虚拟仪器的简介外文翻译
外文翻译---虚拟仪器(LabVIEW)

虚拟仪器(LabVIEW)虚拟仪器是一种高效用于构建数据采集与监测系统图形化编程语言。
使用虚拟仪器,您快速创建用户界面,让您交互控制您的软件系统。
要指定您系统的功能,您只需装配块关系图—一种自然的设计表示科学家和工程师。
测量硬件紧密集成方便了数据采集、分析与演示文稿解决方案的快速发展。
虚拟仪器包含强大的内置度量分析和一个图形的编辑器实现最佳性能。
虚拟仪器是使用于Windows 2000/NT/Me/9x、Mac OS、Linux、Sun Solaris 和HP-UX,有三种不同的开发系统选项。
更快地发展虚拟仪器通过加快发展了对传统的编程提升了4至10倍!使用模块化和层次结构的虚拟仪器,可以原型,设计,并且在一个短时间内修改系统。
您也可以重用虚拟仪器代码轻松快速地在其他应用程序中应用。
更好的投资使用虚拟仪器系统,每个用户有权访问单一的商业文书的成本低于一个完整的检测实验室。
此外,用户还可配置的虚拟仪器系统足够的灵活性,从而更好地长期投资的技术变化与适应。
优化性能虚拟仪器的所有应用程序执行以获得最佳性能的编译速度。
用虚拟仪器专业开发系统或应用程序生成器,可为您的代码的安全通讯生成独立可执行文件或dll。
您甚至可以创建共享的库或从其他编程语言中调用虚拟仪器代码的dll。
开放的开发环境用虚拟仪器在开放开发环境,您可以连接到通过ActiveX、Web、dll、共享的库、SQL (数据库)、DataSocket、TCP/IP和许多其他协议的其他应用程序。
虚拟仪器用于快速创建网络的测量和Web发布和远程数据共享最新的科技集成的自动化系统。
虚拟仪器也可以用于插件数据采集、信号调理、GPIB、VXI、PXI、基于计算机的仪器、串行协议、图像采集和运动控制的驱动程序。
除了在虚拟仪器的开发系统国家仪器还提供多种附加模块和扩展功能的虚拟仪器的工具集。
这使您可以快速构建可定制、鲁棒的测量和自动化系统。
虚拟仪器数据记录和监督控制模块高通道数的分布式应用程序日志记录的虚拟仪器数据和监督控制模块,提供了一个完整的解决方案。
虚拟现实输出设备
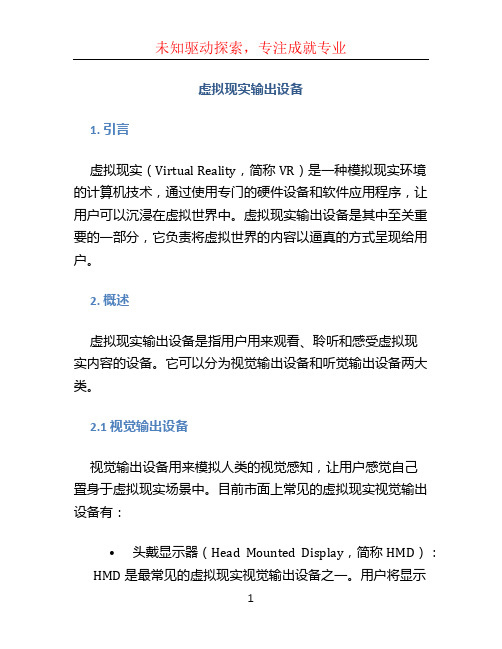
虚拟现实输出设备1. 引言虚拟现实(Virtual Reality,简称VR)是一种模拟现实环境的计算机技术,通过使用专门的硬件设备和软件应用程序,让用户可以沉浸在虚拟世界中。
虚拟现实输出设备是其中至关重要的一部分,它负责将虚拟世界的内容以逼真的方式呈现给用户。
2. 概述虚拟现实输出设备是指用户用来观看、聆听和感受虚拟现实内容的设备。
它可以分为视觉输出设备和听觉输出设备两大类。
2.1 视觉输出设备视觉输出设备用来模拟人类的视觉感知,让用户感觉自己置身于虚拟现实场景中。
目前市面上常见的虚拟现实视觉输出设备有:•头戴显示器(Head Mounted Display,简称HMD):HMD 是最常见的虚拟现实视觉输出设备之一。
用户将显示器戴在头上,可以通过显示器屏幕观看虚拟现实内容。
HMD 通常配备多个传感器,用于追踪用户的头部和眼睛的运动,以实现更加逼真的虚拟现实体验。
•立体显示器:立体显示器是另一种常见的虚拟现实视觉输出设备。
它使用不同的视角和技术,让用户感受到立体和逼真的虚拟现实内容,而无需佩戴头戴显示器。
•投影设备:虚拟现实内容也可以通过投射到物理环境中的方式呈现给用户,这就需要使用投影设备。
投影设备可以将虚拟现实内容投射到墙壁或其他特定的平面上,用户可以通过观看这些投射图像来感受虚拟现实体验。
2.2 听觉输出设备听觉输出设备用来模拟人类的听觉感知,让用户感受到虚拟现实场景中的声音和音效。
常见的虚拟现实听觉输出设备有:•耳机:耳机是最常用的虚拟现实听觉输出设备之一。
用户可以戴上耳机听取虚拟现实内容中的音效和音乐,以增强虚拟现实体验。
•立体声扬声器:除了耳机外,虚拟现实听觉输出设备还包括立体声扬声器。
这些扬声器可以分布在虚拟现实环境中的不同位置,模拟出真实的声音来源和方向,让用户更加沉浸在虚拟现实世界中。
3. 技术原理虚拟现实输出设备的工作原理复杂多样,以下以头戴显示器为例进行介绍。
头戴显示器使用液晶显示屏等技术,将虚拟现实内容呈现给用户。
虚拟仪器技术简介

虚拟仪器的发展方向
• 虚拟仪器的标准化、模块化、网络化。 • 网络技术应பைடு நூலகம்到虚拟仪器领域中是虚拟 仪器发展的大趋势。 • 21世纪的仪器应具有参与性。 • 21世纪的仪器应最大限度实现绿色化。
虚拟仪器的应用领域
• • • • • 应用于生产检测 应用于研究和分析 应用于过程控制和工业自动化 应用于机器监控 图象处理(机械视觉技术)
虚拟仪器的特点
(1)硬件标准化模块化,强调“软件即仪器”的 新概念。 (2)系统集成化,打破了传统仪器小而全的现状。 (3)仪器自定义,便于工作和管理。 (4)程序设计图形化(G语言),计算可视化。 (5)内嵌丰富的数据信号处理功能 (6) 基于计算机网络技术和接口技术,利用虚拟 仪器技术可方便地实现测量、控制过程的网络化。
本书的结构
• 第1-2章:Labview 入门,前面板和程序框图设计方法,这是 Labview编程最基本技能。 • 第3章:程序结构 • 第4章: 数组、簇、波形 • 第5章:图形控件和图形数据显示 • 第6章:Express VI • 第7章:字符串和数据文件 • 第8章:硬件内容:数据采集及信号调理 • 第9章:数据分析与处理 第10章:动态程序控制 • 第11-20章:专题内容: • 第11章:仪器控制、 • 第15章:频率测量 • 第19章:网络应用
模拟仪器->数字化仪器->智能仪器; 单台仪器->层叠式仪器系统阶段 从80年代进入虚拟仪器系统时代, 虚拟仪器技术是21世纪仪器的发展方向! 虚拟仪器将在许多品种和领域内逐步取代 传统硬件仪器,使成千上万种传统仪器演 变为计算机软件!
The Software is The Instrument!
虚拟仪器的构成及分类
labview虚拟仪器程序设计及应用
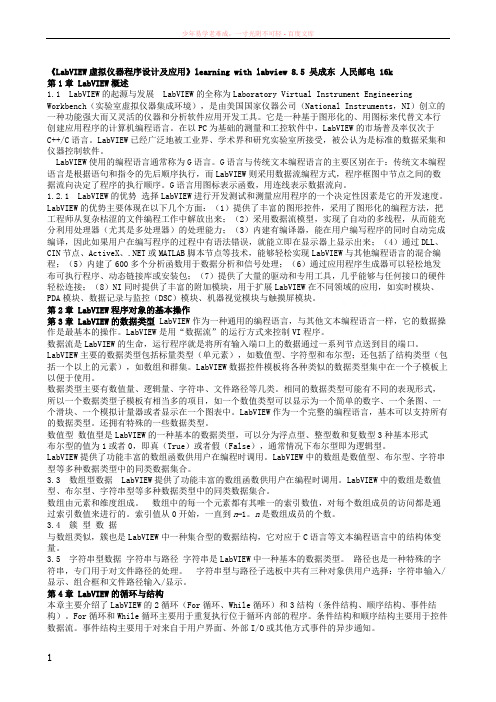
《LabVIEW虚拟仪器程序设计及应用》learning with labview 8.5 吴成东人民邮电 16k第1章 LabVIEW概述1.1 LabVIEW的起源与发展 LabVIEW的全称为Laboratory Virtual Instrument Engineering Workbench(实验室虚拟仪器集成环境),是由美国国家仪器公司(National Instruments,NI)创立的一种功能强大而又灵活的仪器和分析软件应用开发工具。
它是一种基于图形化的、用图标来代替文本行创建应用程序的计算机编程语言。
在以PC为基础的测量和工控软件中,LabVIEW的市场普及率仅次于C++/C语言。
LabVIEW已经广泛地被工业界、学术界和研究实验室所接受,被公认为是标准的数据采集和仪器控制软件。
LabVIEW使用的编程语言通常称为G语言。
G语言与传统文本编程语言的主要区别在于:传统文本编程语言是根据语句和指令的先后顺序执行,而LabVIEW则采用数据流编程方式,程序框图中节点之间的数据流向决定了程序的执行顺序。
G语言用图标表示函数,用连线表示数据流向。
1.2.1 LabVIEW的优势选择LabVIEW进行开发测试和测量应用程序的一个决定性因素是它的开发速度。
LabVIEW的优势主要体现在以下几个方面:(1)提供了丰富的图形控件,采用了图形化的编程方法,把工程师从复杂枯涩的文件编程工作中解放出来;(2)采用数据流模型,实现了自动的多线程,从而能充分利用处理器(尤其是多处理器)的处理能力;(3)内建有编译器,能在用户编写程序的同时自动完成编译,因此如果用户在编写程序的过程中有语法错误,就能立即在显示器上显示出来;(4)通过DLL、CIN节点、ActiveX、.NET或MATLAB脚本节点等技术,能够轻松实现LabVIEW与其他编程语言的混合编程;(5)内建了600多个分析函数用于数据分析和信号处理;(6)通过应用程序生成器可以轻松地发布可执行程序、动态链接库或安装包;(7)提供了大量的驱动和专用工具,几乎能够与任何接口的硬件轻松连接;(8)NI同时提供了丰富的附加模块,用于扩展LabVIEW在不同领域的应用,如实时模块、PDA模块、数据记录与监控(DSC)模块、机器视觉模块与触摸屏模块。
基于LabVIEW的虚拟仪器外文翻译
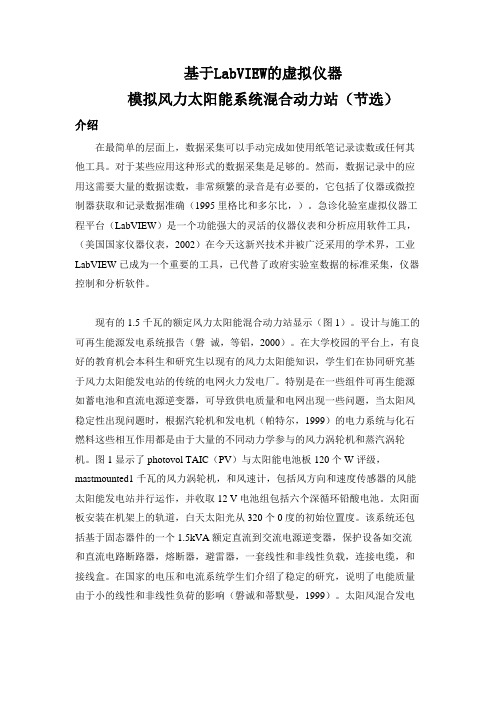
基于LabVIEW的虚拟仪器模拟风力太阳能系统混合动力站(节选)介绍在最简单的层面上,数据采集可以手动完成如使用纸笔记录读数或任何其他工具。
对于某些应用这种形式的数据采集是足够的。
然而,数据记录中的应用这需要大量的数据读数,非常频繁的录音是有必要的,它包括了仪器或微控制器获取和记录数据准确(1995里格比和多尔比,)。
急诊化验室虚拟仪器工程平台(LabVIEW)是一个功能强大的灵活的仪器仪表和分析应用软件工具,(美国国家仪器仪表,2002)在今天这新兴技术并被广泛采用的学术界,工业LabVIEW已成为一个重要的工具,已代替了政府实验室数据的标准采集,仪器控制和分析软件。
现有的1.5千瓦的额定风力太阳能混合动力站显示(图1)。
设计与施工的可再生能源发电系统报告(磐诚,等铝,2000)。
在大学校园的平台上,有良好的教育机会本科生和研究生以现有的风力太阳能知识,学生们在协同研究基于风力太阳能发电站的传统的电网火力发电厂。
特别是在一些组件可再生能源如蓄电池和直流电源逆变器,可导致供电质量和电网出现一些问题,当太阳风稳定性出现问题时,根据汽轮机和发电机(帕特尔,1999)的电力系统与化石燃料这些相互作用都是由于大量的不同动力学参与的风力涡轮机和蒸汽涡轮机。
图1显示了photovol TAIC(PV)与太阳能电池板120个W评级,mastmounted1千瓦的风力涡轮机,和风速计,包括风方向和速度传感器的风能太阳能发电站并行运作,并收取12 V电池组包括六个深循环铅酸电池。
太阳面板安装在机架上的轨道,白天太阳光从320个0度的初始位置度。
该系统还包括基于固态器件的一个1.5kVA额定直流到交流电源逆变器,保护设备如交流和直流电路断路器,熔断器,避雷器,一套线性和非线性负载,连接电缆,和接线盒。
在国家的电压和电流系统学生们介绍了稳定的研究,说明了电能质量由于小的线性和非线性负荷的影响(磐诚和蒂默曼,1999)。
虚拟仪器毕业设计外文翻译

译文1、虚拟仪器的产生背景当今我们处于一个正在高度发展的信息社会,要求在有限的时空上实现大量信息的交换,必然带来信息密度的急剧增大,要求电子系统对于信息的处理速度越来越高,功能越来越强,这使得系统结构日趋复杂。
一方面电子技术及市场的发展从客观上要求测试仪器向自动化及柔性化的方向发展,另一方面,电子技术及市场的发展也给虚拟仪器的产生提供了可能。
在这种形式下,基于微计算机的虚拟仪器逐步变得现实,它的出现和广泛使用为测试系统的设计提供一个极佳的模式,并且使工程师们在测量和控制方面得到强大功能和灵活性。
2虚拟仪器的概念虚拟仪器(Virtual Instrument,简称VI)的概念是由美国国家仪器公司(NI)在20世纪80年代最早提出的。
虚拟仪器就是在以通用计算机为核心的硬件平台上,由用户设计定义、具有虚拟前面板、测试功能由测试软件实现的一种计算机仪器系统。
其核心的思想是利用计算机的强大资源使本来需要硬件实现的技术软件化,以便最大限度地降低系统成本,增强系统功能与灵活性。
虚拟仪器代表着从传统硬件为主的测试系统到以软件为中心的测试系统的根本性转变。
虚拟仪器的出现是仪器发展史上的一场革命,代表着仪器发展的最新方向和潮流,对科学技术的发展和工业生产的进步将产生不可估量的影响。
虚拟仪器具有性能高、扩展性强、开发时间短、无缝集成等优势。
3. 图形化虚拟仪器开发平台—LABVIEW 简介及其优势LABVIEW是Laboratory Virtual Instrument Engineering Workbench (实验室虚拟仪器集成开发环境)的简称,是由美国国家仪器公司(National instruments, IN)创立的一个功能强大而又灵活的仪器和分析应用开发工具。
Labview一种图形化的编程语言,主要用来开发数据采集,仪器控制及数据处理分析等软件,功能强大。
目前,该开发软件在国际测试、测控行业比较流行,在国内的测控领域也得到广泛应用。
虚拟仪器的基本概念、特点和构成
图17-11 三角波基波信号检测VI的前面板 图17-12 三角波基波信号检测VI的框图程序
◆思考与练习2
1、LabVIEW应用程序由哪几部分构成? 2、在上述三角波基波信号检测VI中增加“幅
值”和“相位”测量并进行显示。
项目十七 虚拟仪器
[知识链接一] 虚拟仪器的基本概念 [知识链接二] LabVIEW 8.5编程基础
[知识链接一] 虚拟仪器的基本概念
一、虚拟仪器的概念
虚拟仪器(Virtual Instrument,简称VI)是计算 机技术与仪器技术深层次结合的产物,是对传统 仪器概念的重大突破,是仪器领域内的一次革命。
I/O接口设备组成。 (2)软件结构 虚拟仪器软件由应用程序和I/O接口仪器驱动程序两大部
分构成。 应用程序包含实现虚拟面板功能的前面板软件程序和定
义测试功能的流程图软件程序等两个方面的程序。 I/O接口仪器驱动程序用来完成特定外部硬件设备的扩展、
驱动与通信
虚拟仪器的构成方式主要有五种类型
图17-2 虚拟仪器的构成方式
图17-7 控件选板
(3)函数选板
函数选板仅位于程序框图。函数选板中包含创建 程序框图所需的VI和函数。按照VI和函数的类型, 将VI和函数归入不同子选板中。
图17-8 函数选板
三、LabVIEW中的Express VIs
LabVIEW的最主要特性是其快捷性,主要体现在程 序框图窗口的函数选板中包含了许多功能强大的 Express VI(快速VI)。它将过去的基本函数面向 应用做了进一步的打包,把常用的测量功能集成于 一些简单易用、交互式的VI中。
用户在程序开发过程中,只需在整个程序流程图中 简单地调用Express VI程序,并使用属性设置页面 配置系统的采集、分析与显示功能,实现应用程序 的快速开发与设计,极大地提高了程序开发效率。
虚拟仪器外文翻译
LabVIEW1.overviewLabVIEW is a program development environment, by the national instruments (NI) research and development company, similar to the C and BASIC development environment, but with other computer language LabVIEW significant difference is: other computer language is based on the text, and the language code of graphical LabVIEW use scripting language G program, application is in the form of block diagram.A complete, LabVIEW virtual instrument system of open application software development, and use it to form instrument testing system and data collecting system can simplify the design procedure. With Visual C++ LabVIEW, Visual Basic,LabWindows/CVI, etc, which adopts different programming language is based on the text language program Code (Code), and abVIEW L is using graphical programming language), Graphic (G instead of the traditional diagram of the Code. The Lab VIEW of equipment with the scientists and engineers icon in the habit of basic agreement, this makes the icon programming process and thinking process is very similar.LabVIEW convenient calls Windows DLL and user-defined function in the DLL, LabVIEW also provides CIN (C) Node with any users can use by C + + language or, if the ANSI C, compiled program modules, makes a open LabVIEW development platform. LabVIEW also directly support dynamic data exchange (DDE), structured query language (SQL), TCP and UDP network protocol. In addition, the LabVIEW also provides special used for program development kit, users can easily set breakpoints, dynamic program execution to very intuitive image observation data transmission process, and convenient debug.The operation mechanism is LabVIEW macroeconomic sense is no longer the von neumann traditionally computer system structure of the method. The traditional computer language (such as C) to the order of execution by parallel structure in LabVIEW mechanism; Essentially, it is a kind of control Flow structure with graphical Data Flow pattern (Data Flow Mode), this kind of means to ensure the process of any Node Function in hire those knowledgeable programmers only after all it can only be executed Data.That is to say, in the data flow in the concept of program execution, and it is the data driven by operating system, calculate machine and so on.Since LabVIEW program is data flow driven, data flow design program, a goal only when it's all input can only be effective, And the goal of output only when it is complete. So, in VIEW of the Lab is connected the data flow between nodes function control program execution sequence, and don't like text program execution sequence by rows of constraint. Thus, we can be connected through the rapid development of concise function node applications, even can have multiple data synchronization operation channel, the so-called Multithreading (Multithreading).2.Data Storage and Reporting with NI LabVIEWThe continued increase in processing and storage capacity and the decrease of hardware and software costs has resulted in an explosion of collected data being acquired. But while technology is enabling faster and richer data retention, storing, managing, and sharing data remains the real challenge. Traditional software packages tend to take one of two limiting approaches: 1) they force you into a particular format that is not exchangeable with other applications or users or 2) saving data is left so open ended you waste time trying to determine the best way to organize and save your data to disk so you can share it.NI LabVIEW, designed for the entire engineering process, includes built-in functionality to help you easily save data to disk and create professional reports. By providing easy yet robust interfaces for file I/O and reporting, you can make the most of your acquired data to make decisions faster.(1)File I/O Designed Specifically for Engineering DataDespite the fact that LabVIEW offers a wide variety of file I/O options, these traditional file types rarely meet all the criteria you need in a file format. For example, ASCII files are exchangeable, but are very large and slow to read and write. On the other hand, binary file read and write speeds can keep up with high-speed hardware, but are difficult to share with others.Because of the drawbacks of traditional file I/O, National Instruments developed the Technical Data Management Streaming (TDMS) file format to meet the specific needs and high demands of engineers and scientists. TDMS files are based on the TDM data model for saving well-organized and documented test and measurement data. The TDM data model offers three levels of hierarchy, as shown in Figure 2 – file, group, and channel. The file level can contain an unlimited number of groups, and each group can contain and unlimited number of channels. Because of this channel grouping, you can organize your data to make it easier to understand. For example,you may have one group for your raw data and another group for your analyzed data within one file, or you may have multiple groups that correspond to sensor types or locations.Figure 1. The TDM data model meets the specific requirements of measurementdata.Also, you can insert your own custom properties at each of the three levels. Each level accepts an unlimited number of custom-defined attributes to achieve well-documented and search-ready data files. The descriptive information located in the TDMS file, a key benefit of this model, provides an easy way to document the data much like you would document code. As your documentation requirements increase, you do not have to redesign your application, you simply extend the data model to meet your needs.(2)Multiple Easy-to-Use Programming InterfacesBecause it was developed to meet the needs of all engineers, TDMS offers ease of use, high-speed streaming, and exchangeability. Like many operations in LabVIEW, you can use multiple interfaces to write TDMS files. Y ou can quickly read and write TDMS files using a virtual instrument (VI) such as the Write To Measurement File Express VI or, for the best performance and customization, use the primitive TDMS VIs from the File I/O palette. Also, when using LabVIEW with NI-DAQmx, you can use the Configure Logging VI from the DAQ palette or log directly from the NI DAQ Assistant(3)Files Exchangeable with Other Programs such as Microsoft ExcelBecause you may be required to work in additional applications, TDMS is easily exchangeable across other programs. Y ou can open TDMS files in Microsoft Excel using the TDM Excel Add-In, which installs with NI software and is available free at. Y ou also can use a C DLL for reading and writing TDMS files in other programming languages. NI is committed to helping you write well-organized and documented data using the TDMS file format, regardless of which products you use.(4)Custom and Legacy File Format Reading and WritingAlthough ideally you can choose the file format for each application you work on, you may still be restricted to reading and writing in a custom format due to legacy files or hardware that uses custom formats. Understanding that many engineers face this challenge, NI developed the DataPlugin technology so that you can use these custom formats in LabVIEW. As seen in Figure 4, a DataPlugin acts as a file parser that tells LabVIEW and other NI software how to read your custom file formats and maps them to the TDM hierarchy model in memory.Figure 2. Using a DataPlugin, you can map any file format onto the TDM datamodel.National Instruments provides more than 200 free, downloadable DataPlugins for the most common file formats. For custom formats, you can create your own DataPlugins in LabVIEW and NI DIAdem software using a documented API, or request that an NI expert create a DataPlugin for you. Using DataPlugins, you are no longer limited by custom formats and applications, and have options for how to use your data.3.Organizing and Managing Y our Data with DataFinder T echnology With many applications, the amount of data being collected can quickly become overwhelming. Typically, at that point, you might turn to a database to begin storing your data for faster search and trending. National Instruments makes it easy to interact with a database using the LabVIEW Database Connectivity Toolkit by abstracting the low-level structured query language (SQL) queries. However, moving your existing data to a database, maintaining the database, and creating applications for accessingdata can become extremely costly and time-consuming.In response to this challenge, NI developed NI DataFinder technology, included in the LabVIEW DataFinder Toolkit and DIAdem, for managing test files without the headache and expense of setting up and maintaining a large database. With NI DataFinder, you can perform Internet-like searches across all your data files, regardless of format and location within your company intranet. Simply point NI DataFinder to the location of your data files, and within seconds you can search for your files just as you would search for information on the Internet.NI DataFinder automatically builds and maintains an index of all files that meet the file type and location criteria in the NI DataFinder configuration. Y ou can use properties automatically stored in the NI DataFinder index in query conditions. When a valid data file is created, deleted, or edited, NI DataFinder automatically notices and reindexes the hierarchy and properties of the file. When you save properties not yet in NI DataFinder in a newly created file, these properties are automatically added to the index. NI DataFinder dynamically manages its own data tables and updates them based on file events and the contents of each file. Therefore, unlike many expensive database solutions, you can change and add information as your needs change without redesigning your data management solution. Using the NI DataFinder, you can quickly find trends and correlations in the large amounts of data you have saved during your tests.4.Multiple Programming Approaches in NI LabVIEWNI LabVIEW is a graphical dataflow programming environment. When using dataflow in LabVIEW, you define an execution flow in code by creating diagrams that show how data moves between functions (known as virtual instruments, or VIs). However, with LabVIEW, you can combine multiple programming approaches besides graphical data flow (G) in a single application. Use this flexibility to select your tool of choice for creating algorithms and solving an infinite variety of engineering problems.(1)Defining Programming ApproachesThe phrase …programming approaches‟ encompasses different languages for programming, models of computation, levels of abstraction, methods for interacting with existing code, and ways for representing algorithms. Over the years, National Instruments has added interfaces and methods for communication in LabVIEW to extend the number of approaches that are available.Y ou can write and import multipleapproaches into the same block diagram as the familiar G dataflow language. LabVIEW compiles all of these approaches for the appropriate hardware target, which can span desktop computers, real-time OSs, field-programmable gate arrays (FPGAs), mobile devices, and embedded processors such as ARM.1(2)Programming in GData flow, the fundamental LabVIEW programming method, was the original, and only, programming approach when NI introduced LabVIEW 1.0 in 1986. Unlike sequential-style programming, the flow of data in a dataflow program dictates when, and in what order, operations are executed. In sequential languages such as C and C++, the order of the commands in the source code (as opposed to the availability of data) determines the order in which execution will occur.G follows a dataflow model for running functions and primitives, or VIs. A block diagram function or node executes when all its inputs are available. When a node completes execution, it supplies data to its output terminals and passes the output data to the next node in the dataflow path.Figure 3. A and B are added, and the result is multiplied by C and displayed.The graphical code in Figure 2 shows how a mathematical equation can be represented in G. This diagram consists of two nodes (an add node and a multiply node), and has three numerical inputs (A, B, and C). First, A and B are added. The multiplication node does not execute until both inputs are provided, so it depends on the addition node to complete and provide the result of A + B, at which point it computes the result – (A+B)*C.Although it is possible to explicitly define variables in G, one of the most obvious differences between G code and other languages is that the functional equivalent of a traditional variable is a wire. Instead of passing variables between functions, wires define the functions to which a value is passed. Other familiar programming concepts such as While Loops, For Loops, conditional code, callback functions, and digital logic are all part of the G dataflow programming language(3)Using Configuration-Based ProgrammingIn 2003, National Instruments released NI LabVIEW 7 Express, which featured Express VIs – a new technology designed to further simplify common programming tasks and algorithm creation. Unlike traditional VIs, Express VIs abstracted tasks by offering a configuration-based approach to programming.LabVIEW distinguishes Express VIs with large blue icons. When you place an Express VI on the block diagram, a dialog appears so you can configure how the function executes. After completing the configuration, the LabVIEW development environment writes the necessary code (represented by the Express VI) for you. Y ou can view and modify this code, and you can change the Express VI configuration by simply double-clicking the Express VI icon.Consider the task of reading real-world signals into software for analysis. LabVIEW is designed to make integration with hardware for I/O simple and easy thanks to native drivers and support for thousands of instruments. However, even a task that would otherwise take a handful of VIs to execute can be simplified to a single Express VI. The DAQ Assistance Express VI prompts you to select the channels you want to send and receive I/O to and from, and configure parameters such as sample rate, terminal configuration, scales, triggering, and synchronization. Y ou also can preview the data within the interface before saving the configuration.Express VIs do not offer the same low-level control as VIs, which is why you may prefer to write the code entirely using VIs. New users interested in learning low-level constructs can easily convert an Express VI to the underlying G code by right-clicking the Express VI and selecting Open Front Panel. Normal VIs can do everything an Express VI can do. The LabVIEW Professional Development System also includes a utility for creating custom Express VIs.(4)Incorporating C-Based SyntaxWe can incorporate sequentially executed text-based syntax into a VI block diagram using one of several techniques. The Formula Node offers an inline structure that supports a syntax similar to traditional C programming. Much like C, every line ends with a semicolon and variables must have a defined scope.The Inline C Node is similar to the Formula Node with additional support and functionality for low-level programming and header files without the overhead of a function call. Y ou can use the Inline C Node for any C code, including assembly directives and #defines, that syntactically is between the curly braces in a C file.The Inline C Node is available only for targets that use generated C code. The Inline C Node is not supported for desktop Windows targets.(5)Interfacing with Built AssembliesInstead of importing source code to a LabVIEW block diagram, you may want to call into built assemblies or reuse built LabVIEW applications in other environments. Applications written in LabVIEW can easily reuse existing code and algorithms developed in other languages or programming approaches. Additionally, you might need to build an assembly from LabVIEW code, which includes the programming approaches discussed above, to be called by a different environment.LabVIEW offers multiple solutions for both scenarios. LabVIEW can call external code in DLLs or shared libraries and code exposed through ActiveX or .NET interfaces. In addition, you can reuse LabVIEW code in other programming languages by building a LabVIEW DLL or shared library, or by using ActiveX.If you have existing C code and need to reuse it in LabVIEW, one technique is to build the code as a DLL and call it using the Call Library Function Node. In fact, based on your C application architecture, you can use simple LabVIEW parallel programming to run two or more existing C routines in parallel without the additional complexity of C-based multithreaded programming. To make importing external libraries simple, LabVIEW includes the Import Shared Library Wizard, which automatically creates or updates a LabVIEW wrapper VI project library for Windows .dll file, Mac OS .framework file, or Linux .so file functions.Interfacing with the command-line is also possible with the System Exec.vi, which provides OS-specific interfaces for calling executables and other build libraries.(6)aking Advantage of Flexible ProgrammingThe combination of multiple programming approaches in a single development environment offers the advantage of reusing existing code and algorithms developed in other languages. It also makes it possible to combine simple, high-level abstractions with lower-level code that gives you more visibility and control of your application. These abstraction layers represent highly complex operations in simple, easy-to-read representations, but can be coupled with functions that give low-level control over application behavior and hardware interfaces. Thanks to tight integration with I/O, you can combine these approaches with real-world signals to take advantage of the most recent hardware technology such as multicore CPUs, FPGAs, andembedded processors.5.The Benefits of Programming Graphically in NI LabVIEW Graphical program design and programming simple, intuitive, and development of high efficiency. With the continuous development of the virtual instrument technology and graphical programming language test and control will become the most promising field development direction.Graphical programming language, which is also known as "G" language. Use this kind of language programming, basically don't write code, instead of chart or diagram. It was possible use technical personnel, scientists, engineers, familiar terminology and concepts, therefore, ICONS, LabVIEW is a tool for end users. It can enhance your own science and engineering construction, provides realizing instrument programming and convenient way of data acquisition system. Use it to research, design, testing principle and realization instrument system, can greatly improve the work efficiency.(1)abVIEW: Graphical, Dataflow ProgrammingLabVIEW is different from most other general-purpose programming languages in two major ways. First, G programming is performed by wiring together graphical icons on a diagram, which is then compiled directly to machine code so the computer processors can execute it. While represented graphically instead of with text, G contains the same programming concepts found in most traditional languages. For example, G includes all the standard constructs, such as data types, loops, event handling, variables, recursion, and object-oriented programming.The second main differentiator is that G code developed with LabVIEW executes according to the rules of data flow instead of the more traditional procedural approach (in other words, a sequential series of commands to be carried out) found in most text-based programming languages like C and C++. Dataflow languages like G (as well as Agilent VEE, Microsoft Visual Programming Language, and Apple Quartz Composer) promote data as the main concept behind any program. Dataflow execution is data-driven, or data-dependent. The flow of data between nodes in the program, not sequential lines of text, determines the execution order.This distinction may seem minor at first, but the impact is extraordinary because it renders the data paths between parts of the program to be the developer‟s main focus. Nodes in a LabVIEW program (in other words, functions, structures such as loops, subroutines, and so on) have inputs, process data, and produce outputs. Onceall of a given node‟s inputs contain valid data, that node executes its logic, produc es output data, and passes that data to the next node in the dataflow path. A node that receives data from another node can execute only after the other node completes execution.(2)ntuitive Graphical ProgrammingLike most people, engineers and scientists learn by seeing and processing images without any need for conscious contemplation. Many engineers and scientists can also be characterized as “visual thinkers,” meaning that they are especially adept at using visual processing to organize information. In other words, they think best in pictures. This is often reinforced in colleges and universities, where students are encouraged to model solutions to problems as process diagrams. However, most general-purpose programming languages require you to spend significant time learning the specific text-based syntax associated with that language and then map the structure of the language to the problem being solved. Graphical programming with G provides a more intuitive experience.Figure 4. Data originates in the acquisition function and then flows intuitively to the analysis and storage functions through wires.(3)utomatic Parallelism and PerformanceDataflow languages like LabVIEW allow for automatic parallelization. In contrast to sequential languages like C and C++, graphical programs inherently contain information about which parts of the code should execute in parallel. For example, a common G design pattern is the Producer/Consumer Design Pattern, in which two separate While Loops execute independently: the first loop is responsible for producing data and the second loop processes data. Despite executing in parallel (possibly at different rates), data is passed between the two loops using queues, which are standard data structures in general-purpose programming languages.Parallelism is important in computer programs because it can unlockperformance gains relative to purely sequential programs due to recent changes in computer processor designs. For more than 40 years, computer chip manufacturers increased processor clock speed to increase chip performance. Today, however, increasing clock speeds for performance gains is no longer viable because of power consumption and heat dissipation constraints. As a result, chip vendors have instead moved to new chip architectures with multiple processor cores on a single chip.To take advantage of the performance available in multicore processors, you must be able to use multithreading within your applications (in other words, break up applications into discrete sections that can be executed independently). If you use traditional text-based languages, you must explicitly create and manage threads to implement parallelism, a major challenge for nonexpert programmers.In contrast, the parallel nature of G code makes multitasking and multithreading simple to implement. The built-in compiler continually works in the background to identify parallel sections of code. Whenever G code has a branch in a wire, or a parallel sequence of nodes on the diagram, the compiler tries to execute the code in parallel within a set of threads that LabVIEW manages automatically. In computer science terms, this is called “implicit parallelism” because you do not have to specifically write code with the purpose of running it in parallel; the G language takes care of parallelism on its own.Beyond multithreading on a multicore system, G can provide even greater parallel execution by extending graphical programming to field-programmable gate arrays (FPGAs). FPGAs are reprogrammable silicon chips that are massively parallel – with each independent processing task assigned to a dedicated section of the chip –but they are not limited by the number of processing cores available. As a result, the performance of one part of the application is not adversely affected when more processing is added.6.Hardware Integration with NI LabVIEW(1)ave Development Time with Simpler System IntegrationMost measurement and control hardware comes with software. Usually, that software only works with the device or devices similar to the one the software came with, and the software likely has a fixed, limited feature set. When you want to do more than you can with the included software, such as incorporate multiple devices or add processing and reporting, you face the often daunting task of getting the hardware to work in a different software environment.System integration, getting everything setup and configured such that you begin programming a system, can be a major undertaking, often taking more time than the programming, measurement, or test you wish to perform. Integrating different hardware devices with traditional tools is littered with time-wasting steps and possible incompatibilities, increasing risk. First, you have to find the correct drivers for all of your hardware, and then you have to figure out how to install them and call them from software. Once your drivers are usable, you need them to communicate with the hardware and learn the programming model that the driver designer decided was appropriate for that particular device. LabVIEW can help save you time and frustration by eliminating some of these steps and making others markedly easier.LabVIEW is one software tool that can span all of your hardware components. Drivers are readily available for common hardware devices. Each hardware driver shares a similar, familiar programming model, and examples of how to use the model install directly into LabVIEW.(2)onnect to Any HardwareWith LabVIEW, you can use all of your hardware with a single development environment. Connectivity is made possible with driver software, which serves as the communication layer between LabVIEW and your hardware. LabVIEW driver software supplies seamless integration across multiple types of instruments, buses, and sensors, including data acquisition devices; boxed instruments; modular instruments; motion controllers and motor drives; machine vision and image processing hardware; wireless sensors; and field-programmable gate arrays (FPGAs). In the rare event that a LabVIEW driver doesn‟t already exist, you also can import drivers from other programming languages or use low-level communication to implement your own driver.(3)I HardwareWith more than 50 million I/O channels sold in the last 10 years, National Instruments is a global market leader in PC-based data acquisition, with a complete family of data acquisition products for desktop, portable, industrial, and embedded applications. Y ou can use NI-DAQmx driver software to integrate more than 200 data acquisition devices in LabVIEW on a variety of major buses and form factors, including USB, PCI, PCI Express, PXI, PXI Express, wireless, and Ethernet.(4)Third-Party HardwareLabVIEW does more than just connect to NI hardware. LabVIEW also connectsto thousands of third-party instruments through instrument drivers. The Instrument Driver Network (IDNet) offers more than 8,000 free drivers for instruments from more than 275 third-party vendors that make your hardware work with LabVIEW.From:。
实验虚拟仪器基础——NIELVIS入门
5)虚拟仪器(NI ELVIS)基础实验[实验目的]1.了解虚拟仪器概念2.学习NI ELVIS软面板仪器的使用,并进行实际测量3.了解G语言,LabVIEW编程初步[实验原理]一.虚拟仪器简介1.软件即仪器虚拟仪器(Virtual Instrument,简称VI)是基于计算机的软硬件测试平台。
虚拟仪器技术的优势在于可由用户定义自己的专用仪器系统,且功能灵活,很容易构建,所以应用面极为广泛。
20世纪80年代,随着计算机技术的发展,个人电脑可以带有多个扩展槽,就出现了插在计算机里的数据采集卡。
它可以进行一些简单的数据采集,数据的后处理由计算机软件完成,这就是虚拟仪器技术的雏形。
1986年,美国National Instruments公司(简称NI公司)提出了“软件即仪器”的口号,推出了NI-LabVIEW开发和运行程序平台,以直观的流程图编程风格为特点,开启了虚拟仪器的先河。
2.与传统仪器比较虚拟仪器∙使用者定义功能∙软件定义的界面∙网络/互联网的连接传统仪器∙制造商定义功能∙固定的界面∙有限的扩展功能3.LabVIEW图形化开发环境LabVIEW是一种图形化的编程语言和开发环境。
它功能强大且灵活,包含内容丰富的数据采集、分析、显示和存储工具。
LabVIEW用于实现对实际物理量的采集、分析和表达,利用它可以方便快捷地建立自己的虚拟仪器。
以LabVIEW为代表的图形化程序语言,又称为G语言。
使用这种语言编程时,基本上不需要编写程序代码,而是“绘制”程序流程图。
LabVIEW与虚拟仪器有着紧密联系,在LabVIEW中开发的程序都被称为VI(或虚拟仪器),其扩展名为vi。
VI包括三个部分:前面板(Front Panel)、程序框图(Block Diagram)和图标/连接器(Icon and Connector Pane)。
程序前面板用于设置输入数值和观察输出量,用于模拟真实仪表的前面板。
在程序前面板上,输入量称为控制器(Control),输出量称为显示器(Indicator)。
准确的说,什么是LabVIEW,它又能为我做什么呢? 毕业论文外文文献翻译
本科毕业设计(论文)外文翻译译文:准确的说,什么是LabVIEW,它又能为我做什么呢?每个人的LabVIEWLabVIEW是Laboratory Virtual Instrument Engineering Workbench的英文缩写,它是一种图形化的编程环境,使用图形化的符号来创建程序(通过连线把函数节点连接起来,数据就是在这些连线上流动的);在这点上,它不同于传统的文本编程语言像C,C++,或者Java。
然而,LabVIEW不仅仅是一种编程语言,它是专门为那些工作中需要大量编程的工作的工程师和科学家们设计的一种交互式程序开发和执行的系统。
LabVIEW开发环境可以工作在装有windows,mac os x,或linu任何一种操作系统的计算机上。
LabVIEW创建的程序可以在上述平台上运行,同时也可以运行于microsoft pocket pc,mocrosoft windows ce,palm os和大量的嵌入式平台,包括现场可编程门阵列(FPGAs),数字信号处理器(DSPs)和微处理器。
许多使用功能强大的图形化编程语言LabVIEW的用户亲切的称之为“G”语言(取自graphical),LabVIEW能够让你的开发效率提高几个数量级。
使用传统语言可能需要几周或者几个月才能完成的程序,如果用LabVIEW编写,几个小时就能完成,其中一个原因是LabVIEW是专为用户设计的,用来进行测量,分析数据和显示结果。
另一个原因是LabVIEW有丰富的图形化用户接口(GUI),使用这些接口使变成变得很容易。
它也非常适合用来进行仿真,表述思想,编写一般程序,或者讲述基本编程概念。
LabVIEW可以提供比标准的实验室仪器更加灵活的仪器,因为这种仪器是基于软件的,是由你来定义仪器的功能,而不是由仪器制造来定义。
为了完成你的任务,一个完整的虚拟仪器配置包括:你的电脑,即插即用的硬件和LabVIEW。
使用LabVIEW你能够准确的创建你所需要的虚拟仪器,这种仪器的价格是传统仪器价格的几分之一。
- 1、下载文档前请自行甄别文档内容的完整性,平台不提供额外的编辑、内容补充、找答案等附加服务。
- 2、"仅部分预览"的文档,不可在线预览部分如存在完整性等问题,可反馈申请退款(可完整预览的文档不适用该条件!)。
- 3、如文档侵犯您的权益,请联系客服反馈,我们会尽快为您处理(人工客服工作时间:9:00-18:30)。
中文3800字毕业设计(论文)外文资料翻译系(院):交通工程系专业:车辆工程姓名:学号:外文出处:LabVIEW based Advanced Instrumentation Systems, 2007: 1-31(用外文写)附件: 1.外文资料翻译译文;2.外文原文。
附件1:外文资料翻译译文虚拟仪器的简介Author : Grzegorz Polakqw , Mieczyslaw摘要:本文介绍了基于Lab VIEW软件虚拟仪器的技术特点和设计方法。
虚拟仪器的关键技术是应用软件,仪器的主要功能多是由软件来实现的。
所谓“软件即仪器”。
目前设备多采用单一模拟器技术,无法真正实现装备的实际性能。
使用虚拟仪器不但可以节约大量模拟设备的经费投入,而且能够提高质量与效率。
与目前大多数模拟设备的经费投入,而且能够提高质量和效率。
与目前大多数模拟设备相比,虚拟仪器能够让使用人员主动参与生产过程甚至设计过程。
有利于使用者进行主动和与探索式学习。
关键词:虚拟仪器 Lab VIEW 设计学习目标读者在完成本章阅读将有下面一个了解:—虚拟仪器的历史—虚拟仪器的演变—虚拟仪器的定义—虚拟仪器的体系结构—Lab VIEW的演变—使用Lab VIEW创建的虚拟仪器—Lab VIEW的优势—虚拟仪器在发动机工程的应用—超越个人电脑的虚拟仪器1.1简介一种基于用户从环境或从被测单元收集数据,并显示信息的一种仪器,这样一种仪器可以采用变频器来测试如随着温度或压力的变化的物理参数的变化,采集信息并将其转换成相应的电信号,例如电压和频率的变化。
这种仪器也被定义为一种物理软件设备。
它对获得的来自另一台仪器的数据进行分析和处理,然后在显示器或录音设备上输出数据,这种记录仪包括示波器,频谱分析仪等。
基于对源数据的收集和分析的这种形式仪器得到广泛应用。
1.2虚拟仪器简介虚拟仪器是一个跨学科领域,包括温度、压力、距离、光和声音的频率和振幅,以及包括电压、电流和频率在内的电气参数。
为了创建用于灵活控制和监控的精密仪器,其兼有了传感、硬件和软件技术。
虚拟仪器的概念诞生于19世纪70年代后期,当时随着微处理器技术的完善使一台机器的功能更容易被使用,其软件更改也更方便。
虚拟仪器的灵活性在很大程度上取决于专用硬件。
通常,只有应用特定的程序,将信号调理模块和模拟数字转换器作为接口,连接到外部仪器中使用,因此,计算机或使用专门的板载,控制和采集数据的处理器的仪器,不能简单定义为虚拟仪器。
随着在生物技术越来越复杂的应用,利用虚拟仪器可以有效的降低技术设备和生产成本。
虚拟仪器得到更加深入的研究。
1.3虚拟仪器的历史从历史上看,虚拟仪器系统和测量棒、温度计和尺度一样,都起源于遥远的过去。
到了近代,虚拟仪器系统已普遍运用到几乎所有设备,例如,一个由机电压力表传感器连接到另一个传感器的信号调理电路,从信号处理、输出到显示器面板,也许能形成一条记录,其中的微量元素对不断变化的条件,通过机械手臂相联系到一个旋转的滚筒,创造一种随压力变化的时间纪录。
但是,直到20世纪80年代采用应用程序,由单一路线到中央控制面板,才组成了一个阵列显示物理数据,利用计数器装置连接开关旋钮套、物理仪器和个别按钮控制的复杂系统才得以应用,例如过程控制。
1.4 虚拟仪器的演变因为虚拟仪器技术结合主流商业技术,结合灵活的软件和多种便于控制的硬件设备的电脑技术,所以工程师和科学家们可以创建用户定义的系统,以满足他们的具体应用需求。
利用虚拟仪器,工程师和科学家们可以缩短开发时间,设计更高品质的产品,并降低设计成本。
一种集合数据收集、工具种类繁多、电脑化控制和操作的仪器被设计,并在商业市场上广泛流通,就是现在所谓的“虚拟仪器。
“1.5 早期挑战虚拟仪器是必要的,因为它提供了适用于当今的概念:产品和工艺设计,开发和交付所需的快速适应性检测仪器。
只有在虚拟仪器的条件下,工程师和科学家才可以创建自己需要的模块,才能跟上世界的要求。
1.6 虚拟仪器虚拟仪器提供了一个测量和自动化系统建设的新模式,并成为主流。
其成功的关键包括电脑技术的快速进步、爆炸性的低成本、高性能数据转换器(半导体)的开发以及系统设计软件的出现。
这些因素为用户访问虚拟仪器系统提供了非常广泛的基础。
虚拟仪器系统是一个由用户控制,通过电脑桌面操作,发展起来用于电脑测试,用于控制硬件服务和信息输出或者数据记录,并在电脑屏幕上显示的技术系统,其利用桌面计算机的外部设备接口收集和整理测试和测量数据。
虚拟仪器还扩展到基于PC系统的用于控制、收集和处理数据的程序电脑化仪器系统。
也有几个在公开文献对虚拟仪器的定义。
桑特定义为“具有一般功能,具有特定程序的一种虚拟工具。
”戈德堡介绍说,“虚拟仪器是一些专门的亚基组成,一些通用的电脑,一些软件,和一个小诀窍“。
虽然是非正式的,但这些对虚拟仪器定义却具有一般概念的基本思想,即虚拟与足够的资源,“如果我们只是模拟,加载其他计算机软件的话,那么任何计算机都可以模拟任何其他计算机。
”这种普遍性介绍了虚拟仪器的基本功能属性:通过软件更改的形式,使用户能够将其功能修改以满足广泛的应用。
虚拟仪器是由以下模块组成:传感器模块、传感器接口、信息系统的接口、处理模块、数据接口、用户界面。
一个有效的用户界面,展示了对虚拟仪器的控制效率和检测精度,影响操作者对于测量结果的解释。
因为电脑的使用界面比传统仪器的用户界面更容易影响和改变,就有可能购买更多的演示效果,为用户界面进行自定义。
根据报告和互动功能,我们可以将虚拟仪器的接口分为四类:终端用户界面、图形用户界面、多通道用户界面和虚拟与增强现实接口。
集成功能的模块限制了虚拟仪器的灵活性。
最简单,最灵活的表达方式,就是建立一个为一个单一的、单片的应用程序软件,采用物理的方法集合为一体的综合虚拟仪器,这种方法能达到最佳的性能,但是维护和制作困难,因此,一个被认为在建模和设计时,面向对象的设计仪器,它更方便地使用模块化组成。
虚拟仪器的每一个模块,都能结合其他对象,利用虚拟仪器的界面实现数据信息交换。
类似的做法是面向组件的方法,其中,除了元件对象的逻辑分离外,它们在物理上也在不同的单元放置,以便重用。
另一种方法,在其基本理念到面向对象的方法相似,是一种非常规的采用内分层控制器方法来解决传感器模块功能集成结构的耦合模式。
这种传感器模型应用于很多领域,包括对人体生理信号的传感器电交互系统。
在这种传感器的互动模式,从遥感的原始数据流,例如脑电图(EEG)的数据,经过最多两个信号预处理,然后才传递到任意一个应用程序或直接到主体的水平。
第二个是允许选择的命令层,允许将即插即用功能一样复杂的处理机制整合起来,发挥组织更灵活的功能来需求解决方案被应用于虚拟仪器数据处理。
1.7 Lab VIEW的演变任何虚拟仪器的核心都是灵活的软件,世界上最好的虚拟仪器软件平台之一——Lib VIEW,即实验室虚拟仪器工程工作台的扩大的缩写。
Lab VIEW的确是一个强大的信号采集、测量分析和数据演示,没有了传统开发工具的复杂性的一种灵活性的编程语言,提供了一种图形化开发环境。
1986年,美国国家仪器公司将虚拟仪器引入Macintosh,它具有快速性和一致性,作为一种高效、功能强大的编程语言持续吸引了工程师和科学家在测试、控制和设计中的应用。
如今,虚拟仪器是数千名工程师和科学家首选的图形化开发环境。
有了合适的软件工具,工程师和科学家们可以高效地创建自己的应用程序,通过设计,可以整合一个特定的进程,适合自己需要的例程。
他们还可以创建一个最适合应用程序目的的和那些可以进行交流的相应的用户界面。
他们可以定义怎样、何时从设备获取信息、如何处理、操纵和存储数据、结果如何呈现给用户。
凭借强大的软件,我们可以将连续的做出结果的程序输入到仪器,使其适应信号的变化或者利用或多或少的处理能力显示必要的结果。
1.8使用Lab VIEW创建的虚拟仪器Lab VIEW是虚拟仪器的一个组成部分,因为它提供了一个工程师和科学家在考虑具体应用需要的、易于使用的开发环境。
Lab VIEW提供了更容易连接到其他的硬件和软件的各种强大的功能。
图形化编程是Lab VIEW提供工程师和科学家最强大的特性之一。
在Lab VIEW的条件下,用户可以通过一个在计算机屏幕上创建的图形用户界面,自定义虚拟仪器,通过它人们可以实现:开发仪器的实用程序、控制选定的硬件、获得数据的分析、显示结果。
1.9 Lib VIEW 的优势对软件的选择很重要,因为软件是整个系统的的核心组成部分。
选择合适的软件可以最大限度地提高生产率,同时一个软件如果不适应需要则会消耗时间和生产力。
Lab VIEW可帮助用户从开始到完成的过程中利用更少的时间完成更多的工程。
相对于其他开发软件,Lab VIEW有几个方面有助于提高生产力。
例如易学易用等。
1.10超越个人电脑的虚拟仪器近日,商用PC技术已经被应用到嵌入式系统。
例如Windows CE中, Intel x86处理器,PCI和Compact PCI总线,嵌入式以太网开发。
由于虚拟仪器严重的对商业成本和性能优势技术依赖,它也被扩大到具有更多的嵌入式的和实时的能力。
举例来说,Lab VIEW在Linux上的运行,就像嵌入式电子投标系统从Ventur COM的实时嵌入式操作系统的具体指标体系一样自然流畅。
虚拟仪器的使用可以通过安放在系统中的一个工具箱,放在桌面上的一个嵌入式系统中。
一个一人注目的技术变化、影响嵌入式系统开发的是计算机网络设计体系和网络交流。
随着电脑的普及,以太网现在已经成为全球公司和企业的标准基础设施。
综述虚拟仪器在日新月异的计算机技术推动下日益强大,在一个开放的框架的基础上提供我们更多力量,去创建和定义更多的系统。
这个概念不仅确保了成果在未来的使用,而且也提供了更多的灵活性,以适应需求的变化和扩展。
虚拟仪器的设计在科学家和工程师利用Lab VIEW的不断开发和完善下,创造了更亲近的开发环境和更强大的功能。
最后,它提供了用于用户设计自定义的进一步加强直观界面的虚拟仪器系统软件。
Lab VIEW就是此类软件的例子。
Lab VIEW生动的开发环境,提供了具有表现性和灵活性的编程语言,特别是在测量和自动化应用上,提供了高水平的函数关系和实用工具。
附件2:外文原文(复印件)Introduction to Virtual InstrumentationAuthor : Grzegorz Polakqw , Mieczyslaw Abstract : The technique characteristics and the design methods of virtual instrument on Lab VIEW software are introduced. The key techniques of the virtual instrument is software, the main function of the instrument is realized by the software, so called " software namely instrument" . The weapon equipments cannot realize its real performance because o f its single simulator technology. Use of virtual instrument couled not only save a great quantity of funds for equipments, but also increase the quality and efficiency. The people w ho use the virtual instrument can take participate in the equipments procedure of produce and design.Key Words: virtual instrument Lab VIEW designLearning Objectives. On completion of this chapter the reader will have a knowledge on:–History of Instrumentation Systems–Evolution of Virtual Instrumentation–Premature Challenges of VI–Definition of Virtual Instrumentation–Architecture of Virtual Instrumentation–Evolution of Lab VIEW–Creating Virtual Instruments using Lab VIEW–Advantages of Lab VIEW–Virtual Instrumentation in the Engineering Process–Virtual Instruments Beyond the Personal Computer1.1 IntroductionAn instrument is a device designed to collect data from an environment, or from a unit under test, and to display information to a user based on the Collected data, Such an instrument may employ a transd user to sense changes In a physical parameter, such as temperature or pressure, and to convert the Sensed information into electrical signals, such as voltage or frequency variations. The term instrument may also be defined as a physical software device .That performs an analysis on data acquired from another instrument and then outputs the processed data to display or recording devices. This second category of recording instruments may include oscilloscopes, spectrum analyzers, and digital millimeters. The types of source data collected and analyzed by Instruments may thus vary widely.1.2 Introduction to Virtual Instrumentationtemperature, pressure, distance, frequency and amplitudes of light and sound, and electrical parameters including voltage, current, and frequency. Virtual instrumentation is an interdisciplinary field that merges sensing, hardware, and software technologies in order to create flexible and sophisticated instruments for control and monitoring applications. The concept of virtual instrumentation was born in late1970s,when microprocessor technology enabled a machine’s function to be more easily changed by changing its software. The flexibility is possible as the capabilities of a virtual instrument depend very little on dedicated hardware –commonly, only application specifi c signal conditioning module and the analog-to-digital converter used as interface to the external world. Therefore, simple use of computers or specialized onboard processors in instrument control and data acquisition cannot be defined as virtual instrumentation. Increasing number of biomedical applications use virtual instrumentation to improve insights into the underlying nature of complex phenomena andreduce costs of medical equipment and procedures.1.3 History of Instrumentation SystemsHistorically, instrumentation systems originated in the distant past, with measuring rods, thermometers, and scales. In modern times, instrumentation systems have generally consisted of individual instruments, for example, an electromechanical pressure gauge comprising a sensing transducer wired to signal conditioning circuitry, outputs a processed signal to a display panel and perhaps also to a line recorder, in which a trace of changing conditions is linked onto a rotating drum by a mechanical arm, creating a time record of pressure changes. Complex systems such as chemical process control applications employed until the 1980s consisted of sets of individual physical instruments wired to a central control panel that comprised an array of physical data display devices such as dials and counters, together with sets of switches, knobs, and buttons for controlling the instruments.1.4 Evolution of Virtual InstrumentationVirtual instrumentation combines mainstream commercial technologies, such as the PC, with flexible software and a wide variety of measurement and control hardware, so engineers and scientists can create user-defined systems that meet their exact application needs. With virtual instrumentation, engineers and scientists reduce development time, design higher quality products, and lower their design costs. A large variety of data collection instruments designed specifically for computerized control and operation were developed and made available on the commercial market, creating the field now called “virtual instrumentation.”1.5 Premature ChallengesVirtual instrumentation is necessary because it delivers instrumentation with the rapid adaptability required for today’s concept, product, and process design, development, and delivery. Onlywith virtual instrumentation can engineers and scientists create the user-defined instruments required to keep up with the world’s demands. 1.6 Virtual InstrumentationVirtual instrumentation achieved mainstream adoption by providing a new model for building measurement and automation systems. Keys to its success include rapid PC advancement; explosive low-cost, high-performance data converter (semiconductor) development; and system design software emergence. These factors make virtual instrumentation systems accessible to a very broad base of users.A virtual instrumentation system is a software that is used by the user to develop a computerized test and measurement system, for controlling an external measurement hardware device from a desktop computer, and for displaying test or measurement data on panels in the computer screen. The test and measurement data are collected by the external device interfaced with the desktop computer. Virtual instrumentation also extends to computerized systems for controlling processes based on the data collected and processed by a PC based instrumentation system.There are several definitions of a virtual instrument available in the open literature. Santori defines avirtual instrument as “an instrument whose general function and capabilities are determined in software. ”Goldberg describes that “ a virtual instrument is composed of some specialized subunits, some general-purpose computers, some software, and a little know-how”. Although informal, these definition capture the basic idea of virtual instrumentation and virtual concepts in general–provided with sufficient resources, “ any computer can simulate any other if we simply load it with software simulating the other computer .”This universality introduces one of the basic properties of a virtual instrument–its ability to change form through software, enabling a user to modify its function at willto suit a wide range of applications.A virtual instrument is composed of the following blocks:–Sensor module–Sensor interface–Information systems interface–Processing module–Data base interface–User interfaceAn effective user interface for presentation and control of a virtual instrument affects efficiency and precision of an operator do the measurements and facilitates result interpretation. Since computer’s user interfaces are much easier shaped and changed than conventional instrument’s user interfaces, it is possible to employ more presentation effects and to customize the interface for each user. According to presentation and interaction capabilities, we can classify interfaces used in virtual instrumentation in four groups:–Terminal user interfaces–Graphical user interfaces–Multimodal user interfaces and–Virtual and augmented reality interfacesFunctional integration of modules governs flexibility of a virtual instrument. The simplest, and the least flexible way, is to create a virtual instrument as a single, monolithic application with all software modules of the virtual instruments logically and physically integrated. This approach can achieve the best performance, but makes difficult maintenance and customization. Therefore, it is more convenient to use modular organization. An object-oriented method was identified as natural approach in modeling and design of instruments. Each module of a virtual instrument is then implemented as an object with clearly defined interface, integrated with other objects usingmessage interchange. Similar approach is component-oriented approach, where, in addition to logical separation of components into objects, they are physically placed into different unit to allow reuse. Another approach, similar in its basic idea to the object-oriented approach, is a structural coupling paradigm for nonconventional controllers that define the layered approach to functional integration of sensor modules. This sensor model was applied in many domains, including electrophysiological interaction systems with sensors for human physiological signals. In this sensor interaction model, a stream of rawdata from the sensing hardware, for example electroencephalogram (EEG) data, passes through up to two levels of signal preprocessing before it is either passed to an application or presented directly to a subject. Second command layer, which is optional, allows more flexible organization of data processing and plug-and-play like integration of complex processing mechanisms into a virtual instrument solution.1.7 Evolution of Lab VIEWAt the heart of any virtual instrument is flexible software, and National Instruments invented one of the world’s best virtual instrumentation software platforms –Lab VIEW expanded as Laboratory Virtual Instrumentation Engineering Workbench. Lab VIEW is a powerful graphical development environment for signal acquisition, measurement analysis, and data presentation, giving the flexibility of a programming language without the complexity of traditional development tools. Since1986, when National Instruments introduced Lab VIEW for the Macintosh, it has quickly and consistently attracted engineers and scientists looking for a productive, powerful programming language to use in test, control and design applications. Today, Lab VIEW is the preferred graphical development environment for thousands of engineers and scientists. With the right software tool, engineers and scientists can efficiently create their own applications, by designing andintegrating the routines that a particular process requires. They can also create an appropriate user interface that best suits the purpose of the application and those who will interact with it. They can define how and when the application acquires data from the device , how it processes, manipulates and stores the data, and how the results are presented to the user. With powerful software, we can build intelligence and decision-making capabilities into the instrument so that it adapts when measured signals change inadvertently or when more or less processing power is required.1.8 Creating Virtual Instruments Using Lab VIEWLab VIEW is an integral part of virtual instrumentation because it provides an easy-to-use application development environment designed specifically with the needs of engineers and scientists in mind. Lab VIEW offers powerful features that make it easy to connect to a wide variety of hardware and other software. Graphical Programming is one of the most powerful feature that Lab VIEW offers engineers and scientists. With Lab VIEW, the user can design custom virtual instruments by creating a graphical user interface on the computer screen through which one can:–Operate the instrumentation program–Control selected hardware–Analyze acquired data–Display results1.9 Advantages of Lab VIEWThe choice of software is important because software is generally the central component that ties the entire system together. Choosing the right software can maximize productivity, while a software package that does not fitthe needs could drain time and productivity. Lab VIEW helps the user to do more projects done in less time, by streamlining the process from inception through completion. There are several areasin Lab VIEW that contribute to a significant gain in productivity when compared to other development software . for example easy to learn, easy to use,1.10 Virtual Instruments. Beyond the Personal ComputerRecently, commercial PC technologies have been migrating into embedded systems. Examples include Windows CE, Intel x86-based processors, PCI and Compact PCI buses, and Ethernet for embedded development. Because virtual instrumentation relies so heavily on commercial technologies for cost and performance advantages, it also has expanded to encompass more embedded and real-time capabilities. For example, Lab VIEW runs on Linux as well as the embedded ETS real-time operating system from Ventur Com on specifi c embedded targets. The option of using virtual instrumentation as a scalable framework that extends from the desktop to embedded devices should be considered a tool in the complete toolbox of an embedded systems developer. A dramatic technology change example that affects embedded systems development is networking and the Web. With the ubiquity of PCs , Ethernet now dominates as the standard network infrastructure for companies worldwide.SummaryVirtual instrumentation is fueled by ever-advancing computer technology and offers us the power to create and define a system based on an open framework . This concept not only ensures that a work will be usable in the future but also provides the flexibility to adapt and extend as needs change. Lab VIEW was designed with scientists and engineers in mind, providing powerful tools and a familiar development environment created specifically for the design of virtual instruments. Finally, system design software that provides an intuitive interface for designing custom instrumentation systems furthers virtual instrumentation . Lab VIEW is an example of such software. The Lab VIEWgraphical development environment offers the performance and flexibility of a programming language, as well as high-level functionality and configuration utilities designed specifically for measurement and automation applications.欢迎您的下载,资料仅供参考!。