测量系统分析方法
MSA测量系统分析流程及方法

MSA测量系统分析流程及方法MSA(测量系统分析)是对测量系统稳定性、可靠性和能力的评估,用于确认测量结果的准确性和可靠性。
它可以用于评估任何测量系统,包括设备、仪器和应用程序。
以下是MSA的流程和方法:1.确定测量系统的目的和应用:在开始MSA之前,首先需要明确测量系统的目的和应用。
这将有助于确定需要分析的关键因素以及选择适当的方法。
2.选择测量系统分析方法:根据测量系统的类型和目的,选择适当的MSA方法。
常见的方法包括GR&R(重复性与再现性)分析、准确性、稳定性和线性度分析。
3.收集数据:使用标准样本或实际样本来收集测量数据。
应该保证数据具有代表性和充分,以便能够全面评估测量系统的性能。
4.重复性与再现性(GR&R)分析:这是评估测量仪器和操作员之间的可重复性和再现性的方法。
它通常包括重复性(同一操作员重复测量同一样本)和再现性(不同操作员在不同时间重复测量同一样本)的分析。
5.准确性分析:准确性是评估测量结果与真实值之间的偏差程度。
可以使用标准样本或比较方法(如正交试验)来评估准确性。
如果测量系统有偏差,可以进行校正,以提高测量的准确性。
6.稳定性分析:稳定性是指测量系统的输出是否随时间而变化。
稳定性分析可以通过收集数据的不同时间点来进行。
7.线性度分析:线性度是指测量系统对于不同输入值的响应是否是线性的。
线性度分析可以通过收集不同输入值对应的测量数据来进行。
8.分析结果和改进措施:对收集到的数据进行分析,并得出结论和建议。
如果测量系统的性能不符合要求,应制定相应的改进措施,例如修理、更换或校准测量设备,培训操作员,改进测量方法等。
9.持续监控和改进:MSA是一个持续改进的过程,应确保测量系统的性能得到持续监控和改进。
定期重复MSA分析,以确保测量系统的稳定性和准确性,及时发现和纠正潜在问题。
总结起来,MSA的流程包括确定目的和应用、选择方法、收集数据、进行分析,最后制定改进措施和持续监控。
MSA-测量系统分析-GRR
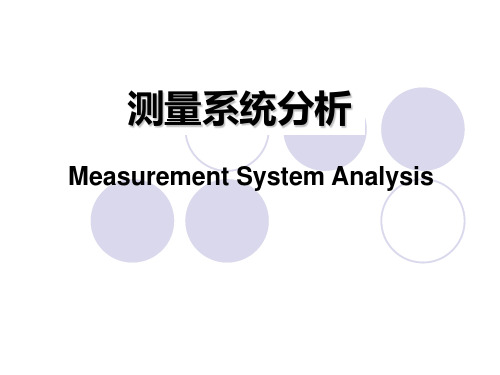
思考题 1
MSA被广泛应用于评估针对机械特性的测量系统, 那么:
针对电气特性(如本公司产品的BB, RF特性)的 测量系统(BT, FT) ,是否也一样适用?
● 误差超过30% — 不可接受的,必须改进测量系统。
测量系统的最终可接受性不应该单纯由一组指数来决定。测 量系统的长期表现也应该利用长性能的图形分析得到评审。
5、系统测量中的注意点:
为最大限度地减少误导结果的可能性,应采取下列步骤:
1> 测量应按照随机顺序,以确保整个研究过程中产生的任何漂移或变 化将随机分布。
4、小结
√ 误差是不可避免的,有测量就有误差。 √ 误差来自测量系统。 √ 误差随着测量系统、时间的改变而变化,从而产生
误差的变异,即测量变异。 √ 通过改进测量系统,可以减小误差。
内容
一、 测量系统的定义 二、 认识误差 三、 GR&R 四、 稳定性 五、 不确定度 六、 测量系统分析
1、名词解释
变差 √评价人内部:技巧、位置、缺乏经验、操作技能或培训、意
识、疲劳 √环境内部:对温度、湿度、振动、清洁的小幅度波动 √错误的假设—稳定,适当的操作 √缺乏稳健的仪器设计或方法,一致性不好 √量具误用 √失真(量具或零件)、缺乏坚固性 √应用—零件量、位置、观测误差(易读性、视差)
4、造成再现性误差的原因
3、如何“减小”误差?
- 多次测量取平均值 - 多人测量取平均值 - 使用更“高级”的测量设备 - 改进测量方法 - 使用辅助工具 - 向更高级别的标准看齐 - 培训 - 测量环境的要求 - 改进被测工件,方便测量
测量系统分析方法
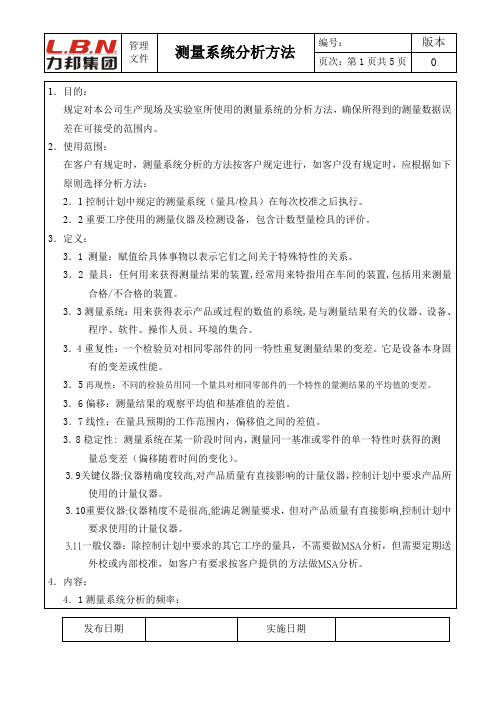
(7) 计算各位评价人的漏发和误发的概率,并将计算及判定结果填到表5中,计算公式为:
漏发率=将合格判定为不合格的次数/(合格的件数×3)
误发率=将不合格判定为合格的次数/(不合格的件数×3)
4.4偏倚分析
4.4.1获取1个样本并确定其相对可追溯标准的基准值。
4.4.2在全尺寸检验设备上,对一个基准值进行精密测量。
附表五:《计数型假设性试验分析报告表》
编制:审核:批准:
确定,“代码”栏用“I”、“II”、“III”代表零件是位于I区、II区还是III
区);
(4) 用交叉表法来评价每个评价人与其它人的结果(如表1所示);这些表格的目
的在于确定评价人之间一致性的程度。
表1:A*B交叉表
为确定一致性的程度,应计算Kappa,当Kappa等于1时,表示有完全的一致性,为
0时,表示一致性不比可能性来得好。Kappa的计算公式为:
4.4.3让一位评价人用正被评价的量具测量同一零件至少10次。
4.4.4计算这10次读数的平均值,基准值与平均值之间的差值表示测量系统的偏移。即:偏移=观测平均值-基准值。
4.4.5计算偏移%:偏移%=偏移/过程变差,其中过程变差=6б极差。
4.4.6偏移的接受准则:偏移和零没有明显差别,零偏移必须位于偏移T分布的95%的置信区间内。
(5) 建立另一组交叉表(如表3所示),以便将每个评价人与参考决定进行比较。
计算Kappa值,评价每个评价人与参考之间的一致性。
表3 A*参考 交叉表
(6) 计算测量系统的有效性(如表4),计算公式为:有效性=
表4 有效性判定计算表
对有效性的判定准则为:当有效性大于或等于80%时,就认定为评价人的有效性可接
测量系统分析报告怎么做
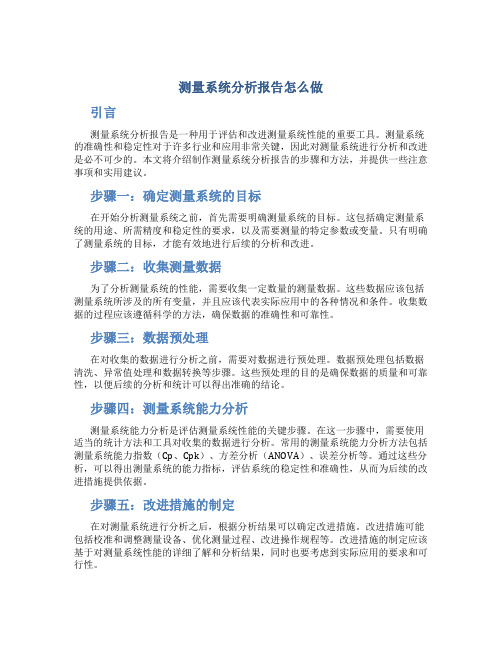
测量系统分析报告怎么做引言测量系统分析报告是一种用于评估和改进测量系统性能的重要工具。
测量系统的准确性和稳定性对于许多行业和应用非常关键,因此对测量系统进行分析和改进是必不可少的。
本文将介绍制作测量系统分析报告的步骤和方法,并提供一些注意事项和实用建议。
步骤一:确定测量系统的目标在开始分析测量系统之前,首先需要明确测量系统的目标。
这包括确定测量系统的用途、所需精度和稳定性的要求,以及需要测量的特定参数或变量。
只有明确了测量系统的目标,才能有效地进行后续的分析和改进。
步骤二:收集测量数据为了分析测量系统的性能,需要收集一定数量的测量数据。
这些数据应该包括测量系统所涉及的所有变量,并且应该代表实际应用中的各种情况和条件。
收集数据的过程应该遵循科学的方法,确保数据的准确性和可靠性。
步骤三:数据预处理在对收集的数据进行分析之前,需要对数据进行预处理。
数据预处理包括数据清洗、异常值处理和数据转换等步骤。
这些预处理的目的是确保数据的质量和可靠性,以便后续的分析和统计可以得出准确的结论。
步骤四:测量系统能力分析测量系统能力分析是评估测量系统性能的关键步骤。
在这一步骤中,需要使用适当的统计方法和工具对收集的数据进行分析。
常用的测量系统能力分析方法包括测量系统能力指数(Cp、Cpk)、方差分析(ANOVA)、误差分析等。
通过这些分析,可以得出测量系统的能力指标,评估系统的稳定性和准确性,从而为后续的改进措施提供依据。
步骤五:改进措施的制定在对测量系统进行分析之后,根据分析结果可以确定改进措施。
改进措施可能包括校准和调整测量设备、优化测量过程、改进操作规程等。
改进措施的制定应该基于对测量系统性能的详细了解和分析结果,同时也要考虑到实际应用的要求和可行性。
步骤六:实施改进和监控效果在确定了改进措施之后,需要实施这些措施,并监控改进效果。
这可以通过再次收集和分析测量数据来实现。
对新采集的数据进行分析,与之前的数据进行对比,以评估改进措施的有效性和效果。
测量系统分析及质量控制

测量系统分析及质量控制测量系统是指用于获取和分析各种尺寸和特征的工具、设备和流程。
它对于制造业和各种其他行业来说至关重要,因为它能够确保产品和服务的准确性、一致性和可靠性。
为了确保测量系统的正确性,必须进行一系列的分析和控制。
在本文中,我们将探讨测量系统分析及其在质量控制中的应用。
第一部分:测量系统分析测量系统分析是指有意识地评估测量系统可能出现的误差、偏差和不确定性。
这种分析通常由专业技术人员在适当的环境下进行。
在进行这种分析时,需要考虑到各种因素,例如测量设备、测量方法、测量对象和环境条件等。
以下是一些常见的测量系统分析方法。
1. 重复性和再现性分析重复性是指在相同测量条件下重复测量同一物品所得到的结果之间的差异。
再现性是指在不同测量条件下测量同一物品所得到的结果之间的差异。
通过重复性和再现性分析,可以确定测量系统的稳定性和准确性。
2. 直线度和平面度分析直线度和平面度是指物体表面偏离真实的直线或平面的程度。
通过直线度和平面度分析,可以确定测量设备的准确性和精度。
3. 单设备多样本分析单设备多样本分析是指使用同一测量设备测量多个相同或类似的物品。
通过这种方法,可以确定测量设备的稳定性和准确性。
以上是一些常见的测量系统分析方法,但不局限于这些。
在实际应用中,根据需要进行具体的分析方法。
第二部分:测量系统质量控制在测量系统分析的基础上,可以对测量系统进行质量控制。
两者有许多相似之处,但也存在一些不同之处。
测量系统质量控制的目的在于确保测量系统的准确性和可靠性。
以下是一些常见的测量系统质量控制方法。
1. 标准化测量环境测量设备必须在一个标准化的环境中使用。
这意味着温度、湿度、光线等条件必须受到控制。
通过维持稳定的环境条件,可以减少测量结果的不确定性。
2. 维护和标定测量设备必须经常进行维护和标定。
这意味着要确保设备处于最佳状态,并能够提供可靠的测量结果。
每台设备必须按照规定的周期进行标定。
标定过程是使用已知尺寸或特征的物品对测量系统进行比较,以确保测量系统的准确性。
测量系统分析报告

测量系统分析报告一、引言测量系统的分析是生产过程中必不可少的一环,它对于质量控制和监督至关重要。
测量系统分析的目的是评估测量系统的准确性和可重复性,以确定其是否满足生产过程的要求。
小样法是一种常用的测量系统分析方法,本报告旨在使用小样法分析一个具体测量系统的准确性和可重复性。
二、方法和过程本次测量系统分析的目标是分析电子公司生产线上一个长度测量仪的测量系统。
使用小样法进行测量系统分析的基本步骤包括:1.选择样本:从生产线上随机选择一些样本进行测试。
为了保证结果的可靠性,样本的数量应足够,通常建议至少30个样本。
2.进行测量:使用仪器(测量仪)对所选样本进行测量。
所有的测量都应该在相同的条件下进行,例如温度、湿度等环境因素应保持一致。
3.数据处理:将所得的测量数据进行分析和处理,包括计算准确度和可重复性统计量,并作出相应的图表和曲线。
4.结果评估:根据准确度和可重复性统计量的结果,评估测量系统的性能,并采取相应的改进措施。
三、结果与分析根据上述步骤,我们在该电子公司生产线上随机选择了35个样本,并使用该长度测量仪进行测量。
所得的数据经过处理得出以下结果:1. 准确度:对于所选样本的测量结果,计算平均值和标准偏差,得到整体的准确度指标。
在本次分析中,平均值为50.5cm,标准偏差为0.2cm。
根据要求,该测量仪的准确度要求在±0.5cm之内,因此该结果表明该测量系统的准确度是满足要求的。
2. 可重复性:对于相同样本的多次测量结果,计算标准偏差和可重复性指标。
在本次分析中,标准偏差为0.1cm,可重复性为0.15cm。
根据要求,该测量仪的可重复性要求在±0.3cm之内,因此该结果表明该测量系统的可重复性是满足要求的。
四、结论通过小样法测量系统分析,我们得出以下结论:1. 对于该电子公司生产线上的长度测量仪,其准确度满足要求,在±0.5cm之内。
2. 对于相同样本的多次测量结果,测量系统的可重复性也满足要求,在±0.3cm之内。
测量系统分析MSA--原理和通用方法
b= ∑y/n-a*(∑x/n)
R2=
[∑xy-∑x∑y/n]2 [∑x2-((∑x)2/n)]*[∑y2-((∑y)2/n)]
线性由最佳拟合直线的斜率而不是拟合优度(R2 )的值确定,斜率越低,线性越好。
分辨力对测量系统变差的影响
分 辨 力 合 适 的 控 制 图
0.145 0.144 0.143 0.142 0.141 0.14 0.139 0.138 0.137 0.136 0.135
0.02
0.015
0.01
0.005
0
0.14555(UCL) 控制上限
0.13571(LCL) 控制下限
0.1810(UCL) 控制上限
用规定的检测方式测量每个零件以确定其基准 值和确认包含了被检量具的工作范围;
让通常情况下使用该量具的操作人之一用该量 具测量每个零件12次;
计算每个零件平均值和偏移平均值; 计算回归直线和直线的拟合优度。
线性计算方法
Y=b+aX
其中:X=基准值;Y=偏倚;a=斜率
a=
∑xy-(∑x∑y/n) ∑x2-(∑x)2/n
再现性或评价人变差(AV或σo)由评价人的最 大平均差(XDIFF)乘以一个常数(K2)得出。 K2取决于量具分析中的评价人数量。评价人变 差包含设备变差,必须减去设备变差来校正。 AV=√[XDIFF×K2]2-(EV)2/n*r
n=零件数,r=试验次数
重复性和再现性——数据分析
测量系统变差重复性和再现性(R&R或σm)的 计算是将设备变差的平方与评价人变差的平方 相加并开方得出: R&R=√[(EV)2+(AV)2]
比较,确定测量系统的重复性是否适于应用。
测量系统分析MSAGRR
测量系统分析MSAGRRMSA(测量系统分析)GRR(重复性与再现性)是一种统计方法,用于评估测量系统的准确性和可靠性。
在质量控制和过程改进中,准确的测量是确保产品或过程符合规范要求的关键因素。
本文将详细介绍MSAGRR的概念、目的、步骤以及如何进行数据分析。
一、MSAGRR概念MSAGRR是通过测量系统进行多次测量,并评估测量数据重复性和再现性的一种方法。
重复性是指在相同条件下,同一测量人对同一测量对象进行多次测量得到的结果的一致性;再现性是指在相同条件下,不同的测量人对同一测量对象进行多次测量得到的结果的一致性。
MSAGRR利用统计分析的方法确定各个组成部分对测量结果的影响程度,进而评估测量系统的准确性和可靠性。
二、MSAGRR目的MSAGRR的目的是评估测量系统的准确性和可靠性,确定测量系统是否适用于特定的质量控制和过程改进需求。
通过进行MSAGRR分析,可以识别出测量系统中的问题,进而采取相应的措施进行改进,以提高测量数据的准确性和可靠性。
三、MSAGRR步骤1.确定测量目标:明确需要评估的测量系统和测量对象,明确需要测量的特定要素。
2.收集数据:选择代表性的样本,并由多个测量人在相同条件下对同一测量对象进行多次测量。
每个测量人至少进行10次测量。
3.分析数据:使用统计软件和工具对收集到的数据进行分析,包括计算测量系统的重复性、再现性和误差等指标。
4.判断测量系统的准确性和可靠性:根据分析结果,判断测量系统是否满足质量控制和过程改进的要求。
5.提出改进建议:如果分析结果显示测量系统存在问题,需要提出相应的改进建议,并采取相应的措施进行改进,以提高测量系统的准确性和可靠性。
四、数据分析MSAGRR的数据分析主要包括以下几个方面:1.重复性和再现性分析:分别计算测量系统的重复性和再现性指标。
重复性指标通常采用方差分析方法进行计算,包括组内变异和总变异;再现性指标通常采用方差分析方法进行计算,包括测量人变异和总变异。
简单明了的MSA(测量系统分析)方法
MSA(MeasurementSystemAnalysis)使用数理统计和图表的方法对测量系统的分辨率和误差进行分析,以评估测量系统的分辨率和误差对于被测量的参数来说是否合适,并确定测量系统误差的主要成分。
以事实和数据驱动管理,而数据是测量的结果,因此在开展统计分析时,要特别强调数据本省的质量和相应的测量系统分析。
测量:是指对具体事物赋予数值,以表示它们与特定特性之间的关系。
在这个过程中,由人员、仪器或量具、测量对象、操作方法和环境构成的整体就是测量系统。
所谓测量系统分析,是指运用统计学的方法对测量系统进行评估,在合适的特性位置测量正确的参数,了解影响测量结果的波动来源及分布,并确认测量系统是否符合工程需求。
任何实测数据的波动都可以看作过程的波动和测量系统的波动之和,即σ2总=σ2过程+σ2测量系统六个常见的测量系统评估项目稳定性、偏倚、线性、分辨率、重复性和再现性。
其中偏倚是测量系统准确度的度量。
01偏倚Bias测量观察平均值与该零部件采用精密仪器测量的标准平均值的差值02线性表征量具预期工作范围内偏倚值的差别03稳定性表征测量系统对于给定的零部件或标准件随时间变化系统偏倚中的总偏差量,与通常意义上的统计稳定性是有区别的04重复性指同一个评价人,采用同一种测量仪器,多次测量同一零件的同一特性时获得的测量值(数据)的偏差05再现性指由不同的评价人,采用相同的测量仪器,测量同一零件的同一特性时测量平均值的偏差通常,前三种指标用于评价测量系统的准确性,后两种指标用于评价测量系统的精确性。
测量系统的准确性可以通过对设备的校准等对测量系统进行维护、监控,也就是说,通过对测量系统的分辨率、偏倚、线性和稳定性进行分析后进行校准后可以解决其准确性问题。
工程上通常用测量系统的精确性也就是其重复性和再现性来研究其统计特性,就是通常所说的“GR&R研究”。
测量系统分析流程及方法测量系统分析是一项重要的系统工程。
测量系统分析方法
测量系统分析方法在测量系统中,测量数据的准确性和可靠性非常重要。
无论是在生产过程中的质量控制还是在科学研究中,正确的测量结果都是做出准确决策的基础。
因此,必须对测量系统进行分析,以确保其满足要求,并提供可靠的结果。
MSA使用一系列统计方法和工具来评估测量系统的性能。
它涉及对测量系统的稳定性、准确度、重复性和再现性等方面进行评估。
首先,稳定性是指测量系统的一个重要属性。
它描述了测量系统是否在相同条件下产生一致的结果。
通过对测量数据的分析,可以确定测量系统是否具有稳定性。
如果测量值在相同条件下有很大的差异,则意味着测量系统不稳定,可能需要进行调整或改进。
其次,准确度是测量系统的另一个关键属性。
它表示测量系统是否接近被测量对象的真实值。
通过与参考值进行比较,可以衡量测量系统的准确度。
如果测量结果与参考值接近,则可以认为测量系统具有较高的准确度。
另外,重复性和再现性是评估测量系统一致性的两个重要指标。
重复性指在相同条件下,同一测量人员对相同对象进行测量时的一致性。
再现性指在相同条件下,不同测量人员对相同对象进行测量时的一致性。
通过对重复性和再现性进行分析,可以确定测量系统是否可靠和一致。
MSA使用一系列工具来评估测量系统的性能,包括测量系统分析图、方差分析、偏倚分析等。
这些工具可以帮助确定测量系统的弱点,并提出改进建议。
最后,一旦发现测量系统存在问题,需要采取适当措施来改善。
这可能涉及校准测量设备、提供培训以改进操作人员的技能,或更换不可靠的测量设备等。
总之,测量系统分析(MSA)是一种评估和改善测量过程的重要方法。
通过对测量系统的分析,可以确保测量结果的准确性和可靠性,为决策提供正确的依据。
在各个领域中应用MSA可以提高质量控制和科学研究的可靠性,从而推动整体业绩的提升。
- 1、下载文档前请自行甄别文档内容的完整性,平台不提供额外的编辑、内容补充、找答案等附加服务。
- 2、"仅部分预览"的文档,不可在线预览部分如存在完整性等问题,可反馈申请退款(可完整预览的文档不适用该条件!)。
- 3、如文档侵犯您的权益,请联系客服反馈,我们会尽快为您处理(人工客服工作时间:9:00-18:30)。
测量系统分析(MSA)方法测量系统分析(MSA)方法**** 1.目的对测量系统变差进行分析评估,以确定测量系统是否满足规定的要求,确保测量数据的质量。
2.范围适用于本公司用以证实产品符合规定要求的所有测量系统分析管理。
3.职责质管部负责测量系统分析的归口管理;公司计量室负责每年对公司在用测量系统进行一次全面的分析;各分公司(分厂)质检科负责新产品开发时测量系统分析的具体实施。
4.术语解释测量系统(Measurement system):用来对被测特性赋值的操作、程序、量具、设备以及操作人员的集合,用来获得测量结果的整个过程。
偏倚(Bias):指测量结果的观测平均值与基准值的差值。
稳定性(Stability):指测量系统在某持续时间内测量同一基准或零件的单一特性时获得的测量平均值总变差,即偏倚随时间的增量。
重复性:重复性(Repeatability)是指由同一位检验员,采用同一量具,多次测量同一产品的同一质量特性时获得的测量值的变差。
再现性: 再现性(Reproductivity) 是指由不同检验员用同一量具,多次测量同一产品的同一质量特性时获得的测量平均值的变差。
分辨率(Resolution):测量系统检出并如实指示被测特性中极小变化的能力。
可视分辨率(Apparent Resolution):测量仪器的最小增量的大小,如卡尺的可视分辨率为。
有效分辨率(Effective Resolution):考虑整个测量系统变差时的数据等级大小。
用测量系统变差的置信区间长度将制造过程变差(6δ)(或公差)划分的等级数量来表示。
关于有效分辨率,在99%置信水平时其标准估计值为GR&R。
分辨力(Discrimination):对于单个读数系统,它是可视和有效分辨率中较差的。
盲测:指在实际测量环境中,检验员事先不知正在对该测量系统进行分析,也不知道所测为那一只产品的条件下,获得的测量结果。
计量型与计数型测量系统:测量系统测量结果可用具体的连续的数值来表述,这样的测量系统称之为计量型测量系统; 测量系统测量结果用定性的数据来表述,如用通过或不能通过塞规的方式来描述一只圆棒直径尺寸,这样的测量系统称之为计数型测量系统。
计量型测量系统和计数型测量系统的分析将用到不同的方法。
5.工作程序:测量系统分析时机:在下述三种情况下必须进行测量系统分析。
新产品开发时;检验员发生变更或新购量具或经维修过的量具投入使用前;定期做,公司规定每年进行一次全面的测量系统分析,分析范围覆盖所有合格在用的不同型号规格的量具,分析内容覆盖测量系统五性。
测量系统分析条件测量作业必须标准化;检验员必须是经培训合格人员;测量仪器必须是检定合格状态;质量特性测量值可重复。
计量型测量系统分析稳定性分析选取一个样本并确定其相对于可追溯标准的基准值,如果不能得到,则选择一个落在使用的量程中程数的产品,并指定它作为标准样本进行稳定性分析。
定期(天,周,月)测量基准样品3-5次,决定样本容量和频率时考虑的因素有:校准周期、使用频率、修理次数和使用环境等。
读数应在不同时间读取以代表测量系统实际使用的情况。
将测量值描绘在《量具稳定性分析报告》记录的XBAR-R控制图上。
计算控制界限,并参照Q/HC31006A—2002《SPC(统计过程控制)应用方法》控制图判读规则对不稳定或失控作出判断,如有不稳或异常现象应进行原因分析,并采取相应措施(如对量具进行校准或维修)。
测量系统稳定性分析记录于《量具稳定性分析报告》中。
偏倚分析(独立样本法)获取一个样本并确定其相对于可追溯标准的基准值, 如果不能得到,则选择一个落在使用的量程中程数的产品,并对其用精密的量具(通常精度为被分析量具的4~10倍)测量10次计算平均值,此值作为“基准值”。
由一位检验员,以常规方式对样品测量10次,并计算10次读数的平均值, 此值即为“观测平均值”。
计算偏倚偏倚=观测平均值--基准值制造过程变差=6δ偏倚%=偏倚/制造过程变差×100%制造过程变差可从以前的过程控制图得出,或从同时进行的过程能力研究得出,如无法求得时,可用规格公差代替。
偏倚接受准则:a、对测量重要特性的测量系统偏倚%10%时可接受;b、对测量一般特性的测量系统10%≤偏倚%≤30%时可接受;c、偏倚%>30%,拒绝接受。
偏倚分析记录于《量具偏倚分析报告》线性分析选择5个产品,它们的测量值要覆盖量具的工作量程。
用精密量具测量每个产品以确定它们各自的“基准值”并确认其尺寸覆盖了被分析量具的工作量程。
由被分析量具的操作员盲测每个产品12次,并计算测量平均值和偏倚。
绘图:以基准值为X轴,偏倚为Y轴作散布图。
使用以下公式求最佳拟合这些点的回归直线和直线的相关系数R。
y=b+ax式中:x为基准值y为偏倚b为截距a为斜率a=/b=(ΣYi-aΣXi)/nR2=2/{×}线性=斜率×(制造过程变差)=Q/HC31007A—2002线性%= ×100%线性判读准则线性程度判读a、R2=1,完全相关,点散布在一条直线上;b、R2=0,完全不相关,X与Y的变化完全不存在任何依存关系;c、0<R2<1,不完全相关;线性接受准则a、对测量重要特性的测量系统,线性%≤5%时可接受;b、对测量一般特性的测量系统,线性%≤10%时可接受;c、线性%>10%,拒绝接受。
线性分析记录于《量具线性分析报告》。
重复性和再现性分析(R &R)确定研究对象、工序、量具、产品和质量特性后可采用下列方法进行分析。
极差(R)法选取两位检验员A、B和5个产品,每个检验员对每个产品盲测一次,将测量结果记入《量具极差法分析表》表格中。
计算产品测量的极差R,测量极差R为检验员A和B测量结果差的绝对值。
计算产品测量的平均极差R=∑Ri/5。
计算量具的双性(重复性和再现性的合成,简称双性),即测量过程变差:GR&R=d2式中:GR&R表示量具(Gage)重复性和再现性的合成,表示99%的置信区间,即2个检验员用同一量具测量同一产品的同一特性的测量结果99%落在GR&R区间内,d2可从《测量系统分析用d2值表》中查出。
计算双性占制造过程变差的百分数% GR&R= (GR&R/过程变差)×100%。
GR&R接受准则:a、% GR&R<10%可接受;b、10%≤% GR&R≤30%,依据质量特性的重要性及量具的重要性、成本及维修费用,决定是否接受;c、% GR&R>30%,不能接受。
均值极差法(X&R法)确定二至三名检验员,标以A、B、C,检验员选取需注意代表性,如生产部门检验员与质检部门检验员的相互搭配、白班与夜班检验员的相互搭配等。
抽取同一种型号产品样本5至10件,标上编号,抽取产品时最好保证产品质量特性测量值覆盖该特性值整个公差范围,另注意检验人员应无法看到产品编号,以保证盲测。
每一检验员对同一产品的同一特性重复测量2~3次,将测量结果记录在QR/HC20423-012A《量具重复性和再现性数据表》中。
根据《量具重复性和再现性数据表》中的数据作《量具重复性和再现性X-R控制图》,并判读,判读规则如下:a)、极差图判读参照《SPC(统计过程控制)应用方法》控制图判读规则;b)、均值图:在控制限内的点代表测量误差,如果一半或更多的平均值落在极限之外,则该测量系统足以检查出产品之间差异,测量系统有效分辨率足够,该测量系统可以提供过程控制、过程能力分析有用的数据,当一半以下落在控制限外,则测量系统不足以检查出产品之间差异,不能用于过程控制及过程能力分析。
负责组织测量系统分析的人员,依照《量具重复性和再现性数据表》和质量特性规格,按标准规定的格式出具QR/HC20423-013A《量具重复性和再现性报告》。
结果分析重复性与再现性比较分析A、如果重复性(EV)比再现性(AV)大,原因可能是:——量具需要维修;——应重新设计量具使其更精密;——应改进量具的夹紧或定位装置;——产品变差太大。
B、如果再现性(AV)大于重复性(EV),则可能存在以下原因:——需要对检验员进行如何使用量具和读数的培训;——量具表盘上的刻度值不清楚;——可能需要某种形式的夹具来帮助检验员更为一致地使用量具。
&R接受准则%EV、%AV、%R&R三个误差都<10%——测量系统可接受;%EV、%AV、%R&R三个误差在10%到30%之间——测量系统可能被接受,依据量具的重要性、量具成本以及修理费用而定。
%EV、%AV、%R&R三个误差有一个超过30%——测量系统不能接受,需要改进,应努力找到问题所在并纠正。
计数型测量系统分析(小样法)任取同一型号的产品20件(应包括有合格及不合格的产品)并予以编号,编号不可让检验员知道,也不可让他们知道正在做测量系统分析,以保证盲测。
选择两位检验员分为A、B。
由这两位检验员测量所有产品两次,并将测量结果记录于QR/HC20423-014A《计数型量具检验记录表》,合乎规格界线的零件则填入“YES”,反之则填入“NO”。
结果判读A、若测量结果(每只产品四个数据)相同,则测量系统被接受。
B、若测量结果不一致,则此测量系统须被改进或再评价。
C、若测量系统不能被改进,则不能被接受,应寻求替代的测量系统。
计数型测量系统只能指出产品是好是坏,不能指出产品好坏程度。
测量系统分析方法适用性的确定新产品开发时, 测量系统采用线性、重复性、再现性、偏倚分析方法,由分公司(分厂)质检科进行分析;考虑量具随时间变化的程度,做稳定性分析,由公司计量室进行分析;每年一次的测量系统五性分析,由公司计量室进行。
6.相关文件检验、测量和试验设备的控制程序质量记录的控制程序1.记录本办法产生记录按《质量记录的控制程序》进行整理、保存、归档。
记录为:《量具稳定性分析报告》《量具偏倚分析报告》《量具线性分析报告》《量具重复性和再现性极差法分析记录表》《量具的重复性和再现性数据记录表》《量具重复性和再现性X-R控制图》《量具的重复性和再现性报告》《计数型量具检验记录表》8.附件 :《控制图的常数和公式表》。