变速器上壳体工艺规程及夹具设计
变速器箱体加工工艺规程及轴承座孔加工工序夹具设计
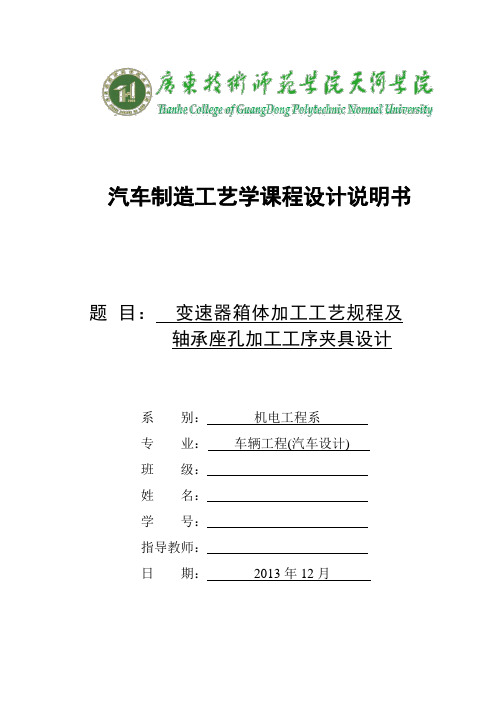
汽车制造工艺学课程设计说明书题目:变速器箱体加工工艺规程及轴承座孔加工工序夹具设计系别:机电工程系专业:车辆工程(汽车设计)班级:姓名:学号:指导教师:日期:2013年12月变速器箱体加工工艺规程及轴承座孔加工工序夹具设计摘要本次课程设计的任务确定变速器箱体材料、毛坯,制定加工工艺规程,设计加工工序夹具等。
该零件的工艺工程中包括了铣平面、镗内孔、钻孔、攻螺纹、铣端面等工序,难度程度适合于工艺课程设计的需要。
它要求学生综合地运用所学过的专业知识,针对一个具体的工程实际零件进行机械加工工艺规程制定及专用机床夹具设计,使学生初步具备制定机械加工工艺规程及设计专用机床夹具的能力,为随后的毕业设计进行一次综合训练和准备,也可为以后所从事的车辆设计工作打下坚实的基础。
变速器箱体是汽车重要的零部件,加工工艺过程复杂,适合学生锻炼学习。
关键词:变速器箱体;工艺过程;夹具目录1分析零件并确定其生产类型 (1)1.1零件的作用: (1)1.2零件的生产类型: (1)2选择毛坯尺寸,设计毛坯图 (2)2.1选择毛坯 (2)2.2确定机械加工余量、毛坯尺寸和公差 (2)2.4确定毛坯尺寸 (2)2.5确定毛坯尺寸公差 (3)2.6绘制毛坯图 (3)3选择加工方法 (4)3.1定位基准的选择 (4)3.2平面的加工 (4)3.3孔的加工 (4)3.4螺纹加工 (4)4制定工艺路线 (5)5工序设计 (7)5.1选择加工设备 (7)5.2选择夹具 (7)5.3选择刀具 (7)5.4选择量具 (7)6确定切削用量和基本时间 (9)6.1工序30 (粗镗φ67.8mm孔)切削用量及基本时间的确定 (9)6.2工序35 (半精镗φ71.3mm孔)切削用量及基本时间的确定 (9)6.3工序40 (精镗φ72mm孔)切削用量及基本时间的确定 (10)6.4工序45 (粗镗φ57.8mm孔)切削用量及基本时间的确定 (11)6.5工序50 (半精镗φ61.3mm孔)切削用量及基本时间的确定 (12)6.6工序55 (精镗φ62mm孔)切削用量及基本时间的确定 (13)6.7工序60 (粗镗φ75.8mm孔)切削用量及基本时间的确定 (14)6.8工序65 (半精镗φ79.3mm孔)切削用量及基本时间的确定 (15)6.9工序40 (精镗φ80mm孔)切削用量及基本时间的确定 (15)7专用夹具设计 (17)7.1定位方案 (17)参考文献 (19)总结 (20)附录 (21)变速器箱体加工工艺规程及轴承座孔加工工序夹具设计1分析零件并确定其生产类型1.1零件的作用:变速器箱体的材料HT150,是减速箱箱体零件主要作用:(1)起支承作用,并在此基础上安装轴、轴承、齿轮等零件;(2)用以连接机器设备与地面的基础零件;(3)利用它们的结构工艺起到其它零件的定位作用。
汽车差速器壳加工工艺及夹具设计

摘要随着社会的发展,汽车在生产和生活中的越来越广泛,差速器是汽车中的重要部件,其壳体的结构及加工精度直接影响差速器的正常工作,因此研究差速器的加工方法和工艺的编制是十分必要和有意义的。
本次设计主要内容有:差速器的工作原理结构分析,差速器壳体的工艺编制,夹具的设计及加工中对定位基准的选择,工序和工装设计中切削用量,夹紧力的计算等。
机床夹具的种类很多,其中,使用范围最广的通用夹具,规格尺寸多已标准化,并且有专业的工厂进行生产。
而广泛用于批量生产,专为某工件加工工序服务的专用夹具,则需要各制造厂根据工件加工工艺自行设计制造。
本设计的主要内容是设计钻床夹具和铣床夹具,需要对零件上Φ22的孔进行铣削加工端面的铣削加工。
由于某些原因,没有上传完整的毕业设计(完整的应包括毕业设计说明书、相关图纸CAD/PROE、中英文文献及翻译等),此文档也稍微删除了一部分内容(目录及某些关键内容)如需要的朋友,请联系我的叩扣:二二壹五八玖一壹五一关键词:差速器,壳体,工艺规程,夹具设计AbstractAlong with social development motor vehicle production and life in anincreasingly wide differential device is an important vehicle componentsand its interior structure and processing precision differential devicedirectly affect the normal work study differential device case processingmethods and techniques of preparation is necessary andmeaningful. Thecurrent design of the main elements: differential devicestructuresoperating principles of analysis differential device case preparationprocesses design and smooth-bore jig for positioning baseline processingoptions smooth-boredesign processes suits cutting consumption increasedcomputing power.Machine toolfixture of many kinds, among them, the most widely used common fixture, sizespecifications have been standardized, and a professional production plant. While widely used in batch production, designed for a certain workpiece processing services for the fixture, it needs each factory according to workpiece machining technology to design and manufacture. The main contents of this design is the design of drilling jig and milling fixture, the need for parts than22hole milling face milling.Key Words:differential device,case,technological process,jig design致谢目录摘要 (1)Abstract (1)目录 (2)第1章绪论 (4)1.1 课题的背景及意义 (4)1.2 差速器的主要分类 (5)1.2.1 开式差速器 (5)1.2.2 限滑差速器 (5)1.3 差速器结构 (6)1.3论文主要内容 (6)第2章零件的分析 (6)2.1 零件的作用 (6)2.2 零件的工艺分析 (7)第3章工艺规程设计 (8)3.1 基准面的选择 (8)3.1.1 粗基准的选择 (9)3.1.2 精基准的选择 (9)3.2 毛坯的制造形式 (9)3.3 制订工艺路线 (9)3.3.1. 工艺线路方案一 (9)3.3.2 工艺路线方案二 (10)3.3.3. 工艺方案的比较与分析 (10)3.4 机械加工余量、工序尺寸及毛坯尺寸的确定 (11)3.4.1 外圆表面 (11)3.5 内圆表面 (13)3.4.3 端面 (14)3.4.4 凸台 (15)3.4.5 孔类 (15)第4章 确定差速器切削用量及基本工时 (15)4.1 工序1 铣φ200外圆右端面(大头)。
二级减速器箱体盖工艺规程及夹具设计
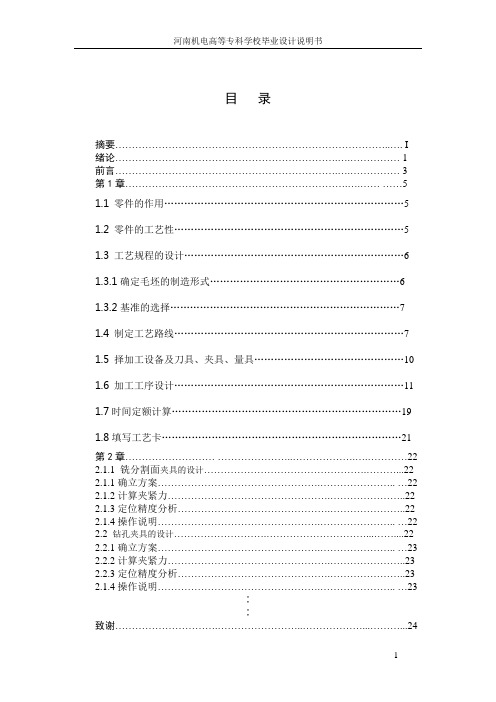
目录摘要 (I)绪论 (1)前言 (3)第1章 (5)1.1 零件的作用 (5)1.2零件的工艺性 (5)1.3工艺规程的设计 (6)1.3.1确定毛坯的制造形式 (6)1.3.2基准的选择 (7)1.4制定工艺路线 (7)1.5 择加工设备及刀具、夹具、量具 (10)1.6加工工序设计 (11)1.7时间定额计算 (19)1.8填写工艺卡 (21)第2章 (22)2.1.1 铣分割面夹具的设计 (22)2.1.1确立方案........................................................................ (22)2.1.2计算夹紧力 (22)2.1.3定位精度分析 (22)2.1.4操作说明........................................................................ (22)2.2 钻孔夹具的设计 (22)2.2.1确立方案........................................................................ (23)2.2.2计算夹紧力 (23)2.2.3定位精度分析 (23)2.1.4操作说明........................................................................ (23)∶∶致谢 (24)参考文献........................................................................ (25)摘要本文设计了二级减速器上箱体机械加工工艺规程,合理选择了工艺过程中的机床刀具和量具,设计了铣分割面工序和钻螺栓孔工序的专用机床夹具。
并计算了该夹具使用的精度保证,计算结果表明两套夹具均可,保证了零件的加工要求。
汽车后桥减速器壳工艺规程设计及其夹具设计

优秀设计引言毕业设计是学生的最后一个教学环节,我这次毕业设计的题目是某汽车后桥减速器壳工艺规程设计及其夹具设计。
汽车在正常行驶时,发动机的转速很高,只靠变速箱来降低,会使变速箱的尺寸增大。
同时,转速下降,扭矩必然增加,也就加大了变速箱与变速箱后一级传动机构的传动负荷。
因此,在动力向左右驱动轮分流的差速器之前需要设置一个主减速器。
而主减速器壳是汽车后桥主减速器的一部分。
主减速器壳体加工精度的高低直接影响着差速器壳及主、被动齿轮的配合精度,因而其加工工艺直接影响车桥和整车质量。
我此次毕业设计的任务是对汽车后桥减速器壳进行工艺分析并且设计其夹具。
经过查阅相关资料,并且结合所学的机械知识,对该零件进行工艺分析,确定出合理的加工工艺方案,并选择切削用量及其工艺装备。
了解零件的结构特点及技术要求,查阅相关书籍,例如夹具方面的教材及图册,经过反复的研究、设计、比较、试验,最终设计出一套合理的夹具,即车法兰止口的夹具。
最后在老师和同学的帮助下,经过不断地修改、检查,最终完成了汽车后桥减速器壳工艺规程及其夹具设计。
本次毕业设计使我在机械方面受益匪浅。
特别是刘老师在工作中对我的耐心辅导,他对学生强烈的责任感和严谨的治学态度,无不给我以深刻的影响。
由于类似的大型课题很少接触,经验能力方面的欠缺,错误之处一定存在,恳请各位老师给予批评指正,以便今后的工作尽善尽美。
目录目录 (2)第1章零件的分析 (4)1.1减速器壳在汽车上的位置及功用 (4)1.2减速器壳的结构特点及技术要求 (4)1.2.1结构特点 (4)1.2.2技术要求分析 (5)第2章工艺规程的设计 (7)2.1生产类型的确定 (7)2.1.1生产纲领的确定 (7)2.1.2零件年产量的确定 (7)2.1.3生产类型的确定 (7)2.1.4生产类型对应的工艺特征 (7)2.2毛坯的选择 (8)2.2.1铸件的精度等级选择: (8)2.2.2毛坯余量及偏差的选择 (8)2.3各加工表面的加工方法的选择 (10)2.3.1加工方法的确定 (10)2.3.2加工阶段的划分 (12)2.4制定加工工艺路线 (13)2.5工艺方案的分析 (17)2.6确定各工序的加工余量、工序尺寸、切削用量及工时定额 (18)2.6.1确定各工序的加工余量 (18)2.6.2确定各工序的工序尺寸 (19)2.6.3确定各工序的切削用量 (20)2.6.4确定各工序的工时定额 (26)2.7确定各工序的工艺装备和机床的选择 (43)2.7.1刀具的选择 (43)2.7.2量具的选择: (44)2.7.3夹具的选择 (45)2.7.4机床设备的选择: (46)2.8选择定位基准的原则 (46)2.8.1粗基准的选择 (46)2.8.2精基准的选择 (47)2.9合理夹紧方法的确定 (48)2.9.1夹紧力的方向 (48)2.9.2夹紧力的作用点 (48)第3章夹具的设计 (50)3.1夹具设计的目的 (50)3.2所设计夹具的工序内容、工序所用的机床和刀具 (50)3.2.1 工序内容 (50)3.2.2 工序所用的机床和刀具 (51)3.3夹具设计满足的要求 (51)3.4定位基准及定位元件的选择 (51)3.5夹紧元件的选择 (52)3.6定位误差的计算 (53)3.6.1产生定位误差的原因 (53)3.6.2定位误差的计算 (53)3.7切削力及夹紧力计算 (55)结论 (57)致谢 (58)参考文献 (59)附录A (65)附录B (72)第1章零件的分析1.1减速器壳在汽车上的位置及功用汽车正常行驶时,发动机的转速通常在2000至3000r/min左右,如果将这么高的转速只靠变速箱来降低下来,那么变速箱内齿轮副的传动比则需很大,而齿轮副的传动比越大,两齿轮的半径比也越大,换句话说,也就是变速箱的尺寸会越大。
变速箱体的机械加工工艺规程及专用夹具设计与制作

湖南工贸技师学院技师论文案例报告题目:设计“变速箱体”零件的机械加工工艺规程及相关工序的专用夹具内容:1.零件图一张2.毛坯图一张3.机械加工工艺过程综合卡片一张(或机械加工工艺规程卡片一套)4.夹具装配图一张5.夹具体零件图一张6.课程设计说明书一份原始资料:该零件图样,Q=20000台/年,n=1件/台,每日1班班级学号:9 号学生:吕沛思指导教师:张璐青系(教研室)主任:王定勇变速箱体的工艺与夹具的设计与制作湖南工贸技师学院吕沛思摘要:本文对变速箱体的加工难点、生产类型进行了分析,针对零件的结构特点进行毛坯设计、对其工艺过程进行了设计。
为提高生产效率,设计了铣削窄槽夹具,对其它箱体零件的加工有一定的借鉴意文。
关键词:变速箱工艺夹具设计一、分析零件图纸并确定其生产类型1.零件的作用变速箱体的材料HT200,是减速箱的重要零件(见图立体1-1及零件图1-2),其主要作用是:①、起支承作用,并在此基础上安装轴类零件及轴上零件。
②、利用它们的工艺结构起到其他重要零件的定位作用。
③、用以连接机器设备与地面的基础零件。
图1-1 变速箱体立体图2.零件的结构分析该零件是属于箱体零件,通过对该零件图的重新绘制,对零件有些深入的了解。
此零件为典型的箱体类零件,并不是所有的表面和轮廓都要加工,除几个轴承孔外,其他部分加工精度要求不高,都比较容易获得。
主要保证好输入轴与输出轴孔的精度以及两个面的位置度。
此零件的工艺路线完全按照:先面后孔,先粗后精,先主后次,基准先行的一般工艺原则所进行的。
其设计基准与装配基准为底平面,所以应先将其加工完成。
两侧面与轴承孔的中心线有垂直度的要求,但是精度要求并不是特别高,容易保证形位公差要求。
此零件孔较多,但大部是小螺丝孔,只要能满足装配即可。
考虑到加工该零件所需要刀具繁多,而且为大批量生产,所以选在数控立式和卧式加工中心上完成加工。
因此要设计专用夹具,其后有根据工艺路线专门设计的夹具具体分析。
变速器拨叉工艺规程及夹具设计

变速拨叉零件的机械加工工艺及工艺装备设计摘要:汽车制造工艺学课程设计,是在学完汽车制造工艺学后进行的一项教学环节;在老师的指导下,要求在设计中能初步学会综合运用以前所学过的全部课程,并且独立完成的一项工程基本训练。
通过课程设计达到以下目的:1、能熟练的运用机械制造工艺学的基本理论和夹具设计原理的知识,正确地解决一个零件在加工中的定位,夹紧以及合理制订工艺规程等问题的方法,培养学生分析问题和解决问题的能力。
2、通过对零件某道工序的夹具设计,学会工艺装备设计的一般方法。
通过学生亲手设计夹具的训练,提高结构设计的能力。
3、课程设计过程也是理论联系实际的过程,并学会使用手册、查询相关资料等,增强学生解决工程实际问题的独立工作能力。
关键词:拔叉;工艺分析;工艺规格设计;夹具设计序言:拨叉是用来推动变速器齿轮,改变齿轮位置的工具,通过将齿轮改变位置来改变齿比,以达到变速的目的,变速器的齿轮都是装载主轴和副轴上,通过拨叉来推动它们前进或者后退,就可以改变齿比,所以它对汽车领域的作用是非常重要的。
一、零件的分析1.1零件的作用题目所给的零件是汽车变速器的拨叉。
它位于汽车变速机构中,主要起换档,使主轴回转运动按照工作者的要求工作,获得所需的速度和扭矩的作用。
零件的φ25孔与操纵机构相连,φ55半孔则是用于与所控制齿轮所在的轴接触。
通过上方的力拨动下方的齿轮变速。
两件零件铸为一体,加工时分开。
1.2零件的工艺分析零件的材料为HT200,灰铸铁生产工艺简单,铸造性能优良,但塑性较差、脆性高,不适合磨削,为此以下是拨叉需要加工的表面以及加工表面之间的位置要求:1.小头孔φ25023.00+;2.小头孔轴线侧面端面的距离03.023-3.大头半圆孔Ф4.0055+及其端面;4.两孔中心距Ф1.02.05.134--5.16×8槽;6.φ40外圆斜面;7. 工件尺寸为40的外侧面8.大头半圆孔两端面与小头孔中心线的垂直度误差为0.1mm ;槽端面与小头孔中心线的垂直度误差为0.08m 。
汽车变速箱上盖的机械加工工艺规程及夹具设计

摘要汽车变速箱上盖是汽车变速箱的重要组成部分。
它与变速箱箱体装配,为变速箱内部的齿轮、轴等工作元件提供一个稳定安全的工作环境,防止内部零件在暴露环境下工作。
上盖上还设计了检查窗,是为了便于观查内部元件的工作情况。
本设计说明书是在毕业设计过程中撰写完成的,是对变速箱上盖加工工艺、工装设计的说明、分析和论证。
主要内容有:上盖的工艺规程制定、典型加工工序分析、专用夹具设计、专用刀具设计、专用量具设计。
通过这些我对变速箱上盖零件制造活动有一个总体的,全貌的了解与把握,能够掌握金属切削过程的基本规律,掌握机械加工的基本知识,能选择加工方法与机床,刀具,夹具及加工参数,具备制定工艺规程的能力和掌握机械加工精度和表面质量的基础,初步具备分析解决现场工艺问题的能力。
关键词:工艺;工装;夹具;刀具ABSTRACTMotor vehicle gearbox shelters is an important component of the gearbox. Box it and gearbox assembly, the internal gear for the transmission, axle components, and other work.It provide a stable and secure working environment to prevent exposure of internal components in the working environment. Also stamped on the design of the inspection windows, in order to facilitate the investigation of the internal components of the work.The design specification is in the process of writing graduate design completed, the gearbox cover processing technology, tooling design of the note, analysis and feasibility studies. Elements include: the superstructure of developing a point of order, the typical processing of special fixture design, special-purpose tool designed for measuring tool design.I passed these on the gearbox cover parts manufacturing activities have an overall, the understanding and grasp the full picture, metal-cutting process to be able to master the basic law, grasp the basic knowledge of mechanical processing, and processing methods can choose machine tools, cutting tools, fixtures and processing Parameters, with the development of protocols and the ability to master precision machining and surface quality of the foundation, a preliminary analysis of the scene to solve problems.Key words: Technology; Tooling; Fixture; Tool目录绪论 (1)1 机械加工工艺规程的制定 (2)1.1零件的工艺性分析 (2)1.1.1 零件的功用 (2)1.1.2 零件的结构特点与工艺性 (2)1.1.3 主要加工表面及其技术要求 (2)1.2确定生产类型 (2)1.3零件毛坯选择 (4)1.3.1 零件毛坯材料选择 (4)1.3.2 变速箱上盖的毛坯 (4)1.3.3 毛坯的制造方式 (4)1.4零件加工工艺规程的制定 (5)1.4.1 选择加工方法和加工方案 (5)1.4.2 定位基准的选择 (5)1.4.3 热处理及检验的选择与安排 (6)1.4.4 拟定工艺路线 (6)1.4.5 选择各工序加工机床设备及工艺装备 (8)1.4.6 确定各工序的工序尺寸、表面粗糙度及检验方法 (10)1.4.7 确定典型工序的切削用量及工序基本工时定额 (11)1.4.8 工艺过程的技术经济性分析 (15)2 夹具设计 (16)2.1铣床夹具的设计 (16)2.1.1 夹具功能简图和工作原理 (16)2.1.2 铣床夹具的定位方案设计 (17)2.1.3 铣床夹具的定位误差分析 (18)2.1.4 切削力与夹紧力的计算 (18)2.1.5 铣床夹具的夹紧装置与机构设计 (21)2.1.6 铣床夹具的动力装置设计 (23)2.2钻床夹具的设计 (24)2.2.1 钻床夹具的定位方案设计 (24)2.2.2 钻床夹具的定位误差分析 (25)2.2.3 钻削力与夹紧力的计算 (26)2.2.4 夹具的夹紧装置与机构设计 (30)2.2.5 钻床夹具的动力装置设计 (32)3 专用刀、量具设计 (33)3.1专用刀具设计. (33)3.1.1 钻铰复合刀具设计应考虑的问题 (33)3.1.2 钻铰复合刀具设计步骤及方法 (34)3.1.3 钻铰复合刀具结构尺寸图 (36)3.2专用量具设计 (37)3.2.1 量规工作尺寸的确定 (37)3.2.2 量规的技术要求 (39)3.2.3 量规的结构尺寸 (39)结论 (41)致谢 (42)参考文献 (43)附录A 英文文献 (44)附录B 中文翻译 (52)绪论制造业是国家发展与社会进步的基础,而汽车制造将是未来面对普通消费者的主要的机械制造产品,而随着国家的发展人民生活水平的提高,人们对汽车的需求和要求必定变的更多,所以我们有必要对汽车及汽车零件的设计与加工投入更多的精力。
XZ25-50变速箱箱体工艺及粗镗孔夹具设计锥形套注塑模具设计
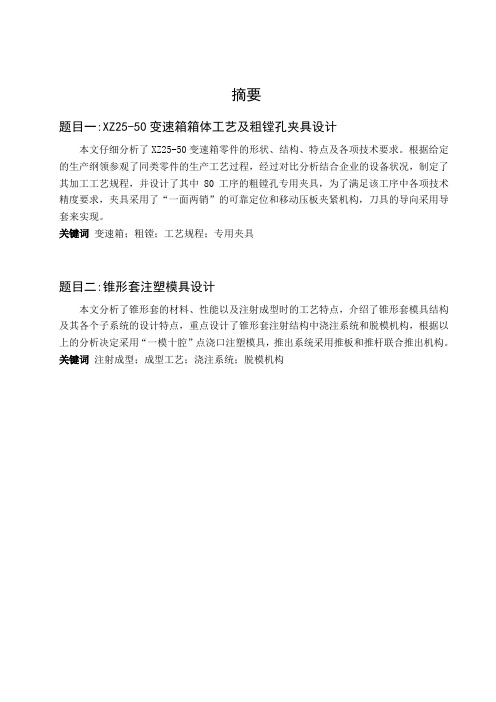
摘要题目一:XZ25-50变速箱箱体工艺及粗镗孔夹具设计本文仔细分析了XZ25-50变速箱零件的形状、结构、特点及各项技术要求。
根据给定的生产纲领参观了同类零件的生产工艺过程,经过对比分析结合企业的设备状况,制定了其加工工艺规程,并设计了其中80工序的粗镗孔专用夹具,为了满足该工序中各项技术精度要求,夹具采用了“一面两销”的可靠定位和移动压板夹紧机构,刀具的导向采用导套来实现。
关键词变速箱;粗镗;工艺规程;专用夹具题目二:锥形套注塑模具设计本文分析了锥形套的材料、性能以及注射成型时的工艺特点,介绍了锥形套模具结构及其各个子系统的设计特点,重点设计了锥形套注射结构中浇注系统和脱模机构,根据以上的分析决定采用“一模十腔”点浇口注塑模具,推出系统采用推板和推杆联合推出机构。
关键词注射成型;成型工艺;浇注系统;脱模机构题目一:ABSTRACTThis paper have a detailed analysis of the XZ25-50 gear box parts’ shape, structure, characte ristics and the various technical requirements. According to the production programe, the vist to the similar parts’ production process is had . By having a comparative analysis combining to the equipment situation of business, it’s machining technology regulations are developed and the eightieth process’ rough boring special fixture is designed. In order to meet the process’ various technical precision, the fixture is adopted the form of a face two pin to give a reliable location, adopted the mobile plate to clamp the parts and used the oritented sleeve to achive the tool-orientation.Keyword Gearbox Rough boring Technology regulations special fixture题目二:ABSTRACTThe cone-thimble’s material, performance and technology characters during cone-thimble injection molding are analyzed, the structure of cone-thimble mold and design specialty ineach of its sub-systems are introduced separately. Importantly,to design the demoulding mechanism and pouring system in the structure of cone-thimble mold. According to the above analysis, mold is adopted a mold ten cavity point gate injection mold and adopted the pushing-plate and putters compound pushing- mechanism.Keyword Injection moulding Moulding technology Casting system Demoulding mechanism目录绪论 (1)课题一: (2)1 箱体零件加工工艺规程设计 (2)1.1 XZ25-50 变速器壳体的用途 (2)1.2零件的工艺分析 (2)1.3 确定箱体的生产类型 (2)1.4 确定箱体毛坯制造形式和尺寸 (2)1.4.1 确定毛坯的制造种类和制造方法 (3)1.4.2 毛坯余量和工序余量的确定 (3)1.5 定位基准的选择 (3)1.5.1 粗基准的选择 (3)1.5.2 精基准的选择 (3)1.6 确定箱体零件各加工表面的加工方案 (4)1.7 确定工艺方案的原则及注意问题 (4)1.7.1 粗、精加工阶段分开原则 (4)1.7.2 工序集中和分散原则 (5)1.7.3 制定工艺方案应注意的其它方面 (5)1.8 工艺路线的确定 (6)1.9 确定各表面的切削用量和基本工时 (6)1.9.1 工序50粗精铣上表面 (6)1.9.2 工序60钻上表面各螺纹底孔以及孔 (7)1.9.3 工序70攻上表面各螺纹以及铰孔 (8)1.9.4 工序80粗精铣左右表面 (9)1.9.5 工序90粗镗-半精镗-精镗左右面上轴承孔,扩铰倒档孔 (9)1.9.6 工序100钻左右面上的螺纹底孔以及孔 (12)1.9.7 工序110攻左右面上的螺纹 (14)1.9.8 工序120粗精铣前后各面和倒档孔内端面以及铣倒档孔内槽 (15)1.9.9 工序130钻前后面上的螺纹底孔以及孔 (16)2.0 工序140攻前后面上的螺纹孔以及孔 (18)2专用夹具的设计 (21)2.1 对镗床夹具的具体的要求 (21)2.2 夹具体的毛坯结构 (21)2.3夹具元件的选择与设计 (21)2.4专用夹具的设计步骤 (22)2.5绘制夹具总装配图 (22)2.6标注夹具总装配图上个部分尺寸和技术要求 (22)2.7夹具公差配合的制订 (23)2.7.1制订夹具公差与技术条件的依据 (23)2.7.2制定夹具公差和技术条件的基本原则 (23)2.8夹具公差的制订 (24)2.9夹具技术条件的制订 (24)2.9.1 定位元件之间或定位元件对夹具体底面之间的相互位置要求 (24)2.9.2 定位元件与连接元件间的相互位置要求 (24)2.9.3 对刀元件与连接元件间的相互位置要求 (24)2.9.4 定位元件与引导元件间的相互位置要求 (24)2.10 夹具设计部分的计算 (24)2.10.1 基准的选择 (24)2.10.2 切削夹紧力的计算 (24)2.10.3 定位误差的分析 (25)课题二: (27)1 原始材料的分析 (27)1.1分析塑件的成型特性 (27)1.2分析塑件的结构及工艺性 (27)1.3塑件的体积和质量 (27)2 分型面的选择与浇注系统的设计 (29)2.1 塑件成型位置及分型面的选择 (29)2.1.1塑件成型位置 (29)2.1.2塑件分型面的选择 (29)2.2 型腔数目、布置的设计以及浇注系统的确定 (30)2.2.1 注射机的选择 (30)2.2.2 型腔数目的确定 (31)2.2.3 多型腔的布置设计及浇注系统的确定 (31)2.3 浇注系统的设计 (32)2.3.1浇注系统的设计原则 (32)2.3.2 主流道的设计 (33)2.3.3分流道的设计 (33)2.3.4浇口的设计 (34)2.3.5浇口位置的选择 (36)2.3.6冷料穴和拉料杆的设计 (36)2.3.7排气系统的设计 (37)3 成型零部件的设计 (38)3.1成型零件结构的设计 (38)3.1.1凹模的结构设计 (38)3.1.2型芯结构设计 (38)3.2成型零件工作尺寸的计算 (38)3.2.1腔径向尺寸计算 (38)3.2.2型腔的深度尺寸 (39)3.2.3型芯的径向尺寸的计算 (39)3.2.4型芯高度计算 (39)3.3型腔侧壁及底板厚度的计算 (39)3.3.1型腔侧壁厚度计算 (39)3.3.2底板厚度的计算 (40)4 注塑模具导向与脱模机构设计 (41)4.1导向机构设计 (41)4.1.2导套设计(GB/T4169.3-1984) (42)4.2推出机构形式的设计 (42)4.3脱模力的计算 (43)4.4推出零件尺寸的确定 (44)5 冷却系统的设计 (45)5.1 冷却回路的布置 (45)5.2 冷却系统的结构选择 (45)6模架的选用 (46)7注塑机(XS-ZY-125)参数校核 (47)7.1最大注射量的校核 (47)7.2锁模力校核 (47)7.3注塑机开模行程的校核 (47)8 模具的装配和试模 (49)8.1模具的装配 (49)8.2模具的安装 (50)8.3模具的试模 (50)结论 (51)致谢....................................................... 错误!未定义书签。
- 1、下载文档前请自行甄别文档内容的完整性,平台不提供额外的编辑、内容补充、找答案等附加服务。
- 2、"仅部分预览"的文档,不可在线预览部分如存在完整性等问题,可反馈申请退款(可完整预览的文档不适用该条件!)。
- 3、如文档侵犯您的权益,请联系客服反馈,我们会尽快为您处理(人工客服工作时间:9:00-18:30)。
编号:沈阳工学院毕业设计(论文)题目:上壳体工艺规程及夹具设计院(系):机电工程系专业:机械设计制造及其自动化学生姓名:学号:指导教师:职称:2015 年5月10 日摘要本设计上壳体零件加工过程的基础上。
主要加工部位是平面和孔加工。
在一般情况下,确保比保证精密加工孔很容易。
因此,设计遵循的原则是先加工面后加工孔表面。
孔加工平面分明显的阶段性保证粗加工和加工精度加工孔。
的基础上,通过输入输出底面作一个良好的基础过程的基础。
主要的流程安排是支持在定位孔过程中的第一个,然后进行平面和孔定位技术支持上加工孔。
整个过程是一个组合的选择工具。
专用夹具夹具的选择,有自锁机构,因此,更高的生产力,对于大批量,满足设计要求。
关键词:工艺,工序,切削用量,夹紧,定位,误差AbstractBased on this design process of shell parts. The main processing part is plane and hole machining. In general, it is easy to ensure precision machining holes than guarantee. Therefore, the design principle is the first processing surface after machining hole surface. Phase plane hole machining obvious to ensure the accuracy of machining and rough machining hole. On the basis of the foundation, through the input and output of the bottom surface as a good basis for the process. The main process is supported in the positioning hole in the process of the first, and then the processing hole plane and hole positioning technology support. The whole process is a combination of selection tool. Special fixture fixture selection, a self-locking mechanism, therefore, higher productivity, in large quantities, meet the design requirements.Key words: process, process, cutting, clamping, positioning, error目录摘要........................................................................................................................................ I I Abstract (III)1 序言 (1)2 零件的分析 (2)2.1 零件的形状 (2)2.2 零件的工艺分析 (2)3 工艺规程设计 (4)3.1 确定毛坯的制造形式 (4)3.2 基面的选择 (4)3.3 制定工艺路线 (4)3.3.1工艺路线方案一 (5)3.3.2 工艺路线方案二 (5)3.3.3 工艺方案的比较与分析 (6)3.4 选择加工设备和工艺装备 (7)3.4.1机床选用 (7)3.4.2选择刀具 (7)3.4.3选择量具 (7)3.5 机械加工余量、工序尺寸及毛坯尺寸的确定 (7)3.6 确定切削用量及基本工时 (9)4 设计钻底面孔夹具 (22)4.1设计分析 (22)4.2设计方案论证 (22)4.3切削力及夹紧力的计算 (22)4.4 设计及操作的简要说明 (23)4.5 结构分析 (23)4.6 夹具的公差 (25)4.7 工序精度分析 (26)5 铣侧面夹具设计 (27)5.1 问题的提出 (27)5.2 夹具设计 (27)5.2.1夹具体设计 (27)5.2.2定位基准的选择 (27)5.2.3定位方案和元件设计 (28)5.2.4定位误差的计算 (28)5.2.5夹紧力计算 (29)5.2.6夹紧机构的设计 (31)5.2.7定向键与对刀装置设计 (32)5.2.8确定夹具体结构尺寸和总体结构 (34)5.2.9夹具设计及操作的简要说明 (35)总结 (36)参考文献 (37)致谢 (38)1 序言机械加工工艺是规定产品或零件机械加工工艺过程和操作方法,是指导生产的重要的技术性文件。
它直接关系到产品的质量、生产率及其加工产品的经济效益,生产规模的大小、工艺水平的高低以及解决各种工艺问题的方法和手段都要通过机械加工工艺来体现,因此工艺规程的编制的好坏是生产该产品的质量的重要保证的重要依据。
在编制工艺时须保证其合理性、科学性、完善性。
而机床夹具是为了保证产品的质量的同时提高生产的效率、改善工人的劳动强度、降低生产成本而在机床上用以装夹工件的一种装置,其作用是使工件相对于机床或刀具有个正确的位置,并在加工过程中保持这个位置不变。
它们的研究对机械工业有着很重要的意义,因此在大批量生产中,常采用专用夹具。
而本次对于零件加工工艺及夹具设计的主要任务是:⑴完成零件加工工艺规程的制定;⑵完成专用夹具的设计。
通过对零件的初步分析,了解其零件的主要特点,加工难易程度,主要加工面和加工粗、精基准,从而制定出零件加工工艺规程;对于专用夹具的设计,首先分析零件的加工工艺,选取定位基准,然后再根据切削力的大小、批量生产情况来选取夹紧方式,从而设计专用夹具。
2 零件的分析2.1 零件的形状题目给的零件是上壳体零件,主要作用是起连接作用。
零件的实际形状如上图所示,从零件图上看,该零件是典型的零件,结构比较简单。
具体尺寸,公差如下图所示。
2.2 零件的工艺分析由零件图可知,其材料为HT20-40,该材料为灰铸造,具有较高强度,耐磨性,耐热性及减振性,适用于承受较大应力和要求耐磨零件。
上壳体零件主要加工表面为:1. 粗铣底面、半精铣,表面粗糙度a R 值为3.2m μ。
2. 粗铣、半精铣上端面,表面粗糙度a R 值3.2m μ。
3. 车外圆,表面粗糙度a R 值3.2m μ。
5.两侧面粗糙度a R 值6.3m μ、12.5m μ,面粗糙度a R 值6.3m μ。
上壳体共有两组加工表面,他们之间有一定的位置要求。
现分述如下:(1).底部端面的加工表面:这一组加工表面包括:端面,内圆,倒角钻孔并攻丝。
这一部份只有端面有6.3的粗糙度要求。
其要求并不高,粗车后半精车就可以达到精度要求。
而钻工没有精度要求,因此一道工序就可以达到要求,并不需要扩孔、铰孔等工序。
(2).端面的加工表面:这一组加工表面包括:端面,粗糙度为3.2;的端面,并带有倒角;中心孔。
其要求也不高,粗车后半精车就可以达到精度要求。
其中,内圆直接在车床上做镗工就行了。
3 工艺规程设计本上壳体假设年产量为10万台,每台车床需要该零件1个,备品率为19%,废品率为0.25%,每日工作班次为2班。
该零件材料为HT20-40,考虑到零件在工作时要有高的耐磨性,所以选择铸铁铸造。
依据设计要求Q=100000件/年,n=1件/台;结合生产实际,备品率α和废品率β分别取19%和0.25%代入公式得该工件的生产纲领N=2XQn(1+α)(1+β)=238595件/年3.1 确定毛坯的制造形式零件材料为HT20-40,铸件的特点是液态成形,其主要优点是适应性强,即适用于不同重量、不同壁厚的铸件,也适用于不同的金属,还特别适应制造形状复杂的铸件。
考虑到零件在使用过程中起连接作用,分析其在工作过程中所受载荷,最后选用铸件,以便使金属纤维尽量不被切断,保证零件工作可靠。
年产量已达成批生产水平,而且零件轮廓尺寸不大,可以采用砂型铸造,这从提高生产效率,保证加工精度,减少生产成本上考虑,也是应该的。
3.2 基面的选择基面选择是工艺规程设计中的重要工作之一,基面选择的正确与合理,可以使加工质量得到保证,生产效率得以提高。
否则,不但使加工工艺过程中的问题百出,更有甚者,还会造成零件大批报废,使生产无法正常进行。
粗基准的选择,对像上壳体这样的零件来说,选好粗基准是至关重要的。
对本零件来说,如果外圆的端面做基准,则可能造成这一组内外圆的面与零件的外形不对称,按照有关粗基准的选择原则(即当零件有不加工表面时,应以这些不加工表面做粗基准,若零件有若干个不加工表面时,则应以与加工表面要求相对应位置精度较高的不加工表面做为粗基准)。
对于精基准而言,主要应该考虑基准重合的问题,当设计基准与工序基准不重合时,应该进行尺寸换算,这在以后还要专门计算,此处不在重复。
3.3 制定工艺路线制定工艺路线的出发点,应当是使零件的几何形状、尺寸精度及位置精度等技术要求能得到合理的保证。
在生产纲领已经确定为成批生产的条件下,可以考虑采用万能性机床配以专用夹具,并尽量使工序集中来提高生产率。
除此以外,还应当考虑经济效果,以便使生产成本尽量下降。
3.3.1工艺路线方案一10 铸造铸造20 时效时效30 涂底漆涂底漆40 粗铣粗铣底部大端面50 精铣精铣底部大端面60 粗铣粗铣顶部凸台端面70 精铣精铣顶部凸台端面80 钻扩铰钻扩铰底部2-φ11孔, 2-φ13孔,钻,14-φ11孔90 铣削铣削中间凹槽两端面100 铣削铣削两侧面110 钻孔钻凸台φ26120 钻攻丝钻M16螺纹孔并攻丝130 钻扩铰钻扩铰左侧4-φ16、φ20台阶孔140 钻扩铰钻扩铰右侧4-φ16、φ20台阶孔150 钻钻左侧4-φ9.6孔机加工160 钻扩铰钻扩铰右侧φ8.5、φ9、φ12台阶孔170 去毛刺去毛刺180 检查检查3.3.2 工艺路线方案二10 铸造铸造20 时效时效30 涂底漆涂底漆40 粗铣粗铣底部大端面50 精铣精铣底部大端面60 粗铣粗铣顶部凸台端面70 精铣精铣顶部凸台端面90 铣削铣削中间凹槽两端面100 铣削铣削两侧面110 钻孔钻凸台φ2680 钻扩铰钻扩铰底部2-φ11孔, 2-φ13孔,钻,14-φ11孔120 钻攻丝钻M16螺纹孔并攻丝130 钻扩铰钻扩铰左侧4-φ16、φ20台阶孔140 钻扩铰钻扩铰右侧4-φ16、φ20台阶孔150 钻钻左侧4-φ9.6孔机加工160 钻扩铰钻扩铰右侧φ8.5、φ9、φ12台阶孔170 去毛刺去毛刺180 检查检查3.3.3 工艺方案的比较与分析上述两个方案的特点在于:方案一的定位和装夹等都比较方便。