨反应和氨气的提取。
在合成氨反应过程中,氮气和氢气以1:3的比例进入反应器,在压力为100-250bar、温度为300-500°C下进行化学反应。
合成氨厂上半年工作总结

合成氨厂上半年工作总结
经过上半年的努力,合成氨厂取得了一定的成绩。
在全体员工的共同努力下,我们克服了种种困难,取得了一定的进展,现将上半年的工作总结如下:首先,在生产方面,我们严格执行生产计划,保证了产品的质量和产量。
通过技术改进和设备更新,我们成功提高了生产效率,降低了生产成本,为公司创造了良好的经济效益。
其次,在安全生产方面,我们加强了安全生产意识,严格执行各项安全规定,有效预防了事故的发生,确保了员工的人身安全和设备的完好。
同时,我们还加强了环境保护工作,严格控制废气排放和废水排放,保护了周边环境的清洁和整洁。
再者,在员工培训方面,我们加强了员工的技术培训和安全教育,提高了员工的专业素质和安全意识,为公司的可持续发展奠定了坚实的人才基础。
最后,在企业文化建设方面,我们举办了各种形式的文体活动,增强了员工的凝聚力和团队合作精神,营造了和谐的企业氛围。
总的来说,上半年合成氨厂取得了一定的成绩,但也存在一些不足之处,比如设备老化、能源消耗等问题,需要我们进一步努力。
希望在下半年,我们能够继续保持良好的工作态度,积极应对各种挑战,为公司的发展贡献自己的力量。
相信在全体员工的共同努力下,合成氨厂一定能够取得更加辉煌的成绩!。
合成氨工程师总结

合成氨工程师总结引言合成氨是工业领域中非常重要的化学品,在肥料等领域中有着广泛的应用。
作为一名合成氨工程师,我在这里将结合自己多年的工作经验,总结出一些关于合成氨生产的经验和技巧,供大家参考。
合成氨生产的基本流程合成氨的生产采用哈伯-卡斯特别克法(Haber-Bosch Process)。
该法制氮通过高温高压与氢气反应,生成氨,然后再对氨进行纯化和分离。
具体流程如下:1.制氢:从天然气、石油或煤炭等原料中制得氢气。
2.空气分离,获得氮气。
3.加压:将制得的氢气和氮气混合,加压到200至250倍大气压。
4.加热:经过加压后再加热至至少400℃,触发化学反应。
5.冷却:将反应产生的高温氨气进行降温冷却。
6.正常压力分离:利用吸附剂,将氨气和未反应的气体分离。
7.压缩:将氨气进行压缩,以便进入下一个处理步骤。
8.分离:对氨气进行进一步的纯化和分离,以达到取得高纯度氨气的目的。
优化合成氨的制造1.温度和压力的控制在进行哈伯-卡斯特别克法制程时,必须控制好反应中的温度和压力。
氢气和氮气反应时,需要高温和高压环境下进行,但温度过高和压力过高都会对反应产率造成负面影响。
2.选择合适的反应器目前,常用的反应器有普通固定床反应器、流化床反应器和MIDREX反应器三种类型。
其中,MIDREX反应器通常被认为是最有效的反应器,能够提高氨气的产出效果。
3.使用合适的催化剂合成氨的反应中需要使用催化剂促进反应的进行。
使用合适的催化剂,可以大大提高反应效率,并降低反应的温度和压力。
4.控制气体的流量和化学反应速度在工业生产中,气体流量和反应速率是一个非常重要的因素。
为了保证反应的顺利进行,需要对这两个因素进行精准的控制。
总结合成氨生产是一项非常重要的工业过程,它对于农田肥料等领域有着广泛的应用。
作为一名合成氨工程师,需要具备扎实的化学基础知识、综合分析和决策能力,并且不断攻克制程中的难点。
通过合理优化制程,才能够实现经济效益的最大化,从而为社会和个人带来更多的价值。
化工工艺学合成氨知识点总结
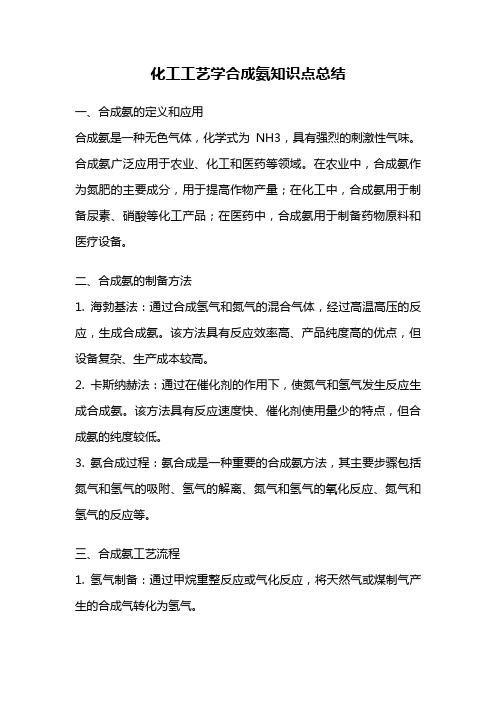
化工工艺学合成氨知识点总结一、合成氨的定义和应用合成氨是一种无色气体,化学式为NH3,具有强烈的刺激性气味。
合成氨广泛应用于农业、化工和医药等领域。
在农业中,合成氨作为氮肥的主要成分,用于提高作物产量;在化工中,合成氨用于制备尿素、硝酸等化工产品;在医药中,合成氨用于制备药物原料和医疗设备。
二、合成氨的制备方法1. 海勃基法:通过合成氢气和氮气的混合气体,经过高温高压的反应,生成合成氨。
该方法具有反应效率高、产品纯度高的优点,但设备复杂、生产成本较高。
2. 卡斯纳赫法:通过在催化剂的作用下,使氮气和氢气发生反应生成合成氨。
该方法具有反应速度快、催化剂使用量少的特点,但合成氨的纯度较低。
3. 氨合成过程:氨合成是一种重要的合成氨方法,其主要步骤包括氮气和氢气的吸附、氢气的解离、氮气和氢气的氧化反应、氮气和氢气的反应等。
三、合成氨工艺流程1. 氢气制备:通过甲烷重整反应或气化反应,将天然气或煤制气产生的合成气转化为氢气。
2. 氮气制备:通过空分设备或压缩空气制氮设备,将空气中的氮气分离出来。
3. 氢气和氮气的混合:将制备好的氢气和氮气按照一定的比例混合。
4. 反应器反应:将混合气体送入反应器中,在催化剂的作用下进行氨合成反应。
5. 分离和纯化:将反应产生的氨气通过冷凝和吸附等分离技术,去除杂质,提高氨的纯度。
6. 储存和运输:将纯净的合成氨储存于气体储罐中,通过管道或压缩瓶等方式进行运输。
四、合成氨工艺的优化和改进1. 催化剂的研发与改进:不断研发新型催化剂,提高反应速率和选择性,降低能耗和催化剂使用量。
2. 反应条件的优化:通过调节反应温度、压力和气体比例等参数,优化反应条件,提高合成氨的产率和纯度。
3. 能源利用的改进:采用新型的能源供应方式,如使用太阳能、风能等可再生能源,减少对传统能源的依赖。
4. 废气处理的改进:对于合成氨生产中产生的废气进行处理,减少对环境的污染。
5. 生产工艺的改进:通过改进工艺流程和设备结构,提高生产效率,降低生产成本。
- 1、下载文档前请自行甄别文档内容的完整性,平台不提供额外的编辑、内容补充、找答案等附加服务。
- 2、"仅部分预览"的文档,不可在线预览部分如存在完整性等问题,可反馈申请退款(可完整预览的文档不适用该条件!)。
- 3、如文档侵犯您的权益,请联系客服反馈,我们会尽快为您处理(人工客服工作时间:9:00-18:30)。
原料气的制取1工艺条件(1)水碳比,表示转化操作所用的工艺蒸汽量。
在约定条件下,水碳比愈高,甲烷平衡含量愈低。
(2)温度烃类蒸汽转化是吸热的可逆反应,温度增加,甲烷平衡含量下降。
反应温度每降低10℃,甲烷平衡含量约增加1-1.3%(3)压力烃类蒸汽转化为体积增大的可逆反应,增加压力,甲烷平衡含量也随之增大。
(4)二段转化的空气量:加入空气量的多少,可从二段炉出口温度上反映出来,但不能它来控制炉温和出口甲烷含量的手段。
因为空气量的加入有合成反应的氢氮比决定。
(5)二段出口甲烷含量:二段炉出口残余甲烷每降低0.1%,合成氨产量可增加1.1-1.4%。
一般控制在0.2-0.4%。
五、反应机理(反应的微观步骤)在催化剂的表面,甲烷转化的速度比甲烷分解的速度快的多,中间产物中不会有碳生成。
其机理为在催化剂表面甲烷和水蒸气解离次甲基成和原子态氧,在催化剂表面被吸附并互相作用,最后生成CO、CO2和H2。
2、催化剂甲烷蒸汽转化是吸热的可逆反应,提高温度对化学平衡和反应速度均有利。
但无催化剂存在时,温度1000℃反应速度还很低。
因此,需要采用催化剂以加快反应速度。
由于烃类蒸汽转化是在高温下进行的,并存在着析炭问题,因此,除了要求催化剂有高活性和高强度外,还要求有较好的耐热性和抗析炭性。
催化剂的还原转化催化剂大都是以氧化镍形式提供的,使用前必须还原成为具有活性的金屑镍,其反应为工业生产中,一般都不采用纯氢气还原,而是通入水蒸气和天然气的混合物,只要催化剂局部地方有微弱活性并产生极少量的氢,就可进行还原反应,还原的镍立即具有催化能力而产生更多的氢。
为使顶部催化剂得到充分还原,也可以在天然气中配入—些氢气。
还原了的催化剂不能与氧气接触,否则会产生强烈的氧化反应、即半水煤气的制取制气过程工作循环:间歇式气化时,自上一次开始送入空气至下一次再送入空气止,称为一个工作循环。
1.吹风:吹入空气,提高燃料层温度,回收显热和潜热后吹风气放空。
2.蒸汽一次上吹制气:自下而上送入水恭汽进行气化反应,燃料层上部温度升高,下部降低。
3.蒸汽下吹:水蒸汽自上而下进行气化反应,使燃料层温度趋于均衡。
4.二次上吹制气:将炉底部下吹煤气排净,为吹入空气作准备。
5.空气吹净:回收此部分吹风气,作为半水煤气中氮的主要来源。
间歇式制气工作循环中各阶段气体的流向硫化物的脱除固体燃料气化所制得的原料气中的粉尘主要是飞灰和固体燃料的微粒。
这些粉尘随着气体而被带出炉外。
粉尘的危害:引起设备和管道的堵塞、系统阻力的增加和造成鼓风机、压缩机等机械过早地磨损;粉尘在气体流过的设备中沉降,会把设备中的催化剂、拉西环或其它类型的填料堵塞。
常用设备:旋风分离器。
工作原理是分散于气体中的固体微粒在离心力的作用下有较大的离心力,该力足以克服气体阻力飞向器壁,微粒碰到器壁而下落,并聚集于旋风分离据的锥形底内,然后间歇地排出器外。
干法:脱硫净化度高,并能脱除各种有机硫。
但干法脱硫剂或者不能再生或者再生非常困难,并且只能周期性操作,设备庞大,劳动强度高,因此,干法脱硫仅适用于气体硫含量较低和净化度要求高的场合。
(1).原料气的硫化氢含量中等,如硫化氢含量为2—3%左右的粗天然气净化,当前应用最广泛的是烷基醇胺法,如一乙醇胺法、二乙醇胺法、二甘醇胺法、二异丙醇胺法等。
(2).原料气的硫化氢、二氧化碳等酸性气体含量较高时,只物理溶剂或物理—化学混合溶剂吸收,再生放出的硫化氢气体用克劳斯法回收硫磺。
这类方法的共同特点是蒸汽与热的消耗小,在高酸性气体分压时溶剂的吸收能力强,如环丁砚法聚乙二醇二甲醚法,冷甲醇法等。
(3).原料气的硫化氢含量低,但二氧化碳含量较高时,用直接氧化法脱硫。
如蒽醌二磺酸钠法、氨水催化法等。
这类方法的共同特点是直接从溶液中回收硫磺,没打台硫尾气放空造成公害的间肥。
但溶液的硫容量低。
(4).气体中有机硫的脱除以固体于法为主,同时干法脱硫广泛用作精细脱硫的手段。
如近代以天然气、轻油等为原料的大型合成氨中,广泛应用活性炭、氧化锌、钴—钼催化剂等于法脱硫,使原料气中总硫含量降至1ppm以下。
用于天然气的干法脱硫,尚需要根据天然气的含硫量、硫的形态和是否有重质烃(C3以上)来选用合适的方案。
如果天然气中重质烃的含量很低,总的含硫量在10ppm左右,而且所含硫分系以硫化氢和硫醇形态出现,则采用活性炭即可满足脱硫要求。
如果天然气中除硫化氢和硫醇外,还含有重质烃时,则采用氧化锌脱硫较好,氧化锌也能脱除少量的硫氧化碳。
如天然气中有机硫含量较高,或有噻酚等难于脱除的硫分时,一般采用钴-钼或镍—钼催化剂,在400°C左右将有机硫加氢转化成硫化氢,然后再用氧化锌脱除硫化氢。
(二)再生的基本原理与催化剂的选择碱性吸收剂只能将原料气中的硫化氢吸收到溶液中,不能使硫化氢氧化为单质硫。
因此,需借助其他物质来实现。
通常是在溶液中添加催化剂作为载氧体,氧化态的催化剂将硫化氢氧化成为单质硫,其自身呈还原态。
还原态催化剂在再生时被空气中的氧氧化后恢复氧化能力,如此循环使用。
此过程可示意为:显然,选择适宜的载氧催化剂是湿式氧化法的关键。
这个载氧催化剂必须既能氧化硫化氢又能被空气中的氧所氧化。
因此,从氧化还原反应的必要条件来衡量,此催化剂的标准电极电位的数值范围必须大于硫化氢的电极电位小于氧的电极电位,即:o.14v<Eo<1 23v。
实际选择催化剂时考虑到催化剂氧化硫化氢,一方面要充分氧化为单质硫,提高脱硫液的再生效果;另一方面又不能过度氧化生成副产物硫代硫酸盐和硫酸盐,影响脱硫液的再生效果。
同时,如果催化剂的电极电位太高,氧化能力太强,再生时被空气氧化就越困难。
因此,常用有机醇类作催化剂,其E。
范围是o.2一o.75v,其他类型催化剂的E0值一般为o.141一o.75V。
表3—7是几种常见催化剂的E0值。
二、栲胶脱硫机理吸收塔内反应:1)NaCO3+H2S=NaHS+ NaHCO32)氧化反应:脱硫液中的偏钒酸钠氧化硫氢化钠生成单质硫,自身被还原为焦钒酸钠。
2NaHS+4NaVO3+H2O=Na2V4O9+4NaOH+2S反应过程中五价钒被还原成四价钒。
但这个反应不能用吹空气的方法倒转回去使钒再生,必须靠氧化态栲胶TEos将四价钒氧化成五价钒,而还原后的还原态栲胶则可利用吹空气法再生.3) 再生反应:焦钒酸钠被氧化态栲胶氧化成偏钒酸纳,恢复其氧化硫氢化物的能力,栲胶呈还原态。
Na2V409+2TEos+2NaOH+H20=4NaV03+2TErs4)还原态栲胶被空气氧化再生为氧化态栲胶TErs+02=TEos+H205)反应中生成的NaOH与溶液中的NaHC03反应生成Na2C03: NaOH+NaHC03=Na2C03+H2OCO的变换变换催化剂一、对催化剂的要求1、活性好2、活性温度低3、较好的选择性4、催化剂对毒物灵敏性小、机械强度高、耐热性好、使用寿命长、价格低廉及原料易得等三、耐硫变换催化剂钴钼系催化剂是当前耐硫变换催化剂的主流,催化剂中钴钼以氧化态存在,使用前必须进行硫化,使氧化钴、氧化钼完全转化为活性组分硫化钴、硫化钼。
为使活性组分处于稳定状态,正常操作时气体中应有一定的总硫含量,对催化剂进行硫化,可用含氢的二硫化碳,也可直接用硫化氢或用含硫化物的原料气,硫化反应如下:上述硫化反应是可逆的。
一、中变流程中温变换工艺流程的主要持点是:a.采用低温高活性的中变催化剂,降低了入炉气体中水蒸气量。
b.采用段间喷水冷激降温,减少系统热负荷及阻力降,相对地提了原料气自产蒸汽的比例,减少外加蒸汽量。
c.变换与合成,铜洗构成第二换热网络,使热能利用更趋合理。
其中有两种模式,是“汽流程”模式,一是“水流程”模式。
前者系指合成塔设后置式废识或中旨式废锅产生蒸汽供变换月,变换工段则设置第二热水塔回收系统余热供桔炼再生铜液用;后者在合成塔后设岂水加热器以热水形式向变换系统补充热能,并通过变换—[段设置的两个饱和热水塔使自产蒸汽达到变换反应所需的汽/气。
两种模式都是充分利用合成及变换反席热,去掉传统工艺中出锅沪向变换、铜洗送汽,实现蒸汽自给,降低能耗。
d.采用电炉升温,革新了变换系统燃烧炉升温方法,使之达到操作简单、平稳、省时、节能的效果。
二、中变串低变流程中变串低变工艺是80年代中期发展起来的。
就目前中、小型厂而言,所谓中变串低变流程,就是在B107等铁铬系催化剂之后串入钴钼系耐硫变换催化剂。
由于耐硫变换催化剂活性温度范围宽(在160一460℃之间都具有良好的活性),操作温度可以比中变大幅度降低。
耐硫变换催化剂可放在中变炉最后一段,也可另设一低变炉串在中变炉后。
因4—13系中变串低变局部工艺流程因,其余部分与团4—l 2的中变流程相同。
从中变炉出来的气体由于中变串低变所用汽/气低而含有5%一7%的一氧化碳,气体经主热交换器3降温回收热量后进入低变炉14继续反应,进一步降低气体中一氧化碳含量.然后经水加热器、热水塔、第二热水塔回收热量后送压缩工段。
在中变串低变流程中,由于耐硫变换催化剂的串入,操作条件发生较大的变化。
一方面入炉半水煤气的汽/气有较大幅度的降低,为实现蒸汽自给提供T有力的保证;另一方面变换气中一氧化碳含量也出单一中交流程的冰一3.5%降到o.8%一1.5%,使铜洗负荷减轻合成半水煤气消耗降低;并且由丁中变后串联耐硫变换催化剂,使变换系统的操作弹性大大增加。
大型氨厂为厂降低变换气中一氧化碳含量以中温变换串联采用铜基催比剂的低温变换流程为主。
低温变换的效果对其经济效益影响较大,低变炉出口一氧化碳每降低o.1%,日增产氨量就达10t以上。
三、全低变流程全低变工艺全部使用宽温区的钴钼系耐硫变换催化剂取代传统的铁铬系中变催化剂。
国内全低变工艺自1990年实现工业生产后,经过几年的实践已获得成功,并在不断推广。
全低变工艺由于催化剂的起始活性温度低,变换炉入口温度及炉内热点温度都大大低十中变炉入口及热点温度,使变换系统处于较低的温度范围内操作,催化剂对过低的汽/气不会产生析炭及生成烃类等副反应,因而只要在满足出口变换气中一氧化碳含量的前提下,可不受限制地降低入炉蒸汽含量,使全低变流程蒸汽消耗比中变及中变串低变流程大大降低,合成废热锅炉副产的蒸汽供变换有余。
而对于采用重油部分氧化法急冷流程的氨厂,因其制得的煤气温度约200 c并为水蒸气所饱和,可直接使用耐硫变换催化剂进行变换,从而大大简化了流程。
但也由于入炉原料气温度低,气体中的油污、杂质等容易直接进入炉内,使催化剂活性下降。
一、多段变换护的工艺特征(一)多段间接换热式图4—15(a)为多段间接校热式变换炉示意图。
此处为了示意方便、简单,把段间换热器放在炉内。
原料气经换热器预热达到催化剂所要求的温度后进入第一段床层,在绝热条件厂进行反废,温升值与原料气组成及变换率有关。